锡的火法精炼
锡提炼方式
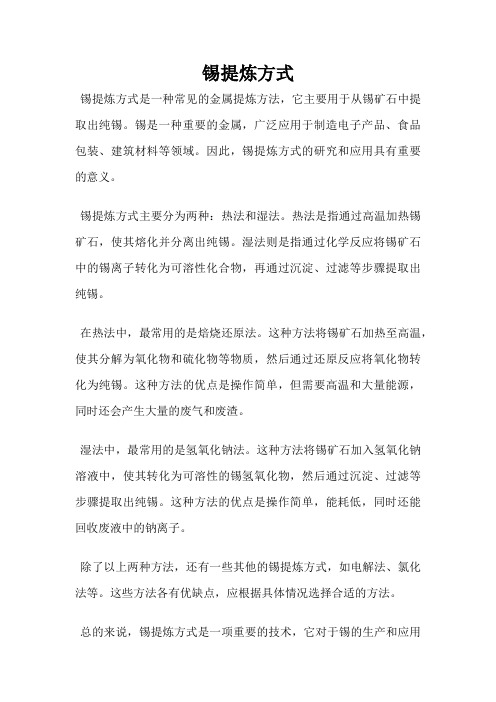
锡提炼方式
锡提炼方式是一种常见的金属提炼方法,它主要用于从锡矿石中提取出纯锡。
锡是一种重要的金属,广泛应用于制造电子产品、食品包装、建筑材料等领域。
因此,锡提炼方式的研究和应用具有重要的意义。
锡提炼方式主要分为两种:热法和湿法。
热法是指通过高温加热锡矿石,使其熔化并分离出纯锡。
湿法则是指通过化学反应将锡矿石中的锡离子转化为可溶性化合物,再通过沉淀、过滤等步骤提取出纯锡。
在热法中,最常用的是焙烧还原法。
这种方法将锡矿石加热至高温,使其分解为氧化物和硫化物等物质,然后通过还原反应将氧化物转化为纯锡。
这种方法的优点是操作简单,但需要高温和大量能源,同时还会产生大量的废气和废渣。
湿法中,最常用的是氢氧化钠法。
这种方法将锡矿石加入氢氧化钠溶液中,使其转化为可溶性的锡氢氧化物,然后通过沉淀、过滤等步骤提取出纯锡。
这种方法的优点是操作简单,能耗低,同时还能回收废液中的钠离子。
除了以上两种方法,还有一些其他的锡提炼方式,如电解法、氯化法等。
这些方法各有优缺点,应根据具体情况选择合适的方法。
总的来说,锡提炼方式是一项重要的技术,它对于锡的生产和应用
具有重要的意义。
随着科技的不断进步,锡提炼方式也在不断改进和创新,为锡的生产和应用提供了更好的技术支持。
粗锡火法精炼流程及原理

粗锡火法精炼流程及原理The process of crude tin fire refining involves several main steps, including desulfurization, oxidation, and reduction. 粗锡火法精炼的过程大致分为除硫、氧化和还原几个主要步骤。
First, the crude tin is heated in a reverberatory furnace to drive off the sulfur, a process known as desulfurization. 首先,将粗锡放入反射炉中加热,驱赶硫磺的过程被称为除硫。
During this process, the sulfur in the tin combines with the oxygen in the air to form sulfur dioxide gas, which is then released from the furnace. 在这个过程中,锡中的硫与空气中的氧结合成二氧化硫气体,然后释放出炉外。
Next, the oxidized tin is then heated in the presence of a reducing agent, such as carbon or charcoal, to remove the remaining impurities and achieve the desired purity level. 紧接着,被氧化的锡在还原剂的作用下(如碳或木炭)加热,以除去余下的杂质,达到期望的纯度水平。
Finally, the purified tin is cast into molds to form ingots or other desired shapes for further processing and use. 最后,经过精炼的锡被铸造成锭或其他所需形状,以便进行进一步的加工和应用。
金属冶炼中的炼锡工艺

应对资源短缺和价格上涨的挑战
多元化原料来源
开发多种锡矿资源,降低对单一矿源的依赖,保证原材料的稳定供应。
提高生产效率
通过改进工艺技术和设备,提高炼锡的生产效率,降低生产成本,增强企业的市场竞争力。
THANK YOU
循环经济
建立循环经济体系,实现废物的减量 化、资源化和无害化处理。例如,将 废渣和废弃物进行回收和再利用,减 少对资源的依赖和环境的污染。
05
未来炼锡工艺的发展趋势和挑战
新材料和新技术在炼锡工艺中的应用
新型耐火材料的研发
随着新材料技术的不断发展,新型耐火材料在炼锡工艺中的应用将更加广泛, 能够承受更高的温度和更复杂的化学环境,提高生产效率和产品质量。
在汽车制造业中的应用
1 2 3
发动机部件制造
在汽车发动机部件的制造过程中,锡因其良好的 耐高温性和抗腐蚀性而被用于制造气缸套和排气 管等关键部件。
焊接工艺
锡在汽车制造业中广泛应用于焊接工艺,能够提 高焊接质量和效率,确保汽车各部件的可靠性和 安全性。
润滑油添加剂
在某些润滑油中添加锡化合物作为添加剂,能够 提高润滑油的抗氧化性能和抗磨性能,延长发动 机使用寿命。
蒸馏原理
利用不同物质沸点的差异,通过加热和冷凝的方法使杂质与纯锡分 离。
02
炼锡工艺流程
原料准备
01
原料来源
炼锡所需的原料主要来自矿山开 采的锡精矿,以及其他伴生金属 矿石。
原料品质
02
03
原料储存
为确保产品质量,需对原料进行 严格的质量检测和控制,去除杂 质。
粗锡火法精炼流程及原理

粗锡火法精炼流程及原理下载温馨提示:该文档是我店铺精心编制而成,希望大家下载以后,能够帮助大家解决实际的问题。
文档下载后可定制随意修改,请根据实际需要进行相应的调整和使用,谢谢!并且,本店铺为大家提供各种各样类型的实用资料,如教育随笔、日记赏析、句子摘抄、古诗大全、经典美文、话题作文、工作总结、词语解析、文案摘录、其他资料等等,如想了解不同资料格式和写法,敬请关注!Download tips: This document is carefully compiled by theeditor. I hope that after you download them,they can help yousolve practical problems. The document can be customized andmodified after downloading,please adjust and use it according toactual needs, thank you!In addition, our shop provides you with various types ofpractical materials,such as educational essays, diaryappreciation,sentence excerpts,ancient poems,classic articles,topic composition,work summary,word parsing,copy excerpts,other materials and so on,want to know different data formats andwriting methods,please pay attention!粗锡火法精炼流程。
1. 熔炼。
将粗锡原料装入熔炼炉并熔化。
加入助熔剂(如石灰石)以去除杂质。
金属冶炼锡精炼与提纯工艺
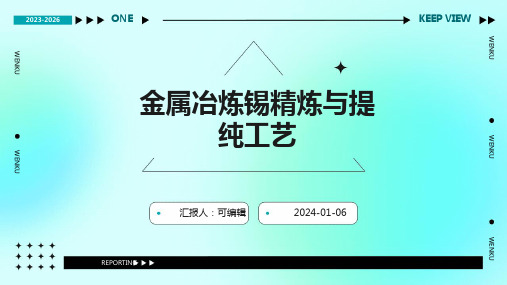
废水处理
废水来源
01
废水主要来源于锡精炼与提纯过程中的冷却、洗涤和化学反应
等环节。
处理方法
02
废水应进行预处理、沉淀、过滤和生物处理等环节,去除废水
中的有害物质和悬浮物,使废水达到排放标准。
循环利用
03
对于可循环利用的废水,应进行回收处理,实现水资源的节约
ቤተ መጻሕፍቲ ባይዱ
利用。
废渣处理
01
02
03
废渣来源
废渣主要来源于锡精炼与 提纯过程中的残渣、沉淀 物和废弃物等。
粗锡熔炼
熔炼设备
采用适宜的熔炼设备,如反射炉、电炉等,将原料加热至熔融状态。
熔炼过程
在熔融状态下,进行充分的搅拌、混合,使锡与其他金属充分分离。
粗锡除杂
除杂方法
根据锡中杂质的种类和含量,采用不同 的除杂方法,如化学沉淀法、溶剂萃取 法等。
VS
除杂效果
通过除杂处理,降低锡中杂质的含量,提 高锡的纯度。
色谱分离法提纯
色谱分离法提纯锡是一种利用不同物质在固定相和流动相之 间的吸附和脱附性能差异进行分离的方法。该方法具有分离 效果好、操作简便等优点,但同时也存在分离时间长、固定 相消耗量大等缺点。
色谱分离法提纯锡的原理是将粗锡中的杂质吸附在固定相上 ,而锡则不被吸附随流动相流出。通过控制流动相的流速和 温度,使不同杂质在不同的时间被洗脱下来,从而达到提纯 的目的。常用的固定相有硅胶、活性炭等。
PART 01
锡精炼工艺概述
锡精炼的定义与目的
定义
锡精炼是指通过一系列物理或化学手段,去除锡中杂质,提高锡的纯度的过程 。
目的
获得高纯度锡,满足不同领域对锡的品质要求,如电子、化工、冶金等。
碱渣火法冶炼提取粗锡工艺分析
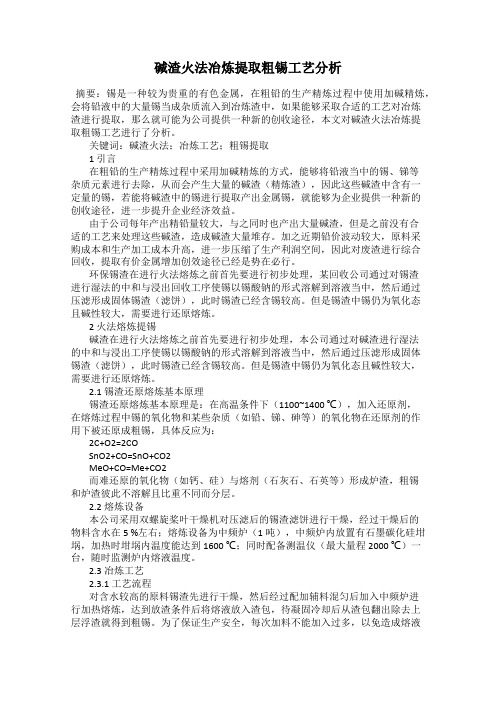
碱渣火法冶炼提取粗锡工艺分析摘要:锡是一种较为贵重的有色金属,在粗铅的生产精炼过程中使用加碱精炼,会将铅液中的大量锡当成杂质流入到冶炼渣中,如果能够采取合适的工艺对冶炼渣进行提取,那么就可能为公司提供一种新的创收途径,本文对碱渣火法冶炼提取粗锡工艺进行了分析。
关键词:碱渣火法;冶炼工艺;粗锡提取1 引言在粗铅的生产精炼过程中采用加碱精炼的方式,能够将铅液当中的锡、锑等杂质元素进行去除,从而会产生大量的碱渣(精炼渣),因此这些碱渣中含有一定量的锡,若能将碱渣中的锡进行提取产出金属锡,就能够为企业提供一种新的创收途径,进一步提升企业经济效益。
由于公司每年产出精铅量较大,与之同时也产出大量碱渣,但是之前没有合适的工艺来处理这些碱渣,造成碱渣大量堆存。
加之近期铅价波动较大,原料采购成本和生产加工成本升高,进一步压缩了生产利润空间,因此对废渣进行综合回收,提取有价金属增加创效途径已经是势在必行。
环保锡渣在进行火法熔炼之前首先要进行初步处理,某回收公司通过对锡渣进行湿法的中和与浸出回收工序使锡以锡酸钠的形式溶解到溶液当中,然后通过压滤形成固体锡渣(滤饼),此时锡渣已经含锡较高。
但是锡渣中锡仍为氧化态且碱性较大,需要进行还原熔炼。
2 火法熔炼提锡碱渣在进行火法熔炼之前首先要进行初步处理,本公司通过对碱渣进行湿法的中和与浸出工序使锡以锡酸钠的形式溶解到溶液当中,然后通过压滤形成固体锡渣(滤饼),此时锡渣已经含锡较高。
但是锡渣中锡仍为氧化态且碱性较大,需要进行还原熔炼。
2.1 锡渣还原熔炼基本原理锡渣还原熔炼基本原理是:在高温条件下(1100~1400 ℃),加入还原剂,在熔炼过程中锡的氧化物和某些杂质(如铅、锑、砷等)的氧化物在还原剂的作用下被还原成粗锡,具体反应为:2C+O2=2COSnO2+CO=SnO+CO2MeO+CO=Me+CO2而难还原的氧化物(如钙、硅)与熔剂(石灰石、石英等)形成炉渣,粗锡和炉渣彼此不溶解且比重不同而分层。
金属冶炼锡精炼与提纯工艺

市场需求持续增长
随着电子、化工、食品包装和医 疗器械等行业的不断发展,锡精 炼与提纯的市场需求将持续增长 。
技术创新推动产业
发展
随着科技的不断进步,锡精炼与 提纯技术将不断创新,提高产品 质量和降低成本,推动产业的可 持续发展。
环保要求提高
随着环保意识的提高,锡精炼与 提纯行业将面临更高的环保要求 ,推动产业向绿色、环保方向发 展。
物理方法主要利用杂质与锡的物理性质差异,如密度、熔点、沸点等进行分离。
化学方法则是利用杂质与锡的化学性质差异,通过加入适当的化学试剂,使杂质转 化为易于分离的物质。
锡精炼的方法
常用的锡精炼方法有电解法、真空蒸 馏法、化学提纯法等。
真空蒸馏法是在真空条件下,利用杂 质与锡的沸点差异进行分离。
电解法是利用电解原理,使杂质在电 极上析出或留在阳极泥中,从而达到 提纯目的。
化学提纯法则是通过加入适当的化学 试剂,使杂质转化为易于分离的物质 ,如氯化物、硫化物等。
锡精炼的设备与工具
01
锡精炼的主要设备包括电解槽、 真空蒸馏炉、化学反应釜等。
02
工具包括坩埚、钳子、铁钩等, 用于装载和处理锡原料和精炼产 物。
03
锡提纯工艺
锡提纯的原理
物理法
01
利用锡与其他杂质在物理性质上的差异进行分离,如密度、熔
固体废弃物处理
对固体废弃物进行分类处理, 可回收部分进行回收利用,不 可回收部分进行无害化处理。
噪声控制
采用消音、减震等措施对噪声 进行控制,减少对周围居民的
影响。
05
锡精炼与提纯的应用领域与发 展前景
锡精炼与提纯的应用领域
ห้องสมุดไป่ตู้01
02
锡冶炼过程中的金属精炼技术考核试卷

D.冷凝法
7.以下哪些因素会影响锡熔析精炼的效果?()
A.熔炼温度
B.熔炼时间
C.添加剂的种类和数量
D.粗锡的成分
8.在锡的电解精炼中,以下哪些做法是正确的?()
A.定期清理阴极
B.保持电解质浓度稳定
C.避免阳极过载
D.提高电流密度以加快精炼速度
9.锡精炼过程中,以下哪些金属可以通过加入特定化合物的方式去除?()
A.提高电流效率
B.防止阴极过载
C.避免阴极短路
D.所有以上原因
17.锡精炼过程中,以下哪种方法用于去除粗锡中的铅?()
A.硫酸化处理
B.氯气处理
C.电解处理
D.磷酸处理
18.在电解精炼锡时,通常使用的电解质是什么?()
A.硫酸钠溶液
B.氯化钠溶液
C.硫酸溶液
D.硫酸铜溶液
19.锡精炼过程中,以下哪种操作可能导致产品质量下降?()
4.粗锡中的铜和铅可以通过加入氯化钠去除。()
5.锡的电解精炼中,阴极上只能沉积纯锡。()
6.火法精炼锡的过程中,所有的废气都可以通过冷凝法处理。()
7.在锡的精炼过程中,物理精炼和化学精炼可以完全替代。()
8.定期更换电解质是提高锡电解精炼效率的重要措施。()
9.锡精炼过程中,阳极泥含有较高比例的金属,可以直接丢弃。()
4.针对锡冶炼过程中的废气和废渣处理,请提出几种环保措施,并简要说明其工作原理和效果。
标准答案
一、单项选择题
1. C
2. B
3. B
4. C
5. B
6. B
7. D
8. C
9. D
10. A
11. D
12. B
炼锡工艺流程

炼锡工艺流程
炼锡工艺流程主要包括以下步骤:
1. 矿石破碎:将锡矿石进行破碎,将其粉碎成一定大小的颗粒,以便于后续的焙烧。
2. 焙烧:将锡矿石放入炉中进行高温焙烧,使其中的硫化物分解,生成氧化物。
焙烧温度一般在700℃以上。
3. 还原:将焙烧后的锡矿石与碳一起放入炉中进行还原,使氧化锡还原为金属锡。
还原温度一般在1200℃以上。
4. 精炼:将还原后的锡进行精炼,去除其中的杂质,得到纯净的锡。
此外,炼前处理是为了除去对冶炼有害的硫、砷、锑、铅、铋、铁、钨、铌、钽等杂质,同时达到综合回收各种有用金属的目的。
炼前处理的方法包括精癣焙烧和浸出等作业,根据所含杂质的种类不同,可采用一个或几个作业组成的联合流程。
炼渣用烟化炉挥发方法,这样产出的废渣含锡低,金属回收率高,同时大量减少了铁的循环。
粗锡精炼主要是除去铁、铜、砷、锑、铅、铋和银等杂质,同时综合回收有用金属。
一般分为火法精炼和电解精炼。
以上是炼锡工艺流程的简要介绍,如需了解更多信息,建议咨询专业人士或查阅相关书籍文献。
金属冶炼锡冶炼工艺

锡冶炼技术面临的挑战
高能耗
01
锡冶炼工艺需要消耗大量的能源,如何降低能耗是当前面临的
重要挑战之一。
高污染
02
锡冶炼工艺会产生大量的废弃物,如何减少废弃物的排放和提
高废弃物的处理效率是当前面临的重要挑战之一。
资源短缺
03
锡是一种稀有金属,资源有限,如何提高锡资源的利用率和开
发新的锡资源是当前面临的重要挑战之一。
一些大型锡矿山采用露天 和地下联合开采的方式, 以提高采矿效率。
锡矿的预处理技术
选矿
通过物理或化学方法将锡 矿石中的有用成分富集, 提高品位,以便于后续的 冶炼。
烧结
将锡矿石粉与适量的黏土 或石灰石粉混合后,在高 温下烧结成块状,以提高 其机械强度和冶炼性能。
球团
将锡矿石粉与适量的黏土 、水和膨润土混合后制成 球团,经过干燥和烧结后 用于冶炼。
锡冶炼工艺的历史和发展
历史
锡冶炼工艺已有数百年的历史。早期的锡冶炼工艺主要采用简单的火法炼锡, 随着技术的发展,逐渐演变为现代的湿法炼锡工艺。
发展
随着环保要求的提高和技术的不断进步,锡冶炼工艺也在不断改进和完善。新 型的锡冶炼工艺在提高锡的回收率、降低能耗和减少环境污染方面取得了显著 进展。
锡冶炼工艺的基本原理
冶炼过程
火法冶炼过程包括炼化、熔炼、精 炼等步骤,以获得纯度较高的锡。
火法冶炼的特点
火法冶炼具有较高的生产效率和较 低的成本,但会产生一定的废气和 废渣。
锡的湿法冶炼
湿法冶炼原理
湿法冶炼是通过化学反应将锡精 矿中的锡提取出来。
提取过程
湿法冶炼过程包括浸出、净化、 电解等步骤,以获得纯度较高的
锡。
一种高纯锡的制备方法

一种高纯锡的制备方法
制备高纯度的锡可以采用多种方法,以下是一种常见的制备高纯锡的方法:
1. 高温精炼法:首先,将普通的锡材料放入高温熔炉中进行熔化。
随着温度的升高,杂质和其他材料会在熔融锡表面形成氧化物或其他化合物的形式,形成浮渣。
然后,将浮渣从熔融锡中分离出来。
重复这个过程几次,可以逐渐提高锡的纯度。
2. 电解法:这种方法利用电解的原理来分离杂质。
将锡放置在电解槽中作为阳极,将纯净的金属作为阴极,然后在一定的电流和温度条件下进行电解。
通过电解反应,杂质会被逐渐聚集在阳极上,而纯净的锡则沉积在阴极上。
经过多次电解,可以得到高纯度的锡。
3. 气相冷凝法:这种方法利用锡的蒸汽在低温条件下冷凝的特性来分离杂质。
首先,将锡材料加热到高温,使其蒸发成蒸汽。
然后,将蒸汽通过冷凝器,使锡重新凝结成纯净的金属。
由于不同杂质的沸点和凝点不同,可以通过控制冷凝温度和速度来实现对杂质的分离。
这些方法都可以用于制备高纯度的锡,但具体的操作条件和步骤可能会因实际情况而有所不同。
粗锡火法精炼除杂工艺除铜实践及除砷试验探索

粗锡火法精炼除杂工艺除铜实践及除砷试验探索许耀月(云南锡业股份有限公司冶炼分公司,云南 个旧 661000)摘 要:针对锡火法精炼中粗锡杂质不稳定,砷铁比不稳定,传统方法在粗锡精炼除杂过程中作业时间长,添加剂单耗高的问题,通过将熔融后的粗锡溶液中加入硫元素以及自身中含有的硫元素,与粗锡中的主要杂质铜发生反应,将形成的铜化合物去除;将除铜后的粗锡溶液中加入硝石,再利用NaCl吸收粗锡中的砷与硝石发生反应得到的砷酸盐,以此完成粗锡火法精炼除杂,得到高纯度的锡。
关键词:粗锡;火法精炼;除杂;除铜;除砷中图分类号:TF811 文献标识码:A 文章编号:1002-5065(2019)23-0016-2Practice of Copper Removal and Arsenic Removal by Crude Tin Fire Refining ProcessXU Yao-yue(Smelting Branch of Yunnan Tin Industry Co., Ltd., Gejiu 661000,China)Abstract: In view of the instability of crude tin impurities and unstable arsenic-iron ratio in tin-fired refining, the traditional method has a long operation time and a high consumption of additives in the process of removing impurities in crude tin refining. Add sulfur and the sulfur contained in it, react with the main impurity copper in crude tin to remove the copper compounds formed; add the saltpeter to the crude tin solution after removing copper, and then use NaCl to absorb arsenic in the crude tin The arsenate obtained by reacting with saltpeter is used to complete the crude tin pyrolysis to remove impurities and obtain high-purity tin.Keywords: crude tin; fire refining; impurity removal; copper removal; arsenic removal为了满足工业对锡纯度要求,将火法精炼除杂工艺用于粗锡提纯中。
锡的火法精炼

锡的冶炼--锡的火法精炼一、粗锡的精炼(一)杂质对锡性质的影响锡精矿还原熔炼产出的粗锡含有许多许多杂质,即使是从富锡精矿炼出的锡其纯度通常也不能满足工业应用上的要求。
为了达到标准牌号的精锡,总要进行锡的精炼。
粗锡中常见的杂质有铁、砷、锑、铜、铅、铋和硫,对锡的性质影响较大。
铁:含0%~0.05%Fe,锡的腐蚀性和可塑性没有明显的影响;含铁量化合物生成,锡的硬度增大。
达到百分之几后,锡中有FeSn2砷:砷有毒。
包装食品和生活用品的锡箔、镀锡薄板用的锡,含砷量限定在0.015%以下。
砷引起锡的外观和可塑性变坏,增加锡液的粘度。
含有0.055%As,锡硬度增至布氏硬度8.7,锡的脆性也增大,锡的断面成粒状。
锑:含0.24%Sb,对锡的硬度和其他机械性能没有显著的影响。
含锑升高到0.5%,锡的伸长率降低,硬度和抗拉强度增加,但锡展性不变。
铜:用作镀层的锡含铜越少越好,因为铜不仅形成有毒的化合物,还会降低镀层的稳定性。
含有约0.05%Cu,会增加锡的硬度、拉伸强度和屈服点。
铅:镀层用的锡含铅不应大于0.04%,因为铅的化合物有互性。
用于马口铁镀锡的精锡近年要求含铅量更低,最好能低于0.01%,以保证食品的质量。
铋:含0.057%Bi的锡,拉伸强度极限13.72MPa(纯锡为18.62 MPa~20.58MPa),布氏硬度4.6(纯锡为4.9~5.2)。
铝和锌:在镀锡中含铝或锌不应大于0.002%。
含锌大于0.24%,锡的硬度增加3倍,并降低锡的延长率。
(请补充铝对锡的影响)(二)粗锡的一般成分及精锡标准各冶炼厂生产的粗锡成分波动范围很大,这主要取决于锡精矿的成分、精矿炼前处理作业及处理的工艺流程等。
一般而言,粗锡成分大体可分为三类,一类是处理冲积砂矿所获得的很纯净锡精矿,含锡在75%以上,含杂质很少,采用反射炉两段熔炼,其粗锡含锡在99%以上,只含少量的杂质元素;第二类是处理脉锡矿所获得的含锡在50%以上的锡精矿,经过炼前处理除去部分杂质后采用一段还原熔炼,其粗锡含锡99%以上,含有较高的杂质元素;第三类是处理脉锡矿所获得的含锡约40%的锡精矿,其它杂质含量高,又没有炼前处理作业,其粗锡品位在80%左右,粗锡中杂质元素含量高。
有色冶金概论-锡冶金
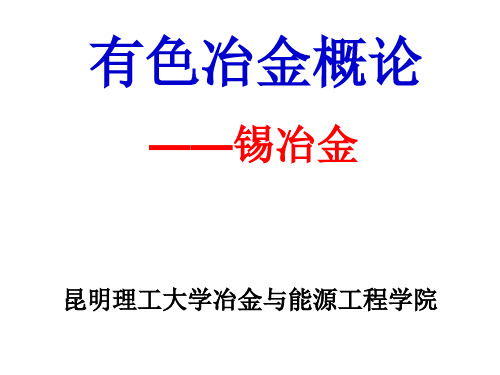
6.1 概述
我国炼锡厂大多采用“锡精矿还原熔炼 - 粗锡火法精炼 - 焊 锡电解或真空蒸馏-锡炉渣烟化处理”的工艺流程,使用的还原 熔炼设备主要是反射炉、电炉、回转短窑熔炼技术、卡尔多炉 和澳斯麦特炉,其中澳斯麦特炉最有广泛的工业应用前景。我 国锡冶炼工艺的特点是适于处理中等品位的锡精矿,并采用烟 化炉处理富锡炉渣以取代传统的二段熔炼法。 我国锡冶炼技术在很多方面居于世界先进水平:烟化炉硫 化挥法直接处理富锡炉渣已被世界各国炼锡厂广泛采用 ;以电 热连续结晶机脱除粗锡中的铅和铋,继之用真空蒸馏炉处理结 晶机的副产品粗焊锡,成为我国锡火法精炼的特色之一。电热 连续结晶机已成为锡火法精炼系统的标准设备,被誉为20世纪 锡冶金工业最重大的发明之一。
6.3 炼锡原料及方法
(2)还原熔炼
锡精矿还原熔炼所用的设备主要为奥斯麦特炉、反射炉、电 炉。电炉温度高,还原气氛强,既适于还原难熔精矿,又适于 炼渣,特别适宜于处理含铁比较少的锡精矿。 在锡的还原熔炼过程中,铁的还原是不可避免的。高温时, 铁在锡中的溶解度大,随着温度的下降,铁便从锡液中析出, 析出的块状晶体称为硬头。 在一定的还原条件下,还原出的铁(或加入的含铁物料) 可以作为锡的还原剂,因此精矿熔炼加入硬头和精炼浮渣等含 铁物料配料是合理的,但这个还原作用受到粗锡允许含铁量的 限制。粗锡含铁越低,炉渣含锡(SnO)越高。
6.3 炼锡方法
云锡Ausmelt熔炼工艺流程
6.3 炼锡原料及方法
(2)还原熔炼
SnO2被还原成金属锡,要经过SnO的阶段,SnO是易挥发 的化合物,不可避免的会有锡与SnO的挥发,而且还原生成的 金属锡在氧化气氛下也会生成SnO挥发,降低锡的直收率。
SnO是弱碱性物质,能与酸性氧化物如 SiO2 形成低熔点炉 渣,降低锡的直收率。
锡的冶炼与炼锡流程

通过化学反应,使锡从溶液中 沉淀出来。
精制
将沉淀物中的杂质去除,得到 纯锡。
湿法冶炼工艺流程
包括酸浸、沉淀、精制等工序 ,得到纯锡。
03
炼锡流程
原料准备
锡精矿
从矿山开采出的锡矿石经过破碎、磨 细、选矿等工序后得到锡精矿。
备料
将锡精矿和其他辅助原料按照一定比 例混合,准备好用于熔炼的原料。
辅助原料
土壤污染
炼锡过程中产生的废渣和废弃物中含有的重金属离子和有害物质会 渗透到土壤中,对土壤生态造成破坏。
锡冶炼的可持续发展
节能减排
采用先进的生产技术和设备,提高能源利用效率 ,减少能源消耗和污染物排放。
资源回收利用
对炼锡过程中产生的废渣和废弃物进行回收和再 利用,提高资源利用率。
生态恢复
对受到污染的土壤和水体进行治理和生态恢复, 促进生态系统的平衡和可持续发展。
炼锡过程中需要添加适量的辅助原料 ,如铁矿石、石灰石、萤石等,以调 整熔炼过程中的化学成分和物理性质 。
熔炼
熔炼目的
将备料加热至高温,使锡 和其他杂质元素分离,得 到粗锡。
熔炼设备
常用的熔炼设备有反射炉 、电炉、感应炉等。
熔炼过程
在高温下,锡精矿中的锡 与其他杂质元素发生反应 ,形成熔融状态,通过除 去杂质,得到粗锡。
制定更加严格的环保法规和标准,加大对违法行为的处罚力度。
提高环保意识
加强环保宣传教育,提高企业和公众的环保意识。
推广环保技术
鼓励企业采用环保技术和设备,推动绿色生产。
THANK YOU
开发新的冶炼技术和方法
探索新的冶炼工艺
研究新的冶炼技术和方法,提高锡的提取率和纯度,降低环境污 染。
- 1、下载文档前请自行甄别文档内容的完整性,平台不提供额外的编辑、内容补充、找答案等附加服务。
- 2、"仅部分预览"的文档,不可在线预览部分如存在完整性等问题,可反馈申请退款(可完整预览的文档不适用该条件!)。
- 3、如文档侵犯您的权益,请联系客服反馈,我们会尽快为您处理(人工客服工作时间:9:00-18:30)。
锡的冶炼--锡的火法精炼一、粗锡的精炼(一)杂质对锡性质的影响锡精矿还原熔炼产出的粗锡含有许多许多杂质,即使是从富锡精矿炼出的锡其纯度通常也不能满足工业应用上的要求。
为了达到标准牌号的精锡,总要进行锡的精炼。
粗锡中常见的杂质有铁、砷、锑、铜、铅、铋和硫,对锡的性质影响较大。
铁:含0%~0.05%Fe,锡的腐蚀性和可塑性没有明显的影响;含铁量化合物生成,锡的硬度增大。
达到百分之几后,锡中有FeSn2砷:砷有毒。
包装食品和生活用品的锡箔、镀锡薄板用的锡,含砷量限定在0.015%以下。
砷引起锡的外观和可塑性变坏,增加锡液的粘度。
含有0.055%As,锡硬度增至布氏硬度8.7,锡的脆性也增大,锡的断面成粒状。
锑:含0.24%Sb,对锡的硬度和其他机械性能没有显著的影响。
含锑升高到0.5%,锡的伸长率降低,硬度和抗拉强度增加,但锡展性不变。
铜:用作镀层的锡含铜越少越好,因为铜不仅形成有毒的化合物,还会降低镀层的稳定性。
含有约0.05%Cu,会增加锡的硬度、拉伸强度和屈服点。
铅:镀层用的锡含铅不应大于0.04%,因为铅的化合物有互性。
用于马口铁镀锡的精锡近年要求含铅量更低,最好能低于0.01%,以保证食品的质量。
铋:含0.057%Bi的锡,拉伸强度极限13.72MPa(纯锡为18.62 MPa~20.58MPa),布氏硬度4.6(纯锡为4.9~5.2)。
铝和锌:在镀锡中含铝或锌不应大于0.002%。
含锌大于0.24%,锡的硬度增加3倍,并降低锡的延长率。
(请补充铝对锡的影响)(二)粗锡的一般成分及精锡标准各冶炼厂生产的粗锡成分波动范围很大,这主要取决于锡精矿的成分、精矿炼前处理作业及处理的工艺流程等。
一般而言,粗锡成分大体可分为三类,一类是处理冲积砂矿所获得的很纯净锡精矿,含锡在75%以上,含杂质很少,采用反射炉两段熔炼,其粗锡含锡在99%以上,只含少量的杂质元素;第二类是处理脉锡矿所获得的含锡在50%以上的锡精矿,经过炼前处理除去部分杂质后采用一段还原熔炼,其粗锡含锡99%以上,含有较高的杂质元素;第三类是处理脉锡矿所获得的含锡约40%的锡精矿,其它杂质含量高,又没有炼前处理作业,其粗锡品位在80%左右,粗锡中杂质元素含量高。
粗锡的一般成分列表4-1。
锡锭的化学成分,应符合表4-2的规定成分。
(三) 锡的精炼方法精炼锡通常采用火法冶金和湿法冶金(电解)两种方法。
火法精炼锡的过程是由一系列的连续作业组成的,其中每一种业能够除能够除去一种或两种杂质。
火法的优点是生产能力较高,并且不使金属长期停滞在生产过程中,积压的锡量少。
此外,火法精炼使杂质能够依次地提取出来,并富集于各种精炼渣中,这就为综合回收这些金属提供了条件。
国内外炼锡厂多数厂是以火法精炼为主,辅以电解精炼,少数冶炼厂采用全电解精炼。
火法精炼是利用锡与杂质对氧、硫和氯的亲合力的差别,以及与杂质生成不溶于液于液体锡的化合物的药剂作用,来达到精炼目的。
这些工序具有一个共同的特点,即生成的化合物杂质浮在液体锡上,可以固体或粘性产物形式从金属表面捞去。
二、锡的火法精炼(一)火法精炼的原则流程各炼锡厂粗锡所含杂质不同,生产规模不同,以及原料供应及设备条件不一样,因而火法精炼流程也不一样。
对于熔炼含杂质少的高品位精矿所产的粗锡,如马来西亚、泰国等,只用1~2道火法精炼作业就能得到高级精锡,精炼回收率达到99.45%。
处理粗锡含杂质高的火法精炼流程比较长。
我国某冶炼厂,由于粗锡杂质含量高,采用图4-11所示的火法精炼流程,其中每一道作业除去一种或两种杂质,而有的杂质在几种作业中逐步除去。
例如砷就在三个作业中相继除去(离心除铁、砷,凝析除铁、砷,加铝除砷、锑)。
图4-11 锡火法精炼原则流程(二)熔析、凝析法除铁、砷熔析法、凝析法的理论根据是铁、砷等杂质在锡液中与锡生成的高熔点金属间化合物在锡液中的溶解度随温度升高而增大。
熔析法将含铁、砷高的固体粗锡(生产中称为乙粗锡),加热到锡熔点以上,高熔点金属间化合物保持固体状态,而锡熔化成液体,分开固体和液体,从而使锡与铁、砷分离;相反,凝析法是将含铁、砷料低的已熔成液体粗锡(称为甲粗锡)降温,由于溶解度降低,铁、砷及其化合物结晶为固体析出,分离出固体后,得较纯的液体锡,达到锡与铁、砷分离。
1.熔析法、凝析法除铁、砷的原理锡精矿还原熔炼得到的乙粗锡是以锡为主含铁、砷较高的粗锡,一般含 1.5%~5%As,1%~10%Fe。
根据Sn-Fe系状态图(图4-12),锡和铁生成Fe3Sn、Fe3Sn2、Fe1.3Sn、FeSn、FeSn2等金属间化合物。
取Sn-Fe系的富锡端部分状态图(图4-13)说明加热过程中铁与锡分离的情况,当温度升到232℃,开始熔析出较纯的液体锡并不断移去,温度在232~496℃间,铁以FeSn2化合物保持固体状态留在粗锡残锭上。
当温度由496℃升到901℃时,含铁的粗锡残锭中不断熔化并析出未形成化合物的液态残锡外,同时金属间化合物不断分解而析出液态锡,而剩下的Sn-Fe合金视熔析温度不同分别以FeSn、Fe3Sn2、Fe3Sn、ɑ-Fe等形态残留在固相残渣中(称为熔析渣)。
可见,在升温过程中固体渣(熔析渣)含锡逐渐降低,而含铁逐渐升高;相反,熔析出的锡随温度升高,含铁量上升,其铁的溶解度值为:从Sn-As系状态图(图4-14)富锡端可以看出,砷或Sn3As2化合物在锡液里的溶解度随随温度上升而增大。
熔析温度在232~596℃时,Sn3As2保持固体状态与锡液分离,超过596℃,Sn3As2将熔化,失除砷作用,故处理含砷高而含铁低的粗锡时,熔析温度应低于596℃。
粗锡中铁、砷同时存在,对熔析除铁、砷有利,因为铁对砷的亲合力大,生成两个化合物Fe2As(熔点931℃)和FeAs(熔点1031℃),其间还有ε相(Fe3As2)包晶化合物。
这些化合物和ε相的熔点和分解解温度都很高而保留于熔析渣里。
粗锡中存在许多杂质,相互生成一些难熔化合物,表4-3列出可能存在的化合物,这些化合物在乙粗锡熔析时大部分留在固体渣(熔析渣)中,因此,熔析除铁、砷时,也附带除去一些别的杂质,如硫、锑、铜等。
熔析法可除去粗锡中大部分铁、砷,但不能使其含量达到符合精锡标准,因此,在熔析除铁、砷后粗锡需经凝析法处理。
凝析法是将液体精锡降温,铁和砷在锡液中的溶解度减小,达到过饱和状态成固休析出而分离。
在锡的熔点232℃时,铁的溶解度为0.001%,在300℃时,铁的溶解度为0.0046%。
因此,将粗锡液温度降低到锡深点附近,由锡液中凝析出FeSn2的细粒晶体,可使含铁量降低到约0.001%,能满足精锡的含铁要求。
在相同温度下锡液能溶解的砷量比铁多。
在232℃时,砷的溶解度为0.14%~0.18%。
锡液中若有铁和砷共同存在,对除砷有利,锡液中As/Fe值减少时温度对砷在锡液中溶解度的影响。
故锡液中有铁存在时有利于凝析除砷。
2. 熔析法除铁、砷实践的生产工艺及设备在炼锡厂熔析设备主要用反射炉,少数也用电炉。
用反射炉作熔析设备,其炉床为斜底,面积较小。
否则加入乙粗锡。
熔析作业后期翻渣出渣都不方便,炉内各点温度也不均匀,炉床面积以10m2左右为宜。
炉床用粘土砖砌成,三面高,向放锡口方向倾斜。
也有的工厂炉床分为两个区,温度较高的区域靠近燃烧室,用耐火砖砌成,靠炉尾一端是温度较低的区域,用生铁板做成,粗锡先在低温区熔析,而后再扒到高温区处理。
熔析法为间断作业,在反射炉中操作,每个工班处理一炉,也有三个班处理四炉的。
出完前一炉熔析渣,炉温尚保持在700℃以上,接着进下一批乙粗锡。
锡锭从侧墙炉门加入,也有从炉顶加入到炉膛中,靠近火室的一端多加些锡锭,靠炉气出口的一端少些,使乙锡受热均匀。
乙粗锡进完后,炉温下降至300℃,然后逐渐升温,使熔析速度加快。
熔析过程到后期,开始翻渣,把料堆底部受热少含锡高的固休料翻到面上,以便升高温度,降低含锡量,炉温相应地提高到800~900℃。
当发现熔析渣有变稀的趋势时,应降低炉温,避免生成Sn-Fe合金大块,这样才能降低熔析渣含锡,同时又不致给出渣和清炉造成困难。
翻渣操作每炉2~3次。
当熔析渣变成红色粒状/表面无锡珠,便可出渣。
从开始进料到出渣完毕约4~7h;但遇到处理含砷高而含铁很低的乙粗锡,因熔析温度不允许升得太快和过高(低于600℃),作业时间长达8~9h。
熔析控制的技术条件主要是温度。
3.凝析法除铁、砷实践生产工艺及设备火法精炼中凝析除铁、砷,加铝除锑、砷和加硫除铜所用的制设备都由精炼锅的搅拌两部分组成。
在操作中有的工厂采用空气、蒸汽吹炼液体锡。
采用这种方法时,除去部分铁与其杂质一起除去。
熔锡由沉降桶直接倒入大铸铁锅中,并鼓风或使蒸汽通过熔化的锡,使其“沸腾”。
在靠近锅附近的鼓风管或蒸汽管内安装聚水器,因为液态水的任何“液滴”,若被鼓入熔融锡内,将引起猛烈爆炸。
在金属表面上有糊状的浮渣生成,捞去浮渣。
此外,有的炼锡厂,由于铅、砷、锑在焙烧时除去,铜、铋含量极少,需要除去的杂质只有铁,因此,只需将反射炉精锡冷却至300℃,用浮渣笼取去表面渣,吹入0.49MPa的压缩空气保持温度400℃,扒渣两次,即得到精锡,全部过程只用3.5~5小时。
凝析除铁、砷采取加锯木屑促使晶体悬浮物与液体锡达到分离。
粗锡装锅后,锡液的温度为280℃~300℃,观察有无砷、铁化合物结晶析出。
如果锡液的温度高,看不到砷、铁化合物结晶析出时,则应降温搅拌,加入适量的锯木屑,捞去浮渣(炭渣),呈现洁净的锡液面。
随着温度逐步降低,砷、铁化合物结晶析出逐渐增多,如果粗锡含砷多,含铁很少,Sn3As2结晶析出,锡液面上有砂粒状耀眼的粒子,这时降温凝析、搅拌凝聚,投进锯木屑吸附,投入量以不影响旋涡正常为适度,并捞去浮渣。
要多次降温、搅拌、加锯木屑、捞去浮渣重复操作。
结粗锡含水量铁、砷相等或铁比砷多的情况,液态粗锡降温冷却时,铁和砷优先结合,生成Fe—As固体化合物。
它们的密度小于锡液的密度,上浮在锡液表面,再加上它们凝聚性强,凝聚成非常粘稠的浮渣。
这时开始搅拌并加入锯木屑,促使晶粒凝聚和上浮,锯木屑也增加这些浮渣的孔隙度,有助锡液滴汇聚增大,穿过浮渣层回到锡液中。
上述作业也要反复多次进行,直到将温度降至锡液熔点附近,强烈搅拌而不再析出渣子,则铁已除到0.003%以下,砷达到0.03%以下,完成凝析作业。
利用砷和铁的性质曾做过生产实验。
粗锡中的砷除到0.2%以下时,往锡液中加入一些含铁高的粗锡,而后凝析加锯木屑,可进一步降低砷在锡中的含量。
但粗锡含砷在0.2%以上时,补加铁就没有意义了。
此时,没有铁的存在,砷不仅能以Sn3As2结晶析出,而且产出的晶体粒子相互碰撞而长大,无粘稠性。
所产生的炭渣机械带走的锡很少。