南充轻烃回收装置工艺改造方案研究
分析轻烃回收装置节能技术
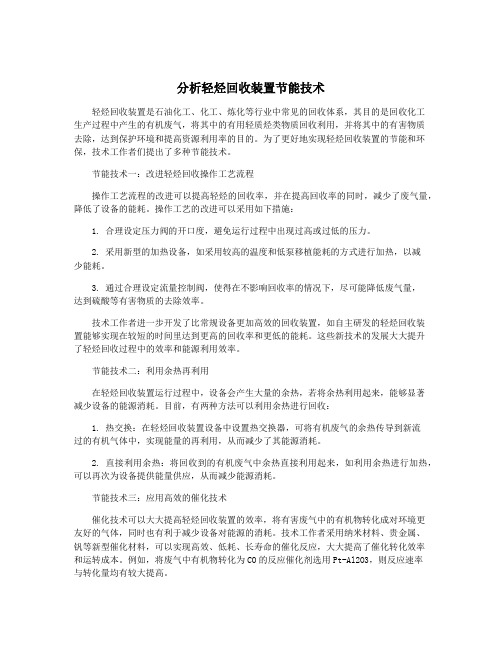
分析轻烃回收装置节能技术轻烃回收装置是石油化工、化工、炼化等行业中常见的回收体系,其目的是回收化工生产过程中产生的有机废气,将其中的有用轻质烃类物质回收利用,并将其中的有害物质去除,达到保护环境和提高资源利用率的目的。
为了更好地实现轻烃回收装置的节能和环保,技术工作者们提出了多种节能技术。
节能技术一:改进轻烃回收操作工艺流程操作工艺流程的改进可以提高轻烃的回收率,并在提高回收率的同时,减少了废气量,降低了设备的能耗。
操作工艺的改进可以采用如下措施:1. 合理设定压力阀的开口度,避免运行过程中出现过高或过低的压力。
2. 采用新型的加热设备,如采用较高的温度和低泵移植能耗的方式进行加热,以减少能耗。
3. 通过合理设定流量控制阀,使得在不影响回收率的情况下,尽可能降低废气量,达到硫酸等有害物质的去除效率。
技术工作者进一步开发了比常规设备更加高效的回收装置,如自主研发的轻烃回收装置能够实现在较短的时间里达到更高的回收率和更低的能耗。
这些新技术的发展大大提升了轻烃回收过程中的效率和能源利用效率。
节能技术二:利用余热再利用在轻烃回收装置运行过程中,设备会产生大量的余热,若将余热利用起来,能够显著减少设备的能源消耗。
目前,有两种方法可以利用余热进行回收:1. 热交换:在轻烃回收装置设备中设置热交换器,可将有机废气的余热传导到新流过的有机气体中,实现能量的再利用,从而减少了其能源消耗。
2. 直接利用余热:将回收到的有机废气中余热直接利用起来,如利用余热进行加热,可以再次为设备提供能量供应,从而减少能源消耗。
节能技术三:应用高效的催化技术催化技术可以大大提高轻烃回收装置的效率,将有害废气中的有机物转化成对环境更友好的气体,同时也有利于减少设备对能源的消耗。
技术工作者采用纳米材料、贵金属、钒等新型催化材料,可以实现高效、低耗、长寿命的催化反应,大大提高了催化转化效率和运转成本。
例如,将废气中有机物转化为CO的反应催化剂选用Pt-Al2O3,则反应速率与转化量均有较大提高。
浅谈轻烃回收装置的设计分析

浅谈轻烃回收装置的设计分析[摘要]本单位轻烃装置已连续运行24年,超过服役年限,轻烃的回收利用能耗及操作费用过高,经济效益明显降低设备严重老化,随着天然气产量递减,原轻烃厂装置已经不能满足目前及今后的生产需要。
而且由于本工程的的噪音对居民伤害较大因此为了满足油田的生产以及居民的生活,进一步提高油田的经济效益选择新站址选用新工艺建设一套轻烃装置十分必要和迫切的。
[关键词]轻烃经济效益回收装置油田生产本文以某单位重建轻烃回收装置为对象,对其进行设计。
从理论和实践的角度阐述了改造的可行性和必要性。
目前我国的轻烃回收装置多为20世纪80年代建造,由于受到当时设备、技术、人员等方面的影响,轻烃装置基本上都采用的是低压操作。
轻烃回收装置只能勉强的维持低效益运行。
但是,随着社会的进步,科技的日益发达,科学研究也在不断地深入和改进,而对于轻烃回收作为油田新的经济增长点,也愈来备受人们关注,希望轻烃回收装置高收率、低能耗。
1轻烃回收技术简介从国内外轻烃回收技术的现状可以看出,我国轻烃回收技术与国外先进技术还有一定的距离。
国内天然气资源丰富,发展轻烃回收技术具有重要的意义。
为提高我国轻烃回收技术水平,建议采取以下措施:(1)消化吸收国外先进技术,在有条件的地区建设较大规模的深冷回收液烃装置,采用先进工艺积水和设备,降低能耗,提高轻烃产品收率。
(2)为提高设计技术水平,组织国内科研人员开发目前急需的主要工艺计算软件,开发研制多流道板翘式换热器和高效浮阎塔,提高填料塔的设计水平。
(3)重叠式制冷、混合冷剂制冷等制冷工艺在国内尚未得到应用,积极开展研究工作和开发工业试验装置,尽快改变轻烃回收装置中制冷工艺单一的现状。
(4)轻烃回收中的关键设备压缩机和透平膨胀在国内得到广泛的应用,但与国外同类产品相比,其技术性能有待进一步提高和完善。
(5)积极开展和研制轻烃回收装置,提高设计水平,逐步形成系列化、通用化、标准化产品。
2设计原则严格遵循国家现行的有关方针、政策、法令、标准、规范,贯彻“安全、可靠、适用、效益、环保、现代”的指导思想,采取各种有效措施,优化总体布局,提高整体技术水平和综合经济效益。
轻烃回收工艺技术及其进展

轻烃回收工艺技术及其进展轻烃是指石油提炼或天然气加工过程中产生的低碳烷烃类化合物,包括乙烷、丙烷、丁烷等。
由于轻烃具有高热值、易燃、易挥发以及广泛的应用价值,因此对于轻烃的回收工艺技术的研究具有重要意义。
本文将介绍目前常用的轻烃回收工艺技术以及其进展。
轻烃回收工艺技术主要包括吸附分离、膜分离、蒸馏分离和冷凝分离等。
吸附分离是一种通过固体吸附剂将轻烃从混合气中吸附出来的技术,常用的吸附剂包括活性炭、分子筛等。
膜分离是利用半透膜的分离性能将轻烃分离出来的技术,常用的膜材料包括聚酯膜、聚丙烯膜等。
蒸馏分离是根据轻烃在不同温度下的沸点差异进行分离的技术,常用的蒸馏设备包括塔式蒸馏塔、萃取塔等。
冷凝分离是通过降低轻烃的温度使其从气态转化为液态从而实现分离的技术,常用的冷凝设备包括冷凝器、冷冻器等。
在膜分离技术中,聚酯膜是一种常用的膜材料,其具有良好的选择性和透过率,能够实现对轻烃的高效分离。
为了提高聚酯膜的分离性能,研究人员通过改变共聚合物的比例、添加增渗剂等手段对膜材料进行改性。
聚丙烯膜也被广泛研究,其具有较高的烷烃选择性和较低的分离性能损失,因此具有良好的应用潜力。
在蒸馏分离技术中,塔式蒸馏塔是最常用的分离设备之一,其通过控制不同温度层的塔体来实现轻烃的分馏。
为了提高对轻烃的分离效果,研究人员通过改变塔体结构、优化操作参数等手段对蒸馏设备进行改进。
萃取塔也是一种常用的蒸馏设备,其通过溶剂的加入来实现对轻烃的选择性提取。
冷凝分离技术主要包括冷凝器和冷冻器两种方式。
冷凝器通过将轻烃的温度降低到其饱和蒸汽压以下,使其从气态转化为液态从而实现分离。
冷冻器则通过降低轻烃的温度至其凝点以下,使其凝结成冷凝液从而实现分离。
为了提高冷凝分离的效果,研究人员通过改变冷却剂的流动方式、提高冷却剂的温度差等手段对冷凝设备进行改进。
轻烃回收工艺技术的研究不断取得进展,吸附分离、膜分离、蒸馏分离和冷凝分离等技术不断被改进和创新,以满足不同场景和需求下的轻烃回收。
提高南充轻烃回收装置C3+收率的途径探讨

提高南充轻烃回收装置C3+收率的途径探讨摘要:南充轻烃回收装置因原料气重烃含量降低、膨胀机处理量不足、脱乙烷塔底温波动大等原因,造成装置目前C3+收率不足70%。
为解决这一问题,对该装置进行了全面系统的分析与研究,提出将再生气工艺流程、脱乙烷塔底温工艺流程进行改造、对装置区老化或选取不合理的仪表进行更换等措施,达到提高C3+收率的目的。
关键词:轻烃回收C3+收率膨胀机脱乙烷塔重沸器一、前言南充轻烃回收装置设计处理气量为20×104m3/d,气源为来自八南干线的天然气,采用的制冷方式为透平膨胀机制冷,主要产品有液化石油气和轻质油。
目前该装置因气源不足且气量波动大、部分工艺流程不合理等因素,造成装置运行不平稳、设备常处于半负荷运行状态、主要工艺运行参数与设计值相差较大,导致装置运行效率低,C3+收率不足70%。
因此,本文针对南充轻烃回收装置收率低的问题,对该装置进行分析与研究,并就如何提高C3+收率提出对策及建议。
二、影响装置C3+收率的因素及原因分析1.原料气组成的变化研究表明,在相同的温度和压力条件下,原料气的重烃含量越高,C3+收率越高。
原料气的重烃组分含量低于设计时气样的重烃含量,影响装置C3+收率。
2.膨胀机处理量不足2.1处理量对膨胀机运行效率的影响按照设计要求,要获取较高的C3+收率,膨胀机的出口温度和分离温度应分别控制在-60℃和-90℃左右。
但由于膨胀机处理量不同,导致膨胀机出口温度及分离温度亦不一样。
只有当处理量达到16万方以上时,膨胀机的出口温度和分离温度才分别接近或达到-90℃和-60℃。
但装置在生产期间,膨胀机实际处理量一般只为13.0-15.0万方,造成分离温度和膨胀机的出口温度与设计值相差较大,影响C3+收率。
2.2.处理量不足的原因分析2.2.1气源不足。
南充轻烃回收装置主要处理秋林大安寨、八角场大安寨、须家河组凝析气藏气,由于油气藏开产时间较长,近年来勘探开发未取得较大突破,目前产量较低导致进装置原料气量不足、与设计值相差较大。
对改进轻烃回收装置的探索

2 建立改进模型
在轻烃 回收的过程 中, 键组分一 股为C 关 或c 所 以 , 模型 的改进 目 就确定 为装置 。 本 标 总能耗 和 C+ 3 的组 分 回收量 比值 最低 , 以反 映 出轻烃 的 回收成 本。 优化变量是 膨胀机和增 压 机端 出 口压力以 及蒸发器 出 口的温度 。 经过 分 析, 这两个 变量 都能 用于生 产控 制 。 一模 型 这 的约束 条件主要 有设 备参 数的 限制和 轻烃 中 c , 组分 含量 等限 制 , 中设备 操 作的参 数主 其 要有压缩机出 口的压力小于或等于5 0 a 膨 . MP , 胀机 出 口的压力大于 或等于0 1MP , .5 a 这是 由 装 置外输 千气 压力所 决定 的 。 当前 , 内对 天然 气直 接 冷凝 所 得到 的 国 轻烃 中 C+ 2中组 分 含 量 的大 小还 缺 乏 相对 应 的标准 , 也没 有文献 对此 进行过 研 究。 一般 来 说 , , 分的 含量还 要结 合装 置的 经济性 来 C 组 确定 。 过流 程 模拟 , 够得 到 重 、 两种 不 通 能 轻 同组成 原料 气后 , 烃 中c 轻 , 组分 含量 对于 回
如图4 所示 , 通过 调整增 压机 出 口的压 力 , 能 够得到 单位 C 耗随 着压 力的变化 关 系。 , 能 从 图4 行分析 , 曲线在0 8 P 进 当 . M a~ 1 O a 间的 范 围 内 几 乎 呈 现 出 竖 直 的 . MP 之 状 态 。 压 力 不 断 提 高 之后 , 位 丙烷 以 上 在 单 组 分 的 能 耗 出 现 了急 剧 的 下 降 趋 势 , 曲 当 线在 1 O a .MP 这一 区 间之 内时 , . MP ~2 O a 能 耗 下 降的速度逐渐减 慢 , 当压 力在2 5 a , . MP 时 就 达到 了 曲线的 最低点 , 当压 力在2 5 a .MP 之 后 , 位 能耗 又 随之 开 始升 高 。 以 , 原 料 单 所 轻 3 改进结果分析 时 的装置 的最佳操作压 力应 当在2 5 a 近 .MP 附 3 1 原料 工艺参 数 的改进 .重 进 行优 选 。 果 将增 压机 的 出 口压 力分 别设 如 如 图3 所示 , 要逐 步对 增压 机的 出 口压 力 顶在 15 a 2 0 a2 5 a 就能得 出蒸发 .MP 、 .MP 、 .MP , 进 行调 整 , 以得 到 单位 C+ 3 能耗随 着压 力的 变 器 出 口温 度 和单 位 丙烷 以 上 组 分 之 间的 关 化关系。 系。 由于 增压 机 出 口压 力 的 增大 , 首先 引起 3 3不 同原 料气 改进 结果 的比较 . 了单位 C 能 耗 的下 降 , 过 极小 值 之后 , 经 又 重 、 两种原 料气 的改进 结果 进行分 析 , 轻 随 着压 力 的升 高而 加 大 。 是 因为 增加 了压 对改 进后 重 、 两种 原料 气所 对应 的C 这 轻 收率 力, 装置的 总能 耗不断 增加 , 初始增 加压 力 都有 比较 大幅 度的提 高 , 么单 位 c 而 那 能耗 也 时 , 能 耗 重组 分 的冷 凝 量增 加 得 比较 快 , 随 之大 大 降低 , 进之后 仍然 属于 中、 c 改 低压 操 而 达到 了某 一压 力之 后 , 组分 的冷 凝量 作 , 就使原 装置 几乎不 需要 变动工 艺设备 、 c 重 这 就 基本 不再 增加 。 所以 , 比较适 宜 的工作 压 力 管 线等 , 就能 够实 现这一 压力 的要求 , 从而 节 应 当在 2 0 a 近进行 优选 。 果将压 力分 省 了由于 压 力提 高 所产 生 的 固定资 本投 资 。 1MP 附 如 别 设 定 在2. MPa 2. 0 0 、 5 MPa 1 2 MP 1 可见 , 、 . 4 a、 。 一旦提 高 了装 置的 制冷 能力 , 完全 能 就 0 MP , 么 , 整 蒸发 器 的 出 口温 度 , 能 够 实现 装 置在 最 优 工艺 条 件下 的 操作 。 4 a那 调 就 得 到单 位 C 组 分 能耗 值 和 蒸发 器 出 口温 度 之 间 的关 系 。 4 研究结论 3 2轻 原料工 艺参 数的 改进 . 通 过 改进 改进 轻烃 回收 装 置 的 工艺 参 数 , 设备 得到 了更新 , 保 了装 置 的安 全 、 使 确
100万方天轻烃回收装置工艺的设计轻烃回收毕业论文

1244EJC天然气(煤层气)与管道网
5205
EJC天然气(煤层气)与管道网美国GPM气体公司Goldsmith天然气处理厂NGL回收装置即在改造后采用了GSP法。该装置在1976年建成,处理量为220×104m3/d,原采用单级膨胀机制冷法,1982年改建为两级膨胀机制冷法,处理量为242×104m3/d,最高可达310×104m3/d,但其乙烷收率仅为70%。之后改用单级膨胀机制冷的GSP法,乙烷收率有了明显提高,在1995年又进一步改为两级膨胀机制冷的GSP法,设计处理量为380×104m3/d,乙烷收率(设计值)高达95%。
2. 直接换热(DHX)法
DHX法是由加拿大埃索资源公司于1984年首先提出,并在JudyCreek厂的NGL回收装置实践后效果很好,其工艺流程见图5-18。
图中的DHX塔(重接触塔)相当于一个吸收塔。该法的实质是将脱乙烷塔回流罐的凝液经过增压、换冷、节流降温后进入DHX塔顶部,用以吸收低温分离器进该塔气体中的C3+烃类,从而提高C3+收率。将常规膨胀机制冷法(ISS)装置改造成DHX法后,在不回收乙烷的情况下,实践证明在一样条件下C3+收率可由72%提高到95%,而改造的投资却较少。
1987年Ovaoff工程公司等提出的GSP与LSP是对单级膨胀机制冷工艺(ISS)和多级膨胀机制冷工艺(MTP)的改进。典型的GSP与LSP流程分别见图1.1。
GSP是针对较贫气体(c;烃类含量按液态计小于400mL/m3)、LSP是针对较富气体(C2+烃类含量按液态计大于400mL/m3)而改进的NGL回收方法。表5-10列出了处理量为283×104m3/d的NGL回收装置采用ISS、MTP与GSP等工艺方法时的主要指标对比。
提升轻烃回收装置运行效率的措施
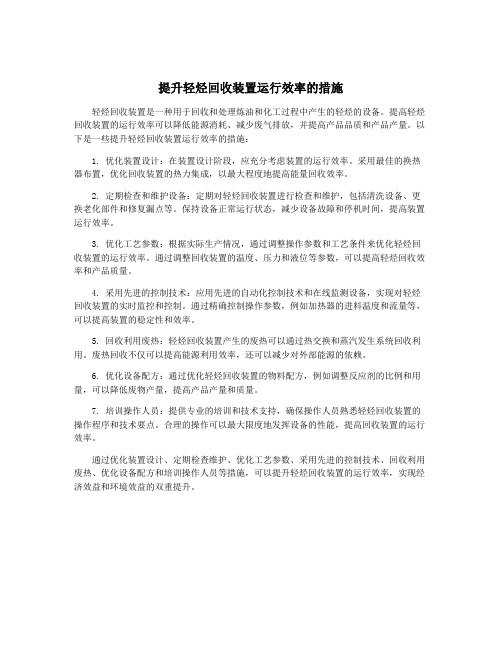
提升轻烃回收装置运行效率的措施轻烃回收装置是一种用于回收和处理炼油和化工过程中产生的轻烃的设备。
提高轻烃回收装置的运行效率可以降低能源消耗、减少废气排放,并提高产品品质和产品产量。
以下是一些提升轻烃回收装置运行效率的措施:1. 优化装置设计:在装置设计阶段,应充分考虑装置的运行效率。
采用最佳的换热器布置,优化回收装置的热力集成,以最大程度地提高能量回收效率。
2. 定期检查和维护设备:定期对轻烃回收装置进行检查和维护,包括清洗设备、更换老化部件和修复漏点等。
保持设备正常运行状态,减少设备故障和停机时间,提高装置运行效率。
3. 优化工艺参数:根据实际生产情况,通过调整操作参数和工艺条件来优化轻烃回收装置的运行效率。
通过调整回收装置的温度、压力和液位等参数,可以提高轻烃回收效率和产品质量。
4. 采用先进的控制技术:应用先进的自动化控制技术和在线监测设备,实现对轻烃回收装置的实时监控和控制。
通过精确控制操作参数,例如加热器的进料温度和流量等,可以提高装置的稳定性和效率。
5. 回收利用废热:轻烃回收装置产生的废热可以通过热交换和蒸汽发生系统回收利用。
废热回收不仅可以提高能源利用效率,还可以减少对外部能源的依赖。
6. 优化设备配方:通过优化轻烃回收装置的物料配方,例如调整反应剂的比例和用量,可以降低废物产量,提高产品产量和质量。
7. 培训操作人员:提供专业的培训和技术支持,确保操作人员熟悉轻烃回收装置的操作程序和技术要点。
合理的操作可以最大限度地发挥设备的性能,提高回收装置的运行效率。
通过优化装置设计、定期检查维护、优化工艺参数、采用先进的控制技术、回收利用废热、优化设备配方和培训操作人员等措施,可以提升轻烃回收装置的运行效率,实现经济效益和环境效益的双重提升。
轻烃回收工艺的发展方向及新技术探讨

第21卷第2期2003年6月天 然 气 与 石 油Natural Gas And OilVol.21,No.2Jun.2003收稿日期:2002-09-04;修回日期:2002-09-12 作者简介:王 健(1964-),女,四川自贡市人,工程师,学士,1985年毕业于成都科技大学化学工程专业,从事油气加工设计及管理工作。
电话:(028)86014414。
文章编号:1006-5539(2003)02-0020-03轻烃回收工艺的发展方向及新技术探讨王 健(中国石油集团工程设计有限责任公司西南分公司,四川成都610017)摘 要:低温分离技术的发展,推动和促进了轻烃回收工艺的进步。
但总体来说能耗高、收率低仍然是制约轻烃回收工艺发展的重要因素。
近年来对轻烃回收工艺的研究也主要是围绕这两方面开展,同时开发利用了一些新技术和新工艺。
关键词:轻烃回收;能耗;收率;新工艺中图分类号:T E868 文献标识码:C1 引言为满足天然气长输管线的烃露点要求,回收天然气中很有价值的乙烷/丙烷,近年来气田轻烃回收作为各气田新的经济增长点,越来越受到人们重视,轻烃回收工艺也得到了较大发展。
在众多的轻烃回收方法中,低温回收工艺是当前主要采用的方法,深冷分离技术的发展,推动和促进了轻烃回收工艺的进步,并得到更为广泛的应用[1]。
2 低温回收工艺的研究发展方向低温回收工艺过程中最主要、最关键的步骤就是制冷工艺。
它直接影响装置的投资、能耗和回收率三大经济指标。
工业上采用的制冷方法大致有:节流制冷、膨胀机制冷、热分离机制冷、外冷源制冷和复合制冷。
目前对制冷工艺的研究紧紧围绕节能降耗和提高轻烃回收率两方面开展。
2 1 节能降耗现有轻烃回收装置大多能耗较高,制冷效率较低,因此节能降耗一直是轻烃回收技术中的一个重要研究课题。
节能的途径只有两种:一种是考虑单个设备如膨胀机或压缩机的能耗,合理选择设备型号;另一种就是从优化制冷方案着手,从可以采用的多种方法中筛选出最佳制冷方案,达到最佳的节能效果和经济效益。
轻烃回收装置工艺
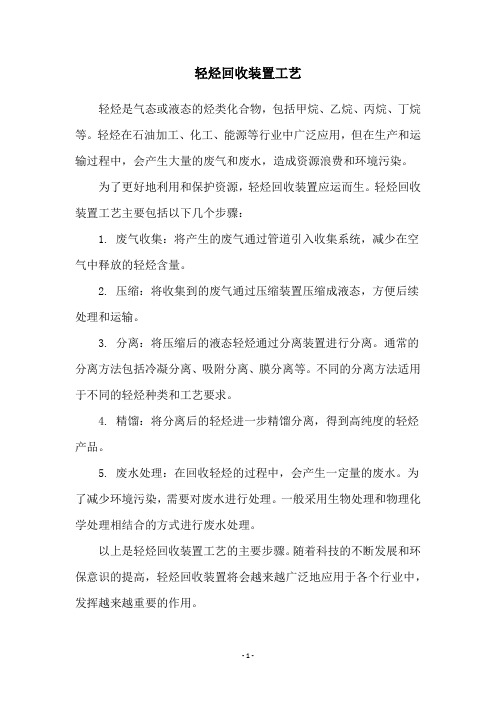
轻烃回收装置工艺
轻烃是气态或液态的烃类化合物,包括甲烷、乙烷、丙烷、丁烷等。
轻烃在石油加工、化工、能源等行业中广泛应用,但在生产和运输过程中,会产生大量的废气和废水,造成资源浪费和环境污染。
为了更好地利用和保护资源,轻烃回收装置应运而生。
轻烃回收装置工艺主要包括以下几个步骤:
1. 废气收集:将产生的废气通过管道引入收集系统,减少在空气中释放的轻烃含量。
2. 压缩:将收集到的废气通过压缩装置压缩成液态,方便后续处理和运输。
3. 分离:将压缩后的液态轻烃通过分离装置进行分离。
通常的分离方法包括冷凝分离、吸附分离、膜分离等。
不同的分离方法适用于不同的轻烃种类和工艺要求。
4. 精馏:将分离后的轻烃进一步精馏分离,得到高纯度的轻烃产品。
5. 废水处理:在回收轻烃的过程中,会产生一定量的废水。
为了减少环境污染,需要对废水进行处理。
一般采用生物处理和物理化学处理相结合的方式进行废水处理。
以上是轻烃回收装置工艺的主要步骤。
随着科技的不断发展和环保意识的提高,轻烃回收装置将会越来越广泛地应用于各个行业中,发挥越来越重要的作用。
- 1 -。
轻烃回收中DHX工艺研究

算 , 了进 一步 的研 究 探讨 , 做 以考 察 D X : 艺 对原 H 1 : 料气 的适 应性 。结果 发 现 原料 气 中的 C 含量 大 于 1% 时 , H 0 D X工 艺 已经 失 去 了其 优越 性 , 至不 能 甚 使用 。
D X工艺 , H 原料 气 中 c/ 对 该 ] 艺 c ,c 二 回 收率 提 高幅度有显 著影 响 , c 含量 对此 影 响较 小 , 料 而 原 气 中 c/ 越小 , H Ic D X工 艺 c 回收率 提 高 幅度 越
无 法 应 用 DHX 工 艺 。 关键词 : 烃 回收 ; HX 工 艺 ; 应 性 ; 究 轻 D 适 研
文 章 编 号 : 0 —59 2 1 )20 1 -9 1 653 (0 0 0 - 80 0 0 文 献标 识 码 : A
D X工 艺 ( i c H a E c ag ) 加 拿 大 埃 H Dr t et xhn e 是 e
单 级膨胀 机 制 冷 法相 比 , H D X工 艺 C 率 的提 高 收 幅度 主要取决 于 气体 中 C/ : 积分 数之 比 , 气 C 体 而
体 中 C 烃 类含量 对其 影响甚 小 ㈡ J 。文献 : 统计
子量小吸收能力又强 , C 的吸收作用和蒸发后产 在 生 的冷 量直接 与原 料气 换 热 下 , 使原 料 气 的温 度 进 步降低 , 从而 获得高 的 C 收率 。我 国大港 压气 站
一
了全 国各 油 田 3 8种 伴 生 气 组 成 , 平 均 组 成 列 于 其
表 1 。
%
19 9 5年 引进 了美 国 P R—Q I UP公 司 10×1 m / 0 0 d
表 1 原料气组成的统计结所 有 的原 料 气 都 适 用 于 并
轻烃回收工艺技术措施探讨
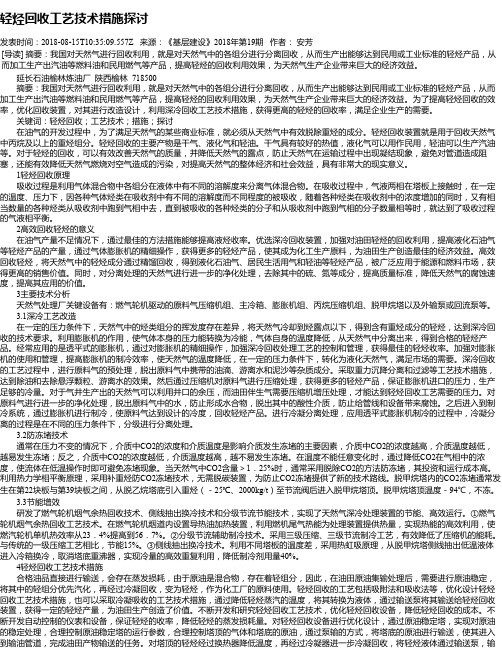
轻烃回收工艺技术措施探讨发表时间:2018-08-15T10:35:09.557Z 来源:《基层建设》2018年第19期作者:安芳[导读] 摘要:我国对天然气进行回收利用,就是对天然气中的各组分进行分离回收,从而生产出能够达到民用或工业标准的轻烃产品,从而加工生产出汽油等燃料油和民用燃气等产品,提高轻烃的回收利用效果,为天然气生产企业带来巨大的经济效益。
延长石油榆林炼油厂陕西榆林 718500摘要:我国对天然气进行回收利用,就是对天然气中的各组分进行分离回收,从而生产出能够达到民用或工业标准的轻烃产品,从而加工生产出汽油等燃料油和民用燃气等产品,提高轻烃的回收利用效果,为天然气生产企业带来巨大的经济效益。
为了提高轻烃回收的效率,优化回收装置,对其进行改造设计,利用深冷回收工艺技术措施,获得更高的轻烃的回收率,满足企业生产的需要。
关键词:轻烃回收;工艺技术;措施;探讨在油气的开发过程中,为了满足天然气的某些商业标准,就必须从天然气中有效脱除重烃的成分。
轻烃回收装置就是用于回收天然气中丙烷及以上的重烃组分。
轻烃回收的主要产物是干气、液化气和轻油。
干气具有较好的热值,液化气可以用作民用,轻油可以生产汽油等。
对于轻烃的回收,可以有效改善天然气的质量,并降低天然气的露点,防止天然气在运输过程中出现凝结现象,避免对管道造成阻塞,还能有效降低天然气燃烧对空气造成的污染,对提高天然气的整体经济和社会效益,具有非常大的现实意义。
1轻烃回收原理吸收过程是利用气体混合物中各组分在液体中有不同的溶解度来分离气体混合物。
在吸收过程中,气液两相在塔板上接触时,在一定的温度、压力下,因各种气体烃类在吸收剂中有不同的溶解度而不同程度的被吸收,随着各种烃类在吸收剂中的浓度增加的同时,又有相当数量的各种烃类从吸收剂中跑到气相中去,直到被吸收的各种烃类的分子和从吸收剂中跑到气相的分子数量相等时,就达到了吸收过程的气液相平衡。
2高效回收轻烃的意义在油气产量不足情况下,通过最佳的方法措施能够提高液烃收率。
轻烃回收工艺技术措施探讨
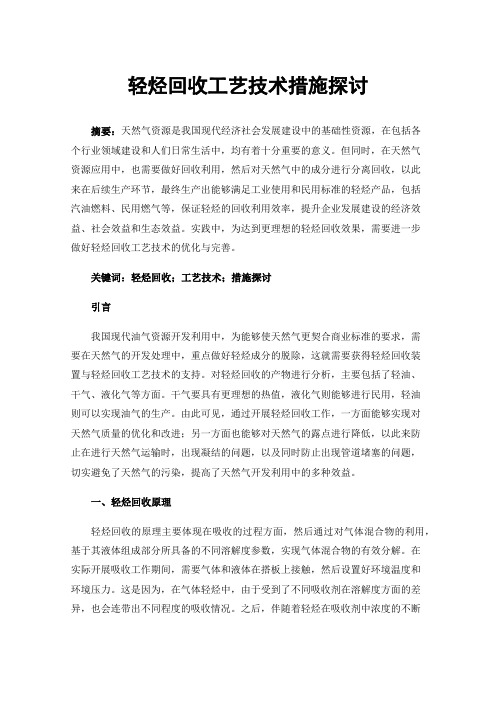
轻烃回收工艺技术措施探讨摘要:天然气资源是我国现代经济社会发展建设中的基础性资源,在包括各个行业领域建设和人们日常生活中,均有着十分重要的意义。
但同时,在天然气资源应用中,也需要做好回收利用,然后对天然气中的成分进行分离回收,以此来在后续生产环节,最终生产出能够满足工业使用和民用标准的轻烃产品,包括汽油燃料、民用燃气等,保证轻烃的回收利用效率,提升企业发展建设的经济效益、社会效益和生态效益。
实践中,为达到更理想的轻烃回收效果,需要进一步做好轻烃回收工艺技术的优化与完善。
关键词:轻烃回收;工艺技术;措施探讨引言我国现代油气资源开发利用中,为能够使天然气更契合商业标准的要求,需要在天然气的开发处理中,重点做好轻烃成分的脱除,这就需要获得轻烃回收装置与轻烃回收工艺技术的支持。
对轻烃回收的产物进行分析,主要包括了轻油、干气、液化气等方面。
干气要具有更理想的热值,液化气则能够进行民用,轻油则可以实现油气的生产。
由此可见,通过开展轻烃回收工作,一方面能够实现对天然气质量的优化和改进;另一方面也能够对天然气的露点进行降低,以此来防止在进行天然气运输时,出现凝结的问题,以及同时防止出现管道堵塞的问题,切实避免了天然气的污染,提高了天然气开发利用中的多种效益。
一、轻烃回收原理轻烃回收的原理主要体现在吸收的过程方面,然后通过对气体混合物的利用,基于其液体组成部分所具备的不同溶解度参数,实现气体混合物的有效分解。
在实际开展吸收工作期间,需要气体和液体在搭板上接触,然后设置好环境温度和环境压力。
这是因为,在气体轻烃中,由于受到了不同吸收剂在溶解度方面的差异,也会连带出不同程度的吸收情况。
之后,伴随着轻烃在吸收剂中浓度的不断增加,同样会产生一定数量轻烃在吸收剂中完成到气相的传递,并最后达到吸收轻烃分析与吸收剂跑到气相轻烃分子数量的平衡。
二、轻烃回收意义油气资源是我国现代经济社会发展与各个行业领域建设以及人们日常生活中的重要资源能源。
80万方每天轻烃回收装置工艺设计

80万方每天轻烃回收装置工艺设计引言轻烃是石油加工过程中产生的一种有机化合物,包括丙烷、丁烷等。
随着全球能源需求的增长,轻烃的回收和利用变得越来越重要。
本文将介绍一种每天可处理80万方轻烃的回收装置的工艺设计。
装置概述80万方每天轻烃回收装置的主要组成部分包括进料系统、分离系统、回收系统和产品储存系统。
进料系统进料系统主要用于将原料输送到分离系统。
在本装置中,主要的原料是轻烃气体混合物,需要通过管道输送到分离塔。
分离系统分离系统是整个工艺的核心部分。
在分离塔中,轻烃混合物将被分离成不同的组分,以实现轻烃的回收。
分离塔的设计需要考虑到不同组分的沸点差异,并采用合适的精馏工艺。
回收系统回收系统用于将轻烃组分从分离塔中回收,并将其转化为可用产品。
在本装置中,回收系统包括凝析塔、可用产品的分离和处理等。
产品储存系统产品储存系统用于将回收的产品储存在合适的容器中,以备后续使用或出售。
工艺设计80万方每天轻烃回收装置的工艺设计需要考虑以下几个方面:轻烃混合物的成分、分离塔的设计、回收系统的选择以及产品储存系统的设计。
轻烃混合物的成分在进行工艺设计之前,需要对轻烃混合物的成分进行分析。
根据不同的成分含量,可以确定分离塔的操作参数和回收系统的工艺选择。
分离塔的设计分离塔的设计需要根据轻烃混合物的成分和分离要求来确定。
首先,需要选择合适的塔板类型和塔板间距。
其次,还需要考虑塔的高度和直径,以保证分离效果和操作效率。
回收系统的选择回收系统的选择取决于回收产品的要求和工艺经济性。
常见的回收系统包括凝析回收、吸附回收和膜分离回收等。
在选择适当的回收系统时,需要考虑到其回收效率、操作成本和装置复杂程度等因素。
产品储存系统的设计产品储存系统的设计需要考虑到产品的性质和需要。
常见的储存方式包括液态储存和气态储存。
在设计过程中,需要考虑到储存容器的安全性和可用性。
结论80万方每天轻烃回收装置的工艺设计需要综合考虑轻烃混合物的成分、分离塔的设计、回收系统的选择和产品储存系统的设计。
提升轻烃回收装置运行效率的措施
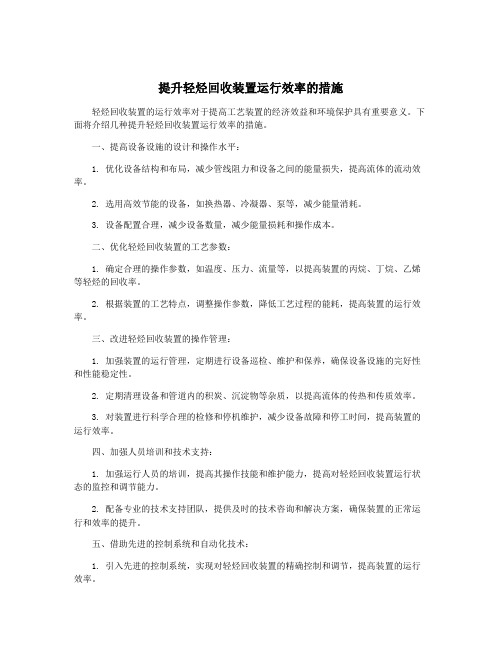
提升轻烃回收装置运行效率的措施轻烃回收装置的运行效率对于提高工艺装置的经济效益和环境保护具有重要意义。
下面将介绍几种提升轻烃回收装置运行效率的措施。
一、提高设备设施的设计和操作水平:1. 优化设备结构和布局,减少管线阻力和设备之间的能量损失,提高流体的流动效率。
2. 选用高效节能的设备,如换热器、冷凝器、泵等,减少能量消耗。
3. 设备配置合理,减少设备数量,减少能量损耗和操作成本。
二、优化轻烃回收装置的工艺参数:1. 确定合理的操作参数,如温度、压力、流量等,以提高装置的丙烷、丁烷、乙烯等轻烃的回收率。
2. 根据装置的工艺特点,调整操作参数,降低工艺过程的能耗,提高装置的运行效率。
三、改进轻烃回收装置的操作管理:1. 加强装置的运行管理,定期进行设备巡检、维护和保养,确保设备设施的完好性和性能稳定性。
2. 定期清理设备和管道内的积炭、沉淀物等杂质,以提高流体的传热和传质效率。
3. 对装置进行科学合理的检修和停机维护,减少设备故障和停工时间,提高装置的运行效率。
四、加强人员培训和技术支持:1. 加强运行人员的培训,提高其操作技能和维护能力,提高对轻烃回收装置运行状态的监控和调节能力。
2. 配备专业的技术支持团队,提供及时的技术咨询和解决方案,确保装置的正常运行和效率的提升。
五、借助先进的控制系统和自动化技术:1. 引入先进的控制系统,实现对轻烃回收装置的精确控制和调节,提高装置的运行效率。
2. 利用自动化技术,对装置的运行进行实时监测和数据分析,及时发现问题并采取相应措施,提高装置的运行效率和稳定性。
总结而言,要提升轻烃回收装置的运行效率,需要从设备设施的设计和操作水平、工艺参数的优化、操作管理的改进、人员培训和技术支持、控制系统和自动化技术等多个方面综合考虑和改进。
通过采取合适的措施,可以提高轻烃回收装置的回收率,降低能耗,达到节能减排和经济效益的目的。
分析轻烃回收装置节能技术
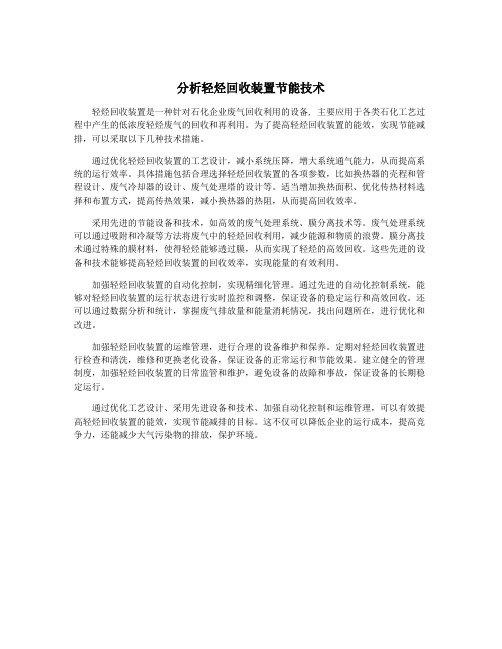
分析轻烃回收装置节能技术轻烃回收装置是一种针对石化企业废气回收利用的设备, 主要应用于各类石化工艺过程中产生的低浓度轻烃废气的回收和再利用。
为了提高轻烃回收装置的能效,实现节能减排,可以采取以下几种技术措施。
通过优化轻烃回收装置的工艺设计,减小系统压降,增大系统通气能力,从而提高系统的运行效率。
具体措施包括合理选择轻烃回收装置的各项参数,比如换热器的壳程和管程设计、废气冷却器的设计、废气处理塔的设计等。
适当增加换热面积、优化传热材料选择和布置方式,提高传热效果,减小换热器的热阻,从而提高回收效率。
采用先进的节能设备和技术,如高效的废气处理系统、膜分离技术等。
废气处理系统可以通过吸附和冷凝等方法将废气中的轻烃回收利用,减少能源和物质的浪费。
膜分离技术通过特殊的膜材料,使得轻烃能够透过膜,从而实现了轻烃的高效回收。
这些先进的设备和技术能够提高轻烃回收装置的回收效率,实现能量的有效利用。
加强轻烃回收装置的自动化控制,实现精细化管理。
通过先进的自动化控制系统,能够对轻烃回收装置的运行状态进行实时监控和调整,保证设备的稳定运行和高效回收。
还可以通过数据分析和统计,掌握废气排放量和能量消耗情况,找出问题所在,进行优化和改进。
加强轻烃回收装置的运维管理,进行合理的设备维护和保养。
定期对轻烃回收装置进行检查和清洗,维修和更换老化设备,保证设备的正常运行和节能效果。
建立健全的管理制度,加强轻烃回收装置的日常监管和维护,避免设备的故障和事故,保证设备的长期稳定运行。
通过优化工艺设计、采用先进设备和技术、加强自动化控制和运维管理,可以有效提高轻烃回收装置的能效,实现节能减排的目标。
这不仅可以降低企业的运行成本,提高竞争力,还能减少大气污染物的排放,保护环境。
轻烃回收工艺技术研究与应用课程

轻烃回收工艺技术研究与应用课程简介轻烃回收工艺技术研究与应用课程是石油与化学工程领域的一门重要课程。
该课程主要研究轻烃回收的工艺技术及其在工业应用中的重要性。
轻烃是指石油和天然气中碳数较小、分子量较轻的烃类化合物,如甲烷、乙烷、丙烷等。
这些轻烃可以作为燃料、化工原料和石油加工中的重要产品,但在传统的石油加工及化工过程中常常会产生大量的轻烃废气和废液。
轻烃回收工艺技术的研究和应用可以实现对这些轻烃资源的有效回收利用,减少环境污染,提高能源利用效率。
课程内容1.轻烃回收的意义与现状:介绍轻烃回收的重要性及其在环保、能源利用等方面的意义,讨论目前轻烃回收技术的现状和存在的问题。
2.轻烃回收的工艺与设备:介绍轻烃回收的一般工艺路线及其涉及的设备,包括分离塔、冷凝器、压缩机等,重点讲解各种回收工艺的原理和操作。
3.轻烃回收技术的研究方法:介绍轻烃回收技术研究的常用方法,包括实验研究、数值模拟、工艺优化等,培养学生的研究能力和创新思维。
4.轻烃回收工艺的应用案例:通过案例分析的方式,介绍轻烃回收技术在不同工业领域的应用,如石油加工、化工生产、能源利用等,展示轻烃回收技术在实际应用中的效果和优势。
5.轻烃回收技术的创新与发展:探讨轻烃回收技术的创新方向和未来发展趋势,鼓励学生思考如何改进和优化现有的轻烃回收工艺,提出新颖的技术方案。
学习目标通过学习轻烃回收工艺技术研究与应用课程,学生将具备以下能力:1.理解轻烃回收的意义与重要性,认识轻烃资源的价值,以及轻烃回收对环境保护和能源利用的促进作用。
2.掌握轻烃回收的基本工艺和设备,了解各种轻烃回收技术的原理和操作流程。
3.掌握轻烃回收技术的研究方法,能够进行实验研究、数值模拟和工艺优化等方面的工作。
4.了解轻烃回收技术在不同工业领域的应用案例,了解其应用效果和优势。
5.培养创新意识和能力,思考如何改进和优化现有的轻烃回收工艺,提出新颖的技术方案。
学习方式该课程采用理论讲授、实践操作和案例分析相结合的教学方式。
分析轻烃回收装置节能技术
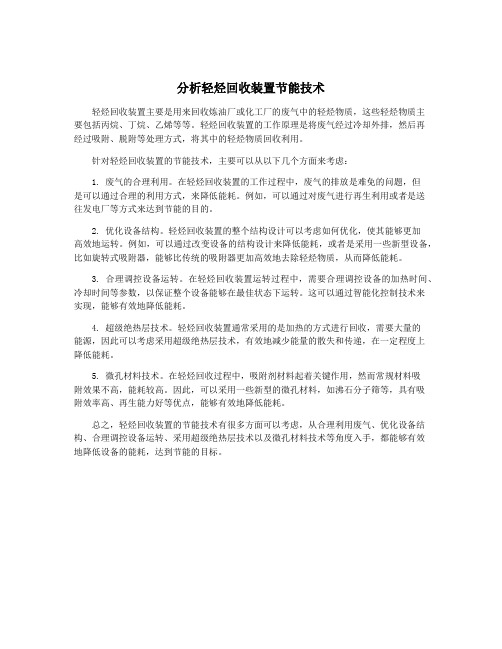
分析轻烃回收装置节能技术轻烃回收装置主要是用来回收炼油厂或化工厂的废气中的轻烃物质,这些轻烃物质主要包括丙烷、丁烷、乙烯等等。
轻烃回收装置的工作原理是将废气经过冷却外排,然后再经过吸附、脱附等处理方式,将其中的轻烃物质回收利用。
针对轻烃回收装置的节能技术,主要可以从以下几个方面来考虑:1. 废气的合理利用。
在轻烃回收装置的工作过程中,废气的排放是难免的问题,但是可以通过合理的利用方式,来降低能耗。
例如,可以通过对废气进行再生利用或者是送往发电厂等方式来达到节能的目的。
2. 优化设备结构。
轻烃回收装置的整个结构设计可以考虑如何优化,使其能够更加高效地运转。
例如,可以通过改变设备的结构设计来降低能耗,或者是采用一些新型设备,比如旋转式吸附器,能够比传统的吸附器更加高效地去除轻烃物质,从而降低能耗。
3. 合理调控设备运转。
在轻烃回收装置运转过程中,需要合理调控设备的加热时间、冷却时间等参数,以保证整个设备能够在最佳状态下运转。
这可以通过智能化控制技术来实现,能够有效地降低能耗。
4. 超级绝热层技术。
轻烃回收装置通常采用的是加热的方式进行回收,需要大量的能源,因此可以考虑采用超级绝热层技术,有效地减少能量的散失和传递,在一定程度上降低能耗。
5. 微孔材料技术。
在轻烃回收过程中,吸附剂材料起着关键作用,然而常规材料吸附效果不高,能耗较高。
因此,可以采用一些新型的微孔材料,如沸石分子筛等,具有吸附效率高、再生能力好等优点,能够有效地降低能耗。
总之,轻烃回收装置的节能技术有很多方面可以考虑,从合理利用废气、优化设备结构、合理调控设备运转、采用超级绝热层技术以及微孔材料技术等角度入手,都能够有效地降低设备的能耗,达到节能的目标。
轻烃回收装置液化气塔操作平衡分析及改进措施
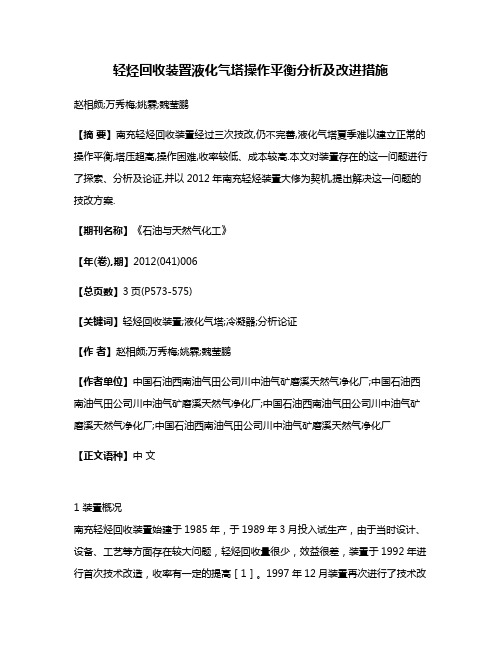
轻烃回收装置液化气塔操作平衡分析及改进措施赵相颇;万秀梅;姚霖;魏莹鹏【摘要】南充轻烃回收装置经过三次技改,仍不完善,液化气塔夏季难以建立正常的操作平衡,塔压超高,操作困难,收率较低、成本较高.本文对装置存在的这一问题进行了探索、分析及论证,并以2012年南充轻烃装置大修为契机,提出解决这一问题的技改方案.【期刊名称】《石油与天然气化工》【年(卷),期】2012(041)006【总页数】3页(P573-575)【关键词】轻烃回收装置;液化气塔;冷凝器;分析论证【作者】赵相颇;万秀梅;姚霖;魏莹鹏【作者单位】中国石油西南油气田公司川中油气矿磨溪天然气净化厂;中国石油西南油气田公司川中油气矿磨溪天然气净化厂;中国石油西南油气田公司川中油气矿磨溪天然气净化厂;中国石油西南油气田公司川中油气矿磨溪天然气净化厂【正文语种】中文1 装置概况南充轻烃回收装置始建于1985年,于1989年3月投入试生产,由于当时设计、设备、工艺等方面存在较大问题,轻烃回收量很少,效益很差,装置于1992年进行首次技术改造,收率有一定的提高[1]。
1997年12月装置再次进行了技术改造,将核心设备热分离机更换为透平膨胀机,装置处理气量由原来的10×10 4m3/d提高到14×10 4 m3/d。
2005年9月~10月,装置进行了第三次大幅度的工艺、仪表技术改造,改造后装置设计日处理气量20×10 4 m3/d,轻烃回收率有较大提高。
经过2006年试运行,装置精馏系统暴露出了一系列工程设计、设备、仪表方面的问题,两塔操作极不平稳。
2008年底大修时,对液化气冷凝器、回流罐及附属管线进行了保冷改造,经过生产证实,效果仍然不理想,尤其是液化气塔夏季难以建立正常的操作平衡,塔压超高,操作困难、收率较低、成本较高。
2 液化气塔的顶温控制工艺流程及操作现状2.1 液化气塔顶温控制工艺流程理论上塔顶出来的液化气气相(1.2 MPa,60℃±5℃)经液化气冷凝器冷-301冷却后进入回流罐,回流罐液位要求控制在40%~60%,从回流罐出来的液化气(30℃±5℃)经回流泵加压后分成两路,一路经产品调节阀LIC-05至储罐,另一部分作为塔顶回流,通过塔顶温度与回流泵出口流量FIC-G01,串级调节控制塔顶温度。
- 1、下载文档前请自行甄别文档内容的完整性,平台不提供额外的编辑、内容补充、找答案等附加服务。
- 2、"仅部分预览"的文档,不可在线预览部分如存在完整性等问题,可反馈申请退款(可完整预览的文档不适用该条件!)。
- 3、如文档侵犯您的权益,请联系客服反馈,我们会尽快为您处理(人工客服工作时间:9:00-18:30)。
图1 南充轻烃回收装置工艺流程图注:1,3.原料气分离器;2,10,13.冷却器;4.干燥器;5.加热炉;6.冷箱(主、副换热器、低温分离器);7.热分离机;8.脱乙烷塔;9.脱丙丁烷塔;11.回流罐;12.回流泵*蒋洪,1966年生,讲师,硕士;1986年毕业于西南石油学院储运专业,现在西南石油学院油气储运教研室从事教学和科研工作。
地址:(637001)四川省南充市。
电话:(0817)2603433转3349。
南充轻烃回收装置工艺改造方案研究蒋 洪* 梁 政(西南石油学院)吴小朴 龙 平(南充天然气公司)蒋洪等.南充轻烃回收装置工艺改造方案研究.天然气工业,1998;18(5):80~83摘 要 四川南充轻烃回收装置采用热分离机制冷工艺,装置每天生产液化气1.5t ,轻油1.0t,热分离机的等熵效率仅为35%~40%,丙烷收率不足15%,回收装置经济效益较差。
因此,为了提高回收装置的产品收率和经济效益,对其工艺装置进行技术改造十分必要。
由于热分离机的等熵效率低,制冷效果差,热分离机出口含大量的液烃未回收,脱乙烷塔顶温度比原设计值偏高,造成回收装置丙烷收率低。
采用SHBWR 状态方程作为工艺计算模型,通过工艺计算和方案对比分析,在充分利用现有流程中的设备、节省改造费用的条件下,提出了透平膨胀机制冷、二次分离的工艺改造方案。
改造后的轻烃回收装置于1997年12月投产,与原有装置相比,降低了制冷温度,提高了液烃收率,达到了工艺设计的改造效果。
主题词 轻烃回收装置 技术 工艺 计算 研究 运行南充轻烃回收装置的技术现状四川南充轻烃回收装置于1989年3月正式投产,生产液化气和轻油,采用热分离机制冷工艺,其工艺流程如图1所示,该工艺流程的轻烃回收路线为:原料气y 脱水y 热分离机制冷y 低温分离y 液烃分馏y 液化气和轻油原有装置每天生产液化气1.5t,轻油1.0t 。
装置正常运行时,流程中低温分离器的温度为-40e ,热分离机的出口温度为-69e ,脱乙烷塔顶温度为-20e 。
通过工艺计算可知,热分离机的等熵效率仅为35%~40%,丙烷收率不足15%,回收装置的经济效益较差。
因此,针对南充现有轻烃回收装置#80#化工与综合利用天 然 气 工 业 1998年9月的技术现状,分析造成现有装置丙烷收率低的原因,对其工艺装置进行技术改造,提高回收装置的产品收率和经济效益,具有十分重要的现实意义。
工艺计算模型11,22本文采用SHBWR状态方程建立了气液平衡模型,在此基础上进一步开发了部分气化和部分冷凝、节流制冷、膨胀机制冷、精馏计算等工艺过程的计算程序。
其主要关系式如下:(1)压力方程p=Q RT+B0RT-A0-C0T2+D0T3-E0T4置工Q2+bRT-a-dT每天Q3+A a+dT较差Q6+c Q3T2(1+C Q2)ex p(-C Q2)(1)式中:p为系统压力,M Pa;T为系统温度,K;Q为气相或液相的密度,kmol/m3;R为气体常数,取8.3143@10-3kJ/(kmol#K);B0、A0、C0、D0、E0、a、b、c、d、A、C为状态方程的11个参数,表达式见文献112。
(2)气、液相等温焓差H-H0=B0RT-2A0-4C0T2+5D0T3-6E0T4等熵Q+1 22bRT-3a-4dTQ2+15A6a+7dTFI Q5+cC T23-3+12C Q2-C2Qe u4exp(-C Q2.) S(2)式中:H为气相或液相在p、T下的焓值,kJ/kmol;H0为理想气体混合物的焓值,kJ/kmol。
(3)气、液相等温熵差S-S 0=-R l n(Q RT)-B0R+2C0T3-3D0T4+4E0T5hn Q-1 2bR+dT2ecQ2+A d Q5T2+2cC T31-1+12C Q2f texp(-C Q2io)(3)式中:S为气相或液相在p、T下的熵值,kJ/(kmol# K);S0为理想气体混合物的熵值,kJ/(kmol#K)。
工艺方案研究1.设计的基础数据装置处理量14@104m3/d,原料气压力1.9~ 2.1MPa(绝),干气外输压力0.6~0.7MPa(绝),原料气组分及组成(摩尔百分数)见表1。
2.丙烷收率低的原因分析根据轻烃回收装置的工艺流程及气源条件,通过工艺计算和分析,造成回收装置丙烷收率低的原因有以下三方面。
表1原料气组分及组成N2CO2C1C2C31.0410.2688.19 6.332.48iC4nC4iC5nC5C6+0.360.6430.1490.2070.34(1)采用热分离机制冷工艺,由于热分离机的等熵效率低,在有限差压下制冷效果差。
如果取等熵效率为50%,通过工艺计算,制冷温度为-49e,丙烷收率为36.9%。
而热分离机的等熵效率仅有35%~40%,如果考虑压损、冷损等因素,则实际丙烷收率远低于36.9%。
(2)工艺流程采用一次分离回收丙烷及以上重组分,而热分离机出口含大量的液烃未回收,造成较多的液烃损失。
如果制冷温度取-49e,热分离机出口液烃中的丙烷含量占原料气中丙烷含量的18%。
(3)回收装置中脱乙烷塔顶温度为-20e,比原设计值高近15e,造成脱乙烷塔顶丙烷损失量较大。
3.方案对比通过对回收装置进行工艺计算和分析可知,为了降低制冷温度,提高丙烷收率,必须改变制冷方式和工艺流程。
根据现有气源条件,对多种工艺方案对比和分析,筛选出二种可能的工艺方案:¹采用透平膨胀机制冷;º冷剂制冷+透平膨胀机制冷。
二种工艺方案的流程示意图见图2、3。
运用自己开发的电算程序对二种方案进行工艺设计计算,主要设计计算结果列于表2。
从表2可知,选择外部冷剂加透平膨胀机制冷工艺,制冷温度为-82.18e,丙烷收率为84.97%,与原装置设计参数相比,其主要工艺参数变化较大,经对流程中各单体设备的工艺设计和校核计算表图2透平膨胀机制冷工艺流程示意图#81#第18卷第5期天然气工业化工与综合利用图3外部冷剂+膨胀机制冷工艺流程示意图表2工艺方案计算结果项目方案一方案二气体处理量(m3/d)14@10414@104冷剂预冷温度(e)-0.0膨胀机的等熵效率0.750.75低温分离器1压力(M Pa) 2.1 2.1温度(e)-48.60-82.18液化量(kg/h)411.97997.72膨胀机膨胀端出口压力(M Pa)0.70.7温度(e)-85.76-115.26脱乙烷塔压力(M Pa) 1.5 1.5塔顶温度(e)-29.51-43.51塔釜温度(e)67.8761.98回收率(%)C366.7084.97 C3+C476.1388.45 C3+82.9092.18 C5+98.8398.75液化气产量(kg/h)315.18369.93轻油产量(kg/h)136.95136.87明,除增设外部冷剂制冷机组和更换热分离机外,原有流程中的大部分设备都需要更换,改造费用投资大。
而选择透平膨胀机制冷工艺,只需将热分离机更换为透平膨胀机和增设一台低温分离器,在国内能选到适合本工况条件的透平膨胀机,并且原有装置中的大部分设备都能利用,同时又保证了丙烷有较高的收率,降低了改造费用,因此,选择透平膨胀机制冷工艺方案是南充轻烃回收装置的合理的工艺改造方案。
工艺改造原则流程针对南充轻烃回收装置,通过工艺计算和方案对比分析,确定了合理的工艺改造方案,其工艺原则流程方框图如图4所示。
图4工艺原则流程方框图该工艺流程具有以下特点。
(1)采用等熵效率高的膨胀机制冷、二次分离的工艺流程,降低了制冷温度,回收膨胀机出口产生的液烃,提高了丙烷收率。
(2)由于制冷温度的降低和脱乙烷塔进料量的增大,给脱乙烷塔顶冷凝器提供了足够的冷量,保证了脱乙烷塔的正常工作。
(3)充分利用现有装置的设备,节省了改造费用。
改造后的装置运行状况改造后的南充轻烃回收装置,于1997年12月投产运行,因装置改造工期短,改造后的回收装置采用了透平膨胀机制冷,没有增设图4中低温分离器2,未回收膨胀机出口处的液烃,采用一次分离流程,装置的日处理量为14@104m3,原料气压力为1.8 M Pa时,装置的主要运行参数见表3。
从表3可见,改造后的轻烃回收装置与原有装置相比,降低了制冷温度,提高了液烃收率,增加了液化气和轻油的产量,达到了工艺设计的改造效果。
表3改造后回收装置运行的主要参数低温分离器1膨胀端出口处脱乙烷塔产品量压力(M Pa)温度(e)压力(M Pa)温度(e)塔顶温度(e)液化气(t/d)轻油(t/d)1.9-60.60.6-95.4-30.0 4.0 1.5结论及建议(1)现有轻烃回收装置中热分离机的等熵效率仅为35%~40%,制冷效果较差,丙烷收率不足15%。
#82#化工与综合利用天然气工业1998年9月(2)采用透平膨胀机更换原有装置中的热分离机,降低了制冷温度,提高了产品收率。
充分利用现有回收装置的设备,节省了改造费用。
(3)因膨胀机出口处液烃含量较大,建议回收这一部分液烃,进一步提高液烃收率。
(4)对结构简单、价格较低、且不受带液影响的热分离机进行研究和改进,使热分离机在我国轻烃回收工艺中得到进一步推广应用。
参考文献1郭天民等编.多元气)液平衡和精馏.北京:化学工业出版社,1983:263~2732白执松,罗光熹编著.石油及天然气物性预测.北京:石油工业出版社,1995:49~50(收稿日期1998-03-04编辑王瑞兰)综合治理丹8井提高气井生产能力四川石油管理局川南矿区魏光宇基本情况四川石油管理局川南矿区丹凤气田的丹8井为单独裂缝系统,产层为P1m2a,气层中部井深2982m,地质储量2.8@108m3。
该井于1982年1月14日投产,初期产量在10@104m3/d左右。
产气量缓慢逐年下降至1988年的5@104m3/d左右,生产正常,不产地层水,产少量凝析水。
1990年4月19日开始泡排助排生产,较好地保证了该井在井口压力接近输压的情况下,连续稳定的生产。
1992年2月28日,油管被掉入井内的一支外径为36mm、长1425mm、重6.5kg的CY613)A型压力计堵塞,另一方面环空中安装ª127.0mm封隔器,阻塞了环空的通道。
经过多次开关井和/诱导放空0后发现油管不能生产,开井差压降为零(放空),套管勉强能生产(估计封隔器部分坏),但只能生产二至三天就平输压停产,月产气量20@104~30@ 104m3。
由于套管带水不好,产量逐月下降,有被水淹停产的危险。
生产能力低的原因(1)气井剩余储量少,仅为0.56@ 108m3。
(2)能量低,月平均油压仅为1.60 M Pa。
由于压力低,开井后常平输压而关井,所以该井间歇生产。