精益生产 案例
精益生产成功案例
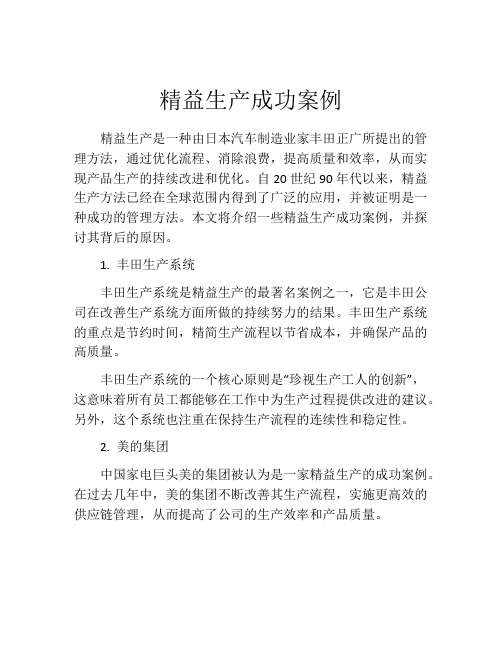
精益生产成功案例精益生产是一种由日本汽车制造业家丰田正广所提出的管理方法,通过优化流程、消除浪费,提高质量和效率,从而实现产品生产的持续改进和优化。
自20世纪90年代以来,精益生产方法已经在全球范围内得到了广泛的应用,并被证明是一种成功的管理方法。
本文将介绍一些精益生产成功案例,并探讨其背后的原因。
1. 丰田生产系统丰田生产系统是精益生产的最著名案例之一,它是丰田公司在改善生产系统方面所做的持续努力的结果。
丰田生产系统的重点是节约时间,精简生产流程以节省成本,并确保产品的高质量。
丰田生产系统的一个核心原则是“珍视生产工人的创新”,这意味着所有员工都能够在工作中为生产过程提供改进的建议。
另外,这个系统也注重在保持生产流程的连续性和稳定性。
2. 美的集团中国家电巨头美的集团被认为是一家精益生产的成功案例。
在过去几年中,美的集团不断改善其生产流程,实施更高效的供应链管理,从而提高了公司的生产效率和产品质量。
美的集团还注重员工的培训和发展,积极实施“知识共享”与“技能传承”等管理模式,使员工能够充分地参与到公司的生产过程中,提高员工的生产效率和质量。
3. GE电气GE电气公司也被视为精益生产管理方法的成功实践者。
GE电气公司致力于优化生产流程,提高生产效率和质量,并减少产品制造过程中的浪费。
GE电气公司采用的精益生产管理方式是“快速反应制造”,即在产品制造过程中遵循快速反应的原则,避免不必要的等待和延迟。
同时,公司还采取了标准化和自动化的生产流程,并专注于对员工进行培训和发展。
以上三个案例展示了在实践精益生产管理方法时所采取的共性策略。
这些成功案例的主要特点包括优化供应链,精简生产流程,采用标准化和自动化的生产技术,培养员工的技能和知识。
另外,这些公司还注重提高产品的质量和关注客户的需求。
总之,精益生产方法已经被广泛证明是一种成功的管理方法。
这些成功案例表明,对于公司而言,采用精益生产方法是提高生产效率和产品质量的一个重要途径,同时,也可以为公司带来更高的效益和利润。
化工企业精益生产案例
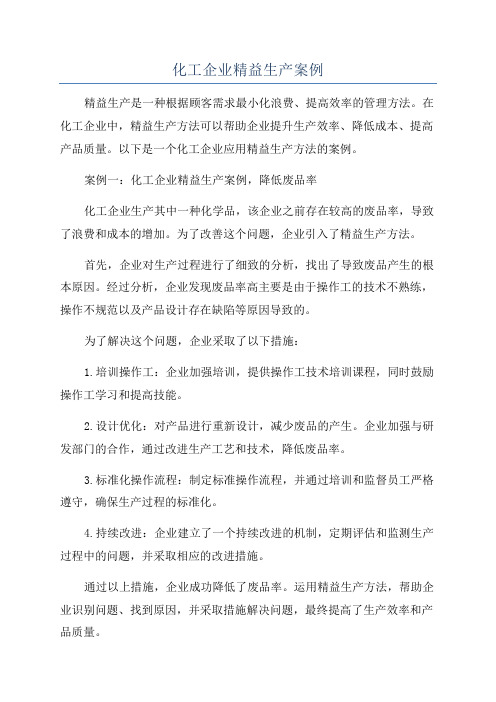
化工企业精益生产案例精益生产是一种根据顾客需求最小化浪费、提高效率的管理方法。
在化工企业中,精益生产方法可以帮助企业提升生产效率、降低成本、提高产品质量。
以下是一个化工企业应用精益生产方法的案例。
案例一:化工企业精益生产案例,降低废品率化工企业生产其中一种化学品,该企业之前存在较高的废品率,导致了浪费和成本的增加。
为了改善这个问题,企业引入了精益生产方法。
首先,企业对生产过程进行了细致的分析,找出了导致废品产生的根本原因。
经过分析,企业发现废品率高主要是由于操作工的技术不熟练,操作不规范以及产品设计存在缺陷等原因导致的。
为了解决这个问题,企业采取了以下措施:1.培训操作工:企业加强培训,提供操作工技术培训课程,同时鼓励操作工学习和提高技能。
2.设计优化:对产品进行重新设计,减少废品的产生。
企业加强与研发部门的合作,通过改进生产工艺和技术,降低废品率。
3.标准化操作流程:制定标准操作流程,并通过培训和监督员工严格遵守,确保生产过程的标准化。
4.持续改进:企业建立了一个持续改进的机制,定期评估和监测生产过程中的问题,并采取相应的改进措施。
通过以上措施,企业成功降低了废品率。
运用精益生产方法,帮助企业识别问题、找到原因,并采取措施解决问题,最终提高了生产效率和产品质量。
案例二:化工企业精益生产案例,提高设备利用率化工企业发现,其生产线的设备利用率较低,导致生产效率不高。
为了提高设备利用率,企业采用了精益生产方法。
首先,企业通过对生产线进行分析,找出导致设备利用率低的原因。
经过分析,企业发现设备故障率高、设备停机时间长以及设备维护不到位等原因导致了设备利用率低的问题。
为了解决这个问题,企业采取了以下措施:1.设备维护:企业加强设备的维护工作,定期检查和保养设备,防止故障的发生。
2.培训操作员:加强员工对设备操作的培训,提高操作员对设备使用和维护的技能。
3.优化生产计划:根据设备的特点和生产需求,优化生产计划,减少设备闲置时间。
精益生产案例
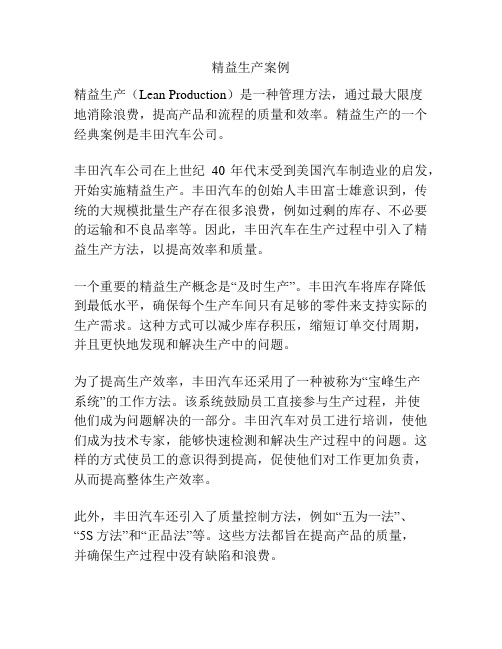
精益生产案例精益生产(Lean Production)是一种管理方法,通过最大限度地消除浪费,提高产品和流程的质量和效率。
精益生产的一个经典案例是丰田汽车公司。
丰田汽车公司在上世纪40年代末受到美国汽车制造业的启发,开始实施精益生产。
丰田汽车的创始人丰田富士雄意识到,传统的大规模批量生产存在很多浪费,例如过剩的库存、不必要的运输和不良品率等。
因此,丰田汽车在生产过程中引入了精益生产方法,以提高效率和质量。
一个重要的精益生产概念是“及时生产”。
丰田汽车将库存降低到最低水平,确保每个生产车间只有足够的零件来支持实际的生产需求。
这种方式可以减少库存积压,缩短订单交付周期,并且更快地发现和解决生产中的问题。
为了提高生产效率,丰田汽车还采用了一种被称为“宝峰生产系统”的工作方法。
该系统鼓励员工直接参与生产过程,并使他们成为问题解决的一部分。
丰田汽车对员工进行培训,使他们成为技术专家,能够快速检测和解决生产过程中的问题。
这样的方式使员工的意识得到提高,促使他们对工作更加负责,从而提高整体生产效率。
此外,丰田汽车还引入了质量控制方法,例如“五为一法”、“5S方法”和“正品法”等。
这些方法都旨在提高产品的质量,并确保生产过程中没有缺陷和浪费。
由于实施了精益生产,丰田汽车取得了巨大的成功。
丰田汽车以其高质量、可靠性和高效率而闻名全球。
丰田车的生产周期非常短,车辆的质量也得到了高度保证。
丰田汽车通过精益生产方法的实施,有效地提高了生产效率,减少了浪费,并提高了产品质量。
这为其他企业提供了一个成功的案例,也促进了全球制造业的转型和发展。
精益生产案例

从去年上半年开始,该公司聘请了专业咨询机构到厂指导,对各 类产品的工艺流程进行梳理,并用秒表计算每一道工序,绘制 成样板线。这之后,无论哪个岗位的员工从事哪道工艺流程, 都可按图索骥,在精益生产模式下完成生产任务。 样板线的成功,坚定了三鸥革新的决心和恒心。去年7月以后, 精益生产在公司2000多名员工中全面实施,并很快完成了流程 再造,取得了显著成效。 在该企业一个生产车间里,公司规定,每天实施精益生产,一日 都不隔断。在线员工只要一按呼叫灯,就会有专职员工前来配 送物料,品质管理员、机修、电工和线长也会视情况上线服务, 使线上员工专注于生产,降低无效劳动,实现生产效率最大化。 如今,与实施精益生产前比较,一年多时间里,三鸥公司库存量 降低了72%,流动资金节省近1600万元。过去,公司里有9个仓 库,现在只需原材料和成品两个仓库,腾出的1万多平方米仓库 变成了生产车间。为了配合样板线建立,提高设备自动化率, 公司还购置了新装备,人均生产效率提高30%。由于生产流程 的优化,节省出200台设备,重新组线15条,降低了设备重复购 买率,每年增加生产能力50万件。 企业创新管理,主要目的是追求利润最大化。三鸥实施精益生产 以来,各种成本降低了,产品利润率增加了5%。
• 以生产现场中发生的质量问题为例:根据公司ISO9001质量管理体系 的要求,当出现质量问题时,由员工填写《工序质量反馈单》,经部 长确认后,由品质人员给出处理意见。当员工按处理意见完成后,还 需要填写《纠正预防措施表》,由品质人员确认。当确认为报废时, 还需要填写《废品报告单》通知财务部和库房后,才能重新下料。在 整个过程中,所造成的工时等损失,并没有单独核算,而是计入正常 工时中。因此,按照这种方法,虽然质量体系得到维持运行,但是质 量成本损失无法计算,更谈不上有的放矢地进行改善了 • 在实施质量成本方法后,品质部把上述表格合并为《工序质量反馈处 理单》一张表格,并重新规划了流程: • 首先由制造人员填写“质量问题”以上的栏目,经部长确认后,交由 品保人员填写“产生原因及解决措施”栏目,并进行质量责任判定, 提出处理意见,交给责任部门及责任人签字,根据不同的处理意见, 进行相应的流程处理:
非常好的精益生产案例值得借鉴

非常好的精益生产案例值得借鉴前言精益生产是一种专注于提高效率和降低浪费的经营管理方法。
通过消除不必要的步骤和资源浪费,精益生产可以帮助企业实现更高的产出和更好的质量,从而获得竞争优势。
本文将介绍一些非常好的精益生产案例,展示出这种方法的实际应用和可行性,以供其他企业借鉴。
案例一:丰田汽车丰田汽车是精益生产的经典案例之一。
丰田公司以“丰田生产方式”(Toyota Production System,TSP)闻名于世。
TSP 的核心思想是通过限制生产速度来提高质量,消除浪费和降低成本。
丰田将员工视为最重要的资源,鼓励员工参与改进流程,并不断学习和提高。
通过实施流程改进和标准化操作,丰田成功地降低了库存水平、缩短了交付周期,并提高了产品的质量。
流程改进丰田汽车通过实施精细的生产计划和精确的生产控制来改进流程。
他们使用所谓的“拉动式生产”(Pull Systems),这意味着生产进程只会在下一阶段需要材料和部件时才会启动,以此保持生产流程的稳定性。
这种方式可以防止过度生产和库存积压,并减少浪费。
标准化操作丰田汽车非常注重标准化操作。
他们制定了详细的作业指导书,确保每位员工都能按照标准程序工作。
通过标准化操作,丰田能够减少错误和变量,并提高整体生产效率。
标准化操作还使得员工之间可以互相替代,以应对人员变动和流程变化。
持续改进丰田汽车秉持着“持续改进”的信念。
他们鼓励员工积极参与改进流程,并通过小改进和创新来不断提高生产效率和质量。
丰田实行所谓的“就地解决问题”(Genchi Genbutsu),即员工应该亲自去现场了解问题并找到解决方案。
这种方法帮助丰田构建了一个持续改进的文化,使得所有员工都在努力寻找问题并付诸行动。
案例二:美国空军美国空军也是一个非常成功的精益生产案例。
空军一直致力于在各个领域实施精益生产,以提高效率、降低成本,并最大限度地满足任务需求。
下面将以飞机维修作业为例,介绍空军如何运用精益生产方法改进维修流程:改进维修流程空军通过改进维修流程来提高效率。
从三个案例看精益生产成效

从三个案例看精益生产成效背景介绍:2009年6月16日,南通醋酸纤维有限公司携手上海卓制商务咨询有限公司,在参加了数次丰田精益研修之旅后,正式启动了精益生产项目。
如今一年时间过去了,精益生产是否取得了成效,生产、管理又发生了哪些变化呢?2009年6月16日,南通醋酸纤维有限公司正式启动精益生产项目,开始构建以精益生产理念、工具、方法为基础,结合南纤生产、管理、文化特点,不断优化制造和管理流程,持续改善、精益求精的流程型制造企业生产方式。
如今一年时间过去了,精益生产是否取得了成效,生产、管理又发生了哪些变化?近日,记者带着这些问题来到了南纤生产一线。
案例一:“顾氏防尾板”“防尾板里有乾坤,持续改进无畏途,功夫不负有心人,兢兢业业树新风。
”这段顺口溜在纺丝生产部广为流传,它所赞颂的精益生产成果是应用在6#纺丝机上的“顾氏防尾板”。
它的设计者叫顾滨,是D班的一名引丝主操工人。
纺丝生产部部长黄建新对记者说:“熟悉引丝岗位情况的员工都知道,一旦引丝上线不佳,前方丝带的丝股极易被丝股尾部弄断,甚至造成吸废丝或断带,每年造成的断头、废丝、断带为数不少。
”在2009年的一次QC课题攻关中,顾滨设计出了简易型防绊丝装置。
他找来废弃的纸板材料、玻璃纸和胶带进行手工制作,在试用过程中起到了一定效果。
在今年D班领衔攻关的《降低6#纺丝机断头率》QC课题中,顾滨作为成员,积极参与破解难题。
“当课题再次碰到如何降低断头率的问题时,我认识到,要想一劳永逸,必须借助新手段、新装置。
”顾滨说。
随后,他主动承担起了新装置的设计任务。
经过几天仔细琢磨,在生产准备值班长白羽飞与机修值班长戴建、维修工刘铭国的协助下,顾滨很快设计出了新装置的示意图,工友们又协助他造好了新装置并进行了两次安装试用,大家发现纺丝机断头事故大幅减少。
为了鼓励顾滨的“发明”,南纤将该装置命名为“顾氏防尾板”。
通过进一步改进群众性活动管理流程、鼓励包括管理人员在内的全体员工提改进建议、每季度评选“金点子奖”等措施,南纤鼓励全员积极参与公司管理,有力推动了班组QC小组活动的深入开展,这成为精益生产取得成效的有力支撑。
精益生产不均衡的例子

精益生产不均衡的例子
1. 在一个汽车制造厂中,由于供应链管理不善,供应商交付零部件的时间经常延误,导致生产线出现空闲和拥堵。
这种不均衡现象会降低生产效率,导致产能浪费。
2. 在一个餐饮行业的快餐连锁店中,由于店内工作人员的分配不合理,导致某些工作岗位人手不足,而其他工作岗位人员过剩,致使顾客在点餐、取餐等环节等待时间过长,而其它区域则显得冷清。
这种不均衡现象会给顾客带来不良的消费体验,并可能导致部分员工工作负荷过重而影响工作效率。
3. 在一个电子产品生产工厂中,由于生产线中某一具体环节的生产能力较低,而其他环节生产能力过剩,导致整个生产过程中的瓶颈环节频繁发生。
这种不均衡现象会导致生产周期延长、生产成本增加,甚至会影响到产品的及时交付。
4. 在一个服装制造企业中,由于设计部门和生产部门之间的沟通不畅,导致设计部门设计出来的样板与生产部门的加工能力不匹配。
这种不均衡现象会导致生产过程中频繁出现加工错误和调整样板的情况,给企业带来额外的时间和资源浪费。
这些例子都是精益生产中因为不均衡而导致生产效率下降、资源浪费等问题的案例。
精益生产案例

精益生产案例引言精益生产是一种通过最大限度地减少浪费,提高生产效率和产品质量的方法。
它始于丰田生产系统,如今已经被广泛应用于各种行业和组织中。
本文将介绍三个精益生产的案例,以展示其在不同领域的应用。
案例一:汽车制造在汽车制造业中,精益生产被广泛用于提高生产效率和降低成本。
丰田汽车公司是精益生产的典型代表之一。
他们采用了精益生产的原则和技术,通过提高生产线的流程效率,使得汽车制造过程更加高效和可持续。
丰田的生产线采用了“单件流水线”模式,每个工人都负责完成整个工作过程,从而减少了不必要的等待和处理时间。
此外,丰田还推崇“质量至上”的原则,通过在每个生产环节中设置严格的质量控制标准,确保产品质量。
另一个值得注意的案例是日本的一个零件制造公司。
该公司通过消除浪费和优化工作流程,成功地提高了生产效率。
他们分析了原本复杂的生产流程,将其简化为一系列简单的步骤,让每个工人都能清楚地知道自己的工作内容和目标。
案例二:医疗服务精益生产同样适用于医疗服务行业。
一个典型的案例是德国某医院的急诊科。
该医院采用了精益生产的原则和工具,通过优化流程和增加资源的使用效率,将就医时间缩短了70%。
在过去,患者在急诊科等待就医时间往往较长。
该医院通过对患者流程进行重新设计,将患者按照病情严重程度进行分类,并在每个分类中设置不同的诊疗团队。
这样,医护人员可以更有效地处理患者,避免了等待时间过长的问题。
此外,该医院还引入了标准化的医疗流程,并充分利用ICT技术,提供了在线预约、电子病历等便捷服务。
这些措施不仅提高了医疗服务的质量,也提高了患者的满意度。
案例三:酒店管理精益生产的原则也可以应用于酒店管理领域。
一个例子是一家高端度假村酒店。
这家酒店通过精益生产的方法,优化了业务流程,提高了客户满意度,并在市场上取得了成功。
首先,酒店管理团队对酒店的工作流程进行了深入分析,并找出了其中的浪费和问题。
然后,他们采取了一系列措施,如优化客房清洁流程、提高服务质量等。
精益生产案例

精益生产案例精益生产(Lean Production)是一种以精益思维为基础的生产管理方法,旨在通过减少浪费、提高效率和质量,实现生产过程的优化。
下面列举10个精益生产案例,以展示其在不同领域的应用和效果。
1. 丰田生产系统(T oyota Production System,简称TPS)是精益生产的典型案例。
TPS通过标准化流程、零库存、及时生产等手段,实现了生产效率和质量的大幅提升。
丰田汽车以其高效、灵活和质量稳定的生产模式成为全球汽车行业的典范。
2. 亚马逊的仓储和物流管理也是一个成功的精益生产案例。
亚马逊通过使用先进的仓储机器人、优化的物流网络和实时数据分析,实现了高效的订单处理和快速的配送服务,提高了客户满意度。
3. 丹麦乐高公司采用精益生产方法,实现了高效的生产和供应链管理。
乐高通过精细的计划、准确的库存控制和灵活的生产调度,保证了产品的高质量和及时交付,同时降低了库存成本。
4. 耐克公司在生产和供应链管理中采用了精益生产的方法。
耐克通过减少生产过程中的浪费、优化供应链和加强与供应商的合作,提高了生产效率和产品质量,同时缩短了产品上市时间。
5. 日本的富士康科技集团(Foxconn)是全球最大的电子制造服务公司之一,也是精益生产的成功案例。
富士康通过引进先进的生产设备、标准化工作流程和持续的员工培训,实现了高效的生产和质量控制,为客户提供高品质的电子产品。
6. 美国的快餐连锁企业麦当劳通过精益生产的方法,实现了订单处理和服务的高效率。
麦当劳通过优化餐厅布局、标准化工作流程和使用先进的点餐系统,提高了订单处理速度和客户满意度。
7. 日本的丸红公司是一家全球知名的物流和供应链管理公司,也是精益生产的典范。
丸红公司通过优化仓储和运输流程、精细的库存管理和实时数据分析,实现了高效的物流运作和准时交货。
8. 德国汽车制造商奔驰公司采用精益生产方法,实现了高质量和高效率的生产。
奔驰通过持续改进生产流程、优化零部件供应和自动化生产线,提高了生产效率和产品质量。
精益生产实施案例
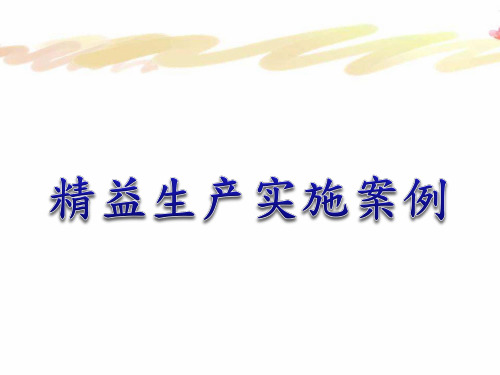
关系
了解设备 功能结构
2、发生源困 难部位对策
1、初期清扫
异常 发现 能力
改善意识 推进方法
缺陷意识 专业眼光
120件产品
假效率
8个人1天 生产
100件产品
真效率
个别效率与整体效率
例 能力需求:100件/H
项目 能力 达成率 奖金 效率
工序1 100件/H
100% 标准产量奖金 个别效率合格
工序2 125件/H
125% 125%奖金 个别效率高
工序3 80件/H
80% 0
个别效率低
工序4 100件/H
80% 0
ISO9001
合理化过程
制度化过程
整理、整顿
物料管制与追溯性
使用整理(要与不要)的手段与整顿(识别系统)的观念 使用物料管制程序,配合识别系统,可达到
可达到
1、控制不合格材料
1、减少库存,增加资金周转率
2、使材料易于追溯
2、先进先出,减少呆废料
3、明确管理责任
3、明确管理责任
整理、整顿
首件检查、现场管理等控制程序及追溯性
自主维护 七阶段
(1)初期清扫 (2)发生源困难部位对策 (3)制定自主保全临时基准 (4)总点检 (5)自主点检 (6)标准化 (7)自主管理
(1)初期清扫
清扫就是点检 点检发现不正常
找出发生源
●垃圾、灰尘、异物等祸害无穷 ●把不正常看为不正常
●活用五官和直觉 ●加油、拧紧很重要
●不正常要改善
明确困难部位
(4)总点检
(5)自主点检
确定总点检项目
点检项目分担
教育培训 实践总点检
精益生产经典案例

精益生产改善案例生产管理追求无库存,就是要彻底改变以超量库存保发货的传统做法,变以造型为中心的推动式生产为以清理为起点的拉动式生产。
实行期量流或一个流生产方式,逐步扩大看板生产品种,造型生产线实行柔性生产,生产作业计划和生产统计应用计算机管理,大幅度地压缩工序、在制品和成品库存,最大限度地降低资金占用,提高生产组织管理水平。
质量管理追求无缺陷,就是要不断提高质量管理和产品质量水平。
质量管理要从“全面质量管理”转向“零缺点管理”,进一步减少不良损失,用精益思想研究和实施质量改进和攻关,提高产品的工艺水平。
落实质量责任制,严格厂内质量评审,严肃工艺纪律,使每个环节、每道工序、每名职工都切实做到精心操作,严格把关,确保产品内在质量和表面质量达到优质品标准。
设备管理追求无停台,就是要提高设备的可动率和开动率,提高工装的工艺水平和使用寿命。
要坚持以生产现场为中心,抓好现场巡检,现场维修,实行设备封闭管理。
工装采取快速换模方法,满足小批量多品种生产的需求。
要通过采用一系列有效措施,不断提高设备工装的技术状态,为保证生产顺利进行和生产优质产品提供可靠的必要条件。
成本管理追求无浪费,就是要狠抓投入产出管理,做到少投入,多产出,优质低耗,降低成本。
深入开展三级经济核算,抓好产品收到率、原材料投入、成品产出率、清理合格率等环节的考核。
要整顿库房,对原材料、产成品、备品、备件等重新制定最高最低储备限额,做到用最低的储备满足生产的需要,大幅度地降低消耗,减少浪费,活化资金,降低产品成本。
优化生产,就是全厂每个生产环节都要达到整体优化标准,建立起以车间主任为首,以生产工人为主体,以生产现场为中心的现场“三为”管理机制。
实施生产要素一体化管理,强化现场“5S”管理和定置管理,现场工位器具标准化、改善生产现场环境,提高现场文明生产水平,使生产要素达到最佳状态。
优质服务,就是要强化科室为一线,后方为前方服务。
职能科室要切实转变工作作风,提高工作质量、服务质量和工作效率,充分发挥指导服务的职能。
精益生产成功案例

精益生产成功案例精益生产是一种管理理念和方法,旨在通过消除浪费,提高生产效率和品质,实现持续的改进和提升。
下面我们将介绍一些精益生产的成功案例。
1.丰田生产系统(TPS):丰田汽车公司是精益生产的开创者。
TPS主要关注生产过程中的浪费和瑕疵,并通过“Just-in-Time”(即时生产)和“Jidoka”(自动停工)的原则,实现了高效的生产和优质的产品。
TPS的成功在于其对员工参与和持续改进的鼓励,以及对质量问题的立即回应。
2.通用电气:通用电气公司采用精益生产理念,优化了其生产流程和供应链管理。
通过分析和优化整个生产过程中的活动和环节,通用电气成功地减少了废品、库存和停工时间。
精益生产的应用帮助通用电气实现了高效生产和投资回报,同时提高了产品质量和客户满意度。
3.美国电子零件制造公司(AMEC):AMEC是一家为全球电子制造企业提供电子零件生产和组装服务的公司。
AMEC采用了精益生产的原则,在生产流程中消除了多余的步骤和浪费。
该公司通过提高生产效率和质量,降低成本和交货时间,有效提升了其竞争力。
AMEC还鼓励员工积极参与,提供培训和奖励机制,以促进持续改进和创新。
4.日本曙光灯泡公司:日本曙光灯泡公司是一家生产灯泡和光源产品的公司。
该公司采用精益生产的原则,通过持续改进和创新,实现了生产效率的提高和成本的降低。
曙光灯泡公司注重员工的培训和参与,鼓励他们提出改进建议,并将其纳入生产流程中,以实现更好的效果。
通过精益生产的应用,曙光灯泡公司成功地提高了生产效率和产品质量,同时降低了生产成本。
5.伊顿公司:伊顿公司是一家全球性的动力管理企业,采用精益生产的原则优化了其生产和供应链管理。
伊顿通过减少库存、提高生产效率和质量,实现了较高的客户满意度和市场份额。
该公司还通过精益思维培养了员工的持续改进意识和能力,并鼓励他们参与决策和问题解决过程。
以上是一些成功应用精益生产的案例,这些企业通过消除浪费、提高效率和质量,实现了更高水平的竞争力和持续的发展。
精益生产经典案例

精益生产经典案例
精益生产是一种通过消除浪费、提高效率和质量的管理方法,它在全球范围内得到了广泛的应用。
下面我们将介绍一些精益生产的经典案例,希望能够给大家带来一些启发和思考。
第一个案例是丰田生产系统。
丰田生产系统是精益生产的典范,它通过精益的管理理念和方法,实现了高效率、高质量和低成本的生产。
丰田生产系统强调的是对员工的尊重和信任,鼓励员工参与持续改进和创新,从而实现了生产过程的精益化。
第二个案例是通用电气公司的精益生产实践。
通用电气公司在生产过程中采用了精益生产的方法,通过价值流映射和精益工具的运用,实现了生产效率的提高和浪费的减少。
同时,通用电气公司还注重员工的培训和激励,使员工能够更好地参与精益生产的实践和改进。
第三个案例是福特汽车公司的精益生产实践。
福特汽车公司在生产过程中引入了精益生产的理念和方法,通过价值流分析和持续改进,实现了生产效率和质量的提升。
福特汽车公司还注重产品的标准化和流程的优化,从而降低了生产成本和提高了产品的竞争力。
以上这些案例都充分展现了精益生产的优势和价值,它不仅可以帮助企业提高生产效率和质量,还可以促进员工的参与和团队的协作。
希望这些经典案例能够给大家带来一些启发,促使更多的企业和组织能够引入精益生产的理念和方法,实现持续改进和可持续发展。
精益生产经典案例

精益生产改善案例生产管理追求无库存,就是要彻底改变以超量库存保发货的传统做法,变以造型为中心的推动式生产为以清理为起点的拉动式生产。
实行期量流或一个流生产方式,逐步扩大看板生产品种,造型生产线实行柔性生产,生产作业计划和生产统计应用计算机管理,大幅度地压缩工序、在制品和成品库存,最大限度地降低资金占用,提高生产组织管理水平。
质量管理追求无缺陷,就是要不断提高质量管理和产品质量水平。
质量管理要从“全面质量管理”转向“零缺点管理”,进一步减少不良损失,用精益思想研究和实施质量改进和攻关,提高产品的工艺水平。
落实质量责任制,严格厂内质量评审,严肃工艺纪律,使每个环节、每道工序、每名职工都切实做到精心操作,严格把关,确保产品内在质量和表面质量达到优质品标准。
设备管理追求无停台,就是要提高设备的可动率和开动率,提高工装的工艺水平和使用寿命。
要坚持以生产现场为中心,抓好现场巡检,现场维修,实行设备封闭管理。
工装采取快速换模方法,满足小批量多品种生产的需求。
要通过采用一系列有效措施,不断提高设备工装的技术状态,为保证生产顺利进行和生产优质产品提供可靠的必要条件。
成本管理追求无浪费,就是要狠抓投入产出管理,做到少投入,多产出,优质低耗,降低成本。
深入开展三级经济核算,抓好产品收到率、原材料投入、成品产出率、清理合格率等环节的考核。
要整顿库房,对原材料、产成品、备品、备件等重新制定最高最低储备限额,做到用最低的储备满足生产的需要,大幅度地降低消耗,减少浪费,活化资金,降低产品成本。
优化生产,就是全厂每个生产环节都要达到整体优化标准,建立起以车间主任为首,以生产工人为主体,以生产现场为中心的现场“三为”管理机制。
实施生产要素一体化管理,强化现场“5S”管理和定置管理,现场工位器具标准化、改善生产现场环境,提高现场文明生产水平,使生产要素达到最佳状态。
优质服务,就是要强化科室为一线,后方为前方服务。
职能科室要切实转变工作作风,提高工作质量、服务质量和工作效率,充分发挥指导服务的职能。
5个案例,秒懂精益生产精髓

Mindset & Innovation40网印工业Screen Printing Industry2020.05理念与新知精益生产,创造性地解决了适应市场多品种、少批量产品需求带来的切换和浪费问题,被称为是当前工业界最佳的一种生产组织体系和方式。
在疫情突发与经济下滑的形势下,印刷企业更应该向管理要效益,组织精益生产,提高劳动利用率,达到降低成本、缩短生产周期和改善产品质量的目的。
精益生产的优势体现在日常工作中的点点滴滴,下面分享5个经典案例,希望能给大家带来启示。
自动化与防呆防错 一个小改善的大效果有一家生产复印机的工厂,他们的复印机里面有一个小风扇,这个小风扇非常重要,一旦装反了,就会导致机械损坏。
但由于是流水线作业,操作工在装配时,由于疲劳、遗忘等多种原因,可能会出错。
主管就要求操作工装好后要进行检查,用手摸一下,试下风向。
但是每天生产数千台复印机,操作工人可能就会产生错觉,有风?没风?不开心了,走神了,总之还是会产生装反的现象。
后来,在复印机旁边装了一个小风车,如果装配正确就会有风,风车会转,因此只要风车会转,装配就是完好的,否则,就是错误的。
因此,这家公司复印机的生产合格率就大大提高了。
强化管理之——目视化的改善某企业有一个开放式的大办公室,有200人在一起办公。
由于管理不到位,经常发生办公室的灯、空调没有关的现象。
最近,公司高层也知道了此事,指示行政部必须强化管理,尽快解决此问题。
于是行政部想了许多办法,如:出台制度、人走灯灭、保安检查、领导值班检查、进行处罚、公告等。
一开始还能起到一定作用,但时间一长,由于监督不到位,老问题还是继续发生,制度落实不好。
其实,制度固然重要,但不能迷信制度。
这属于无意识犯错,无意识犯错是不可以用制度来约束的。
管理很重要,但员工的自主管理更重要。
5个案例,秒懂精益生产精髓Mindset & Innovation 41网印工业Screen Printing Industry2020.05理念与新知一个公司通过努力也想出了好办法:他们在公司的门上设计了一个卡通画,只要一锁门,就会有一个卡通画跳出来,问“你关灯了吗?”通过这种人性化的管理和提醒,忘记关灯和空调的现象终于杜绝了。
精益生产防错法案例
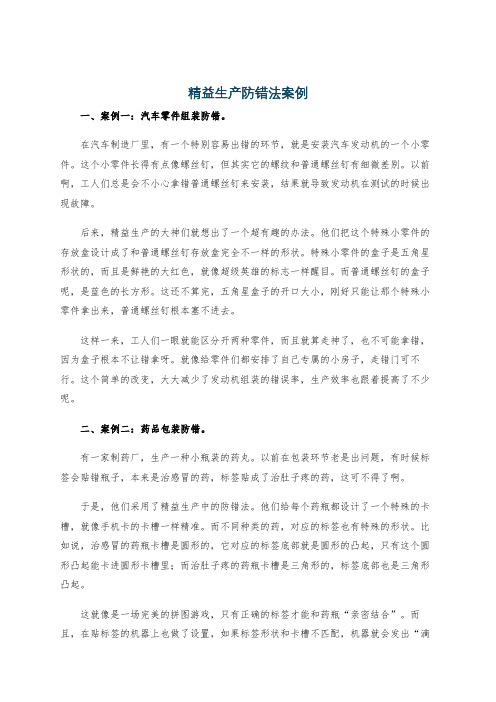
精益生产防错法案例一、案例一:汽车零件组装防错。
在汽车制造厂里,有一个特别容易出错的环节,就是安装汽车发动机的一个小零件。
这个小零件长得有点像螺丝钉,但其实它的螺纹和普通螺丝钉有细微差别。
以前啊,工人们总是会不小心拿错普通螺丝钉来安装,结果就导致发动机在测试的时候出现故障。
后来,精益生产的大神们就想出了一个超有趣的办法。
他们把这个特殊小零件的存放盒设计成了和普通螺丝钉存放盒完全不一样的形状。
特殊小零件的盒子是五角星形状的,而且是鲜艳的大红色,就像超级英雄的标志一样醒目。
而普通螺丝钉的盒子呢,是蓝色的长方形。
这还不算完,五角星盒子的开口大小,刚好只能让那个特殊小零件拿出来,普通螺丝钉根本塞不进去。
这样一来,工人们一眼就能区分开两种零件,而且就算走神了,也不可能拿错,因为盒子根本不让错拿呀。
就像给零件们都安排了自己专属的小房子,走错门可不行。
这个简单的改变,大大减少了发动机组装的错误率,生产效率也跟着提高了不少呢。
二、案例二:药品包装防错。
有一家制药厂,生产一种小瓶装的药丸。
以前在包装环节老是出问题,有时候标签会贴错瓶子,本来是治感冒的药,标签贴成了治肚子疼的药,这可不得了啊。
于是,他们采用了精益生产中的防错法。
他们给每个药瓶都设计了一个特殊的卡槽,就像手机卡的卡槽一样精准。
而不同种类的药,对应的标签也有特殊的形状。
比如说,治感冒的药瓶卡槽是圆形的,它对应的标签底部就是圆形的凸起,只有这个圆形凸起能卡进圆形卡槽里;而治肚子疼的药瓶卡槽是三角形的,标签底部也是三角形凸起。
这就像是一场完美的拼图游戏,只有正确的标签才能和药瓶“亲密结合”。
而且,在贴标签的机器上也做了设置,如果标签形状和卡槽不匹配,机器就会发出“滴滴滴”的警报声,就像在大声喊“错啦,错啦”。
自从采用了这个方法,药品包装贴错标签的错误几乎就没有再出现过了。
三、案例三:电子厂电路板焊接防错。
在电子厂里面,电路板焊接是个技术活,但也很容易出错。
精益生产管理的成功案例

精益生产管理的成功案例精益生产管理(Lean Production Management)促使企业实现高效运营、降低成本并提升质量。
下面将介绍三个成功应用精益生产管理的案例。
案例一:丰田汽车公司丰田汽车公司是一个广为人知的精益生产管理的成功案例。
该公司在汽车制造业中引入了丰田生产系统(Toyota Production System),凭借其卓越的精益管理理念,有效地提高了效率、质量和利润。
丰田生产系统强调持续改进和减少浪费。
通过精确计划、高效布局和员工参与决策等措施,丰田成功地降低了库存、提高了生产灵活性,同时还能满足客户需求。
案例二:波音公司波音公司是另一个成功应用精益生产管理的案例。
该航空制造企业采用了精益管理的方法来提高生产效率、降低成本并提供高质量的产品。
波音公司运用精益生产管理来优化供应链、改进生产流程、减少制造时间和提高资源利用率。
通过精细制定的生产计划、物料缩短流程和追求卓越质量的理念,波音不断提高产品竞争力,为客户提供满意的解决方案。
案例三:日本服装公司日本一些服装公司通过精益生产管理的方式,实现了生产过程的高效、卓越的质量和最小化的浪费。
这些公司主要通过以下措施来提升业绩。
首先,改善生产流程。
服装企业会合理安排生产线,确保各个生产环节之间的流程顺畅,并减少传统大量存货。
其次,强调员工培训和参与,使每个人都能理解自己的角色和责任,并为精益生产目标贡献力量。
再次,注重质量管理。
这些企业通过引入严格的质量控制措施,确保产品达到最高标准。
结论:以上三个案例展示了精益生产管理在不同行业中的成功应用。
丰田汽车公司、波音公司和日本服装公司通过实施精益管理的策略,优化了生产流程、提高了质量、降低了成本,进而实现了业务的卓越表现。
这些成功案例表明,精益生产管理已经成为许多企业提高竞争力和持续发展的重要工具。
精益提案案例大全
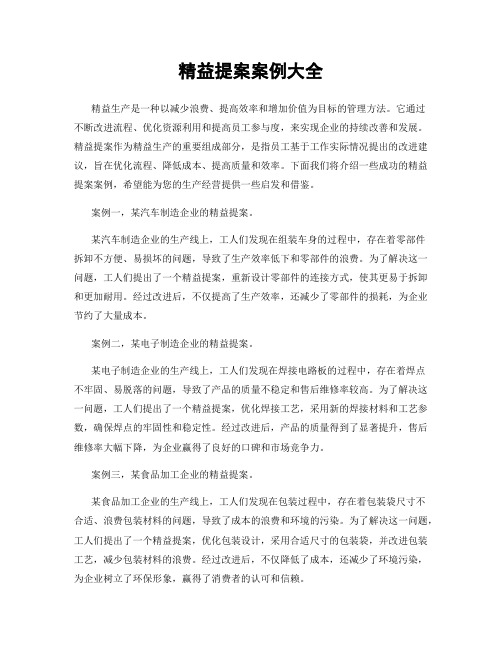
精益提案案例大全精益生产是一种以减少浪费、提高效率和增加价值为目标的管理方法。
它通过不断改进流程、优化资源利用和提高员工参与度,来实现企业的持续改善和发展。
精益提案作为精益生产的重要组成部分,是指员工基于工作实际情况提出的改进建议,旨在优化流程、降低成本、提高质量和效率。
下面我们将介绍一些成功的精益提案案例,希望能为您的生产经营提供一些启发和借鉴。
案例一,某汽车制造企业的精益提案。
某汽车制造企业的生产线上,工人们发现在组装车身的过程中,存在着零部件拆卸不方便、易损坏的问题,导致了生产效率低下和零部件的浪费。
为了解决这一问题,工人们提出了一个精益提案,重新设计零部件的连接方式,使其更易于拆卸和更加耐用。
经过改进后,不仅提高了生产效率,还减少了零部件的损耗,为企业节约了大量成本。
案例二,某电子制造企业的精益提案。
某电子制造企业的生产线上,工人们发现在焊接电路板的过程中,存在着焊点不牢固、易脱落的问题,导致了产品的质量不稳定和售后维修率较高。
为了解决这一问题,工人们提出了一个精益提案,优化焊接工艺,采用新的焊接材料和工艺参数,确保焊点的牢固性和稳定性。
经过改进后,产品的质量得到了显著提升,售后维修率大幅下降,为企业赢得了良好的口碑和市场竞争力。
案例三,某食品加工企业的精益提案。
某食品加工企业的生产线上,工人们发现在包装过程中,存在着包装袋尺寸不合适、浪费包装材料的问题,导致了成本的浪费和环境的污染。
为了解决这一问题,工人们提出了一个精益提案,优化包装设计,采用合适尺寸的包装袋,并改进包装工艺,减少包装材料的浪费。
经过改进后,不仅降低了成本,还减少了环境污染,为企业树立了环保形象,赢得了消费者的认可和信赖。
以上案例充分展示了精益提案在企业生产中的重要作用,通过员工的智慧和创新,不断改进和优化生产流程,实现了降本增效、提质增效的目标。
希望这些案例能给您带来一些启发,激发您的创造力和改进意识,为企业的精益生产注入新的活力和动力。
精益生产成功案例

精益生产网站案例1一家专业生产汽车刹车盘(鼓)美资公司,在中国设有 2 家工厂,产品几乎覆盖了美国、欧洲、日本和韩国的所有车型。
同时水泵的可提供型号达到了 500 种,主要是满足上面这几个国家主流车型的需要。
同时,借助市场调研和与一些客户的紧密合作,该公司 -的产品型号数一直在稳定地伴随市场的需要而增加。
1 、成品库存:目视化管理已经有意识的应用,问题在于目前存货量水平较高,约占年销售收入的近 15 % , 增加了制造成本(储存、运输及管理)及呆滞库存的风险,尤为重要的是,库存给制造过程中的种种浪费(如等待、延误等)。
2 、生产线及半成品管理:部分数控机床一人三机操作,减少了人员等待的和搬运距离,说明公司具备了一定的精益思想;但更多工序人员、机器、材料都存在不同的等待,同时加工生产和周转批量较大,造成较长的生产周期,尤其是存在瓶颈工序,该工序在制品( WIP )存量较多,导致生产流程不够顺畅,制约了生产效率。
3 、现场管理:装配线、毛坯铸造、热处理车间现场管理和目视控制的改善机会较显著,突出表现在:- 装配线产品追溯性标示过程复杂,造成冗杂处理的浪费;手工打标记等不仅劳动强度大,而且容易造成疲劳错误。
- 装配工位的作业方法、时间分析以及人机工程(材料传送和取放过程)等方面有待进一步完善。
- 铸造车间产品种类和生产区域无标示,将导致分检的时间损失及混淆。
- 铸造现场、热处理车间 5S 尚有较大改进空间,尤其是整顿、清洁和进一步的标准化工作。
4 、其他影响:同时,制造方式的变革也暴露出在原来的成批生产方式中隐藏至深的大量问题,如设备故障多发,维修速度慢以及缺乏保养;设备换模具时间长;刀具整备时间长;作业员技能单一等。
改善效果:经过三个月的维持与改善,同时辅以培训 , 一些主要问题得到明显的改善:·在不影响现有产出情况下,较大幅度降低成品库存总量。
总库存量减少了 4 0 % 。
·按照用户的需求节拍,进行小批量多频次的生产和物料周转(目标:单件流),缩短生产周期。
- 1、下载文档前请自行甄别文档内容的完整性,平台不提供额外的编辑、内容补充、找答案等附加服务。
- 2、"仅部分预览"的文档,不可在线预览部分如存在完整性等问题,可反馈申请退款(可完整预览的文档不适用该条件!)。
- 3、如文档侵犯您的权益,请联系客服反馈,我们会尽快为您处理(人工客服工作时间:9:00-18:30)。
Our strengths is having had big contracts with many agencys of Vietnam’s government. Now, We are implementing contract with Bien Hoa police deparment to upgrade its computer system with the money upto 3.5 billion Vietnam Dongs. Doing successfully many big contracts like this help us to sign next big contracts
பைடு நூலகம்- 171, 30/04 street, Trung Dung ward, Bien Hoa city,
Dong Nai province.
- Stores:
32 Vo Thi Sau street -Bien Hoa city,
270 Pham Van Thuan street - Bien Hoa city.
province.
After 8 years, we have raised the capital up to 15 billion Vietnam Dong and had three stores: at company, 32 Vo Thi Sau street -Bien Hoa city, 270 Pham Van Thuan street - Bien Hoa city. We have total 56 employees including board of managers, personnel, marketing, accounting, engineering, receiving and delivering department.
Businesses are structured in different ways to
meet different needs. They are individual
proprietorship, limited liability partnership, corporation…
TAN BACH KHOA COMPANY PROFILE
Prepared by: Bui Dinh Thinh Nguyen Anh Tuan Ngo Thi Giang Huong Tran Thi Mai Huong Vo Thi Uyen Date : Apr 21,2011
Head quarter:
althought we pay very small money adverting our product,
just some banner at stores and maintaining our Website.
Through all kinds of our businesses, we get turnover an average of 5.7 billion Vietnam Dongs each years. That number is very small in comparison
Today we talk about limited liability
partnership. Its name is Tan Bach Khoa.
Our company located at number 171, 30/04 street, Trung Dung ward, Bien Hoa city, Dong Nai
We sell many computer products, electronic products, for example: desktop, laptop, network
system equipment, switchboard system equipment,
printer, photocopier, Digital camera, software, computer components. We have created brand name BKC of computer to serve and bring credit to customers. We also provide some services: assembling, maintaining, and repairing all product we sell. The products is sold in local market
the Chief Exercutive officer (CEO) of
our company, I would make some recommendations:
Increase advertisement, and stores Increase customers which are foreign companys and our retail Increase more services for example maintaining
with other company producing other products and
services. But it is impressive in comparison with companys working in computer service in Bien Hoa.
If I were
Infomation technology for other companys (tuan)