最新实验二加工精度的统计分析
加工误差统计分析的常规方法(精)

实验二 加工误差统计分析的常规方法机械加工要保证产品质量,就要保证加工精度。
要保证加工精度就要确定误差,而确定误差主要有统计和分析计算法。
统计法又可分为分布曲线法和点图法两种。
一、 实验目的及要求:1.通过实验进一步了解:(1)大批量生产情况下,零件的统计特性及引起尺寸波动的原因。
(2)系统性误差和随机性误差的特性及其对零件加工精度的影响。
2.通过实验进一步掌握:⑴分布曲线法和点图分析法的具体方法,并应用其方法分析零件加工中出现加工误差的主要原因,并想出解决的措施。
⑵掌握分析和解决加工误差问题的四个阶段(调查、分析、测试、验证)的具体方法。
3.要求:⑴测试尺寸精度要求为0.001mm 。
⑵ 绘制分布曲线和X —R 图均用方格纸。
⑶书写整洁,计算准确,绘图精心。
二、 实验原理:由于机械加工中存在着偶然性和系统性误差的综合影响,致使单个零件的加工误差不断变化,故不能依据单个工件误差推断整批工件误差情况。
统计分析法就是以对生产现场的观察和对一定数量的工件测量所得结果为基础,用数理统计方法进行处理。
以确定由于全部作用因素的共同影响而得到的尺寸分布范围,研究误差的性质及其影响,评定加工精度。
1.对某一工序在一次调整下加工的一批零件,测量它们加工的实际尺寸。
再按尺寸大小将整批零件分布若干组,算出每组零件(频数)及其占全部零件的百分比(频率)。
以各组尺寸和频率(频数)为坐标可作出频率直方图。
当零件数目越多,尺寸间隔取得越小时,尺寸分布的折线将接近为曲线,称为实验尺寸分步曲线。
理论和实验证明,在调整好的机床上加工,如果没有突出的因素(如刀具磨损、热变形等)在起作用,如加工情况正常,则一批工件的实际尺寸分布符合正态分布规律,正态分布曲线方程式为: 2)(21)(21δμπδφ-=X e X式中:X – 工件实际尺寸;δ- 均方根偏差;μ- 全部零件尺寸的平均值和分散中心;μ和δ可根据实验测得的结果计算:n Xi ∑=μ n Xi )(μδ-∑=正态分布曲线反映了零件的实际尺寸大部分集中在平均尺寸x 的周围。
实训报告零件加工精度分析

一、摘要本次实训旨在通过对零件加工过程的分析,探讨影响零件加工精度的因素,并提出相应的改进措施。
通过对零件加工工艺、加工设备、加工参数等方面的深入研究,本文对提高零件加工精度提出了一些有益的建议。
二、引言零件加工精度是衡量机械产品质量的重要指标。
高精度的零件可以保证产品的性能、可靠性和使用寿命。
然而,在实际生产过程中,由于各种因素的影响,零件加工精度往往难以达到预期目标。
因此,分析影响零件加工精度的因素,并提出相应的改进措施,对于提高零件加工精度具有重要意义。
三、零件加工精度分析1. 材料选择材料选择是影响零件加工精度的关键因素之一。
不同材料的物理性质、机械性能和加工性能对零件加工精度产生较大影响。
(1)硬度:硬度高的材料在加工过程中更容易产生变形和磨损,从而影响加工精度。
(2)塑性:塑性大的材料在加工过程中更容易产生加工硬化,导致加工精度降低。
(3)热膨胀系数:热膨胀系数大的材料在加工过程中更容易产生热变形,影响加工精度。
2. 加工工艺加工工艺是影响零件加工精度的直接因素。
(1)加工方法:不同的加工方法对零件加工精度产生不同的影响。
例如,车削加工精度高于铣削加工。
(2)加工顺序:加工顺序对零件加工精度有较大影响。
一般来说,先加工精度要求高的部位,再加工精度要求低的部位。
(3)加工参数:加工参数包括切削速度、进给量、切削深度等。
这些参数对零件加工精度产生直接的影响。
3. 加工设备加工设备是保证零件加工精度的物质基础。
(1)机床精度:机床精度越高,零件加工精度越高。
(2)刀具精度:刀具精度对零件加工精度有较大影响。
刀具磨损或损坏会导致加工精度降低。
(3)测量设备:测量设备精度越高,对零件加工精度的控制越准确。
4. 操作人员操作人员的技术水平、熟练程度和责任心对零件加工精度产生一定影响。
(1)技术水平:技术水平高的操作人员能够更好地掌握加工工艺和操作要领,提高零件加工精度。
(2)熟练程度:熟练程度高的操作人员能够更好地控制加工过程,降低误差。
加工误差统计分析实验报告

加工误差统计分析实验报告加工误差统计分析实验报告引言:加工误差是指在工业生产过程中,由于各种原因导致产品尺寸、形状和表面质量与设计要求之间的差异。
加工误差的控制对于保证产品质量、提高生产效率和降低成本具有重要意义。
本实验旨在通过对加工误差进行统计分析,探讨误差来源及其影响因素,为工业生产过程中的质量控制提供参考依据。
实验设计:本实验选取了一台数控铣床进行实验,以铣削加工尺寸为研究对象。
首先,我们选择了一种常见的零件,对其进行加工。
然后,通过测量加工后的尺寸与设计要求进行对比,得到加工误差数据。
最后,我们对这些数据进行统计分析,探究加工误差的分布规律和影响因素。
实验过程:1. 加工准备:选择合适的刀具、夹具和工艺参数,进行加工准备工作。
2. 加工操作:按照设计要求进行铣削加工,并记录下每次加工后的尺寸数据。
3. 尺寸测量:使用测量工具对加工后的零件进行尺寸测量,并记录测量结果。
4. 数据整理:将测量得到的数据整理成表格,方便后续的统计分析。
统计分析:1. 加工误差分布:通过绘制加工误差的频率分布直方图,我们可以观察到误差值的分布情况。
通常情况下,加工误差符合正态分布,但也可能存在其他分布形式,例如偏态分布或双峰分布。
通过分析分布形式,可以判断加工过程中是否存在特殊的误差来源。
2. 加工误差与加工参数的关系:通过对加工误差与加工参数(如切削速度、进给速度等)进行相关性分析,可以了解不同参数对加工误差的影响程度。
这有助于我们确定合适的工艺参数范围,以减小加工误差。
3. 加工误差与刀具磨损的关系:刀具磨损是导致加工误差增大的重要因素之一。
通过对加工误差与刀具磨损程度进行相关性分析,可以判断刀具寿命与加工误差之间的关系,进而合理安排刀具更换周期,以保证加工质量。
4. 加工误差与工件材料的关系:不同材料的加工性能不同,可能导致加工误差的差异。
通过对加工误差与工件材料进行相关性分析,可以了解不同材料对加工误差的影响程度,为材料选择和工艺优化提供依据。
实验二 加工误差统计分析实验

实验二 加工误差统计分析实验一、实验目的1.培养学生综合运用数理统计、计算机技术、加工精度分析等方面知识的能力。
2.熟练掌握在实际生产中工艺过程精度统计分析的内容和方法。
3.学会分析在加工过程中各种误差因素对加工精度的影响。
4.学会用分布图法计算零件废品率和合格品率和点图分析法。
二、实验设备及工件1.普通车床2.检具和测量系统3.工件4.计算机三、实验原理1、工艺过程的分布图分析法(1)样本容量n 的确定 样本容量不能太大或太小。
本实验取n=100。
(2)样本数据的测量 使用检测仪器实测100个试件尺寸,并按加工顺序纪录在数据表中。
(3)异常数据的剔除当工件测量数据服从正态分布时,|x k -x |>3σ,则x k 为异常数据,应于以剔除。
(4)实际分布图的绘制a .确定尺寸间隔数j 尺寸间隔数(尺寸分组数)j 不可随意确定。
一般可参考下表选取。
b .确定尺寸间隔大小(区间宽度)Δx 只要找到样本中个体的最大值x max 和x min 即可算得的jx x x min max -=∆ 为了使x max 和x min 皆落在尺寸间隔中,在坐标轴上取j=j+1个点。
c .画实际分布图 列出测量数据的计算表格如下表所示。
画图时,实际频数值应在尺寸区间中点的纵坐标上。
计算表格(5)理论分布图的绘制将以概率密度为纵坐标的理论分布图转化成以频数为纵坐标的理论分布图。
正态分布曲线的理论频数曲线最大值和拐点处的理论频数值分别为:xn xn y f ∆=∆='σ14.0max maxxn xn y f ∆=∆='σσσ124.0 理论频数曲线最大值的横坐标为x ;两个拐点的横坐标分别为(σ±x );分散范围为(σ3+x )和(σ3-x )。
根据这些数据,就可以画出以频数为纵坐标的理论分布曲线。
(6)工艺过程的分布图分析a .判断加工误差性质 如果通过检验,确认样本是服从正态分布的,就可以认为工艺过程中变值系统性误差很小(或不显著);如果工件尺寸误差的实际分布中心x 与公差带中心有偏移ε,表明工艺过程中有常值系统性误差存在。
加工误差统计分析实验报告

加工误差统计分析实验报告一、实验目的通过统计分析加工误差数据,探究加工工艺对产品加工误差的影响,并提出相应的改进措施。
二、实验原理加工误差是指产品实际尺寸与设计尺寸之间的差异,主要受到原材料、加工设备、操作工艺等因素的影响。
统计分析可以通过数学模型和数据处理方法,定量地描述和评估加工误差的分布情况,为加工工艺改进提供依据。
三、实验步骤1.随机选择一批相同产品进行加工,保持其他加工条件不变。
2.测量每个产品的实际尺寸,记录数据并整理成表格。
3.统计每组数据的平均值、方差以及标准差。
4.构建加工误差的概率分布函数,通过正态性检验和偏度、峰度检验判断数据是否符合正态分布。
5.进行加工误差数据的t检验,分析不同因素对加工误差的影响程度。
四、实验数据产品编号,实际尺寸 (mm)--------,--------------1,10.012,10.02...,...100,10.08五、数据处理及分析1.计算平均值、方差和标准差:平均值μ=(10.01+10.02+...+10.08)/100=10.05方差s^2=((10.01-10.05)^2+(10.02-10.05)^2+...+(10.08-10.05)^2)/99标准差s=√s^22.正态性检验:根据实验数据计算样本均值和样本标准差,绘制加工误差的概率密度分布曲线。
通过观察曲线形状以及进行偏度、峰度检验,判断数据是否符合正态分布。
3.t检验:根据产品加工误差数据,进行t检验来分析不同因素对加工误差的影响程度。
比如,可以比较不同机器加工出的产品误差是否有显著性差异。
六、实验结果分析1.样本加工误差符合正态分布,数据较为集中,无明显偏离。
2.通过t检验发现:不同机器加工出的产品误差差异不显著,说明机器之间的加工稳定性较好。
3.根据样本数据及数据处理结果,可以得到加工误差的基本分布情况,对加工工艺的控制和改进提供依据。
例如,可以调整机器参数、改进操作工艺等。
加工误差统计分析实验报告

实验价值:为企业提供有效的 质量控制方法和改进措施
添加 标题
加工误差的定义:加工误差是指零件加 工后实际几何参数(尺寸、形状和位置) 与理想几何参数的偏离程度。
添加 标题
加工误差的分类:根据其产生的原因和 性质,加工误差可分为随机误差、系统 误差和粗大误差三类。
添加 标题
随机误差:由于加工过程ຫໍສະໝຸດ 各种因素的 影响,使加工误差的大小和方向随机变 化,具有单向性、对称性和抵偿性。
加工误差的影响程度:对产 品质量、生产效率、成本等 方面的影响
加工误差产生的原因:机床、 刀具、夹具、测量仪器等因 素导致的误差
加工误差的分类:系统误差、 随机误差、粗大误差等
加工误差的检测方法:直接 测量法、间接测量法、比较
测量法等
提高加工精度:采用更精确的加工设备和工艺,减少误差 加强过程控制:对加工过程进行严格监控,确保每个环节的准确性 引入先进技术:采用先进的误差检测和校正技术,提高加工精度 加强员工培训:提高员工对加工误差的认识和技能水平,减少人为因素造成的误差
,a click to unlimited possibilities
01 实 验 目 的 02 实 验 原 理 03 实 验 步 骤 04 实 验 结 果 05 实 验 结 论 06 参 考 文 献
实验目的:分析加工误差的来 源和影响因素
实验意义:提高加工精度,降 低误差,提高产品质量
实验目标:确定加工误差的分 布规律和变化趋势
采集方法:直接 测量、间接测量、 组合测量
采集工具:测量 仪器、传感器、 计算机等
数据处理:对采 集到的数据进行 预处理、分析、 整理等操作
数据收集:通过实验测量获得数 据
数据处理:对数据进行预处理和 变换
机械加工精度统计分析实验报告

机械加工精度统计分析实验报告本实验旨在通过统计分析机械加工的精度,探究机械加工过程中不同因素对精度的影响,为提高机械加工精度提供科学依据。
一、实验原理机械加工精度的影响因素非常多,但可以归纳为以下几个方面:(1)机床精度:机床本身的精度、刚性和稳定性对精度有重要影响;(2)刀具:刀具的质量和几何参数对精度有直接影响;(3)工件材料和形状:不同材料和形状的工件对加工精度有一定的要求;(4)加工工艺和操作者技术水平:包括切削参数、刀具与工件的相对位置关系、刀具使用寿命等等。
二、实验设备和实验材料(1)机床:普通数控加工中心(2)刀具:含钨合金刀片、硬质合金刀片、PVD涂层刀片(3)工件材料:铝合金(4)测量仪器:三坐标测量仪、千分尺三、实验步骤(1)将铝合金工件装夹在机床上,并使用不同品牌和型号的刀具进行加工,记录加工参数。
(2)将加工后的工件放在三坐标测量仪上进行精度测量和分析。
(3)记录每组数据,并根据不同刀具和加工参数进行分析、比较。
四、实验结果分析本次实验所得到的加工精度数据如下表:| 刀具类型 | 刀具品牌 | 加工参数 | 加工精度(mm) ||----------|----------|---------|----------------|| 钨合金刀片 | 刀片A | 速度18m/min,进给量0.2mm/r,切深0.5mm | 0.02 || 钨合金刀片 | 刀片B | 速度15m/min,进给量0.1mm/r,切深0.3mm | 0.01 | | 硬质合金刀片 | 刀片A | 速度20m/min,进给量0.2mm/r,切深0.5mm | 0.015 | | 硬质合金刀片 | 刀片B | 速度22m/min,进给量0.2mm/r,切深0.4mm | 0.018 | | PVD涂层刀片 | 刀片A | 速度25m/min,进给量0.3mm/r,切深0.6mm | 0.015 | | PVD涂层刀片 | 刀片B | 速度20m/min,进给量0.2mm/r,切深0.5mm | 0.013 |从表中可以看出,不同刀具、不同品牌和型号的刀具加工同一种材料的精度差异很明显。
加工误差的统计分析实验报告

加工误差的统计分析实验报告
《加工误差的统计分析实验报告》
在工业生产中,加工误差是一个常见的问题,它会直接影响产品的质量和性能。
为了解决这一问题,我们进行了一项加工误差的统计分析实验,以期找到有效
的控制和改善方法。
实验过程中,我们选择了一批相同规格的零件进行加工,并对加工过程中的误
差进行了详细记录和分析。
首先,我们对零件的尺寸进行了测量,并得到了一
系列的数据。
然后,我们使用统计学方法对这些数据进行了处理和分析,得出
了一些有价值的结论。
通过实验,我们发现加工误差的分布呈现出一定的规律性,大部分误差集中在
一个较小的范围内,但也存在一些异常值。
此外,我们还发现了一些可能导致
加工误差的原因,比如加工设备的精度、操作人员的技术水平等。
基于实验结果,我们提出了一些改善措施。
首先,我们建议对加工设备进行定
期检修和维护,以保证其加工精度。
其次,我们还提出了加强操作人员培训和
技术指导的建议,以提高其加工技术水平。
最后,我们还计划对加工工艺进行
优化,以减小加工误差的发生概率。
总的来说,通过这次实验,我们对加工误差有了更深入的了解,并提出了一些
有效的改善措施。
我们相信,通过这些措施的实施,我们能够有效地控制和减
小加工误差,提高产品的质量和性能。
希望我们的实验报告能够对其他相关领
域的研究和实践提供一定的借鉴和参考。
加工误差统计分析的常规方法(精)

实验二 加工误差统计分析的常规方法机械加工要保证产品质量,就要保证加工精度。
要保证加工精度就要确定误差,而确定误差主要有统计和分析计算法。
统计法又可分为分布曲线法和点图法两种。
一、 实验目的及要求:1.通过实验进一步了解:(1)大批量生产情况下,零件的统计特性及引起尺寸波动的原因。
(2)系统性误差和随机性误差的特性及其对零件加工精度的影响。
2.通过实验进一步掌握:⑴分布曲线法和点图分析法的具体方法,并应用其方法分析零件加工中出现加工误差的主要原因,并想出解决的措施。
⑵掌握分析和解决加工误差问题的四个阶段(调查、分析、测试、验证)的具体方法。
3.要求:⑴测试尺寸精度要求为0.001mm 。
⑵ 绘制分布曲线和X —R 图均用方格纸。
⑶书写整洁,计算准确,绘图精心。
二、 实验原理:由于机械加工中存在着偶然性和系统性误差的综合影响,致使单个零件的加工误差不断变化,故不能依据单个工件误差推断整批工件误差情况。
统计分析法就是以对生产现场的观察和对一定数量的工件测量所得结果为基础,用数理统计方法进行处理。
以确定由于全部作用因素的共同影响而得到的尺寸分布范围,研究误差的性质及其影响,评定加工精度。
1.对某一工序在一次调整下加工的一批零件,测量它们加工的实际尺寸。
再按尺寸大小将整批零件分布若干组,算出每组零件(频数)及其占全部零件的百分比(频率)。
以各组尺寸和频率(频数)为坐标可作出频率直方图。
当零件数目越多,尺寸间隔取得越小时,尺寸分布的折线将接近为曲线,称为实验尺寸分步曲线。
理论和实验证明,在调整好的机床上加工,如果没有突出的因素(如刀具磨损、热变形等)在起作用,如加工情况正常,则一批工件的实际尺寸分布符合正态分布规律,正态分布曲线方程式为: 2)(21)(21δμπδφ-=X e X式中:X – 工件实际尺寸;δ- 均方根偏差;μ- 全部零件尺寸的平均值和分散中心;μ和δ可根据实验测得的结果计算:n Xi ∑=μ n Xi )(μδ-∑=正态分布曲线反映了零件的实际尺寸大部分集中在平均尺寸x 的周围。
实验2 加工误差的统计分析

实验2 加工误差的统计分析1.实验目的与要求1.1 通过本实验使学生掌握加工误差统计分析的基本原理和方法;运用此方法综合分析零件加工尺寸的变化规律。
1.2 学习设计实验线路,正确选择与使用有关测量装置,测量工具和仪器。
1.3 正确地进行采样和运算,并绘制点图,实验分布曲线图。
1.4 绘制R x -质量控制图。
1.5 确定本工序的工序能力系数p C ,(也称精度系数),并分析本工序加工的稳定性。
2.基本原理2.1 加工误差及其变化规律由各种工艺因素所产生的加工误差可分为两大类,即系统性误差和随机性误差。
系统性误差主要有因调整因素引起的常值系统误差Δ常和因刀具磨损、工艺系统热变形等引起的有规律变化趋势的变值系统性误差Δ变。
随机性误差Δ随是由于尺寸的分散造成的,亦称瞬时尺寸分散。
整批零件尺寸的分散还应包含有规律变化着的系统性误差。
在加工过程中,随机性误差和系统性误差是同时存在,而且混在一起的。
因此,生产实际中,常用统计分析法来研究加工精度问题。
2.2 分布曲线法 2.2.1 理论分布曲线大量的实验、统计分析表明:当一批工件总数足够多时,加工中的误差是由相互独立的随机因素引起的,而且这些误差因素中又都没有任何优势的倾向,则其分布是服从正态分布的。
也就是说,随机误差分布曲线,是正态分布曲线,它是描述正态分布密度函数的图形。
理论正态分布曲线是连续的、对称的曲线。
如图3.1所示,它的方程式如下:⎥⎥⎦⎤⎢⎢⎣⎡⎪⎭⎫ ⎝⎛--=221ex p 21σμπσx y式中,y ——分布的概率密度;x ——自变数,它属于某一组随机变数的集合X ;μ——随机变数总体的均值(分散中心): ∑==Ni ixN11μ N 为样本总数σ——均方差:∑=-=Ni i x N12)(1μσ 生产实际中,加工误差统计分析时,可得x =μ,x 为工件尺寸分布平均值;N 为工件的数量;i x 为工件尺寸。
图3.1 正态分布曲线如果改变参数x =μ(σ保持不变),则曲线沿x 轴平移而不改变其形状,这说明μ是表征分布曲线位置的参数。
加工误差的统计分析实验报告

加工误差的统计分析实验报告加工误差的统计分析实验报告引言:加工误差是指在制造过程中,由于各种原因导致产品尺寸、形状或性能与设计要求存在差异的现象。
在现代制造业中,加工误差是无法完全避免的,但通过统计分析可以帮助我们了解误差的分布规律,从而采取相应的措施来提高产品的质量和可靠性。
本实验旨在通过对一批产品的加工误差进行统计分析,探究误差的分布特征和影响因素,为制造过程的优化提供依据。
实验方法:本实验选取了一批相同规格的螺钉作为研究对象,通过测量螺钉的直径来评估加工误差。
实验过程中,我们首先随机抽取了100个样本,然后使用数显卡尺对每个样本进行测量,记录下测量结果。
为了确保实验的可靠性,我们对每个样本进行了三次测量,并取平均值作为最终的测量结果。
实验结果:经过测量和数据处理,我们得到了100个样本的直径测量结果。
将这些数据进行统计分析,得到了以下结果:1. 均值分析:通过计算样本的平均值,我们得到了螺钉直径的平均加工误差为0.02mm。
这表明整个样本的加工误差整体上偏向于偏小。
2. 方差分析:通过计算样本的方差,我们得到了螺钉直径的加工误差的方差为0.005mm²。
方差是衡量数据分散程度的指标,方差越大,则加工误差的分布越广泛。
在本实验中,方差较小,说明螺钉的加工误差相对稳定。
3. 正态性检验:为了判断螺钉直径的加工误差是否符合正态分布,我们进行了正态性检验。
通过绘制直方图和Q-Q图,并进行Shapiro-Wilk检验,我们发现螺钉直径的加工误差符合正态分布。
这对于后续的数据分析和处理具有重要意义。
讨论与结论:通过对螺钉直径加工误差的统计分析,我们可以得出以下结论:1. 螺钉直径的加工误差整体上偏向于偏小。
这可能是由于制造过程中对尺寸的控制较为严格,导致加工误差偏向于小的一侧。
2. 螺钉直径的加工误差相对稳定。
方差较小,说明加工误差的分布相对集中,制造过程的稳定性较高。
3. 螺钉直径的加工误差符合正态分布。
加工精度实验报告

加工精度实验报告摘要本实验通过测量加工零件的尺寸精度和形状精度,评估了加工设备的加工精度,并探讨了影响加工精度的因素。
实验结果表明,加工设备的加工精度受到多种因素的影响,如机床本身的精度、刀具的磨损和切削参数的选择等。
为了获得更高的加工精度,需要对加工设备进行维护和调整,并优化加工工艺参数。
引言加工精度是指加工零件的尺寸和形状与设计要求的误差。
在现代制造业中,加工精度是一个非常重要的指标,因为它影响着产品的质量、性能和可靠性。
因此,对加工精度进行评估和改善是制造业中不可避免的问题。
为了评估加工设备的加工精度,本实验采用了三种不同的测量方法,包括千分尺测量、光学测量和三坐标测量。
通过对不同加工设备加工的样品进行测量,比较了它们的加工精度,并探讨了影响加工精度的因素。
实验方法1.千分尺测量千分尺是一种常用的测量工具,用于测量小尺寸物体的精度。
在本实验中,使用千分尺测量了加工零件的尺寸精度。
具体步骤如下:(1)将千分尺放置在加工零件上,并调整刻度使其与零件表面接触。
(2)读取千分尺的刻度,并记录下来。
(3)对同一位置进行多次测量,计算平均值并计算误差。
2.光学测量光学测量是一种非接触式测量方法,用于测量加工零件的形状精度。
在本实验中,使用了光学测量仪对加工零件进行测量。
具体步骤如下:(1)将加工零件放置在光学测量仪上,并调整其位置和方向。
(2)启动光学测量仪,并进行校准。
(3)对加工零件进行扫描,并记录下扫描数据。
(4)对扫描数据进行处理,计算出加工零件的形状误差。
3.三坐标测量三坐标测量是一种高精度测量方法,用于测量加工零件的尺寸和形状精度。
在本实验中,使用了三坐标测量仪对加工零件进行测量。
具体步骤如下:(1)将加工零件放置在三坐标测量仪上,并调整其位置和方向。
(2)启动三坐标测量仪,并进行校准。
(3)对加工零件进行扫描,并记录下扫描数据。
(4)对扫描数据进行处理,计算出加工零件的尺寸和形状误差。
实验结果本实验通过对不同加工设备加工的样品进行测量,比较了它们的加工精度。
加工精度实验报告

加工精度实验报告摘要:本文旨在探究加工精度对产品质量的影响,通过对比实验,结合理论分析,得出了一些有价值的结论。
实验结果表明,加工精度对产品的尺寸精度、表面质量和机械性能都有着重要的影响。
因此,在实际生产中,应该注重加工精度控制,以提高产品质量和竞争力。
关键词:加工精度;尺寸精度;表面质量;机械性能引言:随着现代工业的发展,各种机械设备和工具的精度要求越来越高。
在生产加工中,加工精度是影响产品质量的重要因素之一。
本文通过实验探究加工精度对产品质量的影响,为提高产品质量和竞争力提供借鉴。
实验设计:本实验选取了两种不同的加工方式,分别为高速铣削和传统铣削。
在同样的工艺参数和刀具条件下,分别对不同加工方式下的尺寸精度、表面质量和机械性能进行了比较分析。
实验结果:(1)尺寸精度通过对比实验结果发现,高速铣削的尺寸精度要明显优于传统铣削。
高速铣削的尺寸误差范围更小,尺寸精度更高。
(2)表面质量高速铣削的表面质量也要优于传统铣削。
高速铣削的表面光洁度更高,表面粗糙度更小,表面有利于涂装和喷漆。
(3)机械性能在机械性能方面,高速铣削的材料强度和韧性要更好。
高速铣削的材料在削除时产生的应力更小,没有产生过多的热量,从而使得材料的韧性和强度得到保持。
分析讨论:从实验结果可以看出,加工精度对产品质量有着重要的影响。
高精度加工方式可以有效地提高产品的尺寸精度、表面质量和机械性能。
因此,在实际生产中,应该注重加工精度控制,以提高产品质量和竞争力。
此外,随着科技的发展和人们对产品质量的要求越来越高,高速铣削等高精度加工方式将会越来越受到重视和应用。
结论:本实验通过对比研究高速铣削和传统铣削的加工精度,得出了加工精度对产品质量的重要影响。
高精度加工方式可以有效地提高产品的尺寸精度、表面质量和机械性能。
因此,在实际生产中,应该注重加工精度控制,以提高产品质量和竞争力。
机械制造工艺学 加工精度统计分析实验报告(0903)
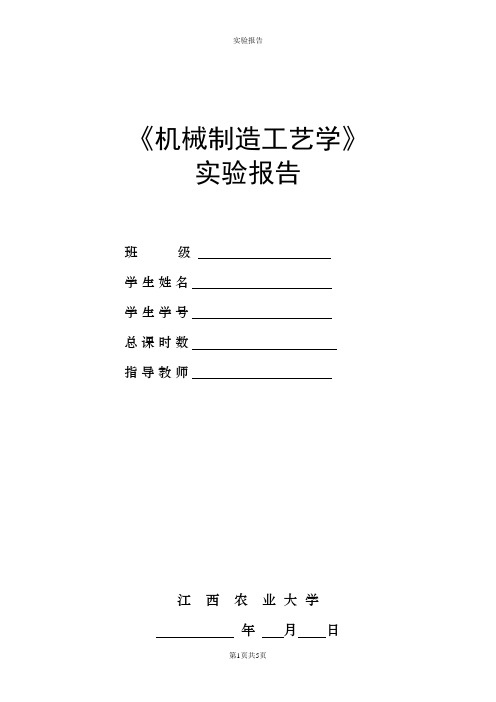
《机械制造工艺学》实验报告班级学生姓名学生学号总课时数指导教师江西农业大学年月日机械制造加工精度的统计分析一、实验目的:1.通过实验掌握加工精度统计分析的基本原理和方法,运用此方法综合分析零件尺寸的变化规律。
2.通过实验结果,分析影响加工零件精度的原因提出解决问题的方法,改进工艺规程,以达到提高零件加工精度的目的,进一步掌握统计分析在全面质量管理中的应用。
3.加工零件每组50个,采用外圆柱体测量装置或量具,测出每一个尺寸,做出其尺寸的分布图,计算其数量指标,分析产生误差的原因,并提出从何性质的误差上着手采取何种对策防止废品。
二、实验用材料、工具、设备1.50个被测工件(轴)。
2.千分尺一只(量程25~50);3.记录用纸和计算器。
三、实验原理:生产实际中影响加工误差的因素是复杂的,因此不能以单个工件的检测得出结论,因为单个工件不能暴露出误差的性质和变化规律,单个工件的误差大小也不能代表整批工件的误差大小。
在一批工件的加工过程中,即有系统性误差因素,也有随机性误差因素。
在连续加工一批零件时,系统性误差的大小和方向或是保持不变或是按一定的规律而变化,前者称为常值系统误差,如原理误差、一次调整误差。
机床、刀具、夹具、量具的制造误差、工艺系统的静力变形系统性从=误差。
如机床的热变形、刀具的磨损等都属于此,他们都是随着加工顺序(即加工时间)而规律的变化着。
在加工一批零件时,误差的大小和方向如果是无规律的变化,则称为随机性误差。
如毛坯误差的复映、定位误差、加紧误差、多次调整误差、内应力引起的变形误差等都属于随机性误差。
鉴于以上分析,要提高加工精度,就应以生产现场内对许多工件进行检查的结果为基础,运行数理统计分析的方法去处理这些结果,进而找出规律性的东西,用以找出解决问题的途径,改进加工工艺,提高加工精度。
常用的统计分析有点图法和分布曲线法。
四、实验步骤:1.对工件预先编号(1~50)。
2.用千分尺对50个工件按序对其直径进行测量。
加工精度统计分析

加工精度统计分析一、实验目的和要求1、掌握加工精度统计分析的基本方法。
2、通过对测的数据进行处理分析,判断该工序能否保证加工精度,有无废品,找出产生加工误差的原因。
3、了解计算机在加工精度统计分析中的应用。
二、实验内容在M224半自动内圆磨床上,连续加工一批同样尺寸的套类零件(如图),取样100个进行测量,获取孔尺寸数据。
三、实验用设备和仪器1、M224半自动内圆磨床一台;2、千分表、内径表杆一套,卡尺一把;3、计算机一台。
四、实验原理在大批生产中,为了对某一工序的加工状况进行分析、了解需要从该工序连续生产出来的一批零件中,抽出部分零件,通过测量,获取有关数据,应用统计分析的方法,来判断该工序的生产状况,进而控制生产过程,保证产品质量。
这种方法可用图1来表示。
其中,母体,是指该工序一次调整机床,加工出零件的总数、样本,是指从该工序中抽取的部分样件。
在调整法加工时,如果加工过程满足:1、加工系统中无变值系统性误差(或其影响很小);2、引起尺寸分散的偶然性误差是相互独立的;3、引起尺寸分散的诸偶然性误差中,无一起主导作用,则所加工的零件,其尺寸参数的分布,服从于正态分布。
对服从正态分布的参数,在应用统计分析的进行数据处理时,应从以下几个方面进行;(1)异常数据剔除在测取样本数据时,有时会出现一个或几个过大或过小的数据,这些数据的出现,是属于正常的呢?还是因为工件有硬质点,或测量时疏忽大意而至,这就需要我们加以判断,如果是非正常出现,应予以剔除,判断方法,采用莱因达准则。
莱因达准则的原理,是从以下思想出发后,特大或特小的数值,其出现的概率很小,如果抽取的样本,服从正态分布,则数值超出6α范围以外的概率为小概率事件,小概率事件可视为不可能事件,不可能事件一旦发生,则可视为事件的出现并非偶然。
即其中含有过失误差,因此可以将超出6α范围以外的数据剔附除(为了简化利用莱因达准则鉴别过失误差的计算,可先从样本数值中,观察确定特大或特小的值一个)将其剔除,计算剔除后样本的均值和均方差,再用6α书评定剔除是否正确,即:若 |Xk -X|≤3αXk 予以保留若 |Xk -X |>3αXk 予以剔除(其中:Xk 为假设的过失误差数据)每剔除一个异常数据,再剔除下一个数据时,要重新计算均值和均方差,直到全部数据均为非异常数据为止。
实验二加工精度的统计分析

实验二加工精度的统计分析一实验目的1.通过实验掌握加工精度统计分析的基本原理和方法,运用此方法综合分析零件尺寸的变化规律。
2.通过实验结果,分析影响加工零件精度的原因提出解决问题的方法,改进工艺规程,以达到提高零件加工精度的目的,进一步掌握统计分析在全面质量管理中的应用。
二设备与仪器1.M1080无心磨床。
2.测微仪二台。
3.块规一组(根据所用选择)。
4.千分尺一支(量程25~50)。
5.试件200个(可顺次选取100个)6.记录用纸、计算器。
三实验原理生产实际中影响加工误差的因素是复杂的,因此不能以单个工件的检测得出结论,因为单个工件不能暴露出误差的性质和变化规律,单个工件的误差大小也不能代表整批工件的误差大小。
在一批工件的加工过程中,即有系统性误差因素,也有随机性误差因素。
在连续加工一批零件时,系统性误差的大小和方向或是保持不变或是按一定的规律而变化,前者称为常值系统误差,如原理误差、一次调整误差。
机床、刀具、夹具、量具的制造误差、工艺系统的静力变形系统性从=误差。
如机床的热变形、刀具的磨损等都属于此,他们都是随着加工顺序(即加工时间)而规律的变化着。
在加工一批零件时,误差的大小和方向如果是无规律的变化,则称为随机性误差。
如毛坯误差的复映、定位误差、加紧误差、多次调整误差、内应力引起的变形误差等都属于随机性误差。
鉴于以上分析,要提高加工精度,就应以生产现场内对许多工件进行检查的结果为基础,运行数理统计分析的方法去处理这些结果,进而找出规律性的东西,用以找出解决问题的途径。
本实验就是在无心磨床上,顺次磨削200个活塞销,然后连续取出100个活塞销进行测量,用数理统计分析的方法,根据实验结果,从中找出规律,改进加工工艺,提高加工精度。
常用的统计分析有点图法和分布曲线法。
1.点图法实验时,从顺次磨削的200个活塞销中,连续取出100个活塞销进行测量,测量后知它们的尺寸是各不相同的,这种现象称之为尺寸分散。
实验二加工误差统计分析实验指导书

实验二加工误差统计分析实验指导书一、实验目的通过学生检测工件尺寸、计算,画出直方图,分析误差性质,理解影响加工误差的因素,掌握加工误差统计分析的基本原理和方法,运用统计分析法研究一批零件在加工过程中尺寸的变化规律,分析其误差的原因。
二、实验要求1.实验前要复习“加工误差统计分析”一节的内容。
2.通过实验绘制“实际分布图”。
3.根据实际分布图分析影响加工误差的因素,推算该工序加工的产品合格率与废品率;试提出解决上述问题的途径。
三.实验仪器及材料外径千分尺、工件100件。
工件零件图:四.实验内容1.对连续加工的一批试件(约100件)测量其尺寸,并记录在“测量值记录表”中。
把测量所得的尺寸大小分组,每组的尺寸间隔为0.002毫米。
2.实际分布曲线(直方图):以工件尺寸(或误差)为横坐标,以频数或频率密度作纵坐标,作出该批零件加工尺寸的等宽直方图。
再连接直方图中每一直方宽度的中点(组中值)得到一条折线,即实际分布曲线。
3.分析判断实验结果:通过对实际分布图分析,判断影响该批零件加工精度的主要误差因素;推断该工序的工艺能力,确定工艺等级;推断该工序加工的成品率与废品率;试提出解决上述工艺问题的措施。
五、实验原理和方法在机械加工中应用数理统计方法对加工误差(或其他质量指标)进行分析,是进行过程控制的一种有效方法,其基本原理是利用加工误差的统计特性,对测量数据进行处理,作出分布图,据此对加工误差的性质、工序能力及工艺稳定性等进行识别和判断,进而对加工误差作出综合分析。
详见教材相关章节。
1.初选分组数K :一般应根据样本容量来选择表1 分组数K 的选定2.确定组距找出样本数据的最大值Ximax 和最小值Ximin ,并按下式计算组距:max min'11x x Rd k k -==--选取与计算的d'值相近的且为测量值尾数整倍数的数值为组距。
3.确定分组数1R k d =+4.确定组界,各组组界为:min (1)2dx i d +-±5.统计各组频数ni (即落在各组组界范围内的样件个数)6.画直方图以样本数据值为横坐标,标出各组组界;以各组频数为纵坐标,画出直方图。
- 1、下载文档前请自行甄别文档内容的完整性,平台不提供额外的编辑、内容补充、找答案等附加服务。
- 2、"仅部分预览"的文档,不可在线预览部分如存在完整性等问题,可反馈申请退款(可完整预览的文档不适用该条件!)。
- 3、如文档侵犯您的权益,请联系客服反馈,我们会尽快为您处理(人工客服工作时间:9:00-18:30)。
实验二加工精度的统
计分析
实验二加工精度的统计分析
一实验目的
1.通过实验掌握加工精度统计分析的基本原理和方法,运用此方法综合分析零件尺寸的变化规律。
2.通过实验结果,分析影响加工零件精度的原因提出解决问题的方法,改进工艺规程,以达到提高零件加工精度的目的,进一步掌握统计分析在全面质量管理中的应用。
二设备与仪器
1.M1080无心磨床。
2.测微仪二台。
3.块规一组(根据所用选择)。
4.千分尺一支(量程25~50)。
5.试件200个(可顺次选取100个)
6.记录用纸、计算器。
三实验原理
生产实际中影响加工误差的因素是复杂的,因此不能以单个工件的检测得出结论,因为单个工件不能暴露出误差的性质和变化规律,单个工件的误差大小也不能代表整批工件的误差大小。
在一批工件的加工过程中,即有系统性误差因素,也有随机性误差因素。
在连续加工一批零件时,系统性误差的大小和方向或是保持不变或是按一定的规律而变化,前者称为常值系统误差,如原理误差、一次调整误差。
机床、刀具、夹具、量具的制造误差、工艺系统的静力变形系统性从=误差。
如机床的热变形、刀具的磨损等都属于此,他们都是随着加工顺序(即加工时间)而规律的变化着。
在加工一批零件时,误差的大小和方向如果是无规律的变化,则称为随机性误差。
如毛坯误差的复映、定位误差、加紧误差、多次调整误差、内应力引起的变形误差等都属于随机性误差。
鉴于以上分析,要提高加工精度,就应以生产现场内对许多工件进行检查的结果为基础,运行数理统计分析的方法去处理这些结果,进而找出规律性的东西,用以找出解决问题的途径。
仅供学习与交流,如有侵权请联系网站删除谢谢11
本实验就是在无心磨床上,顺次磨削200个活塞销,然后连续取出100个活塞销进行测量,用数理统计分析的方法,根据实验结果,从中找出规律,改进加工工艺,提高加工精度。
常用的统计分析有点图法和分布曲线法。
1.点图法
实验时,从顺次磨削的200个活塞销中,连续取出100个活塞销进行测量,测量后知它们的尺寸是各不相同的,这种现象称之为尺寸分散。
把每一活塞的测量尺寸记录下来,然后以活塞销的加工顺序为横坐标,以量得的尺寸为纵坐标,用两根平滑的曲线AA、BB画出点子的上下限,再在其中间画出其平均值曲线00。
这条00线就表示了变值系统误差的变化,其产生根源主要是砂轮的磨损,如图2—1所示。
尺寸
0102030405060708090100
测量工件序号
图2—1
2.分布曲线法
把测量所得的数据按尺寸大小分组,每组有尺寸间隔为0.005mm,则可分成(Xmax—Xmin)/0.005组。
以每组内试件数n为分子,试件总数
仅供学习与交流,如有侵权请联系网站删除谢谢11
仅供学习与交流,如有侵权请联系网站删除 谢谢11
m 为分母,则频率n/m 为纵坐标,以尺寸范围的中点x 为横坐标,就可以作为成如图2—2所示的活塞销实际直径尺寸分布折线图。
图2—2:
1020304050频率(%)
四 实验步骤
1.对试件预先编号(1~100或1~200).
2.活塞销磨削前尺寸为35.05-0.01
-0.10,第一次磨削余量为0.05,按规定尺寸调整机床,试磨数件后,所得尺寸应在公差带中心偏下。
3.机调整后,按序号1~200连续磨削试件至结束。
4.第二次活塞销磨削前尺寸为35-0.02 -0.09mm ,第二次磨削余量为0.05mm ,活塞销要求尺寸34.95-0.03
-0.08mm ,调整机床尺寸34.88mm ,按序号1~200连续磨削试件至结束。
5.调整测微仪尺寸为34.95,从200工件中顺次取出100个活塞销,将试件擦洗干净,在测微仪上按序号顺次测量活塞销的外径为保证测量的准确性和可靠性可在其上测量三个点,取其平均值,把结果填入表2—1中(第16页)。
仅供学习与交流,如有侵权请联系网站删除 谢谢11
五 数据处理
1.根据测量记录表2—1中的数据,以活塞销的加工顺序为横坐标,以量得的尺寸为纵坐标作点图,用两根平溪的曲线AA 、BB 画出点子的上下限,再在其中间画出其平均曲线00(图2—3,第18页)。
2.计算下列数值:
① 工件平均尺寸 (分散范围中心) x =∑=n
1i i n /x =
② 均方根误差 σ=
∑-=n
1
i 2
/)(n i x x =
③ x 图的中心线
x =k k
i i x /1∑==
④R 图的中心线
R =k x /k
1i i ∑==
⑤x 图的上控制界限 =x u x +A R = ⑥x 图的下控制界限 =x L x -A R = ⑦R 图的下控制界限 R u = D R =
3.作出X —R 图,分析工艺的稳定性(图2—4,第18页)。
x 图反映了变值系统性误差的变化规矩规律,R 图反映随机性误差的大小。
4.计算工艺能力系数Cp=T/6σ
5.把测量所得的数据(表2--1)按尺寸大小分组,每组的尺寸间隔为0.005mm,则可分成(Xmax—Xmin)/0.005组,把各范围内的试件数量填入表2—3内,以每组内试件数m为分子,试件总数n为分母,则频率m/n为纵坐标,以每组中点X为横坐标,就可以作成如图2—2所示的活塞销实际直径尺寸分布折线图(图2--5)。
六要求
1.根据点图写出△常、△变、△随。
2.X—R的波动反应了什么问题。
3.根据分布折线图,△系统等于多少,加工下一批工件应怎样调整磨床。
仅供学习与交流,如有侵权请联系网站删除谢谢11
加工精度统计分析实验报告
表2—1 活塞销外径尺寸测量记录表
活塞销毛坯尺寸
活塞销要求尺寸磨床调整尺寸
仅供学习与交流,如有侵权请联系网站删除谢谢11
仅供学习与交流,如有侵权请联系网站删除 谢谢11
表2—2 A 、D 数值表
计算下列数值
① 工件平均尺寸 (分散范围中心) x =∑=n
1i i n /x =
② 均方根误差 σ=
∑-=n
1
i 2
/)(n i x x =
③ x 图的中心线
x =k k
i i x /1∑==
④R 图的中心线
仅供学习与交流,如有侵权请联系网站删除 谢谢11
R =k x /k
1
i i ∑==
⑤x 图的上控制界限 =x u x +A R = + = ⑥x 图的下控制界限 =x L x -A R = + = ⑦R 图的下控制界限 R u = D R = + =
⑧把活塞销的测量尺寸输入计算机进行计算以上数值。
二 活塞销的尺寸点图(图2—2)
246810
10
20
30
40
50
60
70
80
90100
测量工件序号
尺寸
三 x —R (图2—4)
0 5 10 15 20 25
活塞销外径测量结果表2—3
仅供学习与交流,如有侵权请联系网站删除谢谢11
四 分布折线图(图2—5)
活塞销实际直径分布折线图
10
20
30
40
50
尺寸频率(%)
五计算
公差带中心 =
分散范围中心 =
△系统 =
工艺能力系数Cp=T/6σ=
六、分布图分析(与公差带T比较)
⒈判断工序精度6σ能否满足加工精度要求T
⒉常值性误差是多少?如何调整消除常值性误差?
⒊计算废品率,并判定废品率是否可修?要只允许有可修废品,如何调整?
⒋区分主要误差性质,从何种性质的误差上着手,采取何种对策来消灭废品?。