A3报告-CB312行李箱与侧围间隙过小的调查分析2014.08.20
现阶段下线车辆间隙面差共性问题评审(2198)-11-15

首先要确保机盖与 翼子板面差
实际值再确认一下
零件尺寸问题,由SQE 首先要确保前门和 来料控制 翼子板间隙 零件尺寸问题,由SQE 首先要确保前门和 来料控制 翼子板间隙
冲压件整改合格后 从新验证 左前门上铰链往+X方 向微调,或锁扣往-Z 方向微信 零件尺寸问题,由SQE 首先要确保前门和 来料控制 后门间隙 零件尺寸问题,由SQE 首先要确保前门和 来料控制 后门间隙 行李架有胶垫,不 是贴合状态 数据上仪表台就 高,不是平的 左前门上铰链往-Y方 向微调 左前门上铰链往-Y方 向微调 沿用件,数据间隙 为1.0MM
30 31 32 33 34 35 36 37 38 39 40 41 42 43 44 45 46 47 48 49 50
左后门槛踏板与行李箱饰板面差,间隙约1.5mm 右后门槛踏板与行李箱饰板面差,间隙约2mm 左C柱上饰板前、后部与行李箱饰板面差 杯托与左、右侧行李箱饰板不贴合 左侧行李箱饰板与四角窗间隙约5mm 右侧行李箱饰板与四角窗间隙约3mm 左D柱上饰板前端与行李箱饰板面差,间隙约1.5mm 右D柱上饰板前端与行李箱饰板面差 左D柱上饰板前端上部与顶棚不贴合 左、右后轮眉与后保不贴合,最大间隙约1mm 加油口盖板四周间隙不均 左侧四角窗下部亮条与侧围间隙不均,最大约2mm 右侧四角窗下部亮条与侧围间隙不均,最小约1mm,最大约3mm 后保与左、右侧围面差 扰流板与左、右侧围面差 左后尾灯固定部分与侧围间隙不均,最小约1mm,最大约4mm 右后尾灯固定部分与侧围间隙不均,最小约1mm,最大约4.5mm 背门与左侧围间隙不均,最小约3mm,最大约6mm 背门与右侧围间隙约8.5mm 左后尾灯固定与活动部分最大间隙约2mm 右后尾灯固定与活动部分间隙约4.5mm
行李箱护板SE分析标准

行李箱护板分析标准
1.产品结构
1.1后行李箱至口高度不一致,行李箱密封条装配后不密封,易出现漏水。
对策:修改数据做平,保证后行李箱至口高度一致。
1.2后围内装饰板装配后,存在和行李舱左侧装饰板的间隙及段差管理困难的末端形状
间隙阶差 管理困难
后围内装 饰板
行李舱左侧 装饰板
后行李箱至口高度不一致
对策:变更后围内饰板的末端形状
1.3行李舱左侧装饰板的中央部位上没有固定点造成维持形状及位置决定困难 对策:行李舱左侧装饰板上增加固定点(右图)
1.4左后柱中装饰板的安全带取出用的装配孔没有造成无法操作 对策:增加取出安全带用装配孔
1.5右后柱中装饰板的固定销方向和操作方向相异造成无法操作 对策:变更右后柱中装饰板的固定销方向(如右图)
行李舱侧装饰
无固定点
讨论变更形状
后围内装饰板
增加决定形状及位置用的固定点
左后柱中装饰板
没有安全带取出用的装配孔
后排两侧安全带总成
右后柱中装饰板
增加取出安全带用的装配
1.6行李舱左侧装饰板上的紧急开启把手取出操作困难. 对策:行李舱左侧装饰板上增加键槽
1.7行李舱左侧装饰板的孔(Φ10.2)对比,紧急开启把手的外径(Φ7.5)太小,会往箭头方向移动有噪音
对策:行李舱左侧装饰板的孔大小变更(Φ10.2 → Φ8.5)
Φ10.2
行李舱左侧装饰板
Φ8.5
Φ10.2
行李舱左侧装饰板
紧急开启把手
Φ7.5
行李舱左侧装饰板
紧急开启把手
左后柱中装饰板
右后柱中装饰板
固定销方向相异。
汽车后保与行李箱盖间隙值研究

( C h e w Au t o mo b i l e C o mp a n y L T D. , A n h u i Wu h u 2 4 1 0 0 0 )
Ab s t r a c t :Th e t r u n k l i d a n d r e a r b u mpe r i n t e r f e r e nc e i n a ne w c a r d e v e l o p me n t a n d t r i a l p r o d u c t i o n i n Ch e w
大到 1 I mm。
和上 安装 固定 支架 需要更 改模 具 , 需要 大约 2 5天 的
的 费用加起 来 大约 是 3 0万元 。
由计 算 得知 ,调 整之 后 ,后 保 险杠与 行 李箱盖 时 间。缓冲块 的设 变也 需要 3 0天 左右 的 时问 。全 部 的配 合 问隙最 小值 是 5 . 5 m m,显 然是满 足 要求 的 。
2 mm,并且 边沿 去掉 2 mm,避免 与后保 的干 涉 。与 李 箱盖 X 方 向间隙值 定义 偏 小 ,而 导致 产 生约 3 O 后 保 上安 装 固定 支架相 配 合 的后 围外板 本 体上 面 的 万 元 的额 外设 变 费用 。后 期 新开 发 ,根据 车 型 及 生 焊 接 型面 向 内凹进 ,向 一x方 向移 动 2 mm,使 后保 产 工 艺控制 的情 况不 同 , 设计 间隙值 建议 定 义为 7 ~ 安装 固定支 架 整体 向 一x方 向移动 2 mm。下 安装 固 1 l mm, 规避 消 费者 使用 一段 时 间后 才 出现 的干涉 风 定 支 架等其 余 部分不 变动 。 险 。同 时,后保 凸台高度 建议 定义 为 1 0 mm 左右 , 0 。左 右 的倾斜角 ,规避 后 期此 处 的流水 设计 后保 上 安装 孔 8 . 5 mm, 下安 装孔 ( I ) l O . 5 给 出一个 1 mE,将 安装 孔径 单边 间 隙控 制 到 0 . 2 5 m m,控 制后 及行 李箱 盖过 关等 的隐 患 。同时 ,在汽 车设 计 阶段 ,
车身间隙面差问题改善方法
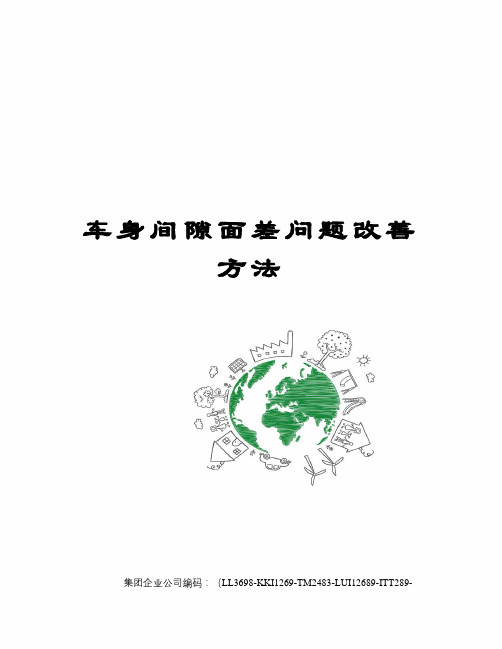
车身间隙面差问题改善方法集团企业公司编码:(LL3698-KKI1269-TM2483-LUI12689-ITT289-车身间隙面差问题改善方法作者:宗广达柴晨光董章群户玉?文章来源:长城汽车股份有限公司技术中心,河北省汽车工程技术研究中心?发布时间:2014-04-02白车身间隙面差对于车身质量有着重要的影响。
本文结合白车身间隙面差现场调试经验,介绍了白车身间隙面差问题的一般改善方法以及改善思路。
车身外观就像是人的脸面,它的好坏往往决定着人们对这款车的第一印象,甚至直接构成车辆销售的第一评判标准。
车身的间隙面差问题是决定车身外观好坏的一项重要因素,因此如何保证车身的间隙面差品质就成了各汽车生产厂的重要目标。
本文主要介绍白车身间隙面差问题的改善方法。
间隙面差影响因素间隙面差问题不仅是车身调试问题中的难点,同时也是一个综合性问题。
影响车身间隙面差问题的因素有很多种,只有把每种影响因素都控制到位才能保证间隙面差的精度与稳定。
1.车门外板单件的影响车门外板单件(见图1)主要影响车门总成的间隙,一般对面差的影响可以忽略不计,但是如果车门外板的刚度比较大,与内板单件的料厚及强度相似,这时也需要考虑车门外板对面差的影响(一般窗框和车门主体为一体冲压件时会出现此种情况),所以我们要对外板单件翻边棱线进行重点控制。
2.车门内板单件的影响车门内板单件(见图2)主要影响车门总成的面差,包边总成的面差基本上和内板的面差一致(上述提到的内外板强度相近的除外)。
当内板的修边线过大时会对总成的间隙造成一定影响,同时也会影响包边质量,所以要重点对包边面的面差进行控制。
3.焊装夹具的影响焊装夹具的作用主要是使制件能够按照匹配结构在正确的位置进行焊接,以及避免焊接变形。
焊装夹具的定位块精度及结构对车门总成及车身精度都有很大的影响(见图3)。
另外,合理的定位夹紧结构还可以有效控制焊接变形的影响,所以如何让夹具能够焊接出符合要求的总成也是控制间隙面差问题的有效手段。
前后门窗饰板间隙偏小问题分析与解决

10.16638/ki.1671-7988.2020.13.055前后门窗饰板间隙偏小问题分析与解决曹倩(上汽通用汽车有限公司尺寸工程科,上海201206)摘要:随着汽车行业的竞争日趋激烈,汽车产品的感官质量越发受到重视,而外饰匹配是其中一项重要的衡量标准。
文章针对某车型前后门窗饰板间隙问题,依据尺寸链详细剖析各个环节的原因,综合考虑项目节点、更改难度、成本等因素,采用了偏差控制的方法有效解决问题。
分析过程采取手工样件验证、重复装配实验、Python数据分析等手段,最终消除了缺陷。
文章旨在分享实际生产过程中解决相关复杂问题的思路与经验。
关键词:外饰匹配;偏差控制;均值偏移;数据波动中图分类号:U463.83+9.2 文献标识码:A 文章编号:1671-7988(2020)13-176-03Analysis of Front Door and Rear Door Appliques’ Gap IssueCao Qian(SAIC General Motors Corporation Limited Dimension Engineering Division, Shanghai 201206)Abstract:With the increasingly fierce competition in automobile industry, the perception quality has been paid more attention, and the exterior matching is a quite important evaluation criterion. This paper focuses on the gap between front door and rear door applique of a certain model, according to the dimension chain to analyses each relevant cause, and considering the project schedule, difficulty level, and cost, finally the deviation control method is adopted. The analysis process adopts manual sample verification, repeated assembly experiments, and Python tool to eliminate the defect. Here aims to share the ideas and experience of solving related complex problems during manufacture.Keywords: Exterior matching; Deviation control; Mean deviation; Data fluctuationCLC NO.: U463.83+9.2 Document Code: A Article ID: 1671-7988(2020)13-176-03前言随着生活水平的提高,人们不仅关注汽车的性能,对外观和精致度也平添了更多的期待。
旅行箱质量问题分析
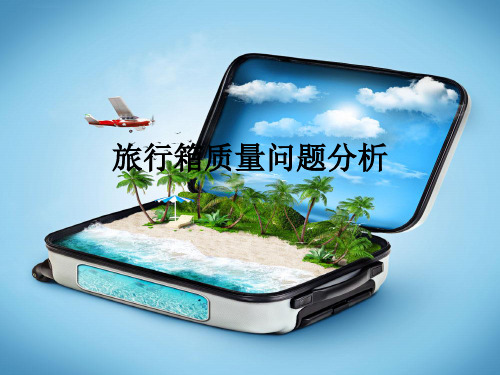
拉杆质量差
• 标准规定,拉杆开关应顺畅。质量好的拉 杆,除应具有足够的刚度外,主杆与伸缩 杆配合间隙应合理,锁钮灵活有效。此次 抽检发现部分产品拉杆与伸缩杆之间的配 合间隙过大,拉杆拖出后晃动现象严重。 有的产品在进行外观检验时,拉杆锁钮按 下后拉杆两边不平行,造成拉杆拔不出来。
产品标识Байду номын сангаас规范
• 不按照国家有关规定应在产品及产品包装 上,注明产品名称、产品等级、材质、规 格(型号)、厂名、厂址,联系电话、执 行标准等信息
解决措施
• 监督部门加强监督,安检部门加强安检, 购买者检查再三。
旅行箱质量问题分析
提把用料差,强度低
• 提把是搬动箱包时用到的重要部件,要求 必须具备一定的强度。本次抽查中有9种 产品该项不合格。有的产品用再生塑料生 产,结构单薄,制造粗糙;有的产品在进 行负重试验时箱体刚提起来提把就发生了 断裂。
走轮脱落
• 旅行衣箱、旅行软箱安装走轮可使消费者 省力方便地携带物品。轮子转动时,轮轴 会逐渐升温,普通塑料走轮及其支架会变 软、变形,最终造成走轮整体损坏。标准 要求,走轮在规定的负重条件下应行走8 公里。有的产品在规定负重条件下行走不 到4公里即出现走轮支架损坏、轮子脱落 的现象,主要原因是走轮及支架材料差, 不耐热。
旅行箱调研报告

旅行箱调研报告旅行箱调研报告一、调研目的本次调研旨在了解消费者对旅行箱的需求和喜好,以帮助企业更好地研发和生产旅行箱产品,提升市场竞争力。
二、调研方法1.问卷调查:设计并发放问卷给目标消费群体,了解他们对旅行箱的需求、购买习惯和意见建议。
2.实地观察:前往旅行箱销售商店进行实地观察,了解市场上旅行箱的种类、价格和销售情况。
三、主要发现1.消费者对旅行箱的需求集中在轻便、耐用和大容量三个方面。
轻便是旅行者非常看重的因素,便于携带和运输;耐用是确保旅行箱能经受住多次使用和长途旅行的考验;大容量能够提供更多的空间装载旅行物品。
2.消费者对旅行箱的外观设计也有一定的要求,包括简约大方、时尚个性和多样选择等。
一些消费者认为旅行箱作为旅行的配件之一,希望能够展现个人风格和时尚品味。
3.消费者普遍购买旅行箱的渠道以实体店为主,比较重视亲身试用和观察产品质量。
然而,越来越多的消费者也倾向于在电商平台上购买旅行箱,主要考虑方便快捷和价格透明。
4.对于旅行箱的价格,消费者普遍认为价格在500-1000元之间为合理范围,高于1000元的产品需求较少。
5.消费者对旅行箱的品牌影响力和市场口碑有一定的关注,有些消费者会选择知名品牌产品,认为它们更能保证产品质量和售后服务。
6.消费者对旅行箱的材质有一定要求,常见的材质选择有ABS、PC和铝合金。
ABS材质轻便且价格较低,适合短途旅行;PC材质轻薄而且坚固耐用,适合长途旅行;铝合金材质耐用且防潮防锈,适合经常出差或长时间旅行。
7.消费者对旅行箱的功能性也有一定要求,包括防水、防震、防刮擦等。
另外,一些消费者也希望旅行箱有扩容功能,方便在旅途中存放购物物品。
四、建议1.企业在研发和生产旅行箱时应注重材质的选择和质量把控,提供多样化的选项以满足消费者不同的需求和预算。
2.加强旅行箱的外观设计,注重品牌形象和个性化,与时尚潮流相结合。
3.拓展销售渠道,尤其要重视电商平台的发展,提供方便快捷的购买方式。
检查行李舱
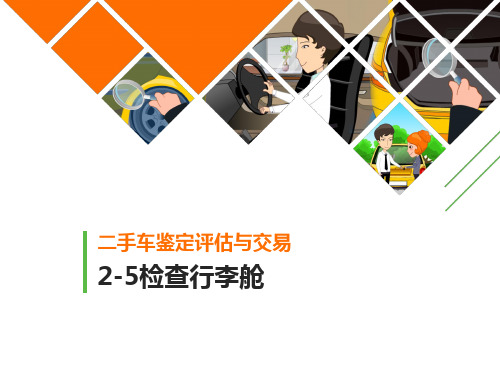
车辆后部检查内容
(6)后备箱内板 检查后备箱内板是否平整、变形。 (7)后翼子板内衬 检查后翼子板内衬是否变形;拆开内 衬,查验焊接原点是否存在,是否平滑,是否有打胶喷漆 现象。 (8)备胎槽 未发生过碰撞的车辆备胎槽边缘是完整而圆 滑的,当车辆受过撞击修复以后是不可太可能完全恢复到 原来自然顺滑的状态的,必然会留有褶皱。 (9)随车工具 检查随车工具(三角警示牌、千斤顶、车 载灭火器、轮胎扳手、牵引环等。需要注意的是,不同品 牌车型随车工具不同)是否齐全,是否有水点锈。 (10)备胎 检查是否有备胎;如果有备胎,胎压是否正 常,备胎是否老化,是否有磨损,是否有裂痕。 (11)液压杆或支撑杆 检查液压杆或支撑杆是否正常工 作,焊接原点是否存在,是否平滑,是否有喷漆现象。
车辆后部事故情况检查
(6)掀开备胎箱盖,查看底板有无变形或整形 痕迹,焊接点是否为原厂,如下图所示。若车 尾被撞过,底板则会高低不平。
备胎箱底板及焊接原点检查
14
THANK YOU
谢谢观看
后备箱
1
任务分析
二手车后备箱的检查,主要要观察是否有过追尾事故的 痕迹。然后要看是否有过修复、被锈蚀的痕迹。备胎工 具是否齐全,密封条是否原装有无修复痕迹。
2
学习目标
1.能够鉴别后备箱盖是否修复或更换。 2.能够鉴别后尾灯是否更换、破损。 3.能够鉴别上顶板、导水槽、后围板、后备箱内板、后翼子板内 衬、备胎槽是否变形、修复或更换。 4.能够鉴别液压杆或支撑杆是否损坏、修复或更换。
二手车鉴定评估与交易
2-5检查行李舱
任务描述
对车辆行李舱进行检查时,重点检查车辆后备箱盖情况 、上顶板、导水槽、后围板、后备箱内板、后翼子板内衬、 备胎槽、液压杆或支撑杆、随车工具、备胎等情况。
浅谈汽车内外饰间隙段差问题影响因素及解决方法

qiyekejiyufazhan0引言整车从开发到量产中间环节众多,尺寸偏差从前期设计到制造过程中的冲压、焊接及装配不断累积和传递,此外考虑零部件本身尺寸精度的影响,整车的偏差就更加难以控制;因此,各种偏差不断地影响着整车内外饰品质的输出,整车工厂下线也不可避免地出现各种各样的内外饰间隙段差问题。
以往整车企业专注于解决制造和零部件匹配精度的问题,对于尺寸感知质量的要求不高,很少关注内外饰配合的品质;但随着汽车行业的快速发展,消费者对汽车客观感知效果的要求日益增高,消费者对内外饰间隙段差的关注度大大增强,这就要求汽车企业加大在提升内外饰配合品质方面的投入,快速高效地解决内外饰质量问题,提升消费者满意度。
1汽车内外饰间隙段差影响因素整车的制造品质贯穿于前期的造型设计到后期的量产全过程;合理的定位、分配和制定公差、模具设计、检具设计及恰当的装配工艺对整车达到既定品质和功能尤为关键。
整车制造过程环节众多,尺寸偏差在各环节中累积和传递,设计合理性、零件质量水平、装配过程合理性及质量检查方式方法等均会影响汽车内外饰间隙段差,进而影响整车品质输出。
1.1设计偏差整车开发过程工作内容多且复杂,设计上覆盖造型设计、零部件定位系统和公差设计、工装设计、夹具设计、检具设计及测量设计等。
整车造型设计阶段的间隙面差目标值定义的合理性、整车及零部件定位和公差设计与校核的合理性、制造过程偏差分析的合理性及零件夹具、检具和测量设计的合理性对整车间隙段差的输出具有极大的影响。
设计偏差对于整车内外饰间隙段差品质输出极其不利。
目前,许多企业均已引入尺寸工程的概念,通过整车及零部件定位系统和公差设计信息,把车身设计、制造和检测过程有机连成一体,从设计到量产全过程,通过尺寸链或公差虚拟仿真技术对尺寸设计和要求进行风险评估和预防,有效地监控和改善整车品质。
1.2零件偏差汽车内饰件包括顶衬、饰板、座舱模块、座椅及地毯等;外饰件包括前后保、前后组合灯、后视镜、裙板及扰流板等。
间隙平顺度问题的分析与优化措施

10.16638/ki.1671-7988.2020.09.043间隙平顺度问题的分析与优化措施郭杰1,谢添2,肖国威3(1.北京奔驰汽车有限公司研发一部车身科,北京100176;2.北京奔驰汽车有限公司研发二部AK科,北京100176;3.北京奔驰汽车有限公司研发一部内外饰科,北京100176)摘要:文章基于实际生产中的案例,论述问题的分析解决过程。
首先对该问题的基本情况进行介绍。
针对右侧小尾灯和后备箱盖之间间隙小的问题,阐述分析区域的间隙平顺度标准,以及匹配关系和定位点信息。
然后说明采用绿带方法的具体分析过程,主要包括三相图分析,三坐标对比分析,并总结根本原因。
最后通过验证根本原因的方式,逐步确定长期措施。
文章所采用的分析方法,对生产中出现的质量问题具有重要的参考价值,进而可以减少费用支出,优化质量,提高工作效率。
关键词:汽车;尾灯;匹配;间隙;分析中图分类号:U466 文献标识码:B 文章编号:1671-7988(2020)09-141-05Analysis and Optimization for Gap and Transition IssueGuo Jie1, Xie Tian2, Xiao Guowei3(1.Beijing Benz Autompbile Co., Ltd. RD BIW, Beijing 100176; 2.Beijing Benz Autompbile Co., Ltd. RD AK, Beijing 100176; 3.Beijing Benz Autompbile Co., Ltd. RD EXT, Beijing 100176)Abstract: This article discusses the process of analyzing and solving problems based on actual production cases. Firstly, the article introduced the general situation for this case. For small gap issue between the right-hand taillamp and trunk lid, showed the gap and transition standard of analyzing area, the location point and matching relationship between the small taillamp and trunk lid. Secondly, started the specific analysis process, including 3-phase diagram analysis, CMM analysis, and summarize the root cause from the analysis process. Finally, through verifying the root cause, find the long term solution to solve this issue.The analysis method used in this article has important reference value for quality issues in production. It can effectively solve car issue especially for gap and transition issue, reduce cost, optimize quality and improve work efficiency.Keywords: Vehicle; Taillamp; Matching; Gap; AnalysisCLC NO.: U466 Document Code: B Article ID: 1671-7988(2020)09-141-05前言质量是企业生存和发展的根本,如何高效准确得找到根本原因,解决质量问题是各公司相关部门在探索的方向。
行李箱内板拉深压边力曲线的优化

A ul 0M anufacl u r i ngTechn0109y 汽车翻造技术行李箱内板拉深压边力曲线的优化料陈淑婉①蒋敏②詹艳然③黄胜①(①运城学院机电工程系,山西运城044000;②重庆宇杰汽车设计有限公司,重庆400020;③福州大学机械工程及自动化学院,福建福州350108)摘要:对新型高强度相变诱发塑性钢T 砌暇舢钢板拉深成形的行李箱内板进行研究,将获得的变压边力成形窗口分为若干段,通过数值模拟的方法得到行李箱内板成形质量与各段压边力之间的正交试验数据,经极差分析确定正交试验优化方案;以正交试验数据为训练样本,通过B P 神经网络建立成形质量与各段压边力之间的非线性映射关系。
并以此关系作为多目标遗传算法的适应度函数进行遗传算法优化,获得一组Par et o 最优解集,实现了对行李箱内板成形窗口内压边力曲线的优化。
优化结果表明。
相比于正交试验优选方案,采用遗传算法和神经网络相结合的方法得到的优化方案成形零件时。
能较大程度地提高行李箱内板的成形质量。
关键词:行李箱内板TR I P 600高强钢板变压边力曲线神经网络遗传算法中图分类号:TG 3%文献标识码:B0pt i m i zat i on of bl ank-hol der f or cecur vefor t he dee p dr aw i ngof t r unk Ii d i nner pa ne IC H EN Shuw anO ,JI A N G M i n ②,Z H A N Y a nr a n ③,H U A N G S heng ①((亘)D epar t m ent of M e c hani cal &E l e ct r i cal Engi ne er i ng ,Y uc he ng U ni ver si t y ,Y uncheng 044000,C H N ;@Y uj i eA ut om ot i ve D e si gn C o .。
变大变小的行李箱作文400字
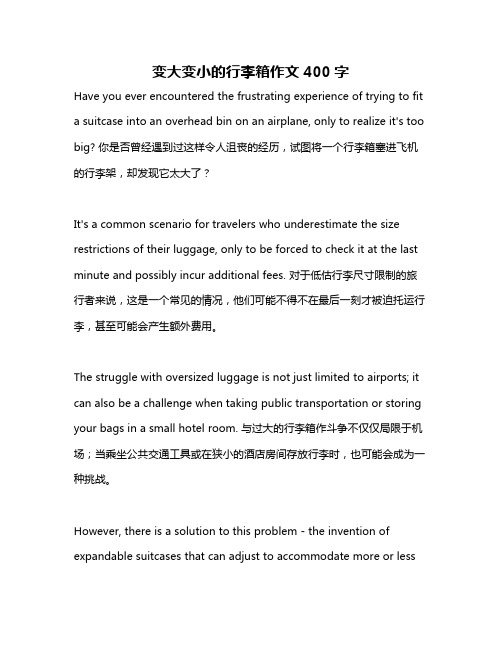
变大变小的行李箱作文400字Have you ever encountered the frustrating experience of trying to fit a suitcase into an overhead bin on an airplane, only to realize it's too big? 你是否曾经遇到过这样令人沮丧的经历,试图将一个行李箱塞进飞机的行李架,却发现它太大了?It's a common scenario for travelers who underestimate the size restrictions of their luggage, only to be forced to check it at the last minute and possibly incur additional fees. 对于低估行李尺寸限制的旅行者来说,这是一个常见的情况,他们可能不得不在最后一刻才被迫托运行李,甚至可能会产生额外费用。
The struggle with oversized luggage is not just limited to airports; it can also be a challenge when taking public transportation or storing your bags in a small hotel room. 与过大的行李箱作斗争不仅仅局限于机场;当乘坐公共交通工具或在狭小的酒店房间存放行李时,也可能会成为一种挑战。
However, there is a solution to this problem - the invention of expandable suitcases that can adjust to accommodate more or lessitems as needed. 然而,这个问题有一个解决方案——可扩展的行李箱的发明,可以根据需要调整以容纳更多或更少的物品。
基于用户行为分析的行李箱设计研究
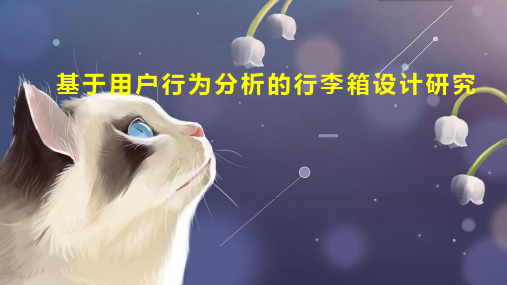
01 引言
03 设计思路 05 结论
目录
02 用户行为分析 04 设计实践
引言
行李箱是人们出行必备的物品之一,尤其在旅游、商务出差等场合中发挥着重 要作用。然而,目前市场上的行李箱设计存在一些问题,如行李箱的尺寸、颜 色、材质等不符合用户需求,行李箱的功能按键设置不合理等。为了解决这些 问题,本次演示将基于用户行为分析的思路,对行李箱设计进行研究。
设计实践
在设计方案实践阶段,我们选择了市场上具有代表性的几款行李箱进行案例分 析。通过实际使用和用户反馈,我们发现以下问题:
1、某款行李箱的尺寸过大,不 便于携带和存储;
2、某款行李箱的材质不够耐用, 易划伤和破损;
3、某款行李箱的功能按键设置 不够合理,使用不够便捷;
4、某款行李箱的内部空间规划 不合理,导致空间利用率低。
1、外观设计:行李箱的外观应该简洁大方,符合不同场合的审美需求。同时, 设计应该注重品牌识别度,让用户能够轻松识别出品牌。
2、材质选择:选择耐用、环保、轻便的材质,如高品质的塑料、合金或者碳 纤维等。考虑使用耐磨、易清洁的材质,以便用户可以长时间使用行李箱。
3、功能按键设置:根据用户行为分析的结果,设计合理的功能按键,以满足 用户在操作过程中的需求。例如,设置轮子开关、拉杆开关、锁扣开关等功能 按键,使用户可以更加方便地操作行李箱。
结论
本次演示基于用户行为分析对行李箱设计进行了深入研究。通过了解用户使用 行李箱的习惯和需求,我们提出了一系列针对性的设计思路和方案。在实践过 程中,我们发现这些设计方案能够有效改善现有行李箱存在的问题并提高用户 的满意度。因此,基于用户行为分析的设计思路对于改进行李箱设计具有重要 的意义。
汽车行李架与车顶间隙过大成因分析及解决方法不均
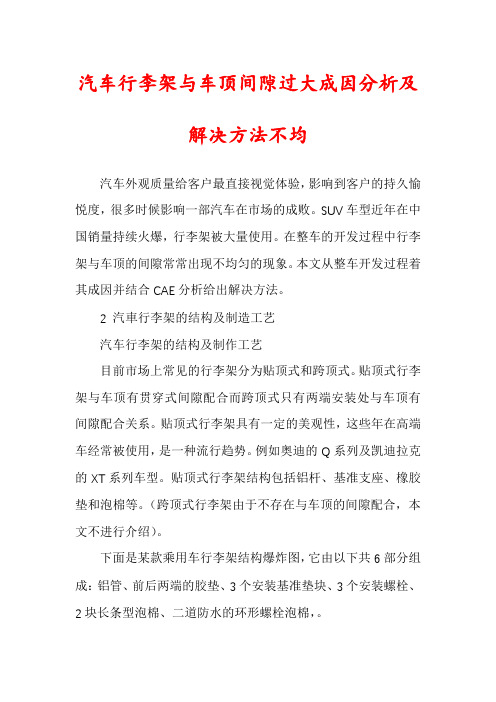
汽车行李架与车顶间隙过大成因分析及解决方法不均汽车外观质量给客户最直接视觉体验,影响到客户的持久愉悦度,很多时候影响一部汽车在市场的成败。
SUV车型近年在中国销量持续火爆,行李架被大量使用。
在整车的开发过程中行李架与车顶的间隙常常出现不均匀的现象。
本文从整车开发过程着其成因并结合CAE分析给出解决方法。
2 汽車行李架的结构及制造工艺汽车行李架的结构及制作工艺目前市场上常见的行李架分为贴顶式和跨顶式。
贴顶式行李架与车顶有贯穿式间隙配合而跨顶式只有两端安装处与车顶有间隙配合关系。
贴顶式行李架具有一定的美观性,这些年在高端车经常被使用,是一种流行趋势。
例如奥迪的Q系列及凯迪拉克的XT系列车型。
贴顶式行李架结构包括铝杆、基准支座、橡胶垫和泡棉等。
(跨顶式行李架由于不存在与车顶的间隙配合,本文不进行介绍)。
下面是某款乘用车行李架结构爆炸图,它由以下共6部分组成:铝管、前后两端的胶垫、3个安装基准垫块、3个安装螺栓、2块长条型泡棉、二道防水的环形螺栓泡棉,。
铝管是行李架的主体结构,贯穿车顶前后,其精度对于行李架总成至关重要,同时是制作精度最难控制部分,直接体现行李架零部件制造商工艺水平。
3 行李架与车顶间隙过大问题的现象及原因分析行李架安装后高低方向在铝管两侧与车顶形成一条长约3M 的配合间隙。
由于配合长度长,当间隙不一致时呈现波浪形或者凹形,给客户不精致的直观感受。
这条配合间隙在整车开发阶段一直是尺寸工程专业面临的难题。
3.1 行李架与车顶间隙一致性差原因分析某型乘用车行李架与车顶间隙配合长度为3m,数据上间隙名义值1.5mm。
整车装上行李架后,在行李架与车顶间隙配合处均匀取11处位置,测量实际间隙值:行李架与车顶的间隙实测值1.75~4mm,一致性2.25mm。
目视效果差,与现代车企的精品外观质量相违背。
从上面行李架与车顶的安装关系可知,行李架螺栓穿过车顶、安装支架与车身进行紧固连接。
在行李架安装时,泡棉挤压后产生的反弹力使车顶向下发生变形,是整车行李架与车顶间隙差的另一个重要影响因素。
汽车行李箱盖产品结构优化设计分析

汽车行李箱盖产品结构优化设计分析发表时间:2019-09-19T14:27:52.233Z 来源:《建筑细部》2019年第4期作者:罗林[导读] 在汽车行业当中,汽车行李箱盖的开启方式和驱动点的改变会使电动开启的用力过大,所以在汽车行李箱盖开发过程中,要将开启施力值减少到合理的范围,满足行李箱盖电动化的需求,本文就主要对汽车行李箱盖产品结构优化设计进行了分析。
罗林四维尔丸井(广州)汽车零部件有限公司 510530摘要:在汽车行业当中,汽车行李箱盖的开启方式和驱动点的改变会使电动开启的用力过大,所以在汽车行李箱盖开发过程中,要将开启施力值减少到合理的范围,满足行李箱盖电动化的需求,本文就主要对汽车行李箱盖产品结构优化设计进行了分析。
关键词:汽车行李箱盖;产品结构;优化分析目前汽车行李箱盖产品主要是基于纯手动的开关来设计后备箱盖的,要对汽车行李箱盖产品结构进行优化和设计,主要目的就是设计手动开启处的用力较小,而电动开启行李箱盖则是从支撑端施力,驱动行李箱盖整体开启和关闭,所以电动开启行李箱盖的过程相对于手动来说是一个较费力的过程,因此在汽车行李箱盖电动开发过程中要在不影响行李箱位置关系和运动关系的同时,对行李箱盖产品结构进行优化,设计如何增加电驱动端力臂长度,减少阻力。
一、压力边和拉延力的计算1、压边力的选择冲压形成过程中的重要工艺参数之一就是压力边,压力边的选择是否合理影响着该过程是否可能出现缺陷。
首先压边力是能够增强板料拉应力,控制板料的流动,如果压边力不足,将会引起板料的破裂和起皱,通常情况下,当压力边增大时,成形力也会随之增大,并且在一定范围内一直,会对板料的起皱有一定的抑制作用,减少拉力不足的情况,但是如果拉应力过大,则会明显增加板料拉裂的趋势,导致板料产生破裂,过大的压力便会加快模具的损耗,减少模具使用寿命,过小压边力,会导致板料流动不足,形成拉裂或起皱的现象。
所以压边力的选取会受到很多因素的影响,其中拉延件的结构形状,对压边力的选择起着决定性的作用,板料的性能、模具的结构压边力的选择,所以需要通过一些模拟仿真实验,通过一些精细的计算来选取合适的压边力。
出差报告

爱锡出差工作总结:总结在验收过程中发现的问题及改善对策(对策是由双方共同开会决定)1. 所有带深度通止规以及深度规限位圈螺母螺母松动,长度不合适(高低不等)等问题对策:爱锡人员全部排查,同一螺母长度,并且在后续长期使用时不会出现松动现象2. 部分通止规止端的非工作面有粗大刀纹,厂家为打磨后就镀层,影响检具外观的美观对策:爱锡排查所有通止规的非工作面,对于有粗大刀纹的,需重新加工该表面,保证检具的表面美观3. 部分深度规的非触摸面(和工件表面接触的平面)未按图纸要求倒角,容易造成检具的装反的风险对策:根据我的了解虽然日后装反后不会影响检具的使用及尺寸,但是ME图纸是要求有倒角的,所以决定爱锡人员全部根据图纸要求倒角4. 缸体和曲轴检具台上安装电子检具的安放架(尼龙材质)不合适,在拿取检具时有过紧和划手等现象对策:爱锡人员重新调整安防架间距或是打磨到合适间隙5. 缸盖009W010301-01检具AX号与检具编号及尺寸刻反向对策:爱锡爱锡更换手柄,重新刻字6. 缸盖AX18252工件底部有R1圆弧,检具通端未倒角,止端没有刻线。
同样类型的其他三套检具目前还未完成,但请注意同样的问题对策:爱锡更新图纸及检具,同时核查同类型检具如:AX18253,18254,182557. 缸盖AX18258 底面有磕碰,需处理对策:爱锡人员处理8. 缸盖AX18304工件表面的刻字错误,关于型号识别应刻1.6XER 1.8XER而实际一个刻1.6XER 一个刻1.8XER对策:爱锡更新刻字以及图纸(包括安放架标牌)9. 缸体AX18319检具尺寸实刻90°,应为45°10. 缸体AX18320 测头和工件干涉对策:爱锡更改11. 缸体AX18331安防架位置位于检具台第二层隔板下,由于间隙过小,造成拿取不方便对策:爱锡将检具台刚换位置12. 缸体AX18352,AX18347限位档块目前采用三个螺丝把紧的方式,在日常使用中很容易使限位挡块上移对策:爱锡增加尼龙限位圈,防止限位圈往上移动13.缸体AX18347两个带表电子检具挡圈在测量时与工件干涉对策:爱锡打磨挡圈,已经完成14.缸体AX18355止端太短,测量不到工件底孔对策:柄部加长至总长为75mm15.缸体AX18357实刻009W020355错误,应该刻成爱锡更改刻字为009W020346对策:爱锡更改16.缸体AX18373 测量不方便,由于测量孔在缸体腔内,所以无法看清是否合格对策:爱锡重新设计,将该检具分为两个检具(一个触摸规一个通止规)需更新图纸检具刻字以及标牌刻字17.缸体AX18376通端测量与工件干涉,弹簧无法回位对策:改为采用一个普通螺纹通规009W020389A和螺纹止规测量009W020389B 18.缸体AX18377 原检测要求为Φ6±0.25 DP thru ,SGM要求更改为Φ6±0.25 64min对策:爱锡更改19. 曲轴AX18431 工位号实刻为OP190,应为OP230对策:爱锡更改20.曲轴AX18399 AX18401标牌尺寸刻字错误对策:爱锡更改标牌21.曲轴AX18422 检具尺寸刻字错误。
油箱口盖板与后侧围段差问题改进
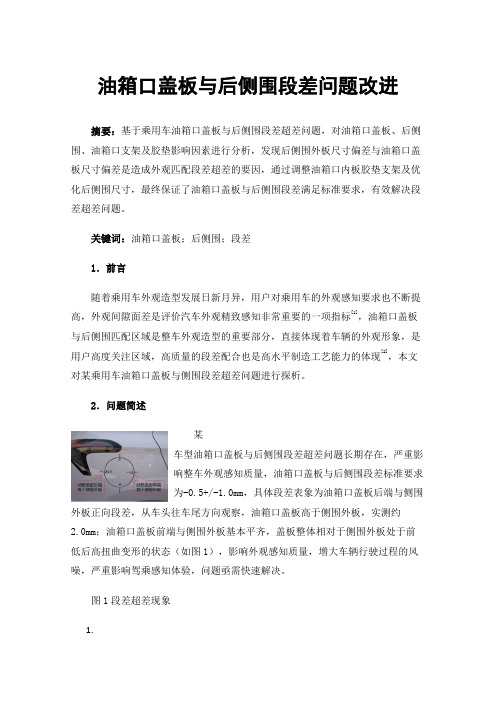
油箱口盖板与后侧围段差问题改进摘要:基于乘用车油箱口盖板与后侧围段差超差问题,对油箱口盖板、后侧围、油箱口支架及胶垫影响因素进行分析,发现后侧围外板尺寸偏差与油箱口盖板尺寸偏差是造成外观匹配段差超差的要因,通过调整油箱口内板胶垫支架及优化后侧围尺寸,最终保证了油箱口盖板与后侧围段差满足标准要求,有效解决段差超差问题。
关键词:油箱口盖板;后侧围;段差1.前言随着乘用车外观造型发展日新月异,用户对乘用车的外观感知要求也不断提高,外观间隙面差是评价汽车外观精致感知非常重要的一项指标[1],油箱口盖板与后侧围匹配区域是整车外观造型的重要部分,直接体现着车辆的外观形象,是用户高度关注区域,高质量的段差配合也是高水平制造工艺能力的体现[2],本文对某乘用车油箱口盖板与侧围段差超差问题进行探析。
2.问题简述某车型油箱口盖板与后侧围段差超差问题长期存在,严重影响整车外观感知质量,油箱口盖板与后侧围段差标准要求为-0.5+/-1.0mm,具体段差表象为油箱口盖板后端与侧围外板正向段差,从车头往车尾方向观察,油箱口盖板高于侧围外板,实测约2.0mm;油箱口盖板前端与侧围外板基本平齐,盖板整体相对于侧围外板处于前低后高扭曲变形的状态(如图1),影响外观感知质量,增大车辆行驶过程的风噪,严重影响驾乘感知体验,问题亟需快速解决。
图1段差超差现象1.影响因素分析根据故障车段差问题表现,发现油箱口盖板与后侧围段差故障点主要体现在油箱口盖板后端与后侧围的配合位置,其他位置段差数据在标准范围值之内。
油箱口盖板与后侧围的段差匹配结构由四个部分组成:侧围外板、油箱口盖板板、加油口支架、胶垫,结合故障车的表象,找到7个末端关联因素:①油箱口盖板尺寸②油箱口支架尺寸③后侧围外板尺寸(油箱口盖板板和支架搭接点)④加油口支架定位⑤油箱口盖板装调操作⑥油箱口盖板胶垫尺寸⑦装配操作过程,针对各个末端潜在影响因素,逐一排查锁定根本原因。
3.1油箱口盖板尺寸分析对油箱口盖板本体零件进行了抽检上检具测量,主要针对油箱口盖板外板表面与检具型面的段差数据进行抽查,线旁不同批次抽检5件油箱口盖板,在检具上选取上图4个测点进行数据测量,油箱口盖板与检具段差标准-0.5-0.5mm(如图2),抽检5件的具体测量数据显示零件外表面尺寸数据正常(如表1),且日常生产的油箱口盖板每件都需要经过该检具进行校准才允许装配。
乘用车尾门外饰板与后侧围段差问题探析

乘用车尾门外饰板与后侧围段差问题探析发布时间:2021-07-02T14:14:33.147Z 来源:《中国科技信息》2021年8月作者:韦帅黄军庆计克榜蓝奇[导读] 基于乘用车尾门外饰板与后侧围段差超差问题,对后侧围、外饰板及尾门进行分析,发现右后侧围位置尺寸偏差与外饰板安装板螺母偏移是造成外观匹配段差超差的要因,通过更换螺母热压头及增加侧围定位工装,最终保证了外饰板与后侧围段差满足检验标准,促进问题有效解决。
上汽通用五菱汽车股份有限公司广西柳州韦帅黄军庆计克榜蓝奇 545007摘要:基于乘用车尾门外饰板与后侧围段差超差问题,对后侧围、外饰板及尾门进行分析,发现右后侧围位置尺寸偏差与外饰板安装板螺母偏移是造成外观匹配段差超差的要因,通过更换螺母热压头及增加侧围定位工装,最终保证了外饰板与后侧围段差满足检验标准,促进问题有效解决。
关键词:段差;外饰板;后侧围1.前言乘用车外观造型发展变化日新月异,用户对乘用车的感知要求也不断提高,尾门与侧围匹配区域作为乘用车整体造型的重要组成部分,直接反映着整车的外观形象,是用户高度关注区域,高质量的车身配合也是制造商高水平工艺控制能力的体现[1],本文对某乘用车尾门外饰板与后侧围段差超差问题进行探析。
2.问题简述某乘用车在生产制造过程中,出现尾门外饰板与后侧围外板段差超差的现象,严重影响整车外观感知,尾门外饰板与后侧围段差标准要求为-2~1mm(如图1),具体段差表象为尾门外饰板与右后侧围外板负段差,尾门外饰板低于右后侧围外板,实测-2.7~-1mm;尾门外饰板与左后侧围外板正段差,从车头往车尾观察,尾门外饰板高于左后侧围外板,实测0.8~3.2mm,右侧属于逆风向段差问题(如图2),车辆行驶过程会产生风切音,增大行驶风噪。
图1段差标准要求图2段差超差表象 3.影响因素分析根据故障车段差超差问题表现模式,发现尾门外饰板与左后侧围外板的段差超差主要集中在外饰板左下角,而与右后侧围外板的段差超差则集中在外饰板的右上角,尾门外饰板呈现出扭曲变形状态。
轿车行李箱盖铰链受力分析及在设计中的应用

轿车行李箱盖铰链受力分析及在设计中的应用行李箱平衡铰链,是指使用弹性元件,可以在行李箱盖开启和关闭时平衡盖重力的铰链结构,因为平衡铰链结构简单、有足够强度和可靠耐久等优点,大部分车型特别是中低档车型,基本上采用这种结构的铰链,其弹性元件采用扭杆。
在行李箱盖使用过程中,一般要求启动开启装置后,能自动弹开一定高度,介在半开(一定的打开角度)状态下要保持静止不动以防落下伤人,同时在最在打开位置时有足够的保持力,以防风力作用下自行落下关闭。
一、轿车行李箱盖平衡铰链的受力分析1、铰链情况介绍:行李箱盖平衡铰链简图如图1所示,图2为左侧铰链的侧视图。
图1 行李箱铰链简图(只装一边扭杆)图2 左侧铰链的左侧视图从图2可以看出,扭杆的运动受铰链支架和联杆的约束,只能绕安装口旋转。
因此,支架、铰链、联杆、扭杆构成了四连杆机构,其中铰链支架为固定杆,其它均可以活动。
图2只为铰链的侧视图,实际零件并不在一个平面内。
但是,把各零件投影到同一个平面内,并不影响受力分析,所以可以把铰链的四连机构看作一个平面四连杆机构来分析。
此平面四连杆机构的受力如图3所示:图3:铰链平面四连杆机构的受力图(数据为设定的)图3中,AD表示铰链支架,AB为扭杆,BC为联杆,CD为铰链,其长度如图所示,而四连杆的之间角度φ1、φ2、φ3和φ4的初始值(即行李箱盖铰链全关时的角度)也已经在图3中表示。
另外,把扭杆的扭矩记为M T,而铰链所受的重力(包含行李箱盖和铰链本身)记为G,但是在分析中,把G换为重力对D点的力矩可能更为方便,因此铰链CD就受到重力矩M G的作用。
显然,M T和M G都为变量,随行李箱铰链的开启角度变化而改变。
2、杆的受力分析:存在摩擦力作用时,BC杆不能视作为一根二力杆,在行李盖向上运动时,BC杆的受力如图4所示。
其中摩擦力作用的效果是一个摩擦力隅。
另外,如果把图4中的摩擦力隅M B和M C定义为正负值,则图4可以用于行李箱盖打开和关闭时的受力。
- 1、下载文档前请自行甄别文档内容的完整性,平台不提供额外的编辑、内容补充、找答案等附加服务。
- 2、"仅部分预览"的文档,不可在线预览部分如存在完整性等问题,可反馈申请退款(可完整预览的文档不适用该条件!)。
- 3、如文档侵犯您的权益,请联系客服反馈,我们会尽快为您处理(人工客服工作时间:9:00-18:30)。
利亚纳A6行李箱盖板组件边缘脱漆真因1侧围外板棱线折弯不到位,导致侧围与行李箱盖板配合间隙过小真因2配门调整不到位,左右间隙不均
待确认
目标:通过质量提升,消除行李箱盖板边缘脱漆现象。
编制: 批准: 审核修订 :
2、把握现状(分解问题)
1、选题理由
3、设定目标
4、把握真因
5、制定对策2.单品精度检查
问题点:
1.完成车侧围与行李箱外板间隙超差(偏小)
2.行李箱盖外板BL 尺寸偏大(符合公差要求)、左右侧围外板棱线BL 尺寸偏小(超差),累积BL 方向偏差
约-2.5mm
3.侧围后段从前住后宽度尺寸递减6、前期效果确认及后序计划小结:1.单品精度影响配合间隙。
行李箱盖板偏大,侧围外板偏小(超差),造成配合间隙过小。
2.焊装配门调整不到位
3.激光跟踪仪到位后,进行总拼夹具精度测量与调整,保证车身一致性
市场售后反馈,利亚纳A6行李箱盖板组件边缘脱漆。
1.严重影响外观质量
2.脱漆部位容易生锈
3.市场隐患大
1.临时对策:①在总装车间进行配门调整,保证行李箱盖左右间隙均匀。
2.永久对策:①侧围整改难度较大,暂不做调整②对行李箱盖板外板包边模进行调整,尺寸走下公差,控制在-0.5~0mm ③焊装配门调整控制,保证行李箱盖与侧围左右间隙均匀①调取2013年03月~2014年04月份CB312白车身测
量数据进行统计分析,具体见工作表4
②侧围后段相对于测量基准整体向右偏移
③从前往后两侧围宽度尺寸有递减趋势
1.工序质量检查
①营业在库车随机抽检30台,合格8台具体见工作表2
②焊装配门线随机抽检20台,合格8台具体见工作表3
③行李箱外板与侧围间隙理论3.5±1.0,实测1.3~3.5mm ,间隙超差(偏小)
①65700-C12A0行李箱盖板组件理论间隙尺寸:3.0±0.5实测L 2.8 R 2.5行李箱外板BL 宽度尺寸偏大约+0.7mm 3.MB 精度分析
2.5mm
2.8mm ①整改效果确认对策前对策后 2.5mm 2.8mm ②64111/511-C1100 右/左侧围外板
理论间隙尺寸:2.0±0.5实测L 1.0~1.5 R 1.2左右侧围棱线BL 方向-1.5~-2.0mm
1.5mm
1.0mm
脱漆间隙4.0间隙2.6。