装配式组合深孔钻加工中几点问题的研究
分析装配式建筑施工中的技术难题与瓶颈

分析装配式建筑施工中的技术难题与瓶颈装配式建筑,也称为预制构件建筑,是一种新兴的建筑技术,其特点是将构件在工厂内进行预制加工后,再运到现场进行组装。
这种建筑方式可以提高施工的效率,并减少对环境的影响。
然而,在实际应用过程中,装配式建筑还存在着许多技术难题和瓶颈,下面将对这些问题进行分析。
一、设计和构件精度难以保证装配式建筑所使用的构件需要在工厂内进行预制加工,在这个过程中设计和构件精度是十分重要的。
然而,由于各种原因会导致设计和构件精度无法完全保证。
比如,在预制加工过程中可能存在设备不稳定、人为因素等问题造成尺寸偏差或者变形;而在运输过程中也难免会受到震动和振动等外力的影响。
这些问题都会给施工带来困扰,因为无论是尺寸偏差还是形状变化都会导致构件之间的连接困难。
二、连接方式与强度不足装配式建筑中连接方式的选择对于整体结构的稳定性和强度至关重要。
然而,目前在连接方式上还没有达到一个完美的解决方案。
常见的连接方式有焊接、螺栓等,但这些方式都有其各自的问题。
比如,焊接存在着热变形、结构强度降低的问题;螺栓紧固则需要严格控制螺栓预压力和紧固力矩,否则容易出现松动和断裂等情况。
三、节能隔音效果有待提高装配式建筑在节能和隔音方面相较于传统建筑还有很大提升空间。
装配式建筑常常使用钢结构或混凝土预制构件,因此导致了墙体隔音性能不理想的问题。
在设计上需要考虑更好的隔音材料和结构设计来提高整体建筑在噪声控制和隔热性能上的表现。
四、施工周期延长尽管装配式建筑可以提高施工效率,但仍存在一些技术难题导致施工周期延长。
例如,精确测量引起的诸多调整步骤可能导致施工时间延长,或者装配过程中出现的构件拟对接不准确也会造成施工时间的浪费。
因此,如何在保证质量的前提下缩短施工周期是一个亟待解决的问题。
五、维护和管理成本高装配式建筑在维护和管理方面存在一定的挑战。
由于结构设计复杂,构件间连接众多,导致隐蔽部位检修困难;同时,专业工人培训和技术储备也是一项庞大的任务。
深孔钻加工常见的10个常见问题和解决措施
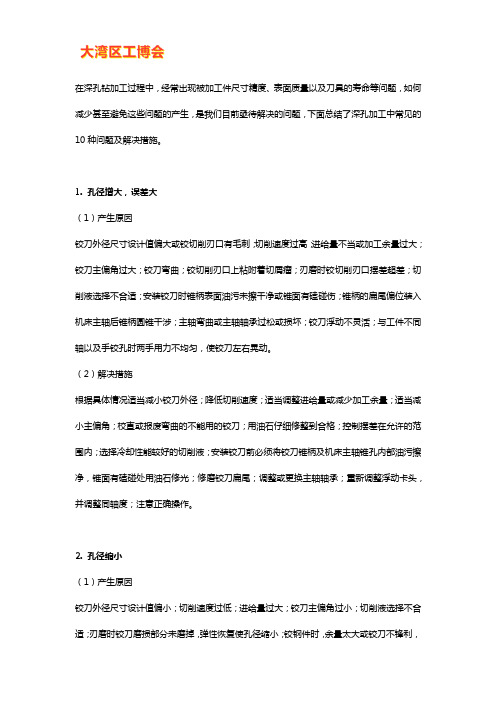
在深孔钻加工过程中,经常出现被加工件尺寸精度、表面质量以及刀具的寿命等问题,如何减少甚至避免这些问题的产生,是我们目前亟待解决的问题,下面总结了深孔加工中常见的10种问题及解决措施。
1. 孔径增大,误差大(1)产生原因铰刀外径尺寸设计值偏大或铰切削刃口有毛刺;切削速度过高;进给量不当或加工余量过大;铰刀主偏角过大;铰刀弯曲;铰切削刃口上粘附着切屑瘤;刃磨时铰切削刃口摆差超差;切削液选择不合适;安装铰刀时锥柄表面油污未擦干净或锥面有磕碰伤;锥柄的扁尾偏位装入机床主轴后锥柄圆锥干涉;主轴弯曲或主轴轴承过松或损坏;铰刀浮动不灵活;与工件不同轴以及手铰孔时两手用力不均匀,使铰刀左右晃动。
(2)解决措施根据具体情况适当减小铰刀外径;降低切削速度;适当调整进给量或减少加工余量;适当减小主偏角;校直或报废弯曲的不能用的铰刀;用油石仔细修整到合格;控制摆差在允许的范围内;选择冷却性能较好的切削液;安装铰刀前必须将铰刀锥柄及机床主轴锥孔内部油污擦净,锥面有磕碰处用油石修光;修磨铰刀扁尾;调整或更换主轴轴承;重新调整浮动卡头,并调整同轴度;注意正确操作。
2. 孔径缩小(1)产生原因铰刀外径尺寸设计值偏小;切削速度过低;进给量过大;铰刀主偏角过小;切削液选择不合适;刃磨时铰刀磨损部分未磨掉,弹性恢复使孔径缩小;铰钢件时,余量太大或铰刀不锋利,易产生弹性恢复,使孔径缩小以及内孔不圆,孔径不合格。
(2)解决措施更换铰刀外径尺寸;适当提高切削速度;适当降低进给量;适当增大主偏角;选择润滑性能好的油性切削液;定期互换铰刀,正确刃磨铰刀切削部分;设计铰刀尺寸时,应考虑上述因素,或根据实际情况取值;作试验性切削,取合适余量,将铰刀磨锋利。
3. 铰出的内孔不圆(1)产生原因铰刀过长,刚性不足,铰削时产生振动;铰刀主偏角过小;铰切削刃带窄;铰孔余量偏;内孔表面有缺口、交叉孔;孔表面有砂眼、气孔;主轴轴承松动,无导向套,或铰刀与导向套配合间隙过大以及由于薄壁工件装夹过紧,卸下后工件变形。
装配式建筑施工问题与对策的分析

装配式建筑施工问题与对策的分析一、介绍装配式建筑是一种先进的施工方式,它通过在工厂预制构件,并在现场进行组装安装,大大缩短了施工周期,提高了施工效率。
然而,在实际的施工过程中,也存在着一些问题和挑战。
本文将就装配式建筑施工中常见的问题进行分析,并提出相应的对策。
二、质量控制问题1. 规范不完善:目前,国内关于装配式建筑的规范和标准体系还不够健全,缺乏统一的设计与生产规程。
这导致了产品质量参差不齐。
2. 加工误差:装配式建筑要求构件精度高,一旦加工误差较大,则可能导致安装困难或者无法拼接。
这需要严格控制加工过程中的质量。
对策:1. 完善规范:推动相关部门尽快补充完善装配式建筑的设计、生产和安装规范标准,在提高产品质量方面加强监管。
2. 强化监测检测:引入现代化仪器设备,加强对装配式建筑构件的监测与检测,及时发现并纠正质量问题。
三、施工管理问题1. 协调难题:装配式建筑涉及多个专业和环节,需要各方进行协同作业。
然而,由于信息不畅通、交流不到位等原因,导致了协调困难。
2. 现场组织不当:装配式建筑在现场组织时需要合理布置作业区域、设备设置等,一旦不合理安排,可能影响施工进度和质量。
对策:1. 强化沟通:各方应加强信息共享,提高沟通效率,加强项目经理的统筹和协调能力。
2. 合理布局:在施工前制定详细的施工方案,并按照计划进行现场组织,确保施工进度和质量。
四、施工安全问题1. 人员防护措施不足:装配式建筑对工人的技术要求较高,如果缺乏必要的培训和防护设备,将增加事故发生的风险。
2. 施工困难导致安全风险:由于装配式建筑存在一些特殊的施工难题,如高空作业、大型构件起吊等,如果不加以妥善解决,将给施工人员带来安全隐患。
对策:1. 培训和教育:加强对参与装配式建筑施工人员的培训和教育,提高他们的技能水平和安全意识。
2. 强化管理:制定严格的安全操作规程,进行经常性的安全检查,确保施工过程中的安全问题得到及时解决。
装配式工程施工中存在的问题剖析

装配式工程施工中存在的问题剖析
随着现代建筑技术不断发展,装配式建筑模式也逐渐成为一种趋势,而在装配式工程施工中,也存在着很多问题。
首先,装配式工程需要在工厂进行制造,难免制造过程中会出现质量问题。
例如,钢结构的加工精度不足、焊接质量不良、墙板安装不牢等问题都有可能影响到整个工程的质量。
其次,装配式工程施工中需要涉及到多种不同的材料和工序,需要考虑到各种材料之间的兼容性以及拼接的密合度。
由于材料和拼接的不匹配,容易导致施工的质量和效率下降。
再次,装配式工程的安装需要严格遵循施工标准和规范,因为如果在安装过程中出现问题,将会给后续施工工作带来很大的影响。
例如,假如构件安装不平整,将会给后续装饰工程施工造成一定困难。
最后,装配式工程在设计过程中需要考虑到整体的审美和美观度。
在设计过程中,需要考虑到各种要素的完美搭配,例如外形、颜色、材料、结构等,保证装配式工程整个项目的美观度。
总的来说,装配式工程施工中存在的问题并不是局限于一个领域的,而是对整个工程的质量和效率产生影响。
为了最大限度地降低这些问题,施工方需要注意材料质量和施工标准的执行,着重于工厂的制造质量控制和各个施工环节的质量管理。
钻研装配式建筑施工的关键技术难题

钻研装配式建筑施工的关键技术难题装配式建筑作为现代建筑领域的一项重要技术创新,具有施工速度快、质量可控、环境友好等诸多优势。
然而,在实际应用过程中,仍然存在着一些关键技术难题需要钻研和解决。
本文将对装配式建筑施工的关键技术难题展开讨论。
一、构件连接技术的研究在装配式建筑施工中,构件之间的连接是至关重要的一环。
目前主流的构件连接方式包括螺栓连接、焊接连接和粘接连接等。
但是由于结构设计和制造工艺等方面存在差异,不同类型的构件连接技术仍然存在着一些问题。
首先,螺栓连接存在着螺纹握力不足、松动易发生等问题。
针对这个问题,可以通过改进螺栓设计、使用高强度螺纹材料以及加强螺栓紧固力矩监控等手段进行改善。
其次,焊接连接容易产生应力集中、变形过大和焊缝裂纹等问题。
为了解决这些问题,可以选择合适的焊接方法和焊工技术,并且在焊接过程中加入应力分散和冷却措施,以提高焊接质量和性能。
最后,粘接连接的关键在于胶黏剂的选择和使用。
当前主要面临的问题是胶黏剂的耐久性、粘结强度以及对环境的适应性等方面。
为了解决这些问题,可以进行多种胶黏剂材料的筛选试验,并结合实际使用条件进行优化设计。
二、装配过程中的误差控制技术装配式建筑施工过程中,误差控制是确保建筑整体质量的重要因素。
由于构件生产、运输和安装等环节都存在一定误差,如何对这些误差进行有效控制,成为一个亟待解决的难题。
第一,在构件生产阶段,需要通过先进的生产设备和精密加工技术来减小构件尺寸偏差。
此外,还可以采用自动化生产线、数控设备等手段来提高生产效率和降低错误率。
第二,在构件运输过程中,需采取科学合理的包装方式,并结合运输车辆稳定性要求,加强固定和保护措施,以避免运输过程中的碰撞和损坏。
第三,在安装过程中,应采用精确测量和定位技术,如激光测量、全站仪等,对构件进行准确定位。
此外,还可以通过调整钢结构支撑、辅助校正等手段来消除误差。
三、建筑物整体性能的评估及优化装配式建筑施工与传统施工方式相比,具有独特的设计思路和构造形式。
探讨钻孔过程中出现的施工质量问题及处理措施

探讨钻孔过程中出现的施工质量问题及处(一)护筒冒水问题:护筒外壁冒水,严重的会引起地基下沉,护筒倾斜和移位,造成钻孔偏斜,甚至无法施工。
造成原因:埋设护筒的周围土不密实,或护筒水位差太大或钻头起落时碰撞。
处理措施:在埋筒时,坑地与四周应选用最正确含水量的黏土分层夯实。
在护筒的适当高度开孔,使护筒内保持1.o〜1.5m 的水头高度。
钻头起落时,应防止碰撞护筒。
发现护筒冒水时,应立即结束钻孔,用粘土在四周填实加固,若护筒严重下沉或移位时,则应重新安装护筒。
(二)孔壁坍陷问题:钻进过程中,如发现排出的泥浆中不断出现气泡,或泥浆突然漏失,则表示有孔壁坍塌迹象。
造成原因:孔壁坍陷的主要原因是土质松散,泥浆护壁不好,护筒周围未用粘土严密填封以及护筒内水位不高。
钻进速度过快、空钻时间过长、成孔后待灌时间过长和灌注时间过长也会引起孔壁坍陷。
处理措施:在松散易坍的土层中,适当埋深护筒,用粘土密实填封护筒四周,使用优质的泥浆,提高泥浆的比重和粘度,保持护筒内泥浆水位高于地下水位。
搬运和吊装钢筋笼时,应防止变形,安放要对准孔位,防止碰撞孔壁,钢筋笼接长时要加快焊接时间,尽可能缩短沉放时间。
成孔后,待灌时间一般不应大于3小时,并控制混凝土的灌注时间,在保证施工质量的情况下,尽量缩短灌注时间(三)缩颈问题:缩颈即孔径小于设计孔径。
造成原因:塑性土膨胀。
处理措施:采用优质泥浆,降低失水量。
成孔时,应加大泵量,加快成孔速度,在成孔一段时间内,孔壁形成泥皮,则孔壁不会渗水,亦不会引起膨胀。
或在导正器外侧焊接一定数量的合金刀片,在钻进或起钻时起到扫孔作用。
如出现缩颈,采用上下反复扫孔的方法,以扩大孔径。
(四)钻孔偏斜问题:成孔后桩孔出现较大垂直偏差或弯曲。
造成原因:钻机安装就位稳定性差,作业时钻机安装不稳或钻杆弯曲所致;地面软弱或软硬不均匀;土层呈斜状分布或土层中夹有大的孤石或其它硬物等情形。
处理措施:先将场地夯实平整,轨道枕木宜均匀着地;安装钻机时要求转盘中心与钻架上起吊滑轮在同一轴线,钻杆位置偏差不大于20cm o在不均匀地层中钻孔时,采用自重大、钻杆刚度大的钻机。
装配式建筑施工过程中的关键问题与对策深入解析与讨论

装配式建筑施工过程中的关键问题与对策深入解析与讨论现代社会快节奏的发展使得装配式建筑成为了一种趋势,其高效、节能的特点受到了广泛关注。
然而,在实际施工过程中,也存在一些关键问题需要解决。
本文将深入解析并讨论装配式建筑施工过程中的几个关键问题,并提出相应对策。
一、设计阶段的合理性由于装配式建筑具有模块化、工厂化特点,因此在设计阶段的合理性显得尤为重要。
首先,需求充分满足是保证装配式建筑成功实施的基础。
在设计阶段,设计师应该考虑到使用者的需求,并将其有效地融入到整体方案中。
其次,强调模块化和可重复使用性。
设计师应该充分利用模块化思维来构思和设计,以提升施工速度和质量。
同时,可重复使用性也需要充分考虑,在施工后退场或重组时能够方便拆卸、翻新或再利用。
二、材料选择与供应链管理在装配式建筑施工过程中,材料的选择及供应链管理是一个关键问题。
首先,要确保所选材料符合国家标准和质量要求,以保证建筑施工后的安全性、可靠性和耐久性。
其次,供应链管理需要做到高效、稳定和专业。
及时采购并配送所需材料对保证装配式建筑施工进度至关重要,因此建立稳定的供应商关系和完善的物流体系非常必要。
三、现场施工与监控装配式建筑的特点是模块化生产后的现场组装,因此现场施工与监控也是关键问题之一。
首先,在施工人员方面,需要确保他们具备足够的技术水平和经验,能够高效地进行组装工作。
其次,采用现代化技术手段来进行施工过程监控可以提升整体质量管理水平。
例如使用摄像头、无人驾驶设备等技术来实现对施工过程的实时监测和调整。
四、运输与安装由于装配式建筑需要从厂房转移到现场进行组装,因此运输与安装也是不可忽视的问题。
在运输方面,需要选择适当的运输工具和方法,并准确计算和控制材料的装载量,以确保运输过程中的安全和高效。
在安装方面,需要严格按照设计方案进行操作,并充分考虑安全因素,避免意外情况的发生。
五、质量控制与验收质量控制与验收是装配式建筑施工过程中的重要环节。
装配式建筑施工工艺常见问题的分析与解决

装配式建筑施工工艺常见问题的分析与解决一、装配式建筑施工工艺的概述装配式建筑施工工艺是一种先期在工厂进行生产、然后再将构件进行运输现场进行组装的建筑施工方法。
相对于传统的施工方式,装配式建筑施工工艺具有时间短、质量可控、环境友好等诸多优势。
然而,在实际操作过程中,也存在一些常见问题需要解决,以下是对这些问题的分析与解决方案。
二、常见问题分析与解决1. 一致性问题:装配式建筑中使用的构件需要具有一致的规格和质量,否则会影响施工过程和施工质量。
分析:一致性问题可能是由于生产工艺不稳定、原材料质量不合格等原因造成的。
解决方案:首先,对于生产工艺进行合理规划和操作,确保每个构件的尺寸、材料和质量达到规定标准。
其次,加强对原材料的质量控制,严格筛选供应商,确保原材料的质量稳定可靠。
2. 运输问题:装配式建筑施工过程中,构件需要进行长距离的运输,运输过程中容易出现构件损坏或丢失的问题。
分析:运输过程中的颠簸、撞击等情况可能导致构件的损坏或丢失。
解决方案:选择合适的运输工具和包装材料,确保装配式构件在运输过程中的安全性。
在长时间运输中,可以使用较大尺寸的包装箱进行集装,减少构件间的相互挤压,同时在包装箱中加入缓冲材料,提高构件的抗震能力。
3. 装配过程中的接口问题:装配式建筑施工过程中,多个构件需要进行拼装,接口的精度和质量直接影响到整个建筑的稳定性和可靠性。
分析:接口问题可能是由于构件尺寸不合格、接口设计不合理等原因造成的。
解决方案:首先,加强对构件尺寸的控制,确保每个构件的尺寸精度满足施工要求。
其次,设计合理的接口结构和拼装方式,尽量减少手工操作的不确定性,可以采用数字化设计和机器自动装配来提高接口的精度和质量。
4. 环境适应问题:装配式建筑施工工艺需要适应各种不同的环境条件,包括气候、地质等。
分析:不同地区的气候条件和地质条件差异较大,可能会对装配式建筑的施工工艺造成影响。
解决方案:在进行装配式建筑施工工艺前,需要充分了解施工地区的气候和地质情况,进行合理的设计和方案制定。
深入研究装配式建筑施工问题与对策

深入研究装配式建筑施工问题与对策装配式建筑施工是一种现代化且快速发展的建筑施工模式,它以工厂化生产和在现场装配为特点。
随着我国经济发展的进一步加快,对于建筑市场需求的迅速增长,装配式建筑作为一种高效、环保、节能的建筑方式逐渐受到广大人民群众和相关政府部门的关注与支持。
然而,在实践中我们也面临着一系列的问题与挑战,在深入研究装配式建筑施工过程中,我们需要探讨并解决以下几个方面的问题:设计方案问题、材料供应问题、质量控制问题、技术培训问题和市场推广问题。
首先,设计方案是装配式建筑施工过程中至关重要的一环。
在装配式建筑施工中,优质合理的设计方案能够有效提高施工效率、降低成本,并确保整个项目能够顺利进行。
因此,在研究装配式建筑施工时,我们需要深入研究设计方案所涉及的各个细节,并针对不同类型和规模的项目提出相应解决方案。
其次,材料供应是装配式建筑施工的另一个重要问题。
在传统的施工模式下,材料供应相对容易控制。
然而,在装配式建筑施工中,由于时间限制和工厂化生产的特点,我们需要精确计划和管理好各个环节的材料供应,确保项目进度的顺利进行。
第三,质量控制是装配式建筑施工中不可忽视的问题。
由于装配式建筑采用的是预制构件进行现场安装,因此对于构件质量的要求较高。
我们需要研究合理有效的质量控制手段,并在实践中加强对装配过程中各个环节质量检测、监控与纠正。
同时,技术培训也是研究装配式建筑施工需要关注的一个方面。
由于这种施工方式与传统施工有很大差异,需要操作人员具备一定技术水平与专业知识才能胜任相关岗位。
因此,在深入研究装配式建筑施工时,有必要加强对相关从业人员技术培训及考评体系的研究与构建。
最后,市场推广问题也是研究装配式建筑施工需要重点考虑的问题之一。
在我国市场上,对于装配式建筑的认可度和接受程度仍然有待提高。
针对这一情况,我们需要研究市场推广手段与策略,加大对装配式建筑施工模式的推广力度,并积极争取政府支持与相关行业的合作。
装配式建筑的施工装配过程中常见问题与解决对策分析

装配式建筑的施工装配过程中常见问题与解决对策分析随着人们对于高效、环保、可持续发展的需求不断增加,装配式建筑作为一种新兴的建筑方式受到了广泛关注和应用。
然而,在装配式建筑的施工装配过程中,仍然存在一些常见问题,如工艺流程不合理、质量控制不严格等。
本文将对这些问题进行深入分析,并提出相应的解决对策。
一、材料质量问题在装配式建筑的施工过程中,材料质量是影响整个项目质量和安全性的重要因素。
常见问题包括原材料质量不达标、构件加工精度偏差大等。
在解决这些问题时,我们可以采取以下对策:1.严格把关原材料供应商:确保所使用的原材料符合相关国家标准和项目要求,可以通过明确指定供应商或者进行材料抽检等方式来加强质量管控。
2.提升构件加工精度:通过引进先进的数控机械设备以及优化操作规程等方法,提高构件加工精度并减少偏差,确保构件的准确度和稳定性。
二、工艺流程问题装配式建筑的施工装配过程中,工艺流程的合理性直接影响着施工效率和质量。
常见问题包括工序繁琐、作业交叉等。
为解决这些问题,我们可以采取以下措施:1.优化工序安排:通过精心规划和优化施工流程,将重复性高、耗时长的工序合并或并行进行,提高施工效率,减少人力资源浪费。
2.合理分区控制:对不同类型和功能的构件进行科学合理的分区,并建立相应的管理体系,避免不必要的交叉作业和混乱情况发生。
三、质量控制问题装配式建筑在施工装配过程中需要严格把控质量。
而在实际操作中,常常出现质量控制不严格等问题。
为解决这些问题,我们可以采取以下对策:1.强化人员培训:加大对从业人员的技能培训力度,提高其专业素质和操作技能,并定期进行考核以保证他们具备一定水平。
2.加强监督检查:建立健全的施工监督和质量检查机制,对施工过程中的每一个环节进行严格把控和监管。
如发现问题及时整改,确保装配式建筑质量安全可靠。
四、安全问题在装配式建筑的施工装配过程中,工人和设备的安全是非常重要的。
常见问题包括作业高空坠落风险大、吊装设备缺乏有效防护等。
装配式建筑施工过程中的关键问题与对策深入探讨

装配式建筑施工过程中的关键问题与对策深入探讨装配式建筑是一种越来越受欢迎的建筑方法,它具有快速、高效、环保等优点。
然而,在装配式建筑施工过程中,也存在着一些关键问题需要解决。
本文将从质量控制、安全管理和人力资源三个方面深入探讨这些问题,并提出相关的对策。
一、质量控制在装配式建筑施工过程中,质量控制是一个至关重要的环节。
以下是在这方面可能出现的关键问题和相应对策:1. 零部件尺寸精度不够:由于生产与运输各个环节可能导致零部件尺寸出现偏差,进而影响整体的拼装效果。
因此,关于零部件尺寸精度的测量和控制非常重要。
可以采用远程激光扫描技术进行实时监测,并使用数值化分析软件进行误差修正。
2. 粘接强度不稳定:在装配式建筑中,粘接往往是连接零部件的主要方式之一。
然而,粘接强度未达到设计要求或者存在很大的波动性会导致整体结构不稳定。
为了解决这个问题,可以利用无损检测技术对粘接工艺进行实时监测,及时发现问题并采取补救措施。
二、安全管理装配式建筑施工过程中的安全管理是一个至关重要的考虑因素。
以下是在这方面可能出现的关键问题和相应对策:1. 高空作业风险:由于装配式建筑中常常需要在高空进行组装和安装工作,一旦发生坠落等事故,将造成严重后果。
针对这个问题,可以加强高空作业人员的培训,并配备合格的安全防护设备,如安全带、网栅等。
2. 火灾隐患:在拼装过程中使用大量的木材或其他易燃材料,也容易引发火灾。
为此,应当设置严格的消防管理制度,并配置消防器材和完善的疏散通道。
同时,施工现场应定期进行火灾隐患检查和演练。
三、人力资源人力资源是推动装配式建筑施工顺利进行的关键因素。
以下是在这方面可能出现的关键问题和相应对策:1. 技术工人缺乏:装配式建筑需要具备专业技能的工人,但目前市场上的装配式建筑技术工人相对匮乏。
为了解决这个问题,可以加强相关技术培训,并鼓励高校设置相关专业,吸引更多人才参与。
2. 施工队伍协作不畅:装配式建筑需要各个环节紧密协作,否则可能导致施工进度延误和质量问题。
装配式建筑施工中常见问题与对策讨论

装配式建筑施工中常见问题与对策讨论一、介绍装配式建筑装配式建筑是指通过在工厂预制构件或模块化部分,然后在现场进行组装的建筑方式。
它具有施工效率高、质量可控、环境友好等优点,因此受到了越来越多的关注和应用。
然而,在实际的装配式建筑施工过程中,也存在一些常见问题需要解决。
二、材料选择与标准化1. 问题:在装配式建筑施工中,材料的选择往往会影响到整体施工质量和使用寿命。
解决对策:首先要选用符合相关标准和规范要求的材料。
其次,需要加强对材料供应商的质量管控,并进行全程监督检查。
2. 问题:由于不同供应商提供的构件可能存在尺寸差异,导致施工中无法精确拼接。
解决对策:推动行业内构件尺寸标准化,鼓励各供应商按照统一规范生产构件,并加强现场精确测量与拼接技术。
三、运输与安装1. 问题:装配式建筑施工需要进行大量的材料运输,运输过程中易受到交通事故、设备故障等不可控因素影响。
解决对策:建立完善的物流体系,合理规划运输路径和时间,确保装配构件的安全运抵现场。
同时,要加强司机培训,并进行有效监督和管理。
2. 问题:装配式建筑安装需要使用吊车、起重机等特殊设备,但设备操作技术水平参差不齐。
解决对策:要求相关人员取得相应资质证书,并进行定期培训与考核。
在现场施工过程中,加强对设备操作环节的监督与指导。
四、质量控制与验收1. 问题:装配式建筑施工中存在验收标准不统一的情况,导致质量把关难度增大。
解决对策:促进行业内制定统一的装配式建筑施工验收标准,并制定相应执法规范。
加强各方之间的沟通与协作,实现质量控制与验收的标准化。
2. 问题:由于装配式建筑涉及多个工序和参与方,施工质量的闭环管理存在一定困难。
解决对策:强化项目全过程质量控制,建立起从设计到施工、使用阶段的闭环管理体系。
加强各参与方之间的沟通与协作,形成质量问题及时沟通解决机制。
五、安全管理1. 问题:装配式建筑在运输、安装和使用阶段都存在一定的安全风险。
解决对策:施工单位要建立完善的安全生产组织体系,并进行相关人员的安全培训。
装配式建筑施工工艺难点解析与研究

装配式建筑施工工艺难点解析与研究一、引言近年来,装配式建筑在全球范围内呈现出快速发展的趋势。
作为一种新型的建筑方式,装配式建筑具有施工周期短、质量可控、环保节能等诸多优势。
然而,在实际施工过程中,仍然存在着一些技术难题和困扰。
本文将就装配式建筑施工中的三大难点进行分析,并提出相应的解决方案。
二、难点一:精确度控制1. 背景介绍装配式建筑对精确度要求较高,尤其是在各个模块连接处的精确匹配上。
由于加工误差、测量误差等原因,常常会导致模块之间无法完全匹配。
2. 解决方案为了解决这一问题,可以采用以下措施:(1)加强生产过程中的质量管控,严格执行相关标准和规范。
(2)加大对工器具及设备支持度和有效性的宣传力度。
(3)开展培训活动,提高操作人员的技术水平和专业素质。
三、难点二:工人技术能力1. 背景介绍装配式建筑需要工人具备较高的技术能力,尤其是在安装过程中需要熟练运用各种工具和材料进行组装。
2. 解决方案为了提高工人的技术能力,可以从以下方面入手:(1)加强培训,提升工人的技术水平。
通过培训课程和实际操作训练,增强他们对装配式建筑施工方法的理解和应用能力。
(2)提供合适的施工环境和条件,为工人创造一个良好的学习和实践机会。
(3)引进先进设备和技术,减少对工人技术要求的依赖性。
四、难点三:信息沟通与协调1. 背景介绍装配式建筑涉及到不同团队之间的紧密合作,各个环节之间需要及时准确地传递信息才能保证施工进展顺利进行。
2. 解决方案为了解决信息沟通与协调问题,可以采取以下措施:(1)规范化管理:在项目启动阶段制定详细的施工计划,并明确各个环节之间的关联和依赖关系,确保信息传递的顺畅性。
(2)建立高效的沟通渠道:通过建立专门的沟通平台或使用现有技术手段,及时准确地将信息传达到各方,并及时解决问题。
(3)加强团队合作:培养团队合作意识,加强不同环节之间的协作与配合,提高整体施工效率。
五、结论装配式建筑是未来建筑行业发展的趋势,然而在实际施工过程中仍然存在一些技术难题。
装配式建筑施工中的工艺缺陷与质量问题分析

装配式建筑施工中的工艺缺陷与质量问题分析随着社会的发展和人们对环境友好型、经济高效型建筑需求的提升,装配式建筑作为一种新兴的施工方式得到了广泛应用。
然而,在装配式建筑施工过程中,工艺缺陷和质量问题经常出现,严重影响了建筑工程的质量和安全性。
本文将从材料选择、加工制造、构件连接以及施工管理等方面对装配式建筑施工中的工艺缺陷与质量问题进行分析。
一、材料选择材料是装配式建筑的基础,选用合适的材料至关重要。
然而,在实际施工中存在以下一些常见问题:1.优劣材料混搭:由于市场上存在各种不同品牌和规格的材料,有些厂商为了节约成本往往倾向于采用低价劣质材料,导致整个结构强度和稳定性下降。
2.材料疲劳:在运输和组装过程中,由于震动或其他力的作用,使得一些细脆材料容易出现疲劳断裂的问题。
3.材料湿度控制:装配式建筑通常需要在工厂内进行加工和预制,如果材料在加工之前没有充分干燥,会导致构件在施工后膨胀或收缩,影响整体的稳定性。
二、加工制造装配式建筑的加工制造是保证质量的关键环节。
然而,由于技术和操作员经验限制,以下问题容易发生:1.尺寸误差:装配式建筑的每个构件都需要精确计算和精细制造,在这个过程中,如果操作不严谨或者设备不准确,就容易造成尺寸误差,进而影响构件的连接和整体结构。
2.表面处理不当:衔接处需要有良好的密合性才能保证整体结构安全稳定。
然而,在实际情况下很多时间因为表面处理不当或涂层质量不过关导致产生裂纹、剥落等问题。
3.剖切负载考虑不足:装配式建筑构件之间要通过各种连接方式进行衔接。
若无法有效传递受力或者强度设计不合理,则可能导致构件连接处的工艺缺陷和力学问题。
三、构件连接装配式建筑施工过程中,构件之间的连接方式是决定整体稳固性的重要因素。
以下是一些可能存在的问题:1.连接强度不足:在现场组装时,如果连接紧固不到位或者材料强度不匹配,就会出现构件之间的脱落和倾斜等情况,进而危害整个建筑结构的安全性。
2.防水处理不当:装配式建筑表面需要进行严密的防水处理,但是有时由于安装时施工细节未注意或人为操作失误,可能造成防水层破损或者渗漏问题。
对装配式建筑施工工艺的关键问题进行分析

对装配式建筑施工工艺的关键问题进行分析装配式建筑是一种新兴的建筑技术,它采用工厂预制和现场组装的方式进行施工。
这种建造方式具有快速、节能、环保等优势,越来越受到各地政府和企业的关注和推广。
然而,在实际施工过程中,装配式建筑还存在一些关键问题需要解决。
本文将对这些问题进行分析,并提出相应的解决方案。
一、材料选择与加工问题在装配式建筑施工中,材料选择与加工是非常重要的一环。
合适的材料和高质量的加工可以确保整个结构的稳定性和耐久性。
1.1 材料选择问题当选择材料时,需要考虑多种因素,如强度、耐候性、阻燃性等。
同时,还应考虑可再生资源利用率和环境影响等因素。
对于不同部位所选用材料要做好合理搭配,以满足不同部位的需求。
1.2 加工问题在装配式建筑施工中,需要对材料进行切割、钻孔等加工。
精细度要求高,而且每个构件都需要按照严格的尺寸要求进行加工。
因此,需要配备高精度设备,并严格控制每个加工环节的质量。
二、运输与搬运问题装配式建筑的构件需要经过远距离运输到施工现场,然后由施工人员进行搬运和组装。
在这个过程中,存在一些运输和搬运问题需要解决。
2.1 运输问题装配式建筑的构件较大,如何选择适当的运输方式是一个关键问题。
对于远距离运输,可以选择铁路、水路或者专用设备进行运输。
同时还需考虑货物固定和保护措施,以确保货物在运输中不受损坏。
2.2 搬运问题装配式建筑的构件需要在施工现场进行搬运和组装。
这就要求搬运设备要满足安全、便捷和高效的要求。
操作人员需要接受专门培训,以确保他们能够正确使用搬运设备,并且做好安全防护措施。
三、质量控制问题在装配式建筑施工过程中,质量控制是一个非常重要且繁琐的任务。
不仅要控制材料和构件的加工质量,还需要对施工过程中的每一个环节进行严格的质量控制。
3.1 构件质量控制装配式建筑的构件需要经过多个环节的加工,如切割、焊接、装配等。
每一环节都需要严格按照施工图纸和技术规范进行操作,并做好相应的记录和检测。
分析装配式建筑施工中的工艺缺陷与改进措施

分析装配式建筑施工中的工艺缺陷与改进措施装配式建筑是指在工厂或制造基地进行部分预制和加工,然后将构件运至现场进行组装的建筑方法。
它能够提高施工效率、降低成本,并减少对环境的影响。
然而,在装配式建筑的施工过程中,也存在着一些工艺缺陷。
本文将分析这些缺陷,并提出改进措施。
一、产生的工艺缺陷1. 封闭性不良装配式建筑在制造过程中使用了大量的密封材料,如密封胶、填缝剂等。
但如果密封材料的选择不当或应用不正常,就会导致施工后的装配式建筑出现封闭性不良问题。
例如,密封胶选择不合适可能会影响隔热和防水效果,填缝剂施工不规范则容易导致漏水、渗水等问题。
2. 连接处质量差装配式建筑中各个构件之间通过连接件进行组合和固定。
若连接件选择不当或制作精度不高,就容易造成连接处质量差的问题。
这包括连接松动、失稳以及强度不足等情况。
不仅影响整体结构的稳定性,还可能会引发安全隐患。
3. 板材表面质量不符合要求装配式建筑中常使用的是各种板材,如墙板、地板等。
然而,由于制造过程中的精度要求和作业条件限制,很容易导致板材表面质量不符合设计要求。
例如出现凹凸不平、破损、色差等问题。
这不仅影响了建筑的外观质量,还可能会降低其使用寿命。
二、改进措施1. 提高生产工艺精度为了避免工艺缺陷的产生,在装配式建筑的制造过程中,应加强对每个环节的管理和控制。
特别是在模具设计和加工、构件生产、组装等关键环节上,应强调精细化操作,并严格把关质量。
2. 优化材料选择与应用密封材料和连接件是保证装配式建筑封闭性和稳定性的关键因素。
因此,在选择这些材料时需考虑其适用性与可靠性,并确保供应商提供合格的产品。
同时,在实际施工过程中也要遵循正确的应用方法,保证施工质量。
3. 强化质量检验与验收对于装配式建筑而言,质量管控是至关重要的。
在生产过程中,应加强对各个构件和材料的检验,确保其符合设计要求;同时,在施工现场也应建立严格的质量验收制度,对已安装完成的构件进行检查,并及时发现并解决存在的问题。
提高组合钻床深孔加工质量的几点措施

提高组合钻床深孔加工质量的几点措施发表时间:2019-06-21T11:53:52.917Z 来源:《科学与技术》2019年第03期作者:张旭辉李钊王清章孙忠军[导读] 分析组合钻床深孔加工技术的不足,积极研究其解决策略,以便于更好的提高组合钻床深孔加工质量。
中国中车青岛四方股份有限公司转向架分厂山东青岛 266111 摘要:随着我国社会经济的发展以及科学技术的应用,我国的加工技术也在不断的更新当中。
组合钻床深孔加工技术,是一门高技术工艺,无论对设备的要求,还是对技术人员的要求都比其它加工工艺要高。
因此,在实际加工过程当中,要及时分析组合钻床深孔加工技术的不足,积极研究其解决策略,以便于更好的提高组合钻床深孔加工质量。
本文对组合钻床深孔加工技术存在的不足之处做出了分析,并对其解决策略做出了探讨,最后提出了提高组合钻床深孔加工质量的几点建议。
关键词:组合钻床深孔加工质量措施组合钻床的应用,解决了钻床加工大型零部件时操作不方便的难题,然而在组合钻床深孔加工中,如对油缸孔、液压阀孔等的加工,一般对加工精度以及工件表面的质量要求较高,再加上被加工料件的切削加工性较差,所以对组合钻床深孔加工质量的要求较高。
因此,如何提高组合钻床深孔加工质量的研究是必备课题。
一、组合钻床深孔加工概述在组合钻床深孔加工中,深孔一般是指孔深超过孔径5倍的圆柱孔。
通常情况下,深孔按照孔深与孔径的比值,即L/D,分为三种:一般深孔、中等深孔、特殊深孔。
从分类中可以看出,比值越大,其加工难度也越来越大。
二、组合钻床深孔加工中影响加工质量的常见问题在组合钻床深孔加工过程中,存在着一些问题影响着组合钻床深孔加工质量,需要对其进行研究。
一般情况下,存在问题主要包括以下几种情况:2.1.孔径缩小或增大在组合钻床深孔加工过程中,造成孔径缩小或增大的原因有多种,主要包括以下几种情况:(1)铰刀外径尺寸设计值偏小或偏大;(2)切削的速度过快或过慢;(3)加工过程中进给量过大或加工余量过大;(4)铰刀在刃磨时刃磨不当;(5)切削液的选择不适合。
装配式组合深孔钻加工中几点问题的研究

装配式组合深孔钻加工中几点问题的研究L—Z217~2000深孔钻床在钻深孔作业时,卷屑容易缠绕在刀具上,并将刀具挤死,甚至撞弯刀杆,增加净误差,提高热误差,导致工件报废,并给工作人员和机床操作人员带来工作危险,本文针对这种情况,结合对切削理论系统分析,确定了通过引进并装配式复合刀具进行切削试验,结合实际对L—Z217~2000深孔钻床进行改良的尝试和探讨从而决定刀具最佳几何参数以及最理想的工艺系统、切削参数,有效改善并解决了断屑、排屑的处理和刀片磨损严重的问题。
从而改良切削工艺,提高刀具寿命,节约了加工成本,提高产品加工质量。
标签:深孔钻削扁钻切削参数0 引言L—Z217x2000卧式深孔钻床一般装配传统“外排屑高速钢扁钻”。
加工中由于有时断屑不够灵敏。
经常生成带状切屑并发生带状切屑缠绕到刀具上挤死刀具甚至撞弯刀杆,致使工件报废和为工作人员带来安全隐患。
为了避免这种现象和改善断屑情况,尝试了引进了美国肯纳公司装配式组合刀具,但是投入使用后发现刀具磨损严重。
而且因为无法打磨机夹镀钛合金刀块的刀刃,在刀顿的时候只能更换新刀块.增加了加工成本昂贵,本文主要在提高刀具寿命和合理使用刀具展开讨论。
1 思路与方法通过结合理论分析与实际工艺试验,对工艺进行探索和改进并针对性地对新形刀具的断屑、排屑原理及其过度磨损原因进行分析,并且进行改进。
主要步骤分为:①刀具几何结构及钻削作业过程中的所受外力的力学分析:②判定刀具以何种形式磨损:③在不同切削参数下进行试验并记录的试验数据;④得出结论,制定相应改进措施和方案。
2 理论分析2.1 刀具的几何结构和所受外力分析新引进的进口刀体钻头装配有“镀钛层的硬质合金”刀块。
如图1。
新型装配式刀具在几何结构上相当于结合了麻花钻和深孔扁钻的组合刀具。
在刀体中心处安装了定心钻(直径为10)可承受部分切削力并提高定位精度,然后在刀体的左右两侧呈不对称结构的装有4片硬质合金。
通过刀体对刀片产生夹持和定位作用当硬质合金刀片磨损后,可通过调整顶丝和楔块延伸刀片,刀片则可以再次使用使用;由于两侧刀片的排列相对于几何中心并不对称,使切屑在两侧受力不均匀,易于断裂而形成较小的切屑,使排屑顺畅的同时非对称排列还可以使切削时的径向力在刀刃上的径向力也可以得到较合理的平衡,散热条件好也相对改善,使热误差减小,如图2。
装配式建筑施工中常见的施工工艺问题及对策

装配式建筑施工中常见的施工工艺问题及对策前言:随着社会的快速发展和人们对环境友好型建筑需求的增加,装配式建筑作为一种新型、可持续发展的建筑方式受到越来越多的关注。
然而,在装配式建筑施工过程中,由于特殊性质和复杂性,常常面临许多施工工艺问题。
本文将重点探讨装配式建筑施工中常见的施工工艺问题,并提出相应的解决对策。
一、生产过程中零部件精度不准确导致组合困难在装配式建筑的生产过程中,如果零部件的精度不准确,很容易导致后续组合时出现困难。
这可能是由于制造设备、外来干扰或操作员技术等因素引起。
针对这个问题,首先需要提高生产设备的精度和稳定性。
可以采用先进的数控设备和自动化机械来代替传统生产方式,以提高生产效率和零部件精度。
其次,需要培养一支技术熟练、素质高的操作员队伍。
提供系统化的培训和专门的技术指导,提高操作员的技术水平和工作质量。
二、模块化制作中尺寸不统一引发安装问题在装配式建筑施工中,尺寸不统一是经常遇到的施工工艺问题之一。
由于每个模块都是在不同的生产线上生产,并且存在材料变形、测量误差等因素,导致模块之间的尺寸存在差异。
为解决这个问题,可以采取以下对策。
首先,在设计阶段应该严格把控每个模块的尺寸要求,充分考虑各种因素并进行充分的测试验证。
其次,在生产过程中设置严格的质检程序,对每个模块进行尺寸检测,确保符合规定标准。
最后,在安装阶段加强现场管理和调整手段,通过现场微调来解决尺寸不统一带来的问题。
三、施工工序协调难度大导致进度延误装配式建筑通常需要多部件同时施工,并且涉及多种专业领域。
不同工序之间协调难度大,容易导致施工进度延误。
针对这个问题,需要加强施工组织和管理。
首先,在施工前要进行充分的计划和排期,并合理安排各个工序的时间,确保能够有序进行。
其次,建立高效的沟通机制和协作平台,及时解决多种专业领域之间的技术疑难问题,减少等待和调整时间。
最后,在施工过程中,及时跟踪和控制进度,发现问题及时处理,并灵活调整资源以适应不同情况。
- 1、下载文档前请自行甄别文档内容的完整性,平台不提供额外的编辑、内容补充、找答案等附加服务。
- 2、"仅部分预览"的文档,不可在线预览部分如存在完整性等问题,可反馈申请退款(可完整预览的文档不适用该条件!)。
- 3、如文档侵犯您的权益,请联系客服反馈,我们会尽快为您处理(人工客服工作时间:9:00-18:30)。
装配式组合深孔钻加工中几点问题的研究
L—Z217~2000深孔钻床在钻深孔作业时,卷屑容易缠绕在刀具上,并将刀具挤死,甚至撞弯刀杆,增加净误差,提高热误差,导致工件报废,并给工作人员和机床操作人员带来工作危险,本文针对这种情况,结合对切削理论系统分析,确定了通过引进并装配式复合刀具进行切削试验,结合实际对L—Z217~2000深孔钻床进行改良的尝试和探讨从而决定刀具最佳几何参数以及最理想的工艺系统、切削参数,有效改善并解决了断屑、排屑的处理和刀片磨损严重的问题。
从而改良切削工艺,提高刀具寿命,节约了加工成本,提高产品加工质量。
标签:深孔钻削扁钻切削参数
0 引言
L—Z217x2000卧式深孔钻床一般装配传统“外排屑高速钢扁钻”。
加工中由于有时断屑不够灵敏。
经常生成带状切屑并发生带状切屑缠绕到刀具上挤死刀具甚至撞弯刀杆,致使工件报废和为工作人员带来安全隐患。
为了避免这种现象和改善断屑情况,尝试了引进了美国肯纳公司装配式组合刀具,但是投入使用后发现刀具磨损严重。
而且因为无法打磨机夹镀钛合金刀块的刀刃,在刀顿的时候只能更换新刀块.增加了加工成本昂贵,本文主要在提高刀具寿命和合理使用刀具展开讨论。
1 思路与方法
通过结合理论分析与实际工艺试验,对工艺进行探索和改进并针对性地对新形刀具的断屑、排屑原理及其过度磨损原因进行分析,并且进行改进。
主要步骤分为:①刀具几何结构及钻削作业过程中的所受外力的力学分析:②判定刀具以何种形式磨损:③在不同切削参数下进行试验并记录的试验数据;④得出结论,制定相应改进措施和方案。
2 理论分析
2.1 刀具的几何结构和所受外力分析
新引进的进口刀体钻头装配有“镀钛层的硬质合金”刀块。
如图1。
新型装配式刀具在几何结构上相当于结合了麻花钻和深孔扁钻的组合刀具。
在刀体中心处安装了定心钻(直径为10)可承受部分切削力并提高定位精度,然后在刀体的左右两侧呈不对称结构的装有4片硬质合金。
通过刀体对刀片产生夹持和定位作用当硬质合金刀片磨损后,可通过调整顶丝和楔块延伸刀片,刀片则可以再次使用使用;由于两侧刀片的排列相对于几何中心并不对称,使切屑在两侧受力不均匀,易于断裂而形成较小的切屑,使排屑顺畅的同时非对称排列还可以使切削时的径向力在刀刃上的径向力也可以得到较合理的平衡,散热条件好
也相对改善,使热误差减小,如图2。
切削刀刃是两侧斜中间高的结构。
切削时切削刀中间部分的切削刃先于两侧的两组切削刃接触待加工面。
使两个切削刃沿着两方向和一定的角度进行切削加工,加工时由于切屑卷曲方向不同因此在两个方向上同时受力不断撕扯,即从切削刃刀尖部分分屑。
切屑弯曲至刀体后,与另一片弯曲的切屑以及刀体碰撞受力使切屑相互挤压。
在挤压与撕扯两种不同方向的力的同时作用下,起到断屑的作用和效果。
定心麻花钻结构如图3:由紧钉螺钉固定在刀体上,由于其直径小,散热差,因此钻头端部水孔保证冷却液直接冷却,切削刃刀体两侧亦加工出类似排屑槽的形状,可加速切屑的流动,易于使切屑紧贴钻心排出。
利于冷却液的顺畅流动。
钻削时,定心麻花钻首先开始切削,118°锋角保证其良好的加工导向性,钻因受到了比两侧轴片更大的轴向载荷,可以改善切削刀片的工作条件。
2.2 刀具磨损分析由于装配式刀具的特点,所有刀片都是由各单体组装而成,虽然使用灵活,但是与整体式刀具相比刚性稍差,在切削作业中在外力的作用下容易引起共振,使得刀头更容易磨损破裂;而且由于结构原因,一般情况下定心钻在不断调整刀头的对中偏差的同时,还要相对于两个侧切削刃首先承受较大的扭矩和轴向切削力,因此定心的麻花钻存在磨损严重的情况。
引起刀具易于损坏的具体要素:①由于定心钻在作业中始终在切削并承担大量轴向切削力和扭矩,而且综合散热差、排屑差导致的摩擦系数增大等因素严重影响了金属应性,因此钻部一般磨损会很严重;②被加工零件由于在材质、密度、性能和组织不均匀等,在加工时时常会导致产生冲击力,引起共振、冲击振动等不利因素,如果导致刀具进给时轴向发生偏斜测绘产生切削刃进给量一侧增大,另一侧减小而受到不平衡的外力,因此很容易使一侧刀片因外力影响磨钝,从而导致另一侧切削刀片也相继磨钝失效;③当工件回转中心与麻花钻工作切人点以及刀杆轴心与麻花钻几何、物理中心不同轴时,容易使麻花钻受力不均导致折断,即使刀杆应性很强足以调整挠度,不同心的问题也会造成由于刀具进给偏斜,不垂直均匀受力从而加速刀刃磨损;④无论钻深孔和浅孔时,孔钻削每转的进给量都要比在使用麻花钻加工同类工序时小得多。
因为深孔钻头的钻杆无法像麻花钻头那样承受那样大的扭矩和应力而造成刀具折断,而且进给量过大的话会引起排屑困難,温度升高或划伤钻头,导致刀具过早损坏和刀刃破损,而且还会增加热误差。
进给量太小时切屑受外力太小又难以折断,使得切屑缠绕刀体产生不利因素,会使钻头过早疲劳损坏或过度啃刀,甚至产生危险。
因此在决定切削速度和进给量必须采用合理的方法;⑤如果刀具切削部分几何角度存在缺陷在切削工作时由于刀具几何形状与工件加工要求不吻合,使主刀和侧刀吃不上力或者吃力部位不准,从而造成新刀具失效的一系列原因。
通过以上理论分析及实验验证,确定了相应的工艺改进措施:①如图4中所示,选取最佳数值和参数安装麻花钻。
实践证明,在加工不同的材料或执行切削参数时的取值应做相应调整,只有在安装刀具组件达到最合理的条件下才能使组合刀具的功效得到最大程度发挥,并减小组件的非正常磨损和保护刀具;②提高毛坯材料的质量,如果粗加工毛坯后存在问题,再好的刀具也不会达到应有效果,因此增加正火工序以使材质细化,使材料密度均匀,从而减少刀具异常进给的几率;③提高刀杆刚性并且改进加工工艺和提高工件装夹定位精度,保证理论要求
的“工件回转轴、刀杆轴线同轴度应在0.1mm;工件回转镜像跳动≤0.008mm工件入刀断面跳动≤0.008mm;床身导轨在水面上的垂直度≤0.04mm;床身导轨在垂直面上的垂直度≤0.04mm。
”
改进工艺及系统参数后效果明显,切削顺利,刀具损耗率降低50%以上。
参考文献:
[1]吴凤和.一种新型的装配式硬质合金扁钻[J].新技术新工艺2002(3);15-16.
[2]王世清.深孔加工技术[M].西北工业大学出版社,2003.
[3]霍乐登.深孔加工[M].北京:国防工业出版社,1984.
注:本文中所涉及到的图表、注解、公式等内容请以PDF格式阅读原文。