机床主要参数的确定
数控机床分级变速机构主要参数的确定

数控机床分级变速机构主要参数的确定1. 介绍数控机床是现代制造业中的重要设备之一,其在加工工艺中发挥着重要作用。
分级变速机构是数控机床中的一个关键组成部分,它可以实现不同转速下的加工效果,从而满足不同加工要求。
本文将介绍数控机床分级变速机构主要参数的确定方法。
2. 常见的数控机床分级变速机构类型数控机床分级变速机构主要包括平行轴齿轮传动、行星齿轮传动、同步带传动等类型。
这些传动方式各自有不同的优点和适用范围,其中平行轴齿轮传动是最常见的一种。
3. 主要参数的确定在进行数控机床分级变速机构参数设计时,需要同时考虑多个方面的因素。
以下是主要参数的确定方法:3.1. 转差系数转差系数是指两个相邻齿轮之间的转速比,其大小直接影响到机床的加工精度和效率。
通常情况下,转差系数应在1.3~1.5之间,过大过小都会影响机床的加工质量。
3.2. 分级比和齿轮模数分级比和齿轮模数是数控机床分级变速机构的两个重要参数。
分级比是指整个机构的转速比,而齿轮模数则是齿轮的直径和齿数之比。
这两个参数的选取应考虑到机床所需的加工精度和转速范围等因素。
3.3. 齿数和齿宽齿数和齿宽是数控机床分级变速机构中的重要设计参数。
齿数的选取应以分级比、齿轮模数等参数为基础,同时还要考虑到机床所需的传动功率和齿轮的强度等因素。
而齿宽则直接影响到齿轮的强度和使用寿命,应根据实际情况加以确定。
4. 总结数控机床分级变速机构的设计和参数的选择对于机床的加工质量和效率都有着重要的影响。
在设计过程中要兼顾多个因素,在不断优化和改进的基础上,使机床的性能和质量不断提升,从而更好地适应现代制造业的发展需求。
5、标准机床参数的设定

标准机床参数的设定1)多次按压MDI键盘上的[SYSTEM]按键,直至屏幕横向功能条出现[参数设定],通过对应横向软键选择,选择后,画面跳转为[参数设定支援]画面。
2)移动光标至[轴设定],通过横向软件选择[操作]---[初始化]---出现[是否设定初始值?]---选择[执行],系统自动将轴设定中的相关参数设定为标准值。
3)设定完成后,将跳转至[报警信息]画面,并增加了[PW0000 必须关断电源]的报警,忽略此报警,再次选择[SYSTEM]按键,进入[参数设定支援]画面,移动光标至[轴设定]处,通过横向软键选择[操作]---[选择],进行以下标准参数设定。
轴设定参数设置列表参数号参数名称参数中文注解设定值1006#3 X DIA 各轴的移动指令为:0: 半径指定。
1: 直径指定。
11320 XZ LIMIT + 各轴的存储行程限位的正方向坐标值调试期间不使用软限位时,此参数设置为-1.机床动作调试完毕后,此参数设置应距离硬件限位5mm。
1321 XZ LIMIT - 各轴的存储行程限位的负方向坐标值调试期间不使用软限位时,此参数设置为1.机床动作调试完毕后,此参数设置应距离硬件限位5mm。
1410 DRY RUN RATE 空运行速度此参数设置为机、电、液协议中轴快速移动速度的一半1420 XZ RAPID FEEDRATE 各轴的快速移动速度此参数设置为机、电、液协议中轴快速移动速度。
1421 XZ RAPID OVR F0 每个轴的快速移动倍率的F0 速度200mm200mm1423 XZ JOG FEEDRA TE 每个轴的JOG 进给速度1000mm1000mm1424 XZ MANUAL RAPID 每个轴的手动快速移动速度此参数设置为机、电、液协议中轴快速移动速度的一半1425 XZ REF RETURN FL 每个轴的手动返回参考点的FL 速度300mm300mm1428 XZ REF FEEDRA TE 每个轴的参考点返回速度3000mm3000mm4)设置参数完毕后,选择横向软键左侧的[回退键],并通过横向软键选择[参数设定],返回至上一级画面,移动光标至[伺服设定]处,通过横向软键选择[操作]---[选择],进入[伺服设定]参数画面,并根据下表设置相应参数 参数名称 中文注解设定值电机代码由于0ID 系统要求使用HRV2功能,所以调试时应根据电机铭牌查询电机代码,并加100为设定值。
如何正确选择数控机床的使用参数

如何正确选择数控机床的使用参数数控机床作为一种重要的现代化加工设备,广泛应用于汽车制造、航空航天、机械制造等领域。
选择正确的使用参数对于保证加工质量、提高生产效率至关重要。
本文将从机床的类型、加工材料、加工工艺等方面来探讨如何正确选择数控机床的使用参数。
首先,在选择数控机床的使用参数之前,我们需要了解加工的具体需求以及机床的类型。
数控机床有多种类型,包括铣床、车床、钻床等,每一种类型的机床在使用参数上也会有所不同。
例如,在选择车床的使用参数时,需要考虑所加工零件的直径、长度、精度等因素。
在选择铣床的使用参数时,则需要考虑工件的尺寸、表面粗糙度要求、加工刀具的类型等因素。
因此,在选择数控机床的使用参数时,必须充分了解所加工零件的具体要求,合理选择机床类型,并根据不同类型的机床进行参数的设置。
其次,在选择数控机床的使用参数时,需考虑所加工材料的类型、性质和硬度。
不同的材料对机床的使用参数有着不同的要求。
例如,对于硬度较高的金属材料,应选择较高的切削速度和进给速度,以确保切削刀具与工件之间的接触时间较短,并减小切削力,提高加工效率。
而对于脆性材料,应选择较小的进给速度和切削速度,以避免过大的切削力造成工件断裂或表面破坏。
在选择数控机床使用参数时,必须根据材料的性质和硬度来调整切削速度、进给速度、进给深度等参数,以实现最佳的加工效果。
此外,在选择数控机床使用参数时,还需要考虑具体的加工工艺。
不同的加工工艺对机床使用参数有着不同的要求。
例如,在进行粗加工时,应选择较大的进给速度和切削速度,以提高加工效率;而在进行精加工时,则需要选择较小的进给速度和切削速度,以提高加工精度。
另外,还需要注意切削液的使用,以降低加工温度、延长刀具寿命,并减少切削过程中产生的摩擦和磨损。
在选择数控机床使用参数时,必须根据具体的加工工艺要求,合理调整各项参数,以实现高效、精确的加工。
最后,在选择数控机床使用参数时,还需要充分考虑机床本身的性能指标和技术参数。
第七章 机床主要参数的确定.
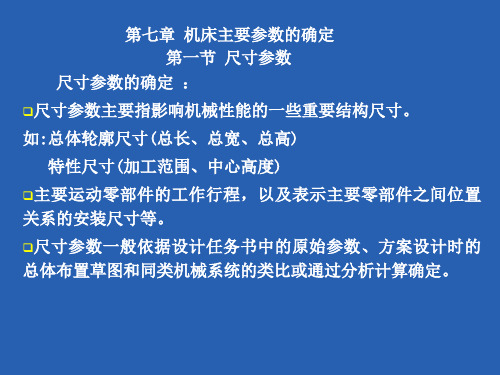
一、主运动电动机功率的确定 机床主运动的功率包括:切削功率P切、空转功率P空和附加机械
摩檫损失P机三部分。 P切与刀具及工件材料有关,普通机床一般根据重负荷切削条
件确定。 P空(KW)随各轴转速变化、摩檫搅油、空气阻力等造成。中型
机床用试验公式估算:(教材P124) P机(附加机械磨擦损失功率)取决于各传动副的机械效率,
——工作台工作面宽度(第二工作面长度) (5)卧式镗床——主轴直径 (6)钻床——钻孔直径
第二主参数 车床-最大工件长度 铣床、龙门刨床-工作台面
其他 车床-刀架工件回转直径,主轴孔 龙门铣床-横梁最高、最低位置
第二节 运动参数
重点掌握以下几个问题: 1、哪些参数属于运动参数? 2、什么是主运动参数、进给运动参数? 3、如何确定机床的最高、最低转速? 4、分级变速采用什么数列? 5、如何选择公比?
作回转主运动机床的主参数是主轴转速,转速与切削速 度的关系是:
n = 1000v/πd。
1.主轴最低(nmin)和最高(nmax)转速的确定 nmin = 1000vmin/πdmax, nmax = 1000vmax/πdmin
(变速范围为 nmax和nmin的比值,即Rn = nmax/nmin)。
通用机床需要确定转速范围(最高、最低转速)及转速
级数(专用、组合机床除外)
1、最高、最低转速的确定(P121) 2、分级变速时的主轴转速数列 *机床的转速按等比数列分级
Байду номын сангаас3、变速范围
Rn=nmax/nmin
4、标准公比和标准数列表7-1
5、公比的选择
从使用性能考虑,小点好!可减少相对功率损失,但使
机床结构复杂,要简化结构要取的大些。
机床的主要指标

这里所说的数控机床主要指标以数控切削机床为主,其他类型机床因与具体工艺关系密切在此不作说明。
数控切削机床主要指标有精度指标、运动性能指标和功能指标。
1)精度指标精度指标包括定位精度和重复定位精度、分辨率和脉冲当量。
(1)定位精度是指机床各轴在数控系统控制下的移动部件在确定的终点所达到的实际位置精度,移动部件实际位置与理想位置之间的误差等,它直接影响零件加工的位置精度。
(2)重复定位精度是反映轴运动稳定性的基本指标,是指在同一数控机床上,应用相同程序代码到达某同一位置所得到连续结果的一致程度。
一般情况下,重复定位精度是呈正态分布的偶然误差,它主要受伺服系统特征、进给系统的间隙与刚性及摩擦特征等因素的影响。
(3)分辨率是指位移和速度两个相邻的分散细节之间可以分辨的最小间隔。
脉冲当量是指数控系统发出的一个进给脉冲使机械运动机构产生的相应位移量,一个脉冲对应的这个位移即为脉冲当量,共数值大小决定机床的加工精度和表面质量。
2)运动性能指标运动性能指标包括主轴系统、伺服驱动系统、坐标行程的技术指标等。
(1)主轴系统的指标主要有主轴转速、扭矩与功率。
目前机械主轴的转速一般在8000r/min以下,扭矩较大;高速主轴转速在10000r/min以上,但扭矩要低于机械主轴。
(2)伺服驱动系统直接控制着机床的进给速度。
进给速度是影响零件加工质量、生产效率以及刀具寿命的主要因素,它受数控装置的运算速度、机床动态特性以及工艺系统刚性等因素的影响。
(3)数控机床各坐标(直线轴、旋转轴)行程的大小构成机床的空间加工范围和曲面加工能达到的状态,是直接体现机床加工能力的指标参数。
(4)进给运动的位移速度和定位精度两个技术指标又是相互制约的,位移速度要求越高,定位精度就越难提高。
3)功能指标功能指标主要包括可控轴数和联动轴数、插补功能、刀具参数补偿功能、监测功能等。
(1)可控轴数是指数控装置能够控制的坐标数;联动轴数是指数控装置控制的坐标轴同时到达空间某一点的坐标数,表示数控装置可同时控制按一定规律完成一定轨迹插补的协调运动控制能力。
61125数控车床参数

61125数控车床参数61125数控车床是一种常见的数控加工设备,它具有多种参数和特性。
首先,让我们从机床的基本参数开始:1. 加工直径,61125数控车床通常具有加工直径的参数,这是指它能够加工的工件的最大直径范围。
这个参数通常是车床的重要参考指标之一。
2. 加工长度,这个参数指的是数控车床能够加工的工件的最大长度范围,也是评价车床加工能力的重要参数之一。
3. 主轴转速,主轴转速是指数控车床主轴的旋转速度范围,通常以转/分或者r/min为单位。
主轴转速的范围将影响到车床的加工适用范围,比如对于不同材料的加工需要不同的转速。
4. 主轴孔径,主轴孔径是指数控车床主轴的孔径大小,这个参数将决定车床能够加工的材料直径范围。
5. 主电机功率,主电机功率是指数控车床主轴驱动电机的功率大小,通常以千瓦(kW)为单位。
主电机功率的大小将直接影响车床的加工能力和效率。
6. X、Z轴行程,X、Z轴行程是指数控车床在X、Z方向上的行程范围,它决定了车床能够加工的工件尺寸范围和加工精度。
7. 快进速度,快进速度是指数控车床在空转状态下X、Z轴的最大移动速度,它影响了车床的加工效率。
8. 定位精度,定位精度是指数控车床在加工过程中的定位精度,这个参数直接关系到加工零件的尺寸精度和加工质量。
此外,61125数控车床还可能具有其他特殊的参数和功能,比如自动换刀、刀具库容量、冷却系统等。
这些参数和功能将根据具体的车床型号和厂家而有所不同。
总的来说,61125数控车床作为一种常见的数控加工设备,具有多种参数和特性,用户在选购和使用时需要根据实际加工需求进行综合考虑。
第7章机床主参数
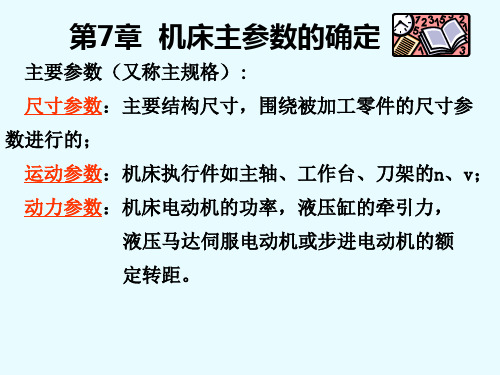
及其它参数。
7.2.4 公比的选用原则
1
● A=1- : 对于通用机床,为使转速损失不大,机床结构又不过于
复杂,一般取 =1.41 or 1.26
●对于大批量生产用的专门化机床,自动化机床,公比应取的小
一些,一般取 =1.12 or 1.26。因为这类机床的生产率高,转速损
失影响较大;另一方面,这类机床不常变速,变速机构可采用变换 齿轮机构,后者能实现小的公比,而结构又比较简单。
●对于大型机床,公比应 取的小一些,一般 = 1.26、
1.12、1.06。因为大型机床切削加工时间长,转速损失的 影响较大。如铣床类。
● 对于非自动化小型机床,公比应取的大一些,一般
取 为1.58、1.78或2,因为在这类机床上,辅助时间
较多,而切削时间所占比重不大,转速损失的影响不大。
7.3 动力参数
如果加工某一工件需要的最有利的切削速度为v,相应
的转速为n:
nj﹤n﹤nj+1
如果采用较高的转速nj+1,必将提高v,刀具耐用度将
降低,以采用较低转速为宜。
这时转速损失为: n- nj 相对转速损失为: A= (n- nj)/n
A= limn n j= n j1 n j = 1- n j
nn j 1
,了解并统计这些机床上常用的主轴转
速如下:
车轴类零件: n=400~900
盘形类:
n=150~300
机修:
n=80~150
车大导程螺距: n=10~40
个别:
nmax=1500 nmin=7
njmax=1273 分析国内外同类 D=400
确定: nmax=1500
nmin=10
第七章机床主要技术参数

10
E1
③为了便于采用双速或三速电动机,公比为2的某次方根
E2
2
机械工程学院 School of Mechanical Engineering
第七章 机床主要技术参数的确定
标准公比
①公比是2的某次方根,其数列每隔若干项增加或缩小2 倍,如 3 2 数列为10、12.5、16、20、25、32、40等, 每隔两级增大2倍。
机械工程学院 School of Mechanical Engineering
第七章 机床主要技术参数的确定 (2)运动参数 ①主运动参数 Ⅰ 主运动最高转速nmax和最低转速nmin Ⅱ 转速级数Z Ⅲ 公比φ Ⅳ 变速范围Rn= nmax/ nmin ②进给运动参数:情况同① (3)动力参数:指主运动、进给运动和其他辅助运动的 动力消耗。
ηS 可以用于主传动功率P主和进给传动功率Ps行粗略估算 车床:Ps=(0.03~0.04) P主(KW)
钻床:Ps=(0.04~0.05) P主(KW)
铣床:Ps=(0.04~0.05) P主(KW)
机械工程学院 School of Mechanical Engineering
第七章 机床主要技术参数的确定 7.3.3 快速运动功率的确定
按照等比数列排列的主轴转速,往往可以通过串联若干滑 移齿轮来实现。所以主轴转速n n=n电•iⅠ•iⅡ•••= n电•i总
因此,主轴转速按照等比数列排列时,充分利用了每一对滑移齿 轮的传动比,用同样数量的齿轮,可得到较多的变速级数。
机械工程学院 School of Mechanical Engineering
第七章 机床主要技术参数的确定 4.公比的选用
设主轴最高转速与最低转速之比值,称为转速范围Rn,则: Rn=nmax /nmin = nZ/n1 =n1φ z-1/n1 =φ z-1 即 z=1+lgRn/lgφ (Z为转速级数) 选用标准公比φ的一般原则: ①用于大批大量生产的自动化与半自动化机床,因为要求较高的 生产率,相对转速损失要小,因此φ要小些,一般取1.12或1.26。 ②大型机床加工大尺寸工件,机动时间长,选择合理的切削速度 对提高生产率作用较大,φ应小些,取1.12或1.26。 ③中型通用机床,万能性较大,因而要求转速级数z要多一些, 但结构又不能过于复杂, φ常取1.26或1.41。 ④小型机床切削加工时间常比辅助时间少,结构要求简单一些, 变速级速也不多,公比φ常取1.58或1.78。
机床的主要技术参数(主参数和基本参数)
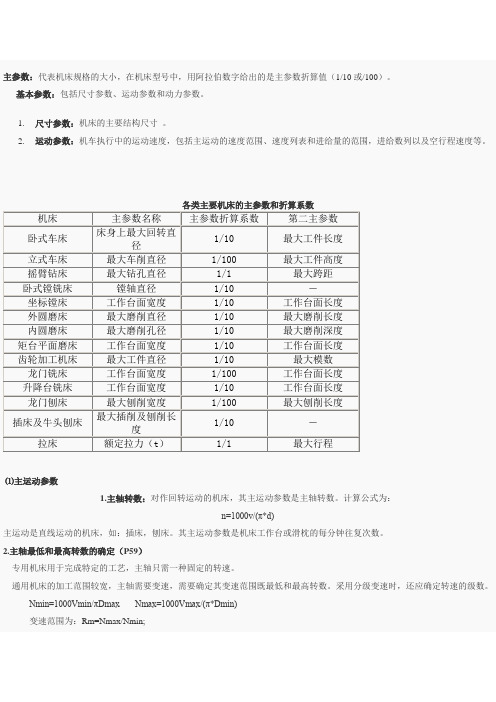
3.有级变速时主轴转速序列
无级变速时,Nmax与Nmin之间的转速是连续变化的
有级变速时,应该在Nmax和Nmin确定后,再进行转速分级,确定各中间级转速。
主运动的有级变速的转速数列一般采用等比数列。
满足n j+1=n jø;n z=n*øz-1
4.标准公比ø
为了便于机床设计和使用,规定了标准公比值:
1.06,1.12,1.26,1.41,1.58,1.78,
2.00
其中,ø=1.06时公比数列的基本公比,其他可以由基本公比派生而来。
⑵进给运动参数
进给量:
a.大部分机床(如车,钻床等):进给量用工件或刀具每转的位移(mm/r)表示;
b.直线往复运动机床(如刨,插床):进给量以每以往复的位移量表示;
c.铣床和磨床:进给量以每分钟的位移量(mm/min)表示。
⑶动力参数
机床的动力参数是指驱动主运动、进给运动和空行程运动的电动机功率。
①主传动功率:
P主=P切+P空+P附
1、切削功率P切:与加工情况.工件和刀具材料及切削用量的大小有关。
P切=Fz*Vc/60000
2、空载功率P空:是指机床不进行切削,及空转时所消耗的功率。
3、附加功率P附:指机床进行切削时,因负载而增加的机械摩擦所耗的功率。
②进给传动功率:通常也采用类比和计算相结合的方法来确定。
③空行程功率:指为节省零件加工的辅助时间和减轻工人劳动强度,在机床移动部件空行程时快速移动所需的传动功率。
其大小由移动部件重量和部件启动时的惯性力决定。
机床主要技术参数

1.机床主要技术参数:(1)尺寸参数:床身上最大回转直径:400mm刀架上的最大回转直径:200mm主轴通孔直径:40mm主轴前锥孔:莫式6号最大加工工件长度:1000mm(2)运动参数:根据工况,确定主轴最高转速有采用YT15硬质合金刀车削碳钢工件获得,主轴最低转速有采用W16Cr4V 高速钢刀车削铸铁件获得。
nmax= = 23.8r/min nmin= =1214r/min根据标准数列数值表,选择机床的最高转速为1180r/min,最低转速为26.5/min公比取1.41,转速级数Z=12。
(3)动力参数:电动机功率4KW 选用Y112M-4型电动机2.确定结构方案:(1)主轴传动系统采用V带、齿轮传动;(2)传动形式采用集中式传动;(3)主轴换向制动采用双向片式摩擦离合器和带式制动器;(4)变速系统采用多联滑移齿轮变速。
3.主传动系统运动设计:(1)拟订结构式:1)确定变速组传动副数目:实现12级主轴转速变化的传动系统可以写成多种传动副组合:A.12=3*4 B. 12=4*3 C。
12=3*2*2D.12=2*3*2 E。
12=2*2*3方案A、B可节省一根传动轴。
但是,其中一个传动组内有四个变速传动副,增大了该轴的轴向尺寸。
这种方案不宜采用。
根据传动副数目分配应“前多后少”的原则,方案C是可取的。
但是,由于主轴换向采用双向离合器结构,致使Ⅰ轴尺寸加大,此方案也不宜采用,而应选用方案D2)确定变速组扩大顺序:12=2*3*2的传动副组合,其传动组的扩大顺序又可以有以下6种形式:A.12=21*32*26 B。
12=21*34*22C.12 =23*31*26 D。
12=26*31*23E.22*34*21 F。
12=26*32*21根据级比指数非陪要“前疏后密”的原则,应选用第一种方案。
然而,对于所设计的机构,将会出现两个问题:①第一变速组采用降速传动(图1a)时,由于摩擦离合器径向结构尺寸限制,使得Ⅰ轴上的齿轮直径不能太小,Ⅱ轴上的齿轮则会成倍增大。
普通车床参数范文

普通车床参数范文普通车床是一种用于金属加工的机床,其参数包括以下几个方面:1.转速范围:普通车床的转速范围通常在几十转/分到几千转/分之间。
转速的选择取决于材料种类、加工方式和工件大小等因素。
一般来说,软材料需要较高转速,硬材料需要较低转速。
2.最大加工直径:普通车床的最大加工直径是指可以加工的最大工件直径。
一般情况下,普通车床的最大加工直径在几十毫米到几百毫米之间,不同型号的车床有不同的加工直径范围。
3.最大加工长度:普通车床的最大加工长度是指可以加工的最长工件长度。
一般情况下,普通车床的最大加工长度在几十毫米到几米之间。
4.主轴孔径:主轴孔径是指普通车床主轴的内径尺寸。
主轴孔径的大小决定了车床可以加工的工件直径。
一般情况下,主轴孔径在几毫米到几十毫米之间。
5.主轴转速:主轴转速是指普通车床主轴的转速。
主轴转速的选择与材料种类、加工方式和工件大小等因素有关。
一般来说,软材料需要较高转速,硬材料需要较低转速。
6.主动力源:普通车床的主动力源通常是电机。
电机的功率大小决定了车床可以承载的工件重量和切削力。
一般情况下,普通车床的电机功率在几十瓦到几千瓦之间。
7.进给方式:普通车床的进给方式有手动进给和自动进给两种。
手动进给需要操作人员手动控制进给速度和方向,适用于简单加工任务;自动进给则由车床控制系统完成进给动作,适用于复杂加工任务。
8.车刀刀架:普通车床的车刀刀架是固定刀具的装置,用于进行切削加工。
车刀刀架通常具有可调节切削角度和进给量的功能,可以实现不同加工需求。
9.床身结构:普通车床的床身结构决定了其刚性和稳定性。
常见的床身结构有平台床身、V床身和箱式床身等。
不同床身结构适用于不同的加工任务和工件大小。
10.控制方式:普通车床的控制方式有手动控制和数控控制两种。
手动控制需要操作人员手动操作车床进行加工,适用于简单任务;数控控制则由计算机控制车床进行加工,适用于复杂加工任务。
总之,普通车床的参数包括转速范围、最大加工直径、最大加工长度、主轴孔径、主轴转速、主动力源、进给方式、车刀刀架、床身结构和控制方式等。
第七章 机床主要参数的确定

第二主参数 车床- 车床-最大工件长度 铣床、龙门刨床- 铣床、龙门刨床-工作台面 其他 车床-刀架工件回转直径, 车床-刀架工件回转直径,主轴孔 龙门铣床-横梁最高、 龙门铣床-横梁最高、最低位置
第二节 运动参数
重点掌握以下几个问题: 重点掌握以下几个问题: 哪些参数属于运动参数? 1、哪些参数属于运动参数? 什么是主运动参数、进给运动参数? 2、什么是主运动参数、进给运动参数? 如何确定机床的最高、最低转速? 3、如何确定机床的最高、最低转速? 分级变速采用什么数列? 4、分级变速采用什么数列? 如何选择公比? 5、如何选择公比?
一、主运动电动机功率的确定 机床主运动的功率包括:切削功率P 空转功率P 机床主运动的功率包括:切削功率P切、空转功率P空和附加机械 摩檫损失P 三部分。 摩檫损失P机三部分。 与刀具及工件材料有关, P切与刀具及工件材料有关,普通机床一般根据重负荷切削条 件确定。 件确定。 (KW)随各轴转速变化 摩檫搅油、空气阻力等造成。 随各轴转速变化、 P空(KW)随各轴转速变化、摩檫搅油、空气阻力等造成。中型 机床用试验公式估算:(教材P124) :(教材 机床用试验公式估算:(教材P124) 附加机械磨擦损失功率)取决于各传动副的机械效率, P机(附加机械磨擦损失功率)取决于各传动副的机械效率, 既齿轮、轴承等切削时压力增大而产生, 增加P 也增加。 既齿轮、轴承等切削时压力增大而产生, P切增加P机也增加。 主电机功率(KW) 主电机功率(KW) : P主= P切+ P机+ P空= P切/η机+ P空 η机= η1+ η2+ η3…… η1、η2、η3见教材 见教材P124表7-2 表 P125图各项功率关系 P125图各项功率关系 在主传动链的结构尚未确定之前,可根据P max和总功率 和总功率η 在主传动链的结构尚未确定之前,可根据P切max和总功率η总 =0.65~0.80确定 确定. =0.65~0.80确定. η总低速时取大值
机床主要技术参数

机床主要技术参数1.机床主要技术参数:(1)尺寸参数:床身上最大回转直径:400mm刀架上的最大回转直径:200mm主轴通孔直径:40mm主轴前锥孔:莫式6号最大加工工件长度:1000mm(2)运动参数:根据工况,确定主轴最高转速有采用YT15硬质合金刀车削碳钢工件获得,主轴最低转速有采用W16Cr4V 高速钢刀车削铸铁件获得。
nmax= = 23.8r/min nmin= =1214r/min根据标准数列数值表,选择机床的最高转速为1180r/min,最低转速为26.5/min公比取1.41,转速级数Z=12。
(3)动力参数:电动机功率4KW 选用Y112M-4型电动机2.确定结构方案:(1)主轴传动系统采用V带、齿轮传动;(2)传动形式采用集中式传动;(3)主轴换向制动采用双向片式摩擦离合器和带式制动器;(4)变速系统采用多联滑移齿轮变速。
3.主传动系统运动设计:(1)拟订结构式:1)确定变速组传动副数目:实现12级主轴转速变化的传动系统可以写成多种传动副组合:A.12=3*4 B. 12=4*3 C。
12=3*2*2D.12=2*3*2 E。
12=2*2*3方案A、B可节省一根传动轴。
但是,其中一个传动组内有四个变速传动副,增大了该轴的轴向尺寸。
这种方案不宜采用。
根据传动副数目分配应“前多后少”的原则,方案C是可取的。
但是,由于主轴换向采用双向离合器结构,致使Ⅰ轴尺寸加大,此方案也不宜采用,而应选用方案D2)确定变速组扩大顺序:12=2*3*2的传动副组合,其传动组的扩大顺序又可以有以下6种形式:A.12=21*32*26 B。
12=21*34*22C.12 =23*31*26 D。
12=26*31*23E.22*34*21 F。
12=26*32*21根据级比指数非陪要“前疏后密”的原则,应选用第一种方案。
然而,对于所设计的机构,将会出现两个问题:①第一变速组采用降速传动(图1a)时,由于摩擦离合器径向结构尺寸限制,使得Ⅰ轴上的齿轮直径不能太小,Ⅱ轴上的齿轮则会成倍增大。
数控机床加工常用的切削参数选择技巧

数控机床加工常用的切削参数选择技巧数控机床是现代制造业中不可或缺的重要设备,它可以高效地加工各种材料,为工业生产提供了巨大的便利。
而在数控机床的加工中,切削参数的选择对于加工质量和效率起着至关重要的作用。
本文将介绍数控机床加工中常用的切削参数选择技巧,帮助读者在实际工作中正确选择合适的切削参数。
首先,切削速度是数控机床加工中最基本的切削参数之一。
切削速度是指工件与刀具相对运动的速度,它直接影响到切削力和加工表面的质量。
在选择切削速度时,需要考虑材料的硬度、切削工具的材料和涂层等因素。
一般而言,硬度较高的材料需要选择较低的切削速度,否则容易造成刀具磨损过快或加工表面粗糙。
其次,进给速度也是切削参数中的重要指标。
进给速度是指在单位时间内工件的移动距离。
合理选择进给速度可以提高加工效率,同时还能减小切削力,延长刀具寿命。
在选择进给速度时,需要考虑切削类型、加工精度要求以及刀具的刃口数等因素。
一般而言,对于粗加工可以选择较大的进给速度,而对于精加工则要选择较小的进给速度,以保证加工表面的质量。
另外,切削深度也是数控机床加工中重要的切削参数之一。
切削深度是指每次切削时刀具与工件之间的距离。
合理选择切削深度可以保证加工表面质量,同时还能控制切削力和刀具寿命。
在选择切削深度时,需要综合考虑材料的硬度、刀具的强度和刚性以及加工要求等因素。
一般而言,切削深度不宜过大,以免造成切削力过大和加工表面粗糙。
除了上述三个常用的切削参数,还有一些其他的切削参数也需要注意。
首先是刀具的几何形状和尺寸,它们与加工表面的精度和质量密切相关。
选择合适的刀具几何形状和尺寸,可以提高加工精度和效率。
其次是刀具的涂层和材料,正确选择刀具的涂层和材料可以延长刀具的使用寿命和降低切削力。
此外,还需要注意切削润滑和冷却条件,保证切削过程的稳定性和切屑的排出。
在实际工作中,我们应该根据具体的加工要求和机床的性能特点来选择合适的切削参数。
同时,也需要不断进行试切和实践,不断总结和改进切削参数的选择,以提高加工效率和加工质量。
多功能精密车床参数

多功能精密车床参数
1. 最大加工直径,这个参数表示车床能够加工的工件的最大直径,通常以毫米或英寸为单位。
2. 最大加工长度,这个参数表示车床能够加工的工件的最大长度,同样通常以毫米或英寸为单位。
3. 主轴转速范围,这个参数表示车床主轴的转速范围,通常以
转/分钟(rpm)为单位。
主轴转速的范围决定了车床可以加工的材
料种类和加工精度。
4. 主轴功率,这个参数表示车床主轴的功率,通常以千瓦(kW)或马力(hp)为单位。
主轴功率的大小直接影响车床的加工能力。
5. X/Y/Z轴行程,这些参数分别表示车床在X、Y、Z方向上的
行程范围,通常以毫米或英寸为单位。
行程范围的大小决定了车床
能够加工的工件尺寸范围。
6. 刀架数量,多功能精密车床通常配备多个刀架,不同的刀架
可以完成不同的加工任务,因此了解车床的刀架数量和类型是非常
重要的。
7. 控制系统,多功能精密车床通常配备数控系统,不同的数控系统具有不同的功能和性能特点,因此选择适合自己加工需求的数控系统也是非常重要的。
以上是一些常见的多功能精密车床参数,对这些参数的了解可以帮助我们选择适合自己加工需求的车床,提高生产效率和加工质量。
写出机床主轴的五个主要结构参数

写出机床主轴的五个主要结构参数机床主轴有着至关重要的地位,它直接影响到机床的精度和性能。
机床的主轴结构主要有五个参数:称重,直径,主轴承,速度和加工方式。
所以掌握机床主轴的五个结构参数是机床的基本知识。
首先是称重,它是机床轴系的最重要参数,表征机床轴系的负荷能力。
机床的称重可以通过检测机床轴系对夹紧装置的受力判断,并用仪器来精确测量。
称重是由机床轴系的直径和质量以及主轴承的质量决定的,因此,机床轴系的称重一般以千斤为单位,在确定机床轴系称重时,要考虑到质量以及主轴承的质量。
其次是直径,它决定机床主轴的转动惯量和负荷能力,对于对精密加工特别是高精度切削的机床,一般要求主轴的直径越大越好,在一般的机床中,直径一般在50-100毫米之间。
紧接着是主轴承,一般情况下机床轴系使用两种主轴承:滚珠主轴承和滑动主轴承。
滚珠主轴承具有较小的摩擦系数,高精度,高速度,但它的结构较复杂,对维护油脂的供应有较高的要求;滑动主轴承的结构更简单,但它的精度不及滚珠主轴承,而且摩擦系数也较大,所以一般不用于高精度的机床轴系。
接下来是速度,它是决定机床轴系运行效率的重要参数,一般情况下,机床轴系的最高转速一般不超过3000转/分钟,这是由机床轴系的加工方式以及主轴承精度决定的。
最后是加工方式,它决定了机床轴系可以采用什么样的加工方式。
这主要是由机床轴系的外形和尺寸决定,一般来说,机床轴系可以采用滚切、钻孔、攻丝、磨削等加工方式。
综上所述,机床主轴的结构主要有五个参数:称重,直径,主轴承,速度和加工方式。
其中,称重决定机床轴系的负荷能力,直径决定机床轴系的转动惯量和负荷能力,主轴承决定机床轴系的精度和摩擦系数,速度决定机床轴系的运行效率,加工方式决定机床轴系的外形和尺寸。
所以,掌握机床主轴的五个参数是机械加工的基本知识,也是机床维修与维护的基本要素。
更进一步地,在选择机床时,除了要考虑机床主轴的五个结构参数外,还要考虑机床的整体结构、主要零部件的可靠性、抗电源干扰能力等技术参数,这些参数也是机床的核心技术指标,也是我们买机床的必然要求。
- 1、下载文档前请自行甄别文档内容的完整性,平台不提供额外的编辑、内容补充、找答案等附加服务。
- 2、"仅部分预览"的文档,不可在线预览部分如存在完整性等问题,可反馈申请退款(可完整预览的文档不适用该条件!)。
- 3、如文档侵犯您的权益,请联系客服反馈,我们会尽快为您处理(人工客服工作时间:9:00-18:30)。
导轨上的作用力
三、空行程功率的确定 空行程功率的确定应参考同类型机床,辅之以计
算,最好再经试验验证。快速(空)行程电动机往 往是满载起动,移动件较重,加速度也较大,因此 计算时必须考虑惯性力。各运动件在电机轴上的当 量转动惯量(kg·m2),可根据动能守恒定理,由式 决定:
式中:Jk ―旋转件的转动惯量(kg·m2) ω k ―各旋转件的角速度(rad/s); mi ―直线运动件的质量(kg); vi ―直线运动件的速度(m/s); ω ― 电动机的角速度(rad/s)。
Next
一、主运动功率的确定
机床主运动的功率,包括切削功率、空转功率损 失和附加机械摩擦损失三部分。进行切削加工时,要 消耗切削功率P切。它与刀具材料、工件材料和所选用 的切削用量的大小有关。如果是专用机床,则工作条 件比较固定,也就是刀具与工件的材料和切削用量的 变化范围较小。这时计算值也比较接近实际情况。若 是普通机床,则刀具与工件的材料和切削用量的变化 都相当大。通常,可根据机床检验时所要求的重负荷 切削条件来确定。
最大的相对转速损失率是当所需的转速 n 趋近于 nj + l时,也就是:
在其他条件(直径、进给、切深)不变的情况下, 转速的损失就反映了生产率的损失。对于普通机床, 如果认为每个转速的使用机会都相等,那么应使 Amax 为一定值,即:
从这里可看出,任意两级转速之间的关系应为: n j十1 =njφ
da― 主运动链中除主轴外所有传动轴轴颈的平均直径。如果
主运动链的结构尺寸尚未确定,初步按电动机功率P选取:
d 主 ― 主轴前后轴颈的平均值(mm); Σ ni ― 当主轴转速为n主时,传动链内除主轴外各传动轴的转
速之和。如传动链内有不传递载荷但也随之作空运转 的轴时,这些轴的转速也应计入(r/min) ; n主 — 主轴转速(r/min) ; kl ― 润滑油粘度影响的修正系数。 N46 号机械油,kl= 1; N32号机械油,kl= 0.9;N15 号机械油,kl= 0.75 ; k2― 系数。主轴用两支承的滚动轴承或滑动轴承,k2=8.5 ; 三支承滚动轴承,k2=10
图 7-1 表示主运动链在某一转速下所消耗的各 项功率之间的关系。当开动机床尚未切削时,就需
要消耗部分功率P空(图 7-1的OB )。随着P切的增
加,P机也在增加。P主沿AB上升,直到A点。这时
机床满载,
p主max
p空
p切max
p机max
p切max
总
在图 7-1 中就是 OA 联线与水平轴夹角 α 的余
在其他条件(切速、切深等)不变的情况下,进给量的损 失也反映了生产率的损失。数控机床和重型机床的进给为无级 调整;普通机床多采用分级调整。如进给链为外联系传动链, 为使相对损失为一定值,则进给量的数列也应取等比数列。有 的往复主运动机床,例如刨床和插床,进给运动是间歇的,为 使进给机构简单,采用了棘轮机构,进给量由每次往复转过的 齿数而定,则是等差数列。供大量生产用的自动和半自动车床, 常用交换齿轮来调整进给量。这时可以不按一定的规则,而用 交换齿轮选择最有利的进给量。卧式车床因为要车螺纹,进给 箱的分级应根据螺纹标准而定。螺纹标准不是一个等比数列, 而是一个分段的等差数列。
机床的转速应该按等比数列(几何级数) 分级。其公比为φ,各级转速应为
最大相对转速损失率为: 变速范围为:
例:有一台车床,主轴转速(r/min)共12级,分别 为:31.5、45、63、90、125、180、250、355、500、 710、1000、1400,公比为φ=1.41,则最大相对转速损 失率:
切,η总=ctgα。当P切从 0上升到P切max时,P主是沿 OBA折线上升的。因此,η总仅对满载时有效。当P切 <P切max时,根据η总总算出的电动机功率将小于实 际值。
二、进给运动功率的确定
在进给运动与主运动共用一个电动机的普通机 床上,如卧式车床和钻床,由于进给运动所消耗的 功率与主运动相比是很小的,因此可以忽略进给所 需的功率。在进给运动与空行程运动共用一个电动 机的机床上,如升降台铣床,也不必单独考虑进给 所需的功率,因为使升降台快速上升所需的空行程 运动功率比进给运动的功率大得多。
进给运动采用单独的普通电动机的机床,如升 降台铣床和龙门铣床,以及用液压缸驱动进给的机 床,如仿形车床、多刀半自动车床和组合机床等, 都需要确定进给运动所需的功率。通常用参考同类 型机床和计算相结合的办法确定。注意比较传动链 的长短和低效率传动副(丝杠螺母、蜗杆蜗轮)的 数量。进给传动链的机械效率,ηs会低至 0.15-0.2。
三、标准公比和标准数列 机床转速是从小到大递增的,因此φ > 1 。
为使最大相对转速损失率不超过 50 % ,即
,则,φ ≤2 。因此1 <Ф ≤2 为方便起见,规定了公比的标准值: 1.06 ,1.12 ,1.26 ,1.41 ,1.58 , 2。 当采用标准公比后,转速数列可从表 7-1 中直 接查出。表中给出了以 1.06 为公比的从 1-10000 的数值。 1.12 = 1.062, 1.26 = 1.064,
实心圆柱形件的转动惯量:
空心圆柱形件的转动惯量:
式中 m―质量(kg) ; ρ―密度(kg/m3,钢的ρ= 7.8x103 kg/m3) D、d 和l― 分别为外径、孔径和厚度(m) 克服惯性的转矩为:
式中 ta ― 电动机起动加速过程的时间(s), 数控机床可取ta为伺服电动机机械时间常数的 3-4 倍;中、小型普通机床可取 ta=0.5s ;大型普通机 床可取ta=1s
1.41 = 1.066, 1.58 = 1.068, 2 = 1.0612 。
此表不仅可用于转速、双行程数和进给量数列,
而且也可用于机床尺寸和功率参数等数列。表中的数 列应优先选用。
四、公比的选用
当确定了最高与最低转速以后,就应选取公比Ф。从使 用性能方面考虑,公比最好选得小一些,以便减少相对转速 损失。但公比越小,级数就越多,将使机床的结构复杂。对 于一般生产率要求较高的普通机床,减少相对转速损失是主 要的,所以公比取得较小,如Ф=1.26 或Ф=1.41等。有些小 型机床希望简化构造,公比Ф可取得大些,如Ф=1.58或Ф=2 等。对于自动机床,减少相对转速损失率的要求更高,常取 Ф=1.12 或Ф=1.26。由于自动机床都是用于成批或大量生产, 变速时间分摊到每一工件,与加工时间相比是很小的,因此 采用交换齿轮变速,既满足了相对转速损失小的要求又简化 了构造。
是工作台工作面宽度; 卧式铣镗床是主轴直径; 立式钻床和摇臂钻床是最大钻孔直径; 牛头刨床和插床是最大刨削和插削长度
也有的机床不用尺寸作为主参数,如拉床的主参 数是额定拉力等。
有的机床,一个主参数还不足以确定机床的规格, 还需第二主参数加以补充:
车床的第二主参数是最大工件长度; 铣床和龙门刨床是工作台工作面长度; 摇臂钻床是最大跨距等。
在确定了 nmax和 nmin后,如采用分级变速 (大多数普通机床),则应进行转速分级;如采 用变速电动机进行无级变速(大多数数控和重型 机床),有时也需用分级变速机构来扩大其调速 范围。
2.分级变速时的主轴转速数列:
如某机床的分级变速机构共有 Z 级,其中 n1 = nmin, nz=nmax , Z 级转速分别为: nl , n2 , n3,…, nj , nj
+ l ,…, nz 如果加工某一工件所需要的最有利的切削速度
为 v ,则相应的转速为n。通常,分级变速机构不能
恰好得到这个转速,而是 n 处于某两级转速 nj , nj + l 之间: nj < n < nj+l如果采用较高的转速nj+l,必将提 高切削速度,刀具的耐用度将要降低。为了不降低
刀具耐用度,以采用较低的转速 nj 为宜。这时转速 的损失为 n-nj ,相对转速损失率为:
1.最低(nmin)和最高(nmax)转速的确定: nmin和nmax的比值是变速范围:
在确定切削速度时应考虑到多种工艺的需要。 切削速度主要与刀具和工件的材料有关。常用的刀 具材料有高速钢、硬质合金和陶瓷等。工件材料可 以是钢、铸铁以及铜铝等有色金属。切削速度可通 过切削试验、查切削用量手册和通过调查得到。
第二节 运动参数
一、主运动参数 回转主运动的机床,主运动参数是主轴转速。
转速(r/min)与切削速度的关系是:
n 1000v
d
式中: n ―转速( r/min ); v― 切削速度( m/min ); d― 工件(或刀具)直径(mm)。
主运动是直线运动的机床,如插床或刨床,主 运动参数是每分钟的往复次数。对于不同的机床, 主运动参数有不同的要求。专用机床和组合机床是 为某一特定工序而设计制造的,每根主轴一般只须 有一个转速,根据最有利的切削速度和直径而定, 故没有变速要求。通用机床是为适应多种零件加工 而设计制造的,主轴需要变速。因此需确定它的变 速范围,即最低与最高转速。如果采用分级变速, 则还应确定转速级数。
此外,还要确定其他一些尺寸参数: 车床常常还要确定在刀架上工件的最大回转直径和 主轴孔允许通过的最大棒料直径等; 龙门铣床还应确定横梁的最高和最低位置等; 摇臂钻床还要确定主轴下端面到底座间的最大和最
小距离,其中包括了摇臂的升降距离和主轴的最大伸 出量等。
当主参数、第二主参数和其他一些尺寸参数确定
后,就基本上确定了该机床所能加工或安装的最大工 件的尺寸。机床的尺寸参数是根据零件尺寸确定的。
第三节 动力参数
动力参数包括电动机的功率,液压缸的牵引 力,液压马达、伺服电动机或步进电动机的额定 转矩等。各传动件的参数(轴或丝杠的直径、齿 轮与蜗轮的模数等)都是根据动力参数设计计算 的。如果动力参数定得过大,将使机床过于笨重, 浪费材料和电力;如果定得过小,又将影响机床 的性能。动力参数可以通过调查、试验和计算的 方法进行确定。