13种气化炉工艺
3组主要气化工艺及8种典型气化炉图文详解
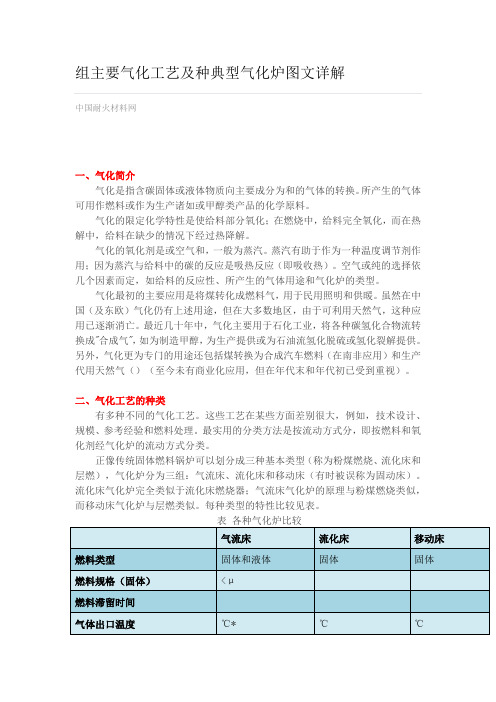
组主要气化工艺及种典型气化炉图文详解中国耐火材料网一、气化简介气化是指含碳固体或液体物质向主要成分为和的气体的转换。
所产生的气体可用作燃料或作为生产诸如或甲醇类产品的化学原料。
气化的限定化学特性是使给料部分氧化;在燃烧中,给料完全氧化,而在热解中,给料在缺少的情况下经过热降解。
气化的氧化剂是或空气和,一般为蒸汽。
蒸汽有助于作为一种温度调节剂作用;因为蒸汽与给料中的碳的反应是吸热反应(即吸收热)。
空气或纯的选择依几个因素而定,如给料的反应性、所产生的气体用途和气化炉的类型。
气化最初的主要应用是将煤转化成燃料气,用于民用照明和供暖。
虽然在中国(及东欧)气化仍有上述用途,但在大多数地区,由于可利用天然气,这种应用已逐渐消亡。
最近几十年中,气化主要用于石化工业,将各种碳氢化合物流转换成"合成气",如为制造甲醇,为生产提供或为石油流氢化脱硫或氢化裂解提供。
另外,气化更为专门的用途还包括煤转换为合成汽车燃料(在南非应用)和生产代用天然气()(至今未有商业化应用,但在年代末和年代初已受到重视)。
二、气化工艺的种类有多种不同的气化工艺。
这些工艺在某些方面差别很大,例如,技术设计、规模、参考经验和燃料处理。
最实用的分类方法是按流动方式分,即按燃料和氧化剂经气化炉的流动方式分类。
正像传统固体燃料锅炉可以划分成三种基本类型(称为粉煤燃烧、流化床和层燃),气化炉分为三组:气流床、流化床和移动床(有时被误称为固动床)。
流化床气化炉完全类似于流化床燃烧器;气流床气化炉的原理与粉煤燃烧类似,而移动床气化炉与层燃类似。
每种类型的特性比较见表。
* 如果在气化炉容器内有淬冷段,则温度将较低。
.气流床气化炉在一台气流床气化炉内,粉煤或雾化油流与氧化剂(典型的氧化剂是氧)一起汇流。
气流床气化炉的主要特性是其温度非常高,且均匀(一般高于℃),气化炉内的燃料滞留时间非常短。
由于这一原因,给进气化炉的固体必须被细分并均化,就是说气流床气化炉不适于用生物质或废物等类原料,这类原料不易粉化。
气化炉制作方法
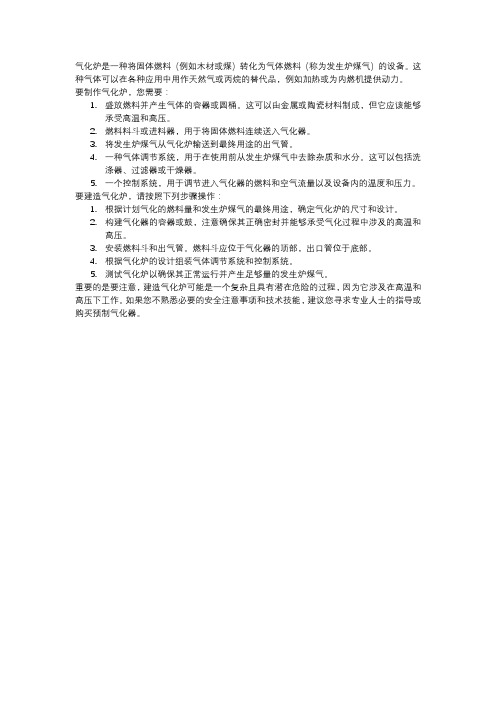
气化炉是一种将固体燃料(例如木材或煤)转化为气体燃料(称为发生炉煤气)的设备。
这种气体可以在各种应用中用作天然气或丙烷的替代品,例如加热或为内燃机提供动力。
要制作气化炉,您需要:
1.盛放燃料并产生气体的容器或圆桶。
这可以由金属或陶瓷材料制成,但它应该能够
承受高温和高压。
2.燃料料斗或进料器,用于将固体燃料连续送入气化器。
3.将发生炉煤气从气化炉输送到最终用途的出气管。
4.一种气体调节系统,用于在使用前从发生炉煤气中去除杂质和水分。
这可以包括洗
涤器、过滤器或干燥器。
5.一个控制系统,用于调节进入气化器的燃料和空气流量以及设备内的温度和压力。
要建造气化炉,请按照下列步骤操作:
1.根据计划气化的燃料量和发生炉煤气的最终用途,确定气化炉的尺寸和设计。
2.构建气化器的容器或鼓,注意确保其正确密封并能够承受气化过程中涉及的高温和
高压。
3.安装燃料斗和出气管。
燃料斗应位于气化器的顶部,出口管位于底部。
4.根据气化炉的设计组装气体调节系统和控制系统。
5.测试气化炉以确保其正常运行并产生足够量的发生炉煤气。
重要的是要注意,建造气化炉可能是一个复杂且具有潜在危险的过程,因为它涉及在高温和高压下工作。
如果您不熟悉必要的安全注意事项和技术技能,建议您寻求专业人士的指导或购买预制气化器。
煤气化工艺流程范文
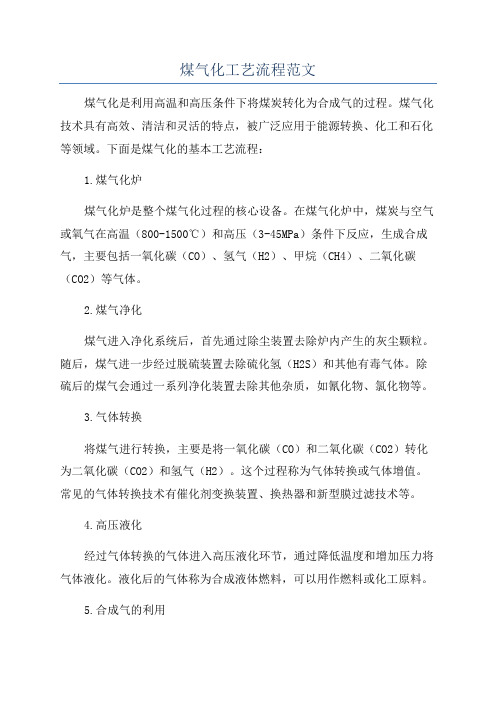
煤气化工艺流程范文煤气化是利用高温和高压条件下将煤炭转化为合成气的过程。
煤气化技术具有高效、清洁和灵活的特点,被广泛应用于能源转换、化工和石化等领域。
下面是煤气化的基本工艺流程:1.煤气化炉煤气化炉是整个煤气化过程的核心设备。
在煤气化炉中,煤炭与空气或氧气在高温(800-1500℃)和高压(3-45MPa)条件下反应,生成合成气,主要包括一氧化碳(CO)、氢气(H2)、甲烷(CH4)、二氧化碳(CO2)等气体。
2.煤气净化煤气进入净化系统后,首先通过除尘装置去除炉内产生的灰尘颗粒。
随后,煤气进一步经过脱硫装置去除硫化氢(H2S)和其他有毒气体。
除硫后的煤气会通过一系列净化装置去除其他杂质,如氰化物、氯化物等。
3.气体转换将煤气进行转换,主要是将一氧化碳(CO)和二氧化碳(CO2)转化为二氧化碳(CO2)和氢气(H2)。
这个过程称为气体转换或气体增值。
常见的气体转换技术有催化剂变换装置、换热器和新型膜过滤技术等。
4.高压液化经过气体转换的气体进入高压液化环节,通过降低温度和增加压力将气体液化。
液化后的气体称为合成液体燃料,可以用作燃料或化工原料。
5.合成气的利用合成气可以通过合成氨、甲醇、乙醇等化学品的合成反应产生相应的化学品。
合成气也可以用于发电和热能供应等非化学工业领域。
6.尾气回收煤气化过程中会产生大量的尾气,其中含有部分有用成分。
为了实现资源的综合利用,需要对尾气回收和再循环利用。
尾气回收可以通过尾气净化、尾气焚烧和尾气发电等方式进行。
总之,煤气化是一种重要的能源转化工艺,可以将煤炭转化为合成气,进而用于化工和石化生产等应用领域。
随着技术的发展,煤气化技术逐渐成熟,能够更加高效和清洁地将煤炭转化为合成气。
尾气回收和综合利用也是煤气化过程中需要考虑的重要环节。
气化炉的制作方法和原理
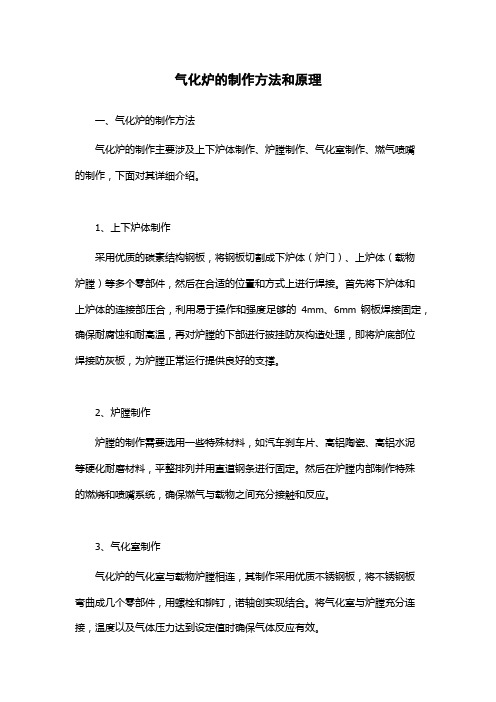
气化炉的制作方法和原理一、气化炉的制作方法气化炉的制作主要涉及上下炉体制作、炉膛制作、气化室制作、燃气喷嘴的制作,下面对其详细介绍。
1、上下炉体制作采用优质的碳素结构钢板,将钢板切割成下炉体(炉门)、上炉体(载物炉膛)等多个零部件,然后在合适的位置和方式上进行焊接。
首先将下炉体和上炉体的连接部压合,利用易于操作和强度足够的4mm、6mm钢板焊接固定,确保耐腐蚀和耐高温,再对炉膛的下部进行披挂防灰构造处理,即将炉底部位焊接防灰板,为炉膛正常运行提供良好的支撑。
2、炉膛制作炉膛的制作需要选用一些特殊材料,如汽车刹车片、高铝陶瓷、高铝水泥等硬化耐磨材料,平整排列并用直道钢条进行固定。
然后在炉膛内部制作特殊的燃烧和喷嘴系统,确保燃气与载物之间充分接触和反应。
3、气化室制作气化炉的气化室与载物炉膛相连,其制作采用优质不锈钢板,将不锈钢板弯曲成几个零部件,用螺栓和铆钉,诺轴创实现结合。
将气化室与炉膛充分连接,温度以及气体压力达到设定值时确保气体反应有效。
4、燃气喷嘴的制作燃气喷嘴的选择包括四种类型,分别为‘U’形喷嘴、‘I’形喷嘴、‘S’形喷嘴和‘H’形喷嘴,其中‘S’形喷嘴和‘I’形喷嘴是日常使用比较常见的两种喷嘴。
在材料上,一般选用耐高温、耐磨、耐腐蚀的石墨材料,制作成相应的喷嘴。
二、气化炉的原理气化炉是利用固体燃料或液体燃料在高温、高压气氛中发生热化学反应,将燃料中的碳、氢、氧等元素在气化过程中分离出来,得到一种气态混合物,称之为合成气。
气化炉的原理主要包括以下两个方面:1、气化原理气化炉主体的气化过程与燃烧有所不同,其燃料在高温、高压气氛下达到化学热反应,将固体或液体燃料转化为气态混合物,籍此获得高效新型燃料气。
因此,气化炉建立在高积压条件下,提高了气化率和合成气质量,有低温式、介温式和高温式三种不同形式的炉型,需要根据需求选用合适的炉型。
2、燃气生成原理气化炉的原始燃料经过气化,产生气态氧化氮、水等成分,在高温压况下,由化学热反应生成化学品,如一氧化碳、氢气、乙烷等,支持启动炉膛,同时也是进行加料安全的重点组成部分。
三种煤气化炉技术介绍

一、概述煤气化技术的开发与应用大约经历了200年的发展历史。
煤气化技术按固体和气体的接触方式可分为固定床、流化床、气流床和熔融床4种,其中熔融床技术还没有实际应用开发,各种煤气化炉的模式见图1。
图1 各种煤气化炉模式图1. 固定床。
固定床气化炉是最早开发出的气化炉,如图1(a)所示,炉子下部为炉排,用以支撑上面的煤层。
通常,煤从气化炉的顶部加入,而气化剂(氧或空气和水蒸气)则从炉子的下部供入,因而气固间是逆向流动的。
特点是单位容积的煤处理量小,大型化困难。
目前,运转中的固定床气化炉主要有鲁奇气化炉和BGC- 鲁奇炉两种。
2.流化床。
流化床气化炉如图1(b)所示,在分散板上供给粉煤,在分散板下送入气化剂(氧、水蒸气),使煤在悬浮状下进行气化。
流化床气化炉不能用灰分融点低的煤,副产焦油少,碳利用率低。
3.气流床。
气流床气化炉如图1(c)所示,粉煤与气化剂(O2、水蒸气)一起从喷嘴高速吹入炉内,快速气化。
特点是不副产焦油,生成气中甲烷含量少。
气流床气化是目前煤气化技术的主流,代表着今后煤气化技术的发展方向。
气流床按照进料方式又可分为湿法进料(水煤浆)气流床和干法进料(煤粉)气流床。
前者以德士古气化炉为代表,还有国内开发的多元料浆加压气化炉、多喷嘴(四烧嘴)水煤浆加压气化炉;后者以壳牌气化炉为代表,还有GSP炉以及国内开发的航天炉、两段炉、清华炉、四喷嘴干粉煤炉。
二、三种先进的煤气化工艺我国引进并被广泛采用的三种先进煤气化工艺——鲁奇气化炉、壳牌气化炉、德士古气化炉。
1.鲁奇气化炉(结构见图2)属于固定床气化炉的一种。
鲁奇气化炉是1939年由德国鲁奇公司设计,经不断的研究改进已推出了第五代炉型,目前在各种气化炉中实绩最好。
德国SVZ Schwarze Pumpe公司已将这种炉型应用于各种废弃物气化的商业化装置。
我国在20世纪60年代就引进了捷克制造的早期鲁奇炉并在云南投产。
1987年建成投产的天脊煤化工集团公司从德国引进的4台直径3800mm的Ⅳ型鲁奇炉,先后采用阳泉煤、晋城煤和西山官地煤等煤种进行试验,经过10多年的探索,基本掌握了鲁奇炉气化贫瘦煤生产合成氨的技术,现建成的第五台鲁奇炉已投产,形成了年产45万吨合成氨的能力。
各种气化炉工艺比较

煤制合成气技术比较作者/来源:陈英1,任照元2(1.兖矿鲁南化肥厂,山东滕州277527;2.水煤浆气化及煤化工国家工程研究中日期:2009-1-13Texaco水煤浆气化、Shell粉煤加压气化和GSP气化技术都是典型的洁净煤气化技术,各有特点,各企业在改造或新建时应根据煤种、灰熔点、装置规模、产品链设定和投资情况进行合理选择。
下面就上述气化技术及其选择和使用情况进行分析和评价,供大家参考。
1 Shell气流床加压粉煤气化该工艺在国外还没有用于化肥生产的成功范例。
中石化巴陵分公司是第一家引进该技术用于化肥原料生产的厂家。
到目前为止,国内已先后有18家企业引进了此项技术(装置)。
但该工艺选择的是废锅流程,由于合成原料气含有的蒸汽较少,3.0MPa下仅为14%;因此用于生产合成氨后续变换工序要补充大量的水蒸气,用于甲醇生产也要补充一部分水蒸气于变换工序,工艺复杂,也使系统能量利用不合理。
湖北双环科技股份有限公司是第一家正式投运的厂家,于2006年5月开始试车。
据反映,试车期间曾发生烧嘴处水冷壁烧漏,输煤系统不畅引发氧煤比失调、炉温超温,渣口处水冷壁管严重腐蚀,水冷液管内异物堵塞和烧嘴保护罩烧坏等问题。
引进该技术的项目投资大。
2006年5月贵州天福与Shell签约,气化岛规模为每小时17.05万m3CO+H2,投资9.7亿元人民币,为同规模水煤浆气化岛投资的1.8倍。
气化装置设备结构复杂,制造周期长。
气化炉、导管、废锅内件定点西班牙、印度制造,加工周期14~18个月,海运3个月;压力壳可国内制造,但材料仍需进口,周期也较长;设备、仪表、材料的国产化率与水煤浆气化相比差距比较大。
建厂时间长(3~5 a),将使企业还贷周期长,财务负担加重。
2001年与Shell签约的中石化巴陵分公司、湖北双环、柳州化工股份有限公司只有双环于2006年5月试车;2003年与Shell签约的中石化湖北化肥分公司、中石化安庆分公司、云天化集团公司、云维集团沾化分公司只有安庆于2006年10月开始煮炉。
气化炉工作原理

气化炉工作原理
气化炉是一种能将固态燃料转化为可燃气体的设备。
它的工作原理是在一定温度下,通过一系列化学反应将固态燃料转化为可燃气体,并将其用于燃烧或能源转换。
气化炉的工作原理主要包括以下几个步骤:
1. 干馏:首先,固态燃料如煤、木材或生物质等被放入气化炉中。
然后,在几百摄氏度的高温下,燃料开始发生干馏反应。
在这个步骤中,由于高温作用,燃料分解并释放出气体、液体和固体产物。
2. 热解:在干馏过程中,燃料中的碳氢化合物进一步分解,产生可燃的气体,如一氧化碳和氢气。
这个过程称为热解反应。
3. 氧化:气化炉中的气体进一步与空气中的氧气进行反应,发生氧化反应。
一氧化碳会与氧气反应生成二氧化碳,氢气会与氧气反应生成水蒸气。
这个氧化过程中会释放出大量的热量。
4. 清除杂质:通过气化炉的上部,废气中的杂质如灰尘、硫化物和氯化物等会被清除或被减少,以防止对后续的燃烧设备或其它使用设备造成损害。
5. 燃烧:气化炉产生的可燃气体可以被用作燃料,供给发电装置、工业锅炉或热处理设备等。
这些设备中,可燃气体可以与空气进行充分的混合,然后进行燃烧,产生高温和高压的蒸汽或热能。
通过这些步骤,气化炉实现了固态燃料的有效利用,将其转化为可燃气体,从而提供了一种高效、清洁的能源转换方式。
气化炉技术简介

气化炉技术简介
气化炉是一种将燃料转化为气体的设备,主要用于生产煤气、合成气、水煤浆等气体燃料。
气化炉的工作原理是利用燃料与氧气反应产生高温气流,将燃料转化为气化物。
气化炉技术可以分为多种类型,其中常用的有固定床气化、流化床气化、壁式气化、旋转气化等。
每种气化炉技术有其独特的特点和应用范围。
固定床气化炉是一种最早应用的气化炉技术,主要用于气化煤、木材、生物质等。
其特点是在一个固定的垂直炉床中加入燃料,通过在上部喷入气体使其气化,然后将气化气体经过冷却、除尘处理后作为燃料使用。
流化床气化炉是一种以流化床技术为基础的气化炉,主要用于气化煤、生物质等。
其特点是利用高速气流将燃料悬浮在气流中,形成床层,然后在床层中加热气体使其气化,并将气化产物从床层中带走。
壁式气化炉是以固定床气化为基础的气化炉技术,主要用于气化煤、石油焦等。
其特点是利用旋流器将燃料投入炉膛,然后在炉壁上加热使其气化,并将气化产物从顶部排出。
旋转气化炉是一种采用旋转床技术的气化炉,主要用于气化生物质。
其特点是将燃料放置在旋转床中,然后旋转床加热将燃料气化,并将气化产物通过顶部排出。
气化炉技术具有高效节能、减少污染等优点,已广泛应用于化工、能源、冶金等行业。
煤气化炉技术介绍

煤气化炉技术介绍煤气化炉是一种将煤炭转化为合成气的设备,通过在高温、高压和缺氧的条件下将煤炭转化为合成气,这个过程被称为煤气化。
煤气化炉技术已经得到了广泛的应用,主要用于发电、化工、冶金等行业。
煤气化炉的工作原理是将煤炭与氧气或水蒸气进行接触反应,通过引入适量的氧气或水蒸气,可以改变煤炭的化学构成,生成大量的一氧化碳和氢气,这些气体被称为合成气。
合成气是一种重要的中间能源,可以用于发电、制氢、制造合成燃料和化学品等。
煤气化炉主要分为固定床煤气化炉、流化床煤气化炉和顶喷床煤气化炉等几种不同的类型。
固定床煤气化炉是最早发展的一种煤气化技术,它通过将煤炭放置在固定的反应床上,然后通过床下的气体进行气化反应。
固定床煤气化炉具有结构简单、操作稳定的优点,但是其反应效率较低,需要较长的气化时间。
流化床煤气化炉是一种更为高效的煤气化技术,它利用气化剂从底部垂直进入炉体,使煤炭床达到流态化,从而提高了反应速率和传热效率。
流化床煤气化炉具有反应效率高、适应性强的优点,广泛应用于工业生产中。
顶喷床煤气化炉是一种新型的煤气化技术,它通过将气化剂从顶部喷入煤床反应器中,实现了煤炭的均质气化。
顶喷床煤气化炉具有操作简单、反应效率高、产气质量好的优点,被认为是未来煤气化炉的发展方向之一煤气化炉的操作参数包括炉温、炉压、气化剂流量、气化剂比和煤炭粒径等。
炉温是影响煤气化反应速率和产物组成的重要参数,通常在800-1600摄氏度之间。
炉压是指气化炉内的压力,一般较高,可以保持合成气的高浓度。
气化剂流量和比例决定了反应过程中气化剂的含氧量和所产生的合成气组成。
煤炭的粒径对煤气化反应速率和产物分布也有影响,通常要求煤炭粒径在20-100mm之间。
煤气化炉的优点是可以有效利用煤炭资源,将其转化为更高价值的产品,提高了能源利用效率。
同时,煤气化炉还可以减少煤炭燃烧过程中产生的大量有害气体排放,可以减少对环境的污染。
此外,煤气化炉还可以根据不同的需求调整产气组成和比例,灵活性较强。
气化炉的流程说明

)原料煤储运(YT1000)原料煤由伊泰集团下属的酸刺沟煤矿火车运至煤制油公司,经螺旋卸车机(VL-1001/1002)粒度约50mm卸至原煤场,由带式输送机(VA-1001-2-3-4-5A/B)共计10条,输送能力200T/H经由带式除铁器(VM-1001-2A/B)除去金属类,由齿辊破碎机(VB-1001)将原煤碎到10mm以下,通过振动筛滤去大于10mm的颗粒送入制浆工序原煤料仓(V1101A/B),工作时序为间歇。
2)料浆制备(YT1100)制浆工序的任务是给煤浆制备提供质量合格的水煤浆。
从煤储运系统来的直径小于10mm的煤约80T/h(含水量10.%)加到煤斗(V1101A/B)中,煤斗中的煤经过皮带给煤机(J1101A/B)送入磨煤机(H1101A/B)中,通过控制给煤速率(或磨机负荷)以控制满足煤气化需要的煤浆。
作为助熔剂的石灰石从石灰石料斗(V1102A/B)中通过石灰石螺旋给料器(J1102A/B)送入磨煤机,石灰石的添加量将由原料煤的灰熔点决定,以便控制煤的灰熔点低于1300℃,依据06年9月3日上海会议决定暂时取消助熔剂加入,相关设计保留。
添加剂从添加剂槽(V1103)中通过添加剂泵(P1102A/B/C)送到磨煤机中,添加剂的添加量(干基)大约为(未确定),该量将根据煤浆的黏度作以调整,煤浆黏度一般控制在500-1200cp。
来自制浆水槽(V1112)的水通过制浆水泵P1112A/B送入磨煤机H1101A/B,该水量控制在总量约45t/h,在实际生产中,实际加水量将根据原煤含水量和煤浆浓度做一定的调整。
在磨煤机中,原煤与水,助熔剂,添加剂经磨制成浓度为60%的水煤浆,经过滚筒筛S1101A/B,滤去较大煤粒后,进入低压煤浆槽T1102A/B,最后由低压煤浆泵P1102A/B送入大煤浆槽V1106中,其总流量为110m3/h.(总量为二台低压料浆泵给料量)。
制浆界区的排污冲洗水将被收集进磨煤水池V1107中,再由研磨水池泵P1104A/B送出界区。
三种煤气化炉技术介绍
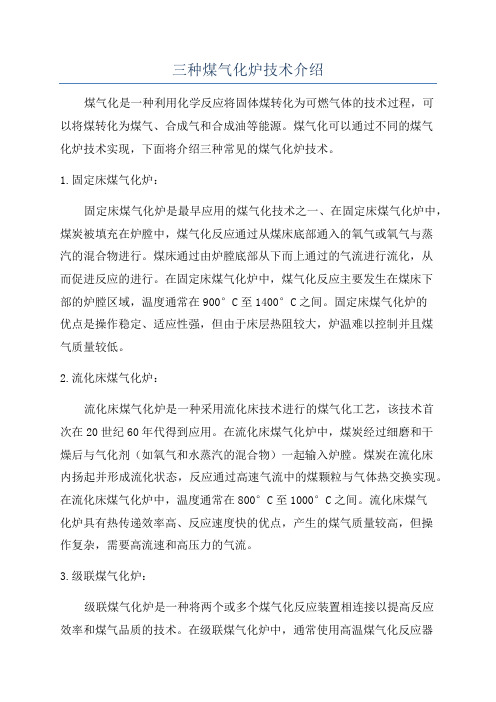
三种煤气化炉技术介绍煤气化是一种利用化学反应将固体煤转化为可燃气体的技术过程,可以将煤转化为煤气、合成气和合成油等能源。
煤气化可以通过不同的煤气化炉技术实现,下面将介绍三种常见的煤气化炉技术。
1.固定床煤气化炉:固定床煤气化炉是最早应用的煤气化技术之一、在固定床煤气化炉中,煤炭被填充在炉膛中,煤气化反应通过从煤床底部通入的氧气或氧气与蒸汽的混合物进行。
煤床通过由炉膛底部从下而上通过的气流进行流化,从而促进反应的进行。
在固定床煤气化炉中,煤气化反应主要发生在煤床下部的炉膛区域,温度通常在900°C至1400°C之间。
固定床煤气化炉的优点是操作稳定、适应性强,但由于床层热阻较大,炉温难以控制并且煤气质量较低。
2.流化床煤气化炉:流化床煤气化炉是一种采用流化床技术进行的煤气化工艺,该技术首次在20世纪60年代得到应用。
在流化床煤气化炉中,煤炭经过细磨和干燥后与气化剂(如氧气和水蒸汽的混合物)一起输入炉膛。
煤炭在流化床内扬起并形成流化状态,反应通过高速气流中的煤颗粒与气体热交换实现。
在流化床煤气化炉中,温度通常在800°C至1000°C之间。
流化床煤气化炉具有热传递效率高、反应速度快的优点,产生的煤气质量较高,但操作复杂,需要高流速和高压力的气流。
3.级联煤气化炉:级联煤气化炉是一种将两个或多个煤气化反应装置相连接以提高反应效率和煤气品质的技术。
在级联煤气化炉中,通常使用高温煤气化反应器作为第一级反应器,将煤炭和气化剂进行气化反应;然后,将第一级反应器的产物气流引入低温煤气化反应器中进行进一步的气化和合成反应。
级联煤气化炉可通过优化不同反应器之间的温度和气体组成来实现高效率的煤气化过程。
级联煤气化炉的优点是可以提高煤气化效率和产气量,并可根据需要调整煤气的组成。
综上所述,固定床煤气化炉、流化床煤气化炉和级联煤气化炉是三种常见的煤气化炉技术。
每种技术都有其特点和适用范围,可以根据具体需求选择合适的煤气化炉技术。
柴火气化炉制作方法

柴火气化炉制作方法柴火气化炉是一种利用生物质能源进行气化反应,产生可燃气体的设备。
它可以将木材、秸秆、玉米秸秆等生物质材料转化为可燃气体,用于取暖、烹饪或发电。
下面,我将介绍柴火气化炉的制作方法,希望对您有所帮助。
首先,准备好所需材料和工具。
您需要准备一根直径约30厘米、长度约1米的钢管作为气化炉的主体,还需要准备一些金属板、焊接设备、隔热材料、阀门、管道等。
工具方面,您需要准备电焊机、电钻、砂纸、量具、切割机等。
接下来,开始制作气化炉的主体。
首先,将钢管切割成合适的长度,然后在管壁上打孔,用于气体的进出。
接着,将金属板焊接成一个圆筒形的炉体,并将其固定在钢管上。
在炉体的底部留出一个小口,用于放入生物质材料。
然后,在炉体的顶部安装一个阀门,用于控制气体的排放。
然后,进行隔热处理。
在炉体的外部,需要包裹一层隔热材料,以减少热量的散失。
可以选择石棉布、陶瓷纤维等材料进行包裹,确保炉体能够高效地保持燃烧温度。
接着,安装气化炉的管道系统。
将一根直径较小的钢管连接到炉体的底部小口上,用于进气。
另外,还需要连接一根排气管道,将产生的可燃气体引出并储存或直接利用。
最后,进行调试和使用。
在安装完管道系统后,需要对气化炉进行调试,确保气体的产生和排放正常。
然后,可以将生物质材料放入炉体中,点燃并关闭阀门,等待一定时间后打开阀门,即可使用产生的可燃气体。
总的来说,制作柴火气化炉并不复杂,只要具备一定的焊接和机械加工技能,就可以完成。
希望以上内容对您有所帮助,祝您制作成功!。
气化炉的工艺流程
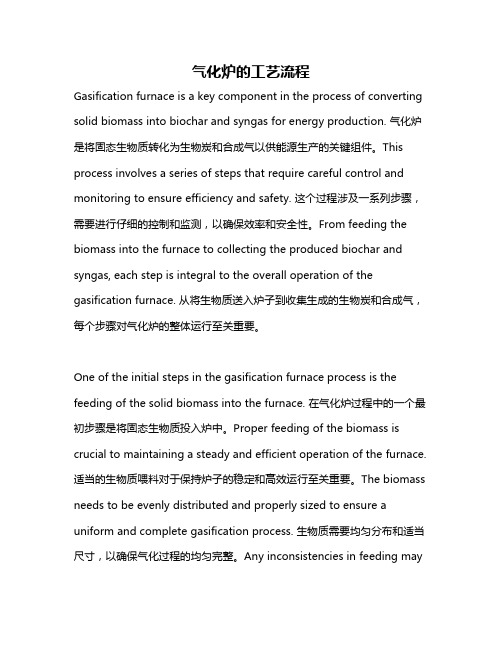
气化炉的工艺流程Gasification furnace is a key component in the process of converting solid biomass into biochar and syngas for energy production. 气化炉是将固态生物质转化为生物炭和合成气以供能源生产的关键组件。
This process involves a series of steps that require careful control and monitoring to ensure efficiency and safety. 这个过程涉及一系列步骤,需要进行仔细的控制和监测,以确保效率和安全性。
From feeding the biomass into the furnace to collecting the produced biochar and syngas, each step is integral to the overall operation of the gasification furnace. 从将生物质送入炉子到收集生成的生物炭和合成气,每个步骤对气化炉的整体运行至关重要。
One of the initial steps in the gasification furnace process is the feeding of the solid biomass into the furnace. 在气化炉过程中的一个最初步骤是将固态生物质投入炉中。
Proper feeding of the biomass is crucial to maintaining a steady and efficient operation of the furnace. 适当的生物质喂料对于保持炉子的稳定和高效运行至关重要。
The biomass needs to be evenly distributed and properly sized to ensure a uniform and complete gasification process. 生物质需要均匀分布和适当尺寸,以确保气化过程的均匀完整。
气化炉的结构及技术要求

气化炉的结构及技术要求 Jenny was compiled in January 20216.2气化炉的制造6.2.1 气化炉的结构及技术要求煤气化炉又称煤气发生炉(gasproducer)。
煤气化的主要设备。
根据煤的性质和对煤气产品的要求有多种气化炉型式。
分为、和气流床等形式。
煤在煤气化炉内会发生一系列复杂的物理变化和化学变化,主要有:煤的干燥、煤的干馏和煤的气化反应。
其中干燥指煤中水分的挥发,是一个简单的物理过程,而干馏和气化反应都是复杂的热化学过程,受煤种、温度、压力、加热速率和气化炉形式等多种因素的影响,和生产操作密切相关,是需要特别重视的。
煤的干馏又称为煤的热分解或热解,指煤中的有机物在高温下发生分解而逸出煤中的挥发成分,并残存半焦或焦炭的过程。
气化炉中的气化反应,是一个极其复杂的体系。
由于煤炭的“分子”结构很复杂,其中含有碳、氢、氧和其它元素,因而在讨论气化反应时总是以如下假定为基础,即仅考虑煤炭中的主要元素碳,且气化反应前发生煤的干馏和热解。
这样一来,气化反应主要是指煤中的碳和气化剂中的氧气、水蒸气和氢气的反应,也包括碳与反应物以及反应产物之间进行的反应。
某化工机械厂生产的气化炉的结构如图所示,该气化炉燃烧室筒体内径3200mm,主体高度19074mm。
上球形封头、燃烧室筒体、筒体锻件材料为耐热钢SA387Cr11Cl2,相对应中国标准为图6-5气化炉的结构14CrMoR。
,上球形封头厚度60mm,燃烧室筒体壁度78mm,筒体锻件的筒体部分壁度78mm。
激冷室腐蚀比较严重,所以内部堆焊。
故气化炉激冷室筒体采用复合钢板SA387Cr11Cl2+316L,筒体复合钢板厚度(78+4)mm,激冷室筒体内径3192mm。
筒体锻件壁面在激冷室侧的要堆焊耐蚀层。
下锥体封头材料为耐热钢SA387Cr11Cl2,内表面堆焊堆焊耐蚀层,厚度为((82+6)mm,气化炉主体高度19074mm。
气化炉技术特性参数:设计压力5.56MPa,设计温度455℃,工作介质:高温煤气、煤气、熔渣、黑水等。
13种气化炉工艺
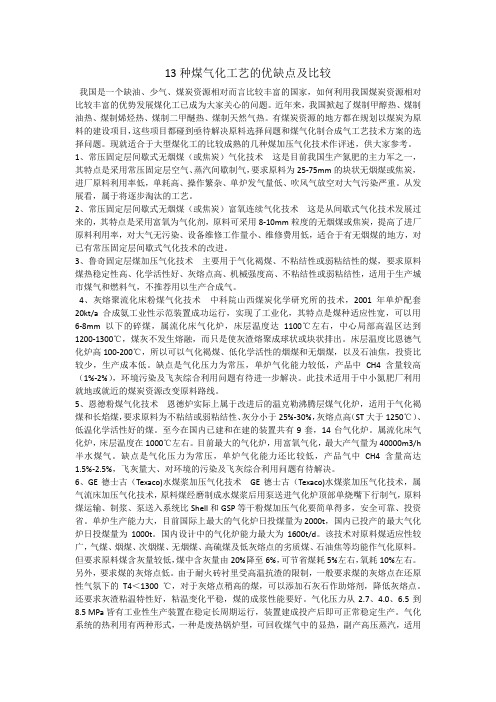
13种煤气化工艺的优缺点及比较我国是一个缺油、少气、煤炭资源相对而言比较丰富的国家,如何利用我国煤炭资源相对比较丰富的优势发展煤化工已成为大家关心的问题。
近年来,我国掀起了煤制甲醇热、煤制油热、煤制烯烃热、煤制二甲醚热、煤制天然气热。
有煤炭资源的地方都在规划以煤炭为原料的建设项目,这些项目都碰到亟待解决原料选择问题和煤气化制合成气工艺技术方案的选择问题。
现就适合于大型煤化工的比较成熟的几种煤加压气化技术作评述,供大家参考。
1、常压固定层间歇式无烟煤(或焦炭)气化技术这是目前我国生产氮肥的主力军之一,其特点是采用常压固定层空气、蒸汽间歇制气,要求原料为25-75mm的块状无烟煤或焦炭,进厂原料利用率低,单耗高、操作繁杂、单炉发气量低、吹风气放空对大气污染严重。
从发展看,属于将逐步淘汰的工艺。
2、常压固定层间歇式无烟煤(或焦炭)富氧连续气化技术这是从间歇式气化技术发展过来的,其特点是采用富氧为气化剂,原料可采用8-10mm粒度的无烟煤或焦炭,提高了进厂原料利用率,对大气无污染、设备维修工作量小、维修费用低,适合于有无烟煤的地方,对已有常压固定层间歇式气化技术的改进。
3、鲁奇固定层煤加压气化技术主要用于气化褐煤、不粘结性或弱粘结性的煤,要求原料煤热稳定性高、化学活性好、灰熔点高、机械强度高、不粘结性或弱粘结性,适用于生产城市煤气和燃料气,不推荐用以生产合成气。
4、灰熔聚流化床粉煤气化技术中科院山西煤炭化学研究所的技术,2001年单炉配套20kt/a合成氨工业性示范装置成功运行,实现了工业化,其特点是煤种适应性宽,可以用6-8mm以下的碎煤,属流化床气化炉,床层温度达1100℃左右,中心局部高温区达到1200-1300℃,煤灰不发生熔融,而只是使灰渣熔聚成球状或块状排出。
床层温度比恩德气化炉高100-200℃,所以可以气化褐煤、低化学活性的烟煤和无烟煤,以及石油焦,投资比较少,生产成本低。
缺点是气化压力为常压,单炉气化能力较低,产品中CH4含量较高(1%-2%),环境污染及飞灰综合利用问题有待进一步解决。
16种气化炉工艺汇总!

16种气化炉工艺汇总!图片来源由气化炉团队成员提供鲁奇加压气化工艺鲁奇炉造气工艺流程简图◆◆◆技术特点1、以碎煤为原料,进入炉煤的处理费用低;2、耗氧率低;3、气化后煤气质量较好;4、煤气成分有利。
粗煤气中H2/CO的比为2.0,不经变换或者少量变换既可用于F-T合成,甲醇合成,天然气合成等工艺。
5、产物热回收方便。
6、气化工艺成熟,设备国产化率高,造价较低,在投资上较气流床占有较大优势。
BGL气化(液态排渣鲁奇炉)BGL气化工艺是在Lurgi气化工艺基础上发展起来的,最大的改进是将鲁奇的固态排渣改为熔融态排渣,提高了操作温度,同时也提高了生产能力,更适合灰熔点低的煤种。
BGL气化工艺流程简图◆◆◆技术特点1、与其他以氧气为主的气化系统相比,BGL气化炉耗氧量较低,从而使总效率明显提高;2、煤料床顶部的气体温度一般为-450℃、因而不需要昂贵的热回收设备;3、气体出口处凝结的焦油和油类副产品可保护炉壁金属表面使之不受腐蚀,这样,炉壁使用低成本的碳钢就足够了;4、灰渣是质地紧密的固体物质,封存了微量元素。
灰渣无害并具非浸溶性,适于作建筑材料;5、气化过程中无飞灰产生;原始产品气的CO2含量低;能够满足改变负荷的要求;6、气化炉可快速开机和关机;7、水蒸汽/氧气喷射系统(利用的是与鼓风炉里相似的喷嘴)可使焦油和油类副产品气化;8、喷嘴也可用来把其他废物喷入气化炉中进行焚烧;9、在气化炉底部的高温区,炉壁被一层固体灰渣所保护;10、煤中90%以上的能量被转化成可利用的燃料;11、原煤可被气化,粉煤可另加工成型煤投入或从喷嘴喷入;12、BGL设备不必由专门生产商提供部件一可确保当地供应部件;13、可利用成熟的气体处理技术予以脱除原始产品气中的硫;14、净化后的产品气可直接用作燃料气,其热值约为13MJ/m3,或用作各种化工工艺所需的原料气;15、气体出口温度低、无需产生高压水蒸汽,提高了工艺效率,并可灵活选择气化炉场地。
气化工艺流程简介

气化工艺流程简介从煤运系统来的原煤(粒度<10mm)进入煤仓(V1101),经过煤称重进料机(W1101)精确计量后,与来自滤液槽澄清的滤液及部分原水及添加剂进入磨煤机(M1101)。
煤和水在添加剂的作用下,磨成一定浓度、粘度、有一定粒度分布的可泵送的水煤浆。
水煤浆经过滚筒筛(S-1101)。
除去大颗粒后,自流入磨煤机出口槽(V1102),经磨煤机出料槽泵(P1101)加压、煤浆振动筛(S1201)筛分后,贮存在煤浆槽(V1201)内备用。
煤浆槽内的煤浆分别经两台煤浆给料泵(P1201)加压后送至气化炉的四个工艺烧嘴。
由空分系统来的高压氧气先分四路,再各分为两路,分别送入气化炉(R1301),在气化炉燃烧室内进行部分氧化反应,生成的粗合成气、熔渣及未完全反应的碳通过燃烧室下部的渣口与洗涤冷却水沿洗涤冷却管并流向下,进入气化炉洗涤冷却室,粗合成气被冷却后在洗涤冷却室的液位以下以鼓泡的形式进行洗涤和进一步冷却,由洗涤冷却室上部空间出气化炉。
出气化炉的粗合成气经过混合器(X1403)润湿及旋风分离器(V1408)分离大部分润湿的细灰后送水洗塔(T1401)进一步洗涤除尘,将合成气含尘量降至<1mg/Nm3后送净化系统。
熔渣在洗涤冷却室的水浴中通过静态破渣器破碎后被锁斗循环水夹带进入锁斗(V1307)定期排入渣池。
未完全反应的碳颗粒悬浮在黑水中,随黑水到渣水处理工序作进一步处理。
水洗塔中部含固量较低的洗涤黑水经黑水循环泵(P1401)加压后分两路,一路经黑水过滤器(V1309)过滤后送入气化炉激冷环,另一路送入混合器分别作为洗涤、润湿水。
从气化炉、旋风分离器、水洗塔出来的三股洗涤黑水经液位、流量串级调节控制并减压后送入蒸发热水塔(T1402)蒸发室。
减压后的黑水在蒸发热水塔蒸发室内发生闪蒸,水蒸汽及部分溶解在黑水中的酸性气CO2、H2S等被迅速闪蒸出来。
通过上升管进入蒸发塔上部热水室,与低压灰水泵来的灰水直接接触,低压灰水被加热。
主要气化工艺对比

主要气化工艺对比气化工艺● 水煤浆加压气化①GE水煤浆加压气化工艺GE水煤浆加压气化法为目前世界上先进的气化技术之一,属气流床加压气化法。
其特点是该工艺对煤的适应范围较宽,可利用粉煤,单台气化炉生产能力较大,气化操作温度高,液态排渣,碳转化率高,煤气质量好,甲烷含量低,不产生焦油、萘、酚等污染物。
排出粗灰渣可以用做水泥的原料和建筑材料。
三废处理简单,易于达到环境保护的要求。
生产控制水平高,易于实现过程自动化及计算机控制。
A. 加压水煤浆气化的优点a)煤种适应性广年轻烟煤,粉煤皆可作原料,灰熔点要求不超过1350℃,煤可磨性和成浆性好,制得煤浆浓度要高于60%(wt)为宜。
b)气化压力范围大从2.5~8.0MPa(G)皆有工业化装置,以4.0MPa(G)和6.5MPa(G)较为普遍,气化压力高可节省合成气压缩功。
c)气化炉热量利用有激冷工艺制得含蒸汽量高的合成气如用于生产合成氨、甲醇、制氢等,在变换工序不需再外加蒸汽,也可采用废锅流程回收热量副产高压蒸汽,但废锅设备价格较高,可择优选用。
d)气化炉内无传动装置,结构比较简单。
e)单位体积产气量大,一台直径3200mm,6.5MPa气化炉产生气体,可日产甲醇1500吨。
f)有效气成分高,CO+H2≥80%(v%),排渣无污染,污水污染小易处理。
因高温气化,气体中含甲烷很低(CH4≤0.1%),无焦油,气化炉排渣无污染可用作铺路路渣,污水含氰化物少易处理。
g)产品气一氧化碳和氢含量高是碳一化学最好合成原料气,可用来生产合成氨,甲醇,制氢,羟基合成原料气,用途广泛。
h)碳转化率高最高可达98%。
B. 水煤浆气化对煤质要求a)GE水煤浆气化对煤质适应性较广。
除褐煤、泥煤及热值低于22940kJ/kg ,灰熔点高于1350℃的煤不太适用外,其他粘结性煤,含灰量较高的煤,石油焦,烟煤均可作原料。
b)煤中灰含量对消耗指标的影响,煤中的灰含量增加会增加氧气的消耗,同时也增加每m3(标)(CO+H2)气体的煤消耗量,一般煤中灰含量从20%(wt)降到6%(wt),可节省5%无灰干基煤消耗,节省氧气消耗10%左右。
气化炉的工艺流程
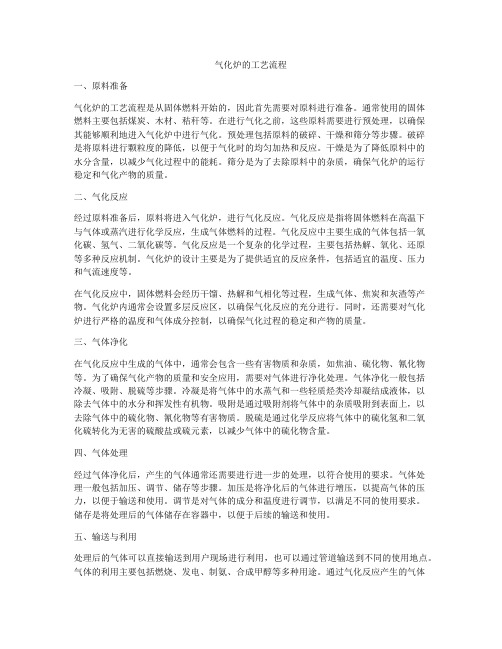
气化炉的工艺流程一、原料准备气化炉的工艺流程是从固体燃料开始的,因此首先需要对原料进行准备。
通常使用的固体燃料主要包括煤炭、木材、秸秆等。
在进行气化之前,这些原料需要进行预处理,以确保其能够顺利地进入气化炉中进行气化。
预处理包括原料的破碎、干燥和筛分等步骤。
破碎是将原料进行颗粒度的降低,以便于气化时的均匀加热和反应。
干燥是为了降低原料中的水分含量,以减少气化过程中的能耗。
筛分是为了去除原料中的杂质,确保气化炉的运行稳定和气化产物的质量。
二、气化反应经过原料准备后,原料将进入气化炉,进行气化反应。
气化反应是指将固体燃料在高温下与气体或蒸汽进行化学反应,生成气体燃料的过程。
气化反应中主要生成的气体包括一氧化碳、氢气、二氧化碳等。
气化反应是一个复杂的化学过程,主要包括热解、氧化、还原等多种反应机制。
气化炉的设计主要是为了提供适宜的反应条件,包括适宜的温度、压力和气流速度等。
在气化反应中,固体燃料会经历干馏、热解和气相化等过程,生成气体、焦炭和灰渣等产物。
气化炉内通常会设置多层反应区,以确保气化反应的充分进行。
同时,还需要对气化炉进行严格的温度和气体成分控制,以确保气化过程的稳定和产物的质量。
三、气体净化在气化反应中生成的气体中,通常会包含一些有害物质和杂质,如焦油、硫化物、氰化物等。
为了确保气化产物的质量和安全应用,需要对气体进行净化处理。
气体净化一般包括冷凝、吸附、脱硫等步骤。
冷凝是将气体中的水蒸气和一些轻质烃类冷却凝结成液体,以除去气体中的水分和挥发性有机物。
吸附是通过吸附剂将气体中的杂质吸附到表面上,以去除气体中的硫化物、氰化物等有害物质。
脱硫是通过化学反应将气体中的硫化氢和二氧化硫转化为无害的硫酸盐或硫元素,以减少气体中的硫化物含量。
四、气体处理经过气体净化后,产生的气体通常还需要进行进一步的处理,以符合使用的要求。
气体处理一般包括加压、调节、储存等步骤。
加压是将净化后的气体进行增压,以提高气体的压力,以便于输送和使用。
- 1、下载文档前请自行甄别文档内容的完整性,平台不提供额外的编辑、内容补充、找答案等附加服务。
- 2、"仅部分预览"的文档,不可在线预览部分如存在完整性等问题,可反馈申请退款(可完整预览的文档不适用该条件!)。
- 3、如文档侵犯您的权益,请联系客服反馈,我们会尽快为您处理(人工客服工作时间:9:00-18:30)。
13种煤气化工艺的优缺点及比较我国是一个缺油、少气、煤炭资源相对而言比较丰富的国家,如何利用我国煤炭资源相对比较丰富的优势发展煤化工已成为大家关心的问题。
近年来,我国掀起了煤制甲醇热、煤制油热、煤制烯烃热、煤制二甲醚热、煤制天然气热。
有煤炭资源的地方都在规划以煤炭为原料的建设项目,这些项目都碰到亟待解决原料选择问题和煤气化制合成气工艺技术方案的选择问题。
现就适合于大型煤化工的比较成熟的几种煤加压气化技术作评述,供大家参考。
1、常压固定层间歇式无烟煤(或焦炭)气化技术这是目前我国生产氮肥的主力军之一,其特点是采用常压固定层空气、蒸汽间歇制气,要求原料为25-75mm的块状无烟煤或焦炭,进厂原料利用率低,单耗高、操作繁杂、单炉发气量低、吹风气放空对大气污染严重。
从发展看,属于将逐步淘汰的工艺。
2、常压固定层间歇式无烟煤(或焦炭)富氧连续气化技术这是从间歇式气化技术发展过来的,其特点是采用富氧为气化剂,原料可采用8-10mm粒度的无烟煤或焦炭,提高了进厂原料利用率,对大气无污染、设备维修工作量小、维修费用低,适合于有无烟煤的地方,对已有常压固定层间歇式气化技术的改进。
3、鲁奇固定层煤加压气化技术主要用于气化褐煤、不粘结性或弱粘结性的煤,要求原料煤热稳定性高、化学活性好、灰熔点高、机械强度高、不粘结性或弱粘结性,适用于生产城市煤气和燃料气,不推荐用以生产合成气。
4、灰熔聚流化床粉煤气化技术中科院山西煤炭化学研究所的技术,2001年单炉配套20kt/a合成氨工业性示范装置成功运行,实现了工业化,其特点是煤种适应性宽,可以用6-8mm以下的碎煤,属流化床气化炉,床层温度达1100℃左右,中心局部高温区达到1200-1300℃,煤灰不发生熔融,而只是使灰渣熔聚成球状或块状排出。
床层温度比恩德气化炉高100-200℃,所以可以气化褐煤、低化学活性的烟煤和无烟煤,以及石油焦,投资比较少,生产成本低。
缺点是气化压力为常压,单炉气化能力较低,产品中CH4含量较高(1%-2%),环境污染及飞灰综合利用问题有待进一步解决。
此技术适用于中小氮肥厂利用就地或就近的煤炭资源改变原料路线。
5、恩德粉煤气化技术恩德炉实际上属于改进后的温克勒沸腾层煤气化炉,适用于气化褐煤和长焰煤,要求原料为不粘结或弱粘结性、灰分小于25%-30%,灰熔点高(ST大于1250℃)、低温化学活性好的煤。
至今在国内已建和在建的装置共有9套,14台气化炉。
属流化床气化炉,床层温度在1000℃左右。
目前最大的气化炉,用富氧气化,最大产气量为40000m3/h 半水煤气。
缺点是气化压力为常压,单炉气化能力还比较低,产品气中CH4含量高达1.5%-2.5%,飞灰量大、对环境的污染及飞灰综合利用问题有待解决。
6、GE德士古(Texaco)水煤浆加压气化技术GE德士古(Texaco)水煤浆加压气化技术,属气流床加压气化技术,原料煤经磨制成水煤浆后用泵送进气化炉顶部单烧嘴下行制气,原料煤运输、制浆、泵送入系统比Shell和GSP等干粉煤加压气化要简单得多,安全可靠、投资省。
单炉生产能力大,目前国际上最大的气化炉日投煤量为2000t,国内已投产的最大气化炉日投煤量为1000t。
国内设计中的气化炉能力最大为1600t/d。
该技术对原料煤适应性较广,气煤、烟煤、次烟煤、无烟煤、高硫煤及低灰熔点的劣质煤、石油焦等均能作气化原料。
但要求原料煤含灰量较低,煤中含灰量由20%降至6%,可节省煤耗5%左右,氧耗10%左右。
另外,要求煤的灰熔点低。
由于耐火砖衬里受高温抗渣的限制,一般要求煤的灰熔点在还原性气氛下的T4<1300 ℃,对于灰熔点稍高的煤,可以添加石灰石作助熔剂,降低灰熔点。
还要求灰渣粘温特性好,粘温变化平稳,煤的成浆性能要好。
气化压力从2.7、4.0、6.5到8.5 MPa皆有工业性生产装置在稳定长周期运行,装置建成投产后即可正常稳定生产。
气化系统的热利用有两种形式,一种是废热锅炉型,可回收煤气中的显热,副产高压蒸汽,适用于联合循环发电;另一种是水冷激型,制得的合成气水气比高达1.3~1.4,能满足后续CO 变换工序的需要,变换工序不需要外供蒸汽同,适用于制氢、制合成氨、制甲醇等化工产品。
气化系统不需要外供蒸汽、高压氮气及输送气化用原料煤的N2和CO2。
气化系统总热效率高达94%-96%,高于Shell干粉煤气化(为91%-93%)和GSP干粉煤气化(为88%-92%)。
气化炉结构简单,为耐火砖衬里。
气化炉无转动装置或复杂的膜式水冷壁内件,所以制造方便、造价低,同时由于采用热壁炉,炉内热容量比较大,气化炉升温至1000℃以上后,即可直接喷水煤浆投料,生产安全可靠。
在开停车和正常生产时无需连续燃烧一部分液化气或燃料气(合成气)。
煤气除尘也比较简单,可以了只需要一个文丘里洗涤器和一台洗涤塔就可以了,无需价格昂贵的高温高压飞灰过滤器,投资省。
单炉年运转时间为270~300天,碳转化率达96%-98%,有效气成分(CO+H2)为80%-83%;有效气(CO+H2)比氧耗为336-410m3/km3,有效气(CO+H2)比煤耗为550-620kg/km3。
国外已建成投产的装置有6套,15台气化炉;国内已建成投产的装置有8套,24台气化炉,正在建设、设计的装置还有4套,13台气化炉。
已建成投产的装置最终产品有合成氨、甲醇、醋酸、醋酐、氢气、一氧化碳、燃料气、联合循环发电。
各装置建成投产后,一直连续稳定、长周期运行。
装备国产化率已达90%以上,由于国产化率高,装置投资较其它加压气化装置都低。
水煤浆加压气化与其它加压气化装置建设费用的比例为Shell法:GSP法:多喷嘴水煤浆加压气化:水煤浆法=(2-2.5):(1.4-1.6):(1.2-1.3):1。
对于水煤浆加压气化技术国内已掌握了丰富的工程技术经验,已培养出一大批掌握该技术的设计、设备制造、建筑安装、煤种评价、试烧和工程总承包的单位及工程技术人员,所以从建设、投产到正常连续运行的周期比较短,这是业主所期望的。
缺点是气化用原料煤受气化炉耐火衬里的限制,适宜于气化低灰熔点的煤。
碳转化率较低,比氧耗和比煤耗较高。
气化炉耐火砖使用寿命较短,一般为1-2年,国产砖寿命为一年左右,1台投煤量为1000t/d的气化炉耐火砖约需500万元左右,有待改进。
气化烧嘴寿命较短,一般使用2个月后,需停车进行检查、维修或更换喷嘴头部,有待改进和提高。
我国自鲁南化肥厂第一套水煤浆加压气化装置(2台气化炉)1993年建成投产以来,相继建成了上海焦化厂气化装置(4.0 MPa气化,4台气化炉,于1995年建成投产),渭河化肥厂气化装置(6.5 MPa气化,3台气化炉,于1996年建成投产),淮南化肥厂气化装置(4.0 MPa气化,3台气化炉,于2000年建成投产),金陵石化公司化肥厂气化装置(4.0 MPa 气化,3, , , , 台气化炉,于2005年建成投产),浩良河化肥厂气化装置(3.0~4.0 MPa气化,3台气化炉,于2005年建成投产),南化公司气化装置(8.5 MPa气化,2006年建成投产),南京惠生气化装置(6.5 MPa气化,2007年建成投产)等装置。
由于我国有关生产厂的精心消化吸收,已掌握了丰富的连续稳定运转经验,新装置一般都能顺利投产,短期内便能连续稳定、高产、长周期运行。
并且掌握了以石油焦为原料的气化工艺技术。
还有一点需要提一下的是煤耗和氧耗问题,它与原料煤质的关系比较大。
无论是Shell法或GSP法,在用干粉煤气化时,需向气化炉内输入过热蒸汽,其用量以有效气(CO+H2)计为120~150 kg/km3,过热蒸汽与粉煤的比例为(0.22~0.25)∶1,相当于水煤浆中含水20%。
干粉煤气化宣传资料上介绍的煤耗和氧耗,实际上是忽略了生产过热蒸汽所用的煤耗。
在正常生产时,如需燃烧一部分然料气,必将增加氧耗及燃料气耗(折煤耗),备煤时煤干燥需要增加煤耗。
宣传资料介绍,这两种方法的煤耗和氧耗比较低,有效气(CO+H2)煤耗为550~600 kg/km3,氧耗为330~360 m3/km3,加上以上这些煤耗和氧耗,实际上有效气(CO+H2)总煤耗将为590~670 kg/km3,总氧耗将为380~410 m3/km3。
煤耗和氧耗不仅不低,而且比水煤浆气化法高或相仿。
另外还要考虑制备干煤粉及输送干煤粉增加的电耗和激冷用返回气循环压缩机增加的电耗。
鉴于以上几点,水煤浆加压气化工艺技术是一项成熟、国产化率高、投资省、建成后就能顺利投产,长周期稳产高产的工艺技术。
存在的缺点有待在生产实践中改进提高。
7、多元料浆加压气化技术多元料浆加压气化技术是西北化工研究院提出的,具有自主知识产权。
其基本生产装置与水煤浆加压气化技术相仿,属气流床单烧嘴下行制气。
典型的多元化料浆组成为煤60%-65%、油料10%-15%,水20%-30%,粘度不大于2500cP。
但在制备多元化料浆时掺入油类的办法与当前我国氮肥工业以煤代油改变原料路线的方针不符合,是不可取的,有待改进。
8、多喷嘴(四烧嘴)水煤浆加压气化技术“九五”期间,华东理工大学、兖矿鲁南化肥厂、中国天辰化学工程公司承担了国家重点科技攻关课题“新型(多喷嘴对置)水煤浆气化炉开发”。
该技术为气流床多烧嘴下行制气,气化炉内用耐火砖衬里。
开发成功后,相继在山东德州华鲁恒升化工有限公司建设了一套气化压力为6.5MPa、日处理煤750t的气化炉系统,于2005年6月正式投入运行,至今运转良好。
在山东滕州兖矿国泰化工有限公司建设了两套气化压力为 4.0MPa、气化温度约为1300℃、日处理煤1150t的气化炉系统,配套生产240kt/a甲醇,联产IGCC联合循环发电,发电能力为71.8MW,现在实际发电能力已达到80MW。
于2005年7月21日一次投料成功,运行至今。
经考核验收,同样以北宿洗煤为原料气化,多喷嘴水煤浆加压气化与单烧嘴加压气化相比,气化技术指标见表4,气化用煤种分析见表5。
表4:多喷嘴气化与单烧嘴气化结果对比表项目多喷嘴气化单烧嘴气化(Texaco) 有效气(CO+H2)含量/% 84.9 82~83 碳转化率/% >98 96~98 有效气比煤耗/kg/km3 535 约547 有效气比氧耗/m3/km3 314 约336 表5 气化用煤质分析表项目数值项目数值项目数值工业分析元素分析灰熔点/℃水分(Mad)/% 2.18 全硫(Stad)/% 2.84 DT 1090 灰分(Ad)/% 7.32 碳(Cad)/% 74.73 ST 1100 挥发分(Vdaf)/% 45.44 氢(Had)/% 5.13 HT 1120 固定碳(FC)/% 49.46 氧(Oad)/% 8.77 FT 1130 氮(Nad)/% 1.20多喷嘴气化炉与单烧嘴气化炉相比,有效气成分提高2~3个百分点,CO2含量降低2~3个百分点,碳转化率提高2~3个百分点,比煤耗可降低约2.2%,吨甲醇煤耗减少100~150kg,比氧耗可降低6.6~8%,这是很有吸引力的。