TIG焊常见缺陷及预防
史上最全!!常见焊接缺陷产生原因、危害及防止措施
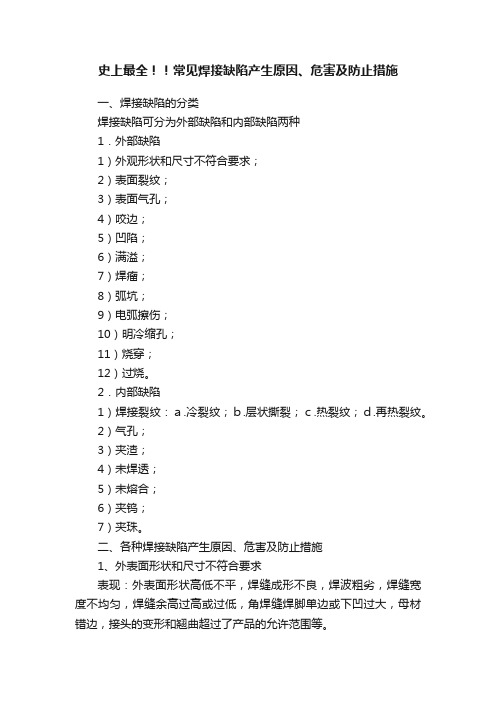
史上最全!!常见焊接缺陷产生原因、危害及防止措施
一、焊接缺陷的分类
焊接缺陷可分为外部缺陷和内部缺陷两种
1.外部缺陷
1)外观形状和尺寸不符合要求;
2)表面裂纹;
3)表面气孔;
4)咬边;
5)凹陷;
6)满溢;
7)焊瘤;
8)弧坑;
9)电弧擦伤;
10)明冷缩孔;
11)烧穿;
12)过烧。
2.内部缺陷
1)焊接裂纹:a.冷裂纹;b.层状撕裂;c.热裂纹;d.再热裂纹。
2)气孔;
3)夹渣;
4)未焊透;
5)未熔合;
6)夹钨;
7)夹珠。
二、各种焊接缺陷产生原因、危害及防止措施
1、外表面形状和尺寸不符合要求
表现:外表面形状高低不平,焊缝成形不良,焊波粗劣,焊缝宽度不均匀,焊缝余高过高或过低,角焊缝焊脚单边或下凹过大,母材错边,接头的变形和翘曲超过了产品的允许范围等。
危害:焊缝成形不美观,影响到焊材与母材的结合,削弱焊接接头的强度性能,使接头的应力产生偏向和不均匀分布,造成应力集中,影响焊接结构的安全使用。
产生原因:焊件坡口角度不对,装配间隙不匀,点固焊时未对正,焊接电流过大或过小,运条速度过快或过慢,焊条的角度选择不合适或改变不当,埋弧焊焊接工艺选择不正确等。
防止措施:选择合适的坡口角度,按标准要求点焊组装焊件,并保持间隙均匀,编制合理的焊接工艺流程,控制变形和翘曲,正确选用焊接电流,合适地掌握焊接速度,采用恰当的运条手法和角度,随时注意适应焊件的坡口变化,以保证焊缝外观成形均匀一致。
2、焊接裂纹
表现:在焊接应力及其他致脆因素共同作用下,焊接接头中局部地区的金属原子结合力遭到破坏形成的新界面所产生的缝隙,具有尖锐的缺口和大小的长宽比特征。按形态可分为:纵向裂纹、横向裂纹、弧坑裂纹、焊趾裂纹、焊根裂纹、热影响区再热裂纹等。
焊接——焊接缺陷及防治措施
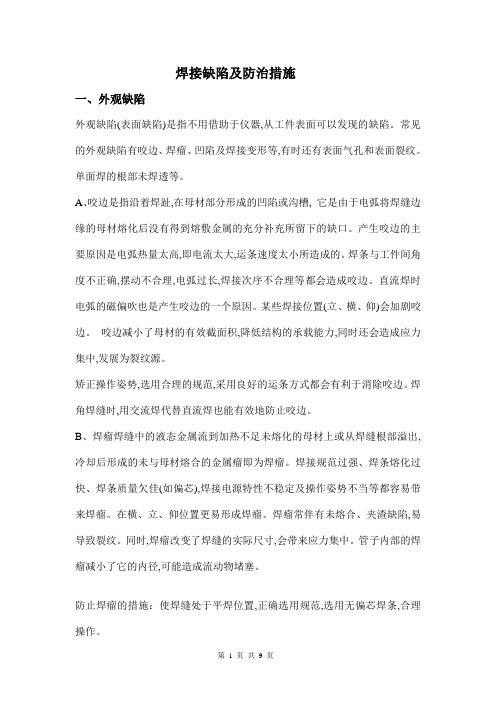
焊接缺陷及防治措施
一、外观缺陷
外观缺陷(表面缺陷)是指不用借助于仪器,从工件表面可以发现的缺陷。常见的外观缺陷有咬边、焊瘤、凹陷及焊接变形等,有时还有表面气孔和表面裂纹。单面焊的根部未焊透等。
A、咬边是指沿着焊趾,在母材部分形成的凹陷或沟槽, 它是由于电弧将焊缝边缘的母材熔化后没有得到熔敷金属的充分补充所留下的缺口。产生咬边的主要原因是电弧热量太高,即电流太大,运条速度太小所造成的。焊条与工件间角度不正确,摆动不合理,电弧过长,焊接次序不合理等都会造成咬边。直流焊时电弧的磁偏吹也是产生咬边的一个原因。某些焊接位置(立、横、仰)会加剧咬边。咬边减小了母材的有效截面积,降低结构的承载能力,同时还会造成应力集中,发展为裂纹源。
矫正操作姿势,选用合理的规范,采用良好的运条方式都会有利于消除咬边。焊角焊缝时,用交流焊代替直流焊也能有效地防止咬边。
B、焊瘤焊缝中的液态金属流到加热不足未熔化的母材上或从焊缝根部溢出,冷却后形成的未与母材熔合的金属瘤即为焊瘤。焊接规范过强、焊条熔化过快、焊条质量欠佳(如偏芯),焊接电源特性不稳定及操作姿势不当等都容易带来焊瘤。在横、立、仰位置更易形成焊瘤。焊瘤常伴有未熔合、夹渣缺陷,易导致裂纹。同时,焊瘤改变了焊缝的实际尺寸,会带来应力集中。管子内部的焊瘤减小了它的内径,可能造成流动物堵塞。
防止焊瘤的措施:使焊缝处于平焊位置,正确选用规范,选用无偏芯焊条,合理操作。
C、凹坑凹坑指焊缝表面或背面局部的低于母材的部分。
凹坑多是由于收弧时焊条(焊丝)未作短时间停留造成的(此时的凹坑称为弧坑),仰立、横焊时,常在焊缝背面根部产生内凹。凹坑减小了焊缝的有效截面积,弧坑常带有弧坑裂纹和弧坑缩孔。
TIG焊接过程故障及焊接缺陷
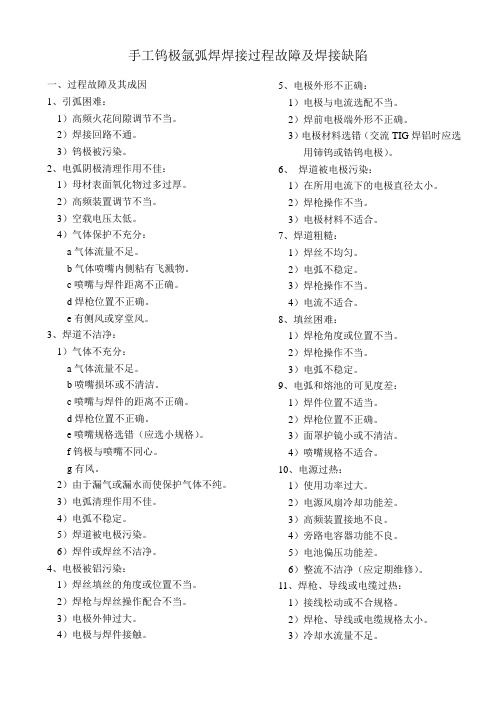
手工钨极氩弧焊焊接过程故障及焊接缺陷
一、过程故障及其成因
1、引弧困难:
1)高频火花间隙调节不当。
2)焊接回路不通。
3)钨极被污染。
2、电弧阴极清理作用不佳:
1)母材表面氧化物过多过厚。
2)高频装置调节不当。
3)空载电压太低。
4)气体保护不充分:
a气体流量不足。
b气体喷嘴内侧粘有飞溅物。
c喷嘴与焊件距离不正确。
d焊枪位置不正确。
e有侧风或穿堂风。
3、焊道不洁净:
1)气体不充分:
a气体流量不足。
b喷嘴损坏或不清洁。
c喷嘴与焊件的距离不正确。
d焊枪位置不正确。
e喷嘴规格选错(应选小规格)。
f钨极与喷嘴不同心。
g有风。
2)由于漏气或漏水而使保护气体不纯。3)电弧清理作用不佳。
4)电弧不稳定。
5)焊道被电极污染。
6)焊件或焊丝不洁净。
4、电极被铝污染:
1)焊丝填丝的角度或位置不当。
2)焊枪与焊丝操作配合不当。
3)电极外伸过大。
4)电极与焊件接触。5、电极外形不正确:
1)电极与电流选配不当。
2)焊前电极端外形不正确。
3)电极材料选错(交流TIG焊铝时应选用铈钨或锆钨电极)。
6、焊道被电极污染:
1)在所用电流下的电极直径太小。2)焊枪操作不当。
3)电极材料不适合。
7、焊道粗糙:
1)焊丝不均匀。
2)电弧不稳定。
3)焊枪操作不当。
4)电流不适合。
8、填丝困难:
1)焊枪角度或位置不当。
2)焊枪操作不当。
3)电弧不稳定。
9、电弧和熔池的可见度差:
1)焊件位置不适当。
2)焊枪位置不正确。
3)面罩护镜小或不清洁。
4)喷嘴规格不适合。
10、电源过热:
1)使用功率过大。
2)电源风扇冷却功能差。
3)高频装置接地不良。
焊接常见缺陷产生的原因及其预防措施
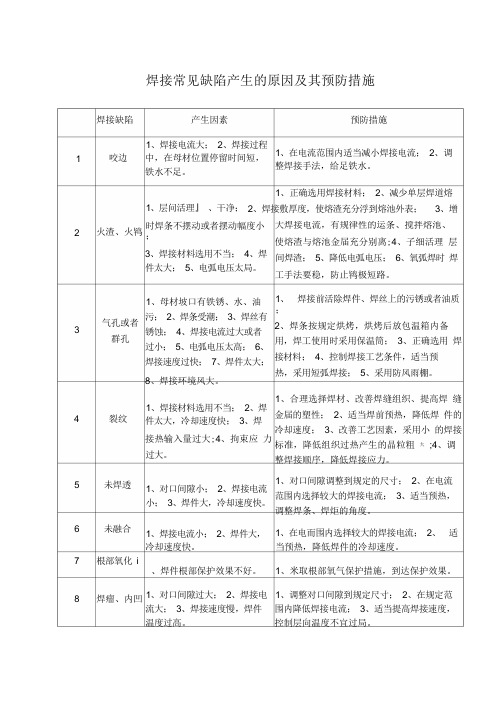
焊接常见缺陷产生的原因及其预防措施
1 2 3 4
5 6 7 8 焊接缺陷
咬边
火渣、火鸨
气孔或者
群孔
裂纹
未焊透
未融合
根部氧化i
焊瘤、内凹
产生因素
1、焊接电流大;
2、焊接过程
中,在母材位置停留时间短,
铁水不足。
预防措施
1、在电流范围内适当减小焊接电流;
2、调
整焊接手法,给足铁水。
1、正确选用焊接材料;
2、减少单层焊道熔
1、层问活理』、干净;
2、焊接敷厚度,使熔渣充分浮到熔池外表;
3、增
时焊条不摆动或者摆动幅度小
;
3、焊接材料选用不当;
4、焊
件太大;5、电弧电压太局。
1、母材坡口有铁锈、水、油
污;2、焊条受潮;3、焊丝有
锈蚀;4、焊接电流过大或者
过小;5、电弧电压太高;6、
焊接速度过快;7、焊件太大;
8、焊接环境风大。
1、焊接材料选用不当;
2、焊
件太大,冷却速度快;3、焊
接热输入量过大;4、拘束应力
过大。
1、对口间隙小;
2、焊接电流
小;3、焊件大,冷却速度快。
1、焊接电流小;
2、焊件大,
冷却速度快。
、焊件根部保护效果不好。
1、对口间隙过大;
2、焊接电
流大;3、焊接速度慢,焊件
温度过高。
大焊接电流,有规律性的运条、搅拌熔池、
使熔渣与熔池金届充分别离;4、子细活理层
间焊渣;5、降低电弧电压;6、氧弧焊时焊
工手法要稳,防止鸨极短路。
1、焊接前活除焊件、焊丝上的污锈或者油质
;
2、焊条按规定烘烤,烘烤后放包温箱内备
用,焊工使用时采用保温筒;3、正确选用焊
接材料;4、控制焊接工艺条件,适当预
热,采用短弧焊接;5、采用防风雨棚。
1、合理选择焊材、改善焊缝组织、提高焊缝
金届的塑性;2、适当焊前预热,降低焊件的
焊条电弧焊常见焊接缺陷及防止措施
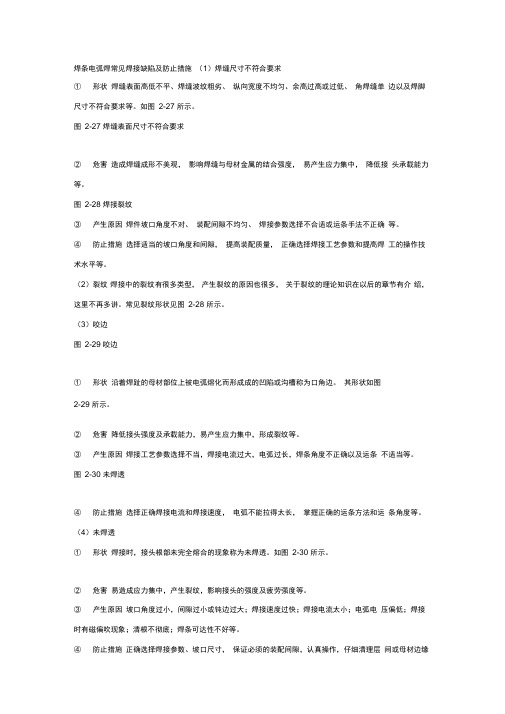
焊条电弧焊常见焊接缺陷及防止措施(1)焊缝尺寸不符合要求
①形状焊缝表面高低不平、焊缝波纹粗劣、纵向宽度不均匀、余高过高或过低、角焊缝单边以及焊脚尺寸不符合要求等。如图2-27 所示。
图2-27 焊缝表面尺寸不符合要求
②危害造成焊缝成形不美观,影响焊缝与母材金属的结合强度,易产生应力集中,降低接头承载能力等。
图2-28 焊接裂纹
③产生原因焊件坡口角度不对、装配间隙不均匀、焊接参数选择不合适或运条手法不正确等。
④防止措施选择适当的坡口角度和间隙,提高装配质量,正确选择焊接工艺参数和提高焊工的操作技术水平等。
(2)裂纹焊接中的裂纹有很多类型,产生裂纹的原因也很多,关于裂纹的理论知识在以后的章节有介绍,这里不再多讲。常见裂纹形状见图2-28 所示。
(3)咬边
图2-29 咬边
①形状沿着焊趾的母材部位上被电弧熔化而形成成的凹陷或沟槽称为口角边。其形状如图
2-29 所示。
②危害降低接头强度及承载能力,易产生应力集中,形成裂纹等。
③产生原因焊接工艺参数选择不当,焊接电流过大,电弧过长,焊条角度不正确以及运条不适当等。
图2-30 未焊透
④防止措施选择正确焊接电流和焊接速度,电弧不能拉得太长,掌握正确的运条方法和运条角度等。(4)未焊透
①形状焊接时,接头根部未完全熔合的现象称为未焊透。如图2-30 所示。
②危害易造成应力集中,产生裂纹,影响接头的强度及疲劳强度等。
③产生原因坡口角度过小,间隙过小或钝边过大;焊接速度过快;焊接电流太小;电弧电压偏低;焊接时有磁偏吹现象;清根不彻底;焊条可达性不好等。
④防止措施正确选择焊接参数、坡口尺寸,保证必须的装配间隙,认真操作,仔细清理层间或母材边缘
焊接的六大缺陷,产生原因、危害
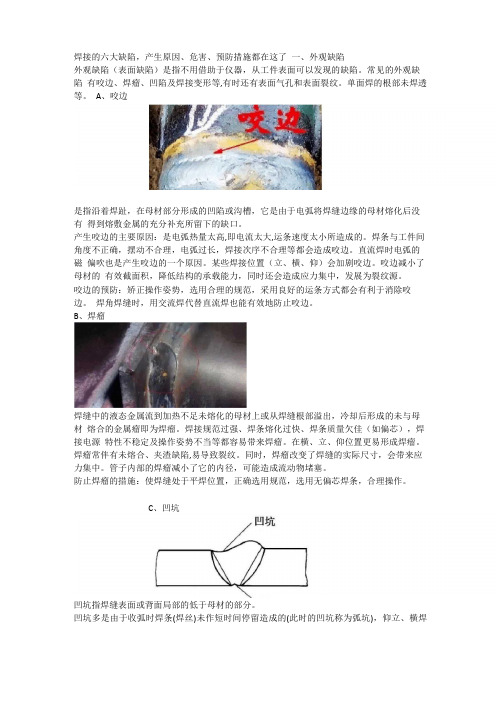
焊接的六大缺陷,产生原因、危害、预防措施都在这了一、外观缺陷
外观缺陷(表面缺陷)是指不用借助于仪器,从工件表面可以发现的缺陷。常见的外观缺陷有咬边、焊瘤、凹陷及焊接变形等,有时还有表面气孔和表面裂纹。单面焊的根部未焊透等。A、咬边
是指沿着焊趾,在母材部分形成的凹陷或沟槽,它是由于电弧将焊缝边缘的母材熔化后没有得到熔敷金属的充分补充所留下的缺口。
产生咬边的主要原因:是电弧热量太高,即电流太大,运条速度太小所造成的。焊条与工件间角度不正确,摆动不合理,电弧过长,焊接次序不合理等都会造成咬边。直流焊时电弧的磁偏吹也是产生咬边的一个原因。某些焊接位置(立、横、仰)会加剧咬边。咬边减小了母材的有效截面积,降低结构的承载能力,同时还会造成应力集中,发展为裂纹源。
咬边的预防:矫正操作姿势,选用合理的规范,采用良好的运条方式都会有利于消除咬边。焊角焊缝时,用交流焊代替直流焊也能有效地防止咬边。
B、焊瘤
焊缝中的液态金属流到加热不足未熔化的母材上或从焊缝根部溢出,冷却后形成的未与母材熔合的金属瘤即为焊瘤。焊接规范过强、焊条熔化过快、焊条质量欠佳(如偏芯),焊接电源特性不稳定及操作姿势不当等都容易带来焊瘤。在横、立、仰位置更易形成焊瘤。焊瘤常伴有未熔合、夹渣缺陷,易导致裂纹。同时,焊瘤改变了焊缝的实际尺寸,会带来应力集中。管子内部的焊瘤减小了它的内径,可能造成流动物堵塞。
防止焊瘤的措施:使焊缝处于平焊位置,正确选用规范,选用无偏芯焊条,合理操作。
C、凹坑
凹坑指焊缝表面或背面局部的低于母材的部分。
凹坑多是由于收弧时焊条(焊丝)未作短时间停留造成的(此时的凹坑称为弧坑),仰立、横焊
常见焊接缺陷及防止措施和注意事项
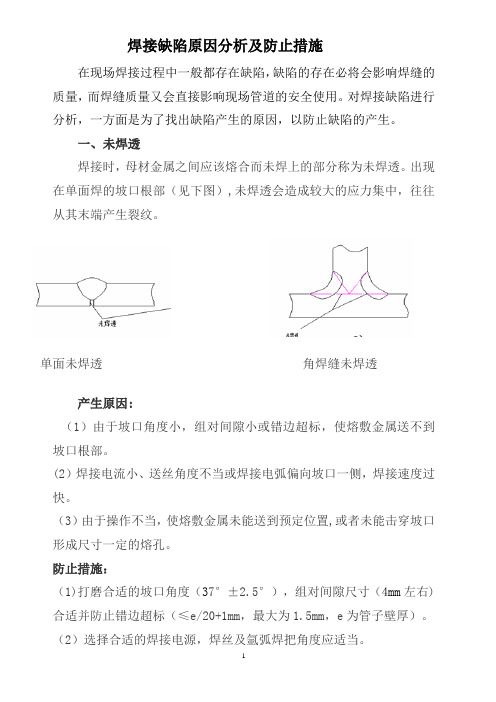
焊接缺陷原因分析及防止措施
在现场焊接过程中一般都存在缺陷,缺陷的存在必将会影响焊缝的质量,而焊缝质量又会直接影响现场管道的安全使用。对焊接缺陷进行分析,一方面是为了找出缺陷产生的原因,以防止缺陷的产生。
一、未焊透
焊接时,母材金属之间应该熔合而未焊上的部分称为未焊透。出现在单面焊的坡口根部(见下图),未焊透会造成较大的应力集中,往往从其末端产生裂纹。
单面未焊透角焊缝未焊透
产生原因:
(1)由于坡口角度小,组对间隙小或错边超标,使熔敷金属送不到坡口根部。
(2)焊接电流小、送丝角度不当或焊接电弧偏向坡口一侧,焊接速度过快。
(3)由于操作不当,使熔敷金属未能送到预定位置,或者未能击穿坡口形成尺寸一定的熔孔。
防止措施:
(1)打磨合适的坡口角度(37°±2.5°),组对间隙尺寸(4mm左右)合适并防止错边超标(≤e/20+1mm,最大为1.5mm,e为管子壁厚)。
(2)选择合适的焊接电源,焊丝及氩弧焊把角度应适当。
(3)掌握正确的焊接操作方法,氩弧焊丝的送进应稳、准确、熟练地击穿尺寸适宜的熔孔,应把熔敷金属送至坡口根部。
二、未熔合
这种缺陷常出现在坡口的侧壁、多层焊的层间及焊缝的根部(见下图)。
产生原因:
(1)由于焊丝和氩弧焊把角度不当,电弧不能良好地加热坡口两侧母材金属,致坡口面母材母材金属未能充分熔化。
(2)在焊接时由于上侧坡口金属熔化后产生下坠,影响下侧坡口面金属的加热熔化,造成“冷接"。
(3)2GT位置操作时,在上、下坡口面击穿顺序不对,未能先击穿下坡口后击穿上坡口,或者在上、下坡口面上击穿熔孔位置未能错开一定的距离,使上坡口熔化金属下坠产生粘接,造成未熔合。
TIG缺陷分析
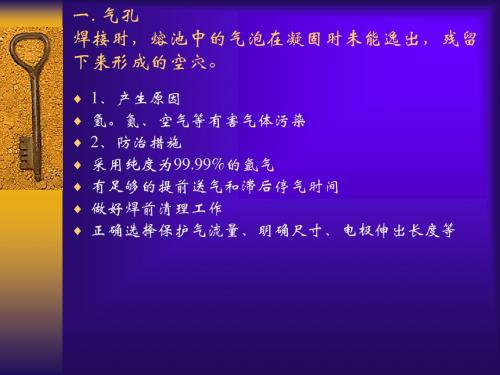
1、产生原因 氢。氮、空气等有害气体污染 2、防治措施 采用纯度为99.99%的氩气 有足够的提前送气和滞后停气时间 做好焊前清理工作 正确选择保护气流量、明确尺寸、电极伸出长度等
二、夹钨:过大的电流引起钨极熔化和蒸发、或 操作过程中钨极与铁水接触导致其微粒进入熔池 造成污染。
焊接工艺选择错误或执行不严格
焊接参数不正确或收弧过快
裂纹
再见
操作不当,送丝过急 电流过大
坡口间隙过大
防止措施:
调至合适电流,送丝均匀
扎丝
九、射穿
产生原因:
电流过大、焊接过程中热量过于集中 防止措施:
调小电流,正确操作,加快摆动节奏。
射穿
裂纹:焊接后焊口的冷却过程产 生的热应力超过材料强度所导致 的裂纹
焊件强行组对 焊件与焊材不匹配
1、原因: 接触引弧或钨电极熔化。 2.防止措施: 采用高频振荡器或高压脉冲发生器引弧 减小电流或加大钨极直径,旋紧钨电极夹头和减小钨电 极伸出长度。 调换有裂纹或撕裂的钨电极
三、未焊透 焊接时接头根部未完全熔透的现象叫未焊透。
产生原因 : 焊缝坡口钝边过大,坡口角度太小、错 边等。 焊接电流过小,送丝不均匀 焊接速度过快或过慢 焊丝位置不当,焊接电弧未熔焊到焊口 根部。
常见焊接缺陷类型产生原因与避免方法
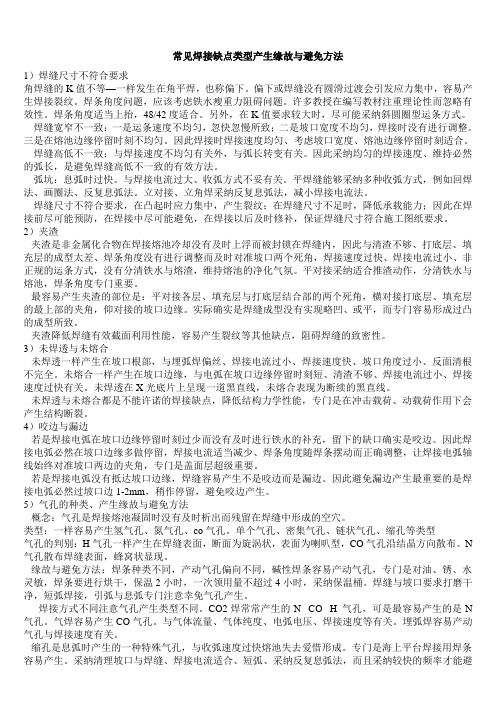
常见焊接缺点类型产生缘故与避免方法
1)焊缝尺寸不符合要求
角焊缝的K值不等—一样发生在角平焊,也称偏下。偏下或焊缝没有圆滑过渡会引发应力集中,容易产生焊接裂纹。焊条角度问题,应该考虑铁水瘦重力阻碍问题。许多教授在编写教材注重理论性而忽略有效性。焊条角度适当上抬,48/42度适合。另外,在K值要求较大时,尽可能采纳斜圆圈型运条方式。焊缝宽窄不一致:一是运条速度不均匀,忽快忽慢所致;二是坡口宽度不均匀,焊接时没有进行调整。三是在熔池边缘停留时刻不均匀。因此焊接时焊接速度均匀、考虑坡口宽度、熔池边缘停留时刻适合。焊缝高低不一致:与焊接速度不均匀有关外,与弧长转变有关。因此采纳均匀的焊接速度、维持必然的弧长,是避免焊缝高低不一致的有效方法。
弧坑:息弧时过快。与焊接电流过大、收弧方式不妥有关。平焊缝能够采纳多种收弧方式,例如回焊法、画圈法、反复息弧法。立对接、立角焊采纳反复息弧法,减小焊接电流法。
焊缝尺寸不符合要求,在凸起时应力集中,产生裂纹;在焊缝尺寸不足时,降低承载能力;因此在焊接前尽可能预防,在焊接中尽可能避免,在焊接以后及时修补,保证焊缝尺寸符合施工图纸要求。
2)夹渣
夹渣是非金属化合物在焊接熔池冷却没有及时上浮而被封锁在焊缝内,因此与清渣不够、打底层、填充层的成型太差、焊条角度没有进行调整而及时对准坡口两个死角,焊接速度过快、焊接电流过小、非正规的运条方式,没有分清铁水与熔渣,维持熔池的净化气氛。平对接采纳适合推渣动作,分清铁水与熔池,焊条角度专门重要。
最容易产生夹渣的部位是:平对接各层、填充层与打底层结合部的两个死角,横对接打底层、填充层的最上部的夹角,仰对接的坡口边缘。实际确实是焊缝成型没有实现略凹、或平,而专门容易形成过凸的成型所致。
TIG焊中产生气孔的因素及其防止措施 DU
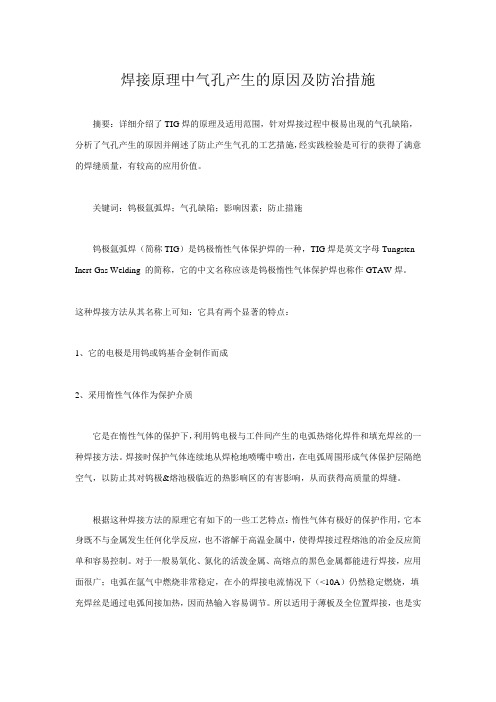
焊接原理中气孔产生的原因及防治措施
摘要:详细介绍了TIG焊的原理及适用范围,针对焊接过程中极易出现的气孔缺陷,分析了气孔产生的原因并阐述了防止产生气孔的工艺措施,经实践检验是可行的获得了满意的焊缝质量,有较高的应用价值。
关键词:钨极氩弧焊;气孔缺陷;影响因素;防止措施
钨极氩弧焊(简称TIG)是钨极惰性气体保护焊的一种,TIG焊是英文字母Tungsten Inert-Gas Welding 的简称,它的中文名称应该是钨极惰性气体保护焊也称作GTAW焊。
这种焊接方法从其名称上可知:它具有两个显著的特点:
1、它的电极是用钨或钨基合金制作而成
2、采用惰性气体作为保护介质
它是在惰性气体的保护下,利用钨电极与工件间产生的电弧热熔化焊件和填充焊丝的一种焊接方法。焊接时保护气体连续地从焊枪地喷嘴中喷出,在电弧周围形成气体保护层隔绝空气,以防止其对钨极&熔池极临近的热影响区的有害影响,从而获得高质量的焊缝。
根据这种焊接方法的原理它有如下的一些工艺特点:惰性气体有极好的保护作用,它本身既不与金属发生任何化学反应,也不溶解于高温金属中,使得焊接过程熔池的冶金反应简单和容易控制。对于一般易氧化、氮化的活泼金属、高熔点的黑色金属都能进行焊接,应用面很广;电弧在氩气中燃烧非常稳定,在小的焊接电流情况下(<10A)仍然稳定燃烧,填充焊丝是通过电弧间接加热,因而热输入容易调节。所以适用于薄板及全位置焊接,也是实
现单面焊双面成形的理想焊接方法;由于填充焊丝不通过焊接电流,不存在熔滴过渡问题,焊接过程没中有飞溅,焊缝成形美观;氩气在焊接过程中仅仅只是单纯的保护隔离作用,因此对工件表面状态要求较高。焊件在焊前要进行表面清洗,除锈、去锈、去灰尘等杂质;钨极承载电流的能力有限,过大的电流会引起钨棒的熔化和蒸发,其微粒有可能进入熔池而出现夹钨,所以TIG焊的焊接电流会受到钨棒限制,故焊接速度较小,生成效率较低;TIG
常见焊接缺陷及防止措施和注意事项
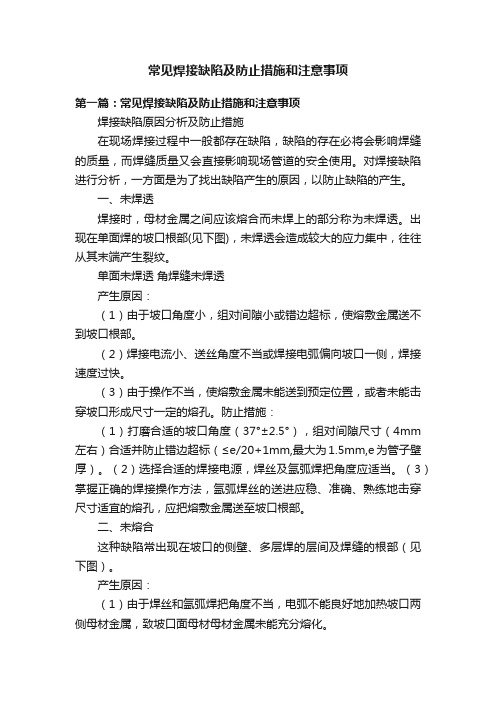
常见焊接缺陷及防止措施和注意事项
第一篇:常见焊接缺陷及防止措施和注意事项
焊接缺陷原因分析及防止措施
在现场焊接过程中一般都存在缺陷,缺陷的存在必将会影响焊缝的质量,而焊缝质量又会直接影响现场管道的安全使用。对焊接缺陷进行分析,一方面是为了找出缺陷产生的原因,以防止缺陷的产生。
一、未焊透
焊接时,母材金属之间应该熔合而未焊上的部分称为未焊透。出现在单面焊的坡口根部(见下图),未焊透会造成较大的应力集中,往往从其末端产生裂纹。
单面未焊透角焊缝未焊透
产生原因:
(1)由于坡口角度小,组对间隙小或错边超标,使熔敷金属送不到坡口根部。
(2)焊接电流小、送丝角度不当或焊接电弧偏向坡口一侧,焊接速度过快。
(3)由于操作不当,使熔敷金属未能送到预定位置,或者未能击穿坡口形成尺寸一定的熔孔。防止措施:
(1)打磨合适的坡口角度(37°±2.5°),组对间隙尺寸(4mm 左右)合适并防止错边超标(≤e/20+1mm,最大为1.5mm,e为管子壁厚)。(2)选择合适的焊接电源,焊丝及氩弧焊把角度应适当。(3)掌握正确的焊接操作方法,氩弧焊丝的送进应稳、准确、熟练地击穿尺寸适宜的熔孔,应把熔敷金属送至坡口根部。
二、未熔合
这种缺陷常出现在坡口的侧壁、多层焊的层间及焊缝的根部(见下图)。
产生原因:
(1)由于焊丝和氩弧焊把角度不当,电弧不能良好地加热坡口两侧母材金属,致坡口面母材母材金属未能充分熔化。
(2)在焊接时由于上侧坡口金属熔化后产生下坠,影响下侧坡口面金属的加热熔化,造成“冷接”。
(3)2GT位置操作时,在上、下坡口面击穿顺序不对,未能先击穿下坡口后击穿上坡口,或者在上、下坡口面上击穿熔孔位置未能错开一定的距离,使上坡口熔化金属下坠产生粘接,造成未熔合。
最全焊接缺陷及防治措施,没有缺陷你的技术就是最高了
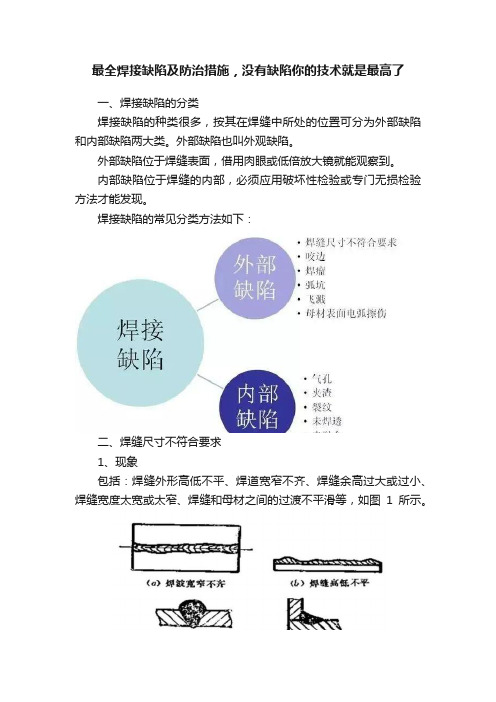
最全焊接缺陷及防治措施,没有缺陷你的技术就是最高了
一、焊接缺陷的分类
焊接缺陷的种类很多,按其在焊缝中所处的位置可分为外部缺陷和内部缺陷两大类。外部缺陷也叫外观缺陷。
外部缺陷位于焊缝表面,借用肉眼或低倍放大镜就能观察到。
内部缺陷位于焊缝的内部,必须应用破坏性检验或专门无损检验方法才能发现。
焊接缺陷的常见分类方法如下:
二、焊缝尺寸不符合要求
1、现象
包括:焊缝外形高低不平、焊道宽窄不齐、焊缝余高过大或过小、焊缝宽度太宽或太窄、焊缝和母材之间的过渡不平滑等,如图1所示。
2、原因分析
(1)焊缝坡口角度、宽度及组装间隙不统一。
(2)焊条直径选择不当,造成填充层过高,失去坡口轮廓线,使盖面宽窄不一,焊缝过高,波纹粗劣。
(3)背面清根刨缝质量差,焊道宽度不一。
(4)焊接电流过大或过小,运条手法和角度不当以及焊速不均匀。
3、危害性
尺寸过小的焊缝,会降低焊接接头的强度;尺寸过大的焊缝,不仅浪费焊接材料,也会增大焊接结构的变形。焊缝金属向母材的过渡处若不平滑,出现尖角,会造成应力集中,降低焊接结构的承载能力。
4、预防措施
(1)采用自动和半自动切割机或刨边机加工坡口。
(2)焊缝组对间隙应控制在标准规范要求值以内,背面用碳弧气刨清根后,采用砂轮修整刨槽及碳化层,使刨槽宽窄一致。
(3)选用适当的焊接电流和焊条直径,遵守焊接工艺,熟练掌握操作技术,保持焊速均匀;手工焊操作人员要熟练地掌握运条速度和焊条角度,以获得成形美观的焊缝。
5、处理方法
对于焊缝余高过高,应用砂轮修整,宽窄不一或高度不够处,应
重新补焊,且补焊连接处应圆滑过渡。
TIG焊在塞焊中常见问题及解决措施
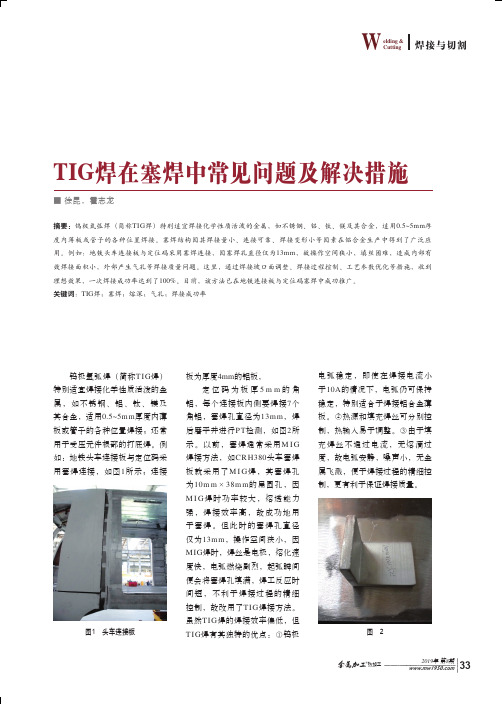
2019年 第8期热加工
33
TIG 焊在塞焊中常见问题及解决措施
■ 徐昆,霍志龙
摘要:钨极氩弧焊(简称TIG 焊)特别适宜焊接化学性质活泼的金属,如不锈钢、铝、钛、镁及其合金,适用0.5~5mm 厚度内薄板或管子的各种位置焊接。塞焊结构因其焊接量小、连接可靠、焊接变形小等因素在铝合金生产中得到了广泛应用。例如:地铁头车连接板与定位码采用塞焊连接,因塞焊孔直径仅为13mm ,故操作空间狭小,填丝困难,造成内部有效焊接面积小,外部产生气孔等焊接质量问题。这里,通过焊接坡口面调整、焊接过程控制、工艺参数优化等措施,收到理想效果,一次焊接成功率达到了100%。目前,该方法已在地铁连接板与定位码塞焊中成功推广。关键词:TIG 焊;塞焊;熔深;气孔;焊接成功率
钨极氩弧焊(简称TIG 焊)特别适宜焊接化学性质活泼的金属,如不锈钢、铝、钛、镁及其合金,适用0.5~5mm 厚度内薄板或管子的各种位置焊接;还常用于受压元件根部的打底焊。例如:地铁头车连接板与定位码采用塞焊连接,如图1所示;连接
板为厚度4mm 的铝板,
定位码为板厚5m m 的角铝,每个连接板内侧要焊接7个角铝,塞焊孔直径为13m m ,焊后磨平并进行PT 检测,如图2所示。以前,塞焊通常采用M I G 焊接方法,如CRH380头车塞焊板就采用了M I G 焊,其塞焊孔为10m m ×38m m 的扁圆孔,因M I G 焊时功率较大,熔透能力强,焊接效率高,故成功地用于塞焊。但此时的塞焊孔直径仅为13m m ,操作空间狭小,因MIG 焊时,焊丝是电极,熔化速度快,电弧燃烧剧烈,起弧瞬间便会将塞焊孔填满,焊工反应时间短,不利于焊接过程的精细控制,故改用了TIG 焊接方法。虽然TIG 焊的焊接效率偏低,但
焊工必看——常见焊接缺陷大全
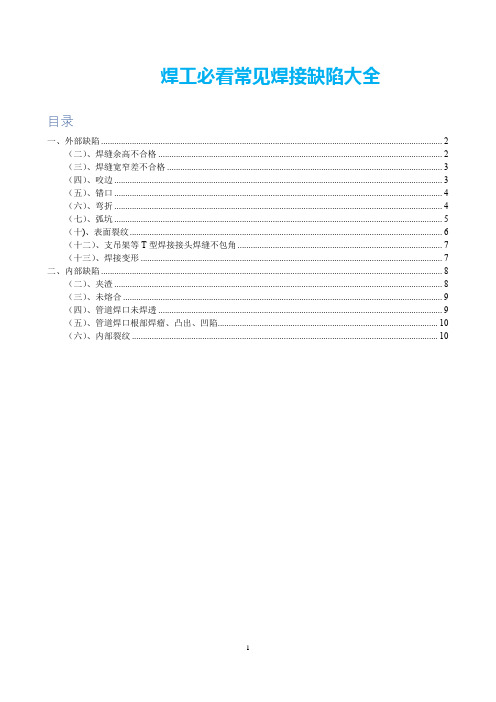
焊工必看常见焊接缺陷大全
目录
一、外部缺陷 (2)
(二)、焊缝余高不合格 (2)
(三)、焊缝宽窄差不合格 (3)
(四)、咬边 (3)
(五)、错口 (4)
(六)、弯折 (4)
(七)、弧坑 (5)
(十)、表面裂纹 (6)
(十二)、支吊架等T型焊接接头焊缝不包角 (7)
(十三)、焊接变形 (7)
二、内部缺陷 (8)
(二)、夹渣 (8)
(三)、未熔合 (9)
(四)、管道焊口未焊透 (9)
(五)、管道焊口根部焊瘤、凸出、凹陷 (10)
(六)、内部裂纹 (10)
一、外部缺陷
(一)、焊缝成型差
1、现象
焊缝波纹粗劣,焊缝不均匀、不整齐,焊缝与母材不圆滑过渡,焊接接头差,焊缝高低不平。
2、原因分析
焊缝成型差的原因有:焊件坡口角度不当或装配间隙不均匀;焊口清理不干净;焊接电流过大或过小;焊接中运条(枪)速度过快或过慢;焊条(枪)摆动幅度过大或过小;焊条(枪)施焊角度选择不当等。
3、防治措施
⑴焊件的坡口角度和装配间隙必须符合图纸设计或所执行标准的要求。
⑴焊件坡口打磨清理干净,无锈、无垢、无脂等污物杂质,露出金属光泽。
⑴加强焊接联系,提高焊接操作水平,熟悉焊接施工环境。
⑴根据不同的焊接位置、焊接方法、不同的对口间隙等,按照焊接工艺卡和操作技能要求,选择合理的焊接电流参数、施焊速度和焊条(枪)的角度。
4、治理措施
⑴加强焊后自检和专检,发现问题及时处理;
⑴对于焊缝成型差的焊缝,进行打磨、补焊;
⑴达不到验收标准要求,成型太差的焊缝实行割口或换件重焊;
⑴加强焊接验收标准的学习,严格按照标准施工。
(二)、焊缝余高不合格
TIG焊常见缺陷与预防措施
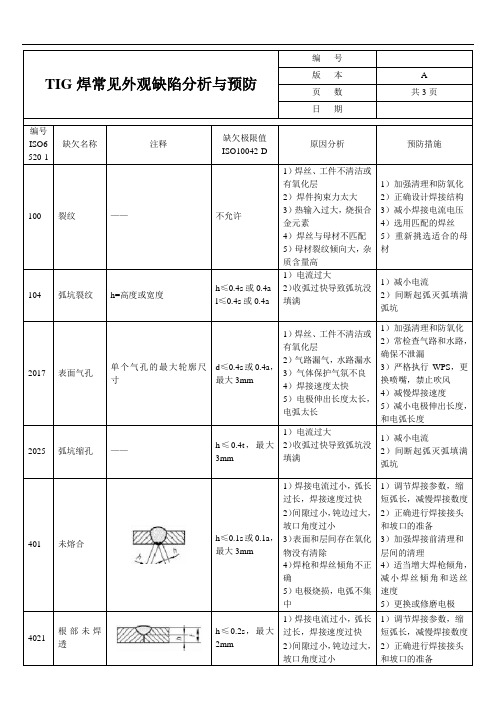
TIG焊常见外观缺陷分析与预防编号
版本 A 页数共3页日期
编号
ISO6 520-1 缺欠名称注释
缺欠极限值
ISO10042-D
原因分析预防措施
100 裂纹——不允许1)焊丝、工件不清洁或
有氧化层
2)焊件拘束力太大
3)热输入过大,烧损合
金元素
4)焊丝与母材不匹配
5)母材裂纹倾向大,杂
质含量高
1)加强清理和防氧化
2)正确设计焊接结构
3)减小焊接电流电压
4)选用匹配的焊丝
5)重新挑选适合的母
材
104 弧坑裂纹h=高度或宽度h≤0.4s或0.4a
l≤0.4s或0.4a
1)电流过大
2)收弧过快导致弧坑没
填满
1)减小电流
2)间断起弧灭弧填满
弧坑
2017 表面气孔单个气孔的最大轮廓尺
寸
d≤0.4s或0.4a,
最大3mm
1)焊丝、工件不清洁或
有氧化层
2)气路漏气,水路漏水
3)气体保护气氛不良
4)焊接速度太快
5)电极伸出长度太长,
电弧太长
1)加强清理和防氧化
2)常检查气路和水路,
确保不泄漏
3)严格执行WPS,更
换喷嘴,禁止吹风
4)减慢焊接速度
5)减小电极伸出长度,
和电弧长度
2025 弧坑缩孔——h≤0.4t,最大
3mm
1)电流过大
2)收弧过快导致弧坑没
填满
1)减小电流
2)间断起弧灭弧填满
弧坑
401 未熔合h≤0.1s或0.1a,
最大3mm
1)焊接电流过小,弧长
过长,焊接速度过快
2)间隙过小,钝边过大,
坡口角度过小
3)表面和层间存在氧化
物没有清除
4)焊枪和焊丝倾角不正
确
5)电极烧损,电弧不集
中
1)调节焊接参数,缩
短弧长,减慢焊接数度
2)正确进行焊接接头
和坡口的准备
3)加强焊接前清理和
层间的清理
4)适当增大焊枪倾角,
常见的焊接缺陷及危害
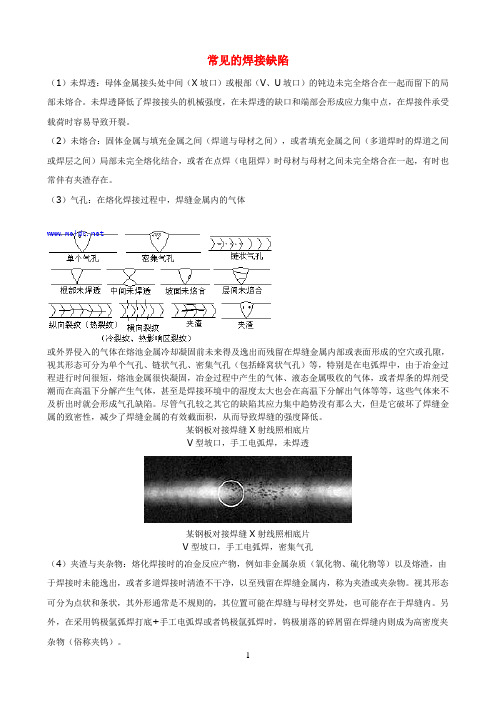
常见的焊接缺陷
(1)未焊透:母体金属接头处中间(X坡口)或根部(V、U坡口)的钝边未完全熔合在一起而留下的局部未熔合。未焊透降低了焊接接头的机械强度,在未焊透的缺口和端部会形成应力集中点,在焊接件承受载荷时容易导致开裂。
(2)未熔合:固体金属与填充金属之间(焊道与母材之间),或者填充金属之间(多道焊时的焊道之间或焊层之间)局部未完全熔化结合,或者在点焊(电阻焊)时母材与母材之间未完全熔合在一起,有时也常伴有夹渣存在。
(3)气孔:在熔化焊接过程中,焊缝金属内的气体
或外界侵入的气体在熔池金属冷却凝固前未来得及逸出而残留在焊缝金属内部或表面形成的空穴或孔隙,视其形态可分为单个气孔、链状气孔、密集气孔(包括蜂窝状气孔)等,特别是在电弧焊中,由于冶金过程进行时间很短,熔池金属很快凝固,冶金过程中产生的气体、液态金属吸收的气体,或者焊条的焊剂受潮而在高温下分解产生气体,甚至是焊接环境中的湿度太大也会在高温下分解出气体等等,这些气体来不及析出时就会形成气孔缺陷。尽管气孔较之其它的缺陷其应力集中趋势没有那么大,但是它破坏了焊缝金属的致密性,减少了焊缝金属的有效截面积,从而导致焊缝的强度降低。
某钢板对接焊缝X射线照相底片
V型坡口,手工电弧焊,未焊透
某钢板对接焊缝X射线照相底片
V型坡口,手工电弧焊,密集气孔
(4)夹渣与夹杂物:熔化焊接时的冶金反应产物,例如非金属杂质(氧化物、硫化物等)以及熔渣,由于焊接时未能逸出,或者多道焊接时清渣不干净,以至残留在焊缝金属内,称为夹渣或夹杂物。视其形态可分为点状和条状,其外形通常是不规则的,其位置可能在焊缝与母材交界处,也可能存在于焊缝内。另外,在采用钨极氩弧焊打底+手工电弧焊或者钨极氩弧焊时,钨极崩落的碎屑留在焊缝内则成为高密度夹杂物(俗称夹钨)。
- 1、下载文档前请自行甄别文档内容的完整性,平台不提供额外的编辑、内容补充、找答案等附加服务。
- 2、"仅部分预览"的文档,不可在线预览部分如存在完整性等问题,可反馈申请退款(可完整预览的文档不适用该条件!)。
- 3、如文档侵犯您的权益,请联系客服反馈,我们会尽快为您处理(人工客服工作时间:9:00-18:30)。
13、 环境温湿度、风速达不到焊接要求;
14、 氩气流量失控:
15、 定位焊点的影响:定位焊后,焊点两端修磨不到位,出现悬空焊缝。
16、 水冷焊矩出现故障
1、 加强气体保护效果
2、 工件和焊丝表面焊前必须严格的清理,去除工件表面的氧化膜、油脂、水分和漆等杂质,露出金属光泽。同时对焊丝表面的油脂、铁锈也要用砂纸进行打磨直到露出金属光泽,再用丙酮擦拭之。。
缺陷
产生原因
防止措施
夹钨
1、 钨极直接接触焊件引弧
2、 钨电极熔化
1、 采用高频振荡器或高压脉冲发生器引弧
2、 减小焊接电流或增大钨电极直径,旋转钨电极夹头和减小钨电极长度
3、 调换有裂纹或撕裂的钨电极
4、 加强焊工基本技能的培训
5、 正确处理钨丝的打磨角度。
6、 选择质量好的钨棒做电极。
气体保护
效果差
17、 定位焊焊缝两端修磨成缓坡形,将搭焊部分修磨完。
咬边
1、 焊接工艺参数不正确,操作技术不正确造成的,如焊接电流大,电弧电压高,焊接速度太快
2、 焊接停留时间不足
3、 焊枪倾角不恰当
4、 焊机轨道不平等原因
1、 选择适当的焊接电流、电压和焊接速度
2、 加强焊工基本技能培训。
3、严格按焊接工艺要求,正确选择焊接电流。
6、 增加送丝速度
7、 封底焊清根要彻底,
错边
1、 装配质量差
2、 热输入量大
1、 施焊加强装配质量检查,严把装配质量关,控制合理的错边量,采取适当调整措施
2、 选择适当的焊接工艺参数和焊接速度,利用刚性夹持的方法予以控制
焊接坍塌
悬空施焊
在背面用垫板(钢制、铝制、铜制或石墨制)托住液态金属
5、 弧长过长
6、 钨电极端头未磨好
1、 做好焊前清理工作
2、 加宽坡口,缩短弧长
3、 去除污染部分
4、 使用正确尺寸的钨电极及夹头
5、 调整喷嘴距离
6、 重新磨制钨极端圆锥角大小
钨极损耗过剧
1、 气保护不好,钨电极氧化
2、 反极性连接,枪与焊机极性接反
3、 夹头过热
4、 钨电极直径过小
5、 停焊时钨电极被氧化
氢、氮、空气、水气等有害气体污染,氩气纯度不高
1、采用纯度为99.99%(体积分数)的氩气
2、有足够的提前送气和滞后停气时间
3、正确连接气管和水管,不可混淆
4、做好焊前清理工作
5、正确选择保护气体流量、喷嘴尺寸、电极伸出长度等
电弧不稳
1、 焊件上有油污
2、 接头坡口太窄
3、 钨电极污染
4、 钨电极直径过大
2、 正确选用焊接参数(如焊接电流、焊接速度、对接间隙)
3、 加强焊工基本技能的培训,消除根部未熔合缺陷产生。
4、正确处理钨丝的打磨角度和焊接停留时间。
5、增加送丝速度和焊接电压,减小焊丝伸出长度
6、减小焊接表面的不平度,提高行走速度
7、坡口边缘有一定不平度时,应增加停留时间,减小行走速度
8、 坡口角度应足够大,利于坡口底部完全熔合
1、 电流密度过大,导致焊丝熔断
2、 钨电极尖端烧损造成的
3、 多层焊时,每层焊道间的熔渣未清除干净, 焊接电流过小, 焊接速度过快; 焊道成型不良; 轨道设定不当
4、 焊缝边缘有氧割或碳弧气刨残留的熔渣;
5、 坡口角度或焊接电流太小, 或焊接速度过快。封底时, 焊丝偏离焊缝中心, 也易形成夹渣。
1、 焊前修磨钨电极时端部不能太尖,以防钨电极烧损
2、 加强焊接过程的层道清理,每层应认真清除熔渣
3、 控制焊接电流, 选用合适的焊接电流和焊接速度;
4、 严格控制焊丝质量, 改善焊道成型;
5、 目镜不要太暗。
6、 加强焊工基本技能的培训,控制铁水与熔渣分离
7、 。焊接接地线应该在工件中合理接地,控制电弧偏吹。
8、 加强组对安装质量 ,正确选取坡口尺寸, 认真清理坡口边缘,
4、采用较低的行走速度
5、降低焊接电压
6、减小送丝速度
7、 增加弧坑边缘停留时间
8、 改变焊枪角度,利用电弧力填充金属
9、 焊机轨道要平整。
焊瘤
操作不当或焊接规范不当,如焊接电流过小,而立焊、横焊时电流过大,焊接速度太慢,电弧过长
调整并选择合适的焊接工艺参数
凹坑
1、焊接电流过大;
2、焊接间隙过大;
3、填充金属量不足;
9、 封底焊清根不彻底
1、 加强装配质量检查,严把装配质量关,控制合理的错边量,保证装配间隙;
2、 认真操作;正确选用焊接参数(如焊接电流、焊接速度、对接间隙;
3、 加强坡口质量检查,清理坡口污物及焊道(层) 与焊道(层) 的夹渣。
4、 加强焊工基本技能的培训。
5、 使用合适规格的焊材,正确处理钨丝的打磨角度。
3、 增加送丝速度
未熔合
1、 多层焊时, 层间和坡口侧壁渣清理不干净
2、 焊接工艺不恰当,焊接电流偏小,电弧过长,焊接线能量不足,焊接行走速度过大
3、 焊接区表面不清洁
4、 焊缝弧坑太大
5、 焊接接头设计不恰当
6、 焊件装配间隙太小等。
7、 电弧偏在坡口一边
1、 认真操作,注意层间修整,清理坡口污物及焊道(层) 与焊道(层) 的夹渣。
9、 封底焊清根要彻底,
未焊透
1、 装配间隙过小;
2、 焊接工艺不恰当,焊接电流过小, 电弧电压偏低, 焊接速度过大; 焊接电弧偏吹现象;
3、 送丝速度过小
4、 焊接操作不当,
5、 接头设计不恰当
6、 焊件坡口表面氧化膜、油污等没有清除干净,
7、 焊接时该处流入熔渣妨碍了金属之间的熔合
8、 电弧偏在坡口一边
1、 清理喷嘴,缩短喷嘴距离,适当增加氩气流量
2、 增大钨电极直径或改为正接法
3、 磨光钨电极,调换夹头,增大夹头直径
4、 调换大直径钨电极
5、 增加滞后停气时间,不少于1s/10A
6、 更改焊枪与焊机输出的连接
焊缝微观组织粗大
电流小,焊接速度慢,高温停留时间长,促使晶粒长大
适当调整电流和焊接速度
夹杂物
3、 氩气纯度应符合要求,氩气瓶的内压力不能过低,氩气流量必须合适,避免出现紊流,要保证气路通畅,不得有堵漏现象发生,防止保护气体送给中断;
4、 喷嘴直径应适当,并符合要求。喷嘴内壁污垢必须清除干净。
5、 钨极伸出长度不宜过大或过小
6、 提前送气和滞后关气
7、 加强操作人员的培训,提高操作技能,基本功应过硬等
9、 封底焊渣应彻底清除,要注意防止焊偏。
裂纹
1、 焊件或焊接材料选择不当;
2、 熔深与熔宽比过大;
3、 ห้องสมุดไป่ตู้头设计不恰当,焊接应力大,接头拘束应力高;
4、 焊道太小
5、 焊接热量减小
6、 焊缝热影响区硬化
7、 焊接残余应力过大
8、 氢脆
1、加强气体保护效果。
2、控制焊缝形状,避免深而宽的焊缝; 改善应力状态。
气孔
1、 焊前清理不到位,工件和焊丝表面质量差。有油污、铁锈和水分,
2、 氩气纯度、气体流量不合适、气路不通畅,保护区受到破坏,导致焊接过程中气体保护效果不好,
3、 喷嘴直径不适当
4、 钨极伸出长度不合适,过大使保护效果变差,过小会阻挡焊工视线,钨极与焊丝易碰撞发生短路使焊接无法进行。
5、 焊接速度过快,导致气体保护效果变差
4、熄弧时间过短;
5、焊接突然中断
1、正确选择焊接电流和焊接速度,
2、控制焊缝组装间隙均匀
3、适当加快填充金属的添加量。
烧穿
1、焊接过程中温度过高,如坡口形状不良,装配间隙太大,焊接电流太大,焊接速度过慢;
2、操作不当,电弧过长且在焊缝处停留时间太长;
3、接头熔深不恰当
1、减小组对间隙,严格控制装配质量,2、正确选择焊接电流,适当提高焊接速度
6、 引弧处钨极与熔池发生氧化产生气孔,收弧处熔池冷却过快,有害气体来不及溢出。
7、 操作人员的操作技能的不够熟练
8、 焊接电流过大或过小,电源极性不适当, 电弧过长,电弧电压偏高;
9、 引弧方法或接头不良等
10、 焊接参数变化大, 加上结构造成的磁偏吹及对口间隙处空气对流的影响, 使电弧不易保护
11、 焊缝待焊处局部被污染;
13、 选择设备性能稳定的电焊机且标定合格。
14、 按工艺评定要求,控制氩气流量
15、 限制母材及焊接材料的含水量焊丝在清洗之前一定要认真挑选检查其表面质量,不允许存在这些缺陷。清洗后的焊丝要在60~80℃的烘箱内烘干,烘干时间为0.5~2 个小时,随用随取。为避免焊丝清洗后的重复污染。
16、 焊接完成时,保持焊枪位置直到焊缝金属凝固。
8、 适当预热除去水分; 焊前应对焊接材料除湿,采用合适的焊接电流、焊接速度, 焊接速度应尽可能小些。控制焊接电弧的合适长度。
9、 穿堂风较大时,不宜焊接;,一旦由于某种原因出现蜂窝状气孔时,需立即停焊,并用砂轮机打磨
10、 要注意所使用的水冷焊矩是否可靠
11、 加强组对安装质量
12、 按国家标准要求,加强施工环境控制,现场建立合理的施工清洁区。 加强现场通风条件,控制空气潮湿度小于等于90%。
3、调整接头设计,提供足够的焊缝填充金属。
4、克服拘束条件,以减小焊接应力。
5、 减少电弧电压、减小送丝速度或同时进行
6、用含Mn量较高的焊丝
7、采用清洁的焊丝,用干燥的保护气体
8、仔细清理坡口边缘的油污、水份和锈迹, 减少氢的来源;
9、选择合理的焊接工艺参数和线能量, 适当减小焊接速度
10、认真执行工艺规程,控制一定的层间温度等