第2章 加工精度分析与制造质量监控技术
机械加工过程中的质量控制与检测技术

机械加工过程中的质量控制与检测技术随着科技的不断进步,机械工程在制造领域发挥着重要的作用。
机械加工是制造过程中不可或缺的环节,而质量控制与检测技术则是确保机械制造的关键。
本文将探讨机械加工过程中的质量控制与检测技术,并介绍其中一些常用的方法。
一、质量控制的重要性在机械加工过程中,质量控制是确保产品符合设计要求的关键。
一旦产品质量出现问题,不仅会影响到产品的性能和可靠性,还可能导致安全隐患和经济损失。
因此,质量控制在机械工程中具有重要意义。
二、质量控制方法1. 设计阶段的质量控制:在机械加工之前,设计阶段的质量控制非常关键。
通过合理的设计和工艺规划,可以减少制造过程中的错误和缺陷,提高产品的质量和可靠性。
2. 加工参数的控制:在机械加工过程中,控制加工参数是确保产品质量的重要手段。
例如,对于数控加工,控制切削速度、进给速度和切削深度等参数,可以保证加工精度和表面质量。
3. 检测与测量:质量控制离不开检测与测量。
通过使用各种测量工具和设备,如千分尺、游标卡尺和高度规等,可以对产品的尺寸和形状进行测量,以确保其符合设计要求。
三、常用的检测技术1. 硬度检测:硬度是材料抵抗外力的能力,对于机械加工来说非常关键。
硬度检测可以通过硬度计等设备进行,以评估材料的硬度是否符合要求。
2. 表面粗糙度检测:表面粗糙度对于机械零件的功能和耐久性有着重要影响。
通过使用表面粗糙度仪等设备,可以对零件表面的光洁度进行检测,以确保其满足设计要求。
3. 尺寸测量:尺寸测量是机械加工中最常见的检测技术之一。
通过使用精密测量工具,如三坐标测量机和光学投影仪,可以对零件的尺寸进行精确测量,以确保其符合设计要求。
四、质量控制与检测技术的挑战在机械加工领域,质量控制与检测技术面临着一些挑战。
首先,随着制造工艺的不断发展,产品的复杂性和精度要求不断提高,对质量控制和检测技术提出了更高的要求。
其次,制造过程中的变异性和误差也会对质量控制造成挑战,需要采取措施来减少其影响。
第二章 机械加工精度及其控制(一)

考虑最简单的情况,主轴回转中心在x方向上作简谐直线运动,其频 率与主轴转速相同,幅值为2e。则刀尖的坐标值为:
X ( R e) cos Y R sin
式中 R —— 刀尖回转半径; φ—— 主轴转角。 显然,上式为一椭圆。
e
径向跳动对镗孔精度影响
S 8 R h
式中 R ——球头刀半径; h ——允许的残留高度。
h
S
空间曲面数控加工
16
例2:用阿基米德蜗杆滚刀滚切渐开线齿轮 采用阿基米德蜗杆或法向直廓蜗杆代替渐开线基本蜗杆 而产生的刀刃齿廓近似造型误差。 由于滚刀刀齿有限,实际加工出的尺形是一条有微小折 线组成的曲线,和理论的光滑渐开线有差异。
19
20:29
20
1)导轨在水平面内的直线度(弯曲) Y
对于车床和外圆磨床由于刀尖相对于工件回转轴线在加工表面径向方向的变 化属敏感方向,故其对零件的形状精度影响很大。
R y
车床导轨在水平面内有弯曲后,纵向 进给中刀具相对工件轴线不能平行。因而 工件表面上形成形状误差。当导轨向后凸 时工件产生鞍形误差,向前凸时工件产生 鼓形误差。
间的相互位置)对理想几何参数的偏离程度, 从保证产品使用性能分析允许有一定的加工误 差。
20:29 3
3、两者关系:
两者从不同角度来评定加工零件的几何参数。
加工精度的高低是由加工误差的小大来表示的 ,保证和提高加工精度问题,实际上是限制和 降低加工误差问题。
4、加工精度的合理制定:
一般加工精度越高则加工成本相对越高,生产
26
回转精度:
机床主轴在回转时实际回转轴线对理想回转轴线的相一致程度。
机械加工质量分析及控制

机械加工质量分析及控制机械加工质量分析及控制一、引言二、机械加工质量分析机械加工质量的分析主要包括以下几个方面:1.表面粗糙度分析机械加工的表面粗糙度对于产品的外观和性能有着重要影响。
通过使用表面粗糙度测量仪器,可以对机械加工的表面粗糙度进行评估。
常用的表面粗糙度参数包括Ra、Rz等。
2.尺寸精度分析机械加工的尺寸精度是指产品的实际尺寸和设计图纸上的尺寸之间的偏差。
通过使用测量工具和仪器,可以对机械加工的尺寸精度进行评估。
常用的尺寸精度参数包括公差、尺寸偏差等。
3.形状偏差分析机械加工的形状偏差是指产品的实际形状和设计图纸上的形状之间的偏差。
通过使用形状测量仪器,可以对机械加工的形状偏差进行评估。
常用的形状偏差参数包括圆度误差、平面度误差等。
三、机械加工质量控制为了确保机械加工的质量,需要进行相应的控制措施。
以下是几个常用的机械加工质量控制方法:1.工艺参数控制调整机械加工的工艺参数,可以对机械加工的质量进行控制。
例如,通过调整切削速度、进给速度和切削深度等参数,可以控制机械加工的表面粗糙度和尺寸精度。
2.设备状态监控对机械加工设备的状态进行监控,可以及时发现并修复设备故障,避免对产品质量的影响。
常用的设备状态监控方法包括振动监测、温度监测等。
3.质量检验与统计分析对机械加工的产品进行质量检验,并进行统计分析,可以及时发现并纠正加工过程中的问题。
常用的质量检验方法包括外观检查、尺寸测量等。
四、机械加工质量的分析和控制是确保产品质量的重要手段。
通过对表面粗糙度、尺寸精度和形状偏差等进行分析,可以找出问题所在。
通过工艺参数控制、设备状态监控和质量检验与统计分析等控制措施,可以提高机械加工的质量水平。
机械加工质量分析与控制课件

能够全面了解机械加工过程和产品的质量情况,找出影响质量的因素并 采取相应的措施进行改进,提高加工过程的稳定性和产品质量的可靠性。
PART 03
机械加工质量控制技术
加工参数优化
切削参数优化
根据工件材料、刀具材料和加工 条件,选择合适的切削速度、进 给速度和切削深度,以提高加工 效率和加工质量。
案例二:某生产线上的加工质量控制
总结词
通过引入自动化检测设备和加工监控系统,确保生产线上的产品质量稳定。
详细描述
某生产线在加工过程中,产品质量不稳定,合格率波动较大。为了解决这一问题, 引入了先进的自动化检测设备和加工监控系统。这些设备可以实时监测加工过程 中的各项参数,及时发现并纠正异常,确保产品质量稳定。
精细化检验标准
制定更加精细化的检验标准和方法,提高检 验的准确性和可靠性,确保机械加工质量符 合要求。
全过程质量控制模式
全过程质量追溯
建立全过程的质量追溯体系,对机械加工过程中的每一个 环节进行记录和追溯,便于质量问题的定位和解决。
01
全过程监控与评估
对机械加工全过程进行实时监控和评估, 及时发现和解决潜在的质量问题,确保 加工质量的稳定性和可靠性。
自动化检测与修正
利用机器视觉和自动化检测技术,实现机械加工零件的自动检测和 误差修正,提高加工精度和一致性。
精细化质量控制标准
精细化工艺参数控制
对机械加工过程中的各项工艺参数进行精细 化控制,确保工艺参数的稳定性和准确性, 提高加工质量。
精细化材料质量控制
加强材料采购、存储和使用等环节的管理,确保材 料质量的稳定性和可靠性,降低因材料问题导致的 质量风险。
加工误差补偿
误差建模
机械零件的加工精度检测与控制
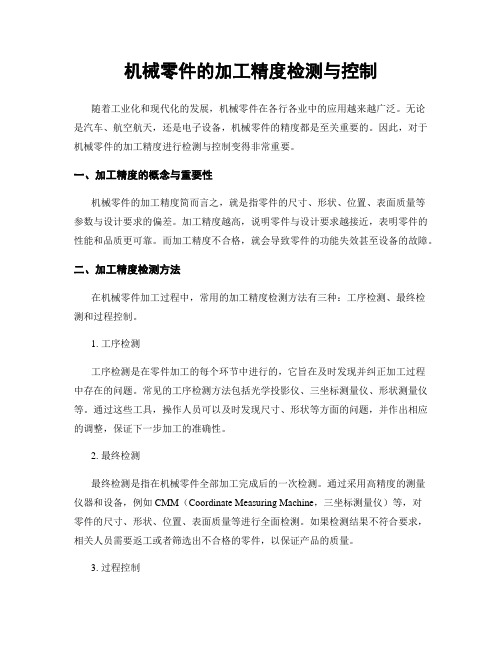
机械零件的加工精度检测与控制随着工业化和现代化的发展,机械零件在各行各业中的应用越来越广泛。
无论是汽车、航空航天,还是电子设备,机械零件的精度都是至关重要的。
因此,对于机械零件的加工精度进行检测与控制变得非常重要。
一、加工精度的概念与重要性机械零件的加工精度简而言之,就是指零件的尺寸、形状、位置、表面质量等参数与设计要求的偏差。
加工精度越高,说明零件与设计要求越接近,表明零件的性能和品质更可靠。
而加工精度不合格,就会导致零件的功能失效甚至设备的故障。
二、加工精度检测方法在机械零件加工过程中,常用的加工精度检测方法有三种:工序检测、最终检测和过程控制。
1. 工序检测工序检测是在零件加工的每个环节中进行的,它旨在及时发现并纠正加工过程中存在的问题。
常见的工序检测方法包括光学投影仪、三坐标测量仪、形状测量仪等。
通过这些工具,操作人员可以及时发现尺寸、形状等方面的问题,并作出相应的调整,保证下一步加工的准确性。
2. 最终检测最终检测是指在机械零件全部加工完成后的一次检测。
通过采用高精度的测量仪器和设备,例如CMM(Coordinate Measuring Machine,三坐标测量仪)等,对零件的尺寸、形状、位置、表面质量等进行全面检测。
如果检测结果不符合要求,相关人员需要返工或者筛选出不合格的零件,以保证产品的质量。
3. 过程控制在机械零件加工的整个过程中,通过控制加工设备的参数和监测加工过程中的数据,可以实现对加工精度的控制。
例如,通过对切削力、切削转速、进给速度等参数的实时监测和控制,可以及时调整加工过程中的问题,提高零件的加工精度。
三、加工精度控制的现状与挑战虽然加工精度检测与控制在现代工业中已经得到广泛应用,但仍面临一些挑战。
1. 多种零件加工不同的机械零件具有不同的形状、材料和制造要求,因此对于不同的零件,需要采用不同的加工精度检测与控制方法。
如何在不同的加工环境中选择合适的检测与控制方法,是一个需要技术人员深入研究的问题。
加工精度分析与制造质量监控技术

导轨在垂直平面内的直线度误差:卧式车床导轨
在垂直面内的直线度误差△2可引起被加工工件的形状 误差和尺寸误差。但△2对加工精度的影响要比△1小 得多。由图可知,若因△2而使刀尖由a下降至b,不难 推得工件半径R的变化量。
2.4.2表面质量对仪器使用性能的影响
1.表面粗糙度对耐磨性的影响
表面粗糙度对零件表面磨损的影响很大。一般 说表面粗糙度值愈小,其磨损性愈好。但表面粗糙 度值太小,润滑油不易储存,接触面之间容易发生 分子粘接,磨损反而增加。因此,接触面的粗糙度 有一个最佳值,其值与零件的工作情况有关,工作 载荷加大时,初期磨损量增大,表面粗糙度最佳值 也加大。
全取决于刀具的制造精度。如:所谓“电子配钥匙”
成形运动法: 成形运动法 使刀具相对于工件做有规律的切削成形运动,
从而获得所要求的零件表面形状。如:滚齿、车螺纹
非成形运动法:通过对加工表面形状的检测,由工人对其进
行相应的修整加工,以获得所要求的形状精度。尽管非成形 运动法是获得零件表面形状精度的最原始方法,效率相对比 较低 。
3.减少工艺系统受力变形的途径 1)提高机床零部件间结合表面的质量 2)对部件运动面预加负载 3)提高工件定位基面的精度和减少定位基面的表面 粗糙度 4)使用辅助支承提高工艺系统刚度 5)采用合理安装夹紧方式减少装夹变形
2.2.6 工艺系统的受热变形
1.工艺系统的热源: 摩擦热、切削热辐射热及环境温度等 2.刀具热变形 :刀具受热以后,引起刀具热伸长,刀尖位置
2.表面质量对配合质量的影响
表面粗糙度值的大小将影响配合表面的配合 质量。对于间隙配合,粗糙度值大会使磨损加大, 间隙增大,破坏了要求的配合性质。对于过盈配合, 装配过程中一部分表面凸峰被挤平,实际过盈量减 小,降低了配合件间的连接强度。
机械加工中的精度控制技术和测量方法

机械加工中的精度控制技术和测量方法随着科技和工业的发展,各类机械的制造和加工技术也在不断进步。
对于机械制造业来说,精度控制是一个重要的方面。
机械零件的精度对机器设备的稳定性、运转效能和寿命等方面都有着重要的影响。
本文将从机械加工中的精度问题以及如何控制精度两个方面进行探讨。
机械加工中的精度问题机械零件的精度一般用公差来描述,而机械加工中的公差通常分为六种基本公差。
这六种公差是长度公差、角度公差、平面度公差、垂直度公差、同轴度公差和圆度公差。
这些公差都是机械零件制造中需要控制的方面,控制精度的方法一般分为几种:1. 设计公差与制造公差的匹配。
在设计机械零件时需要考虑到每个零件的制造公差,在计算和设计时把制造偏差预留进去,以确保就算制造偏差出现,机械零件的实际精度依然能够符合要求。
2. 采用精度先进的加工设备和工艺。
在现代机械制造中,精度先进的加工设备和工艺已经很普及了。
这些设备可以大大提高机械零件的精度,并且在制造过程中能够自动检测和修正制造偏差。
3. 加强人员培训与管理。
机械零件的制造不仅需要先进的设备和工艺,更需要经验丰富、技术纯熟的操作人员。
因此,对于机械厂家来说,加强培训和管理是保证零件精度的重要手段。
机械加工中的测量方法机械加工中的精度控制需要采用科学的测量方法来进行检测和评估。
以下是几种常用的精度测量方法:1. 示值式仪器法: 示值式仪器法是一种常见的测量方法,可以利用分度规、卡尺、螺旋测微计等示值式测量仪器来进行测量,通过示值式测量仪器可以获取到测量设备的位置坐标和尺寸数值。
2. 光学测量法: 光学测量法是一种非接触式测量方法,可以使用显微镜、投影测量机等设备对机械零件进行测量。
光学测量法具有精度高、速度快、非接触等优点,适用于对复杂形状的零件进行测量。
3. 数值式测量法: 数值式测量法是指利用计算机数值处理测量数据的方法,可以通过测量设备的感应信号将测量数据上传到计算机中进行处理和分析,从而得出测量结果。
零件加工中的质量控制技术

零件加工中的质量控制技术在零件加工这个领域中,质量的控制显得尤为重要,因为它关乎着整个产品的质量,甚至直接关系到用户的安全和利益。
在这篇文章中,我将介绍几种常用的零件加工中的质量控制技术。
一、检验与测试技术在加工过程中,我们需要对产品进行检验和测试。
检验的方法一般有目视检查、量具尺寸检查、硬度测量、材料成分检测、X 光、磁粉探伤和超声波探伤等。
测试的方法一般有静载试验、疲劳试验、耐蚀试验和环境试验等。
在进行检验和测试时,需要严格按照标准操作,准确记录数据。
如果发现质量问题,需要及时退回改制,或者追查原因,保证产品不会出现质量问题,确保用户的安全和利益。
二、数控加工技术数控加工技术是一种基于计算机数控系统的高效加工技术,它可以显著提高加工质量的稳定性和一致性,同时也可以提高加工的灵活性和生产效率。
数控加工技术的优势在于精度高、效率高和成本低。
它能够精确地控制加工参数,如切割速度、加工深度和刀具路线等,从而保证零件的精度和质量。
另外,数控机床还可以实现自动化生产,减少人为误差,同时也能够高效地处理大批量工件。
三、CAD技术CAD技术即计算机辅助设计技术,它为零件加工提供了强有力的支持。
通过使用CAD软件,加工人员可以在计算机上进行零件设计和三维造型,然后与数控机床相结合,实现高精度、高效的加工过程。
CAD技术可以大幅降低人为误差和误差率,同时提高设计和制造的速度和效率。
因为设计和制造工序紧密相连,所以CAD技术不仅可以减少制造过程中的错误,还可以减少中间流程,提高生产效率。
四、连续改进技术连续改进技术是一种持续不断地优化加工过程和产品设计的方法,它重视与时间的比较和与不同版本之间的比较,目的是不断优化产品和工艺,提高质量和降低成本。
连续改进技术的精髓在于持续改进,在日常工作中发现问题、解决问题、持续完善过程、提高质量等核心目标。
通过持之以恒的改进工作,可以不断提高加工质量,为用户提供更好的产品和服务。
机械制造中的精密测量与质量控制

机械制造中的精密测量与质量控制在机械制造领域,精密测量与质量控制是至关重要的环节。
它们对于确保机械产品的质量、性能和可靠性具有重要作用。
本文将探讨精密测量与质量控制的重要性,以及其在机械制造中的应用。
一、精密测量的重要性精密测量是指通过使用高精度的测量仪器和技术手段,对机械产品的尺寸、形状、表面质量等进行测量和评估。
精密测量主要用于以下几个方面:1.质量控制:精密测量可以帮助制造商监控产品的质量,并及时发现和纠正生产过程中的问题。
通过测量和分析数据,可以确定产品是否符合设计要求,并对生产过程进行调整和改进。
2.工艺优化:精密测量可以提供有关产品和生产工艺的详细数据。
通过分析这些数据,制造商可以了解生产过程中可能存在的问题,并针对性地进行优化,以提高产品的质量和生产效率。
3.性能评估:精密测量可以对机械产品的性能进行评估和验证。
通过测量关键参数,如尺寸、形状、表面质量等,可以确定产品是否符合设计要求,并预测其在实际使用中的性能表现。
二、精密测量的应用在机械制造领域,精密测量广泛应用于各个环节和阶段。
下面我们将分别介绍几个典型的应用场景。
1.产品设计:精密测量在产品设计阶段起到了至关重要的作用。
通过对所设计产品进行精密测量,可以验证设计是否满足要求,并进行必要的修改和改进。
2.原材料检测:精密测量在原材料检测中也扮演着重要角色。
通过对原材料进行精密测量,可以确保其质量和尺寸满足制造要求,避免因材料质量不良而导致的产品质量问题。
3.加工工艺控制:精密测量可以在机械加工过程中实时监测产品的尺寸和形状变化,并及时调整和控制工艺参数,以确保产品的精度和质量。
4.最终产品检测:精密测量在最终产品的检测中起到了关键作用。
通过对最终产品进行全面、精确的测量,可以确保产品达到设计要求,并对不合格产品进行筛查和修正。
三、质量控制的重要性除了精密测量外,质量控制也是机械制造中不可或缺的环节。
质量控制旨在确保产品的质量稳定和一致性,避免产品质量问题对用户和企业造成损失。
02-仪器制造技术-gbi-第二章 加工精度分析与制造质量监控技术2

§2.2.2 机床误差
Precision Engineering Lab., Xiamen Univ.
机床误差主要包括:
主轴回转误差 机床导轨误差 机床传动链误差
§2.2.2 机床误差
Precision Engineering Lab., Xiamen Univ.
1. 主轴回转误差
主轴回转误差是指主轴 实际回转线对其理想回 转轴线的漂移。 为便于研究,可将主轴 回转误差分解为径向圆 跳动、端面圆跳动和倾 角摆动三种基本型式。
§2.2.2 机床误差
Precision Engineering Lab., Xiamen Univ.
2. 机床导轨误差
导轨扭曲对加工精度的影响,影响显著。
Precision Engineering Lab., Xiamen Univ.
刨床、铣床等平面加工机床,工作台(或滑枕)的直线运动 精度直接影响加工表面度,它们的误差敏感方向为垂直方向 镗床的误差敏感方向是随主轴回转变化的,故导轨在水平面 及垂直面内的直线度误差均直接影响加工精度。 普通镗床上镗孔,如果以镗刀杆进给时,那么导轨不直、扭曲 或镗杆轴线不平行等误差,都会引起所镗出的孔与其基准的 相互互位臵误差,不产生孔的形状误差 如果工作台进给,导轨不直或扭曲,都会引起所加工的孔的 轴线不直。当导轨主轴不平行时,则镗出孔是椭圆形的。
Precision Engineering Lab., Xiamen Univ.
车削时(如图所示),设 主轴轴线仍沿Y方向作简谐 直线运动,则工件1处切出 的半径比在2、4处小一个 振幅A,而在工件3处切出 的半径则比2、4处大一个 振幅A。这样在工件的上述 4点直径都相等,在其它各 点处的直径误差也甚小, 故车削出的工件表面接近 于一个真圆。
机械制造质量分析与控制讲义

机械制造质量分析与控制讲义1. 概述机械制造中的质量分析与控制是确保产品达到规定质量要求的重要环节。
质量分析和控制涉及到各个阶段的过程,包括材料选择、加工工艺、装配和检测等。
本讲义将介绍机械制造质量分析与控制的基本概念、方法和工具,以帮助读者理解和应用相关知识,提高产品质量。
2. 质量分析2.1 质量特性在机械制造中,产品的质量特性是指产品在设计、加工和使用过程中需要满足的各项要求,例如尺寸精度、表面质量、材料性能等。
通过对质量特性进行分析,可以确定各项指标的上下限,并制定相应的控制措施。
质量损失是指由于产品质量不合格而引起的各种损失,包括质量成本、客户投诉、产品退货等。
质量分析的一个重要目标是减少质量损失,提高产品质量水平。
2.3 质量分析方法质量分析方法包括统计分析、故障模式与影响分析(FMEA)、六西格玛等。
统计分析可以通过收集和分析大量数据,了解产品的质量水平和变异程度。
FMEA是通过系统性地分析设计和制造过程中的故障模式,评估故障的潜在后果,并制定相应控制措施。
六西格玛则是一种通过改进过程的方法,以达到减少缺陷和提高质量的目标。
3.1 质量控制方法质量控制方法包括工艺控制、装配控制和检测控制。
工艺控制是通过控制加工工艺参数,确保产品的尺寸和表面质量在规定范围内。
装配控制是通过控制装配工艺参数以及装配工人的技术水平,保证产品装配时的质量要求。
检测控制是通过使用各种检测手段,对产品进行检测和验证,以确保产品达到规定的质量要求。
3.2 质量控制工具质量控制工具有很多种类,其中包括流程图、控制图、散点图、直方图等。
这些工具可以帮助我们分析和控制各个环节的质量问题,快速找出问题的根本原因,并采取相应的改进措施。
4.1 PDCA循环PDCA循环是质量改进的基本方法,即计划(Plan)、执行(Do)、检查(Check)和行动(Action)的循环。
通过不断地进行PDCA循环,我们可以逐步改进产品的质量水平,提高生产效率。
机械加工质量分析与控制

实际加工时不可能也没有必要把零件做得与理想零件 完全一致,而总会有一定的偏差,即加工误差。只要这 些误差在规定的范围内,即能满足机器使用性能的要求。
二、尺寸、形状和位置精度间的关系
独立原则是处理形位公差和尺寸公差关系的基本原则, 即尺寸精度和形位精度按照使用要求分别满足;在一般 情况下,尺寸精度高,其形状和位置精度也高;通常, 零件的形状误差约占相应尺寸公差的30%~50%;位置 误差约为尺寸公差的65%~85%。
这样,上述四点工件的直径都相等,其它各点直径 误差也很小,所以车削出的工件表面接近于一个真圆。 Y2+Z2=R2+A2Sin2φ 由此可见,主轴的纯径向跳动对车削加工工件的圆 度影响很小。
图4-5 车削时纯径向跳动对加工精度的影响
②轴向窜动对车、镗削加工精度的影响
主轴的轴向窜动对内、外圆的加工精度没有影 响,但加工端面时,会使加工的端面与内外圆轴 线产生垂直度误差。 主轴每转一周,要沿轴向窜动一次,使得切出 的端面产生平面度误差(图4-6)。当加工螺纹时, 会产生螺距误差。
(扭曲)
现以卧式车床为例,说明导轨误差是怎样影响工件 的加工精度的。
(1)导轨在水平面内直线度误差的影响 当导轨在水平面内的直线度误差为△y时,引起工件在 半径方向的误差为(图4-9): △R=△y
由此可见:床身导轨在水平面内如果有直线度误差,使工件 在纵向截面和横向截面内分别产生形状误差和尺寸误差。
(3)驱动丝杠误差的产生
Z1
1
2
Z2
z1 i12 z2
2 i121
图 车螺纹的传动误差示意图
S-工件导程;T-丝杠导程;Z1~Z8-各齿轮齿数
若齿轮Z1有转角误差δ1,造成Z2的转角误差为: δ12=i12δ1 传到丝杠上的转角误差为δ1n,即: Z1
NC加工质量控制及测量 论文

江苏科技大学本科生毕业论文(设计)题目: NC质量管控及测量姓名:学院: 江苏科技大学继续教育学院专业: 机械设计制造及其自动化班级:学号:指导教师: 职称:2013 年1 月24 日江苏科技大学教务处制目录摘要 (3)关键词 (3)Abstract (3)Key words (3)绪论 (3)第一章质量要求与检测方案 (4)1.1零件 (4)1.1.1质量要求 (4)1.1.2主要管控 (4)1.2检测设备及选用 (4)1.2.1测量设备 (4)1.2.2测量仪器的选用 (4)1) 1.3检测 (5)1.3.1测量仪与测量方法 (5)第二章NC质量检测分析 (7)2.1 三坐标测量 (7)2.1.1孔、轴直径测量及误差 (7)2.1.2同轴度测量及误差 (7)2.1.3位置度测量及误差评价 (7)第三章测量精度讨论及评估 (8)3.1公差 (9)3.1.1几何测量基准和基准要素 (10)3.1.2测量不确定度和测量误差 (10)3.1.3测量工艺 (10)致谢 (11)参考文献 (11)NC质量管控及测量机械设计制造及自动化专业学生指导教师摘要:随着科学技术快速发展,CNC制造业面临着不同方面的发展要求,要最大程度地让CNC加工和精密仪器相结合以达到合格产品的目标。
本文从几个方面介绍先进制造技术,主要阐述了CNC质量控制和检测。
CNC加工从毛胚到成品的每道工序都要周密考虑,以提高机加工精度。
基于CNC加工过程中超差不可避免的特点,要通过融合多种软件及工具进行对产品测量。
本着从测量数据对质量控制,对检测关键过程进而识别并控制,实现CNC产品全面全过程全方位全要素控制,不断改善检测和服务水准,以适应全方面的要求,保证质量体系的适宜和有效性。
关键词:量具;非接触三次元;加工精度;误差;测量数据Abstract:With the rapid development of science and technology, CNC manufacturing industry is facing different aspects of the development requirements to maximize the combined in order to achieve the goal of qualified products for CNC machining and precision instruments.This paper introduces advanced manufacturing technology from several aspects, mainly on the quality control and testing of CNC. CNC machined from blanks each process to the finished product should be well thought out, in order to improve the machining accuracy. Through the integration of a variety of software and tools based on the CNC machining process super inevitable measurement products. Spirit of quality control from the measured data, and thus identify the detection of key processes and controls, CNC products a comprehensive whole process of all-round total factor control, and constantly improve the detection and service standards to meet the full requirements to ensure appropriate quality system and effectiveness.Key words:Gage; non-contact three-dimensional; machining accuracy; error; measurement data绪论:检测是以量具、仪器或专用检具对加工好零件进行检测、比较,得到误差值和判断是否符合质量要求的一个过程。
加工质量及技术要求分析

加工质量及技术要求分析
加工质量及技术要求分析是对加工产品的加工精度、表面质量、尺寸偏差、加工工艺、使用性能等进行评估和验证的过程。
其目的是确保加工产品符合客户的要求和设计要求,保证产品的质量和性能稳定可靠。
加工质量的评估主要包括以下几个方面:
1. 加工精度:衡量产品加工的精确程度,包括直线度、圆度、平行度、垂直度等。
2. 表面质量:衡量产品表面的光滑度和均匀度,包括表面粗糙度、毛刺、划痕等。
3. 尺寸偏差:测量产品的尺寸偏差,包括直径、长度、宽度、高度等。
4. 加工工艺:评估产品的加工工艺是否符合要求,包括加工流程、加工设备、加工工具等。
5. 使用性能:评估产品的使用性能是否符合设计要求,包括承载能力、耐久性、稳定性等。
为了保证加工质量,需要采取一系列的技术手段,如精密加工设备、高精度的测量仪器、科学严谨的加工工艺以及严格的质量控制流程等。
同时,还需要不断改进和提高加工技术,并加强对加工质量的质量监控和质量管理,不断提高产品加工水平与竞争力。
- 1、下载文档前请自行甄别文档内容的完整性,平台不提供额外的编辑、内容补充、找答案等附加服务。
- 2、"仅部分预览"的文档,不可在线预览部分如存在完整性等问题,可反馈申请退款(可完整预览的文档不适用该条件!)。
- 3、如文档侵犯您的权益,请联系客服反馈,我们会尽快为您处理(人工客服工作时间:9:00-18:30)。
2. 机床导轨误差 导轨在水平面内的直线度、导轨在垂直面内的直 线度和双导轨间在垂直方向的平行度(扭曲)。 导轨在水平面内的直线度误差: 导轨在水平面内的直线度误差:卧式车床导轨在水平 面内的直线度误差△1将直接反映在被加工工件表面 的法线方向(加工误差的敏感方向)上,对加工精 度的影响最大 。 误差的敏感方向: 加工误差对加工精度影响最 大的方向,为误差的敏感方向。 例如:车削外 圆柱面,加工误差敏感方向为外圆的直径方向。
3.机床传动链误差 3.机床传动链误差 传动链误差是指机床内联系传动链始末两端传动 传动链误差 元件间相对运动的误差。 例如:车削螺纹的加工,主轴与刀架的相对运动 关系不能严格保证时,将直接影响螺距的精度。 减少传动链传动误差的措施: 减少传动链传动误差的措施 1) 减少传动件的数目,缩短传动链。传动元件 越少,传动累积误差就越小,传动精度就越高。 2) 提高传动元件精度和采用校正装置
误差复映规律:当毛坯有形状误差或位置误差时, 误差复映规律:当毛坯有形状误差或位置误差时,加工 后工件仍会有同类的加工误差。 后工件仍会有同类的加工误差。但每次走刀后工误差将逐步 减少。 减少。 若每次走刀复映系数为K1、 K2、 …、Kn,则K总=
…
K 1 . K2
Kn
动画演示
3.减少工艺系统受力变形的途径 1)提高机床零部件间结合表面的质量 2)对部件运动面预加负载 3)提高工件定位基面的精度和减少定位基面的表面 粗糙度 4)使用辅助支承提高工艺系统刚度 5)采用合理安装夹紧方式减少装夹变形
3.获得位置精度的主要方法 一次装夹获得法:零件表面的位置精度在一次安装 一次装夹获得法: 中,由刀具相对于工件的成形运动位置关系保证。 多次装夹获得法:通过刀具相对工件的成形运动与 多次装夹获得法 工件定位基准面之间的位置关系来保证零件表面 的位置精度。
2.2 影响机械加工精度的工艺因素
2.2.1 方法误差
ΔR
ΔZ
d R R+ Δ R 导轨垂直面直线度
ΔZ
垂直平面
图2-4 导轨垂直面内直线度误差
前后导轨存在平行度误差(扭曲) 前后导轨存在平行度误差(扭曲): 刀架运动时会产生 摆动,刀尖的运动轨迹 是一条空间曲线,使工 件产生形状误差。由图 可见,当前后导轨有了 扭曲误差△3之后,由 几何关系可求得△R≈ (H/B)△3。一般车床 的H/B≈2/3,外圆磨床 的H/B≈1,车床和外圆 磨床前后导轨的平行度 误差对加工精度的影响 很大。
2.2.3 夹具误差和磨损
夹具的作用是使工件相对于刀具和机床具有正 确的位置,因此夹具的制造误差对工件的加工精 度(特别是位置精度)有很大影响。一般夹具的 制造公差应小于被加工工件的公差。 夹具误差包括: (1)夹具各元件之间的位置误差; (2)夹具中各定位元件和导向元件的磨损; (3)夹具在机床上的安装误差。
毛坯误差复映现象 : 若毛Fra bibliotek有椭圆形状误差。让刀具调整到图上 (P48)双点划线位置,在毛坯椭圆长轴方向上的 背吃刀量为αp1,短轴方向上的背吃刀量为αp2。 由于背吃刀量不同,切削力不同,工艺系统产生的 让刀变形也不同,对应于αp1产生的让刀为y1,对 应于αp2产生的让刀为y2,故加工出来的工件B仍然 存在椭圆形状误差。由于毛坯存在圆度误差△毛= αp1-αp2,因而引起了工件的圆度误差△工=y1-y2, 且△毛愈大,△工愈大,这种现象称为加工过程中 的毛坯误差复映现象。△工与△毛之比值K称为误 差复映系数,它是误差复映程度的度量。
第二章 加工精度分析
2.1基本概念
2.1.1精度的基本含义
机械加工精度 指零件加工后,其几何参数(尺寸、形状和各表面间相互位 置)与理想几何参数的符合程度。 加工误差 指零件加工后实际几何参数与理想几何参数的偏差。 加工误差越小,加工精度越高。 机械加工精度包括 尺寸精度:加工后零件的实际尺寸与零件理想尺寸相符的程度。 形状精度:加工后零件的实际形状与零件理想形状相符的程度。 位置精度:加工后零件的实际位置与零件理想位置相符的程度。
变形。 例如:机床主轴前、后端受热不均,将造成主轴 抬高,并倾斜。
5.减少工艺系统热变形的措施:减少发热和隔热;改善
散热条件;均衡温度场;改进机床结构 ;加快温度场的 平衡 ;控制环境温度。
导轨磨床热变形
立式铣床受热变形形态 外圆磨床受热变形形态
合理设计机床结构
2.2.7 工件安装、调整和测量的误差
方法误差(原理误差):指采用了近似的 成形运动或近似的刀刃轮廓进行加工而产生 的误差,一般多为形状误差。如图2-1 在实际生产中,采用理论上完全准确的 方法进行加工往往会使机床的结构复杂,刀 具的制造困难,加工的效率降低。而采用近 似加工方法,则常常可使工艺装备简单化, 生产成本降低,故在满足产品精度要求的前 提下,原理误差的存在是允许的 。
2.2.5 工艺系统受力变形
1.基本概念
机械加工工艺系统在切削力、夹紧力、惯性力、重力、 传动力等的作用下,会产生相应的变形,从而破坏了刀具 和工件之间的正确的相对位置,使工件的加工精度下 降。
如图a示,车细长轴时,工件在切削力的作用下会发生变 形,使加工出的轴出现中间粗两头细的情况;又如在内圆 磨床上进行切入式磨孔时,图b,由于内圆磨头轴比较细, 磨削时因磨头轴受力变形,而使工件孔呈锥形。
2) 定尺寸刀具法:零件的尺寸精度是由具有一定尺寸的刀 调整法: 3) 调整法:按试切好的工件或标准样件或对刀装置等,调
数控法: 4) 数控法:使用一定的装置(自动测量或数字控制),在工
件达到要求尺寸时,自动停止加工。
2.获得形状精度的主要方法 仿形法:用特定形状的刀具切削工件,工件表面形状 仿形法 和精度完全取决于刀具的制造精度。如:所谓“电 子配钥匙” 成形运动法:使刀具相对于工件做有规律的切削成形 成形运动法 运动,从而获得所要求的零件表面形状。如:滚齿、 车螺纹 非成形运动法: 非成形运动法:通过对加工表面形状的检测,由工人 对其进行相应的修整加工,以获得所要求的形状精 度。尽管非成形运动法是获得零件表面形状精度的 最原始方法,效率相对比较低 。
工艺系统刚度的倒数等于其各组成部分刚度的倒数和。
工艺系统刚度对加工精度的影响主要有以下几种情况
• 由于机床刚度变化引起的误差 • 由于切削力变化引起的误差 加工过程中,由于工件的加工余量发生变化工件材质不均等 因素引起的切削力变化,使工艺系统变形发生变化,从而产 生加工误差。 • 由于夹紧变形引起的误差 工件在装夹时,由于工件刚度较低或夹紧力着力点不当, 会使工件产生相应的变形,造成加工误差。 • 其它作用力的影响 传动力与惯性力
2.1.2 获得规定加工精度的方法 1.尺寸精度的获得方法 试切法: 1) 试切法 即试切--测量--再试切--直至测量结果达到图
纸给定要求的方法 。试切法的效率低,对操作者的技术水 平要求较高,多用于单件、小批生产或高精度零件的加工。 具或组合刀具保证的,常用于孔、槽面、成形表面的加工。 (用刀具的相应尺寸来保证加工表面的尺寸 ) 整刀具相对于工件加工表面的位置,并在加工过程中保持 这一位置,从而获得零件所要求的尺寸精度。调整法多用 于成批、大量生产。
1.工件安装误差 2.调整误差 3.测量误差
2.2.8 工件内应力引起的 变形
• 残余应力 内应力):没有外力 残余应力(内应力 内应力 作用而存在于零件内部的应力 • 产生 产生:在热处理工序中由于工件 壁厚不均匀、冷却不均、金相组 织的转变等原因,使工件产生内 应力。
• 减小内应力变形误差的途径 1.改进零件结构——设计零件时,尽量做到壁厚均匀, 结构对称,以减少内应力的产生。 2.增设消除内应力的热处理工序 时效 自然时效:将毛坯或工件长期放在室内或室外, 使其受气温变化的影响,自然松弛和变形,以减小 内应力。 人工时效:将铸件加热到550~650℃进行去应力 退火,它比自然时效节省时间,残余应力去除较为 彻底。 3.合理安排工艺过程——粗加工和精加工宜分阶段进 行,使工件在粗加工后有一定的时间来松弛内应力。
图 例
镗杆变形
加工后成鞍形
夹紧变形
力作力用位置
刚度:物体抵抗使其变形的能力 J=F/Y F:外力 Y:外力作用方向上的变形量 静刚度:引起弹性变形的外力是一个大小、方向和 作用点都不变的静力,由此力和变形决定的刚度 称为静刚度。静刚度影响加工精度。 动刚度:引起弹性变形的外力是一个交变力,则力 的变形所决定的刚度称为动刚度。动刚度影响表 面质量。 2. 工艺系统刚度及其对加工精度的影响 在机械加工过程中,机床、夹具、刀具和工件 在切削力作用下,都将分别产生变形Y机、Y夹、Y刀、 Y工,致使刀具和被加工表面的相对位置发生变化, 使工件产生加工误差。
2.3 加工误差分析
• 2.3.1 加工误差的性质
• 按其统计性质的不同可分为系统误差和随机误差两大类。 按其统计性质的不同可分为系统误差和随机误差两大类。 •(一)系统误差 ( •1、常值系统误差 1 •加工的一批零件中,所产生的大小和方向都保持不变的误差称 加工的一批零件中, 加工的一批零件中 为常值系统误差。例如加工原理误差、机床、夹具、 为常值系统误差。例如加工原理误差、机床、夹具、刀具的制 造误差及工艺系统受力变形等都属于常值系统误差。 造误差及工艺系统受力变形等都属于常值系统误差。 •2、变值系统误差 2 •加工一批零件中,所产生的大小和方向都按一定规律变化的误 加工一批零件中, 加工一批零件中 称为变值系统误差。如机床、夹具、 差,称为变值系统误差。如机床、夹具、刀具等在热平衡前的 热变形,刀具的磨损等都属于变值系统误差。 热变形,刀具的磨损等都属于变值系统误差。 • (二)随机误差 • 加工一批零件中,所产生的大小和方向不同且无规律变化的 加工一批零件中, 误差,称为随机误差。如毛坯的尺寸误差,定位、夹紧误差, 误差,称为随机误差。如毛坯的尺寸误差,定位、夹紧误差, 残余应力引起的加工误差。 残余应力引起的加工误差。