PCABS手机壳工艺设计
手机底壳工艺流程
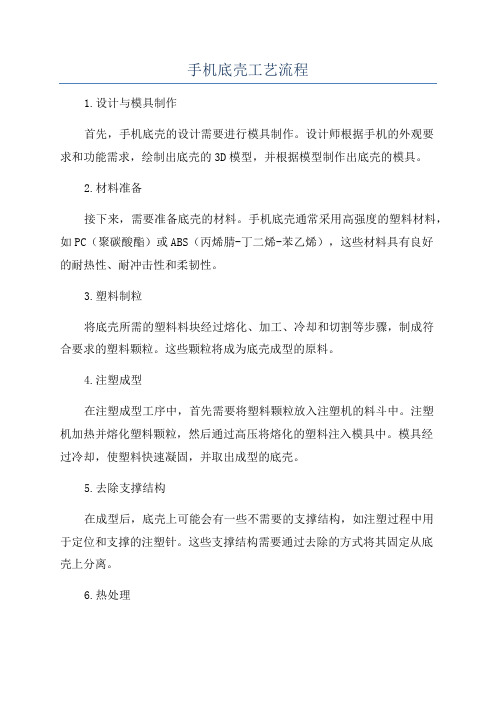
手机底壳工艺流程1.设计与模具制作首先,手机底壳的设计需要进行模具制作。
设计师根据手机的外观要求和功能需求,绘制出底壳的3D模型,并根据模型制作出底壳的模具。
2.材料准备接下来,需要准备底壳的材料。
手机底壳通常采用高强度的塑料材料,如PC(聚碳酸酯)或ABS(丙烯腈-丁二烯-苯乙烯),这些材料具有良好的耐热性、耐冲击性和柔韧性。
3.塑料制粒将底壳所需的塑料料块经过熔化、加工、冷却和切割等步骤,制成符合要求的塑料颗粒。
这些颗粒将成为底壳成型的原料。
4.注塑成型在注塑成型工序中,首先需要将塑料颗粒放入注塑机的料斗中。
注塑机加热并熔化塑料颗粒,然后通过高压将熔化的塑料注入模具中。
模具经过冷却,使塑料快速凝固,并取出成型的底壳。
5.去除支撑结构在成型后,底壳上可能会有一些不需要的支撑结构,如注塑过程中用于定位和支撑的注塑针。
这些支撑结构需要通过去除的方式将其固定从底壳上分离。
6.热处理热处理是为了提高底壳的硬度和强度而进行的一道工艺。
通常,底壳会被放入恒温炉中进行一段时间,使其加热到一定温度,然后快速冷却。
这样可以改变底壳的晶体结构,使其具有更好的物理性能。
7.表面处理底壳在成型后需要进行表面处理以提高外观质量和防刮性能。
这包括抛光、喷漆、喷涂等工艺。
抛光可以使底壳的表面光滑,喷漆可以为底壳添加颜色,喷涂可以增加抗刮擦能力。
8.装配经过表面处理后,底壳将进行装配工序。
这包括安装电池、电路板、摄像头等零部件。
底壳会通过螺丝、卡扣等方法将各个零部件固定在一起,形成完整的手机底壳。
9.检测与质量控制在生产过程中,对底壳的质量进行检测与控制是至关重要的。
质检人员会对底壳进行外观检查、尺寸测量、材料测试等多项检测,以确保底壳符合设定的质量标准。
10.包装与运输最后,底壳会进行包装,并根据需要进行分类和分装。
通常采用透明塑料袋、泡沫箱等形式进行包装,然后进行销售或运输到手机组装生产线。
总结:手机底壳的制造工艺流程包括设计与模具制作、材料准备、塑料制粒、注塑成型、去除支撑结构、热处理、表面处理、装配、检测与质量控制以及包装与运输等环节。
手机外壳的注塑模设计

编号:毕业设计(论文)说明书题 目: 手机外壳的注塑模设计学 院: 机电工程学院专 业: 机械设计制造及其自动化学生姓名: xxxx学 号: xxxx指导教师: xxxx职 称: 实验师题目类型: 工程设计 软件开发20xx 年 6 月 3 日随着科学技术的飞速发展,越来越多的人开始使用移动手机,因此手机外壳的生产也是也是一项重要的研究。
而且,模具现在在世界上发展的越来越迅速,发展前景很好。
在实际生产中大多数都采用注塑模,因此本文研究的就是手机外壳的注塑模设计。
本文介绍了制作手机外壳的注塑模的设计,对手机外壳进行相应的结构工艺分析、材料分析等;通过比较选择ABS工程塑料作为制作手机壳的原材料;利用SolidWorks 软件完成对塑件的建模。
对注射模进行了设计与计算,其中包括注射机的选择、注射模结构的设计以及模具中成型零部件、结构零部件、浇注系统、推出系统、冷却系统等的设计以及相关的模具材料的选用。
由于塑件较小,需求量较大所以在设计中采用了一模两腔的加工方法;在分析塑件结构时发现塑件在内侧有凸台,所以采用斜导柱内抽芯机构来对塑件进行内抽芯,方便了模具的开模。
在进行设计计算的过程中,利用AutoCAD 和CAXA电子图板绘制了模具的二维装配图以及各个零部件的二维图。
在本次毕业设计的过程中,复习和巩固了许多大学所学的机械知识,例如机械制图、塑料成型工艺及模具设计等课程,提升了自己的能力,取得了良好的效果。
关键词:ABS工程塑料;手机壳;斜导柱内抽芯With the rapid development of science and technology, more and more people start using mobile phone, so mobile phone casing production is also an important study. Moreover, the mold is now developing more and more rapidly in the world, the prospect of it is very gond. Injection molding is used in most of the actual production,so this study is to design injection mold of mobile telephone shell.This article describes the injection mold design of mobile phone shell, phone shell structure corresponding process analysis, materials analysis; By comparing with other materials, selected ABS plastic as raw material to product mobile phone shell; use SolidWorks software to complete the modeling of plastic parts. Injection mold is designed and calculated, including the choice of injection machine, injection mold structure design and mold forming components, structural parts, gating system, the introduction of the selection system, cooling system design and related mold material . Since the plastic parts is small, so the demand for larger processing methods used in the design of a two cavity mold; plastic parts in the analysis of structural plastic parts found on the inside there are bosses, so the use of the inner bevel pillar core pulling mechanism for pulling the plastic parts were inside, to facilitate the mold is open. During the course of the design calculations, using AutoCAD and CAXA electronic drawing board to draw a two-dimensional mold assembly drawing and two-dimensional map of the various components. In this graduation design process, review and consolidate the mechanical knowledge learned many universities, such as mechanical drawing, plastic molding process and mold design courses to enhance their ability to obtain good results.Keywords: ABS plastic; phone shell; bevel pillar inner core pulling目录引言 (1)1 塑料成型简介 (1)2 手机外壳的成型工艺设计分析 (1)2.1手机外壳塑件的材料的选用 (2)2.2塑件的结构工艺分析 (3)2.2.1塑件的壁厚 (3)2.2.2塑件的尺寸精度 (3)2.2.3塑件的脱模斜度 (4)2.2.4塑件的表面粗糙度 (4)2.2.5塑件的体积和质量 (5)2.3塑料材料的分析 (5)2.3.1塑件材料的力学性能 (5)2.3.2塑件材料的注射工艺参数 (6)3 注射模设计 (7)3.1注射成型工艺 (7)3.2注射模结构与注射机的选定 (8)3.2.1注射模具的结构组成 (8)3.2.2注射机的初步选择 (9)3.3注射机的参数的校核 (10)3.3.1最大注射量的校核 (11)3.3.2锁模力的校核 (11)3.3.3最大注射压力的校核 (13)3.3.4注射机与模具配合尺寸的校核 (13)3.3.5开模行程的校核 (14)3.3.6推出装置的校核 (15)3.4塑件在模具中的位置确定 (16)3.4.1型腔数量及其排列方式 (16)3.4.2分型面的设计 (17)3.5注射系统的设计 (18)3.5.1主流道的设计 (18)3.5.2冷料穴的设计 (19)3.5.3浇口的设计 (20)3.5.4浇注系统的平衡 (20)4 成型零部件的设计 (21)4.1成型零部件的结构设计 (21)4.1.1凹模的机构设计 (21)4.1.2 型芯的结构设计 (22)4.2成型零部件工作尺寸的计算 (22)4.2.1型腔和型芯径向尺寸的计算 (23)4.2.2型腔深度和型芯高度的尺寸计算 (24)4.3型腔侧壁和垫板厚度的计算 (25)5 结构零部件的设计 (27)5.1模架的选用 (27)5.2支撑零部件的设计 (28)5.3合模导向机构的设计 (28)6 推出机构设计 (29)6.1推出机构的设计要求 (29)6.2推出力的计算 (30)6.3一次推出机构 (30)7 侧向分型与抽芯机构设计 (31)7.1斜导柱设计 (31)7.2斜导柱长度计算 (31)7.3侧滑块的设计 (32)8 温度调节系统 (32)9 模具材料的选用 (33)10 结论 (33)谢辞 (34)参考文献 (35)附录 (36)桂林电子科技大学毕业设计(论文)报告用纸第1 页共42 页引言我国塑料工业在近二十年的时间内发展迅速,据调查显示,早就在2004年,塑料制品的年产量已经成为我国第一,按照生产物的体积来计算,塑料的早已超过有色金属以及钢铁的总和,成为我国第一大生产品。
手机塑料外壳注塑模设计

手机塑料外壳注塑模设计手机是现代人生活中不可或缺的一个工具,而手机的外壳材料一直是手机设计中非常重要的一个环节。
最常见的手机外壳材料是塑料,同时塑料外壳的注塑模设计对手机的外观和性能也起着至关重要的作用。
塑料外壳注塑模设计可以分为以下几个方面:模具尺寸、注塑件的壁厚与充填情况、注塑成型工艺和材料选择等。
首先,模具尺寸的设计对于手机塑料外壳的样式和尺寸有着直接的影响。
在确定外壳的大小和形状后,需要设计出一个能够完全适应外壳形状的模具,模具的尺寸和形状将决定注塑过程中外壳的大小和形状。
需要注意的是,模具尺寸与注塑过程中的温度和压力也有着密切的关系,因此在考虑模具尺寸的同时需要充分考虑注塑成型所需的参数条件。
其次,注塑件的壁厚与充填情况也是影响手机塑料外壳质量和外观的重要因素。
注塑件的壁厚不应过薄或过厚,过薄会影响外壳的强度和耐用性,过厚则会增加注塑成本,同时容易导致注塑情况不佳。
因此,需要根据手机的功能及外壳的设计来确定注塑件的壁厚。
此外,充填情况也会影响注塑件的质量和外观,需要根据原料特性和注塑模具的设计来确定充填条件。
注塑成型工艺是塑料外壳的注塑模设计中非常重要的一环。
注塑成型过程中的温度、压力、时间和速度等参数对产品的质量有着显著的影响。
这些参数的选择取决于注塑原料的性质、注塑件的大小和形状以及模具的设计。
在注塑过程中要充分考虑这些参数,并进行调整,以确保产品的质量达到要求。
最后,材料的选择也是塑料外壳注塑模设计的重要因素。
不同的材料会对产品的性能、外观和成本产生不同的影响。
常用的塑料材料包括ABS、PC、PA、PP等,不同的材料具有不同的性质和特点。
例如,ABS具有较高的耐用性和强度,PC具有较高的透明度和耐高温性能。
在进行材料选择时需要综合考虑注塑件的功能、外观和成本等因素。
总的来说,手机塑料外壳注塑模设计是一个综合考虑多个因素的复杂过程,需要考虑模具尺寸、注塑件的壁厚与充填情况、注塑成型工艺和材料选择等诸多方面。
手机外壳生产工艺

手机外壳生产工艺
手机外壳的生产工艺主要包括原材料选型、模具设计、注塑成型、表面处理和组装等环节。
首先是原材料选型。
手机外壳通常由塑料或金属材料制成。
塑料外壳通常采用工程塑料,如ABS、PC或PP等,这些材料
具有良好的机械性能和耐热性。
金属外壳一般采用铝合金或铜合金等,这些材料具有较好的机械性能和导热性能。
在选材时需要考虑到手机外壳的强度、重量、制造成本等因素。
其次是模具设计。
模具是手机外壳生产的重要工具,影响到产品的外观和尺寸精度。
根据外壳的形状和结构特点,设计师需要制定合适的模具结构和尺寸。
同时还需要考虑到模具的制造工艺、成本和使用寿命等因素。
注塑成型是手机外壳生产的核心环节。
通过注塑机将熔化的塑料材料注入到模具中,待塑料冷却固化后取出外壳。
注塑过程需要控制注塑温度、压力和注射时间等参数,以确保外壳的尺寸精度和表面质量。
接下来是表面处理。
手机外壳通常需要进行喷漆、喷涂或电镀等表面处理,以提升外观质量和耐磨性。
喷漆和喷涂可以实现各种颜色和纹理效果,而电镀可以提供金属的光泽和耐腐蚀性。
最后是组装。
生产完成的手机外壳需要经过组装工序与其他部件结合,形成完整的手机产品。
组装时需要保证外壳与其他部件的精准配合和固定,同时还需要进行功能测试和质量检查等,
以确保产品的性能和质量。
综上所述,手机外壳的生产工艺涉及到多个环节,需要精细的材料选型、模具设计、注塑成型、表面处理和组装等工艺步骤。
通过合理的工艺流程和严格的质量控制,可以生产出外观精美、功能齐全、质量可靠的手机产品。
abs、pc-abs塑料件电镀工艺流程

ABS、PC/ABS塑料件电镀工艺流程工艺流程式产品代号作用及特点除油/预溶胀MT-810 去除油污,并对工件表面进行整理亲水MT-812 改善整理后塑料表面的亲水情况一次粗化硫酸+铬酸盐二次粗化铬酸盐+硫酸中和还原MT-820 Na2SO3e及其它还原剂整面MT-830 改善粗化后的塑料表面状态,使之更加均匀活化MT-833 适合各种塑料的高稳定性、高活化强度的胶体钯解胶MT-840 该过程为室温高速解胶,约30秒左右化学镍MT-860 弱碱性,中低温(30-50℃)工艺,沉积速度快(≥10μm/H), 使用周期可达8-10周期焦铜时间3-5分钟,温度35-40℃酸铜+半亮镍(+高硫镍)+光亮镍(+镍封)+铬注:1、是否用高硫镍和镍封,视产品CASS试验阶段而定;2、整个工艺流程中,亲水后应直接粗化,其余各步骤之间应有水洗;3、整个作业过程不必更换挂具;4、该工艺对PC/ABS复合材料要求PC 含量≤40%;对于PC 含量≥40%或者纯PC料為了防止電鍍後的變形,倒是需要注意塑料件模具的流道和各部入水的設計。
比如刻意設計一些輔助連接骨位,以利於導電等.电镀又真空镀与水镀两种。
4x h3E%h.Y 真空镀可以配出各类颜色,颜色的可选择性不如塑胶啤件那么多,要注意,部分颜色中含有重金属成分,玩具产品可能无法通过检测。
U.q塑料电镀的应用装饰性应用装饰性应用(1) 汽车及其他交通工具类在汽车追求轻量化而又豪华美观发展过程中,塑料电镀起到了至关重要的作用。
从车门拉手、汽车商标、标徽、车内饰、反光镜、表盘装饰、操作杆头、方向盘装饰、高级车轮壳罩等,都在大量采用塑料电镀制品。
不仅仅是汽车装饰零件,在摩托车和自行车上也有大量采用的例子,因为增加塑料配件的用量对于降低车体自重是非常有效的措施,但是,如果没有电镀金属作为其表面的装饰和防护,要想在汽车摩托车行业大量采用塑料是很困难的。
现在为汽车塑料进行电镀加工的厂商已经有很大规模,有些加工企业已经可以承揽从模具设计制造到塑料成型、电镀加工一体化的订单。
塑料模具毕业设计:手机壳注塑模具设计
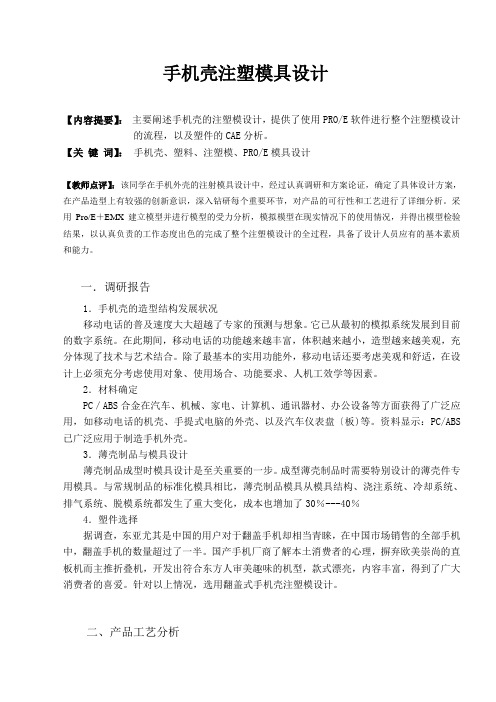
手机壳注塑模具设计【内容提要】:主要阐述手机壳的注塑模设计,提供了使用PRO/E软件进行整个注塑模设计的流程,以及塑件的CAE分析。
【关键词】:手机壳、塑料、注塑模、PRO/E模具设计【教师点评】:该同学在手机外壳的注射模具设计中,经过认真调研和方案论证,确定了具体设计方案,在产品造型上有较强的创新意识,深入钻研每个重要环节,对产品的可行性和工艺进行了详细分析。
采用Pro/E+EMX建立模型并进行模型的受力分析,模拟模型在现实情况下的使用情况,并得出模型检验结果,以认真负责的工作态度出色的完成了整个注塑模设计的全过程,具备了设计人员应有的基本素质和能力。
一.调研报告1.手机壳的造型结构发展状况移动电话的普及速度大大超越了专家的预测与想象。
它已从最初的模拟系统发展到目前的数字系统。
在此期间,移动电话的功能越来越丰富,体积越来越小,造型越来越美观,充分体现了技术与艺术结合。
除了最基本的实用功能外,移动电话还要考虑美观和舒适,在设计上必须充分考虑使用对象、使用场合、功能要求、人机工效学等因素。
2.材料确定PC/ABS合金在汽车、机械、家电、计算机、通讯器材、办公设备等方面获得了广泛应用,如移动电话的机壳、手提式电脑的外壳、以及汽车仪表盘〔板)等。
资料显示:PC/ABS 已广泛应用于制造手机外壳。
3.薄壳制品与模具设计薄壳制品成型时模具设计是至关重要的一步。
成型薄壳制品时需要特别设计的薄壳件专用模具。
与常规制品的标准化模具相比,薄壳制品模具从模具结构、浇注系统、冷却系统、排气系统、脱模系统都发生了重大变化,成本也增加了30%---40%4.塑件选择据调查,东亚尤其是中国的用户对于翻盖手机却相当青睐,在中国市场销售的全部手机中,翻盖手机的数量超过了一半。
国产手机厂商了解本土消费者的心理,摒弃欧美崇尚的直板机而主推折叠机,开发出符合东方人审美趣味的机型,款式漂亮,内容丰富,得到了广大消费者的喜爱。
针对以上情况,选用翻盖式手机壳注塑模设计。
手机壳工艺请解
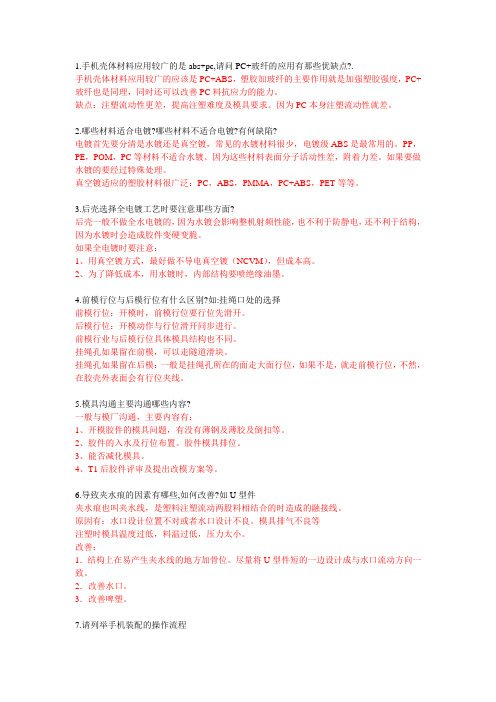
1.手机壳体材料应用较广的是abs+pc,请问PC+玻纤的应用有那些优缺点?.手机壳体材料应用较广的应该是PC+ABS,塑胶加玻纤的主要作用就是加强塑胶强度,PC+玻纤也是同理,同时还可以改善PC料抗应力的能力。
缺点:注塑流动性更差,提高注塑难度及模具要求。
因为PC本身注塑流动性就差。
2.哪些材料适合电镀?哪些材料不适合电镀?有何缺陷?电镀首先要分清是水镀还是真空镀,常见的水镀材料很少,电镀级ABS是最常用的。
PP,PE,POM,PC等材料不适合水镀。
因为这些材料表面分子活动性差,附着力差。
如果要做水镀的要经过特殊处理。
真空镀适应的塑胶材料很广泛:PC,ABS,PMMA,PC+ABS,PET等等。
3.后壳选择全电镀工艺时要注意那些方面?后壳一般不做全水电镀的,因为水镀会影响整机射频性能,也不利于防静电,还不利于结构,因为水镀时会造成胶件变硬变脆。
如果全电镀时要注意:1、用真空镀方式,最好做不导电真空镀(NCVM),但成本高。
2、为了降低成本,用水镀时,内部结构要喷绝缘油墨。
4.前模行位与后模行位有什么区别?如:挂绳口处的选择前模行位:开模时,前模行位要行位先滑开。
后模行位:开模动作与行位滑开同步进行。
前模行业与后模行位具体模具结构也不同。
挂绳孔如果留在前模,可以走隧道滑块。
挂绳孔如果留在后模:一般是挂绳孔所在的面走大面行位,如果不是,就走前模行位,不然,在胶壳外表面会有行位夹线。
5.模具沟通主要沟通哪些内容?一般与模厂沟通,主要内容有:1、开模胶件的模具问题,有没有薄钢及薄胶及倒扣等。
2、胶件的入水及行位布置。
胶件模具排位。
3、能否减化模具。
4、T1后胶件评审及提出改模方案等。
6.导致夹水痕的因素有哪些,如何改善?如U型件夹水痕也叫夹水线,是塑料注塑流动两股料相结合的时造成的融接线。
原因有:水口设计位置不对或者水口设计不良。
模具排气不良等注塑时模具温度过低,料温过低,压力太小。
改善:1.结构上在易产生夹水线的地方加骨位。
手机外壳材质与工艺
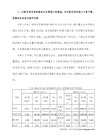
车床:有一个夹头夹住各种材料车成一个椭圆,整圆的杯子等。
铣床:跟CNC相近,但它是用手动和自动开关控制的锣床。
喷砂:把一个透明杯子喷成半透明的沙粒状。
IMD
IMD的中文名称:注塑表面装饰技术 即IMD(In-Mole Decoratiom),IMD是目前国际风行的表面装饰技术,主要应用于家电产品的表面装饰及功能性面板,常用在手机视窗镜片及外壳、洗衣机控制面板、冰箱控制面板、空调控制面板、汽车仪表盘、电饭煲控制面板多种领域的面板、标志等外观件上。
外观纹理有麻面和光面之分
麻面,即表面模具内火花纹,亚光磨砂质感.火花纹可以控制粗细,也可以是规则的图案阵列.
光面,即表面模具内抛光,高光效果.
塑壳不适宜表面丝印字符.
2,喷漆
喷漆一般是喷两层,特别点的喷三层
颜色 由底漆决定
表面效果 由面漆决定
喷漆中可添加银粉和珍珠粉等, 所以比注塑壳的颜色漂亮.
手机制造相关工艺
一,壳体材料
PC
聚碳酸酯(Polycarbonate) ,不能电镀
聚碳酸酯是一种热塑性工程塑料,聚碳酸酯有优良的电绝缘性能和机械性能,尤其以抗冲击性能最为突出,韧性很高,透明度高(誉为“透明金属”)、无毒、加工成型方便。它不但可替代某些金属,还可替代玻璃、木材等。
日常常见的应用有光碟,眼睛片,水瓶,防弹玻璃,护目镜、银行防子弹之玻璃、车头灯等等.
手机上多用于壳体塑材.
PMMA
俗称有机玻璃,又叫压克力或亚克力. 透明度是所有塑料中最高的
无与伦比的高光亮度, 韧性好,不易破损;色彩鲜艳,可满足不同品位的个性追求。
手机壳注塑模具设计说明书

本科毕业论文(设计)题目手机壳模具设计与结构设计作者机械工程学院学院专业料成型与控制工程学号指导教师二〇一六年二月二十二日摘要本次设计就是将手机壳作为设计模型,将注塑模具的相关知识作为依据,阐述塑料注塑模具的整体设计过程。
该毕业设计的内容是手机壳的注塑模具,材料为PC,根据其结构形状特点以及通过对手机壳成型工艺的正确分析,确定型腔的总体布局,选择分型面,确定脱模方式,设计浇注系统等;同时本文对注塑模具进行简要介绍,对注塑模具中的主要零件进行设计计算,在设计过程中着重考虑其生产实际中的经济性和合理性。
关键词:注塑模具;注射成型;分型面AbstractThis design is the air refreshing agent box as a design model, the injection mold related knowledge as the basis, elaborated the whole design process of plastic injectio n mould.The content of graduation design is the injection mold of air refreshing agent box, the material is PC, according to the structure characteristics and the correct analysis of the air refreshing agent box molding process, to determine the overall layout of the cavity, the choice of parting surface, gating system design to determine the stripping method, etc.; at the same time this paper gives a brief introduction about the injection mould, the main parts of injection mold design and calculation, in the design process focuses on the actual production in the economy and rationality.Keywords:The plastic mold;the parametrization;;divides the profile目录摘要 (I)Abstract..................................................... I I第一章绪论 (1)1.1 模具介绍 (3)1.2 模具在加工工业中的地位 (3)1.3 模具的发展趋势 (3)第二章该塑件材料分析和工艺性分析 (4)2.1 材料分析 (6)2.2 工艺分析 (7)2.2.1尺寸及精度 (8)2.2.2表面粗糙度 (9)2.2.3形状 (9)2.2.4斜度 (9)第三章拟定成型工艺 (10)3.1制件成型方法 (10)3.2制件的成型参数 (10)3.3确定型腔数目.............................. 错误!未定义书签。
手机壳生产工艺流程

手机壳生产工艺流程手机壳的生产工艺流程通常包括以下几个步骤:设计、模具制作、注塑成型、表面处理、装配和包装。
首先是设计阶段。
根据客户的需求和市场趋势,设计师将绘制出手机壳的设计图纸,包括尺寸、形状、颜色等。
设计师还需考虑到手机壳的结构,如是否需要开槽给按键、插孔等留出空间。
接下来是模具制作。
模具是生产手机壳的关键工具,它决定了最终产品的质量和形状。
制作模具需要使用CAD软件进行设计,并使用CNC机床进行加工。
通常会先制作一块模具样板进行测试和确认。
第三步是注塑成型。
工人将预先加热的塑料颗粒(如PC、ABS等)放入注塑机的料斗中。
注塑机会将塑料颗粒加热并融化,然后通过一定的压力将熔融塑料注入到模具的腔室中。
随着注塑机的开合,模具中的塑料将逐渐冷却固化,最终形成手机壳的外观。
注塑成型完成后,手机壳的表面通常还需要进行处理。
常见的处理方式有喷漆、丝印和贴膜等。
喷漆是将涂料均匀喷涂在手机壳外表面,增加手机壳的美观度和防刮性。
丝印是将墨水通过丝网印刷技术印在手机壳上,可以印制各种图案和文字。
贴膜则是将一层薄膜覆盖在手机壳的外表面,提供额外的保护,如防指纹、防刮等功能。
之后是装配阶段。
工人将已经注塑成型和处理过表面的手机壳组装上其他配件,如按键、插孔、摄像头等。
装配阶段需要仔细检查每个配件的质量和安装是否正确,确保手机壳的功能完整。
最后是包装环节。
手机壳通常会以小包装盒的形式出售,因此需要将每个手机壳放入对应的包装盒中,还可以加入说明书和防潮包等。
包装的设计和质量也需要考虑,以吸引消费者的注意并确保产品安全。
以上就是手机壳生产的工艺流程。
通过不断优化和改进工艺流程,可以提高手机壳的质量和生产效率,满足市场需求。
PC+ABS手机壳工艺设计

PC+ABS 手机壳工艺设计+ABS塑胶原料介绍PC+ABS是PC塑胶原料与ABS塑胶原料共混物,可以综合PC和ABS的优良性能,一方面可以提高ABS的耐热性、抗冲击和拉伸强度;另一方面可以降低PC成本和熔体粘度,改善加工性能,减少塑件内应力和冲击强度对塑件厚度的敏感性。
PC+ABS广泛的用于手机外壳、汽车工业、计算机、复印机和电器设备等。
PC+ABS的密度为cm3左右,玻璃化转变温度为130 C,熔融温度为230 C ~270 C, PC+ABC具有较高的强度、刚性,很好的耐热性,优良的尺寸稳定性,良好的光稳定性,低的成型收缩率,良好的成型性能,使得PC + ABS 原料做出的塑件的尺寸稳定性比较高。
PC+ABS^于其中含有的PC的含量很高,流动性不是很好,注射成型薄壁、复杂壳形塑件普遍容易出现脆裂或断裂的现象。
2.生产工艺1.方法现阶段,生产手机壳主要采用注射成型的方法。
2.生产条件a.在注射步骤时,要有适当的树脂温度和时间,防止树脂降解,所述温度时间,能保证[(B-A)- A]X 100%< 30%公式中:A为原料的熔融指数,B为成品的熔融指数。
如果能保持[ (B-A)- A]X 100%< 15%更好。
树脂料管设定温度为:射嘴为265 C ~275 C, N1为270 C ~280C, N2为265 C ~275C, N3为260 C ~270C,将塑胶的熔胶温度控制在270 C ~290C范围内,N1为料筒中段前端的温度,N2为料筒中段中间部份温度,N3为料筒中段后端的温度。
b.注射加工时要有适当的树脂温度,使用合适的料管设定温度,因为手机壳使用的注塑机的射嘴尺寸一般较小, 所以设定温度不要太高, 以免高温的情况下长时间的滞留导致材料降解。
当出现品质问题,例如充不满、缩水等,如需要将料管温度提高至极限时,要确认材料是否降解,最理想的方法是通过改善模具设计来提高填充能力。
c.注射前,将模具上附着的油脂和润滑脂等环境化学物质擦拭干净。
手机壳 工艺流程

手机壳工艺流程手机壳是一种保护手机外壳的装饰物,现在已经成为了人们生活中不可缺少的配件之一。
手机壳的加工过程经过多道工序,我们来详细介绍一下手机壳的工艺流程。
首先是材料准备。
手机壳一般由塑料材料制成,主要有PC、ABS等塑料材料。
选择适合的材料是确保手机壳质量的重要因素之一。
接下来是模具制作。
手机壳的外形多种多样,为了让手机壳能够精准地与手机匹配,需要根据需求制作模具。
通常会采用CAD设计软件进行设计,并利用数控铣床进行加工。
然后是注塑成型。
注塑是制作塑料制品的常用方法。
将预先加热和塑化的塑料料粒通过注射机注入到模具中,经过冷却固化后取出即可得到手机壳的初始形状。
接着是表面处理。
手机壳的外观要求通常比较高,需要进行表面处理以增加其美观度和质感,常见的处理方法有喷涂、染色和镀膜等。
这些处理方法可以根据客户需求进行选择,同时也要考虑到处理成本和效果。
之后是图案印刷。
为了使手机壳更加个性化,通常会在手机壳表面印上图案或文字。
印刷方法主要有丝网印刷、烫金印刷和喷墨印刷等。
不同的印刷方法有不同的印刷效果和耐久性,请根据具体需求进行选择。
最后是装配和质检。
经过上述步骤后,手机壳会进行装配,包括安装按钮、摄像头等配件。
然后进行质检,确保手机壳的质量达到标准,没有明显的缺陷。
通过上述一系列的工艺过程,手机壳制造完成。
当然,在整个过程中还包括了材料采购、原材料库存管理,以及生产计划和订单管理等相关工作。
总之,手机壳的制作并不是一项简单的工作,需要经过多道工序和专业的操作才能够完成。
每一个步骤都需要严格控制质量,以确保最终产品能够满足客户的需求和期望。
手机壳工艺流程的完整性和高效性是实现批量生产的关键。
手机基础材料工艺

键帽ABS/PC 键帽ABS/PC 支架ABS/钢片 支架ABS/钢片 ABS/ PCB
钢片/铝片 钢片/ 硅胶 DOME
PET(UV热转印) PET(UV热转印) 热转印
键帽ABS/PC 键帽ABS/PC PCB
硅胶 DOME
e.材料:钢片 钢片 工艺:1.机械拉丝 2.镭雕拉丝 f. 材料:铝片 铝片 工艺:1.机械拉丝 2.镭雕拉丝
3.镭雕图案 3.镭雕图案 4.批花
PC+Rubber/ABS+Rubber
键帽ABS/PC 键帽ABS/PC 支架ABS/钢片 支架ABS/钢片 ABS/ PCB 硅胶 DOME
钢片/铝片 钢片/
按键 a.材料:PC+Rubber/ABS+Rubber PC+Rubber/ABS+Rubber 工艺:1.喷漆 2.电镀(含电铸模) 3.字符镭雕 b.材料:透明PC 透明PC 透明 工艺:1.注塑 2.背面丝印 2.背面丝印
c.材料:PET PET 工艺:1.(纹理或造型)UV热转印 d.材料:玻璃 玻璃 工艺:1.切割 2.背面丝印
d.材料:铝合金 铝合金 工艺:1.氧化(着色/+强度/二次氧化) 2.机械拉丝/镭雕拉丝 4.批花 e.材料:锌合金 锌合金 工艺:1.电镀(水镀/真空镀+UV) 2.镭雕拉丝 3.镭雕图案
3.镭雕图案
ABS+PC
ABS+五金
五金
屏_镜片 a.材料:PMMA PMMA 工艺:1.背面丝印 b.材料:玻璃 玻璃 工艺:1.背面丝印 c.材料:PET PET 工艺:1.背面丝印 2.背面电镀 2.背面电镀 2.背面电镀
手机设计—基础材料/工艺
A壳/B壳/电池盖/装饰件 a.材料:ABS& b.材料:透明PC 透明PC 透明 工艺:1.IML 2.电镀 c.材料:不锈钢 不锈钢 工艺:1.电镀(水镀/真空镀+UV) 2.机械拉丝/镭雕拉丝 4.ED+UV 3.镭雕图案
手机外壳的材料与工艺
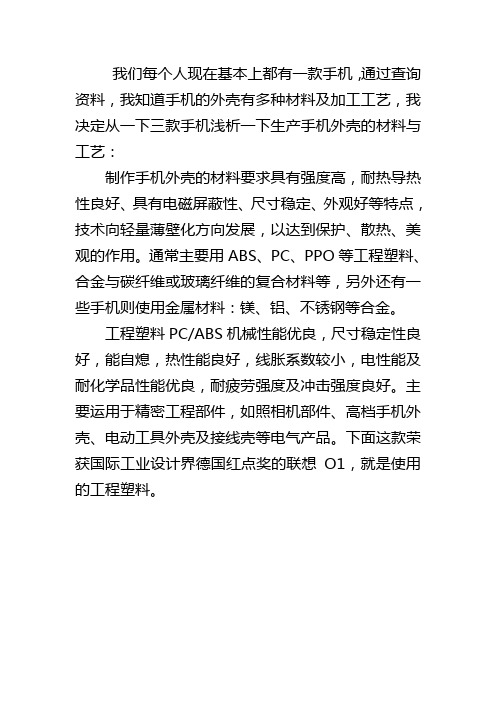
我们每个人现在基本上都有一款手机,通过查询资料,我知道手机的外壳有多种材料及加工工艺,我决定从一下三款手机浅析一下生产手机外壳的材料与工艺:制作手机外壳的材料要求具有强度高,耐热导热性良好、具有电磁屏蔽性、尺寸稳定、外观好等特点,技术向轻量薄壁化方向发展,以达到保护、散热、美观的作用。
通常主要用ABS、PC、PPO等工程塑料、合金与碳纤维或玻璃纤维的复合材料等,另外还有一些手机则使用金属材料:镁、铝、不锈钢等合金。
工程塑料PC/ABS机械性能优良,尺寸稳定性良好,能自熄,热性能良好,线胀系数较小,电性能及耐化学品性能优良,耐疲劳强度及冲击强度良好。
主要运用于精密工程部件,如照相机部件、高档手机外壳、电动工具外壳及接线壳等电气产品。
下面这款荣获国际工业设计界德国红点奖的联想O1,就是使用的工程塑料。
从图片中我们可以看到联想O1给人的感觉是非常棒的,虽然仍然采用工程塑料的材质,不过并没有想象中的质感不足。
整机的体积为115.8*61.5*12mm,大小适中,普通人单手就可以握住。
主色调为黑色,银边点缀两侧,稳重而不显呆板。
上方的听筒比较个性的设计为小长条,下方也有对应的话筒设计,保证了上下方的对称。
从这款手机我们可以感觉到加工工艺的重要作用,虽然材料为传统的工程塑料,但采用了磨砂质感的后盖,这样的做法是的其非常舒适,且不用担心沾染指纹。
而且边框的抛光处理给人奢侈华丽的感觉,而不是像很多其他工程塑料给人一种简陋通俗的感觉。
由此,我们可以知道传统材料经过适当的加工工艺可以给人耳目一新的感觉,我们应当加大对加工工艺的重视。
下面一款手机是市场上很畅销的LG KG70 Shine。
LG KG70 Shine从上市开始一直受到很多消费者的喜爱。
它的外观就如同它的名字Shine(闪耀)一般光彩夺目。
正如大家从图片中所见到的一样,KG70正因为那帅帅的设计,刚毅有力的显效,闪亮的金属机身让人爱不释手,它时尚靓丽的外观令众多消费者倾倒,同时也成就了惊人的销量成绩,全金属的银色外观简直是一个艺术品一样美丽。
手机结构工艺介绍
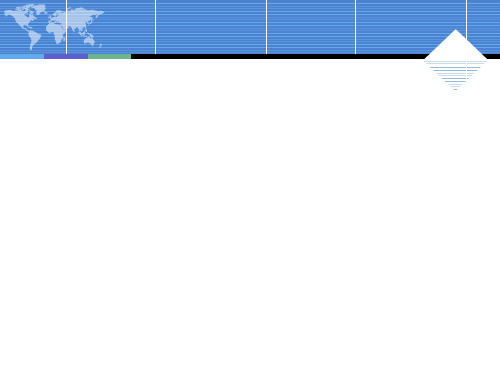
喇叭网孔为不 锈钢腐蚀
A68不锈钢 面饰件图 案为腐蚀 工艺
金属饰件——电铸镍
2、电铸镍 (1)电铸原理:
是在含有镍离子的电解液中,通以低压直流电,使镍离子得到电 子被还原,不断在阴极沉积成金属镍的过程。
(2)性能: 镍在潮湿空气中表面形成致密的氧化膜,不但能阻止继续被氧化
,而且能耐碱、盐溶液的腐蚀。金属泽感强,不易锈蚀。
切亮边、 车CD纹、 葵花纹
金属饰件——不锈钢、铝合金
(8)真空离子镀(PVD): 利用金属气相物理沉积的
方法,在清洗完全干净的五金装 饰件表面沉积一层或数层所需的 功能性或装饰性镀层的方法,表 面颜色由电镀靶材和气体决定, 颜色可以在基本色基础上微调, 真空离子镀颜色只能根据PVD色 板选择所需颜色,不如铝合金饰 件氧化工艺颜色丰富。
·ABS:注塑流动性好,较易成 型,价格比PC低,适合电镀。
PC原料 ABS原料
注塑壳体——注塑材料
·PC+ABS:PC与ABS共混物可以综合PC和ABS的优良 性能,一方面有ABS注塑好的流动性,另一方面 又兼顾了PC的抗冲击性好的特点。
PMMA材料
PMMA材料
·PMMA:俗称有机玻璃,又 叫亚克力。硬度比透明PC 高,常用于做透明件。
(6)激光雕刻: 激光雕刻是通过高能激光束作用于金属表面,造成表面原子层蒸
发而产生永久性标记的一种加工方法。
(7)高光切削: 主要在铝合金上切高亮边、CD纹、葵
花纹等。 高光切削是在 CNC机床上使用钻石刀
、 人造钻石刀、硬质合金刀具,对铝合 金、不锈钢等金属进行切削的加工,使装 饰件产生出高光亮面的工艺。切削过程中 由于发热会使铝表面产生一层氧化膜,使 加工面长期保持光亮。
手机外壳配方设计

手机外壳配方设计一、实验目的1、掌握塑料改性配方设计的基本知识;2、了解聚乙烯塑料加工常用的设备(如高速混合机、双螺杆挤出机、塑料注射机等)的基本结构原理与操作方法;3、掌握聚烯烃配方试验的混合、混炼、注射制样等基本操作方法;4、掌握塑料基本性能的测试方法。
二、改性塑料配方设计实验任务、目标、提示与要求改性塑料新材料配方设计实验任务、目标、提示与要求见下表所示。
三、设计过程1.前言目前,手机常用塑胶材料主要有PC、ABS和PC+ABS三大类.日本手机主要采用PC+ABS,甚至采用ABS做手机外壳;韩国几家制造商最早采用纯PC材料。
GE公司原来不推荐采用PC材料做手机外壳,主张采用PC+ABS材料,但最近一两年也推出适合做子机外壳的PC材料。
近年来,各大手机厂商采用PC材料做手机壳的比例正在逐渐上升。
表1为几种材料的一般特性表:2.材料介绍2.1 PC PC学名聚碳酸酯。
材料的性能特点:①强度高,抗拉伸强度69MPa、抗弯曲强度96MPa。
②耐高温,长期使用可耐130摄氏度温度环境。
②透明性好,无毒。
④原料配色及表面涂覆不如ABs。
⑤Pc应选高流动性牌号。
适用于翻盖机和在恶劣环境下使用的手机。
2.2 ABS ABS(丙烯脂—丁二烯—苯乙烯共聚物)材料的性能特点:①强度低,抗拉伸强度43MPa,抗弯曲强度79MPa。
②不耐温,长期使用温度不得高于60摄氏度。
③流动性、着色及表面喷涂和电镀性能均好。
2.3 PC+ABS PC与ABS的合成材料,取前面两者之特点,具有优良的成型加工性能,流动性好,强度较高(抗拉伸强度56MPa,抗弯曲强度86MPa)。
PC+ABS材料主要用于直板机和一般外观、色彩要求高而对环境无特殊要求的翻盖机3.PC与ABS比例的选择PC 中加入ABS 制成的PC/ ABS 合金确能改善其性能并保持二者原有的性能优势。
查文献得[1]50%ABS 对50% PC 的合金效果最佳, 此时材料的冲击强度呈最高值。
手机注塑工艺(3篇)
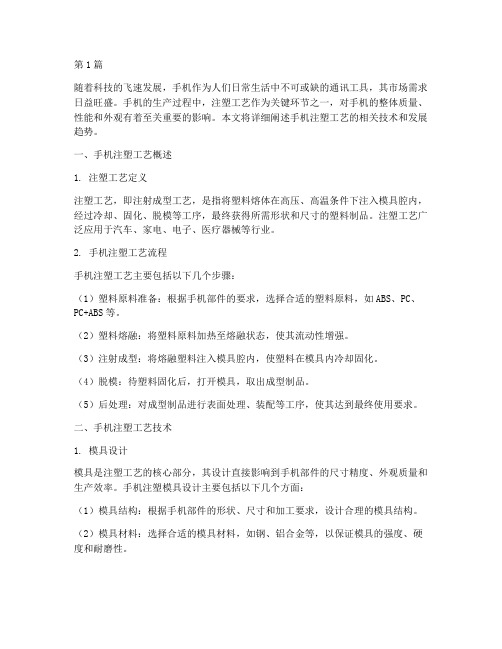
第1篇随着科技的飞速发展,手机作为人们日常生活中不可或缺的通讯工具,其市场需求日益旺盛。
手机的生产过程中,注塑工艺作为关键环节之一,对手机的整体质量、性能和外观有着至关重要的影响。
本文将详细阐述手机注塑工艺的相关技术和发展趋势。
一、手机注塑工艺概述1. 注塑工艺定义注塑工艺,即注射成型工艺,是指将塑料熔体在高压、高温条件下注入模具腔内,经过冷却、固化、脱模等工序,最终获得所需形状和尺寸的塑料制品。
注塑工艺广泛应用于汽车、家电、电子、医疗器械等行业。
2. 手机注塑工艺流程手机注塑工艺主要包括以下几个步骤:(1)塑料原料准备:根据手机部件的要求,选择合适的塑料原料,如ABS、PC、PC+ABS等。
(2)塑料熔融:将塑料原料加热至熔融状态,使其流动性增强。
(3)注射成型:将熔融塑料注入模具腔内,使塑料在模具内冷却固化。
(4)脱模:待塑料固化后,打开模具,取出成型制品。
(5)后处理:对成型制品进行表面处理、装配等工序,使其达到最终使用要求。
二、手机注塑工艺技术1. 模具设计模具是注塑工艺的核心部分,其设计直接影响到手机部件的尺寸精度、外观质量和生产效率。
手机注塑模具设计主要包括以下几个方面:(1)模具结构:根据手机部件的形状、尺寸和加工要求,设计合理的模具结构。
(2)模具材料:选择合适的模具材料,如钢、铝合金等,以保证模具的强度、硬度和耐磨性。
(3)冷却系统:设计合理的冷却系统,以控制塑料的冷却速度和固化时间,提高产品质量。
(4)模具表面处理:对模具表面进行抛光、镀膜等处理,以提高其光洁度和耐磨性。
2. 注塑设备注塑设备是注塑工艺的关键设备,主要包括注射机、模具和控制系统等。
手机注塑设备应具备以下特点:(1)高精度:注射机应具备较高的注射精度,以保证手机部件的尺寸精度。
(2)高效率:注射机应具备较高的生产效率,以满足手机市场的需求。
(3)稳定性:注射机应具备良好的稳定性,以保证产品质量的稳定性。
(4)智能化:控制系统应具备智能化功能,如自动调节温度、压力等参数,以提高生产效率。
PC+ABS手机壳工艺设计
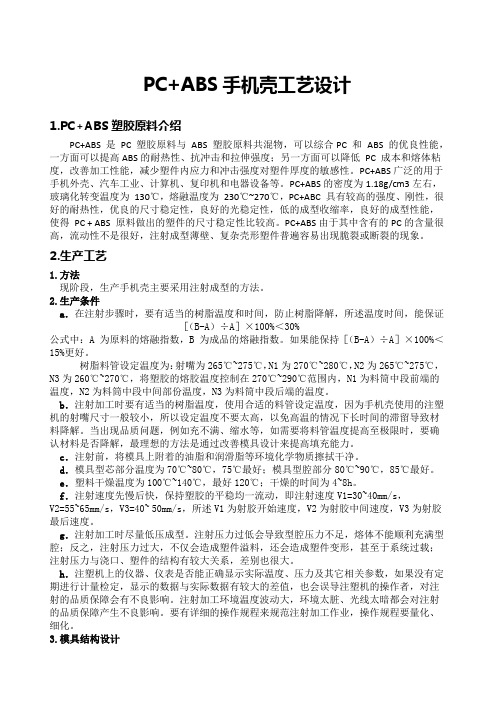
PC+ABS手机壳工艺设计1.PC+ABS塑胶原料介绍PC+ABS 是PC 塑胶原料与ABS 塑胶原料共混物,可以综合PC 和ABS 的优良性能,一方面可以提高ABS的耐热性、抗冲击和拉伸强度;另一方面可以降低PC 成本和熔体粘度,改善加工性能,减少塑件内应力和冲击强度对塑件厚度的敏感性。
PC+ABS广泛的用于手机外壳、汽车工业、计算机、复印机和电器设备等。
PC+ABS的密度为1.18g/cm3左右,玻璃化转变温度为130℃,熔融温度为230℃~270℃,PC+ABC 具有较高的强度、刚性,很好的耐热性,优良的尺寸稳定性,良好的光稳定性,低的成型收缩率,良好的成型性能,使得PC + ABS 原料做出的塑件的尺寸稳定性比较高。
PC+ABS由于其中含有的PC的含量很高,流动性不是很好,注射成型薄壁、复杂壳形塑件普遍容易出现脆裂或断裂的现象。
2.生产工艺1.方法现阶段,生产手机壳主要采用注射成型的方法。
2.生产条件a.在注射步骤时,要有适当的树脂温度和时间,防止树脂降解,所述温度时间,能保证[(B-A)÷A]×100%<30%公式中:A 为原料的熔融指数,B 为成品的熔融指数。
如果能保持[(B-A)÷A]×100%<15%更好。
树脂料管设定温度为:射嘴为265℃~275℃,N1为270℃~280℃,N2为265℃~275℃,N3为260℃~270℃,将塑胶的熔胶温度控制在270℃~290℃范围内,N1为料筒中段前端的温度,N2为料筒中段中间部份温度,N3为料筒中段后端的温度。
b.注射加工时要有适当的树脂温度,使用合适的料管设定温度,因为手机壳使用的注塑机的射嘴尺寸一般较小,所以设定温度不要太高,以免高温的情况下长时间的滞留导致材料降解。
当出现品质问题,例如充不满、缩水等,如需要将料管温度提高至极限时,要确认材料是否降解,最理想的方法是通过改善模具设计来提高填充能力。
手机后盖 制造
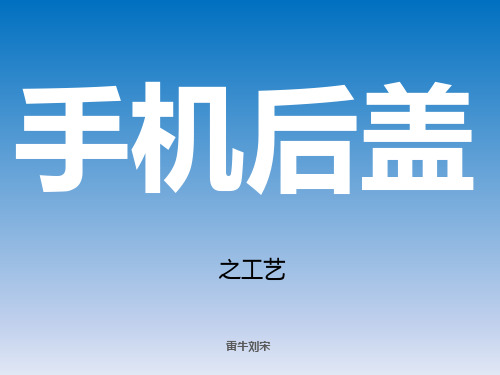
型腔的布局 • 均等的分得 所需的压力
• 型腔与主流
道之间的距 离注射入模 • 对称式布局
后盖模具设计
浇注系统的设计 • 主浇道 第一分浇道 第二分浇道
第三分浇道
• 浇口 型腔 • 冷料穴
• 适应所用塑料的成型特性的要求
• 模具成型塑件的型腔数 • 塑件大小及形状 • 塑件外观
后盖模具设计
模具排气系统 • 迅速、完全排气
• 不妨碍制件的脱模。
• 便于制造、清理,尽量设 计在凹模的一面。 • 排气孔不应朝向操作面, 防止注射漏料伤人,并且 设计在料流的终点 • 排气孔不应有死角,表面 进行抛光处理 • 与模具的分型面、浇口进 行综合考虑
后盖模具设计
模具导向系统 • 1.定位作用:合模时维持动 定模之间的一定方位,合 模后保持模腔的正确形状。
⑧ 对于薄肉产品,在 分流道上设置顶针, 即可将产品带出。
模具材料的选用
零件名称 凹模和主型芯 型芯和镶块 导柱、导套 成型零部件 主流道浇口套 推杆、拉料杆 各种模板、推板、固定 板、模座等 性能要求 硬度为250~280HB, 易于切削加工 淬火变形小,淬透性好 的高碳合金钢 表面耐磨、有韧性、抗 曲、不易折断 强度高、耐磨性好、热 处理变形小 耐磨性好,有时还要求 耐腐蚀 一定的强度和耐磨性 一定的强度和刚度 材料选用 50和55调质钢 9CrWMn、Cr12MoV 和3Cr2W8V T8(A) Cr12MoV 45钢 T8(A) 45钢
后盖工艺性分析
塑件的壁厚 注射充模时的熔体流动、固化定型时的冷却速度和时间、 塑件的成型质量、塑件的原材料 壁厚尽量均匀 倒角 塑件的圆角 塑件的转角处和内部联接处采用圆角过度 孔 尽量采用简单孔型 孔的周边应增加壁厚 整体尺寸 考虑 公差 精度
- 1、下载文档前请自行甄别文档内容的完整性,平台不提供额外的编辑、内容补充、找答案等附加服务。
- 2、"仅部分预览"的文档,不可在线预览部分如存在完整性等问题,可反馈申请退款(可完整预览的文档不适用该条件!)。
- 3、如文档侵犯您的权益,请联系客服反馈,我们会尽快为您处理(人工客服工作时间:9:00-18:30)。
P C A B S手机壳工艺设
计
Standardization of sany group #QS8QHH-HHGX8Q8-GNHHJ8-HHMHGN#
PC+ABS手机壳工艺设计
+ABS塑胶原料介绍
PC+ABS 是 PC 塑胶原料与 ABS 塑胶原料共混物,可以综合PC 和 ABS 的优良性能,一方面可以提高ABS的耐热性、抗冲击和拉伸强度;另一方面可以降低 PC 成本和熔体粘度,改善加工性能,减少塑件内应力和冲击强度对塑件厚度的敏感性。
PC+ABS广泛的用于手机外壳、汽车工业、计算机、复印机和电器设备等。
PC+ABS的密度为cm3左右,玻璃化转变温度为 130℃,熔融温度为 230℃~270℃,PC+ABC 具有较高的强度、刚性,很好的耐热性,优良的尺寸稳定性,良好的光稳定性,低的成型收缩率,良好的成型性能,使得 PC + ABS 原料做出的塑件的尺寸稳定性比较高。
PC+ABS由于其中含有的PC的含量很高,流动性不是很好,注射成型薄壁、复杂壳形塑件普遍容易出现脆裂或断裂的现象。
2.生产工艺
1.方法
现阶段,生产手机壳主要采用注射成型的方法。
2.生产条件
a.在注射步骤时,要有适当的树脂温度和时间,防止树脂降解,所述温度时间,能保证
[(B-A)÷A]×100%<30%
公式中:A 为原料的熔融指数,B 为成品的熔融指数。
如果能保持[(B-A)÷A]×100%<15%更好。
树脂料管设定温度为:射嘴为265℃~275℃,N1为270℃~280℃,N2为265℃
~275℃,N3为260℃~270℃,将塑胶的熔胶温度控制在270℃~290℃范围内,N1为料筒中段前端的温度,N2为料筒中段中间部份温度,N3为料筒中段后端的温度。
b.注射加工时要有适当的树脂温度,使用合适的料管设定温度,因为手机壳使用的注塑机的射嘴尺寸一般较小,所以设定温度不要太高,以免高温的情况下长时间的滞留导致材料降解。
当出现品质问题,例如充不满、缩水等,如需要将料管温度提高至极限时,要确认材料是否降解,最理想的方法是通过改善模具设计来提高填充能力。
c.注射前,将模具上附着的油脂和润滑脂等环境化学物质擦拭干净。
d.模具型芯部分温度为70℃~80℃,75℃最好;模具型腔部分80℃~90℃,85℃最好。
e.塑料干燥温度为100℃~140℃,最好120℃;干燥的时间为4~8h。
f.注射速度先慢后快,保持塑胶的平稳均一流动,即注射速度V1=30~40mm/s,
V2=55~65mm/s,V3=40~ 50mm/s,所述V1为射胶开始速度,V2为射胶中间速度,V3为射胶最后速度。
g.注射加工时尽量低压成型。
注射压力过低会导致型腔压力不足,熔体不能顺利充满型腔;反之,注射压力过大,不仅会造成塑件溢料,还会造成塑件变形,甚至于系统过载;注射压力与浇口、塑件的结构有较大关系,差别也很大。
h.注塑机上的仪器、仪表是否能正确显示实际温度、压力及其它相关参数,如果没有定期进行计量检定,显示的数据与实际数据有较大的差值,也会误导注塑机的操作
者,对注射的品质保障会有不良影响。
注射加工环境温度波动大,环境太脏、光线太暗都会对注射的品质保障产生不良影响。
要有详细的操作规程来规范注射加工作业,操作规程要量化、细化。
3.模具结构设计
a.分型面的选择及排气槽设计
模具结构采用二板模结构,在考虑选择动、定模的分型方案时,经过分析,应以该塑件的最大轮廓处为动、定模的分型面,故选择手机外壳的底面为模具的动、定模分型面。
排气槽主要设置在定模芯上,排气槽设置的位置选在分流道末端、熔融塑料体的四周及熔合线处,排气槽深度为,宽度为3mm,以防溢流,排气槽周围要开深、4mm宽的引气槽,通过动、定模板的间隙将气体排出模具,在定模型芯中间的气体通过一个直径为4mm的小孔及定模芯底部的引气槽、定模芯的倒角、动模板和定模板的间隙将气体排出模
具。
b.浇注系统的设计
由于塑件尺寸精度要求较高,且外表面要求光滑,所以该模具采用1模1腔的二板模结构及潜伏式浇口浇注系统。
要求最佳的浇口数量和位置,合理的流道系统形状和排布位置,并对浇口尺寸、流道尺寸进行优化。
在主浇口和分流道的末端设有冷料穴,以防浇口被熔融塑料前锋面上的冷料堵塞。
c.脱模机构的设计
由于塑件正面有两处倒扣,背面有10处倒扣,为了便于脱模,决定在定模部份设计两个滑块、在动模部份设计5个斜顶和5个滑块进行抽芯,同时为了使塑件从动模芯中脱模,决定增加14支顶针和两支司筒针,为了保证动模斜顶的强度,动模斜顶分为两节结构形式,由斜顶和斜顶导杆组成,动模斜顶和顶针固定在顶针固定板上。
整个脱模机构采用弹簧顶出
复位系统,以确保顶出平稳、可靠。
d.冷却系统的设计
该模具的冷却系统主要根据动、定模芯的结构特点以及模具元件的分布来布置水道。
为了避免冷却水道与相关的模具元件发生干涉,而又不影响其冷却效果,决定在动、定模芯上设计一进一出的内循环式冷却水道,为了防止漏水,在动、定模板上开设密封槽,采用密封圈进行密封。
e.定模滑块的结构设计
定模滑块整个结构由斜导柱、滑块、滑块镶件、锲紧块、弹簧、定距拉杆、滑块压板、斜导柱压板、浇口套压板等零件组成。
其中定距拉杆与顶板通过螺纹连接在一起,锲紧块与顶板通过螺纹连接在一起,滑块镶件与滑块通过螺纹连接在一起,滑块压板与定模板连接在一起形成滑块移动的导滑槽,开模时,在4个弹簧力的作用下,定模座板与定模板先分开,顶板带动锲紧块和斜导柱分开,斜导柱带动滑块镶件从塑件中分离出来,合模时,在斜导柱和锲紧块的作用下,带动整个滑块结构回到原来位置。
f.模具的结构
该模具属于两板模,模架采用龙记模架,模具所有活动部分保证定位准确,动作可靠,不得有卡滞现象,固定零件紧固无松动。
其模具工作过程是:动、定模合模,熔融塑料经塑化、计量后通过注塑机注入模具密封型腔内,经保压、冷却后,开模。
4.模具工作过程
模具的工作过程包括:模具闭合→模具锁紧→注射→保压→补塑→冷却→开模→推出塑件。
手机保护壳的模具工作过程:在注射机锁模机构的作用下,导柱和导套进行合模导向,动模和定模闭合。
型腔零件由定模板与动模板组成,并由注射机合模系统提供的锁模力锁紧;然后注射机开始注射,塑料熔体经过定模上的浇注系统进入型腔;待熔体充满型腔并经过保压、补塑和冷却定形后开模。
开模时,在注射机锁模系统的带动下向后移动,模具从动模和定模分型面分开,塑件包在型芯上随动模一起后移。
同时,拉料杆将浇注系统的主流道凝料从浇口套中拉出。
当动模移动到一定距离后,注射机的顶杆接触推板,堆出机构开始中动作,使推杆和拉料杆分别将塑件和浇注系统凝料从型芯和冷料穴中推出,塑件与浇注系统凝料一起从模具中落下,至此完成一次注射过程。
合模时,复位杆使模具复位,并准备下一次注射。