石油炼化公司的各个装置工艺的流程图大全及其简介
石油炼化常用的七种工艺流程
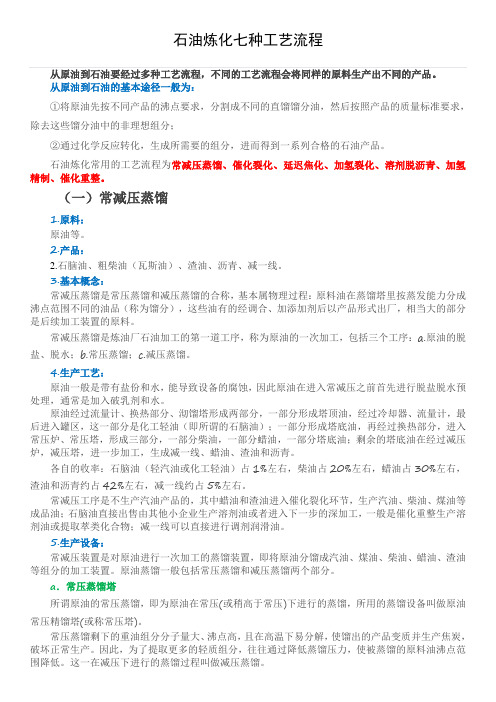
石油炼化七种工艺流程从原油到石油要经过多种工艺流程,不同的工艺流程会将同样的原料生产出不同的产品。
从原油到石油的基本途径一般为:①将原油先按不同产品的沸点要求,分割成不同的直馏馏分油,然后按照产品的质量标准要求,除去这些馏分油中的非理想组分;②通过化学反应转化,生成所需要的组分,进而得到一系列合格的石油产品。
石油炼化常用的工艺流程为常减压蒸馏、催化裂化、延迟焦化、加氢裂化、溶剂脱沥青、加氢精制、催化重整。
(一)常减压蒸馏1.原料:原油等。
2.产品:2.石脑油、粗柴油(瓦斯油)、渣油、沥青、减一线。
3.基本概念:常减压蒸馏是常压蒸馏和减压蒸馏的合称,基本属物理过程:原料油在蒸馏塔里按蒸发能力分成沸点范围不同的油品(称为馏分),这些油有的经调合、加添加剂后以产品形式出厂,相当大的部分是后续加工装置的原料。
常减压蒸馏是炼油厂石油加工的第一道工序,称为原油的一次加工,包括三个工序:a.原油的脱盐、脱水;b.常压蒸馏;c.减压蒸馏。
4.生产工艺:原油一般是带有盐份和水,能导致设备的腐蚀,因此原油在进入常减压之前首先进行脱盐脱水预处理,通常是加入破乳剂和水。
原油经过流量计、换热部分、沏馏塔形成两部分,一部分形成塔顶油,经过冷却器、流量计,最后进入罐区,这一部分是化工轻油(即所谓的石脑油);一部分形成塔底油,再经过换热部分,进入常压炉、常压塔,形成三部分,一部分柴油,一部分蜡油,一部分塔底油;剩余的塔底油在经过减压炉,减压塔,进一步加工,生成减一线、蜡油、渣油和沥青。
各自的收率:石脑油(轻汽油或化工轻油)占1%左右,柴油占20%左右,蜡油占30%左右,渣油和沥青约占42%左右,减一线约占5%左右。
常减压工序是不生产汽油产品的,其中蜡油和渣油进入催化裂化环节,生产汽油、柴油、煤油等成品油;石脑油直接出售由其他小企业生产溶剂油或者进入下一步的深加工,一般是催化重整生产溶剂油或提取萃类化合物;减一线可以直接进行调剂润滑油。
石油化工催化裂化装置工艺流程图

炼油生产安全技术-催化裂化的装置简介类型及工艺流程催化裂化技术的发展密切依赖于催化剂的发展。
有了微球催化剂,才出现了流化床催化裂化装置;分子筛催化剂的出现,才发展了提升管催化裂化.选用适宜的催化剂对于催化裂化过程的产品产率、产品质量以及经济效益具有重大影响。
催化裂化装置通常由三大部分组成,即反应¾再生系统、分馏系统和吸收稳定系统。
其中反应––再生系统是全装置的核心,现以高低并列式提升管催化裂化为例,对几大系统分述如下:㈠反应––再生系统新鲜原料(减压馏分油)经过一系列换热后与回炼油混合,进入加热炉预热到370℃左右,由原料油喷嘴以雾化状态喷入提升管反应器下部,油浆不经加热直接进入提升管,与来自再生器的高温(约650℃~700℃)催化剂接触并立即汽化,油气与雾化蒸汽及预提升蒸汽一起携带着催化剂以7米/秒~8米/秒的高线速通过提升管,经快速分离器分离后,大部分催化剂被分出落入沉降器下部,油气携带少量催化剂经两级旋风分离器分出夹带的催化剂后进入分馏系统。
积有焦炭的待生催化剂由沉降器进入其下面的汽提段,用过热蒸气进行汽提以脱除吸附在催化剂表面上的少量油气。
待生催化剂经待生斜管、待生单动滑阀进入再生器,与来自再生器底部的空气(由主风机提供)接触形成流化床层,进行再生反应,同时放出大量燃烧热,以维持再生器足够高的床层温度(密相段温度约650℃~68 0℃)。
再生器维持0.15MPa~0。
25MPa (表)的顶部压力,床层线速约0。
7米/秒~1。
0米/秒。
再生后的催化剂经淹流管,再生斜管及再生单动滑阀返回提升管反应器循环使用。
烧焦产生的再生烟气,经再生器稀相段进入旋风分离器,经两级旋风分离器分出携带的大部分催化剂,烟气经集气室和双动滑阀排入烟囱。
再生烟气温度很高而且含有约5%~10% CO,为了利用其热量,不少装置设有CO 锅炉,利用再生烟气产生水蒸汽。
对于操作压力较高的装置,常设有烟气能量回收系统,利用再生烟气的热能和压力作功,驱动主风机以节约电能。
石油化工49张装置流程图!概要

常减压电脱盐装置原则流程脱后原油去换热CDU装置原则流程VDU装置原则流程轻烃回收装置原则流程压缩干气补充新氢热低分反应进料泵原料升压泵R-101R-102热高分加氢裂化反应部分流程图加氢裂化分馏部分流程图(一)加氢裂化分馏部分流程图(二)粗汽油凝缩油泵吸收塔底泵补充吸收泵间凝液泵催化吸收稳定部分流程图干气脱硫贫液泵液化气脱硫贫液泵常减压液化气至脱硫醇常减压液化气进料泵加氢裂化液化气进料泵过剩空气至焚烧炉液化气脱硫醇碱液再生部分流程图汽油进料泵活化剂泵精汽油泵防胶剂注入泵防胶剂配制泵汽油脱硫脱硫醇装置流程图碳二、碳三馏分脱乙烷塔回流泵丙烷馏分泵丙烯塔回流泵丙烯产品泵脱戊烷塔回流及产品泵戊烷馏分泵气体分馏装置流程图缓冲罐加氢精加氢反应油连续重整预加氢反应部分流程图预加氢反应液相连续重整预加氢分馏部分流程图重整反应器三连续重整反应部分流程图汽油至脱戊烷塔分馏生构化加氢至管网装置来连续重整再接触部分流程图连续重整后分馏部分流程图统连续重整再生部分流程图1.0MPa连续重整热工部分流程图塔来缓冲罐异构化装置流程图苯抽提装置流程图原料油缓冲罐原料油泵新氢酸性水柴油泵分馏塔底重沸炉泵石脑油塔顶气柴油加氢分馏部分流程图低分油航煤加氢反应部分流程图航煤加氢分馏部分流程图酸性气分液制硫燃烧制硫余热锅冷凝冷却转化成型硫封液硫尾气分液硫磺回收制硫部分流程图尾气焚烧炉硫磺回收尾气部分流脱硫富液闪蒸脱硫溶剂储脱硫溶剂再生再生塔顶回流溶剂再生装置流程图汽提塔顶分液罐酸性水汽提装置流程丙烯洗涤塔PP装置闪蒸、汽蒸部分流程图PPPP装置造粒部分流程图储运系统装置、罐区油品系统管线冲洗原则流程图。
石油炼化常用的七种工艺流程样本
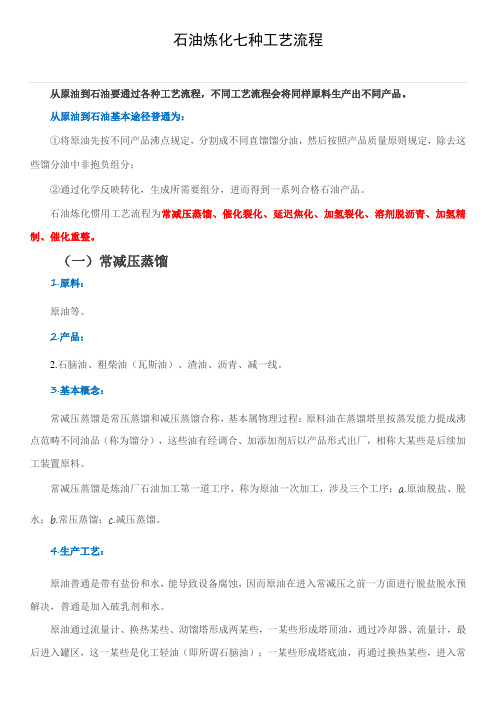
石油炼化七种工艺流程从原油到石油要通过各种工艺流程,不同工艺流程会将同样原料生产出不同产品。
从原油到石油基本途径普通为:①将原油先按不同产品沸点规定,分割成不同直馏馏分油,然后按照产品质量原则规定,除去这些馏分油中非抱负组分;②通过化学反映转化,生成所需要组分,进而得到一系列合格石油产品。
石油炼化惯用工艺流程为常减压蒸馏、催化裂化、延迟焦化、加氢裂化、溶剂脱沥青、加氢精制、催化重整。
(一)常减压蒸馏1.原料:原油等。
2.产品:2.石脑油、粗柴油(瓦斯油)、渣油、沥青、减一线。
3.基本概念:常减压蒸馏是常压蒸馏和减压蒸馏合称,基本属物理过程:原料油在蒸馏塔里按蒸发能力提成沸点范畴不同油品(称为馏分),这些油有经调合、加添加剂后以产品形式出厂,相称大某些是后续加工装置原料。
常减压蒸馏是炼油厂石油加工第一道工序,称为原油一次加工,涉及三个工序:a.原油脱盐、脱水;b.常压蒸馏;c.减压蒸馏。
4.生产工艺:原油普通是带有盐份和水,能导致设备腐蚀,因而原油在进入常减压之前一方面进行脱盐脱水预解决,普通是加入破乳剂和水。
原油通过流量计、换热某些、沏馏塔形成两某些,一某些形成塔顶油,通过冷却器、流量计,最后进入罐区,这一某些是化工轻油(即所谓石脑油);一某些形成塔底油,再通过换热某些,进入常压炉、常压塔,形成三某些,一某些柴油,一某些蜡油,一某些塔底油;剩余塔底油在通过减压炉,减压塔,进一步加工,生成减一线、蜡油、渣油和沥青。
各自收率:石脑油(轻汽油或化工轻油)占1%左右,柴油占20%左右,蜡油占30%左右,渣油和沥青约占42%左右,减一线约占5%左右。
常减压工序是不生产汽油产品,其中蜡油和渣油进入催化裂化环节,生产汽油、柴油、煤油等成品油;石脑油直接出售由其她小公司生产溶剂油或者进入下一步深加工,普通是催化重整生产溶剂油或提取萃类化合物;减一线可以直接进行调剂润滑油。
5.生产设备:常减压装置是对原油进行一次加工蒸馏装置,即将原油分馏成汽油、煤油、柴油、蜡油、渣油等组分加工装置。
石油炼化常用的七种工艺流程
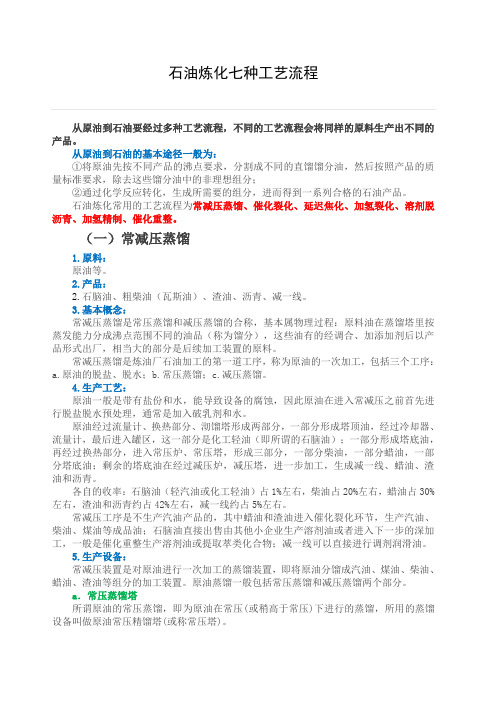
石油炼化七种工艺流程从原油到石油要经过多种工艺流程,不同的工艺流程会将同样的原料生产出不同的产品。
从原油到石油的基本途径一般为:①将原油先按不同产品的沸点要求,分割成不同的直馏馏分油,然后按照产品的质量标准要求,除去这些馏分油中的非理想组分;②通过化学反应转化,生成所需要的组分,进而得到一系列合格的石油产品。
石油炼化常用的工艺流程为常减压蒸馏、催化裂化、延迟焦化、加氢裂化、溶剂脱沥青、加氢精制、催化重整。
(一)常减压蒸馏1.原料:原油等。
2.产品:2.石脑油、粗柴油(瓦斯油)、渣油、沥青、减一线。
3.基本概念:常减压蒸馏是常压蒸馏和减压蒸馏的合称,基本属物理过程:原料油在蒸馏塔里按蒸发能力分成沸点范围不同的油品(称为馏分),这些油有的经调合、加添加剂后以产品形式出厂,相当大的部分是后续加工装置的原料。
常减压蒸馏是炼油厂石油加工的第一道工序,称为原油的一次加工,包括三个工序:a.原油的脱盐、脱水;b.常压蒸馏;c.减压蒸馏。
4.生产工艺:原油一般是带有盐份和水,能导致设备的腐蚀,因此原油在进入常减压之前首先进行脱盐脱水预处理,通常是加入破乳剂和水。
原油经过流量计、换热部分、沏馏塔形成两部分,一部分形成塔顶油,经过冷却器、流量计,最后进入罐区,这一部分是化工轻油(即所谓的石脑油);一部分形成塔底油,再经过换热部分,进入常压炉、常压塔,形成三部分,一部分柴油,一部分蜡油,一部分塔底油;剩余的塔底油在经过减压炉,减压塔,进一步加工,生成减一线、蜡油、渣油和沥青。
各自的收率:石脑油(轻汽油或化工轻油)占1%左右,柴油占20%左右,蜡油占30%左右,渣油和沥青约占42%左右,减一线约占5%左右。
常减压工序是不生产汽油产品的,其中蜡油和渣油进入催化裂化环节,生产汽油、柴油、煤油等成品油;石脑油直接出售由其他小企业生产溶剂油或者进入下一步的深加工,一般是催化重整生产溶剂油或提取萃类化合物;减一线可以直接进行调剂润滑油。
石油炼化常用的七种工艺流程
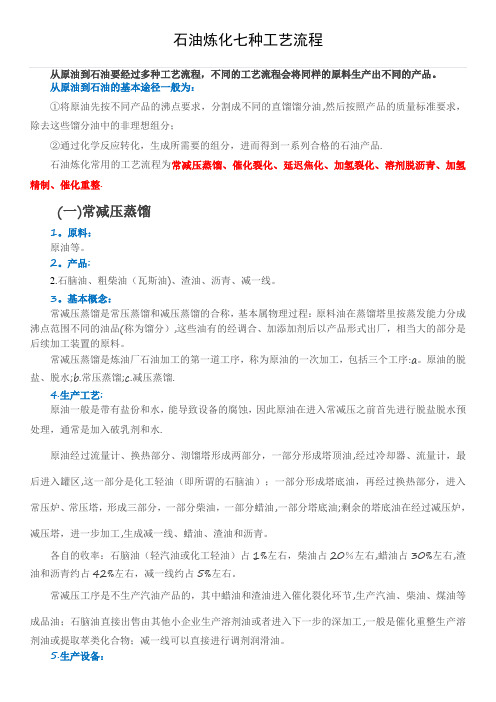
石油炼化七种工艺流程从原油到石油要经过多种工艺流程,不同的工艺流程会将同样的原料生产出不同的产品。
从原油到石油的基本途径一般为:①将原油先按不同产品的沸点要求,分割成不同的直馏馏分油,然后按照产品的质量标准要求,除去这些馏分油中的非理想组分;②通过化学反应转化,生成所需要的组分,进而得到一系列合格的石油产品.石油炼化常用的工艺流程为常减压蒸馏、催化裂化、延迟焦化、加氢裂化、溶剂脱沥青、加氢精制、催化重整.(一)常减压蒸馏1。
原料:原油等。
2。
产品:2.石脑油、粗柴油(瓦斯油)、渣油、沥青、减一线。
3。
基本概念:常减压蒸馏是常压蒸馏和减压蒸馏的合称,基本属物理过程:原料油在蒸馏塔里按蒸发能力分成沸点范围不同的油品(称为馏分),这些油有的经调合、加添加剂后以产品形式出厂,相当大的部分是后续加工装置的原料。
常减压蒸馏是炼油厂石油加工的第一道工序,称为原油的一次加工,包括三个工序:a。
原油的脱盐、脱水;b.常压蒸馏;c.减压蒸馏.4.生产工艺:原油一般是带有盐份和水,能导致设备的腐蚀,因此原油在进入常减压之前首先进行脱盐脱水预处理,通常是加入破乳剂和水.原油经过流量计、换热部分、沏馏塔形成两部分,一部分形成塔顶油,经过冷却器、流量计,最后进入罐区,这一部分是化工轻油(即所谓的石脑油);一部分形成塔底油,再经过换热部分,进入常压炉、常压塔,形成三部分,一部分柴油,一部分蜡油,一部分塔底油;剩余的塔底油在经过减压炉,减压塔,进一步加工,生成减一线、蜡油、渣油和沥青。
各自的收率:石脑油(轻汽油或化工轻油)占1%左右,柴油占20%左右,蜡油占30%左右,渣油和沥青约占42%左右,减一线约占5%左右。
常减压工序是不生产汽油产品的,其中蜡油和渣油进入催化裂化环节,生产汽油、柴油、煤油等成品油;石脑油直接出售由其他小企业生产溶剂油或者进入下一步的深加工,一般是催化重整生产溶剂油或提取萃类化合物;减一线可以直接进行调剂润滑油。
石油炼化常用的七种工艺流程

石油炼化七种工艺流程从原油到石油要经过多种工艺流程,不同的工艺流程会将同样的原料生产出不同的产品。
从原油到石油的基本途径一般为:①将原油先按不同产品的沸点要求,分割成不同的直馏馏分油,然后按照产品的质量标准要求,除去这些馏分油中的非理想组分;②通过化学反应转化,生成所需要的组分,进而得到一系列合格的石油产品。
石油炼化常用的工艺流程为常减压蒸馏、催化裂化、延迟焦化、加氢裂化、溶剂脱沥青、加氢精制、催化重整。
(一)常减压蒸馏1.原料:原油等。
2.产品:2.石脑油、粗柴油(瓦斯油)、渣油、沥青、减一线。
3.基本概念:常减压蒸馏是常压蒸馏和减压蒸馏的合称,基本属物理过程:原料油在蒸馏塔里按蒸发能力分成沸点范围不同的油品(称为馏分),这些油有的经调合、加添加剂后以产品形式出厂,相当大的部分是后续加工装置的原料。
常减压蒸馏是炼油厂石油加工的第一道工序,称为原油的一次加工,包括三个工序:a.原油的脱盐、脱水;b.常压蒸馏;c.减压蒸馏。
4.生产工艺:原油一般是带有盐份和水,能导致设备的腐蚀,因此原油在进入常减压之前首先进行脱盐脱水预处理,通常是加入破乳剂和水。
原油经过流量计、换热部分、沏馏塔形成两部分,一部分形成塔顶油,经过冷却器、流量计,最后进入罐区,这一部分是化工轻油(即所谓的石脑油);一部分形成塔底油,再经过换热部分,进入常压炉、常压塔,形成三部分,一部分柴油,一部分蜡油,一部分塔底油;剩余的塔底油在经过减压炉,减压塔,进一步加工,生成减一线、蜡油、渣油和沥青。
各自的收率:石脑油(轻汽油或化工轻油)占1%左右,柴油占20%左右,蜡油占30%左右,渣油和沥青约占42%左右,减一线约占5%左右。
常减压工序是不生产汽油产品的,其中蜡油和渣油进入催化裂化环节,生产汽油、柴油、煤油等成品油;石脑油直接出售由其他小企业生产溶剂油或者进入下一步的深加工,一般是催化重整生产溶剂油或提取萃类化合物;减一线可以直接进行调剂润滑油。
石油炼制过程和主要工艺简介

石油炼制的主要过程和工艺简介石油、天然气是不同烃化合物的混合物,简单作为燃料是极大的浪费,只有通过加工处理,炼制出不同的产品,才能充分发挥其巨大的经济价值。
石油经过加工,大体可获得以下几大类的产品:汽油类(航空汽油、军用汽油、溶剂汽油);煤油(灯用煤油、动力煤油、航空煤油);柴油(轻柴油、中柴油、重柴油);燃料油;润滑油;润滑油脂以及其他石油产品(凡士林、石油蜡、沥青、石油焦炭等)。
有的油品经过深加工,又获得质量更高或新的产品。
石油加工,主要是指对原油的加工。
世界各国基本上都是通过一次加工、二次加工以生产燃料油品,三次加工主要生产化工产品。
原油在炼厂加工前,还需经过脱盐、脱水的预处理,使之进入蒸馏装置时,其各种盐类的总含盐量低于5mg/L,主要控制其对加工设备、管线的腐蚀和堵塞。
原油一次加工,主要采用常压、减压蒸馏的简单物理方法将原油切割为沸点范围不同、密度大小不同的多种石油馏分。
各种馏分的分离顺序主要取决于分子大小和沸点高低。
在常压蒸馏过程中,汽油的分子小、沸点低(50~200℃),首先馏出,随之是煤油(60~5℃)、柴油(200~0℃)、残余重油。
重油经减压蒸馏又可获得一定数量的润滑油的基础油或半成品(蜡油),最后剩下渣油(重油)。
一次加工获得的轻质油品(汽油、煤油、柴油)还需进一步精制、调配,才可做为合格油品投入市场。
我国一次加工原油,只获得25%~40%的直馏轻质油品和20%左右的蜡油。
原油二次加工,主要用化学方法或化学-物理方法,将原油馏分进一步加工转化,以提高某种产品收率,增加产品品种,提高产品质量。
进行二次加工的工艺很多,要根据油品性质和设计要求进行选择。
主要有催化裂化、催化重整、焦化、减粘、加氢裂化、溶剂脱沥青等。
如对一次加工获得的重质半成品(蜡油)进行催化裂化,又可将蜡油的40%左右转化为高牌号车用汽油,30%左右转化为柴油,20%左右转化为液化气、气态烃和干气。
如以轻汽油(石脑油)为原料,采用催化重整工艺加工,可生产高辛烷值汽油组分(航空汽油)或化工原料芳烃(苯、二甲苯等),还可获得副产品氢气。
- 1、下载文档前请自行甄别文档内容的完整性,平台不提供额外的编辑、内容补充、找答案等附加服务。
- 2、"仅部分预览"的文档,不可在线预览部分如存在完整性等问题,可反馈申请退款(可完整预览的文档不适用该条件!)。
- 3、如文档侵犯您的权益,请联系客服反馈,我们会尽快为您处理(人工客服工作时间:9:00-18:30)。
炼化公司的各个装置工艺的流程图大全及其简介
从油田送往炼油厂的原油往往含盐(主要是氧化物)带水(溶于油或呈乳化状态),
可导致设备的腐蚀,在设备内壁结垢和影响成品油的组成,需在加工前脱除。
电脱盐基本原理:
为了脱掉原油中的盐份,要注入一定数量的新鲜水,使原油中的盐充分溶解于水中,形成石油与水的乳化液。
在强弱电场与破乳剂的作用下,破坏了乳化液的保护膜,使水滴由小变大,不断聚合形成较大的水滴,借助于重力与电场的作用沉降下来与油分离,因为盐溶于水,所以脱水的过程也就是脱盐的过程。
CDU装置即常压蒸馏部分
常压蒸馏原理:
精馏又称分馏,它是在精馏塔内同时进行的液体多次部分汽化和汽体多次部分冷凝的过程。
原油之所以能够利用分馏的方法进行分离,其根本原因在于原油内部的各组分的沸点不同。
在原油加工过程中,把原油加热到360~370℃左右进入常压分馏塔,在汽化段进行部分汽化,其中汽油、煤油、轻柴油、重柴油这些较低沸点的馏分优先汽化成为气体,而蜡油、渣油仍为液体。
VDU装置即减压蒸馏部分
减压蒸馏原理:
液体沸腾必要条件是蒸汽压必须等于外界压力。
降低外界压力就等效于降低液体的沸点。
压力愈小,沸点降的愈低。
如果蒸馏过程的压力低于大气压以下进行,这种过程称为减压蒸馏。
轻烃回收装置是轻烃的回收设备,采用成熟、可靠的工艺技术,将天然气中比甲烷或乙烷更重的组分以液态形式回收。
RDS即渣油加氢装置,渣油加氢技术包含固定床渣油加氢处理、切换床渣油加氢处理、移动床渣油加氢处理、沸腾床渣油加氢处理、沸腾床渣油加氢裂化、悬浮床渣油加氢裂化、渣油加氢一体化技术及相应的组合工艺技术。
加氢裂化,是一种石化工业中的工艺,即石油炼制过程中在较高的压力和温度下,氢气经催化剂作用使重质油发生加氢、裂化和异构化反应,转化为轻质油(汽油、煤油、柴油或催化裂化、裂解制烯烃的原料)的加工过程。
反应-再生系统是催化裂化装置的核心,该系统由反应和再生部分组成。
反应部分主要有:
1.在提升管下端设置预提升段,提升介质可用蒸汽或干气(或两者混合使用);
2.根据原料油、回炼油、油浆的性质,设置多层进料喷嘴,选择适宜的喷嘴形式和进料位置;
3.增设提升管温度控制系统;
4.在提升管出口安装油气快速分离系统;
5.设置汽提段,沉降器旋风分离器回收下来的催化剂,在汽提段用过热蒸汽将其中夹带的油气置换出来后进入再生器。
再生部分主要有:
1.再生器设有辅助燃烧室,用于开工时加热主风、再生器升温;
2.再生器内设有主风分布器,实现合理布风,保证正常流化和催化剂再生效果;
3.再生器设有两级旋风分离器,用于气固分离,降低催化剂损失;
4.增设内取热器或外取热器,取走再生烧焦过剩热量,控制再生温度;
5.设有催化剂装卸设施,用于开、停工装卸催化剂,控制适宜的催化剂平衡活性;
6.部分装置设有CO助燃剂加入系统。
催化裂化分馏系统主要由分馏塔、柴油汽提塔、回炼油罐以及塔顶油气冷凝冷却系统、各中段循环回流及产品的热量回收系统组成。
其主要任务是将来自反应系统的高温油气脱过热后,根据各组分沸点的不同切割为富气、汽油、柴油、回炼油和油浆等馏分,通过工艺因素控制,保证各馏分质量合格;
同时可利用分馏塔各循环回流中高温位热能作为稳定系统各重沸器的热源。
部分装置还合理利用分馏塔顶油气的低温位热源。
吸收稳定系统主要包括吸收塔、解析塔、稳定塔和凝缩油罐、汽油碱洗沉降罐以及相应的冷换设备。
该系统的主要任务是将来自分馏系统的粗汽油和来自气压机的的压缩富气分离成干气、合格的稳定汽油和液态烃。
一般控制液态烃C2以下组分不大于2%(体积)、C5以上组分不大于1.5%(体积)。
常说的催化裂化装置烟气能量回收系统,一般包括催化裂化烟气轮机系统和催化裂化烟气余热回收锅炉两部分。
少数装置再生系统不完全燃烧再生的,再生烟气中含有CO,则可能还要在烟气余热回收锅炉前设置CO焚烧炉。
之所以要设置烟气能量回收系统,主要是因为催化裂化装置的再生烧焦要控制一定的氧分压,再生烧焦过程又是放热反应,所以离开再生器的烟气的压力较高,温度较高,为了充分回收烟气的压力能和热能,世界上大型的催化裂化装置上均配置烟气能量回收系统。
尽管烟气能量回收系统技术较为复杂,但经济效益十分显着。
根据原油的含硫量及加工深度的不同,炼厂干气不同程度地含有H2S等硫化物。
除炼制低硫原油的干气在作为燃料气使用时不需脱硫外,一般炼油厂的干气不管是作为燃料使用还是用作化工装置的原料,都需要先进行脱硫。
可见,干气脱硫在现代炼化厂中起着至关重要的作用。
干法脱硫主要用于需要较高脱硫率的场合。
气体分馏是常规的精细分馏过程,根据原料中各组分间相对挥发度的不同,按要求将其分为目的产品。
国内外在气体分馏的工艺技术上是一致的,都是通过一系列塔,根据产品方案的要求,将液化气分离成单个的组分或馏分。
MTBE装置即甲基叔丁基醚装置
连续重整预加氢的过程是在催化剂和H2的作用下,使原料中的硫、氮、氧等化合物进行加氢分解,生成易于除去的H2S、NH3和H2O,然后经预加氢反应分离罐、汽提塔除去;原料中的烯烃则加氢生成饱和烃,原料中的砷、铜、铅等金属被吸附在催化剂上而除去。
同时由于重整催化剂非常娇贵并且价格昂贵,预加氢还负责切割馏分和去除水分的作用。