文献翻译-集成张力水平系统在连续轧制线的应用
收放卷张力控制定义及应用

收放卷张力控制定义及应用收放卷张力控制定义及应用张力控制是指能够持久地控制原料在设备上输送时的张力的能力。
这种控制对机器的任何运行速度都必须保持有效,包括机器的加速、减速和匀速。
即使在紧急停车情况下,也应有能力保证被分切物不破损。
张力控制的稳定与否直接关系到分切产品的质量。
若张力不足,原料在运行中产生漂移,会出现分切复卷后成品纸起皱现象;若张力过大,原料又易被拉断,使分切复卷后成品纸断头增多。
张力控制系统主要应用于对带材和线材生产线中的卷取机和开卷机的控制。
例如,为了提高产品质量,使所卷带材表面平整、厚度均匀和带卷紧而且齐,必须对卷取机(或开卷机)和压延机之间的张力进行控制,使之恒定。
控制张力的方法分为间接法和直接法两类。
间接法又可采用两种方式:一种是在保持驱动电动机的电枢电流恒定的条件下,通过调节使电动机的磁通量随带卷(或线卷)直径成比例地变化,维持张力的恒定;另一种方式是调节电动机电枢电压,使电枢电流随带卷直径成比例变化来保持张力恒定。
直接法是对张力的直接反馈控制。
用张力计测量实际的张力值,作为反馈信号,以控制张力恒定。
直接法的优点是控制系统简单,可避免卷径变化、速度变化和空载转矩等对张力的影响,精度较高。
缺点是张力计的响应速度较慢。
在实际工业生产中,间接法远比直接法应用为广。
所谓的张力控制,通俗点讲就是要能控制电机输出多大的力,即输出多少牛顿。
反应到电机轴即能控制电机的输出转距。
真正的张力控制不同于靠前后两个动力点的速度差形成张力的系统,靠速度差来调节张力的实质是对张力的PID控制,要加张力传感器。
而且在大小卷启动、停止、加速、减速、停车时的调节不可能做到象真正的张力控制的效果,张力不是很稳定。
肯定会影响生产出产品的质量。
闭环式全自动张力控制是由张力传感器直接测定料带的实际张力值,然后把张力数据转换成张力信号反馈回张力控制器,通过此信号与控制器预先设定的张力值对比,计算出控制信号,自动控制执行单元则使实际张力值与预设张力值相等,以达到张力稳定目的。
张力系统的原理及应用

张力系统的原理及应用1. 引言张力系统是一种通过施加拉力或压力来保持物体的平衡或稳定的系统。
在各个行业中,张力系统被广泛应用于维持物体形状、控制运动和传输力量等关键任务中。
本文将介绍张力系统的基本原理和常见应用领域。
2. 张力系统的原理张力系统的工作原理基于平衡力的原理。
当物体受到外部力或负荷作用时,张力系统通过调节拉力或压力来实现平衡。
以下是张力系统的基本原理:2.1 张力的定义张力是指绳线或其他类似结构中作用于某一截面上的拉力。
根据牛顿第三定律,张力在相反方向同时作用于相邻的两个截面上,使得整个结构保持平衡。
2.2 张力系统的要素张力系统包括以下要素: - 张力元件:通常是绳、链或带状物等。
- 支撑点:用于支撑、固定张力元件的点。
- 外部力:通过张力元件传输给物体的力。
- 物体负荷:施加在物体上的外力。
2.3 平衡条件张力系统的平衡取决于以下条件: - 任何两个支撑点之间的张力力量相等。
-外部力和物体负荷的合力为零。
- 张力元件维持恒定的长度。
2.4 张力系统的调节当外部力或物体负荷发生变化时,张力系统会通过自身的调节机制来保持平衡。
该调节机制可以通过改变张力元件的长度或调整支撑点的位置来实现。
3. 张力系统的应用张力系统在许多领域中发挥着重要作用。
以下是一些常见的应用领域:3.1 材料加工张力系统在材料加工中起到了关键作用。
例如在纺织业中,张力系统通过维持纱线的张力来保持纱线的平稳传输和控制织物的质量。
类似地,在印刷业中也广泛使用张力系统来保持纸张和印刷带的稳定性。
3.2 运动控制张力系统在运动控制中也有广泛应用。
例如,在旗帜或帆布悬挂中,张力系统通过调整绳索的张力来控制旗帜或帆布的展开和收束。
此外,在工业自动化领域,张力系统在输送带和绳索传动系统中也起到了重要作用。
3.3 航空航天在航空和航天领域,张力系统被广泛用于控制和平衡飞行器的运动。
例如,在卫星部署和空中加油中,张力系统被用来控制绳索和油管的张力,确保操作的安全性和稳定性。
冷轧连续镀锌机组带钢张力控制算法研究

冷轧连续镀锌机组带钢张力控制算法研究摘要:张力是工业生产过程中的重要参数。
在带钢连续镀锌过程中,带钢张力的波动是造成带钢产品质量下降及制约连续镀锌机组高速运行的重要原因。
关键词:冷轧,张力控制。
Strip Tension Control in Continuous Galvanizing Process Abstract: Tension is the importance parameter for the industrial production. In continuous galvanizing process, strip tension is an important factor that decides whether the continuous galvanizing line works steadily and promptly or not.Key words: cold-rolling, tension control引言连续镀锌机组是生产高质量冷轧带钢的关键设备,带钢在该机组中进行再结晶退火处理,以完善带钢的微观组织,提高带钢的塑性和冲压成形性。
经过镀锌的带钢防腐性能大大提高。
带钢具有合适的张力是带钢高速运行及防止带钢跑偏和热瓢曲,获得良好带钢板形的重要条件之一。
张力的波动不仅会影响带钢产品的质量,严重时会导致带钢断带,造成连续镀锌机组停产。
镀锌机组一旦停产,将会产生废品和协议品。
因此,掌握带钢张力的动态特性,保证带钢在连续镀锌过程中具有合适、稳定的张力,是提高带钢产品质量和产量的重要手段。
连续镀锌机组工艺过程十分复杂,设备众多,自动化控制系统所涉及的范围非常广泛,但控制方法和应用的理论并不像冷连轧机那样复杂。
各个工艺段存在共同的自动化控制功能,分别为:物料跟踪功能,带钢速度控制,带钢张力控制,设备的顺序动作控制,急停连锁控制;数据采集与处理,二级数据库管理,炉区数学模型控制,气刀测厚镀层控制。
张力控制——精选推荐
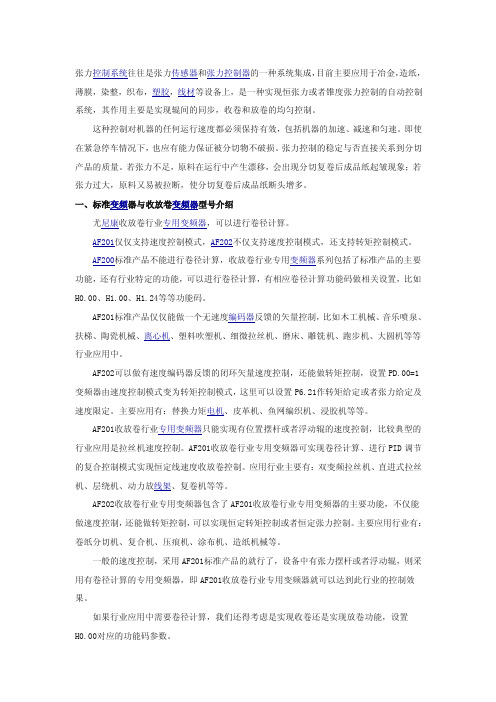
张力控制系统往往是张力传感器和张力控制器的一种系统集成,目前主要应用于冶金,造纸,薄膜,染整,织布,塑胶,线材等设备上,是一种实现恒张力或者锥度张力控制的自动控制系统,其作用主要是实现辊间的同步,收卷和放卷的均匀控制。
这种控制对机器的任何运行速度都必须保持有效,包括机器的加速、减速和匀速。
即使在紧急停车情况下,也应有能力保证被分切物不破损。
张力控制的稳定与否直接关系到分切产品的质量。
若张力不足,原料在运行中产生漂移,会出现分切复卷后成品纸起皱现象;若张力过大,原料又易被拉断,使分切复卷后成品纸断头增多。
一、标准变频器与收放卷变频器型号介绍尤尼康收放卷行业专用变频器,可以进行卷径计算。
AF201仅仅支持速度控制模式,AF202不仅支持速度控制模式,还支持转矩控制模式。
AF200标准产品不能进行卷径计算,收放卷行业专用变频器系列包括了标准产品的主要功能,还有行业特定的功能,可以进行卷径计算,有相应卷径计算功能码做相关设置,比如H0.00、H1.00、H1.24等等功能码。
AF201标准产品仅仅能做一个无速度编码器反馈的矢量控制,比如木工机械、音乐喷泉、扶梯、陶瓷机械、离心机、塑料吹塑机、细微拉丝机、磨床、雕铣机、跑步机、大圆机等等行业应用中。
AF202可以做有速度编码器反馈的闭环矢量速度控制,还能做转矩控制,设置PD.00=1变频器由速度控制模式变为转矩控制模式,这里可以设置P6.21作转矩给定或者张力给定及速度限定。
主要应用有:替换力矩电机、皮革机、鱼网编织机、浸胶机等等。
AF201收放卷行业专用变频器只能实现有位置摆杆或者浮动辊的速度控制,比较典型的行业应用是拉丝机速度控制。
AF201收放卷行业专用变频器可实现卷径计算、进行PID调节的复合控制模式实现恒定线速度收放卷控制。
应用行业主要有:双变频拉丝机、直进式拉丝机、层绕机、动力放线架、复卷机等等。
AF202收放卷行业专用变频器包含了AF201收放卷行业专用变频器的主要功能,不仅能做速度控制,还能做转矩控制,可以实现恒定转矩控制或者恒定张力控制。
冷连轧机组板带张力测量系统分析及改进
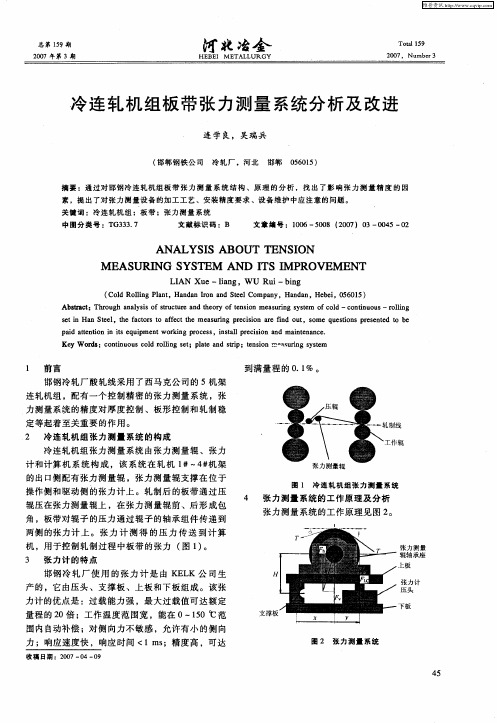
图 1 冷 连 轧 机 组 张 力 测 量 系 统
4 张力测 量 系统 的工作原 理及 分析 张力测 量 系统 的工作 原理见 图 2 。
辊轴 承座
上 板
邯 钢 冷 轧 厂使 用 的 张 力 计 是 由 K L 公 司生 EK
产的 ,它 由压头 、支 撑板 、 上板 和下 板组成 。该张
Ke or s:c tn usc l o ln e ;p ae a d srp;tnso , s rng s se yW d on iuo o d r li g s t l t ti n e i n m ' u i y tm a
1 前 言
到满量 程 的 0 1 。 .%
维普资讯
总 第 1 9期 5
20 07年 第 3期
河 北 冶全
H EBE M ETAL I LU R G Y
To a 5 tl1 9
2 0 0 7, N u b r3 m e
冷 连 轧 机 组 板 带 张 力 测 量 系统 分析 及 改进
中 图 分 类 号 :T 3 37 G 3 . 文献 标 识 码 :B 文 章编 号 :10 5 0 【07 3— 0 5— 2 0 6— 08 2 0 )0 0 4 0
ANALYS S AB I 0UT TENS 0N 1
M EAS UR G YS M S TE AND TS I P I M R0VEM ENT
邯 钢冷轧 厂酸 轧线 采用 了西 马克 公 司的 5机架 连轧机组 ,配 有一个 控 制精 密 的张力 测量 系统 ,张 力测量 系统 的精度对 厚 度控 制 、板形控 制和 轧 制稳
定等起着 至关 重要 的作 用 。
2 冷连 轧机 组张 力测量 系统 的构 成
复杂断面型钢连轧机微张力控制系统的研究
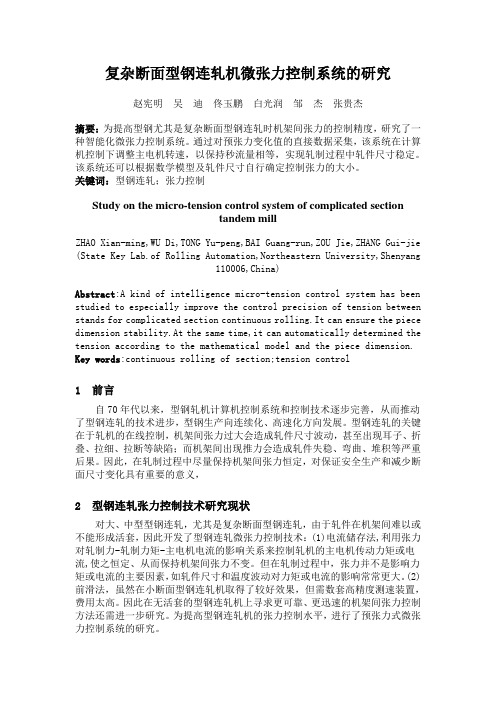
复杂断面型钢连轧机微张力控制系统的研究赵宪明吴迪佟玉鹏白光润邹杰张贵杰摘要:为提高型钢尤其是复杂断面型钢连轧时机架间张力的控制精度,研究了一种智能化微张力控制系统。
通过对预张力变化值的直接数据采集,该系统在计算机控制下调整主电机转速,以保持秒流量相等,实现轧制过程中轧件尺寸稳定。
该系统还可以根据数学模型及轧件尺寸自行确定控制张力的大小。
关键词:型钢连轧;张力控制Study on the micro-tension control system of complicated sectiontandem millZHAO Xian-ming,WU Di,TONG Yu-peng,BAI Guang-run,ZOU Jie,ZHANG Gui-jie (State Key Lab.of Rolling Automation,Northeastern University,Shenyang110006,China)Abstract:A kind of intelligence micro-tension control system has been studied to especially improve the control precision of tension between stands for complicated section continuous rolling.It can ensure the piece dimension stability.At the same time,it can automatically determined the tension according to the mathematical model and the piece dimension. Key words:continuous rolling of section;tension control1 前言自70年代以来,型钢轧机计算机控制系统和控制技术逐步完善,从而推动了型钢连轧的技术进步,型钢生产向连续化、高速化方向发展。
轧钢机中英文对照外文翻译文献
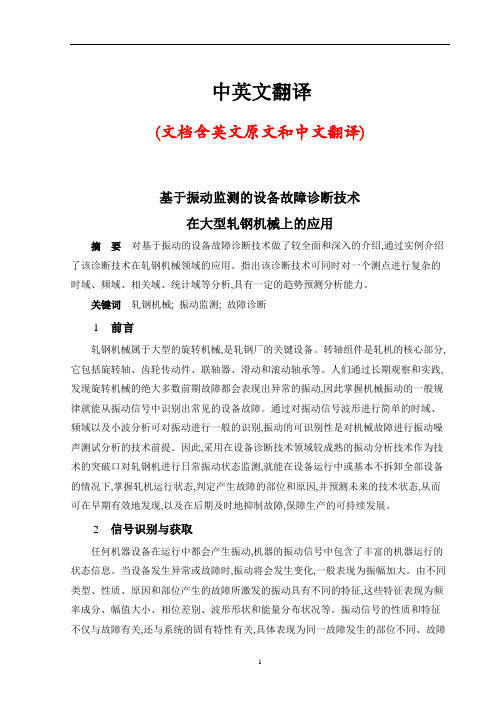
中英文翻译(文档含英文原文和中文翻译)基于振动监测的设备故障诊断技术在大型轧钢机械上的应用摘要对基于振动的设备故障诊断技术做了较全面和深入的介绍,通过实例介绍了该诊断技术在轧钢机械领域的应用。
指出该诊断技术可同时对一个测点进行复杂的时域、频域、相关域、统计域等分析,具有一定的趋势预测分析能力。
关键词轧钢机械; 振动监测; 故障诊断1前言轧钢机械属于大型的旋转机械,是轧钢厂的关键设备。
转轴组件是轧机的核心部分,它包括旋转轴、齿轮传动件、联轴器、滑动和滚动轴承等。
人们通过长期观察和实践,发现旋转机械的绝大多数前期故障都会表现出异常的振动,因此掌握机械振动的一般规律就能从振动信号中识别出常见的设备故障。
通过对振动信号波形进行简单的时域、频域以及小波分析可对振动进行一般的识别,振动的可识别性是对机械故障进行振动噪声测试分析的技术前提。
因此,采用在设备诊断技术领域较成熟的振动分析技术作为技术的突破口对轧钢机进行日常振动状态监测,就能在设备运行中或基本不拆卸全部设备的情况下,掌握轧机运行状态,判定产生故障的部位和原因,并预测未来的技术状态,从而可在早期有效地发现,以及在后期及时地抑制故障,保障生产的可持续发展。
2信号识别与获取任何机器设备在运行中都会产生振动,机器的振动信号中包含了丰富的机器运行的状态信息。
当设备发生异常或故障时,振动将会发生变化,一般表现为振幅加大。
由不同类型、性质、原因和部位产生的故障所激发的振动具有不同的特征,这些特征表现为频率成分、幅值大小、相位差别、波形形状和能量分布状况等。
振动信号的性质和特征不仅与故障有关,还与系统的固有特性有关,具体表现为同一故障发生的部位不同、故障激励传递通道(即传递函数)不同,其振动特征和响应亦会有较大的差别。
总之,设备的振动是由故障激励和系统特性所共同决定的,但很多情况下,振动特征和故障类型之间并不是一一对应的关系,不能简单地对号入座,这就给振动的识别带来一定的困难。
张力控制在高线生产中的应用与探讨
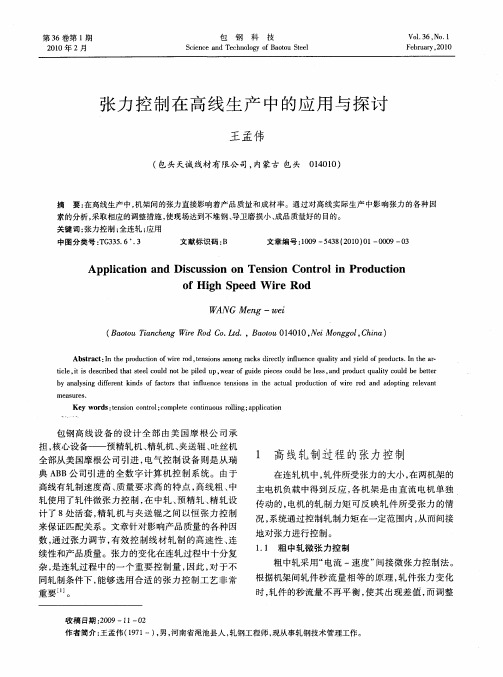
粗 中轧 采用 “ 电流 一速 度 ” 间接微 张力 控 制法 。 根据 机架 间轧件 秒 流 量 相 等 的原 理 , 件 张 力 变化 轧
同轧 制条 件下 , 够 选用 合 适 的张 力 控 制工 艺 非 常 能
第3 6卷第 1期
21 0 0年 2月
包
钢
科
技
Vo . 6, 1 3 No. 1 F br r 2 0 e uay, 01
S in e a d Te h oo y o a tu S e l c e c n c n l g fB o o t e
张力 控 制在 高线 生 产 中 的应 用 与 探 讨
王 孟伟
( 包头 天诚 线材有 限公 司 , 内蒙古 包头 04 1 ) 100
摘
要: 在高线生产 中 , 机架问的张力直接影响着产 品质量 和成材率 。通过对 高线实 际生产 中影 响张力 的各种 因
素 的分析 , 采取相应 的调整措施 , 现场达到不堆钢 、 使 导卫 磨损小 、 品质量好 的 目的。 成
WANG e g —we M n - i
( a t inhn i o o Ld , a t 1 0 0 N i n g lC i ) B oo Ta ceg W r R dC . t. B o u0 4 1 , e Mog o, hn u e o a
Ab t a t I h r d cin o r o t n i n mo gr c sd rcl n u n e q ai n il f r d cs I h r sr c :n t e p o u t f e rd,e so sa n k i t i f e c u lt a d ye d o o u t . n t ea - o wi a e y l y p t l i i d s r e h tse lc ud n t e pl d u w a fg i e p e e o l e ls , n rd c u i o l eb t r i e, s e ci d ta t e o l o i p, e ro u d i c s c u d b e s a d p o u tq a t c u d b et c t b b e l y e b n lsn i e e t kn s o a t r t a n u n e t n i n n t e a t a p o u t n o r o n d p i g r lv n y a ay i g d f r n i d f fco s h ti f e c e so s i h cu r d ci fwi r d a d a o t ee a t f l l o e n
微张力自动控制在棒材连轧中的应用
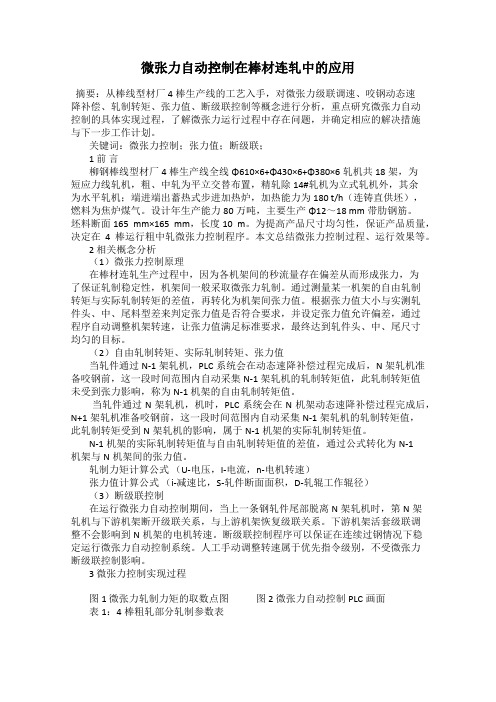
微张力自动控制在棒材连轧中的应用摘要:从棒线型材厂4棒生产线的工艺入手,对微张力级联调速、咬钢动态速降补偿、轧制转矩、张力值、断级联控制等概念进行分析,重点研究微张力自动控制的具体实现过程,了解微张力运行过程中存在问题,并确定相应的解决措施与下一步工作计划。
关键词:微张力控制;张力值;断级联;1 前言柳钢棒线型材厂4棒生产线全线Φ610×6+Φ430×6+Φ380×6轧机共18架,为短应力线轧机,粗、中轧为平立交替布置,精轧除14#轧机为立式轧机外,其余为水平轧机;端进端出蓄热式步进加热炉,加热能力为180 t/h(连铸直供坯),燃料为焦炉煤气。
设计年生产能力80万吨,主要生产Φ12~18 mm带肋钢筋。
坯料断面165 mm×165 mm,长度10 m。
为提高产品尺寸均匀性,保证产品质量,决定在4棒运行粗中轧微张力控制程序。
本文总结微张力控制过程、运行效果等。
2 相关概念分析(1)微张力控制原理在棒材连轧生产过程中,因为各机架间的秒流量存在偏差从而形成张力,为了保证轧制稳定性,机架间一般采取微张力轧制。
通过测量某一机架的自由轧制转矩与实际轧制转矩的差值,再转化为机架间张力值。
根据张力值大小与实测轧件头、中、尾料型差来判定张力值是否符合要求,并设定张力值允许偏差,通过程序自动调整机架转速,让张力值满足标准要求,最终达到轧件头、中、尾尺寸均匀的目标。
(2)自由轧制转矩、实际轧制转矩、张力值当轧件通过N-1架轧机,PLC系统会在动态速降补偿过程完成后,N架轧机准备咬钢前,这一段时间范围内自动采集N-1架轧机的轧制转矩值,此轧制转矩值未受到张力影响,称为N-1机架的自由轧制转矩值。
当轧件通过N架轧机,机时,PLC系统会在N机架动态速降补偿过程完成后,N+1架轧机准备咬钢前,这一段时间范围内自动采集N-1架轧机的轧制转矩值,此轧制转矩受到N架轧机的影响,属于N-1机架的实际轧制转矩值。
译文
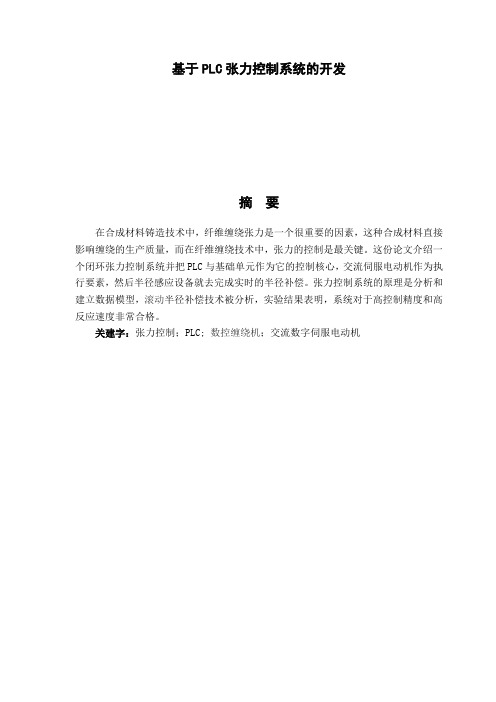
表格1张力的静态差异率的分析
状态
设置 张力/N
Tmax/N
Tmin/N
△T/N
Tm/N
δ/%
恒定的张力
10
10.253
9.894
0.359
10.109
3.55
变化的 张力
5
5.126
4.964
0.162
5.077
3.19
10
10.261
9.952
0.309
Байду номын сангаас10.111
[4]LossieM,BrusselH V.用单纤维缠绕的设计原理.复合材料制造1994; 5(1): 5-13.
[5]illerG A.纺织品单纤维缠绕中的张力控制,Mecha-tronics1995; 5(2): 117-131.
[6]DudzinskiM.了解中心驱动网络缠绕—第一部分。动力传送设计1995; 37(4): 27-31.
基于PLC张力控制系统的开发
摘要
在合成材料铸造技术中,纤维缠绕张力是一个很重要的因素,这种合成材料直接影响缠绕的生产质量,而在纤维缠绕技术中,张力的控制是最关键。这份论文介绍一个闭环张力控制系统并把PLC与基础单元作为它的控制核心,交流伺服电动机作为执行要素,然后半径感应设备就去完成实时的半径补偿。张力控制系统的原理是分析和建立数据模型,滚动半径补偿技术被分析,实验结果表明,系统对于高控制精度和高反应速度非常合格。
参考
[1]楞X W.纤维缠绕理论.山东:山东科学技术出版社, 1990. [中文]
[2]王Q S.基于PLC的精确张力控制系统的基础和实验研究.博士论文,预测:高科技的建立预测, 2005. [中文]
连轧作业区的微张力控制轧制的应用实践
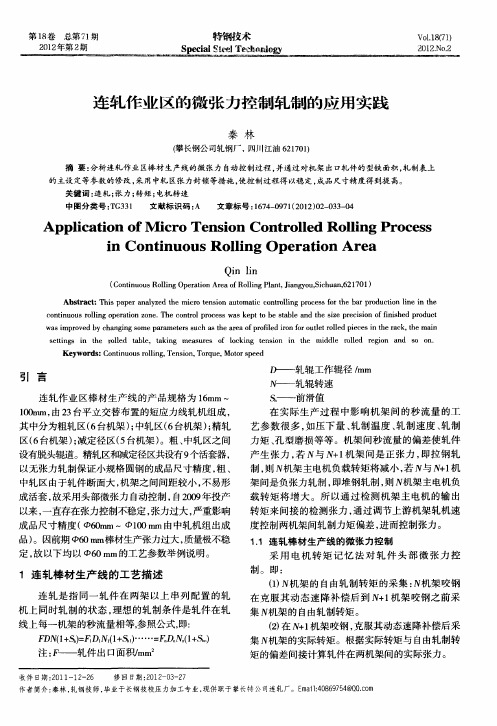
特钢技术
S e il a | c r o y p c a j S Te  ̄ d g
Vo.87 ) 1 (1 1
2 1 . . 0 2No 2
连 轧作 业 区 的微 张 力控 制 轧 制 的 应 用实 践
秦 林
( 攀长钢公 司轧钢厂 ,四川江油 6 10 ) 271
品 ) 因前期 6 m棒 材生产张力过 大 , 。 0m 质量 极不稳
载 转 矩 将 增 大 。所 以通 过 检 测 机 架 主 电机 的 输 出
转矩来 间接的检测张力 , 通过调节上游机架轧机速
度控 制两 机架 间轧制 力矩 偏差 , 而控制 张力 。 进
11 连 轧棒 材生产 线 的微张 力控 制 .
中 图分 类 号 : G 3 T 31
文献标识码 : A
文 章标 号 :6 4 0 7 ( 0 20 — 3 — 4 17 — 9 12 1 )2 0 3 0
A pp i a i n fM i r n i n Co r le R o lng Pr c s lc to 0 c o Te s o nt o l d l i o es
引 言
连 轧 作 业 区棒 材 生 产线 的产 品规 格 为 1 m 6 m~
D 一
轧辊 工作 辊径 / m m
N 一 轧辊 转 速 _ - S—— 前滑 值 在 实 际 生 产 过 程 中影 响 机 架 间 的秒 流 量 的工
10 m, 2 台平立 交替 布置 的短应 力线 轧机 组成 , 0m 由 3 其 中分 为粗轧 区 ( 台机架 )中轧 区 ( 6 ; 6台机架 )精 轧 ; 区( 6台机架 )减 定径 区 ( 台机架 ) ; 5 。粗 、 中轧 区之 间 设有脱头辊 道。精轧 区和减定径区共 设有 9 个活套器 ,
连续热镀锌钢板生产线张力调节系统和实现方法
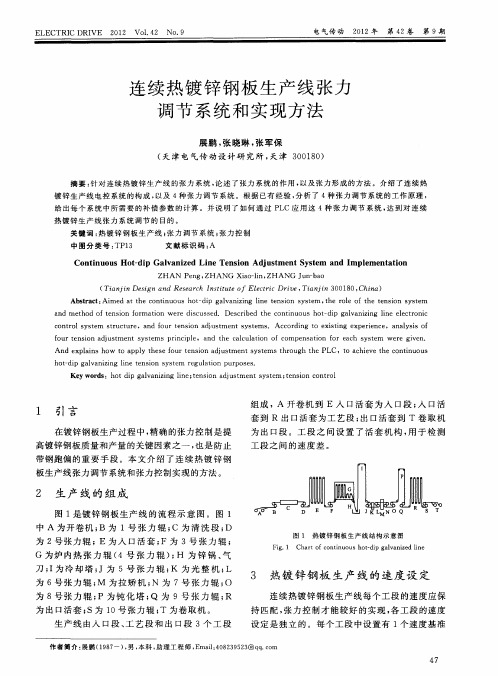
C n i u u t i la ie n e so j sme tS se a dI lme tt n o t o sHo— p Gav nz d LieT n in Ad u t n y tm n mpe n ai n d o
图 1 热 镀锌 钢 板 生产 线 结 构 示 意 图
Fi . Ch r fc n i u u o — i a v n z d l e g1 a to o tn o s h td p g l a ie i n
刀 ; 为冷 却 塔 ; I J为 5号 张 力 辊 ; 为 光 整 机 ; K L
1 引 言
在 镀锌钢板 生产过程 中 , 确 的张力控制 是提 精
组 成 , 开卷 机 到 E入 口活 套 为入 口段 ; 口活 A 入
套 到 R 出 口活 套为 工艺 段 ; 口活 套到 T 卷取 机 出 为 出 口段 。工 段 之 间设 置 了活 套 机 构 , 于检 测 用 工 段之 间 的速度 差 。
摘 要 : 对连续热镀锌生产线 的张力系统 , 述了张力系统的作用 , 针 论 以及 张 力形 成 的 方 法 。介 绍 了 连 续 热
镀 锌 生 产线 电 控 系 统 的 构 成 , 以及 4种 张 力 调 节 系 统 。根 据 已有 经 验 , 析 了 4种 张 力 调 节 系 统 的 工 作 原 理 , 分
An x li sh w o a p yt eef u e so du t n y tmst r u h tePL d e pan o t p l h s o rtn in a j sme ts se h o g h C,t c iv h o tn o s oa he et ec niu u
棒线材连轧中的张力控制

棒 线 材 连 轧 中 的 张 力控 制
李
( 1 . 河钢集 团钢研总 院, 河北
杰 , 刘 毅 , 张艳春 z
石家庄 0 5 0 0 2 3 ; 2 . 河北钢建集团 , 河北 唐山 0 6 3 0 0 0 )
摘
要: 对棒 线材 生产 中的连轧 张力进行 了系统分析 , 提 出张力控 制对生产过程的稳定性和最终产品 的尺 寸精
一
张力轧制的直接结果就是造成产品尺寸在长度
方 向上不 均匀 , 即头尾 孔 型过充 满 , 尤其 是 尾部 尺 寸 变大 尤 为突 出。 张力对 产 品尺 寸波 动 的影 响 实质上
收 稿 日期 : 2 0 1 7 — 0 7 — 1 0
定范 围 内张力 对成 品尺寸 的影 响 ,从 而 实现 高精
由于棒线材轧制都是横 向和竖向两个方 向交替
压 缩变 形 ,适 当的 张力对 成 品尺寸 的影 响 可 以在下 游 的无 张力 轧制 状态 中消除 ( 棒 材轧 机 ) 或 者在 高线 精 轧机 组轧 制后 控制 在最 后 的尾部 3 ~ 1 O m( 1 ~ 3圈 ) 之 内 ,带有 减定 径机 组 的棒 线材 轧 机则 基本 消 除 了
制 过程 顺利 进行 。
我国 目 前装备 的棒线材轧机绝大多数为全连续 轧制 。棒材轧机的典型装备为粗轧机组、 中轧机组 ,
均布 置 为六机 架平 立交 替 ;精 轧机 组 布置 六 架可 翻 转 的平立 交替 轧机 , 多数 为 高刚度 轧 机 。 一般 中轧 机 组 和精 轧机组 配有 5 - 6个 活套 。高速 线材 轧 机 的典 型装 备 为 国产 摩根 五代 机 型 ,引进 生 产线 带 有减 定
连轧 过程 中的张力 精确 控制 是必 要条 件 r 。 1 棒 线 生产连 轧概 述
KELK 张力计在1450mm 冷轧机生产中的应用
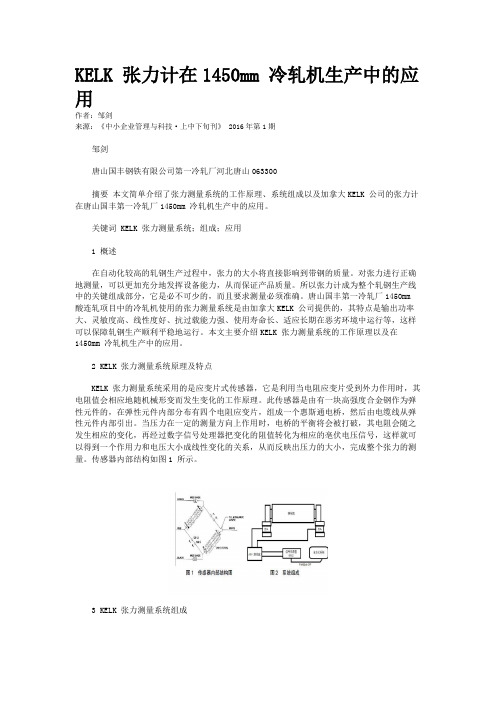
KELK 张力计在1450mm 冷轧机生产中的应用作者:邹剑来源:《中小企业管理与科技·上中下旬刊》 2016年第1期邹剑唐山国丰钢铁有限公司第一冷轧厂河北唐山063300摘要本文简单介绍了张力测量系统的工作原理、系统组成以及加拿大KELK 公司的张力计在唐山国丰第一冷轧厂1450mm 冷轧机生产中的应用。
关键词 KELK 张力测量系统;组成;应用1 概述在自动化较高的轧钢生产过程中,张力的大小将直接影响到带钢的质量。
对张力进行正确地测量,可以更加充分地发挥设备能力,从而保证产品质量。
所以张力计成为整个轧钢生产线中的关键组成部分,它是必不可少的,而且要求测量必须准确。
唐山国丰第一冷轧厂1450mm 酸连轧项目中的冷轧机使用的张力测量系统是由加拿大KELK 公司提供的,其特点是输出功率大、灵敏度高、线性度好、抗过载能力强、使用寿命长、适应长期在恶劣环境中运行等,这样可以保障轧钢生产顺利平稳地运行。
本文主要介绍KELK 张力测量系统的工作原理以及在1450mm 冷轧机生产中的应用。
2 KELK 张力测量系统原理及特点KELK 张力测量系统采用的是应变片式传感器,它是利用当电阻应变片受到外力作用时,其电阻值会相应地随机械形变而发生变化的工作原理。
此传感器是由有一块高强度合金钢作为弹性元件的,在弹性元件内部分布有四个电阻应变片,组成一个惠斯通电桥,然后由电缆线从弹性元件内部引出。
当压力在一定的测量方向上作用时,电桥的平衡将会被打破,其电阻会随之发生相应的变化,再经过数字信号处理器把变化的阻值转化为相应的亳伏电压信号,这样就可以得到一个作用力和电压大小成线性变化的关系,从而反映出压力的大小,完成整个张力的测量。
传感器内部结构如图1 所示。
3 KELK 张力测量系统组成KELK 张力测量系统主要包括以下3 个部分:淤两只张力传感器(简称“压头”),传感器分别安装在轧机的传动侧和操作侧,主要用于测量轧机两侧的张力;于一个现场信号接线箱(含两组接线端子排),信号接线箱主要用于张力传感器与信号处理器信号的连接;盂一套数字信号处理器GPA2,信号处理器GPA2 主要用于处理计算现场传感器传输过来的信号,并且将计算出来的模拟量以及数字量传输给PLC。
张力对冷轧板带变形的干预作用

张力对冷轧板带变形的干预作用摘要:在轧制生产的过程当中会对板带施加张力,这是保证轧制过程当中能够顺利进行的主要方式。
在70年代末,意大利的一位相关学家提出了张力改变后,能够改变冷轧板的形状,这个理念一经提出,就得到了许多的实验,在实验的过程当中发现张力的改变,确实能对冷轧板的厚薄程度造成影响。
本次研究基于这一理论,探讨张力对冷轧板带造成的影响。
关键词:张力;冷轧板带;变形复杂的板带材通常无法用简单的板凸度来进行表述,比如1/4边浪,中浪,和边浪以及复合浪等都是无法用简单的板凸度来进行阐述的。
而影响板带的形状的因素也较多,通常来说有轧辊辊形、工艺以及板带材构成。
在冷轧板制作的过程当中,如果张力不均匀,就会导致冷轧板出现边缘断裂。
一旦出现边缘断裂,很容易造成危险事故,这类危险事故会对工作人员的生命安全造成威胁,因此为了防止冷轧板带的边缘断裂,就必须要增加冷轧板带的制作工程,使得张力均匀施加。
一、张力张力是指物体在受到一定的拉力作用时,存在于物体内部但是垂直于物体与张力面接触两点的一种相互牵引的力量。
比如被拉伸的绳段,绳段内部就有张力,绳段内部和绳段的两端形成了相互作用力。
张力也存在于弦的内部,如果把弦考虑成两个部分,那么张力就会对这两个部分产生一种相互拉扯的力量。
在弦被拉扯的过程当中,如果张力过大,就会导致弦的断裂,如果张力小且能够控制,就会产生弦的震颤。
通过张力的大小,就能够调整弦发出的声响和发出声响的频率,因此许多演奏者在进行演奏时,通常是靠张力来调整弦的音高的。
通常来说,如果将弦紧绷那么张力也会随之增加,拉的长度较小时,需要采用胡克定律来描述这个张力是否大或者小。
张力的含义具有以下几点。
1.张力是一对互相平衡的力量,能够引起物体的身长,在物体的身长过程当中,维持物体的平衡。
2.在一些富含弹性的物体被拉伸时产生的力叫做张力。
3.在哲学当中张力的含义指的是矛盾和不相融合的意思。
4.小提琴弦在波动时产生的力量[1]。
连轧时的张力设定计算和张力的自动控制
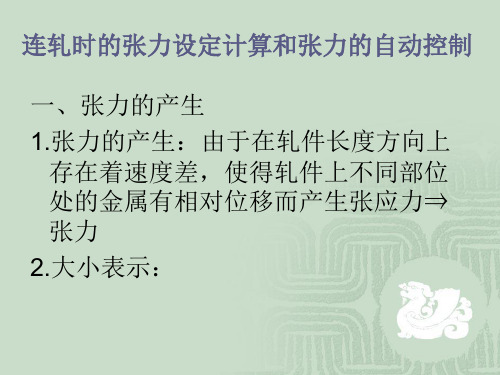
(2)确定活套量与摆角之间的关系 ⇒自动控制的数学模型 公式展开后、处理后得:
即:
∴ 连轧时的活套量Δl,即 F(θ) ,它是 与活套辊的摆角θ的平方成正比。也 即:θ角的变化反映出活套量的变 化, 这形成了一个重要的概念,连轧 时张力计算机控制就是对活套高度的 控制, 其实质是控制活套辊的摆角θ。
(2)双机连轧张力的检测 ①检测手段: 直接检测:张力计测得,受温度制约 间接检测:通过检测轧制压力和电动 机力矩的方法来确定张力值的大小 ② 检测过程分析:电机力矩MD=MC+Md 按各项展开后得:
对于R3轧机,TH=0, 则: Th= 因此,只要检测出右边各项的值,便可 以计算出机架间轧件的张力值。
(2)动态速降: = (2%~3%)nmax 或 (3)活套量的形成 :因动态速降造成 vH(i+1) <vhi,而动态速降的恢复时间约 为 03s~0.5s,因而在 i 和 i 十 1 机架 之间便形成了一定的活套量Δld, Δld值 较小,一般为30~50mm ⇒ 微套量小 张力连轧是当代宽带钢热连轧的一个 重要特点。
(2)控制系统的调节 ∵ ,而 Ia较小,U或E的微小 变化都会引起 Ia的很大变化。 ∴ 通过U来调节,很灵敏,并且反应 快 ⇒ 电枢电流控制部分是主要的, 而磁场控制部分仅在卷径D变化时 才起作用,变化较慢。
(3)系统控制原理
Ia的调节控制
磁场控制
(4)优缺点 I∝T和Φ∝D ,控制直观。 由于Φ∝D ,故只要不在最大卷径情 况下,不论是高速还是低速,电动机 都处于弱磁工作状态,所以电动机转 矩得不到充分利用。
(2)双机连轧时: R3机架的轧制力矩: 张力所产生的力矩: ∴只要检测出双机连轧时R3的电枢电流 值及轧制压力,其余参数为已知⇒ T 例题:P276
冷轧生产线中张力检测信号的处理策略研究

冷轧生产线中张力检测信号的处理策略研究摘要:文章首先从操作原理与公式表达两个角度出发,对冷轧生产线中张力检测信号处理的技术原理进行了探讨。
其后,以湛江三高炉系统冷轧工程连退机组三电系统为案例分析对象,阐述了冷轧生产线中张力检测信号处理的应用背景,并由此提出了相关处理条件与处理要点。
最后,结合滤波处理、角度补偿处理、平滑处理、风险处理四个部分,研究了冷轧生产线中张力检测信号处理的主要技术方法。
关键词:冷轧生产线;带钢张力;张力检测信号;信号处理技术引言:在冷轧生产过程中,带钢张力控制是极为关键的技术环节。
若带钢张力控制的效果不佳,不仅会对产品的生产质量造成负面影响,还会引发设备、经济、安全等多方面的生产风险。
进一步来看,带钢张力的直接控制是以张力检测信号作为主要依据的。
所以,为了保证冷轧生产线的安全稳定运行,有必要对张力检测信号的处理策略展开研究分析。
1 冷轧生产线中张力检测信号处理的技术原理在冷轧生产线中,对生产系统张力信息的检测采集主要是依靠张力仪实现的。
通常情况下,张力仪主要由压头和信号处理单元两部分组成。
其中,压头数量多为2个,用于通过物理作用感知带钢张力,并生成相应的压力信号。
在冷轧生产系统中,压头的安装位置通常在张紧辊的轴承座与机械框架之间。
信号处理单元主要由控制模块、接线端子箱以及隔离放大器三个部分组成。
当压头受力后,其生成的压力信号便会自动传输给信号处理单元,并经过过滤、放大、转换等处理后,输出为用于表示冷轧生产中带钢张力的数字信息。
其后,数字处理系统再将动态获取的张力信息发送给自动化生产控制系统,便可实现钢带张力的精准控制与风险监测。
最后,钢带张力在系统控制下完成调整后,张力仪仍会将新的张力信息反馈给自动化生产控制系统。
由此,便会形成持续性的控制闭环,从而为冷轧生产线的良性运转提供保障[1]。
在张力检测信号处理技术的公式表达方面,主要按照压头所受作用力类型的差异分为两种:若压头所受作用力为水平向,则公式为;若压头所受作用力为垂直向,则公式为。
- 1、下载文档前请自行甄别文档内容的完整性,平台不提供额外的编辑、内容补充、找答案等附加服务。
- 2、"仅部分预览"的文档,不可在线预览部分如存在完整性等问题,可反馈申请退款(可完整预览的文档不适用该条件!)。
- 3、如文档侵犯您的权益,请联系客服反馈,我们会尽快为您处理(人工客服工作时间:9:00-18:30)。
附录AIntegrating Tension Leveling Systems into ContinuousProcessing LinesThe demand for higher quality has required all participants in the manufactureing sequence to improve their product. Flat rolled metal finishers have looked to shape improvement., via tension leveling ,as a means to achieve this goal. The issues of equipment location and integration , leveler and bridle configurations, drive system options and drive controls are considerations that must be addressed.The incorporation of tension leveling into a continuous processing line requires a decision as to its primary purpose. The priority of the criteria, ie, improved shape, improved processing or both , determines its location in the line.If final shape is the only criterion, the leveling equipment should be located in either the process or delivery section is undesirable. However, this location does have the advantages of minimal chance of material damage before recoiling and it is unnecessary to increase accumulator and exit bridle roll diameters. Both locations have the advantage of processing clean material but there is the disadvantage of possible pick up (in the case of coating lines) on the bridle and leveler rolls.In the case of process lines with planting or coating units, it is necessary to insure that the finish will not be affected by the elongation produced by the leveling process.For improved processing, the tension leveler is located in either the entry section or the beginning of the process section before or after cleaning. The entry section location has the advantage of allowing a leveler roll change during a coil change but there is the disadvantage of tension transient from stopping and jogging. The process section after the cleaning unit location has the advantage eliminating dirt contamination on the bridle and leveler rolls. In addition, it may reduce the number of bridle rolls and eliminate the need for a collection system for the oil squeezed fromthe strip by the leveler rolls.Almost all of the systems installed in tinning, pickling and electrogalvanizing lines have been located in the beginning of the process section. Hot dip galvanizing lines have units after coating with an equal number in the process or delivery section. In annealing lines, the units have been located in the delivery section, while paint lines have them in the entry section.ConfigurationOnce the location is determined, the system can be configured. The configuration include:Leveler configuration(manufacturer).Leveler work roll diameter(manufacturer).Leveler module configuration(manufacturer).Bridle roll size(manufacturer or user).Bridle roll covering(manufacturer or user).Driver configuration(manufacturer or user).Driver integration(manufacturer).The leveler configuration and module design vary with the type of material and location of the leveler in the process line. Essentially, the leveler consists of four or more work roll modules and a curvature correction (crossbow) module .The size and number of work rolls is a function of material thickness range, yield strengths, line speed, elongation and tension constraints. Work roll diameter is determined by the highest yield strength at the minimum thickness (maximum diameter) and the maximum thickness (minimum diameter) for type of materials to be processed.Leveler modulesWork roll diameters are small; therefore, support structures are required to provide rigidity. For ease of maintenance, work rolls and their backup systems are configured into removable modules. The modules are configured to provide the work roll rigiditywithout restricting the angle of wrap. The most common module configurations are:1. Work roll supported by two large diameter full-faced backup rolls.2. Work roll supported by small diameter segmented backup rolls.3.Work roll supported by two medium diameter full-faced backup rollssupported by three rows of segmented backup rolls.4. Work roll supported by two medium to relatively large diameter full-facedbackup rolls, each supported by two narrow-faced rolls.Modules employing segmented or narrow-faced backup rolls do not use automatic lubrication system because of the possibility of contaminating the strip. this type of module requires planned maintemance base on footage processed due to the lied amount of pre-lubrication.Measures taken to extend module life are a function of the type of line and location of the leveler in the line the leveler’s work rolls may be chrome plated to prevent pickup and/or rusting. The backup rolls may be grooved to remove contaminants and coated to extend life and/or prevent rust.Resultvia tension leveling is an important facility in the producing line of steel’s hot-rolling. The via tension leveling should provide qualified billets gratifying the request of the rolling process. A great deal of research work has been done to reduce the energy consumption of the via tension leveling. Some useful achievements were presented in the literature, including the optimal setting method and combustion control for the reheating furnace. However, up to now the reheating process and the rolling process have been controlled separately, which can not bring along the optimizing of the total energy consumption of the hot-rolling process, the facility usage and the production quality, although the optimizing of the energy consumption of the reheating furnace were considered by several control methods. In order to reduce the total energy consumption of the reheating process and the rolling process, and to decreaseproducing accidents at the same time, this paper presents a new object-oriented integrated optimal control strategy of the hot-rolling process based on the modeling of reheating process with rolling process cooperatively, which provides a better solution to the above-mentioned problem. The billet temperature is an important parameter that connects the reheating process and the rolling process, and this paper establishes a mathematical model of the variety of the billet temperature using mechanism analysis and discrete state space method. The mathematical model establishes the stable foundation for the integrated optimal control of the reheating process and reheating process. The issues of reheating furnace temperature optimal setting and combustion control method design are important to achieve the integrated optimal control of the reheating process and the rolling process. This paper analyzes deeply the question of how to determine and optimize the objective function in the tension leveling setting, and improves the existing method to make the via tension leveling setting accord with the aim of producing process better. Also, this paper presents a new combustion control method by means of the optimizing of air-fuel ratio, which is realized by combining the feedforward of fuel analysis with feedback of surviving oxygen analysis. In order to solve the question of furnace temperature optimizing on line, this paper presents an integrated optimal control strategy of the hot-rolling process based on the abstraction of fuzzy rule and neural network. This strategy can feed the production information of the rolling process back to the reheating process in time, and can give the presetting value of the furnace temperature corresponding dynamic compensation. In order to apply the integrated optimal control method for the hot-rolling process, this paper establishes a via tension leveling -feedback-oriented and rolling-load-feedback-oriented integrated optimal control model respectively and simulation results are given to demonstrate the effectiveness of the scheme.附录B集成张力水平系统在连续轧制线的应用关于较高的质量的要求已在制造的序列中要求所有参与者改进他们的产品。