铸件生产工艺过程控制补充规定 (1)
铸造生产过程的质量控制
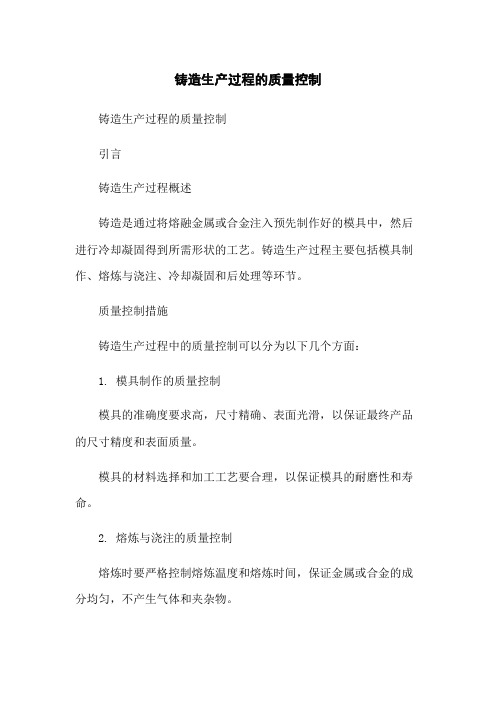
铸造生产过程的质量控制铸造生产过程的质量控制引言铸造生产过程概述铸造是通过将熔融金属或合金注入预先制作好的模具中,然后进行冷却凝固得到所需形状的工艺。
铸造生产过程主要包括模具制作、熔炼与浇注、冷却凝固和后处理等环节。
质量控制措施铸造生产过程中的质量控制可以分为以下几个方面:1. 模具制作的质量控制模具的准确度要求高,尺寸精确、表面光滑,以保证最终产品的尺寸精度和表面质量。
模具的材料选择和加工工艺要合理,以保证模具的耐磨性和寿命。
2. 熔炼与浇注的质量控制熔炼时要严格控制熔炼温度和熔炼时间,保证金属或合金的成分均匀,不产生气体和夹杂物。
浇注时要控制浇注温度和速度,避免产生气孔、夹渣和缩松等缺陷。
3. 冷却凝固的质量控制控制冷却速度和冷却方式,以避免产生组织缺陷,如晶粒过大、晶界不清晰等。
控制凝固过程中的温度变化,以避免产生应力和变形。
4. 后处理的质量控制清理杂质和缺陷,如夹渣、气孔等。
进行热处理、表面处理或机械加工,以改善产品的性能和表面质量。
质量控制方法为了有效控制铸造生产过程中的质量,可以采取以下几种方法:1. 设计质量控制在产品设计阶段,就应考虑产品的铸造性,合理设计产品的几何形状和壁厚,减少可能出现的缺陷和变形。
2. 工艺参数控制对每个工艺环节中的关键参数进行严格控制,如熔炼温度、浇注温度和速度等。
在铸造过程中,通过实时监测温度、压力和流速等参数,进行及时调整和控制。
3. 检测和检验使用各种检测设备和仪器,如X射线探伤仪、超声波检测仪等,对产品进行无损检测,以发现和排除可能存在的缺陷。
进行物理和化学性能的检验,如拉伸试验、硬度测试和成分分析等。
4. 信息化管理建立完善的质量管理体系,进行全过程的质量记录和数据分析,发现问题并采取措施进行改进。
运用信息化技术,实现数据的实时监控和追溯,提高生产过程的透明度和可控性。
结论铸造生产过程的质量控制是确保最终产品质量的重要环节。
通过合理的质量控制措施和方法,可以有效避免铸造过程中可能出现的缺陷和变形,提高产品的质量和性能。
铸造生产过程质量控制点

铸造生产过程质量控制点铸造生产过程质量控制点铸造生产过程质量控制点是指在铸造生产过程中,通过采取一系列控制措施,以确保铸件质量达到设计要求的关键环节和要点。
铸造生产过程质量控制点的正确选择和实施,对于提高铸造生产过程质量、减少废品率具有重要意义。
以下是铸造生产过程中一些常见的质量控制点。
1.原材料控制原材料是影响铸件质量的关键因素之一。
在铸造生产过程中,需要对原材料进行严格的控制,包括熔炼炉料及加入剂的选择、原材料配比的控制等。
只有选择合适的原材料并正确使用,才能保证铸造产品质量的稳定性和一致性。
2.熔炼控制熔炼过程是铸造生产中最关键的环节之一。
在熔炼过程中,需要控制炉温、炉料的投入速度、炉内压力等参数,以确保金属液的质量稳定。
对于特殊材料的熔炼过程,还需要控制熔炼环境的气氛、熔炼时间等因素。
3.浇注控制浇注过程是将熔融金属注入到型腔中的过程。
在浇注过程中,需要控制浇注速度、浇注温度、浇注方式等因素,以保证浇注质量和铸件的致密性。
还需要控制浇注过程中金属液的气体排出情况,避免气孔的产生。
4.型腔控制型腔是铸造中形成铸件形状和尺寸的关键部位,对铸件质量有着重要影响。
型腔控制包括型腔设计、制造和维护等环节。
必须确保型腔的准确尺寸和光洁度,避免型腔表面的破损和变形,以确保铸件的形状精度和表面质量。
5.冷却控制冷却过程是铸件从熔融状态到固态过程中的一个关键环节。
在冷却过程中,需要控制冷却速度、冷却介质、冷却时间等因素,以保证铸件组织的均匀性和致密性。
还需要控制冷却过程中的温度梯度,避免铸件产生应力和变形。
6.热处理控制对于某些特殊材料或要求较高的铸件,还需要进行热处理过程。
热处理过程包括加热、保温和冷却等环节。
在热处理过程中,需要控制温度、保温时间、冷却速度等参数,以确保铸件组织的改善和性能的提升。
7.表面处理控制铸件的表面处理是为了提高铸件的表面质量和耐腐蚀性。
表面处理包括喷砂、抛光、电镀等工艺。
在表面处理过程中,需要控制处理剂的使用和浸溶时间,以保证铸件表面的光洁度和处理效果。
铸件质量控制计划
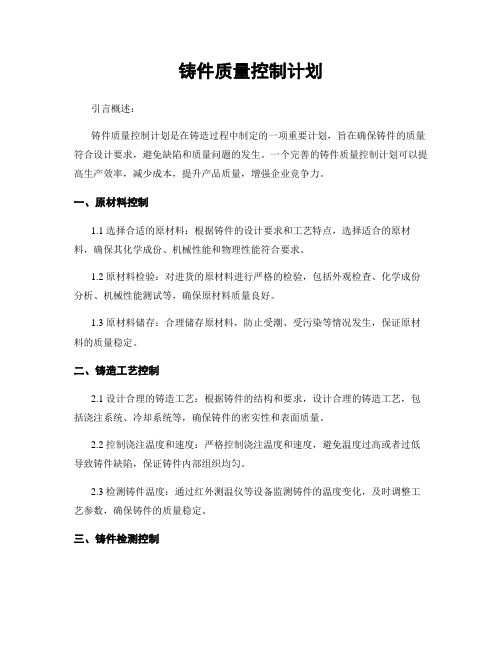
铸件质量控制计划引言概述:铸件质量控制计划是在铸造过程中制定的一项重要计划,旨在确保铸件的质量符合设计要求,避免缺陷和质量问题的发生。
一个完善的铸件质量控制计划可以提高生产效率,减少成本,提升产品质量,增强企业竞争力。
一、原材料控制1.1 选择合适的原材料:根据铸件的设计要求和工艺特点,选择适合的原材料,确保其化学成份、机械性能和物理性能符合要求。
1.2 原材料检验:对进货的原材料进行严格的检验,包括外观检查、化学成份分析、机械性能测试等,确保原材料质量良好。
1.3 原材料储存:合理储存原材料,防止受潮、受污染等情况发生,保证原材料的质量稳定。
二、铸造工艺控制2.1 设计合理的铸造工艺:根据铸件的结构和要求,设计合理的铸造工艺,包括浇注系统、冷却系统等,确保铸件的密实性和表面质量。
2.2 控制浇注温度和速度:严格控制浇注温度和速度,避免温度过高或者过低导致铸件缺陷,保证铸件内部组织均匀。
2.3 检测铸件温度:通过红外测温仪等设备监测铸件的温度变化,及时调整工艺参数,确保铸件的质量稳定。
三、铸件检测控制3.1 X射线探伤:对铸件进行X射线探伤,检测铸件内部是否存在气孔、夹杂等缺陷,及时发现并进行修补。
3.2 超声波探伤:利用超声波技术对铸件进行探伤,检测铸件的内部结构是否均匀,确保铸件的质量可靠。
3.3 磁粉探伤:采用磁粉探伤技术对铸件进行检测,发现铸件表面是否存在裂纹、夹杂等缺陷,及时处理。
四、表面处理控制4.1 砂型表面处理:对砂型进行喷涂、涂覆等表面处理,保证砂型表面光滑、坚固,避免对铸件表面造成损伤。
4.2 清理铸件表面:清理铸件表面的氧化皮、砂粒等杂质,确保铸件表面光洁,提高铸件的外观质量。
4.3 表面涂层处理:根据需要对铸件进行表面涂层处理,如喷漆、镀层等,提高铸件的耐腐蚀性和美观度。
五、质量记录与追溯5.1 记录生产数据:对每一批次生产的铸件进行详细记录,包括原材料检验报告、生产工艺参数、检测结果等,便于追溯质量问题。
铸件质量控制计划

铸件质量控制计划引言概述铸件质量控制计划是在铸造过程中制定的一项重要计划,旨在保证铸件的质量达到客户要求的标准。
通过制定合理的质量控制计划,可以有效地避免铸件浮现缺陷和质量问题,提高产品的合格率和客户满意度。
一、原材料控制1.1 选择合适的原材料在铸件生产过程中,选择合适的原材料是保证铸件质量的关键。
应根据产品的要求和使用环境,选择合适的原材料,确保其化学成份和性能符合标准要求。
1.2 严格把控原材料质量在采购原材料时,应严格把控原材料的质量,检验其化学成份、机械性能等指标是否符合要求。
必要时可以委托第三方机构进行检测,确保原材料的质量稳定可靠。
1.3 建立原材料质量档案建立原材料的质量档案,记录原材料的来源、质量证明、检测报告等信息,以便追溯和核查原材料的质量。
二、生产工艺控制2.1 制定详细的工艺流程制定详细的铸造工艺流程,包括模具设计、熔炼工艺、浇铸工艺等环节,确保每一个步骤都符合标准要求。
2.2 严格执行工艺规范在生产过程中,严格执行工艺规范,确保每道工序按照要求进行,避免浮现疏漏和错误。
2.3 加强过程监控加强生产过程的监控,及时发现和处理问题,确保生产过程的稳定性和可控性。
三、设备保养和维护3.1 定期检查设备状态定期检查铸造设备的状态,确保设备运行正常,避免因设备故障导致的质量问题。
3.2 建立设备维护计划建立设备维护计划,定期进行设备维护和保养,保证设备的正常运行和使用寿命。
3.3 培训维护人员对设备维护人员进行培训,提高其维护技能和意识,确保设备维护工作的有效进行。
四、质量检验和控制4.1 制定质量检验标准制定铸件的质量检验标准,包括外观质量、尺寸精度、化学成份、机械性能等指标,确保检验的全面和准确。
4.2 建立质量检验流程建立质量检验流程,明确检验的步骤和责任人,确保每一个环节都得到有效执行。
4.3 强化质量问题处理对于发现的质量问题,要及时进行处理和整改,分析问题原因,并采取有效措施避免问题再次发生。
铸造生产过程的质量控制

铸造生产过程的质量控制铸造生产过程的质量控制1. 原材料的质量控制铸造过程中使用的原材料主要包括金属合金和砂型材料。
为了保证产品的质量,必须对原材料进行质量控制。
具体控制措施包括:选择高质量的原材料供应商,并建立稳定的供应链。
对原材料进行严格的检验和筛选,确保其符合产品的要求。
对原材料进行化学成分分析和物理性能测试,以确保其质量符合标准。
2. 模具制造过程的质量控制模具是铸造过程中的重要工具,其质量直接影响到产品的精度和表面质量。
为了保证模具的质量,必须对模具制造过程进行质量控制。
具体控制措施包括:制定模具制造工艺和工作指导书,确保每个环节都符合标准要求。
对模具材料进行质量检查和测试,以确保其质量达到要求。
对模具零部件进行尺寸检验和装配检验,确保模具的准确性和稳定性。
3. 铸造工艺参数的质量控制铸造工艺参数是影响产品质量的重要因素,必须进行严格的质量控制。
具体控制措施包括:确定合理的铸造温度和压力,以确保产品的致密性和机械性能。
控制铸造过程中的冷却速率和凝固时间,以确保产品的表面质量和内部组织结构。
对铸造过程中的熔炼和浇注过程进行监控和调整,以确保产品的成分和收缩率符合要求。
4. 产品质量的检验和测试铸造产品的质量必须进行全面的检验和测试,以确保其质量达到要求。
具体控制措施包括:对产品外观进行目测和尺寸测量,以检查产品的表面质量和尺寸精度。
对产品进行物理性能测试,包括硬度、拉伸强度等指标。
对产品进行化学成分分析,以确保其成分符合标准要求。
对产品进行无损检测,如X射线检测、超声波检测等,以检查产品的内部质量。
5. 不良品的处理和纠正措施在质量控制过程中,可能会出现一些不合格的产品或过程。
为了保证产品质量,必须及时进行处理和纠正措施。
具体控制措施包括:对不良品进行分类和评估,确定其影响范围和原因。
采取相应的纠正措施,如返工、修复、补救等。
对纠正措施进行跟踪和评估,以确保问题得到彻底解决。
以上就是铸造生产过程中常用的质量控制方法和措施。
铸造工艺操作规程

铸造工艺操作规程第一章总则第一条本操作规程适用于铸造工艺中的各个环节,对于保证铸件质量、提高生产效率具有重要意义。
第二条本操作规程的目的是规范铸造工艺操作流程,保障铸件质量,确保生产安全。
第三条操作规程中的术语定义参照相关国家标准进行解释。
第四条管理人员应对操作人员进行相关知识的培训,确保操作人员具备相关技能。
第五条所有操作人员必须遵守本操作规程,严禁个人行为违反或忽视操作规程。
第二章铸模制备第六条铸模制备前应检查模具是否完整,有无破损及模具内有无异物。
第七条铸模材料应符合相关标准,模具表面应光滑平整。
第八条铸模制备前应根据铸件形状和尺寸选用适当的模具。
第九条铸模制备前应清除模具内外的杂质,确保模具干净。
第十条铸模制备时,应将模具加热到适当温度,以提高铸造效果。
第三章铸造操作第十一条铸造前应确认铸造设备和铸造材料的质量符合要求。
第十二条铸造前应先预热模具,然后按照工艺要求将金属液体倒入模具内。
第十三条铸造过程中应严格控制液体温度,保持注入速度平稳。
第十四条铸造过程中应根据铸件形状和尺寸调整模具的压力。
第十五条铸造完成后,应及时进行冷却处理,防止铸件产生变形。
第四章检验和修复第十六条铸造完成后,应对铸件进行外观检查,确保没有裂纹、气孔等缺陷。
第十七条铸件尺寸应符合图纸要求,凡超过公差范围的应进行修复。
第十八条铸件修复时应根据实际情况选用合适的修复工艺和材料。
第十九条铸件修复后应进行再次检验,确保修复后的铸件质量符合要求。
第五章安全注意事项第二十条铸造过程中应配备必要的安全设备,保障操作人员的人身安全。
第二十一条铸造过程中严禁操作人员戴带、手表等物品,以免发生事故。
第二十二条铸造过程中应配备合适的防护用具,如手套、护目镜等。
第二十三条铸造过程中如有异常情况发生,应立即停工并报告相关人员。
第二十四条铸造设备和工作区域应保持清洁,防止杂物堆积引发事故。
第六章管理和监督第二十五条管理人员应定期检查生产现场,确保操作规程的执行。
铸造工艺管理规定

铸造工艺管理规定编制:审核:批准:1目的规范铸造工艺,确保铸造车间生产过程得到有效控制,特制定本规程。
2适用范围适用于铸造车间生产组织。
3职责3.1铸造工艺员负责制定和修改铸造生产工艺。
3.2铸造车间主任负责组织车间各岗位人员按铸造工艺进行生产。
3.3铸造检验员负责监督铸造车间生产工艺执行情况。
3.4技术厂长负责考核铸造车间违反生产工艺的情况。
4管理规定4.1制芯4.1.1铸造车间主任负责根据铸造周计划,编制“型芯作业计划”4.1.2制芯工每次投入混砂碾中的树脂砂不得超过200kg,按照0.6%的比例加入A组/B组冷芯树脂进行混砂,每次混砂时间不得低于20秒。
4.1.3射芯机制芯将混好的芯砂要立即从混砂碾中投入射芯机料斗中,合模前芯盒表面均匀喷涂脱模剂,然后按照《射芯机操作规程》进行合模吹三乙胺,吹胺时间不得低于60秒。
4.1.4启模出芯前应戴好防护手套,轻度均匀用力从芯盒中取出砂芯,放入货架上晾干备用。
4.1.5当班结束射芯机料斗内、混砂机内必须清理干净,严禁残留芯砂。
4.2混粘土型砂4.2.1浇铸工倒完铁水后将铸件从砂型中扒出并运送到清砂工作区域内存放,混砂工负责清理废砂内残留的铁渣、水冒口。
4.2.2混砂工先将800kg的新砂,均匀的洒在废砂上面,再用装载机推入混砂线的回收砂料斗内过筛,把过筛分离出的废芯砂、废铁分类存放。
4.2.3混砂工戴好防护面具,把陶土、煤粉依次投入混砂线内各自的料斗中备用。
4.2.4严格按照《混砂线操作规程》开机混砂。
4.2.5加料时间为陶土:3秒;煤粉:5秒;水:18秒;混砂时间80秒,严禁私自更改混砂配比和混砂时间。
4.2.6混砂工负责填写每班次的《混砂用料记录》。
4.3造型4.3.1造型工在造型之前,先检查模型在造型机型板上是否牢固,模型是否完好,型板上的定位销是否松动,然后把模型均匀的涂上脱模剂,按照《造型机操作规程》振砂造型。
4.3.2变形、开焊的砂箱严禁使用,有铁锈的砂箱要用铁锤轻击砂箱,震落铁锈方可使用。
铸造工艺操作规程(三篇)

铸造工艺操作规程第一章总则第一条为规范铸造工艺操作,确保生产过程的安全、质量和效益,特制定本规程。
第二条铸造工艺操作规程(以下简称规程)适用于铸造生产过程中的各个环节。
第三条规程的制定主要依据国家相关标准、法律法规和公司内部要求。
第四条违反规程的铸造工艺操作行为,将按照公司相关制度进行处罚,情节严重的将追究责任。
第二章生产准备第五条铸造工艺操作前,必须做好生产准备工作,包括材料准备、设备准备和人员组织。
第六条材料准备应按照工艺要求进行,材料必须符合国家标准和规范。
第七条设备准备应确保设备的正常运行和安全性能,必要时进行维修和保养。
第八条人员组织要合理安排,确保操作人员经过培训和合格考核,具备相关技能和操作经验。
第九条高温和有毒有害物质的准备和处理要合理安排,严格遵守安全操作规程。
第三章铸造工艺操作规程第十条铸造工艺操作过程中必须遵守以下规程:(一)严格按照工艺流程进行操作,严禁擅自更改或跳过工艺步骤。
(二)保持操作区域的整洁、干净,防止杂物进入工艺流程。
(三)确保操作人员穿戴统一的劳动防护用具,如手套、护目镜、防护服等。
(四)严禁无证上岗和酒后操作,操作人员必须保持良好的工作状态。
(五)严格遵守有关火灾预防规定,禁止在操作区域吸烟、使用明火等危险行为。
(六)操作过程中,要及时记录操作参数和异常情况,并向上级汇报。
(七)遵循能耗和环保要求,控制能源消耗,合理利用资源。
第四章质量控制第十一条铸造工艺操作中必须严格执行质量控制措施,确保产品质量符合要求。
第十二条在生产过程中,必须对原材料进行质量检查,严禁使用不合格材料。
第十三条操作人员必须按照质量控制要求,进行操作记录和产品检验,确保产品合格。
第十四条必要时,要进行工艺过程控制,包括温度、时间和速度等参数的调整。
第十五条接受质检部门的监督和检查,按照规定提交样品和资料。
第五章安全保障第十六条在铸造工艺操作过程中,必须严格遵守安全规定,确保安全生产。
第十七条在高温环境操作时,必须做好防火防烫措施,保证操作人员的人身安全。
球墨铸铁铸件的补缩工艺[1]
![球墨铸铁铸件的补缩工艺[1]](https://img.taocdn.com/s3/m/95563257ad02de80d4d84021.png)
收稿日期:2010-09-19; 修订日期:2010-10-20作者简介:牟行辉(1974- ),四川射洪人,工程师.从事铸铁件铸造工艺设计和质量控制工作.Email:m u_xinghu i@V ol.32N o.1Jan.2011铸造技术F OU N DRY T ECH NO LO GY工艺技术 Technology球墨铸铁铸件的补缩工艺牟行辉(陕西秦川机床工具集团有限公司,陕西宝鸡721009)摘要:通过分析和总结在生产实践过程中球墨铸铁铸件产生缩孔缩松缺陷以及成功解决办法,对球铁铸件凝固收缩理论提出理解和看法:铸件的补缩及缺陷产生取决于压力,由于球铁的凝固特性使石墨化膨胀和凝固收缩分离,薄壁件截面凝固差异不明显,石墨化膨胀压力无法有效利用,厚大件的截面凝固的差异大,容易实现石墨化膨胀压力的利用。
铸造补缩工艺的设计原则就是提供并保持这样的压力,对薄壁要强调外部压力补缩,厚壁则充分利用石墨化膨胀压力自补缩。
关键词:球墨铸铁;缩孔缩松;补缩;凝固压力中图分类号:TG255 文献标识码:A 文章编号:1000-8365(2011)01-0007-04Feeding Process of the Ductile Iron CastingsMU Xing -hui(Qinchuan Machine Tool Group C orp.,Baoji 721009,C hina)Abstract:By analyzing and summ arizin g the process of practice in the production of du ctile iron castings produ ced Shrinkage Defects an d successful solution.Make to some un derstand an d view of du ctile iron castings solidification theory:Feeding a castin g depend upon the pressure.For the solidification ch aracteristic of th e sph eroidal graph ite cast iron,th e expan sion of the graphitization are not syn chronized shrin k.In thin wall,no fu nction of the the expansion pressure of the graphitization because fewer division of solidification,and the thick wall,the more division with solidification in section,so th e expan sion and the shrink will be segistration.So the inten tion of the feeding process disign are su pporting and keepin g on pressu re.Th e th in wall,pressu re shall be su pported with others,and the thick wall,th e pressu re maybe exploit th e th e the expansion of the graphitization.Key words:Du ctile C ast Iron;Shrinkage;Feedin g;Solidification Pressure1 球铁凝固收缩工艺理论对球墨铸铁件采用什么样的工艺措施解决和防止缩孔缩松,目前的共识是,铸型必须具有足够的刚性和强度,化学成分接近共晶成分、加强球化和孕育处理以产生足够的石墨化膨胀。
铸造业生产规章制度

铸造业生产规章制度第一章总则第一条为加强铸造业生产管理,提高生产效率,确保产品质量,保障员工安全,制定本规章制度。
第二条本规章制度适用于公司所有铸造业生产环节的管理,具体包括原料采购、生产过程控制、产品质量检验等。
第三条公司铸造业生产管理委员会负责本规章制度的制定、执行和监督。
第四条公司铸造业生产管理委员会设立生产监督部门,负责具体执行本规章制度的工作。
第二章原料采购管理第五条公司铸造业生产采购部门需按照公司采购管理制度进行原料采购工作,保证采购的原料符合国家、地方法规标准。
第六条原料采购部门应对每批原材料进行进货检验,检测各项指标符合公司要求。
第七条原料采购部门应保存采购原料的相关证明文件,包括合格证、质量检测报告等。
第八条公司铸造产品的原料必须进行分级储存,在符合条件的库房中进行储存管理。
第九条公司铸造产品的原料必须按照规定的比例参与生产过程,不得随意更改使用。
第三章生产过程控制第十条公司铸造产品的生产过程需按照工艺流程进行,并保证生产过程中的各项要求。
第十一条生产过程控制应加强现场管理,保证生产现场整洁有序,设备正常运转。
第十二条生产过程中必须按照工艺要求进行参数调节,保证产品质量稳定。
第十三条生产过程中需定期进行质量抽检,对产品质量进行监控。
第十四条生产过程中必须严格遵守安全操作规程,确保员工安全。
第四章产品质量检验第十五条公司铸造产品的质量检验应根据国家、行业标准进行,确保检验准确可靠。
第十六条产品质量检验部门必须对每批产品进行检验,不合格品必须及时处理。
第十七条对于关键产品,需进行重点检验,并保存检验记录。
第十八条产品质量检验结果需及时反馈给生产部门,并进行相关处理。
第五章安全生产管理第十九条公司铸造产品生产过程中,必须严格遵守安全操作规程、安全操作流程,保障员工安全。
第二十条公司必须定期进行安全培训,提高员工安全意识。
第二十一条生产现场必须配备安全设施,保障员工生命财产安全。
第二十二条生产设备必须定期检查维护,确保设备正常运转。
铸造生产过程质量控制点

铸造生产过程质量控制点一、原料检验原料检验是确保产品质量的第一步,主要包括铸造用沙、金属材料和添加剂等的检验。
1.铸造用沙的检验:包括沙粒度检测、含水率检测、化学成分和矿物组成检测等。
沙粒度应符合设计要求,含水率应控制在一定范围内,化学成分和矿物组成应符合标准。
2.金属材料的检验:包括铁水、铝水、铜液等金属的化学成分检测、包括有害杂质的检测等。
金属的化学成分应符合设计要求,有害杂质应控制在合理范围内。
3.添加剂的检验:包括炭素稳定剂、铁矿粉、红土等添加剂的化学成分检测、水分检测等。
添加剂的化学成分应符合标准要求,水分应控制在合理范围内。
二、铸型制备铸型制备是铸造过程中至关重要的环节,主要包括模具制备和芯制备两个方面。
1.模具制备:模具制备的关键是模具材料的选择和加工工艺的控制。
模具材料应具有足够的强度和韧性,并且耐用性好。
加工工艺应控制模具尺寸的精度和表面质量,以及模腔的几何形状和位置精度。
2.芯制备:芯的制备需要控制芯盒尺寸的精度、芯材的化学成分和物理性能、芯粘结剂的配比和固化工艺等。
芯盒尺寸的精度直接影响最终铸件的尺寸精度,芯材的物理性能与化学成分直接关系到芯的强度和稳定性,芯粘结剂的配比和固化工艺决定芯的强度和表面质量。
三、铸造操作铸造操作是铸造生产中最关键的环节,主要包括浇注、冒口设置、冷却措施和除渣等。
1.浇注:控制浇注的速度、浇注的位置和浇注的角度等,以防止铸件内部出现夹渣、气孔等缺陷。
2.冒口设置:合理设置冒口位置和数量,以利于铸件内部的气体和夹渣排除,防止缩孔、砂眼等缺陷的产生。
3.冷却措施:采取适当的冷却措施,控制最终铸件的显微组织和性能。
包括调整浇注温度、铸件的冷却速率和冷却时间等。
4.除渣:及时清除铸件上的渣滓,防止渣滓对铸件品质的影响。
四、冷却处理冷却处理是铸件的重要环节,主要包括冷却速率、冷却时间和冷却介质等控制。
1.冷却速率:控制铸件的冷却速率,会影响到铸件的显微组织和力学性能。
铸造生产过程的质量控制

铸造生产过程的质量控制铸造生产过程的质量控制1·引言本文档旨在提供一个铸造生产过程的质量控制参考框架,以确保铸造产品质量达到预期标准。
本文档分为以下几个部分:质量策划、工艺流程控制、工艺参数控制、检验与测试、不合格品处理和纠正措施。
2·质量策划在铸造生产过程中,质量策划是确保产品质量的重要步骤。
以下是质量策划的细化内容:2·1 确定产品质量标准和规范2·2 制定产品及生产过程检验计划2·3 根据产品特性确定质量保证措施2·4 制定质量培训计划2·5 确定质量审核和监督措施3·工艺流程控制良好的工艺流程控制是确保铸造生产过程质量稳定的关键。
以下是工艺流程控制的细化内容:3·1 设计工艺流程图3·2 确定工艺参数范围3·3 制定操作规程和作业指导书3·4 确定关键控制点及控制方法3·5 制定工艺异常处理程序4·工艺参数控制控制工艺参数是确保产品质量一致性的关键。
以下是工艺参数控制的细化内容:4·1 确定关键工艺参数4·2 设定合理的工艺参数范围4·3 使用计量设备进行工艺参数检测与记录4·4 制定工艺参数调整措施5·检验与测试检验与测试是铸造生产过程中质量控制的重要环节,以保证产品符合标准和规范要求。
以下是检验与测试的细化内容:5·1 制定检验项目及方法5·2 确定样本容量和频率5·3 质量控制检验和产品检验5·4 缺陷评定和分类5·5 检验记录和报告6·不合格品处理对于不合格品,需要采取合适的处理措施,以确保产品质量和客户满意度。
以下是不合格品处理的细化内容:6·1 不合格品鉴定和分类6·2 制定不合格品处理程序6·3 进行原因分析和改进措施制定6·4 进行不合格品追溯和召回措施7·纠正措施在发现质量问题时,需要及时采取纠正措施以防止再次发生。
铸造生产过程质量控制点
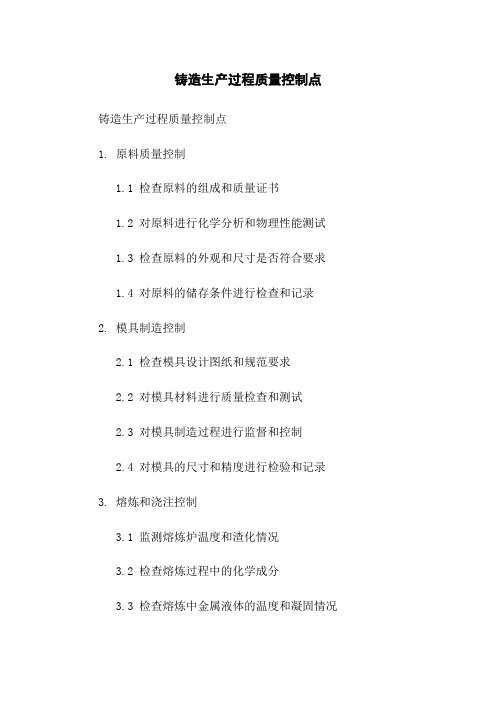
铸造生产过程质量控制点铸造生产过程质量控制点1. 原料质量控制1.1 检查原料的组成和质量证书1.2 对原料进行化学分析和物理性能测试 1.3 检查原料的外观和尺寸是否符合要求1.4 对原料的储存条件进行检查和记录2. 模具制造控制2.1 检查模具设计图纸和规范要求2.2 对模具材料进行质量检查和测试2.3 对模具制造过程进行监督和控制2.4 对模具的尺寸和精度进行检验和记录3. 熔炼和浇注控制3.1 监测熔炼炉温度和渣化情况3.2 检查熔炼过程中的化学成分3.3 检查熔炼中金属液体的温度和凝固情况3.4 对铸件的浇注过程进行监控和记录4. 铸造件外观和尺寸控制4.1 对铸件外观进行目测和检验4.2 使用光谱仪和显微镜对铸件进行化学成分和微观结构的分析4.3 使用激光扫描仪等设备对铸件的尺寸进行测量和记录4.4 对铸件进行外观和尺寸的合格判定5. 热处理控制5.1 对铸件进行退火、正火、淬火等热处理工艺的控制5.2 监测热处理过程中的温度和时间5.3 对热处理后的铸件进行硬度测试和金相分析5.4 对热处理后的铸件进行尺寸和外观的检验和记录6. 特殊工艺控制6.1 对特殊工艺参数进行监控和调整6.2 对特殊工艺工序进行质量检查和控制6.3 对特殊工艺产品的性能进行测试和验证附件:1. 铸造原料的质量证书样本2. 模具设计图纸和规范要求范本3. 铸造工艺流程图4. 铸造件外观和尺寸检验记录表5. 热处理工艺参数记录表6. 特殊工艺工序质量检查表法律名词及注释:1. 质量证书:指由生产厂商或供应商提供的证明原料质量合格的文件。
2. 模具设计图纸:指铸造过程中用于指导模具制造的图纸和规范要求。
3. 化学成分:指铸件材料中各元素的含量。
4. 光谱仪:用于分析金属材料化学成分和物理性能的仪器。
5. 显微镜:用于观察和分析铸件的微观结构和缺陷的仪器。
6. 激光扫描仪:用于测量和记录铸件尺寸的仪器。
7. 退火:指通过加热和冷却的方式改变金属材料的组织结构和性能的工艺。
铸件加工规章制度模板范本

铸件加工规章制度模板范本一、总则为了加强铸件加工车间的管理,规范员工的行为,保障生产安全,提高生产效率,提高产品质量,制定本规章制度。
本规章制度适用于铸件加工车间的全体员工。
二、生产管理1. 员工必须接受岗前培训,熟悉各自的岗位职责和工作流程,经考核合格后方可上岗。
2. 员工必须严格遵守操作规程,正确使用设备、工具,禁止违章操作。
3. 设备应定期进行维护、保养,确保设备正常运行。
4. 生产过程中,员工应做好自检、互检工作,确保产品质量。
5. 生产过程中,发现问题应立即报告班长或工程师,采取措施予以解决。
6. 生产结束后,员工应做好设备、工作现场的清洁工作,关闭电源、水源等。
三、质量管理1. 员工必须了解并掌握产品质量标准,严格按照标准进行生产。
2. 员工应做好生产过程中的质量控制,确保产品质量。
3. 对于不合格品,应立即标识、隔离,并报告班长或工程师处理。
4. 班长或工程师应对不合格品进行分析,找出原因,制定改进措施,并跟踪实施效果。
5. 定期进行质量培训,提高员工的质量意识。
四、安全管理1. 员工必须遵守安全生产规定,佩戴劳动防护用品。
2. 车间内禁止吸烟、使用明火,严禁携带易燃、易爆物品进入车间。
3. 设备运行中,严禁触摸运动部件,禁止在设备运行时进行维修、保养。
4. 车间内消防器材应定点放置,专人管理,员工应熟练掌握消防器材的使用方法。
5. 定期进行安全检查,发现问题及时整改。
五、环境管理1. 员工应保持工作环境的整洁,定期进行清扫、整理。
2. 废料、废液应按照公司规定进行分类、存放,不得随意丢弃。
3. 车间内应保持通风良好,确保员工的健康。
4. 定期进行环境检测,确保车间内环境符合要求。
六、人员管理1. 员工应按时到岗,做好交接班工作。
2. 员工应遵守公司纪律,服从领导安排。
3. 员工之间应相互尊重,团结协作,共同完成生产任务。
4. 定期进行员工培训,提高员工的业务水平。
七、奖惩制度1. 对违反本规章制度的员工,公司将按照相关规定给予处罚。
铸造生产过程质量控制点
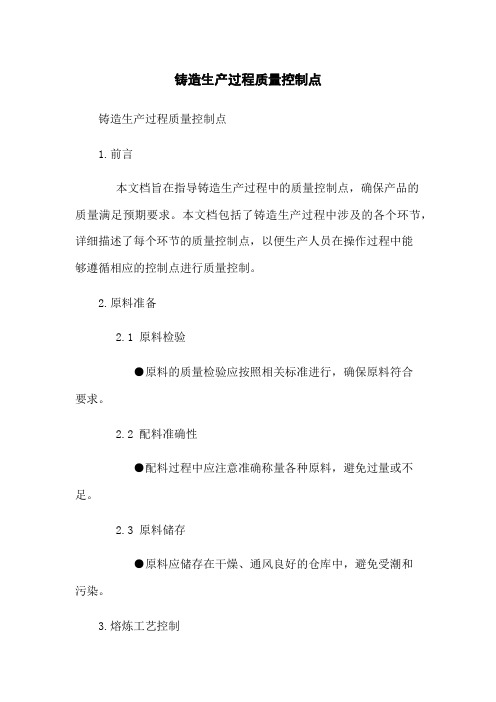
铸造生产过程质量控制点铸造生产过程质量控制点1.前言本文档旨在指导铸造生产过程中的质量控制点,确保产品的质量满足预期要求。
本文档包括了铸造生产过程中涉及的各个环节,详细描述了每个环节的质量控制点,以便生产人员在操作过程中能够遵循相应的控制点进行质量控制。
2.原料准备2.1 原料检验●原料的质量检验应按照相关标准进行,确保原料符合要求。
2.2 配料准确性●配料过程中应注意准确称量各种原料,避免过量或不足。
2.3 原料储存●原料应储存在干燥、通风良好的仓库中,避免受潮和污染。
3.熔炼工艺控制3.1 炉温控制●确保炉温达到合适的熔化点,避免熔炼温度过高或过低。
3.2 熔炼时间控制●控制熔炼时间,使金属能够充分熔化并达到均匀状态。
3.3 炉膛清洁●定期对炉膛进行清洁,清除炉渣和其他杂质。
4.浇注工艺控制4.1 浇注温度控制●控制浇注温度,确保金属在浇注过程中不过热或过冷。
4.2 浇注速度控制●控制浇注速度,使金属能够充分填充模具,并形成理想的形状。
4.3 浇注压力控制●控制浇注压力,确保金属在浇注过程中能够均匀充实。
5.硬化工艺控制5.1 冷却时间控制●控制冷却时间,使铸件能够充分硬化。
5.2 冷却介质控制●选择合适的冷却介质,确保铸件冷却均匀。
5.3 温度检测●对冷却后的铸件进行温度检测,确保其达到硬化要求。
6.表面处理工艺控制6.1 砂型清理●对铸件表面的砂型进行清理,移除可能存在的杂质和砂粒。
6.2 表面修整●对铸件表面进行修整,去除可能存在的凹凸不平的部分。
6.3 防锈处理●对铸件进行防锈处理,防止氧化和腐蚀。
附件:●附件1、原料质量检验标准●附件2、浇注工艺参数记录表●附件3、硬化工艺参数记录表●附件4、表面处理工艺记录表法律名词及注释:●1.法律名词1、注释1●2.法律名词2、注释2●3.法律名词3、注释3。
铸件加工规章制度范本

铸件加工规章制度范本一、目的为了保障铸件加工质量,提高生产效率,确保员工安全,维护企业利益,特制定本规章制度。
本制度适用于我公司铸件加工车间的全体工作人员。
二、范围1. 生产准备(1)生产前应根据生产计划和技术要求,准备好所需的设备、工具、材料等。
(2)对设备进行常规检查,确保设备正常运行。
(3)对新员工进行岗位培训,确保员工掌握所需技能和安全知识。
2. 生产过程(1)严格按照工艺规程和操作规程进行生产,确保产品质量。
(2)做好生产过程中的自检和互检,发现问题及时报告班长或质检员。
(3)保持工作环境整洁,定期清理设备和工作场地。
(4)严格控制原材料和辅料的质量,不合格的原材料和辅料不得投入使用。
(5)加强设备维护保养,确保设备精度。
3. 质量管理(1)实行质量管理责任制,各级管理人员和员工都要积极参与质量管理。
(2)严格把控生产过程中的各个环节,确保产品符合技术要求。
(3)对产品质量问题进行追踪,找出原因,采取措施予以改进。
(4)定期对产品质量进行统计分析,提高产品质量水平。
4. 安全生产(1)员工必须严格遵守安全生产规定,佩戴劳动防护用品。
(2)生产过程中应遵循安全操作规程,防止事故发生。
(3)定期进行安全教育培训,提高员工安全意识。
(4)设备应定期进行安全检查,发现问题及时整改。
5. 环境保护(1)严格执行环保法规,减少生产过程中的环境污染。
(2)妥善处理废气、废水、废渣等废弃物,防止对环境造成污染。
(3)加强噪声治理,降低噪声对员工和周边环境的影响。
(4)推广绿色生产,提高资源利用率。
6. 员工培训和激励(1)定期组织员工参加技能培训,提高员工业务水平。
(2)设立奖励制度,激励员工提高工作效率和质量。
(3)加强员工之间的沟通与协作,提高团队凝聚力。
(4)关心员工生活,解决员工困难,提高员工满意度。
三、惩罚措施1. 违反本制度的相关规定,造成产品质量问题的,视情节轻重,对相关人员进行警告、罚款、降级等处罚。
金属铸件生产质量管理制度

金属铸件生产质量管理制度1. 质量管理体系概述金属铸件生产质量管理制度是为了确保金属铸件生产过程中的质量控制,提高产品质量,满足用户需求而建立的一套制度。
该制度涵盖了质量管理的各个方面,包括质量目标、责任分工、流程控制、质量检验、纠正措施等。
通过有效实施质量管理制度,可以不断改善生产过程中的质量问题,提高金属铸件的一次合格率,降低不良品率,提升企业的竞争力。
2. 质量目标与策略2.1 质量目标(1)提高金属铸件生产一次合格率,力争达到100%;(2)降低不良品率,将不良品率控制在5%以内;(3)持续改进产品质量,提高用户满意度。
2.2 质量策略(1)严格按照技术规范和标准操作流程进行生产;(2)强化员工培训,提高技术水平和质量意识;(3)加强设备维护保养,确保设备正常运行;(4)建立完善的质量评估体系,及时发现和纠正问题。
3. 质量管理责任3.1 企业质量管理职责制度(1)总经理:全面负责企业质量管理工作,确保质量目标的实现;(2)质量经理:负责质量管理体系的建立、运行和改进,并组织相关培训;(3)生产经理:负责生产过程中的质量控制和质量问题的解决;(4)员工:严格按照操作规程进行操作,确保产品质量。
3.2 质量管理小组成立质量管理小组,由各相关部门的代表组成,定期召开会议,讨论并解决质量管理中的问题,推动质量管理工作的落实。
4. 质量管理流程控制4.1 生产计划管理(1)根据订单和产品要求制定生产计划,明确生产周期和数量;(2)生产计划需与销售部门和技术部门进行有效沟通,确保订单的准确传达和产品的及时交付。
4.2 原材料采购与质量控制(1)建立供应商评估制度,选择具备良好质量记录的供应商;(2)建立原材料入库检验制度,对进货原材料进行抽样检验,确保质量符合要求。
4.3 生产过程控制(1)严格执行生产工艺和操作规程,确保每道工序的合格品率;(2)设立中间检验环节,针对关键工序进行抽检,及时发现和纠正问题。
铸造生产过程质量控制点

铸造生产过程质量控制点目录1.介绍1.1.目的1.2.范围1.3.定义2.质量控制点概述2.1.质量控制流程2.2.质量控制点安排3.原材料质量控制点3.1.原材料检验3.2.原材料存储条件3.3.原材料跟踪标识4.铸造工艺质量控制点4.1.铸造温度控制4.2.铸造压力控制4.3.铸型清洁度检验4.4.熔炼工艺参数检验5.成品质量控制点5.1.型腔尺寸检验5.2.成品外观检验5.3.成品力学性能检验5.4.成品表面处理6.过程监控和记录6.1.生产数据采集6.2.质量记录保存6.3.问题处理和纠正措施7.文档附件7.1.铸造生产工艺流程图7.2.质量控制流程图7.3.相关检验报告附录:本文档涉及法律名词及注释:1.质量控制:指通过制定和执行标准和规范,采取各种措施追踪和监督生产过程,以确保产品质量符合要求。
2.原材料检验:对进入生产流程的原材料进行物理、化学、机械性能等方面的检验,以确保其质量符合要求。
3.铸造温度控制:在铸造过程中控制金属液体的温度,以确保成品质量。
4.铸型清洁度检验:对铸型进行清洗,以确保成品表面无砂眼、裂纹等缺陷。
5.成品外观检验:对成品的外观进行检查,以确保成品无明显缺陷和损伤。
6.成品力学性能检验:对成品进行拉伸、压缩、弯曲等测试,以评估其力学性能。
7.成品表面处理:对成品表面进行喷涂、研磨等处理,以美化外观和保护成品。
本文档涉及附件:1.铸造生产工艺流程图2.质量控制流程图3.相关检验报告全文结束 \。
铸造过程质量控制管理方案

铸造过程质量控制管理方案一、前言。
咱们搞铸造的都知道,这铸造就像一场魔法秀,把各种原材料变成各种酷炫的铸件。
但这魔法可不能乱施,得好好控制质量才行,不然就变成“灾难现场”啦。
所以呢,咱们得搞个超棒的质量控制管理方案,让咱们的铸造产品个个都是“尖子生”。
二、原材料管理。
1. 供应商选择。
咱们找供应商就像找对象,得精挑细选。
不能光看脸(价格),还得看看内在(质量)。
得找那些口碑好、有信誉的供应商。
就像找对象要打听人品一样,咱们得去调查供应商的生产工艺、质量管控措施。
定期去供应商那儿瞅瞅,就像去对象家做客一样,看看他们有没有啥“不良习惯”(质量问题)。
建立一个供应商评价体系,像给对象打分一样。
从原材料的质量稳定性、交货期、服务态度等方面来打分。
分数低的,哼哼,就像不称职的对象一样,得考虑换啦。
2. 原材料检验。
原材料进来的时候,那可得瞪大了眼睛检查。
就像海关检查违禁品一样严格。
每一批原材料都要抽样,按照标准进行各种检测,像化学成分分析、物理性能测试啥的。
要是发现不合格的,那就毫不留情地退货,就像拒绝不良商品一样。
对检验结果做好记录,这记录就像原材料的“档案”一样。
以后要是出了问题,咱们就能翻档案找到根源。
三、模具管理。
1. 模具设计与制造。
模具可是铸造的“灵魂”啊。
在设计模具的时候,就得让那些懂行的工程师像打造艺术品一样精心设计。
要考虑铸件的形状、尺寸精度、脱模方便性等各种因素。
就像设计一件超级合身的衣服一样,每个细节都得照顾到。
制造模具的时候,得找那些技术高超的工匠。
就像找大厨做菜一样,技术差的可不行。
要对模具制造过程进行监控,确保每一步都符合要求。
2. 模具维护与保养。
模具用了一段时间就得保养,就像汽车要定期保养一样。
每次使用完模具,要清理干净,看看有没有磨损或者损坏的地方。
要是发现小问题,就得及时修理,就像给人治病一样,小病不治就会变成大病。
定期对模具进行全面检查和维护,延长模具的使用寿命。
要是模具老是出问题,就像一个老生病的人一样,会影响整个铸造生产的质量和效率。
- 1、下载文档前请自行甄别文档内容的完整性,平台不提供额外的编辑、内容补充、找答案等附加服务。
- 2、"仅部分预览"的文档,不可在线预览部分如存在完整性等问题,可反馈申请退款(可完整预览的文档不适用该条件!)。
- 3、如文档侵犯您的权益,请联系客服反馈,我们会尽快为您处理(人工客服工作时间:9:00-18:30)。
宝鼎重工股份有限公司QC/BD 60-2014 大型铸钢件生产过程控制补充规定版次 A/0
1.目的
规范生产工艺过程,避免由于生产过程工艺执行不规范造成的铸造缺陷,特制定本规定。
2.范围
适用于铸钢件生产工序的质量控制
3.工作程序
a)对于较大尺寸泥芯,尤其是轴孔泥芯,应在泥芯内部参杂木屑、干
燥煤渣等退让性较好的辅料,内孔泥芯圆头及外模圆角处与钢水接
触表面包裹铬铁矿砂,内孔铬铁矿砂厚度控制在20-35mm,外模圆
角处铬铁矿砂厚度控制在15-25mm;
b)严格控制铸件的保温时间,一般控制为2小时/100kg(厚壁铸件适当
延长),薄壁类铸件可视具体情况减小保温时间,铸件开箱后铸件本
体温度原则上不宜高于500℃;因生产需要开箱圈的,在开箱圈后
应将铸件用型砂捂好保温。
c)清砂过程避免撞击铸件,禁止采用撞击的方法开箱,中间泥芯原则
上应该在热处理前清通,以保证铸件在热处理过程有足够的退让性,
避免因收缩受阻造成的表面收缩裂纹。
d)普碳钢及碳锰钢大冒口(直径大于600mm或腰圆340以上)的切割,
切割后应立即进炉去应力热处理;高碳钢(碳含量0.45%以上)及
低合金钢应在去应力热处理后再热割冒口,原则上切割温度不低于
350℃,热割冒口后及时进炉细化晶粒热处理;
e)采用吹氧棒氧熔铁夹砂,原则上应在去应力退后后进行,高碳钢及
低合金钢类必须先预热到350℃以上,再进行吹氧,吹氧结束必须
立即进炉再次去应力退火处理;
f)铸件在去应力退火处理时,必须严格控制升温速度,一般控制在
80-120℃/h。
g)技术部负责对新产品的首件或特殊钢种铸件进行技术跟踪并记录,
技术跟踪节点为:造型过程、浇注过程、清砂后表面检查(包括冒
口补缩)、热处理(检查热处理记录盘)、热处理后检查(表面缺陷、
机械性能结果)、粗加工后检查(加工面缺陷、无损探伤结果)。
h)铸造分厂负责将新产品的首件或特殊钢种铸件的生产检验节点时间
通知技术部。
i)本补充规定与国家相关标注冲突的,以国家相关标准为准。
编制:娄彪
审核:陈江忠
批准:钱少伦。