涂装改善措施
涂装质量提升建议措施

涂装质量提升建议措施概述涂装是产品表面的重要保护层,直接关系到产品的质量和美观度。
然而,在涂装过程中常常会出现涂层质量不稳定、涂装附着力差、色差等问题,影响了产品的质量和竞争力。
本文将针对涂装质量提出一些建议措施,旨在提升产品涂装质量。
1. 优化涂装工艺涂装工艺是影响涂装质量的重要因素。
要提升涂装质量,可以从以下几个方面进行优化:1.1 预处理:在涂装前,必须对产品进行充分的预处理。
包括去除表面污垢、氧化层、锈迹等,以及进行适当的打磨和喷砂处理。
只有在表面条件良好的情况下,才能保证涂层附着力和质量的稳定。
1.2 涂料选择:根据不同产品的需求,选择适合的涂料。
包括优良的附着力、耐磨性和耐腐蚀性等特性。
同时,还需要考虑涂料的成本、环保性和使用寿命等方面。
1.3 喷涂工艺控制:通过调整喷涂设备的气压、喷嘴直径、喷涂速度等工艺参数,控制涂层的均匀性和厚度。
还可以采用喷涂机器人等自动化设备,提升涂装的精度和效率。
2. 加强涂装过程控制为了提升涂装质量,还需要加强涂装过程的控制。
具体措施如下:2.1 质量检验:对每批次的涂装产品进行质量检验。
包括涂层附着力、硬度、耐腐蚀性等指标的测定。
及时发现和排除涂装质量问题,确保产品符合质量要求。
2.2 操作规范:建立涂装操作规范,明确工艺流程和操作规程。
包括涂装前的准备工作、涂装过程的操作步骤以及涂装后的处理方式等。
通过规范操作,减少人为因素对涂装质量的影响。
2.3 设备维护:定期检查和维护涂装设备,确保设备正常运行。
包括清洁喷枪、更换涂料罐等。
同时,还要对设备进行定期的涂装效果检验,确保设备的准确性和稳定性。
3. 人员培训和质量意识提升提高涂装质量还需要加强人员培训和质量意识的提升。
3.1 技术培训:对涂装人员进行相关技术培训,包括涂装工艺、涂装设备的使用和维护等方面的培训。
提高人员的专业知识和操作技能,减少操作失误对涂装质量的影响。
3.2 质量意识塑造:通过组织质量意识培训和交流活动,提升涂装人员的质量意识。
常见涂装弊病及防止措施
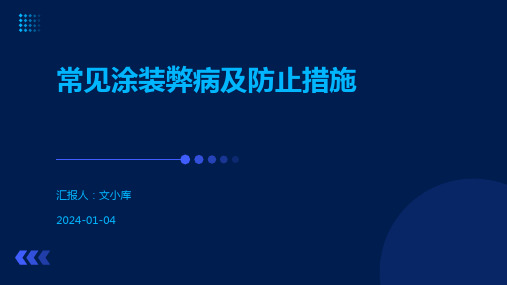
选择合适的涂料
总结词
选择合适的涂料是防止涂装弊病的关键。
详细描述
根据涂装需求和涂装对象的特点,选择符合要求的涂料类型和品牌,确保涂料的质量和性能满足使用 要求。同时,要注意涂料的配套性和相容性,避免因涂料不匹配导致涂层起泡、开裂等问题。
控制涂装环境
总结词
控制涂装环境是保证涂装质量的重要措施。
详细描述
涂装环境应保持清洁、干燥、无尘,温度和湿度要适宜。过高的温度、过低的湿度或灰尘污染都可能导致涂层表 面出现颗粒、不平整等问题。同时,要避免在雨天、雾天或强风中进行涂装作业,以免影响涂层质量。
提高涂装技术水平
总结词
提高涂装技术水平是防止涂装弊病的根 本途径。
VS
详细描述
加强涂装工人的技能培训和技术交流,提 高他们的操作水平和责任心。采用先进的 涂装技术和设备,如静电喷涂、自动涂装 线等,提高涂装的均匀性和平整度。同时 ,要严格执行涂装工艺规程,确保每道工 序的质量控制。
加强涂装后保养
总结词
加强涂装后保养是防止涂装弊病的重要环节 。
详细描述
按照保养要求定期对涂层进行保养和维护, 保持涂层的完整性和美观度。避免硬物刮擦 、高温烘烤和化学腐蚀等损害涂层的行为, 及时修复损坏的涂层,延长涂层的使用寿命 。同时,要注意对保养材料的选用和质量把 控,确保保养效果。
04
涂装弊病的修复方法
THANKS
谢谢您的观看
常见涂装弊病及防止措施
汇报人:文小库 2024-01-04
目录
• 涂装弊病概述 • 常见涂装弊病 • 防止涂装弊病的措施 • 涂装弊病的修复方法
01
涂装弊病概述
涂装弊病的定义
01
涂装弊病是指在涂装过程中出现 的质量问题,如表面缺陷、颜色 不均、起泡、脱落等。
外墙涂料整改措施

外墙涂料整改措施一、背景介绍外墙涂料是建造物外墙装饰和保护的重要材料,对建造物外观和耐久性起着关键作用。
然而,一些外墙涂料存在质量问题,可能导致涂料剥落、变色、开裂等现象,影响建造物的外观和使用寿命。
为了解决这些问题,制定外墙涂料整改措施是至关重要的。
二、问题分析1. 质量问题:外墙涂料可能存在粘结力不足、耐候性差、易剥落等质量问题,需要进行整改。
2. 工艺问题:施工工艺不规范、涂料配比不当等问题也会导致外墙涂料质量不达标,需要进行整改。
3. 管理问题:监督管理不到位、质量检验不严格等问题也是导致外墙涂料质量问题的原因之一,需要加强管理和监督。
三、整改措施1. 质量控制a. 选择优质涂料:在进行外墙涂料施工时,选择质量可靠、符合国家标准的涂料产品,确保涂料质量达标。
b. 强化质量检验:对涂料原材料进行严格检验,确保符合相关标准,同时对涂料施工过程进行抽样检验,及时发现问题并进行整改。
c. 加强质量管理:建立涂料施工质量管理制度,明确责任分工,加强对施工过程的监督和检查,确保施工质量符合要求。
2. 工艺改进a. 施工工艺规范化:制定涂料施工工艺规范,明确涂料施工的步骤和要求,确保施工过程符合标准。
b. 配比优化:根据不同的外墙材料和环境条件,合理调整涂料的配比,确保涂料与墙体的粘结力和耐候性。
c. 施工技术培训:加强对涂料施工人员的培训,提高其技术水平和工艺操作能力,确保施工质量和效果。
3. 管理加强a. 监督检查:加强对涂料施工过程的监督和检查,确保施工符合规范要求,及时发现和纠正问题。
b. 质量追溯:建立涂料施工质量追溯制度,对涂料供应商和施工单位进行备案管理,确保质量可追溯。
c. 宣传教育:加强对涂料施工质量管理的宣传教育,提高涂料施工单位和业主的质量意识,共同推动外墙涂料质量的提升。
四、整改效果评估1. 质量检验:对整改后的外墙涂料进行抽样检验,确保质量达标。
2. 经济效益:整改后的外墙涂料质量提高,减少了维修和更换的频率和费用,节约了维护成本。
涂装过程中出现的技术问题和整改措施

流挂主要产生原因:(1)喷枪距离被喷涂表面过近,或者横向移动速度太慢,或喷涂单次重叠过多,或喷嘴磨损太大,造成局部漆膜过厚;(2)涂料稀释过度,导致涂料黏度太小;(3)被涂表面(或涂料本身)温度过高,影响了涂料的触变性、或被涂表面(或涂料本身)温度过低,影响了涂料中溶剂的蒸发速率,使干燥时间过长;(4)涂料的触变机理不够充分,流平性有问题。
处理方法:把产生流挂的油漆打磨平整,重新修补。
纠正预防:(1)喷枪与被涂物表面保持合适的距离,控制好移动速度,减少单次喷涂重叠次数,及时更换被磨损的喷嘴,控制漆膜厚度;(2)涂料稀释适量,合适的喷漆黏度;(3)保持被涂表面(或涂料本身)合适的温度以及施工条件;(4)联系油漆公司,由其协助解决因涂料触变机理不够充分,导致的流挂。
漏涂主要产生原因:自检不到位,员工缺少责任心。
漏涂处理方法:及时检查,进行补涂。
纠正预防:加强员工质量意识教育,提高过程自检能力。
明显刷痕主要产生原因:(1):刷涂时,涂料黏度过大;(2)刷子毛过硬或者刷子被多次使用,已经磨损;(3)刷涂后,未及时抹平、修整到位;(4)被涂物表面温度或者环境温度过高,溶剂挥发速度太快;(5)涂料流平性能不佳。
刷痕处理方法:刷痕严重的,需要重新打磨平整,重新刷涂。
纠正预防:(1)加入适量的稀释剂,调整刷涂黏度;(2)及时更换刷涂工具;(3)正确操作,刷涂后及时抹平;(4)环境温度高于35 ℃时,禁止在室外涂装;在室内涂装,有条件的,可以开除湿机制冷功能,降低环境温度或者被涂物表面温度,同时加入稀释剂,减少其挥发速度;(5)联系技术服务,根据指导,添加合适的流平剂。
橘皮主要产生原因:(1)环境温度(或者被涂物表面温度)过高,溶剂挥发过快;(2)一次性喷涂漆膜过厚;(3)喷漆工操作不当,喷枪距离构件太远;(4)喷涂压力太低或喷嘴磨损,导致油漆雾化不良;(5)涂料本身流平性不好,在漆膜干燥过程中,涂层内部流动性过早停止。
汽车涂装的缺陷和改进措施
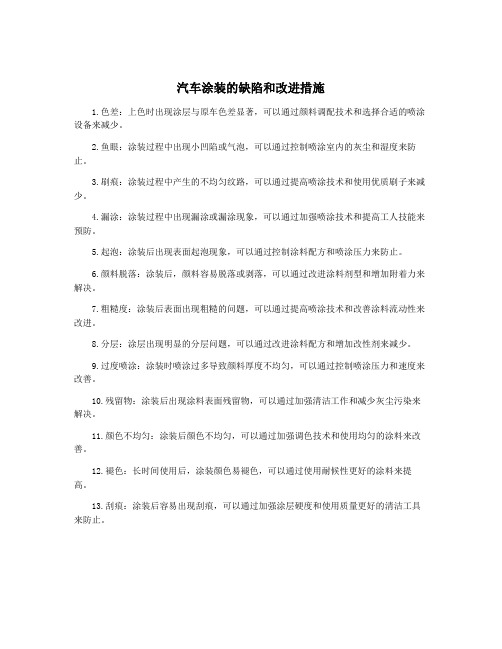
汽车涂装的缺陷和改进措施
1.色差:上色时出现涂层与原车色差显著,可以通过颜料调配技术和选择合适的喷涂设备来减少。
2.鱼眼:涂装过程中出现小凹陷或气泡,可以通过控制喷涂室内的灰尘和湿度来防止。
3.刷痕:涂装过程中产生的不均匀纹路,可以通过提高喷涂技术和使用优质刷子来减少。
4.漏涂:涂装过程中出现漏涂或漏涂现象,可以通过加强喷涂技术和提高工人技能来预防。
5.起泡:涂装后出现表面起泡现象,可以通过控制涂料配方和喷涂压力来防止。
6.颜料脱落:涂装后,颜料容易脱落或剥落,可以通过改进涂料剂型和增加附着力来解决。
7.粗糙度:涂装后表面出现粗糙的问题,可以通过提高喷涂技术和改善涂料流动性来改进。
8.分层:涂层出现明显的分层问题,可以通过改进涂料配方和增加改性剂来减少。
9.过度喷涂:涂装时喷涂过多导致颜料厚度不均匀,可以通过控制喷涂压力和速度来改善。
10.残留物:涂装后出现涂料表面残留物,可以通过加强清洁工作和减少灰尘污染来解决。
11.颜色不均匀:涂装后颜色不均匀,可以通过加强调色技术和使用均匀的涂料来改善。
12.褪色:长时间使用后,涂装颜色易褪色,可以通过使用耐候性更好的涂料来提高。
13.刮痕:涂装后容易出现刮痕,可以通过加强涂层硬度和使用质量更好的清洁工具来防止。
涂装常见问题及解决办法
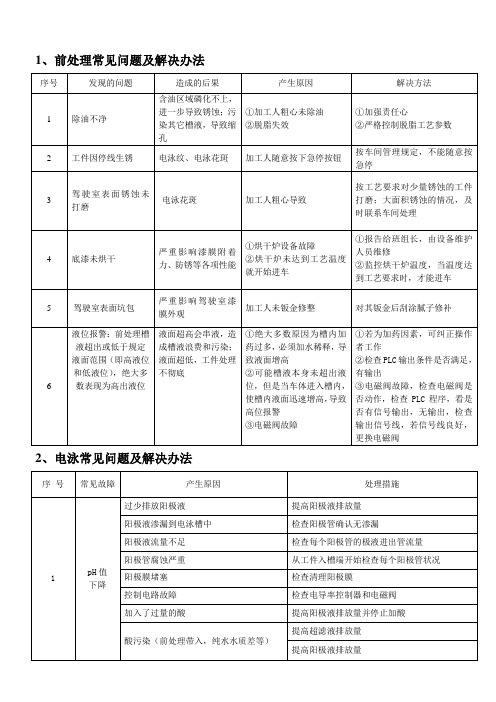
1、前处理常见问题及解决办法序号发现的问题造成的后果产生原因解决方法1 除油不净含油区域磷化不上,进一步导致锈蚀;污染其它槽液,导致缩孔①加工人粗心未除油②脱脂失效①加强责任心②严格控制脱脂工艺参数2 工件因停线生锈电泳纹、电泳花斑加工人随意按下急停按钮按车间管理规定,不能随意按急停3 驾驶室表面锈蚀未打磨电泳花斑加工人粗心导致按工艺要求对少量锈蚀的工件打磨;大面积锈蚀的情况,及时联系车间处理4 底漆未烘干严重影响漆膜附着力、防锈等各项性能①烘干炉设备故障②烘干炉未达到工艺温度就开始进车①报告给班组长,由设备维护人员维修②监控烘干炉温度,当温度达到工艺要求时,才能进车5 驾驶室表面坑包严重影响驾驶室漆膜外观加工人未钣金修整对其钣金后刮涂腻子修补6 液位报警:前处理槽液超出或低于规定液面范围(即高液位和低液位),绝大多数表现为高出液位液面超高会串液,造成槽液浪费和污染;液面超低,工件处理不彻底①绝大多数原因为槽内加药过多,必须加水稀释,导致液面增高②可能槽液本身未超出液位,但是当车体进入槽内,使槽内液面迅速增高,导致高位报警③电磁阀故障①若为加药因素,可纠正操作者工作②检查PLC输出条件是否满足,有输出③电磁阀故障,检查电磁阀是否动作,检查PLC程序,看是否有信号输出,无输出,检查输出信号线,若信号线良好,更换电磁阀2、电泳常见问题及解决办法序号常见故障产生原因处理措施1 pH值下降过少排放阳极液提高阳极液排放量阳极液渗漏到电泳槽中检查阳极管确认无渗漏阳极液流量不足检查每个阳极管的极液进出管流量阳极管腐蚀严重从工件入槽端开始检查每个阳极管状况阳极膜堵塞检查清理阳极膜控制电路故障检查电导率控制器和电磁阀加入了过量的酸提高阳极液排放量并停止加酸酸污染(前处理带入,纯水水质差等)提高超滤液排放量提高阳极液排放量检查纯水电导和工件滴水电导2 pH值上升阳极液排放过量减少阳极液排放,适当提高阳极液的电导率阳极液流失到电泳槽之外检查阳极液系统确认无渗漏控制电路故障检查电导率控制器和电磁阀碱性物质污染(前处理带入,纯水水质差等)提高超滤液排放量检查纯水电导和工件滴水电导原漆补加量大(中和剂加料量相对不足)补加酸,减少阳极液排放量3 电导率下降UF液排放过量,包括UF液的意外损失停止UF液排放,并监测电导率,意外损失故障排除NV值太低补足NV值在规定范围之内4 电导率上升UF系统故障尽快恢复UF系统正常工作,增加UF液排放量槽液中游离酸含量增加降低阳极液电导率,排放UF液NV值太高停止补漆槽温及测试温度偏高加强槽温控制,规范测试方法补加纯水电导率过高确保纯水电导率小于10μs/cm原漆加入量过大(超过槽液的5%)采用少量多次的方法补加原漆前处理带入高电导率的物质控制工件滴水电导小于30μs/cm5 NV值降低原漆补给不足根据耗量,及时补给原漆UF液漂洗系统回流入槽失衡,导致槽液体积增加检查UF液贮槽液位,控制0次喷淋和超滤液回流速度槽液流失检查系统中是否泄漏,包括转移贮槽槽液液位太高降低纯水补给速度6 NV值升高原漆加入量过大相应于消耗量,降低原漆加入量往槽中补给纯水不足补足纯水加入量7 灰分下降颜料浆加量不足补加高颜料份色浆NV值下降增加固体份,监测P/B槽液循环不良,以致颜料产生重力沉降检查设备的循环功能及循环喷射管道是否堵塞8 灰分升高颜料浆加量过大补加低颜料份漆,或补加乳液NV值增加降低固体份:监测P/B9 溶剂量下降高挥发损失检查漆液温度是否在所要求的范围内;添加流平剂来调整溶剂含量UF液渗漏过度检查超滤系统是否渗漏UF液清洗喷淋压力过大,导致挥发损失增加调整喷淋压力槽液NV值下降增加槽液固体份10 溶剂含量上升流平助剂和溶剂加量过大停止加入流平剂和溶剂,并监测各项溶剂含量原漆加入过大降低原漆加入量生产量大,槽液更新快增加超滤排放,并监测溶剂含量11 漆膜薄槽液pH值低调整pH值至要求范围内槽温偏低调整槽温至控制范围的上限槽中有机溶剂含量偏低适当补加有机溶剂槽液NV值偏低提高槽液固体份槽液电导偏低减少UF液的损失施工电压低,泳涂时间不足提高泳涂电压,延长泳涂时间极板与电源连接不良,极板被腐蚀,极夜K值低,极罩隔膜堵塞检查极板、极罩和极夜系统,定期清理和更换工件通电不良清理挂具,使工件通电良好磷化膜太厚控制磷化膜厚度在工艺范围内12 漆膜厚泳涂电压偏高调低泳涂电压槽液温度偏高降温至工艺要求范围之内槽液NV值偏高降低槽液的NV 值溶剂含量偏高排放UF液,补加纯水,延长新槽的熟化时间槽液K值高排放UF液增加纯水被涂物周围循环不好通常因泵、过滤器和换热器堵塞所致改善循环系统13起皱涂膜在烘烤时流平性差或在泳涂时成膜性差增加有机溶剂含量湿膜展平性差,漆温过高使漆温度在工艺要求范围内漆膜偏厚降低施工电压烘烤时升温太快,造成漆膜流平性差而造成严重皱纹调节升温曲线14 漆膜粗糙泳涂电压偏高降低电压至要求范围槽温过高降低槽液温度泳涂速度过快除电压和温度外,pH值、K值也应下降磷化膜不均匀消除磷化不均入槽泳涂工件温度偏高确保涂装工件温度在32℃以下工件表面受磷化渣污染改进磷化除渣系统:增加磷化后喷淋清洗电压波动大控制电压脉动不超过5%,用示波器检查整流器,排除故障入槽工件带入的杂质离子多检查去离子水的pH值,K值清除污染源15 漆膜有颗粒槽液pH值偏高,碱性物质混入槽液中;温度偏高,树脂析出或凝聚控制槽液pH值,严禁有碱性物质混入槽中加强过滤,加速槽液的更新槽内有沉淀死角和裸露金属消除沉淀死角和产生沉淀膜的裸露件电泳槽液和后冲洗液杂质污染,过滤不良加强过滤,推荐试验精度为25微米的过滤元件,减少泡沫入槽被涂物表面不洁,磷化后水洗不良确保被涂物表面清洁,不应有磷化沉渣,防止二次污染在烘干过程中落上杂质粒状污物保持烘道清洁,检查并消除空气尘埃污染源补给涂料或树脂溶解不良,有颗粒确保新补涂料溶解良好,中和分散均匀后,检查应无颗粒16 缩孔槽液中混入油污在槽液循环系统设除油过滤袋,同时清查油污源被涂物前处理脱脂不良或清洗后又落油污加强被涂物的脱脂工序,确保磷化膜不被二次污染泳后清洗液中混入油污提高后清洗水质,加强过滤烘干室内不净,循环风内含油保持烘干室和循环热风的清洁P/B比失调,颜料份偏低调整P/B比,补加颜料浆补给涂料有缩孔或树脂溶解不良,中和不好加强涂料补加管理,确保补给涂料的溶解中和,过滤良好17 针孔槽液中杂质离子含量过高,电解反应剧烈,被涂物表面产生气体过多排放UF液,加纯水,降低杂质离子含量电泳涂装后,被涂物出槽清洗不及时湿涂膜产生返溶被涂物电泳出槽后,应立即用UF液冲洗,时间不超过1分钟为宜磷化膜空隙率高,易含气泡调整磷化结晶致密槽液温度偏低或搅拌不充分湿膜脱泡不良加强槽液搅拌,确保槽液温度在工艺范围之内被涂物入槽端槽液面流速低,有泡沫堆积控制液面流速大于0.2m/s,消除堆积的泡沫18 水滴痕湿膜带水滴,水珠在烘干前未挥发掉吹掉水滴、水珠,升高晾干区的温度,加强排风从挂具和线链上滴落的水珠采取措施防止水滴落在被涂物上进入烘干室后,升温过急避免升温过急或增加预加热纯水洗不足增加纯水洗19 干漆迹泳后冲洗不良加强泳后冲洗管理,检查喷嘴是否堵塞或布置不当加大冲洗水量槽液温度偏高,涂装环境温度低适当降低温度,提高环境温度入槽段液面有泡沫浮游,泡沫吸附在被涂物表面上,被沉积的漆膜包裹加大入槽部位液面流速,消除液面的泡沫20 涂层斑印入槽段电压过高,造成电解反应剧烈降低入槽段电压,在入槽段不设或少设电极被涂物表面干湿不均或有水滴吹掉被涂物面的水滴,确保被涂物全干或全湿状态进入电泳槽磷化膜疏松或太薄调整前处理工艺,确保磷化膜质量符合入槽电泳工艺要求磷化后水洗不充分加强磷化后清洗工艺磷化后水洗水质不良加强水质管理,纯水清洗后滴水电导率不应大于30μs/cm磷化处理过的被涂面再次被污染防止磷化后湿膜的二次污染,保持环境整洁,防止挂具滴水被涂物的结构造成在可能的条件下改结构21 二次流痕泳后清洗工艺选择不当对复杂结构的被涂物应选用浸喷结合式清洗工艺,或用水冲或用压缩空气吹掉夹层中的槽液进入烘干区时,升温过急加强晾干功能,在烘干前预加热由于电泳系统管路中泵、阀门泄漏造成爆气检查系统有关泵、阀门等设备22 槽液气泡主、副槽溢流落差太大造成气泡调整溢流堰高度,减少落差由于循环不足,造成槽液表面流动不畅,以致涂装件入口处带进的气泡不宜消失且越积越多检查循环系统相关设备的工作正常与否,如有必要则需维修。
建筑外墙涂装质量通病防治措施
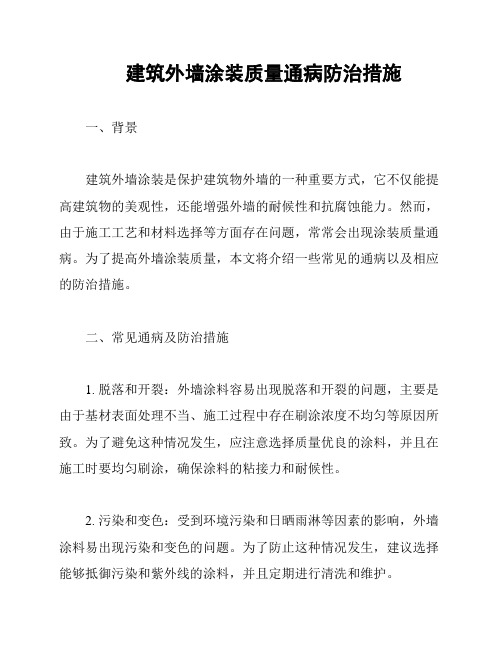
建筑外墙涂装质量通病防治措施
一、背景
建筑外墙涂装是保护建筑物外墙的一种重要方式,它不仅能提高建筑物的美观性,还能增强外墙的耐候性和抗腐蚀能力。
然而,由于施工工艺和材料选择等方面存在问题,常常会出现涂装质量通病。
为了提高外墙涂装质量,本文将介绍一些常见的通病以及相应的防治措施。
二、常见通病及防治措施
1. 脱落和开裂:外墙涂料容易出现脱落和开裂的问题,主要是由于基材表面处理不当、施工过程中存在刷涂浓度不均匀等原因所致。
为了避免这种情况发生,应注意选择质量优良的涂料,并且在施工时要均匀刷涂,确保涂料的粘接力和耐候性。
2. 污染和变色:受到环境污染和日晒雨淋等因素的影响,外墙涂料易出现污染和变色的问题。
为了防止这种情况发生,建议选择能够抵御污染和紫外线的涂料,并且定期进行清洗和维护。
3. 水泡和鼓泡:涂料涂刷后,表面容易出现水泡和鼓泡现象,这主要是由于施工时存在湿度过高或者涂料干燥时间不足等原因所致。
为了防止水泡和鼓泡的问题,应在施工前仔细检查湿度和涂料使用要求,并确保施工环境适宜。
4. 裂纹和起皮:外墙涂料可能会出现裂纹和起皮的问题,这主要是由于基材强度不足、涂料与基材之间的相容性差等原因所致。
为了避免这种情况发生,建议选择与建筑物基材相适应的涂料,并进行充分的基材处理。
三、总结
建筑外墙涂装质量的提高对于建筑物的保护和美观至关重要。
通过选择优质的涂料,注意施工过程中的细节,并定期进行清洗和维护,可以有效预防和解决外墙涂装质量通病的问题。
建筑行业相关从业人员应加强对涂装质量防治措施的了解和实践,提升施工质量和客户满意度。
涂装质量控制

涂装质量控制摘要:涂装质量对于产品的外观和保护至关重要。
本文将探讨涂装质量控制的必要性、涂装质量控制的方法以及如何改善涂装质量。
引言:涂装质量直接影响产品的外观、耐久性和质量。
不良的涂装质量可能导致产品在运输或使用过程中出现脱落、剥落或变色,从而影响整体产品的质量和评价。
因此,为了确保产品的外观完美和实现高质量涂装,涂装质量控制至关重要。
一、涂装质量控制的必要性涂装质量控制的主要目的是确保涂装的均匀性、附着力和耐久性。
这对于产品的美观度和性能至关重要。
涂装过程中可能发生的问题包括涂层不均匀、气泡、流挂、翘曲、沙粒和脱层等。
这些问题可能导致涂装产品不符合质量要求,影响产品的市场表现和客户满意度。
因此,通过涂装质量控制,可以及时发现并解决这些问题,提高涂装产品的质量和性能。
二、涂装质量控制的方法1. 原材料质量控制:涂装质量控制的第一步是确保原材料的质量。
涂料、清洗剂和底漆等原材料的质量对涂装产品的质量起着至关重要的作用。
因此,应对原材料进行严格的质量控制,确保其符合产品要求。
2. 涂装过程的控制:涂装过程包括表面准备、底漆涂装和面漆涂装等环节。
在每个环节中,都需要采取相应的控制措施来确保涂装质量的一致性和稳定性。
针对不同的涂装过程,可以采取以下控制措施:- 表面准备过程中,可以使用化学清洗、机械处理或砂光等方法,以确保表面平整和清洁。
- 底漆涂装时,可以使用适当的喷涂设备和涂料标准来确保涂层的均匀性和附着力。
- 面漆涂装时,可以控制喷涂厚度、喷涂速度和喷涂距离等参数,以确保涂层的均匀性和光滑度。
3. 检验和测试:涂装质量控制的一个重要环节是检验和测试。
通过对涂装产品进行检验和测试,可以及时发现涂装质量问题,并采取相应的措施进行改进。
常用的检验和测试方法包括目视检查、涂层厚度测量、附着力测试和耐久性测试等。
三、如何改善涂装质量1. 培训和教育:为涂装操作人员提供适当的培训和教育,使其掌握涂装技术和质量控制知识。
汽车涂装工艺中常见的技术问题及解决方法
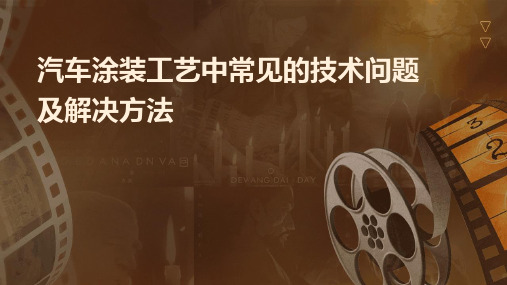
涂层附着力问题解决方法
涂层附着力不足
加强涂装前的表面处理,确保表面无杂质、油污等;控制涂 料的施工粘度和涂层厚度,避免过厚的涂层导致附着力下降 ;选择合适的底漆和面漆配套,提高涂层的附着力。
涂层剥落
检查涂装前的表面处理是否到位,加强脱脂、除锈等处理; 控制涂料的施工粘度和涂层厚度,避免过厚的涂层导致附着 力下降;选择合适的底漆和面漆配套,提高涂层的附着力。
采用现代化的检测仪器和设备,提高质量监控的准确性和可靠性,确保涂层质量的 稳定性和一致性。
04
未来发展趋势
高性能涂料的应用
高性能涂料具有优异的耐候性、防腐 性和装饰性,能够提高汽车外观质量 和延长使用寿命。
随着环保要求的提高,水性涂料、高 固体分涂料等环保型高性能涂料在汽 车涂装中得到广泛应用。
汽车涂装工艺中常见的技术问题 及解决方法
• 常见技术问题 • 解决方法 • 预防措施 • 未来发展趋势
01
常见技术问题
涂装表面缺陷
01
02
03
表面粗糙
涂装表面出现颗粒、凸起 、凹陷等缺陷,影响外观 和质感。
桔皮现象
涂层表面呈现类似桔皮状 的波纹,影响涂层的平滑 度和光泽度。
流挂现象
涂料在垂直表面流动、堆 积,形成泪痕、波浪状等 不均匀涂层。
涂层色差问题解决方法
涂层颜色不一致
加强涂装前的表面处理,确保表面无杂质、油污等;控制涂料的施工粘度和涂层 厚度,避免过厚的涂层导致颜色不均匀;选择合适的涂料品牌和型号,确保颜色 的一致性。
涂层出现色差
加强涂装前的表面处理,确保表面无杂质、油污等;控制涂料的施工粘度和涂层 厚度,避免过厚的涂层导致颜色不均匀;选择合适的涂料品牌和型号,确保颜色 的一致性;加强涂装后的质量检查,及时发现并处理色差问题。
涂料涂装常见问题及解决措施

过期的涂料不能使用,因为其性能会下降。
按照说明书正确使用涂料
使用前应详细阅读涂料使用说明书,按照规定的比例和方法进行稀 释和调配。
涂装表面缺陷问题解决措施
表面预处理
01
对涂装表面进行清洁、打磨等预处理,以去除油脂、污垢、水
分等杂质,提高涂层的附着力和外观质量。
控制涂装厚度
02
涂装时应控制涂层的厚度,避免过厚或过薄,以确保涂层的平
涂装时应控制涂层的厚度 ,避免过厚或过薄,以确 保涂层的附着力和稳定性 。
04 涂料涂装案例分析
案例一:建筑外墙涂料涂装问题解决方案
01 02
涂料脱落
建筑外墙涂料涂装中,由于墙体表面处理不当,涂层与基层粘结不牢, 易导致涂料脱落。解决方法:加强墙体表面处理,确保基层平整、清洁 、无油污,使用粘结力强的涂料品种。
展望
绿色环保
未来的涂料涂装行业将更加注重 环保,研发低VOC、低污染的环 保型涂料将成为行业发展的主要
趋势。
高性能材料
随着科技的不断进步,高性能材料 将成为涂料涂装行业的重要发展方 向,如高耐候、高防腐、高装饰性 涂料等。
智能化涂装
利用先进的智能化技术,实现涂装 过程的自动化、数字化、智能化, 提高涂装效率和涂装质量。
THANKS FOR WATCHING
感谢您的观看
漆面起泡
汽车涂料涂装后,由于底材处理不当或涂层间附着力不足,易导致漆面起泡。解决方法: 加强底材处理,使用除锈剂清除锈迹、油污等,选用附着力强的涂料品种。
漆面龟裂
汽车长时间使用后,由于紫外线照射、温度变化等因素,易导致漆面龟裂。解决方法:选 用耐紫外线、抗老化性能好的涂料品种,定期保养汽车表面。
喷涂中常见不良现象及改善对策
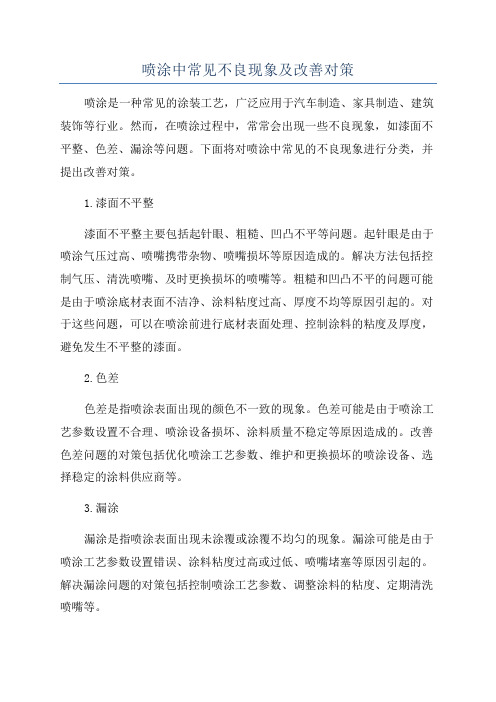
喷涂中常见不良现象及改善对策喷涂是一种常见的涂装工艺,广泛应用于汽车制造、家具制造、建筑装饰等行业。
然而,在喷涂过程中,常常会出现一些不良现象,如漆面不平整、色差、漏涂等问题。
下面将对喷涂中常见的不良现象进行分类,并提出改善对策。
1.漆面不平整漆面不平整主要包括起针眼、粗糙、凹凸不平等问题。
起针眼是由于喷涂气压过高、喷嘴携带杂物、喷嘴损坏等原因造成的。
解决方法包括控制气压、清洗喷嘴、及时更换损坏的喷嘴等。
粗糙和凹凸不平的问题可能是由于喷涂底材表面不洁净、涂料粘度过高、厚度不均等原因引起的。
对于这些问题,可以在喷涂前进行底材表面处理、控制涂料的粘度及厚度,避免发生不平整的漆面。
2.色差色差是指喷涂表面出现的颜色不一致的现象。
色差可能是由于喷涂工艺参数设置不合理、喷涂设备损坏、涂料质量不稳定等原因造成的。
改善色差问题的对策包括优化喷涂工艺参数、维护和更换损坏的喷涂设备、选择稳定的涂料供应商等。
3.漏涂漏涂是指喷涂表面出现未涂覆或涂覆不均匀的现象。
漏涂可能是由于喷涂工艺参数设置错误、涂料粘度过高或过低、喷嘴堵塞等原因引起的。
解决漏涂问题的对策包括控制喷涂工艺参数、调整涂料的粘度、定期清洗喷嘴等。
4.气泡和鱼眼气泡和鱼眼是由于涂料中存在挥发性溶剂或含有不溶性杂质所引起的。
改善气泡和鱼眼问题的对策包括选择低挥发性的涂料、筛选涂料中的杂质、加强喷涂区域的通风等。
5.粘结不良粘结不良是指喷涂表面涂层与底材之间粘结力不强,容易剥离或起皮的现象。
粘结不良可能是由于底材表面处理不当、涂料与底材之间的相容性差等原因造成的。
改善粘结不良问题的对策包括增强底材表面的粗糙度、选择合适的涂料和底材、确保涂层与底材之间的相容性等。
总结起来,喷涂中常见的不良现象包括漆面不平整、色差、漏涂、气泡和鱼眼、粘结不良等问题。
改善这些问题的对策包括优化喷涂工艺参数、维护和更换损坏的喷涂设备、选择稳定的涂料供应商、控制涂料的粘度和厚度、清洗喷嘴、选用低挥发性的涂料、筛选涂料中的杂质、加强喷涂区域的通风、增强底材表面的粗糙度、选择合适的涂料和底材、确保涂层与底材之间的相容性等。
涂装环境改进措施

涂装环境改进措施1. 引言涂装环境是指涂装作业进行时的工作环境和条件。
良好的涂装环境对于保证涂装作业的质量、提高涂装效率和保护工人健康至关重要。
在涂装作业中,涂装环境改进措施的实施可以减少涂装过程中的问题,提高涂装质量,同时也可以降低对环境的污染。
本文将介绍几种常见的涂装环境改进措施。
2. 使用高效的通风系统在涂装作业中,通风系统起着至关重要的作用。
它们可以帮助排除涂料中产生的有害气体、蒸汽和粉尘,从而保证涂装作业的质量,并保护工人的健康。
使用高效的通风系统可以保持涂装环境的清洁和无尘,并保证空气流动的良好性。
通风系统应该设计为能够将有害物质排放到室外,以防止室内空气污染。
3. 确保使用合适的涂料选择合适的涂料对于改善涂装环境至关重要。
使用低挥发性有机化合物(VOC)含量较低的涂料可以降低涂装作业中的气体排放量。
此外,选择含有较少有害金属和溶剂的涂料也可以减少对环境的污染。
因此,涂装作业应该遵循选择环保型涂料的原则,这有助于改善涂装环境并减少对环境的危害。
4. 使用先进的喷涂设备喷涂设备是改善涂装环境的重要因素之一。
现代的喷涂设备具有高效的喷涂功能和较低的涂料损耗。
高喷涂效率可以减少喷涂时间,提高涂装效率。
较低的涂料损耗意味着更少的涂料用于涂装,从而减少了对环境的污染。
此外,在使用喷涂设备时,应该保持设备的良好维护和清洁,以确保喷涂效果的一致性和质量。
5. 做好工作区域的划分在涂装作业中,合理划分工作区域可以减少涂料喷溅和污染的范围。
涂装区域应该与其他区域有明确的分隔,并设有合适的屏障和隔离设施,以防止涂料和有害物质扩散到其他区域。
工作区域应该干净、整洁,并设有适当的收集和处理涂料残留物和废料的设施。
6. 加强职工的专业培训和防护设备的使用涂装作业需要操作人员具备一定的涂装技能,并正确使用相关的防护设备。
因此,加强职工的涂装技能培训是改善涂装环境的关键。
培训应包括正确使用涂装设备、涂料的选择和使用、安全操作规程的掌握等内容。
涂装质量问题整改措施

涂装质量问题整改措施涂装质量问题的整改措施涂装质量问题是指在汽车生产过程中出现的涂料施工问题,如涂层厚度不均匀、起皮、开裂、脱落等。
这些问题不仅影响了汽车的外观质量,还可能导致涂层无法有效保护车身表面,影响车辆的使用寿命。
因此,必须采取有效的整改措施,确保涂装质量达到标准要求。
首先,对涂装过程进行全面检查和评估。
通过对涂装过程中每个环节的操作和设备的检查,确定涂装质量问题的具体原因。
例如,可能是喷涂设备调整不当导致涂料施工不均匀,或者是喷涂工艺参数设置不准确导致涂料起皮开裂。
只有对问题进行深入分析和定位,才能有针对性地制定整改措施。
其次,加强操作人员的培训和技能提升。
涂装工艺本身是一项繁琐的过程,操作人员需要具备良好的操作技巧和丰富的经验。
因此,企业应加强对操作人员的培训,提高他们的专业水平。
可以邀请涂装行业的专家进行技术培训,还可以组织内部的培训班,加强对员工的技能提升。
第三,优化涂装设备和工艺流程。
现代汽车涂装设备和工艺已经非常先进,但仍然存在一些缺陷和不足之处。
因此,企业应对涂装设备进行更新和升级,采用更先进的技术和设备,以提高涂装质量。
同时,还应对涂装工艺流程进行优化,将每个环节的操作规范化和标准化,以确保每个车辆都能够得到一致的涂装质量。
最后,建立涂装质量监控体系。
企业可以建立涂装质量监控点,对涂装过程中的每个环节进行实时监控和记录,及时发现和解决涂装质量问题。
此外,还可以建立涂装质量评估体系,对涂装质量进行定期评估和检查,及时发现质量问题并进行整改。
通过建立完善的质量监控体系,可以最大程度地保障涂装质量的稳定性和一致性。
总之,涂装质量问题对于汽车制造企业来说是一个非常重要的问题,必须要引起足够的重视。
通过深入分析和定位问题原因,加强操作人员的培训和技能提升,优化涂装设备和工艺流程,建立涂装质量监控体系,才能有效地解决涂装质量问题,提高涂装质量,提升企业的竞争力。
涂装质量问题分析及控制措施

涂装质量问题分析及控制措施摘要:本文旨在分析涂装过程中可能出现的质量问题,并提出相应的控制措施。
涂装工艺在许多行业中被广泛应用,是保护、装饰和改进产品外观的重要步骤。
然而,涂装过程中可能出现的质量问题会影响产品质量和客户满意度。
因此,了解涂装质量问题的原因和解决措施对于提高质量控制水平非常重要。
1. 引言涂装是将涂料、油漆或其他涂层材料施加到物体表面以达到保护、改善外观和增加耐用性的工艺。
涂装质量是指涂层的外观、附着力、耐久性以及其他与产品性能相关的特征。
涂装质量问题的存在可能会导致涂层剥落、颜色差异、气泡、裂纹等问题,进而影响产品质量和市场竞争力。
2. 涂装质量问题分析2.1 涂层剥落涂层剥落是涂装过程中常见的质量问题之一。
其主要原因包括:表面预处理不良、粘结不牢固、含油污染、环境温度过高或过低等。
要解决涂层剥落问题,可以通过改善表面处理工艺、优化涂层配方、控制工作环境温度等方式进行。
2.2 颜色差异颜色差异是指涂装后产品表面显示出的色彩不一致现象。
引起颜色差异的原因可能包括:涂料配方、涂装工艺参数、油漆施加均匀度等。
要解决颜色差异问题,可以通过优化涂料配方、加强涂装工艺控制、提高涂料施加均匀度等手段进行。
2.3 气泡涂装过程中产生气泡是一种常见的质量问题。
气泡的原因可能包括:底材表面污染、底漆施加不均匀、涂装时的温度不适宜等。
为了解决气泡问题,可以通过改善底材清洁工艺、调整底漆施加参数、控制涂装温度等方法进行。
2.4 裂纹裂纹是涂装后产品表面出现的线条状划痕或裂缝现象。
裂纹的原因可能包括:涂料干燥不均匀、涂料层厚度过大、涂层收缩应力等。
解决裂纹问题的措施包括:调整涂装工艺参数、施工轻薄涂料层、增加底漆涂层等。
3. 涂装质量控制措施为了提高涂装质量,需采取一系列的控制措施。
以下是几种常见的控制方法:3.1 清洁表面:在涂装之前,对待涂物的表面进行彻底的清洁工艺是非常重要的。
通过去除油脂、灰尘和杂质等污染物可确保涂层与底材之间的粘接性,从而减少剥离和气泡等问题的出现。
涂装厂打磨员工改善提案

涂装厂打磨员工改善提案随着涂装行业的发展,打磨工作在涂装过程中扮演着重要的角色。
然而,我们在实际工作中发现,打磨工作存在一些问题,如效率低下、质量不稳定等。
为了提高打磨工作的效率和质量,我们提出以下改善提案。
一、改善培训和技能提升打磨工作需要一定的技能和经验,因此我们应该加强员工的培训和技能提升。
首先,我们可以邀请专业的打磨技术人员进行培训,教授他们先进的打磨技术和方法。
其次,我们可以组织内部培训班,让有经验的员工与新员工分享经验和技巧。
通过提升员工的技能水平,可以提高打磨工作的效率和质量。
二、改善工作环境和设备良好的工作环境和设备是提高打磨工作效率的重要条件。
我们应该确保打磨区域的通风良好,以减少粉尘对员工健康的影响。
同时,我们还应该配备先进的打磨设备,提高工作效率和质量。
定期检查和维护设备,确保其正常运行,避免因设备故障而影响工作进度。
三、优化工作流程合理的工作流程可以提高工作效率和质量。
我们可以通过以下方式优化打磨工作流程。
首先,合理安排工作任务,根据不同的产品和要求,制定详细的工作计划。
其次,合理分配人力资源,确保每个员工都能充分发挥自己的专长。
此外,我们还可以引入一些自动化设备,减少人工操作,提高工作效率。
四、建立质量管理体系建立质量管理体系是确保打磨工作质量稳定的重要手段。
我们可以制定一套完善的质量管理制度,包括质量检查、质量评估和质量改进等环节。
通过定期的质量检查和评估,及时发现问题并采取措施进行改进。
同时,我们还可以建立员工奖惩机制,激励员工提高工作质量。
五、加强沟通和团队合作打磨工作需要多个环节的协调和配合,因此加强沟通和团队合作非常重要。
我们可以定期组织工作会议,让员工交流工作中的问题和经验。
同时,建立一个良好的团队氛围,鼓励员工相互帮助和支持。
通过加强沟通和团队合作,可以提高工作效率和质量。
通过改善培训和技能提升、改善工作环境和设备、优化工作流程、建立质量管理体系以及加强沟通和团队合作等措施,我们可以提高涂装厂打磨工作的效率和质量。
涂装工作总结范文(3篇)

第1篇一、前言随着我国经济的快速发展,涂装行业在制造业中的地位日益凸显。
作为我国制造业的重要组成部分,涂装行业在提高产品附加值、提升产品品质、延长产品使用寿命等方面发挥着重要作用。
本人在过去的一年里,积极参与涂装工作,现将个人工作总结如下,以期为今后的工作提供借鉴和改进。
二、工作回顾1. 涂装工艺优化(1)针对生产过程中出现的质量问题,我积极与工艺工程师、生产部门沟通,分析原因,找出解决问题的方法。
通过优化涂装工艺,提高了涂装质量,降低了返工率。
(2)针对不同产品特性,制定合理的涂装工艺参数,确保涂装效果。
如针对金属表面处理,采用酸洗、磷化、钝化等工艺,提高涂层的附着力;针对塑料表面处理,采用喷砂、火焰等工艺,提高涂层的附着力。
2. 涂装设备管理(1)负责涂装设备的日常维护保养,确保设备正常运行。
定期对设备进行检查、清洗、润滑,减少设备故障率。
(2)针对设备故障,及时上报并协助维修部门进行处理,确保生产进度不受影响。
3. 涂装现场管理(1)加强涂装现场管理,提高现场作业效率。
对涂装区域进行合理划分,确保作业区域清洁、有序。
(2)加强对操作人员的培训,提高操作技能。
定期开展涂装工艺、安全知识等方面的培训,提高操作人员的安全意识和技能水平。
4. 涂装质量控制(1)严格执行涂装工艺标准,确保涂装质量。
对涂装过程进行全程监控,发现问题及时处理。
(2)对涂装产品进行严格检验,确保产品合格。
对不合格产品进行返工处理,直至合格。
5. 团队协作与沟通(1)与各部门保持良好沟通,及时了解生产需求,确保涂装工作顺利进行。
(2)积极参与团队活动,提高团队凝聚力,共同为公司的目标努力。
三、工作亮点与成果1. 涂装质量提升通过优化涂装工艺、加强涂装设备管理、提高操作人员技能等措施,涂装质量得到显著提升。
涂装产品合格率由去年的90%提升至今年的95%。
2. 降低了生产成本通过优化涂装工艺、提高设备利用率、降低能源消耗等措施,涂装成本得到有效控制。
涂装车间年度工作计划

涂装车间年度工作计划一、综述涂装车间作为整个企业生产装配流程中的重要环节,对产品的外观质量和保护至关重要。
在新的一年里,涂装车间需要制定详细的年度工作计划,以确保涂装质量的稳定提高,并为企业的发展做出贡献。
二、总体目标1. 提高涂装质量:通过改进工艺、引进先进设备和持续培训,提高涂装质量,减少缺陷率。
2. 提高生产效率:通过优化生产流程、提高生产效率,降低涂装成本。
3. 树立环保意识:加强环保意识,减少废水、废气排放,提高涂装车间的环境质量。
4. 强化安全工作:加强安全培训,降低事故发生率,保障员工的生命安全。
三、详细计划与措施1. 改进工艺:(1)优化涂装流程:分析现有涂装流程,寻找短板环节,制定改进计划,并落实到位。
(2)完善涂装工艺规范:建立标准化的涂装工艺规范,明确各个工序的操作步骤及要求,确保质量稳定。
(3)加强涂装参数管理:建立并实施涂装参数管理制度,对每台设备的参数进行监控和调整,以确保涂装效果的一致性。
2. 引进先进设备(1)评估现有设备:对涂装车间现有设备进行全面评估,确定哪些设备需要更换或升级。
(2)引进新设备:根据评估结果,制定设备引进计划,并在年度内逐步引进新设备,以提高涂装效率和质量。
(3)培训员工:对新设备进行培训,确保员工熟练掌握操作方法,充分发挥新设备的作用。
3. 持续培训(1)技术培训:定期组织技术培训,包括涂装工艺、设备操作、质量控制等方面的培训,提高员工的专业素质。
(2)安全培训:加强安全培训,培养员工的安全意识和应急处理能力,降低事故发生的概率。
4. 环保措施(1)减少废水排放:优化涂装工艺,加强废水处理设备的维护,减少废水排放。
(2)减少废气排放:升级涂装设备,改善废气处理装置,降低废气排放浓度。
(3)定期检查环保设施:定期检查涂装车间的环保设施,确保其正常运行,符合环保要求。
5. 安全工作(1)加强安全宣传:通过会议、宣传栏、培训等形式,加强对安全工作的宣传,提高员工的安全意识。
涂装车间质量提升总结(通用)

在汽车制造工厂,涂装车间是一个至关重要的环节,涂装质量直接影响到汽车整体质量和外观。
为了不断提高涂装车间的质量水平,通用汽车公司进行了一系列的改进措施。
本文将从五个方面对涂装车间质量提升总结进行详细阐述。
引言概述涂装车间是汽车制造工厂中关键的环节,对汽车的外观和质量有着重要的影响。
通用汽车公司一直致力于提高涂装车间的质量水平,通过引入新技术和改进工艺来提升涂装质量。
本文将从生产过程、设备更新、员工培训、质量控制和数据分析五个方面对涂装车间质量提升进行总结。
正文内容1.生产过程的改进1.1引入先进的涂装工艺1.2优化生产流程1.3加强品质意识和质量教育现代涂装工艺的引入使得涂装车间能够更加高效地完成涂装工作,同时也提高了涂装质量。
优化生产流程能够减少涂装过程中的时间浪费和资源浪费,提高车间整体效率。
加强对员工的品质意识和质量教育是提升质量的重要手段,让员工在涂装过程中能够更加注重细节和质量,从而提高涂装的精度和一致性。
2.设备更新和维护2.1引进先进的涂装设备2.2定期进行设备维护和检修2.3更新涂装设备的软件和控制系统先进的涂装设备能够提供更好的涂装效果和控制力度,从而大大提升涂装质量。
定期进行设备维护和检修能够保持设备的稳定性和可靠性,减少故障和停机时间。
更新涂装设备的软件和控制系统可以提升设备的自动化程度和精度,减少人为操作的因素对涂装质量的影响。
3.员工培训和技能提升3.1培养专业技能和涂装经验丰富的人员3.2引入新的培训方法和工具3.3建立良好的团队合作氛围员工是涂装车间质量的关键因素,他们的技能水平和经验直接影响到涂装质量的稳定性和一致性。
通过培养专业技能和经验丰富的员工,能够提升涂装车间的整体质量水平。
引入新的培训方法和工具,如虚拟现实技术、模拟训练等,能够提高员工的学习效果和培训质量。
同时,建立良好的团队合作氛围能够加强员工之间的沟通和协作,提高涂装质量的整体表现。
4.质量控制4.1引入全面的质量控制体系4.2设置关键质量指标和监控措施4.3加强对原材料和涂料的质量管控引入全面的质量控制体系能够确保涂装产品的质量稳定性和一致性,通过质量控制来规范和管理涂装生产过程。
喷涂质量提升方案

喷涂质量提升方案背景介绍喷涂是一种常见的涂料施工方式,适用于金属、木材、塑料等各种材料表面的涂装。
在工业化生产中,喷涂加工被广泛应用,但是由于施工技术、环境因素、材料选择等多个方面的问题,喷涂质量往往难以达到理想水平,因此需要制定相应的提升方案,优化喷涂工艺,从而提高产品的质量水平和生产效率。
提升方案1. 增加前期准备工作喷涂前的准备工作对于涂装质量的影响非常大,实施前期准备工作可以有效提高涂装效果和产品质量。
具体措施如下:•清洁工具和材料:更换干净的工具和材料,注意不同材质表面的不同清洁方式,确保材料表面达到准备工作的标准要求。
•完整性测试:对于材料表面缺陷和瑕疵进行测试和检查,做出合适的修整和处理措施。
•表面处理:用相应的材料处理剂去除表面的油污和污垢。
不同类型的表面处理剂的选择应根据具体表面的材质来进行。
•环境准备:保持喷涂环境的整洁和干燥,通风条件良好,避免灰尘和杂质对涂料产生影响。
2. 选择合适的涂料涂料的选择和适应性对喷涂效果和生产效率至关重要。
选择适合具体涂装环境的涂料,从而提高涂装质量和经济效益。
具体措施如下:•了解材料特性:选择相应的涂料针对不同的材料进行涂覆,要考虑到材料的性质和用途。
•选择适用材料:根据使用条件选择具有良好适应性能的涂料,避免涂料的剥落和粘性差异等问题。
•合理配比:根据涂料厚度和施工方式合理配比涂料材料,在施工时保证涂料的稳定性和流动性。
3. 设计清晰的涂装方案涂装方案是决定涂装效果和质量的重要因素之一,在制定当中应该充分考虑产品的特点和工艺条件。
采用合理的涂装方案,可以达到更好的喷涂效果:•精确涂装计量:涂料的质量和数量要根据产品需求精确相符,并且在涂覆过程中需持续监测涂层的厚度和均匀度。
•合理施工方式:涂装工艺的选择根据不同材质的特点,例如完整性,粘着,表面光洁度和环保性等等。
•施工条件控制:在涂装过程中确保环境的干燥度和稳定性,以避免在涂装过程中产生不必要的杂质和质量问题。
- 1、下载文档前请自行甄别文档内容的完整性,平台不提供额外的编辑、内容补充、找答案等附加服务。
- 2、"仅部分预览"的文档,不可在线预览部分如存在完整性等问题,可反馈申请退款(可完整预览的文档不适用该条件!)。
- 3、如文档侵犯您的权益,请联系客服反馈,我们会尽快为您处理(人工客服工作时间:9:00-18:30)。
原因
为了质量提高做什么?
対策
1 2
塗料着色材違い 焼付け温度高いとき光沢無い
3
4 5
塗装‘回数
杭芝機電有限公司
16
Hangzhi
**不良の原因と対策
艶光沢違'30%(
原因
为了质量提高做什么?
対策 ①性能に影響が無い、両方の光沢を承認 する ②光沢の有無サンプルを性能試験行う。 ■余熱無し品'a(を二次塗装すると 光沢は?⇒影響なし ①余熱温度の影響を試験をする。 余熱無し品で確認'a)⇒光沢無し。 ■余熱による光沢影響なし。 6/5
35% 30% 25% 20% 15% 10% 5% 0%
9日 .2 8 4日 17 日 30 日 7日 16 日 21 日 3月 5月 3月 4月 5月 26 5月 5月 5月 26 日 /4
課題
対策
1
2 3 4 5
投入数と良品数
修理品の歩留り 異常値発生時の連絡 4M変更管理
毎日数値化
良品と区分け 不良が多発した時の対応 材料変更 洗浄、塗布材料変更 杭芝機電有限公司 13
1 2
塗装直前の塵付着 塗布作業後に塵付着
3
監督者、作業者、検査員の意識不 足
杭芝機電有限公司
22
Hangzhi
**不良の原因と対策
伤不良
原因
为了质量提高做什么?
対策 ①焼付け温度が低い ②前処理条件不安定で塗膜密着不十分 ■お客様と強度4HでOKか確認する 6/8
1
製品組立て時シャフトに傷が付く ■テフロン塗膜が軟らかい。 '4H OK;5H NG)でもお客様 からキズクレームあり。
目視 目視 供應商材質証明書確認
这样的資料使用? 作業者是知道了?
杭芝機電有限公司
5
塗装作業工程と不良発生要
Hangzhi
部材供給
因
0 1 2 3 4 工程5へ
工程0: 部品受入れ 跳動不良 凹不良
工程1: 前処理 推杆上水渍しみ 剥離不良 膨不良
工程2; 塗料(調合) 色顔不良
工程3; 噴射
工程4: マスキング
这样的话是不是 好? 这样的資料使用? 作業者是知道了?
563 300 263 94 59 48 25 18 7 5 4 2 1 53% 47% 17% 10% 9% 4% 3% 1% 1% 1% 0% 0% 0% 0% 0% 0% 0% 0% 0% 原因 対策1 人) ( 対策2 材料部品) 対策3 方法) ( (
2
杭芝機電有限公司
23
Hangzhi
テフロン塗装の基本管理(大糖複合材料有限公司;李総経理)
PTFE
FEP 240~340℃
テフロンの種類
1.潤滑 '顆粒;焼付温度( 280~340℃ 塗料メーカ推奨;220℃;30分 280℃;15分 Binder'PI樹脂(+PTEF'潤滑成分( 3~5%+顔料 2.不沾 '溶融膜;焼付温度( 370~420℃ 色 差異理由 温度(余熱&焼付け) > 湿度(湿度) >
検査作業者のレベル 検査環境 再現性確認 明るさ 照明種類'波長(
这个工序非常是不 是能着重要,异常 管理?
3 4
5
不良混入 検査前・後品の区分 11
杭芝機電有限公司
Hangzhi
重要工程管理・改善点
課題 1 2 梱包前部品バラ置き
'品質管理的方法(
为了质量提高做什么? 8 梱包
対策 打痕対策
3
9
輸送
1 2 3
課題 適正パレットか? 外箱は丈夫か?
対策
杭芝機電有限公司
12
Hangzhi
重要工程管理・改善点
課題 1 2 修理品の方法 処理時期
'品質管理的方法(
为了质量提高做什么? 10 修理品対策
対策 一般品と同じ? 修理品だけ区分け
3
这个工序非常是不 是能着重要,异常 管理? 11 不良統計& 分析対策
検査数量 (6/2) 良品 不良数量 推杆上水渍 凸点 露底 凹点 铁芯基材伤 异物 膠水付者 劃傷 推杆划伤 異色 塗層不良 調動不良 杆上有圏 少送 塗層過長 塗層少 汚
杭芝機電有限公司
14
Hangzhi
不断挑戦 日日進歩
Hang Zhi
杭芝機電有限公司 15
Hangzhi
**不良の原因と対策
2
原材料内部有缺陷、拉伸磨加工 后可以看出有凹陷 'Φ18⇒Φ16.15~16.20(
杭芝機電有限公司
20
Hangzhi
**不良の原因と対策
凸 不良'2%(
原因
为了质量提高做什么?
対策 ■作業者への注意指示 ■作業者への注意指示
1 2
塗装工場での部品と部品の衝突、 干渉 塗装工場での部品と治具、装置な どと干渉
3
治具への取り付け、取り外し時に
■作業者への注意指示
杭芝機電有限公司
21
Hangzhi
**不良の原因と対策
異物不良'2%(
原因
为了质量提高做什么?
対策 ■塗布工程でのエアーブロー徹底 ■乾燥工程に入るまでに塵付着防止の為 乾燥コンベア周囲に難燃カーテンの設置 ■乾燥コンベア&現場の清掃 ■監督者、作業者、検査員作業者への注 意指示教育
Hangzhi
冷蔵庫用ドア開閉 ソレノイドの塗装品質改善
'杭芝(
2011年6月5日
杭芝機電有限公司
1
Hangzhi
現状的品質状況
机加工 ? 装 杭芝
'品質的問題(
日期 12/22-4/6 5/16-26 1.杭芝受入数量: 45,605 11,050 2.不良品数量 8,166 4551 3.不良率 18% 41% ④劃傷 3% 12% ⑤凹点 2% 10% ⑧凸点 1% 8% 4% 不 ⑩杆上有圏 ①跳動不良 3% 3% 良 内 ②異色 3% 2% 容 ⑥膠水附者 1% 2% ⑨塗層不良 1% 1% ③露底 3% ⑦塗層少 1%
塗装材料問題
劃傷 塗層不良 異色 塗層少
4.
Hangzhi
不良数量 検査数量 良品 不良数量 凹点 ? 物 凸点 劃傷 露底 塗層過長 膠水付者 異色 推杆? 伤 铁芯基材伤 推杆上水渍 ? 化前 喷? 干燥后 97 39 58 20 16 15 5 1 1
不良分析から真因対策を実施
烧结后 搬送后 ? 包前 563 40% 300 60% 263 21% 25 16% 7 15% 59 5% 4 1% 48 1% 5 1 2 18 94 53% 47% 4% 1% 10% 1% 9% 1% 3% 17%
6/5
2
3 4
■280℃で様品作成'5本( ■170℃で様品作成'5本(
6/7 6/8
杭芝機電有限公司
17
Hangzhi
**不良の原因と対策
推杆上水渍 '7%(
原因
为了质量提高做什么?
対策 ①水洗后用気槍吹干,還有残留用布擦干. 6/4 ②全数检查、如有印迹要擦干。 ■不良様品で検査員の教育実施 実施記録を(杭芝)へ報告 6/7
不良数量 検査数量 良品 不良数量 凹点 ? 物 凸点 劃傷 露底 塗層過長 膠水付者 異色 推杆? 伤 铁芯基材伤 推杆上水渍
53% 47% 4% 1% 10% 1% 9% 1% 3% 17%
杭芝機電有限公司
4
Hangzhi
外観検査基準&強度仕様??
検査内容 規格 方法 検査方式
検査項目
2
3
外観
5
6
7
8
9
工程5: 余熱&塗布 強度不足 異 物 凸不良
工程6: 乾燥&焼付け 強度不足 傷不良
工程7; 検査 不良流出 傷不良 不良仕様
工程8; 梱包
工程9: 輸送・管理
傷不良
膠水附者
跳動不良
杭芝機電有限公司
6
Hangzhi
重要工程管理・改善点
燐化処理
課題 部材受入れ検査 1 2 3 4 5 処理液交換時期 処理時間と温度 洗浄水のph値管理 乾燥温度と時間 部品搬送時打痕 課題
対策
2
3 4 5
粘度管理・確認
原材料、溶剤寿命 混合容器の管理
課題 1 マスキング方法 冶具交換タイミング ばらつき'斑(
対策
4
塗布前処理 マスキング
2 3 4 5
杭芝機電有限公司
8
Hangzhi
重要工程管理・改善点
課題 1 均一塗布 斑無塗布
'品質管理的方法(
为了质量提高做什么? 5 塗布
対策
2
25% 20% 15% 10% 5% 0%
5月 26 日
3月 9日
5月 4日
5月 7日
9日
.2
8
4日
17 日
30 日
7日
16 日
21 日 5月
3月
5月
3月
4月
5月
26
5月
4.
5月
26 日
/4
杭芝機電有限公司
2
Hangzhi
6/2不良品の分析と対策
563 300 263 94 59 48 25 18 7 5 4 2 1 53% 47% 17% 10% 9% 4% 3% 1% 1% 1% 0% 0% 0% 0% 0% 0% 0% 0% 0% 原因 対策1 人) ( 対策2 材料部品) 対策3 方法) ( (
1 2
燐化后水洗液残留,直接進行烘 干、造成印蹟. 流出
杭芝機電有限公司
18
Hangzhi
**不良の原因と対策
露 底'3%(
原因