加热反应炉PLC控制系统的设计
基于PLC控制的加热反应炉系统设计

I/O通道分配
PLC的I/O接线图
顺序功能图
工程的建立
(1)双击桌面“MCGS组态环境”图标,进入组态环境,屏幕中间 窗口为工作台。
(2)单击“文件”菜单,弹出下拉菜单,单击“新建工程”。
(3)单击“文件”菜单,弹出下拉菜单,单击“工程另存为”,弹 出文件保存窗口.
(4)选择希望的路径,在文件名一栏内输入工程名,如“加热反应 炉监控系统”,单击“保存”按钮,工程建立完毕。
在MCGS中添加变量
建立画面
(1)单击屏幕左上角的工作台图标,弹出“工作台”窗口。 (2)单击“用户窗口”选项卡,进入“用户窗口”页。 (3)单击右侧“新建窗口”按钮,出现“窗口0”图标. (4)单击“窗口属性”,弹出“用户窗口属性设置”窗口。 (5)在“窗口名称”栏内填入“加热反应炉监控画面”,“窗口位置”选“最大化显示”,其他不变。单击“确
谢谢
基于PLC控制的加热反应炉系统设计
•指 导 老 师 : 罗 麦 丰 •电气1201班 陈言革 周佳明
引言
加热反应炉是冶金、化工工业常用的重要设备,过去仅依靠 人工经验进行操作,往往存在送料、温度、压力等条件变化时不 能实施有效控制的问题,产品质量不稳定甚至出现次品,造成原 料浪费,给企业带来经济损失。可编程序控制器PLC以其可靠性 高、功能强、控制灵活等特点,已成为目前工业现场环境的首选 控制装置。它不仅能实现复杂的逻辑顺序控,还能完成少量模拟量 的过程控制,且编程简单,使用方便。
认”按钮。 (6)观察“工作台”的“用户窗口”,“窗口0”图标已变为“加热反应炉监控画面”。 (7)选中“加热反应炉监控画面”,单击右键,弹出下拉菜单,选中“设置为启动窗口”,如图,则当MCGS运
行时,将自动加载该窗口。 (8)单击“保存”按钮。Fra bibliotek监控画面
PLC设计-加热控制

课程名称:PLC课程设计设计题目:加热反应炉PLC控制系统的设计院系:专业:年级:姓名:指导教师:年月日课程设计任务书专业姓名学号开题日期:年 3 月 23 日完成日期:年 6 月 28 日题目加热反应炉PLC控制系统的设计一、设计的目的加热炉温度控制在许多领域中得到广泛的应用。
这方面的应用大多是基于单片机进行PID控制,然而单片机控制的DDC 系统软硬件设计较为复杂,特别是涉及到逻辑控制方面更不是其长处,然而PLC在这方面却是公认的最佳选择。
采用 PLC来对反应炉进行全自动控制,提高生产效率,并且降低劳动力成本。
二、设计的内容及要求对反应炉的控制主要分为3个阶段。
第一阶段,送料控制,检测下液面、炉内温度和炉内压力是否小于给定值,若是则开启排气阀和进料阀。
当液位上升到上液位设定值时,关闭排气阀和进料阀。
延时20S,开启氮气阀,氮气进入反应炉,炉内压力上升。
当压力上升到给定值时,关闭氮气阀。
第二阶段,加热反应控制,接通反应炉电源,开始对反应炉加温。
当温度上升到给定值时,切断加热电源。
延时10min,加热过程结束。
第三阶段,泄放控制,打开排气阀使炉内压力降到给定值以下,打开泄放阀,当炉内溶液下降到下液面以下,关闭泄放阀和排气阀。
系统恢复到原始状态准备进入下一循环。
三、指导教师评语四、成绩指导教师 (签章)年月日摘要从上世纪80年代至90年代中期,PLC得到了快速的发展,在这时期,PLC在处理模拟量能力、数字运算能力、人机接口能力和网络能力得到大幅度提高,PLC逐渐进入过程控制领域,在某些应用上取代了在过程控制领域处于统治地位的DCS系统。
PLC 具有通用性强、使用方便、适应面广、可靠性高、抗干扰能力强、编程简单等特点。
PLC在工业自动化控制特别是顺序控制中的地位,在可预见的将来,是无法取代的。
温度控制系统广泛应用于工业控制领域,如钢铁厂、化工厂、火电厂等锅炉的温度控制系统,电焊机的温度控制系统等。
加热炉温度控制在许多领域中得到广泛的应用。
基于PLC控制的加热炉温度控制系统设计

基于PLC控制的加热炉温度控制系统设计概述加热炉是工业生产中常见的设备之一,其主要作用是提供高温环境用于加热物体。
为了确保加热炉的稳定性和安全性,需要设计一个可靠的温度控制系统。
本文将介绍一个基于PLC(可编程逻辑控制器)控制的加热炉温度控制系统设计方案。
系统设计原理在加热炉温度控制系统中,PLC作为核心控制器,通过监测温度传感器的输出信号,根据预设的温度设定值和控制策略,控制加热炉的加热功率,从而实现对加热炉温度的稳定控制。
以下是系统设计的主要步骤:1.硬件设备选择:选择适合的温度传感器和控制元件,如热电偶、温度控制继电器等。
2.PLC选型:根据实际需求,选择合适的PLC型号。
PLC需要具备足够的输入输出点数和计算能力。
3.传感器连接:将温度传感器接入PLC的输入端口,读取实时温度数据。
4.温度控制策略设计:根据加热炉的特性和工艺需求,设计合适的温度控制策略。
常见的控制策略包括比例控制、积分控制和微分控制。
5.控制算法实现:根据温度控制策略,编写PLC程序,在每个采样周期内计算控制算法的输出值。
6.加热功率控制:使用控制继电器或可调功率装置,控制加热炉的加热功率。
7.温度反馈控制:通过监测实际加热炉温度和设定值之间的差异,不断修正加热功率控制,使加热炉温度稳定在设定值附近。
系统硬件设计基于PLC控制的加热炉温度控制系统的硬件设计主要包括以下几个方面:1.温度传感器:常用的温度传感器有热电偶和热敏电阻。
根据加热炉的工艺需求和温度范围,选择适合的温度传感器。
2.PLC:选择适合的PLC型号,根据实际需求确定PLC的输入输出点数和计算能力。
3.控制继电器或可调功率装置:用于控制加热炉的加热功率。
根据加热炉的功率需求和控制方式,选择合适的继电器或可调功率装置。
4.运行指示灯和报警器:用于显示系统的运行状态和报警信息。
PLC程序设计PLC程序是基于PLC的加热炉温度控制系统的关键部分,其主要功能是实现温度控制算法。
论文基于PLC的加热水炉实时恒温控制系统的设计

论文基于PLC的加热水炉实时恒温控制系统的设计基于PLC(可编程逻辑控制器)的加热水炉实时恒温控制系统的设计可以按照以下步骤进行:1. 系统硬件设计:- 选择适宜的PLC设备,根据实际需求选择I/O模块和通信模块等。
- 连接传感器和执行器,如温度传感器、电磁阀等,确保能够实时感知水温和控制加热。
2. 确定控温策略:- 确定恒温控制的目标温度范围和波动范围。
- 设置上下温度阈值,当温度超过或低于阈值时触发相应的控制措施。
3. 编写PLC程序:- 根据控温策略编写PLC程序,包括数据采集、控制逻辑和输出控制。
- 采集温度数据,并与设定温度进行比较,判断是否需要调整加热控制。
- 控制加热元件,如电磁阀或电热丝,通过开关控制加热或停止加热。
4. 实现实时控制:- PLC具有实时性能,可以按照设定的周期执行控制循环。
- 在每个控制周期内,读取温度传感器数据,与设定温度进行比较,并控制加热元件的工作状态。
5. 实现安全保护功能:- 添加安全保护功能,如超温保护和过热保护。
当温度超过安全阈值时,立即停止加热,并触发报警。
6. 可视化界面:- 开发人机界面(HMI)以便于操作和监控系统状态。
- 显示实时温度、设定温度和加热状态等信息,并提供手动控制和设定温度的功能。
7. 调试和测试:- 对系统进行调试和测试,确保控温系统的可靠性和稳定性。
- 在实际运行过程中进行验证,对系统进行进一步调整和优化。
需要注意的是,此处提供的是基本的设计步骤,具体的实施和细节会根据具体的加热水炉的要求和PLC设备的特点有所不同。
在设计过程中,应遵循相关的安全准则和标准,确保系统的可靠性和安全性。
同时,建议寻求专业工程师的指导和支持,并对系统进行全面的测试和验证。
基于PLC电热炉温度控制系统设计

基于PLC电热炉温度控制系统设计随着工业自动化的不断发展,PLC(可编程逻辑控制器)在工业生产中的应用越来越广泛。
其中,电热炉温度控制系统是一个重要的应用领域。
本文将就基于PLC电热炉温度控制系统设计展开深入的研究,以期能为相关领域的工程师和技术人员提供有价值的参考。
首先,我们将介绍PLC电热炉温度控制系统的基本原理和工作流程。
在一个典型的电热炉中,温度是一个重要参数,它直接影响着产品质量和生产效率。
传统上,人工操作是常用的温度控制方法。
然而,这种方法存在许多缺点,如操作不稳定、效率低下等。
而基于PLC技术设计的电热炉温度控制系统能够自动化地实现对温度进行精确、稳定地控制。
接下来我们将详细介绍PLC在电热炉温度控制系统中所起到的作用。
首先是传感器部分,在这个部分中我们会介绍温度传感器的种类和工作原理,并详细解释如何选择合适的传感器以及如何进行正确的安装和校准。
接下来是控制器部分,我们将介绍PLC控制器的基本原理以及其在温度控制中的应用。
此外,我们还将讨论PLC在数据采集和通信方面的作用,以及如何进行数据处理和分析。
然后,我们将详细介绍PLC电热炉温度控制系统设计中所需要考虑的关键因素。
首先是系统稳定性和可靠性。
在电热炉温度控制系统中,稳定性是至关重要的因素。
我们将讨论如何通过合适的控制算法来实现系统稳定,并介绍一些常用的控制算法,如PID(比例-积分-微分)算法等。
此外,我们还将讨论硬件设计方面需要考虑的因素,如电路设计、电源设计等。
接下来是安全性问题。
在一个工业生产环境中,安全问题是非常重要且不可忽视的因素。
我们将讨论一些常见安全问题,并提出相应解决方案。
最后,在本文中我们还将介绍一些实际案例,并对其进行分析和评估。
这些案例将涵盖不同的行业和应用领域,以期能够提供更多的实践经验和参考。
综上所述,本文将从基本原理、PLC技术应用、关键因素考虑以及实际案例分析等方面对基于PLC电热炉温度控制系统设计展开深入研究。
课程设计(论文)-基于PLC的电加热炉温度控制系统设计

课程设计(论文)-基于PLC的电加热炉温度控制系统设计引言电加热炉在很多工业生产过程中都扮演着重要角色,而温度控制是电加热炉设计中一个至关重要的问题。
在传统控制方式中,人工干预方案过程复杂,效率较低,不利于生产效率和产品质量的提高。
本文将介绍基于PLC的电加热炉温度控制系统的设计思路、实现原理和结果。
一、设计思路本设计将采用PID控制算法,该算法具有高效、稳定、精度高等优点。
通过对电加热炉加热、冷却及温度等变量进行采样处理,并将PID控制器中的比例、积分、微分三个参数进行调节,使电加热炉的温度控制在预定温度范围内。
二、实现原理本设计所用的硬件设备主要包括PLC、温度传感器、电源、电加热炉及调节阀等。
其中,PLC负责对相关参数的采集与计算,并通过输出信号控制电加热炉内加热、冷却和温度调节。
具体实现步骤如下:1.系统启动后,PLC获取温度传感器采集到的温度值,并将该值与预定温度进行比较,如果温度低于预定温度,PLC将对电源输出信号,让电加热炉进行加热;否则,PLC关闭电加热炉,让炉内温度保持稳定。
2.为了防止温度超过预定值,PLC同时监控温度,当温度高于预定值时,PLC会输出信号关闭电加热炉并打开冷却阀,降低炉内温度。
3.PLC采用PID算法计算比例、积分、微分三个参数,通过对这三个参数的调节,控制电加热炉的加热和冷却过程。
当温度波动较大时,PID控制器会对加热、冷却速度进行调整,使系统实现温度稳定控制。
三、实验结果在实验中,我们将预定温度设置为400℃,测试结果表明:通过使用本文设计的基于PLC的电加热炉温度控制系统,可以让电加热炉的温度控制在预定温度范围内,而且精度高、控制稳定且效率高。
整个系统具有操作简单,实现成本低等优点,可以满足很多工业生产过程中对温度精确控制的需求。
结论本文通过对基于PLC的电加热炉温度控制系统的设计、实现、测试与分析,证明了该系统具有高效、精度高、稳定性强等多方面的优点。
加热反应炉PLC控制系统设计
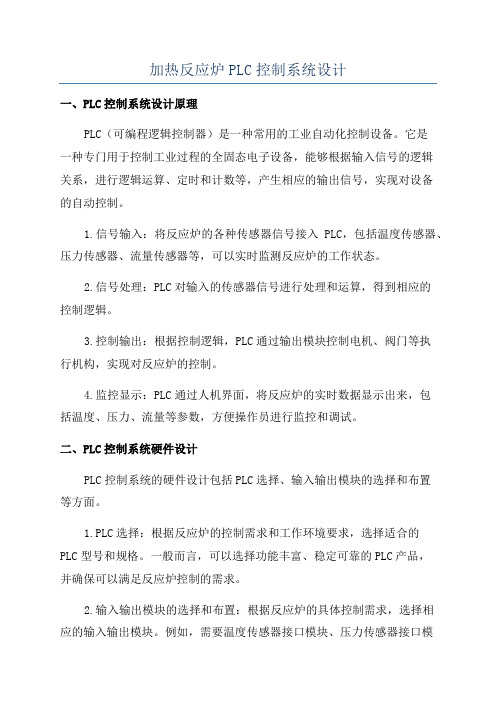
加热反应炉PLC控制系统设计一、PLC控制系统设计原理PLC(可编程逻辑控制器)是一种常用的工业自动化控制设备。
它是一种专门用于控制工业过程的全固态电子设备,能够根据输入信号的逻辑关系,进行逻辑运算、定时和计数等,产生相应的输出信号,实现对设备的自动控制。
1.信号输入:将反应炉的各种传感器信号接入PLC,包括温度传感器、压力传感器、流量传感器等,可以实时监测反应炉的工作状态。
2.信号处理:PLC对输入的传感器信号进行处理和运算,得到相应的控制逻辑。
3.控制输出:根据控制逻辑,PLC通过输出模块控制电机、阀门等执行机构,实现对反应炉的控制。
4.监控显示:PLC通过人机界面,将反应炉的实时数据显示出来,包括温度、压力、流量等参数,方便操作员进行监控和调试。
二、PLC控制系统硬件设计PLC控制系统的硬件设计包括PLC选择、输入输出模块的选择和布置等方面。
1.PLC选择:根据反应炉的控制需求和工作环境要求,选择适合的PLC型号和规格。
一般而言,可以选择功能丰富、稳定可靠的PLC产品,并确保可以满足反应炉控制的需求。
2.输入输出模块的选择和布置:根据反应炉的具体控制需求,选择相应的输入输出模块。
例如,需要温度传感器接口模块、压力传感器接口模块、流量传感器接口模块等。
在布置上,应将各个输入输出模块与相应的传感器和执行机构合理连接,进行布线。
3.电源供应:PLC控制系统的正常运行需要稳定可靠的电源供应。
因此,在硬件设计中,需要考虑到电源的选用和设计,确保PLC系统能够正常供电。
4.信号线路的防护:加热反应炉通常在恶劣的工作环境中,存在较高的温度、湿度和噪声等因素。
为了确保PLC控制系统的稳定性和可靠性,需要对控制信号线路进行合理的防护设计,如使用屏蔽线缆、接地措施等。
三、PLC控制系统软件设计PLC控制系统的软件设计包括PLC编程和人机界面设计。
1.PLC编程:根据反应炉的控制需求,使用相应的编程语言进行PLC程序的编写。
基于PLC控制的加热炉温度控制系统设计

基于PLC控制的加热炉温度控制系统设计加热炉温度控制系统设计的主要目的是确保加热炉内的温度能够稳定地控制在设定温度范围内,以满足生产工艺的要求。
在该系统中,采用了PLC控制器作为主要控制设备,通过控制加热元件的加热功率,实现温度的控制和稳定。
系统硬件设计部分:1.传感器选择:温度传感器是系统中最重要的硬件部分之一、根据实际需求,可选择热电偶、热敏电阻或红外线无接触温度传感器等。
同时,加热炉的材质和工作温度范围也需要考虑在内,以保证传感器的稳定性和耐高温性能。
2.控制器选择:采用PLC控制器作为主要控制设备,有较好的可编程性和灵活性,可根据实际需求进行编程,实现各种温度控制算法。
此外,PLC还可以通过其输入输出接口与其他设备进行通信,实现数据交换和协同控制。
3.加热元件选择:加热炉中常用的加热元件有电热器和电阻丝。
选择合适的加热元件需要考虑炉内的加热效果、功率调节范围、炉内均匀性等因素,以确保能够满足工艺要求。
系统软件设计部分:1.温度控制算法:根据实际需求,可以选择PID控制算法或者模糊控制算法等。
PID控制算法通过对比实际温度值和设定温度值,计算控制器输出,并通过加热元件的控制来调节温度。
模糊控制算法则根据温度误差和误差变化率的模糊逻辑关系,计算控制器输出。
2.界面设计:PLC控制器通常配备了显示屏或者触摸屏界面,可通过界面对系统进行监控和操作。
界面设计需要直观、简明,并能够实时显示和记录温度的变化情况,以便运维人员进行监测和调整。
3.安全保护功能:在系统设计中应考虑温度过高或过低的情况,设置相应的安全保护功能。
例如,当温度超出设定范围时,系统应自动停止加热元件的供电,并产生警告信号,以避免发生安全事故。
总结:基于PLC控制的加热炉温度控制系统设计需要综合考虑硬件和软件两方面因素。
通过合理选择传感器、控制器和加热元件,并设计合适的温度控制算法和安全保护功能,可以实现对加热炉温度的准确控制和稳定性,提高生产工艺的效率和品质。
PLC设计-加热控制

课程名称:PLC课程设计设计题目:加热反应炉PLC控制系统的设计院系:专业:年级:姓名:指导教师:年月日课程设计任务书专业姓名学号开题日期:年 3 月23 日完成日期:年 6 月28 日题目加热反应炉PLC控制系统的设计一、设计的目的加热炉温度控制在许多领域中得到广泛的应用。
这方面的应用大多是基于单片机进行PID控制,然而单片机控制的DDC 系统软硬件设计较为复杂,特别是涉及到逻辑控制方面更不是其长处,然而PLC在这方面却是公认的最佳选择。
采用 PLC来对反应炉进行全自动控制,提高生产效率,并且降低劳动力成本。
二、设计的容及要求对反应炉的控制主要分为3个阶段。
第一阶段,送料控制,检测下液面、炉温度和炉压力是否小于给定值,若是则开启排气阀和进料阀。
当液位上升到上液位设定值时,关闭排气阀和进料阀。
延时20S,开启氮气阀,氮气进入反应炉,炉压力上升。
当压力上升到给定值时,关闭氮气阀。
第二阶段,加热反应控制,接通反应炉电源,开始对反应炉加温。
当温度上升到给定值时,切断加热电源。
延时10min,加热过程结束。
第三阶段,泄放控制,打开排气阀使炉压力降到给定值以下,打开泄放阀,当炉溶液下降到下液面以下,关闭泄放阀和排气阀。
系统恢复到原始状态准备进入下一循环。
三、指导教师评语四、成绩指导教师(签章)年月日摘要从上世纪80年代至90年代中期,PLC得到了快速的发展,在这时期,PLC在处理模拟量能力、数字运算能力、人机接口能力和网络能力得到大幅度提高,PLC逐渐进入过程控制领域,在某些应用上取代了在过程控制领域处于统治地位的DCS系统。
PLC具有通用性强、使用方便、适应面广、可靠性高、抗干扰能力强、编程简单等特点。
PLC在工业自动化控制特别是顺序控制中的地位,在可预见的将来,是无法取代的。
温度控制系统广泛应用于工业控制领域,如钢铁厂、化工厂、火电厂等锅炉的温度控制系统,电焊机的温度控制系统等。
加热炉温度控制在许多领域中得到广泛的应用。
加热反应炉PLC控制系统的设计
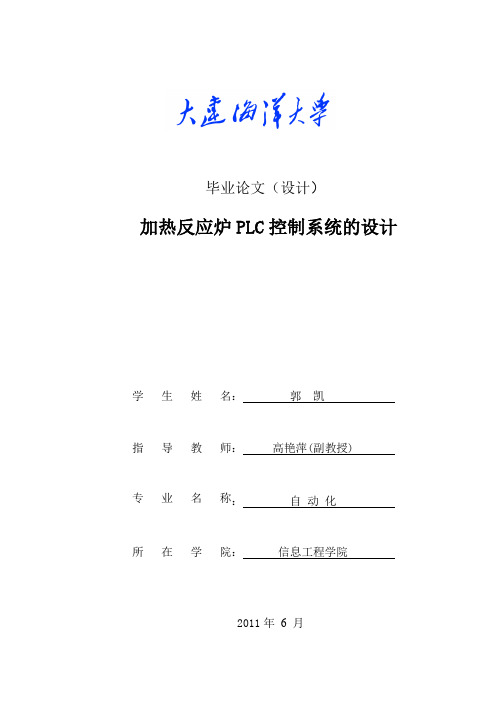
毕业论文(设计)加热反应炉PLC控制系统的设计学生姓名:郭凯指导教师:高艳萍(副教授) 专业名称:自动化所在学院:信息工程学院2011年6 月目录摘要 (I)Abstract .................................................................................I I 第一章引言 . (1)1.1研究的目的和意义 (1)1.2国内外研究现状 (1)1.3研究的内容 (1)第二章控制系统设备简介 (2)2.1 PLC的定义 (2)2.2 PLC的特点 (2)2.3 PLC的通信联网 (3)2.4 PLC的应用领域 (3)2.5 MCGS组态软件简介 (4)2.6 加热反应炉简介 (7)第三章控制画面的创建 (9)3.1工程的建立 (9)3.2变量的定义 (9)3.3控制画面的设计与制作 (10)3.4动画连接 (11)3.5控制程序的编写 (11)3.6 数据显示画面的设计与制作 (12)第四章控制系统的设计 (17)4.1加热反应炉对电气控制系统的要求 (17)4.2系统设计方案 (17)4.3 对象和范围的确定 (19)4.4 电路设计 (20)4.5系统硬件图设计 (20)4.6控制系统的软件设计 (23)第五章系统抗干扰措施 (27)5.1 电磁干扰的类型及其影响 (27)5.2 电磁干扰主要来源 (27)5.3 加热反应炉控制系统的抗干扰措施 (28)第六章结论 (30)致谢 (31)参考文献 (32)摘要加热反应炉是工业生产中的重要设备,为了安全生产避免事故的发生,应用PLC 对它进行实时监控是非常必要的。
本设计实现PLC对加热反应炉的可视化控制,该控制技术可以对真空炉的温度、真空度和水开关状态等参数进行检测,并根据操作前的设定值,进行升温和保温控制,实现加热反应炉内水位变化实时曲线和历史曲线的显示输出,当设备状态异常或各参数越限时立即报警。
PLC设计-加热控制
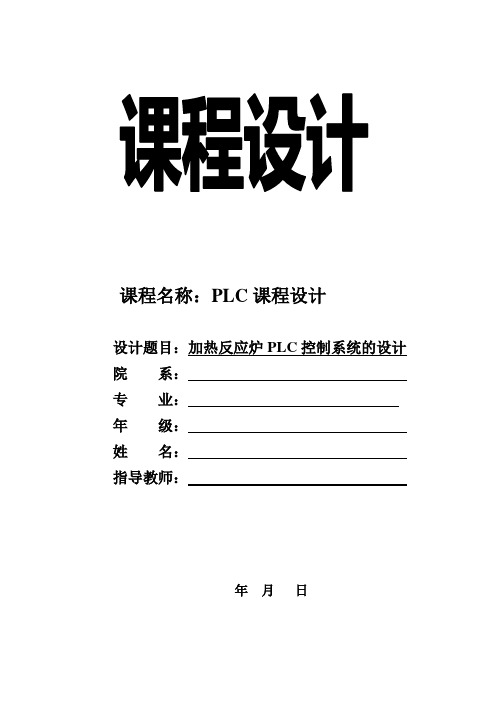
课程名称:PLC课程设计设计题目:加热反应炉PLC控制系统的设计院系:专业:年级:姓名:指导教师:年月日课程设计任务书专业姓名学号开题日期:年 3 月23 日完成日期:年 6 月28 日题目加热反应炉PLC控制系统的设计一、设计的目的加热炉温度控制在许多领域中得到广泛的应用。
这方面的应用大多是基于单片机进行PID控制,然而单片机控制的DDC 系统软硬件设计较为复杂,特别是涉及到逻辑控制方面更不是其长处,然而PLC在这方面却是公认的最佳选择。
采用 PLC来对反应炉进行全自动控制,提高生产效率,并且降低劳动力成本。
二、设计的内容及要求对反应炉的控制主要分为3个阶段。
第一阶段,送料控制,检测下液面、炉内温度和炉内压力是否小于给定值,若是则开启排气阀和进料阀。
当液位上升到上液位设定值时,关闭排气阀和进料阀。
延时20S,开启氮气阀,氮气进入反应炉,炉内压力上升。
当压力上升到给定值时,关闭氮气阀。
第二阶段,加热反应控制,接通反应炉电源,开始对反应炉加温。
当温度上升到给定值时,切断加热电源。
延时10min,加热过程结束。
第三阶段,泄放控制,打开排气阀使炉内压力降到给定值以下,打开泄放阀,当炉内溶液下降到下液面以下,关闭泄放阀和排气阀。
系统恢复到原始状态准备进入下一循环。
三、指导教师评语四、成绩指导教师(签章)年月日摘要从上世纪80年代至90年代中期,PLC得到了快速的发展,在这时期,PLC在处理模拟量能力、数字运算能力、人机接口能力和网络能力得到大幅度提高,PLC逐渐进入过程控制领域,在某些应用上取代了在过程控制领域处于统治地位的DCS系统。
PLC具有通用性强、使用方便、适应面广、可靠性高、抗干扰能力强、编程简单等特点。
PLC在工业自动化控制特别是顺序控制中的地位,在可预见的将来,是无法取代的。
温度控制系统广泛应用于工业控制领域,如钢铁厂、化工厂、火电厂等锅炉的温度控制系统,电焊机的温度控制系统等。
加热炉温度控制在许多领域中得到广泛的应用。
基于PLC的加热反应炉自动控制系统设计
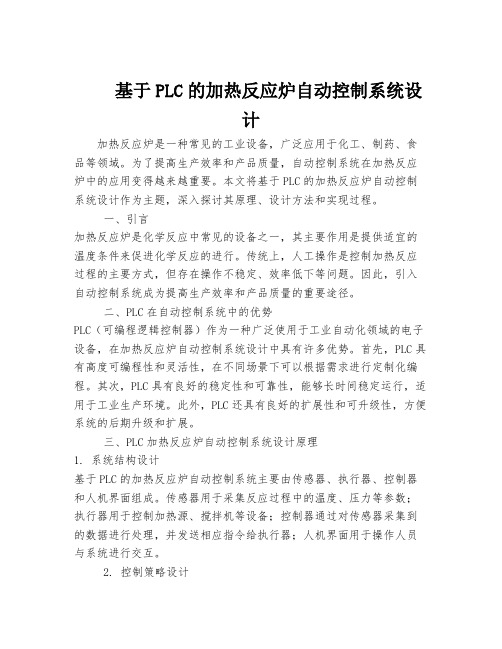
基于PLC的加热反应炉自动控制系统设计加热反应炉是一种常见的工业设备,广泛应用于化工、制药、食品等领域。
为了提高生产效率和产品质量,自动控制系统在加热反应炉中的应用变得越来越重要。
本文将基于PLC的加热反应炉自动控制系统设计作为主题,深入探讨其原理、设计方法和实现过程。
一、引言加热反应炉是化学反应中常见的设备之一,其主要作用是提供适宜的温度条件来促进化学反应的进行。
传统上,人工操作是控制加热反应过程的主要方式,但存在操作不稳定、效率低下等问题。
因此,引入自动控制系统成为提高生产效率和产品质量的重要途径。
二、PLC在自动控制系统中的优势PLC(可编程逻辑控制器)作为一种广泛使用于工业自动化领域的电子设备,在加热反应炉自动控制系统设计中具有许多优势。
首先,PLC具有高度可编程性和灵活性,在不同场景下可以根据需求进行定制化编程。
其次,PLC具有良好的稳定性和可靠性,能够长时间稳定运行,适用于工业生产环境。
此外,PLC还具有良好的扩展性和可升级性,方便系统的后期升级和扩展。
三、PLC加热反应炉自动控制系统设计原理1. 系统结构设计基于PLC的加热反应炉自动控制系统主要由传感器、执行器、控制器和人机界面组成。
传感器用于采集反应过程中的温度、压力等参数;执行器用于控制加热源、搅拌机等设备;控制器通过对传感器采集到的数据进行处理,并发送相应指令给执行器;人机界面用于操作人员与系统进行交互。
2. 控制策略设计在加热反应过程中,温度是一个重要参数。
通过对温度进行实时监测和调节,可以实现对反应过程的精确控制。
常见的温度控制策略有比例-积分-微分(PID)控制和模型预测控制(MPC)。
PID控制是一种经典且简单有效的方法,适用于线性系统;而MPC在非线性系统中具有更好的性能。
3. 程序设计PLC的程序设计是实现加热反应炉自动控制的关键步骤。
程序设计需要根据具体的反应过程和控制策略,将控制逻辑转化为PLC可执行的指令。
加热反应炉的PLC控制(1)
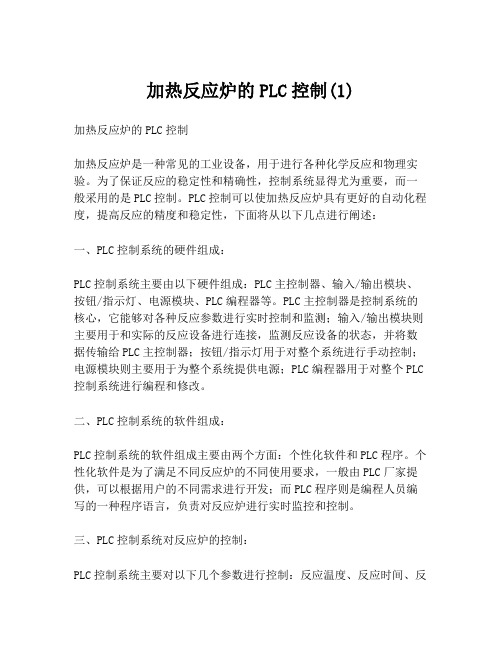
加热反应炉的PLC控制(1)加热反应炉的PLC控制加热反应炉是一种常见的工业设备,用于进行各种化学反应和物理实验。
为了保证反应的稳定性和精确性,控制系统显得尤为重要,而一般采用的是PLC控制。
PLC控制可以使加热反应炉具有更好的自动化程度,提高反应的精度和稳定性,下面将从以下几点进行阐述:一、PLC控制系统的硬件组成:PLC控制系统主要由以下硬件组成:PLC主控制器、输入/输出模块、按钮/指示灯、电源模块、PLC编程器等。
PLC主控制器是控制系统的核心,它能够对各种反应参数进行实时控制和监测;输入/输出模块则主要用于和实际的反应设备进行连接,监测反应设备的状态,并将数据传输给PLC主控制器;按钮/指示灯用于对整个系统进行手动控制;电源模块则主要用于为整个系统提供电源;PLC编程器用于对整个PLC 控制系统进行编程和修改。
二、PLC控制系统的软件组成:PLC控制系统的软件组成主要由两个方面:个性化软件和PLC程序。
个性化软件是为了满足不同反应炉的不同使用要求,一般由PLC厂家提供,可以根据用户的不同需求进行开发;而PLC程序则是编程人员编写的一种程序语言,负责对反应炉进行实时监控和控制。
三、PLC控制系统对反应炉的控制:PLC控制系统主要对以下几个参数进行控制:反应温度、反应时间、反应的加料量、反应的搅拌速度等。
在控制反应温度时,PLC控制系统会通过读取感温器的温度信号,然后根据预设的温度参数去进行温度的调节;在控制反应时间时,PLC会根据时间参数进行监控和控制;在不同的反应阶段根据不同的反应条件,控制反应的加料量、反应的搅拌速度等等。
四、PLC控制系统在故障排查方面的优势:PLC控制系统的优点在于其具有完善的故障检测和排查功能。
一旦设备发生故障时,PLC系统会自动进行检测和诊断,并能在第一时间提醒操作人员进行处理,以避免设备的进一步损坏。
综上所述,PLC控制系统显然是一种适合加热反应炉的控制方式,它可以实现反应炉的智能化、自动化、稳定化,提高工作效率和精度,也可以保证反应设备的安全性和稳定性。
基于PLC的加热反应炉电气控制系统的设计
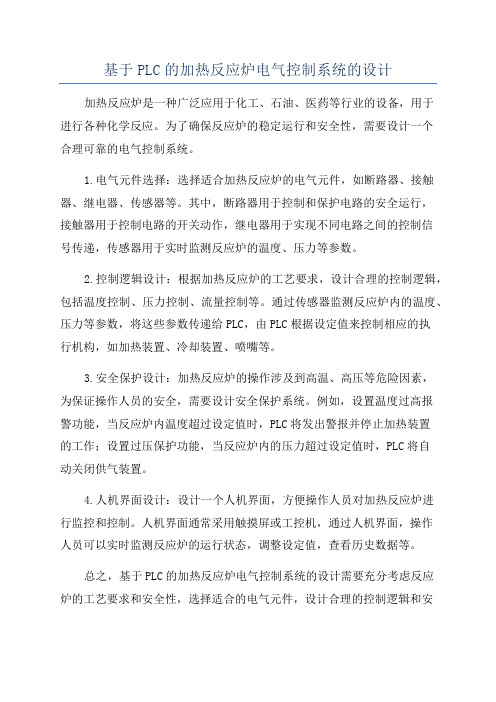
基于PLC的加热反应炉电气控制系统的设计加热反应炉是一种广泛应用于化工、石油、医药等行业的设备,用于进行各种化学反应。
为了确保反应炉的稳定运行和安全性,需要设计一个合理可靠的电气控制系统。
1.电气元件选择:选择适合加热反应炉的电气元件,如断路器、接触器、继电器、传感器等。
其中,断路器用于控制和保护电路的安全运行,接触器用于控制电路的开关动作,继电器用于实现不同电路之间的控制信号传递,传感器用于实时监测反应炉的温度、压力等参数。
2.控制逻辑设计:根据加热反应炉的工艺要求,设计合理的控制逻辑,包括温度控制、压力控制、流量控制等。
通过传感器监测反应炉内的温度、压力等参数,将这些参数传递给PLC,由PLC根据设定值来控制相应的执行机构,如加热装置、冷却装置、喷嘴等。
3.安全保护设计:加热反应炉的操作涉及到高温、高压等危险因素,为保证操作人员的安全,需要设计安全保护系统。
例如,设置温度过高报警功能,当反应炉内温度超过设定值时,PLC将发出警报并停止加热装置的工作;设置过压保护功能,当反应炉内的压力超过设定值时,PLC将自动关闭供气装置。
4.人机界面设计:设计一个人机界面,方便操作人员对加热反应炉进行监控和控制。
人机界面通常采用触摸屏或工控机,通过人机界面,操作人员可以实时监测反应炉的运行状态,调整设定值,查看历史数据等。
总之,基于PLC的加热反应炉电气控制系统的设计需要充分考虑反应炉的工艺要求和安全性,选择适合的电气元件,设计合理的控制逻辑和安全保护功能,并提供简单易用的人机界面。
只有设计合理的电气控制系统,才能保证加热反应炉的稳定运行和安全性。
加热反应炉的PLC控制-V1
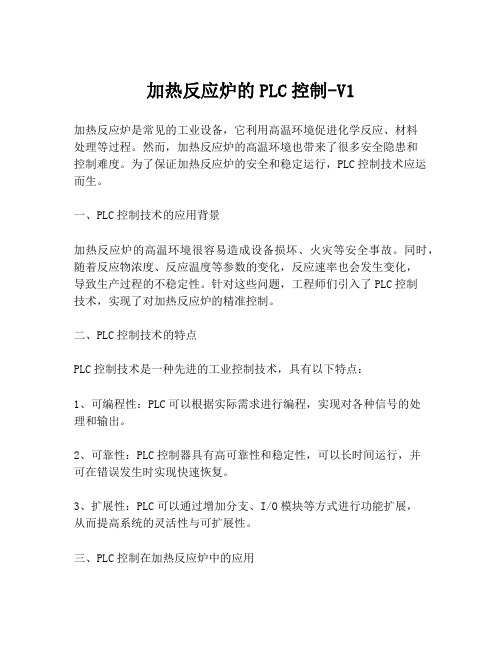
加热反应炉的PLC控制-V1加热反应炉是常见的工业设备,它利用高温环境促进化学反应、材料处理等过程。
然而,加热反应炉的高温环境也带来了很多安全隐患和控制难度。
为了保证加热反应炉的安全和稳定运行,PLC控制技术应运而生。
一、PLC控制技术的应用背景加热反应炉的高温环境很容易造成设备损坏、火灾等安全事故。
同时,随着反应物浓度、反应温度等参数的变化,反应速率也会发生变化,导致生产过程的不稳定性。
针对这些问题,工程师们引入了PLC控制技术,实现了对加热反应炉的精准控制。
二、PLC控制技术的特点PLC控制技术是一种先进的工业控制技术,具有以下特点:1、可编程性:PLC可以根据实际需求进行编程,实现对各种信号的处理和输出。
2、可靠性:PLC控制器具有高可靠性和稳定性,可以长时间运行,并可在错误发生时实现快速恢复。
3、扩展性:PLC可以通过增加分支、I/O模块等方式进行功能扩展,从而提高系统的灵活性与可扩展性。
三、PLC控制在加热反应炉中的应用PLC控制在加热反应炉中的应用有以下几个方面:1、温度控制:PLC可以通过控制温度传感器等设备,实现对加热反应炉内部温度的实时监测和控制。
当温度达到预设范围外时,PLC可以自动调整加热功率,使温度维持在预定范围内。
2、化学反应:PLC可以实现对反应物料质量和浓度的自动监控和控制,精确控制加热反应炉中反应的速率和程度。
3、安全控制:PLC可以对加热反应炉中各种安全保护装置进行监测,当出现问题时,可以实时报警并自动实现停止加热等操作,防止意外事故的发生。
四、PLC控制技术在加热反应炉中的应用实例1、温度控制示例:PLC可以实现对加热反应炉的温度自动调整。
例如,设定将炉内温度保持在1000℃左右,可以在PLC中编写控制逻辑,包括获取温度数据、计算当前偏差值、调整控制参数等,最终实现对加热功率的调整。
2、化学反应控制示例:为了实现对反应速率和程度的精确控制,PLC可以对加热反应炉中的反应物料质量和浓度进行自动监测和控制。
基于西门子PLC和上位机的加热反应炉控制系统设计

本科毕业论文(设计)题 目 基于西门子PLC 和上位机的加热反应炉控制系统设计学生姓名 叶 涛专业名称 电气工程及其自动化指导教师 胡静波2014年 05 月 06 日基于西门子PLC和上位机的加热反应炉控制系统设计摘要:加热反应炉是工业生产中非常常见和重要的设备,广泛应用于生物、制药、食品、冶炼等工业。
为了简化操作流程,提高生产效率,减少人工劳动力,有效提高节能减排能力,避免一些事故发生,本设计采用PLC控制并应用人机界面进行在线监控。
人机界面多PLC实现可视化控制,可以对反应炉的温度、液位、各进出电磁阀、搅拌电机在线监控操作。
并且对生产过程中的温度、液位等过程变量进行在线和历史曲线显示记录与报警。
与此同时,可多各个参数实现在线设置避免停机对生产带来影响。
采用这样的控制方法可以进行安全生产,提高物料利用率、减少人力物力的投入,进而提搞经济效率。
此控制系统以PLC 为核心,通过I/O口采集现场设备信息进行处理,通过专用数据线与上位机通信并进行实时监控。
采用PID算法,运用PLC梯形图编程语言进行编程,实现锅炉温度的自动控制。
通过离线仿真模拟测试,采用西门子PLC与WinCC flexible 的结合控制能够有效方便的对系统进行设计仿真修改。
关键词:加热反应炉;PLC;WinCC flexible;在线监控;人机界面;PIDThe design for the control system of heating-reactor which is based onSiemens PLC and WINCCAbstract:Heating-reactor is the equipment which is very usual and important in industrial manufacture and widely used in biology, pharmacy, food, smelt etc. In order to simplify the operational process, enhance productivity, save manual labor, improve the ability of energy conservation and emission reduction and avoid accident, this project use PLC to control and HMI to monitor online. HMI and PLC could control the reactor visually and monitor the temperature, liquid level, in and out magnetic valves and mixer motor of the reactor online. And it could record and give an alarm in on-line and historic curve display of variables, such as temperature, liquid level in production. In the meantime, from the heating-reactor we can set up the parameters online to avoid the bad influence to the production when the server goes down suddenly. With this control method, we can produce safely, enhance the utilization rate of materials, save manpower and material resources, and then, we can improve economic efficiency. This control system as the core of PLC, deals with the equipment’s information that is taken by I/O port, monitor in real time by the communication of dedicated data line and the host PC. With PID algorithm and programming in PLC ladder language, the automation of the temperature of the reactor becomes achievable. From the offline simulation test, we can find that with the association control of Siemens PLC and WinCC flexible, we can design, revise and simulate the system efficiently and conveniently.Key words:Heating-reactor; PLC; WinCC flexible; On-line monitoring; HMI; PID目录1 引言 (1)1.1 研究目的和意义 (1)1.2国内外研究现状 (1)1.3研究内容 (2)2 控制系统主要设备介绍 (3)2.1 PLC (3)2.1.1基本结构 (3)2.1.2 PLC的特点 (4)2.1.3 PLC选型 (5)2.2 人机界面 (6)2.2.1人机界面概述 (6)2.2.2人机界面分类 (7)2.2.3人机界面的工作原理 (7)2.2.4 TP270 (8)2.3 加热反应炉简介 (8)3 控制系统设计 (10)3.1加热反应炉工艺目的与要求 (10)3.2工艺流程图 (10)3.3 硬件电路图 (11)3.3.1 电气控制系统原理图的设计 (11)3.3.2电气控制元器件的选择 (14)3.3.3 控制柜的设计 (14)3.3.4电气图绘制 (15)4 画面设计 (16)4.1组态软件 (16)4.1.1组态软件的功能 (16)4.2 WinCC flexible概述 (17)4.2.1 WinCC flexible功能与特点 (17)4.2.2 WinCC Flexible系统的结构 (18)4.3 组态画面创建 (20)4.3.1 新建项目 (20)4.3.2 组态项目变量表 (21)4.3.3画面绘制与变量链接 (22)4.3.4 报警与趋势图 (23)5 程序设计 (25)5.1 STEP7-Micro/WIN32西门子编程软件 (25)5.1.1、硬件连接 (25)5.1.2软件的安装 (25)5.2 程序设计 (26)5.2.1程序设计方法 (26)5.2.2 顺序控制设计法 (26)5.2.3 梯形图编写 (27)5.3 PID程序编写 (29)5.3.1 S7-200与PID (29)6 系统仿真 (31)6.1 WinCC flexible仿真软件 (31)6.2 S7-PLCSIM 仿真软件 (31)6.3 WinCC flexible与STEP 7的集成 (31)7 结论 (33)附录一硬件电气图 (34)附录二PLC程序梯形图 (35)参考文献 (40)致谢 (41)1 引言1.1 研究目的和意义加热反应炉是工业生产中常用的重要设备,过去仅依靠人工经验进行操作,往往存在送料、温度等条件变化时不能实施有效控制的问题,产品质量不稳定甚至出现次品,造成原料浪费,给企业带来经济损失。
- 1、下载文档前请自行甄别文档内容的完整性,平台不提供额外的编辑、内容补充、找答案等附加服务。
- 2、"仅部分预览"的文档,不可在线预览部分如存在完整性等问题,可反馈申请退款(可完整预览的文档不适用该条件!)。
- 3、如文档侵犯您的权益,请联系客服反馈,我们会尽快为您处理(人工客服工作时间:9:00-18:30)。
毕业论文(设计)加热反应炉PLC控制系统的设计学生姓名:郭凯指导教师:高艳萍(副教授) 专业名称:自动化所在学院:信息工程学院2011年6 月目录摘要 (I)Abstract ..........................................................................................................I I 第一章引言 (1)1.1研究的目的和意义 (1)1.2国内外研究现状 (1)1.3研究的内容 (1)第二章控制系统设备简介 (2)2.1 PLC的定义 (2)2.2 PLC的特点 (2)2.3 PLC的通信联网 (3)2.4 PLC的应用领域 (3)2.5 MCGS组态软件简介 (4)2.6 加热反应炉简介 (7)第三章控制画面的创建 (9)3.1工程的建立 (9)3.2变量的定义 (9)3.3控制画面的设计与制作 (10)3.4动画连接 (11)3.5控制程序的编写 (11)3.6 数据显示画面的设计与制作 (12)第四章控制系统的设计 (17)4.1加热反应炉对电气控制系统的要求 (17)4.2系统设计方案 (17)4.3 对象和范围的确定 (19)4.4 电路设计 (20)4.5系统硬件图设计 (20)4.6控制系统的软件设计 (23)第五章系统抗干扰措施 (27)5.1 电磁干扰的类型及其影响 (27)5.2 电磁干扰主要来源 (27)5.3 加热反应炉控制系统的抗干扰措施 (28)第六章结论 (30)致谢 (31)参考文献 (32)大连海洋大学本科毕业论文(设计)摘要摘要加热反应炉是工业生产中的重要设备,为了安全生产避免事故的发生,应用PLC 对它进行实时监控是非常必要的。
本设计实现PLC对加热反应炉的可视化控制,该控制技术可以对真空炉的温度、真空度和水开关状态等参数进行检测,并根据操作前的设定值,进行升温和保温控制,实现加热反应炉内水位变化实时曲线和历史曲线的显示输出,当设备状态异常或各参数越限时立即报警。
这不仅能进行安全生产,还可以提高经济效益减少不必要的人力物力的投入。
该控制系统以可编程控制器为核心,通过专用数据线和上位机通信,利用组态软件对整个系统进行实时监控,模拟实验调试结果表明,PLC和MCGS的结合有利于PLC 控制系统的设计、检测,具有良好的应用价值。
关键词:加热反应炉,PLC,MCGS,监控,报警I大连海洋大学本科毕业论文(设计)AbstractAbstractThermal reaction furnaces are important equipment in factory. It is necessary to application of PLC control in real-time in order to prevent safety accidents.The visual control of thermal reaction furnace is realized in this paper by using commom configuration software programmable logic controller.The furnace control technology for temperature, vacuum, water switch status testing.And according to the settings before the operation, to control the heating and insulation.The heating the reactor to achieve real-time water level changes within the historical curve and the curve shows the output.It can also alarm with equipment state abnormal or various parameters on the limit.This not only for safety, but also increase economic efficiency to reduce unnecessary investment in human and material resources.The control system uses programmable logic controller as the core.Programmable logic controller through the dedicated data lines and the host computer ing the configuration software for real-time monitoring of the entire system.The simulation experiment debugging results show that,the combination of PLC and MCGS is conducive to the PLC design, testing, and has a good value.Key words:Thermal reaction furnaces, PLC, MCGS,technology monitor, alarmII大连海洋大学本科毕业论文(设计)第一章引言第一章引言1.1研究的目的和意义加热反应炉是工业生产中常用的重要设备,过去仅依靠人工经验进行操作,往往存在送料、温度、压力等条件变化时不能实施有效控制的问题,产品质量不稳定甚至出现次品,造成原料浪费,给企业带来经济损失。
可编程序控制器PLC以其可靠性高、功能强、控制灵活等特点,已成为目前工业现场环境的首选控制装置。
它不仅能实现复杂的逻辑顺序控制,还能完成少量模拟量的过程控制,且编程简单,使用方便。
使用自动控制系统能有效的提高生产的安全性,大大降低了事故的发生率,并能提高生产效率,使原材料的使用率达到最大。
1.2国内外研究现状国际上对加热炉的优化控制开始于70年代,我国从80年代才开始对这方面进行研究。
我国现有工业锅炉中,很多设备自动化程度不高,热效率在40%左右,随着企业的经济增长模式向依靠技术进步转变,对生产自动化的要求越来越迫切,改变锅炉运行中传统手动、半自动操作方式,实现自动化控制和管理,提高热效率,保障安全运行已经势在必行。
在钢铁领域,以前人们对加热炉优化控制研究主要集中在钢坯的升温过程的数学模型、炉温优化设定以及燃烧控制,近年来智能控制技术正逐步被应用到加热炉炉温控制中。
我国的加热炉相当一部分还处于基地式仪表控制,表盘显示的水平,软件操作不宜为普通工人所掌握。
为改变这种落后状况,有效途径之一就是进行加热炉监测和控制系统的技术改造。
加热炉的工作目标是在最短的时间内采取最经济的方式把颅内的钢坯加热到所要求的状态。
可编程序控制器的发展加速了热处理自动化,并有与其它工序组成自动热处理线的趋势。
1.3研究的内容本课题主要研究通过可编程控制器对加热反应炉工作过程的控制,通过使用MCGS 组态软件,并结合现场的通用I / O 设备(传感器和板卡),对加热反应炉进行进料和排料、进气和排气、加热等自动控制,主要分为三个阶段送料控制,加热反应控制和泄放控制,进行数据实时显示报表输出和历史数据的记录和报表输出,并对反应炉内水位变化进行实时曲线显示输出和历史曲线显示输出。
1大连海洋大学本科毕业论文(设计)第二章控制系统设备简介第二章控制系统设备简介2.1 PLC的定义PLC即可编程控制器(Programmable logic Controller,是指以计算机技术为基础的新型工业控制装置。
在1987年国际电工委员会(International Electrical Committee)颁布的PLC标准草案中对PLC做了如下定义:PLC英文全称Programmable Logic Controller ,中文全称为可编程逻辑控制器,定义是:一种数字运算操作的电子系统,专为在工业环境应用而设计的。
它采用一类可编程的存储器,用于其内部存储程序,执行逻辑运算,顺序控制,定时,计数与算术操作等面向用户的指令,并通过数字或模拟式输入/输出控制各种类型的机械或生产过程.PLC是可编程逻辑电路,也是一种和硬件结合很紧密的语言,在半导体方面有很重要的应用,可以说有半导体的地方就有PLC。
PLC是一种专门为在工业环境下应用而设计的数字运算操作的电子装置。
它采用可以编制程序的存储器,用来在其内部存储执行逻辑运算、顺序运算、计时、计数和算术运算等操作的指令,并能通过数字式或模拟式的输入和输出,控制各种类型的机械或生产过程。
PLC及其有关的外围设备都应该按易于与工业控制系统形成一个整体,易于扩展其功能的原则而设计。
国际电工委员会(IEC)在其标准中将PLC定义为:可编程控制器是一种数位运算操作的电子系统,专为在工业环境应用而设计的。
它采用一类可编程的存储器,用于其内部存储程序,执行逻辑运算、顺序控制、定时、计数与算术操作等,面向用户的指令,并通过数字或模拟式输入/输出控制各种类型的机械或生产过程。
可编程控制器及其有关外部设备,都按易于与工业控制系统联成一个整体,易于扩充其功能的原则设计。
2.2 PLC的特点1.可靠性高,抗干扰能力强高可靠性是电气控制设备的关键性能。
PLC由于采用现代大规模集成电路技术,采用严格的生产工艺制造,内部电路采取了先进的抗干扰技术,具有很高的可靠性。
一些使用冗余CPU 的PLC的平均无故障工作时间则更长。
从PLC的机外电路来说,使用PLC构成控制系统,和同等规模的继电接触器系统相比,电气接线及开关接点已减少到数百甚至数千分之一,故障也就大大降低。
此外,PLC带有硬件故障自我检测功能,出现故障时可及时发出警报信息。
在应用软件中,应用者还可以编入外围器件的故障自诊断程序,使系统中除PLC以外的电路及设备也获得故障自诊断保护。
这样,整个系统具有极高的可靠性也就不奇怪了。
2.配套齐全,功能完善,适用性强PLC发展到今天,已经形成了大、中、小各种规模的系列化产品。
可以用于各种规模的工业控制场合。
除了逻辑处理功能以外,现代PLC大多具有完善的数据运算能力,可用于各种数字控制领域。
近年来PLC的功能单元大量涌现,使PLC渗透到了位置控制、温度控制、CNC2大连海洋大学本科毕业论文(设计)第二章控制系统设备简介等各种工业控制中。