基于GEFANUCRx3iPACsystem系列电动机正反转的控制_刘博
GEPLCPACSystems培训教材
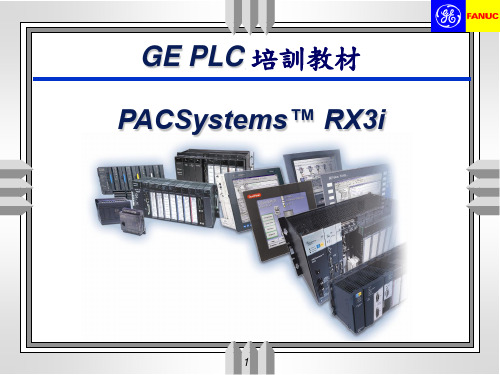
Multipurpose Power Supply
Multipurpose Power Supply Configured for Redundancy
18
Backplane Wattage Available
40 watts
80 Watts
120 Watts
160 watts
40 Watts and redundant supply
記憶體 (Word)
10M
I/O 本地 AI/O
I/O 遠程
2624 1312 32K DI 32K DO 32K AI 32K AO
掃描時間
0.23 ms/K
通訊
RS485 (內建) RS232 (內建) Ethernet Modbus Genius DeviceNet
可 Redundant
IC695CMU310
送電及內部處理
輸入掃描 程序掃描 輸出掃描
診斷及除錯處理
5
PLC 控制系統的基本工作原理(2)
程式掃描: CPU從第一條用 戶程式開始, 根據輸入映像 表, 及其他數據狀態來確定 對外部設備的控制, 將控制 訊息送到輸出映像表.
送電及內部處理
輸入掃描 程序掃描 輸出掃描
輸出掃描: 將輸出映像表的 狀態傳送到輸出模塊, 開設 下一個掃描週期.
Multipurpose Power Supply
Multipurpose Power Supply
Multipurpose Power Supply Configured for Redundancy
Multipurpose Power Supply Configured for Redundancy
GE Fanuc RX3i PACSystem IC695ACC302智能辅助电池模块说明说明书

Rx3i PacSystem919-535-3180*******************GE Fanuc IC695ACC302/automation/ge-fanuc/rx3i-pacsystem/IC695ACC302Battery PackPACSystems*IC695ACC302GFK-2592 Auxiliary Smart Battery ModuleMarch 2011The IC695ACC302 Auxiliary Smart Battery Module is an Enhanced version of IC693ACC302. In addition to providing an extended RAM memory backup time compared to that of the standard memory backup batteries (IC698ACC701) for PACSystems CPUs, the smart battery module has a battery monitoring circuit that enables the user to detect the Low Battery state in advance before it is completely drained. The Auxiliary Smart Battery Module replaces the standard CPU RAM backup battery in your control system for the PACSystems CPUs.Pre-installation CheckUpon receiving the battery pack, verify the package contents, which includes the following:▪ IC695ACC302 Auxiliary Smart Battery Module having cable with 4-pin female JAE connector ▪Enabling adapter cable with 4-pin male to 2-pin female connectorDate CodeThe date code is located on the product label on the front of the auxiliary battery module. The date codeconsists of four digits, such as 1011. The first two digits represent the year of manufacture in the 21st century, such as 10 for the year 2010. The last two digits represent the fiscal week of manufacture for the indicated year; for example 11 stands for fiscal week 11.2Auxiliary Smart Battery ModuleGFK-2592Installation1. With power removed from the equipment, drill four #29 (0.136”) holes in the panel mo unting surface, andtap for #8-32 threads, according to the hole pattern shown in the following figure. Use care to keep metal chips from falling into other equipment.2. Securely attach the Smart Battery Module to the panel mounting surface using four #8-32 x ½” flat headmachine screws. 3. While installing the battery to the CPU, first connect the 4-pin Male JAE connector on the enablingadapter cable to the female 4-pin JAE connector on the battery pack as shown in the following figure. (Installing the 4-pin connector enables the battery.).Note1: The battery will begin to drain immediately if attached to the CPU in Power OFF condition. Tomaximize battery life, it is recommended that you install the fresh battery after power has been turned ON to the attached CPU. Note2: Once the enabling adapter cable is connected, the battery starts to drain, even if it is not attached tothe CPU. So, it is recommended to disconnect the enabling adapter cable from the battery pack when the battery is not in use. Even though the discharge current would be negligible with just the enabling adapter cable connected, this can affect Battery life if left in this condition for long durations.Auxiliary Smart Battery Module 3GFK-25924. Connect the 2-pin female connector of the enabling adapter cable to the CPU battery terminals.EXPLOSION WARNING– Do not Install or replace battery pack unless the area is known to be non-hazardous.5. If installed, remove the standard RAM memory backup battery from the system after installing the newauxiliary smart battery module.Note: Refer to the PACSystems CPU Reference Manual, GFK-2222 for details on avoiding loss of PLC RAM memory contents when replacing a RAM memory backup battery. The standard RAM memory backup battery must be removed from the system when using the auxiliary battery module. DiagnosticsNote: Only qualified personnel, who are trained in electrical safety practices and procedures, should perform testing of the IC695ACC302 auxiliary smart battery module. This module is not user-serviceable. TheIC695ACC302 contains a built-in 1-Amp fuse that will open if the unit is subjected to a short-circuit or severe overload condition. This fuse is sealed inside the battery pack and is not replaceable.To test the unit for an open fuse condition:∙Turn off PLC power.∙Unplug the IC695ACC302 auxiliary smart battery module from the CPU.∙Carefully check the auxiliary smart battery module enabling adapter cable connector pins (2 pin Female connector) for presence of voltage (>2.0V) with a DC voltmeter. If the indicated voltage ispresent, the fuse is not open. If no voltage is present, the internal fuse has probably opened and the IC695ACC302 auxiliary smart battery module will have to be replaced.4 Auxiliary Smart Battery Module GFK-2592Safe Handling and DisposalFor Safe handling and d isposal of dead battery modules, reference the manufacturer’s Material Safety Data Sheet (MSDS) and the Battery Disposal Document that are included with this product.CAUTION– Risk of fire, explosion, and burns. Do not short-circuit, crush, incinerate, or disassemble battery.*The nominal backup values are estimated at 20ºC. Backup time increases approximately 17% at 60ºC and decreases approximately 32% at 0ºC.Note:The CPU detects the low battery condition only while the CPU has power. If a low battery condition occurs while the CPU is powered down, the CPU logs a Low Battery fault upon powerup as soon as it detects the signal from the smart battery.However, because the current drain on the battery is negligible with the CPU powered up, logging ofa Low Battery fault is not likely to occur, unless a good battery is replaced with a low battery while theCPU has power. This would indicate to the user that a good battery has been accidentally replaced with a depleted battery.The Battery LED or the fault table indicates the battery status. For details on the operation of specific CPU models, refer to the PACSystems CPU Reference Manual, GFK-2222.Auxiliary Smart Battery Module 5GFK-2592Smart Battery OperationThe battery output voltage is > 2.5 V when the battery is operating in its good state. At the end of the battery good period, the battery output drops to <2.5 V for the battery low state. The period for the battery low state is 15 days for all CPU models. Once battery output voltage drops to <2.5V, the PACSystems CPU detects this as a battery low condition, a Low Battery fault is logged in the CPU fault table and the Battery LED on the CPU starts blinking in red (depending upon the CPU).Once the battery low state is active, the user has 15 days of accumulative battery backed energy left for CPU RAM retention during power loss. If the battery is not replaced within 15 days of accumulative power loss, the CPU RAM memory contents will be lost as the battery output voltage drops to 0V.If the Battery Low condition occurs when the controller is in the Power OFF state, a low battery fault will be logged in the Fault table only at the time when the controller is powered ON. The Battery Low period of 15 days is counted as soon as the Battery Good period is over, but not necessarily when the low battery fault is logged.Consider the following scenario.Controller Power DownBattery GoodThe Battery Low period of 15 days starts at Point A, but the low battery fault is logged only at Point B, once the controller is powered ON. So, the user should make a note that the timestamp of the Low Battery fault may not give the exact start of the 15 days Battery Low period.6 Auxiliary Smart Battery Module GFK-2592The Battery Low indication is not supported on all the PACs CPUs. The table shown below lists the compatible CPU models.Note 1: √- Denotes compatibility of the battery pack with the CPU model.× - Denotes the CPU and battery pack combination is not suitable. (Use of the battery with the CPE030/CRE030 and CPE040/CRE040 is possible, but not recommended due to reduction in battery life as compared toIC693ACC302.)Note2:For CPU320-Fx with CPU Firmware Revisions 6.02 and higher, the battery packs are compatible. The previous revisions of the CPU320 do not support Battery Low detection; hence these new battery packs are notcompatible.Note3:For CRU320-Cx with CPU Firmware Revisions 6.02 and higher the battery packs are compatible. The previous revisions of the CRU320 do not support Battery Low detection; hence these new battery packs are notcompatible.Agency CertificationsThis product is a Listed Accessory for PACSystems Rx3i and Rx7i family of PLC’s and has been evaluated to the following standards for use in ordinary and hazardous areas.∙UL 2054:2004∙ANSI/ISA 12.12.0.1:2007 (UL File E157515)∙EN 60079-0:2006∙EN 60079-15:2005In order to maintain agency certifications this product must be mounted in an enclosure with mechanical impact strength equal or greater than 3.5 Joules.ATEX Marking and InformationII 3 G Ex nA IIC T6 Ta: 0-60C。
QuickPannel View的使用方法
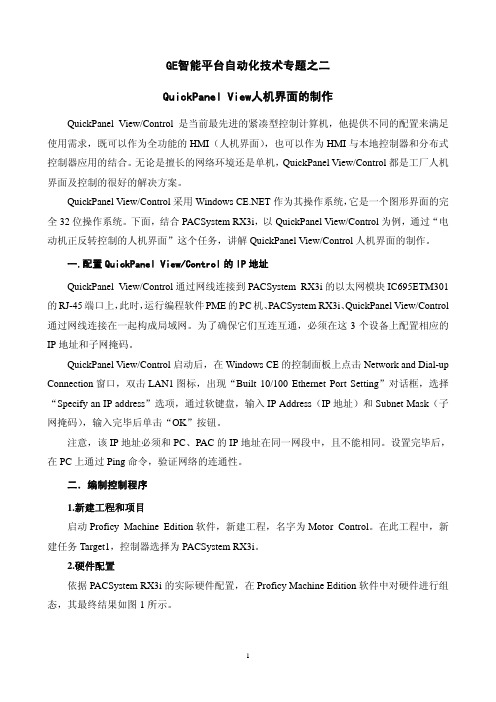
GE智能平台自动化技术专题之二QuickPanel View人机界面的制作QuickPanel View/Control 是当前最先进的紧凑型控制计算机,他提供不同的配置来满足使用需求,既可以作为全功能的HMI(人机界面),也可以作为HMI与本地控制器和分布式控制器应用的结合。
无论是擅长的网络环境还是单机,QuickPanel View/Control都是工厂人机界面及控制的很好的解决方案。
QuickPanel View/Control采用Windows 作为其操作系统,它是一个图形界面的完全32位操作系统。
下面,结合PACSystem RX3i,以QuickPanel View/Control为例,通过“电动机正反转控制的人机界面”这个任务,讲解QuickPanel View/Control人机界面的制作。
一.配置QuickPanel View/Control的IP地址QuickPanel View/Control通过网线连接到PACSystem RX3i的以太网模块IC695ETM301的RJ-45端口上,此时,运行编程软件PME的PC机、PACSystem RX3i、QuickPanel View/Control 通过网线连接在一起构成局域网。
为了确保它们互连互通,必须在这3个设备上配置相应的IP地址和子网掩码。
QuickPanel View/Control启动后,在Windows CE的控制面板上点击Network and Dial-up Connection窗口,双击LAN1图标,出现“Built 10/100 Ethernet Port Setting”对话框,选择“Specify an IP address”选项,通过软键盘,输入IP Address(IP地址)和Subnet Mask(子网掩码),输入完毕后单击“OK”按钮。
注意,该IP地址必须和PC、PAC的IP地址在同一网段中,且不能相同。
GEPLC第3讲 PACsystem RX3i指令系统1
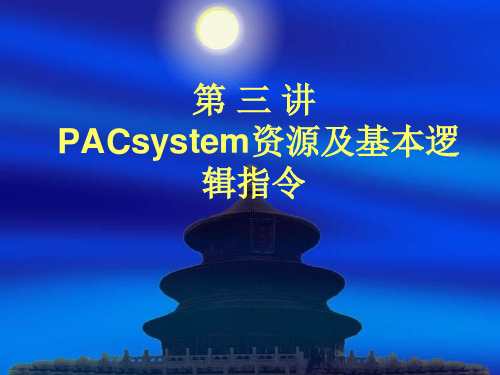
%AQ %R %W
%P*
字变量的寻址方式
直接寻址 如%AI0001,表示直接读取AI0001位 置中的数据。 间接寻址(非直接变量 ) 例如,如果%R00101 的值为1000, 则@R00101 使用的是%R01000 内包含的 值。
字变量中的位
允许设定字的某一位的值,可以将这一 位做为二进制表达式输入输出以及函数和调 用的位参数(例如PSB)。 这个特征只适用于保持型存储器的位变 量。 可使用编程器或者HMI 将字中的某一位 设定为ON 或OFF,也可以监控这一位。 C 块也可以对字中的某一位进行读取, 更改和写入操作。
1. 字(寄存器)变量
类型 %AI 描述 前缀%AI 代表模拟量输入寄存器。模拟量输入寄存器保存模拟量 输入值或者其他的非离散值。 前缀%AQ 代表模拟量输出寄存器。模拟量输出寄存器保存模拟量 输出值或者其他的非离散值。 前缀%R 代表系统寄存器变量。系统寄存器保存程序数据,比如计 算结果。 保持型的海量存储区域,变量为%W (字存储器)类型 前缀%P 代表程序寄存器变量。在_MAIN 块中存储程序数据。这些 数据可以从所有程序块中访问。%P 数据块的大小取决于所有块的最 高的%P 变量值。%P 地址只在LD程序中可用,包括LD 块中调用的C 块,P 变量不是整个系统范围内可用的。
4种定时结点的周期一定,ON与OFF的时间相等,即 其占空比为1:1。
常用系统状态变量
其它重要系统状态变量:
#FST_SCN(%S00001), 第一个扫描周期ON。常用于初始化。
#LST_SCN(%S00002), CPU执行最后一个扫描周期清除。
#ALW_ON, %S00007, always ON。 #ALW_OFF , %S00008, always OFF。
GE PACSYSTEM RX3i模件说明书
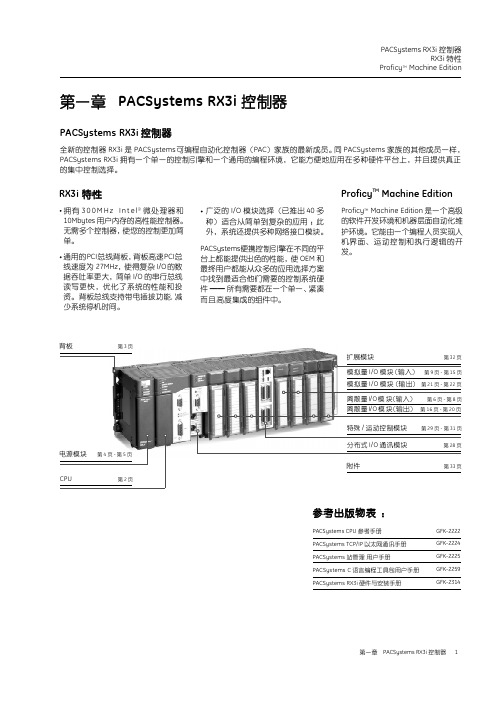
PACSystems RX3i 控制器第一章 PACSystems RX3i 控制器全新的控制器 RX3i 是 PACSystems 可编程自动化控制器 (PAC ) 家族的最新成员。
同 PACSystems 家族的其他成员一样,PACSystems RX3i 拥有一个单一的控制引擎和一个通用的编程环境,它能方便地应用在多种硬件平台上,并且提供真正的集中控制选择。
GFK-2222GFK-2224GFK-2225GFK-2259GFK-2314参考出版物表 :PACSystems CPU 参考手册PACSystems TCP/IP 以太网通讯手册PACSystems 站管理 用户手册PACSystems C 语言编程工具包用户手册PACSystems RX3i 硬件与安装手册背板 第3页电源模块 第4页-第5页扩展模块 第32页模拟量I/O 模块(输入) 第9页-第15页模拟量I/O 模块(输出) 第21页-第22页CPU 第2页离散量I/O 模块(输出) 第16页-第20页离散量I/O 模块(输入) 第6页-第8页分布式I/O 通讯模块 第28页特殊/运动控制模块 第29页-第31页RX3i 特性Proficy TM Machine Edition拥有300M H z I n t e l 微处理器和10Mbytes 用户内存的高性能控制器。
无需多个控制器,使您的控制更加简单。
广泛的 I/O 模块选择(已推出40多种)适合从简单到复杂的应用;此外,系统还提供多种网络接口模块。
PACSystems 便携控制引擎在不同的平台上都能提供出色的性能,使 OEM 和最终用户都能从众多的应用选择方案中找到最适合他们需要的控制系统硬件 —— 所有需要都在一个单一、紧凑而且高度集成的组件中。
通用的PCI 总线背板,背板高速PCI 总线速度为 27MHz ,使得复杂 I/O 的数据吞吐率更大,简单 I/O 的串行总线读写更快,优化了系统的性能和投资。
基于GE FANUC Rx3i PAC System系列电动机正反转的控制
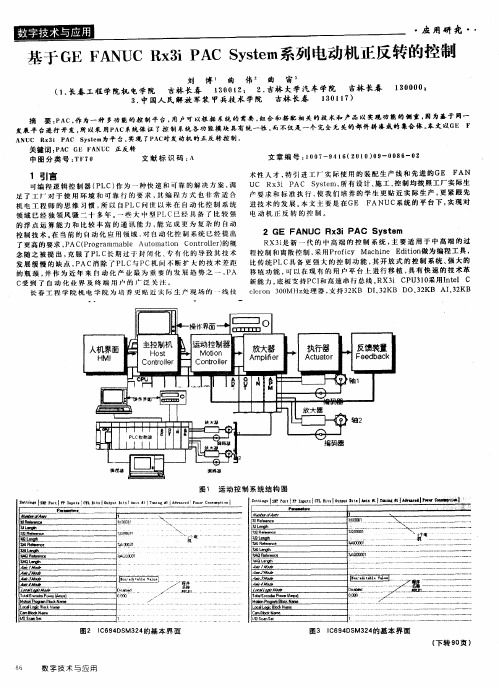
机 电 工 程 师 的 思 维 习 惯 , 以 自PLC问 世 以 来 在 自 动 化 控 制 系 统 所 领 域 已 经 独 领 风 骚 二 十 多 年 。 砦 大 中 型 P 一 IC已 经 具 备 了 比 较 强 的 浮 点 运 算 能 力 和 比 较 丰 富 的 通 讯 能 力 , 完 成 更 为 复 杂 的 自 动 能 控 制 技 术 。 当 前 的 自 动 化 应 用 领 域 , 自 动 化 控 制 系 统 已 经 提 出 在 对 了更 高 的 要 求 , AC( r g a P P o r mma l Au o to Co tolr的 概 be t main n r le ) 念 随之 被 提 出 , 服 了P 克 LC长期 过 于 封 闭 化 、专 有 化 的 导 致 其 技 术 发 展 缓 慢 的 缺 点 , AC消 除 了 P P LC与 PC机 问 不 断 扩 大 的 技 术 差 距
产 要 求 和 标 准 执 行 , 我 们 培 养 的 学 生 更 贴 近 实 际 生 产 , 紧 跟 先 使 更 进 技 术 的 发 展 。 文 主 要 是 在 GE FANUC系 统 的 平 台 下 , 现 对 本 实 电 动机 正 反 转 的 控 制 。 2 GE FANUC Rx3 PAC Sys em i t
1引言
可 编 程 逻 辑 控 制 器 ( LC) 为 一 种 快 速 和 可 靠 的 解 决 方 案 , P 作 满
足 了 工 厂 对 于 使 用 环 境 和 可 靠 行 的 要 求 , 编 程 方 式 也 非 常 适 合 其
UC x i AC ytm, R 3 P S se 所有设 计 、 施工 、 制均 按照 工厂 实际生 控
关 键 词 :AC P GE FA U 正 反 转 NC
GE Fanuc RX3i PACSystem IC695CMM004 四通道串行通信模块说明书
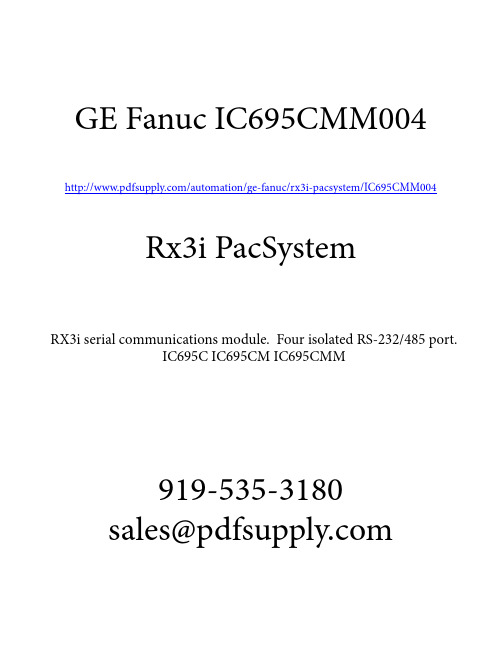
Rx3i PacSystem919-535-3180*******************GE Fanuc IC695CMM004/automation/ge-fanuc/rx3i-pacsystem/IC695CMM004RX3i serial communications module. Four isolated RS-232/485 port.IC695C IC695CM IC695CMMPACSystems™ RX3iIC695CMM002 and IC695CMM004 GFK-2461B Serial Communications Modules August 2007communications capabilities of the RX3i system.in the main PACSystems RX3i backplane.module can only be configured for DNP3 Master or Slave.Additional module features include:▪Port-to-port isolation and port-to-backplane isolation▪▪Hardware handshake: RTS/CTS for RS-232▪57.6K, 115.2K▪▪indicators▪▪Flash memory for future upgradesThese modules must be located in an RX3i Universal Backplane.RX3i Serial Communications can be hot-inserted and removedfollowing the instructions in the PACSystems RX3i System Manual,GFK-2314.2 RX3i Serial Communications Modules GFK-2461BRelease InformationThis release is an upgrade of previous version 1.10.Release HistoryRelease UpgradeKitCommentsIC695CMM002-AA IC695CMM004-AA N/A InitialReleaseIC695CMM002-AB IC695CMM004-AB 44A753277-G0244A753278-G02Supports CCM Slave ProtocolIC695CMM002-AC IC695CMM004-AC 44A753277-G0344A753278-G03Supports DNP3 Master and DNP3 Slave ProtocolNew for this ReleaseThis release of the RX3i Serial Module adds support for Distributed Network Protocol 3.0 Master and Slave to the other protocols: MODBUS Master/Slave, CCM, and Serial I/O. This module does not operate with COMMREQs but rather uses preconfigured mappings of the I/O reference memory.MODBUS Master and MODBUS Slave Protocols now support the configuration of 1 stop bit, for compatibility with some GE Fanuc Automation MODBUS Slaves.CompatibilityProgrammer: Proficy® Machine Edition Logic Developer 5.6 with Service Pack 2 SIM 10RX3i CPU: PACSystems RX3i CPU Version 5.00 or later is required to be able to use the timesynchronization feature on a DNP3 Master port.Problems Resolved for This ReleaseWhen parity is set to none in the port configuration for the Modbus Master or Modbus Slave protocols, the stop bits were forced to 2. This restriction has now been removed and the stop bits can be set to 1 or 2.RX3i Serial Communications Modules 3GFK-2461BRestrictions and Open Issues in this Release1. When multiple group objects (i.e. %I and %AI memory) are read in a single request, the DNP3 port willignore all but the first object. Operations of multiple group objects should be split into multiple successiveexchanges (i.e. exchange 1 - %I, exchange 2 - %AI).2. The DNP3 slave port has problems using the link layer to validate frame receipt. The DNP3 organizationencourages users not to do this.3. These modules do not support GE Fanuc special MODBUS commands for use with a Daniels FlowComputer.4. PLC Reference Address and Reference Length Parameters do not support bit length/start. Bit and Non-Byte Length operations must begin on a byte boundary.5. When a port is configured for CCM Slave protocol, and:▪ a new configuration is stored to the PLC using Machine Edition, or▪the system is power-cycled, or▪the module is hot-inserted,if the first query received from the CCM Master is a Read Scratchpad request, the module will reject thatrequest. All subsequent Read Scratchpad requests will be successful unless one of the above conditionsoccurs again.Operating NotesThe maximum resolution for the MODBUS drop delay is 420us, so the minimum time for a drop delay is 420us.Installation in Hazardous Locations•EQUIPMENT LABELED WITH REFERENCE TO CLASS I, GROUPS A, B, C & D, DIV. 2 HAZARDOUSLOCATIONS IS SUITABLE FOR USE IN CLASS I, DIVISION 2, GROUPS A, B, C, D OR NON-HAZARDOUSLOCATIONS ONLY•WARNING - EXPLOSION HAZARD - SUBSTITUTION OF COMPONENTS MAY IMPAIR SUITABILITY FOR CLASSI, DIVISION 2;•WARNING - EXPLOSION HAZARD - WHEN IN HAZARDOUS LOCATIONS, TURN OFF POWER BEFOREREPLACING OR WIRING MODULES; AND•WARNING - EXPLOSION HAZARD - DO NOT CONNECT OR DISCONNECT EQUIPMENT UNLESS POWER HASBEEN SWITCHED OFF OR THE AREA IS KNOWN TO BE NONHAZARDOUS.4 RX3i Serial Communications ModulesGFK-2461BSpecifications: IC695CMM002 and IC695CMM004Refer to the PACSystems RX3i System Manual , GFK-2314, for product standards and general specifications.Number of Serial PortsIC695CMM002: two independent serial ports IC695CMM004: four independent serial portsConnectors RJ-45 Number of Serial Communications Modules per CPU Six in the main CPU backplaneIC695CMM002 ********************************************Backplane power requirementsIC695CMM004********************************************LEDs Module OK, Port Fault, Port Status (2 or 4)Port TypeRS-232 or RS-485/22. 4-wire (full duplex) or 2-wire (half-duplex) operation for RS-485/422Flow Control for R-232 Selectable: Hardware (CTS/RTS) or noneBaud rates 1200, 2400, 4800, 9600, 19.2K, 38.4K, 57.6K, 115.2k Parity Even, odd, noneData bits 7, 8 Stop bits1, 2Operating Temperature 0°C to + 60°CInput Impedance Zin > 96 kOhm for RS-485/422 3 kOhm < Zin < 7 kOhm for RS-232 Max Overvoltage +/- 25VChannel-Channel Crosstalk –55dB minimumIsolationPort to Backplane and to frame ground: 250 VAC continuous; 1500 VAC for 1 minute, 2550VDC for one second. Port to port: 500VDC continuous, 710VDC for one minute.In order to meet emission and immunity requirements for the EMC directive (CE mark), shielded cable must be used with this module.RX3i Serial Communications Modules 5GFK-2461BLEDsSerial PortsEach port is a standard RJ-45 female connector with the following pin assignments. For MODBUS applications,note that these pin assignments are different than the standard MODBUS pin assignments. If the port isconfigured for MODBUS master or slave operation, custom cables are needed.6 RX3i Serial Communications Modules GFK-2461BIf the Serial Communications module is communicating with a Series 90-30 CPU363 or external PACSystemsRX3i CPU, the connections are:RX3i Serial Module CPU363/RX3iRD('B')T+ ToT- ToRD('A')SD('B')R+ ToSD('A')R- ToTerminationBy default, each port is set for no termination. Termination is needed if the module is the first or last device on an RS-485 network, even if there is only one other device on the network. Termination can be provided using either an external resistor as shown below or the port’s built-in 120-Ohm termination. If line termination other than 120 Ohms is required, an appropriate external resistor must be supplied.User-Supplied Termination for RS-485Termination using the built-in 120-Ohm resistor can be provided by either setting the appropriate RS-4851. Remove the module’s faceplate by pressing in on the side tabs and pulling the faceplate away from themodule.2. With the module oriented as shown, move either the upper or lower jumper:。
GE Fanuc RX3i PacSystem IC694ALG223 16通道单端电流输入模块说明

Rx3i PacSystem919-535-3180*******************GE Fanuc IC694ALG223/automation/ge-fanuc/rx3i-pacsystem/IC694ALG223Input module, analog 16 point single ended, current. IC694A IC694ALIC694ALG9-16 PACSystems™ RX3i System Manual – October 2005 GFK-2314CAnalog Input Module, 16 Channel, Current: IC694ALG223The 16–Channel Analog Current Input module, IC694ALG223, provides 16 single–ended inputs. Each input can be configured using the configuration software for any of three input ranges:▪ 4 to 20 mA▪ 0 to 20 mA▪ 4 to 20 mA EnhancedHigh and Low alarm limits are available on all ranges. In the 4 to 20 mA Enhanced range, a low alarm limit can be set up to detect input current from 4 mA to 0 mA, providing open-wire fault detection in 4 to 20 mA applications.The module also reports module status and external power supply status to the CPU using its assigned program reference addresses. This module can be installed in any I/O slot in an RX3i system.Module PowerThis module consumes 120 mA from the 5 VDC bus on the PLCbackplane. It also requires 65 mA plus current loop current(s) from a user-supplied +24 VDC supply.LEDsThe MODULE OK LED provides module status information on power–up as follows:▪ ON : status is OK, module configured;▪ OFF : no backplane power or software not running (watchdog timer timed out);▪ Continuous rapid flashing : configuration data not received from CPU;▪Slow flashes, then OFF : failed power–up diagnostics or encountered code execution error.The User Supply LED indicates that the external 24 VDC supply is within specifications.GFK-2314C Chapter 9 Analog Input Modules 9-17Specifications: IC694ALG223Number of Channels 1 to 16 selectable; single-endedInput Current Ranges 0 to 20 mA, 4 to 20 mA and 4 to 20 mA Enhanced (selectableper channel)CalibrationFactory calibrated to:4 µA per count on 4 to 20 mA range5 µA per count on 0 to 20 mA and 4 to 20 mA Enhanced rangeUpdate Rate13 milliseconds (all 16 channels) Resolution at 4–20 mA 4 µA (4 µA/bit) Resolution at 0–20 mA 5 µA (5 µA/bit) Resolution at 4–20 mA Enhanced5 µA (5 µA/bit)Absolute Accuracy *+/-0.25% of full scale @ 25°C (77°F): +/- 0.5% of full scale over specified operating temperature range Linearity< 1 LSB from 4 to 20 mA (4 to 20 mA range) < 1 LSB from 100 µA to 20 mA (0 to 20 mA and 4 to 20 mA Enhanced ranges)Isolation, Field to Backplane (optical) and to frame ground250 VAC continuous; 1500 VAC for 1 minute Common Mode Voltage0 volts (single-ended channels) Cross–Channel Rejection > 80dB from DC to 1kHz Input Impedance250 Ohms Input Low Pass Filter Response19 Hz External Supply Voltage Range20 to 30 VDC External Supply Voltage Ripple10%Internal Power Consumption 120 mA from the +5 VDC bus on the backplane65 mA from 24 VDC external user power supply (in addition to current loop currents)Refer to Appendix A for product standards and general specifications.* In the presence of severe RF interference (IEC 801–3, 10V/m), accuracy may be degraded to +/-5% FS.9-18 PACSystems™ RX3i System Manual – October 2005 GFK-2314CConfiguration: IC694ALG223Module IC694ALG223 is configured with the configuration software. Its configurable parameters are described below.Parameter ChoicesDescriptionActive Channels 1 to 16 The number of channels to be scanned. Channels are scanned in sequential, contiguous order. Reference Address for Input DataThe memory location for input data from the module. Each channel provides 16 bits of analog input data to the PLC CPU.Reference Address for Status DataThe memory location for where status information from the module starts.Length8, 16, 24, 32, 40The number of status bits reported to the PLC. Bits 1 – 8 provide basic module diagnostics. Bits 9 – 24 contain channel 1 – 8 high alarm and low alarm status. Bits 25 – 40 contain channel 9 – 16 highalarm and low alarm status. Data formats are shown in this section.Range4-20 mA (default), 0-20 mA, or4-20 mA enhancedIn the 4-20 mA range, input currents from 4 to 20 mA are reported to the CPU as values from 0 to 32000 units. In the 0 to 20 mA range, input currents from 0 to 20 mA are reported to the CPU as values from 0 to 3200 units. In the 4 to 20 mA enhanced range, currents from 4 to 20 mA are reported to the CPU as values form 0 to 32000 units. Currents below 4 mA are reported as negative values with 0 represented as –8000 units.4-20 mA = 0 to 32759 0-20 mA = 0 to 32759 Alarm Low 4-20 mA enhanced = -8000 to +32759Each channel can be assigned a low alarm limitalarm. Values entered without a sign are assumed to be positive. Be sure the alarm low values are appropriate for the selected range.4-20 mA = 1 to 32760 0-20 mA = 1 to 32760 Alarm High 4-20 mA enhanced = -7999 to +32760Each channel can also be assigned a high alarm limit. Values entered without a sign are assumed to be positive. Be sure the alarm high values are appropriate for the selected range.I/O Scan Set Default = 1Assign the module to one of the I/O Scan Sets defined in the CPU configuration.GFK-2314C Chapter 9 Analog Input Modules 9-19Data Format: IC694ALG223The 12-bit resolution module analog input data is stored in the PLC CPU in 16–bit 2’scomplement format as shown below.MSB LSB X 11 10 9 8 7 6 5 4 3 2 1 0 X X XInput ScalingIn the 4 to 20 mA range, input data is scaled so that 4 mA corresponds to a count of 0 and 20 mA corresponds to a count of 32000.In the 0 to 20 mA range, 0 mA corresponds to a count of 0 and 20 mA corresponds to a count of 32000. Full 12–bit resolution is available over the 4 to 20 mA and 0 to 20 mA ranges. 4 to 20 mA Enhanced range can also be configured. In that range, 0 mA corresponds to a count of -8000, 4 mA corresponds to a count of 0 (zero) and 20 mA corresponds to a count of +32000. A low alarm limit can be set up to detect input current from 4 mA to 0 mA, providing open-wire fault detection in 4 to 20 mA applications.Analog values are scaled over the range of the converter. Factory calibration adjusts the analog value per bit (resolution) to a multiple of full scale (4 µA/bit). This calibration leaves a normal 12–bit converter with 4000 counts (normally 212 = 4096 counts). The data is then scaled with the 4000 counts over the analog range. The data is scaled as shown below.4Current (mA)0200Scaled DataUnits (decimal)4000Status Data: IC694ALG223Analog Module IC694ALG223 can be configured to return 8, 16, 24, 32, or 40 status bits to the PLC CPU. This status data provides the following information about module operation:Module OK = 1, not OK = 0Power Supply OK = 1, below limit = 0Reserved1 2 3 4 5 6 7 8Channel 1 Low Alarm: 1 = above limit, 0 = at limit or belowChannel 1 High Alarm: 1 = below limit, 0 = at limit or aboveChannel 2 Low Alarm: 1 = above limit, 0 = at limit or belowChannel 2 High Alarm: 1 = below limit, 0 = at limit or aboveChannel 3 Low Alarm: 1 = above limit, 0 = at limit or belowChannel 3 High Alarm: 1 = below limit, 0 = at limit or aboveChannel 4 Low Alarm: 1 = above limit, 0 = at limit or belowChannel 4 High Alarm: 1 = below limit, 0 = at limit or above9 10 11 12 13 14 15 16Channel 5 Low Alarm: 1 = above limit, 0 = at limit or belowChannel 5 High Alarm: 1 = below limit, 0 = at limit or aboveChannel 6 Low Alarm: 1 = above limit, 0 = at limit or belowChannel 6 High Alarm: 1 = below limit, 0 = at limit or aboveChannel 7 Low Alarm: 1 = above limit, 0 = at limit or belowChannel 7 High Alarm: 1 = below limit, 0 = at limit or aboveChannel 8 Low Alarm: 1 = above limit, 0 = at limit or belowChannel 8 High Alarm: 1 = below limit, 0 = at limit or above17 18 19 20 21 22 23 24Channel 9 Low Alarm: 1 = above limit, 0 = at limit or belowChannel 9 High Alarm: 1 = below limit, 0 = at limit or aboveChannel 10 Low Alarm: 1 = above limit, 0 = at limit or belowChannel 10 High Alarm: 1 = below limit, 0 = at limit or aboveChannel 11 Low Alarm: 1 = above limit, 0 = at limit or belowChannel 11 High Alarm: 1 = below limit, 0 = at limit or aboveChannel 12 Low Alarm: 1 = above limit, 0 = at limit or belowChannel 12 High Alarm: 1 = below limit, 0 = at limit or above25 26 27 28 29 30 31 32Channel 13 Low Alarm: 1 = above limit, 0 = at limit or belowChannel 13 High Alarm: 1 = below limit, 0 = at limit or aboveChannel 14 Low Alarm: 1 = above limit, 0 = at limit or belowChannel 14 High Alarm: 1 = below limit, 0 = at limit or aboveChannel 15 Low Alarm: 1 = above limit, 0 = at limit or belowChannel 15 High Alarm: 1 = below limit, 0 = at limit or aboveChannel 16 Low Alarm: 1 = above limit, 0 = at limit or belowChannel 16 High Alarm: 1 = below limit, 0 = at limit or above33 34 35 36 37 38 39 409-20 PACSystems™ RX3i System Manual – October 2005 GFK-2314CGFK-2314C Chapter 9 Analog Input Modules 9-21Field Wiring: IC694ALG223Terminal Connection1User supplied 24V Input; provides loop power via24VOUT terminal (pin 2)2 +24V loop power tie point3 Current Input, Channel 14 Current Input, Channel 25 Current Input, Channel 36 Current Input, Channel 47 Current Input, Channel 58 Current Input, Channel 69 Current Input, Channel 7 10 Current Input, Channel 8 11 Current Input, Channel 9 12 Current Input, Channel 10 13 Current Input, Channel 11 14 Current Input, Channel 12 15 Current Input, Channel 13 16 Current Input, Channel 14 17 Current Input, Channel 15 18 Current Input, Channel 1619Common connection to input current sense resistors; user supplied 24V input return or 24VINreturn 20 Frame ground connections for cable shieldsField Wiring Terminals Field Wiring* Internally Connected ** Optional Shield Connection24 V。
PAC实验指导书
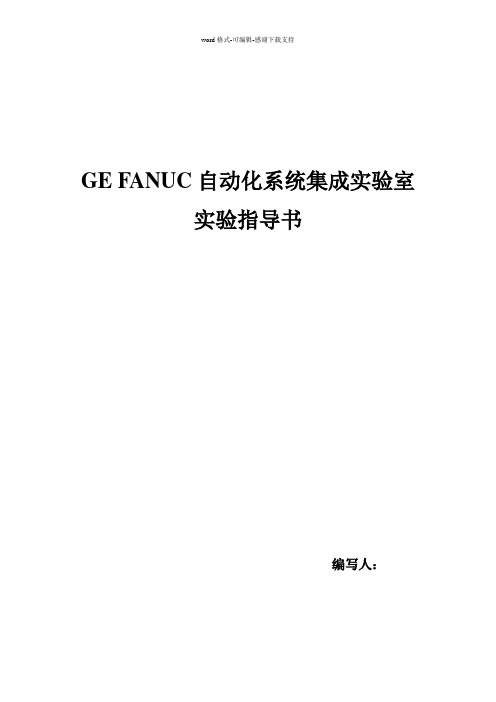
GE FANUC自动化系统集成实验室实验指导书编写人:实验一GE-Fanuc ME软件使用一.实验目的:1.掌握PAC Systems RX3i系统的硬件组成;2. 熟悉GE-Fanuc的应用软件PROFICY MACHINE EDITION(简称ME);3.使用ME软件,掌握硬件配置及其地址分配;4.使用ME软件,掌握上位机和PAC Systems RX3i的通讯。
二.实验设备:1.RX3i可编程序控制器;2.装有PROFICY ME编程软件的电脑;3.导线若干。
三.实验内容:1.了解PAC Systems RX3i系统的硬件组成2. 在ME软件中进行硬件配置,并对其分配地址;3.实现上位机和PAC Systems RX3i的通讯。
4. 将一个程序下载到PLC系统中运行。
四. 实验设备介绍:1.PAC Systems RX3iPAC Systems RX3i的特点PAC Systems RX3i控制器是创新的可编程自动化控制器PAC Systems家族中最新增加的部件。
它是中、高端过程和离散控制应用的新一代控制器。
如同家族中的其它产品一样,PAC Systems RX3i的特点是具有单一的控制引擎和通用的编程环境,提供应用程序在多种硬件平台上的可移植性和真正的各种控制选择的交叉渗透。
使用与PAC Systems RX7i相同的控制引擎,新的PAC Systems RX3i在一个紧凑的、节省成本的组件包中提供了高级的自动化功能。
PAC Systems的可移植性的控制引擎在几种不同的平台上都有卓越的表现,使得初始设备制造商和最终用户在应用程序变异的情况下,能选择最适合他们需要的确切的控制系统硬件。
RX3i部件(1)RX3i CPU高性能处理器:奔腾PIII 300 MHz / PIII1GHz,支持32K DI, 32K DO, 32K AI, 32K AO以及多达5 M字的数据贮存,高达56M存储内存,所有设备文档都可以贮存在CPU中。
PACsystem参考手册说明
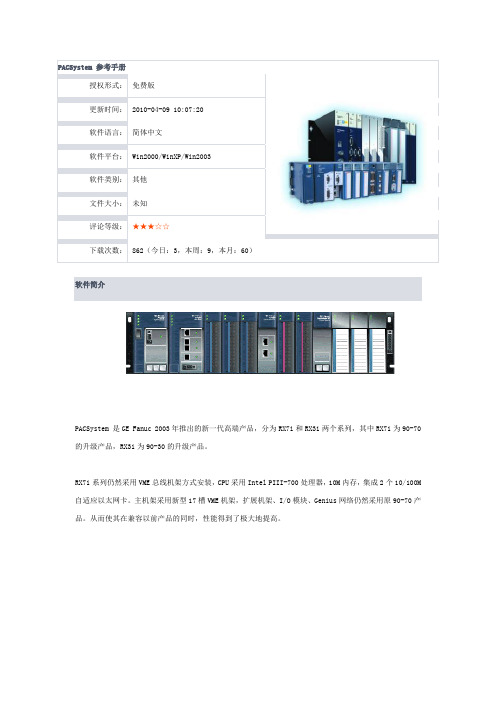
PACSystem 参考手册授权形式:免费版更新时间:2010-04-09 10:07:20软件语言:简体中文软件平台:Win2000/WinXP/Win2003软件类别:其他文件大小:未知评论等级:★★★☆☆下载次数:862(今日:3,本周:9,本月:60)软件简介PACSystem 是GE Fanuc 2003年推出的新一代高端产品,分为RX7i和RX3i两个系列,其中RX7i为90-70的升级产品,RX3i为90-30的升级产品。
RX7i系列仍然采用VME总线机架方式安装,CPU采用Intel PIII-700处理器,10M内存,集成2个10/100M 自适应以太网卡。
主机架采用新型17槽VME机架,扩展机架、I/O模块、Genius网络仍然采用原90-70产品。
从而使其在兼容以前产品的同时,性能得到了极大地提高。
PACSystem RX7i产品名称:PACSystem RX7i产品型号:PACSystem RX7i基本参数:PACSystem RX7i是 GE Fanuc 2003 年推出的新一代高端产品。
RX7i 为 90-70 的升级产品产品介绍:PACSystem RX7i是 GE Fanuc 2003 年推出的新一代高端产品。
RX7i 为 90-70 的升级产品。
作为PAC家族的一员,PACSystems RX7i提供更强大的功能、更大的内存和更高的带宽来处理从中档到高端的各种应用。
同时,也提供其他PACSystem平台的所有创新的功能。
和其他PACSystems一样RX7i有一个单一的控制引擎和通用的编程环境,它能创建一条无缝的移植路径,并且提供真正的集中控制选择。
同时,它还适合从中档到高档的各种应用,其庞大的内存、高带宽和分布式I/O能满足各种重要的系统要求。
RX7i 系列采用 VME64 总线机架方式安装,兼容多种第三方模块。
CPU 采用 Intel PIII-700 处理器, 10M 内存,集成 2个10/100M 自适应以太网卡。
GE Fanuc RX3i PACSystem IC695CPU320 产品说明说明书
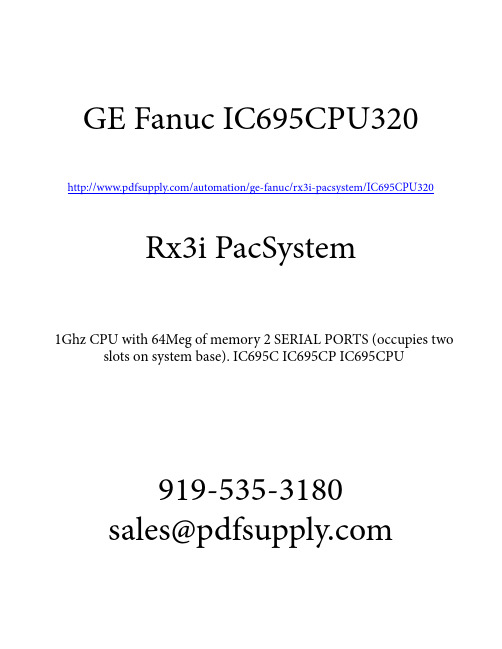
Rx3i PacSystem919-535-3180*******************GE Fanuc IC695CPU320/automation/ge-fanuc/rx3i-pacsystem/IC695CPU3201Ghz CPU with 64Meg of memory 2 SERIAL PORTS (occupies twoslots on system base). IC695C IC695CP IC695CPU2-14 PACSystems™ CPU Reference Manual – March 2009 GFK-2222MIC695CPU320/CRU320 Models■ IC695CPU320: 1 GHz CPU microprocessor ■ IC695CRU320: 1 GHz CPU microprocessor withredundancySerial PortsThe CPU has two independent, on-board serial ports,accessed by connectors on the front of the module. Ports 1 and 2 provide serial interfaces to external devices. Either port can be used for firmware upgrades. For serial port pin assignments and details on serial communications, refer to chapter 12.IndicatorsThe eight CPU LEDs indicate the operating status of various CPU functions.*After initialization sequence is complete.GFK-2222M Chapter 2 CPU Features and Specifications 2-15Specifications – CPU320For environmental specifications, see Appendix A of the PACSystems RX3i System Manual, GFK-2314.Battery: Memory retentionEstimated 30 days using an IC693ACC302 Auxiliary Battery Module at 20ºC.For details on the operation of the Auxiliary Battery Module, refer to the datasheet, GFK-2124. Note:The IC698ACC701 Lithium Battery Pack is not compatible with the CPU320.Program storage Up to 64 Mbytes of battery-backed RAM 64 Mbyte of non-volatile flash user memory Power requirements +3.3 VDC: 1.0 Amps nominal +5 VDC: 1.2 Amps nominal Operating Temperature 0 to 60°C (32°F to 140°F) Floating pointYesBoolean execution speed, typical 0.047 ms per 1000 Boolean instructions Time of Day Clock accuracyMaximum drift of ±2 seconds per day.Can be synchronized to an Ethernet time master within ±2ms of the SNTP time stamp.Elapsed Time Clock (internal timing) accuracy ±0.01% maximum Embedded communications RS-232, RS-485Serial Protocols supported Modbus RTU Slave, SNP, Serial I/OBackplane Dual backplane bus support: RX3i PCI and 90-30-style serial PCI compatibility System designed to be electrically compliant with PCI 2.2 standard Program blocksUp to 512 program blocks. Maximum size for a block is 128KB. Flash memory endurance rating 100,000 write/erase cycles minimumMemory(For a detailed listing of memory areas, refer to chapter 7.)%I and %Q: 32Kbits for discrete%AI and %AQ: configurable up to 32Kwords%W: configurable up to the maximum available user RAMManaged memory (Symbolic and I/O variables combined): configurable up to 64 Mbytes2-16 PACSystems™ CPU Reference Manual – March 2009 GFK-2222MCRU320 SpecificationsNote: For environmental specifications and compliance to standards (for example, FCCor European Union Directives), refer to the PACSystems RX3i System Manual, GFK-2314.Battery: Memory retentionEstimated 30 days using an IC693ACC302 Auxiliary Battery Module at 20ºC. For details on the operation of the Auxiliary Battery Module, refer to the datasheet, GFK-2124. Note:The IC698ACC701 Lithium Battery Pack is not compatible with the CRU320 and must not be used.Program storage Up to 64 Mbytes of battery-backed RAM 64 Mbytes of non-volatile flash user memory Power requirements +3.3 VDC: 1.0 Amps nominal +5 VDC: 1.2 Amps nominal Operating Temperature 0 to 60°C (32°F to 140°F) Floating pointYesBoolean execution speed, typical 0.047 ms per 1000 Boolean instructions Time of Day Clock accuracyMaximum drift of 2 seconds per dayElapsed Time Clock (internal timing) accuracy0.01% maximum Embedded communications RS-232, RS-485Serial Protocols supported Modbus RTU Slave, SNP Slave, Serial I/OBackplane Dual backplane bus support: RX3i PCI and 90-30-style serial PCI compatibility System designed to be electrically compliant with PCI 2.2 standard Program blocks Up to 512 program blocks. Maximum size for a block is 128KB. Memory%I and %Q: 32Kbits for discrete%AI and %AQ: configurable up to 32Kwords%W: configurable up to the maximum available user RAM Symbolic: configurable up to 64 MbytesFlash memory endurance rating 100,000 write/erase cycles minimumMemory error checking and correction (ECC) Single bit correcting and multiple bit checking. Switchover Time*Maximum 1 logic scan, minimum 3.133 msec.Typical Base Sweep Time (Reference Data Transfer List Impact)**3.66 msec: 1K Discrete I/O, 125 Analog I/O and 1K Registers 3.87 msec: 2K Discrete I/O, 250 Analog I/O and 2K Registers4.30 msec: 4K Discrete I/O, 500 Analog I/O and 4K Registers5.16 msec: 8K Discrete I/O, 1K Analog I/O and 8K Registers Maximum amount of data in redundancy transfer listUp to 2 MbytesNumber of redundant redundancy links supportedUp to two IC695RMX128 synchronization links are supported.*Switchover time is defined as the time from failure detection until backup CPU is active in a redundancy system.** Symbolic variable and Reference data can be exchanged between redundancycontrollers. Up to 2 Mbytes of data is available for transfer.Error Checking and Correction, IC695CRU320Rx3i Redundancy CPUs provide error checking and correction (ECC), which results inslightly slower system performance, primarily during power-up, because it uses an extra8 bits that must be initialized.For details on ECC, refer to the PACSystems Hot Standby CPU Redundancy User’sGuide, GFK-2308.Note:Multiple Recoverable Memory Error faults may be generated when a single-bitECC error is detected. When a single-bit ECC error is detected, the valuepresented to the microprocessor is corrected. However, the value stored in RAMis not corrected until the next time the microprocessor writes to thatRAM location.GFK-2222M Chapter 2 CPU Features and Specifications 2-17。
GE Fanuc RX3i PACSystem IC695CPU310 产品说明说明书

Rx3i PacSystem919-535-3180*******************GE Fanuc IC695CPU310/automation/ge-fanuc/rx3i-pacsystem/IC695CPU310300Mhz CPU with 10Meg of memory 2 SERIAL PORTS (occupies two slots on system base) IC695C IC695CP IC695CPUPACSystems RX3iIC695CPU310 GFK-2329AC Central Processing UnitMay 2011The PACSystems* RX3i CPU can be used to perform real time control of machines, processes, and material handling systems. The CPU communicates with the programmer and HMI devices via a serial port using SNP Slave protocol. It communicates with I/O and Intelligent Option modules over a dual backplane bus that provides:■High-speed, PCI backplane for fast throughput of new advanced I/O.■Serial backplane for easy migration of existing Series 90-30 I/O.Features■Contains 10 Mbytes of battery-backed user memory and 10 Mbytes of non-volatile flash user memory.■Configurable data and program memory.■Programming in Ladder Diagram, Structured Text, Function Block Diagram, and C.■Supports auto-located Symbolic Variables that can use any amount of user memory.■Reference table sizes include 32Kbits for discrete %I and %Q and up to 32Kwords each for analog %AIand %AQ.■Supports most Series 90-30 modules and expansion racks. For a list of supported I/O, Communications,Motion, and Intelligent modules, see the PACSystems RX3i Hardware and Installation Manual, GFK-2314.■Supports up to 512 program blocks. Maximum size fora block is 128KB.■In-system upgradeable firmware.■Two serial ports: RS-485 serial port and RS-232.■Ethernet communications via the rack-based Ethernet Interface module (IC695ETM001). For details onEthernet capabilities, refer to TCP/IP EthernetCommunications for PACSystems User’s Manual,GFK-2224.■Time synchronization to SNTP Time Server on Ethernet network when used with an Ethernet module with firmware release 5.0 or later.*indicates a trademark of GE Intelligent Platforms, Inc. and/or its affiliates. All other trademarks are the property of their respective owners.GFK-2329ACImportant Installation Instructions for BatteryDo not connect the battery until the CPU is installed in the rack and the rack is powered on. The battery may then be attached to either of the two terminals in the battery compartment. Once that is done, the CPU may be powered down and normal battery back up operation will begin. To save battery life, do not connect the battery for the first time until the CPU ispowered up.Estimated Battery Life without Power AppliedThe nominal backup values are estimated at 20ºC (68°F). Backup time increases approximately 17% at 60ºC and decreases approximately 32% at 0ºC.Note:When using the Smart Battery, the Battery Low indication can be detected only on the power up condition of the CPU either by the LED indication or the fault table.RX3i CPU Lithium Smart Battery, IC695ACC302:Smart Coin Cell Battery, IC698ACC701C and later:Auxiliary Battery Module, IC693ACC302:200 days at 20ºC (68°F)GFK-2329ACGFK-2329ACImportant Product Information for this ReleaseRelease 6.71 corrects the behavior of the Logic Driven Read/Write to Flash service requests, SVC_REQ56 and SVC_REQ 57.For details, see “Problems Resolved in Release 6.71” on page 5.UpdatesIC695CPU310 can be field upgraded to firmware version 6.71 using the Winloader firmware upgrade utility and upgrade kit 44A752290-G26, which can be downloaded from /support.GFK-2329ACGFK-2329ACGFK-2329ACGFK-2329ACGFK-2329ACGFK-2329ACGFK-2329ACGFK-2329ACInstallation in Hazardous LocationsThe following information is for products bearing the UL marking for Hazardous Locations:⏹WARNING - EXPLOSION HAZARD - SUBSTITUTION OF COMPONENTS MAY IMPAIR SUITABILITY FOR CLASS I,DIVISION 2;⏹WARNING - EXPLOSION HAZARD - WHEN IN HAZARDOUS LOCATIONS, TURN OFF POWER BEFORE REPLACINGOR WIRING MODULES; AND⏹WARNING - EXPLOSION HAZARD - DO NOT CONNECT OR DISCONNECT EQUIPMENT UNLESS POWER HASBEEN SWITCHED OFF OR THE AREA IS KNOWN TO BE NONHAZARDOUS.⏹EQUIPMENT LABELED WITH REFERENCE TO CLASS I, GROUPS A, B, C & D, DIV. 2 HAZARDOUS LOCATIONS ISSUITABLE FOR USE IN CLASS I, DIVISION 2, GROUPS A, B, C, D OR NON-HAZARDOUS LOCATIONS ONLY⏹The tightening torque range for the control terminals is 9.6-11.5 in. lb. Use only wire rated for 90°C. Be sure to observeany additional ratings that are provided with the modules.⏹Batteries: Replace Battery with Matsushita Part No. BR2477A Only. Use of another battery may present a risk of fire orexplosion.” “Caution, Battery may explode if mistreated. DO NOT recharge, disassemble or dispose of in fire.” The correct battery type is available as Accessory Kit IC698ACC701.。
GE Fanuc RX3i PACSystem IC695ALG808 隔离类输出模块说明说明书

Rx3i PacSystem919-535-3180*******************GE Fanuc IC695ALG808/automation/ge-fanuc/rx3i-pacsystem/IC695ALG808Isolated Analog Output module, 8 channels, that is configurable IC695AIC695AL IC695ALGPACSystems™ RX3i GFK-2481 Isolated Analog Output Module, IC695ALG808 November 2007Isolated Analog Voltage/Current Output module IC695ALG808 provides eight configurable voltage or current output channels. Analog channels can be configured for these output ranges:▪Current: 0 to 20mA, 4 to 20mA▪Voltage: +/- 10V, 0 to 10VThe module must be located in an RX3i Universal Backplane. It requires an RX3i CPU with firmware version 5.0 or later. Machine Edition Version 5.7 SP3 Logic Developer-PLC or later must be used for configuration.These modules can be used with a Box-style (IC694TBB032), Extended Box-style (IC694TBB132), Spring-style (IC694TBS032), or Extended Spring-style (IC694TBS132) Terminal Block. Extended terminal blocks provide the extra shroud depth needed for shielded wiring. See the PACSystems RX3i System Manual, GFK-2314 revision B or later for more information about Terminal Blocks. Terminal Blocks are ordered separately.Isolated +24 VDC PowerThe module must receive 24 VDC field power from an external source. The external source must be connected directly to the module’s terminal block. It cannot be connected via the TB1 connector on the RX3i Universal Backplane.Module Features▪Completely software-configurable, no module jumpers to set▪Individually enable or disable channels▪Clamping and Alarm Limits▪ LatchingofAlarms▪Configurable output bias▪Rapid channel acquisition times based on filter frequency▪ On-boarderror-checking▪Configurable scaling and offsets per channel▪High alarm, low alarm, high-high alarm, low-low alarm detection and reporting selectable per channel▪Module fault reporting▪Configurable Hold Last State or Output Defaults2 RX3i Isolated Analog Output ModuleGFK-2481SpecificationsOutput RangesCurrent: 0 to 20mA, 4 to 20mA Voltage: +/- 10V, 0 to 10V Backplane Power Requirements 80mA maximum at 3.3VPower Dissipation within Module7.25 Watts maximum (Vuser=24V)Thermal DeratingSee derating curves later in this document External +Power Supply Voltage Range: 19.2V to 30V (24V nominal) Current: 600mA maximumResolution+/-10V: 15.9 bits, 0 to 10V: 14.9 bits, 0 to 20mA: 15.9 bits, 4 to 20mA : 15.6 bitsOutput Data Format Configurable as floating point IEEE 32 bit or 16-bit integer in a 32-bit field Analog Update Rate(Determined by I/O scan time, application dependent)8 milliseconds (approximate, all eight channels)Output Overvoltage Protection Current outputs only: -30V for 60 seconds, +30V for one hour Calibrated AccuracyAccurate to within 0.15% of full scale at 25°C Accurate to within 0. 25% of full scale at 60°CIn the presence of severe RF interference (IC 801-3, 10V/M), accuracy may be degraded to +/-1% FS.Output Load Reactance Current: 10µH maximum, Voltage: 1µF maximum Maximmum Output Load Current: 1350 Ohms maximum Voltage: 2 Kohms minimumOutput Gain DriftVoltage output: 20ppm per degree C typical Current output: 35ppm per degree C typical Output Settling TimeVoltage or current output: 2ms, 0 to 95% Isolation, Field to Backplane 2550VDC for one secondOutput Points vs. Temperature, Current ModeThermal deratings for module IC695ALG808 are shown below.RX3i Isolated Analog Output Module 3GFK-2481 Release HistoryVersion FirmwareRevisionUpgrade KitIC695ALG808-AA 1.00 None: Initial ReleaseLEDsThe Module OK LED indicates module status. The Field Status LED indicates whether the external +24 VDC power supply is present and is above the minimum level and whether or not faults are present. All LEDs are powered from the backplane power bus.LED IndicatesModule OK ON Green: Module OK and configured.Quick Flashing Green: Module performing powerup sequence.Slow Flashing Green or Amber: Module OK but not configured.OFF: Module is defective or no backplane power presentField Status ON Green No faults on any enabled channel, Terminal Block is present, and field power is present.ON Amber and TB Green: Terminal Block is installed, fault on at least onechannel, or field power is not present.ON Amber and TB Red: Terminal Block not fully removed, field power stilldetected.OFF and TB Red: Terminal block not present and no field power is detected.TB ON Red: Terminal block not present or not fully seated. See above.ON Green: Terminal block is present. See above.OFF: No backplane power to module.4 RX3i Isolated Analog Output ModuleGFK-2481Field WiringThe table below lists wiring connections for the Isolated Analog Output Modules. There are no shield terminals.Terminal AssignmentAssignmentTerminal 1No ConnectNo Connect19 2 Channel 1 Voltage/Current Output Channel 5 Voltage/Current Output20 3 Channel 1 Ground/Return Channel 5 Ground/Return214 No Connect No Connect 225 No ConnectNo Connect23 6 Channel 2 Voltage/Current OutputChannel 6 Voltage/Current Output24 7 Channel 2 Ground/ReturnChannel 6 Ground/Return25 8 No Connect No Connect 26 9 No ConnectNo Connect27 10 Channel 3 Voltage/Current OutputChannel 7 Voltage/Current Output28 11 Channel 3 Ground/ReturnChannel 7 Ground/Return29 12 No Connect No Connect 30 13 No ConnectNo Connect31 14 Channel 4 Voltage/Current OutputChannel 8 Voltage/Current Output32 15 Channel 4 Ground/ReturnChannel 8 Ground/Return33 16 No ConnectNo Connect 34 17 External + Power Supply (+24V In) No Connect 35 18External - Power Supply (+24V Rtn)No Connect36Each channel can be individually configured to operate as a voltage output or a current output - not both simultaneously.No ConnectChannel 1 Output Channel 1 Return No ConnectVoltage..+ -There are no shield terminals on these modules. For shielding, tie cable shields to the ground bar along the bottom of the backplane. M3 tapped holes are provided in the ground bar for this purpose.For technical assistance, please go to /supportAll rights reserved. PACSystems is a Trademark of GE Fanuc Intelligent Platforms, Inc.。
GE Fanuc RX3i PacSystem 919-535-3180 高密度终端块说明说明书
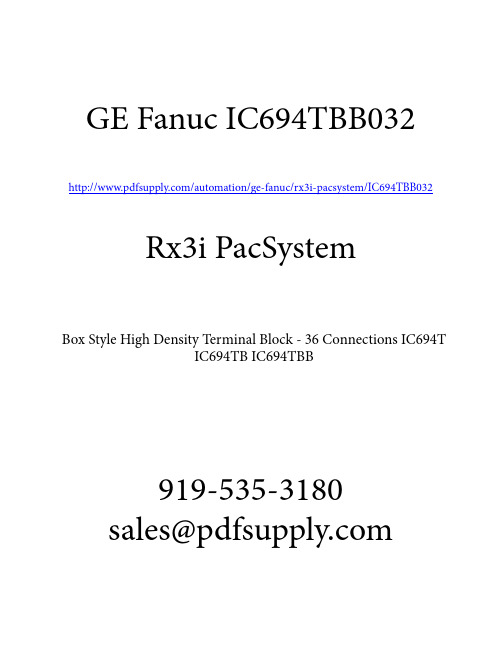
Rx3i PacSystem919-535-3180*******************GE Fanuc IC694TBB032/automation/ge-fanuc/rx3i-pacsystem/IC694TBB032Box Style High Density Terminal Block - 36 Connections IC694T IC694TB IC694TBBHigh-density Terminal BlocksThis chapter describes Terminal Blocks for high-density RX3i modules.Terminal Block Type Catalog Number Box-style Terminal Block, 36 pins, One IC694TBB032Spring-style Terminal Block, 36 pins, One IC694TBS032Extended Box-style Terminal Block, 36 pins, One IC694TBB132Extended Spring-style Terminal Block, 36 pins, One IC694TBS132 Extended High-Density Terminal BlocksExtended High-Density Terminal Blocks IC694TBB132 and IC694TBS132 are functionally-identical to High-Density Terminal Blocks IC694TBB032 and IC694TBS032. The Extended High-Density Terminal Blocks have an outer cover that is approximately ½-inch (13mm) deeper, to accommodate wires with thicker insulation, such as that typically used with AC I/O modules.GFK-2314C 15-115-2 PACSystems™ RX3i System Manual – October 2005 GFK-2314CBox-style Terminal Blocks, 36 Pins: IC694TBB032 and TBB132Box-style Terminal Blocks , IC694TBB032 andIC694TBB132, are used with high-density PACSystemsRX3i modules and equivalent Series 90-30 PLC modules.These terminal blocks provide 36 screw terminals for fieldwiring to the module.Terminal Blocks IC694TBB032 and TBB132 arefunctionally identical. Terminal Block IC694TBB032 comeswith a standard-depth outer cover. When installed, it is thesame depth as most other PACSystems and Series 90-30PLC modules.Extended Terminal Block IC694TBB132 comes with anouter cover that is approximately ½-inch (13mm) deeperthan Terminal Block IC694TBB032, to accommodate wireswith thicker insulation, such as that typically used with ACI/O modules.Specifications: TBB032 and TBB132Torque 7 lb-inWire strip length 0.310 inches (7.87 mm)Wire gauges supported #14-26 AWG (solid or stranded)Connecting Field Wiring to a Box-Style High-density Terminal Block The bottom of the terminal block can be used as a gauge for the wire strip length, as shown below. The stripped wire must be fully-inserted into the terminal block so that the insulation meets the stop position inside the terminal, and the end of the wire is bent. Tightening the terminal screw raises the wire and clamps it in place.GFK-2314C Chapter 15 High-density Terminal Blocks 15-3Spring-style Terminal Blocks, 36 Pins: IC694TBS032 and TBS132 Spring-style Terminal Blocks , IC694TBS032 andIC694TBS132, are used with high-density PACSystemsRX3i modules and equivalent Series 90-30 PLCmodules. These terminal blocks provide 36 spring-styleterminals for field wiring to the module.Terminal Blocks IC694TBS032 and TBS132 arefunctionally identical. Terminal Block IC694TBS032comes with a standard-depth outer cover. Wheninstalled, it is the same depth as most otherPACSystems and Series 90-30 PLC modules.Extended Terminal Block IC694TBS132 comes with anouter cover that is approximately ½-inch (13mm) deeperthan Terminal Block IC694TBS032, to accommodatewires with thicker insulation, such as that typically usedwith AC I/O modules.Specifications: TBS032 and TBS132Wire strip length0.310 inches (7.87 mm) Wire gauges supported#14-28 AWG (solid or stranded)15-4 PACSystems™ RX3i System Manual – October 2005 GFK-2314CInstalling and Removing High-density Terminal BlocksThis section has special installation instructions for High-density Terminal Blocks. See chapter 2 for general installation information. WarningField power must be turned off when installing or removing a Terminal Block assembly. Installing or Removing a Module’s Terminal Block Assembly1. Install the small catalog number label (for example: “ALG600”) supplied with the module inthe slot on the top of the Terminal Block.2. Complete the module wiring and secure the wire bundles to the tie-downs on the bottom ofthe Terminal BlockInserting a Terminal Block in itsCover1. Align the top of the Terminal Block with thebottom of the cover, making sure that thenotches in the Terminal Block match up withthe grooves in the cover.2. Slide the Terminal Block upward until it clicksinto place..GFK-2314C Chapter 15 High-density Terminal Blocks 15-51. 2. 3. Check to be sure the terminalblock is fully seated.Removing a High-density TerminalBlock from the Module1. Open the terminal block door.2. Push the latch down as shown at left veryfirmly until the terminal block is released.3. Pull the terminal block away from themodule until the contacts have separated.Removing a Terminal Block from itsCoverTo remove a Terminal Block from its cover:1. Grasp the sides of the Terminal Block cover.2. Pull down on the bottom of the Terminal Block.。
GE Fanuc RX3i PacSystem IC695PSA140 40W 多用途电源说明书

Rx3i PacSystem919-535-3180*******************GE Fanuc IC695PSA140/automation/ge-fanuc/rx3i-pacsystem/IC695PSA140120/240V AC, 125VDC Multipurpose Power Supply IC695P IC695PSIC695PSA4-16 PACSystems™ RX3i System Manual – October 2005 GFK-2314CMulti-Purpose Power Supply, 120/240 VAC or 125 VDC, 40 Watt: IC695PSA140Power Supply IC695PSA140 is a multi-purpose 40-Watt supply that operates from an input voltagesource in the range of 85 to 264 VAC or 100 VDC to 300 VDC.This power supply provides three outputs:■ +5.1 VDC output,■ +24 VDC relay output that can be used to powercircuits on Output Relay modules.■ +3.3 VDC. This output is used internally by RX3imodules with IC695 catalog numbers.This Power Supply is suitable for use in load-sharing and redundancy applications. Up to 4 Multi-purpose power supplies (PSA140 and/or PSD140) can be used in a PACSystems RX3i (IC695 catalog number) Universal Backplane. Use these Power Supplies if the number of modules required exceeds the capacity of one Power Supply. This Power Supply occupies two backplane slots.The Power Supply indicates when an internal fault occurs so the CPU can detect loss of power or log the appropriate fault code.CautionThis Power Supply cannot be used with RX3i IC695PSD040 or IC695PSA040 Power Supplies in redundant or increased capacity modes. Damage to equipment may result.POWER P/S FAULTGFK-2314C Chapter 4 Power Supplies 4-17LEDsFour LEDs on the Power Supply indicate:■ Power (Green/Amber). When this LED isgreen, it indicates power is being suppliedto the backplane. When this LED is amber, power is applied to the Power Supply but the Power Supply switch is off.■ P/S Fault (Red). When this LED is lit, itindicates the Power Supply has failed and is no longer supplying sufficient voltage to the backplane.■ Over Temperature (Amber). When this LEDis lit, it indicates the Power Supply is near or exceeding its maximum operating temperature.■ Overload (Amber). When this LED is lit, itindicates the Power Supply is near orexceeding its maximum output capability on at least one of its outputs.The CPU Fault Table shows a fault if any Overtemperature, Overload, or P/S Fault occurs.On/Off SwitchThe ON/OFF switch is located behind the door on the front of the module. The switch controls the operation of the outputs of the supply. It does NOT interrupt line power. Projecting tabs next to the switch help prevent accidentally turning it on or off.Wiring TerminalsTerminals for power, ground, and MOV disconnect accept individual 14 to 22 AWG wires. PO W ER P/S F AULT4-18 PACSystems™ RX3i System Manual – October 2005 GFK-2314CSpecifications: IC695PSA140Nominal Rated Voltage Input Voltage Range AC DC120/240 VAC or 125 VDC85 to 264 VAC 100 to 300 VDC Input Power(Maximum with Full Load)70 Watts maximumInrush Current 4 Amps, 250 milliseconds maximum * Output Power40 Watts maximum total5.1 VDC = 30 Watts maximum 3.3 VDC = 30 Watts maximumThe maximum total output power available depends on the ambient temperature, as shown.Output Voltage24 VDC: 19.2 VDC to 28.8 VDC5.1 VDC: 5.0 VDC to 5.2 VDC (5.1 VDC nominal) 3.3 VDC: 3.1 VDC to 3.5 VDC (3.3 VDC nominal)Output Current24 VDC: 0 to 1.6 Amps 5.1 VDC: 0 to 6 Amps 3.3 VDC: 0 to 9 AmpsIsolation (input to backplane): 250 VAC continuous; 1500 VAC for 1 minute Ripple (all outputs) 150 mV Noise (all outputs) 150 mVRide-through time20 ms. This is the length of time the Power Supply maintains valid outputs if the power source is interruptedWiring Terminals Each terminal accepts one 14 AWG to 22 AWG wire. Current per Terminal 6 Amps Number of Daisy-Chained PSA140 SuppliesUp to 4 Number of PSA140 Power Supplies in Universal BackplaneUp to 4* The Inrush Current specification is given as a guide for sizing the external powersource for the IC695PSA140. Peak inrush current may be higher for shorter durations.WarningThe power supply’s door must be closed. During normal operation with an AC power source either 120 VAC or 240 VAC is present on the AC Power Supply. The door protects against accidental shock hazard that could cause severe or fatal injury to personnel.Thermal Deratings: PSA140The maximum output power for Power Supply PSA140 depends on the ambient temperature, as shown below.GFK-2314C Chapter 4 Power Supplies 4-194-20 PACSystems™ RX3i System Manual – October 2005 GFK-2314COvercurrent ProtectionThe 5.1 VDC output is electronically limited to 7 Amps. The 3.3 VDC output is limited to 10 Amps. If an overload (including short circuits) occurs, it is sensed internally and the Power Supply shuts down. Because it is designed for redundancy applications, this Power Supply latches “OFF” in fault conditions and will not automatically try to restart until the overloadcondition is removed. Input power must be cycled to clear a latched fault. However, if the Power Supply is used in a non-redundant application where automatic restarting is required, a jumper plug can be installed.An internal fusable linke in the input line is provided as a backup. The Power Supply usually shuts down before the fusable linke blows. The fusable linke also protects against internal supply faults. The CPU Fault Table shows a fault if any Overtemperature, Overload, or P/S Fault occurs. There is no additional indication if the Power Supply fusable linke blows.In a non-redundancy application, where automatic restarting is may be appropriate, a shunt can be installed on back of the module as shown at left. The shunt must have 0.100 inch spacing on center and accommodate 0.25 inch pins. Example parts are Radio Shack DIP Programming Shunt #276-1512 and DIGI-Key #59000-ND. The module must be removed from the backplane to install the shunt.Field Wiring: IC695PSA140Power Source and Ground ConnectionsThe wires from the power source and ground connect to the terminals on the Power Supply as shown at right. Each terminal accepts one AWG 14 to AWG 22 wire.WarningIf the same external AC power source is used to provide power to two or more RX3i power supplies in the system, connection polarity must be identical at each power supply. A resulting difference in potential can injure personnel or cause damage to equipment.Also, each backplane must be connected to acommon system ground.GFK-2314C Chapter 4 Power Supplies 4-21Input Overvoltage ProtectionThe bottom terminal is normally connected toframe ground with a user-installed jumper as shown lower right. If overvoltage protection is not required or is supplied upstream, no jumper is needed.To Hi-pot test this supply, overvoltage protection must be disabled during the test by removing the jumper. Re-enable overvoltage protection after testing by reinstalling the jumper.In systems with a floating neutral input (the neutral line is not referenced to Protective Earth Ground), this jumper must NOT be installed. In addition, in a floating neutral system, voltage surge protection devices such as MOVs must be installed from L1 to earth ground, and from L2 (Neutral) to earth ground.。
PACSystems RX3i 控制器基板说明书

PACSystems RX3i Controller1 .8Automation & Control SystemsProcess Automation Control SystemsRX3i baseplates are available in 7, 12 and 16 slot configurations to the meet the needs of your application . The RX3i Universal baseplates support hot swap capability to reduce downtime . Expansion bases are available in 5 and 10 slot versions to maximize flexibility .BaseplatesIC695CHS007IC695CHS012 IC695CHS016 IC694CHS398 IC693CHS399 IC694CHS392 IC693CHS393Product NamePACSystems RX3i 7 slot high speed controller base supports only 5 serial bus slots supported . Not expandable .PACSystems RX3i 12 slot high speed controller base supports PCI and serial bus PACSystems RX3i 16 slot high speed controller base supports PCI and serial bus PACSystems RX3i serial 5-slot Expansion Baseplate (serial bus only) PACSystems RX3i serial 5-slot Remote Baseplate (serial bus only) PACSystems RX3i serial 10-slot Expansion Baseplate (serial bus only) PACSystems RX3i serial 10-slot Remote Baseplate (serial bus only) Lifecycle Status Active Active Active Active Mature Active Mature Module TypeUniversal Controller and I/O Base Universal Controller and I/O Base Universal Controller and I/O BaseStandard I/OStandard I/OStandard I/OStandard I/OBackplane Support Supports both PCI and High Speed SerialSupports both PCI and High Speed Serial .Supports both PCI and High Speed Serial .Supports High Speed Serial Only .No PCI support .Supports High Speed Serial Only . No PCI support .Supports High Speed Serial Only . No PCI support .Supports High Speed Serial Only . No PCI support .Module Hot Swap SupportYes Yes Yes No No No No Baseplate OptionController Base and Ethernet Expansion Base .No local base expansionController Base and Ethernet Expansion BaseController Base and Ethernet Expansion BaseExpansionExpansionExpansionExpansionDistance N/A N/A N/A Up to 50 feetUp to 700 feetUp to 50 feetUp to 700 feetNumber of Slots 71216551010Dimension(W x H x D) in . (mm) 10 .43 x 5 .57 x 5 .80 (265 x 142 x 147)18 .01 x 5 .57 x 5 .80 (458 x 142 x 147)23 .7 x 5 .57 x 5 .80 (602 x 142 x 147)10 .43 x 5 .12 x 5 .59 (245 x 130 x 142)10 .43 x 5 .12 x 5 .59 (245 x 130 x 142) 17 .44 x 5 .12 x 5 .59 (443 x 130 x 142)17 .44 x 5 .12 x 5 .59 (443 x 130 x 142)Internal Power Used600 mA @ 3 .3 VDC; 240 mA @ 5 VDC ************;240 mA @ 5 VDC 600 mA @ 3 .3 VDC; 240 mA @ 5 VDC170 mA @ 5 VDC480 mA @ 5 VDC150 mA @ 5 VDC460 mA @ 5 VDC。
GE Fanuc RX3i PacSystem 919-535-3180 输出模块说明说明书

Rx3i PacSystem919-535-3180*******************GE Fanuc IC694MDL752/automation/ge-fanuc/rx3i-pacsystem/IC694MDL752Output module 5/24VDC (TTL) 0.5 amp 32 point negative logic.IC694M IC694MD IC694MDLGFK-2314C Chapter 7 Discrete Output Modules 7-27Output Module, 5/24 VDC (TTL) Negative Logic, 32 Pt: IC694MDL752The 5/24 volt DC (TTL) Negative Logic Outpu t module,IC694MDL752, provides 32 discrete outputs arranged in four isolated groups of eight. Each group has its own common. The outputs arenegative logic or sinking-type outputs (the ON state for a point results in an active low output).The module has two modes of operation. In TTL mode, the outputs can switch loads across +5 VDC (±5%) and are capable of sinking amaximum current of 25mA per point. In 12/24V mode, the outputs can switch loads over the range of +12 to -24 VDC (+20%, -15%) and are capable of sinking a maximum current of 0.5A per point.There are two pins on the I/O connectors for each group common. Each pin has a current-handling capacity of 3 Amps. It is recommended that connections be made to both pins when connecting the common; however, it is required for high-current applications (between 3 and 4 Amps).Each group can be used to drive different loads. For example, the module can drive TTL loads, 12 VDC loads, and 24 VDC loads ondifferent groups. It is important to consider the effects of electrical noise when mixing TTL and inductive-type loads.Each point has an internal pull–up resistor. The resistor passively pulls up the output to the user positive side power input (typically +5V for TTL mode) when the output point FET is OFF, providing a high logic level for TTL applications. All 32 outputs are forced OFF when the CPU isstopped. Power to provide current to the loads must be provided by the user. The module also draws a minimum amount of power from the user supply to provide gate drive to the output devicesBackplane isolation between the field side and logic side is provided by opto–couplers on the module. No special fault or alarm diagnostics are reported. Individual numbered LEDs show the ON/OFF status of each output.This module can be installed in any I/O slot in an RX3i system.7-28 PACSystems™ RX3i System Manual – October 2005 GFK-2314CSpecifications: MDL752Rated Voltage5, and 12 through 24 volts DC, negative logic (active low)Output Voltage Range 4.75 to 5.25 volts DC (TTL mode)10.2 to 28.8 volts DC (12/24V mode)Outputs per Module 32 (four groups of eight outputs each) Isolation:Field to Backplane (optical) and to Frame Ground 250 VAC continuous; 1500 VAC for 1 minute Group to Group 50 VAC continuous; 500 VAC for 1 minute Output Current 25mA per point (maximum in TTL mode)0.5 Amps per point (maximum in 12/24V mode); with 4 Amps maximum per group and 3 Amps maximum per group common pinPower Consumption 260mA (maximum) from 5 volt bus on backplane;(13mA + 3 mA/point ON + 4.7 mA/LED)12 mA (maximum) per group from user supply@ 5VDC and all eight outputs in group ON25 mA (maximum) per group from user supply@ 12 VDC and all eight outputs in group ON44 mA (maximum) per group from user supply@ 24 VDC and all eight outputs in group ONOutput Characteristics Inrush Current 4.6 Amps for 10ms On–state (active low) 0.4 volts DC (maximum in TTL mode) Voltage Drop 0.24 volts DC (maximum in 12/24V mode) Off–state Leakage Current 0.1mA maximum On Response Time 0.5ms maximum Off Response Time 0.5ms maximumRefer to Appendix A for product standards and general specifications.GFK-2314C Chapter 7 Discrete Output Modules 7-29Field Wiring: MDL752Connections to the output circuits are made from the load devices to two male 24–pinconnectors (Fujitsu FCN–365P024–AU) on the front of the module.The module’s connectors can be connected directly to field devices using a cable having a mating female connector on one end and stripped and tinned wires on the other end. You can purchase a pair of pre–wired cables, catalog numbers IC694CBL327 and IC694CBL328 or build cables. Refer appendix B of this manual for more information.Connections can also be made a pair of cables with connectors on each end. These cables connect the module with DIN-rail mounted terminal blocks as described in appendix B.7-30 PACSystems™ RX3i System Manual – October 2005 GFK-2314CTypical Connections: MDL7525V24V5V。
基于FANUC RX3i PAC模糊控制算法的研究
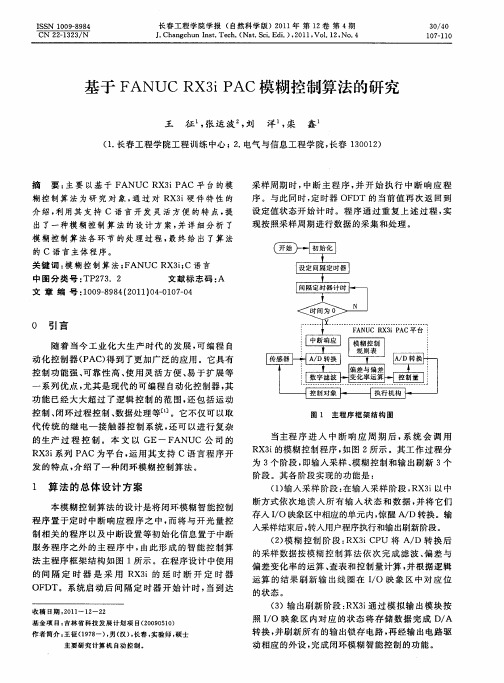
完成 上述 3个 阶段称 作一个 中断 响应周 期 。在 整个 程序 运行 期 间 , X3 的 C U 以一 定 的 扫 描速 R i P 度重 复执 行上 述 3个 阶段 。
3/0 0 4
17lO O一1
基于 F ANUC R 3 P X i AC模 糊 控制 算 法 的 研 究
王 征 张运 波。 刘 洋 栾 鑫 , , ,
(. 1 长春工 程学 院工 程训 练 中心 ; . 2 电气 与信息 工程学 院 , 长春 1 O 1 ) 3 0 2
断方式依 次地 读 入 所 有输 入 状 态 和 数 据 , 并将 它们 存入 IO映象区中相应的单 元 内, 醒 A D转换 。输 / 惊 / 入采样结束后 , 转入用户程序执行 和输 出刷新阶段 。 ( ) 糊 控 制 阶段 : X i P 将 A/ 转 换 后 2模 R 3C U D
照 I0 映象 区 内对 应 的状 态 将 存储 数 据 完 成 D A / /
作 者 简 介 。 征 (9 8 , ( ) 长 春 , 验 师 , 士 王 1 7 一) 男 汉 , 实 硕 主 要 研 究 计 算 机 自动 控 制 。
转 换 , 刷新所 有 的输 出锁 存 电路 , 经输 出电路 驱 并 再 动 相应 的外设 , 完成 闭环模 糊智 能控 制的功 能 。
收 稿 日期 ;0 1 2 2 2 1 —1 - 2 基 金 项 目 t 林 省 科 技 发 展 计 划 项 目( 0 9 50 吉 2001)
运 算 的 结果 刷 新 输 出线 圈 在 IO 映 象 区中 对 应 位 /
的状态 。
( )输 出刷新 阶段 : X i 过模 拟 输 出模 块 按 3 R 3通
!璺 Q ! 墨 :! 堡
GE Fanuc RX3i PACSystem IC694APU300高速计数器模块说明说明书

Rx3i PacSystem919-535-3180*******************GE Fanuc IC694APU300/automation/ge-fanuc/rx3i-pacsystem/IC694APU300High speed counter module 200KHZ A B and C type. IC694A IC694APIC694APU8-2 PACSystems* RX3i – August 2011 GFK-2314DHigh-speed Counter Module: IC694APU300The High-speed Counter module, IC694APU300, provides direct processing of rapid pulse signals up to 80 kHz. The module senses inputs, processes the input count information, and controls the outputs without needing to communicate with a CPU.The High Speed Counter uses 16 bits of discrete input memory (%I), 15 words of analog input memory (%AI), and 16 bits of discrete outputmemory (%Q) in the CPU. The High-speed Counter can be configured to have:▪ 4 identical, independent simple counters ▪ 2 identical, independent more complex counters ▪ 1 complex counterTwo green LEDs indicate the operating status of the module and the status of configuration parameters. Additional module features include:▪ 12 positive logic (source) inputs with input voltage range selection of either 5 VDC or 10 to 30 VDC ▪ 4 positive logic (source) outputs▪ Counts per timebase register for each counter ▪ Internal module diagnostics▪A removable terminal board for field wiringInputs can be used as count signals, direction, disable, edge-sensitive strobe, and preload inputs depending on the counter type selected by the user. Outputs can be used to drive indicating lights, solenoids, relays, and other devices. Power for the module is drawn from the backplane’s 5VDC bus. Power sources for input and output devices must be supplied by the user or by the +24 VDC Isolated output of the power supply. The module also provides a selectable threshold voltage to allow the inputs to respond to either 5VDC signal levels or 10 to 30VDC signal levels.The blue bands on the label show that APU300 is a low-voltage module. This module can be installed in any I/O slot in an RX3i system.Refer to Appendix A for product standards and general specifications.Input ImpedanceGFK-2314D Chapter 8 Discrete Mixed Modules 8-3Field Wiring: APU300Wiring information for APU300 is shown below.Shielded cable must be used for connecting to the High Speed Counter module. The shield for the cable must have a high frequency ground within 6 inches (15.24 cm) of the module to meet the IEC 1000-4-4 levels specified in Appendix A. The cable’s length is limited to 30 meters.Terminals Field WiringAll 12 High Speed Counter inputs are single-ended positive logic (source) type inputs. Transducers with CMOS buffer outputs (74HC04 equivalent) can directly drive the High-speed Counter inputs using the 5V input range. Transducers using TTL totem pole or open-collector outputs must include a 470 ohm pull-up resistor (to 5V) to guarantee compatibility with the High-speed Counter inputs. Transducers using high voltage open collector (sink) type outputs must have a 1K pull-up resistor to + 12V for compatibility with the High-speed Counter 10 to 30 volt input range.The 5VDC threshold is selected by connecting a jumper between two terminals on the detachable terminal board connector. Leaving the threshold selection terminals unconnected places the inputs in the default 10 to 30 VDC voltage range.Do not connect 10 to 30 VDC to the module inputs when the 5 VDC inputrange (pins 13 to 15 jumpered) is selected. Doing so will damage themodule.8-4 PACSystems* RX3i – August 2011 GFK-2314DTerminal Assignments for Each Counter TypeThe following table shows which terminals to use for the type of counter selected during module configuration.(1). Type B counter:A1, B1 are the A and B inputs for counter 1.A2, B2 are the A and B inputs for counter 2.(2) Type C Counter:A1, B1 are the A and B count inputs for (+) loopA2, B2 are the A and B count inputs for (–) loop(3) OUTPWR does not source power for user loads. Output power must be supplied from an external supply.* Inputs and outputs identified by two numbers separated by a decimal point indicate the counter number to the left of the decimal point and the element number on the right. For example, STRB1.2 indicates Counter 1, Strobe 2 input.GFK-2314D Chapter 8 Discrete Mixed Modules 8-5。