数控车床丝杠螺距误差的补偿.
数控车床丝杠螺距误差的补偿
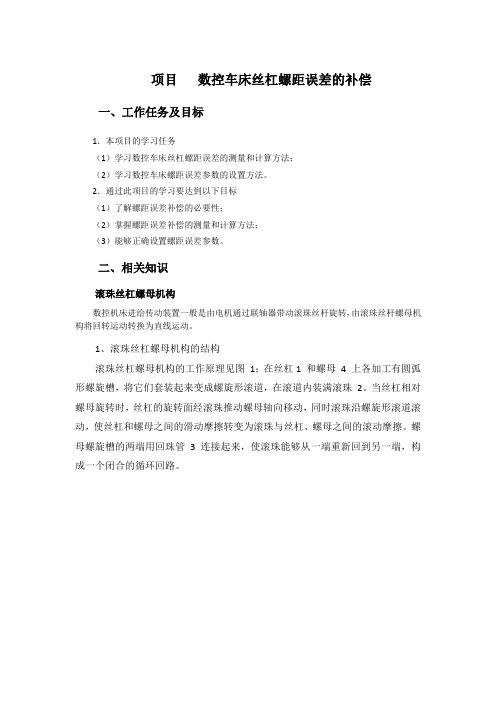
项目数控车床丝杠螺距误差的补偿一、工作任务及目标1.本项目的学习任务(1)学习数控车床丝杠螺距误差的测量和计算方法;(2)学习数控车床螺距误差参数的设置方法。
2.通过此项目的学习要达到以下目标(1)了解螺距误差补偿的必要性;(2)掌握螺距误差补偿的测量和计算方法;(3)能够正确设置螺距误差参数。
二、相关知识滚珠丝杠螺母机构数控机床进给传动装置一般是由电机通过联轴器带动滚珠丝杆旋转,由滚珠丝杆螺母机构将回转运动转换为直线运动。
1、滚珠丝杠螺母机构的结构滚珠丝杠螺母机构的工作原理见图1;在丝杠1 和螺母 4 上各加工有圆弧形螺旋槽,将它们套装起来变成螺旋形滚道,在滚道内装满滚珠2。
当丝杠相对螺母旋转时,丝杠的旋转面经滚珠推动螺母轴向移动,同时滚珠沿螺旋形滚道滚动,使丝杠和螺母之间的滑动摩擦转变为滚珠与丝杠、螺母之间的滚动摩擦。
螺母螺旋槽的两端用回珠管 3 连接起来,使滚珠能够从一端重新回到另一端,构成一个闭合的循环回路。
2、进给传动误差螺距误差:丝杠导程的实际值与理论值的偏差。
例如PⅢ级滚珠丝杠副的螺距公差为0.012mm/300mm。
反向间隙:即丝杠和螺母无相对转动时丝杠和螺母之间的最大窜动。
由于螺母结构本身的游隙以及其受轴向载荷后的弹性变形,滚珠丝杠螺母机构存在轴向间隙,该轴向间隙在丝杠反向转动时表现为丝杠转动α角,而螺母未移动,则形成了反向间隙。
为了保证丝杠和螺母之间的灵活运动,必须有一定的反向间隙。
但反向间隙过大将严重影响机床精度。
因此数控机床进给系统所使用的滚珠丝杠副必须有可靠的轴向间隙调节机构。
图2为常用的双螺母螺纹调隙式结构,它用平键限制了螺母在螺母座内的转动,调整时只要扮动圆螺母就能将滚珠螺母沿轴向移动一定距离,在将反向间隙减小到规定的范围后,将其锁紧。
3、电机与丝杠的联接、传动方式直联:用联轴器将电机轴和丝杠沿轴线联接,其传动比为1:1;该联接方式传动时无间隙;同步带传动:同步带轮固定在电机轴和丝杠上,用同步带传递扭矩;该传动方式传动比由同步带轮齿数比确定,传动平稳,但有传动间隙;齿轮传动:电机通过齿轮或齿轮箱将扭矩传到丝杠,传动比可根据需要确定;该方式传递扭矩大,但有传动间隙。
螺距补偿机理
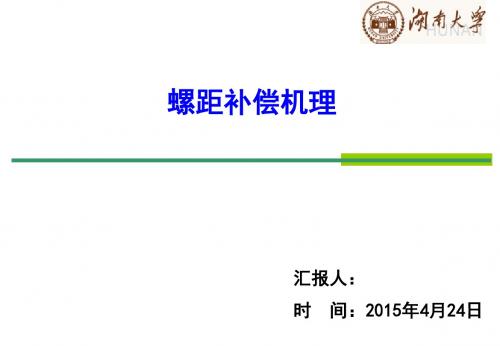
7
二、螺距误差补偿原理
8
二、螺距误差补偿原理
9
二、螺距误差补偿原理
数控系统中设置螺距误差补偿需要NCK(numericcontrol kernel) 的支持,目前可针对某个点把 它的补偿值写入NCK补偿文件。机械零件程序运行 时自动地读取相应补偿文件中各点的补偿数据,并 进行相应的调整,随之产生对应的机械位置变化。
螺距补偿机理
汇报人:
时 间:2015年4月24日
内容提纲
一、螺距误差产 生的原因 二、螺距误差补 偿原理
硬件方法补偿螺 距误差的原理
软件方法补偿螺 距误差原理
单向螺距误差补 偿原理
双向螺距误差补 偿原理
2
一、螺距误差产生的原因
数控机床大都采用滚珠丝杠作为机械传动部件, 电机带动滚珠丝杠,将电机的旋转运动转换为直线运 动。如果滚珠丝杠没有螺距误差,则滚珠丝杠转过的 角度与对应的直线位移存在线性关系。实际上,制造 误差和装配误差始终存在,难以达到理想的螺距精度, 存在螺距误差,其反映在直线位移上也存在一定的误 差,降低了机床的加工精度。
11
二、螺距误差补偿原理
这种断续的脉冲补偿方法给数控机床的 微动开关发出的补偿信号传送给数控装置的电路) 。另外,这种补偿方法比较适用于采用脉冲增量插 补方法、步进电机驱动的开环数控机床,而对于采 用数据采样插补方法、直流或交流伺服电机驱动的 半闭环数控机床,则不适宜。因此,目前,大多数数 控机床补偿滚珠丝杠的螺距误差时均采用软件的方 法。
5
一、螺距误差产生的原因
3. 机床装配过程中,由于丝杠轴线与机床导轨平行 度的误差引起的机床目标值偏差。 螺距误差补偿是将机床实际移动的距离与指令移 动的距离之差,通过调整数控系统的参数增减指令 值的脉冲数,实现机床实际移动距离与指令值相接 近,以提高机床的定位精度。螺距误差补偿只对机 床补偿段起作用,在数控系统允许的范围内补偿将 起到补偿作用。
数控机床螺距误差补偿_杨永

机床经长时间使用后 , 由于磨损 , 精度可能下降 。 通过 该项功能定期测量与补偿 , 可在保持精度的前提下 , 延 长机床使用寿命 。 其补偿原理即将数控机床某轴的指令位置 , 与高 精度测量系统所测得的实际位置相比较 , 计算出在全 行程上的误差 , 并分别绘制出其误差曲线 , 再将该误差 曲线数值化并以表格的形式输入数控系统中 。 1. 2 螺距误差补偿 1. 2. 1 螺距误差补偿步骤 1) 安装高精度位移测量装置 ; 2) 编制简单 程序 , 在整个行程上 , 顺序定位 在一些位置点上 ; 3) 记录运 行到这些点的 实际精确 位置 ; 4) 将 各点处 的误差 标 出 , 形成在不同的指令位 置处的误差表 ; 5) 将该表输 入数控系统 , 按此表进行补偿 。 1. 2. 2 螺距误差补偿举例 图 1 为 X 轴七个点的误差补偿曲线 , 表 1 为输入 数控系统的螺距误差补偿表 。 误差补偿过程中应注意 以下事项 : 1) 对重复定位精度较差的轴 , 因无法准确 确定其误差曲线 , 螺距误差补偿功能无法使用 。 2) 只 有建立机床坐标系后 , 螺距误差补偿才有意义 。 3) 由 31
补偿 点 [ 0] 补偿 点 [ 1] 补偿 点 [ 2] 补偿 点 [ 3] 补偿 点 [ 4] 补偿 点 [ 5]
现代制造工程 2005(11)
数控加工技术
挤出机捏合块数控磨削方法研究
姚海滨 ( 扬州职业大学机械工程系 , 扬州 225009)
摘要 传统的挤出机捏 合块的数学模型在实际运用过程中存在 一些问题 , 不能很 好地保证加 工质量 。 在 分析和 研究捏 合块的磨削机理的基础 上 , 根据在磨削过程中要保证升程曲线连续光滑变化 及相对磨削线速度基本保持不变的要 求 , 从 理论上提出了新的捏合 块磨削控制算法 , 并在实际的加工中得到验证 。 关键词 : 捏合块 数控磨削 软件设计 中图分类号 : TH 16 文献标识码 : A 文章编号 : 1671— 3133(2005)11— 0033— 04
【豆丁-免费】-》数控机床螺距误差补偿与分析

文章编号:1001-2265(2010)02-0098-04收稿日期:2009-09-29;修回日期:2009-10-26作者简介:李继中(1963—),男,湖南人,深圳职业技术学院高级工程师,副处长,从事数控技术研究,(E -mail )ljizhong@szp t .edu .cn 。
数控机床螺距误差补偿与分析李继中(深圳职业技术学院,深圳 518055)摘要:文章通过实例介绍数控机床滚珠丝杆传动机构的螺距误差的测量、补偿依据、补偿方法与操作要点,以及补偿效果的验证与分析。
通过利用英国REN I SHAW 公司的ML10激光干涉仪对F ANUC 0i 系统数控铣床X 轴的螺距误差进行测量、补偿及验证,结果说明,对滚珠丝杆传动机构的反向偏差与螺距误差进行补偿是提高机床精度的一种重要手段。
关键词:滚珠丝杆;螺距误差;反向偏差;补偿;定位精度;激光干涉仪中图分类号:TH16;TG65 文献标识码:AThe Com pen s a ti on and Ana lysis of P itch Error for NC M ach i n i n g ToolsL I J i 2zhong(Shenzhen Polytechnic,Shenzhen 518055,China )Abstract:22、’2Key words:0 引言目前,机床的传动机构一般均为滚珠丝杆副。
当机床几何精度得到保证后,机床轴线的反向偏差与滚珠丝杆的螺距误差是影响机床定位精度与重复定位精度的主要因素,对机床轴线的反向偏差、滚珠丝杆的螺距误差进行补偿能极大地提高机床精度,机床控制系统也对这个两个补偿参量设置了专门的参数,供轴线误差补偿之用,并将其补偿功能作为控制系统的基本控制功能。
1 螺距误差的补偿方式由于加工设备的精度及加工条件的变化影响,滚珠丝杆都存在螺距误差。
螺距误差补偿对开环控制系统和半闭环控制系统具有显著的效果,可明显提高系统的定位精度和重复定位精度;对于全闭环控制系统,由于其控制精度高,螺距误差补偿效果不突出,但也可以进行螺距误差补偿,以便提高控制系统的动态特性,缩短机床的调试时间。
数控车床丝杠螺距误差的补偿
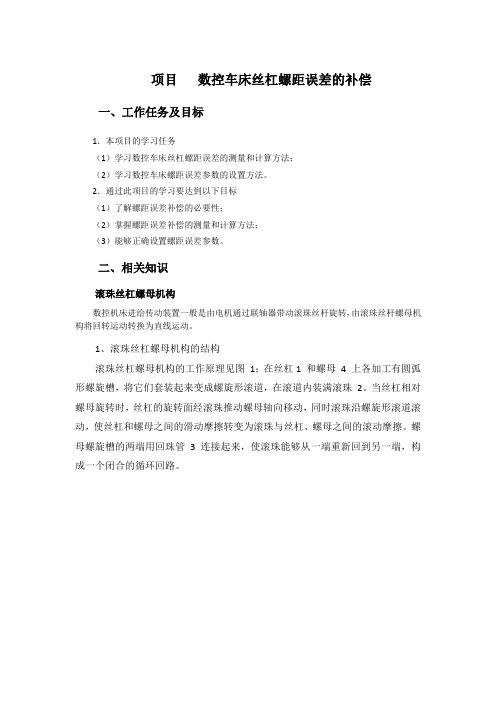
项目数控车床丝杠螺距误差的补偿一、工作任务及目标1.本项目的学习任务(1)学习数控车床丝杠螺距误差的测量和计算方法;(2)学习数控车床螺距误差参数的设置方法。
2.通过此项目的学习要达到以下目标(1)了解螺距误差补偿的必要性;(2)掌握螺距误差补偿的测量和计算方法;(3)能够正确设置螺距误差参数。
二、相关知识滚珠丝杠螺母机构数控机床进给传动装置一般是由电机通过联轴器带动滚珠丝杆旋转,由滚珠丝杆螺母机构将回转运动转换为直线运动。
1、滚珠丝杠螺母机构的结构滚珠丝杠螺母机构的工作原理见图1;在丝杠1 和螺母 4 上各加工有圆弧形螺旋槽,将它们套装起来变成螺旋形滚道,在滚道内装满滚珠2。
当丝杠相对螺母旋转时,丝杠的旋转面经滚珠推动螺母轴向移动,同时滚珠沿螺旋形滚道滚动,使丝杠和螺母之间的滑动摩擦转变为滚珠与丝杠、螺母之间的滚动摩擦。
螺母螺旋槽的两端用回珠管 3 连接起来,使滚珠能够从一端重新回到另一端,构成一个闭合的循环回路。
2、进给传动误差螺距误差:丝杠导程的实际值与理论值的偏差。
例如PⅢ级滚珠丝杠副的螺距公差为0.012mm/300mm。
反向间隙:即丝杠和螺母无相对转动时丝杠和螺母之间的最大窜动。
由于螺母结构本身的游隙以及其受轴向载荷后的弹性变形,滚珠丝杠螺母机构存在轴向间隙,该轴向间隙在丝杠反向转动时表现为丝杠转动α角,而螺母未移动,则形成了反向间隙。
为了保证丝杠和螺母之间的灵活运动,必须有一定的反向间隙。
但反向间隙过大将严重影响机床精度。
因此数控机床进给系统所使用的滚珠丝杠副必须有可靠的轴向间隙调节机构。
图2为常用的双螺母螺纹调隙式结构,它用平键限制了螺母在螺母座内的转动,调整时只要扮动圆螺母就能将滚珠螺母沿轴向移动一定距离,在将反向间隙减小到规定的范围后,将其锁紧。
3、电机与丝杠的联接、传动方式直联:用联轴器将电机轴和丝杠沿轴线联接,其传动比为1:1;该联接方式传动时无间隙;同步带传动:同步带轮固定在电机轴和丝杠上,用同步带传递扭矩;该传动方式传动比由同步带轮齿数比确定,传动平稳,但有传动间隙;齿轮传动:电机通过齿轮或齿轮箱将扭矩传到丝杠,传动比可根据需要确定;该方式传递扭矩大,但有传动间隙。
螺距补偿机理

3
一、螺距误差产生的原因
利用数控系统提供的螺距误差补偿功能,可以 对螺距误差进行补偿和修正,达到提高加工精度的 目的。另外,数控机床经长时间使用后,由于磨损 等原因造成精度下降,通过对机床进行周期检定和 误差补偿,可在保持精度的前提下延长机床的使用 寿命。
4
一、螺距误差产生的原因
数控机床的螺距误差产生原因如下: 1. 滚珠丝杠副处在进给系统传动链的末级。由于丝 杠和螺母存在各种误差,如螺距累积误差、螺纹滚 道型面误差、直径尺寸误差等(其中最主要的是丝 杠的螺距累积误差造成的机床目标值偏差); 2. 滚珠丝杠的装配过程中,由于采用了双支撑结, 使丝杠轴向拉长,造成丝杠螺距误差增加,产生机 床目标值偏差;
22
23
谢谢!
24
13
二、螺距误差补偿原理
距补偿误差表中计算出实际的补偿值,对指令位置 进行补偿,产生实际输出值控制伺服电机。如图3 所示,数控系统以机床零点为基准,在不同的指令 位置,按补偿表中的误差值进行补偿。数控系统在 每段数据插补过程中均进行误差补偿,以获得最高 精度。
14
二、螺距误差补偿原理
实现过程和步骤如下 :
7
二、螺距误差补偿原理
8
二、螺距误差补偿原理
9
二、螺距误差补偿原理
数控系统中设置螺距误差补偿需要NCK(numericcontrol kernel) 的支持,目前可针对某个点把 它的补偿值写入NCK补偿文件。机械零件程序运行 时自动地读取相应补偿文件中各点的补偿数据,并 进行相应的调整,随之产生对应的机械
2.3软件方法螺距误差补偿原理 采用定点的脉冲补偿方法可修正螺距误差,提 高定位精度。其原理是在各坐标轴上设定一些坐标 点,当机床经这些点时,数控系统根据事先测定的 补偿值进行补偿。补偿所需参数如:①各补偿轴起 、终点机床坐标(以机床零点为基准);②补偿间 隔或等分段数;③每段补偿间隔对应补偿值。 将测出的误差值输入到螺距补偿误差表中。当 工作台移动时,系统根据当前位置和指令位置在螺
数控机床的螺距误差检测及补偿

包括导轨副、滚珠丝杠副、联轴节、台面
等精度,只有这些基础精度保证质量,重
复定位精度达到要求后才能谈及误差补偿 的问题,否则会造成紊乱。
图 3 数控机床定位误差曲线
表 1 实验数据记录与数据处理结果
机床型号
测试坐标
机床编号 实
目标点
98021101
0
测试温度
1
2
目标位置(mm)
0
10
20
验
趋近方向
↑↓↑↓↑↓
记 目标 位置
录 偏差 μm
数
1 10 5 8 5 10 7
2
827296
3
524277
4
6 4 6 3 10 5
5
625266
据 平均位置偏差
处
μm
7
3
6 2.8 8.4 6.2
理
X 25℃
…… …… …… …… …… …… …… ……
…
…
测试员
王春海
测试日期
2005.5.22
98
99
100
980
位置偏差反向叠加到数控系统的插补指令上,如 图 1 所示;指令要求该坐标轴运动到目标位置 Pi,目标实际的运动位置是 Pij,由于该点的实际
平均位置偏差为 xi ↑和 xi ↓;将该值填入数控系
统的螺距误差补偿表中,则数控系统在计算时会
图 1 螺距误差补偿原理
自动将目标位置的平均位置偏差叠加到插补指令上,实际的位置是:Pij↑=Pi+ xi ↑和 Pij↓
数控机床的螺距误差检测及补偿
王春海 张增良
(北华航天工业学院机械工程系,河北 廊坊 065000)
摘要 关键词
数控机床传动精度的补偿
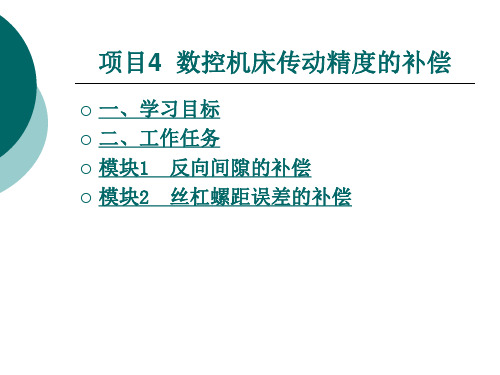
模块1 反向间隙的补偿
(2)用MDI方式将机床移动到测量点位置,如G91 GO1 X-100 F200。
(3)安装百分表,将百分表的刻度调整到0的位置。 (4)用切削进给速度使机床沿相同方向再移动一定距离,如
G91 GO1 X-100 F200。 (5)用相同的切削进给速度从当前点返回到测量点,如G91
上一页 下一页 返回
模块1 反向间隙的补偿
● 2.SIEMENS系统 在SIEMENS 802D中反向间隙的参数为MD32450,将
测得的值A设定到MD32450即可。
四、相关理论知识
(一)传动间隙的来源 传动间隙一般指反向间隙,在数控机床上,由于各坐标轴进
给传动链上驱动部件(如伺服电动机、伺服液压电动机和步进 电动机等)的反向死区、各机械运动传动副的反向间隙等误差 的存在,造成各坐标轴在由正向运动转为反向运动时形成传 动误差,通常也称反向间隙或失动量。
上一页 下一页 返回
模块1 反向间隙的补偿
对于采用半闭环伺服系统的数控机床,反向偏差的存在就会 影响到机床的定位精度和重复定位精度,从而影响产品的加 工精度。如在G01切削运动时,反向偏差会影响插补运动的 精度,若偏差过大就会造成“圆不够圆,方不够方”的情形; 而在G00快速定位运动中,反向偏差影响机床的定位精度, 使得钻孔、撞孔等孔加工时各孔间的位置精度降低。同时, 随着设备投入运行时间的增长,反向偏差还会随因磨损造成 运动副间隙的逐渐增大而增加,因此需要定期对机床各坐标 轴的反向偏差进行测定和补偿。
上一页 下一页 返回
模块1 反向间隙的补偿
(二)反向偏差的测定 反向偏差的测定方法:在所测量坐标轴的行程内,预先向正
向或反向移动一个距离,并以此停止位置为基准,再在同一 方向给予一定移动指令值,使之移动一段距离,然后再往相 反方向移动相同的距离,测量停止位置与基准位置之差。求 出各个位置上的平均值,以所得平均值中的最大值为反向偏 差测量值。在测量时一定要先移动一段距离,否则不能得到 正确的反向偏差值。 测量直线运动轴的反向偏差时,测量工具通常采有千分表或 百分表。若条件允许,可使用双频激光干涉仪进行测量。
螺距误差测定及补偿 电子教材

螺距误差测定及补偿任务内容螺距误差补偿原理VDF850加工中心螺距误差补偿数控机床以其高效高精度,正在机械制造企业中广泛应用。
目前数控机床的传动机构一般采用传动精度较高的滚珠丝杠,滚珠丝杠在生产制造时由于加工设备的精度和加工条件的变化,丝杠和螺母之间存在着误差,如螺距的轴向误差、螺纹滚道的形状误差、直径误差等。
滚珠丝杠在数控机床上进行装配时,由于采用双支撑结构,使丝杠工作载荷较大时轴向尺寸发生变化造成其螺距误差增大。
滚珠丝杠产生的传动误差在全闭环数控机床中由于检测原件(如光栅尺)检测的是机床运动部件的实际位移,将不会对机床加工精度造成影响;而对于工厂中大量使用的半闭环数控机床而言,丝杠、齿形带等机械传动造成的误差不在反馈原件检测范围内,因此若不对此类误差进行适当修正和补偿,势必影响数控机床的定位精度,造成加工质量的不稳定。
要得到高的运动精度和良好的加工质量,必须采用螺距误差补偿功能,精确测量出丝杠不同位置的误差值,利用数控系统对螺距误差进行自动补偿与修正[1]。
另外,数控机床经过长期使用,由于丝杠磨损,运动精度也会下降。
采用该功能定期检测与补偿,可以延长数控机床的使用寿命,保证加工精度。
一、螺距误差补偿原理螺距误差补偿的基本原理是在某进给轴上利用高精度位置检测仪器所测良出的位置(可作为理论位置用)与机床实际运动位置进行比较,计算出该轴全行程上的误差曲线,并将不同位置的误差值输入数控系统中。
机床在经过补偿的轴上运动时,数控系统会根据该位置的补偿数据,自动对该轴的不同位置进行误差补偿,从而减小或消除该轴该位置的定位误差。
螺距误差补偿分单向和双向补偿两种,单向补偿为补偿轴正反向移动时采用相同的数据补偿;而双向补偿为进给轴正反移动时采用不同的数据进行补偿。
由于数控机床丝杠装配时有多种反向间隙消减措施,而且大部分数控机床除了能够进行螺距误差补偿外,还可以进行反向间隙补偿,所以通常仅采用单向螺距误差补偿。
进行螺距误差补偿时应该注意的几个问题:(1)螺距误差补偿仅对定位精度进行补偿,而对重复定位精度无法补偿,而且对于重复定位精度较低的运动轴,由于无法准确确定某点位置误差,因此螺距误差补偿将不会起到预期目的。
数控机床螺距误差测量与补偿
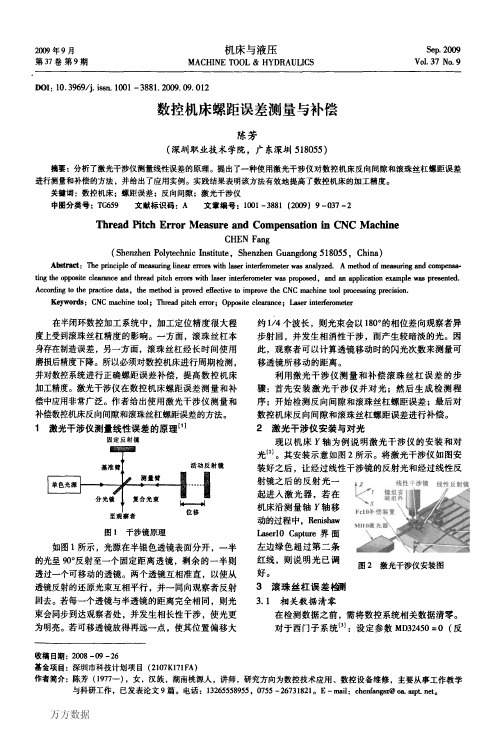
2 辩枷除。岬.鑫、
O ■
看.2
群-4 .6 .8 轴线何置,m“ (b)补偿之后的螺距误差
图3补偿前后螺距误差对比图
(下转第53页)
第9期
李勇勇等:超声辅助电火花沉积装备的设计
·53·
可以降低应力集中。在截面突变处加适当的圆弧过 渡,不仅可以降低应力集中,而且可以使实际谐振频 率恢复到计算值,这一过渡圆弧称为最佳过渡圆弧, 其过渡圆弧半径可以从图4中求取。计算过程如下:
对于FANUC系统,设定下列参数: No.3621=0(各轴负方向最远一端的螺距误差 补偿点的号码); No.3622=20(各轴正方向最远一端的螺距误差 补偿点的号码); No.3620=O(各轴参考点的螺距误差补偿点号码); No.3624=30000(补偿点的间隔); No.3623=0(补偿的倍率); No.1851=26(各轴的反向间隙补偿量); 并将增量值的滚珠丝杠螺距误差输入到系统中。 4.2补偿结果分析
关键词:数控机床;螺距误差;反向间隙;激光干涉仪 中图分类号:TC,659 文献标识码:A 文章编号:1001—3881(2009)9—037—2
Thread Pitch Error Measure and Compensation in CNC Machine
CHEN Fang
(Shenzhen Polytechnic Institute,Shenzhen Guangdong 518055,China)
固定反射镜
基准臂
活矧 射镜
I
.
≥.Mil.1
豳
:复二光主L I 7∥ 分光镜
图1干涉镜原理
如图1所示,光源在半银色透镜表面分开,一半 的光呈90。反射至一个固定距离透镜,剩余的一半则 透过一个可移动的透镜。两个透镜互相准直,以使从 透镜反射的还原光束互相平行,并一同向观察者反射 回去。若每一个透镜与半透镜的距离完全相同,则光 束会同步到达观察者处,并发生相长性干涉,使光更 为明亮。若可移透镜放得再远一点,使其位置偏移大
数控机床定位精度的补偿方法

数控机床定位精度的补偿方法螺距误差补偿这项工作应该是在机床几何精度(床身水平、平行度、垂直度等)调整完成后进行的,这样可以尽量减少几何精度对定位精度的影响。
另外,进行螺距误差补偿时应使用高精度的检测仪器(如激光干涉仪),这样可以先测量再补偿,补偿后再测量,并按照相应的分析标准(如VDI3441、JIS6330、GB10931-89等)对测量数据进行分析,直到达到机床对定位精度的要求范围。
机床的螺距误差补偿功能包括线性轴和旋转轴两种方式,分别可以对直线轴和旋转工作台的定位精度进行补偿。
但有一点需要注意,就是在补偿旋转轴时应注意:在0°~360°之间各补偿点的补偿值总和应为0,以使0°和360°的绝对位置保持一致,否则旋转轴旋转角度每超过360°一次,就产生一次累积误差,从而影响机床的加工精度。
另外,螺距误差补偿功能的实现方法又有增量型和绝对型之分。
所谓补偿就是指通过特定方法对机床的控制参数进行调整,其参数调整方法也依各数控系统不同而各有差异。
所谓增量型是指以被补偿轴上相领两上补偿点间的误差差值为依据来进行补偿,而绝对型是指以被补偿轴上各个补偿点的绝对误差值为依据来进行补偿。
FANUC-0数控系统的螺距误差补偿功能是一种增量型补偿方法,FANUC-0数控系统与螺距误差补偿功能有关的参数如下:765432100011 PML2PML1765432107011 PML2SPML1SPML2和PML1的组合决定误差补偿倍率,它对X、Y、Z和第四轴有效。
PML2S和PML1S的含义与PML2和PML1相同,它对第5、第6轴有效。
设定的补偿值乘以此倍率即为应补偿的误差值。
PML2(S) PML1(S) 补偿倍率1 0 ×10 1 ×21 0 ×41 1 ×80535 BKLX0536 BKLY0537 BKLZ0538 BKL47535 BKL57536 BKL67537 BKL77538 BKL8BKLX、BKLY、BKLZ,BKL4~BKL8依次为X、Y、Z和第4~第8轴的反向间隙补偿量,其设定范围为0~2550(检测单位)0712 PRSX0713 PRSY0714 PRSZ0715 PRS47713 PRS57714 PRS6PRSX、PRSY、PRSZ和PRS4~PRS6依次为X、Y、Z和第4~第6轴的各螺距误差补偿点间的距离。
螺距误差补偿

一、螺距误差产生原因
①滚珠丝杆副处在进给系统传动链的末级,丝杆和螺母存在各种误差,如螺距累积误差、螺纹滚道型面误差、直径尺寸误差等,其中丝杆的螺距累积误差会造成机床目标值偏差。
②滚珠丝杆在装配过程中,由于采用了双支承结构,使丝杆轴向拉长,造成丝杆螺距误差增加,产生机床目标值偏差。
③在机床装配过程中,丝杆轴线与机床导轨平行度的误差会引起机床目标值偏差。
二、螺距误差补偿的作用
螺距误差补偿通过调整数控系统的参数增减指令值的脉冲数,实现机床实际距离与指令移动距离相接近,以提高机床的定位精度。
螺距误差补偿只对机床补偿段起作用,在数控系统允许的范围内起到补偿作用。
数控设备丝杠齿轮间隙及螺距误差补偿_肖乃宽 (1)

数控设备丝杠齿轮间隙及螺距误差补偿
彩虹集团公司 肖乃宽
随着数控设备使用时间的延长 , 丝杠齿轮间隙 及螺距误差也会因使用情况发生较大的变化 。为了 延长设备的使用寿命 , 保持(或提高)数控设备的加 工精度 , 定期对设备进行精度检测并对数控设备进 行齿隙及螺距误差补偿 , 已成为加强设备后期管理 的重要手段之一 。
0 :参考点返回方向和齿隙补偿方向为正方向 ; 1 :参考点返回方向和齿隙补偿方向为负方向 。 2 .PML1 , PML2 :螺距误差补偿倍率(使用于所有 轴)。 真值表如表 1 所示 。
表 1 真值表
PML1 0 0 1 1
PML2 0 1 0 1
倍率
×1 ×2 ×4 ×8
3 .BKLX 、BKLY 、BKLZ 、BKL4 :齿隙补偿量 , 设定范 围 :0 ~ 255 。
成都机床电器研究所
喜获全国机械工业文明单位称号
成都机床电器研究所全体职工近几年来 在蒋宣岱 所长的带 领下 , 内抓管理 , 外拓市 场 , 紧抓两个文明的建设 , 连年来取得了稳定 持续的发展 , 物质文明和精神文明都取得了 较好的成绩 。 经中国机械工业联合会全国机 械工业文明单位评选表彰领导小组及会长办 公会审定 , 成都机床电器研究所被评为全国 机械工业文明单位 。
E -0.00 2 0.005 0.008
F =D -C 0.000 0.006 0.008
G=E -C -0.002 0.004 0.006
H =(F +G)/ 2 -0.001 0.005 0.007
I =H/ X -1
5 7
J =ROUND(I) -1
5 7
N
08实验八 丝杆螺距误差补偿

例如:X 轴总行程为-400mm~+100mm,以参考点为准,每 50mm 为一间隔等距检测点
来测量螺距误差值!
①、直线光栅尺安装到位,数显表安装到位,通过数显表显示记录数据
②、按要求在数控系统中编制测量程序如下:
N01 G90 G00 X0
N16 G04 P5
N02 G04 P5
N17 X-400
入下表中:
测量点 -400~-350 -350~-300 -300~-250 -250~-200 -200~-150
定位值
理论值
误差值
补偿点号
测量点 -150~-100 -100~-50 -50~0
0~+50 +50~+100
定位值
理论值
误差值
补偿点号
将定位值、理论值和误差值填完此表,用直线光栅尺检测丝杆螺距误差任务完成。
螺距误差补偿原理是将机械参考点返回后的位置作为螺距补偿原点,CNC 系统以设定 在螺距误差补偿参数中的螺距补偿量和 CNC 移动指令,综合控制伺服轴的移动量,补偿丝 杠的螺距误差。
螺距误差补偿使用的参数通常有:参考点的补偿点号、负方向最远端的补偿点号、 正方向最远端的补偿点号、补偿点的间隔等等。
螺距误差补偿功能提供了一种补偿方案,要求我们将所检测出的螺距误差值,按照 一定的方法,输入到数控系统中相对应的上述参数中即可。而在螺距误差补偿过程中最 重要的设备就是激光干涉仪,在补偿前通过它测量出丝杆螺距误差,在补偿后通过它来 测量并验证丝杆螺距误差的补偿效果。
距误差补偿画面,再根据补偿点号,将其对应的误差值输入系统中,参数设定完成!
②、为使参数生效,系统关机重起。
3、验证补偿结果
机床断电后重新启动,回参考点后,螺距补偿生效,重复步骤二,再检测定位精度,
螺距补偿机理

二、螺距误差补偿原理
当刀具从终点向起点反向运动,途中反向地经过10 点;假如从20点向10点实际移动了9mm,与预期移动 距离10的偏差是10-9 =1mm,但是由于从终点到起 点是反方向,所以10点在反方向上的补偿是-1mm; 假如实际移动距离为11mm,与预期移动距离10的偏 差是10-11=-1mm,但是由于从终点到起点是反 方向,所以10这个点在反方向上的补偿是1mm其他 各点正方向和反方向上的补偿依此类推。
3
一、螺距误差产生的原因
利用数控系统提供的螺距误差补偿功能,可以 对螺距误差进行补偿和修正,达到提高加工精度的 目的。另外,数控机床经长时间使用后,由于磨损 等原因造成精度下降,通过对机床进行周期检定和 误差补偿,可在保持精度的前提下延长机床的使用 寿命。
4
一、螺距误差产生的原因
数控机床的螺距误差产生原因如下: 1. 滚珠丝杠副处在进给系统传动链的末级。由于丝 杠和螺母存在各种误差,如螺距累积误差、螺纹滚 道型面误差、直径尺寸误差等(其中最主要的是丝 杠的螺距累积误差造成的机床目标值偏差); 2. 滚珠丝杠的装配过程中,由于采用了双支撑结, 使丝杠轴向拉长,造成丝杠螺距误差增加,产生机 床目标值偏差;
5
一、螺距误差产生的原因
3. 机床装配过程中,由于丝杠轴线与机床导轨平行 度的误差引起的机床目标值偏差。 螺距误差补偿是将机床实际移动的距离与指令移 动的距离之差,通过调整数控系统的参数增减指令 值的脉冲数,实现机床实际移动距离与指令值相接 近,以提高机床的定位精度。螺距误差补偿只对机 床补偿段起作用,在数控系统允许的范围内补偿将 起到补偿作用。
20
螺距误差补偿是按轴进行的。针对每一个轴可以设 置每个轴的螺距误差补偿。主轴不设置。
单元设计_丝杠螺距误差补偿及反向间隙补偿调试.

操作、讨论
45mim
归纳
总结
点评任务完成情况
启发
相关机电设备图片、P精度调试的主要内容(课内)
2.了解其他典型机电设备精度调试的相关内容(课外)
课后
体会
总结学生学习情况,进一步提高教学效果。
引导学生搜集资料分析要求十字工作台ppt文档听课回答10mi知识深化丝杠螺距误差和反向间隙补偿方法讲课图片ppt文档听课25mi操作训练按控制要求进行丝杠螺距误差补偿及反向间隙补偿组操作ppt文档操作讨论45mim归纳总结点评任务完成情况启发相关机电设图片ppt文档听课10mim作业1
南京工业职业技术学院
单元教学设计方案
课程名称
机电一体化自动机械仿真学习包
教学单元名称
丝杠螺距误差补偿及反向间隙补偿调试
本单元学时数
2
课程教学团队
丁加军、陈涛
学习目标分析
能力目标:看图片、课件、文档等分析十字工作台手动调试的过程
知识目标:1.丝杠螺距误差和反向间隙概念
2. 丝杠螺距误差和反向间隙补偿方法
学习者分析
有了机械设计基础、机械制造基础、机械制图、机电控制系统、机床数控技术应用等课程为本项目学习打下了良好的基础。
学习內容分析
知识点:1.丝杠螺距误差和反向间隙概念
2. 丝杠螺距误差和反向间隙补偿方法
能力:1.理解丝杠螺距误差和反向间隙概念
2. 丝杠螺距误差和反向间隙补偿调试
学习深度:了解其他典型机电设备的精度调试内容
学习载体:十字工作台装调系统
学习情景:十字工作台装调综合实训室
教学策略
课前公告学生本单元流程,事先分4组,课前预习,先观摩后知识深化
学生活动
- 1、下载文档前请自行甄别文档内容的完整性,平台不提供额外的编辑、内容补充、找答案等附加服务。
- 2、"仅部分预览"的文档,不可在线预览部分如存在完整性等问题,可反馈申请退款(可完整预览的文档不适用该条件!)。
- 3、如文档侵犯您的权益,请联系客服反馈,我们会尽快为您处理(人工客服工作时间:9:00-18:30)。
项目数控车床丝杠螺距误差的补偿
一、工作任务及目标
1.本项目的学习任务
(1)学习数控车床丝杠螺距误差的测量和计算方法;
(2)学习数控车床螺距误差参数的设置方法。
2.通过此项目的学习要达到以下目标
(1)了解螺距误差补偿的必要性;
(2)掌握螺距误差补偿的测量和计算方法;
(3)能够正确设置螺距误差参数。
二、相关知识
滚珠丝杠螺母机构
数控机床进给传动装置一般是由电机通过联轴器带动滚珠丝杆旋转,由滚珠丝杆螺母机构将回转运动转换为直线运动。
1、滚珠丝杠螺母机构的结构
滚珠丝杠螺母机构的工作原理见图 1;在丝杠1 和螺母 4 上各加工有圆弧形螺旋槽,将它们套装起来变成螺旋形滚道,在滚道内装满滚珠 2。
当丝杠相对螺母旋转时,丝杠的旋转面经滚珠推动螺母轴向移动,同时滚珠沿螺旋形滚道滚动,使丝杠和螺母之间的滑动摩擦转变为滚珠与丝杠、螺母之间的滚动摩擦。
螺母螺旋槽的两端用回珠管 3 连接起来,使滚珠能够从一端重新回到另一端,构成一个闭合的循环回路。
2、进给传动误差
螺距误差:丝杠导程的实际值与理论值的偏差。
例如 PⅢ级滚珠丝杠副的螺距公差为 0.012mm/300mm。
反向间隙:即丝杠和螺母无相对转动时丝杠和螺母之间的最大窜动。
由于螺母
结构本身的游隙以及其受轴向载荷后的弹性变形,滚珠丝杠螺母机构存在轴向间隙,该轴向间隙在丝杠反向转动时表现为丝杠转动α角,而螺母未移动,则形成了反向间隙。
为了保证丝杠和螺母之间的灵活运动,必须有一定的反向间隙。
但反向间隙过大将严重影响机床精度。
因此数控机床进给系统所使用的滚珠丝杠副必须有可靠的轴向间隙调节机构。
图2为常用的双螺母螺纹调隙式结构,它
用平键限制了螺母在螺母座内的转动,调整时只要扮动圆螺母就能将滚珠螺母沿轴向移动一定距离,在将反向间隙减小到规定的范围后,将其锁紧。
3、电机与丝杠的联接、传动方式
直联:用联轴器将电机轴和丝杠沿轴线联接,其传动比为 1:1;该联接方式传动时无间隙;
同步带传动:同步带轮固定在电机轴和丝杠上,用同步带传递扭矩;该传动方式传动比由同步带轮齿数比确定,传动平稳,但有传动间隙;
齿轮传动:电机通过齿轮或齿轮箱将扭矩传到丝杠,传动比可根据需要确定;该方式传递扭矩大,但有传动间隙。
同步带传动、齿轮传动中的间隙是产生数控机床反向间隙差值的原因之一。
三、数控系统的半闭环控制
开环数控系统没有位置测量装置,信号流是单向的(数控装置到进给系统)。
故系统结构简单,但由于无位置反馈,机床的控制精度低,容易丢步。
适用于经济型数控机床
半闭环数控系统是在驱动装置(常用伺服电机)或丝杠上安装旋转编码器,采样旋转角度进行位置反馈,因此,其结构简单,不会丢步。
但由于不是直接检测运动部件的实际移动位置,机床进给传动链的反向间隙误差和丝杠螺距误差仍然会影响机床的精度。
适用于普及型(中档)数控机床。
全闭环数控系统通过光栅尺,直接对运动部件的实际移动位置进行检测,消除了机床进给传动链的反向间隙误差和丝杠螺距误差对机床精度的影响。
因此其控制精度高,但结构复杂,成本高,易形成振荡,调试周期长。
适用于高档高精度数控机床。
5.1螺距补偿原理
数控机床软件补偿的基本原理是在机床
的机床坐标系中,在无补偿的条件下,在轴
线测量行程内将测量行程等分为若干段,测
量出各目标位置P;的平均位置偏差x;
把平均位置偏差反向叠加到数控系统的插
补指令上,如下图8所示,指令要求沿X轴运动到目标位置P;,目标实际位置为P }.i,该点的平均位置偏差为x,个;将该值输入系统,则系统CNC在计算时自动将目标位置P;的平均位置偏差x,个叠加到插补指令上,实际运动位置
为:P}.i=P.+ x; 使误差部分抵消,实现误差的补偿。
螺距误差可进行单向和双向补偿。
5.2反向间隙补偿
反向间隙补偿又称为齿隙补偿。
机械传动
链在改变转向时,由十反向间隙的存在,会引
起伺服电机的空转,}fU无工作台的实际运动,
又称失动。
反向间隙补偿原理是在无补偿的条件下,在轴线测量行程内将测量行程等分为若干段,测量出各目标位置P;的平均反向差值B,作为机床的补偿参数输入系统。
CNC系统在控制坐标轴反向运动时,自动先让该坐标反向运动B 值,然后按指令进行运动。
如图9所示,工作台正向移动到O点,然后反向移动到P;点,反向时,电机(丝杆)先反向移动B,后移动到Pi点;该过程CNC系统实际指令运
动值L为:L=P;+ B
反向间隙补偿在坐标轴处十任何方式时均有效。
在系统进行了双向螺距补偿
时,双向螺距补偿的值已经包含了反向间隙,因此,此时不需设置反向间隙的补偿值。
5.3误差补偿的适用范围
从数控机床进给传动装置的结构和数控系统的二种控制方法可知,误差补偿对
半闭环控制系统和开环控制系统具有显著的效果,可明显提高数控机床的定位精度和I重复定位精度。
对全闭环数控系统,由十其控制精度高,采用误差补偿的效果不显著,但也可进行误差补偿。
(一)丝杠螺距误差补偿的必要性
数控机床的直线轴精度表现在进给轴上主要有三项精度:反向间隙、定位精度和重复定位精度,其中反向间隙、重复定位精度可以通过机械装置的调整来实现,而定位精度在很大程度上取决于直线轴传动链中滚珠丝杠的螺距制造精度。
在数控车床生产制造及加工应用中,在调整好机床反向间隙、重复定位精度后,要减小定位误差,用数控系统的螺距误差螺距补偿功能是最节约成本且直接有效的方法。
由于滚珠丝杠副在加工和安装过程中存在误差,因此滚珠丝杠副将回转运动转换为直线运动时存在以下两种误差。
①螺距误差,即丝杠导程的实际值与理论值的偏差②反向间隙,即丝杠和螺母无相对转动时,丝杠和螺母之间的最大窜动。
定位精度的测量仪器可以用激光干涉仪、线纹尺、光栅尺数显表和步距规。
(二)反向间隙补偿
1.步骤一:设定参数
1800
2.步骤二:测量反向间隙值
(1)回参考点
(2)用切削进给使机床移动到测量点
指令:G01 X100.0 F300;
(3)安装百分表,将刻度对
(4)用切削进给,使机床沿相同方向移动到X200.0处
(5)用切削进给返回测量点X100.0处
(6)读取百分表的刻度
(7)按检测单位换算切削进给方式的间隙补偿量
3.步骤三:设置参数1851
参数
设定范围:-9999~+9999
(三)螺距误差补偿
步骤一:测量准备
(1)将Z轴光栅尺与数显表正确连接。
(2)设置滑台的机械坐标系零点,以及正负限位。
如下图所示,设置正限位为48,负限位为-257.
步骤二:设置如下参数:
图2 螺距误差补偿画面
步骤三:测量补偿值并记录
(1)在MDI方式下,输入“G98 G01 Z-257.0 F300”,按下自动循环按钮,滑台运动至Z轴-257mm位置。
(2)输入“G98 G01 Z-255.0 F300”,按下自动循环按钮,滑台运动至Z轴-255mm 位置。
注意:这一步是为了消除反向间隙误差。
(3)按下【单步】按键,把光栅尺数显表清零,输入“G98 G01 W20.0 F300”,按下自动循环按钮,滑台向Z轴正方向运动20mm,记录数显表读数后清零,再次运行以上程序,记录各次读数填入下表。
步骤四:输入补偿值,再次测量,观察补偿效果。
三、实训要点及实施
1.实训要点
(1)本实训项目实施计划根据FANUC 0i mate TD数控系统制定,在实际教学中,采用不同的系统,参数设置可能有所不同
(2)通过本项目要掌握滚珠丝杠反向间隙和螺距误差补偿方法,并能够正确输入补偿参数。
2.工具清单
工具:百分表1个,磁力表座1个,光栅尺数显表1个。
3.项目实施计划
(1)按照反向间隙补偿步骤对机床进行反向间隙的补偿。
(2)按照螺距误差补偿方法对机床进行螺距误差补偿。
四、实训项目报告
实训项目报告一
五、思考题
六、阅读资料。