热轧案例2—顶精轧机后机架辊的分析
热轧工作辊弯辊及横移装置的结构分析及优化
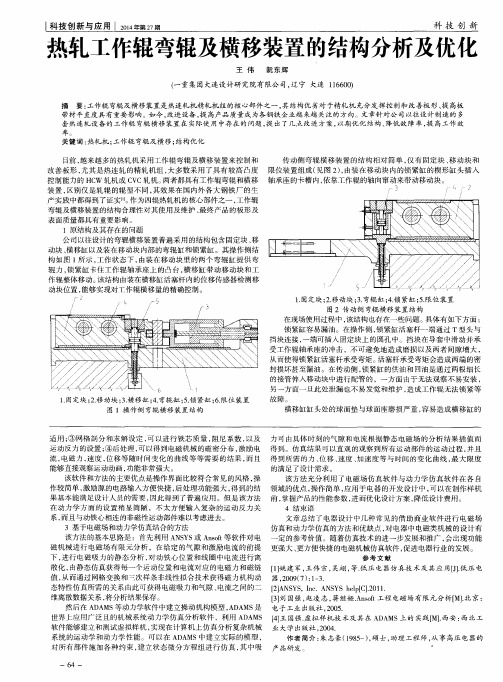
横 移 缸缸 头 处 的球 面垫 与球 面 座磨 损 严 重 , 容 易 造成 横 移 缸 的
适用 ; ③ 网格 剖 分 和 求 解 设 定 , 可 以进 行 铁 芯 质 量 , 阻尼系数 , 以及 力 可 由具体 时刻 的气 隙 和 电 流 根 据静 态 电磁 场 的分 析 结 果 插 值 而 运动 反 力 的设 置 ; ④ 后 处理 , 可 以得 到 电磁 机械 的磁 密分 布 , 激励 电 得 到 。仿 真结 果 可 以直 观 的观察 到所 有 运 动部 件 的运 动过 程 , 并 且 流, 电磁 力 , 速度 , 位 移 等 随 时 间 变 化 的 曲线 等 等 需 要 的结 果 , 而且 得 到 所 需 的 力 、 位移 、 速度 、 加速度等与时间的变化曲线 , 最 大 限度 能够 直 接观 察 运动 动 画 , 功能 非常 强大 。 的满 足 了设 计需 求 。 该软件 和 方 法 的 主要 优点 是 操作 界 面 比较 符 合 常见 的风 格 , 操 该 方法 充 分 利 用 了电 磁 场仿 真 软 件 与 动 力 学 仿 真 软 件 在 各 自 作较 简 单 , 激 励 源 的 电路输 入 方便 快 捷 , 后 处 理功 能 强 大 , 得 到 的结 领 域 的优 点 , 操 作简 单 , 应 用 于 电 器 的开 发 设计 中 , 可 以在 制 作 样机 果 基 本能 满 足设 计 人 员 的需 要 , 因 此得 到 了 普遍 应 用 。但 是 该 方 法 前 , 掌握 产 品 的性 能参 数 , 进 而优 化 设计 方 案 , 降 低设 计 费 用 。 在 动 力 学 方 面 的设 置稍 显 简 陋 ,不 太 方便 输 入 复 杂 的运 动 反 力 关 4 结束 语 系, 而 且 与动 铁心 相 连 的非磁 性 运动 部件 难 以考 虑 进去 。 文章总结了电器设计 中几种常见的借助商业软件进行电磁场 3基 于 电磁 场 和动力 学仿 真 结 合 的方法 仿 真和 动 力学 仿 真 的方 法 和优 缺 点 , 对 电器 中 电磁 类 机 械 的设 计 有 该方 法 的 基本 思 路是 :首 先 利 用 A N S Y S 或A n s o i等 软件 对 电 f 定 的参 考价 值 。随着 仿 真技 术 的进 一步 发 展 和 推广 , 会 出现 功 能 磁 机 械 进 行 电磁 场 有 限 元分 析 ,在 给 定 的 气 隙 和激 励 电流 的前 提 更 强大 、 更 方便 快 捷 的 电磁 机 械仿 真 软件 , 促 进 电 器行 业 的发 展 。 下, 进 行 电 磁 吸力 的静 态 分 析 , 对 动铁 心 位 置 和 线 圈 中 电 流进 行 离 参 考 文献 散化 , 由静 态 仿 真获 得 每一 个 运 动位 置 和 电流 对 应 的 电磁 力 和 磁链 [ 1 ] 姚建军, 王伟宗 , 吴翊 , 等. 低 压 电 器仿 真 技 术 及 其 应 用 低 压 电 值, 从 而通 过 网格 变 换 和 次 样 条非 线 性拟 合 技 术 获得 磁 力 机 构动 器 . 2 0 0 9 ( 7 ) : 1 - 3 . 态 特性 仿 真所 需 的关 系 由此 可 获得 电磁 吸力 和气 隙 、 电流 之 间 的 二 [ 2 ] A N S Y S ,I n c . A N S Y S h e l p [ C ] . 2 0 1 1 . 维 离散 数 据关 系 , 将分 析结 果 保存 。 [ 3 1 刘 国强 , 赵凌志 , 蒋 继娅 . A n s o i工程 电磁 场 有 限 元 分析 [ f M ] . 北京: 然后在 A D A M S等动 力 学软 件 中建 立 操动 机 构模 型 , A D A M S是 电 子 工 业 出版 社 , 2 0 0 5 . 世 界 上应 用 广 泛且 的机 械 系统 动 力 学仿 真 分 析 软件 ,利用 A D A MS f 4 ] 王 国强 . 虚拟 样 机 技 术 及 其 在 A D A M S上 的 实践 [ M ] . 西安 : 西 北 工 软 件 能够 建 立 和测 试 虚拟 样 机 , 实 现 在计 算 机 上仿 真 分 析 复杂 机 械 业 大 学 出版 社 , 2 0 0 4 . 系统 的运 动学 和动 力 学 性 能 。可 以在 A D A MS中建 立 实 际 的 模 型 , 作者简介 : 朱志豪( 1 9 8 5 一 ) , 硕士 , 助理工程 师, 从事高压 电器的
二辊轧机机架辊损坏原因分析及改造

wo k n o d t n n t u t r h r c e it s h e d r l I r u h t e r ' p r to n eo ma in,t e fc o l r ig c n ii s a d sr c u e c a a t rsi t e f e o 1 ' o g wo y a s o e a in a d r f r t o c of . h o h e d r l
维普资讯
0 2 1 J. S an g i. Unv. 01 7 h xi rc A i
山 西 蓑 崇 大 哮 学报
文章 编 号 :1 7 - 1 l ( 0 6 0 — 3) 0 6 18 5 2 0 ) 3 0 i - 2 3
二 辊 轧 机机 架辊 损 坏 原 因分析 及 改 造
要 道 。多 年 来 ,二 辊 机 架 辊 虽 几 经 改 造 . 但 由 于工 怍环 埯 恶 图 l 机 架 辊 辊 子 结 构 示 意 图
Fg 1 i.
轴承
Be i ar ng
劣 ,不 仅 频 繁 启 动 、制 动 ,频 繁 正 转 、反 转 , ( 产 过 程 中 . 生
一
j L』 ~ . — ~
,
生 产 工 序 的 第 一 道 , 其 作 用 可 想 知 ,而 二 辊 . 架 r _ 』 L
辊 [ 。位 于 230mm 二 辊 轧 机 前 后 两 彻 紧 靠 轧 辊 芯 怍 0 i 用 仅 次 于 轧 辊 的主 要 轧 制 设 备 ,也 是 该 厂 中厚 板 生 产 的 l喉 l I
葫 , 邸 志 龙。
( .山 西农 业 大 学 ] 程 技 术 学 院 ,t西 太 O 0 0 ;2 1 : h 荇 8 1 .山 四太 钢 不 锈 钢 热 轧 厂 ,山 西 太 原 00 0 ) 3 3 03
棒线材轧制常见堆钢事故及处理措施

棒线材轧制常见堆钢事故及处理措施一、粗中轧区事故原因分析及对策1、轧件咬入后机架间堆钢故障原因:(1)轧制速度、轧辊直径设定不正确;换辊(槽)后张力设定过小。
(2)钢温波动太大。
(3)轧辊突然断裂。
(4)由于电控系统原因引起某架轧机的电机突然升速或降速。
处理措施:(1)准确设定轧制速度、辊径和张力。
(2)保温待轧,通知加热炉看火工。
(3)更换断辊。
(4)检查电气系统。
2、轧件头部在机架咬入时堆钢故障原因:(1)轧件尺寸不符合要求。
(2)轧槽中有异物或打滑。
(3)导卫安装不良、磨损严重或导卫中夹有氧化铁皮等异物。
(4)坯料内部存在分层、夹杂或冶废等缺陷引起的轧件“劈头”。
(5)上、下辊径不同、磨损不均匀或不同步造成的轧件头部弯曲。
(6)头部钢温过低造成的咬入困难或头部开裂。
(7)轧机机架刚性不好,轧制过程中存在跑偏现象。
(8)坯料“脱方”严重。
(9)轧件出粗轧机架后翘头导致不能顺利咬入下架次或头部冲导卫,简单来说就是翘头。
处理措施:(1)对轧机辊缝作适当调整。
(2)检查、清理或打磨轧槽。
(3)检查、清理、调整或更换导卫。
(4)认真检查坯料。
(5)检查传动部件间隙或更换轧辊。
(6)改善出钢条件。
(7)对轧机机架进行加固;检查锁紧缸的工作状态。
(8)杜绝不合格钢坯入炉。
(9)认真检查前一架次进口导卫是否松动,导卫松动使轧件咬入箱型孔后受到进口导卫的压力,使轧件下部受压较大,导致下部延伸变大而造成翘头,最终未能顺利咬入轧机而堆钢。
3、轧件卡在机架内造成堆钢故障原因:(1)由于钢温过低或轧制速度过高而引起电机过载跳闸。
(2)发生设备或安全事故时紧急停车。
处理措施:应根据具体情况分析处理。
二、预精轧区事故原因分析及对策1、机架间堆钢故障原因:(1)辊径、辊缝设定错误。
(2)导卫安装不准确,导卫被堵塞或被冲掉。
(3)粗、中轧张力过大,轧件在预精轧“甩尾”。
(4)轧机或辊箱轴承烧,导致次架次料型变化。
(5)压下装置自锁性能坏,在轧制时因振动,料型产生变化。
热轧厂HT-2513粗轧工作辊断辊原因分析

2 1 年9 00 月
武汉 工 程 职 业 技术 学 院 学 报
J r l W u nEng ne rngI s iut ou na of ha i e i n tt e
VO122N0. . 3
Sp e e 2 1 e t mb r 0 0
热 轧 厂 HT一2 5 3粗轧 工 作辊 断辊 原 因分 析 1
2 现场 断 口分析
该 辊 断裂 形 态 为辊 身 中部 断成 碎块 、 端 断 口 两 呈 现锥 状 , 可见 断 裂 形 态 为扭 断 ( 图 1 。锥 状 断 见 )
口中部 突 出, 在辊 面 的 中部 突 出轴 线 处存 在 一 条 且 明显 的摩 擦 、 温烧灼 痕迹 , 中并 出现 了一条纵 向 高 其
吴 国胜 余 利 兵 陆献 华
(. 1 武钢 研 究院 湖北 武 汉 :3 0 0 2 武钢股份 热 轧总厂 湖 北 武 汉 :3 0 3 4 0 8 ;. 408 )
摘 要 某 热轧厂粗 轧机 R 3机 架上辊位 HT一2 1 5 3工作辊在 正 常上机使 用过程 中突然发 生辊 身 断裂 事故 。 裂形 态为扭转 断裂 , 材质 为 高铬 复合铸 造轧辊 ; 断 其 对该辊 进行 使 用情况调 查、 现场 断 口 分析和取样 检验 分析 , 明造 成 该辊 断 裂 的原 因主要 是 : 外 层厚 度 没 有 达到 国标 规 定 的技 术要 查 其
求, 加之该 辊 外层 材料 化 学成 份和金 相组 织存 在 若干 质量 问题 , 致 外层 材 料 强韧性 不 足 、 而 发 导 从
生断辊 。
关 键 词 粗 轧 工 作 辊 ; 合 轧 辊 ; 复 高铬 钢 ; 裂 ; 效 分 析 断 失
热轧板带钢精轧工作辊失效原因及预防方法

针对于精轧工作锟失效的危险性比较高,为了能够研究出科学合理的解决方式,相关技术人员对以往发生过的失效情况进行总结,并分析出了以下几种造成工作锟失效的主要原因。
一、高铬离心复合铸铁轧辊脱落问题及解决方式高铬离心复合铸铁轧辊是以含铬12%一22%的高铬白口铸铁为辊身外层材质,以高强度的球墨铸铁为芯部和辊颈材质,采用离心复合浇注工艺而生产的高合金复合铸铁轧辊。
轧辊的非正常失效主要包括辊身剥落、辊身断裂、辊身裂纹等。
1.问题产生的原因。
首先从锟身脱落的情况来看,目前在实际的轧机运行过程中,技术人员经常会在对机械设备的检查时,发现精轧工作锟出现表层金属材料脱落的情况。
工作锟的脱落类型也有很多,主要是根据其脱落的位置进行划分,常见的脱落位置是在轧锟的工作层和锟肩结构当中的情况比较严重。
从工作层的脱落情况来分析,出现这方面的原因与操作人员的操作规范性有一定的关系,为了提高生产效率,轧机经常处于长时间、不停歇的运作状态,这就会导致工作锟承受比较高的压力,尤其是针对于使用使用高Cr 复合铸铁轧辊时,一旦在连续运转过程中压力升高,相应的温度就出现异常。
这些都是造成热轧板带钢精轧工作锟在实际投入使用时出现脱落性失效的主要原因。
而针对于锟肩结构的脱落问题来说,也与设备运行的高压力有关,同时也有设计初期技术人员对锟肩的结构设计,安装工艺方面存在不足的问题,就导致其容易出现脱落情况。
2.预防及解决措施。
要想解决热轧板带钢精轧工作锟脱落失效的问题,就必须要规范操作人员的工作行为,明确规范生产加工的各项工作流程及操作注意事项,并重点关注于温度的控制问题。
同时,还应当安排技术人员定期对设备内部运行状态进行检查、维修和保养,基于科学技术的发展进步,在实际检查过程中,企业可以进购专业的智能探伤设备,目前比较常见的就是超声波探伤方式,能够实现在不拆卸设备的情况下,对内部进行精准探伤,从而保证检查工作不会对生产工作效率造成不良影响。
此外,预防工作还需要从精轧工作锟的生产方面入手,从根本上消除运行当中的不良风险,合理提升轧锟的使用寿命,确保各项工作的平稳运行状态。
热轧轧辊失效分析及预防措施

联 系人 : 占福, 3 岁 , 马 男, 7 博士生 , 轧钢工程师, 乌鲁木齐( 3 o 2 新疆八一钢铁股份有限公司 802 )
E-mai maf y t O 11 l z@b g. B.1 : C 3
~
36 按 制 造工 艺 分 为 铸 造 、 造 、 末 冶 金 、 .%; 锻 粉 喷
射成型 、 堆焊热喷涂等 ; 按结构分为整体辊 、 复合辊 、
镶 装辊 等 ;按 功 能分 为 连铸 辊 、热 轧辊 、冷轧 辊 、
S nm r 、 艺辊 、 道 等 e z i辊 工 辊 。
3 轧 辊 的 失 效 形 式
1 前 言
轧辊是使金属产生塑性变形的一种生产工具, 其在 实 际生产使 用 中 , 于一种 复杂 的应力 状态 , 处 如
轧 辊与 轧件 接 触加 热 、 辊水 冷 却 引起 的周期 性 热 轧 应力 、 轧制 负荷 引起 的接触 应力 、 剪切 应力 以及残 余 应力 等川 。如果轧 辊 的材质 、 加工 、 生产 、 操作 等工 艺
3 1 断 裂 .
不合理 , 就会使轧辊失效 , 出现剥落、 断裂、 辊面损伤 等情况, 任何一种失效形式都会直接导致轧辊寿命
缩短 , 至造 成轧 辊报废 , 甚 因此分 析轧辊 的失 效形 式
轧辊在 生产 中往 往会 发生 突然 断辊事 故 ,其 断
裂部位 主要 为工 作辊 的辊 身 、 颈及 轴头部 位 。 辊 断辊 因轧 制 不 同钢种 、 同品种 、 同 的生 产 工艺 条件 , 不 不 其断裂 部位 有所 不 同。 断裂形 式来 看 , 可能是 一 从 有 次性 的脆断 ,也 可能是 由于疲劳 裂纹 而导致 断辊 l 3 _ ,
可从 内因 、 因两 方面来 分 析 ( 图 1 。 外 如 )
铝板带热轧支承辊常见失效案例

多 的应 力 , 引发 裂纹 和潜 在疲 劳剥 落 。
4 . 3 预 防
点, 且 表 皮下 的最 大 瞬时 剪切应 力 显著 增加 。
3 . 3 预 防措 施
( 1 ) 合 理控 制轧 制乳 液浓 度 尽量 避 免 出现 工 作辊 打滑 现象 ;
4 滑 痕
4 . 1 特 征
滑 痕是 工 作 辊 和 支 承辊 间 的 相 对 滑 动 。 由于 多
数工作辊辊身比支承辊辊身长 , 损伤通常扩展到整个
支承 辊 辊 面或 最 后 在 支 承 辊 上 有 所 减 轻 。如 果 工 作 辊严 重 磨 损 成 一 个 凹 坑 , 损 伤 将 会 在 支 承 辊 辊 端 结 束 。两 种情 况下 会 出现 损伤 , 当打滑 产 生 高 温 或 由于 改变 原 始结 构导 致微 结 构损 坏 时就 会 出 现严 重 裂 纹 。 较大 的摩 擦 滑 动 , 称 为打滑 , 先 由摩 擦 热 损 坏 轧 辊 微 结构 , 然 后在 局部 弱化 区域 引发疲 劳失 效 和剥 落 。
( 8 ) 减 少 辊 身 凸度 量 , 以便 减 少 辊 身 中心 处 的最 大 瞬时剪 切应 力 。
足 或轧 辊磨 损 产 生 裂 纹 而 引 起 的剥 落 。多 数 肩 部 剥 落 与工 作辊 磨损 有关 , 小 块 边 部 剥落 则 与 倒 角不 够 有 关 。滑 动机 理 和 可 变 的线 接 触 压 力 都 有 助 于 控 制 支 承 辊表 面碎 片磨 损 。热 轧 机 中 , 来 自工 作 辊 的 氧化 物 碎 片侵 蚀 支 承 辊 材 料 , 导 致 形 成 凹面 中心 。然 后 , 不
轧机机架辊设计
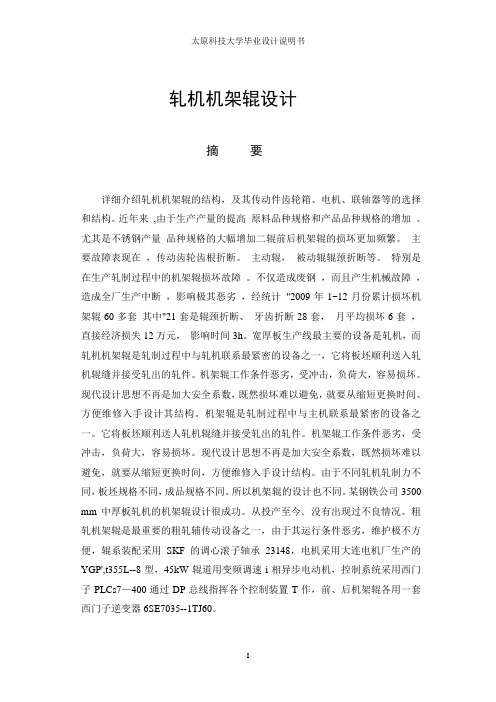
轧机机架辊设计摘要详细介绍轧机机架辊的结构,及其传动件齿轮箱、电机、联轴器等的选择和结构。
近年来,由于生产产量的提高原料品种规格和产品品种规格的增加。
尤其是不锈钢产量品种规格的大幅增加二辊前后机架辊的损坏更加频繁。
主要故障表现在,传动齿轮齿根折断。
主动辊,被动辊辊颈折断等。
特别是在生产轧制过程中的机架辊损坏故障。
不仅造成废钢,而且产生机械故障,造成全厂生产中断,影响极其恶劣,经统计"2009年1~12月份累计损坏机架辊60多套其中"21套是辊颈折断、牙齿折断28套,月平均损坏6套,直接经济损失12万元,影响时间3h。
宽厚板生产线最主要的设备是轧机,而轧机机架辊是轧制过程中与轧机联系最紧密的设备之一,它将板坯顺利送入轧机辊缝并接受轧出的轧件。
机架辊工作条件恶劣,受冲击,负荷大,容易损坏。
现代设计思想不再是加大安全系数,既然损坏难以避免,就要从缩短更换时间、方便维修入手设计其结构。
机架辊是轧制过程中与主机联系最紧密的设备之一。
它将板坯顺利送人轧机辊缝并接受轧出的轧件。
机架辊工作条件恶劣,受冲击,负荷大,容易损坏。
现代设计思想不再是加大安全系数,既然损坏难以避免,就要从缩短更换时间,方便维修入手设计结构。
由于不同轧机轧制力不同,板坯规格不同,成品规格不同。
所以机架辊的设计也不同。
某钢铁公司3500 mm中厚板轧机的机架辊设计很成功。
从投产至今.没有出现过不良情况。
粗轧机架辊是最重要的粗轧辅传动设备之一,由于其运行条件恶劣,维护极不方便,辊系装配采用SKF的调心滚子轴承23148,电机采用大连电机厂生产的YGP',t355L--8型,45kW辊道用变频调速i相异步电动机,控制系统采用西门子PLCs7—400通过DP总线指挥各个控制装置T作,前、后机架辊各用一套西门子逆变器6SE7035--1TJ60。
译文:Detailed presentation roller mill, and its transmission is the gear box, motor, so the choice of axes and structure. in recent years production of raw materials production up by a variety of specifications and specifications of products, especially of stainless steel output specifications for the two rolls and rolls the more frequent failure in the main gears and broken the initiative to roll passive roll off the roll neck, particularly in the production during the roll of the damage caused is not only .Generous board line of the main equipment to be pulled up, and roller mill is during are more closely linked with the device, it will roll smoothly into are the seam and take over the ruts. roller working conditions, shocks and to load the damage. modern design is no longer increase rates. since the damage is difficult to avoid, to change from short time, repair to his design. because of its structure is different from the rolling mill rolling force, during the roll was more closely linked with the host one of the equipment. it will be sent to roller mill smooth seam and take over the ruts. roller working conditions, shocks and to load the damage. modern design is no longer increase security department, since the damage is difficult to avoid, by changing from time to start. the structure of the design is different from the rolling mill rolling force, specifications, with the specifications. it's a roller . A roller mill a most important thing is rough and auxiliary facilities, transmission of the operating conditions are bad and maintain a very inconvenient, roll the assembly to adopt the heart of roller bearings 23148 in dalian, the electrical machinery plant production , t355l --8, 45kw with machinery velocity modulation control motor, and i are an asynchronous system to adopt plc, siemens s7 400 dp bus conductor by various control devices, before and after eliminating roll with a set of siemens become a usurper 6se7035 1tj60 z's, point five关键词:机架辊;集中传动;齿轮箱;交流变频调速电机;联轴器。
中厚板轧机机架辊问题分析及改进建议
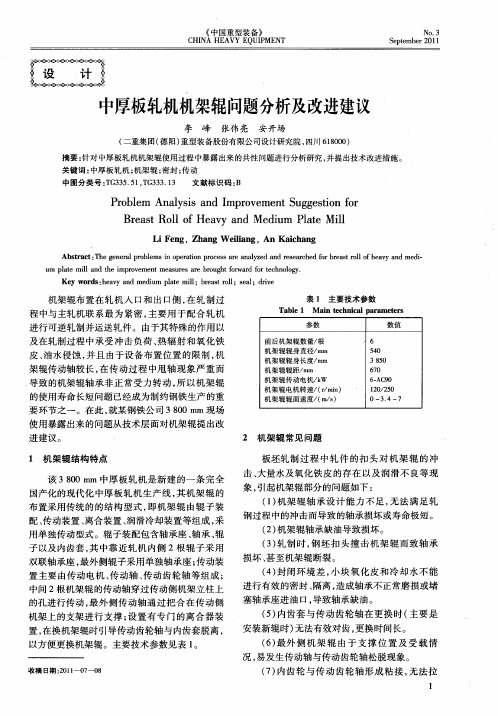
50 4 38 0 5 60 7 6A 9 .CO l0 2 0 2/5 O一 . 7 3 4~
使用 暴露 出来 的 问题从 技术层 面 对机架 辊 提 出改
进建 议 。 1 机 架辊 结构 特点 2 机架 辊 常见 问题
板坯 轧 制 过 程 中轧 件 的 扣 头 对 机 架 辊 的 冲 击、 大量 水及 氧化 铁 皮 的存 在 以及 润 滑 不 良等现 象, 引起 机架辊 部分 的问题如 下 : ( ) 架 辊 轴 承 设 计 能力 不 足 , 法 满 足 轧 1机 无 钢过 程 中的 冲击 而 导致 的轴 承损坏 或 寿命 极 短 。
Ta e 1 M ai t c ni a ar m e e s bl n e h c lp a t r
参数
前 后 机 架 辊 数 量/ 根 ・ 6
数值
皮、 油水侵蚀 , 并且 由于设备布置位置 的限制 , 机 架辊传动轴较长 , 在传动过程 中甩轴现象严重而 导致 的机 架辊 轴 承 非 正 常受 力 转 动 , 以机 架 辊 所
的使 用 寿命长 短 问题 已经成 为制 约钢铁 生 产 的重
要 环节 之一 。在此 , 就某 钢铁 公 司 38 0mm现 场 0
机架辊辊身直径/ m m 机架辊辊身长度/ m m 机 架 辊 辊 距/ m m 机架辊传动电机/ W k 机架辊电机转 速/ rm n (/ i) 机 架 辊 辊 面速 度 / m s (/)
( ) 架辊 轴承 缺油 导致 损坏 。 2机 ( ) 制时 , 3轧 钢坯 扣 头 撞 击 机 架 辊 而 致 轴 承
该 380mm 中厚 板轧 机 是 新 建 的 一 条完 全 0 国产 化 的现代 化 中厚 板 轧 机 生 产 线 , 机 架辊 的 其 布置 采用传 统 的 的结 构 型 式 , 即机 架 辊 由辊 子 装 配 、 动装 置 、 传 离合装 置 、 润滑 冷却装 置 等组成 , 采 用 单 独传 动型式 。辊 子装 配包 含轴 承座 、 承 、 轴 辊 子 以及 内齿 套 , 中靠 近 轧 机 内侧 2根 辊 子采 用 其 双联 轴承座 , 外侧辊 子 采用单 独轴 承座 ; 动装 最 传 置主 要 由传 动 电机 、 动轴 、 动 齿 轮轴 等 组 成 ; 传 传
高线厂精轧机组常见事故原因及解决方案
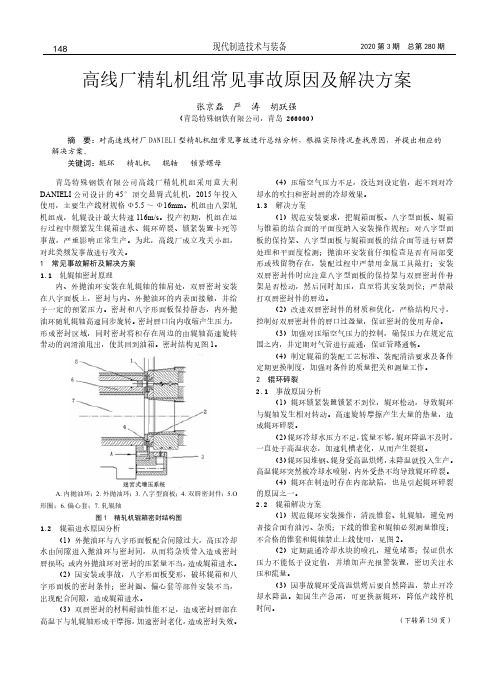
青岛特殊钢铁有限公司高线厂精轧机组采用意大利DANIELI公司设计的45°顶交悬臂式轧机,2015年投入使用,主要生产线材规格Ф5.5~Ф16mm。
机组由八架轧机组成,轧辊设计最大转速116m/s。
投产初期,机组在运行过程中频繁发生辊箱进水、辊环碎裂、锁紧装置卡死等事故,严重影响正常生产。
为此,高线厂成立攻关小组,对此类频发事故进行攻关。
1 常见事故解析及解决方案1.1 轧辊轴密封原理内、外抛油环安装在轧辊轴的轴肩处,双唇密封安装在八字面板上,密封与内、外抛油环的内表面接触,并给予一定的预紧压力。
密封和八字形面板保持静态,内外抛油环随轧辊轴高速同步旋转。
密封唇口向内收缩产生压力,形成密封区域,同时密封将积存在周边的由辊轴高速旋转带动的润滑油甩出,使其回到油箱。
密封结构见图1。
A.内抛油环;2.外抛油环;3.八字型面板;4.双唇密封件;5.O 形圈;6.偏心套;7.轧辊轴图1 精轧机辊箱密封结构图1.2 辊箱进水原因分析(1)外抛油环与八字形面板配合间隙过大,高压冷却水由间隙进入抛油环与密封间,从而将杂质带入造成密封唇损坏;或内外抛油环对密封的压紧量不当,造成辊箱进水。
(2)因安装或事故,八字形面板变形,破坏辊箱和八字形面板的密封条件;密封圈、偏心套等部件安装不当,出现配合间隙,造成辊箱进水。
(3)双唇密封的材料耐油性能不足,造成密封唇部在高温下与轧辊轴形成干摩擦,加速密封老化,造成密封失效。
(4)压缩空气压力不足,没达到设定值,起不到对冷却水的吹扫和密封唇的冷却效果。
1.3 解决方案(1)规范安装要求,把辊箱面板、八字型面板、辊箱与锥箱的结合面的平面度纳入安装操作规程;对八字型面板的保持架、八字型面板与辊箱面板的结合面等进行研磨处理和平面度检测;抛油环安装前仔细检查是否有局部变形或残留物存在,装配过程中严禁用金属工具敲打;安装双唇密封件时应注意八字型面板的保持架与双唇密封件骨架是否松动,然后同时加压,直至将其安装到位;严禁敲打双唇密封件的唇边。
高线精轧机错辊问题的原因分析与控制措施

现代制造技术与装备
2017 第 6 期 总第 247 期
高线精轧机错辊问题的原因分析与控制措施
陈荣军 屈小波
(江苏永钢集团,张家港 215628)
摘 要:介绍了高线精轧机的运行情况,提出了辊箱错辊的危害性,并对错辊的原因从装配和维护角度进行 分析,提出了具体控制错辊的方法。 关键词:精轧机 错辊 固境因素的影响发生尺寸变化而引起辊箱的错辊。 第三,在滚动轴承的装配使用上,要严格控制轧辊轴 的轴向间隙不超过规定的 0.038mm。超过该间隙时,必须要 更换轴承。同时,要控制轴承的使用周期,一般不超过 2 年。 此外, 在设备维护过程中, 要定期更换水封, 保证油品质量, 确保润滑可靠。在紧固轴承压盖时,要严格按照工艺技术 要求执行,保证压盖螺栓紧固力矩在规定值 70N·m。同时, 要将之前的 8.8 级螺栓改为 12.9 级,并在紧固前涂抹 609 螺纹紧固胶,防止螺栓在辊箱运行中松动甚至断裂。 第四,阻尼垫圈要求装配前,轴承压盖自然放置时, 压盖与轴承座两接触端面间有 0.5 ~ 0.8mm 的间隙(可通 过塞尺检查)。当间隙值过大时,必须严格控制紧固力矩, 防止力矩值过大,导致端盖在螺栓紧固力作用下对阻尼垫圈 过分挤压,因为长时间作用会出现橡胶被挤出、缓冲垫从中 间分裂的现象。当间隙值过小(或为负数)时,在轧钢过程 中,轧辊轴在轴承座内产生轴向的微量窜动。一方面,易引 起缓冲垫的端面磨损;另一方面,轴承和缓冲垫在高频率轴 向力和振动的作用下更容易损坏,大大缩减寿命,进而造成 轴向更大的窜动。此外,在影响成品质量的道次上装配进 口的阻尼垫圈,可提高设备的可靠性和在线运转周期。 第五,在日常维护过程中,必须定期安排人员用百分 表检测在线辊箱的轴向窜动量,当轴向窜动量超过 0.15mm 时,应及时安排该辊箱离线保养。
热轧带钢尾部轧破分析及控制方法探讨

热轧带钢尾部轧破分析及控制方法探讨【摘要】热轧带钢尾部轧破主要有跑偏轧破、甩尾轧破、中浪轧破等,生产现场最多的就是跑偏轧破,引起跑偏轧破的各种因素较多,相互间有叠加影响,多因素的轧破严重制约生产。
通过对热轧带钢各类尾部轧破进行详细的成因分析,介绍了减少带钢尾部轧破相应的控制方法及措施。
【关键词】热轧带钢尾部轧破1.前言热连轧带钢生产,精轧在轧制薄规格(1.5*1035/2.0*1250/2.5*1500等以下)、硬质钢种宽轧件带钢时带钢尾部运行极不稳定,控制不好、操作不当不到位,非常容易发生带钢尾部轧破事故。
轧破给生产造成很大的危害,尾部破碎或折断很容易损伤辊面,造成产品的凹凸块缺陷,迫使更换轧辊;破碎残片如与轧件接触,又往往造成轧件表面刮伤或轧废堆钢事故;破碎残片带入卷取机内,轻者要影响卷取机的正常生产,重者还会损坏卷取机各辊面。
因此轧破破坏了精轧的轧制稳定性、连续性,严重时将影响合同完成率、事故辊耗加大,增加了工序制造成本。
随着八钢1750热轧产线轧制品种的多元化,每月生产硬质薄规格批量不断增大,造成带钢在精轧轧制稳定性存在较大问题,尾部轧破事故显得尤为突出,预防、减少带钢尾部轧破成为技术人员和操作人员的重点、难点工作。
2.带钢尾部轧破成因分析及控制方法2.1轧破定义“带钢轧破”,是指在正常生产过程中带钢在穿带、通板、抛钢时跑偏或甩尾的带钢边部或中部折叠进入下游机架,成品带钢表面出现多层重叠或轧穿、撕裂等现象称带钢轧破(如图1)。
图1 带钢轧破外观2.2带钢尾部轧破分类带钢尾部在精轧机内轧破表现形式较多,只有分清轧破各种表现形式,对症分析,才能制定有效的控制方法和操作思路。
(1) 按轧破宽度方向部位分:沿宽度方向尾部轧破形式分为边部(工作侧或传动侧)轧破和中间轧破两种,如图2。
A、边部轧破B、中间轧破图2 尾部轧破部位(2) 按轧破原因分:轧破原因较多,按轧破主要原因分为跑偏轧破、甩尾轧破、中浪或1/4浪叠轧轧破等各种形式,如图3。
热轧支承辊剥落问题根本原因分析及使用建议
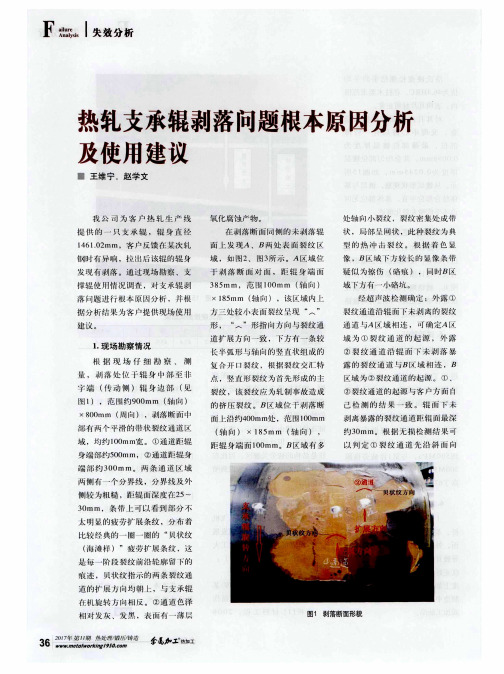
据 分 析 结 果 为 客 户 提 供 现场 使 用
建议。
形, “ 一” 形 指 向方 向与 裂 纹 通 道 扩 展 方 向 一致 ,下 方 有 一 条 较 长半 弧 形 与 轴 向的 竖 直 状 组 成 的 复 合开 门裂纹 ,根 据 裂 纹 交 汇 特
面 上 发 现 、B两 处 表 面 裂 纹 区
域 ,如 图2、图 3 所示 。 区域 位
处 轴 向 小 裂纹 ,裂纹 密 集处 成 带
状 ,局 部 呈 网状 ,此 种 裂 纹 为 典
型 的 热 冲 击 裂 纹 。 根 据 着 色 像 ,B区域 下 方较 长 的 显 像 条 带
l 4 6 1 . 0 2 mm,客户反馈 在某次轧
裂纹 ,该 裂纹 应 为轧 制事 故 造 成 的 挤 压 裂 纹 。B区 域 位 于 剥 落 断
面上 沿 约4 0 0 mm处 ,范 围 1 0 0 mm ( 轴 向 ) ×1 8 5 m m ( 轴 向 ),
② 裂纹 通 道 的 起 源 与客 户方 面 自 己 检 测 的 结 果 一 致 。 辊 面 下 未
纹 未 发现 及 漏检 的 可 能性 。
由 于 支 承 辊 在 机 工 作 时 承 受
法 向 的 接 触 应 力 、 切 向 的摩 擦 力 和 剪 切 应 力 ,以 及 本 身 存在 的 残
另 外 ,A表 面 裂 纹 区 域 下 部
周 边 有 打 磨 痕 迹 ,无 法 确 定打 磨 前 有 无 硌 痕 、色 泽 异 常 等表 面 异 常 情 况 的 存 在 。 客 户 反映 此 处 硬 度 偏 低 。 现 场 初 步 确 定 ,现 状 辊
剥 离暴 露 的 裂 纹 通 道 距辊 而 最深
热轧工作辊弯辊及横移装置的结构分析及优化

热轧工作辊弯辊及横移装置的结构分析及优化工作辊弯辊及横移装置是热连轧机精轧机组的核心部件之一,其结构优劣对于精轧机充分发挥控制和改善板形、提高板带材平直度具有重要影响。
如今,改进设备,提高产品质量成为各钢铁企业越来越关注的方向。
文章针对公司以往设计制造的多套热连轧设备的工作辊弯辊横移装置在实际使用中存在的问题,提出了几点改进方案,以期优化结构、降低故障率,提高工作效率。
标签:热轧机;工作辊弯辊及横移;结构优化目前,越来越多的热轧机采用工作辊弯辊及横移装置来控制和改善板形,尤其是热连轧的精轧机组,大多数采用了具有较高凸度控制能力的HCW轧机或CVC轧机。
两者都具有工作辊弯辊和横移装置,区别仅是轧辊的辊型不同,其效果在国内外各大钢铁厂的生产实践中都得到了证实[1]。
作为四辊热轧机的核心部件之一,工作辊弯辊及横移装置的结构合理性对其使用及维护、最终产品的板形及表面质量都具有重要影响。
1 原结构及其存在的问题公司以往设计的弯辊横移装置普遍采用的结构包含固定塊、移动块、横移缸以及装在移动块内部的弯辊缸和锁紧缸。
其操作侧结构如图1所示,工作状态下,由装在移动块里的两个弯辊缸提供弯辊力,锁紧缸卡住工作辊轴承座上的凸台,横移缸带动移动块和工作辊整体移动。
该结构由装在横移缸活塞杆内的位移传感器检测移动块位置,能够实现对工作辊横移量的精确控制。
传动侧弯辊横移装置的结构相对简单,仅有固定块、移动块和限位装置组成(见图2),由装在移动块内的锁紧缸的楔形缸头插入轴承座的卡槽内,依靠工作辊的轴向窜动来带动移动块。
在现场使用过程中,该结构也存在一些问题。
具体有如下方面:锁紧缸容易漏油。
在操作侧,锁紧缸活塞杆一端通过T型头与挡块连接,一端可插入固定块上的圆孔中。
挡块在导套中滑动并承受工作辊轴承座的冲击,不可避免地造成磨损以及两者间隙增大,从而使得锁紧缸活塞杆承受弯矩。
活塞杆承受弯矩会造成两端的密封损坏甚至漏油。
在传动侧,锁紧缸的供油和回油是通过两根细长的接管伸入移动块中进行配管的,一方面由于无法观察不易安装,另一方面一旦此处泄漏也不易发觉和维护,造成工作辊无法锁紧等故障。
轧机机架精加工后变形分析及对策

安 徽 冶 金 科 技 职 业 学 院 学 报
J u n l f h i c t n l olg fMealr y a d T c n lg o r a u ai a l e o tl g n e h oo y o An Vo o C e u
度没有看到这方面 的推荐 资料 , 否可 以适 当降 是 低。
出炉温 度 t2 0C :5 o 小 时散 热 量 : q=e (2一t)=4* 2*( 5 .t 1 F 5 20—
2 ) 4 8 0K a 0 = 7 4 cl
4 结 论 与 对 策
( )5  ̄ 12 0C出炉 、 后 窗 口光 刀 时机 架 没 有 冷 6天
中图分 类号 : G 3 .3 文献 标识 码 : 文 章编 号 :6 2 94 20 ) 一02 T 331 B 17 —9 9 (0 8 增 0 9—0 1
我公 司 20 07年上 半 年在 科堡 桥 式龙 门镗铣 先
后精  ̄ T_ 轧机 机架 2 , n -重 片 经厂 检检 验尺 寸 和形
级 工程 师 。
放热 时间核 算 :
( 下转 第 3 ) 7页
20 年 增刊 08
翟顺 建 : 防止和 减少薄壁 工件 变形的方 法
・3 ・ 7
螺钉压紧。图 3 中压紧环压在工件 的底 部 , a 是工 件 刚性 比较 弱 的部位 , 易产 生变形 。如把 压 紧环 容
的尺寸稍 改 变 一 下 , 在 工 件 刚性 较 好 的 轮 辐 处 压
一
个压紧环图 4 所示 , b 使压板 的压力通过压紧环
均匀分 布 在工件 的锥面 上 , 这就可 以避免 工件 产 生
高线精轧机组成品辊环爆辊原因分析及控制措施

2019年第4期1前言首钢水钢钢轧事业部高线作业区为全连轧高速线材生产线,设计能力为年产50万t/年,全线由6架粗轧机(平立轧机布置),6架中轧机(平立轧机布置),6架预精轧机(平立轧机布置,后四架为285悬臂辊环紧凑型机组)和10架精轧机(顶交45°轧机)组成,共28道次。
轧件依次进入各机组,全轧线为无扭连续轧制。
在预精轧机组前后及预精轧机组各机架间共设有7个活套装置,用于保证轧件的无张力轧制,以提高产品的尺寸精度。
精轧机组为顶交45°无扭轧机,10架轧机集体传动,采用碳化钨辊环。
在精轧机组内轧件为微张力无扭轧制。
2019年6月份以来,高线在轧制8mm、10mm 规格时频繁发生成品机架辊环爆辊,造成辊环的不正常消耗,严重影响正常生产,同时也带来生产成本的上升。
钢轧事业部决定对高线成品机架辊环冷却进行改进,确保辊环冷却均匀避免爆辊事故发生。
2辊环特性高速线材精轧机组采用的轧辊辊环是碳化钨为主的硬质合金辊环,碳化钨硬质合金辊环由于具有良好的热传导性能,在高温下硬度下降作者简介:李勇,(1978~),男,轧钢助理工程师,从事轧钢技术工作。
高线精轧机组成品辊环爆辊原因分析及控制措施李勇蒙世东胡友红王海益吴俊(首钢水钢钢轧事业部贵州六盘水553028)摘要:本文针对水钢高线轧制各规格成品机架辊环出现爆辊进行探讨分析,采取改进辊环冷却效果进行实践生产,解决成品机架辊环爆辊,提高轧机作业率、降低工人劳动强度。
关键词:碳化钨辊环;爆辊;辊环冷却装置;轧机生产率Cause Analysis and Preventive Measure of Finished-Product Roller GrooveOutburst in High-Speed Finishing Rolling Mill GroupLi Yong Meng Shidong Hu Youhong Wang Haiyi Wu Jun(Industrial Department of Steelmaking and Steel Rolling,Shougang Shuicheng Iron &Steel (Group)Co.,Ltd.,Liupanshui 553028,Guizhou,China)Abstract:The causes of finished-product roller groove outburst in high-speed finishing rolling mill group in Shuigang are investigated and analyzed,the measure to improve cooling effect of roller groove is put into practice to prevent roller groove outburst in finished mill stand and improve effi⁃ciency of rolling mill and reduce labor intensity of workers.Keywords:tungsten carbide roller groove;roller groove outburst;cooling device of roller groove;pro⁃ductivity of rolling mill高线精轧机组成品辊环爆辊原因分析及控制措施11··水钢科技SHUIGANG SCIENCE&TECHNOLOGY第150期图1辊环爆辊示意图少,耐热疲劳性能好,耐磨性好,强度高等特点。
07-耐磨型、高保持精轧后段工作辊

自动化程度高
现代化轧机配备板型控制技术,如CVC、 PC轧制。
一 产品研发背景
--使用条件 现代化轧机轧制品种向多元化、高端化方向发展。
对精轧后段工作辊适应轧制条件的要求更高!
国内不同品种带材轧线数
14 12 10 轧 8 线 数 6 4 2 0 不锈钢 管线钢 硅钢 双相钢 2 6 10 13
不完全统计:国内近50条热带轧线中轧制新品种的轧线20余条, 比例达40%以上。
耐磨型高保持精轧后段工作辊 普通改进型高NiCr
三 产品特点
--辊面保持能力
工作层内的石墨含量、形态
组织控制方案
一致,分布均匀; 工作层内的碳化物含量、形 态一致,分布均匀; 辊面粗糙度保持较好的一致 性,改善板材质量。
辊面保持 能力强
三 产品特点
--辊面保持能力
轧辊不同直径碳化物含量变化
二 研发过程
--产品需求
热轧带钢连轧机精轧后段工作辊必须具备:
高的辊身硬度 高的耐磨损性能 低的硬度降落 良好的辊面保持能力
耐磨型 高保持 精轧后段工作辊
三 产品特点
--硬度及耐磨性提高
形 成 特 有 ( 显 微 硬 度
合金化处理
≥HV2400)碳化物,构 成 耐磨质点; 碳化物形态细小,在轧辊 基体中呈弥散分布。
某厂家实际使用的毫米轧制量对比
4500 4000 3500 3000 2500 2000 1500 1000 500 0
耐磨型高保持精轧后 段工作辊 普通改进型 高NiCr
t/mm
毫米轧制量明显提高30%左右
应用效果
使用下机后轧辊表面照片
表面粗糙度评价良好,完全满足高等级钢板轧制需求!
热轧支承辊剥落问题根本原因分析及使用建议

热轧支承辊剥落问题根本原因分析及使用建议热轧支承辊剥落问题根本原因分析及使用建议■王维宁,赵学文我公司为客户热轧生产线提供的一只支承辊,辊身直径1461.02mm,客户反馈在某次轧钢时有异响,拉出后该辊的辊身发现有剥落。
通过现场勘察、支撑辊使用情况调查,对支承辊剥落问题进行根本原因分析,并根据分析结果为客户提供现场使用建议。
1. 现场勘察情况根据现场仔细勘察、测量,剥落处位于辊身中部至非字端(传动侧)辊身边部(见图1),范围约900mm(轴向)×800mm(周向),剥落断面中部有两个平滑的带状裂纹通道区域,均约100mm 宽。
①通道距辊身端部约500mm,②通道距辊身端部约300mm。
两条通道区域两侧有一个分界线,分界线及外侧较为粗糙,距辊面深度在25~30mm,条带上可以看到部分不太明显的疲劳扩展条纹,分布着比较经典的一圈一圈的“贝状纹(海滩样)”疲劳扩展条纹,这是每一阶段裂纹前沿轮廓留下的痕迹,贝状纹指示的两条裂纹通道的扩展方向均朝上,与支承辊在机旋转方向相反。
②通道色泽相对发灰、发黑,表面有一薄层氧化腐蚀产物。
在剥落断面同侧的未剥落辊面上发现A、B两处表面裂纹区域,如图2、图3所示。
A区域位于剥落断面对面,距辊身端面385mm,范围100mm(轴向)×185mm(轴向),该区域内上方三处较小表面裂纹呈现“︿”形,“︿”形指向方向与裂纹通道扩展方向一致,下方有一条较长半弧形与轴向的竖直状组成的复合开口裂纹,根据裂纹交汇特点,竖直形裂纹为首先形成的主裂纹,该裂纹应为轧制事故造成的挤压裂纹。
B区域位于剥落断面上沿约400mm处,范围100mm (轴向)×185mm(轴向),距辊身端面100mm。
B区域有多处轴向小裂纹,裂纹密集处成带状,局部呈网状,此种裂纹为典型的热冲击裂纹。
根据着色显像,B区域下方较长的显像条带疑似为擦伤(硌痕),同时B区域下方有一小硌坑。
经超声波检测确定:外露①裂纹通道沿辊面下未剥离的裂纹通道与A区域相连,可确定A区域为①裂纹通道的起源,外露②裂纹通道沿辊面下未剥落暴露的裂纹通道与B区域相连,B区域为②裂纹通道的起源。
- 1、下载文档前请自行甄别文档内容的完整性,平台不提供额外的编辑、内容补充、找答案等附加服务。
- 2、"仅部分预览"的文档,不可在线预览部分如存在完整性等问题,可反馈申请退款(可完整预览的文档不适用该条件!)。
- 3、如文档侵犯您的权益,请联系客服反馈,我们会尽快为您处理(人工客服工作时间:9:00-18:30)。
热轧车间典型案例分析之二
——0619乙班顶精轧机后机架辊事故分析
一、前言
2006年6月19日,热轧乙班在生产厚度为14mm钢板,精轧机轧制第一道次时将精轧机后机架辊顶起,影响时间170分钟。
现把这次事故的经过与教训进行一下分析,供大家参考。
二、事故经过
2006年6月19日乙班,生产14mm船板,精轧机第一道,钢板下扣将精轧机后机架辊顶起,钢板倒回机前,停机处理共影响时间170分钟。
三、原因分析
1、机架辊退出没有及时点检发现是造成事故的主要原因。
根据现场设备状况分析,机架辊不退出,不可能将机架辊顶出,所以,机架辊退出是顶机架辊的前提条件,退出后没有及时发现应列为主要因素。
2、中间坯厚度偏薄,造成精轧机第一道压下量小,致使钢板严重下扣将机架辊顶出是造成事故的重要原因。
3、机架辊定位可靠性差也是事故发生的重要原因。
四、教训与反思
1、要进一步加强对操作设备的点检,包括静态和动态的点检,并且责任到人。
在生产过程中,班组长要对关键设备部位及时了解状况(机架辊、液压缸、挡水板等),可采取承包等方式责任到人,明确责权利,杜绝事故的发生。
2、对设备状况、工艺状况的变化缺乏敏锐性。
当钢板翘头时应注意那些问题,扣头时应注意那些问题,班长和点检人应时刻心中有根“弦”,时刻做到心中有“数”,增强工作的责任心。
3、工作想当然、不精准。
中间坯的厚度由精轧机压下工根据品种规格道次以及性能等要素确定,厚度值要力求准确,如发生变化应及时联系沟通。
每个工序都要努力为下道工序创造最优的条件,下道工序就是上道工序的顾客,粗轧机是炉头和看火的顾客,炉头和看火要为粗轧机服务,同样,精轧机是粗轧机的顾客,矫直机是精轧机的顾客,等等,我们讲“为顾客创造价值光荣”,不是空话虚话,不是虚无飘渺的,是实实在在的,每道工序只有为自己的顾客创造最大的价值,
才可能形成整个工序的高价值,才能是光荣的。
相反,别的工序都挺好,就一个工序因为没精准操作出现事故,影响了整个班组,就是可耻的。
我们就是要在全车间形成“为顾客创造价值光荣,以不精准操作为耻”的浓厚氛围。
4、精轧机机架辊定位不牢固,方式落后已不是近期问题,车间将继续大力呼吁,促成机架辊定位系统的改善和优化。
目前已有基本方案,计划按照粗轧机工作辊模式,将护板和机架辊脱离,从根本上杜绝此类事故。
但在改造到位之前,仍需要我们依靠精准工作来杜绝事故发生。