ISO22000:2018危害分析预备步骤控制程序
ISO22000:2018风险识别和应对控制程序
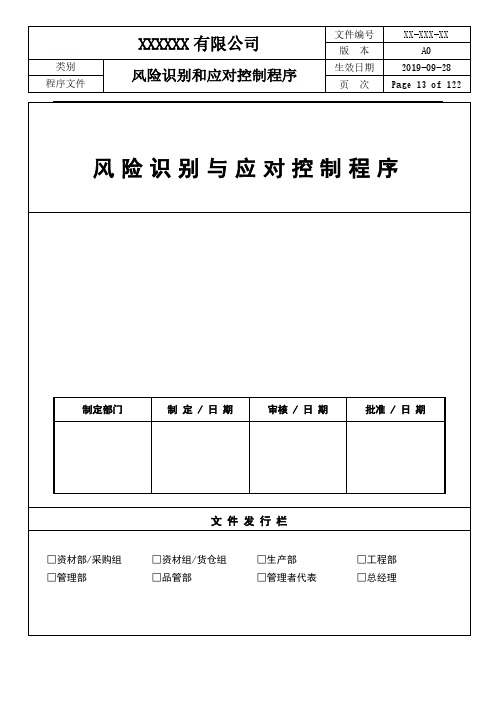
5.10 风险应对措施包括:风险规避、风险降低、风险接受等,并制定可行实施方案。
5.11 对风险措施有效性进行评价,直到目标达成。
6.0 相关文件
6.1《文件、资料和记录管理程序》
6.2《管理评审管理程序》
7.0 相关表单/记录
无
8.0 流程图
工作流程
责任部门
相关记录
无
ห้องสมุดไป่ตู้
5.8.3 资金使用过程中的风险:
主要表现为短期资金风险和长期资金投资风险。
5.8.4 资金回收过程中的风险:
应收款无法及时到位,增加了坏账的出现率。
5.8.5 收益分配过程中的风险:
主要表现在确认风险和对投资者进行收益分配不当而产生的风险。
5.9 对风险等级评价后,找出重要风险项目,确定如何应对风险和机遇。
任。 5.5 环境风险: 5.5.1 产品销售淡季与旺季,影响顾客的采购,也间接影响公司产品生产。 5.5.2 人文环境:
主要体现在不同时间、不同地区、不同民族的人消费习惯不同。 5.5.3 政策环境:
国家宏观经济政策、经济环境的变动,以及个地方的相关政策的变动会间接的影响到企业 资金融入以及企业运营的必要条件。 5.5.4 经济环境: 利率的变动、汇率的变动、同伙膨胀或通货紧缩等。 5.6 经营风险: 5.6.1 原材料供应: 主要包括了原材料的价格、食品安全和送货时间的变化、采购过程的欺诈行为,采购人员的 疏忽,导致原材料数量以及食品安全上的不达标等。 5.6.2 员工风险: 采购人员、服务人员,技术人员和其他生产管理人员,由于他们的疏忽导致的风险,以及各 岗位主要人员的离职等风险。 5.6.3 设施: 生产设备出现意外的故障,甚至损坏等。 5.6.4 供销链风险: 主要包括供应商及顾客违约,以及供应或销售渠道不畅通等风险。 5.6.5 法律纠纷: 消费者投诉等潜在的法律纠纷。 5.7 市场风险: 5.7.1 市场容量: 对市场容量的调查所采用的方法不合适,没有准确的弄清市场对象对产品的用量,使得产品 的产量大于实际需求,而增加公司的投资风险。 5.7.2 市场竞争力:
ISO22000:2018危害分析控制程序

5.1对所有原料、辅料、与产品接触的材料、终产品、各工序进行危害分析,识别各环节的危害,对危害进行风险分析。
5.2危害的严重程度可依据该危害导致的伤害严重程度加以判断,一般划分为四级,如图1:
等级
严重程度
含义
1
轻 微
对消费者健康的危害是可以接受的,是个别发生的,不会造成实质伤害。
2
一 般
等级
发生频率
含 义
1
无
历史上在同行业未发生过或未被报道或极少发生,几乎不可能发生。
2
低
可能会发生,发生概率低。
3
中
可能会发生,发生概率较高。
4
高
在本企业或同行业曾经发生过或发生的可能性较高。
图 2
5.3.2 伤害发生概率以相关的历史数据(本厂、同行业、国家数据)、试验模拟、专家的判断等方法来确定,这些方法可以单独使用,也可以组合使用。当某些历史数据或试验等无法使用时,可仅仅依靠经验判断。
在风险评估矩阵中,用Rl,p表示风险评估值,其中:
l={轻微,一般,严重,非常严重}={1,2,3,4}
P={无,低,中,高}={1,2,3,4}
可依据表3风险评估矩阵对食品安全进行风险评估。
评估矩阵如图3
危
害
严
重
程
度
危害发生的概率
无(1)
低(2)
中()
高(4)
轻微(1)
R1,1
R1,2
R1,3
R1,4
5.4风险评估
5.4.1 风险的计算方法:
R=f(l,p)
表示风险的值, 表示伤害发生的严重程度, 表示伤害发生的概率,
=食品安全小组依据顾客投诉的数据,根据经验所做的判断。
ISO220002018版不合格品和潜在不安全品控制程序
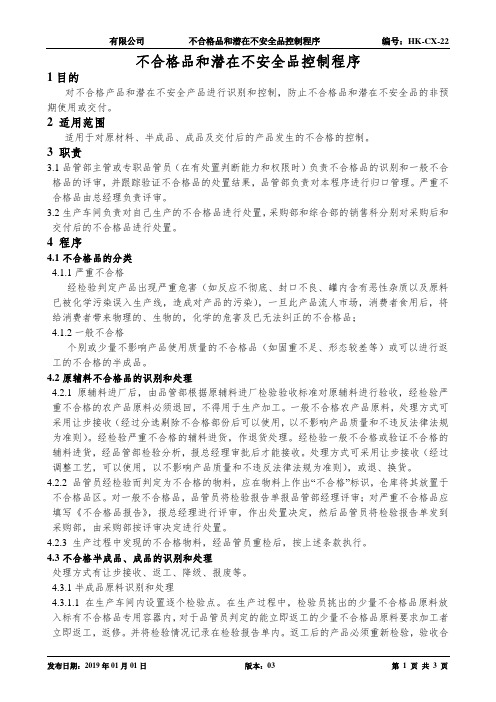
不合格品和潜在不安全品控制程序1目的对不合格产品和潜在不安全产品进行识别和控制,防止不合格品和潜在不安全品的非预期使用或交付。
2 适用范围适用于对原材料、半成品、成品及交付后的产品发生的不合格的控制。
3 职责3.1品管部主管或专职品管员(在有处置判断能力和权限时)负责不合格品的识别和一般不合格品的评审,并跟踪验证不合格品的处置结果,品管部负责对本程序进行归口管理。
严重不合格品由总经理负责评审。
3.2生产车间负责对自己生产的不合格品进行处置,采购部和综合部的销售科分别对采购后和交付后的不合格品进行处置。
4 程序4.1不合格品的分类4.1.1严重不合格经检验判定产品出现严重危害(如反应不彻底、封口不良、罐内含有恶性杂质以及原料已被化学污染误入生产线,造成对产品的污染),一旦此产品流人市场,消费者食用后,将给消费者带来物理的、生物的,化学的危害及已无法纠正的不合格品;4.1.2一般不合格个别或少量不影响产品使用质量的不合格品(如固重不足、形态较差等)或可以进行返工的不合格的半成品。
4.2原辅料不合格品的识别和处理4.2.1原辅料进厂后,由品管部根据原辅料进厂检验验收标准对原辅料进行验收,经检验严重不合格的农产品原料必须退回,不得用于生产加工。
一般不合格农产品原料,处理方式可采用让步接收(经过分选剔除不合格部份后可以使用,以不影响产品质量和不违反法律法规为准则)。
经检验严重不合格的辅料进货,作退货处理。
经检验一般不合格或验证不合格的辅料进货,经品管部检验分析,报总经理审批后才能接收。
处理方式可采用让步接收(经过调整工艺,可以使用,以不影响产品质量和不违反法律法规为准则),或退、换货。
4.2.2 品管员经检验而判定为不合格的物料,应在物料上作出“不合格”标识,仓库将其放置于不合格品区。
对一般不合格品,品管员将检验报告单报品管部经理评审;对严重不合格品应填写《不合格品报告》,报总经理进行评审,作出处置决定,然后品管员将检验报告单发到采购部,由采购部按评审决定进行处置。
ISO22000:2018不合格及潜在不安全产品控制程序

6 相关文件及资料
生效日期 同发行日期 页 次
3/4
页序
A
名 称 不合格及潜在不安全产品控制程序 P-ZHKY-BGS-10
6.1 原料验收作业标准 6.2 报废物品处理作业办法 6.3 标识和可追溯性控制程序 7 使用表单 7.1 不合格品处理单 7.2 品质管制单
生效日期 同发行日期 页 次
4/4
B 召回流程:
依《产品回收作业办法》执行。
C 产品召回的演习
为了确保产品撤回及时有效,检验部门组织每年至少进行一次回收演习。
5.5.5 报废
不合格品核决报废处理时,依《报废物品处理作业办法》执行;
5.6 潜在不安全产品的处理方式 除非检验能提供充分证据(抽样分析、过程监控、控制措施有效)验证潜在不安 全产品符合确定的相关食品安全危害的可按受水平,可将其作为安全产品放行; 否则依不合格产品处理。
名 称 不合格及潜在不安全产品控制程序 P-ZHKY-BGS-10
1.目的:
标识、隔离、处理和记录不合格品及潜在不安全产品,防止不合格品及潜在不安全 产品的非预期使用和交付。
2.适用范围: 从原料进料至制程、成品检验、仓储、产品回收及客户退货各作业中,不合格品与
潜在不安全产品的标识、记录与处理均适用。 3.术语:
5.2 生产过程中发现之不合格品及潜在不安全产品的控制 5.2.1 调湿时水分含量过低由生产部门返工处理。返工后的产品由制程检验重新 检验,合格后办理入库转良,不合格品重新返工直至合格;调湿时水分含
生效日期 同发行日期 页 次Biblioteka 1/4页序A
名 称 不合格及潜在不安全产品控制程序 P-ZHKY-BGS-10
生效日期 同发行日期 页 次
ISO220002018版HACCP计划控制程序

HACCP计划控制程序1目的确保HACCP计划的建立、实施、保持和更新适应危害分析的要求。
2适用范围适用于HACCP计划的建立,实施、保持和更新过程,包括确定关键控制点及其上的关键限值,建立关键控制点的监控系统及其实施。
3职责3.1 食品安全小组负责HACCP计划的建立、保持、更新和确认;3.2 管理者代表负责HACCP计划的审核;3.3总经理负责HACCP计划的批准;3.4 各部门参与和配合实施HACCP包括监控和必要的纠正和纠正措施。
4定义关键控制点:能够施加控制,并且该控制对防止或消除食品安全危害或将其降低到可接受水平是必需的某一步骤。
5程序5.1关键控制点(CCP)的确定5.1.1根据危害分析的结果(危害分析工作单),由HACCP计划管理的控制措施所在的产品和(或)过程步骤即为关键控制点。
5.1.2如果危害分析的结果不能确定关键控制点,潜在的危害须由HACCP前提计划控制。
5.1.3同一危害可能由不止一个关键控制点实施控制;而在某些产品加工中可能识别不出关键控制点。
5.2关键控制点中关键限值(CL)的确定5.2.1设定关键参数5.2.1.1有某一个关键控制点上的食品安全危害都应设立对应的关键参数,关键参数应能严格反映危害水平。
5.2.1.2关键参数应符合有效、直观、简捷快速和经济的原则。
可考虑使用温度、时间、纯度、PH值、水分活度、体积等;5.2.1.3从危害及其可接受水平、相应的控制措施来确定关键参数。
只符合上述原则,应优先考虑直接依据危害来设立关键参数。
5.2.2确定关键限值5.2.2.1针对每个关键参数,确定关键限值。
在关键限值内,应可确保食品安全危害在可接受水平内。
5.2.2.2确定关键限值要基于科学依据,如法规限量、科学文献、工业标准、验证和确认的结果、试验结论、客户和专家意见、公认惯例等。
5.2.2.3当一个关键参数控制多个危害水平时,其关键限值应由对其最不敏感的危害来决定。
ISO22000-2018危害分析预备步骤控制程序

反映加工场所的平面结构、设施设备位置,表明原料、中间产品、成品、废品、垃圾以
及人员在内的流动情况,应特别标明虫害、鼠害的防治设施。
5.6理体系覆盖的食品安全管理体系所覆盖产品或过程类别的流程
图。
5.6.2流程图应清晰、准确和足够详尽,提供食品安全危害可能出现、增加或引入的信息。
危害分析预备步骤控制程序
制定部门
制定/日期
审核/日期
批准/日期
文件发行栏
□资材部/采购组□资材组/货仓组□生产部□工程部
□管理部□品管部□管理者代表□总经理
1、形成文件的信息管理工作流程修改履历
序号
章节
版次
制定或修改內容
日期
1.0目的
确保所有实施危害分析所需的相关信息的保持和更新。
2.0适用范围
适用于实施危害分析所需的相关信息的收集、保持和更新,包括产品描述、流程图(含布置图)
7、相关记录
产品特性描述表
布置图
流程图
过程步骤和控制措施描述表
人、婴儿等)、再加工的食品企业,并应考虑消费群体中确定的食品安全危害的易感人
群;识别预期的处理如直接食用、加热后食用,作为其他食品的原料再加工使用,并
应识别非预期但可能会出现的产品的误处理和误用。
g)包装形式、方法和材料;
h)与食品安全有关的标识,和(或)处理、制备和使用说明书;
i)分销方式:包括运输和销售。
以收集、分析、确定和验证危害分析的相关信息。
5.2危害分析预备步骤的输出进行验证,确保其与实际生产和管理运行完全一致。
a)在危害分析预备步骤的开始和进行当中,质量小组应与相关信息涉及的职能部门或岗位
进行充分沟通,保证信息的可信性和充分性。
ISO22000:2018危害分析控制程序

1、目的规定对从物料本身及来源、运输、贮存、采购、生产以及消费过程,分析可能发生的生物、化学或物理的潜在危害,进行识别和评估分析,并制定预防措施加以控制,确保食品链的质量和食品安全。
2、范围适用于本公司采购和生产全过程。
3、权责3.1总经理:负责危害分析与预防措施的资源提供。
3.2 HACCP小组组长:负责组织HACCP小组成员进行风险识别、潜在不安全和危害分析、评估,制定预防措施。
3.3 HACCP 小组成员:参与风险识别、潜在不安全和危害分析,以及制定预防措施。
3.4其他责任部门:本部门的风险识别、潜在不安全和危害分析,制定预防措施,并执行预防措施。
3.5品管:负责监督预防措施的执行情况,并验证其效果。
4、定义:4.1危害分析(Hazard Analysis)--是指识别出食品中可能存在的给人们身体带来伤害或疾病的生物、化学、物理或其他因素,并评估危害的严重程度和发生的可能性,以便采取措施加以控制。
4.2预防措施(preventive action)-- 为消除潜在不合格或其他潜在不期望情况的原因所采取的措施5、流程图流程确认危害识别危害评估预防措施执行、验证及更新6、控制程序6.1流程确认HACCP小组组织采购、品管、仓库、生产等多个部门,对公司产品从采购、生产至交付的所有工序进行确认,制作流程图,并对该流程图进行现场验证和详细描述,以备进行危害分析,危害分析应考虑的内容(详见《HACCP计划》):a)原料接收直至消费者使用以前所有可能发生的并且一旦发生会对消费者造成不可接受的危害;b)原料和辅料的评估;c)产品的特性;d)加工参数和加工设计;1e)加工设备和布局;f)贮存设施和条件;g)包装及包装材料;h)生产方式;i)与加工有关的卫生状况;j)经验;k)外部信息,尽可能包括流行病学和其他历史数据;l)来自食品链中,可能与终产品、中间产品和消费食品的安全相关的食品安全危害信息;m)立法/执法或顾客要求;等等。
ISO22000:2018应急准备和响应控制程序

5.1.6洪水等自然灾害:影响生产或服务资源的完整性,从而影响食品安全危害控制措施的有效性;
5.1.7供应链的突变:供方发生质量事故导致原物料供应中断,或者运输、贮存等合作伙伴车辆短缺、仓库损坏无法使用或违法被查处等,对最终产品可能存在危害的可能。
5.1.8原料错用、误用,可能造成成品的品质存在潜在食品安全。
4.4库管科:
4.4.1出现影响品质安全事件时对在制产品及尚未入库的产品按照食安小组的意见进行处理。
4.4.2对因本部门原因造成的品质安全事件进行原因分析并采取纠正措施。
4.5检验科:
4.5.1对品质安全应急事件发生时产品品质进行初步判定,对可疑样品张贴明显标识管制封存处理。
4.5.2对可疑样品(原水、原料、成品)取样送检至政府部门相关检验机构检验。
5.1.2突然停电:正在运作的设施设备由于突然停电而停止工作,可能影响产品的质量。
5.1.3厂区周围企业出现化学品、刺激性气体泄漏:公司厂区周围企业出现化学品、刺激性气体泄漏,可能会污染原料、包装材料及成品,影响产品品质及食用安全。
5.1.4关键设备故障:关键设备突发故障可能影响产品质量甚至可能造成品质安全隐患。
4.2食品安全小组组长:品质安全应急程序的协调管理和提供最终处理意见。
4.3食品安全小组:参与评估所有与品质安全有关的事件对产品的影响。
4.3生产科:
4.3.1突发状况(突然停电、停水、附近企业化学品、刺激性气体泄漏)时,对外部造成的事件进行调查并在厂内通报。
4.3.2发生恶意投毒及故意污染事件时,向公安部门报警及协助公安部门调查。
1 目的:
建立应急状况的识别和响应措施,确定可能影响食品安全的潜在事故和紧急情况,制订相应的预案,保证产品的安全和质量。
ISO22000:2018纠正和预防措施控制程序
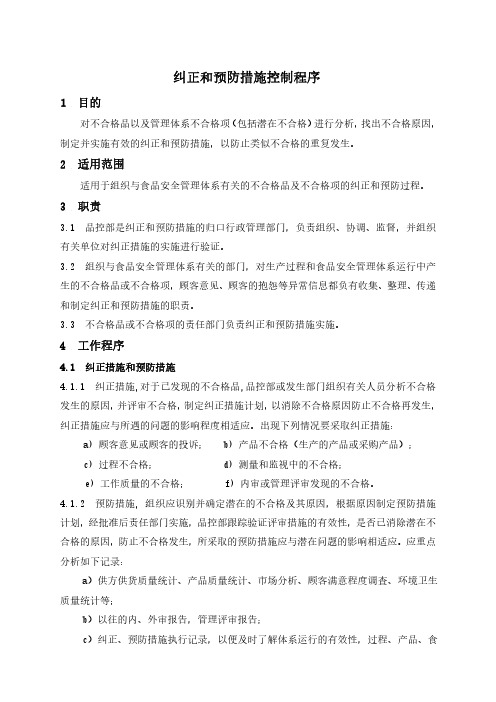
纠正和预防措施控制程序1 目的对不合格品以及管理体系不合格项(包括潜在不合格)进行分析,找出不合格原因,制定并实施有效的纠正和预防措施,以防止类似不合格的重复发生。
2 适用范围适用于组织与食品安全管理体系有关的不合格品及不合格项的纠正和预防过程。
3 职责3.1 品控部是纠正和预防措施的归口行政管理部门,负责组织、协调、监督,并组织有关单位对纠正措施的实施进行验证。
3.2 组织与食品安全管理体系有关的部门,对生产过程和食品安全管理体系运行中产生的不合格品或不合格项,顾客意见、顾客的抱怨等异常信息都负有收集、整理、传递和制定纠正和预防措施的职责。
3.3 不合格品或不合格项的责任部门负责纠正和预防措施实施。
4 工作程序4.1 纠正措施和预防措施4.1.1 纠正措施,对于己发现的不合格品,品控部或发生部门组织有关人员分析不合格发生的原因,并评审不合格,制定纠正措施计划,以消除不合格原因防止不合格再发生,纠正措施应与所遇的问题的影响程度相适应。
出现下列情况要采取纠正措施:a) 顾客意见或顾客的投诉; b) 产品不合格(生产的产品或采购产品);c) 过程不合格; d) 测量和监视中的不合格;e) 工作质量的不合格; f) 内审或管理评审发现的不合格。
4.1.2 预防措施, 组织应识别并确定潜在的不合格及其原因,根据原因制定预防措施计划,经批准后责任部门实施,品控部跟踪验证评审措施的有效性,是否已消除潜在不合格的原因,防止不合格发生,所采取的预防措施应与潜在问题的影响相适应。
应重点分析如下记录:a)供方供货质量统计、产品质量统计、市场分析、顾客满意程度调查、环境卫生质量统计等;b)以往的内、外审报告,管理评审报告;c)纠正、预防措施执行记录,以便及时了解体系运行的有效性,过程、产品、食品安全趋势及顾客的要求和期望,在日常对体系的检查和监督过程中,及时收集分析各方面的反馈信息。
(以下所列不合格包括潜在不合格情况)4.2 不合格原因分析和纠正和预防措施的制定与实施。
ISO22000:2018危害分析与HACCP计划建立控制程序

危害分析与HACCP计划建立控制程序1 目的对影响食品安全的危害进行识别、评价出显著危害,并就此确定关键控制点和建立相应的HACCP计划,使食品安全危害得到有效的控制。
2 适用范围适用于公司的食品安全危害分析及HACCP计划的建立3 职责3.1 总经理负责组织成立食品安全小组,并任命食品安全小组组长;负责对危害分析、HACCP计划的建立进行管理。
3.2 食品安全小组负责编制产品特性、工艺流程图以及工艺描述,进行危害分析,建立HACCP计划。
4 工作程序4.1 食品安全小组的成立总经理牵头成立食品安全小组,食品安全小组成员来自品控部、生产部、综合部、综合部、销售部等公司各部门。
这些人员应接受过相关培训,具备建立、实施食品安全管理体系的能力。
公司应以文件形式规定每个食品安全小组成员的职责。
4.1.1 收集有关的信息在进行危害分析及建立HACCP计划之前,食品安全小组应收集下列信息:(1)原料、辅料、与食品接触材料的卫生安全标准。
(2) 与公司产品有关的国家、行业卫生标准;与公司产品有关的国家、行业质量标准;与公司产品安全相关的外部文献资料。
(3)公司平面图,公司生产区域水路管网图,生产现场的人流、物流图,卫生设施配置图、生产设备分布图、卫生管理区域图、工艺流程图。
(4)产品贮存设施与贮存条件;公司使用的有毒有害物质一览表。
(5)技术文件,卫生管理文件,化学品特性资料。
(6)公司历史上的客户投诉与食品安全事故。
4.1.2 编写产品描述(含终产品的预期用途)(1)食品安全小组编写所有原料、辅料、与产品接触的材料的特性描述,在编写特性描述时,应识别与描述的内容相关的法律法规。
特性描述的内容一般包括以下方面:①化学、生物和物理特性;②配制辅料的组成,包括添加剂和加工助剂;③产地;④生产方式;⑤包装和交付方式;⑥贮存条件和保质期;⑦使用或生产前的预处理;⑧原料和辅料的接收准则或规范,接收准则和规范中,应关注与原料和辅料预期用途相适宜的食品安全要求。
ISO220002018版危害分析控制程序
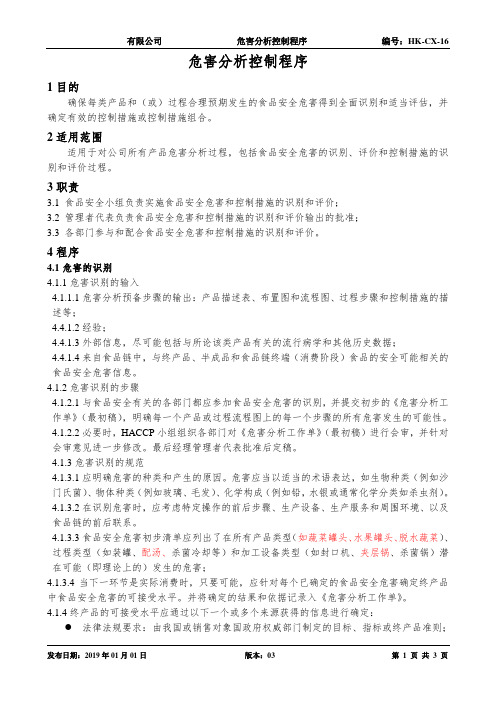
危害分析控制程序1目的确保每类产品和(或)过程合理预期发生的食品安全危害得到全面识别和适当评估,并确定有效的控制措施或控制措施组合。
2适用范围适用于对公司所有产品危害分析过程,包括食品安全危害的识别、评价和控制措施的识别和评价过程。
3职责3.1 食品安全小组负责实施食品安全危害和控制措施的识别和评价;3.2 管理者代表负责食品安全危害和控制措施的识别和评价输出的批准;3.3 各部门参与和配合食品安全危害和控制措施的识别和评价。
4程序4.1危害的识别4.1.1危害识别的输入4.1.1.1危害分析预备步骤的输出:产品描述表、布置图和流程图、过程步骤和控制措施的描述等;4.4.1.2经验;4.4.1.3外部信息,尽可能包括与所论该类产品有关的流行病学和其他历史数据;4.4.1.4来自食品链中,与终产品、半成品和食品链终端(消费阶段)食品的安全可能相关的食品安全危害信息。
4.1.2危害识别的步骤4.1.2.1与食品安全有关的各部门都应参加食品安全危害的识别,并提交初步的《危害分析工作单》(最初稿),明确每一个产品或过程流程图上的每一个步骤的所有危害发生的可能性。
4.1.2.2必要时,HACCP小组组织各部门对《危害分析工作单》(最初稿)进行会审,并针对会审意见进一步修改。
最后经理管理者代表批准后定稿。
4.1.3危害识别的规范4.1.3.1应明确危害的种类和产生的原因。
危害应当以适当的术语表达,如生物种类(例如沙门氏菌)、物体种类(例如玻璃、毛发)、化学构成(例如铅,水银或通常化学分类如杀虫剂)。
4.1.3.2在识别危害时,应考虑特定操作的前后步骤、生产设备、生产服务和周围环境、以及食品链的前后联系。
4.1.3.3食品安全危害初步清单应列出了在所有产品类型(如蔬菜罐头、水果罐头、脱水蔬菜)、过程类型(如装罐、配汤、杀菌冷却等)和加工设备类型(如封口机、夹层锅、杀菌锅)潜在可能(即理论上的)发生的危害;4.1.3.4当下一环节是实际消费时,只要可能,应针对每个已确定的食品安全危害确定终产品中食品安全危害的可接受水平。
ISO22000-2018食品安全管理体系HACCP危害分析资料

2
2
否
外包装感官检查
后续工艺过程高温可以灭杀
否
PRP(供应商管理) PRP(进货验证)
化学性
重金属
原料制程控制不当带来
1
2
2
否
进货验收
无
否
PRP(供应商管理) PRP(进货验证)
迁移物质
材料特性
2
2
4
否
进货验收
无
否
PRP(供应商管理) PRP(进货验证)
物理性
金属
原料制程控制不当带来
1
3
3
否
进货验收
SOP(包装管理)
化学性
无
物理性
无
包装完好就不会发生
13
成品库贮存(同上)
生物性
虫害
鼠害、飞虫
2
2
4
否
虫害控制
无
N
PRP(虫害控制程序)
霉菌
产品受潮
2
2
4
否
储存规定
无
N
PRP(仓库储存)
化学性
无
物理性
无
注:带“☆”的表明有工艺步骤有重复,危害分析内容相同
3.压缩空气危害分析工作表
7.4.2.2危害识别
霉菌酵母菌
环境引入
2
2
4
否
GMP管理、人员个人卫生
无
N
PRP(设备的PM及清洁计划)
化学性
油墨、润滑油
油墨污染、润滑油污染
2
2
4
否
芯轴清洁、加油点管理
N
PRP(润滑油管理及油墨)
物理性
金属异物
零部件松动
iso22000:2018应急准备与响应控制程序

应急准备与响应控制程序 1 目的 本程序的目的是当影响食品安全质量事件突然发生时,能够迅速、准确、有效的予以识别、控制和保护产品,最大限度的消除或降低食品安全事故的危害。
2 适用范围 本程序适用于公司预防食品安全事故的发生和食品安全突发事件发生时的应急处理控制。
3 术语 突发事件:在影响食品安全质量方面导致或可能导致产品的不合法、不安全的异常事件。
如:食品安全卫生事故(食源性疾病)、国内外预警信息、蓄意污染破坏、关键服务中断、自然灾害影响等。
4 职责 4.1 突发事件的发生部门(人员)或发现部门(人员)负责突发事件的紧急报告。
4.2 食品安全小组组长兼任突发事件处理小组组长,负责对突发事件的受理和应急处理的协调指挥。
4.3 发生突发事件时,在应急现场的最高职务的人员负责按本程序在第一时间做出响应。
4.4 有关部门/人员无条件按本程序和职责要求执行相应应急处理工作。
5 工作程序 5.1 突发事件处理小组 成立公司突发事件处理小组并确定职责,由小组识别并建立突发事件发生时需寻求的有关外部组织及联系方式,组长由食品安全小组组长兼任。
小组成员及其职责见附表“食品安全突发事件处理小组成员及职责”。
5.2 突发事件识别 突发事件处理小组负责根据公司生产实际情况,对可预见的可能影响食品安全的潜在事故和紧急情况进行识别,并根据公司、社会和环境的变化不断进行完善。
公司识别的应急状况包括: ①突然停水:清洁工序的质量无法保证和食品加工无法继续进行; ②火灾发生:影响现场产品质量安全和以后生产卫生条件不符合要求; ③突然停电、停气:由电力、天然气支持的正在运作的设施设备停止工作,可能导致原料、半成品和成品的积压变质; ④重要生产设备故障:造成产品积压变质、污染或不合格; ⑤蓄意的污染破坏:污染产品、导致影响健康或生命危险; ⑥关键人员的空岗:影响正常加工,造成产品积压变质或不合格; ⑦关键原辅料的供应中断:影响正常生产,造成过程产品积压变质; ⑧发生食品安全事故:导致影响健康或生命危险; ⑨与公司有关的国内外预警:可能导致产品的不安全不合法; 5.3 应急准备(预案) 由突发事件处理小组针对识别的突发事件情况制定相应的应急准备(预案),如下。
- 1、下载文档前请自行甄别文档内容的完整性,平台不提供额外的编辑、内容补充、找答案等附加服务。
- 2、"仅部分预览"的文档,不可在线预览部分如存在完整性等问题,可反馈申请退款(可完整预览的文档不适用该条件!)。
- 3、如文档侵犯您的权益,请联系客服反馈,我们会尽快为您处理(人工客服工作时间:9:00-18:30)。
h)与食品安全有关的标识,和(或)处理、制备和使用说明书;
i)分销方式:包括运输和销售。
4.4.4原料、辅料、与食品接触材料描述表应包括如下方面的信息,其详略程度应足以识别和评价食品安全危害。
a)化学、生物和物理特性;
b)配制辅料的组成,包括添加剂和加工助剂;
c)产地;
d)生产方法;
e)交付方式,包装和贮存条件;
h)使用或加工前的预处理;
i)与采购原料和辅料预期用途相适宜的食品安全接收准则或规范。
4.5描绘布置图:
反映加工场所的平面结构、设施设备位置,表明原料、中间产品、成品、废品、垃圾以及人员在内的流动情况,应特别标明虫害、鼠害的防治设施。
4.6产品或过程类别的流程图
4.6.1质量、食品安全小组负责绘制管理体系覆盖的食品安全管理体系所覆盖产品或过程类别的流程图。
4.7.1食品质量、安全小组负责利用操作性前提方案和产品描述提供的信息质量、食品安全小组对与流程图对应的每个步骤进行详细的说明。
4.7.2描述应包括如下内容,并规定其严格程度以满足实施危害分析所需。
a)流程的操作和活动;
b)所使用的设施设备和工具;
c)投入或产出的物料;
d)过程参数(如温度、添加物的点/形式,流程等)、应用强度(或严格程度)(如时间、水平、浓度等)和加工差异性(相关时);
1
确保所有实施危害分析所需的相关信息的保持和更新。
2
适用于实施危害分析所需的相关信息的收集、保持和更新,包括产品描述、流程图(含布置图)和工艺步骤的编制、确认。
3
3.1 质量、食品安全小组负责实施危害分析所需的相关信息的收集、审核、确认,保持和更新。
3.2管理者代表负责施危害分析所需的相关信息的批准。
b)危害分析预备步骤的输出最终确定前,质量、食品安全小组应与这些输出涉及的职能部门或岗位共同进行现场验证。可通过现场核对验证其是否符合现状。验证应有记录。
c)生产管理情况有变,危害分析预备步骤的输出不适合时,相关部门应将不适合情况报告质量、食品安全小组,由其根据实际情况进行更新。
d)危害分析预备步骤的输出与现状不一致时,应修订相关的输出或纠正运作,以达到二者一致。修订相关输出按《文件控制程序》进行,纠正运作按《纠正和预防措施控制程序》进行。
4.4.3终产品描述表应包括如下方面的信息,详略程度应足以进行危害分析。
a)产品名称或类似标识,以及加工场所;
b)成份,包括使用的原料;
c)加工方式:如热处理、冷冻、盐渍、烟熏等;
d)与食品安全有关的化学、生物和物理特性:如温度,PH值,水分活度等;
e)预期保质期和贮存条件;
f)预期用途:识别各种产品和(或)过程类型的使用者和消费者如公众、特定群体(老人、婴儿等)、再加工的食品企业,并应考虑消费群体中确定的食品安全危害的易感人群;识别预期的处理如直接食用、加热后食用,作为其他食品的原料再加工使用,并应识别非预期但可能会出现的产品的误处理和误用。
d)当以批次为基础时,还包括在检验程序基础上的分类,如产品抽样和测试;
e)预期使用,如特定预期使用、打开包装前和打开包装后的保质期限,以及其他与食品安全有关的、用于指导/指示顾客的标识。
4.7.4只要可能,控制措施应直接针对食品安全危害的原因或根源提出。
5
文件控制程序
纠正和预防措施控制程序
危害分析控制程序
e)影响选择控制措施及其严格程ห้องสมุดไป่ตู้的外部要求(如来自顾客或主管部门)。
4.7.3可能的控制措施包括贯穿食品链的各种应用措施,包括:
a)食品处理和消费的良好规范中(农业、动物养植、卫生)和良好消费者规范;
b)包括于生产、加工、分销(含运输)、贮藏和零售中应用的方法;
c)食品的内在因素(如pH值和水活度)中;
3.3 各部门参与和配合完成危害分析预备步骤,并报告相关信息不适合情况。
4
4.1危害分析的预备步骤包括产品描述、布置图和流程图的绘制、过程步骤和控制措施的描述,以收集、分析、确定和验证危害分析的相关信息。
4.2危害分析预备步骤的输出进行验证,确保其与实际生产和管理运行完全一致。
a)在危害分析预备步骤的开始和进行当中,质量、食品安全小组应与相关信息涉及的职能部门或岗位进行充分沟通,保证信息的可信性和充分性。
食品安全验证控制程序
各种操作性前提方案
6
产品特性描述表
布置图
流程图
4.6.2流程图应清晰、准确和足够详尽,提供食品安全危害可能出现、增加或引入的信息。
4.6.3流程图应包含如下信息:
a)所有操作步骤的顺序和相互关系;
b)源于外部的过程和分包的工作;
c)原料、辅料和中间产品投入点;
d)返工和循环点;
e)终产品、半成品和副产品转出点及废弃物的排放点。
4.7过程步骤和控制措施的描述
4.3实施危害分析所需的相关信息是公司受控文件,其编审、发放、标识、使用、更改等控制按《文件控制程序》和《记录控制程序》要求进行。
4.4产品描述
4.4.1质量、食品安全小组负责对管理体系覆盖的每一种终产品、原料、辅料、与食品接触材料的产品特性进行描述,编制产品描述表,作为工作文件。
4.4.2产品描述应识别有关的食品安全法定的要求,并收集相关的法律法规。