FANUC_调试参数
FANUC数控系统的常用维修调整参数及设置

FANUC数控系统的常⽤维修调整参数及设置第⼆参考点参数发那科数控系统光栅⽣效NO.1815.1=1 FSSB开放相应接⼝。
⼆、进给轴控制相关参数1423 ⼿动速度1424 ⼿动快进1420 G00快速1620 加减速时间1320 软件限位1326三、回零相关参数NO.1620 快进减速时间300msNO.1420 快进速度 10mNO.1425 回零慢速NO.1428 接近挡铁的速度NO.1850 零点偏置四、SP调整参数NO.3701.1=1 屏蔽主轴NO.4020 电机最⼤转速NO.3741 主轴低档转速(最⾼转速)NO.3742 主轴⾼档转速(最⾼转速)NO.4019.7=1 ⾃动设定SP参数(即主轴引导)NO.4133 主电机代码NO.3111.6=1 显⽰主轴速度NO.3111.5=1 显⽰负载监视器NO.4001.4 主轴定位电压极性(定位时主轴转向)NO.3705.1=1 SOR⽤于换档NO.3732=50 换档速度NO.4076=33 定位速度NO.4002.1=1 外接编码器⽣效NO.4077 定位脉冲数(主轴偏置)NO.3117.0=1 显⽰主轴负载表第⼆参考点参数OM系列:735~738;X/Y/Z/4Oi系列:1241采⽤绝对编码器时,先将参数#1815.4改为0,当回零位置发⽣变化以后,第⼆参考点位置也会发⽣变化。
因此第⼆参考点的数值(参数:1241),就要重新设置,⽅法是先将该轴回零,然后⽤⼿脉将该轴摇⾄原先的位置(特别是换⼑点的轴要与机械⼿配合),这时显⽰器上该轴的数字再乘以每脉冲所⾛的距离的倒数,如0.001us/单脉冲,即乘以1000,输⼊到1241⾥去,可能要经过⼏次修调。
才能确定第⼆参考点。
数值输⼊完后,将#1815.4改为 1。
2,存储⾏程软限位参数O系列:700~702,对应 X/ Y/ Z轴设置值:0~9999999当设置 9999999 时,取消正⽅向软限位703;707,对应 4;-4,⼀般为回转轴704~706,对应-X/-Y/-Z轴设量值:0~ -9999999当设置为 -9999999 时。
发那科系统参数调整
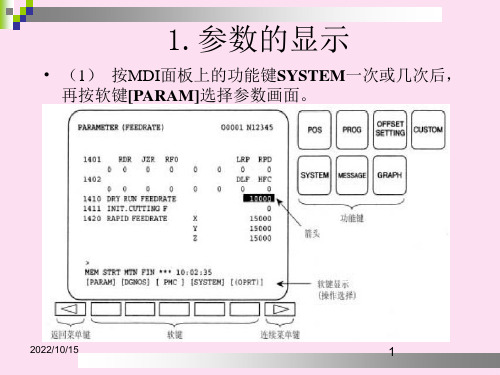
3108#7实际手动速度显示
3111#0伺服调整画面显示
3111#1主轴监控画面显示
3111#5操作监控画面显示
3112#0伺服波型画面显示,需要时1,最后要
为0。
2022/10/15
26
3201,3202,3220,3221,3290程序保护。
会停止。按 RESET键停止参数的输出。
7
通过阅读机/穿孔机 接口输入参数
• (1) 将NC置于急停状态。
• (2) 使参数处于可写状态。
– 1. 按 功能键一次或多次,再按操作选择软件
[SETTING],显示出参数设定画面。
– OFFSET SETTING 2 . 移 动 光 标 , 将 光 标 置 于
20
20
• 5.1400-1600有关速率参数。
如:1401#0=0从接通电源到返回参考点期间,
手动快速运行无效
1402#1=0JOG倍率有效
1410空运行速度
1420各轴快速速度
1422最大切削进给速度
1423各轴JOG速度
1424各轴手动快速移动速度
1425各轴回参考点FL速度
1430各轴最大切削进给速度。
“PARAMETERWRITE” = 1。这样参数成为可写入状态,同时
2022/10/15
3
CNC发生P/S报警100(允许参数写入)。
3
• (3) 按功能键SYSTEM一次或多次后,再按软键
[PARAM],显示参数画面。
• (4) 显示包含需要设定的参数的画面,将光标置于
需要设定的参数的位置上。
行自动初始化。断电再上电后,系统会自动加载部分
电机参数,如果在参数手册上查不到代码,则输入最
FANUC数控系统轴设定参数的调试
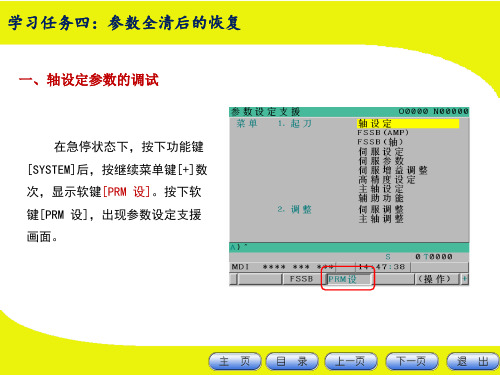
各轴参考点返回操作时的FL速度。
参数 1428
各轴参考点返回速度
参数 1430 各轴最大切削速度。
各轴最大切削速度
学习任务四:参数全清后的恢复
学习任务四:参数全清后的恢复
加减速相关参数
参数
#7
#6
#5
#4
#3
1610
JGLx
#0:CTLx 切削进给或空运行加减速类型 #1:CTBx 切削进给或空运行加减速类型
T1:参数1620设定值 T2:参数1621设定值(T1≧T2)
铃型加减速
学习任务四:参数全清后的恢复
参数 1622 设定值:50-200 参数 1623
各轴切削进给加减速时间常数 各轴切削进给指数加减速的FL速度
除特殊应用外各轴该参数应设定为0,否则加工的直线或圆弧外形不正确
参数 1624 设定值:50-200 参数 1625
U:85 V:86 W:87
各轴轴名称
A:65 B:66 C:67
学习任务四:参数全清后的恢复
学习任务四:参数全清后的恢复
轴属性设定
参数 1022
各轴属性的设定
• 0:既不是基本轴,也不是基本轴的平行轴 • 1:基本轴的X轴 • 2:基本轴的Y轴 • 3:基本轴的Z轴 • 5:X轴的平行轴 • 6:Y轴的平行轴 • 7:Z轴的平行轴
各轴点动进给加减速时间常数 各轴点动进给指数加减速的FL速度
学习任务四:参数全清后的恢复
一、轴设定参数的调试
在急停状态下,按下功能键 [SYSTEM]后,按继续菜单键[+]数 次,显示软键[PRM 设]。按下软 键[PRM 设],出现参数设定支援 画面。
学习任务四:参数全清后的恢复
FANUC系统参数分析和调整解析

FANUC系统参数分析和调整解析FANUC是一个著名的日本工业机器人生产厂商,其生产的机器人系统广泛应用于各个行业的生产线。
FANUC系统参数的分析和调整是机器人操作的关键环节之一,合理的参数设置可以保证机器人的正常运行,提高生产效率和质量。
本文将从系统参数的基本概念、分析和调整方法等方面来进行解析。
首先,需要明确什么是FANUC系统参数。
FANUC系统参数是指机器人控制系统中的一些基础设置,包括速度、加减速度、力矩、位置等参数值,这些参数值会直接影响到机器人的运动性能。
因此,合理地分析和调整这些参数值是非常重要的。
在进行FANUC系统参数分析和调整之前,需要了解机器人的运动学特性和工作环境等相关因素。
运动学特性包括机器人的结构、关节类型、自由度等,而工作环境包括机器人所处的工作空间、工件的形状和重量等。
了解这些因素可以帮助确定适合的参数范围。
对于FANUC系统参数的分析,首先需要根据具体情况选择合适的参数进行测试。
通过调整一些参数值,例如速度,观察机器人在不同速度下的运动情况,可以得出机器人的最佳运行速度范围。
同样地,加减速度、力矩、位置等参数也可以通过类似的方法进行分析。
在进行FANUC系统参数的调整时,需要考虑到机器人的稳定性和安全性。
参数值的调整应该从小范围内逐渐进行,观察机器人在不同参数值下的表现,并根据需求进行适当的调整。
同时,也需要注意机器人的加速度和减速度是否过高,以及机器人在运动过程中的力矩是否过大,以避免机器人发生过载等问题。
除了通过测试和观察来进行参数分析和调整外,还可以使用FANUC提供的软件工具进行辅助。
FANUC提供了一系列的参数配置软件,可以直观地设置和调整各个参数值,并提供参数默认值和范围等参考信息。
总结起来,FANUC系统参数的分析和调整是保证机器人正常运行的重要环节。
合理设置参数值可以提高机器人的运动效率和精度,从而提高生产效率和质量。
参数分析和调整需要根据具体情况和需求进行,通过测试、观察和软件工具的辅助来完成。
FANUC数控系统参数设定
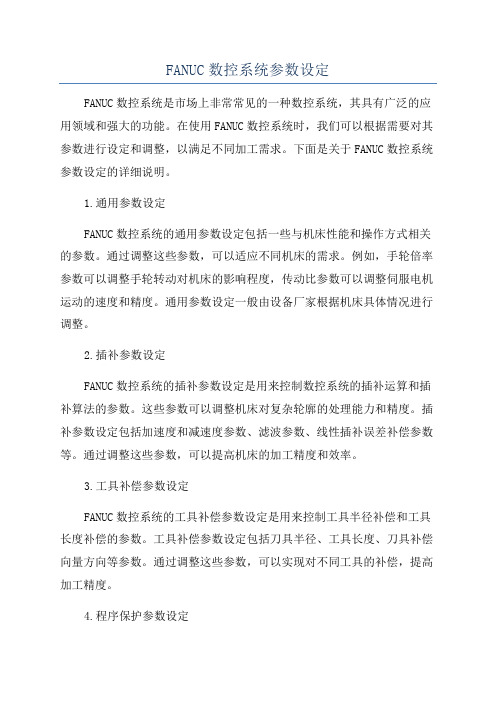
FANUC数控系统参数设定
FANUC数控系统是市场上非常常见的一种数控系统,其具有广泛的应用领域和强大的功能。
在使用FANUC数控系统时,我们可以根据需要对其参数进行设定和调整,以满足不同加工需求。
下面是关于FANUC数控系统参数设定的详细说明。
1.通用参数设定
FANUC数控系统的通用参数设定包括一些与机床性能和操作方式相关的参数。
通过调整这些参数,可以适应不同机床的需求。
例如,手轮倍率参数可以调整手轮转动对机床的影响程度,传动比参数可以调整伺服电机运动的速度和精度。
通用参数设定一般由设备厂家根据机床具体情况进行调整。
2.插补参数设定
FANUC数控系统的插补参数设定是用来控制数控系统的插补运算和插补算法的参数。
这些参数可以调整机床对复杂轮廓的处理能力和精度。
插补参数设定包括加速度和减速度参数、滤波参数、线性插补误差补偿参数等。
通过调整这些参数,可以提高机床的加工精度和效率。
3.工具补偿参数设定
FANUC数控系统的工具补偿参数设定是用来控制工具半径补偿和工具长度补偿的参数。
工具补偿参数设定包括刀具半径、工具长度、刀具补偿向量方向等参数。
通过调整这些参数,可以实现对不同工具的补偿,提高加工精度。
4.程序保护参数设定
5.通讯参数设定
总之,FANUC数控系统的参数设定可以根据实际加工需求进行灵活的
调整和配置,使数控系统更加适应不同的加工任务。
通过合理的参数设定,可以提高机床的加工精度和效率,保证加工质量。
同时,设定好的参数也
可以提高操作的安全性,保护程序的机密性。
FANUC系统参数分析和调整

FANUC系统参数分析和调整FANUC系统参数是指用于调整和配置FANUC控制器操作的一组参数。
这些参数可以影响机床的性能和工作方式。
通过系统参数的分析和调整,可以优化机床的运行和加工效果。
下面将就FANUC系统参数的分析和调整进行详细介绍。
其次,进行FANUC系统参数的分析和调整时,需要有一套科学的方法和步骤。
首先,需要根据实际需要,确定需要分析和调整的系统参数范围。
然后,通过参数手册或操作界面,获取相应的参数数值。
接下来,需要分析当前的参数设置对机床性能和加工效果的影响。
可以通过实际加工试验、工件测量以及观察机床运行情况等方式进行分析。
如果发现参数设置存在问题,可以根据实际需求进行适当的调整。
在调整参数时,需要注意参数范围的合理性和相应的参数之间的关系。
最后,需要对调整后的参数进行测试和验证,确保参数设置的有效性和可靠性。
最后,掌握FANUC系统参数的分析和调整需要进行长期的学习和实践。
FANUC系统参数较为复杂,需要具备一定的机床操作和维护经验。
此外,还需要了解FANUC系统的工作原理和机床运行的相关知识。
可以通过参加培训班、阅读相关文献以及与经验丰富的技术人员交流等方式进行学习。
通过实际操作和实践,逐步提高对FANUC系统参数分析和调整的能力。
总之,FANUC系统参数的分析和调整是机床操作和维护中的重要工作。
正确的参数设置可以优化机床的性能和加工效果,提高生产效率。
通过系统参数的科学分析和合理调整,可以使机床正常运行,并满足实际加工需求。
但是,需要注意参数设置的合理性和相应的参数之间的关系,以及进行长期的学习和实践。
这样,才能真正掌握FANUC系统参数分析和调整的技巧,提高机床操作和维护的水平。
发那科系统参数调整资料

发那科系统参数调整资料一、引言发那科系统参数调整是指对发那科机器人系统的各项参数进行细微调整,以使机器人的运动更加精确、稳定和高效。
良好的系统参数设置可以提高机器人的精度和速度,降低系统故障和能源消耗。
本文将从三个方面介绍发那科系统参数调整的方法和注意事项。
二、系统参数1.传动参数:包括减速比和轴向间隙。
减速比会影响到机械臂的运动速度和扭矩输出,调整时需根据具体需求进行设置。
轴向间隙是指机械臂在轴向移动时的空隙,过大的间隙会使机械臂运动不准确。
2.位置参数:包括机械臂的起始位置和工作空间范围。
机械臂的起始位置应该根据具体工作任务来设置,使机器人在启动时能够快速定位到指定位置。
工作空间范围决定了机械臂可以达到的最大范围,需要根据工作需求和安全考虑进行设置。
3.运动参数:包括速度、加速度和减速度。
这些参数会直接影响机械臂的运动速度和稳定性。
过高的速度和加速度可能导致机械臂震动或失控,过低则会影响工作效率。
调整时需根据具体工作需求和机器人的负载情况进行设置。
三、参数调整方法1.准备工作:在进行参数调整前,必须确保机器人系统已经正常安装和调试完成,并且机械臂没有异常故障。
同时,需要备份系统原始参数,以免出现无法恢复的错误。
2.单一参数调整:在调整参数时,建议逐个参数进行调整,并进行实时观察和测试。
首先将要调整的参数变动到一个较低的值,然后逐渐增加,直到达到最佳效果为止。
3.多参数协同调整:在机器人系统运行过程中,一般需要同时调整多个参数以获得最佳的运动效果。
在进行多参数调整时,建议先调整与位置相关的参数,再调整速度和加速度等参数,最后再微调其他参数。
四、参数调整注意事项1.慎重调整:在进行参数调整时,要小心谨慎,并进行逐步试验,避免一次调整过大而导致机器人运动不稳定或发生故障。
2.多次测试:在调整参数后,需要进行多次测试,以确保调整后的参数能够正常工作。
测试时要观察机器人的运动轨迹、速度和准确度,确保调整效果符合要求。
FANUC系统参数和调整资料
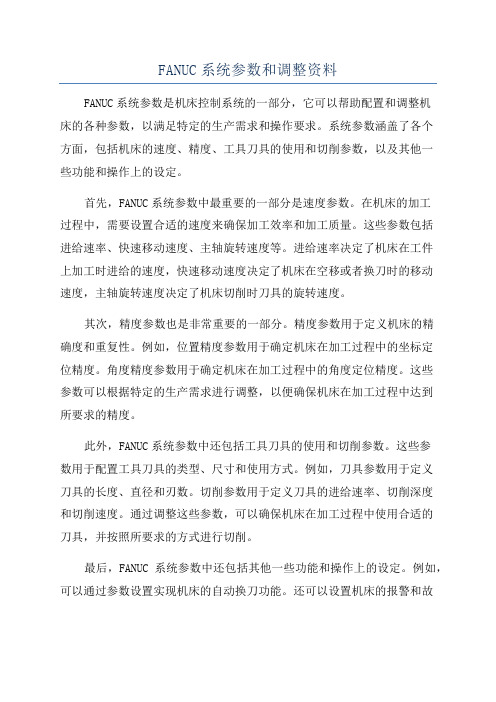
FANUC系统参数和调整资料FANUC系统参数是机床控制系统的一部分,它可以帮助配置和调整机床的各种参数,以满足特定的生产需求和操作要求。
系统参数涵盖了各个方面,包括机床的速度、精度、工具刀具的使用和切削参数,以及其他一些功能和操作上的设定。
首先,FANUC系统参数中最重要的一部分是速度参数。
在机床的加工过程中,需要设置合适的速度来确保加工效率和加工质量。
这些参数包括进给速率、快速移动速度、主轴旋转速度等。
进给速率决定了机床在工件上加工时进给的速度,快速移动速度决定了机床在空移或者换刀时的移动速度,主轴旋转速度决定了机床切削时刀具的旋转速度。
其次,精度参数也是非常重要的一部分。
精度参数用于定义机床的精确度和重复性。
例如,位置精度参数用于确定机床在加工过程中的坐标定位精度。
角度精度参数用于确定机床在加工过程中的角度定位精度。
这些参数可以根据特定的生产需求进行调整,以便确保机床在加工过程中达到所要求的精度。
此外,FANUC系统参数中还包括工具刀具的使用和切削参数。
这些参数用于配置工具刀具的类型、尺寸和使用方式。
例如,刀具参数用于定义刀具的长度、直径和刃数。
切削参数用于定义刀具的进给速率、切削深度和切削速度。
通过调整这些参数,可以确保机床在加工过程中使用合适的刀具,并按照所要求的方式进行切削。
最后,FANUC系统参数中还包括其他一些功能和操作上的设定。
例如,可以通过参数设置实现机床的自动换刀功能。
还可以设置机床的报警和故障监测功能,以及机床的联机通信功能。
这些参数可以根据具体的生产需求进行调整,以满足生产工艺和操作要求。
综上所述,FANUC系统参数是机床控制系统中非常重要的一部分。
它可以帮助配置和调整机床的各种参数,以满足特定的生产需求和操作要求。
通过合理地设置这些参数,可以提高机床的加工效率和加工质量,同时确保机床的稳定性和安全性。
因此,对于机床操作人员和维护人员来说,了解和掌握FANUC系统参数的相关知识非常重要。
FANUC系统参数分析和调整讲解

FANUC系统参数分析和调整讲解首先,我们需要了解FANUC系统参数的种类。
FANUC系统参数主要分为系统参数和用户参数两类。
系统参数是数控系统的基本参数,包括各轴的速度、加减速度、插补误差容限等。
这些参数在机床出厂时已经设置好,一般情况下不需要修改。
而用户参数则是根据具体机床和加工要求进行设置的,包括编程方式、插补方式、快速移动倍率等。
在调整FANUC系统参数之前,我们首先需要进行系统参数分析。
系统参数分析主要包括以下几个方面。
首先是速度参数分析。
速度参数对机床的加工效率和加工质量影响很大。
首先,我们需要分析速度参数是否合理。
速度过快容易引起机床振动,速度过慢会影响加工效率。
其次,我们要分析加减速度参数是否合理,过大或过小的加减速度都会影响机床的稳定性。
其次是插补误差容限分析。
插补误差容限是数控系统对加工路径的容忍度,它决定了机床加工精度的上限。
我们需要根据加工要求和机床精度来分析和调整插补误差容限参数,使其符合要求。
第三是快速移动倍率分析。
快速移动倍率是机床在快速定位时的倍率,它决定了机床快速移动的速度。
过大的快速移动倍率会引起机床冲击,过小会影响加工效率。
另外,我们还需要进行用户参数的分析和调整。
用户参数是根据具体机床和加工要求进行设定的,因此需要根据具体情况进行分析和调整。
例如,编程方式参数。
编程方式参数包括ISO编程方式和自动对称编程方式等。
不同编程方式适用于不同工件的编程,我们需要根据具体工件要求来选择合适的编程方式。
还有插补方式参数。
插补方式参数包括线性插补方式、圆弧插补方式等。
我们需要根据具体工件的加工要求来选择合适的插补方式。
最后是快速移动方式参数。
快速移动方式参数包括梯形快速移动方式、S型快速移动方式等。
不同的快速移动方式对机床的冲击和振动程度不同,我们需要根据机床结构和工件要求来选择合适的快速移动方式。
总之,FANUC系统参数分析和调整是数控机床加工过程中非常重要的一环。
通过合理地分析和调整FANUC系统参数,可以提高机床的加工效率和加工质量,并使其更加稳定可靠。
FANUC调试参数(精)

FANUC机床调试参数系统第一次通电,必须把参数写保护打开(设定画面第一项PWE=1),否则参数无法写入。
在MDI方式下,按软键盘上的SYSTEM,在参数画面下将参数3190#6(CH2)设成1,断电重启,画面上的文字转换成中文。
注:无特殊情况下,第一次通电最好不要进行全清。
一、FSSB设定先把参数8130和10的值设为3,表示3个轴;参数1023设成1;2;3,参数1902#0=0(当参数1902#1 ASE=1时,表示当选择FSSB自动设定方式时,自动设定完成)。
进入SYSTEM,按显示器下的键,画面进入伺服设定,初始化位设为0,将在表5中查得的电机代码输入(0i-Mate系列的Z轴电机代码要比X、Y两轴的代码大1)。
进入伺服调整画面,按照调试手册P15的图中设定X、Y、Z的各项,断电重启。
如果启动后不出现调试手册中P16表1的报警,则FSSB设定完成,否则重新设定FSSB(线路正常情况下)。
如果出现466号报警,将参数2165设为25、25、45(0i-Mate);45、45、45(0i-MC),复位即可消除此报警。
二、主轴设定在参数4133中输入主轴电机代码(表6中查得电机代码),把4019#7设定为1进行自动初始化。
断电重启,设定参数3736为4095,3741号参数为电机的最高转速(即主轴电机的额定转速)。
注:参数4020与3741的值必须一致,否则主轴的转速将与倍率开关的档位不对应三、各种功能对应的参数设定0i-Mate系列按照调试手册中P25-P26的AI先行控制中的参数设定;0i-MC 系列按P26-P27的AI轮廓控制中的参数设定。
其中参数1432为4000~100、1620为150、1621为80。
四、其它参数的设定当以上的参数设好之后,如无出现报警现象,将下面参数输入。
参数如下:参数号功能设定值范围0020I/O通道选择(同设定画面中的设定)0——RS2324——卡138#7=1MDN=1:使用存储卡进行DNC操作有效1002#0JAX=1:手动和回参考点同时控制轴数为3轴1006#5ZMI=1:回零时停在负方向1020各轴的编程名称X——88Y——89Z——901022基本坐标系xx轴的属性X——1Y——2Z——31023各轴的伺服轴号X——1Y——2Z——31241第二参考点的设定1300#2存储式行程检测切换信号EXLM有效LMS=1 1320机床正向软限位1321机床负向软限位1401#4进给率为0时快速移动停止RF0=11410142014211422142314241425162216241800#118211825185120223003#03003#23003#53105#03105#23108#73111#0#1#23117#03190#63202#4321032113605#0空运行速度5000mm/min各轴快速移动速度8000 mm/min各轴快速移动倍率的F0速度500 mm/min最大切削进给速度6000 mm/min各轴手动连续(JOG)进给速度1000 mm/min各轴手动快速移动速度3000 mm/min各轴返回参考点减速后(FL)的速度300 mm/min插补后切削进给时间常数150 ms插补后JOG进给时间常数20 ms位置控制就绪信号PRDY接通之前,速度控制就绪信号VRDY先接通时,不出现伺服报警CVR=1各轴的参考计数器容量8000各轴的伺服位置环增益3000~5000各轴反向间隙补偿量电机旋转方向(根据实际情况调整正负值)X——-111Z——111互锁无效ITL=1各轴互锁无效ITX=1各轴方向互锁无效DIT=1限位开关零点触头接常闭DEC=0限位开关零点触头接常开DEC=1MDI方式显示DPF=1实际主轴速度和T代码显示DPS=1显示手动连续进给速度JSP=1显示伺服设定画面SVS=1显示主轴调整画面SPS=1显示同步误差值是峰值SVP=1在程序检查画面显示打开或关闭主轴速度表和负载表SMS=1显示简体汉字CH2=1程序O9000~99的编辑禁止(刀库用)NE9=1加密解密使用双向螺补功能BDP=13620~3627螺距补偿的设定4077主轴定位5001#5刀具补偿用H代码TPH=1当5001#2OFH=0时有效6071=6当设为0时无效,M00不能调用9001~9009子程序6711加工零件数6712加工零件总数参数6711和6712的设定只有当6700#0为0时有效7113手轮进给倍率1008131#0使用手轮进给HPG=1注:如果软键盘上的键值不对应,将参数3100#2置1,3100#3置0即可如果在手动和回参考点是不能同时控制3轴,将1002#0JAX置1即可栅格量的调整:在诊断画面中,参数302号可以看到各轴的栅格量,最好应在4000~5000之间,栅格量的调整只要调整零点开关的位置当参数4020和3741不一致时,显示出来的主轴转速与主轴倍率选定的不对应攻丝参数设定5200#4(DOV)=1刚性攻丝退刀时倍率有效(倍率值在参数NO.5211中设定)5200#5(PCP)=1刚性攻丝不使用高速深孔攻丝循环5201#0(NIZ)=1进行刚性攻丝的平滑处理5204#0(DGN)=1在诊断画面上显示主轴和攻丝轴的偏差量的偏差值5210=29指令刚性攻丝的M代码5211=200刚性攻丝退刀时的倍率值5241=3000刚性攻丝时主轴的最高转速(第1档)5242=3000刚性攻丝时主轴的最高转速(第2档)5243=3000刚性攻丝时主轴的最高转速(第3档)5261=2000主轴和攻丝轴的直线加减速时间常数(第1档)5262=2000主轴和攻丝轴的直线加减速时间常数(第2档)5263=2000主轴和攻丝轴的直线加减速时间常数(第3档)5280=1000刚性攻丝时主轴和攻丝轴的位置控制回路增益5300=20刚性攻丝时攻丝轴的到位宽度5301=20刚性攻丝时主轴的到位宽度5310=32000刚性攻丝时攻丝轴移动时位置偏差的极限值5311=320005312=8005313=8005314=32000刚性攻丝时主轴移动时位置偏差的极限值刚性攻丝中攻丝轴停止时的位置偏差极限值在刚性攻丝中主轴停止时的位置偏差极限值在刚性攻丝中攻丝轴移动时位置偏差的极限值。
FANUC调试参数(精)

FANUC机床调试参数系统第一次通电,必须把参数写保护打开(设定画面第一项PWE=1),否则参数无法写入。
在MDI方式下,按软键盘上的SYSTEM,在参数画面下将参数3190#6(CH2)设成1,断电重启,画面上的文字转换成中文。
注:无特殊情况下,第一次通电最好不要进行全清。
一、FSSB设定先把参数8130和1010的值设为3,表示3个轴;参数1023设成1;2;3,参数1902#0=0(当参数1902#1 ASE=1时,表示当选择FSSB自动设定方式时,自动设定完成)。
进入SYSTEM,按显示器下的键,画面进入伺服设定,初始化位设为0,将在表5中查得的电机代码输入(0i-Mate系列的Z轴电机代码要比X、Y两轴的代码大1)。
进入伺服调整画面,按照调试手册P15的图中设定X、Y、Z的各项,断电重启。
如果启动后不出现调试手册中P16表1的报警,则FSSB设定完成,否则重新设定FSSB(线路正常情况下)。
如果出现466号报警,将参数2165设为25、25、45(0i-Mate);45、45、45(0i-MC),复位即可消除此报警。
二、主轴设定在参数4133中输入主轴电机代码(表6中查得电机代码),把4019#7设定为1进行自动初始化。
断电重启,设定参数3736为4095,3741号参数为电机的最高转速(即主轴电机的额定转速)。
注:参数4020与3741的值必须一致,否则主轴的转速将与倍率开关的档位不对应三、各种功能对应的参数设定0i-Mate系列按照调试手册中P25-P26的AI先行控制中的参数设定;0i-MC 系列按P26-P27的AI轮廓控制中的参数设定。
其中参数1432为4000~10000、1620为150、1621为80。
四、其它参数的设定当以上的参数设好之后,如无出现报警现象,将下面参数输入。
参数如下:参数号功能设定值范围0020 I/O通道选择(同设定画面中的设定)0——RS2324——卡138#7=1 MDN=1:使用存储卡进行DNC操作有效1002#0 JAX=1:手动和回参考点同时控制轴数为3轴1006#5 ZMI=1:回零时停在负方向1020 各轴的编程名称X——88Y——89Z——901022 基本坐标系中各轴的属性X——1Y——2Z——31023 各轴的伺服轴号X——1Y——2Z——31241 第二参考点的设定1300#2 存储式行程检测切换信号EXLM有效LMS=11320 机床正向软限位1321 机床负向软限位1401#4 进给率为0时快速移动停止RF0=11410 空运行速度5000mm/min1420 各轴快速移动速度8000 mm/min1421 各轴快速移动倍率的F0速度500 mm/min1422 最大切削进给速度6000 mm/min1423 各轴手动连续(JOG)进给速度1000 mm/min1424 各轴手动快速移动速度3000 mm/min1425 各轴返回参考点减速后(FL)的速度300 mm/min1622 插补后切削进给时间常数150 ms1624 插补后JOG进给时间常数20 ms1800#1 位置控制就绪信号PRDY接通之前,速度控制就绪信号VRDY先接通时,不出现伺服报警CVR=11821 各轴的参考计数器容量80001825 各轴的伺服位置环增益3000~50001851 各轴反向间隙补偿量2022 电机旋转方向(根据实际情况调整正负值)X——-111Y——111Z——1113003#0 互锁无效ITL=13003#2 各轴互锁无效ITX=13003#3 各轴方向互锁无效DIT=13003#5 限位开关零点触头接常闭DEC=0限位开关零点触头接常开DEC=13105#0 MDI方式显示DPF=13105#2 实际主轴速度和T代码显示DPS=13108#7 显示手动连续进给速度JSP=13111#0 显示伺服设定画面SVS=1 #1 显示主轴调整画面SPS=1#2 显示同步误差值是峰值SVP=13117#0 在程序检查画面显示打开或关闭主轴速度表和负载表SMS=13190#6 显示简体汉字CH2=13202#4 程序O9000~9999的编辑禁止(刀库用)NE9=13210加密3211解密3605#0 使用双向螺补功能BDP=13620~3627 螺距补偿的设定4077 主轴定位5001#5 刀具补偿用H代码TPH=1当5001#2 OFH=0时有效6071=6 当设为0时无效,M00不能调用9001~9009子程序6711加工零件数6712加工零件总数参数6711和6712的设定只有当6700#0 为0时有效7113 手轮进给倍率1008131#0 使用手轮进给HPG=1注:如果软键盘上的键值不对应,将参数3100#2置1,3100#3置0即可如果在手动和回参考点是不能同时控制3轴,将1002#0 JAX置1即可栅格量的调整:在诊断画面中,参数302号可以看到各轴的栅格量,最好应在4000~5000之间,栅格量的调整只要调整零点开关的位置当参数4020和3741不一致时,显示出来的主轴转速与主轴倍率选定的不对应攻丝参数设定5200#4(DOV)=1 刚性攻丝退刀时倍率有效(倍率值在参数NO.5211中设定)5200#5(PCP)=1 刚性攻丝不使用高速深孔攻丝循环5201#0(NIZ)=1 进行刚性攻丝的平滑处理5204#0(DGN)=1 在诊断画面上显示主轴和攻丝轴的偏差量的偏差值5210=29 指令刚性攻丝的M代码5211=200 刚性攻丝退刀时的倍率值5241=3000 刚性攻丝时主轴的最高转速(第1档)5242=3000 刚性攻丝时主轴的最高转速(第2档)5243=3000 刚性攻丝时主轴的最高转速(第3档)5261=2000 主轴和攻丝轴的直线加减速时间常数(第1档)5262=2000 主轴和攻丝轴的直线加减速时间常数(第2档)5263=2000 主轴和攻丝轴的直线加减速时间常数(第3档)5280=1000 刚性攻丝时主轴和攻丝轴的位置控制回路增益5300=20 刚性攻丝时攻丝轴的到位宽度5301=20 刚性攻丝时主轴的到位宽度5310=32000 刚性攻丝时攻丝轴移动时位置偏差的极限值5311=32000 刚性攻丝时主轴移动时位置偏差的极限值5312=800 刚性攻丝中攻丝轴停止时的位置偏差极限值5313=800 在刚性攻丝中主轴停止时的位置偏差极限值5314=32000 在刚性攻丝中攻丝轴移动时位置偏差的极限值。
FANUC调试参数

FANUC机床调试参数系统第一次通电,必须把参数写保护打开(设定画面第一项PWE=1),否则参数无法写入。
在MDI方式下,按软键盘上的SYSTEM,在参数画面下将参数3190#6(CH2)设成1,断电重启,画面上的文字转换成中文。
注:无特殊情况下,第一次通电最好不要进行全清。
一、FSSB设定先把参数8130和1010的值设为3,表示3个轴;参数1023设成1;2;3,参数1902#0=0(当参数1902#1 ASE=1时,表示当选择FSSB自动设定方式时,自动设定完成)。
进入SYSTEM,按显示器下的键,画面进入伺服设定,初始化位设为0,将在表5中查得的电机代码输入(0i-Mate系列的Z轴电机代码要比X、Y两轴的代码大1)。
进入伺服调整画面,按照调试手册P15的图中设定X、Y、Z的各项,断电重启。
如果启动后不出现调试手册中P16表1的报警,则FSSB设定完成,否则重新设定FSSB(线路正常情况下)。
如果出现466号报警,将参数2165设为25、25、45(0i-Mate);45、45、45(0i-MC),复位即可消除此报警。
二、主轴设定在参数4133中输入主轴电机代码(表6中查得电机代码),把4019#7设定为1进行自动初始化。
断电重启,设定参数3736为4095,3741号参数为电机的最高转速(即主轴电机的额定转速)。
注:参数4020与3741的值必须一致,否则主轴的转速将与倍率开关的档位不对应三、各种功能对应的参数设定0i-Mate系列按照调试手册中P25-P26的AI先行控制中的参数设定;0i-MC 系列按P26-P27的AI轮廓控制中的参数设定。
其中参数1432为4000~10000、1620为150、1621为80。
四、其它参数的设定当以上的参数设好之后,如无出现报警现象,将下面参数输入。
参数如下:参数号功能设定值范围0020 I/O通道选择(同设定画面中的设定)0——RS2324——卡138#7=1 MDN=1:使用存储卡进行DNC操作有效1002#0 JAX=1:手动和回参考点同时控制轴数为3轴1006#5 ZMI=1:回零时停在负方向1020 各轴的编程名称X——88Y——89Z——901022 基本坐标系中各轴的属性X——1Y——2Z——31023 各轴的伺服轴号X——1Y——2Z——31241 第二参考点的设定1300#2 存储式行程检测切换信号EXLM有效LMS=11320 机床正向软限位1321 机床负向软限位1401#4 进给率为0时快速移动停止RF0=11410 空运行速度5000mm/min1420 各轴快速移动速度8000 mm/min1421 各轴快速移动倍率的F0速度500 mm/min1422 最大切削进给速度6000 mm/min1423 各轴手动连续(JOG)进给速度1000 mm/min1424 各轴手动快速移动速度3000 mm/min1425 各轴返回参考点减速后(FL)的速度300 mm/min1622 插补后切削进给时间常数150 ms1624 插补后JOG进给时间常数20 ms1800#1 位置控制就绪信号PRDY接通之前,速度控制就绪信号VRDY先接通时,不出现伺服报警CVR=11821 各轴的参考计数器容量80001825 各轴的伺服位置环增益3000~50001851 各轴反向间隙补偿量2022 电机旋转方向(根据实际情况调整正负值)X——-111Y——111Z——1113003#0 互锁无效ITL=13003#2 各轴互锁无效ITX=13003#3 各轴方向互锁无效DIT=13003#5 限位开关零点触头接常闭DEC=0限位开关零点触头接常开DEC=13105#0 MDI方式显示DPF=13105#2 实际主轴速度和T代码显示DPS=13108#7 显示手动连续进给速度JSP=13111#0 显示伺服设定画面SVS=1 #1 显示主轴调整画面SPS=1#2 显示同步误差值是峰值SVP=13117#0 在程序检查画面显示打开或关闭主轴速度表和负载表SMS=13190#6 显示简体汉字CH2=13202#4 程序O9000~9999的编辑禁止(刀库用)NE9=13210加密3211解密3605#0 使用双向螺补功能BDP=13620~3627 螺距补偿的设定4077 主轴定位5001#5 刀具补偿用H代码TPH=1当5001#2 OFH=0时有效6071=6 当设为0时无效,M00不能调用9001~9009子程序6711加工零件数6712加工零件总数参数6711和6712的设定只有当6700#0 为0时有效7113 手轮进给倍率1008131#0 使用手轮进给HPG=1注:如果软键盘上的键值不对应,将参数3100#2置1,3100#3置0即可如果在手动和回参考点是不能同时控制3轴,将1002#0 JAX置1即可栅格量的调整:在诊断画面中,参数302号可以看到各轴的栅格量,最好应在4000~5000之间,栅格量的调整只要调整零点开关的位置当参数4020和3741不一致时,显示出来的主轴转速与主轴倍率选定的不对应攻丝参数设定5200#4(DOV)=1 刚性攻丝退刀时倍率有效(倍率值在参数NO.5211中设定)5200#5(PCP)=1 刚性攻丝不使用高速深孔攻丝循环5201#0(NIZ)=1 进行刚性攻丝的平滑处理5204#0(DGN)=1 在诊断画面上显示主轴和攻丝轴的偏差量的偏差值5210=29 指令刚性攻丝的M代码5211=200 刚性攻丝退刀时的倍率值5241=3000 刚性攻丝时主轴的最高转速(第1档)5242=3000 刚性攻丝时主轴的最高转速(第2档)5243=3000 刚性攻丝时主轴的最高转速(第3档)5261=2000 主轴和攻丝轴的直线加减速时间常数(第1档)5262=2000 主轴和攻丝轴的直线加减速时间常数(第2档)5263=2000 主轴和攻丝轴的直线加减速时间常数(第3档)5280=1000 刚性攻丝时主轴和攻丝轴的位置控制回路增益5300=20 刚性攻丝时攻丝轴的到位宽度5301=20 刚性攻丝时主轴的到位宽度5310=32000 刚性攻丝时攻丝轴移动时位置偏差的极限值5311=32000 刚性攻丝时主轴移动时位置偏差的极限值5312=800 刚性攻丝中攻丝轴停止时的位置偏差极限值5313=800 在刚性攻丝中主轴停止时的位置偏差极限值5314=32000 在刚性攻丝中攻丝轴移动时位置偏差的极限值。
FANUC调试

FANUC系统调试1、系统全清后2、3281---系统语言,设置15为简体中文3、3004#5(OTH)--不检测超程信号、(G114.0-----G116.0)4、20-----4(使用CF卡)当伺服放大器CX30(ESP)信号断开,产生SV401---伺服器就绪信号关闭--报警5、SV1026报警(轴的分配非法)———参数1023是否正确6、SV417(伺服非法)(no、352译断号)7、*SV401--伺服一V就绪信号关闭8、*SV466电机放大器组合不对。
---放大器的最大电流值和电机的最大电流值不同(1)轴和放大器的连接不正确(2)参数no、2165的设定值不正确9、1001#1(INM):直线轴的最小移动单位(0:公制单位,1:英制单位)10、*no.号参数设置过大电机产生振荡11、伺服参数(速度)页面“速度增益(%)”参数设置过大电机将产生振荡12、No.2021速度环增益。
No.2185设置错误,摇动手轮时出现“SV0410停止时误差太大”报警。
No.1821参考计数器容量分子。
No.2179参考计数器容量分母。
13、No.1815#1(COPT)设置错误出现“SV417+轴”报警。
No.2009#0(DMY)是否使用串行反馈虚设功能,0:不使用,1:使用。
设置错误出现“SV401”报警。
14、No.1820=2(X,Z)(CMR指令乘比)15、伺服参数设立(2000---2999号为伺服专用参数)2084/2085 柔性齿轮比(分子/分母) 2022电机旋转方向No.2021速度环增益 2021负载惯量比(设置过大,电机振荡)2185位置变换脉冲系数 1821参考计数容量2023速度脉冲系数 2165放大器最大电流8130控制轴数(车床为2,铣床为3)《4476#0(OFS):0--OiD专用干SSB设定,1--与Oi-C兼容设定》1240第一参考点在机械坐标系中的位置。
(返回参考点后绝对坐标位置显示页面显示的坐标值)1002#0(JAX)JOG进给,手动快速移动以及手动参考点返回的同时控制轴数为0-1轴,1-3轴14476#0(DFS)当 Oi-MATE-MD系统使用以下放大器A0613-6164,A0613-6165(bisvsp)时设定PRM14776#0--0。
FANUC参数调试步骤

参数调试步骤1.基本参数设定1) 上电全清当系统第一次通电时,最好是先做个全清(上电时,同时按MDI面板上RESET+DEL)。
因为系统在出厂前,在FANUC工厂内经过各项性能测试,里面残留有FANUC工作人员做实验留下的参数,部分PMC程序。
为了消除对您的影响,请务必做一下全清。
全清后一般会出现如下报警:100 参数可输入参数写保护打开(设定画面第一项)。
506/507硬超程报警梯形图中没有处理硬限位信号设定3004#5OTH可消除417 伺服设定不正确重新进行设定伺服参数进行伺服参数初始化。
5136 FSSB 电机号码太小 FSSB设定没有完成或根本没有设定(当系统不带电机时,把1023设定为-1,屏蔽伺服电机,可消除5136报警)手动输入功能参数(9900-9999),根据FANUC提供的出厂参数表正确输入。
然后关断系统电源,再开。
检查参数9900, 8130, 1010的设定是否正确(一般车床为2,铣床3/4)。
2)手动输入功能参数(9900~9999)N09920 P 00101011 N09937 P 00000010N09921 P 01000010 N09938 P 00000000N09922 P 00000000 N09939 P 00000000N09923 P 00000000 N09940 P 00000100N09924 P 00000100 N09941 P 00000001N09926 P 00000000 N09943 P 10011000N09927 P 00010000N09928 P 10100000 N09947 P 10000000N09929 P 00000001 N09953 P 10000000N09930 P 00100110 N09965 P 00000100N09931 P 00000100 N09968 P 111111111 N09932 P 10010000 N09972 P 00000010N09933 P 10000000 N09977 P 00010000N09934 P 00000000 N09988 P 00010000N09935 P 00000000 N09990 P 01101000N09936 P 10010000 N09997 P 000000103)伺服FSSB设定和伺服参数初始化参数1020=88;89;90参数1022设定位1;2;3参数1023设定位1; 2;3;等。
FANUC系统数控机床调试参数

FANUC系统数控机床调试参数在FANUC系统数控机床调试参数方面,有以下几个关键的参数需要注意调整和优化。
首先是加工切削参数,如进给速度、主轴转速、切削深度等。
根据工件材料和加工要求,需要根据实际情况调整这些参数,以获得最佳的加工效果。
进给速度和主轴转速的选择是根据切削力的大小和切削削屑的排出要求来确定的。
切削深度是根据工件材料的韧性和刚度、刃磨质量来确定的。
第二个参数是工具补偿参数。
工具的几何参数和偏差会影响到加工的精度和质量。
需要根据实际情况进行工具测量和补偿,确保加工结果符合要求。
在进行工具补偿时,需要考虑工具的磨损情况和工件的尺寸变化,及时进行补偿调整,以保证加工质量。
第三个参数是机床几何误差补偿参数。
机床的传动系统、导轨系统等都会存在一定的误差,这些误差会对加工结果产生影响。
通过测量和调整机床的几何误差补偿参数,可以提高加工精度和质量。
常见的几何误差包括直线度、平行度、垂直度等,需要根据实际情况进行测量和调整。
第四个参数是检测和调整系统精度的参数。
在进行调试时,需要对系统的精度进行检测和调整。
包括坐标系误差、固定循环误差、热补偿精度等。
根据实际情况进行调整和校正,以提高机床的精度和稳定性。
最后是工作参数的调试。
在调试时,需要根据实际工作情况进行合理的工作参数设定。
包括工件装夹方式、刀具刀路、切削冷却液的使用等。
根据实际情况进行调整和优化,以确保加工过程的安全和稳定。
总之,FANUC系统数控机床调试参数需要综合考虑切削参数、工具补偿参数、机床几何误差补偿参数、检测和调整系统精度的参数以及工作参数等多个方面。
通过合理的调试和优化,可以提高机床的性能和加工质量。
FANUC系统数控机床调试参数
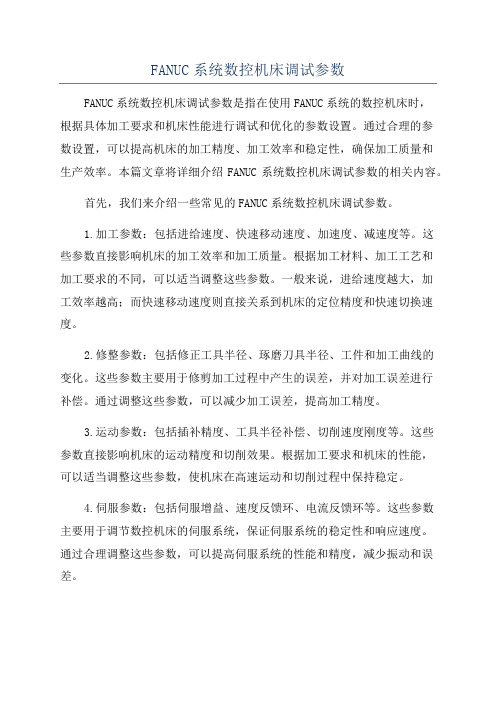
FANUC系统数控机床调试参数FANUC系统数控机床调试参数是指在使用FANUC系统的数控机床时,根据具体加工要求和机床性能进行调试和优化的参数设置。
通过合理的参数设置,可以提高机床的加工精度、加工效率和稳定性,确保加工质量和生产效率。
本篇文章将详细介绍FANUC系统数控机床调试参数的相关内容。
首先,我们来介绍一些常见的FANUC系统数控机床调试参数。
1.加工参数:包括进给速度、快速移动速度、加速度、减速度等。
这些参数直接影响机床的加工效率和加工质量。
根据加工材料、加工工艺和加工要求的不同,可以适当调整这些参数。
一般来说,进给速度越大,加工效率越高;而快速移动速度则直接关系到机床的定位精度和快速切换速度。
2.修整参数:包括修正工具半径、琢磨刀具半径、工件和加工曲线的变化。
这些参数主要用于修剪加工过程中产生的误差,并对加工误差进行补偿。
通过调整这些参数,可以减少加工误差,提高加工精度。
3.运动参数:包括插补精度、工具半径补偿、切削速度刚度等。
这些参数直接影响机床的运动精度和切削效果。
根据加工要求和机床的性能,可以适当调整这些参数,使机床在高速运动和切削过程中保持稳定。
4.伺服参数:包括伺服增益、速度反馈环、电流反馈环等。
这些参数主要用于调节数控机床的伺服系统,保证伺服系统的稳定性和响应速度。
通过合理调整这些参数,可以提高伺服系统的性能和精度,减少振动和误差。
5.轴参数:包括轴偏差补偿、轴运行速度、坐标系转换等。
这些参数主要用于调整数控机床的各个轴的运动精度和坐标系的转换。
通过合理调整这些参数,可以减少机床的位置误差和运动畸变,提高加工精度。
在调试FANUC系统数控机床时,需要根据实际情况进行参数设置和调整。
具体的调试步骤如下:1.根据加工要求和机床性能,确定需要调试的参数和范围。
2.设置机床的调试模式和参数修改权限,确保可以进行参数设置和调整。
3.逐一调试各个参数,根据实际情况进行调整,并记录下参数值和调试结果。
fanuc调试参数

FANUC OI-D系统标准参数设置列表:轴设定参数设置列表参数号参数名称参数中文注解设定值1006#3 X DIA 各轴的移动指令为:0: 半径指定。
1: 直径指定。
11020 XZ AXIS NAME 各轴的名称88901022 XZ AXIS ATTRIBUTE 设定各轴在基本坐标系中排列131023 XZ SERVO AXIS NUM 各轴的伺服轴号 121320 XZ LIMIT + 各轴的存储行程限位的正方向坐标值调试期间不使用软限位时,此参数设置为-1.调试完毕后,此参数设置应距离硬件限位5mm。
1321 XZ LIMIT - 各轴的存储行程限位的负方向坐标值调试期间不使用软限位时,此参数设置为1.调试完毕后,此参数设置应距离硬件限位5mm。
1410 DRY RUN RATE 空运行速度此参数设置为机、电、液协议中轴快速移动速度的一半1420 XZ RAPID FEEDRATE 各轴的快速移动速度此参数设置为机、电、液协议中轴快速移动速度。
1421 XZ RAPID OVR F0 每个轴的快速移动倍率的F0 速度200mm200mm1423 XZ JOG FEEDRA TE 每个轴的JOG 进给速度1000mm1000mm1424 XZ MANUAL RAPID 每个轴的手动快速移动速度此参数设置为机、电、液协议中轴快速移动速度的一半1425 XZ REF RETURN FL 每个轴的手动返回参考点的FL 速度300mm300mm1428 XZ REF FEEDRA TE 每个轴的参考点返回速度3000mm3000mm步骤4:设置参数完毕后,返回至上一级画面,进入[伺服设定]画面,并根据下表设置相应参数 参数名称 中文注解设定值电机代码由于0ID 系统要求使用HRV2功能,所以调试时应根据电机铭牌查询电机代码,并加100为设定值。
如aIF40/3000,电机代码为207,使用HRV2功能时,此参数设置为307.(电机代码表见下面附图)指令倍乘比2柔性齿轮比 N M柔性齿轮比计算方法为:10的6次幂/轴的丝杠螺距X 1000的比值X 机械传动比。
发那科参数调试

步骤一:接线按照设计的机床电柜接线图和系统“连接说明书(硬件)”中(书号:B-61393或B-63503)绘出的接线图仔细接线。
步骤二:通电拔掉CNC系统和伺服(包括主轴)单元的保险,给机床通电。
如无故障,装上保险,给机床和系统通电。
此时,系统会有#401等多种报警。
这是因为系统尚未输入参数,伺服和主轴控制尚未初始化。
步骤三:设定参数1) 系统功能参数(即所谓的保密参数) 这些参数是订货时用户选择的功能,系统出厂时FANUC已经设好。
0C和0i不必设,但是,0D(0TD和0TM)系统须根据实际机床功能设定#932~#935的参数位。
机床出厂时,必须将系统功能参数表交给机床用户。
2) 进给伺服初始化将各进给轴使用的电动机控制参数调入RAM区,并根据丝杠螺距和电动机与丝杠间的变速比配置CMR和DMR。
设参数SVS,使显示器画面显示伺服设定屏(Servo Set)。
0系统设参数#389/0位=0;0i系统设参数#3111/0位=1。
然后在伺服设定屏上设下列各项:a. 初始化位设0 此时,显示器将显示P/S 000报警,其意义是要求系统关机,重新启动。
但不要马上关机,因为其它参数尚未设入。
应返回设定屏继续操作。
b. 指定电动机代码(ID) 根据被设定轴实际使用的电动机型号在“伺服电动机参数说明书(B-65150)”中查出其代码,设在该项内。
c. AMR设0。
d. 设定指令倍比CMR CMR=命令当量/位置检测当量,通常为1。
但该项要求设为其值的3 倍,所以设为2。
e. 设定柔性变速比(N/M) 根据滚珠丝杠螺距和电动机与丝杠间的降速比设定该值。
计算公式为N = 进给轴移动脉冲数/电动机转一转M 1 000 000计算中1个脉冲的当量为1µm。
式中的分子实际就考虑了电动机轴与丝杠间的速比。
将该式约为真分数,其值即为N和M。
该式适用于经常用的伺服半闭环接法,全闭环和使用分离型编码器的半闭环另有算法。
FANUC调试参数

FANUC调试参数FANUC调试参数是指在FANUC机器人系统中,用于优化和调整机器人运行行为的一系列参数。
这些参数涉及到机器人的运动速度、加速度、精度、力控等方面,通过适当的调整可以使机器人实现更好的工作性能和效率。
下面将就FANUC调试参数作详细介绍,这里就不论这个参数在设置时是如何调整的,仅限于对它们的简单介绍。
1.速度参数:用于控制机器人的移动速度,包括关节速度参数和直线速度参数。
关节速度参数主要用于控制关节运动的速度,而直线速度参数用于控制机器人末端执行器的直线运动速度。
2.加速度参数:用于控制机器人的加速度,包括关节加速度参数和直线加速度参数。
关节加速度参数主要用于控制关节运动的加速度,而直线加速度参数用于控制机器人末端执行器的直线运动加速度。
3.精度参数:用于控制机器人的工作精度,包括位置精度参数和重复定位精度参数。
位置精度参数主要用于控制机器人末端执行器的位置控制精度,而重复定位精度参数用于控制机器人进行重复定位任务时的精度。
4.力控参数:用于控制机器人在与物体接触时的力量控制,包括力控增益参数和力控限值参数。
力控增益参数用于调整机器人对外界力量的感知能力,而力控限值参数用于限制机器人对外界力量的响应范围。
5.路径规划参数:用于控制机器人的路径规划行为,包括路径平滑参数和路径跟踪参数。
路径平滑参数用于调整机器人执行轨迹时的平滑程度,而路径跟踪参数用于调整机器人执行轨迹时的精度和稳定性。
6.坐标系参数:用于控制机器人的坐标系转换,包括基座标系参数和工具坐标系参数。
基座标系参数用于定义机器人工作空间的基准坐标系,而工具坐标系参数用于定义机器人末端执行器的位置和方向。
7.强制停止参数:用于控制机器人在异常情况下的停止行为,包括紧急停止参数和限位停止参数。
紧急停止参数用于定义机器人在发生紧急情况时的停止方式,而限位停止参数用于定义机器人在到达关节或坐标限位时的停止方式。
8.传感器参数:用于控制机器人与外界传感器的交互行为,包括传感器接口参数和传感器响应参数。
FANUC_0iMate_MC系统主要全参数调试
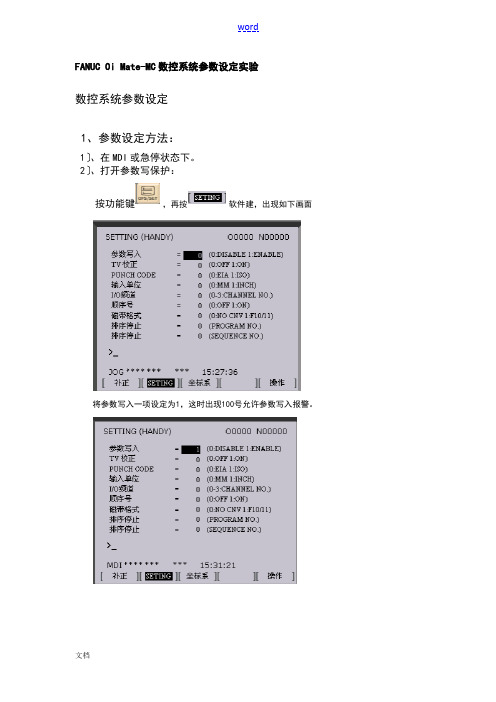
FANUC 0i Mate-MC数控系统参数设定实验
数控系统参数设定
1、参数设定方法:
1〕、在MDI或急停状态下。
2〕、打开参数写保护:
按功能键,再按软件建,出现如下画面将参数写入一项设定为1,这时出现100号允许参数写入报警。
3〕、按系统键。
4〕、按参数软件键。
5〕、找到期望的参数号,用输入参数值。
6〕、参数输入完毕,把参数写保护关闭,方法参照第2步,把参数写入设定为0即可。
重新断电启动。
需要轴设定的参数有如下:
2〕、伺服设定参数
把光标移到伺服设定上
点软件键点扩展软件键
点软件键
点软件键
word
参数设置完毕点设定,重新断电启动就可以了。
文档。