robbins_mgmt10_tb_06
华三路由器软件升级指南
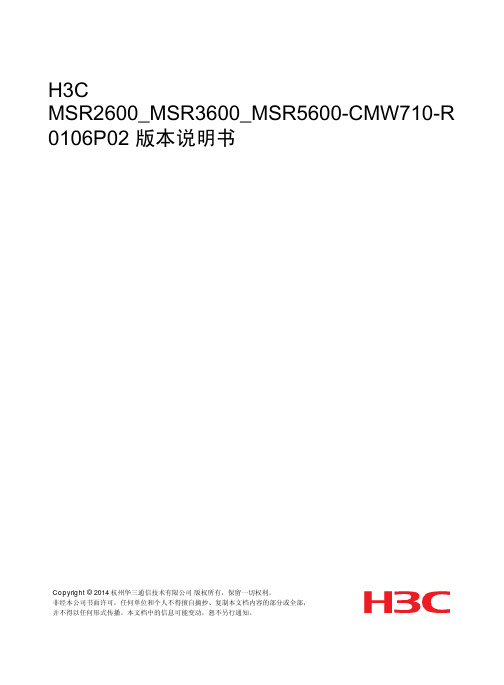
SignalTEK 10G 10G Ethernet Troubleshooter and Band

Why do I need a10G Ethernet T ester?ProblemLAN networks are at risk Solution SignalTEK 10G willAvoid network downtimeTroubleshoot Ethernet connectivity issues faster using diagnostic tools.Pinpoint bottlenecks fasterDiscover which part of your network is causing the bottleneck.Validate network upgradesVerify Multi-Gigabit switch upgrades to 1/2.5/5 and 10Gb/s speeds.Prove the maximum bandwidthProvide “proof of performance” PDF reports to the client.The new SignalTEK 10G measures the maximum bandwidth of the network cabling up to 10 Gigabits per second. Bysimulating actual network traffic users can test, troubleshoot and document network and data cable performance up to 10 Gigabit Ethernet standards.SignalTEK 10G has built-in Wi-Fi connectivity to connect seamlessly to the free AnyWARE Cloud test management system. AnyWARE Cloud offers pre-configuration to eliminate errors on-site, label printer connectivity to save time and “proof of performance” PDF reports for the clients.SignalTEK 10G10G Ethernet Troubleshooter and Bandwidth TesterIncrease your network speedfrom 1Gb/s to 10Gb/sProblemThere are 111 billion metres of Cat5e/Cat6 cabling installed globally that is limited to 1Gb/s bandwidth speeds due to the current switches deployed. Upgrading to Multi-Gigabit switches could increase speed but it is unclear what bandwidth the existing cabling will support.SolutionUse SignalTEK 10G to verify what the data cabling will support (up to 10Gb/s) before spending moneyon new Multi-Gigabit switches delivering2.5/5/10Gb/s speeds. Use the SignalTEK 10G again following the upgrade to prove performance to the client with the “proof of performance” PDF reports.As simple as 1-2-3Easy to understand traffic light status - The simple traffic lightindicator displays Good, Marginal or Poor power level based onIEEE 802.3 1G/10G limits.Max throughput test - The SignalTEK 10G will prove the maximumavailable bandwidth over the fibre link up to 10Gb/s.Discover a faulty SFP – The SFP temperature is measured to helpunderstand if it has become faulty.Will my existing cablinginfrastructure supportMulti-Gigabit technology?10G/Multi-Gigabit Performance90W PoE for AV and Digital SignageTest copper and fibrevertical cablingVoIP testing and troubleshootingMeets your network needs today and tomorrow.The SignalTEK 10G will help to increase network bandwidth without replacing expensive cableinfrastructure, troubleshoot PoE and Ethernet issues and prove the maximum bandwidth up to 10 Gigabits per second.6Testing through Network testing andConduct preventative maintenance testing, audit network capabilities and Prove performance of new cableinstallations up to 10GNetwork T estingThe SignalTEK 10G is also a network tester for troubleshooting and maintenance of active and passive copper and fibre networks.Port & network summary info Press the Autotest button to display summary information and allow for detailed inspection of networkparameters.VLAN detection & operationAutomatic detection of VLAN IDsallows the user to configure SignalTEK10G for operation on a VLAN.Custom WiremapUse a list of wiremap templates forcommon Ethernet cable types aswell as non-Ethernet cables, such asProfinet and ISDN.CDP/LLDP/EDP port informationShow port information using Cisco Discovery Protocol (CPD). Link Layer Discovery Protocol (LLDP) and Extreme Discovery Protocol (EDP).NetscanDisplay list of IP and MAC addressesof every device connected tothe network.72-hour event logFind rogue devices and intermittentissues using the 72-hour event log.SignalTEK 10G logs all network eventsover a 72-hour period to help diagnose connectivity issues faster, reducing hours onsite and reducing trips to the site. Leave the tester onsite, connect remotely tomonitor network activity, view the event log and control all functions of the tester from the office.The SignalTEK 10G will log all network eventsover a 72-hour period to help diagnose connectivity issues faster, reducing hoursonsite and reducing trips to site.72-hour event log captures network events down to the second eliminatingguessworkNo more trial and errorAccurately measure the maximum power available Supports PoE up to 90W (PoE++)Test all PoE Classes (0-8) and Types (af/at/bt)Identifies the powered pairsDetermine whether power is from a switch or mid-span injectorVerify the PoE installationPass / Fail indication to IEEE standards Extended power testSome switches may provide power exceeding their IEEE Class rating. Measure the maximum available power up to 90 watts.PoE T esting.Eliminate GuessworkThe SignalTEK 10Geliminates guesswork when installing, maintaining and troubleshooting wherePoE is deployed up to 90W (PoE++).10Adoption of Power over Ethernet (PoE)In just a few short years we have seen many different applications increasing adopt PoE, such as monitors, digital signage, phones, security cameras, lighting and access control.Previously technicians had to understand all the various standards, device power outputs and cable lengths to be sure a device will operate successfully.The SignalTEK 10G identifies the Class of the PoEsource and power available up to 90W to a PoE device regardless of cable length, cable quality or other factors. A clear pass/fail is provided to IEEE 802.3af/at/bt standards.The SignalTEK 10G identifies the Class of the PoE source and power available up to 90W to a PoE deviceregardless of cable length, cablequality or other factors.11Proof of PerformanceCloud software• Operates anywhere with a web browser – AnyWARE Cloud operates on a PC, Mac and tablet devices (Android and iOS)• Free storage – No need for separate servers or backup systems.• Easy to find project files – Attach all project filesincluding cable layout drawings, videos, and photos into the AnyWARE Cloud. Everything you need in one place. • Share reports easier – Use AnyWARE Cloud to share links to the test reports eliminating the need to manually email large attachments.• Reduce training time with WalkMe – AnyWARE Cloud is embedded with the WalkMe digital adoption platform providing proactive, step-by-step guidance on all key tasks.Fleet management• Easily manage the certifier fleet – Fleet manager allows you to see who has the SignalTEK 10G when the software was last updated and when the results were last synced. Allowing you to manage tester downtime and ensuring results are transferred back to the office and not lost or deleted.Professional PDF reporting• Customer profiles – Create a profile for each of thecustomers with their company logo, address and contact details. This information is automatically pulled through to the reports, saving time.Report formats• Summary report – This is a report showing multiple tests per page.• Detailed report – This is a comprehensive report with all the measurement results with one page per test. Reports can be generated on the SignalTEK 10G or on the free IDEAL AnyWARE Cloud.The AnyWARE Cloudmanagement system allows real time collaboration between Project Managers and Field Technicians. There is no need for Field Technicians to setup the SignalTEK 10G, Project Managers pre-configure thejobs and tests in the AnyWARE Cloud, eliminating potential mistakes and compressing the time taken to prepare reports for customers.Test Management SoftwareIDEAL AnyWARE Cloud Jobs screenIDEAL AnyWARE Cloud Test Result report12ax throughput test up to 10GComplete ConnectivityWi-Fi connectivity to the AnyWARE Cloud management system. USB connection for transferring test dataBuilt-in PDF ReportingReports can be generated directly from the SignalTEK 10G as well as the CloudPartner FinderProvides audible tone and visible indicator when connected tothe remote unitTouchscreenHigh resolution impact resistant touchscreenfor ease of useInternal LoadspeakerAudible tones assist theuser when testingIntuitive UserInterfaceSimplified user interfacefor easy setup andoperationRugged DesignRubberised housing, protected screenand protected measurement portLabel Printer ConnectivityEasily send label IDs to printers for fast and accurate labellingSignalTEK 10GPart NoDescriptionUPGRADE10GFIB UPGRADE SignalTEK 10G - Fibre testing option UPGRADE10GNETUPGRADE SignalTEK 10G - Network testing optionSignalTEK 10G is a future-proof investment as additional features can be unlocked with a simple license key when required. There are two upgrade options to choose from: fibre testing and advanced network testing.Future-proof the investment14Who is SignalTEK 10G designed for?SolutionSignalTEK 10GCT R157000SignalTEK 10GFT R157001SignalTEK 10GNT R157002SignalTEK 10GPRO R157003CategoryDisplays voltage and which pairs have PoEPass / Fail to PoE IEEE standardsMax power available (up to 90 watts)Type (af/at/bt) and Class (1 to 8)P o EF i b r eo p t i o n a lC o p p e rUptime efficiency and 72 hour event log Switch Speed - 100M, 1G, 2.5G, 5G, 10G Testing with packet loss, jitter and delay VLAN, PING, TraceRoute, Hub blink, NetScanProve network performance up to 10GCDP/LLDP/EDP port information N e t w o r ko p t i o n a lPass / Fail to fibre IEEE standards Wiremap, distance to fault, length Optical Tx/Rx power indication Max bandwidth test up to 10Gb/s SFP temperature, vendor and model Cable tracing (with compatible probe)Max bandwidth test up to 10Gb/sData transmission test 1/2.5/5/10GbSupports SFP/SFP+ (MM&SM)Pass / Fail to copper IEEE standardsData transmission test 1/10Gb NbaseT/Multi-Gigabit test 1/2.5/5/10Gb 15Proof of PerformanceIDEAL NETWORKS, SignalTEK and the IDEAL AnyWARE logos are trademarks or registered trademarks of IDEAL INDUSTRIES NETWORKS LIMITED.IDEAL INDUSTRIES NETWORKS LIMITEDStokenchurch House, Oxford Road, Stokenchurch, High Wycombe, Buckinghamshire, HP14 3SX, UK.Tel. +44 (0)1925 428 380 | Fax. +44 (0)1925 428 381********************Specification subject to change without notice. E&OE© IDEAL INDUSTRIES NETWORKS LIMITED 2020Publication no.: 157805 Rev.1SignalTEK 10G10G Ethernet Troubleshooterand Bandwidth TesterOrdering informationOptional Accessories。
SignalTEK 10G 10G Ethernet故障排除和带宽测试仪用户手册说明书

SignalTEK 10G 10G Ethernet Troubleshooter and Bandwidth TesterUser ManualSignalTEK 10GUser ManualGuide d’utilisationBedienungsanleitungGuida utenteManual de usuarioGuia do Usuario用户指南Podręcznik użytkownikaユーザーガイドTREND NETWORKSStokenchurch HouseOxford roadStokenchurchHigh WycombeBuckinghamshireHP14 3SXUnited Kingdom© TREND NETWORKS 2021The information contained in this document is the property of TREND NETWORKS and is supplied without liability for errors and omissions. No part of this document may be reproduced or used except as authorized by contract or other written permission from TREND NETWORKS. The copyright and all restrictions on reproduction and use apply to all media in which this information may be placed. TREND NETWORKS pursues a policy of continual product improvement and reserves the right to alter without notice the specification, design, price or conditions of supply of any product or service. All rights reserved.Les informations dans ce document sont la propriété de TREND NETWORKS et elles sont fournies sans responsabilité pour les erreurs et les omissions. Aucune partie de ce document ne doit être reproduite ou utilisée, sauf en casd’autorisation par contrat ou en cas d’autre autorisation écrite donnée par TREND NETWORKS. Le copyright et toutes les limitations concernant la reproduction et l’utilisation s’appliquent à tous les supports sur lesquels cette information peutêtre placée. TREND NETWORKS améliore continuellement ses produits et se réserve le droit de modifier sans préavis la spécification, la conception, le prix ou les conditions de fourniture d’un produit ou d’un service. Tous droits réservés.Die Informationen in diesem Dokument sind das Eigentum von TREND NETWORKS und werden ohne Gewährleistung der Vollständigkeit oder Korrektheit gegeben. Dieses Dokument darf nur soweit vertraglich oder anderweitig schriftlich von TREND NETWORKS zugesichert ganz oder teilweise vervielfältigt werden. Das Urheberrecht und alle Einschränkungen zur Vervielfältigung und Nutzung gelten für alle Datenträger, auf denen diese Informationen gespeichert werden können. TREND NETWORKS bemüht sich um ständige Produktverbesserungen und behält sich das Recht vor, die Spezifikation, das Design, den Preis oder die Lieferbedingungenjeglicher Produkte oder Dienste ohne Vorankündigung zu ändern. Alle Rechte vorbehalten.Le informazioni contenute nel presente documento sono di proprietà di TREND NETWORKS e sono fornite senza alcuna responsabilità relativa a errori e omissioni. Sono vietati la riproduzione o l’uso di tutto il documento o parte di esso, salvo se autorizzati da contratto o permesso scritto di TREND NETWORKS. Il copyright e tutte le limitazioni sulla riproduzione e l’uso si applicano a tutti i supporti nei quali le presenti informazioni possono essere contenute. TREND NETWORKS segue una politica volta al miglioramento continuo dei prodotti e si riserva il diritto di modificare senza preavviso le specifiche, il disegno, il prezzo o le condizioni di fornitura di qualsivoglia prodotto o servizio. Tutti i diritti riservati.La información que figura en este documento es propiedad de TREND NETWORKS, quien no asume responsabilidad alguna sobre posibles errores u omisiones que puedan existir en este documento. Queda prohibida la reproducción parcial o total de este documento, así como darle un uso distinto al autorizado mediante contrato o autorización escrita por parte de TREND NETWORKS independientemente del formato y soporte de los contenidos. TREND NETWORKS sigue unapolítica de mejora continua del producto y nos reservamos el derecho de modificar sin previo aviso las especificaciones, diseño, precio o condiciones de suministro de cualquier producto o servicio. Todos los derechos reservados.As informações contidas neste documento são de propriedade de TREND NETWORKS e são fornecidas sem responsabilidade sobre erros e omissões. Nenhuma porção deste documento pode ser reproduzida ou usada exceto quando autorizada mediante contrato ou outra permissão por escrito da TREND NETWORKS. Os direitos de cópia e restrições de reprodução e uso são aplicáveis a todas as mídias nas quais estas informações possam ser colocadas. A TREND NETWORKS segue uma política de melhora contínua do produto e se reserva ao direito de alterar sem avisoprévio as especificações, design, preço ou condições de fornecimento de qualquer produto ou serviço. Todos os Direitos Reservados.本文档所包含的信息是美国理想工业公司 (TREND NETWORKS) 的财产,对于本文档中出现的错误或遗漏,提供方概不负责。
NXP SCM-i.MX 6 Series Yocto Linux 用户指南说明书
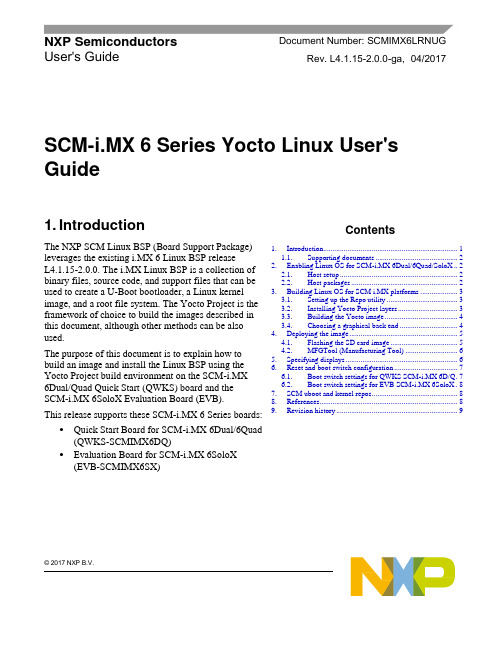
© 2017 NXP B.V.SCM-i.MX 6 Series Yocto Linux User'sGuide1. IntroductionThe NXP SCM Linux BSP (Board Support Package) leverages the existing i.MX 6 Linux BSP release L4.1.15-2.0.0. The i.MX Linux BSP is a collection of binary files, source code, and support files that can be used to create a U-Boot bootloader, a Linux kernel image, and a root file system. The Yocto Project is the framework of choice to build the images described in this document, although other methods can be also used.The purpose of this document is to explain how to build an image and install the Linux BSP using the Yocto Project build environment on the SCM-i.MX 6Dual/Quad Quick Start (QWKS) board and the SCM-i.MX 6SoloX Evaluation Board (EVB). This release supports these SCM-i.MX 6 Series boards:• Quick Start Board for SCM-i.MX 6Dual/6Quad (QWKS-SCMIMX6DQ)• Evaluation Board for SCM-i.MX 6SoloX (EVB-SCMIMX6SX)NXP Semiconductors Document Number: SCMIMX6LRNUGUser's GuideRev. L4.1.15-2.0.0-ga , 04/2017Contents1. Introduction........................................................................ 1 1.1. Supporting documents ............................................ 22. Enabling Linux OS for SCM-i.MX 6Dual/6Quad/SoloX .. 2 2.1. Host setup ............................................................... 2 2.2. Host packages ......................................................... 23.Building Linux OS for SCM i.MX platforms .................... 3 3.1. Setting up the Repo utility ...................................... 3 3.2. Installing Yocto Project layers ................................ 3 3.3. Building the Yocto image ....................................... 4 3.4. Choosing a graphical back end ............................... 4 4. Deploying the image .......................................................... 5 4.1. Flashing the SD card image .................................... 5 4.2. MFGTool (Manufacturing Tool) ............................ 6 5. Specifying displays ............................................................ 6 6. Reset and boot switch configuration .................................. 7 6.1. Boot switch settings for QWKS SCM-i.MX 6D/Q . 7 6.2. Boot switch settings for EVB SCM-i.MX 6SoloX . 8 7. SCM uboot and kernel repos .............................................. 8 8. References.......................................................................... 8 9.Revision history (9)Enabling Linux OS for SCM-i.MX 6Dual/6Quad/SoloX1.1. Supporting documentsThese documents provide additional information and can be found at the NXP webpage (L4.1.15-2.0.0_LINUX_DOCS):•i.MX Linux® Release Notes—Provides the release information.•i.MX Linux® User's Guide—Contains the information on installing the U-Boot and Linux OS and using the i.MX-specific features.•i.MX Yocto Project User's Guide—Contains the instructions for setting up and building the Linux OS in the Yocto Project.•i.MX Linux®Reference Manual—Contains the information about the Linux drivers for i.MX.•i.MX BSP Porting Guide—Contains the instructions to port the BSP to a new board.These quick start guides contain basic information about the board and its setup:•QWKS board for SCM-i.MX 6D/Q Quick Start Guide•Evaluation board for SCM-i.MX 6SoloX Quick Start Guide2. Enabling Linux OS for SCM-i.MX 6Dual/6Quad/SoloXThis section describes how to obtain the SCM-related build environment for Yocto. This assumes that you are familiar with the standard i.MX Yocto Linux OS BSP environment and build process. If you are not familiar with this process, see the NXP Yocto Project User’s Guide (available at L4.1.15-2.0.0_LINUX_DOCS).2.1. Host setupTo get the Yocto Project expected behavior on a Linux OS host machine, install the packages and utilities described below. The hard disk space required on the host machine is an important consideration. For example, when building on a machine running Ubuntu, the minimum hard disk space required is about 50 GB for the X11 backend. It is recommended that at least 120 GB is provided, which is enough to compile any backend.The minimum recommended Ubuntu version is 14.04, but the builds for dizzy work on 12.04 (or later). Earlier versions may cause the Yocto Project build setup to fail, because it requires python versions only available on Ubuntu 12.04 (or later). See the Yocto Project reference manual for more information.2.2. Host packagesThe Yocto Project build requires that the packages documented under the Yocto Project are installed for the build. Visit the Yocto Project Quick Start at /docs/current/yocto-project-qs/yocto-project-qs.html and check for the packages that must be installed on your build machine.The essential Yocto Project host packages are:$ sudo apt-get install gawk wget git-core diffstat unzip texinfo gcc-multilib build-essential chrpath socat libsdl1.2-devThe i.MX layers’ host packages for the Ubuntu 12.04 (or 14.04) host setup are:$ sudo apt-get install libsdl1.2-dev xterm sed cvs subversion coreutils texi2html docbook-utils python-pysqlite2 help2man make gcc g++ desktop-file-utils libgl1-mesa-dev libglu1-mesa-dev mercurial autoconf automake groff curl lzop asciidocThe i.MX layers’ host packages for the Ubuntu 12.04 host setup are:$ sudo apt-get install uboot-mkimageThe i.MX layers’ host packages for the Ubuntu 14.04 host s etup are:$ sudo apt-get install u-boot-toolsThe configuration tool uses the default version of grep that is on your build machine. If there is a different version of grep in your path, it may cause the builds to fail. One workaround is to rename the special versi on to something not containing “grep”.3. Building Linux OS for SCM i.MX platforms3.1. Setting up the Repo utilityRepo is a tool built on top of GIT, which makes it easier to manage projects that contain multiple repositories that do not have to be on the same server. Repo complements the layered nature of the Yocto Project very well, making it easier for customers to add their own layers to the BSP.To install the Repo utility, perform these steps:1.Create a bin folder in the home directory.$ mkdir ~/bin (this step may not be needed if the bin folder already exists)$ curl /git-repo-downloads/repo > ~/bin/repo$ chmod a+x ~/bin/repo2.Add this line to the .bashrc file to ensure that the ~/bin folder is in your PATH variable:$ export PATH=~/bin:$PATH3.2. Installing Yocto Project layersAll the SCM-related changes are collected in the new meta-nxp-imx-scm layer, which is obtained through the Repo sync pointing to the corresponding scm-imx branch.Make sure that GIT is set up properly with these commands:$ git config --global "Your Name"$ git config --global user.email "Your Email"$ git config --listThe NXP Yocto Project BSP Release directory contains the sources directory, which contains the recipes used to build, one (or more) build directories, and a set of scripts used to set up the environment. The recipes used to build the project come from both the community and NXP. The Yocto Project layers are downloaded to the sources directory. This sets up the recipes that are used to build the project. The following code snippets show how to set up the SCM L4.1.15-2.0.0_ga Yocto environment for the SCM-i.MX 6 QWKS board and the evaluation board. In this example, a directory called fsl-arm-yocto-bsp is created for the project. Any name can be used instead of this.Building Linux OS for SCM i.MX platforms3.2.1. SCM-i.MX 6D/Q quick start board$ mkdir fsl-arm-yocto-bsp$ cd fsl-arm-yocto-bsp$ repo init -u git:///imx/fsl-arm-yocto-bsp.git -b imx-4.1-krogoth -m scm-imx-4.1.15-2.0.0.xml$ repo sync3.2.2. SCM-i.MX 6SoloX evaluation board$ mkdir my-evb_6sxscm-yocto-bsp$ cd my-evb_6sxscm-yocto-bsp$ repo init -u git:///imx/fsl-arm-yocto-bsp.git -b imx-4.1-krogoth -m scm-imx-4.1.15-2.0.0.xml$ repo sync3.3. Building the Yocto imageNote that the quick start board for SCM-i.MX 6D/Q and the evaluation board for SCM-i.MX 6SoloX are commercially available with a 1 GB LPDDR2 PoP memory configuration.This release supports the imx6dqscm-1gb-qwks, imx6dqscm-1gb-qwks-rev3, and imx6sxscm-1gb-evb. Set the machine configuration in MACHINE= in the following section.3.3.1. Choosing a machineChoose the machine configuration that matches your reference board.•imx6dqscm-1gb-qwks (QWKS board for SCM-i.MX 6DQ with 1 GB LPDDR2 PoP)•imx6dqscm-1gb-qwks-rev3 (QWKS board Rev C for SCM-i.MX 6DQ with 1GB LPDDR2 PoP) •imx6sxscm-1gb-evb (EVB for SCM-i.MX 6SX with 1 GB LPDDR2 PoP)3.4. Choosing a graphical back endBefore the setup, choose a graphical back end. The default is X11.Choose one of these graphical back ends:•X11•Wayland: using the Weston compositor•XWayland•FrameBufferSpecify the machine configuration for each graphical back end.The following are examples of building the Yocto image for each back end using the QWKS board for SCM-i.MX 6D/Q and the evaluation board for SCM-i.MX 6SoloX. Do not forget to replace the machine configuration with what matches your reference board.3.4.1. X11 image on QWKS board Rev C for SCM-i.MX 6D/Q$ DISTRO=fsl-imx-x11 imx6dqscm-1gb-qwks-rev3 source fsl-setup-release.sh -b build-x11$ bitbake fsl-image-gui3.4.2. FrameBuffer image on evaluation board for SCM-i.MX 6SX$ DISTRO=fsl-imx-fb MACHINE=imx6sxscm-1gb-evb source fsl-setup-release.sh –b build-fb-evb_6sxscm$ bitbake fsl-image-qt53.4.3. XWayland image on QWKS board for SCM-i.MX 6D/Q$ DISTRO=fsl-imx-xwayland MACHINE=imx6dqscm-1gb-qwks source fsl-setup-release.sh –b build-xwayland$ bitbake fsl-image-gui3.4.4. Wayland image on QWKS board for SCM-i.MX 6D/Q$ DISTRO=fsl-imx-wayland MACHINE=imx6dqscm-1gb-qwks source fsl-setup-release.sh -b build-wayland$ bitbake fsl-image-qt5The fsl-setup-release script installs the meta-fsl-bsp-release layer and configures theDISTRO_FEATURES required to choose the graphical back end. The –b parameter specifies the build directory target. In this build directory, the conf directory that contains the local.conf file is created from the setup where the MACHINE and DISTRO_FEATURES are set. The meta-fslbsp-release layer is added into the bblayer.conf file in the conf directory under the build directory specified by the –e parameter.4. Deploying the imageAfter the build is complete, the created image resides in the <build directory>/tmp/deploy/images directory. The image is (for the most part) specific to the machine set in the environment setup. Each image build creates the U-Boot, kernel, and image type based on the IMAGE_FSTYPES defined in the machine configuration file. Most machine configurations provide the SD card image (.sdcard), ext4, and tar.bz2. The ext4 is the root file system only. The .sdcard image contains the U-Boot, kernel, and rootfs, completely set up for use on an SD card.4.1. Flashing the SD card imageThe SD card image provides the full system to boot with the U-Boot and kernel. To flash the SD card image, run this command:$ sudo dd if=<image name>.sdcard of=/dev/sd<partition> bs=1M && syncFor more information about flashing, see “P reparing an SD/MMC Card to Boot” in the i.MX Linux User's Guide (document IMXLUG).Specifying displays4.2. MFGTool (Manufacturing Tool)MFGTool is one of the ways to place the image on a device. To download the manufacturing tool for the SCM-i.MX 6D/Q and for details on how to use it, download the SCM-i.MX 6 Manufacturing Toolkit for Linux 4.1.15-2.0.0 under the "Downloads" tab from /qwks-scm-imx6dq. Similarly, download the manufacturing tool for the SCM-i.MX 6SoloX evaluation board under the "Downloads" tab from /evb-scm-imx6sx.5. Specifying displaysSpecify the display information on the Linux OS boot command line. It is not dependent on the source of the Linux OS image. If nothing is specified for the display, the settings in the device tree are used. Find the specific parameters in the i.MX 6 Release Notes L4.1.15-2.0.0 (available at L4.1.15-2.0.0_LINUX_DOCS). The examples are shown in the following subsections. Interrupt the auto-boot and enter the following commands.5.1.1. Display options for QWKS board for SCM-i.MX 6D/QHDMI displayU-Boot > setenv mmcargs 'setenv bootargs console=${console},${baudrate} ${smp}root=${mmcroot} video=mxcfb0:dev=hdmi,1920x1080M@60,if=RGB24'U-Boot > run bootcmd5.1.2. Display options for EVB for SCM-i.MX 6SXNote that the SCM-i.MX 6SX EVB supports HDMI with a HDMI accessory card (MCIMXHDMICARD) that plugs into the LCD connector on the EVB.Accessory boards:•The LVDS connector pairs with the NXP MCIMX-LVDS1 LCD display board.•The LCD expansion connector (parallel, 24-bit) pairs with the NXP MCIMXHDMICARD adapter board.LVDS displayU-Boot > setenv mmcargs 'setenv bootargs console=${console},${baudrate} ${smp}root=${mmcroot} ${dmfc} video=mxcfb0:dev=ldb,1024x768M@60,if=RGB666 ldb=sep0'U-Boot > run bootcmdHDMI display (dual display for the HDMI as primary and the LVDS as secondary)U-Boot > setenv mmcargs 'setenv bootargs console=${console},${baudrate} ${smp}root=${mmcroot} video=mxcfb0:dev=hdmi,1920x1080M@60,if=RGB24video=mxcfb1:dev=ldb,LDBXGA,if=RGB666'U-Boot > run bootcmdLCD displayu-boot > setenv mmcargs 'setenv bootargs ${bootargs}root=${mmcroot} rootwait rw video=mxcfb0:dev=lcd,if=RGB565'u-boot> run bootcmd6. Reset and boot switch configuration6.1. Boot switch settings for QWKS SCM-i.MX 6D/QThere are two push-button switches on the QWKS-SCMIMX6DQ board. SW1 (SW3 for QWKS board Rev B) is the system reset that resets the PMIC. SW2 is the i.MX 6Dual/6Quad on/off button that is needed for Android.There are three boot options. The board can boot either from the internal SPI-NOR flash inside the SCM-i.MX6Dual/6Quad or from either of the two SD card slots. The following table shows the switch settings for the boot options.Table 1.Boot configuration switch settingsBoot from top SD slot (SD3)Boot from bottom SD slot (SD2)Boot from internal SPI NORDefault1.References6.2. Boot switch settings for EVB SCM-i.MX 6SoloXThis table shows the jumper configuration to boot the evaluation board from the SD card slot SD3.7. SCM uboot and kernel repositoriesThe kernel and uboot patches for both SCM-i.MX 6 QWKS board and evaluation board are integrated in specific git repositories. Below are the git repos for SCM-i.MX 6 uboot and kernel:uBoot repo: /git/cgit.cgi/imx/uboot-imx.gitSCM Branch: scm-imx_v2016.03_4.1.15_2.0.0_gakernel repo: /git/cgit.cgi/imx/linux-imx.gitSCM branch: scm-imx_4.1.15_2.0.0_ga8. References1.For details about setting up the Host and Yocto Project, see the NXP Yocto Project User’s Guide(document IMXLXYOCTOUG).2.For information about downloading images using U-Boot, see “Downloading images usingU-Boot” in the i.MX Linux User's Guide (document IMXLUG).3.For information about setting up the SD/MMC card, see “P reparing an SD/MMC card to boot” inthe i.MX Linux User's Guide (document IMXLUG).9. Revision historyDocument Number: SCMIMX6LRNUGRev. L4.1.15-2.0.0-ga04/2017How to Reach Us: Home Page: Web Support: /supportInformation in this document is provided solely to enable system and softwareimplementers to use NXP products. There are no express or implied copyright licenses granted hereunder to design or fabricate any integrated circuits based on the information in this document. NXP reserves the right to make changes without further notice to any products herein.NXP makes no warranty, representation, or guarantee regarding the suitability of its products for any particular purpose, nor does NXP assume any liability arising out of the application or use of any product or circuit, and specifically disclaims any and all liability, including without limitation consequentia l or incidental damages. “Typical”parameters that may be provided in NXP data sheets and/or specifications can and do vary in different applications, and actual performance may vary over time. All operating parameters, including “typicals,” must be valida ted for each customer application by customer’s technical experts. NXP does not convey any license under its patent rights nor the rights of others. NXP sells products pursuant to standard terms and conditions of sale, which can be found at the following address: /SalesTermsandConditions .NXP, the NXP logo, NXP SECURE CONNECTIONS FOR A SMARTER WORLD, Freescale, and the Freescale logo are trademarks of NXP B.V. All other product or service names are the property of their respective owners.ARM, the ARM Powered logo, and Cortex are registered trademarks of ARM Limited (or its subsidiaries) in the EU and/or elsewhere. All rights reserved. © 2017 NXP B.V.。
Manual Addendum for VMX-B Configured Soft Start Pa

Manual Addendum for VMX-B Configured Soft Start PackagesFor use with wiring diagram # 93-3880 Rev B (CB/FS), or 93-3881 Rev B (MLO), and VMX2 user manual. Introduction: The VMX-B is a configured enclosed soft start, available as a Combination (with C/B or Fused disconnect) package, or as an MLO (Main Lug Only) package, intended for use in Industrial, Commercial, Agricultural, or Infrastructure applications.Line Voltage:By default units are set-up for 460VAC line power, but can be adjusted to operate on 230VAC or208VAC at the reduced HP rating. To adjust the operating voltage simply move wire #1L2B from the 480V (H4) terminal to the 230V (H3) or 208V (H2) terminal.Power Connections:Line Power input is connected directly to the bottom terminals of the Circuit Breaker, or line terminals on MLO (Main Lug Only) units, and the motor is connected to the lugs at the bottom of the VMX2 soft start.Remote Start / Stop Control connections:The VMX-B is set up for 2 or 3 wire remote control using dry contacts rated at 120VAC (0.1Amp).Remote Two Wire Control:Connect a dry (voltage free) maintained contact closure between terminals 1 and 3 of the customerterminal strip as shown here.123456789RUNCustomer Terminals TBC on TCB3000 PCBRemote Three Wire Control:For standard 3-wire control, connect dry (voltage free) contacts for the Stop / Start buttons as shown below of the customer terminal strip. Connect the normally closed “STOP” pushbutton across terminals 1 & 2, and the normally open “START” pushbutton across terminal s 2 & 3 of the customer terminal strip. Note: the unit can be operated in the “Local” position without any external control.123456789STOPCustomer Terminals TBC on TCB3000 PCBSee page 3.TCB3000 Terminal Control BoardSee page 3.TCB3000 Terminal Control BoardRun Status Output ContactsThe VMX-B unit offers 2 Form-C (N.O and N.C.) “RUN” contacts located on the custom er terminal strip, terminals 4 (NC), 5 (NO), 6 (Common), and terminals 7 (NC), 8 (NO) 9 (Common). These contacts reflect a successful RUN command in “SOFT” or “X -LINE” mode, and should be used for any required “Run / Running” status outputs.VMX2 Auxiliary Contacts(TB2 of Soft Starter)NOTE: YELLOWOVERLOAD DIAL MUST BE SET IN ACCORDANCE WITH THE MOTOR “FULL LOAD AMPS” PER MOTOR NAME PLATE DATAThere are 3 programmable Aux contacts available on TB2 of the VMX2 soft start (2 form-C and 1 form-A). The function of these contacts are labeled on the wiring diagrams, but can be changed in the VMX2 programming. Note however, that the contacts may not function properly when operating in the X-LINE mode. (see description below).X-LINE Operation:VMX-B packages are supplied with a SOFT/X-LINE selector switch, located on the TCB3000 PCB that allows the operator to select Full Voltage operation of the motor via the bypass contactor for emergency operation when the soft start may be inoperable.When operated in the X-LINE mode fullstart/stop control is maintained, and the “Run Status Output Contacts” will func tion correctly.During X-LINE operation, the motor will be protected by the external Bi-Metal overload relay which must be set according to the motor FLA and the Current transformer ratio of the unit.Important:Motor FLA and Service Factor must be entered prior to a start attempt see next section on how to set Motor FLA and Service Factor parameters.123456789Customer Terminals TBC on TCB3000 PCB Run StatusOutput ContactsSee page 3. TCB3000 Terminal Control BoardTCB3000 Terminal BoardGreen LED-Control Power ON-E-Stop Not Active-Fuse OKGreen LEDMotor RunningYellow LEDX-Line Mode Enabled(D.O.L. Start)Red LEDFault(Unit Tripped requiresReset Command)Red LEDExternal O/L Tripped(Reset O/L Manuallyby pressing greenbutton on overloadrelay).Programming InstructionsThis document is intended for use with Models: VMX-B Soft Start PackagesMotor FLA and Service Factor must be entered prior to start attemptFor complete parameter list see pages 6-7 of this documentFnRead0000F0010009 000000090179End F001Default Display Function #1Set value of ones digit (flashing) Cursor Position Shift Use up arrow to scroll to F002 and repeat process ReadEntering Motor FLA & SFOperation and TroubleshootingKeypad Operation Display Mode (Default)Fault Mode*NOTES:“PLd” can be caused by a Grounded delta power system. If one input leg me asures ZERO volts to ground, reduce the setting of F051 to “0054” for operation on a “Grounded Delta”.“SS d ” can be caused by operating without a motor connected, ensure the motor is firmly connected.“LcA, Lcc, or Lcd ” indicates that the Surge absorber is damaged; see NOTE 1 on wiring diagram.VMX-B Door Mounted OperatorsIlluminated E-Stop Pushbutton:∙Removes control power from all circuits and VMX2 soft start.∙Push to activate, twist and pull to release.∙Button Lights when E-stop is pressed.Start/Stop Pushbutton and Run Light Assembly:∙Provides Start/Stop control in "Local" mode.∙Provides "Motor Running" indication in all operating modes.Local/Off/Remote Selector:∙Local" selects door mounted Start/Stop control.∙Remote" selects Start/Stop control from customer supplied signals at terminals 1-3 on TBC.∙Off' Turns motor off.Power ON Light:∙Indicates presence of 120VAC control power, derived from main (L1 & L2) line voltages.Fault Light/Reset Pushbutton:∙When lit, indicates that the unit has tripped, and requires "Reset".∙In "Soft" (normal) mode, the "trip" will be displayed on the VMX2 keypad (inside), and will reset upon activation of the reset pushbutton.∙In "X-Iine" mode, the light indicates that the X-line overload inside the panel is tripped, and must be reset manually by pressing the (green) reset key on the overload itself. Then the unit can be reset, using the pushbutton on the door.Note: If the green reset key on the X-line overload is turned to the "A" (auto) position, the O/L relay will reset itself after the required cooldown, after that the unit can be reset by pushing the reset pushbutton without opening the enclosure door.Wiring Diagram # 93-398011REV-02 100418Wiring Diagram # 93-3981。
H3C S5800 版本说明书

H3C S5800_5820X-CMW520-R1810P16 版本说明书Copyright © 2018新华三技术有限公司版权所有,保留一切权利。
非经本公司书面许可,任何单位和个人不得擅自摘抄、复制本文档内容的部分或全部,并不得以任何形式传播。
本文档中的信息可能变动,恕不另行通知。
目录1 版本信息 (1)1.1 版本号 (1)1.2 历史版本信息 (1)1.3 版本配套表 (4)1.4 ISSU版本兼容列表 (5)1.5 版本升级注意事项 (6)2 硬件特性变更说明 (6)2.1 R1810P16版本硬件特性变更说明 (6)2.2 R1810P13版本硬件特性变更说明 (6)2.3 R1810P12版本硬件特性变更说明 (6)2.4 R1810P10版本硬件特性变更说明 (6)2.5 R1810P08版本硬件特性变更说明 (7)2.6 R1810P06版本硬件特性变更说明 (7)2.7 R1810P05版本硬件特性变更说明 (7)2.8 R1810版本硬件特性变更说明 (7)2.9 R1809P11版本硬件特性变更说明 (7)2.10 R1809P10版本硬件特性变更说明 (7)2.11 R1809P09版本硬件特性变更说明 (7)2.12 R1809P06版本硬件特性变更说明 (7)2.13 R1809P05版本硬件特性变更说明 (7)2.14 R1809P03版本硬件特性变更说明 (7)2.15 R1809P01版本硬件特性变更说明 (7)2.16 R1808P27版本硬件特性变更说明 (8)2.17 R1808P25版本硬件特性变更说明 (8)2.18 R1808P23版本硬件特性变更说明 (8)2.19 R1808P22版本硬件特性变更说明 (8)2.20 R1808P21版本硬件特性变更说明 (8)2.21 R1808P17版本硬件特性变更说明 (8)2.22 R1808P15版本硬件特性变更说明 (8)2.23 R1808P13版本硬件特性变更说明 (8)2.24 R1808P11版本硬件特性变更说明 (8)2.25 R1808P08版本硬件特性变更说明 (8)2.26 R1808P06版本硬件特性变更说明 (8)i2.29 F1807P01版本硬件特性变更说明 (9)2.30 R1805P02版本硬件特性变更说明 (9)2.31 R1211P08版本硬件特性变更说明 (9)2.32 R1211P06版本硬件特性变更说明 (9)2.33 R1211P03版本硬件特性变更说明 (9)2.34 R1211P02版本硬件特性变更说明 (9)2.35 R1211版本硬件特性变更说明 (9)2.36 F1209P01版本硬件特性变更说明 (9)2.37 F1209版本硬件特性变更说明 (9)2.38 F1208版本硬件特性变更说明 (10)2.39 F1207版本硬件特性变更说明 (10)2.40 R1206版本硬件特性变更说明 (10)2.41 R1110P05版本硬件特性变更说明 (10)2.42 R1110P04版本硬件特性变更说明 (10)3 软件特性及命令行变更说明 (10)4 MIB变更说明 (10)5 操作方式变更说明 (16)5.1 R1810P16版本操作方式变更 (16)5.2 R1810P13版本操作方式变更 (16)5.3 R1810P12版本操作方式变更 (16)5.4 R1810P10版本操作方式变更 (16)5.5 R1810P08版本操作方式变更 (17)5.6 R1810P06版本操作方式变更 (17)5.7 R1810P05版本操作方式变更 (17)5.8 R1810版本操作方式变更 (17)5.9 R1809P11版本操作方式变更 (17)5.10 R1809P10版本操作方式变更 (17)5.11 R1809P09版本操作方式变更 (17)5.12 R1809P06版本操作方式变更 (17)5.13 R1809P05版本操作方式变更 (18)5.14 R1809P03版本操作方式变更 (18)5.15 R1809P01版本操作方式变更 (18)5.16 R1808P27版本操作方式变更 (18)5.17 R1808P25版本操作方式变更 (18)ii5.20 R1808P21版本操作方式变更 (18)5.21 R1808P17版本操作方式变更 (19)5.22 R1808P15版本操作方式变更 (19)5.23 R1808P13版本操作方式变更 (19)5.24 R1808P11版本操作方式变更 (19)5.25 R1808P08版本操作方式变更 (19)5.26 R1808P06版本操作方式变更 (19)5.27 R1808P02版本操作方式变更 (19)5.28 R1807P02版本操作方式变更 (20)5.29 F1807P01版本操作方式变更 (20)5.30 R1805P02版本操作方式变更 (20)5.31 R1211P08版本操作方式变更 (20)5.32 R1211P06版本操作方式变更 (21)5.33 R1211P03版本操作方式变更 (21)5.34 R1211P02版本操作方式变更 (21)5.35 R1211版本操作方式变更 (21)5.36 F1209P01版本操作方式变更 (21)5.37 F1209版本操作方式变更 (21)5.38 F1208版本操作方式变更 (21)5.39 F1207版本操作方式变更 (22)5.40 R1206版本操作方式变更 (22)5.41 R1110P05版本操作方式变更 (22)5.42 R1110P04版本操作方式变更 (23)6 版本使用限制及注意事项 (23)7 存在问题与规避措施 (23)8 解决问题列表 (24)8.1 R1810P16版本解决问题列表 (24)8.2 R1810P13版本解决问题列表 (24)8.3 R1810P12版本解决问题列表 (25)8.4 R1810P10版本解决问题列表 (26)8.5 R1810P08版本解决问题列表 (27)8.6 R1810P06版本解决问题列表 (28)8.7 R1810P05版本解决问题列表 (28)8.8 R1810版本解决问题列表 (28)iii8.11 R1809P09版本解决问题列表 (30)8.12 R1809P06版本解决问题列表 (31)8.13 R1809P05版本解决问题列表 (32)8.14 R1809P03版本解决问题列表 (33)8.15 R1809P01版本解决问题列表 (34)8.16 R1808P27版本解决问题列表 (36)8.17 R1808P25版本解决问题列表 (36)8.18 R1808P23版本解决问题列表 (38)8.19 R1808P22版本解决问题列表 (38)8.20 R1808P21版本解决问题列表 (39)8.21 R1808P17版本解决问题列表 (39)8.22 R1808P15版本解决问题列表 (40)8.23 R1808P13版本解决问题列表 (41)8.24 R1808P11版本解决问题列表 (42)8.25 R1808P08版本解决问题列表 (44)8.26 R1808P06版本解决问题列表 (44)8.27 R1808P02版本解决问题列表 (46)8.28 R1807P02版本解决问题列表 (49)8.29 F1807P01版本解决问题列表 (50)8.30 R1805P02版本解决问题列表 (50)8.31 R1211P08版本解决问题列表 (53)8.32 R1211P06版本解决问题列表 (53)8.33 R1211P03版本解决问题列表 (57)8.34 R1211P02版本解决问题列表 (57)8.35 R1211版本解决问题列表 (58)8.36 F1209P01版本解决问题列表 (62)8.37 F1209版本解决问题列表 (62)8.38 F1208版本解决问题列表 (63)8.39 F1207版本解决问题列表 (65)8.40 R1206版本解决问题列表 (65)8.41 R1110P05版本解决问题列表 (66)8.42 R1110P04版本解决问题列表 (68)9 相关资料 (70)9.1 相关资料清单 (70)iv10 技术支持 (70)附录 A 本版本支持的软、硬件特性列表 (71)A.1 版本硬件特性 (71)A.2 版本软件特性 (73)附录 B 版本升级操作指导 (84)B.1 简介 (84)B.2 软件加载方式简介 (84)B.3 BootRom界面加载 (85)B.3.1 BootRom界面介绍 (85)B.3.2 通过Console口利用XModem完成加载 (89)B.3.3 通过以太网口利用TFTP完成加载 (100)B.3.4 通过以太网口利用FTP完成加载 (103)B.4 命令行接口加载 (107)B.4.1 通过USB口实现软件加载 (107)B.4.2 通过FTP实现软件加载 (107)B.4.3 通过TFTP实现软件加载 (109)v表目录表1 历史版本信息表 (1)表2 版本配套表 (4)表3 ISSU版本兼容列表 (5)表4 MIB文件变更说明 (10)表5 S5800系列产品硬件特性 (71)表6 S5820X系列产品硬件特性 (72)表7 S5800系列产品软件特性 (73)表8 S5820X系列产品软件特性 (79)表9 交换机软件加载方式一览表 (84)表10 基本BOOT菜单说明 (86)表11 基本BOOT辅助菜单说明 (86)表12 扩展BOOT菜单说明 (87)表13 扩展BOOT辅助菜单说明 (89)表14 通过Console口利用XModem加载系统文件 (93)表15 BootRom升级选择菜单 (94)表16 协议选择及参数设置菜单 (95)表17 通过以太网口利用TFTP加载系统文件 (100)表18 TFTP协议相关参数的设置说明 (102)表19 通过以太网口利用FTP加载系统文件 (104)表20 FTP协议相关参数的设置说明 (105)vi本文介绍了H3C S5800_5820X-CMW520-R1810P16版本的特性、使用限制、存在问题及规避措施等,在加载此版本前,建议您备份配置文件,并进行内部验证,以避免可能存在的风险。
AIX上从MQ 9.0.0.1升级到MQ 9.1.0.0 LTS说明书

Upgrading in AIX from MQ 9.0.0.1 to MQ 9.1.0.0 LTShttps:///support/pages/node/6415777Date last updated: 16-Feb-2021Angel Rivera –r i v e r a@u s.i b m.c o mIBM MQ Support+++ ObjectiveThis tutorial shows all the steps to upgrade in AIX, from MQ 9.0.0.1 Long Term Support (LTS) to MQ 9.1.0.0 LTS.This is a straight upgrade and does not exploit the 'multi-version' feature in which several versions of MQ can co-exist ("side-by-side").The upgrade instructions apply also for MQ 9.2.Notes about older releases:- You can upgrade from MQ 8.0 to MQ 9.1 without first going through MQ 9.0.- You can upgrade from MQ 8.0 to MQ 9.2 without first going through MQ 9.0 orMQ 9.1.- You cannot migrate directly from MQ 7.x to MQ 9.1 or MQ 9.2:- If you are using MQ 7.0, then you will need to upgrade to MQ 8.0, then to MQ 9.1 or MQ 9.2- If you are using MQ 7.1 or MQ 7.5, then you will need to upgrade to MQ 8.0 orMQ 9.0, then to MQ 9.1 or MQ 9.2.Prior to the upgrade, you need to take a full backup of your MQ 9.0 queue managers. Why? Because the upgrade of MQ, such as from MQ 9.0 to MQ 9.1 is NOT reversible.If you need to back out and revert back to MQ 9.0, you will need to delete the upgraded MQ 9.1 queue managers and restore the MQ 9.0 queue managers from backup.The chapters are:Chapter 1: How to get the installation imagesChapter 2: Take a backup of the queue manager data and recovery logsChapter 3: Uninstalling MQ 9.0Chapter 4: Installing MQ 9.1.0.0 LTSChapter 5: Running setmqenv to use MQ 9.1 commandsChapter 6: Creating a queue manager under 9.1Chapter 7: Upgrading an existing queue manager to MQ 9.1++ Overall tasksThe straight upgrade from MQ 9.0 to MQ 9.1 means that only one version of MQ will be available under /usr/mqm.It is necessary to:- uninstall MQ 9.0- and then install MQ 9.1These tasks do NOT alter the contents of /var/mqm (which contains the data for the queue managers). That is, when you uninstall the product from /usr/mqm, the queue managers are NOT deleted.++ Related tutorialshttps:///support/pages/node/6407842Summary of AIX commands to administrate MQhttps:///support/pages/node/6407850Installing in AIX - MQ 9.0.0.1 LTS, applying Fix Pack 9.0.0.11, Uninstalling MQ++ For more information on what new attributes, queues and system objects were introduced in MQ 9.1 and MQ 9.2, see the following technotes:https:///support/pages/node/213019New SYSTEM queues added in MQ 7.1, 7.5, 8.0, 9.0, 9.0.1, 9.1 and 9.2https:///support/pages/node/198031New MQ 7.1, 7.5, 8.0, 9.0, 9.1 and 9.2 attributes in DISPLAY QMGR for new or migrated queue managershttps:///support/pages/node/487355New objects and new attributes for objects in MQ 7.1, 7.5, 8.0, 9.0, 9.0.1, 9.1 and 9.2++ For more information on what is new and what has changed after MQ 8.0, see: https:///support/knowledgecenter/SSFKSJ_9.2.0/com.ibm.mq.sec.doc /q014265_.htmlIBM MQ 9.2.x / IBM MQ / Securing / Confidentiality of messages /Enabling CipherSpecs /Deprecated CipherSpecshttps:///support/knowledgecenter/SSFKSJ_9.2.0/com.ibm.mq.pro.doc /q113110_.htmlIBM MQ 9.2.x / IBM MQ / About IBM MQ /What's new and changed in IBM MQ 9.2.0https:///support/knowledgecenter/SSFKSJ_9.1.0/com.ibm.mq.pro.doc /q113110_.htm#q113110_IBM MQ 9.1.x / IBM MQ / About IBM MQ /What's new and changed in IBM MQ Version 9.1.0++ Note about the licensing1) The following web page from the online manual for MQ has some information on MQ Licenses:https:///support/knowledgecenter/SSFKSJ_9.1.0/com.ibm.mq.pro.doc /q126140_.htmIBM MQ 9.1.x / IBM MQ / About IBM MQ /IBM MQ license information2) You need to have an active subscription to upgrade to newer versions of MQ.If you have questions about licenses and entitlement please consult with your IBM Sales representative.++ Information about the version of AIX used for this tutorial+ROOT+ aglet: /downloads/mq9001# uname -aAIX aglet 2 7 00F944604C00+ROOT+ aglet: /downloads/mq9001# oslevel7.2.0.0+ROOT+ aglet: /downloads/mq9001# oslevel -s7200-05-01-2038++ Current setup of MQ 9.0MQ 9.0 already installed in the default location:/usr/mqmThe data for the queue managers is stored in:/var/mqmThe Queue Managers are:QM90 => Already created with MQ 9.0. To be migrated to MQ 9.1.QM91 => To be created with MQ 9.1.+++ Chapter 1: How to get the installation images++++++++++++++++++++++++++++++++++++++++++++++++++++++++++++++++++ Summary of Part Numbers for MQ on AIX 9.x from IBM Passport Advantage https:///software/passportadvantage/pao_customer.htmlIBM Passport Advantage for the MQ server images:Part Number: CNRD6MLDescription: IBM MQ V9.1.0.0 for AIX eImagePart Number: CC5TPMLDescription: IBM MQ V9.2.0.0 Long Term Support Release for AIX eImage++ MQ 9.1.0.0 (full install) - from IBM Passport Advantagehttps:///support/pages/downloading-ibm-mq-910-older-fix-packs Downloading IBM MQ 9.1.0: Older Fix PacksScroll down to the link:Downloading IBM MQ 9.1.0It is recommended that you search for Part Number, which will provide a more focused list.Part Number: CNRD6MLDescription: IBM MQ 9.1 for AIX eImageDownloaded image name MQ 9.1.0.0:IBM_MQ_9.1_AIX.tar.gzLocal Directory:/downloads/mq9100+++ Chapter 2: Take a backup of the queue manager data and recovery logs++++++++++++++++++++++++++++++++++++++++++++++++++++++++++++++++Take a backup of /var/mqm and any other file system that is used (such as mounted, or via symbolic links) for the storage of the MQ recovery logs and the MQ data for the queue managers.If the queue manager is created in a non-default directory (such as Multi-Instance), ensure that all queue manager data and logs are included in the backup based on the configuration in mqs.ini and qm.ini files.When an MQ 9.0 queue manager is upgraded to MQ 9.1, it goes through some migration steps that are NOT reversible.If for some reason you want to back out later on your upgrade MQ queue manager (at 9.1) back to 9.0, you will NOT be able to use the current data in /var/mqm and you will need to restore from the backup taken when the MQ queue manager was at 9.0. Disclaimer:The MQ Support teams do not recommend or support the action to revert to an earlier version of the product.If any problem were to occur after upgrading to MQ 9.1, the best way to address the situation is to contact MQ Support and get that fixed, rather than by reverting to version MQ 9.0.Given the above disclaimer, please review the following technotes which explain more details on the topic.https:///support/pages/node/88035After upgrading from MQ 5.3 to V6/V7, or from MQ V6 to V7, you want to revert back to previous level++ Reference tutorial for backup in Linux (applicable to AIX)https:///support/pages/node/6114082Backup of an MQ queue manager to move files from one Linux host to another Linux hostThe quick description of the procedure is to take a backup of the files from host-1 and restore them in host-2.+++ Chapter 3: Uninstalling MQ 9.0++++++++++++++++++++++++++++++++++++++++++++++++++++++++++++++++++ Stop all MQ activityAs an MQ Administrator stop the queue managers and clients.For details see the Steps 1 and 2:https:///support/knowledgecenter/SSFKSJ_9.0.0/com.ibm.mq.ins.doc/ q009420_.htmIBM MQ 9.0.x / IBM MQ / Installing and uninstalling / Installing and uninstalling IBM MQ on AIX /Uninstalling or modifying IBM MQ on AIX++ Uninstall the filesetsAs user root proceed with the rest of the steps from the web page mentioned above. Step 3: Log in as root.Step 4: Uninstall or modify IBM MQ using either installp or smit. If IBM MQ was installed in a non-default location, you must use installp.To uninstall or modify IBM MQ by using installp, enter one of the following commands: - To uninstall an installation in the default location /usr/mqm:installp -u mqm- To uninstall an installation in a non-default location:installp -R usil -u mqmwhere usil is the path of the User Specified Installation Location (USIL) specified when the product was installed.The full listing of the uninstall is not included in this current tutorial.But if you want to see the equivalent full listing for the uninstallation of MQ 9.0.0.1 see the companion tutorial:https:///support/pages/node/6407850Installing in AIX - MQ 9.0.0.1 LTS, applying Fix Pack 9.0.0.11, Uninstalling MQ Chapter 9: Appendices showing full output from installp for the scenariosSection 4: Uninstallation of base 9.0.0.1 (Chapter 8)Next step:Ensure that there are no more MQ filesets shown as installed:# lslpp -la "mqm*"lslpp: 0504-132 Fileset mqm* not installed.# ls /usr/mqmls: 0653-341 The file /usr/mqm does not exist.Notice that the mqinst.ini file was updated (the 2 lines about being Primary installation were removed).# cat /etc/opt/mqm/mqinst.iniInstallation:Name=Installation1Description=Identifier=1FilePath=/usr/mqmNow that there are no MQ installations, it is recommended to delete the mqinst.ini file.It will be recreated when MQ 9.1 is installed.# rm /etc/opt/mqm/mqinst.ini# ls /etc/opt/mqm/mqinst.inils: 0653-341 The file /etc/opt/mqm/mqinst.ini does not exist.+++++++++++++++++++++++++++++++++++++++++++++++++++++++++++++++++++ Chapter 4: Installing MQ 9.1.0.0 LTS++++++++++++++++++++++++++++++++++++++++++++++++++++++++++++++++++ Downloading the MQ 9.1.0.0 LTS codeSee Chapter 1: How to get the installation imagesPart Number: CNRD6MLDescription: IBM MQ 9.1 for AIX eImageDownloaded image name MQ 9.1.0.0:IBM_MQ_9.1_AIX.tar.gzLocal Directory:/downloads/mq9100++ Installing MQ 9.1 into /usr/mqmYou need to login as root.Go to the local directory where the file with the MQ 9.0.0.1 code is located (see Chapter 1)# cd /downloads/mq9100Unpack the file:# gunzip IBM_MQ_9.1_AIX.tar.gz# tar -xvf IBM_MQ_9.1_AIX.tarNotice that the extracted files are located into a new directory: MQServer# ls -1FIBM_MQ_9.1_AIX.tarMQServer/Change to the MQServer directory:# cd MQServerInstall the code:# installp -acgXYd . all+-----------------------------------------------------------------------------+ Pre-installation Verification...+-----------------------------------------------------------------------------+ Verifying selections...doneVerifying requisites...doneResults...…+-----------------------------------------------------------------------------+Summaries:+-----------------------------------------------------------------------------+ Installation Summary--------------------Name Level Part Event Result------------------------------------------------------------------------------- mqm.base.runtime 9.1.0.0 USR APPLY SUCCESSmqm.base.runtime 9.1.0.0 ROOT APPLY SUCCESSmqm.server.rte 9.1.0.0 USR APPLY SUCCESS…The full listing of the uninstall is not included in this current tutorial.But if you want to see the equivalent full listing for the uninstallation of MQ 9.0.0.1 see the companion tutorial:https:///support/pages/node/6407850Installing in AIX - MQ 9.0.0.1 LTS, applying Fix Pack 9.0.0.11, Uninstalling MQ Chapter 9: Appendices showing full output from installp for the scenariosSection 1: Installation of base 9.0.0.1 (See Chapter 3)The AIX installation database will indicate that MQ is installed:# lslpp -la "mqm*"Fileset Level State Description---------------------------------------------------------------------------- Path: /usr/lib/objreposmqm.amqp.rte 9.1.0.0 COMMITTED IBM MQ AMQP Servicemqm.ams.rte 9.1.0.0 COMMITTED IBM MQ Advanced - AdvancedMessage Securitymqm.base.runtime 9.1.0.0 COMMITTED IBM MQ Runtime for Client andServermqm.base.samples 9.1.0.0 COMMITTED IBM MQ Samplesmqm.base.sdk 9.1.0.0 COMMITTED IBM MQ Base Kit for Client and…mqm.server.rte 9.1.0.0 COMMITTED IBM MQ Servermqm.web.rte 9.1.0.0 COMMITTED IBM MQ REST API and Consolemqm.xr.service 9.1.0.0 COMMITTED IBM MQ Advanced - TelemetryServicePath: /etc/objreposmqm.base.runtime 9.1.0.0 COMMITTED IBM MQ Runtime for Client andServerPath: /usr/share/lib/objreposmqm.man.en_US.data 9.1.0.0 COMMITTED IBM MQ Man Pages - U.S.EnglishNotice that the mqinst.ini is recreated: # cat /etc/opt/mqm/mqinst.ini Installation:Name=Installation1Description=Identifier=1FilePath=/usr/mqm# /usr/mqm/bin/dspmqinst InstName: Installation1 InstDesc:Identifier: 1InstPath: /opt/mqmVersion: 9.1.0.0Primary: NoState: Available+++++++++++++++++++++++++++++++++++++++++++++++++++++++++++ Chapter 5: Running setmqenv to use MQ 9.1 commands++++++++++++++++++++++++++++++++++++++++++++++++++++++++Now that we finished with the root activities, we can login as an MQ administrator. You can use the following new MQ command to display the information on the installation.mqm@aglet: /home/mqm$ dspmqinstInstName: Installation1InstDesc:Identifier: 1InstPath: /usr/mqmVersion: 9.1.0.0Primary: NoState: Availablemqm@aglet: /home/mqm$ dspmqverName: IBM MQVersion: 9.1.0.0Level: p910-L180705BuildType: IKAP - (Production)Platform: IBM MQ for AIXMode: 64-bitO/S: AIX 7.2InstName: Installation1InstDesc:Primary: NoInstPath: /usr/mqmDataPath: /var/mqmMaxCmdLevel: 910LicenseType: ProductionYou need to run the following MQ command to setup the MQ environment variables: setmqenvBefore running "setmqenv", the following command did not return any entries for environment variables that have "MQ" or "mq" in the names:$ set | grep -i mq(no items returned)It is a bit tricky to invoke the setmqenv command.You need to "source" (run "inline") the utility setmqenv by specifying a leading . (dot) and a blank:$ . /usr/mqm/bin/setmqenv -n Installation1| || +--- blank+--- dotThese are the changes made in the environment by this utility:+ Hint:You can create a script that will run the setmqenv command with the specified syntax.Its usage is an overkill when having only 1 installation in the system, but it becomes very useful if you decide to exploit the multi-version features later on.For example, the script $HOME/bin/set-mq-91 can be created with the contents: $ mkdir $HOME/bin$ cd $HOME/bin$ vi set-mq-91============= begin script# Name: set-mq-91# Purpose: to setup the environment to run MQ 9.1. /usr/mqm/bin/setmqenv -n Installation1# Additional MQ directories for the PATHexportPATH=$PATH:$MQ_INSTALLATION_PATH/java/bin:$MQ_INSTALLATION_PATH/ samp/bin:$MQ_INSTALLATION_PATH/samp/jms/samples:# Add local directory for running Java/JMS programsexport CLASSPATH=$CLASSPATH:.# Display the full fix pack leveldspmqver -f 2# end============= end of scriptNotice that additional directories are included in the PATH. This is going to be explained later. The setmqenv will setup the proper directory forMQ_INSTALLATION_PATH.You will need to specify the script as executable:$ chmod 755 $HOME/bin/set-mq-91You will need to add $HOME/bin in the PATH in your .bashrc or .profile: export PATH=$PATH:$HOME/bin:.You will need to invoke the script with the leading dot!$ . set-mq-91| || +--- blank+--- dot+++ Hint for your bashrc or profileYou can add into your bashrc or profile file the following:. set-mq-91+++++++++++++++++++++++++++++++++++++++++++++++++++++++++++ Chapter 6: Creating a queue manager under 9.1++++++++++++++++++++++++++++++++++++++++++++++++++++++++Let's create a new queue manager. Notice the new line shown in bold font that indicates that Installation1 is used:$ crtmqm -u SYSTEM.DEAD.LETTER.QUEUE QM91IBM MQ queue manager created.Directory '/var/mqm/qmgrs/QM91' created.The queue manager is associated with installation 'Installation1'.Creating or replacing default objects for queue manager 'QM91'.Default objects statistics : 84 created. 0 replaced. 0 failed.Completing setup.Setup completed.Start the queue manager. Notice the lines that indicate the installation and the version under which the queue manager is running:$ strmqm QM91IBM MQ queue manager 'QM91' starting.The queue manager is associated with installation 'Installation1'.5 log records accessed on queue manager 'QM91' during the log replay phase. Log replay for queue manager 'QM91' complete.Transaction manager state recovered for queue manager 'QM91'.IBM MQ queue manager 'QM91' started using V9.1.0.0.Let's display the status$ dspmq -m QM91QMNAME(QM91) STATUS(Running)Let's do a more advanced display of status.$ dspmq -o installation -s -m QM91QMNAME(QM91) STATUS(Running)INSTNAME(Installation1) INSTPATH(/usr/mqm) INSTVER(9.1.0.0)++++++++++++++++++++++++++++++++++++++++++++++++++++++++++++++++++++++++ +++ Chapter 7: Upgrading an existing queue manager from MQ 9.0 to MQ 9.1++++++++++++++++++++++++++++++++++++++++++++++++++++++++++++++++++++++++ Let's display the status of the queue managers.$ dspmqQMNAME(QM90) STATUS(Ended immediately) QMNAME(QM91) STATUS(Running)Notice that the QM90 queue manager was created with MQ 9.0 and its data is still for MQ 9.0.To migrate QM90 from MQ 9.0 to MQ 9.1, you need to start the queue manager with the MQ 9.1 code.The strmqm command will detect that the data needs to be upgraded and it will proceed to upgrade the data.NOTE: The upgrade of the data is NOT reversible!$ strmqm QM90IBM MQ queue manager 'QM90' starting.The queue manager is associated with installation 'Installation1'.5 log records accessed on queue manager 'QM90' during the log replay phase.Log replay for queue manager 'QM90' complete.Transaction manager state recovered for queue manager 'QM90'.Migrating objects for queue manager 'QM90'.Default objects statistics : 1 created. 0 replaced. 0 failed.IBM MQ queue manager 'QM90' started using V9.1.0.0.Let's display the status:$ dspmqQMNAME(QM90) STATUS(Running)QMNAME(QM91) STATUS(Running)- Now display some relevant attributes for the queue manager using runmqsc. Notice the CMDLEVEL and the new VERSION fields:$ runmqsc QM901 : DISPLAY QMGR CMDLEVEL VERSIONAMQ8408I: Display Queue Manager details.QMNAME(QM90) CMDLEVEL(910)VERSION(09010007)+++ end +++。
MSR57P Guardmaster速度监控安全传感器关联系统更新指南说明书

Release NotesMSR57P Guardmaster Speed Monitoring Safety RelayFirmware UpdateCatalog Number 440R-S845AER-NNLAbout This PublicationThis document explains how to install new firmware into the MSR57P safety relay. These release notes correspond to revision 1.006 of the MSR57P firmware.Before You Begin The procedure assumes that you have DriveExplorer software, version5.02.07 or later, installed on your computer and you have successfullyconnected to the MSR57P relay.Topic Page About This Publication 1Before You Begin 1Download the Firmware Update File 2Corrected Anomaly 3Update Firmware 3Confirm the Update 6Download Your Saved Configuration File 6Additional Resources 7TIP If you do not have DriveExplorer software, you can download the freeversion, DriveExplorer Lite, at /drives/driveexplorer/free_ing USB Converter Using Serial ConverterDriveExplorer Software2MSR57P Guardmaster Speed Monitoring Safety Relay Firmware UpdateSave Your MSR57P Configuration to Your Computerunch DriveExplorer software and connect to the relay.2.In the tree view, expand the MSR57P relay.3.Expand the Parameter groups and select the Security group.4.Place the relay in Run mode by setting the P6 [Operating Mode]parameter to 1.5.Record the value of the P10 [Signature ID] parameter.You will need to verify that this value is unchanged after youreload your configuration following the update.6.From the Actions menu, choose Upload and Save to save yourconfiguration.7.Browse to the directory where you want to save your file. the file and click Save.This is the current configuration of the MSR57P relay. Once thefirmware update is complete, you can download thisconfiguration back into the relay.Download the Firmware Update File Follow these steps to obtain the firmware upgrade file.1.Go to/support/firmware.htmland choose Safety Components.2.Click Firmware.3.Click MSR57P Guardmaster Speed Monitoring Safety Relay [ZIP].4.Unzip the file to your hard disk drive.The firmware update process deletes the configuration and restoresthe default parameters. If you save your configuration to yourcomputer, you can reload it following the update.Publication 440R-RN002B-EN-P - April 2010Publication 440R-RN002B-EN-P - April 2010MSR57P Guardmaster Speed Monitoring Safety Relay Firmware Update 3Corrected AnomalyThe anomaly corrected in this firmware revision update is listed in this table.Update Firmware Follow these steps to update the firmware of the MSR57P relay.1.Open DriveExplorer software.2.Click Connect to connect to the MSR57P relay.AnomalyDescriptionUnder specific conditions, it may be possible to enter thehazardous area that is underaccess control of the MSR57Prelay without actively monitoringthe Enabling Switch Monitor Input(ESM_In) once inside the hazardous area.This can occur only when the safety system is being transitioned from Safe Limited Speed (SLS) mode back to the normal Run mode, if the Safe Limited Speed input (SLS_In) is switched from OFF to ON before activating the Reset input (Reset_In). During this scenario, the ESM_In input is monitored only while the hazardous area’s access gate is opening, that is, the Door Monitoring input (DM_In) transitions from closed (ON) to open (OFF). The enabling switch is not monitored for any other conditions while the SLS_In is ON. If the SLS_In is switched back to the OFF position (SLS monitoring requested) before the Reset_In is activated, then the ESM_In will not be monitored until the DM_In transitions from closed (ON) to open (OFF).This anomaly can occur for only these two configurations:•When P21 [Safety Mode] is configured for 6 - Master, Safe Limited Speed with Door Monitoringand Enabling Switch Monitoring (LimSpd DM ES), and P22 [Reset Type] is configured for 1 -Manual reset•When P21 [Safety Mode] is configured for 6 - Master, Safe Limited Speed with Door Monitoringand Enabling Switch Monitoring (LimSpd DM ES), and P22 [Reset Type] is configured for 2 -Manual Monitored (Monitored) resetCorrected firmware generates a Stop Category Fault if the DM_In input is detected in the open (OFF)state while the SLS_In input is ON. A Stop Category Fault causes the relay to initiate the configuredSafe Stop Type.Publication 440R-RN002B-EN-P - April 20104 MSR57P Guardmaster Speed Monitoring Safety Relay Firmware Update3.Select the MSR57P relay and click the information icon to open the relay Properties dialog box.4.Click the Details tab to view the revision levels currentlyinstalled on your MSR57P relay.5.Click Flash Update.6.Click Browse.MSR57P Guardmaster Speed Monitoring Safety Relay Firmware Update 5 7.Find the directory where you installed the files and choose thatdirectory.8.Select 1.006 and click Next.9.On the Confirm Flash Update dialog box, click FLASH to startthe update.It takes approximately 7…10 minutes to update the relay. TheExecuting Flash Update dialog box tracks the progress of theupdate.10.When the update is complete, click Close.11.Click Yes when DriveExplorer software requests to reconnect tothe MSR57P relay.Publication 440R-RN002B-EN-P - April 20106MSR57P Guardmaster Speed Monitoring Safety Relay Firmware UpdateConfirm the Update Follow these steps to confirm that the update was successful.1.Select the MSR57P relay and click the information icontoopen the relay Properties dialog box.2.Click the Details tab and verify that these revisions are shown.3.Close the MSR57P dialog box.Download Your Saved Configuration File Follow these steps to reload your configuration to the relay.1.In the DriveExplorer tree view, expand the MSR57P relay.2.From the Actions menu, choose Download Saved File.3.Click Yes to acknowledge that set-up values may change.4.Browse to the configuration file you saved before performingthe firmware update (*.csf file).5.Select your file and click Open.6.Expand the Parameters and choose the Security group.7.Place the relay in Run mode by setting the P6 [Operating Mode]parameter to 1.pare the value of P10 [Signature ID] to the value yourecorded before the upgrade.The two values should be the same.File Revision ChecksumApplication Program 1.006.010x8481Boot Program 1.006.010x3504Core Boot A 1.003.010xB049Core Executive A 1.006.010x4F65Core Boot B 1.003.010xE9A3Core Executive B 1.006.010xA697After you verify that the Signature ID values match, you mustrevalidate your application, following the guidelines in theGuardmaster MSR57P Speed Monitoring Safety Relay User Manual,publication 440R-UM004.Publication 440R-RN002B-EN-P - April 2010MSR57P Guardmaster Speed Monitoring Safety Relay Firmware Update 7 Additional Resources For information on installing, configuring, and operating an MSR57Prelay, including safety requirements, refer to the Guardmaster MSR57PSpeed Monitoring Safety Relay User Manual, publication 440R-UM004.You can view or download publications at:/literature. To order paper copies oftechnical documentation, contact your local Rockwell Automationdistributor or sales representative.Publication 440R-RN002B-EN-P - April 2010Rockwell Automation SupportRockwell Automation provides technical information on the Web to assist you in using its products. At /support/, you can find technical manuals, a knowledge base ofFAQs, technical and application notes, sample code and links to software service packs, and a MySupport feature that you can customize to make the best use of these tools.For an additional level of technical phone support for installation, configuration, and troubleshooting, we offer TechConnect support programs. For more information, contact your local distributor or Rockwell Automation representative, or visit /support/.Installation AssistanceIf you experience an anomoly within the first 24 hours of installation, review the information that is contained in this manual.You can contact Customer Support for initial help in getting your product up and running.New Product Satisfaction ReturnRockwell Automation tests all of its products to ensure that they are fully operational when shipped from the manufacturing facility. However, if your product is not functioning and needs to be returned, follow these procedures.Documentation FeedbackYour comments will help us serve your documentation needs better. If you have any suggestions on how to improve this document, complete this form, publication RA-DU002, available at /literature/.United States or Canada 1.440.646.3434Outside United States or Canada Use the Worldwide Locator at /support/americas/phone_en.html , or contact your local Rockwell Automation representative.United StatesContact your distributor. You must provide a Customer Support case number (call the phone number above to obtain one) to your distributor to complete the return process.Outside United StatesPlease contact your local Rockwell Automation representative for the return procedure.Publication 440R-RN002B-EN-P - April 2010 Supersedes Publication 440R-RN002B-EN-P - March 2010Copyright © 2010 Rockwell Automation, Inc. All rights reserved. Printed in the U.S.A.Allen-Bradley, Guardmaster, DriveExplorer, Rockwell Software, Rockwell Automation, and TechConnect are trademarks of Rockwell Automation, Inc.Trademarks not belonging to Rockwell Automation are property of their respective companies.。
伟格兴MSATA技术规格书

WELLCORE○R SSD MSATA W10 SeriesProduct Specification V1.0 May-2012NOTE:INFORMATION IN THIS DOCUMENT IS PROVIDED IN CONNECTION WITH WELLCORE PRODUCTS, NO LICENSE, EXPRESS OR IMPLIED, BY ESTOPPEL OR OTHERWISE, TO ANY INTELLECTUAL PROPERTY RIGHTS IS GRANTED BY THIS DOCUMENT, TO ANY INTELLECTUAL PROPERTY RIGHTS IN WELLCORE PRODUCT OR TECHNOLOGY,ALL PRODUCT SPECIFICATIONS ARE PROVIDED FOR REFERENCE ONLY, INFORMATION IN THIS PRODUCT SPECIFICATION IS SUBJECT TO CHANGE AT ANYTIME WITHOUT NOTICE.Wellcorping Technology Co., Ltd© WELLCORE 2011. All rights reserved Table of Contents1.Introduction (3)1.0 Overview (3)1.1 Capacity Specifications (3)1.2 Product Specifications (4)2. Product numbering scheme (5)3. Functional Block Diagram (6)4. Mechanical Information (7)4.0 Form factor (7)4.1 Pin Locations (8)4.2 Signal Descriptions (8)5. Electrical Characteristics (9)6. Environmental Conditions (9)6.0 Temperature (9)6.1 Shock, Vibration (10)7. Supported Command Sets (11)7.0 ATA Command set (11)7.1 ATA COMMAND SPECIFICATIONS (13)7.2 S M A R T command set (17)8.NCQ Command (22)Wellcorping Technology Co., Ltd1.Introduction1.0 OverviewWELLCORE SSD MSATA W10 Series purely consists of semiconductor devices and NAND flash moving parts. It gives rugged features against shock and vibration, used in extreme environment such as industrial PC or automotive device to increase reliability,The SSD is designed to use the SATA interface efficiently during both READs and WRITEs while delivering bandwidth-focused performance. SSD technology enables en-hanced boot times, faster application load times, reduced power consumption, and ex-tended reliability.1.1 Capacity Specifications. This chapter is about the specifications of the W10 Series MSATA SSD.Part Numbers Capacity Flash typeW10SM5*C-***2GB MLC/SLC 4GB MLC/SLC 8GB MLC/SLC 16GB MLC/SLC 32GB MLC/SLC 64GB MLC/SLC 128GB MLC 256GB MLCTable 1 :Capacity Specifications. The letter ‘ * ’ means some information of the products, please visit the table 2 for more information.1.2 Product Specifications◆Form factor:MSATA(JEDEC:MO-300B). Form size : 50.8mm * 30.0mm * 3.85mm(LxWxH)◆SATA 3Gbps Bandwidth Performance. Sequential Read: Up to 160 MB/s. Sequential Write: Up to 160 MB/s. Random 4 KB Reads: Up to 6000 IOPS. Random 4 KB Writes: Up to 1000 IOPS◆Compliant with Serial ATA Revision 2.6 ,◆Support 1.5Gps/3.0Gps SATA I/II interface◆Supports BCH ECC 16 bits or 24 bits in 1024 bytes◆S M A R T (Self-Monitoring, Analysis and Reporting Technology) ◆Supports (NCQ) AND (TRIM) Command set◆Flash management algorithm:. static and dynamic wear-leveling, bad block management algorithm◆Data retention: 10 years◆Read endurance: unlimited◆Write endurance: >9 years. Condition: 100GB write/ day(SSD capacity=100GB, Nand flash endurance =5000 P/E Cycles, SSD WA=1.5)◆MTBF (Mean Time Between Failures): 2,000,000 hours◆Operating temperature:. Commercial: 0℃ ~ +70℃. Industrial: -40℃ ~ +85℃◆Power Consumption:. Active(write/read): 1.4 W. Idle : 0.5 W. Sleep: 0.3 W◆Weight: Up to 10 g◆Certifications: UL; CE; FCC; SATA-IO; Microsoft WHQL ◆Product Ecological Compliance: ROHSWellcorping Technology Co., Ltd2. Product numbering schemeEXAMPLE:P/N: W10SM5MC-032 ,Please refer to the following table content (Table 2).W1010 S M 5 M C-032032WELLCOR WELLCORPING PINGTechnologyTechnology SSD Controller: 10-JMICRON 20-NOVACHIPS 30-SMI 40-SANDFORCE50-PHISON60-S-SATA P-PATA E-PCIE Form Factor : 25-2.5 Inch 18-1.8 Inch 13-1.3 InchM5-50mm MSATA M7-70mm MSATA P5-50mm MSATA(PCIE) P7-70mm MSATA(PCIE)Z3-ZIF 1.3 Inch Z8-ZIF 1.8 Inch MI-MICRO 1.8寸 CF-CF CARD FA-CFAST CARD LF-LIF HS-HALFSLIMNAND NAND FLASH: FLASH: S-SLCM-MLC Operatingtemperature:C-Commercial (0℃~+70℃) I-Industrial (-40℃~+85℃) M-Military (-55℃~+150℃) capacity:001-1GB* * 512-512GB * * 1TB-1000GB* *Table 2: numbering scheme3. Functional Block DiagramFigure 3:Functional Block Diagram4. Mechanical Information4.0 Form Size: 50.8mm*30.0mm*3.85mm(LxWxH),refer Figure 4Figure 4: Form Size4.1 Pin Locations4.2 Signal DescriptionsPin PinDefinitions DefinitionsPin PinDefinitions DefinitionsP1 N o Connect P2 +3.3V P3 N o Connect P4 GND P5 N o Connect P6 +1.5V(No use)P7 N o Connect P8 N o Connect P9 GNDP10 N o Connect P11 N o Connect P12 N o Connect P13 N o Connect P14 N o Connect P15 GND P16 N o Connect P17 N o Connect P18 GND P19 N o Connect P20 N o Connect P21 GNDP22 N o Connect P23 SATA Differential TX+ based on SSD P24 +3.3V P25 SATA Differential TX- based on SSDP26 GND P27 GND P28 +1.5V(No use) P29 GNDP30 N o Connect P31 SATA Differential RX- based on SSD P32 N o Connect P33 SATA Differential RX+ based on SSDP34 GND P35 GND P36 N o Connect P37 GND P38 N o Connect P39 +3.3V P40 GND P41 +3.3V P42 N o Connect P43 GND P44 N o Connect P45 Vendor(No use) P46 N o Connect P47 Vendor(No use) P48 +1.5V(No use)P49 DAS/DSS(No use) P50 GND P51 Presence DetectionP52+3.3V5. Electrical CharacteristicsElectrical Characteristics Value Operating Voltage for 3.3 V (±5%)Min Max 3.14 V 3.47VPower Consumption (TYPE)Active(write/read)IdleSleep 1.4 W 0.5 W 0.3WNotes:1.Active power measured during execution of MobileMark* 2007 with SATA Link PowerManagement (LPM) enabled.2.Idle power defined as SSD at idle with SATA Link Power Management (LPM) enabled.6. Environmental Conditions6.0 TemperatureCase TemperatureOperating Non-operating Commercial :(0℃ ~ +70℃) Industrial: (-40℃ ~ +85℃)-55 ~ 95 ℃Temperature GradientOperating Non-operating 30 (TYP) ℃/hr 30 (TYP) ℃/hrHumidityOperating Non-operating 5 ~ 95% 5 ~ 95%Wellcorping Technology Co., Ltd6.1 Shock and VibrationShockOperating Non-operating 1,500 G (Max) at 0.5 msec 1,500 G (Max) at 0.5 msecVibrationOperating Non-operating 2.17 GRMS (5-700 Hz) Max3.13 GRMS (5-800 Hz) MaxNotes:1.Temperature gradient measured without condensation.2.Shock specifications assume the SSD is mounted securely with the input vibration applied to the drive-mounting screws.Stimulus may be applied in the X, Y or Z axis. Shock specification is measured using Root Mean Squared (RMS) value.3.Vibration specifications assume the SSD is mounted securely with the input vibration applied to the drive-mounting screws. Stimulus may be applied in the X, Y or Z axis. Vibration specification is measured using Root Mean Squared (RMS) value.Wellcorping Technology Co., Ltd© WELLCORE 2011. All rights reserved Command Name Code PARAMETERS USEDCommand NameCodeSCSNCYDRHDFTCHECK POWER MODEE5h O X X O X X DEVICE CONFIGURATION OVERLAY B1h X X X O X O EXECUTE DIAGNOSTICS 90h X X X O X X FLUSH CACHE E7h X X X O X X FLUSH CACHE EXT EAh X X X O X X IDENTIFY DEVICE ECh X X X O X X IDLEE3h O X X O X X IDLE IMMEDIATE E1h X X X O X X NOP00h F F F O X O INITIALIZE DEVICE PARAMETERS 91h O X X O O X READ BUFFER E4h X X X O X X READ DMA C8h or C9h O O O O O X READ DMA EXT 25h O O O O O X READ FPDMA QUEUED 60h O O O O O O READ LOG EXT 2Fh O O O O O O READ MULTIPLE C4h O O O O O X READ MULTIPLE EXT 29h O O O O O X READ NATIVE MAX ADDRESS F8h X X X O X X READ NATIVE MAX ADDRESS EXT 27h X X X O X X READ SECTOR(S) 20h or 21h O O O O O X READ SECTOR(S) EXT 24h O O O O O X READ VERIFY SECTOR(S) 40h or 41h O O O O O X READ VERIFY SECTOR(S) EXT 42h O O O O O X RECALIBRATE10h X X X O X X SECURITY DISABLE PASSWORD F6h X X X O X X SECURITY ERASE PREPARE F3h X X X O X X SECURITY ERASE UNIT F4h X X X O X X SECURITY FREEZE LOCK F5h X X X O X X SECURITY SET PASSWORDF1hXXXOXX7 ATA General Feature Command Set7.0 ATA Command set.This table with the following paragraphs summarizes the ATA command set.Command TableWellcorping Technology Co., Ltd© WELLCORE 2011. All rights reserved SECURITY UNLOCK F2h X X X O X XSEEK 7xh X X O O O XSET FEATURES EFh O X X O X OSET MAX F9h O O O O O OSET MAX ADDRESS EXT 37h O O O O O XSET MULTIPLE MODE C6h O X X O X XSLEEP E6h X X X O X XSMART B0h X X O O X OSTANDBY E2h X X X O X XSTANDBY IMMEDIATE E0h X X X O X XWRITE BUFFER E8h X X X O X XWRITE DMA CAh or CBh O O O O O XWRITE DMA EXT 35h O O O O O XWRITE DMA FUA EXT 3Dh O O O O O XWRITE FPDMA QUEUED 61h O O O O O OWRITE LOG EXT 3Fh O O O O O XWRITE MULTIPLE C5h O O O O O XWRITE MULTIPLE EXT 39h O O O O O XWRITE MULTIPLE FUA EXT CEh O O O O O XWRITE SECTOR(S) 30h or 31h O O O O O XWRITE SECTOR(S) EXT 34h O O O O O XWRITE VERIFY 3Ch O O O O O ONote:O = Valid, X = Don't careSC = Sector Count RegisterSN = Sector Number RegisterCY = Cylinder Low/High RegisterDR = DEVICE SELECT Bit (DEVICE/HEAD Register Bit 4)HD = HEAD SELECT Bit (DEVICE/HEAD Register Bit 3-0)FT = Features RegisterWellcorping Technology Co., Ltd© WELLCORE 2011. All rights reserved 7.1 ATA COMMAND SPECIFICATIONSCHECK POWER MODE (E5h)The host can use this command to determine the current power management mode.Sector Count result value-00h – device is in Standby mode80h – device is in Idle modeFFh – device is in Active mode or Idle modeDEVICE CONFIGURATION OVERLAY (B1h)Individual Device Configuration Overlay (DCO) feature set commands are identified by the value placed in the Feature field.The subcommands and their respective codes are listed below.Device Configuration Overlay Feature field valuesValue CommandsC0h DEVICE CONFIGURATION RESTOREC1h DEVICE CONFIGURATION FREEZE LOCKC2h DEVICE CONFIGURATION IDENTIFYC3h DEVICE CONFIGURATION SETDEVICE CONFIGURATION RESTORE (B1h/C0h)The DEVICE CONFIGURATION RESTORE command provides a method for a host to restore any setting previously changed by a DEVICE CONFIGURATION SET command and to restore the content of the IDENTIFY DEVICE data, IDENTIFY PACKET DEVICE data, and other feature settings in a device to their factory default settings. The results of thisaction are indicated by the data returned from the Input Data of a DEVICE CONFIGURATION IDENTIFY command.DEVICE CONFIGURATION FREEZE LOCK (B1h/C1h)The DEVICE CONFIGURATION FREEZE LOCK command provides a method for the host to prevent accidental modification of a device's DCO settings. After a device has completed a DEVICE CONFIGURATION FREEZE LOCK command without error, the device shall return command aborted for all DEVICE CONFIGURATION SET, DEVICE CONFIGURATION FREEZE LOCK, DEVICE CONFIGURATION IDENTIFY, and DEVICE CONFIGURATIONRESTORE commands until after the device processes a power-on reset. A device shall be in the factory_config state or thereduced_config state after processing a power-on reset. A device shall not exit the DCO_Locked state as the result of processing a hardware reset or a software reset.Wellcorping Technology Co., Ltd© WELLCORE 2011. All rights reserved DEVICE CONFIGURATION IDENTIFY (B1h/C2h)DEVICE CONFIGURATION IDENTIFY (B1h/C2h)The DEVICE CONFIGURATION IDENTIFY command causes a device to return a 512-byte data structure. The content of this data structure indicates the selectable commands, modes, and feature sets that the device is capable of disabling or modifying through processing of a DEVICE CONFIGURATION SET command. If a DEVICE CONFIGURATION SET command reducing a device's capabilities has completed without error, then:a) the response by a device to an IDENTIFY DEVICE, IDENTIFY PACKET DEVICE, and other commands, exceptthe DEVICE CONFIGURATION IDENTIFY command, shall reflect the reduced set of capabilities; andb) the response by a device to a DEVICE CONFIGURATION IDENTIFY command shall reflect the entire set of selectable capabilities.The phrase “is changeable” indicates that the feature may be disabled by the host using a DEVICE CONFIGURATION SET command. If the feature is not changeable then the device may support the feature but the DEVICE CONFIGURATION SET command shall not affect support of the feature.The format of the Device Configuration Overlay data structure is listed below.DCO Identify data structureWordValueDescription0002hData structure revision number1 0007hMultiword DMA modes supported Bit15:3 ReservedBit2 1 = Reporting support for Multiword DMA mode 2 and below is changeable Bit1 1 = Reporting support for Multiword DMA mode 1 and below is changeable Bit0 1 = Reporting support for Multiword DMA mode 0 is changeable 2 007FhUltra DMA modes supported Bit15:7 ReservedBit6 1 = Reporting support for Ultra DMA mode 6 and below is changeable Bit5 1 = Reporting support for Ultra DMA mode 5 and below is changeable Bit4 1 = Reporting support for Ultra DMA mode 4 and below is changeable Bit3 1 = Reporting support for Ultra DMA mode 3 and below is changeable Bit2 1 = Reporting support for Ultra DMA mode 2 and below is changeable Bit1 1 = Reporting support for Ultra DMA mode 1 and below is changeable Bit0 1 = Reporting support for Ultra DMA mode 0 is changeable 3-6Native MAXLBAMaximum LBA (QWord) Bit63:48 ReservedBit47:0 Maximum LBAWellcorping Technology Co., Ltd© WELLCORE 2011. All rights reserved Word Value Description7 0089h Command set/feature set supported part 1Bit15ReservedBit14 1 = Reporting support for the Write-Read-Verify feature set is changeableBit13 1 = Reporting support for the SMART Conveyance self-test is changeableBit12 1 = Reporting support for the SMART Selective self-test is changeableBit11 1 = Reporting support for the Forced Unit Access is changeable Bit10 Reserved for TLCBit9 1 = Reporting support for the Streaming feature set is changeableBit8 1 = Reporting support for the 48-bit Addressing feature set is changeableBit7 1 = Reporting support for the HPA feature set is changeableBit6 1 = Reporting support for the AAM feature set is changeable Bit5 1 = Reporting support for the TCQ feature set is changeableBit4 1 = Reporting support for the PUIS feature set is changeable Bit3 1 = Reporting support for the Security feature set is changeable Bit2 1 = Reporting support for the SMART error log is changeable Bit1 1 = Reporting support for the SMART self-test is changeable Bit0 1 = Reporting support for the SMART feature set is changeable8 0000h Serial ATA Command set/feature set supportedBit15:5 Reserved for Serial ATABit4 1 = Reporting support for the SSP feature set is changeableBit3 1 = Reporting support for asynchronous notification is changeableBit2 1 = Reporting support for interface power management is changeableBit1 1 = Reporting support for non-zero buffer offsets is changeable Bit0 1 = Reporting support for the NCQ feature set is changeable9 0000h Reserved for Serial ATA 10-20 0000h Reserved21 0000h Command set/feature set supported part 2Bit15 1 = Reporting support for the NV Cache feature set is changeable Bit14 1 = Reporting support for the NV Cache Power Management feature set is changeableBit13 1 = Reporting support for WRITE UNCORRECTABLE EXT is changeableBit12 1 = Reporting support for the Trusted Computing feature set is changeableBit11 1 = Reporting support for the Free-fall Control feature set is changeableBit10:0 Reserved22 0000h Command set/feature set supported part 3Bit15:0 Reserved23-207 0000h Reserved208-254 0000h Vender Specific255Checksum +A5h Integrity wordBit15:8 Checksum Bit7:0 SignatureWellcorping Technology Co., Ltd© WELLCORE 2011. All rights reserved DEVICE CONFIGURATION SET (B1h/C3h)The DEVICE CONFIGURATION SET command allows a host to reduce the set of optional commands, modes, or feature sets supported by a device as indicated by a DEVICE CONFIGURATION IDENTIFY command. The DEVICE CONFIGURATION SET command may modify the data returned by IDENTIFY DEVICE or IDENTIFY PACKET DEVICE. When the IDENTIFY DEVICE data or IDENTIFY PACKET DEVICE data is changed, the device shall respond ina manner consistent with the new data.If a bit is set to one in the DEVICE CONFIGURATION SET data transmitted to the device that is not set in the DCO data received from a DEVICE CONFIGURATION IDENTIFY command, no action is taken for that bit.Modifying the maximum LBA of the device also modifies the LBA value returned by a READ NATIVE MAX ADDRESSor READ NATIVE MAX ADDRESS EXT command.EXECUTE DIAGNOSITICS (90h)This command performs the internal diagnostic tests implemented by the drive. See ERROR register for diagnostic codes.FLUSH CACHE (E7h)This command is used by the host to request the device to flush the write cache. If there is data in the write cache, that data shall be written to the media. The BSY bit shall remain set to one until all data has been successfully written or an error occurs.FLUSH CACHE EXT (EAh)48-bit feature set mandatory command. This command is used by the host to request the device to flush the write cache. If there is data in the write cache, that data shall be written to the media. The BSY bit shall remain set to one until all data has been successfully written or an error occurs.IDENTIFY DEVICE (ECh)This commands read out 512Bytes of drive parameter information. Parameter Information consists of the arrangement and value as shown in the following table. This command enables the host to receive the Identify Drive Information from the device.Wellcorping Technology Co., Ltd© WELLCORE 2011. All rights reserved 7.2 SMART COMMAND SETSMART Function Set (B0h)Performs different processing required for predicting device failures, according to the subcommand specified in the Features register. If the Features register contains an unsupported value, the Aborted Command error is returned. If the SMART function is disabled, any subcommand other than SMART ENABLE OPERATIONS results in the Aborted Command error.Code Smart SubcommandD0h READ DATAD1h READ ATTRIBUTE THRESHOLDSD2h ENABLE/DISABLE ATTRIBUTE AUTOSAVED3h SAVE ATTRIBUTE VALUESD8h ENABLE OPERATIONSD9h DISABLE OPERATIONSDAh RETURN STATUSSMART READ DATA (B0h/D0h)This command returns 512-byte SMART Data Structure to the host with PIO data-in protocol. The register file has to contain D0h for Features register, 4Fh for LBA Mid register and C2h for the LBA High register.Byte Description0-1 Data structure revision number2-13 1st attribute data14-361 2nd-30th Individual attribute data362 Off-line data collection status363 Self-test execution status364-365 Total time in seconds to complete off-line data collection366 Reserved367 Off-line data collection capability368-369 SMART capability370 Error logging capability371 Self-test Failure Checkpoint372 Short self-test routine recommended polling time(in minutes)373 Extended self-test routine recommended polling time(in minutes)374-510 Reserved511 Data structure ChecksumWellcorping Technology Co., Ltd© WELLCORE 2011. All rights reserved Byte 2-361: Individual attribute dataByte Description0 Attribute ID1-2 Status Flag3 Attribute Value4 Worst Ever normalized Attribute Value5-10 Raw Attribute Value11 ReservedThe attribute ID information is listed in the following table:ID Description01h Read Error Rate02h Throughput Performance03h Spin Up Time05h Reallocated Sector Count07h Seek Error Rate08h Seek Time performance09h Power-On hours Count0Ah Spin Retry Count0Ch Drive Power Cycle CountA8h SATA PHY Error CountAAh Bad Block CountADh Erase CountAFh Bad Cluster Table CountC0h Unexpected Power Loss CountC2h TemperatureC5h Current Pending Sector CountF0h Write HeadWellcorping Technology Co., Ltd© WELLCORE 2011. All rights reserved MART READ ATTRIBUTE THRESHOLD (B0h/D1h)This command transfers 512 bytes of drive failure threshold data to the host.Byte Description0-1 Data structure revision number2-361 st th1 – 30 Individual attribute threshold data362-510 Reserved1 – 30 Individual attribute threshold data511 Data structure checksumSMART ENABLE/DISABLE ATTRIBUTE AUTOSAVE (B0h/D2h)This command enables and disables the optional attribute autosave feature of the device. This command may either allow the device, after some vendor specified event, to save the device updated attributes to non-volatile memory; or this command may cause the autosave feature to be disabled. The state of the attribute autosave feature, either enabled or disabled, shall be preserved by the device during all power and reset events.A value of zero written by the host into the device’s Count field before issuing this command shall cause this feature to be disabled. Disabling this feature does not preclude the device from saving SMART data to non-volatile memory during some other normal operation (e.g., during a power-on or power-off sequence or during an error recovery sequence).A value of F1h written by the host into the device’s Count field before issuing this command shall cause this feature to be enabled. Any other other non-zero value written by the host into this field before issuing this command is vendor specific. The meaning of any non-zero value written to this field at this time shall be preserved by the device during all power and reset events.SMART SAVE ATTRIBUTE VALUE (B0h/D3h)Saves any modified attribute values.SMART ENABL OPERATIONS (B0h/D8h)Enables the SMART function. This setting is maintained when the power is turned off and then back on. Once the SMART function is enabled, subsequent SMART ENABLE OPERATIONS commands do not affect any parameters.SMART DISABLE OPERATIONS (B0h/D9h)Disables the SMART function. Upon receiving the command, the drive disables all SMART operations. This setting is maintained when the power is turned off and then back on. Once this command has been received, all SMART commands other than SMART ENABLE OPERATIONS are aborted with the Aborted Command error.This command disables all SMART capabilities including any and all timer and event count functions related exclusively to this feature. After command acceptance, this controller will disable all SMART operations. SMART data in no longer be monitored or saved. The state of SMART is preserved across power cycles.Wellcorping Technology Co., Ltd© WELLCORE 2011. All rights reserved SMART RETURN STATUS (B0h/DAh)Reports the drive reliability status.Values reported when a predicted defect has not been detected:Cylinder Low register: 4FhCylinder High register: C2hValues reported when a predicted defect has been detected:Cylinder Low register: F4hCylinder High register: 2ChSTANDBY (E2h)This command causes the device to enter the Standby mode. If the Count field is non-zero then the Standby timer shall be enabled. The value in the Count field shall be used to determine the time programmed into the Standby timer. If the Count field is zero then the Standby timer is disabled.STANDBY IMMEDIATE (E0h)This command causes the drive to set BSY, enter the Sleep mode (which corresponds to the ATA “Standby” Mode), clear BSY and return the interrupt immediately.WRITE BUFFER (E8h)This command enables the host to write the contents of one 512-byte block of data to the device’s buffer. The READ BUFFER and WRITE BUFFER commands shall be synchronized within the device such that sequential WRITE BUFFER and READ BUFFER commands access the same bytes within the buffer.WRITE DMA (CAh)Write data to sectors during Ultra DMA and Multiword DMA transfer. Use the SET FEATURES command to specify the mode value.WRITE DMA EXT (35h)48-bit feature set mandatory command. Write data to sectors during Ultra DMA and Multiword DMA transfer. Use the SET FEATURES command to specify the mode value.WRITE DMA FUA EXT (3Dh)48-bit feature set mandatory command. This command provides the same function as the WRITE DMA EXT command except that regardless of whether volatile and/or non-volatile write caching in the device is enabled or not, the user data shall be written to non-volatile media before command completion is reported.WRITE FPDMA QUEUED (61h)NCQ feature set mandatory 48-bit command. This command causes data to be transferred from the host to the device.Wellcorping Technology Co., Ltd© WELLCORE 2011. All rights reserved WRITE LOG EXT (3Fh)This command writes a specified number of 512 byte blocks of data to the specified log.WRITE MULTIPLE (C5h)This command writes the number of logical sectors specified in the Count field. The number of logical sectors per DRQ data block is defined by the content of IDENTIFY DEVICE data word 59. If the number of requested logical sectors is not evenly divisible by the DRQ data block count, as many full blocks as possible are transferred, followed by a final, partial block transfer. The partial block transfer is for n logical sectors, where:n = Remainder (Count / DRQ data block count).Device errors encountered during WRITE MULTIPLE commands are posted after the attempted device write of the DRQ data block or partial DRQ data block is transferred. The command ends with the logical sector in error, even if the error was in the middle of a DRQ data block. Subsequent DRQ data blocks are not transferred in the event of an error.The contents of the Command Structure following the transfer of a DRQ data block that had a logical sector in error are undefined. The host should retry the transfer as individual requests to obtain valid error information. If IDENTIFY DEVICE data word 59 bit 8 is cleared to zero or IDENTIFY DEVICE data word 59 bits (7:0) are set to zero, and a WRITE MULTIPLE command is received by the device, and no successful SET MULTIPLE MODE command has been processed by the device, the device shall return command aborted. A successful SET MULTIPLE MODE command should precede a WRITE MULTIPLE command.WRITE MULTIPLE EXT (39h)48-bit feature set mandatory command. This command is similar to the Write Sectors command. Interrupts are not presented on each sector, but on the transfer of a block which contains the number of sectors defined by Set Multiple command.WRITE MULTIPLE FUA EXT (CEh)48-bit feature set mandatory command. This command provides the same functionality as the WRITE MULTIPLE EXT command except that regardless of whether volatile and/or non-volatile write caching in the device is enabled or not, the user data shall be written to non-volatile media before command completion is reported.WRITE SECTOR(S) (30h/31h)Write data to a specified number of sectors (1 to 256, as specified with the Sector Count register) from the specified address. Specify “00h” to write 256 sectors.WRITE SECTOR(S) EXT (34h)48-bit feature set mandatory command. Write data to a specified number of sectors (1 to 65536, as specified with the Sector Count register) from the specified address. Specify “00h” to write 65536 sectors.WRITE VERIFY (3Ch)This command is similar to the WRITE SECTOR(S) command, except that each sector is verified before the command is completed.Wellcorping Technology Co., Ltd8 NCQNCQ-Native Command QueuingThe WELLCORE W10 Series supports the Native Command Queuing (NCQ) command set, which includes:•READ FPDMA QUEUED•WRITE FPDMA QUEUEDNote:With a maximum queue depth equal to 32.Wellcorping Technology Co., Ltd。
1PPC控制器故障代码查询重要

Rexroth IndraControl VCP 20Industrial Hydraulics Electric Drivesand ControlsLinear Motion andAssembly Technologies PneumaticsServiceAutomationMobileHydraulicsRexroth VisualMotion 10 Multi-Axis Machine Control R911306327 Edition 01Troubleshooting GuideAbout this Documentation Rexroth VisualMotion 10 Troubleshooting Guide DOK-VISMOT-VM*-10VRS**-WA01-EN-PRexroth VisualMotion 10Multi-Axis Machine ControlTroubleshooting Guide DOK-VISMOT-VM*-10VRS**-WA01-EN-P Document Number, 120-2300-B323-01/ENPart of Box Set, 20-10V-EN (MN R911306370)This documentation describes …•the use of VisualMotion Toolkit for assitance in diagnostics •the proper steps for indentifing diagnostic faults • and the suggested remedies for clearing faults Description ReleaseDateNotes DOK-VISMOT-VM*-10VRS**-WA01-EN-P 08/2004Initial release© 2004 Bosch Rexroth AGCopying this document, giving it to others and the use or communicationof the contents thereof without express authority, are forbidden. Offendersare liable for the payment of damages. All rights are reserved in the eventof the grant of a patent or the registration of a utility model or design(DIN 34-1).The specified data is for product description purposes only and may notbe deemed to be guaranteed unless expressly confirmed in the contract.All rights are reserved with respect to the content of this documentationand the availability of the product.Bosch Rexroth AGBgm.-Dr.-Nebel-Str. 2 • D-97816 Lohr a. MainTel.: +49 (0)93 52/40-0 • Fax: +49 (0)93 52/40-48 85 • Telex: 68 94 21Bosch Rexroth Corporation • Electric Drives and Controls5150 Prairie Stone Parkway • Hoffman Estates, IL 60192 • USATel.: 847-645-3600 • Fax: 847-645-6201/Dept. ESG4 (DPJ)This document has been printed on chlorine-free bleached paper.Title Type of DocumentationDocument TypecodeInternal File Reference Purpose of Documentation Record of Revisions Copyright Validity Published byNoteRexroth VisualMotion 10 Troubleshooting Guide Table of Contents I Table of Contents1VisualMotion Tools for Diagnosing1-1 The Diagnostics Menu.............................................................................................................1-1System Diagnostics.................................................................................................................1-1Tasks Diagnostics...................................................................................................................1-3Drive Overview….....................................................................................................................1-42Monitoring and Diagnostics2-12.1System Diagnostics - Codes and Message...................................................................................2-1Parameters..............................................................................................................................2-2DriveTop..................................................................................................................................2-32.2Control Startup Messages.............................................................................................................2-4PPC Boot-Up Sequence..........................................................................................................2-4Control Firmware Sequence....................................................................................................2-42.3Status Messages (001-199)...........................................................................................................2-5001 Initializing System.............................................................................................................2-5002 Parameter Mode...............................................................................................................2-5003 Initializing Drives...............................................................................................................2-5004 System is Ready...............................................................................................................2-5005 Manual Mode....................................................................................................................2-5006 Automatic Mode: ABCD....................................................................................................2-5007 Program Running: ABCD.................................................................................................2-6008 Single-Stepping: ABCD....................................................................................................2-6009 Select Parameter Mode to Continue................................................................................2-6010 Breakpoint Reached: ABCD.............................................................................................2-6018 Please cycle power to continue........................................................................................2-6019 Executing User Initialization Task....................................................................................2-62.4Warning Messages (201-399).......................................................................................................2-7201 Invalid jog type or axis selected........................................................................................2-7202 Drive %d is not ready.......................................................................................................2-7203 Power Fail detected..........................................................................................................2-7204 Sercos ring was disconnected..........................................................................................2-8205 Parameter transfer warning in Task %c...........................................................................2-8207 Axis %d position limit reached..........................................................................................2-8208 Lost Fieldbus Connection.................................................................................................2-9209 Fieldbus Mapping Timeout...............................................................................................2-9210 File System Defrag: %d completed................................................................................2-10211 Program- & Data memory cleared..................................................................................2-10212 Option Card PLS Warning, see ext. diag.......................................................................2-10213 Sercos cycle time changed.............................................................................................2-11214 PCI Bus Cyclic Mapping Timeout...................................................................................2-11 DOK-VISMOT-VM*-10VRS**-WA01-EN-PII Table of Contents Rexroth VisualMotion 10 Troubleshooting Guide215 RECO I/O Failure, see ext. diag.....................................................................................2-11216 Control PLS %d warning, see ext. diag..........................................................................2-12217 PCI Bus Communication, see ext. diag..........................................................................2-12218 PCI Bus Register Mapping Timeout...............................................................................2-13219 PCI Bus Lifecounter Timeout.........................................................................................2-13220 Excessive deviation in PMG%d, see ext. diag...............................................................2-13221 Excessive Master Position Slip Deviation......................................................................2-13222 ELS Config. Warning, see ext. diag...............................................................................2-14223 PCI Bus reset occurred, cyclic data are invalid..............................................................2-14225 System booted................................................................................................................2-14226 RS485 Serial Communication Error (port X1%d)...........................................................2-15227 Control Over-temperature Warning................................................................................2-15228 Control - SYSTEM WARNING.......................................................................................2-152.5Shutdown Messages (400 - 599).................................................................................................2-16400 EMERGENCY STOP......................................................................................................2-16401 Sercos Controller Error: %02d........................................................................................2-16402 Sercos Config. Error: see ext. diag................................................................................2-16403 System Error see ext. diag.............................................................................................2-17405 Phase %d: Drive did not respond...................................................................................2-17407 Drive %d Phase 3 Switch Error......................................................................................2-17409 Sercos Disconnect Error.................................................................................................2-18411 Drive %d Phase 4 Switch Error......................................................................................2-18412 No drives were found on ring..........................................................................................2-18414 Parameters were lost......................................................................................................2-19415 Drive %d was not found..................................................................................................2-19416 Invalid Instruction at %04x..............................................................................................2-19417 SYSTEM ERROR: pSOS #%04x...................................................................................2-19418 No program is active.......................................................................................................2-20419 Invalid Program File: code = %d....................................................................................2-20420 Drive %d Shutdown Error...............................................................................................2-20421 User Program Stack Overflow........................................................................................2-20422 Parameter transfer error in Task %c..............................................................................2-21423 Unimplemented Instruction.............................................................................................2-21425 Instruction error: see Task %c diag................................................................................2-21426 Drive %d is not ready.....................................................................................................2-22427 Calc: invalid table index %d............................................................................................2-22428 Calc: division by zero......................................................................................................2-22429 Calc: too many operands................................................................................................2-22430 Calc: invalid operator......................................................................................................2-23431 Calc error: see Task %c diag.........................................................................................2-23432 Calc: too many nested expressions...............................................................................2-23433 Setup instruction outside of a task.................................................................................2-23434 Axis %d configured more than once...............................................................................2-23435 Axis %d is not assigned to a task...................................................................................2-24436 General Compiler Error: %04x.......................................................................................2-24438 Invalid Axis Selected: %d...............................................................................................2-24DOK-VISMOT-VM*-10VRS**-WA01-EN-PRexroth VisualMotion 10 Troubleshooting Guide Table of Contents III439 Axis %d: Invalid Motion Type.........................................................................................2-24440 I/O Transfer Error: see task diag....................................................................................2-25450 Event %d: invalid event type..........................................................................................2-25451 Invalid event number ‘%d’..............................................................................................2-25452 More than %d event timers armed.................................................................................2-25453 Homing param. transfer error: %d..................................................................................2-25454 Axis %d homing not complete........................................................................................2-26459 Axis %d target position out of bounds............................................................................2-26460 Invalid program %d from binary inputs...........................................................................2-26463 Ratio command: invalid ratio..........................................................................................2-26464 Can't activate while program running.............................................................................2-27465 Drive %d config. error, see ext. diag..............................................................................2-27467 Invalid ELS Master Option..............................................................................................2-27468 ELS adjustment out of bounds.......................................................................................2-27470 Axis %d velocity > maximum..........................................................................................2-28474 Drive %d cyclic data size too large.................................................................................2-28477 Axis D: probe edge not configured.................................................................................2-28478 Calc: operand out of range.............................................................................................2-28483 Parameter Init. Error: see Task %c diag........................................................................2-29484 Control SYSTEM ERROR..............................................................................................2-29486 Sercos Device %d is not a drive.....................................................................................2-29487 CAM %d is invalid or not stored.....................................................................................2-29488 CAM Error: See Task %c diag........................................................................................2-30489 More than %d CAM axes selected.................................................................................2-30490 System Memory Allocation Error....................................................................................2-30492 Programs were lost, see ext. diag..................................................................................2-30496 Can't execute this instruction from an event..................................................................2-31497 Limit switch config. error, see ext. diag.........................................................................2-31498 Drive %d Shutdown Warning..........................................................................................2-32499 Axis number %d not supported in this version...............................................................2-32500 Axis %d is not referenced...............................................................................................2-32501 Drive %d comm. error, see ext. diag..............................................................................2-33502 ELS and cams not supported in this version..................................................................2-33504 Communication Timeout.................................................................................................2-33505 Axis %d is not configured...............................................................................................2-33508 User Watchdog Timeout.................................................................................................2-33509 Control System Timing Error (%d).................................................................................2-34515 PLC Communications Error............................................................................................2-34516 More than %d registration functions enabled.................................................................2-34519 Lost Fieldbus/PLC Connection.......................................................................................2-35520 Fieldbus Mapping Timeout.............................................................................................2-35521 Invalid Virtual Master ID: %d..........................................................................................2-36522 Invalid ELS Master ID: %d..............................................................................................2-36523 IFS status, facility = 0x%x..............................................................................................2-36524 Hardware Watchdog timeout..........................................................................................2-36525 I/O Configuration error, see ext. diag.............................................................................2-36 DOK-VISMOT-VM*-10VRS**-WA01-EN-PIV Table of Contents Rexroth VisualMotion 10 Troubleshooting Guide526 Sercos Multiplex Channel Config, see ext. diag.............................................................2-37527 Control Initialization Error, see ext. diag.........................................................................2-38528 System Event %d Occurred...........................................................................................2-38529 Invalid ELS Group ID: %d...............................................................................................2-38530 CAM %d is active, can't overwrite..................................................................................2-39531 Invalid variable for Fieldbus/PCI Bus Mapping...............................................................2-39532 Power fail brown out condition detected.........................................................................2-39533 Multiple instances of index CAM: %d found...................................................................2-39534 Hardware Version Not Supported..................................................................................2-40539 Invalid Parameter Number..............................................................................................2-40540 Option Card PLS error....................................................................................................2-40541 Link Ring Error, see ext. diag.........................................................................................2-41542 PLC Cyclic Mapping Timeout.........................................................................................2-42543 PCI Bus Runtime Error...................................................................................................2-42544 RECO I/O Failure, see ext. diag.....................................................................................2-42545 Invalid Coordinated Articulation Function ID: %d...........................................................2-43546 Multiple Instance of Coordinated Articulation Function with ID: %d...............................2-43547 Task %c Coordinated Articulation Error, see ext. diag...................................................2-43548 Invalid Kinematic Number: %d.......................................................................................2-43549 Fieldbus Initialization Error.............................................................................................2-43550 User Initialization Task Timeout.....................................................................................2-44551 Master Slip Config. Error, see ext. diag..........................................................................2-44552 Excessive Master Position Slip Deviation......................................................................2-44553 Invalid Parameter Detected, see C-0-2002....................................................................2-44554 Excessive Deviation in PMG%d, see ext. diag...............................................................2-45555 PCI Bus Register Mapping Timeout...............................................................................2-45556 PCI Bus Lifecounter Timeout.........................................................................................2-45557 PMG%d Maximum allowed deviation window is Zero....................................................2-45558 PMG%d Only 1 axis parameterized...............................................................................2-46559 PMG%d Number of offsets does not match number of Axis..........................................2-46560 PMG%d Max. allowed dev. window is larger than 25% of Modulo................................2-46561 PMG%d Offset is larger than Modulo.............................................................................2-46562 PMG%d Parameterized Axis is not in system................................................................2-46563 Invalid Task Specified, Must be A-D..............................................................................2-46564 PMG%d Invalid configuration, see ext. diag...................................................................2-46565 Axis %d: Configuration error, see ext. diag....................................................................2-47566 Filter sample rate and cutoff frequency mismatch.........................................................2-47567 ELS Config. Error, see ext. diag.....................................................................................2-47568 Axis %d: Assigned Task is Not Defined.........................................................................2-48570 ELS Max. Vel. Exceeded, see ext. diag.........................................................................2-48571 No Program Found.........................................................................................................2-49572 PCI Bus reset occurred, cyclic data is invalid.................................................................2-49573 CAM %d is being built....................................................................................................2-49575 ELS Master for ELS Group %d is invalid........................................................................2-49576 Event for input I%d is already armed, cannot arm again...............................................2-50577 Restored non volatile memory from compact flash........................................................2-50DOK-VISMOT-VM*-10VRS**-WA01-EN-PRexroth VisualMotion 10 Troubleshooting Guide Table of Contents V578 Virtual Master %d Exceeded Its Max. Vel., see ext. diag...............................................2-50579 Group %d Exceeded Its Jog Velocity, see ext. diag......................................................2-51580 pROBE Error Occurred in Task:0x%04X.......................................................................2-51581 Probe Function for Axis # is locked by the PLC.............................................................2-51582 Integrated PLC: PLC Stopped in Operation Mode.........................................................2-51583 Integrated PLC: Internal System Error...........................................................................2-51584 ELS System Master %d is invalid, see ext. diag............................................................2-51585 Drive %d separate deceleration not supported..............................................................2-52586 Master Encoder Card Error, see ext diag.......................................................................2-522.6Integrated PLC Status Messages................................................................................................2-536001 Integrated PLC: Running..............................................................................................2-536002 Integrated PLC: Stopped..............................................................................................2-536002 Integrated PLC: Stopped at Breakpoint........................................................................2-532.7Integrated PLC Error Codes........................................................................................................2-530016 Integrated PLC: Software Watchdog Error...................................................................2-530019 Integrated PLC: Program Checksum Error..................................................................2-530020 Integrated PLC: Fieldbus Master Error.........................................................................2-540021 Integrated PLC: I/O Update Error.................................................................................2-542000 Integrated PLC: Internal SIS System Error..................................................................2-542001 Integrated PLC: Internal Acyclic Access Error.............................................................2-542002 Integrated PLC: Internal Acyclic Memory Error............................................................2-542003 Integrated PLC: PLC Configuration Error.....................................................................2-552004 Integrated PLC: File Access Error................................................................................2-552005 Integrated PLC: Internal Fatal Task Error....................................................................2-556011 Integrated PLC: PLC Program Stopped in Operation Mode........................................2-556012 Integrated PLC: General Error.....................................................................................2-552.8Communication Error Codes and Messages...............................................................................2-56!01 Sercos Error Code # xxxx...............................................................................................2-56!02 Invalid Parameter Number..............................................................................................2-57!03 Data is Read Only...........................................................................................................2-57!04 Write Protected in this mode/phase...............................................................................2-57!05 Greater than maximum value.........................................................................................2-57!06 Less than minimum value...............................................................................................2-57!07 Data is Invalid.................................................................................................................2-57!08 Drive was not found........................................................................................................2-57!09 Drive not ready for communication.................................................................................2-57!10 Drive is not responding...................................................................................................2-57!11 Service channel is not open...........................................................................................2-57!12 Invalid Command Class..................................................................................................2-57!13 Checksum Error: xx (xx= checksum that control calculated).........................................2-58!14 Invalid Command Subclass............................................................................................2-58!15 Invalid Parameter Set.....................................................................................................2-58!16 List already in progress..................................................................................................2-58!17 Invalid Sequence Number..............................................................................................2-58!18 List has not started.........................................................................................................2-58!19 List is finished.................................................................................................................2-58 DOK-VISMOT-VM*-10VRS**-WA01-EN-P。
IBM System x3850 X6 Server 配置指南说明书

3. Connect dark blue SAS cable Connect into dark blue port (SAS0) in PCIe slot 2 in Node0Connect into dark blue port in top IO Module (PORT 0)4. Connect light blue SAS cable Connect into light blue port (SAS1) in PCIe slot 9 in Node0 Connect into light blue port in bo�om IO Module (PORT 0)5. Connect dark red SAS cable Connect into dark red port (SAS1) in PCIe slot 2 in Node1 Connect into dark red port in top IO Module (PORT 1)6. Connect light red SAS cableConnect into light red port (SAS0) in PCIe slot 9 in Node1Connect into light red port in bo�om IO Module (PORT 1)Start - Compute NodesEnd - Storage ShelfStart - Compute Node0End - Compute Node17. Connect dark blue SAS cable Connect into dark blue port (SAS0) in PCIe slot 2 in Node1Connect into dark blue port in top IO Module (PORT 0)8. Connect light blue SAS cable Connect into light blue port (SAS1) in PCIe slot 9 in Node1Connect into light blue port in bo�om IO Module (PORT 0)9. Connect dark red SAS cable Connect into dark red port (SAS1) in PCIe slot 2 in Node0 Connect into dark red port in top IO Module (PORT 1)10. Connect light red SAS cableConnect into light red port (SAS0) in PCIe slot 9 in Node0Connect into light red port in bo�om IO Module (PORT 1)Start - Compute NodesEnd - Expansion ShelfStorage Expansion ShelfConnect into green port (PORT 2) in PCIe slot 1Connect into green port (PORT 2) in PCIe slot 12. Connect yellow SFP28 cableConnect into yellow port (PORT 1) in PCIe slot 1Connect into yellow port (PORT 1) in PCIe slot 181097Database Appliance X9-2-HA.Deploy and Con�gure the ApplianceOracle Database Appliance Deployment and User’s Guide for information about con�guring and deploying the appliance.To get started with your appliance, refer to the Oracle Database Appliance Welcome Kit at: h�p:///goto/oda/docsStart Up the SystemsConnect power to the power supply.Power on the storage shelf and optional storage expansion shelf using the ON/OFF switch on each power supply. The storage shelves must be fully powered on (their Power OK LED steady on) before a�empting to power on the host nodes. This can take several minutes depending on the number of drives installed.On each node, after the green SP OK LED (5) is steady ON, push the power bu�on (6).Wait for the green Power OK LED (7) to turn steady ON. The Power OK LED may blinkfor several minutes. Do not repeatedly push the power bu�ons.141233412131415125678910111718192016Power Supply (PS) 1 with fan modulePower Supply (PS) 1 status indicators: Service Required LED: amber, AC OK LED: green Power Supply (PS) 0 with fan modulePower Supply (PS) 0 status indicators: Service Required LED: amber, AC OK LED: greenPCIe card slot 1: Oracle Dual Port 25Gb Ethernet Adapter provides two ports with SFP28 connections for a private cluster interconnect between server nodesDescriptionPCIe card slot 2: provides two SAS3 connectors used to connect the servers to the storage shelf and the storage expansion shelf PCIe card slot 3: �ller panelPCIe card slot 4: �ller panel, or optional Oracle Dual Port 25Gb Ethernet Adapter, or optional Oracle Quad Port 10GBase-T Adapter For more information about Oracle Database Appliance, go to Oracle Technology Network:h�p:///technetwork/server-storage/engineered-systems/database-appliance/index.html For more information about deployment, go to: h�p:///goto/oda/docsYou can also scan the Quick Response Code with your mobile device to read the documentation.。
IBM Cognos Transformer V11.0 用户指南说明书
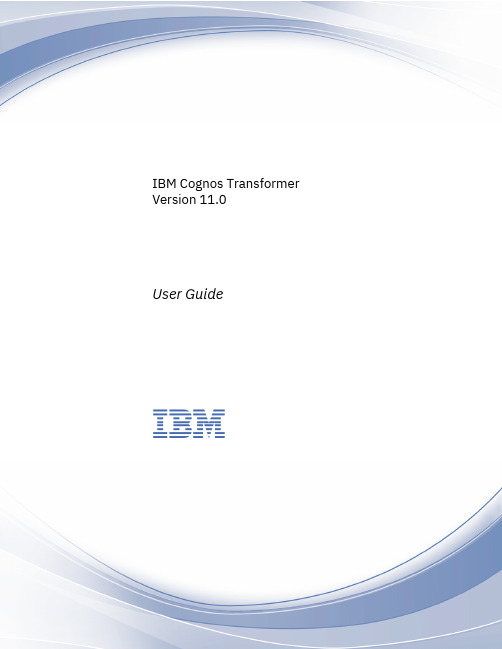
NetApp磁盘阵列安装手册
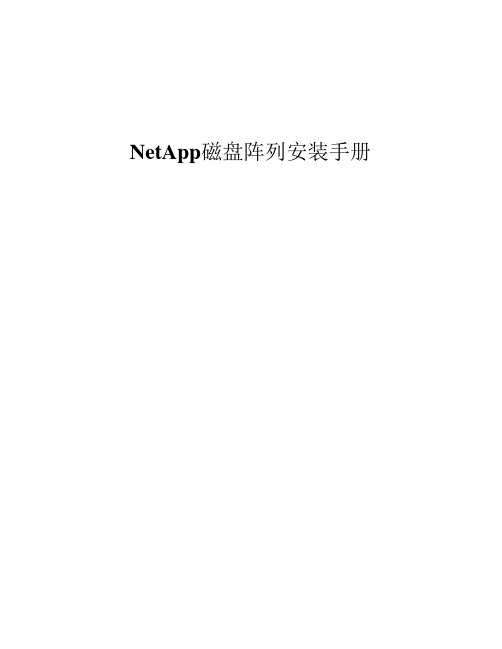
NetApp磁盘阵列安装手册目录目录 (1)一、磁盘阵列的系统安装 (2)1.1初始化磁盘阵列 (2)1.2输入license序列号 (8)1.3配置CIFS (9)1.4在机头中安装阵列操作系统 (11)二、磁盘阵列的SSL安全认证配置 (13)2.1通过浏览器来管理磁盘阵列 (13)2.2配置SSL安全认证 (15)三、磁盘阵列的空间配置和分配 (18)3.1在aggr0中添加新的磁盘 (18)3.2消除磁盘Aggregate的快照预留空间 (22)3.3缩小卷vol0的磁盘空间 (22)3.4创建新的Volume (27)3.5消除Volume的快照预留空间 (31)3.6在新建卷上的参数修改 (33)3.7在IBM主机上安装NetApp磁盘路径管理软件 (34)3.8创建LUN存储单元 (36)3.8.1开启FCP功能 (36)3.8.2创建一个Qtree (38)3.8.3创建一个Lun存储单元 (39)3.8.4在主机上使用LUN来存储数据 (44)一、磁盘阵列的系统安装1.1初始化磁盘阵列NetApp FAS3020C是NetApp产品中一款有双机头的磁盘阵列,需要先在每个机头中安装好操作系统,才能正常使用。
安装步骤如下:1,通过笔记本电脑或其它Windows平台PC机的串口,连接到机头上的串口上;2,通过超级终端,以默认值连接来进行操作;操作过程如下:CFE version 3.0.0 based on Broadcom CFE: 1.0.40Copyright (C) 2000,2001,2002,2003 Broadcom Corporation.Portions Copyright (c) 2002-2005 Network Appliance, Inc.CPU type 0xF29: 2800MHzTotal memory: 0x80000000 bytes (2048MB)CFE> bye输入bye 后,开始启动;CFE version 3.0.0 based on Broadcom CFE: 1.0.40Copyright (C) 2000,2001,2002,2003 Broadcom Corporation.Portions Copyright (c) 2002-2005 Network Appliance, Inc.CPU type 0xF29: 2800MHzTotal memory: 0x80000000 bytes (2048MB)Starting AUTOBOOT press any key to abort...Loading: 0x200000/24732624 0x19963d0/33360796 0x3966f70/1995456 Entry at 0x00200000 Starting program at 0x00200000Press CTRL-C for special boot menu提示按CTRL-C后弹出启动菜单;Special boot options menu will be available.Mon Mar 20 07:54:25 GMT [cf.nm.nicTransitionUp:info]: Interconnect link 0 is UPNetApp Release 7.0.3: Fri Dec 2 06:00:21 PST 2005Copyright (c) 1992-2005 Network Appliance, Inc.Starting boot on Mon Mar 20 07:54:14 GMT 2006(1) Normal boot.(2) Boot without /etc/rc.(3) Change password.(4) Initialize all disks.(4a) Same as option 4, but create a flexible root volume.(5) Maintenance mode boot.Selection (1-5)?4a这里选择4a,初始化所有的磁盘,并且创建一个root卷,此卷将用于操作系统的安装;Zero disks and install a new file system? y选择y,确认将所有的磁盘零化,并且安装新的文件系统;This will erase all the data on the disks, are you sure? Y选择y,确认将删除磁盘上的所有数据;Zeroing disks takes about 80 minutes. .................................................................................................................................................................... .................................................................................................................................................................... .................................................................................................................................................................... .................................................................................................................................................................... .................................................................................................................................................................... .................................................................................................................................................................... .................................................................................................................................................................... ..................................................................Mon Mar 20 09:15:30 GMT [raid.disk.zero.done:notice]: Disk 0a.23 Shelf ? Bay ? [NETAPP X276_S10K7288F10 NA01] S/N [3KR16HQC00007617E7VE] : disk zeroing complete...............Mon Mar 20 09:15:34 GMT [raid.disk.zero.done:notice]: Disk 0a.18 Shelf ? Bay ? [NETAPP X276_S10K7288F10 NA01] S/N [3KR18YGC000076187JGK] : disk zeroing complete ....................Mon Mar 20 09:15:40 GMT [raid.disk.zero.done:notice]: Disk 0a.20 Shelf ? Bay ? [NETAPP X276_S10K7288F10 NA01] S/N [3KR18MYR0000761769S1] : disk zeroing complete .............Mon Mar 20 09:15:43 GMT [raid.disk.zero.done:notice]: Disk 0a.22 Shelf ? Bay ? [NETAPP X276_S10K7288F10 NA01] S/N [3KR18QV900007617LZY3] : disk zeroing complete ..................Mon Mar 20 09:15:48 GMT [raid.disk.zero.done:notice]: Disk 0a.16 Shelf ? Bay ? [NETAPP X276_S10K7288F10 NA01] S/N [3KR18PE1000076187KXZ] : disk zeroing complete ...............Mon Mar 20 09:15:52 GMT [raid.disk.zero.done:notice]: Disk 0a.21 Shelf ? Bay ? [NETAPP X276_S10K7288F10 NA01] S/N [3KR17PT300007617M1P2] : disk zeroing complete .................................................................................................................................................................... ...............Mon Mar 20 09:16:42 GMT [raid.disk.zero.done:notice]: Disk 0a.17 Shelf ? Bay ? [NETAPP X276_S10K7288F10 NA01] S/N [3KR18Y6700007617695Y] : disk zeroing complete .................................................................................................................................................................... .............Mon Mar 20 09:18:44 GMT [raid.disk.zero.done:notice]: Disk 0a.19 Shelf ? Bay ? [NETAPP X276_S10K7288F10 NA01] S/N [3KR1911Z0000761769R8] : disk zeroing completeMon Mar 20 09:18:45 GMT [raid.vol.disk.add.done:notice]: Addition of Disk /aggr0/plex0/rg0/0a.18 Shelf 1 Bay 2 [NETAPP X276_S10K7288F10 NA01] S/N [3KR18YGC000076187JGK] to aggregate aggr0 has completed successfullyMon Mar 20 09:18:45 GMT [raid.vol.disk.add.done:notice]: Addition of Disk /aggr0/plex0/rg0/0a.17 Shelf 1 Bay 1 [NETAPP X276_S10K7288F10 NA01] S/N [3KR18Y6700007617695Y] to aggregate aggr0 has completed successfullyMon Mar 20 09:18:45 GMT [raid.vol.disk.add.done:notice]: Addition of Disk /aggr0/plex0/rg0/0a.16 Shelf 1 Bay 0 [NETAPP X276_S10K7288F10 NA01] S/N [3KR18PE1000076187KXZ] to aggregate aggr0 has completed successfullyMon Mar 20 09:18:45 GMT [wafl.vol.add:notice]: Aggregate aggr0 has been added to the system. Mon Mar 20 09:18:46 GMT [fmmbx_instanceWorke:info]: no mailbox instance on primary sideMon Mar 20 09:18:47 GMT [fmmbx_instanceWorke:info]: Disk 0a.18 is a primary mailbox disk Mon Mar 20 09:18:47 GMT [fmmbx_instanceWorke:info]: Disk 0a.17 is a primary mailbox disk Mon Mar 20 09:18:47 GMT [fmmbx_instanceWorke:info]: normal mailbox instance on primary side Mon Mar 20 09:18:47 GMT [fmmbx_instanceWorke:info]: Disk 0b.18 is a backup mailbox diskMon Mar 20 09:18:47 GMT [fmmbx_instanceWorke:info]: Disk 0b.17 is a backup mailbox diskMon Mar 20 09:18:47 GMT [fmmbx_instanceWorke:info]: normal mailbox instance on backup sideMon Mar 20 09:18:48 GMT [lun.metafile.dirCreateFailed:error]: Couldn't create vdisk metafile directory /vol/vol0/vdisk.DBG: Set filer.serialnum to: 1071155ifconfig e0a mediatype autoConfiguring onboard ethernet e0a.Contacting DHCP server.Ctrl-C to skip DHCP search ...Mon Mar 20 09:18:48 GMT [rc:info]: Contacting DHCP serverMon Mar 20 09:18:52 GMT [rc:info]: DHCP config failedConfiguring e0a using DHCP failed.NetApp Release 7.0.3: Fri Dec 2 06:00:21 PST 2005System ID: 010******* (); partner ID: <unknown> ()System Serial Number: 1071155 ()System Rev: E0slot 0: System BoardProcessors: 1Memory Size: 2048 MBslot 0: Dual 10/100/1000 Ethernet Controller VIe0a MAC Address: 00:a0:98:03:88:13 (auto-unknown-cfg_down)e0c MAC Address: 00:a0:98:03:88:10 (auto-unknown-cfg_down)e0d MAC Address: 00:a0:98:03:88:11 (auto-unknown-cfg_down) slot 0: FC Host Adapter 0a8 Disks: 2176.0GB1 shelf with ESH2slot 0: FC Host Adapter 0b8 Disks: 2176.0GB1 shelf with ESH2slot 0: Fibre Channel Target Host Adapter 0cslot 0: Fibre Channel Target Host Adapter 0dslot 0: SCSI Host Adapter 0eslot 0: NetApp ATA/IDE Adapter 0f (0x000001f0)0f.0 245MBslot 3: NVRAMMemory Size: 512 MBPlease enter the new hostname []: headb输入这个机头的主机名,这里举例为headb;Do you want to configure virtual network interfaces? [n]: y问是否要配置虚拟网卡,如果要创建的话,输入y;Number of virtual interfaces to configure? [0] 1输入要配置几块虚拟网卡,如配置1块虚拟网卡,就输入1;Name of virtual interface #1 []: vif1输入虚拟网卡的名称,这里举例为vif1;Is vif1 a single [s] or multi [m] virtual interface? [m] s选择虚拟网卡的类型是single还是multi,这里选择s;Number of links for vif1? [0] 2虚拟网卡所包含真实网卡的数量,如果用两块网卡绑定成一块虚拟网卡就输入2;Name of link #1 for vif1 []: e0a输入用于绑定的真实网卡的设备名,可以从阵列设备后面的网络接口上看到;Name of link #2 for vif1 []: e0b输入用于绑定的真实网卡的设备名,可以从阵列设备后面的网络接口上看到;Please enter the IP address for Network Interface vif1 []: 192.168.0.88输入虚拟网卡的IP地址;Please enter the netmask for Network Interface vif1 [255.255.255.0]:输入虚拟网卡的掩码,默认就直接回车;Should virtual interface vif1 take over a partner virtual interface during failover? [n]: y是否允许虚拟网卡在故障时切换到另一个机头上,输入y;The clustered failover software is not yet licensed. To enablenetwork failover, you should run the 'license' command forclustered failover.会提示说没有输入Clustered failover功能的license,需要输入才能实现网络切换功能;Please enter the partner virtual interface name to be taken over by vif1 []: vif1输入另一个机头上的会被切换过来的虚拟网卡的名字;Please enter media type for vif1 {100tx-fd, tp-fd, 100tx, tp, auto (10/100/1000)} [auto]:输入虚拟网卡的类型,一般是自适应,选默认auto;Please enter the IP address for Network Interface e0c []:输入网卡e0c的IP地址,不设置就直接回车;Should interface e0c take over a partner IP address during failover? [n]: n是否允许网卡e0c在故障时切换到另一个机头上,这里不配置就输入n;Please enter the IP address for Network Interface e0d []:输入网卡e0d的IP地址,不设置就直接回车;Should interface e0d take over a partner IP address during failover? [n]: n是否允许网卡e0d在故障时切换到另一个机头上,这里不配置就输入n;Would you like to continue setup through the web interface? [n]: n问是否通过web方式来进行继续的安装,输入n,不需要;Please enter the name or IP address of the default gateway:输入默认网关的名字和IP地址,无须输入就直接回车;The administration host is given root access to the filer's/etc files for system administration. To allow /etc root accessto all NFS clients enter RETURN below.Please enter the name or IP address of the administration host:输入超级管理主机的主机名或IP地址,没有就直接回车;Where is the filer located? []: nanjing问磁盘阵列设备的位置,可以随便写,比如南京,就输入nanjing;Do you want to run DNS resolver? [n]:是否配置DNS,输入n,不配置;Do you want to run NIS client? [n]:是否配置NIS,输入n,不配置;This system will send event messages and weekly reports to Network Appliance Technical Support. To disable this feature, enter "options autosupport.support.enable off" within 24 hours. Enabling Autosupport can significantly speed problem determination and resolution should a problem occur on your system. For further information on Autosupport, please see: /autosupport/ Press the return key to continue.提示说,阵列系统默认的自动发送事件日志和周报告功能是打开的,如果需要关闭,请输入options autosupport.support.enable off。
ssd1963ql9使用手册

7.1 MCU INTERFACE .................................................................................................................................................16 7.1.1 6800 Mode ..................................................................................................................................................16 7.1.2 8080 Mode ..................................................................................................................................................16 7.1.3 Register Pin Mapping .................................................................................................................................16 7.1.4 Pixel Data Format ......................................................................................................................................16 7.1.5 Tearing Effect Signal (TE) ..........................................................................................................................17 7.2 SYSTEM CLOCK GENERATION .............................................................................................................................18 7.3 FRAME BUFFER....................................................................................................................................................19 7.4 SYSTEM CLOCK AND RESET MANAGER ...............................................................................................................19 7.5 LCD CONTROLLER ..............................................................................................................................................20 7.5.1 Display Format ...........................................................................................................................................20 7.5.2 General Purpose Input/Output (GPIO) ......................................................................................................20
ACD3图纸(DAA21311AD)

/81.A1
TB2
OCB
PE
PE*DRV
/(16~20).C1
D
TB2
L1*DRV L2*DRV 14 C B L3*DRV A
D
/(16~20).C1
J-Relay
13 _10%) (AC380V+
MR & KOREA & ARO
E
Wiring Diagram
ACD3
E
DAA21311AD
Alex Ren Jason Wu Harry Wang CN187263
2T1 4T2 6T3 14 22 32 44
B
EC4: 1
B
5L3 13 21 31 43
3 1 E*Frame
6E 2 EC4: 2
4 2
3
4 2
/6.D5
1
/6.D7
PE*Frame E&I PANEL
/102C.A8
MC
CDC_ST
7E 1
13
14
7E 2
CDC_ST
/83.E5
PE*NET Frame*PE
A
N
/(7~14).C1
OCB
/96.A1
TBE1: N NET*N PL*N LIH*N PMS*PE
/96.A1 /96.B4 /96.C2
TB2
CB1
PE
PE*DRV
/(16~20).C1
TB2
L1*DRV L2*DRV L3*DRV
PE*NET
TBE2: PE
/(16~20).C1
B
PE*Frame
U1*VAC U2*VAC V1*VAC
SYSTEMSENSOR SS-310-00 1 I56-3381-002 INSTALLATION

SpecificaTiOnS Dimensions: 4.8"W x 5.3"H x 1.6"D (12.2cm W x 11.9 cm H x 3.8 cm D)Weight:0.35 lb. (160 g)Operating Voltage: 20-29 VDCPower Requirements Standby: 3.0 mA max. Trouble:16.0 mA max Alarm w/o strobe: 30 mA max Alarm with strobe: 55 mA maxConnections: Strip terminal, 14 A WG to 22 A WG wire Wiring Distance: 1000 Feet From Duct Smoke Detector Sounder: 85 dBA at ten feetT emperature: 14°F to 140°F (-10°C to 60°C)Humidity: 95% relative humidity; non-condensing Listing:UL 268rTS2, rTS2-aOS, aOS multi-Signaling accessoryinSTaLLaTiOn and mainTenance inSTrucTiOnS3825 Ohio Avenue, St. Charles, Illinois 601741-800-SENSOR2, FAX: 630-377-6495H0621-00I56-3381-002Notice: This manual should be left with the owner/user of this equipment.generaL infOrmaTiOnThe National Fire Protection Association (NFPA) has published codes, stan-dards, and recommended practices for the installation and use of this product. It is recommended that the installer be familiar with theses requirements, with local codes, and any special requirements of the local authority having juris-diction. For further information, consult NFPA 72 and 90A requirements.The System Sensor RTS2 and RTS2-AOS multi-signaling accessories are de-signed for use with System Sensor InnovairFlex 4-wire conventional duct smoke detectors only. The accessory has two bicolored LEDs that indicate the sensor status of up to two connected duct smoke detectors. The key switch on the unit can be used to select a connected duct detector sensor (either sen-sor 1 or sensor 2), and the selected sensor can be tested or both sensors can be reset simultaneously using the test/reset button. LED status indications include: Standby (green blink), Trouble (amber), Maintenance (amber blink) and Alarm (red).With the key switch selected, there is also the capability of obtaining a sen-sitivity measurement of the selected sensor using the SENS-RDR sensitivity reader (sold separately).Specific feaTureS Of The rTS2 and rTS2-aOS incLude:Standby (Green Blink), Trouble (Amber), Maintenance (Amber Blink) • and Alarm (Red) LEDs to indicate detector status Keyswitch to select desired sensor, enable test/reset button and • sensitivity reading T est/reset button• Sensitivity reading ability with SENS-RDR (sold separately)• Selectable continuous or temporal tone• AOS-Add-On-Strobe (included on RTS2-AOS model)• Provisions for single- or double-gang box mounting• Ability to discretely monitor two sensors when duct smoke detectors • are configured in a 2-to-1 set up (See InnovairFlex duct smoke detector manual for reference.)cOnTenTS1 RTS2 or RTS2-AOS Multi-Signaling Accessory1 Mounting Hardware Kit (Contains (2) sets of mounting screws and (1) tam-per resistant outer cover mounting screw.figure 1:figure 3: Wiring diagraminSTaLLaTiOninstalling the mounting plate1. S ecure the mounting plate to a single- or double-gang electrical box with(2) mounting screws provided. Note: If mounting to a single-gang box, the Add-On Strobe (AOS) must be removed prior to mounting. T o remove the AOS, squeeze opposing sides lightly next to arrows and slide vertically. 2. I f applicable, install the AOS onto the mounting plate as shown in Figure 2. Note, the RTS-AOS includes the AOS.Temporal SounderThe RTS2 accessory provides the option of sounding a continuous or temporal pattern. The RTS2 will default to sound in a temporal pattern. For a continu-ous pattern, remove the jumper located just to the right of the “Strobe” text on the mounting plate as shown in Figure 2.WiringWire the RTS2 as shown in Figure 3, for InnovairFlex 4-wire conventional duct smoke detectors. Limit wire runs to 25 ohms or less per interconnecting wire. nOTe:1. I f polarity of Acc. (+) and Acc. ( —) are reversed, an Amber LED on sensor2 of the duct smoke detector power board will exist indicating a trouble condition.2. One RTS2 can be wired to only one InnovairFlex power board.3. I f Aux. (+) and Aux. (—) wires are reversed, the strobe and sounder will not function.installing the Outer cover1.Install the outer cover on the mounting plate by sliding the outer cover over the upper tabs of the mounting plate as shown in Figures 4 and 5.2.Tighten the outer cover mounting screw located at the bottom of the device. Note: The mounting screw can be replaced with the provided tamper resistant Torx screw, if desired.LEDsROUTER COVER L OCKING SCRE W Y READERH0624-00figure 2:OperaTiOnThe green “Standby” will blink every 5 seconds whenever the duct smoke detector is receiving power. The amber “Trouble” LED is lit when the duct smoke detector sensor is missing or the detector cover is removed. The delay to indicate a trouble condition once the cover is removed depends on the dip switch setting on the duct smoke detector power board. An LED with amber blink every 5 seconds indicates that the sensor is in “Maintenance” which in-dicates that the sensor needs to be cleaned or replaced. See T able 1 LED Status Indication for a detailed list of indications.enabling the Test/reset/Sensitivity OperationInsert the key and turn to select either sensor 1 or 2. This will enable the selected sensor to be tested, reset, or sensitivity read. Note all test/reset/sen-sitivity functions can be initiated with the outer cover installed or directly on the mounting plate.Test functionWith the desired sensor selected by the key, press and hold the T est/Reset but-ton for 2 seconds. If the sensor is within its sensitivity limits, the device will alarm within the next 3 seconds.alarm indicationOnce the T est/Reset button has been pressed, the red alarm LED will illumi-nate and the horn will sound (within 5 seconds). If an AOS (add-on strobe) is installed, it will flash.reset functionReset is a common function to both sensors. Press and release the T est/Reset Button. The red alarm LED should turn off on both sensor LEDs and the horn will cease sounding. The strobe will cease flashing (if optioned). The current sensor status will be indicated (See T able 1). Note, the key switch must still be selected for one of the sensors in order for the reset function to be enabled.Sensitivity functionWhen the key is installed and sensor 1 or 2 is selected, the selected sensor sensitivity can be read via a SENS-RDR (sold separately).1. Select the desired sensor with the key.2. P ress the test button on the SENS-RDR. “Ready” should appear on the SENS-RDR display.3. H old the SENS-RDR up to the oval indentation on the mounting plate or outer cover (if installed). Within 10 seconds the sensor sensitivity will be displayed.disabling the Test/reset/Sensitivity OperationWhen the key switch is returned to the neutral (vertical) position and removed, the Test/Reset button will be disabled.H0623-00H0625-00figure 4:figure 5:mode indication Off LEDs off Initialization Green/Amber blinkNormal Green blink Maintenance Amber blink Communication ErrorAmber long blink Trouble Solid Amber AlarmSolid RedTabLe 1: Led STaTuS indicaTiOnS* P lease note that the mode of the LEDs on the RTS2 represent the mode of the respective sensors connected to the InnovairFlex duct power board.** R efer to the InnovairFlex installation and maitenance instructions for additional LED/Status details.System Sensor warrants its enclosed product to be free from defects in materials and workmanship under normal use and service for a period of three years from date of manufacture. System Sensor makes no other express warranty for the enclosed product. No agent, representative, dealer, or employee of the Company has the authority to in-crease or alter the obligations or limitations of this Warranty. The Company’s obligation of this Warranty shall be limited to the replacement of any part of the product which is found to be defective in materials or workmanship under normal use and service during the three year period commencing with the date of manufacture. After phoning System Sensor’s toll free number 800-SENSOR2 (736-7672) for a Return Authorization number, send defective units postage prepaid to: System Sensor, Returns Department, RAThree-Year LimiTed WarranTY#__________, 3825 Ohio Avenue, St. Charles, IL 60174. Please include a note describing the malfunction and suspected cause of failure. The Company shall not be obligated to replace units which are found to be defective because of damage, unreasonable use, modifications, or alterations occurring after the date of manufacture. In no case shall the Company be liable for any consequential or incidental damages for breach of this or any other Warranty, expressed or implied whatsoever, even if the loss or damage is caused by the Company’s negligence or fault. Some states do not allow the exclusion or limitation of incidental or consequential damages, so the above limitation or exclusion may not apply to you. This Warranty gives you specific legal rights, and you may also have other rights which vary from state to state.The sounder or sounder/strobe combination will not operate if the power is cut off for any reason.If power is cut off for any reason, the sounder or strobe/sounder combination will not provide the desired audible or visual warning.The sounder may not be heard. The loudness of the sounder meets or exceeds the current Underwriters Laboratories’ standards. However, the sounder may not alert a sound sleeper or one who has recently used drugs or has been drinking alcoholic beverages. This sounder may not be heard if it is placed in an area that is separated by a closed door, or if it is located on a different floor from the person in a hazardous situation, or if it is placed too far to be heard over ambient noise, such as, traffic, air conditioners, machinery or musical appliances that may prevent alert persons from hearing the alarm. For these reasons, System Sensor recommends that sounders (85dBA minimum at 10 feet) used in a residence shall be placed on every level and in every bedroom that does not have a smoke detector with a built-in sounder.)The sounder may not be heard by persons who are hearing-impaired. In this case, a visual indicator shall also be used.The Sounder and add-on strobe are for supplemental signaling only. The signal strobe may not be seen. The visual warning signal is suitable for direct viewing and must be installed within an area where it can be seen by building occupants. The strobe must not be installed in direct sunlight or ar-eas of high light intensity where the visual flash might be disregarded or not seen.The strobe may not be seen by the visually impaired.The signal strobe may cause seizures. Individuals who have a positive photic response to visual stimuli with seizure, such as epileptics, should avoid pro-longed exposure to environments in which strobe signals, including this strobe, are activated.SENSOR UNITPOWER BOARD UNITH0621-00H0627-00H0614-02H0487-00H0486-00H0489-00Ordering infOrmaTiOn RTS2 Multi-Signaling AccessoryRTS2-AOSMulti-Signaling Accessory with Strobe AOSAdd-On StrobeinnOvairfLex ducT SmOke deTecTOrSD4120 4-Wire Photoelectric Duct Smoke Detector D4120W4-Wire Watertight Duct Smoke Detector D4P120 4-Wire Power Board-Only Component D4S4-Wire Photoelectric Additional SensorOTher acceSSOrieS RTS151 Remote T est/Reset StationRTS151KEYKey-Activated Remote T est/Reset Station APA151 Piezo Annunciator RA100ZRemote Annunciator Alarm SENS-RDRSensitivity ReaderRTS2/AOSRTS2-AOS。
MGate MB3660系列固件发布说明书
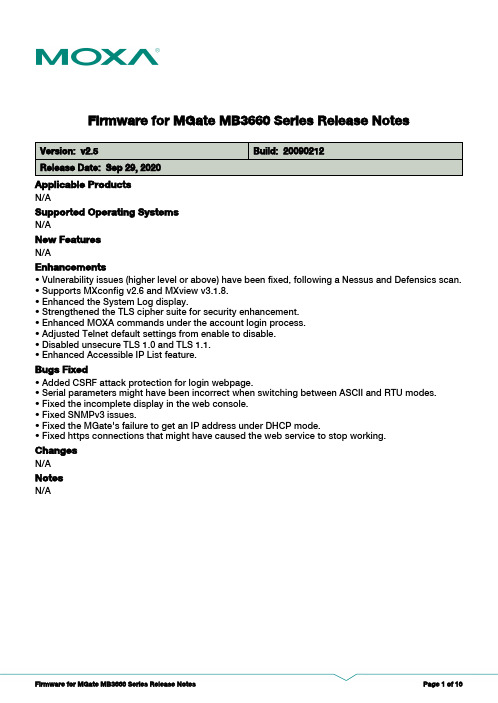
Firmware for MGate MB3660 Series Release NotesSupported Operating SystemsNotesChangesApplicable ProductsBugs Fixed• Vulnerability issues (higher level or above) have been fixed, following a Nessus and Defensics scan.• Supports MXconfig v2.6 and MXview v3.1.8.• Enhanced the System Log display.• Strengthened the TLS cipher suite for security enhancement.• Enhanced MOXA commands under the account login process.• Adjusted Telnet default settings from enable to disable.• Disabled unsecure TLS 1.0 and TLS 1.1.• Enhanced Accessible IP List feature.• Added CSRF attack protection for login webpage.• Serial parameters might have been incorrect when switching between ASCII and RTU modes.• Fixed the incomplete display in the web console.• Fixed SNMPv3 issues.• Fixed the MGate's failure to get an IP address under DHCP mode.• Fixed https connections that might have caused the web service to stop working.EnhancementsN/AN/AN/ANew FeaturesN/AN/ASupported Operating SystemsNotesChangesApplicable ProductsBugs FixedN/AN/AEnhancementsN/AN/ASupports MGate MB3660I-8-2AC and MGate MB3660I-16-2AC new hardware version v1.1.New FeaturesN/AN/ASupported Operating SystemsNotesChangesApplicable ProductsBugs Fixed• Accessible IP List supports denying Web/Telnet console access.• In Agent mode as a Modbus ASCII master, MGate would hang after plugging and unplugging a serial cable.EnhancementsN/AMGate MB3660-8-J-2AC, MGate MB3660I-16-2AC, MGate MB3660-16-J-2AC, MGate MB3660-8-2AC, MGate MB3660-8-2DC, MGate MB3660I-8-2AC, MGate MB3660-16-2AC, MGate MB3660-16-2DC• Supports security features based on IEC-62443.New FeaturesN/AN/ASupported Operating SystemsNotesChangesApplicable ProductsBugs Fixed• Enhanced the complexity of token generation to protect against CSRF attacks.• Enhanced the complexity of the key for password encryption in the web console login process.• Encrypts sensitive information in exported configuration file.• Enhanced the display of auto detection results in MODBUS transparent mode.• Firmware version check problem when upgrading firmware for MGate MB3660I-16-2AC, MB3660-8-J-2AC, and MB3660-16-J-2AC.• Modbus RTU communication would fail if FIFO was disabled.• The FIFO setting would not be activated after clicking the “Submit” button.• Stack-based buffer overflow issue in web console which may cause web service corruption.• Challenge ID generation problem which may cause web console login failure.EnhancementsN/AMGate MB3660-8-J-2AC, MGate MB3660I-16-2AC, MGate MB3660-16-J-2AC, MGate MB3660-8-2AC, MGate MB3660-8-2DC, MGate MB3660I-8-2AC, MGate MB3660-16-2AC, MGate MB3660-16-2DCN/ANew FeaturesN/AN/ASupported Operating SystemsNotesChangesApplicable ProductsBugs Fixed• Improved security of the TCP sequence number.• Improved beeper behavior in DHCP mode.• Modbus RTU diagnose error in agent mode.• Initial error relay state when powered on.EnhancementsN/AMGate MB3660-8-J-2AC, MGate MB3660I-16-2AC, MGate MB3660-16-J-2AC, MGate MB3660-8-2AC, MGate MB3660-8-2DC, MGate MB3660I-8-2AC, MGate MB3660-16-2AC, MGate MB3660-16-2DC• Supports MGate MB3660I-16-2AC, MGate MB3660-8-J-2AC, MGate MB3660-16-J-2AC models.New FeaturesN/AN/ASupported Operating SystemsNotesChangesApplicable ProductsBugs Fixed• The Modbus master in agent mode supports up to 256 commands for each serial port.• Supports multi-master in "routing by IP address" and "routing by TCP port" modes.• Supports sorting of commands in the I/O mapping page.• Supports auto internal memory assign in the command page.• Supports Modbus slave ID 255 in transparent mode.• User password and SNMP community name may be exposed by a buffer overflow issue.EnhancementsN/AMGate MB3660-8-2AC, MGate MB3660-8-2DC, MGate MB3660I-8-2AC, MGate MB3660-16-2AC,MGate MB3660-16-2DC• Supports Auto Device Routing in Modbus transparent mode.• Supports Modbus TCP traffic logs.New FeaturesN/AN/ASupported Operating SystemsNotesChangesApplicable ProductsBugs FixedN/A• Bug in Modbus Master mode which may cause the MGate to reboot under some conditions.EnhancementsN/AMGate MB3660-8-2AC, MGate MB3660-8-2DC, MGate MB3660I-8-2AC, MGate MB3660-16-2AC,MGate MB3660-16-2DCN/ANew FeaturesN/AN/ASupported Operating SystemsNotesChangesApplicable ProductsBugs FixedN/A• Initial delay issue which would stop Modbus communication.EnhancementsN/AMGate MB3660-8-2AC, MGate MB3660-8-2DC, MGate MB3660I-8-2AC, MGate MB3660-16-2AC,MGate MB3660-16-2DCN/ANew FeaturesN/AN/ASupported Operating SystemsNotesChangesApplicable ProductsBugs FixedN/A• Fix the algorithm which may cause Modbus transparent mode to stop communication.• Serial port 13 interface initialization problem.• Modbus traffic exceptions in the serial port are not handled well, which might cause the serial port to stop transmitting data.• When the "Read memory address" is greater or equal to 8192 for the "01 - Read Coils" or "02 -Read Discrete Inputs" functions, data will be written to the wrong internal memory address.EnhancementsN/AMGate MB3660-8-2AC, MGate MB3660-8-2DC, MGate MB3660I-8-2AC, MGate MB3660-16-2AC,MGate MB3660-16-2DCN/ANew FeaturesN/AN/ASupported Operating SystemsNotesChangesApplicable ProductsBugs FixedN/AN/AEnhancementsN/AMGate MB3660-8-2AC, MGate MB3660-8-2DC, MGate MB3660I-8-2AC, MGate MB3660-16-2AC,MGate MB3660-16-2DC• First release.New FeaturesN/AN/A。
IBM Spectrum Control V5.2.12 快速入门指南说明书
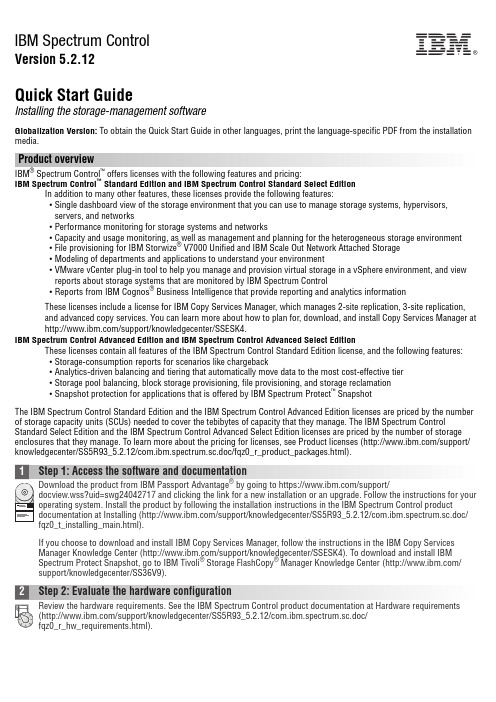
IBM Spectrum ControlVersion 5.2.12Quick Start GuideInstalling the storage-management softwareGlobalization Version:To obtain the Quick Start Guide in other languages, print the language-specific PDF from the installation media.Product overviewIBM®Spectrum Control™offers licenses with the following features and pricing:IBM Spectrum Control™Standard Edition and IBM Spectrum Control Standard Select EditionIn addition to many other features, these licenses provide the following features:v Single dashboard view of the storage environment that you can use to manage storage systems, hypervisors,servers, and networksv Performance monitoring for storage systems and networksv Capacity and usage monitoring, as well as management and planning for the heterogeneous storage environmentv File provisioning for IBM Storwize®V7000 Unified and IBM Scale Out Network Attached Storagev Modeling of departments and applications to understand your environmentv VMware vCenter plug-in tool to help you manage and provision virtual storage in a vSphere environment, and viewreports about storage systems that are monitored by IBM Spectrum Controlv Reports from IBM Cognos®Business Intelligence that provide reporting and analytics informationThese licenses include a license for IBM Copy Services Manager, which manages 2-site replication, 3-site replication, and advanced copy services. You can learn more about how to plan for, download, and install Copy Services Manager at /support/knowledgecenter/SSESK4.IBM Spectrum Control Advanced Edition and IBM Spectrum Control Advanced Select EditionThese licenses contain all features of the IBM Spectrum Control Standard Edition license, and the following features:v Storage-consumption reports for scenarios like chargebackv Analytics-driven balancing and tiering that automatically move data to the most cost-effective tierv Storage pool balancing, block storage provisioning, file provisioning, and storage reclamationv Snapshot protection for applications that is offered by IBM Spectrum Protect™SnapshotThe IBM Spectrum Control Standard Edition and the IBM Spectrum Control Advanced Edition licenses are priced by the number of storage capacity units (SCUs) needed to cover the tebibytes of capacity that they manage. The IBM Spectrum Control Standard Select Edition and the IBM Spectrum Control Advanced Select Edition licenses are priced by the number of storage enclosures that they manage. To learn more about the pricing for licenses, see Product licenses (/support/ knowledgecenter/SS5R93_5.2.12/com.ibm.spectrum.sc.doc/fqz0_r_product_packages.html).If you choose to download and install IBM Copy Services Manager, follow the instructions in the IBM Copy Services Manager Knowledge Center (/support/knowledgecenter/SSESK4). To download and install IBMSpectrum Protect Snapshot, go to IBM Tivoli®Storage FlashCopy®Manager Knowledge Center (/ support/knowledgecenter/SS36V9).2Step 2: Evaluate the hardware configurationReview the hardware requirements. See the IBM Spectrum Control product documentation at Hardware requirements (/support/knowledgecenter/SS5R93_5.2.12/com.ibm.spectrum.sc.doc/fqz0_r_hw_requirements.html).IBM®3Step 3: Evaluate the system configuration and install the prerequisite software Review the software requirements:v Learn about the software requirements for the product at Software requirements (/support/knowledgecenter/SS5R93_5.2.12/com.ibm.spectrum.sc.doc/fqz0_r_sw_requirements.html).v Learn about the hardware, products, and operating systems that you can use with IBM Spectrum Control at/support/docview.wss?uid=swg21386446.4Step 4: Install DB2Before you install IBM Spectrum Control, you must install the version of IBM DB2®Enterprise Server Edition that isincluded with IBM Spectrum Control. IBM Spectrum Control stores the information that it collects about storageresources in a DB2 database.Follow the instructions in DB2 (/support/knowledgecenter/SS5R93_5.2.12/com.ibm.spectrum.sc.doc/ fqz0_t_installing_db2.html).5Step 5: Install IBM Spectrum ControlYou can use an installation program or a command line in silent mode to install IBM Spectrum Control. Follow theinstructions in Installing IBM Spectrum Control (/support/knowledgecenter/SS5R93_5.2.12/com.ibm.spectrum.sc.doc/fqz0_t_installing_tpc.html).6Step 6: (Optional) Install Cognos Business Intelligence reportsThe IBM Spectrum Control installation process includes the option to install IBM Cognos Business Intelligence (BI)reports and the product that is required to produce these reports: Jazz™for Service Management and its reportingservices (IBM Tivoli Common Reporting). Cognos BI produces scheduled reports from the data that is gathered by IBM Spectrum Control.Learn about Cognos BI reports at Reporting (/support/knowledgecenter/SS5R93_5.2.12/com.ibm.spectrum.sc.doc/fqz0_c_webbasedgui_rpting_ic_ov.html). Also learn about the components that you must install to use Cognos BI reports at Install Jazz for Service Management and Tivoli Common Reporting(/support/knowledgecenter/SS5R93_5.2.12/com.ibm.spectrum.sc.doc/fqz0_c_jazzsm_tcr.html).If you choose not to install Cognos BI, you can use the reporting features of the IBM Spectrum Control user interface to produce reports about the status, capacity, and performance of the storage resources that you want to monitor. If you have the Advanced Edition or Advanced Select Edition license, chargeback and consumer reports are available.7Step 7: Get startedFollow the tasks in Getting started with IBM Spectrum Control (/support/knowledgecenter/SS5R93_5.2.12/com.ibm.spectrum.sc.doc/fqz0_r_getting_started.html).More informationFor more information, see the following resources:v PDF product documentation: Printable documentation (/support/knowledgecenter/SS5R93_5.2.12/ com.ibm.spectrum.sc.doc/fqz0_r_printable_pdf_files.html)v Product support: https:///support/entry/myportal/product/tivoli/ibm_spectrum_control/ibm_spectrum_control_standard_edition?productContext=365750483IBM Spectrum Control Version 5.2.12 Licensed Materials - Property of IBM. © Copyright IBM Corp. 2014, 2016. US Government Users Restricted Rights - Use, duplication or disclosure restricted by GSA ADP Schedule Contract with IBM Corp.IBM, the IBM logo, and ®are trademarks or registered trademarks of International Business Machines Corp., registered in many jurisdictions worldwide. Other product and service names might be trademarks of IBM or other companies. A current list of IBM trademarks is available on the web at “Copyright and trademark information” (/legal/copytrade.shtml).Printed in Ireland。
07- TSM V6.1 Monitoring and Reporting

Discovering the value of the IBM Tivoli Storage Manager v6.2 Product Family
Tivoli Storage Manager v6.x Monitoring and Reporting
An IBM Proof of Technology
The Tivoli Monitoring agent is installable on this OS
The agent is NOT installable on this OS but is able to monitor TSM remotely from the Tivoli Monitoring server The agent is NOT installable on this OS but is able to monitor TSM remotely from the Tivoli Monitoring server The agent is NOT installable on this OS but is able to monitor TSM remotely from the Tivoli Monitoring server The Tivoli Monitoring agent is installable on this OS
● Can monitor and report 5.4, 5.5 and 6.x servers ● No need to license DB2, Tivoli Monitoring or Tivoli Common Reporting separately
© 2010 IBM Corporation
- 1、下载文档前请自行甄别文档内容的完整性,平台不提供额外的编辑、内容补充、找答案等附加服务。
- 2、"仅部分预览"的文档,不可在线预览部分如存在完整性等问题,可反馈申请退款(可完整预览的文档不适用该条件!)。
- 3、如文档侵犯您的权益,请联系客服反馈,我们会尽快为您处理(人工客服工作时间:9:00-18:30)。
Management, 10e (Robbins)Chapter 6 Managers as Decision Makers1) Problem identification is purely objective.Answer: FALSEDiff: 2 Page Ref: 121Topic: The Decision-Making Process2) The second step in the decision-making process is identifying a problem. Answer: FALSEDiff: 1 Page Ref: 122Topic: The Decision-Making Process3) A decision criterion defines what is relevant in a decision.Answer: TRUEDiff: 2 Page Ref: 122Topic: The Decision-Making Process4) The fourth step of the decision-making process requires the decision maker to list viable alternatives that could resolve the problem.Answer: TRUEDiff: 1 Page Ref: 123Topic: The Decision-Making Process5) Once the alternatives have been identified, a decision maker must analyze each one.Answer: TRUEDiff: 2 Page Ref: 123Topic: The Decision-Making Process6) The step in the decision-making process that involves choosing a best alternative is termed implementation.Answer: FALSEDiff: 2 Page Ref: 123Topic: The Decision-Making Process7) Making decisions is with the essence of management.Answer: TRUEDiff: 1 Page Ref: 120Topic: Decision-Making Styles8) Managerial decision making is assumed to be rational.Topic: Decision-Making Styles9) One assumption of rationality is that we cannot know all of the alternatives. Answer: FALSEDiff: 3 Page Ref: 124Topic: Decision-Making Styles10) Managers tend to operate under assumptions of bounded rationality. Answer: TRUEDiff: 2 Page Ref: 125Topic: Decision-Making Styles11) Studies of the events leading up to the Challenger space shuttle disaster point to an escalation of commitment by decision makers.Answer: TRUEDiff: 2 Page Ref: 126Topic: Decision-Making Styles12) Managers regularly use their intuition in decision making.Answer: TRUEDiff: 1 Page Ref: 126Topic: Decision-Making Styles13) Rational analysis and intuitive decision making are complementary. Answer: TRUEDiff: 2 Page Ref: 126Topic: Decision-Making Styles14) Programmed decisions tend to be repetitive and routine.Answer: TRUEDiff: 1 Page Ref: 127Topic: Types of Decisions and Decision-Making Conditions15) Rules and policies are basically the same.Answer: FALSEDiff: 2 Page Ref: 128Topic: Types of Decisions and Decision-Making Conditions16) A policy is an explicit statement that tells a manager what he or she ought or ought not to do.Topic: Types of Decisions and Decision-Making Conditions17) The solution to nonprogrammed decision making relies on procedures, rules, and policies.Answer: FALSEDiff: 2 Page Ref: 128Topic: Types of Decisions and Decision-Making Conditions18) Most managerial decisions in the real world are fully nonprogrammed. Answer: FALSEDiff: 1 Page Ref: 128Topic: Types of Decisions and Decision-Making Conditions19) The ideal situation for making decisions is low risk.Answer: FALSEDiff: 2 Page Ref: 129Topic: Types of Decisions and Decision-Making Conditions20) Risk is the condition in which the decision maker is able to estimate the likelihood of certain outcomes.Answer: TRUEDiff: 1 Page Ref: 129Topic: Types of Decisions and Decision-Making Conditions21) Risk is a situation in which a decision maker has neither certainty nor reasonable probability estimates.Answer: FALSEDiff: 3 Page Ref: 129Topic: Types of Decisions and Decision-Making Conditions22) Most managers have characteristics of linear thinking style decision makers. Answer: FALSEDiff: 2 Page Ref: 131Topic: Types of Decisions and Decision-Making Conditions23) According to the boxed feature, "Managing Workforce Diversity," diverse employees tend to make decisions faster than a homogeneous group of employees. Answer: FALSEDiff: 2 Page Ref: 132Topic: Decision-Making StylesSkill: AACSB: Multicultural and Diversity24) The anchoring effect describes when decision makers fixate on initial information as a starting point and then, once set, they fail to adequately adjust for subsequent information.Answer: TRUEDiff: 2 Page Ref: 133Topic: Decision-Making Styles25) The availability bias describes when decision makers try to create meaning out of random events.Answer: FALSEDiff: 2 Page Ref: 134Topic: Decision-Making Styles26) The sunk cost error is when decision makers forget that current choices cannot correct the past.Answer: TRUEDiff: 2 Page Ref: 134Topic: Decision-Making Styles27) Today's business world revolves around making decisions, usually with complete or adequate information, and under minimal time pressure.Answer: FALSEDiff: 3 Page Ref: 135Topic: Effective Decision Making in Today's World28) Managers need to understand cultural differences to make effective decisions in today's fast-moving world.Answer: TRUEDiff: 2 Page Ref: 135Topic: Effective Decision Making in Today's WorldSkill: AACSB: Multicultural and Diversity29) Highly reliable organizations (HROs) are easily tricked by their success. Answer: FALSEDiff: 1 Page Ref: 136Topic: Effective Decision Making in Today's World30) Decision making is typically described as ________, which is a view that is too simplistic.A) deciding what is correctB) putting preferences on paperC) choosing among alternativesD) processing information to completionAnswer: CDiff: 2 Page Ref: 121Topic: The Decision-Making Process31) A series of eight steps that begins with identifying a problem and concludes with evaluating the decision's effectiveness is the ________.A) decision-making processB) managerial processC) maximin styleD) bounded rationality approachAnswer: ADiff: 1 Page Ref: 121Topic: The Decision-Making Process32) ________ is the existence of a discrepancy between an existing and a desired state of affairs.A) An opportunityB) A solutionC) A weaknessD) A problemAnswer: DDiff: 1 Page Ref: 121Topic: The Decision-Making Process33) In identifying the problem, a manager ________.A) compares the current state of affairs with where they would like to beB) expects problems to be defined by neon lightsC) looks for discrepancies that can be postponedD) will not act when there is pressure to make a decisionAnswer: ADiff: 1 Page Ref: 122Topic: The Decision-Making Process34) Which of the following statements is true concerning problem identification?A) Problems are generally obvious.B) A symptom and a problem are basically the same.C) Well-trained managers generally agree on what is considered a problem.D) The problem must be such that it exerts some type of pressure on the manager to act.Answer: DDiff: 2 Page Ref: 122Topic: The Decision-Making Process35) What is the second step in the decision-making process?A) identifying decision criteriaB) allocating weights to the criteriaC) analyzing alternativesD) identifying a problemAnswer: ADiff: 2 Page Ref: 122Topic: The Decision-Making Process36) To determine the ________, a manager must determine what is relevant or important to resolving the problem.A) geocentric behavior neededB) number of allowable alternativesC) weighting of decision criteriaD) decision criteriaAnswer: DDiff: 2 Page Ref: 122Topic: The Decision-Making Process37) What is the third step in the decision-making process?A) allocating weights to the criteriaB) analyzing the alternativesC) selecting the best alternativeD) implementing the alternativeAnswer: ADiff: 2 Page Ref: 122Topic: The Decision-Making Process38) If all criteria in the decision making are equal, weighting the criteria ________.A) improves decision making when large numbers of criteria are involvedB) is not neededC) produces excellent decisionsD) improves the criteriaAnswer: BDiff: 3 Page Ref: 122Topic: The Decision-Making Process39) In allocating weights to the decision criteria, which of the following is helpfulto remember?A) All weights must be the same.B) The total of the weights should sum to 1.0.C) Every factor criterion considered, regardless of its importance, must receive some weighting.D) Assign the most important criterion a score, and then assign weights against that standard.Answer: DDiff: 3 Page Ref: 122Topic: The Decision-Making Process40) What is the step where a decision maker wants to be creative in coming up with possible alternative?A) allocating weights to the criteriaB) analyzing alternativesC) developing alternativesD) identifying decision criteriaAnswer: CDiff: 1 Page Ref: 123Topic: The Decision-Making Process41) When analyzing alternatives, what becomes evident?A) the strengths and weaknesses of each alternativeB) the weighting of alternativesC) the list of alternativesD) the problemAnswer: ADiff: 1 Page Ref: 123Topic: The Decision-Making Process42) When developing alternatives in the decision-making process, what must a manager do?A) list alternativesB) evaluate alternativesC) weight alternativesD) implement alternativesAnswer: ADiff: 2 Page Ref: 123Topic: The Decision-Making Process43) Selecting an alternative in the decision-making process is accomplished by ________.A) choosing the alternative with the highest scoreB) choosing the one you like bestC) selecting the alternative that has the lowest priceD) selecting the alternative that is the most reliableAnswer: ADiff: 1 Page Ref: 123Topic: The Decision-Making Process44) In Step 6 of the decision-making process, each alternative is evaluated by appraising it against the ________.A) subjective goals of the decision makerB) criteriaC) assessed valuesD) implementation strategyAnswer: BDiff: 2 Page Ref: 123Topic: The Decision-Making Process45) ________ includes conveying a decision to those affected and getting their commitment to it.A) Selecting an alternativeB) Evaluating the decision effectivenessC) Implementing the alternativesD) Analyzing alternativesAnswer: CDiff: 2 Page Ref: 123Topic: The Decision-Making Process46) Which of the following is important in effectively implementing the chosen alternative in the decision-making process?A) getting upper-management supportB) double-checking your analysis for potential errorsC) allowing those impacted by the outcome to participate in the processD) ignoring criticism concerning your chosen alternativeAnswer: CDiff: 2 Page Ref: 123-124Topic: The Decision-Making Process47) The final step in the decision-making process is to ________.A) pick the criteria for the next decisionB) reevaluate the weightings of the criteria until they indicate the correct outcomeC) evaluate the outcome of the decisionD) reassign the ratings on the criteria to find different outcomesAnswer: CDiff: 2 Page Ref: 124Topic: The Decision-Making Process48) Which of the following is important to remember in evaluating the effectiveness of the decision-making process?A) You should ignore criticism concerning the decision-making process.B) You may have to start the whole decision process over.C) You will have to restart the decision-making process if the decision is less than50 percent effective.D) Ninety percent of problems with decision making occur in the implementation step.Answer: BDiff: 3 Page Ref: 124Topic: The Decision-Making Process49) Managers are assumed to be ________; they make consistent,value-maximizing choices within specified constraints.A) rationalB) leadersC) organizedD) satisficersAnswer: ADiff: 1 Page Ref: 124Topic: Decision-Making Styles50) It is assumed that a perfectly rational decision maker ________.A) does not follow rational assumptionsB) does not consider value maximizing as an objectiveC) offers inconsistent decisionsD) would be objective and logicalAnswer: DDiff: 2 Page Ref: 124Topic: Decision-Making Styles51) Managers can make rational decisions if ________.A) the problem is ambiguousB) the goals are unclearC) the alternatives are limitedD) time constraints existAnswer: CDiff: 3 Page Ref: 124Topic: Decision-Making Styles52) Which of the following is not a valid assumption about rationality?A) The problem is clear and unambiguous.B) A single, well-defined goal is to be achieved.C) Preferences are clear.D) Preferences are constantly changing.Answer: DDiff: 3 Page Ref: 124Topic: Decision-Making Styles53) When managers circumvent the rational decision-making model and find ways to satisfice, they are following the concept of ________.A) jurisprudenceB) bounded rationalityC) least-squared exemptionsD) self-motivated decisionsAnswer: BDiff: 2 Page Ref: 125Topic: Decision-Making Styles54) Because managers can't possibly analyze all information on all alternatives, managers ________, rather than ________.A) maximize; satisficeB) maximize; minimizeC) satisfice; minimizeD) satisfice; maximizeAnswer: DDiff: 2 Page Ref: 125Topic: Decision-Making Styles55) The type of decision making in which the solution is considered "good enough" is known as ________.A) intuitionB) satisfyingC) maximizingD) satisficingAnswer: DDiff: 2 Page Ref: 125Topic: Decision-Making Styles56) When a decision maker chooses an alternative under perfect rationality, she________ her decision, whereas under bounded rationality she chooses a ________ decision.A) minimizes; satisficingB) satisfices; maximizingC) maximizes; satisficingD) maximizes; minimizingAnswer: CDiff: 3 Page Ref: 125Topic: Decision-Making Styles57) An increased commitment to a previous decision despite evidence that it may have been wrong is referred to as ________.A) economies of commitmentB) escalation of commitmentC) dimensional commitmentD) expansion of commitmentAnswer: BDiff: 2 Page Ref: 126Topic: Decision-Making Styles58) Intuitive decision making is ________.A) not utilized in organizationsB) a conscious process based on accumulated judgmentC) making decisions based on experience, feelings, and accumulated judgmentD) important in supporting escalation of commitmentAnswer: CDiff: 2 Page Ref: 126Topic: Decision-Making Styles59) In studying intuitive decision making, researchers have found that ________.A) managers do not make decisions based on feelings or emotionsB) managers use data from their subconscious mind to help make their decisionsC) rational thinking always works better than intuitiveD) accumulated experience does not support intuitive decisionsAnswer: BDiff: 2 Page Ref: 126Topic: Decision-Making Styles60) All of the following are aspects of intuition except ________.A) experienced-based decisionsB) affect-initiated decisionsC) cognitive-based decisionsD) programmed decisionsAnswer: DDiff: 1 Page Ref: 127Topic: Decision-Making Styles61) ________ are straightforward, familiar, and easily defined.A) Unstructured problemsB) Structured problemsC) Unique problemsD) Nonprogrammed problemsAnswer: BDiff: 2 Page Ref: 127Topic: Types of Decisions and Decision-Making Conditions62) Structured problems align well with which type of decision making?A) programmedB) satisficingC) intuitionD) gut feelingAnswer: ADiff: 2 Page Ref: 127Topic: Types of Decisions and Decision-Making Conditions63) ________ decision making is relatively simple and tends to rely heavily on previous solutions.A) NonprogrammedB) LinearC) SatisficingD) ProgrammedAnswer: DDiff: 2 Page Ref: 127Topic: Types of Decisions and Decision-Making Conditions64) A procedure ________.A) is an explicit statement detailing exactly how to deal with a decisionB) is a series of interrelated sequential steps to respond to a structured problemC) is a set of guidelines that channel a manager's thinking in dealing with a problemD) allows a manager to use broad decision-making authorityAnswer: BDiff: 2 Page Ref: 127Topic: Types of Decisions and Decision-Making Conditions65) A ________ is an explicit statement that tells a manager what he or she can or cannot do.A) procedureB) policyC) ruleD) solutionAnswer: CDiff: 2 Page Ref: 128Topic: Types of Decisions and Decision-Making Conditions66) A policy ________.A) typically contains an ambiguous termB) is used frequently when a manager faces a structured problemC) allows little discretion on the part of the managerD) offers strict rules as to how a problem should be solvedAnswer: ADiff: 2 Page Ref: 128Topic: Types of Decisions and Decision-Making Conditions67) What is a difference between a policy and a rule?A) A policy establishes parameters.B) A rule establishes parameters.C) A policy is more explicit.D) A rule is more ambiguous.Answer: ADiff: 2 Page Ref: 128Topic: Types of Decisions and Decision-Making Conditions68) A ________ typically contains an ambiguous term that leaves interpretation up to the decision maker.A) systemB) ruleC) solutionD) policyAnswer: DDiff: 2 Page Ref: 128Topic: Types of Decisions and Decision-Making Conditions69) A business school's statement that it "strives for productive relationships with local organizations" is an example of a ________.A) ruleB) policyC) procedureD) commitmentAnswer: BDiff: 2 Page Ref: 128Topic: Types of Decisions and Decision-Making Conditions70) Unstructured problems ________.A) are easily solvedB) present familiar circumstancesC) force managers to deal with incomplete or ambiguous informationD) are routineAnswer: CDiff: 2 Page Ref: 128Topic: Types of Decisions and Decision-Making Conditions71) Nonprogrammed decisions are best described as ________.A) recurring, but difficult to makeB) very similar to problems in other areas of the organizationC) requiring more aggressive action on the decision maker's thought processesD) unique and nonrecurringAnswer: DDiff: 2 Page Ref: 128Topic: Types of Decisions and Decision-Making Conditions72) When problems are ________, managers must rely on ________ in order to develop unique solutions.A) structured; nonprogrammed decision makingB) structured; pure intuitionC) unstructured; nonprogrammed decision makingD) unstructured; programmed decision makingAnswer: CDiff: 2 Page Ref: 128Topic: Types of Decisions and Decision-Making Conditions73) Lower-level managers typically confront what type of decision making?A) uniqueB) nonroutineC) programmedD) nonprogrammedAnswer: CDiff: 2 Page Ref: 128Topic: Types of Decisions and Decision-Making Conditions74) Which of the following is likely to make the most programmed decisions?A) the CEO of PepsiCoB) the vice president of General Motors Cadillac DivisionC) the head of the Minute Maid Division at Coca-ColaD) the manager of the local McDonald'sAnswer: DDiff: 1 Page Ref: 128Topic: Types of Decisions and Decision-Making Conditions75) ________ is a situation in which a manager can make accurate decisions because the outcome of every alternative is known.A) CertaintyB) RiskC) UncertaintyD) MaximaxE) MaximinAnswer: ADiff: 1 Page Ref: 129Topic: Types of Decisions and Decision-Making Conditions76) If an individual knows the price of three similar cars at different dealerships, he or she is operating under what type of decision-making condition?A) riskB) uncertaintyC) certaintyD) factualAnswer: CDiff: 1 Page Ref: 129Topic: Types of Decisions and Decision-Making Conditions77) A retail clothing store manager who estimates how much to order for the current spring season based on last spring's outcomes is operating under what kind of decision-making condition?A) seasonalB) riskC) uncertaintyD) certaintyAnswer: BDiff: 3 Page Ref: 129Topic: Types of Decisions and Decision-Making Conditions78) ________ is a situation in which a decision maker has neither certainty nor reasonable probability estimates available.A) CertaintyB) RiskC) UncertaintyD) MaximaxAnswer: CDiff: 1 Page Ref: 130Topic: Types of Decisions and Decision-Making Conditions79) Nonprogrammed decisions are typically made under a condition of ________.A) certaintyB) low levels of riskC) uncertaintyD) reliabilityAnswer: CDiff: 3 Page Ref: 129Topic: Types of Decisions and Decision-Making Conditions80) A person at a horse racetrack who bets all of his or her money on theodds-based long shot to "win" (rather than "place" or "show") is making what kind of choice?A) maximaxB) maximinC) minimaxD) miniminAnswer: ADiff: 2 Page Ref: 130Topic: Types of Decisions and Decision-Making Conditions81) What best describes the psychological orientation of an individual making a "maximax" choice?A) optimistB) realistC) pessimistD) satisficerAnswer: ADiff: 2 Page Ref: 130Topic: Types of Decisions and Decision-Making Conditions82) Optimistic managers could be expected to utilize their maximax orientation when they ________.A) maximize the maximum payoffB) maximize the minimum payoffC) minimize the maximum regretD) minimize the minimum regretAnswer: ADiff: 1 Page Ref: 130Topic: Types of Decisions and Decision-Making Conditions83) What is the psychological orientation of a decision maker who makes a "maximin" choice?A) optimistB) realistC) pessimistD) satisficerAnswer: CDiff: 2 Page Ref: 130Topic: Types of Decisions and Decision-Making Conditions84) Which of the following best describes "maximizing the minimum possible payoff"?A) maximaxB) maximinC) minimaxD) miniminAnswer: BDiff: 2 Page Ref: 130Topic: Types of Decisions and Decision-Making Conditions85) A manager who desires to minimize his or her maximim "regret" will opt for a ________ choice.A) maximaxB) maximinC) minimaxD) miniminTopic: Types of Decisions and Decision-Making Conditions86) Many managers use ________ or rules of thumb to simplify their decision making.A) heuristicsB) biasesC) errorsD) habitsAnswer: ADiff: 1 Page Ref: 133Topic: Decision-Making Styles87) When decision makers tend to think they know more than they do or hold unrealistically positive views of themselves and their performance, they are exhibiting ________.A) self-serving biasB) the anchoring effectC) immediate gratification biasD) overconfidence biasAnswer: DDiff: 1 Page Ref: 133Topic: Decision-Making Styles88) When decision makers seek out information that reaffirms their past choices and discount information that contradicts past judgments, they are exhibiting________.A) availability biasB) the anchoring effectC) self-serving biasD) confirmation biasAnswer: DDiff: 2 Page Ref: 133Topic: Decision-Making Styles89) When decision makers assess the likelihood of an event based on how closely it resembles other events or sets of events, they are using ________.A) availability biasB) framing biasC) selective perception biasD) representation biasTopic: Decision-Making Styles90) What is the tendency for decision makers to falsely believe that they would have accurately predicted the outcome of an event once that outcome is actually known?A) the hindsight biasB) the sunk costs errorC) the randomness biasD) the selective perception biasAnswer: ADiff: 2 Page Ref: 134Topic: Decision-Making Styles91) To make effective decisions in today's fast-moving world, managers need to ________.A) use the five-stage decision-making processB) know when it is time to call it quitsC) ignore cultural differencesD) identify their style of decision makingAnswer: BDiff: 1 Page Ref: 135Topic: Effective Decision Making in Today's World92) What is a characteristic that the experts say an effective decision-making process has?A) It is inconsistent.B) It acknowledges only objective thinking.C) It focuses on all factors even those that do not seem important.D) It requires only as much information and analysis as is necessary. Answer: DDiff: 2 Page Ref: 136Topic: Effective Decision Making in Today's World93) What term is used by Navy aviators to describe a gut feeling that something isn't right?A) leemersB) the creepsC) uneasinessD) regretAnswer: ADiff: 3 Page Ref: 136Topic: Effective Decision Making in Today's World94) Managers of highly reliable organizations (HROs) get the input of ________ and let them make decisions.A) CEOsB) frontline workersC) customersD) suppliersAnswer: BDiff: 1 Page Ref: 136Topic: Effective Decision Making in Today's World95) When highly reliable organizations (HROs) face complexity, they ________.A) try to simplify dataB) aim for deeper understanding of the situationC) defer to the expertsD) act, then thinkAnswer: BDiff: 2 Page Ref: 136Topic: Effective Decision Making in Today's WorldDecisions, Decisions (Scenario)Sondra needed help. Her insurance company's rapid growth was necessitating making some changes, but what changes? Should they add to the existing information system or should they buy a new system? She was given the responsibility of analyzing the company's present information system and deciding what the company should do that would give them plenty of room. She was confused and needed help in making the correct decision.96) According to the decision-making process, the first step Sondra should take is to ________.A) analyze alternative solutionsB) identify decision criteriaC) evaluate her decision's effectivenessD) identify the problemAnswer: DDiff: 2 Page Ref: 121Topic: The Decision-Making Process97) According to the decision-making process, the second step Sondra should take is to ________.A) analyze alternative solutionsB) identify decision criteriaC) evaluate her decision's effectivenessD) allocate weights to the criteriaAnswer: BDiff: 2 Page Ref: 121Topic: The Decision-Making Process98) Allocating weights to the criteria is the step in the decision-making process that occurs between identifying the decision criteria and ________.A) developing the alternativesB) selecting alternativesC) implementing the alternativeD) identifying the problemAnswer: ADiff: 3 Page Ref: 121Topic: The Decision-Making Process99) When Sondra is conveying her decision to those affected and getting their commitment to it, she is performing which step in the decision-making process?A) analyzing alternative solutionsB) selecting alternativesC) implementing the alternativeD) identifying the problemAnswer: CDiff: 2 Page Ref: 121Topic: The Decision-Making Process100) The very last step Sondra should take, according to the decision-making process, is to ________.A) analyze alternative solutionsB) select alternativesC) implement the alternativeD) evaluate the decision's effectivenessAnswer: DDiff: 1 Page Ref: 121Topic: The Decision-Making Process。