高密度三维封装技术_李秀清
三维封装技术创新发展

三维封装技术创新发展(2020年版)先进封测环节将扮演越来越重要的角色。
如何把环环相扣的芯片技术链系统整合到一起,才是未来发展的重心。
有了先进封装技术,与芯片设计和制造紧密配合,半导体世界将会开创一片新天地。
从半导体发展趋势和微电子产品系统层面来看,先进封测环节将扮演越来越重要的角色。
如何把环环相扣的芯片技术链系统整合到一起,才是未来发展的重心。
有了先进封装技术,与芯片设计和制造紧密配合,半导体世界将会开创一片新天地。
现在需要让跑龙套三十年的封装技术走到舞台中央。
日前,厦门大学特聘教授、云天半导体创始人于大全博士在直播节目中指出,随着摩尔定律发展趋缓,通过先进封装技术来满足系统微型化、多功能化成为集成电路产业发展的新的引擎。
在人工智能、自动驾驶、5G网络、物联网等新兴产业的加持下,使得三维(3D)集成先进封装的需求越来越强烈,发展迅猛。
一、先进封装发展背景封装技术伴随集成电路发明应运而生,主要功能是完成电源分配、信号分配、散热和保护。
伴随着芯片技术的发展,封装技术不断革新。
封装互连密度不断提高,封装厚度不断减小,三维封装、系统封装手段不断演进。
随着集成电路应用多元化,智能手机、物联网、汽车电子、高性能计算、5G、人工智能等新兴领域对先进封装提出更高要求,封装技术发展迅速,创新技术不断出现。
于大全博士在分享中也指出,之前由于集成电路技术按照摩尔定律飞速发展,封装技术跟随发展。
高性能芯片需要高性能封装技术。
进入2010年后,中道封装技术出现,例如晶圆级封装(WLP,Wafer Level Package)、硅通孔技术(TSV,Through Silicon Via)、2.5D Interposer、3DIC、Fan-Out 等技术的产业化,极大地提升了先进封装技术水平。
当前,随着摩尔定律趋缓,封装技术重要性凸显,成为电子产品小型化、多功能化、降低功耗,提高带宽的重要手段。
先进封装向着系统集成、高速、高频、三维方向发展。
封装基板技术的发展

封装基板技术的发展封装基板技术是电子元器件制造的关键环节之一,它旨在将电子元器件连接到电路板上,并提供物理支撑和电气连接。
随着电子产品的不断发展和智能化需求的增加,封装基板技术也在不断发展。
以下是封装基板技术的发展所经历的几个重要阶段:1.初期阶段(1960年代-1980年代)封装基板技术起源于20世纪60年代,这个阶段主要采用双面贴片和通孔技术。
双面贴片技术通过在电路板的两面安装元器件,并进行焊接连接来实现电气连接。
通孔技术则是通过铜箔覆盖的孔洞,在两个电路层之间传导信号。
这个时期,封装基板技术主要使用单层板或双层板,功能也相对简单,并且生产周期较长。
2.高密度阶段(1990年代)进入20世纪80年代,随着电子器件越来越小型化,封装基板技术也逐渐发展为多层板和高密度连接技术。
多层板技术允许多个电路层叠放在一起,通过通过通孔或盲孔进行连接。
高密度连接技术则用于增加连接器端子的数目,提高连接器的密度。
这一阶段的封装基板技术大幅提高了电子器件的集成度和性能。
3.超高密度阶段(2000年代)进入21世纪,随着电子产品对小型、高性能、高可靠性的要求日益严格,封装基板技术发展到了超高密度阶段。
这一阶段的关键技术是微细线路、微细通孔和微阵列连接器等。
微细线路技术通过减小线路宽度和间距来实现更高的线路密度。
微细通孔技术则通过缩小通孔径向直径,增加通孔数量来提高连接密度。
微阵列连接器技术则可以实现大量信号和功率的高速连接。
这些技术的应用大大推动了封装基板技术的进一步发展。
4.3D封装阶段(2024年代至今)近年来,随着电子产品对体积更小、性能更强的需求增加,封装基板技术也逐渐发展到3D封装阶段。
3D封装技术通过垂直堆叠多个芯片,提高器件的集成度,并通过封装互连技术实现芯片和封装基板之间更高密度的互连。
目前的主要的3D封装技术有通过硅通孔封装(TSV)和硅基互连(SIP)两种。
这些技术将推动封装基板技术向更高集成度和更高性能的方向发展。
可替代的三维封装方法

可替代的三维封装方法
佚名
【期刊名称】《《军民两用技术与产品》》
【年(卷),期】2006(000)012
【摘要】美国空军实验室(AFRL)和阿肯色州立大学在“合作研发协议”的支持下,联合开发出可替代的三维(3D)封装方法。
三维封装方法是一种连接封装三维硅(Si)晶片的方法,需要将三维硅晶片从上到下垂直连接起来。
此封装方法十分稳定,研究人员已对其结构进行了一系列测试,来验证此方法的可靠性和电学性能。
【总页数】1页(P29)
【正文语种】中文
【中图分类】TB383
【相关文献】
1.版画“三维”展示的不可替代 [J], 陈立新;高国珍;李莉
2.侧面送风冷却LED的热封装方法及其三维数值仿真研究 [J], 马璐;刘静
3.基于三维封装模型的高压芯片封装散热方法研究 [J], 宣慧
4.基于三维封装模型的高压芯片封装散热方法研究 [J], 宣慧
5.煤的工业分析方法灰分的测定——创建快速灰化法可替代方法0.3g煤样灰化法并进行方法的确认 [J], 岳文;刘洋;张进
因版权原因,仅展示原文概要,查看原文内容请购买。
LICVD

Page
12
反应装置
激光辐照硅烷气体 热解 分子(SiH4)时.硅烷分子很容易
热解生成的气构硅 Si(g)在一定温度和压力条件下开 始成核和生长,形成纳米微粒。
特点: 该法具有清洁表面、粒子大小可精确控制、无粘结、 粒度分布均匀等优点,并容易制备出几纳米至几十 纳米的非晶态或晶态纳米微粒。
Page 13
分析评价
合成纳米粒子过程:包括原料处理、原料蒸发、 反应气配制、成核与生长、捕集等过程。
特点:无污染、反应快 、选择性好,易精确 控制;激光能量高度集中,温度梯度大,有利 于成核粒子快速固化;可以制得高纯,超细、 均匀的纳米粒子。 应用:Si, Si3N4, SiC, Fe/C/Si,以及金属氧化物 等纳米粒子。
Page 10
反应装置
激光束照在反应气
体上形成了反应焰,
经反应在火焰中形 成微粒,由氩气携 带进入上方微粒捕
集装置。
Page
11
反应装置
实例:LCVD法制备纳米硅
用连续输出的CO2激光(10.6μm)辅照硅烷气体分子(SiH4) 时,硅烷分子发生热解:
SiH4 Si 2H 2
在反应过程中,Si的成核速率大于1014/cm3,粒子直径 可控制小于1100 nm,且粉体的纯度高。
基本原理
• 激光诱导化学气相反应合成纳米粉末的实验装置: • 包括激光器、反应器、纯化装置、真空系统、气路与控制系统
激光诱导化学气相反应合成纳米粉末的实验系统:1-激光器,2-聚焦透 镜,3-反应器,4-光束截止屏,5-反应器喷嘴,6-混气室,7-质量流量 计,8-压力表,9-稳压器,10-气体调节阀,11-净化器,12-反应气, 13-惰性气体,14-分流器,15-收集器,16-绝对捕集器,17-气阻调节 阀,18-尾气处理器,19-缓冲器,20-真空泵
pcb产业未来发展趋势

pcb产业未来发展趋势PCB产业未来发展趋势引言近年来,随着新兴技术的不断涌现和全球数字化转型的加速,PCB(Printed Circuit Board,印制电路板)产业作为电子产品的重要组成部分,正迎来全新的发展机遇。
本文将从技术发展、市场需求、环保要求等多个方面,探讨PCB产业未来的发展趋势。
一、技术发展趋势1.1 多层、高密度PCB随着电子产品追求小型化和轻量化,多层、高密度PCB得到了越来越广泛的应用。
未来,随着可靠性要求和信号传输速率的提高,多层、高密度PCB将会成为市场的主流趋势。
1.2 HDI(High Density Interconnector)技术HDI技术是指通过使用微细线路、盖孔填充、埋孔、埋板到板连接和脱附连接等创新工艺,实现更高密度、更低成本、更复杂的电路设计。
随着智能手机、平板电脑等高端产品的需求增长,HDI技术将在未来得到更广泛的应用。
1.3 柔性PCB柔性PCB具有高度灵活性和可弯曲性的特点,能够适应不规则布局的电子产品需求。
未来,随着可穿戴设备、可折叠手机等产品的普及,柔性PCB将成为重要的发展趋势。
1.4 小型化和集成化随着元器件的小型化和集成化,未来的PCB设计将更加注重电路板上的空间利用率和线路布局的紧凑性。
高性能、高可靠性的小型化和集成化PCB将成为发展的主要方向。
二、市场需求趋势2.1 5G技术的推广随着全球5G技术的推广,5G通信设备的需求将呈爆发式增长。
而5G通信设备的高频率和高速率要求将进一步推动PCB产业的发展,特别是需要满足更高信号传输要求的高频PCB。
2.2 智能家居与物联网智能家居和物联网的发展将进一步推动PCB产业的需求。
随着智能家居和物联网设备的普及,对较小、较灵活的PCB的需求将进一步增长。
同时,物联网设备的复杂性也将推动PCB产业向更高端、更复杂的方向发展。
2.3 电子汽车的兴起电子汽车作为未来汽车产业的重要发展方向,将对PCB产业带来新的机遇。
高密度电子封装技术研究与优化设计

高密度电子封装技术研究与优化设计随着电子设备的不断发展和进步,电子封装技术也在不断演进。
高密度电子封装技术是电子封装领域的重要研究方向之一,它主要关注如何在有限的空间内尽可能多地集成电子元器件,并保证其稳定性和可靠性。
本文将探讨高密度电子封装技术的研究与优化设计。
一、高密度电子封装技术的研究现状当前,随着电子产品的迅猛发展,人们对电子封装技术的要求也越来越高,特别是对于高密度集成的需求。
因此,高密度电子封装技术的研究正日益受到重视。
目前,该领域的研究主要集中在以下几个方面:1. 新型封装材料的研究:为了实现高密度电子封装,需探索开发新型封装材料,例如高导热性的金属基底、高强度的无机封装材料等。
这些材料的研究可有效提高电子封装的稳定性和可靠性。
2. 纳米材料在封装中的应用:纳米材料具有较高的表面积和特殊的电子性质,可在电子封装中发挥重要作用。
目前,纳米金属、纳米碳材料等广泛应用于高密度电子封装中,以提高电路的导电性和散热性能。
3. 封装工艺的研究:高密度电子封装需要精细的工艺控制和优化设计。
封装工艺研究的关键是如何实现精密的组装和焊接技术,以确保电子元器件的紧凑性和可靠性。
二、高密度电子封装技术的优化设计原则在研究高密度电子封装技术时,有几个关键的优化设计原则需要遵循,以确保高密度电子封装的可靠性和稳定性。
1. 热管理:高密度电子封装技术要求在有限的空间内集成更多的元器件,因此热量管理成为关键。
优化设计应包括散热设计、良好的热传导性能和热障设计等,以确保元器件在高温环境下的稳定工作。
2. 电磁兼容性(EMC):电子封装密度的增加可能会导致电磁干扰和辐射水平的提高。
优化设计应包括屏蔽设计、正确布置和连接电源线和信号线等,以减少电磁干扰,并确保电子封装的稳定性和可靠性。
3. 可靠性测试:在高密度电子封装技术的研究中,可靠性测试是不可或缺的一部分。
优化设计应包括使用合适的可靠性测试方法和评估标准,以确保电子封装的性能和可靠性,并及时发现和解决潜在的问题。
揭开国外先进制造工艺的奥秘:现代制造工艺=主体工序+辅助工序+环节工序

揭开国外先进制造工艺的奥秘:现代制造工艺=主体工序+辅
助工序+环节工序
李治国
【期刊名称】《中国机电工业》
【年(卷),期】1997(000)001
【总页数】2页(P24-25)
【作者】李治国
【作者单位】无
【正文语种】中文
【中图分类】F407.406.2
【相关文献】
1.强化工序间检测是实现现代制造工艺的一项基础工作 [J], 朱正德
2.揭开国外先进制造工艺的奥秘:试论怎样赶上国外先进制造水平 [J], 李治国
3.工序尺寸,工序废品与工序能力 [J], 余光国;何宁
4.应用统计分析软件解决工序质量问题的研究
——以整流管堵漏工序为例 [J], 李娅波;卢盛辉;潘彬彬
5.应用统计分析软件解决工序质量问题的研究——以整流管堵漏工序为例 [J], 李娅波;卢盛辉;潘彬彬
因版权原因,仅展示原文概要,查看原文内容请购买。
高密度三维封装技术_李秀清

图 3 二维封装与三维封装的互连效率比较
在折叠柔性电路中 , 先将裸芯片安装在柔 性材料上 , 然后将其折叠 , 形成三维叠层 , 如 图 4 所示 。 引线键合叠层芯片是一种采用引线键合技 术实现垂直互连的方法。 可直接与 M CM 基板 进行引线键合 。 这种方法是采用引线键合工艺 将叠层芯片与平面 M CM 基板键合在一起的 , 如图 5所示 。也可采用基板与 IC引线键合的方 法。 采用这种方法需要有一母芯片和一子芯片 , 母芯片充当子芯片的基板 , 互连就通过子芯片 与母芯片基板上的焊点相连 , 如图 6所示。 3. 2 叠层 IC之间的区域互连 在区域互连中 , 垂直互连并不与叠层元件
半导体情报
27
线板 ( PW B) 上安装时 , 互连约占系统总功耗 的 10 % ; 如果用 M CM 技术 , 系统功耗可降低 1 /5, 其功耗要比使用 PW B低 8 % ; 若采用三维 封装技术 , 由于缩短了互连长度并减小了寄生 效应 , 则可使系统功耗进一步降低。 2. 6 速度 由于三维封装降低了系统功耗 , 因此在不 增加功耗的情况下 , 三维器件的跃迁速度 (频 率 ) 会更快。 此外 , 三维器件的寄生效应 (电 容和电感 )、 体积与噪声均有所降低 , 跃迁速度 显著提高 , 从而改进了系统的性能。 2. 7 互连效率 使用三维封装结构可为叠层中的中心元件 提供 116个相邻元件 , 而在二维封装中可提供 的相邻元件却仅有 8 个 (图 3)。 因此 , 缩短叠 层的互连长度可降低芯片间的传播延迟。 此外 , 与传统封装技术所用的通孔布线互连相比 , 三 维封装的垂直互连可最大限度地利用互连的效 率。
半导体情报
25
高密度三维封装技术
李秀清
(河北半导体研究所 , 石家庄 050051) 摘要 简要介绍为满足日益增长的低功耗 、 轻重量 、 小体积系统的应用需求而涌现出的 多种裸芯片封装与多芯片叠层封装技术。 详细讨论三维封装的垂直互连工艺 。 主要分析 三维封装技术的硅效率 、 复杂程度、 热处理、 互连密度 、 系统功率与速度等问题 。 关键词 三维封装 垂直互连 裸芯片叠层 多芯片模块叠层
先进的MEMS封装技术

倒装焊技术是90年代发展起来的一种新的芯片 和基板连接技术。所谓倒装焊就是在芯片有源面的 铝压焊块上做凸焊点,然后将芯片倒扣,直接与基 板连接的技术,它能实现圆片级芯片尺寸封装 (W L P - C S P )。正是由于与基板直接相连,倒装 焊实现了封装的小型化、轻便化,可缩小封装后器 件的体积和重量。由于焊球阵列(B G A )的凸点 可以布满整个管芯,所以增加了 I/O 互连密度;由 于“连线”的缩短,引线电感变小、串扰变弱、 信号传输时间缩短等,使电性能得到了提高。因 此,倒装焊技术比引线键合技术更为先进,具有很 大的发展潜力。
考虑到倒装焊技术的一系列优势,可以用这项 技术完成 MEMS 芯片和基板的互连。已经有人用板 上倒装芯片(FCOB)技术封装压力传感器[的结构如图 4 所示。
图2 采用倒装焊封装的微麦克风
3.2 多芯片封装 多芯片封装(M C P )是将 M E M S 芯片和信号
鉴于倒装焊技术本身的一系列优点,它已成为 M E M S 封装中有吸引力的选择。采用倒装焊的 MEMS 封装在国外已经成为一个热点,相当多的大 学与研究所(包括一些微电子公司)已开展这方面 的工作,如针对倒装焊回流过程中焊料表面氧化物 的处理提出了各自的解决方法,还有的公司考虑将 SBB(Stud Bump Bonding)技术应用于 MEMS 封 装等[ 2 ]。
June 2003
Semiconductor Technology Vol.28 No.6 7
专题报道
2.2 外壳要求
因为大多数 MEMS 器件的外壳上需要有非电信 号的通路,所以它不能简单地把 MEMS 芯片密封在 封装体里,必须留有同外界直接相连的通路,用来 传递光、热、力等物理信息。对这种 MEMS 封装, 不同的器件需要不同开口的外壳。除此以外,外壳 材料本身也有要求,像磁敏 M E M S 器件,虽然可 以密封在管壳里,但是它要求外壳必须是非导磁材 料,常见的用铁镍合金作为引线框架的管壳就不能 使用;像微麦克风 M E M S 器件则要求外壳既有开 口,可以接受外界的声音,又能屏蔽电磁干扰信 号,以避免其对微弱的麦克风输出信号的干扰,所 以普通的塑料封装就不适用。
混合封装能实现最佳的电路保护

混合封装能实现最佳的电路保护
Mark.,HW;李秀清
【期刊名称】《半导体情报》
【年(卷),期】1990(000)006
【摘要】混合电路需要一个密封的管壳将电路保护起来,尤其是芯片与布线的混合更是如此。
只要观察一下封装好的混合电路器件便可知道外部封装是总体组装的一个重要组成部分。
据统计,这种封装约占混合电路器件总成本的14%,1990年将增加到16%。
混合封装的作用是安装和保护陶瓷混合电路,即厚膜电路或薄膜电路,以便提供一个密封的环境。
这种封装必须保证散热好、尺寸小以及为下步组装提供可靠的连接方法——通常是焊到一块印刷电路板上。
【总页数】4页(P32-35)
【作者】Mark.,HW;李秀清
【作者单位】不详;不详
【正文语种】中文
【中图分类】TN450.594
【相关文献】
1.国有企业混合所有制改革必然性分析与最佳改革成效实现路径研究 [J], 杨薇薇
2.为您的应用选择最佳的过流电路保护方法 [J], Kent Hou
3.采用最小封装尺寸实现业界最佳的转换器保护功能 [J],
4.陶氏化学ENGAGE POEs为光伏封装胶膜提供最佳选择用于光伏组件封装胶膜的POEs具有更佳的电气性能及防潮性 [J],
5.飞思卡尔在经济高效的大功率RF晶体管塑料封装领域实现突破——超模压塑料封装内的RF设备旨在以2GHz的频率提供与气腔封装一样的性能,同时降低放大器的成本并改进自动化装配 [J],
因版权原因,仅展示原文概要,查看原文内容请购买。
高密度封装覆铜板在航天航空电子中的应用研究

高密度封装覆铜板在航天航空电子中的应用研究导语:随着现代电子技术的飞速发展,航天航空电子作为高科技领域的重要组成部分,对电路板的要求越来越高。
高密度封装覆铜板作为电路板的重要材料,在航天航空电子中发挥着重要的作用。
本文将研究高密度封装覆铜板在航天航空电子中的应用,并探讨其优势和挑战。
1. 引言航天航空电子是一项关系国家利益和民众安全的高科技领域。
随着航天航空器的各种功能的不断升级和需求的增加,电子设备的集成度和性能要求也在不断提高。
高密度封装覆铜板作为电子设备的关键部分之一,能够满足航天航空电子对信号传输、可靠性和空间利用率等方面的高要求。
2. 高密度封装覆铜板的优势2.1 信号传输性能高密度封装覆铜板具有较好的信号传输性能。
其铜涂层良好,能够有效降低信号传输中的损耗。
同时,高密度封装覆铜板采用层层堆叠的设计,能够实现信号的跨层引导和交互,提高了整个电路板的信号传输效果。
2.2 空间利用率航天航空电子器件对空间的利用率要求非常高。
高密度封装覆铜板采用多层封装的设计,提高了电路板的可堆叠性,有效利用了板内空间。
同时,高密度封装覆铜板采用高精度的制造工艺,能够实现电路板的精密封装,并使得电路板更加紧凑。
2.3 可靠性航天航空环境极其恶劣,对电子设备的可靠性提出了很高的要求。
高密度封装覆铜板具有更好的可靠性。
其封装工艺精良,能够有效隔离电路板与外部环境的接触,防止电路板受到外界因素的干扰。
此外,高密度封装覆铜板采用高质量的制造材料,能够应对航天航空环境的高温、低温、辐射等极端条件,提供可靠的电子设备保障。
3. 高密度封装覆铜板的应用3.1 航天器通信系统航天器通信系统是航天航空电子中的重要组成部分,对信号传输效果和可靠性要求极高。
高密度封装覆铜板能够提供高质量的信号传输通道,保障航天器与地面的有效通信。
3.2 航空导航系统航空导航系统是航空电子中的关键部分,对精确的导航和定位要求较高。
高密度封装覆铜板的高精度制造工艺能够提供精确的电路连接和引导,保障导航系统的准确性和可靠性。
三维高密度组装技术
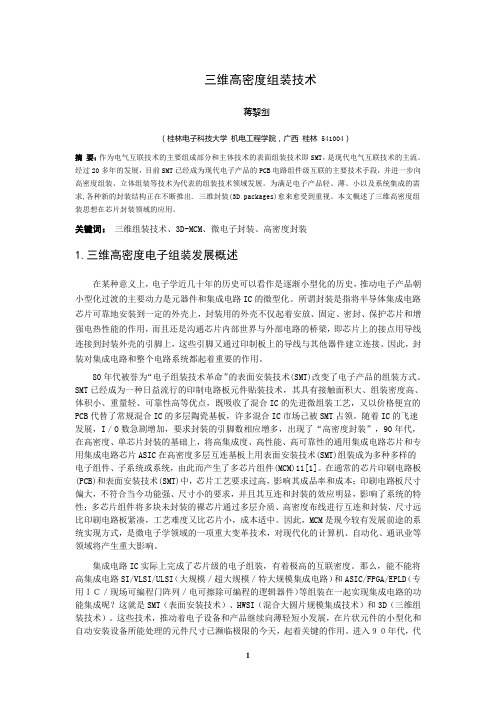
三维高密度组装技术蒋黎剑(桂林电子科技大学机电工程学院,广西桂林 541004)摘要:作为电气互联技术的主要组成部分和主体技术的表面组装技术即SMT,是现代电气互联技术的主流。
经过20多年的发展,目前SMT已经成为现代电子产品的PCB电路组件级互联的主要技术手段,并进一步向高密度组装、立体组装等技术为代表的组装技术领域发展。
为满足电子产品轻、薄、小以及系统集成的需求,各种新的封装结构正在不断推出. 三维封装(3D packages)愈来愈受到重视。
本文概述了三维高密度组装思想在芯片封装领域的应用。
关键词:三维组装技术、3D-MCM、微电子封装、高密度封装1.三维高密度电子组装发展概述在某种意义上,电子学近几十年的历史可以看作是逐渐小型化的历史,推动电子产品朝小型化过渡的主要动力是元器件和集成电路IC的微型化。
所谓封装是指将半导体集成电路芯片可靠地安装到一定的外壳上,封装用的外壳不仅起着安放、固定、密封、保护芯片和增强电热性能的作用,而且还是沟通芯片内部世界与外部电路的桥梁,即芯片上的接点用导线连接到封装外壳的引脚上,这些引脚又通过印制板上的导线与其他器件建立连接。
因此,封装对集成电路和整个电路系统都起着重要的作用。
80年代被誉为“电子组装技术革命”的表面安装技术(SMT)改变了电子产品的组装方式。
SMT已经成为一种日益流行的印制电路板元件贴装技术,其具有接触面积大、组装密度高、体积小、重量轻、可靠性高等优点,既吸收了混合IC的先进微组装工艺,又以价格便宜的PCB代替了常规混合IC的多层陶瓷基板,许多混合IC市场己被SMT占领。
随着IC的飞速发展,I/O数急剧增加,要求封装的引脚数相应增多,出现了“高密度封装”,90年代,在高密度、单芯片封装的基础上,将高集成度、高性能、高可靠性的通用集成电路芯片和专用集成电路芯片ASIC在高密度多层互连基板上用表面安装技术(SMT)组装成为多种多样的电子组件、子系统或系统,由此而产生了多芯片组件(MCM)11[1]。
《基于多层LCP基板的高密度系统集成技术》记录

《基于多层LCP基板的高密度系统集成技术》阅读记录目录一、内容概览 (1)二、多层LCP基板概述 (2)1. 定义与特点介绍 (3)2. LCP材料及其应用现状 (4)三、高密度系统集成技术基础 (5)1. 高密度系统集成概念与重要性 (6)2. 集成技术分类及特点分析 (7)四、基于多层LCP基板的高密度系统集成技术介绍 (8)1. 技术原理及发展历程 (9)2. 关键工艺技术研究 (10)(1)高精度制造与加工技术 (11)(2)电路设计与布局优化技术 (13)(3)可靠性与稳定性保障技术 (14)五、多层LCP基板高密度系统集成技术应用领域分析 (15)1. 通信领域应用现状及前景展望 (17)2. 计算机硬件领域应用案例分析 (17)3. 消费电子产品的应用示范研究及市场趋势预测分析以及改进方向分析提出19一、内容概览引言部分简要介绍了当前电子产业发展的趋势以及面临的挑战,从而引出了多层LCP基板的重要性。
强调了高密度系统集成技术在推动电子产业发展中的关键作用。
接下来,文章介绍了多层LCP基板的基本概念和特点。
包括其优良的电气性能、热稳定性、机械强度以及良好的加工性能等。
也指出了多层LCP基板在制造上的难点和挑战。
文章重点阐述了多层LCP基板在高密度系统集成中的应用。
包括其在芯片封装、电路板设计、半导体器件等领域的具体应用实例。
分析了多层LCP基板如何帮助实现更高密度的系统集成,从而提高系统的性能和效率。
文章还讨论了多层LCP基板技术的最新发展动态和未来趋势。
包括新材料、新工艺、新技术在多层LCP基板领域的应用,以及这些技术对未来高密度系统集成的影响。
文章对多层LCP基板在高密度系统集成技术中的优势进行了总结,并对其面临的挑战和可能的风险进行了分析。
同时也提出了一些建议,以便读者更好地理解和应用多层LCP基板技术。
通过阅读本文,我对多层LCP基板在高密度系统集成技术中的应用有了更深入的了解,并对未来该领域的发展前景充满了期待。
高密度封装进展之一 元件全部埋入基板内部的系统集成封装(上)

高密度封装进展之一元件全部埋入基板内部的系统集成封装
(上)
田民波
【期刊名称】《印制电路信息》
【年(卷),期】2003(000)009
【摘要】将无源元件及IC等全部埋入基板内部的三维封装,不仅能提高电子设备的整体性能,有利于轻薄短小化,而且由于钎焊连接部位减少,可提高可靠性并能有效降低封装的总价格.
【总页数】5页(P3-7)
【作者】田民波
【作者单位】清华大学材料科学与工程系,100084
【正文语种】中文
【中图分类】TN4
【相关文献】
1.日本CCL技术的新进展(三、上)——日立化成工业公司近年IC封装用基板材料技术进展综述 [J], 祝大同
2.高密度封装进展(之一):元件全部埋置于基板内部的系统集成封装 [J], 田民波
3.高密度封装进展(之一)——元件全部埋置于基板内部的系统集成封装(一)[J], 田民波
4.高密度封装进展之五——采用无源元件和有源元件埋入技术实现的模块内系统封
装 [J], 田民波
5.高密度封装进展之一:元件全部埋入基板内部的系统集成封装(下) [J], 田民波因版权原因,仅展示原文概要,查看原文内容请购买。
- 1、下载文档前请自行甄别文档内容的完整性,平台不提供额外的编辑、内容补充、找答案等附加服务。
- 2、"仅部分预览"的文档,不可在线预览部分如存在完整性等问题,可反馈申请退款(可完整预览的文档不适用该条件!)。
- 3、如文档侵犯您的权益,请联系客服反馈,我们会尽快为您处理(人工客服工作时间:9:00-18:30)。
2. 2 硅效率 芯片在印制电路板 ( PCB)上所占的面积是 封装技术的主要问题之一。 在 M CM 中 , 由于 使 用了 裸 芯片 使 芯片 所 占 面积 减 小 20 %~ 90 %。 而三维封装可更加有效地利用硅电路板 , 即提高了硅效率。与其它二维封装技术相比 , 三
第 35卷 第 6期 1998年 12月
图 1 三维技术与 M CM 技术的硅效率对比
2. 3 延迟 延迟指的是信号在两个系统功能电路块之 间传播所需要的时间 。 在高速系统中 , 总延迟 主要受飞行时间的限制 , 飞行时间即信号沿互 连进行传播 (飞行 ) 所用的时间 , 飞行时间与 互连长度成正比。 若要降低延迟就必须缩短互 连 , 如图 2中所示的那样 , 使用三维封装技术 可最大限度地缩短互连长度 , 并因此降低寄生 电容和电感 , 减小信号的传播延迟 。 M CM 可使 信号延迟降低 300 % , 而与之相比 , 三维封装中 的电子元件则非常紧凑 , 其信号延迟比 M CM 要小得多 。
图 4 用柔性材料实现 IC 的折叠与互连
图 7 Hughes公司开发的微型弹簧 垂直互连方法的原理图 图 5 用引线键合实现垂直互连的方法
半导体情报
27
线板 ( PW B) 上安装时 , 互连约占系统总功耗 的 10 % ; 如果用 M CM 技术 , 系统功耗可降低 1 /5, 其功耗要比使用 PW B低 8 % ; 若采用三维 封装技术 , 由于缩短了互连长度并减小了寄生 效应 , 则可使系统功耗进一步降低。 2. 6 速度 由于三维封装降低了系统功耗 , 因此在不 增加功耗的情况下 , 三维器件的跃迁速度 (频 率 ) 会更快。 此外 , 三维器件的寄生效应 (电 容和电感 )、 体积与噪声均有所降低 , 跃迁速度 显著提高 , 从而改进了系统的性能。 2. 7 互连效率 使用三维封装结构可为叠层中的中心元件 提供 116个相邻元件 , 而在二维封装中可提供 的相邻元件却仅有 8 个 (图 3)。 因此 , 缩短叠 层的互连长度可降低芯片间的传播延迟。 此外 , 与传统封装技术所用的通孔布线互连相比 , 三 维封装的垂直互连可最大限度地利用互连的效 率。
收稿日期 : 1998- 09- 29
积小 、 厚度薄 、 易于携带 、 速度快 、 可靠性高 和价格低的特点。 就目前各个技术领域的发展来看 , 要实现 上述要求 , 关键就在于封装技术 。 进入 90年代 以来 , 微电子封装技术迎来了 “爆炸式 ” 的发 展时期 , 微电子封装正在逐步从传统的面向器 件转为面向系统、 面向最终用户 , 封装的功能 在此基础上得到极大的加强和提高 。 随着各种电子系统复杂程度的日益提高 , 市 场对低功耗 、轻重量小型封装技术的要求也随之 增加。许多航空航天产品也要求在系统功能增加 的同时还必须不断减小系统体积并降低系统重 量。 为了满足这一市场需求 , 近年来出现了许多
High Density 3D Packaging Technology
Li Xi uqi ng
( Hebei Semiconductor Research Inst itu te , Shij iaz huang 050051)
Abstract T his paper i ntroduces a number of bare a nd m ul tichip mo dule stacki ng t echnologi es that a re em ergi ng t o meet the ev er i ncreasi ng dema nds f or lo w po wer consumpti on, lo w weight and compact systems. Vertical interconnect techniques a re review ed in details. T echno logical i ssues such as silico n ef ficiency , co mpl exi ty , speed and po w er consum pti on etc. a re brief ly di scussed. Keywords 3D packagi ng Vertical i nt erconnectio n Bare die stacki ng M CM st acki ng
图 3 二维封装与三维封装的互连效率比较
在折叠柔性电路中 , 先将裸芯片安装在柔 性材料上 , 然后将其折叠 , 形成三维叠层 , 如 图 4 所示 。 引线键合叠层芯片是一种采用引线键合技 术实现垂直互连的方法。 可直接与 M CM 基板 进行引线键合 。 这种方法是采用引线键合工艺 将叠层芯片与平面 M CM 基板键合在一起的 , 如图 5所示 。也可采用基板与 IC引线键合的方 法。 采用这种方法需要有一母芯片和一子芯片 , 母芯片充当子芯片的基板 , 互连就通过子芯片 与母芯片基板上的焊点相连 , 如图 6所示。 3. 2 叠层 IC之间的区域互连 在区域互连中 , 垂直互连并不与叠层元件
图 2 二维结构与三维结构的布线长度比较
2. 4 噪声 通常 , 噪声会对一有用信号产生干扰。 噪 声频率与封装和互连设计的关系很密切 。 数字 系统中的噪声源主要包括反射噪声 、串扰噪声、 同步开关噪声和电磁干扰 。 这些噪声源的大小 取决于信号通过互连时的上升时间 。 上升时间 越快 , 噪声就越大。 如前所述 , 三维封装技术 通过缩短互连长度降低了噪声 , 并因此减小了 相关的寄生效应 ,达到了提高系统性能的目的。 2. 5 功耗 电子系统的寄生电容与互连长度成正比 , 只要减小寄生效应就可降低总功耗 。 在印制布
直互连是指设计三维模块中的电源 、 接地及层 间信号时所需的互连 。 下面介绍互连的类型 。 3. 1 叠层 IC 间的外围互连 叠层互连工艺包括叠层载带、 焊接边缘导 体、 腔面薄膜导体、 互连基板与腔体外部、 折 叠柔性电路和引线键合叠层芯片的连接等。 叠层载带是用载带自动键合 ( T AB) 实现 IC 互连的一种方法。 这种方法可进一步分成 。使 PCB上的叠层 T AB和引线框架上的 T AB 用 PCB上 T AB方法的公司主要有 Intel Japan 和 Ma tsushit a Elect ri c Indust rial Com pany 等 公司 。 这种方法主要应用于高密度存储卡 ; 目 前使用引线框架 T AB 工艺的公司主要有富士 通等 。 这种方法主要用于 DRAM 芯片设计 。 边缘导体键合工艺的目的是利用焊接边缘 导体实现 IC 间的垂直互连 。 该工艺有四个关键 步骤 : 第一是在叠层上滴漏焊料 , 在边缘上形 成垂直导体 ; 第二是用焊料填充芯片载体与隔 板上的通孔 ; 第三是基板通孔间的焊点连接 ; 第 四是在芯片边缘上形成焊料球 。 腔面上的薄膜导体是一层在真空条件下向 基板上溅射或蒸发的导电材料 , 其目的是要在 腔面上形成垂直互连 。 为实现基板与腔面的互 连 , 可采用 Texas Inst rum ent s 等公司开发的 T AB 引线与硅基板焊点相连的方法和叠层面 上的倒装芯片键合方法以及在 T SOP 封装两 侧焊接 PCB板等方法 。
类型 容量 / M b 分立 S R AM 重量 DR AM 1 4 1 4 16 S R AM 体积 DR AM 1 4 1 4 16 1678 872 1357 608 185 3538 1588 2313 862 363 二维 783 249 441 179 69 2540 862 1542 590 227 三维 133 41 88 31 69 195 145 132 113 113 分立 /三维 12. 6 21. 3 15. 4 19. 6 16. 8 18. 1 10. 9 17. 5 7. 6 3. 2 二维 /三维 5. 9 6. 1 5. 0 5. 0 6. 2 13. 0 5. 9 11. 6 5. 2 2. 0
维封装技术的硅效率超过 100 % , 如图 1所示。
2 三维封装技术的优点
2. 1 体积与重量 在三维封装中 , 由于用三维器件取代了单 芯片封装 , 因而封装尺寸和重量显著减小 , 其 减小幅度与垂直互连密度、 热性能以及所需强 度等工艺过程有一定的关系 。 与传统封装相比 , 采用三维封装技术可使系统尺寸与重量降低到 原来的 1 /40 ~ 1 /50 。 表 1对三维裸芯片封装与 分立封装和平面封装 (如 M CM 等 ) 的重量和 体积进行了比较。 很显然 , 三维封装的体积仅 为 M CM 的 1 /5 ~ 1 / 6, 是分立封装技术的 1 / 10 ~ 1 /20; 其重量是 M CM 的 1 /2 ~ 1 / 13, 是分立 元器件的 1 / 3 ~ 1 / 19 。此外 , 在 Aladdi n并行处 理器中应用时 , 其重量和体积仅为 Cray X-M P 基准处理器的 1 / 660和 1 / 2700 。 表 1 三维封装技术与其它二维封装 在体积与重量上的对比
2. 8 带宽 互连带宽 , 尤其是存储带宽经常是影响计 算和通信系统的关键因素 , 低的延迟和宽的总 线非常重要。例如在著名的 Intel Pentium 处理 器中 , CPU 和二级缓冲存储器共同封装在同一 个多腔针栅阵列 ( Pin Grid Array ) 中以获得较 大的存储带宽 。 三维封装技术有望应用于集成 CPU 和存储器芯片 , 且不会增加多腔针栅阵列 的成本 。
26
半导体情报
第 35卷 第 6期 1998年 12月
新型三维封装技术 。 这类封装技术采用将裸芯片 或多芯片模块 ( M CM ) 沿 Z 轴层叠起来的方法 , 使系统的封装体积大大减小 。 由于这种 Z 面技 术大大缩短了总的互连长度 , 系统的寄生电容显 著减小 , 从而使系统的总功耗降低了 30 % 左右 , 达到提高系统工作性能的目的 。
3 三维电子系统的垂直互连
三维封装的关键技术是垂直互连工艺 。 垂