辊弯和辊形
弯辊与窜辊

WRS(Work Rool Shifting)工作辊窜辊一、综述所谓工作辊窜辊就是工作辊就是工作辊沿轴线方向上的水平移动,工作辊的窜辊是均匀工作辊磨损的优选措施,同时对提高弯辊的功效,降低工作辊的过度挠曲及减小有害接触区有一定的作用。
工作辊的窜辊有四个液压缸进行控制,分别分布在上下工作辊操作侧的入口侧和出口侧,每个液压缸上都有一个位置传感器,通过传感器检测工作辊的窜动位置,在窜动过程中必须保持上下工作辊偏离中心线的位置同步、上工作辊入口侧和出口侧两个液压缸的位置同步、下工作辊入口侧和出口侧两个液压缸的位置同步,这些都通过传感器检测的数值反馈到程序内部进行计算并把计算的结果输出到对应的伺服阀来进行调节。
工作辊的窜辊分为正窜和负窜:所谓正窜就是指上工作辊向驱动侧移动,下工作辊向操作侧移动,使辊的弯曲度增加(positive),能有效减少边部波浪;所谓负窜是指上工作辊向操作侧移动,下工作辊向驱动侧移动,使辊的弯曲度减小(negtive),使边部波浪产生的可能性增加。
窜辊是在静态状态下进行的,在1+4热连轧项目中应用在精轧部分,在自动模式下窜动的位置由二级(过程自动化)给定,手动模式下操作员可以根据经验值进行设定值的调整,窜辊在板带材进入机架前已经提前摆好位置并锁定,在轧制过程中是不允许进行窜动的,窜动的目的主要是减小轧辊的磨损,但对板带材的平整度控制也有一定的影响,另外在换辊时窜动一定的位置可以方便上工作辊落在下工作辊的支撑位置方便工作辊的抽出。
A x ial_shif t.dsf二、功能概述窜辊包括三个功能单元1、位置控制:控制的计算、模式选择、监视2、设定点的选择:模式选择、轴向位置的设定点、窜动速度3、辅助功能:伺服阀的监视、压下位置的补偿、预设的实际值计算的结果用来控制伺服阀的输出,伺服阀的输出不能超过极限值,限定值与压力和电流有关,监视功能包括窜动速度、位置、阀的输出,模式选择包括轧制模式和换辊模式自动模式下,在带材进入机架前二级会把设定值通过SDH 发给一级的WRS 功能单元进行控制,控制的速度和轧制力以及机架的速度有关,伺服阀的运动范围+100—-100,检修模式下可以沿轴向位置移动不会被锁定,但移动速度只有1mm/s,位置设定(自动,手动介入,换辊模式的固定位置) 0,8 1.0 5.014.0F Roll [MN]Without Strip With Strip1/20001/30001/4000v WRS / v Rollv WRS v Roll F Roll : Shifting Speed: Rolling Speed: Roll ForceWork_Roll_Shifting_Speed_01.vsd 辅助功能:辊缝开口度的补偿调校,弯辊必须是打开的状态(机架和换完辊后的零位校准)三、 软件结构(CFC )FolderDescription F_STAND00xProject name COFinishing mill CO mmon charts, blocks for the sysfunctions of all sub-rack CPU's FP_Nx Plant area F inishing mill P rocess, stand x (x=1..4)P01 STM(Logic part)逻辑部分P03 TEC(Technological part)工艺控制部分P03 GCS(Controller part)控制部分CPU CPUfolder FunctionfolderFunction charts CountnumberP01 100_STM330_WRS P01_STM_WRS_INP Input Interface输入接口441P01_STM_WRS_HMI HMI Interface HMI接口442P01_STM_WRS_LOG Logic 逻辑功能443P01_STM_WRS_REF Reference 参考值444P01_STM_WRS_MAM Maintenance Mode 检修模式445P01_STM_WRS_MSG Messages 信息446P01_STM_WRS_OUT Output interface 输出接口447P03 200_TEC350_WRS P03_GCS_WRS_TEC Technological part工艺控制部分330P03 300_GCS350_WRS P03_GCS_WRS_PAR Control parameter 控制参数400P03_GCS_WRS_ACT Actual values 实际值330P03_GCS_WRS_TOP Top Controller 上辊控制340P03_GCS_WRS_BOT Bottom Controller 下辊控制350 P01_STM_WRS_INP机架信息、窜动控制系统、压下控制系统、P01_STM_WRS_HMIP01_STM_WRS_LOGOperation logic 操作逻辑LOO name WRS Work Roll Shifting Status 状态WRS_A_00 WRS Top Control On/Off 上辊控制开/关WRS_A_01 WRS Bottom Control On/Off下辊控制开/关WRS_A_02 WRS Manual Mode 手动模式WRS_A_03 WRS Automatic Mode 自动模式WRS_A_04 WRS To Center Position 中间位置WRS_A_05WRS_B_00 WRS Manual Intervention Status手动干预状态WRS_B_01 WRS Position Manual Increase 手动加WRS_B_02 WRS Position Manual Decrease 手动减WRS Valve Status 阀状态WRS_C_00 WRS Check valve Top Entry WRS_C_02 WRS Check valve Top Exit WRS_C_03 WRS Check valve Bottom Entry WRS_C_04 WRS Check valve Bottom Exit WRS_C_05 HMI中控制模式的选择WRS(Work Rool bending)工作辊弯辊一、综述对于工作辊的弯辊主要的目的是为了保证带材的平整度,自动状态下弯辊力的大小会由二级提前根据板坯的参数计算出来下发到一级执行,一级在执行过程中会根据现场收集的适时数据不断进行调整以保证达到最精确的控制,同时操作员也可以根据经验进行手动干预,正常情况下不建议进行人工干预,除非异常情况下必须进行有效的干预才能保证设备的安全运行时操作员才可以采取正确的干预方式。
轧钢工-简答题246

1.轧钢机有哪些安全装置?答案:安全臼、梅花轴套、联轴节、过电流继电器和热继电器。
2.产生打滑的原因?答案:产生打滑的原因是钢坯由于加热温度高时间长氧化铁皮严重,并不易脱落,或者压下量过大。
遇到这种情况,可降低轧辊转速,并启动工作辊道给轧件以推力,使之顺利通过轧槽。
3.活套支持器有什么作用?答案:活套支持器设置在精轧机组各机座之间,它用来张紧精轧机座间出现的带钢活套,使连轧机相邻机座间的带钢在一定张力状态下贮存一定的活套量,作为机架间速度不协调时的缓冲环节。
4.为什么精轧机组采用升速轧制?答案:为了安全生产防止事故,精轧机组穿带速度不能太高,并且在带钢轧出最终机架之后,进入卷取机之前,带钢运送速度也不能太高,以免带钢在辊道上产生飘浮。
因此,采取低速穿带然后与卷取机同步升速进行高速轧制的办法,可使轧制速度大幅度提高。
采用升速轧制,可使带钢终轧温度控制得更加精确和使轧制速度大为提高,减少了带钢头尾温度差,从而为轧制更薄的带钢(0.8毫米)创造了条件。
5.加热的目的是什么?答案:①提高钢的塑性;②使坯料内外温度均匀;③改变金属的结晶组织:坯料的不均匀组织结构及非金属夹杂物形态与不均匀分布,在高温加热中扩散而改善了结晶组织。
对于高速钢,长时保温可消除或减轻碳化物的偏析。
坯料加热的质量直接影响到板带钢的质量、产量、能耗及轧机寿命。
6.板带轧机压下装置的特点是什么?答案:(1)轧辊调整量小。
(2)调整精度高。
(3)经常的工作制度是“频繁的带钢压下”。
(4)必须动作快,灵敏度高。
(5)轧辊平行度的调整要求严格。
7.影响轧辊辊缝形状的因素有哪些?答案:(1)轧辊的弹性弯曲变形。
(2)轧辊的热膨胀。
(3)轧辊的磨损。
(4)轧辊的弹性压扁。
(5)轧辊的原始辊型。
8.轧辊调整装置的作用有哪些?答案:轧辊调整装置的作用有:(1)调整轧辊水平位置(调整辊缝),以保证轧件按给定的压下量轧出所要求的断面尺寸。
(2)调整轧辊与辊道水平面间的相互位置,在连轧机还要调整各机座间轧辊的相互位置,以保证轧线高度一致(调整下辊高度)。
第三章 弯 曲 (2)

ρ = r + xt
r:弯曲件内弯曲半径 t:材料厚度 x:中性层位移系数,查表。 弯曲件展开尺寸计算:
r/t < 0.5时,因为圆角区域发生了严重变薄,其相邻的直边也变薄,因 此需要采用经验公式计算。 对于复杂形状的弯曲件,在初步计算后,还需要反复试弯,不断修 正才能确定坯料尺寸。
3 回弹值的确定: 为了得到形状与尺寸精确的弯曲件,需要实现确定回弹值, 因为影响因素很多,理论计算方法往往不精确,而且很复杂,因此 一般是根据经验数值以及简单的计算来初步确定模具工作部分尺寸, 然后在试模时校正。
图3-21
产生偏移的原因: 1 弯曲坯料形状不对称; 2 弯曲件两边折弯个数 不相等; 3 弯曲凸凹模结构不对 称。
图3-22
控制偏移措施: 1 采用压料装置。
图3-23
2 利用工艺孔限制坯料移动。 3 对偏移量进行补偿。
4 对不对称零件,先成对弯曲,再切断。 5 尽量采用对称凸凹模结构
图3-24
0 .7 K B t σ b F自 = r+t
2
U型件:
]型件:
F = 2.4 Btσ b ac 自
上式中: F自:自由弯曲在冲压行程结束时的弯曲力; B:弯曲件的宽度; r:弯曲件的内弯曲半径; t:弯曲件材料厚度; σb:材料抗拉强度; K:安全系数,一般取1.3 a、c:系数; 校正弯曲时的弯曲力: 校正弯曲时的弯曲力一般按照下式计算:
2 应力状态 长度方向:弯曲内区受压,外区受拉,切向应力是绝对值最大的主应 力; 厚度方向:在变形区内存在径向压应力,在板料表面为0,由表及里 逐渐增加,到达中性层时达到最大值; 宽度方向:对于窄板,由于可以自由变形,因此内外区都为0,对于 宽板,内区为压应力,外区为拉应力
轧辊凸度计算范文

轧辊凸度计算范文
轧辊凸度计算是一个在轧制过程中非常重要的参数,它直接影响到轧
制产品的质量和工艺参数的选择。
凸度是指轧辊外表面上存在的非规则形状,它是沿轧辊辊向方向规律变化的。
在轧辊凸度计算中需要考虑的因素
包括轧辊弹性变形、轧制力、轧制过程中润滑条件等。
轧辊凸度的测量可以使用多种方法,包括以X射线或激光测量凸度的
非接触方法,以及使用厚度计或轧制力传感器等传统方法。
其中,非接触
方法不会对轧辊表面造成损害,适用于高质量表面轧辊的凸度测量;而传
统方法则较为简单,易于实施。
需要注意的是,在进行凸度测量时需要对
轧辊进行冷却,以免温度影响凸度测量结果。
凸度计算是根据测量到的轧辊凸度数据进行的。
根据轧制过程的特点,凸度可分为弯曲凸度和辊形凸度。
其中,弯曲凸度是由于轧辊弯曲而产生的,它主要取决于轧辊弹性变形和轧制力;辊形凸度是由于轧辊外表面上
存在的非规则形状而产生的,它主要取决于轧辊的制造工艺、磨削状况以
及使用寿命等。
凸度计算可以采用经验公式和数值模拟方法。
常用的经验公式包括微
积分法、有限元法和正弦公式等。
其中,微积分法适用于凸度分布较为规
律的情况;有限元法适用于凸度分布较为复杂的情况;正弦公式适用于较
为简单的凸度计算。
数值模拟方法则利用计算机模拟轧制过程,通过有限
元分析等方法计算轧辊的凸度分布。
在凸度计算时,还需要考虑轧辊的磨损和修复对凸度的影响。
轧辊的
磨损会导致轧辊凸度的变化,需要在计算中进行补偿。
轧辊的修复也会对
轧辊凸度产生影响,需要进行相应的调整。
1-加热辊弯成型技术

加热辊弯成型技术高光祖(武汉钢铁设计研究院信息室 430080) 摘 要 介绍了加热辊弯成型工艺的特点,着重就具有加热室的辊弯成型机和热轧—热弯成型机作了分析。
还就因外加热辊弯成型技术的发展作了评述。
主题词 型材 辊弯成型 加热 工艺 现状 冷弯成型的产品由于加工硬化,断面各部分机械性能不均匀,因此容易出现裂纹。
在采用低塑性高强度材质时,这一状况更加突出。
另外,对于断面厚度不同,局部带有尖角的型钢品种,用冷弯成型工艺是难以生产的。
以航天航空器材为例,这类结构首要问题是重量。
钛合金具有极佳的强/重比,良好的韧性、耐蚀和耐疲劳性能,因此大量使用于飞机制造,以减轻重量。
但钛材冷弯成型性能不好,应在650~800℃热弯成型。
另外,任何材料在成型弯曲半径极小时重量最轻。
飞机构架型材各弯曲部位都要求达到最小曲率半径。
因而需采用加热辊弯成型工艺才容易达到加工要求。
图1表示帽型钛质型材通过减小曲率半径减轻重量的情况。
曲率半径从冷弯典型最小值,即板厚的5倍减到热弯最小值即板厚的1.5倍,可减轻11%的重量。
1 加热辊弯成型工艺及特点加热加辊弯成型工艺是国外60年代末图1 0.050in厚帽型型材加大弯曲度可大量减轻重量,但型材高度和铺放面宽度要保持不变。
・22・焊管・第23卷第2期・2000年3月开发的技术。
可分两类:一类是配置加热室预热带材及成型辊对带钢高温成型的工艺;另一类是热轧—热弯组合成型工艺。
1.1 具有加热室的辊弯成型机采用冷带材为原料,由加热室对带材辐射加热,同时加热成型辊至800℃。
通过电偶温度传感器控制设定温度,可按要求的型材加工温度和成型速度进行调节。
10机架成型机由60HP 可变速传动装置经万向接轴传动,成型速度5~40ft /min (1.5~12m /min )。
每个成型辊的轴孔都开有切槽如图2所示,切槽内充填绝热材料,以减少传递到辊轴图2 成型辊和成型辊隔套的轴孔均有切槽以绝热且辊轴通水冷却的热量,提高成型温度的均匀性。
辊弯成型工艺研究

辊弯成型工艺研究辊弯成型工艺研究是金属材料加工中,一种常见的成形工艺。
它利用辊弯机将金属材料进行弯曲,从而得到所需要的外形尺寸、曲率半径及几何精度的带弯部件。
辊弯成型工艺是一种比较古老的工艺,早在20世纪50年代就开始使用。
在辊弯成型工艺中,金属材料通过两个相对运动的辊子,实现弯曲加工。
根据不同的材料及加工要求,可选择不同类型的辊弯机,如气动式辊弯机、液压式辊弯机、数控辊弯机等。
辊弯机可分为卧式及立式两种,其中立式辊弯机又可分为3轴辊弯机、4轴辊弯机及5轴辊弯机。
辊弯成型工艺具有加工精度高、效率高、成本低等优点,在航空航天、汽车、冶金、电子、机械等行业被广泛应用。
但是,辊弯成型工艺也存在一些缺点,如加工尺寸受到加工参数的限制,加工厚度范围狭窄,加工能力受到材料性能限制等。
因此,在辊弯成型工艺研究中,需要考虑许多因素,如设计理念、选择辊弯机型号、选择加工参数、选择工具材料等。
首先,要确定好设计理念,以便正确的选择辊弯机型号及加工参数。
其次,应仔细研究辊弯机的结构特点,确定合适的机型,以保证加工效率及加工精度。
在选择加工参数方面,要根据材料的性能及加工精度,选择合理的加工参数,以保证加工效果。
另外,在选择工具材料方面,也要考虑到工具使用寿命、曲率半径及弯曲精度等因素。
总之,辊弯成型工艺研究是一项比较复杂的工作,需要考虑许多因素,以保证加工效果及成型精度。
此外,要根据实际情况,不断优化辊弯成型工艺,以提高加工效率及精度,满足不断发展的加工要求。
Roll bending forming technology research is a common forming process in metal material processing. It uses roll bending machine to bend the metal material, so as to obtain the bent parts with required shape size, curvature radius and geometric precision. Roll bending forming technology is a relatively old technology, which has been used since the 1950s.In roll bending forming process, the metal material is bent by two relative moving rolls. According to different materials and processing requirements, different types of roll bending machines can be selected, such as pneumatic rollbending machine, hydraulic roll bending machine, CNC roll bending machine, etc. Roll bending machines can be divided into horizontal andvertical types, among which vertical roll bending machines can be further divided into 3-axis, 4-axis and 5-axis roll bending machines.Roll bending forming technology has advantages of high processing accuracy, high efficiency and low cost. It is widely used in aerospace, automobile, metallurgy, electronics, machinery and other industries. However, roll bending forming technology also has some disadvantages, such as the processing size is limited by processing parameters, the processing thickness range is narrow, and the processing capacity is limited by material properties.Therefore, in the research of roll bending forming technology, many factors need to be considered, such as design concept, selection of roll bending machine model, selection of processing parameters, selection of tool materials, etc. First of all, it is necessary to determine the designconcept in order to select the right roll bending machine model and processing parameters. Secondly, the structure characteristics of the roll bending machine should be studied carefully to determinethe appropriate model in order to ensure the processing efficiency and accuracy. In terms of selecting processing parameters, reasonable processing parameters should be selected according to the material properties and processing accuracy to ensure the processing effect. In addition, when selecting the tool materials, the service life of the tools, curvature radius and bending accuracy should also be taken into account.In a word, the research of roll bending forming technology is a complicated work, which needs to consider many factors to ensure the processing effect and forming accuracy. In addition, according to the actual situation, the roll bending forming technology should be optimized continuously to improve the processing efficiency and accuracy, so as to meet the constantly developing processing requirements.。
直缝焊管的辊压弯曲成型一般都需经过三种基本弯曲工序
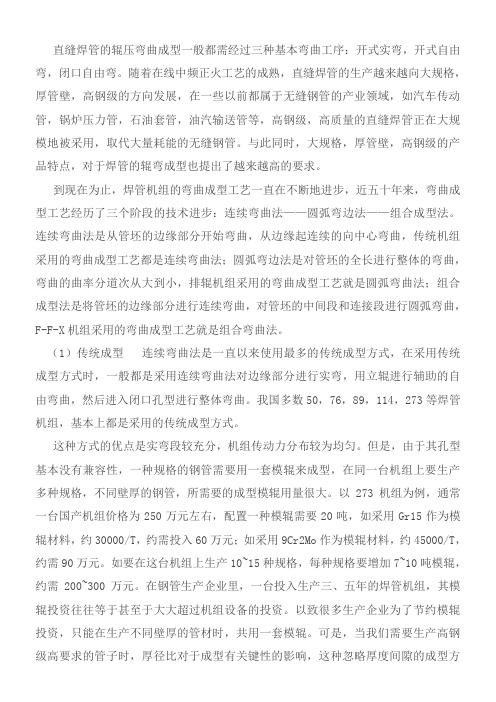
直缝焊管的辊压弯曲成型一般都需经过三种基本弯曲工序:开式实弯,开式自由弯,闭口自由弯。
随着在线中频正火工艺的成熟,直缝焊管的生产越来越向大规格,厚管壁,高钢级的方向发展,在一些以前都属于无缝钢管的产业领域,如汽车传动管,锅炉压力管,石油套管,油汽输送管等,高钢级,高质量的直缝焊管正在大规模地被采用,取代大量耗能的无缝钢管。
与此同时,大规格,厚管壁,高钢级的产品特点,对于焊管的辊弯成型也提出了越来越高的要求。
到现在为止,焊管机组的弯曲成型工艺一直在不断地进步,近五十年来,弯曲成型工艺经历了三个阶段的技术进步:连续弯曲法——圆弧弯边法——组合成型法。
连续弯曲法是从管坯的边缘部分开始弯曲,从边缘起连续的向中心弯曲,传统机组采用的弯曲成型工艺都是连续弯曲法;圆弧弯边法是对管坯的全长进行整体的弯曲,弯曲的曲率分道次从大到小,排辊机组采用的弯曲成型工艺就是圆弧弯曲法;组合成型法是将管坯的边缘部分进行连续弯曲,对管坯的中间段和连接段进行圆弧弯曲,F-F-X机组采用的弯曲成型工艺就是组合弯曲法。
(1)传统成型连续弯曲法是一直以来使用最多的传统成型方式,在采用传统成型方式时,一般都是采用连续弯曲法对边缘部分进行实弯,用立辊进行辅助的自由弯曲,然后进入闭口孔型进行整体弯曲。
我国多数50,76,89,114,273等焊管机组,基本上都是采用的传统成型方式。
这种方式的优点是实弯段较充分,机组传动力分布较为均匀。
但是,由于其孔型基本没有兼容性,一种规格的钢管需要用一套模辊来成型,在同一台机组上要生产多种规格,不同壁厚的钢管,所需要的成型模辊用量很大。
以273机组为例,通常一台国产机组价格为250万元左右,配置一种模辊需要20吨,如采用Gr15作为模辊材料,约30000/T,约需投入60万元;如采用9Cr2Mo作为模辊材料,约45000/T,约需90万元。
如要在这台机组上生产10~15种规格,每种规格要增加7~10吨模辊,约需200~300万元。
连铸辊的失效形式及原因分析

连铸辊的失效形式及原因分析摘要:连铸辊是连铸机上最关键的部件,它承担着承重、驱动钢坯和活动坯模的功能。
其失效形式主要表现为辊子表面的裂纹和小直径辊的弯曲,当裂纹扩展到不能承受外载时,便会发生断裂事故。
本文通表面过裂纹失效形式的分析,指出了裂纹产生的原因和避免裂纹产生的措施;延长了连铸辊子的使用寿命,提高产品质量。
关键词:连铸辊;表面裂纹;脱落;堆焊1.背景连铸辊是扇形段的核心构成部件,在使用过程中,主要承担承载、驱动钢坯和活动坯模的功能。
它连续不断地与内部还未凝固的高温铸坯接触,不仅反复承受着局部高温加热和水冷的交变冷热冲击循环作用,而且还受到板坯鼓胀力和静压力的交变机械应力的作用,以及滞坯、漏钢等异常浇钢情况,工况条件十分恶劣。
使用一段时间后,辊体会产生变形,辊面还会出现不同程度的网状裂纹、氧化腐蚀、磨损等问题。
这些问题将会直接导致钢坯出现质量问题,为更好的保障钢坯的质量,降低连铸辊对钢坯质量影响,提高连铸辊的使用寿命,有必要对连铸辊的失效形式进行分析。
2.连铸辊主要失效形式及分析连铸辊主要的失效形式为:表面裂纹、辊子磨损和辊子弯曲。
2.1表面裂纹连铸辊由于反复受到与高温板坯的接触和冷却的影响容易产生热裂纹(冷热疲劳裂纹);辊子停止时在辊子表面产生拉应力,此反复的应力引起热裂纹。
疲劳裂纹与下列因素有关:2.1.1热负荷:辊子与炙热的铸坯直接接触而被加热,继而又被喷淋水所冷却,经受着强烈的冷热交变热负荷。
最大温度值、接触时间、冷却速度、温度变化的快慢等因素影响着裂纹的产生和扩展。
2.1.2疲劳:辊子表面的所受的热负荷和机械应力的交替作用,使辊子产生疲劳裂纹。
2.1.3腐蚀:辊子表面的腐蚀是由于与冷却水接触相造成的。
冷却水成分因环境的变化,酸性过大导致应力腐蚀和晶间腐蚀发生,增大表面裂纹的产生。
冷却水在裂纹内汽化还会产生气蚀现象。
2.1.4摩擦:辊坯表面易产生氧化铁皮。
辊子与辊坯上下表面间的摩擦会引起较强的磨损。
辊弯成型技术理论及应用研究现状
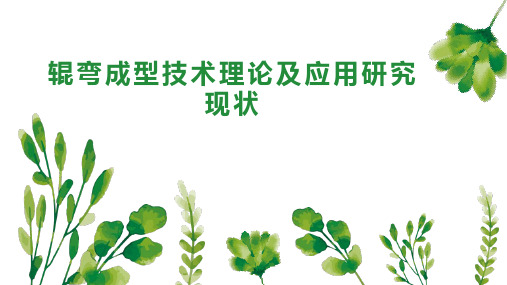
自20世纪80年代以来,快速成型技术得到了快速发展。目前,国际上已经出 现了许多具有代表性的快速成型技术,如立体光刻(SLA)、叠层实体制造 (LOM)、熔融沉积制造(FDM)等。这些技术的不断发展,使得快速成型设备的 性能和精度得到了显著提高,同时也降低了制造成本。
2、国内研究现状
近年来,我国在快速成型技术领域也取得了长足进展。众多科研机构和企业 纷纷投入巨资进行研发和应用,使得我国快速成型设备的生产和制造能力不断提 升。国内研究现状呈现出技术水平逐步提高、应用领域不断拓展的良好态势。
本次演示通过对光固化快速成型的理论、技术及应用的深入研究,发现该技 术在缩短产品开发周期、降低制造成本、提高产品质量等方面具有显著优势。同 时,光固化快速成型技术的应用前景广泛,可为各行各业提供个性化的定制服务, 满足多元化的市场需求。然而,光固化快速成型技术的发展仍存在一定的局限性, 例如设备成本高、材料价格贵等问题,需要进一步加以解决。
随着计算机技术的不断发展,计算机辅助设计系统在异形管连续辊弯成型工 艺中得到了广泛应用。通过引入计算机辅助设计系统,可以大大提高生产效率、 降低生产成本、缩短产品开发周期,同时还能提高产品的质量和精度。
计算机辅助设计系统在异形管连续辊弯成型工艺中的应用包括软件和硬件技 术的使用。在软件方面,常用的软件包括CAD、CAM和CAE等,这些软件可以帮助 设计师进行产品的设计、分析和优化。在硬件方面,随着计算机技术的不断发展, 高性能计算机和高速网络的使用为异形管连续辊弯成型工艺提供了强有力的支持。
三、辊弯成型应用研究
1、汽车制造业
在汽车制造业中,辊弯成型技术被广泛应用于制造汽车零部件,如车门、发 动机罩、后备箱等。利用辊弯成型技术可以生产出具有较高强度和稳定性的零部 件,提高汽车的整体性能和安全性。
辊弯成型
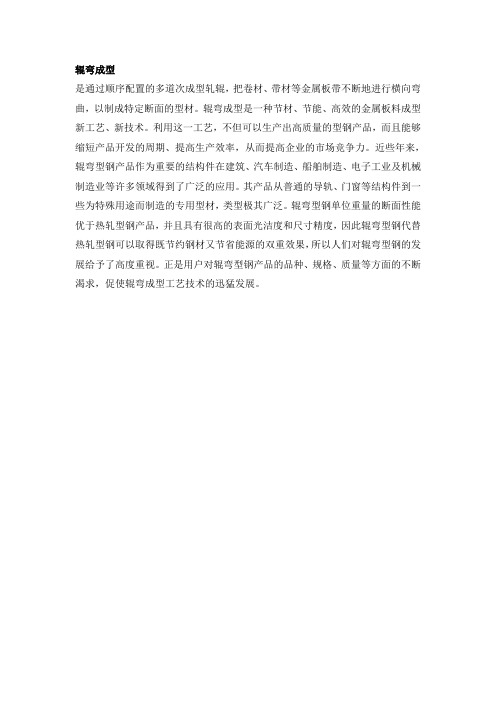
辊弯成型
是通过顺序配置的多道次成型轧辊,把卷材、带材等金属板带不断地进行横向弯曲,以制成特定断面的型材。
辊弯成型是一种节材、节能、高效的金属板料成型新工艺、新技术。
利用这一工艺,不但可以生产出高质量的型钢产品,而且能够缩短产品开发的周期、提高生产效率,从而提高企业的市场竞争力。
近些年来,辊弯型钢产品作为重要的结构件在建筑、汽车制造、船舶制造、电子工业及机械制造业等许多领域得到了广泛的应用。
其产品从普通的导轨、门窗等结构件到一些为特殊用途而制造的专用型材,类型极其广泛。
辊弯型钢单位重量的断面性能优于热轧型钢产品,并且具有很高的表面光洁度和尺寸精度,因此辊弯型钢代替热轧型钢可以取得既节约钢材又节省能源的双重效果,所以人们对辊弯型钢的发展给予了高度重视。
正是用户对辊弯型钢产品的品种、规格、质量等方面的不断渴求,促使辊弯成型工艺技术的迅猛发展。
辊弯成型工艺研究
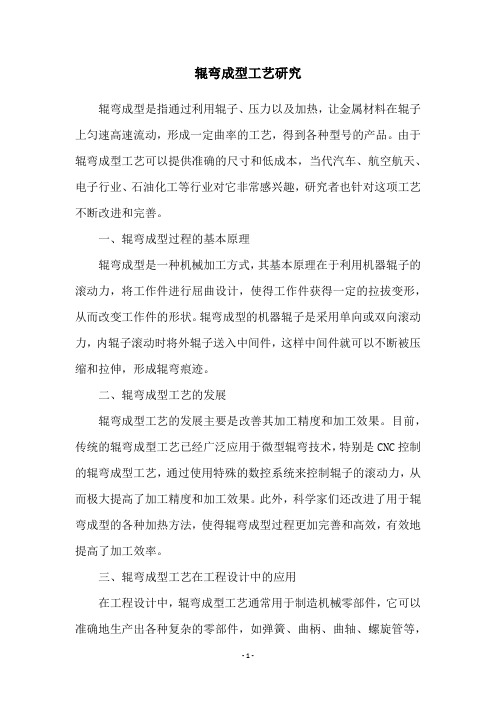
辊弯成型工艺研究辊弯成型是指通过利用辊子、压力以及加热,让金属材料在辊子上匀速高速流动,形成一定曲率的工艺,得到各种型号的产品。
由于辊弯成型工艺可以提供准确的尺寸和低成本,当代汽车、航空航天、电子行业、石油化工等行业对它非常感兴趣,研究者也针对这项工艺不断改进和完善。
一、辊弯成型过程的基本原理辊弯成型是一种机械加工方式,其基本原理在于利用机器辊子的滚动力,将工作件进行屈曲设计,使得工作件获得一定的拉拔变形,从而改变工作件的形状。
辊弯成型的机器辊子是采用单向或双向滚动力,内辊子滚动时将外辊子送入中间件,这样中间件就可以不断被压缩和拉伸,形成辊弯痕迹。
二、辊弯成型工艺的发展辊弯成型工艺的发展主要是改善其加工精度和加工效果。
目前,传统的辊弯成型工艺已经广泛应用于微型辊弯技术,特别是CNC控制的辊弯成型工艺,通过使用特殊的数控系统来控制辊子的滚动力,从而极大提高了加工精度和加工效果。
此外,科学家们还改进了用于辊弯成型的各种加热方法,使得辊弯成型过程更加完善和高效,有效地提高了加工效率。
三、辊弯成型工艺在工程设计中的应用在工程设计中,辊弯成型工艺通常用于制造机械零部件,它可以准确地生产出各种复杂的零部件,如弹簧、曲柄、曲轴、螺旋管等,它可以满足复杂零部件的任何特殊要求,并有效地提高了工程效率。
辊弯成型工艺还可以用于制作各种表面质量高、材质软、硬度可调的金属制品,它能够有效地提高工程所需产品的精度度和硬度。
四、辊弯成型工艺的可能发展辊弯成型工艺的未来可能会发展出更多可能性,如运用三维扫描技术,提高辊弯成型工艺的加工效率,增加辊弯成型机械的精度,降低加工的能耗,提高加工的质量,以使辊弯成型工艺能够更好地适应多样化的加工环境和复杂的结构要求。
综上所述,辊弯成型工艺目前已经得到了实际应用,未来还将会不断发展,完善其加工效率、质量及精度,为各大行业提供更优质的产品。
加热辊弯成型技术

加热辊弯成型技术加热辊弯成型技术是一种常用的金属加工方法,它通过使用热辊对金属材料进行加热,然后利用辊轮的弯曲作用使金属材料产生形变,从而达到制造所需产品的目的。
该技术广泛应用于航空、汽车、建筑等领域,具有成本低、效率高、制造精度高等优点。
一、加热辊弯成型技术的原理加热辊弯成型技术主要是通过对金属材料进行加热,使其变得柔软,然后利用辊轮的弯曲作用将其弯曲成所需的形状。
具体来说,该技术包括以下几个步骤:1. 加热:首先需要将金属材料放置在加热设备中进行加热,使其达到一定的温度。
加热温度的选择要根据金属材料的种类和厚度来确定,一般在材料的熔点以上。
2. 弯曲:加热后的金属材料变得柔软,此时需要将其放置在辊轮上,通过调节辊轮的位置和角度,使其对金属材料产生弯曲作用。
为了获得所需的弯曲角度和曲线形状,可能需要多次进行弯曲操作。
3. 冷却:完成弯曲后,金属材料需要进行冷却,以保持其形状。
冷却方法可以是自然冷却或者通过外部冷却设备进行加速冷却。
1. 航空领域:加热辊弯成型技术在航空领域被广泛应用于制造飞机机身、机翼等部件。
由于航空器对材料的轻量化要求较高,加热辊弯成型技术可以使得金属材料在保持强度的同时实现复杂曲线的成型,从而满足航空器的设计要求。
2. 汽车领域:汽车制造中需要大量的金属部件,如车身、车门等。
加热辊弯成型技术可以使得金属材料在不断变化的曲率下保持较高的强度和韧性,从而实现汽车部件的精确成型。
3. 建筑领域:加热辊弯成型技术在建筑领域被广泛应用于制造钢结构建筑中的梁柱、屋面等部件。
通过加热辊弯成型技术,可以使得钢材在保持强度的同时实现各种复杂的形状,满足建筑设计的要求。
三、加热辊弯成型技术的优势1. 成本低:相比传统的加工方法,加热辊弯成型技术无需复杂的模具和设备,可以大大降低制造成本。
2. 效率高:加热辊弯成型技术可以在较短的时间内完成金属材料的成型,提高生产效率。
3. 制造精度高:加热辊弯成型技术可以实现金属材料的精确成型,形状和尺寸的控制精度高,可以满足复杂产品的制造要求。
弯辊技术
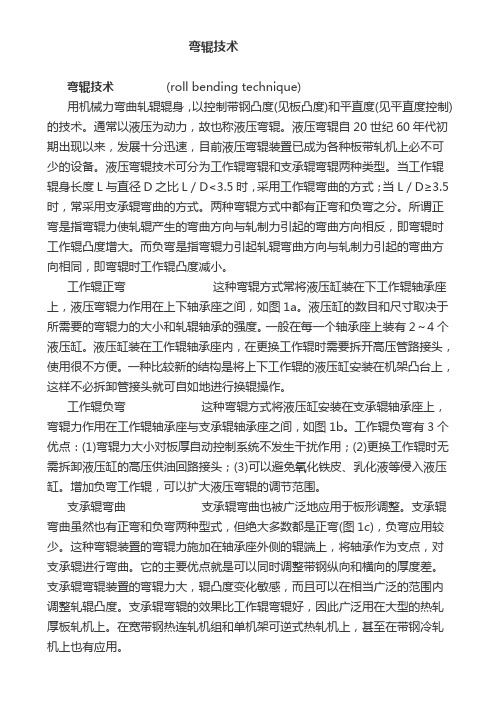
弯辊技术弯辊技术 (roll bending technique)用机械力弯曲轧辊辊身,以控制带钢凸度(见板凸度)和平直度(见平直度控制)的技术。
通常以液压为动力,故也称液压弯辊。
液压弯辊自20世纪60年代初期出现以来,发展十分迅速,目前液压弯辊装臵已成为各种板带轧机上必不可少的设备。
液压弯辊技术可分为工作辊弯辊和支承辊弯辊两种类型。
当工作辊辊身长度L与直径D之比L/D<3.5时,采用工作辊弯曲的方式;当L/D≥3.5时,常采用支承辊弯曲的方式。
两种弯辊方式中都有正弯和负弯之分。
所谓正弯是指弯辊力使轧辊产生的弯曲方向与轧制力引起的弯曲方向相反,即弯辊时工作辊凸度增大。
而负弯是指弯辊力引起轧辊弯曲方向与轧制力引起的弯曲方向相同,即弯辊时工作辊凸度减小。
工作辊正弯这种弯辊方式常将液压缸装在下工作辊轴承座上,液压弯辊力作用在上下轴承座之间,如图1a。
液压缸的数目和尺寸取决于所需要的弯辊力的大小和轧辊轴承的强度。
一般在每一个轴承座上装有2~4个液压缸。
液压缸装在工作辊轴承座内,在更换工作辊时需要拆开高压管路接头,使用很不方便。
一种比较新的结构是将上下工作辊的液压缸安装在机架凸台上,这样不必拆卸管接头就可自如地进行换辊操作。
工作辊负弯这种弯辊方式将液压缸安装在支承辊轴承座上,弯辊力作用在工作辊轴承座与支承辊轴承座之间,如图1b。
工作辊负弯有3个优点:(1)弯辊力大小对板厚自动控制系统不发生干扰作用;(2)更换工作辊时无需拆卸液压缸的高压供油回路接头;(3)可以避免氧化铁皮、乳化液等侵入液压缸。
增加负弯工作辊,可以扩大液压弯辊的调节范围。
支承辊弯曲支承辊弯曲也被广泛地应用于板形调整。
支承辊弯曲虽然也有正弯和负弯两种型式,但绝大多数都是正弯(图1c),负弯应用较少。
这种弯辊装臵的弯辊力施加在轴承座外侧的辊端上,将轴承作为支点,对支承辊进行弯曲。
它的主要优点就是可以同时调整带钢纵向和横向的厚度差。
支承辊弯辊装臵的弯辊力大,辊凸度变化敏感,而且可以在相当广泛的范围内调整轧辊凸度。
弯辊与窜辊

WRS(Work Rool Shifting)工作辊窜辊
一、综述
所谓工作辊窜辊就是工作辊就是工作辊沿轴线方向上的水平移动,工作辊的窜辊是均匀工作辊磨损的优选措施,同时对提高弯辊的功效,降低工作辊的过度挠曲及减小有害接触区有一定的作用。
工作辊的窜辊有四个液压缸进行控制,分别分布在上下工作辊操作侧的入口侧和出口侧,每个液压缸上都有一个位置传感器,通过传感器检测工作辊的窜动位置,在窜动过程中必须保持上下工作辊偏离中心线的位置同步、上工作辊入口侧和出口侧两个液压缸的位置同步、下工作辊入口侧和出口侧两个液压缸的位置同步,这些都通过传感器检测的数值反馈到程序内部进行计算并把计算的结果输出到对应的伺服阀来进行调节。
工作辊的窜辊分为正窜和负窜:所谓正窜就是指上工作辊向驱动侧移动,下工作辊向操作侧移动,使辊的弯曲度增加(positive),能有效减少边部波浪;所谓负窜是指上工作辊向操作侧移动,下工作辊向驱动侧移动,使辊的弯曲度减小(negtive),使边部波浪产生的可能性增加。
窜辊是在静态状态下进行的,在1+4热连轧项目中应用在精轧部分,在自动模式下窜动的位置由二级(过程自动化)给定,手动模式下操作员可以根据经验值进行设定
值的调整,窜辊在板带材进入机架前已经提前摆好位置并锁定,在轧制过程中是不允许进行窜动的,窜动的目的主要是减小轧辊的磨损,但对板带材的平整度控制也有一定的影响,另外在换辊时窜动一定的位置可以方便上工作辊落在下工作辊的支撑位置方便工作辊的抽出。
m
D R I V
E S I D E 50 m m
50 m m
g
A x i a l _s h i f t .d s f
二、 1、 位置控制:控制的计算、模式选择、监视。
影响板型的因素
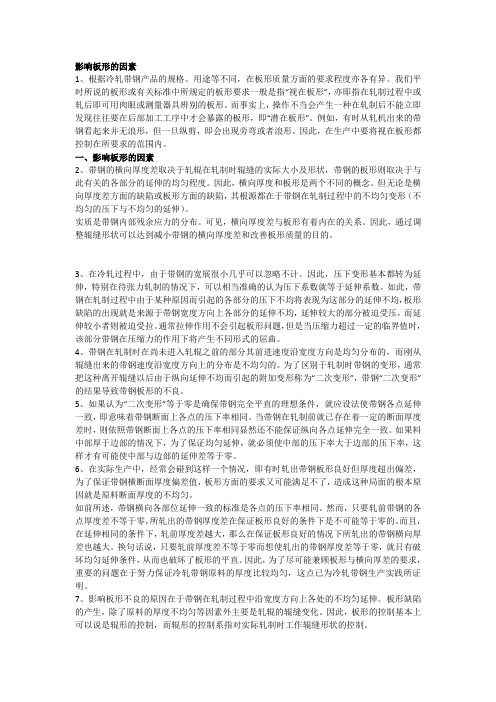
影响板形的因素1、根据冷轧带钢产品的规格、用途等不同,在板形质量方面的要求程度亦各有异。
我们平时所说的板形或有关标准中所规定的板形要求一般是指“视在板形”,亦即指在轧制过程中或轧后即可用肉眼或测量器具辨别的板形。
而事实上,操作不当会产生一种在轧制后不能立即发现往往要在后部加工工序中才会暴露的板形,即“潜在板形”。
例如,有时从轧机出来的带钢看起来并无浪形,但一旦纵剪,即会出现旁弯或者浪形。
因此,在生产中要将视在板形都控制在所要求的范围内。
一、影响板形的因素2、带钢的横向厚度差取决于轧辊在轧制时辊缝的实际大小及形状,带钢的板形则取决于与此有关的各部分的延伸的均匀程度。
因此,横向厚度和板形是两个不同的概念。
但无论是横向厚度差方面的缺陷或板形方面的缺陷,其根源都在于带钢在轧制过程中的不均匀变形(不均匀的压下与不均匀的延伸)。
实质是带钢内部残余应力的分布。
可见,横向厚度差与板形有着内在的关系。
因此,通过调整辊缝形状可以达到减小带钢的横向厚度差和改善板形质量的目的。
3、在冷轧过程中,由于带钢的宽展很小几乎可以忽略不计。
因此,压下变形基本都转为延伸,特别在待张力轧制的情况下,可以相当准确的认为压下系数就等于延伸系数。
如此,带钢在轧制过程中由于某种原因而引起的各部分的压下不均将表现为这部分的延伸不均,板形缺陷的出现就是来源于带钢宽度方向上各部分的延伸不均,延伸较大的部分被迫受压,而延伸较小者则被迫受拉。
通常拉伸作用不会引起板形问题,但是当压缩力超过一定的临界值时,该部分带钢在压缩力的作用下将产生不同形式的屈曲。
4、带钢在轧制时在尚未进入轧辊之前的部分其前进速度沿宽度方向是均匀分布的,而刚从辊缝出来的带钢速度沿宽度方向上的分布是不均匀的。
为了区别于轧制时带钢的变形,通常把这种离开辊缝以后由于纵向延伸不均而引起的附加变形称为“二次变形”,带钢“二次变形”的结果导致带钢板形的不良。
5、如果认为“二次变形”等于零是确保带钢完全平直的理想条件,就应设法使带钢各点延伸一致,即意味着带钢断面上各点的压下率相同。
高强钢-超高强钢局部加热辊弯成形技术研究

高强钢-超高强钢局部加热辊弯成形技术探究高强度钢材是现代工程结构中越来越重要的材料,但同时也存在成形难度大、加工性能差等问题,这限制了其应用范围。
局部加热辊弯成形技术是提高高强度钢材加工效率和质量的重要技术手段之一。
本文系统综述了高强度钢材局部加热辊弯成形技术的探究现状和进步趋势,分析了不同加热方法和参数对于成形质量的影响,总结了高强度钢材局部加热辊弯成形技术在航空、汽车、高速铁路等领域的应用状况。
针对现有探究中存在的问题,如热影响区域过大、成形质量低等,提出了将来探究的方向和进步趋势,包括针对不同材质的局部加热策略、加热控制策略的优化、自适应辊弯成形等方面的探究。
本文的探究效果可以为高强度钢材局部加热辊弯成形技术的探究和应用提供参考。
关键词:高强度钢材;局部加热;辊弯成形;热影响区域;优化策略Abstract:High-strength steel is an increasingly important material in modern engineering structures, but it also faces difficulties in forming and poor processingperformance, which limits its application range. Local heating roller bending forming technology is one ofthe important technical means to improve theprocessing efficiency and quality of high-strength steel. This paper systematically reviews the research status and development trend of local heating roller bending forming technology for high-strength steel, analyzes the influence of different heating methodsand parameters on the forming quality, and summarizes the application of local heating roller bendingforming technology for high-strength steel in aviation, automobile, high-speed railway and other fields. Aimed at the problems existing in the current research, such as too large thermal affected zone and low forming quality, the future research direction and development trend are proposed, including local heating strategies for different materials, optimization of heatingcontrol strategies, adaptive roller bending forming, etc. The research results of this paper can provide reference for the research and application of local heating roller bending forming technology for high-strength steel.Keywords: high-strength steel; local heating; roller bending forming; thermal affected zone; optimization strategy。
《2024年中厚板矫直机矫直辊变形及弯辊模型研究》范文

《中厚板矫直机矫直辊变形及弯辊模型研究》篇一一、引言中厚板矫直机是钢铁生产线上重要的设备之一,用于对轧制后的中厚板进行矫直处理。
矫直辊作为矫直机的核心部件,其性能直接影响到矫直效果和产品质量。
然而,在实际生产过程中,矫直辊常常会出现变形和弯曲等问题,这些问题不仅影响矫直效果,还可能对设备造成损害。
因此,研究矫直辊的变形及弯辊模型具有重要的理论和实践意义。
本文将就中厚板矫直机矫直辊的变形及弯辊模型进行研究,以期为实际生产提供理论支持。
二、矫直辊的变形原因分析矫直辊的变形主要是由于长期受到力的作用以及使用过程中的热处理和化学处理等多种因素引起的。
首先,长期承受力的作用导致矫直辊表面和内部发生塑性形变;其次,矫直辊在热处理过程中可能产生热应力导致形变;最后,矫直辊表面的腐蚀、氧化等因素也会对其结构产生影响,进而导致变形。
三、矫直辊的弯辊模型研究为了更好地理解矫直辊的变形过程并对其进行有效控制,建立弯辊模型是关键。
本文将通过以下步骤对弯辊模型进行研究:1. 确定影响矫直辊变形的因素:包括矫直力、矫直速度、温度等。
2. 建立数学模型:根据矫直辊的物理特性和实际工作情况,建立数学模型,描述矫直辊的变形过程。
3. 模型验证:通过实际生产数据对模型进行验证和修正,确保模型的准确性和可靠性。
4. 模型应用:将弯辊模型应用于实际生产中,通过调整矫直力、速度等参数,实现对矫直辊变形的有效控制。
四、实验研究及结果分析为了验证弯辊模型的准确性和有效性,本文进行了以下实验研究:1. 实验设计:选取不同规格的中厚板进行矫直实验,记录矫直过程中的各项参数及矫直辊的变形情况。
2. 数据分析:对实验数据进行整理和分析,得出不同条件下矫直辊的变形规律及影响因素。
3. 结果分析:将实验结果与弯辊模型进行对比,验证模型的准确性。
同时,分析实验过程中出现的问题及原因,为进一步优化弯辊模型提供依据。
五、结论与展望通过对中厚板矫直机矫直辊的变形及弯辊模型进行研究,本文得出以下结论:1. 矫直辊的变形主要受矫直力、温度、速度等因素的影响。
- 1、下载文档前请自行甄别文档内容的完整性,平台不提供额外的编辑、内容补充、找答案等附加服务。
- 2、"仅部分预览"的文档,不可在线预览部分如存在完整性等问题,可反馈申请退款(可完整预览的文档不适用该条件!)。
- 3、如文档侵犯您的权益,请联系客服反馈,我们会尽快为您处理(人工客服工作时间:9:00-18:30)。
n L hctg125'
d
d
加工不同曲率半径的辊弯件:调节中间 辊与下面两个辊子到三辊的同时 辊压,留下一段平直部分。
这些直边在校圆时也难以完全消除,故 一般对板材端头进行预弯。
常用的预弯方法:
辊弯中,从平板一次弯得的曲率半径有一个极限。 在三个辊子成等腰三角形时,用下式计算中间辊
辊形工艺辊形工艺生产率高,适用于生 产批量大的等截面长工件
可与多种工艺过程结合:如冲孔、起伏 成形、焊接、定尺剪切等。
辊形工艺设计要点如下:
1 带料宽度
辊形的带料宽度应按应变中性层的展开长度计 算。
2 导向线
为使毛坯从平板状态顺利向前移动而成形,应 设置水平导向线和垂直导向线.
水平导向线从第一组辊轮开始到最后一组辊轮 为止始终保持在同一水平面上:
垂直导向线垂直于辊轮轴线, 使导向线两侧的材料变形量基 本相等的一条基准线。
3 弯曲角度与直边升角
在一组辊轮中,同时弯曲的角不应超过二个。 一次弯曲的角度也有相应的参考值。
辊形时,直边最大高度应符合直线向上的关系, 其设计方法为控制成形直边升角。材料不同, 直边升角也有所不同(1°25’)。
4 花形展开图与辊形顺序
上下辊轮直径一致的直径是辊轮的节圆直径,也称辊 形线。在节圆上带料可无滑移地送进。
从第一对辊轮到最后一对辊轮,节圆直径应依次递增 0.4%(带料厚度小于0.3mm时取0.25%),使辊轮对材 料始终朝送进方向给以拉伸作用。
简单截面的辊形,辊轮工位间距为d,成 形设备的全长为L,辊轮组数n为:
花型展开图就是确定辊形顺序的过程,有三种:
①先内后外 (图a),可使毛坯边缘平直,易于材料流向 两边,被广泛应用于宽板等的成形:
②采用先外后内的弯曲顺序(图b),可以充分发挥工作 型辊的变形作用,多用于管形件等的成形;
③内、外整体进行缓和的过渡弯曲,然后再对急剧过渡 的角度作精加工。
5 辊轮节圆直径与辊轮组数
辊弯和辊形
辊弯:是辊轮旋转时在摩擦力的带动下, 使板材连续进入辊轮之间而弯曲成形的 一种加工方法,一般用于有大弯曲半径 的零件。
辊形(辊压成形):将带料通过带有型槽的 数组成形辊轮,渐次进行多道弯曲成形, 从而得到所需截面形状的零件
一、辊弯
将毛坯送入成等腰三角形的三个辊子之 间进行辊弯成形,下面两个辊子支承毛 坯,而中间辊施压使毛坯弯曲,
与下面两个辊于中心连线之距离s:
s r t R 2 2 a2 r R1
式中 R1、R2—分别为上下辊轮的半径,
a—下辊轮的半中心距: r—辊弯件内层回弹前的曲率半径, t—料厚。
二、辊形
带料进入辊轮入口开始弯曲变形,通过 辊轮截面4后,此组辊轮成形完毕,再进 入下一组辊轮。
辊形工艺的特点