露天矿卡车运输系统最佳调度
露天矿挖机卡车智能化调试系统(2)(1)

露天矿智能化调度系统目录一、系统概况 (3)二、系统组成 (4)三、系统功能 (5)3.1优化调度 (5)3.2设备管理 (7)3.3自动计量 (7)3.4地图监控 (7)3.5地图编辑 (8)3.6生产数据统计 (9)3.7预警系统 (10)3.8 水位监控 (10)3.9 车辆防碰撞预警 (11)四、系统管理模块 (11)4.1 挖机管理 (11)4.2卡车管理 (12)4.3卡车水位实时监测预警系统 (13)4.4 露天矿车辆防撞预警系统 (14)4.5 调度管理 (15)五、系统十大特点 (16)5.1全自动的实时调度 (16)5.2直观方便的调度界面 (16)5.3司机对全局信息的知情 (16)5.4电铲装载能力的自动采集 (17)5.5特殊物料的自动派车 (17)5.6长距离派车问题的解决 (17)5.7灵活的局部定铲派车 (17)5.8高适应的智能终端 (18)5.9语音提示 (18)5.10系统适应性强 (18)露天矿挖机卡车智能化调度系统一、系统概况现在化露天矿山已全部采用机械化(挖机、电铲、卡车、钻车、洒水车、加油车等),机械化设备的投入将产能推向了高峰,但随着机械化的投入,运行效率是每一个矿山人不断思考的地方,如何提高每台设备的运行效率,如何规避卡车行进过程中的碰撞,如何实现自动化调试,如何实现油耗、卡车水箱水量监测以及及时提醒,是现在矿山人迫切需要实现的智能化需求。
综合运用现代化高新信息化技术,包括全球化定位技术、GIS、无线通信、人工智能、系统工程理论和最先进的优化技术等方式,对露天矿的主要设备(挖机、电铲、卡车、钻车、洒水车、加油车等)的精准工作位置、工作状态、工作量进行全天候数据化监控,自动适应采矿生产过程中的各种变化,实现对卡车、挖机的自动化调试,达到优化生产、安全生产、提高效率、提高产能、增加利润、降低油耗的目的。
建立生产监控、智能调度、智能生产指挥管理系统,彻底改变传统的生产管理模式,提高了企业的管理水平和信息化水平,为露天矿生产管理方式提供一场新的变革,为数字化矿山建设奠定基础,同时也是21世纪现代化矿山建设体系的必然要求和重要发展方向。
矿井运输调度方案
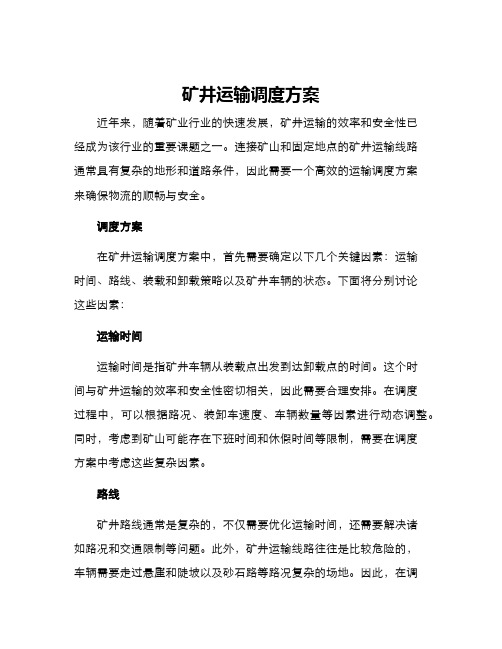
矿井运输调度方案近年来,随着矿业行业的快速发展,矿井运输的效率和安全性已经成为该行业的重要课题之一。
连接矿山和固定地点的矿井运输线路通常具有复杂的地形和道路条件,因此需要一个高效的运输调度方案来确保物流的顺畅与安全。
调度方案在矿井运输调度方案中,首先需要确定以下几个关键因素:运输时间、路线、装载和卸载策略以及矿井车辆的状态。
下面将分别讨论这些因素:运输时间运输时间是指矿井车辆从装载点出发到达卸载点的时间。
这个时间与矿井运输的效率和安全性密切相关,因此需要合理安排。
在调度过程中,可以根据路况、装卸车速度、车辆数量等因素进行动态调整。
同时,考虑到矿山可能存在下班时间和休假时间等限制,需要在调度方案中考虑这些复杂因素。
路线矿井路线通常是复杂的,不仅需要优化运输时间,还需要解决诸如路况和交通限制等问题。
此外,矿井运输线路往往是比较危险的,车辆需要走过悬崖和陡坡以及砂石路等路况复杂的场地。
因此,在调度方案中需要制定合理的路线规划和车辆调度策略,以确保车辆能够在安全的路线上运输。
装载和卸载策略在挖掘过程中,石头会通过装载/卸载站点进出矿井车辆。
因此,在制定调度方案时,需要考虑如何最大化矿井车辆的搬运能力。
在划分装载站点和卸载站点时,需要根据矿山的地形、矿物类型、矿物矿化度和固定地点的距离等因素进行评估,并根据结果设计出一个适合的装载和卸载策略。
矿井车辆状态在调度方案中,需要考虑矿井车辆的实际运营状态,以最大化车辆的利用率。
矿井车辆状态通常包括可用车辆数量和空载/载重状态。
在考虑这些因素时,需要采取极为精细的调度时间表,并设定一个指标,以指导从装载到卸载过程的可跟踪流程。
总结综上所述,矿井运输调度方案包括运输时间、路线确定、装载和卸载策略以及矿井车辆状态等关键因素。
为确保物流的顺畅与安全,需要制定合理的调度方案,并在调度过程中对调度方案进行动态调整,以应对各种复杂情况。
只有这样,才能保证矿井运输的效率和安全性,为矿业行业的发展作出贡献。
露天矿生产的车辆安排

露天矿生产的车辆安排摘要针对本问题的分析,我们按照“规划铲位到卸点的最优路线和次数→规划卸点回到铲位所需最优车辆资源数→根据以上两个规划寻求最优卡车调度方案”—三步走的方式,针对原则一和原则二分别建立数学模型如下:原则一:第一步:我们用整数规划的方法求取满足最优目标的由铲位到卸点的运输次数和路线,解决岩石和矿石的最优运输问题。
目标为总运量最小;第二步:根据第一步规划求得的运输路线及次数规划出卸点到铲位所需最优车辆资源数。
目标为空载时间最短,最小为吨公里;第三步:根据以上两个规划指导和求取相应调度问题。
目标为总发车次数最少。
对题目中的实际问题求得结果为:最少发车次数为13辆,铲车数为7。
原则二:目标1:最大的产量,并且满足产量、质量要求,同时优先考虑岩石产量并且总运量最小;由于问题已确定了车辆数,所以无需对车辆数范围的规划目标2:具体安排在解第二问时我们采用了一个快速算法,虽然不能保证每辆车都不等待,但避免了,大规模整数规划,所以我们认为这种简化是合理的。
最后,结合模型分析对模型进行了评价。
所用铲车数为7,卡车数为20,总运量:103488吨.一、问题的分析在满足对矿山采运资源的限制条件下,我们将该问题的两个目标转化为最优规化问题。
经分析后我们采用三步规划的方法,在可解的条件下,将问题划归为三个整数规划问题。
为达到问题的两个最优目标,我们采用目标到调度的逆向分析方法,以“规划铲位到卸点的最优路线和次数→规划卸点回到铲位所需最优车辆资源数→根据以上两个规划指导和求取相应调度问题”三步走的方式求解问题的最终目标。
首先我们用整数规划的方法求取满足最优目标的由铲位到卸点的运输次数和路线,解决岩石和矿石的最优运输问题。
其次,再根据第一步规划求得的运输路线及次数规划出卸点到铲位所需最优车辆资源数。
最后,根据前两步结果,指导和安排相应车辆的调度,达到第一步对最优目标的规划。
二、模型的假设及说明在已满足题目中所有假设条件的前提下,我们补充两点如下:1). 模型只考虑满足题目要求的调度计划本身,而不考虑如何保证一个计划的内容在现实过程中实现;2). 卡车在一个班次中始终保持正常运行,不出故障;3). 电铲和卸点都不能同时为两辆及两辆以上卡车服务。
露天矿GPS卡车调度管理系统(TDTK宣传页)

露天矿GPS卡车智能调度管理系统系统简介:露天矿采用大型自卸汽车进行运输作业,由于采区作业范围广,地点移动变化大,设备状态变化快,调度的难度也大。
采用传统对讲及跑现场的人工调度方式很难及时、全面、准确掌握现场作业条件的频繁变化。
调度员仅靠个人经验人工调度生产,无法保障采矿过程的实时优化、高效。
另外,人工调度模式下无法实现对采矿作业人员和设备的实时监督,管理难度大,管理成本高。
露天矿GPS卡车智能调度管理系统通过采用全球卫星定位技术(GPS)、计算机及网络技术、无线数字通信技术、矿山系统工程及优化理论、地理信息系统技术(GIS)、电子技术等高新技术,对传统的人工调度系统及管理体制进行改造,通过采集生产设备动态信息,实时监控和优化调度卡车、电铲、辅助设备等设备的运行,从而形成一种信息化、智能化、社会化的新型现代调度控制系统和全方位的采矿生产管理控制自动化决策平台,是数字矿山的关键技术内容之一。
本系统由调度中心、通讯及差分系统、车载智能终端三部分构成,实现对露天矿主要采矿设备(卡车、电铲、洒水车、平路机、推土机、加油车等)的位置及工作状态的跟踪,实时监视卡车及电铲的运行情况,适应采矿生产过程中情况的变化,系统以GPS定位技术为依托,线性规划算法模型为优化基础,无线通讯为数据传输手段,计算机技术为工具,在露天矿设备数量一定的情况下,实现对卡车、电铲等采矿设备的实时优化调度,自动、及时、高效地安排矿山设备的生产作业,达到优化管理矿山生产过程、提高产量,节省费用、取得较高经济效益之目的。
功能概述:优化调度:根据GPS信号跟踪和标注车辆和设备位置,实现实时监控,并自动统计电铲能力和各个运输周期数据;系统提供设备的历史回放功能;统筹所有电铲、卸点、重车和空车的实时运行状态,在满足生产中各种约束条件的情况下,为每台空车指派最合适的目标电铲,为每台重车指派最合适的目标卸点;在调度模块中有配煤控制功能。
二维监视:实时二维地图显示界面,可以显示所有相关的工程位置,如采掘面、装载区域/装载点、卸载区域/卸载点(排土场和破碎站)、储煤场、加油站、停车场、维修厂/车间、矿区道路网、矿区边界等,动态实时显示运输设备在道路网上的运行状况,并可以显示或查询各工程位置的相关基础数据(位置/GPS坐标、名称、类型、物料、状态等等)。
露天矿卡车地调度

承诺书我们仔细阅读了中国大学生数学建模竞赛的竞赛规则.我们完全明白,在竞赛开始后参赛队员不能以任何方式(包括电话、电子邮件、网上咨询等)与队外的任何人(包括指导教师)研究、讨论与赛题有关的问题。
我们知道,抄袭别人的成果是违反竞赛规则的, 如果引用别人的成果或其他公开的资料(包括网上查到的资料),必须按照规定的参考文献的表述方式在正文引用处和参考文献中明确列出。
我们郑重承诺,严格遵守竞赛规则,以保证竞赛的公正、公平性。
如有违反竞赛规则的行为,我们将受到严肃处理。
我们参赛选择的题号是(从A/B/C/D中选择一项填写):我们的参赛报名号为(如果赛区设置报名号的话):所属学校(请填写完整的全名):西安交通大学参赛队员(打印并签名): 1. 计红林2. 万日栋3. 尧文斌指导教师或指导教师组负责人 (打印并签名):日期: 2012 年 8 月 10 日赛区评阅编号(由赛区组委会评阅前进行编号):2011高教社杯全国大学生数学建模竞赛编号专用页赛区评阅编号(由赛区组委会评阅前进行编号):赛区评阅记录(可供赛区评阅时使用):评阅人评分备注全国统一编号(由赛区组委会送交全国前编号):全国评阅编号(由全国组委会评阅前进行编号):露天矿生产的车辆调度一.问题提出钢铁工业是国家工业得到基础之一,铁矿是钢铁工业的主要原料基地。
提高采矿玉树设备的利用率是增加露天矿经济效益的首要任务。
露天矿里有若干个铲位,每个铲位已预先根据铁含量将石料分成平均铁含量不低于25%的矿石和低于25%的岩石。
每个铲位的矿石、岩石数量以及矿石的平均铁含量都是已知的(如附表12-1和附表12-2所示)每个铲位之多能安排一台电铲,电铲平均装车时间为5分钟。
卸货地点有卸矿石的矿石漏、2个铁路倒装场和卸岩石的岩石漏、岩场等(如附图所示),每个卸点都有各自的产量要求。
要求应该尽量把矿石按矿石卸点需要的铁含量(假设都为29.5±1%,称为品味限制)搭配起来送到卸点,搭配的量在一个班次(8小时)内满足品味限制即可。
露天矿生产车辆调度的最优化选择

矿石量 1
1.1
1
1
1.1 1.3 1.1
岩石量 1.3 1.1 1.4 1.2 1.2 1.4 1.1
3 问题分析
该露天矿卡车运输作业为每日 3 班,每班 8 h。该 问题所要研究的是一个生产班次内的生产计划,即 求出在总运量最小的前提下出动几辆卡车,分别在 哪些线路上运输,从而求出具体的生产计划和相应
2 问题背景
在我国,自卸卡车由 20 世纪的载重 10 余吨发 展到今天的载重 200 t,载重量越大的自卸卡车损耗 越大。例如,载重为 154 t 的卡车,平均时速为 28 km/h, 每个班次每台车的消耗接近 1 t 柴油,发动机点火时 也需要消耗相当多的电瓶能量,故一个班次只在开 始工作时点火一次,卡车等待时的油耗也是相当可 观的,原则上在安排时不应发生卡车等待的情况。因 此,对于载重量日益变大的卡车的合理调度和安排 显得日益重要。对于矿业企业来说,提高采矿运输设 备的利用率是增加露天矿经济效益的首要任务,于
铲位 卸点
铲位 1 铲位 2 铲位 3 铲位 4 铲位 5 铲位 6 铲位 7
矿场 A 4
4
3
4
4
4
2
矿场 B 5
4
5
4
3
3
3
岩场 A 2
4
3
4
5
5
3
(3)每辆卡车在 Xi 到 Yj 路线上 8 h 最多可运行 的次数为:
Bij =[(60 × 8 -(Aij - 1)× 5)÷ Tij] 其中 Bij 是以该路线上最后装车的那台车来计 算的,如果按第一台装车的车来计算,则有:
铲位 卸点
露天矿运输系统优化与卡车调度问题研究

露天矿运输系统优化与卡车调度问题研究相对于井工开采,露天矿具有产量大、回采率高、全员效率高等特点,但因其多采用“电铲-卡车”间断式开采,且电铲、卡车都是专业的超大型设备,所以设备投资大、油耗较高。
在保证设备利用率和产能的同时,如何有效地节能降耗,成为露天开采中迫切需要解决的问题。
通常从矿山开发规划、装运设备、生产计划和物流作业管理的改进三个层面进行节能降耗。
本文分别从露天矿路网优化和卡车物流调度两个层面,改进矿山的生产物流过程。
其研究有助于露天开采中缩短平均运距、提高卡车有效使用率,实现节能降耗。
中间桥是在露天矿的两帮中间利用排土堆积成一条通路。
与端帮运输相比,中间桥节省卡车运距,在一定条件下合理采用中间桥运输,可以节省总的开采成本。
卡车运输是“电铲-卡车”间断式露天开采中燃油消耗的主要环节。
合理的卡车调度分派、装卸位置匹配及运输路径安排可以减少卡车等待时间、缩短运输距离,在保障产能的同时节能降耗。
围绕露天矿中间桥运输系统和卡车调度,进行如下研究:1)针对复杂地质条件下的大型露天矿,研究中间桥运输系统的适用性。
传统上,中间桥运输系统的应用多局限于近水平地层的间断式开采工艺。
本文就矿坑遭遇背斜及断层等复杂地质条件下中间桥运输系统的适用性进行分析,以搭桥内排运费不大于双环内排运费建立优化不等式,并给出相应的服务水平优化决策模型。
以具有背斜及断层等复杂地质条件的某露天矿为例,论证中间桥运输系统的适用性,还对中间桥搭设水平、服务水平等关键问题进行优化决策,应用中取得一定经济效益。
2)以露天矿“电铲-卡车”生产系统的生产计划与调度实际为背景,研究其中的卡车调度问题。
针对矿山的实际运输车辆和道路条件及效益要求,在考虑开采优先顺序的情况下,以总的运输价值为优化目标,建立问题的整数规划模型。
通过分析问题和模型的特征,提出有效不等式和问题的性质,引入问题上界。
利用问题的性质和上界,设计一种启发式算法和改进策略对问题进行求解。
露天矿卡车调度

一、系统概述丹东东方测控技术有限公司自主研发的露天矿GPS车辆智能调度管理系统综合运用计算机技术、现代通讯技术、全球卫星定位(GPS)技术、系统工程理论和最优化技术等先进手段,建立的生产监控、智能调度、生产指挥管理系统,对生产采装设备、移动运输设备、卸载点及生产现场进行实时监控和优化管理。
露天矿GPS车辆智能调度管理系统实现了优化卡车运输,降低总运输功和采装与运输设备的等待时间,节能降耗,有效提高采装与运输效率;实现电铲、卡车、钻机调度,优化生产,合理配矿,提高资源利用率;及时应对生产中出现的突发事件,以实现及时响应生产、及时调整生产和安全生产。
二、系统功能●优化卡车运输,降低总运输功率和采装运输设备的等待时间,实时应对电铲故障等各种原因导致不能作业的情况,减少生产运输环节不必要的空跑和消耗,有效提高采装与运输效率;●对采运作业的电铲和卡车进行自动优化和调度。
实现电铲、卡车、钻机、推土机、平路机、加油车等设备的远程调度,优化生产、合理配矿,提高资源利用率;●及时对生产中出现的突发事件,以实现及时响应生产、及时调整生产和安全生产。
三、系统特点⏹全自动的实时调度:系统根据实际生产中电铲、矿车、卸点、物料等情况的变化适时进行自动调度;⏹直观方便的调度界面:可以清晰地看到车的运行方向和车流规划的信息。
整个自动调度界面直观、美观,派车一目了然;⏹司机对全局信息的知情:司机知道全场的工作状况(比如电铲是否处于工作状态,卸点是否处于堵塞状态等);司机可以实时的掌握自身产量信息;⏹人性化的电子地图监视与历史行车轨迹回放:如果是 C/S 模式,调度室和网络上其他的地图文件不同步,会造成道路网络发生变化,出现网络上的地图不一致的现象,而我们的电子地图是 B/S 模式,调度室和网络上其他的地图文件是同步的;⏹电铲装载能力的自动采集:系统会准确地自动采集电铲的装载能力,调度无需人工设定电铲能力来适应现场生产。
采用多种方法核算,设计精细方案,准确地自动采集了电铲强度,确保了采场车流动态而合理的分配。
智能卡车调度系统在露天矿的应用

智能卡车调度系统在露天矿的应用摘要:露天矿是以挖掘为核心、运输为系带的大型生产行业,施工生产效率和经济效益的高低,取决于车辆调度是否合理,而车辆的合理分配是生产计划和任务完成的关键因素。
传统的人工调度存在管理难度大、生产效率低等问题。
为解决这些问题,矿山GPS(Global Positioning System,全球定位系统)卡车智能调度系统应运而生。
本文对智能卡车调度系统在露天矿的应用进行分析。
关键词:智能卡车调度系统;露天矿;应用,1智能卡车调度系统调度理论卡车调度系统基于计算机技术,依托GPS卫星,以矿山数据库为核心,综合利用无线传输技术,集成各个生产指挥环节,将GPS位置信息发送到内置GPS接收模块的终端设备,实现实时动态调度,具有生产管理、监控、统计、决策、优化等功能。
卡车调度理论包含确定最优路线、车流规划、实时调度三个方面。
(1)确定最优路线。
最优路线的确定旨在适应矿山配置形态变化,它在庞大的采场道路网中解算出所有两点间的最短路线。
在图论和运筹学中,最短路径算法通常用来求解最优路径。
常用的算法有Dijkstra、Floyd、矩阵算法、动态规划算法等。
(2)车流规划。
车流规划就是通过数学规划,在满足运输量、剥采比、车流连续性、产品质量搭配等约束条件下,对发往各装卸点的车流进行优化分配,其结果是对运输系统中卡车进行实时调度的基础。
(3)实时调度。
实时调度是在车流规划的基础上,应用适当的实时调度准则,根据当前系统的运行情况,对卡车进行实时调度,给出每台卡车优化的运行方向。
2卡车调度系统架构组成露天矿智能卡车调度系统,通常包括硬件系统和软件系统。
从功能板块来说,包括综合管理平台、生产与安全管理系统、设备辅助管理系统、系统辅助管理系统、地质模块管理系统和智能调度系统。
从构架来说,该系统通过GPS及北斗双星定位,包含4GLTE通讯基站、车载终端、挖机终端、调度控制中心等硬件设施建设及调度控制软件程序(如图1)。
露天矿生产的车辆调度优化安排

表 1 各铲位和各卸点之间的距离 (cm)
矿石漏 倒装场 Ⅰ
岩场 岩石漏 倒装场 Ⅱ
铲位 1
5. 26 1. 90 5. 89 0. 64 4. 42
铲位 2
5. 19 0. 99 5. 61 1. 76 3. 86
铲位 3
4. 21 1. 90 5. 61 1. 27 3. 72
铲位 4
4. 00 1. 13 4. 56 1. 83 3. 16
4 模型的建立
4. 1 模型的初建 :依据原则一建立数学模型 :
p q1 + q2
6 6 min
m ijk ×x ij
j =1 k =1
第2期
周 硕等 :露天矿生产的车辆调度优化安排
3 9
w
6 min rk k =1
pw
6 6 m ijk × d Ε f j ( j = 1 , 2 , …, q1 + q2)
线性规划模型 ,可以求解出运输路线和运输次数 ;第二阶段运用 MA TLAB 软件求解 。在第一阶段 , 我们
可以得出运输次数的矩阵 :
(1) 用此矩阵按位乘以各个运输路线运输一次的运行时间 ,则可以得出各个运输路线的运输时间 。
(2) 再将各个卸点的运输时间除以一个班次的时间就可以得出每个卸点应停的卡车数 , 这可能并
q1 + q2 w
6 6 m ijk × d Φ bi ( i = 1 , …, p)
i =1 k =1
20
6 rk Φ w
k =1
pw
pw
6 6 6 6 m ijk ×d ×gj Ε
m ijk ×ci ( j = 1 , 2 , …, q1)
i =1 k=1
露天矿生产的车辆安排

露天矿生产的车辆安排露天矿生产的车辆安排(CMCM2003B)摘要本文要解决的问题主要围绕减少实际中的经济成本而展开的。
在经济运作中,减少成本是作为露天矿生产带来利润最大化的有效手段之一。
而合理安排有效路线和车次,成为了解决减少成本问题的关键。
鉴于铲点到卸点线路的复杂性,我们把问题分成两个层次加以解决。
首先我们采用了整体规划的算法,建立了数学模型以求得最小运输量。
其基本思想是提取重要的约束性条件,对于总产量达最小的目标函数进行约束,运用lingo程序求出其最优解,最后得出最小运输量为85628.62吨,且第5、6、7个铲点没有使用。
对于层次二,通过解决层次一所得出具体流量计算卡车在各个路线上一个班次最多可以运行的次数及各路线上需要的卡车数,从而得出所有路线要出动13辆卡车.问题重述此题类似与产地与销地的运输的整数规划问题。
10个矿位,5个卸点,运输矿石和岩石两种产品。
此题的重点在于限制条件的提取,由于题中所给条件较多如:每个铲位至多能安置一台电铲,电铲的平均装车时间为5分钟。
卸货地有卸矿石的矿石漏、2个铁路倒装场和卸岩石的岩石漏、岩场等。
每个卸点都有各自的产量要求,岩石卸点的品味限制都为29.5% 1%。
电铲和卸点都不能同时为两辆及两辆以上卡车服务。
卡车每次都是满载运输,且在一个班次中不存在卡车等待情况,卡车只在开始时点火一次。
卡车的平均卸车时间为3分钟。
一个班次为8小时等等。
总之,限制条件比较隐晦,需要从题中认真挖掘。
本文需要解决的问题是如何设计一个班次使得总运量(吨公里)最小,同时出动最少的卡车,从而运输成本最小。
一个班次的生产计划应该包含以下内容:出动几台电铲,分别在哪些铲位上;出动几辆卡车,分别在哪些路线上各运输多少次。
因此问题可转化为:1、如何在满足所有限制条件的条件下,使得一个班次内所有卡车的总运量最小。
2在总运量最小的情况下,如何设计卡车路线,使得出动的卡车数最少,从而使总成本最低。
卡车自动化调度系统在露天矿的应用

5 ・ 8
露天采矿技术 21年第2 0 2 期
卡 车 自动化调度 系统在露天矿 的应用
陈彦 方
( 中煤龙化哈 尔滨矿业有 限公 司,黑龙 江 哈 尔滨 14 5 ) 5 84
摘
要: 露天矿 卡 车 自动化 调度 系统是 数 字矿 山建设 的组 成部 分 , 降低 采运 设备 非 生 产 时 间、 高生 是 提
外 屋 屣
嘲/ 豆、 霪 一暑
术与计算机技术 、 通信技术 、 电子技术 、 自动控制技 术、 卫星 定位技 术 、 化理论 等相 结合 的产物 。露 天 优
矿 生产 自动化调 度系统 用 于汽车 运输露 天矿 对 卡车
图 1 卡 车 调 度 系 统 组 成 及 其 对 外 关 系
关键 词 : 露天矿 ; 优化调 度 ; 安全 ; S ME H
中图分类号 : 9 . U4 2 9 6
1 概 述
文献标 识码 : B
文章编号 :6 1—9 1 2 1)0 17 8 6( 0 2 2—0 5 0 8—0 4 生产 情况 , 而起到优 化车 队运行 、 从 准确 执行 生产 计
露大采矿投木 21年 期 0 第2 2
表制 作 、 备运 行 回放等 功能 。 设
・9 5・
调 度 中心 ; 当设 备需要 向调 度 中心报告 情况 时 ( 如设
备故障等) ,终端竞争向调度中心发送这些信息 , 并
同时报 告 自己的位 置 、 状态 等 。 实现 了车辆 管理 的智
生产 中存在 的 问题 , 产调度 指挥 的盲 目性 、 生 滞后 性
划 等作 用 , 以此达 到提 高 矿 山产量 、 节省 费 用 、 得 取 较 高经济效 益之 目的 。 它是提 高露 天矿生 产能力 、 节 省投 资、 降低成本 、 高矿 山管理 效率 的有效手段 , 提 是 汽车运输露 天矿达 到世界先进水 平 的关键技术之一 。
露天矿生产车辆调度的最优化选择

( 内蒙 古科技 大 学 矿 业工 程学 院 , 内蒙 古 包 头市 摘 041) 10 0 要 : 天矿 采矿 生产 的车辆 安排是 一 个 大规 模 的优 化调 度 问题 , 助运 筹 学 中的非 线 露 借
性规 划理论 和 方法 , 实际情 况 出发 , 立 了车辆 安排 调 度 应该 遵循 的原 则 , 从 确 并根 据 这 些
产计 划和相应 的总运量及 矿石岩 石产量 。
( )对 于不 同线 路上 的卡 车是否会 等待 同一 台 5
铲车来 装车 的问题 , 以通 过宏 观 控制 的方式 力争 可
加 H 避免 , 每台铲 车每 5mn装 1车 , 多装 9 i 8h最 6车 ,
9 4 4
由该 问题 分析可知 , 要实现经 济效益 的最 大化 , 必 须满足 以下 2个 条件 : ( )卡 车 的 总 运 量 最 小 , 时 卡 车 不 存 在 等 1 同 待 J 象 , 现 即卡车一 直处于运 行状态 。 ( )各卸 点的产量要求 必须满 足 。 2 在条件 ( ) , 1 下 首先 以总运 量 最 小 以 及各 卸 点 的产量要 求为 目标使 运输 车辆数量最 小 。
到选 矿 厂 、破碎 站 或 矿场 , 剥 离 的岩 土运 送 到 排 把
1 , 个 每个卸 点都 有各 自的产量 要求 , 体数 据见 具
图 1表 1表 2 、 、 。
土场, 将生 产 中所需 的人 员 、设 备 和 材料 运 送 到 工 作地 点 。 我 国 自卸卡 车 目前 已由 2 0世 纪 的载 重 不 到 2 0 t 发展 到今 天 的载重 2 0 t载 重量 越 大 的 自卸 卡 车 0 , 损耗越 大 。 因此 , 于 载重 量 日益 变 大 的卡 车 的合 对
露天矿卡车调度系统关键技术分析

端 完成 车 辆 的 定 位 及 信 息 的 发送 , P 通 所 有 车 载 终 端 的 GP 数 据 转 换 成 本 地 地 理 产 的 运 行 情 况 对 通 往 各 装 、 载 点 的 车 辆 G RS S 卸 信 链 路 完 成 信 息 的 交 互 , 控 中 心 信 息 管 坐 标 , 将 差 分 改 正 数 加 入 到地 理坐 标 上 , 进 行 规 划 , 得 从 电 铲 到 排 卸 点 和 从 排 卸 监 并 求
露天矿卡车计算机自动调度系统调度算法设计

大 而 集 中 , 藏 浅 , 用 露 天 开 采 , 用 调 度 系 统 前 埋 采 应
已拥 有 主要 大 型 采 矿 设 备 如 下 : 5 1 4 t和 3 0 t 动 2 电
轮卡车 共 4 9台 ; 3m3和 1 1 6m3电 铲 共 9台 ; 机 钻
1 3台 ; 药 车 7台 , 装 日处 理 矿 石 量 可 达 7 2万 td . /。 人 工 调 度 主要 采 用 开 班 固定 配 车 方 式 , 接 班 交
p t ( P)a ei m utbefrmiely u om-e t h n el erpo rmmig ( P)o es i befrt -e t ah B l r h s i l o n o t r rl e c ag ,n a rga g t a a f ad i n L n ut l o i rl e a me ad
Ab t a t I o s r c n c mb n t n wih t e p o u t n p a tc fDe i g C p e i e t e d v l p e t h so y a d s se i a i t h r d c i r c ie o x n o p r M n , h e eo m n i r n y t m o o t c mp n n so r c i a c i g s se a e d c i e Th e l o t ms r l t g t r c ip t h n y t m , andy b t o o e t f tu k d s t h n y tm r e rb d. r e ag r h e a i o t k d s a c i g s s e n r p s i n u e s
c a g n y a i p o r mm i g o e f r r l i g r a— i e d s a c i g a e h g l h e . h n ea d d n m c r g a n n o e i n e lt i t h n ih i t a z m p r g d
露天矿的车辆调度安排

露天矿的车辆调度安排摘要本文针对露天矿的车辆安排,为了提高设备利用率以增加经济效益,在卡车不等待的前提满足产量和品位的要求,根据两条原则制定了一个班次的实际生产计划。
模型Ⅰ:针对原则一,建立道路能力、电铲能力、卸点能力、铲位储量、产量任务、铁含量、电铲数量、车辆数量、整数等约束条件,根据原则一建立目标函数的整数规划模型。
目标函数(最小吨公里):min =∑∑==51101*154*i j ij ij d num 。
将模型用Lingo 软件编程求解,综合分析给出生产计划:出动7辆铲车,13辆卡车,总运量为85628.2吨公里,具体的派车方案(见表二)。
模型Ⅱ:针对原则二,在约束条件与原则一相同的条件下,建立多目标非线性整数规划模型,利用主要目标法将多目标问题转化为单目标优化问题,根据主要目标列出最小费用函数求解,并将所求解转化为约束条件,然后逐步约束求解,将非线性规划问题转化为线性问题。
建立主要目标函数:总产量最大∑∑==51101154*max i j ij num ;次要目标函数:岩石产量优先()∑=+10143154*max j j j num num ;最后的目标函数:总运量最小min∑∑==51101*154*i j ij ijd num。
用Lingo 软件编程求解,综合分析给出生产计划:出动7辆铲车,20辆卡车,最大的产量101640.0吨, 岩石产量为49280.00吨, 矿石产量为52360.00 吨;总运输量为142385.3吨公里, 具体的派车方案(见表四)。
问题的进一步优化,从实际生产可行的角度,结合原则一与原则二,在模型中引入各铲位(卸点)的工作饱和因子P ,对以上最优方案进行了综合调整,通过图像分析,对P 取不同值进行了灵敏度分析,近而选取最优P 值下给出实际生产的车辆安排方案(见表六、表七)。
建立快速算法模型,在尽量不影响模型结果的前提下,分析原则一与原则二的简化方法,分别得到满足原则一与原则二的快速算法。
露天矿GPS 卡车调度系统数据流处理方法
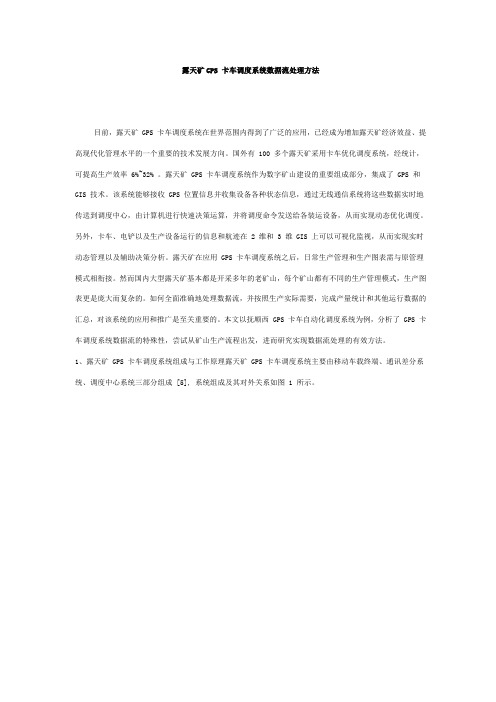
露天矿GPS 卡车调度系统数据流处理方法目前,露天矿 GPS 卡车调度系统在世界范围内得到了广泛的应用,已经成为增加露天矿经济效益、提高现代化管理水平的一个重要的技术发展方向。
国外有 100 多个露天矿采用卡车优化调度系统,经统计,可提高生产效率 6%~32% 。
露天矿 GPS 卡车调度系统作为数字矿山建设的重要组成部分,集成了 GPS 和GIS 技术。
该系统能够接收 GPS 位置信息并收集设备各种状态信息,通过无线通信系统将这些数据实时地传送到调度中心,由计算机进行快速决策运算,并将调度命令发送给各装运设备,从而实现动态优化调度。
另外,卡车、电铲以及生产设备运行的信息和航迹在 2 维和 3 维 GIS 上可以可视化监视,从而实现实时动态管理以及辅助决策分析。
露天矿在应用 GPS 卡车调度系统之后,日常生产管理和生产图表需与原管理模式相衔接。
然而国内大型露天矿基本都是开采多年的老矿山,每个矿山都有不同的生产管理模式,生产图表更是庞大而复杂的。
如何全面准确地处理数据流,并按照生产实际需要,完成产量统计和其他运行数据的汇总,对该系统的应用和推广是至关重要的。
本文以抚顺西 GPS 卡车自动化调度系统为例,分析了 GPS 卡车调度系统数据流的特殊性,尝试从矿山生产流程出发,进而研究实现数据流处理的有效方法。
1、露天矿 GPS 卡车调度系统组成与工作原理露天矿 GPS 卡车调度系统主要由移动车载终端、通讯差分系统、调度中心系统三部分组成 [5], 系统组成及其对外关系如图 1 所示。
图 1 露天矿卡车调度系统组成及其对外关系移动车载终端接收 GPS 信息并实时解算自己的坐标位置;调度中心根据需要以轮询方式采集每台车载终端的信息:当车载终端收到对其轮询指令后将自己的车号、位置、状态等信息发向调度中心;当设备需要向调度中心报告情况时 ( 如设备故障等 ) ,终端竞争向调度中心发送这些信息,并同时报告自己的位置、状态等。
露天矿卡车调度决策方案及模型设计

露天矿卡车调度决策方案及模型设计摘要露天矿卡车调度决策的基本要求是在满足生产管理需要的前提下,在不同的调度原则下,尽量使卡车调度系统简便、经济、实用,保证在最大限度地发挥整个工艺系统的效率和生产能力,并使运输成本最低。
本文利用数学规划理论对现在露天矿生产的车辆进行安排。
首先,我们在原则一的条件下,建立规划模型,并利用规划软件LINGO编写程序,得到需要出动的电铲数量以及它们在铲位上的分布,有几条路线上有卡车运输,并且得到每条路线上的车次和总的车次,然后,建立最少卡车数量的规划模型,最后,对不同的路线进行赋权,而且结合定点配车原则,以卸点为中心确定各条路线上的卡车数,并安排它们的运输方式。
对于原则二,其约束条件基本与原则一相同,我们在LINGO上编写复杂的程序,执行并得到相应的结果。
通过求解,在原则一下,得到:出动7辆电铲,在铲位5,铲位6,铲位9上没有电铲,需要最少出动14辆卡车,相应矿物量如下表:对于原则二,我们通过附录的程序得到3组相同产量且最大,第一组为在铲位4,铲位6,铲位9上没有电铲;第二组为在铲位4,铲位6,铲位8上没有电铲;第三组为在铲位5,铲位6,铲位8上没有电铲,他们的总产量都为10.3488(万吨)。
于是,我们考虑在岩石优先的条件下,发现第二组的岩石产量为4.80864(万吨),而其它两组为4.928(万吨),这样就可以去掉第二组;然后,计算其它两组的总运量,第一组为12.7578(万吨),第三组为12.6512(万吨),这样就得到最后的答案:在铲位5,铲位6,铲位8上没有电铲,相应的岩石产量为4.928(万吨),矿石产量为5.4208(万吨)。
在模型中,我们还给出一个班次的生产计划,而且给出制定一个班次生产计划的快速算法。
在模型的建立过程中,为了保证模型具有更大的实用性,我们建立了通用的规划模型,然后,才对问题进行求解,这不仅是求解的过程也是检验模型实用性的过程。
问题重述钢铁工业是国家工业的基础之一,铁矿是钢铁工业的主要原料基地。
- 1、下载文档前请自行甄别文档内容的完整性,平台不提供额外的编辑、内容补充、找答案等附加服务。
- 2、"仅部分预览"的文档,不可在线预览部分如存在完整性等问题,可反馈申请退款(可完整预览的文档不适用该条件!)。
- 3、如文档侵犯您的权益,请联系客服反馈,我们会尽快为您处理(人工客服工作时间:9:00-18:30)。
露天矿卡车运输系统最佳调度的数学模型及其数值解法研究马义飞 李祥仪(北京科技大学资源工程系,北京,100083)摘 要 文章分析了目前卡车调度系统的建模情况,应用最佳控制的理论建立了卡车调度系统的数学模型,并结合一简例,分析了数值解法,给出简例的数值解。
通过对数值解的分析,说明数学模型和数值解法都是正确的。
关键词 计算机控制;卡车调度;最佳控制;数学模型中图法分类号 TD 571:O 224A M a them a tic M ode l of O p ti m a l C ontro lfo r T ruck D is pa tch S ys tem in O pe nca s t M iningM a Y ifei L i X iangyi(B eij ing U n iversity of S cience &T echnology ,B eij ing ,100083Ch ina )Abs tra c t T h is p ap er has exam ined the m odelling of truck disp atch system in op encast m in 2ing .W ith the op ti m al theo ry ,a m athem atical m odel has been con structed .T ak ing a si m p le case as exam p le ,the p ap er has analyzed the com p u tati onal m ethod of the p rob lem ,w ith the m ethod ,calcu lated the si m p le case and go t good resu lts w h ich p roved that the m athem atical m odel and the so lving m ethod are co rrect .Ke y w o rds com p u ter con tro l ;truck disp atch ;op ti m al con tro l ;m athem atical m odel1 当前国内外计算机卡车调度系统的应用情况[1] 国际上流行的计算机卡车调度系统是美国模块公司的D ISPA TCH ,它是综合监控系统,经过多年的发展,现在达到对设备状态自动监控,GPS 定位,自动派车的阶段。
它的软硬件功能都很强,目前在世界范围内的50多座矿山成功地应用该系统。
但是,它的价格昂贵,一套D ISPA TCH 需外汇$3000000;维护困难,购买的软件对矿山管理人员而言是黑箱,维护长期依赖国外,非常不便。
所以,我国的计算机卡车调度系统,要立足国内开发。
国内也积极开发实用计算机卡车调度系统,1990年由本钢南芬铁矿、马鞍山矿山研究院、东北工学院组成的联合课题组开发了南芬铁矿生产调度计算机辅助系统。
1994年,霍林河矿 收稿日期:1998-08-10马义飞,男,1954年7月出生,北京科技大学资源工程学院博士研究生;李祥仪,北京科技大学资源工程学院教授,博导。
第8卷 第1期 运 筹 与 管 理 V o l .8,N o.11999年3月 O PERA T I ON S R ESEA RCH AND M ANA GE M EN T SC IEN CE M ar .,1999务局与煤科总院西安分院、中国矿业大学合作,开发完成计算机控制自动化卡车调度系统。
据文[1]中计算,该系统在不增加采、掘、运设备的情况下可使产量提高5◊~6◊,每年可获300多万元收益,建立卡车调度系统的投资在投入使用后2年内便可收回。
计算机卡车调度系统大体可分为两大部分,硬件系统,包括中央处理计算机、信号采集、传输设备等;软件系统,包括信息处理、根据最优准则确定最优派车方案,直至自动发出指令、派车。
本文不研究硬件,在硬件设备到位之后,软件及数学模型是发挥系统效果的关键。
目前的软件通常是分步建模,计算机模拟实现。
(见图1)更新运行时间实时调度程序按照各种规则实时调度车流规划程序给出卡车的运行范围及车流量最佳线路程序给出卡车运行最佳线路及时间矿山地形矿坑配置及约束系统中的随机情况图1 卡车调度过程示意图F ig.1 D iagram of truck dispatch p rocess 最佳线路的方法和程序已比较成熟,这里不作讨论。
车流规划通常用线性规划[2]或多目标规划[3]建模。
线性规划建模时分别考虑下列目标:(1)班费用最小或赢利最大;(2)产量最大;(3)卡车数量少;(4)单位运输功最少。
在优化车流分配的基础上,用动态规划调配空车到电铲,并考虑电铲的优先权,尽量实现线性规划的结果。
多目标规划模型的目标是:(1)第一优先级目标,系统出动卡车数量少;(2)第二优先级目标,赢利最大;45运 筹 与 管 理 1999年第8卷(3)第三优先级目标,品位最佳。
从上面的叙述可知,目前的模型车流规划与动态派车是分别处理的,对车流规划的结果只能“尽量实现”,而卡车调度系统是一个完整的动态控制系统,优化与派车不能分开。
本文试图用最佳控制的理论建立数学模型,作为卡车调度系统控制的补充。
它的优点是,所定义的电铲剩余工作时间实质上是一个综合指标,既考虑了电铲利用率最大,又考虑了卡车等待时间最短;所求出的最优控制就是在一定时期内,按照指标函数所给目标的派车方案。
当然,本文的研究还是初步的,没有给出其它几种目标下的指标函数的数学表述。
本文的意义在于把最佳控制理论第一次引入计算机卡车调度系统。
2 卡车运输系统最佳调度问题的提法[4][5]211 状态方程首先,把所研究的时间区间分为K 个时间段,第t k 段简记为k ,并且,下面凡出现(k )的地方,都表示对时间区间k 而言,不再一一重复。
在装载点上设:(1)x i (k )第i 台电铲前等待装车的卡车的总容量,i =1,2,…,m 。
m —为电铲数,把m 个电铲等待的卡车的总容量以矢量X (k )表示;(2)u i (k )为k 时间区间内来到电铲i 的卡车总容量,i =1,2,…,m ,总括起来以矢量U (k )表示。
而U (k )往前推一个运行时间就是派往电铲的卡车容量,所以,U (k )是可以控制的;(3)r i (k )为k 时间区间内电铲i 完成的装载量,i =1,2,…,m ,总的以矢量R (k )表示。
这样,装载点的状态转移方程为:X (k +1)=X (k )-R (k )+U (k )它表示,电铲前等待的空车容量随装车而减少,随来车而增多。
另外,对控制应有约束:u m (k )=nC n =1,2,…取正整数;C 为卡车装载能力,n ≤N w (k ) N w (k )为k 时刻在派车点等待派出的卡车数。
显然,这个系统是可控的,因为,通过改变U ,可以改变X 的每一个分量。
212 目标泛函先定义电铲的剩余工作时间:t i =x i r i 它的意义是,目前在电铲i 前等待的卡车,电铲需要多少时间装完。
为充分利用每台电铲的能力,以及使卡车等待时间最少,令每台电铲的剩余工作时间基本相等;这样,有目标泛函:m in J =∑k -1k =1∑m -1i =1(x i +1(k )r i +1-x i (k )r i)23 简例及数值解法研究311 系统描述55第1期 马义飞等:露天矿卡车运输系统最佳调度的数学模型及其数值解法研究不失一般性,设某露天矿有5台电铲,在某时刻k 在电铲前等待的卡车容量分别为:x 1(k ),x 2(k ),x 3(k ),x 4(k ),x 5(k );电铲装载速率分别为:r 1,r 2,r 3,r 4,r 5;派往电铲的卡车容量分别为:u 1(k ),u 2(k ),u 3(k ),u 4(k ),u 5(k )。
312 最佳控制的数学模型(1)状态方程x 1(k +1)=x 1(k )-r 1+u 1(k )x 2(k +1)=x 2(k )-r 2+u 2(k )x 3(k +1)=x 3(k )-r 3+u 3(k )x 4(k +1)=x 4(k )-r 4+u 4(k )x 5(k +1)=x 5(k )-r 5+u 5(k ) (2)目标泛函J =∑k -1k =1∑4i =1(x i +1(k )r i +1-x i (k )r i )2+(x 5(k )r 5-x 1(k )r 1)2 (3)H 函数和协方程H =∑4i =1(x i +1(k )r i +1-x i (k )r i )2+(x 5(k )r 5-x 1(k )r 1)2+Κ1(k +1)(x 1(k )-r 1+u 1(k ))+Κ2(k +1)(x 2(k )-r 2+u 2(k ))+Κ3(k +1)(x 3(k )-r 3+u 3(k ))+Κ4(k +1)(x 4(k )-r 4+u 4(k ))+Κ5(k +1)(x 5(k )-r 5+u 5(k ))Κ1(k )=Κ1(k +1)+4x 1(k ) r 1 r 1-2x 2(k ) r 1 r 2-2x 5(k ) r 1 r 5Κ2(k )=Κ2(k +1)+4x 2(k ) r 2 r 2-2x 1(k ) r 1 r 2-2x 3(k ) r 2 r 3Κ3(k )=Κ3(k +1)+4x 3(k ) r 3 r 3-2x 2(k ) r 2 r 3-2x 4(k ) r 3 r 4Κ4(k )=Κ4(k +1)+4x 4(k ) r 4 r 4-2x 3(k ) r 3 r 4-2x 5(k ) r 4 r 5Κ5(k )=Κ5(k +1)+4x 5(k )r 5 r 5-2x 1(k ) r 1 r 5-2x 4(k ) r 4 r 5313 解法首先对U 取满足约束的U 0,用状态方程计算对应于U 0的X 0,用协态方程计算Κ(矢量),用目标泛函计算相应的J 0,接下来求规划问题:m in H (U ) (把H 看成是U 的函数)满足对U 的约束,得到新的U ,再计算对应于新U 的X ,Κ,J ,若新U 及对应的X 使J 有所下降,U 赋给U 0继续前面的计算,否则,U 0及X 0为所求。
算法步骤是:第一步 读入原始数据;第二步 取满足约束的U 0第三步 计算相应的X ,Κ,J ;第四步 将J 与前一个J 做比较,若有所下降,转向第五步,否则转向第七步;第五步 计算规划问题参数;65运 筹 与 管 理 1999年第8卷第六步 解规划问题,求得新的U ,返回到第三步;第七步 取当前的U 为最优解,计算相应的X ,输出,停止。