12_13_Plotek_GB
ENG_CD_1452674_C3_1452674-c_drw (1)
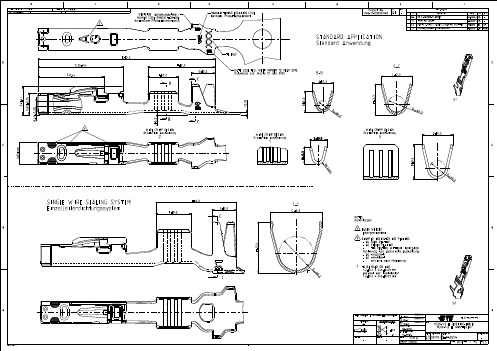
THIS DRAWING IS UNPUBLISHED. RELEASED FOR PUBLICATION ALL RIGHTS RESERVED.
7
19
6
5
4
3
2
1
REVISIONS
P LTR DESCRIPTION DATE DWN APVD
C
COPYRIGHT 2000
-
2
REVISION Aenderungsstand / NUMBER CODE PRODUCTIONTOOL Nummercode Produktionswerkzeug
22DEC2006 14AUG2009
R.M. R.M. EG
RM
PARTS 7-1452... ADDED, DRAWING MODIFIED 07DEC2011
24APR2013
Abr Raab
STANDARD APPLICATION Standard Anwendung
K
D
TE Logo H F G DATE CODE E.G. WEEK NUMBER 12 YEAR 2013 Datumscde z.B. Woche 12 Jahr 2013
A A A
0.080.15
2.6
0.13 25 35 9
7 6 5 7 6 5 7 6 5 7
1
-
-
-
-
-
-
-
-
-
-
-
-
3.55 3.95 967056-1 for 963143-1 for n n
2
1.81.80.84.24.32.62.62.06.40.8 16
7-1452668-3 A 7-1452668-2 A 7-1452668-1 A 7-1452671-3 A 7-1452671-2 A 7-1452671-1 A 2141861-3 A A A 2141861-2
AD9653 AD9253 AD9633 模数转换器用户指南说明书

One Technology Way · P.O. Box 9106 · Norwood, MA 02062-9106 · Tel: 781.329.4700 · Fax: 781.461.3113 · EVALUATING THE AD9653/AD9253/AD9633 ANALOG-TO-DIGITAL CONVERTERSPrefaceThis user guide describes the AD9653, AD9253 and AD9633 evaluation boards, AD9653-125EBZ,AD9253-125EBZ and AD9633-125EBZ, which provide all of the support circuitry required to operate these parts in their various modes and configurations. The application software used to interface with the devices is also described.The AD9653AD9253 and AD9633 data sheets provide additional information and should be consulted when using the evaluation board. All documents and software tools are available at/hsadcevalboard. For additional information or questions, send an email to*******************************.Typical Measurement SetupFigure 1. Evaluation Board Connection—AD9653-125EBZ, AD9253-125EBZ or AD9633-125EBZ (on Left)and HSC-ADC-EVALCZ (on Right)FeaturesFull featured evaluation board for the AD9653/AD9253/AD9633qSPI interface for setup and controlqExternal, on-board oscillator, or AD9517 clocking optionqBalun/transformer or amplifier input drive optionqOn-board LDO regulator needing a single external 6 V, 2 A dc supplyqVisualAnalog® and SPI controller software interfacesqHelpful DocumentsAD9653, AD9253 or AD9633 data sheetqHigh speed ADC FIFO evaluation kit (HSC-ADC-EVALCZ)qAN-905 Application Note, VisualAnalog Converter Evaluation Tool Version 1.0 User ManualqAN-878 Application Note, High Speed ADC SPI Control SoftwareqAN-877 Application Note, Interfacing to High Speed ADCs via SPIqAN-835 Application Note, Understanding ADC Testing and EvaluationqDesign and Integration FilesSchematics, layout files, bill of materialsqEquipment NeededAnalog signal source and antialiasing filterqSample clock source (if not using the on-board oscillator)q2 switching power supplies (6.0 V, 2.5 A), CUI EPS060250UH-PHP-SZ providedqPC running Windows®qUSB 2.0 portqAD9653-125EBZ, AD9253-125EBZ or AD9633-125EBZ boardqHSC-ADC-EVALCZ FPGA-based data capture kitqGetting StartedThis section provides quick start procedures for using the AD9653-125EBZ, AD9253-125EBZ or AD9633-125EBZ board. Both the default and optional settings are described.Configuring the BoardBefore using the software for testing, configure the evaluation board as follows:1.Connect the evaluation board to the data capture board, as shown in Figure 1.2.Connect one 6 V, 2.5 A switching power supply (such as the CUI, Inc., EPS060250UH-PHP-SZ that is supplied) to the AD9653-125EBZ, AD9253-125EBZ or AD9633-125EBZ.3.Connect one 6 V, 2.5 A switching power supply (such as the supplied CUI EPS060250UH-PHP-SZ) to the HSC-ADC-EVALCZ board.Connect the HSC-ADC-EVALCZ board (J6) to the PC using a USB cable.4.5.On the ADC evaluation board, confirm that the jumpers are installed as shown in Figure 2 and Table 1.On the ADC evaluation board, use a clean signal generator with low phase noise to provide an6.input signal to the desired A and/or B channel(s). Use a 1 m, shielded, RG-58, 50 Ω coaxial cable to connect the signal generator. For best results, use a narrow-band, band-pass filter with 50 Ωterminations and an appropriate center frequency. (Analog Devices, Inc., uses TTE, Allen Avionics, and K&L band-pass filters.)Evaluation Board HardwareThe evaluation board provides the support circuitry required to operate the AD9653, AD9253 andAD9633 in their various modes and configurations. Figure 1 shows the typical bench characterization setup used to evaluate AC performance. It is critical that the signal sources used for the analog input and clock have very low phase noise (<1 ps rms jitter) to realize the optimum performance of the signal chain. Proper filtering of the analog input signal to remove harmonics and lower the integrated or broadband noise at the input is necessary to achieve the specified noise performance.See the Getting Started section to get started, and visit UG-328 Design Support for the complete schematics and layout diagrams. These diagrams demonstrate the routing and grounding techniques that should be applied at the system level when designing application boards using these converters.Power SuppliesThis evaluation board comes with a wall-mountable switching power supply that provides a 6 V, 2 A maximum output. Connect the supply to a 100 V ac to 240 V ac, 47 Hz to 63 Hz wall outlet. The output from the supply is provided through a 2.1 mm inner diameter jack that connects to the printed circuit board (PCB) at P101. The 6 V supply is fused and conditioned on the PCB before connecting to the low dropout linear regulators that supply the proper bias to each of the various sections on the board.The evaluation board can be powered in a nondefault condition using external bench power supplies. To do this, remove the E101, E102, E103 and E104 ferrite beads to disconnect the outputs from theon-board LDOs. This enables the user to bias each section of the board individually. Use P102 andP103 to connect a different supply for each section. A 1.8 V, 0.5 A supply is needed for 1.8V_AVDD and 1.8V_DRVDD. Although the power supply requirements are the same for AVDD and DRVDD, it is recommended that separate supplies be used for both analog and digital domains. The SPI and its level shifters and alternate clock options require a separate 3.3 V, 0.5 A analog supply.Two additional supplies, 5V_AVDD and 3V_AVDD, are used to bias the optional input path amplifiers and optional AD9517-3 clock chip. If used, these supplies should each have 0.5 A current capability. Input SignalsWhen connecting the ADC clock and analog source, use clean signal generators with low phase noise, such as the Rohde & Schwarz SMA, or HP 8644B signal generators or an equivalent. Use a 1 m shielded, RG-58, 50 Ω coaxial cable for connecting to the evaluation board. Enter the desired frequency and amplitude (see the Specifications section in the data sheet of the respective part). When connecting the analog input source, use of a multipole, narrow-band band-pass filter with 50 Ωterminations is recommended. Analog Devices uses band-pass filters from TTE and K&L Microwave, Inc. Connect the filters directly to the evaluation board.If an external clock source is used, it should also be supplied with a clean signal generator as previously specified. Analog Devices evaluation boards typically can accept ~2.8 V p-p or 13 dBm sine wave input for the clock.Output SignalsThe default setup uses the Analog Devices high speed converter evaluation platform (HSC-ADC-EVALCZ) for data capture. The serial LVDS outputs from the ADC are routed to ConnectorP1002 using 100 Ω differential traces. For more information on the data capture board and its optional settings, visit /hsadcevalboard.Jumper SettingsSet the jumper settings/link options on the evaluation board for the required operating modes before powering on the board. The functions of the jumpers are described in Table 1. Figure 2 shows the default jumper settings.Table 1. Jumper SettingsJumperDescriptionJ202This jumper selects between internal V REF and external V REF .To choose the internal 1 V reference, connect Pin 3 (DUT_SENSE) to Pin 5 (GND).To use the on-board ADR130 1 V reference, connect Pin 2 (DUT_SENSE) to Pin 1 (AVDD), and connect Pin 4 (DUT_VREF) to Pin 6 (EXT_REF).To apply a reference voltage from an external off-board source, connect Pin 2 (DUT_SENSE)to Pin 1 (AVDD) and apply the reference voltage to Pin 4 (DUT_VREF). The AD9653 canaccommodate reference voltages from 1.0 V to 1.3 V; the AD9253 and AD9633 referencevoltage is specified to be 1.0 V.J204Use this jumper to power down the ADC. Using the SPI, the PDWN pin can be configured to be STBY (standby).J302This jumper sets the ADC for SPI communications with the HSC-ADC-EVALCZ .Connect Pin 1 to Pin 2 for SDIO, Pin 4 to Pin 5 for SCLK, and Pin 8 to Pin 9 for CSB.J803This jumper enables the on-board crystal oscillator.Figure 2. Default Jumper Connections for AD9653-125EBZ /AD9253-125EBZ /AD9633-125EBZ Board Evaluation Board CircuitryThis section explains the default and optional settings or modes allowed on the AD9653-125EBZ ,AD9253-125EBZ and the AD9633-125EBZ boards.PowerPlug the switching power supply into a wall outlet rated at 100 V ac to 240 V ac, 47 Hz to 63 Hz. Connect the DC output connector to P101 on the evaluation board.Analog InputThe four channel inputs on the evaluation board are set up for a double balun-coupled analog input with a 50 Ω impedance. The default analog input configuration supports analog input frequencies of up to ~200 MHz.VREFThe default VREF configuration is to connect the SENSE pin to AGND for internal VREF operation. This is done by connecting Pin 3 to Pin 5 on Header J202. An external reference voltage can be provided to the AD9653, AD9253 and AD9633. Connecting Pin 2 to Pin 1 on Header J202 puts the ADC in a mode where it requires a reference voltage from an external source. The external on-board 1.0 V reference is provided by the ADR130. This external reference can be connected to the ADC by connecting Pin 4 to Pin 6 on Header J202. Alternatively, if an external off-board reference is desired, connect Pin 2 to Pin1 on Header J202 and apply the reference voltage directly to Pin 4 of Header J202. The AD9653 can accommodate reference voltages from 1.0 V to 1.3 V; the AD9253 and AD9633 reference voltage is specified to be 1.0 V.RBIASRBIAS has a default setting of 10 kΩ (R205) to ground and is used to set the ADC core bias current. Note that using a resistor value other than a 10 kΩ, 1% resistor for RBIAS may degrade the performance of the device.ClockThe default clock input circuit is derived from a simple transformer-coupled circuit using a high bandwidth 1:1 impedance ratio transformer (T801/T802) that adds a low amount of jitter to the clock path. The clock input is 50 Ω terminated and ac-coupled to handle single-ended sine wave types of inputs. The transformer converts the single-ended input to a differential signal that is clipped byCR801 before entering the ADC clock inputs. The AD9653, AD9253 and AD9633 ADCs are equipped with an internal 8:1 clock divider to facilitate usage with higher frequency clocks. When using the internal divider and a higher input clock frequency, remove CR801 to preserve the slew rate of the clock signal.The AD9653-125EBZ, AD9253-125EBZ and AD9633-125EBZ boards are set up to be clocked through the transformer-coupled input network from the crystal oscillator, Y801. This oscillator is a low phase noise oscillator from Valpey Fisher (VFAC3-BHL-125MHz). If a different clock source is desired, remove C810 (optional) and Jumper J803 to disable the oscillator from running and connect the external clock source to the SMA connector, J802 (labeled CLK+).PDWNTo enable the power-down feature, add a shorting jumper across J204 at Pin 1 and Pin 2 to connect the PDWN pin to DRVDD.Modes of OperationStandalone (PIN) ModeThe AD9653/AD9253/AD9633 ADCs can operate in pin mode if there is no need to program and change the default modes of operation via the SPI. For applications that do not require SPI mode operation, the CSB pin is tied to AVDD, and the SDIO/OLM pin controls the output lane mode. Table 2 and Table 3 specify the settings for pin mode operation.Table 2. Output Lane Mode (OLM) Pin SettingsOLM Pin Voltage Output ModeAVDD (Default)Two-lane. 1× frame, 16-bit serial outputGND One-lane. 1× frame, 16-bit serial outputTable 3. Digital Test Pattern (DTP) Pin SettingsSeected DTP Output Mode Resulting D0±x and D1±xNormal Operation10 kΩ to AGND Normal operationDTP AVDD1000 0000 0000 0000Additional information on the lane modes is provided in the AD9653, AD9253 and AD9633 data sheets.Default ModeTo operate the device under test (DUT) using the SPI, follow the jumper settings for J302 as shown in Table 1.How To Use The Software For TestingSetting up the ADC Data CaptureAfter configuring the board, set up the ADC data capture using the following steps:1.Open VisualAnalog on the connected PC. The appropriate part type should be listed in the status bar of the VisualAnalog – New Canvas window. Select the template that corresponds to the type of testing to be performed (see Figure 3, where the AD9253 is shown as an example).Figure 3. VisualAnalog, New Canvas Window2.After the template is selected, a message appears asking if the default configuration can be used to program the FPGA (see Figure 4). Click Yes, and the window closes.Figure 4. VisualAnalog Default Configuration Message3.To change features to settings other than the default settings, click the Expand Display button,located on the bottom right corner of the window (see Figure 5), to see what is shown in Figure 6. 4.Change the features and capture settings by consulting the detailed instructions in the AN-905 Application Note, VisualAnalog Converter Evaluation Tool Version 1.0 User Manual. After the changes are made to the capture settings, click the Collapse Display button.Figure 5. VisualAnalog Window Toolbar, Collapsed DisplayFigure 6. VisualAnalog, Main Window Expanded DisplayEvaluation And TestSetting up the SPI Controller SoftwareAfter the ADC data capture board setup is complete, set up the SPI controller software using the following procedure:1.Open the SPI controller software by going to the Start menu or by double-clicking theSPIController software desktop icon. If prompted for a configuration file, select the appropriate one. If not, check the title bar of the window to determine which configuration is loaded. Ifnecessary, choose Cfg Open from the File menu and select the appropriate file based on your part type. Note that the CHIP ID(1) box should be filled to indicate whether the correct SPI controller configuration file is loaded (see Figure 7).Figure 7. SPI Controller, CHIP ID(1) BoxClick the New DUT button in the SPIController window (see Figure 8)2.Figure 8. SPI Controller, New DUT Button3.In the ADCBase 0 tab of the SPIController window, find the CLOCK DIVIDE(B) box (see Figure9). If using the clock divider, use the drop-down box to select the correct clock divide ratio, ifnecessary. For additional information, refer to the data sheet, the AN-878 Application Note, High Speed ADC SPI Control Software, and the AN-877 Application Note, Interfacing to High Speed ADCsvia SPI.Figure 9. SPI Controller, CLOCK DIVIDE(B) Box4.Note that other settings can be changed on the ADCBase 0 tab (see Figure 9) and the ADC A, ADC B, ADC C, and ADC D tabs (see Figure 10) to set up the part in the desired mode. TheADCBase 0 tab settings affect the entire part, whereas the settings on the ADC A, ADC B, ADC C, and ADC D tabs affect the selected channel only. See the appropriate part data sheet, the AN-878 Application Note, High Speed ADC SPI Control Software, and the AN-877 Application Note,Interfacing to High Speed ADCs via SPI, for additional information on the available settings.Figure 10. SPI Controller, Example ADC A Page5.Click the Run button in the VisualAnalog toolbar (see Figure 11).Figure 11. Run Button (Encircled in Red) in VisualAnalog Toolbar, Collapsed DisplayAdjusting the Amplitude of the Input SignalThe next step is to adjust the amplitude of the input signal for each channel as follows:Adjust the amplitude of the input signal so that the fundamental is at the desired level. Examine 1.the Fund Power reading in the left panel of the VisualAnalog Graph - AD9253 FFT window(see Figure 12).Figure 12. Graph Window of VisualAnalogRepeat this procedure for Channel B, Channel C, and Channel D.2.3.Click the disk icon within the VisualAnalog Graph - AD9253 FFT window to save theperformance plot data as a .csv formatted file. See Figure 13 for an example.Figure 13. Typical FFT, AD9253Troubleshooting TipsIf the FFT plot appears abnormal, do the following:If you see an abnormal noise floor, go to the ADCBase0 tab of the SPIController window andqtoggle the Chip Power Mode in MODES(8) from Chip Run to Reset and back.If you see a normal noise floor when you disconnect the signal generator from the analog input, be qsure that you are not overdriving the ADC. Reduce the input level if necessary.In VisualAnalog, click the Settings icon in the Input Formatter block. Check that NumberqFormat is set to the correct encoding (twos complement by default). Repeat for the other channels.If the FFT appears normal but the performance is poor, check the following:Make sure that an appropriate filter is used on the analog input.qMake sure that the signal generators for the clock and the analog input are clean (low phase noise). qChange the analog input frequency slightly if noncoherent sampling is being used.qMake sure that the SPI configuration file matches the product being evaluated.qIf the FFT window remains blank after Run in VisualAnalog (see Figure 11) is clicked, do the following:Make sure that the evaluation board is securely connected to the HSC-ADC-EVALCZ board.qMake sure that the FPGA has been programmed by verifying that the DONE LED is illuminated onqthe HSC-ADC-EVALCZ board. If this LED is not illuminated, make sure that the U4 switch on the board is in the correct position for USB CONFIG.Make sure that the correct FPGA program was installed by clicking the Settings icon in the ADCqData Capture block in VisualAnalog. Then select the FPGA tab and verify that the proper FPGA bin file is selected for the part.If VisualAnalog indicates that the FIFO Capture timed out, do the following:Make sure that all power and USB connections are secure.qProbe the DCO signal at P1002 (Pin A10 and/or Pin B10) on the evaluation board, and confirm that a qclock signal is present at the ADC sampling rate.© Analog Devices, Inc. All rights reserved. Trademarks andregistered trademarks are the property of their respective 。
G121SN01 V3 spec. 20071107

(V) Preliminary Specifications() Final SpecificationsModule 12.1 Inch Color TFT-LCD Model Name G121SN01 V3Customer DateChecked &Approved by______ Note: This specification is subject to change without notice. Approved by Date Debbie Chiu 2007/11/07 Prepared bySam Chen___ 2007/11/07 General Display Business Division / AU Optronics CorporationContents1. Operating Precautions (4)2. General Description (5)2.1 Display Characteristics (5)2.2 Optical Characteristics (6)3. Functional Block Diagram (9)4. Absolute Maximum Ratings (10)4.1 Absolute Ratings of TFT LCD Module (10)4.2 Absolute Ratings of Environment (10)5. Electrical Characteristics (11)5.1 TFT LCD Module (11)5.2 Backlight Unit (13)6. Signal Characteristic (15)6.1 Pixel Format Image (15)6.2 Scanning Direction (15)6.3 Signal Description (16)LVDS Signal Format:6.4 The Input Data Format (17)6.4 The Input Data Format (18)6.5 Interface Timing (19)6.6 Power ON/OFF Sequence (20)7. Connector & Pin Assignment (21)7.1 TFT LCD Module: LVDS Connector (21)7.2 Backlight Unit: Lamp Connector (21)8. Reliability Test Criteria (22)9. Mechanical Characteristics (23)9.1 LCM Outline Dimension (Front View) (23)9.2 LCM Outline Dimension (Rear View) (24)9.3 Screw Hole Depth and Center Position (25)10. Label and Packaging (26)10.1 Shipping Label (on the rear side of TFT-LCD display) (26)10.2 Carton Package (26)11. Safety (27)11.1 Sharp Edge Requirements (27)11.2 Materials (27)11.3 Capacitors (27)11.4 National T est Lab Requirement (27)Record of RevisionVersion and Date Page Old Description New Description Remark0.0 2007/11/07 All First Draft All1. Operating Precautions1) Since front polarizer is easily damaged, please be cautious and not to scratch it.2) Be sure to turn off power supply when inserting or disconnecting from input connector.3) Wipe off water drop immediately. Long contact with water may cause discoloration or spots.4) When the panel surface is soiled, wipe it with absorbent cotton or soft cloth.5) Since the panel is made of glass, it may be broken or cracked if dropped or bumped on hard surface.6) Since CMOS LSI is used in this module, take care of static electricity and insure human earth whenhandling.7) Do not open nor modify the module assembly.8) Do not press the reflector sheet at the back of the module to any direction.9) In case if a module has to be put back into the packing container slot after it was taken out from thecontainer, do not press the center of the CCFL Reflector edge. Instead, press at the far ends of the CCFL Reflector edge softly. Otherwise the TFT Module may be damaged.10) At the insertion or removal of the Signal Interface Connector, be sure not to rotate nor tilt the InterfaceConnector of the TFT Module.11) After installation of the TFT Module into an enclosure (Notebook PC Bezel, for example), do not twist norbend the TFT Module even momentary. At designing the enclosure, it should be taken into consideration that no bending/twisting forces are applied to the TFT Module from outside. Otherwise the TFT Module may be damaged.12) Cold cathode fluorescent lamp in LCD contains a small amount of mercury. Please follow local ordinances orregulations for disposal.13) Small amount of materials having no flammability grade is used in the LCD module. The LCD module should besupplied by power complied with requirements of Limited Power Source (IEC60950 or UL1950), or be applied exemption.14) The LCD module is designed so that the CCFL in it is supplied by Limited Current Circuit (IEC60950 or UL1950).Do not connect the CCFL in Hazardous Voltage Circuit.15) Severe temperature condition may result in different luminance, response time and lamp ignition voltage.16) Continuous operating TFT-LCD display under low temperature environment may accelerate lamp exhaustion andreduce luminance dramatically.17) The data on this specification sheet is applicable when LCD module is placed in landscape position.18) Continuous displaying fixed pattern may induce image sticking. It’s recommended to use screen saver or shufflecontent periodically if fixed pattern is displayed on the screen.2. General DescriptionG121SN01 V3 is a Color Active Matrix Liquid Crystal Display composed of a TFT-LCD display, a driver circuit, and a backlight system. The screen format is intended to support SVGA (800(H) x 600(V)) screen and 16.2M (RGB8-bits) or 262K colors (RGB 6-bits). All input signals are LVDS interface compatible. Inverter card of backlight is not included.G121SN01 V3 is designed for industrial display applications.2.1 Display CharacteristicsThe following items are characteristics summary on the table under 25 ℃ condition:Items Unit SpecificationsScreen Diagonal [inch] 12.1Active Area [mm] 246.0(H) x 184.5(V)Pixels H x V 800x3(RGB) x 600Pixel Pitch [mm] 0.3075 x 0.3075Pixel Arrangement R.G.B. Vertical StripeDisplay Mode TN, Normally WhiteNominal Input Voltage VDD [Volt] 3.3 typ.Typical Power Consumption [Watt] 7.8W (64 Gray Bar Pattern, exclude inverter)Weight [Grams] 660g (typ.)Physical Size [mm] 279.0(H)x 209.0(V) x 11.0(D) (typ.)Electrical Interface 1 channel LVDSSurface Treatment AG, Hardness 3HSupport Color 16.2M/262K colorsTemperature RangeOperatingStorage (Non-Operating) [o C][o C]-30 to +85 (+85℃as panel surface temperature)-30 to +85RoHS Compliance RoHS Compliance2.2 Optical CharacteristicsThe optical characteristics are measured under stable conditions at 25℃ (Room Temperature): Item Unit Conditions Min. Typ. Max. NoteWhite Luminance [cd/m2] IRCFL= 6.0mA(center point)320 400 - 1Uniformity 13 Points - 1.25 1.60 1, 2, 3,Contrast Ratio - 600 - 4[msec] Rising - 10 20 5[msec] Falling - 2530 Response Time[msec] Rising + Falling - 35 50 5 6[degree] [degree] Horizontal (Right)CR = 10 (Left)60607070--6Viewing Angle[degree] [degree]Vertical (Upper)CR = 10 (Lower)45555060--6 Red x 0.590 0.620 0.650Red y 0.310 0.340 0.370Green x 0.275 0.305 0.335Green y 0.555 0.585 0.615Blue x 0.115 0.145 0.175Blue y 0.112 0.115 0.118White x 0.283 0.313 0.343Color / ChromaticityCoordinates(CIE 1931)%White y 0.299 0.329 0.359 Color Gamut 55Note 1: Measurement methodEquipment Pattern Generator, Power Supply, Digital Voltmeter, Luminance meter (SR_3 or equivalent)Aperture1with 50cm viewing distance ∘Test Point Center Environment < 1 luxNote 2: Definition of 13 points positionNote 3: The luminance uniformity of 13 points is defined by dividing the minimum luminance values by the maximum test point luminance.δW13 = Maximum Brightness of Thirteen PointsMinimum Brightness of Thirteen PointsModule Driving EquipmentNote 4: Definition of contrast ratio (CR):Note 5: Definition of response time:The output signals of photo detector are measured when the input signals are changed from “White ” to “Black ” (falling time) and from “Black ” to “White ” (rising time), respectively. The response time interval is between 10% and 90% of amplitudes. Please refer to the figure as below.Note 6: Definition of viewing angleViewing angle is the measurement of contrast ratio 10, at the screen center, over a 180° horizontal and 180°≧vertical range (off-normal viewing angles). The 180° viewing angle range is broken down as below: 90° (θ) horizontal left and right, and 90° (Φ) vertical high (up) and low (down). The measurement direction is typically perpendicular to the display surface with the screen rotated to its center to develop the desired measurement viewing angle.Contrast ratio (CR)=Brightness on the “White ” state Brightness on the “Black ” state3. Functional Block DiagramThe following diagram shows the functional block of the 12.1 inch color TFT/LCD module:LVDS Connector: MSB240420-EMating Type:P240420 or compatibleLamp Connector: JST BHR-03VS-1Mating Type:SM03(4.0)B-BHS-1-TB4. Absolute Maximum Ratings4.1 Absolute Ratings of TFT LCD ModuleItem Symbol Min Max Unit Logic/LCD Drive Vin -0.3 +3.6 [Volt]4.2 Absolute Ratings of EnvironmentItem Symbol Min Max Unit Operating Temperature TOP -30 +85 [o C] Operation Humidity HOP 8 95 [%RH] Storage Temperature TST -30 +85 [o C] Storage Humidity HST 5 95 [%RH] Note: Maximum Wet-Bulb should be 39℃ and no condensation.5. Electrical Characteristics5.1 TFT LCD Module5.1.1 Power SpecificationSymbol Parameter Min Typ Max Units RemarkVDD Logic/LCD DriveVoltage3.0 3.3 3.6 [Volt]IDD VDD Current - 285 325 [mA] VDD=3.3V, All Black PatternI rush LCD Inrush Current - - 1.5 [A] Vin=3.3V, With Black Pattern,Rising time=500us, PDD VDD Power - 0.94 1.07 [Watt] VDD=3.3V, All Black PatternVDDrp Allowable Logic/LCDDrive Ripple Voltage - 100[mV]p-pVDDns Allowable Logic/LCDDrive Ripple Noise 100[mV]p-p5.1.2 Signal Electrical CharacteristicsInput signals shall be low or Hi-Z state when VDD is off.Note: LVDS Signal Waveform.Symbol ItemMin. Typ. Max. Unit Remark|VID | Input Differential Voltage250 350 450 [mV]VICM Differential Input Common Mode Voltage1.0 1.252.0 [V] VTH Differential Input High Threshold - - 100 [mV] VCM=1.25V VTL Differential Input Low Threshold-100 - - [mV] VCM=1.25VCLKClock frequency304050MHz5.2 Backlight Unit5.2.1 Parameter guideline for CCFLFollowing characteristics are measured under a stable condition using an inverter at 25 (Room Temperature):℃Symbol ParameterMin. T yp. Max. UnitRemark IRCFLCCFL operation range3 6 6.5 [mA] rms (T a=25oC) Note 1, 2 FCFL CCFL Frequency 40 55 60 [KHz] (T a=25o C) Note 3 ViCFL 0oC) (reference) CCFL Ignition Voltage - 930 1,120 [Volt] rms (T a= 0o C) ViCFL (25o C) (reference) CCFL Ignition Voltage -770930[Volt] rms (T a=25o C)PCFL CCFL Power consumption (inverter excluded) 3.8 6.7 7.7 [Watt] (T a=25oC) Note 4 Lamp Life50,000-Hrs(T a=25oC) Note 2 IRCFL = 6mANote 1: IRCFL is defined as the return current of an inverter. (In Figure 1)(Figure 1: Measurement of return current)A stable IRCFL is a current without flicker or biasing waveform provided by inverter that ensures the backlight perform to its specification. The ideal sine waveform should be symmetric in positive and negative polarities and the asymmetry rate of the inverter waveform should be below 10%.ReferenceDC Bias = (| Ip – I-p| / Irms ) x 100 % <10%Crest Factor = Ip or (I-p) / Irms should have the range within 1.414 + 10%It is recommended to use the inverter with detection circuit ( ie: balance and protection circuit) to avoid overvoltage, overcurrent, or mismatching waveform.Note 2: The definition of lamp life means when any of following conditions happen:a) Luminance falls to 50% or less of the initial value.b) Normal lighting is no more available (flickering, pink lighting, no lighting, etc.)c) Lamp voltage or lighting start voltage exceeds the specified value.Lamp life time shortens according toa) Placing methodology: mercury is unevenly distributed in portrait mountingb) Environmental condition: low temperature reduces the presence of mercury vapor, which results inapproximately lamp life of 1,000 hoursc) CCFL surface temperature: Presence of gradient in lamp surface temperature causes uneven mercurymigrationd) Inverter design: its resonance capacitor should be fine-tuned with the impedance of CCFLe) Over driving current ( > 6.5 mA) shortens lamp life time dramatically.Note 3: CCFL frequency should be carefully determined to avoid interference between inverter and TFT LCD. Higher frequency will induce higher leakage current and further impact lamp life.Note 4: Calculator value for reference (IRCFLxVCFLx2=PCFL).Note 5: The display is with dual lamp design, and the CCFL current in above table refers to each lamp6. Signal Characteristic 6.1 Pixel Format ImageFollowing figure shows the relationship between input signal and LCD pixel format.6.2 Scanning DirectionThe following figures show the image seen from the front view. The arrow indicates the direction of scan.Fig. 1 Normal scan (Pin19 = GND/NC)Fig. 2 Reverse scan (Pin19 = High)6.3 Signal DescriptionThe module uses a LVDS receiver embedded in AUO’s ASIC. LVDS is a differential signal technology for LCD interface and a high-speed data transfer device. Mating LVDS transmitter: THC63LVDM83A or equivalent device Pin Assignment:Pin# Signal Name Description1VCC 3.3V Power Supply2VCC 3.3V Power Supply3GND GND46-8Bit SEL Select 6 or 8 Bits LVDS Input (VCC:8Bits ; GND/NC: 6Bits)5RIN0-Negative(-) LVDS differential data input6RIN0+Positive(+) LVDS differential data input7GND GND8RIN1-Negative(-) LVDS differential data input9RIN1+Positive(+) LVDS differential data input10GND GND11RIN2-Negative(-) LVDS differential data input12RIN2+Positive(+) LVDS differential data input13GND GND14CLKIN-Clock Signal(-)15CLKIN+Clock Signal(+)16GND GND17RIN3-Negative(-) LVDS differential data input(Used for 8Bits LVDS Input; NC for 6Bits)18RIN3+Positive(+) LVDS differential data input(Used for 8Bits LVDS Input; NC for 6Bits)19REVERSE Display Reversed Function(VCC: Display Reverse; GND/NC: Normal Display)20NC/GND AUO Test Function Pin(Do not set this pin to High)Note1: Pin19 can be used for enabling “reverse scan” function.Refer to section 6.1 for scanning direction.Signal Description:Signal Name DescriptionRxIN0-, RxIN0+ LVDS differential data input (Red0-Red5, Green0)RxIN1-, RxIN1+ LVDS differential data input (Green1-Green5, Blue0-Blue1)RxIN2-, RxIN2+ LVDS differential data input (Blue2-Blue5, Hsync, Vsync, DE)CKIN-, CKIN+ LVDS differential clock inputReverse High: Reverse Display; NC/GND: Normal DisplayVDD +3.3V Power SupplyGND GroundNC No ConnectionNote: Input signals shall be low or Hi-Z state when VDD is off.LVDS Signal Format: 6/8 SEL = Low (GND)6/8 SEL = High6.4 The Input Data FormatSignal Name Description+RED5 +RED4 +RED3 +RED2 +RED1 +RED0 Red Data 5 (MSB)Red Data 4Red Data 3Red Data 2Red Data 1Red Data 0 (LSB)Red-pixel DataRed-pixel DataEach red pixel’s brightness data consists of these6 bits pixel data.+GREEN5 +GREEN4 +GREEN3 +GREEN2 +GREEN1 +GREEN0 Green Data 5 (MSB)Green Data 4Green Data 3Green Data 2Green Data 1Green Data 0 (LSB)Green-pixel DataGreen-pixel DataEach green pixel’s brightness data consists of these6 bits pixel data.+BLUE5 +BLUE4 +BLUE3 +BLUE2 +BLUE1 +BLUE0 Blue Data 5 (MSB)Blue Data 4Blue Data 3Blue Data 2Blue Data 1Blue Data 0 (LSB)Blue-pixel DataBlue-pixel DataEach blue pixel’s brightness data consists of these6 bits pixel data.CLK Data Clock The typical frequency is 40MHz. The signal isused to strobe the pixel data and DE signals.All pixel data shall be valid at the falling edge whenthe DE signal is high.DE Display Timing This signal is strobed at the falling edge of CLK.When the signal is high, the pixel data shall be validto be displayed.VSYNC Vertical Sync The signal is synchronized to CLK.HSYNC Horizontal Sync The signal is synchronized to CLK.Note: Output signals from any system shall be low or Hi-Z state when VDD is off.6.5 Interface Timing6.5.1 Timing CharacteristicsDE only modeParameter Symbol Min. Typ. Max. Unit ConditionClock frequency 1/ T Clock 33.6 39.8 48.3 MHzPeriod T V 608 628 650 Active T VD 600 600 600 Vertical SectionBlanking T VB 8 28 50 T LinePeriod T H 920 1056 1240 Active T HD 800 800 800 Horizontal SectionBlankingT HB120256440T ClockNote1: Frame rate is 60 Hz.Note2: Typical value refer to VESA Standard6.5.2 Input Timing Diagram6.6 Power ON/OFF SequenceVDD power and lamp on/off sequence is as below. Interface signals are also shown in the chart. Signals from any system shall be Hi-Z state or low level when VDD is off.VDD0V0V0VPower ON/OFF sequence timingValueUnitsParameterMin. Typ. Max.T10.5 - 10 msT2 0 - 50 msT3 0 - 50 msT4 0 - 10 msT5 200 - msT6 200 - msT7 500 - - MsThe above on/off sequence should be applied to avoid abnormal function in the display. Please make sure to turn off the power when you plug the cable into the input connector or pull the cable out of the connector.7. Connector & Pin AssignmentPhysical interface is described as for the connector on module. These connectors are capable of accommodating the following signals and will be following components.7.1 TFT LCD Module: LVDS ConnectorConnector Name / Designation Signal ConnectorManufacturer STMConnector Model Number MSB240420-EMating Model Number P240420 or compatibleMating LVDS transmitter: THC63LVDM83A or equivalent device7.2 Backlight Unit: Lamp ConnectorConnector Name / Designation Lamp ConnectorManufacturer JSTConnector Model Number JST BHR-03VS-1 or compatibleMating Model Number JST SM03(4.0)B-BHS-1-TBPin no. Symbol Function Remark1 H CCFL power supply (H.V.) Cable color: Pink2 NC No connection3 L CCFL power supply (GND) Cable color: White8. Reliability Test CriteriaItems Required Condition Note High TemperatureOperation 85, 240Hrs℃ (center point of panel surface) Note 1, 2, 3 Low TemperatureOperation -30, 240Hrs℃Note 1, 2, 3 Hot Storage 85, 240Hrs℃Note 1, 2, 3 Cold Storage -30, 240Hrs℃Note 1, 2, 3High temperature & high humidity operation 50, 90%RH, 240Hrs℃(No condensation)Note 1, 2, 3Shock Test(Non-Operating) 50G/11ms, ±X, ±Y, ±Z, half-Sin, one time Note 1, 2, 3Vibration Test (Non-Operating) 1.5G, random 10H Z ~ 200H Z ~ 10H Z30 minutes for each Axis (X, Y, Z), 15min/SweepNote 1, 2, 3On/off test On 10sec/OFF 10 sec, 30,000 cycles Note 1, 2, 3 Contact Discharge: Max±8KV, 150pF(330Ω) 1sec, 8 points, 25times/point.ESDAir Discharge: Max ±15KV, 150pF(330Ω) 1sec, 8 points, 25times/pointNote 3, 4Thermal shock (non-operation) 1. -20±3…30minutes℃℃60±3…30minutes℃℃2. 100 cycles3. T emperature transition time within 5 minutesNote 1, 2, 3Attitude Test Operation:14,000ft / 8hrsNon-Operation: 40,000ft / 24hrsNote 3Note 1: Evaluation should be tested after storage at room temperature for one hour.Note 2: There should be no change which might affect the practical display function when the display quality test is conducted under normal operating condition.Note 3: Judgment: 1. Function OK 2. No serious image quality degradationNote 4: According to EN61000-4-2 , ESD class B: Some performance degradation allowed. No data lost, self-recoverable. No hardware failures.9.3 Screw Hole Depth and Center PositionScrew type: M3 screwScrew hole minimum depth, from side surface =2.7mm (See drawing) The Max. Diameter of the mounting screw head is 6.0mmScrew Torque: Maximum 6.0 kgf-cm10. Label and Packaging10.1 Shipping Label (on the rear side of TFT-LCD display)10.2 Carton PackageMax capacity: 20 TFT-LCD modules per carton.Max weight: 17 kg per cartonOutside dimension of carton: 576(L) mm x 326(L) mm x 420(H) mm11. Safety11.1 Sharp Edge RequirementsThere will be no sharp edges or comers on the display assembly that could cause injury.11.2 MaterialsToxicityThere will be no carcinogenic materials used anywhere in the display module. If toxic materials are used, they will be reviewed and approved by the responsible AUO toxicologist.11.3 CapacitorsIf any polarized capacitors are used in the display assembly, provisions will be made to keep them from being inserted backwards.11.4 National Test Lab RequirementThe display module will satisfy all requirements for compliance to:UL 60950 U.S.A. Information Technology Equipment。
CC1310 Skyworks 433MHz PA参考设计说明书

Application ReportSWRA528–May2017 CC1310Skyworks433MHz PA Reference Design Albin Zhang and Richard WallaceABSTRACTThe frequency range426MHz-435MHz is designated for ISM applications in several countries.This frequency range is commonly known as the433MHz band.Each country has their specific frequency band range and the China ISM band defined by SRRC is430MHz-432MHz and433.00MHz-434.79 MHz.CC1310reference design[8]operates from420MHz to510MHz with15dBm output power.If higher output power is required in the433MHz band,TI provides a reference design[3]with Skyworks Solutions.The combination of CC1310wireless MCU[2]and SKY66115-11FEM[4],addresses customers’needs for easy-to-use,long-range,low-power and low-cost solutions serving applications across the Internet of Things(IoT).The reference design covered in this application report can support up to+20dBm TX power with high power efficiency at433MHz.Contents1Introduction (2)2Design (2)3Measurement Results (8)4Summary (11)5References (11)List of Figures1CC1310EM-SKY66115-4051Board (2)2CC1310Block Diagram (3)3Schematic-CC1310EM-SKY66115-4051Rev2_0_x (4)4CC1310EM-SKY66115-4051Layout (5)5DIO Configuration in SmartRF Studio7 (6)6Tx Mode Configuration (7)7Rx mode configuration (8)8Matching of the Antenna With ANT1and ANT2Components (10)9Antenna Bandwidth at VSWR:2 (10)List of Tables1SKY66115-11Truth Table (6)2Conducted Output Power and Harmonics,3.3V (8)3TX Output Power,Current Consumption vs.Power Table,3.3V (9)TrademarksSmartRF is a trademark of Texas Instruments.Cortex is a registered trademark of ARM Limited.Introduction 2SWRA528–May 2017CC1310Skyworks 433MHz PA Reference Design1IntroductionThe design covered in this application note is based on the CC1310from the CC13xx family.It provides a range extension solution with the FEM from Skyworks (SKY66115-11)and a compact on-board helical PCB antenna.Figure 1310EM-SKY66115-4051Board2DesignWhen designing a wireless system,the maximum range between the transmitter and receiver is one of the most important parameters that will dominate the system configuration and installation.In the AMR system,the range is critical so that all households’meters can be read otherwise this must be done manually or adding more concentrators,which is expensive.To achieve a long range the output power can be increased to the maximum limit specified by the regulations and the data rate reduced as much as possible for the application.One of the efficient approaches to increase range is to increase the TX power.2.1CC1310The CC1310has been specifically designed for long range,city-wide low power networks.This is used in home automation,building automation and outdoor wide-area networks.The main advantages of CC1310are high sensitivity (-124dBm with a 0.625kbps data rate),strong co-existence (up to 80dB blocking),lowest power consumption (61µA /MHz ARM Cortex M3).CC1310can be basically split into four low-power sections as shown in Figure 2:•Main CPU with Cortex ®-M3•RF Core with radio controller.The RF core is a highly flexible and capable radio system that interfaces the analog RF and base-band circuits,handles data to and from the system side,and assembles the information bits in a given packet structure. Design •General Peripherals•Sensor ControllerFor more in-depth information on the CC1310,see the CC1310SimpleLink™Ultra-Low-Power Sub-1GHz Wireless MCU Data Sheet(SWRS181).1310Block Diagram2.2SchematicThe RF core of CC1310is highly configurable and the radio front-end can be set to differential or single ended.With a differential output configuration,the maximum output is14dBm.With a single endedoutput,the maximum output is11dBm.Several customers have requested an output power up to20dBm, the CC1310transmitter was configured as a single ended port(RF_P set to Tx)connected to an external FEM with an integrated amplifier,see Figure3.If an output power of14dBm is sufficient then thestandard reference design for420MHz to510MHz can be used[8].The schematic shown in Figure3is a general schematic(Rev2.0.x)to cover the ISM frequency bands from400MHz to510MHz;the BOM is specified for three different ISM frequency bands:•470MHz–510MHz:BOM-CC1310EM-SKY66115-4051Rev2.0.1•420MHz–440MHz:BOM-CC1310EM-SKY66115-4051Rev2.0.2•400MHz–420MHz:BOM-CC1310EM-SKY66115-4051Rev2.0.3Design 4SWRA528–May 2017CC1310Skyworks 433MHz PA Reference DesignThe FEM used is from Skyworks (SKY66115-11).The SKY66115-11consists of an amplifier and a switch contained in the package.It also includes a shutdown mode to minimize power consumption.The transmit path contains an amplifier optimized for saturated performance.SKY66115-11is internally matched for CC1310,which enables optimum transmit output power and efficiency for 50Ωload impedance.The transmit path passes through a low-pass filter before being entering to one side of the SPDT switch.The receive path has a bypass function from the other side of the SPDT switch.The reference design [3]shown in Figure 3is based upon 3.3V supply voltage.Two RF output options are available.Mounting C72,the RF path is routed to the RF connector (J1)that allows an externalantenna or conductive RF testing.Mounting C63,connects the compact PCB antenna.ANT1,ANT2and ANT3compose of the antenna matching circuit.A low-pass filter (C484,C485,C486and L332)is incorporated on the ANT port to provide additional filtering and/or limit unwanted signals from entering the receive path.CC1310can support several RF port options,described in the wiki page [7].For better Rx sensitivity,the reference design adopts a single-end,external-bias RF front-end design.L1is used for the external bias circuit.C11,L11and L12compose a matching circuit to optimize the RX sensitivity.The reference design [3]utilizes noise decoupling on the power and control lines of the SKY66115-11.Figure 3.Schematic -CC1310EM-SKY66115-4051Rev2_0_x Design 2.3LayoutThe design[3]is based on a0.8mm thick,two-layer PCB.The top layer and bottom layer are shown in Figure4.All components are positioned on the top layer apart from the evaluation module(EM)connectors.The CC1310EM-SKY66115-4051is based upon the7x7QFN package.The RF frond-end design can be re-used for5x5QFN and4x4QFN packages.A PCB helical antenna is incorporated in the EM design.The antenna is routed on both the top andbottom layers.It is important to incorporate the matching components(ANT1,ANT2and ANT3)as well if the antenna structure is to be copied to another design.Changing the PCB thickness will change theresonance of the antenna and this would require new antenna matching values for ANT1and ANT2(ANT3:DNM).1310EM-SKY66115-4051LayoutThe top view is shown on the left side;the bottom view is shown on the right side.Design 6SWRA528–May 2017CC1310Skyworks 433MHz PA Reference Design2.4SmartRF™StudioTo evaluate the reference design it is recommended to use the EM on the SmartRF06EB with SmartRF Studio software.The supported functions are continuously being updated and the software can be downloaded [6].With SmartRF studio 7(version 2.4.3),new features have been added to support 433MHz –510MHz reference designs.•Default recommended setting on 430-510MHz band.•DIOs configuration based on the truth table of the FEM.•RF front-end mode configuration.For more information on SmartRF Studio7,see /tool/smartrftm-studio .Figure 5,Figure 6and Figure 7illustrate how to configure the CC1310EM-SKY66115-4051board.2.4.1DIO ConfigurationBased on the truth table of the SKY66115-11shown in Table 1,SmartRF Studio should have the DIO configured as shown in Figure 5.Table 1.SKY66115-11Truth TableDIO_1(CTX):LOW &DIO_30(CSD):HIGH ---->Rx DIO_1(CTX):HIGH &DIO_30(CSD):HIGH ---->Tx DIO_1(CTX):X &DIO_30(CSD):LOW ---->SleepFigure 5.DIO Configuration in SmartRF Studio 7 Design 2.4.2RF Front-End ConfigurationFigure6and Figure7show the configuration of Tx and Rx modes separately.This is configured in the CMD_PROP_RADIO_DIV_SE radio operation commands.For the Tx path configuration shown in Figure6,RF_P is set to single-end option.The txpowerparameters should also be configured based on Table3.For the Rx path shown in Figure7,RF_N is set to single-end option.Figure6.Tx Mode ConfigurationMeasurement Results 8SWRA528–May 2017CC1310Skyworks 433MHz PA Reference DesignFigure 7.Rx mode configuration3Measurement ResultsAll measurements results were performed on the CC1310EM-SKY66115-4051at 433MHz (BOM Rev 2.0.2)EM mounted on the SmartRF06EB.Software control is based on SmartRF Studio 2.4.3.3.1Tx Output Power and HarmonicsThe output power was measured at 433.92MHz.The harmonics were measured up to the 10th harmonic.The txpower register is set to 0x1CC7.Table 2.Conducted Output Power and Harmonics,3.3VHamonics fc 2fc 3fc 4fc 5fc 6fc 7fc 8fc 9fc 10fc Frequency (MHz)433.92867.841301.761735.682169.62603.523037.443471.363905.284339.2Level (dBm)20.5-37-49-55-55-55-55-55-55-55 Measurement Results 3.2Tx Output Power Dynamic Range and Current ConsumptionOutput power and current consumption were measured across the power table at433.92MHz.Theaverage results are shown in Table3.In the CMD_PROP_RADIO_DIV_SETUP,the power can be configured in the txpower register,which is shown in Figure6.Table3.TX Output Power,Current Consumption vs.Power Table,3.3VPower Table0x08C00x00410x10C30x10430x14C40x18C50x18C60x1CC7Output power12.316.31818.919.319.619.820dBm 5262.871.475.978.179.781.682.4mA CurrentconsumptionThe SKY66115-11maximum input power rating on the PIN_TX is limited 1310should limit the TX Power control IB bit of txpower register below0x07.3.3Rx Current ConsumptionThe static Rx current consumption was measured at6.3mA with3.3V power supply.3.4SensitivityThe sensitivity was measured with50kbps datarate setting on CC1310EM-SKY66115-4051at433MHz (BOM Rev2.0.2)to-106.4dBm during normal temperature and3.3V power supply.If the data rate is reduced from50kbps and Long Range Mode utilized,then the following sensitivitylevels can be achieved on the on CC1310EM-SKY66115-4051at433MHz(BOM Rev2.0.2)Ref Design:●5kbps sensitivity:-117dBm● 2.5kbps sensitivity:-119dBm● 1.25kbps sensitivity:-120dBm●0.625kbps sensitivity:-121dBm3.5Antenna DesignThe PCB helical antenna shown in Figure4has been matched to433.92MHz with ANT1:6.8pF and ANT2:91nH.For more information,see Figure8.The antenna is matched for the complete band of470 MHz–510MHz.For more information,see Figure8and Figure9.This antenna design,matching tuning and testing results are based on the CC1310EM-SKY66115-4051 board at433MHz(BOM Rev2.0.2)plugging on the SmartRF06EB board with the free spaceenvironment.In antenna design theory,some of the nearby materials will impact the antennaperformances,for example,grounded conductor,plastic/rubber cases,and so forth.For a realistic product antenna design,it is necessary to consider the mechanical case impacts and do proper tuning.Measurement Results 10SWRA528–May 2017CC1310Skyworks 433MHz PA Reference DesignFigure 8.Matching of the Antenna With ANT1and ANT2ComponentsFigure 9.Antenna Bandwidth at VSWR:2 Summary 11SWRA528–May 2017Submit Documentation Feedback Copyright ©2017,Texas Instruments Incorporated CC1310Skyworks 433MHz PA Reference Design 4SummaryThe CC1310EM-SKY66115-4051reference design at 433MHz (BOM Rev 2.0.2)is a low cost,easy-to-use,high efficiency solution with 20dBm output power for 3.3V supply.Tx current consumption at 20dBm is approximately 82mA.The antenna is also integrated into the PCB that provides a compact,costless antenna solution.5References1.Achieving Optimum Radio Range (SWRA479)2.CC1310SimpleLink™Ultra-Low-Power Sub-1GHz Wireless MCU Data Sheet (SWRS181)3.CC1310EM-SKY66115-4051Reference Design (Rev:2.0.x)(SWRC334)4.SKY66115-11Data Sheet 5.Antenna Quick Guide (SWRA351)6.SmartRF Studio Download 7.CC1310Front-end Configurations Wiki page 13xxEM-7XD-4251Rev1_1_1IMPORTANT NOTICE FOR TI DESIGN INFORMATION AND RESOURCESTexas Instruments Incorporated(‘TI”)technical,application or other design advice,services or information,including,but not limited to, reference designs and materials relating to evaluation modules,(collectively,“TI Resources”)are intended to assist designers who are developing applications that incorporate TI products;by downloading,accessing or using any particular TI Resource in any way,you (individually or,if you are acting on behalf of a company,your company)agree to use it solely for this purpose and subject to the terms of this Notice.TI’s provision of TI Resources does not expand or otherwise alter TI’s applicable published warranties or warranty disclaimers for TI products,and no additional obligations or liabilities arise from TI providing such TI Resources.TI reserves the right to make corrections, enhancements,improvements and other changes to its TI Resources.You understand and agree that you remain responsible for using your independent analysis,evaluation and judgment in designing your applications and that you have full and exclusive responsibility to assure the safety of your applications and compliance of your applications (and of all TI products used in or for your applications)with all applicable regulations,laws and other applicable requirements.You represent that,with respect to your applications,you have all the necessary expertise to create and implement safeguards that(1) anticipate dangerous consequences of failures,(2)monitor failures and their consequences,and(3)lessen the likelihood of failures that might cause harm and take appropriate actions.You agree that prior to using or distributing any applications that include TI products,you will thoroughly test such applications and the functionality of such TI products as used in such applications.TI has not conducted any testing other than that specifically described in the published documentation for a particular TI Resource.You are authorized to use,copy and modify any individual TI Resource only in connection with the development of applications that include the TI product(s)identified in such TI Resource.NO OTHER LICENSE,EXPRESS OR IMPLIED,BY ESTOPPEL OR OTHERWISE TO ANY OTHER TI INTELLECTUAL PROPERTY RIGHT,AND NO LICENSE TO ANY TECHNOLOGY OR INTELLECTUAL PROPERTY RIGHT OF TI OR ANY THIRD PARTY IS GRANTED HEREIN,including but not limited to any patent right,copyright,mask work right,or other intellectual property right relating to any combination,machine,or process in which TI products or services are rmation regarding or referencing third-party products or services does not constitute a license to use such products or services,or a warranty or endorsement e of TI Resources may require a license from a third party under the patents or other intellectual property of the third party,or a license from TI under the patents or other intellectual property of TI.TI RESOURCES ARE PROVIDED“AS IS”AND WITH ALL FAULTS.TI DISCLAIMS ALL OTHER WARRANTIES OR REPRESENTATIONS,EXPRESS OR IMPLIED,REGARDING TI RESOURCES OR USE THEREOF,INCLUDING BUT NOT LIMITED TO ACCURACY OR COMPLETENESS,TITLE,ANY EPIDEMIC FAILURE WARRANTY AND ANY IMPLIED WARRANTIES OF MERCHANTABILITY,FITNESS FOR A PARTICULAR PURPOSE,AND NON-INFRINGEMENT OF ANY THIRD PARTY INTELLECTUAL PROPERTY RIGHTS.TI SHALL NOT BE LIABLE FOR AND SHALL NOT DEFEND OR INDEMNIFY YOU AGAINST ANY CLAIM,INCLUDING BUT NOT LIMITED TO ANY INFRINGEMENT CLAIM THAT RELATES TO OR IS BASED ON ANY COMBINATION OF PRODUCTS EVEN IF DESCRIBED IN TI RESOURCES OR OTHERWISE.IN NO EVENT SHALL TI BE LIABLE FOR ANY ACTUAL,DIRECT,SPECIAL, COLLATERAL,INDIRECT,PUNITIVE,INCIDENTAL,CONSEQUENTIAL OR EXEMPLARY DAMAGES IN CONNECTION WITH OR ARISING OUT OF TI RESOURCES OR USE THEREOF,AND REGARDLESS OF WHETHER TI HAS BEEN ADVISED OF THE POSSIBILITY OF SUCH DAMAGES.You agree to fully indemnify TI and its representatives against any damages,costs,losses,and/or liabilities arising out of your non-compliance with the terms and provisions of this Notice.This Notice applies to TI Resources.Additional terms apply to the use and purchase of certain types of materials,TI products and services. These include;without limitation,TI’s standard terms for semiconductor products /sc/docs/stdterms.htm),evaluation modules,and samples(/sc/docs/sampterms.htm).Mailing Address:Texas Instruments,Post Office Box655303,Dallas,Texas75265Copyright©2017,Texas Instruments Incorporated。
IOS-MAT-0066-10

Issued bySignatureAuthorised bySignature Replaces:Björn Johansson and Stellan GrönbergProduct Requirements & Compliance/Product Laws & StandardsPär Stenmark Manager Product Requirements & Compliance/IKEA of SwedenAA-163938-9Surface coatings and coverings – general requirementsContentsThis specification describes IKEA requirements on surface coatings and coverings, solvents and thinners used to treat surfaces before and after coating/covering the products as well as surface cleaning, metal surface treatment and stainless steel surfaces, in respect of chemical content, physical properties, visual qualities, and documentation. The specification is valid for application of surface coatings and coverings (see section 6 Definitions ) to all substrates except the following:•Coating on leather• Printing and coating on textiles• Non-film-forming printing on paper and cardboard other than foil/covering (whereas film-forming printing on paper is included in the IOS-MAT-0066; and printing/coating on foil covering is also included in IOS-MAT 0066, as part of the covering).• Coatings applied to paper during the production process of paper. This coating is considered as part of the paper and included within the scope of IOS-MAT-0010. • Ceramic glazes • Enamel on metal• Inorganic decorations which are fused into/onto glass, enamel, or ceramic glazes• Glue-based filler used for spot application (e.g. white glue with saw dust, or hotmelt glue) • Mirror paint that is in the scope of IOS-MAT-0088• Coatings on zip fasteners that are in the scope of IOS-PRG-0029 • Bed slats coated with glue in the scope of IOS-MAT-0109 • Labels that are in the scope of IOS-PRG-0019• Plastic film applied on paper (this is in the scope of IOS-MAT-0010)About this specificationThis specification addresses IKEA suppliers as well as their surface coating and coveringsuppliers. The purpose of this specification is to describe IKEA requirements concerning surface coatings and coverings in order to:• Minimise harmful effects to environment and health from IKEA articles.• Ensure compliance of IKEA articles with health and environment regulations in all IKEA markets.• Ensure the quality of surfaces on IKEA articles, such as surface resistance, surface appearance, correct colour and gloss, and good workmanship. This document is connected to IOS-TM-0002 Surface resistance – test methods.All references to standards and legislations shall be seen as referring to the latest updated version, unless otherwise stated.Implementation of changesChanges in this specification, version no AA-163938-10, shall be implemented in production at the latest from packaging date stamp 1619 (year 2016 week 19).Products having a packaging date stamp earlier than specified above shall be shipped to IKEA before shipping products compliant with this version of the specification.Signing of the self declaration by the coating/covering supplier means that all their materials delivered after signature date comply with all applicable requirements in IOS-MAT-0066 version 10 (AA-163938-10) – regardless of the specification’s latest implementation date for the IKEA supplier of the changed requirements.Renewal of verification documentationSigning of the self declaration by the coating/covering supplier means that all their materials delivered after signature date comply with all applicable requirements in IOS-MAT-0066 version 10 (AA-163938-10) – regardless of the specification’s latest implementation date stamp for the changed requirements in the IKEA sales article.Changes to regulations and lists referred to in this documentWhen new substances are added to lists of substances (in laws, in standards or by authorities), or classified according to classifications, which are referred to in this specification, the requirements for these substances shall be fulfilled within four months after the substance has been added to the cited list, unless otherwise specified by IKEA.Annual self declarations do not need extra renewal in case new substances are added to the lists of banned substances, unless otherwise stated.Table of contents1Chemical requirements (4)1.1Surface coatings and coverings – requirements for all substrates (4)1.1.1Additional requirements specifically for powder coatings – all substrates (10)1.1.2Additional requirements specifically for UV coatings – all substrates (11)1.2Additional requirements for surface coatings and coverings for solid wood, wood-based materials, and wood-like natural materials (12)1.2.1Additional requirements specifically for UV coatings (14)1.3Additional requirements for surface coatings and treatments for metal substrates (15)1.4Additional requirements for surface coatings for polymeric substrates (16)1.5Additional requirements for surface coatings for glass (16)2Physical properties (16)2.1Surface resistance (16)2.1.1Applicability of surface resistance requirements tables 2.1.A to 2.1.K (16)2.1.2Verifying tests of surface resistance (16)2.1.3Surface resistance requirements (17)2.1.4Scope of surface resistance tables regarding wood-like natural materials (21)2.2Surface coating/covering adhesion (21)2.3Coating blocking and stickiness (21)3Visual requirements (22)3.1Colours (22)3.1.1Colour samples (22)3.1.2Approval of colour and tolerances (22)3.2Gloss (23)3.3Surface appearance and defects in coating film/finish (23)3.4Fingerprints (23)3.5Textured paints (23)4Metal surfaces – coatings and stainless steel (24)4.1Service conditions (24)4.1.1Requirements (25)4.2Corrosion requirements and test methods (26)4.2.1Neutral salt spray test (26)4.2.2Acetic acid salt spray test (26)4.2.3Dip test (26)4.2.4Minimum thickness (28)4.2.5Stainless steel – grinding and polishing requirements (28)4.2.6Use of polishing and finishing compounds (28)4.3Corrosion and coating thickness test frequency (30)5Documentation (30)5.1Verifying tests (30)5.2Sample information (30)5.2.1Test to verify the chemical content (30)5.2.2Test to verify the physical properties (31)5.2.3Test to verify the corrosion on metal surfaces (31)5.3Requirements on test reports and self declarations (31)5.4Safety Data Sheets (SDS) and Technical Data Sheets (TDS) (31)5.5Self declarations (32)5.5.1Inorganic coatings (32)5.5.2Water-based degreasing, iron phosphating and electrolytic zinc plating (32)5.5.3UV coatings (32)5.5.4Solvents used for cleaning (32)5.6Documentation exception (32)5.7Certificate of Compliance of CPSA/CPSIA (33)5.8Warning limits (investigation limits) as a support for compliance (33)6Definitions (34)Appendix A: List of allowed biocides used as preservatives during storage (41)Appendix B: Test methods for surface resistance – deviations and comments (42)Appendix C: Surface coating/covering declaration of chemical substances by surface coating/covering supplier (43)Appendix D: Lead test requirement according to 16 CFR, Part 1303 (USA) (48)Appendix E: Polishing and finishing compounds for metal substrates declaration of chemical substances by polishing and finishing supplier (51)References (53)Summary of Changes in version 10 (55)1Chemical requirementsWhen choosing surface coating and covering materials, and production processes, the aim shall be to select an alternative which minimises any harmful effects to health and environment:•In the raw material•During the production process•During use of the article•When the article becomes wastePrior to packing, the finished surface shall be cured and well ventilated. Requirements on emissions and odour from the final product are stated in IOS-MAT-0010 Chemical compounds and substances.The IKEA supplier is responsible that only surface coating and covering components and systems, which are guaranteed by the coating/covering supplier to fulfil the requirements listed below on content of chemical substances, are used in the production of IKEA products.The IKEA supplier is also responsible to secure that there is no contamination of the surface coating/covering leading to non-compliance with the IKEA chemical requirements in this specification.Note: Solvent for cleaning/degreasing includes solvents used before and after the application ofa surface coating/covering, as well as on surfaces that are not coated/covered.1.1Surface coatings and coverings – requirements for all substrates Table 1.1 Surface coatings and coverings – general requirementsSurface coating/ covering Substance Requirements Test method MinimumDocumentRequirementLiquid coatings •Alkylphenolethoxylates(APEO)•Alkylphenols(AP)•AlkylphenolphosphitesNot allowed to be used.Contamination limit value: 0.10 % in theready-to-use mixture.Extraction(methanol +ammoniumacetate) +HPLC anddetection byMS DADSelfdeclaration(SD)Table 1.1 Surface coatings and coverings – general requirementsSurface coating/ covering Substance Requirements Test method MinimumDocumentRequirementLiquid coatings Biocides of allkindsAddition of biocides used as preservativesfor products during storage (=in-canpreservatives) is only allowed according tothe list of allowed biocides in Appendix A.The concentration of individual biocides, orof mixtures of biocides as parts of aweighted sum (see Appendix A forexplanation), shall not exceed the limits inAppendix A.Addition of biocides used for any otherpurpose is not allowed, unless otherwisestated in the product documentation(Biocides used as film and woodpreservatives are included in IOS-MAT-0098).Addition of biocides is also allowed afterpermission from IKEA. Permission is neededfor all biocides not listed in Appendix A. SeeTable C1 in Appendix C.Apart from the above, biocides used aspreservatives for products during storagebut not in Appendix A and coming fromcoating ingredients that are used at aconcentration of maximum2 % of the final coating component can beused, as long as they are not CMR and theirsum concentration is not above5 ppm (0.0005 %) in the final surfacecoating component.Screeningtest. Differentextraction andanalysismethodsdepending onwhich mate-rials and sub-stances to betested.SDTable 1.1 Surface coatings and coverings – general requirementsSurfacecoating/coveringSubstance Requirements Test method MinimumDocumentRequirement All types ofsurfacecoatings/coverings,thinners,and pre-treatmentCMRsubstancescategory 1Aand 1B andSubstances ofVery HighConcern(SVHC)CMR substances category 1A and 1B andSVHC are not allowed to be used.Contamination limit value: 0.10 %For coatings, this contamination limit valueis valid for each separate coatingcomponent.Some examples of CMR substances that arenot allowed:•N-methyl-2-pyrrolidone (NMP)(CAS no: 872-50-4)•2-ethoxy-ethanol (ethyl glycol) (CASno: 110-80-5)•2-ethoxy ethylacetate (ethyl glycolacetate) (CAS no: 111-15-9)•Dimethylformamide (DMFA, DMFO)(CAS no: 68-12-2)•2-methoxy ethanol (Ethylene glycolmonomethyl ether, EGME) (CAS no:109-86-4)•2-methoxy ethylacetate (methyl glycolacetate EGMEA) (CAS no: 110-49-6)Note: The following CMR substances areallowed to be used in the followingprocesses:•Inorganic nickel compounds and boricacid/borates used in electrochemicalplating baths•Inorganic nickel compounds used whenanodizing•Inorganic cobalt compounds used inbath for post-treatment after electrolyticzinc plating•Formaldehyde – only according tosection 1.2, 1.3 and 1.5.Screeningtest. Differentextraction andanalysismethodsdepending onwhichmaterials andsubstances tobe tested.SDSurfacecoveringsElementalchlorinebleachingPulp that has been bleached with elementalchlorine is not allowed to be used in themanufacturing of supporting paper.-- SDAll types ofsurfacecoatings/covering,thinners,and pre-treatmentFragrances Fragrances, perfumes and masking agentsare not allowed to be used withoutapproval from IKEA.-- SDTable 1.1 Surface coatings and coverings – general requirementsSurface coating/ covering Substance Requirements Test method MinimumDocumentRequirementLiquid coatings, and coverings Organotin(tinorganic)compoundsNo kind of organotin compounds areallowed to be used.Contamination limit value for sum of allorganotin compounds:2.5 mg/kg dry surface material.The limit values refer to the alkyl/aryl tincation without the counter ion.Note: test requirement refers to organotinslisted in the definition of organotincompounds.Exception: In polyurethane coatings onglass, dibutyltin dilaurate (DBTL, CAS no:77-58-7) including monoalkyltin compoundsare allowed to be used as catalyst at amaximum concentration of 0.05% totalorganotin in the ready-to-use mixture.Extraction andGC-MSFor EDcoating: SDand Testreport (TR)For allothers: SDAll types of surface coatings/ coverings Phthalates The following phthalates are not allowed tobe used:•phthalates defined as CMR substancescat 1A or 1B•phthalates that are SVHC•phthalates listed on theState of California“Proposition 65” list•di-n-octyl phthalate, DNOP(CAS no. 117-84-0)Contamination limit value: 500mg/kg forsum of all phthalates. For coatings, thislimit is valid both in the solid content of theready-to-use mixture and in the dry surfacematerial.Note: For information purposes, IKEA willaim to keep an updated list on IKEASupplier Portal of phthalates that areclassified as CMR or SVHC by the EuropeanUnion or that are on the CalifornianProposition 65 list, and thus in the scope ofthis requirement.Extraction andGC-MSSDSurface coatings and coverings PVC (Polyvinylchloride)Not allowed to be used -- SDTable 1.1 Surface coatings and coverings – general requirementsSurface coating/ covering Substance Requirements Test method MinimumDocumentRequirementIsocyanate -containing liquid coatings TDI and HDImonomersMonomer levels of:•TDI (toluene diisocyanate, CAS no:26471-62-5)•HDI (hexamethylene diisocyanate,(CAS no: 822-06-0)In isocyanate-containing liquid coatings andhardeners (prepolymer solution) shall beless than 0.5 % by weight for the sum ofthese diisocyanates monomers in eachcoating component.In 1-component PU systems, the sum ofthese diisocyanates monomers shall be lessthan 0.25 % by weight in the ready-to-usemixture.LC-MS/MS SDOil Waste oil Not allowed to be used -- SD Heavy metal content in coatings and coveringsAll types of surface coatings/ coverings Cadmium (Cd)and itscompoundsNot allowed to be used.Contamination limit value:40 mg Cd/kg dry surface material.Total digestionfollowed byAAS or ICPSDAll types of surface coatings Lead (Pb) andits compoundsNot allowed to be used.Contamination limit value:90 mg Pb/kg dry surface material.Total digestionfollowed byAAS or ICP incompliancewith 16 CFRPart 1303(CPSC – CH-E1003) (USA)SD and TR1for solidfilms infurniturearticles inthe scope of16 CFR, Part1303 (USA),seeAppendix D2, 3SD for allothersurfacecoatings.All types of surface coverings Lead (Pb) andits compoundsNot allowed to be used.Contamination limit value:90 mg Pb/kg dry surface material.Total digestionfollowed byAAS or ICPSDNote: For the purpose of lead testing in accordance with 16 CFR, part 1303, surface coatings applied on coverings are considered as a surface coating, and lead requirements on surface coating as above applies, see Table 1.1. Lead (Pb) and its compounds.1 The TR may be replaced by tests of lead by the coating supplier in coating products that are identical in all material respects to those used in production of the furniture article, see Appendix D. Test reports from these tests of lead in coating products shall be handed over by the coating supplier to the IKEA supplier for registration in the IKEA Connect database, see section 5.2 This requirement is valid regardless of whether a furniture article, as defined in Appendix D, is delivered to the USA or not.3 The content of other heavy metals that are analysed in the same test (on dry surface coating from the final article) shall also be reported in the test report.Table 1.1 Surface coatings and coverings – general requirementsSurface coating/ covering Substance Requirements Test method MinimumDocumentRequirementAll types of surface coatings/ coverings Mercury (Hg)and itscompoundsNot allowed to be used.Contamination limit value:10 mg Hg/kg dry surface material.Total mercurycontent bymicro-wavedigestion andcold vapourAASSDAll types of surface coatings/ coverings Migration ofheavy metalsincluding theircompounds(Sb, As, Ba,Cd, Cr, Pb,Hg, Se)Surface coating films and covering systemson all products shall not exceed limits forheavy metal migration. For limits, see EN71-3:1994/A1:2000.EN 71-3:1994/A1:2000SDSolvent compositionLiquid coatings, pre-treatment, thinners, and solvents for cleaning/ degreasing AromatichydrocarbonsolventsThe content of total aromatic hydrocarbonsolvents shall be less than 1.0 % by weightin the liquid fraction of each surface coatingcomponent.Examples:•Toluene (CAS no: 108-88-3)•Xylene (CAS no (group): 1330-20-7)•Ethylbenzene(CAS no: 100-41-4)•Styrene (CAS no: 100-42-5)•Trimethylbenzenes and higher aromatichydrocarbonsFurthermore, benzene-containing solventsare not allowed to be used. Contaminationlimit value in the solvent: 0.10 % benzene(CAS no: 71-43-2) of each surface coatingcomponent.ISO 11890-2 SDLiquid coatings, pre-treatment, thinners, and solvents for cleaning/ degreasing ChlorinatedhydrocarbonsolventsUse of chlorinated hydrocarbon solvents isnot allowed.Contamination limit value: 0.10 % for thesum of all chlorinated hydrocarbons in theliquid fraction of each surface coatingcomponent.Examples:•Methylene chloride(CAS no: 75-09-2)•Chloroform (CAS no: 67-66-3)•Perchloroethylene(CAS no: 127-18-4)•Trichloroethylene(CAS no: 79-01-6)•1,1,1-trichloroethane(CAS no: 71-55-6)Headspacegas chromato-graphy withelectroncapturedetection(HSGC-ECD)SD1.1.1 Additional requirements specifically for powder coatings – all substratesNote : these requirements are in addition to the requirements in Table 1.1Table 1.1.1 Additional requirements specifically for powder coatings – all substrates Substance RequirementsTest method MinimumDocumentation requirementDi-organotin and tri-organotin compoundsTri-organotins are not allowed to be used. Contamination limit value: 1 mg/kg for sum of tri-organotin compounds in the dry surface material.Di-organotin compounds are allowed to be used, but the sum of di-organotin and tri-organotin compounds shall not be more than 2.5 mg/kg in the dry surface material. Note: All tri-organotin compounds arebanned, and all di-organotins are restricted to the sum limit of 2.5 mg/kg, but the minimum test demand only includes those tri- and di-organotins that are listed in the definition of organotin compounds.The limit values refer to the alkyl/aryl tin cation without the counter ion.Extraction and GC-MSSD and TRTGIC(Triglycidyl isocyanurate)Powder coatings shall not contain any addition of TGIC hardener (CAS no: 2451-62-9). This cross-linking agent is primarily used in polyester-based powder coatings.Contamination limit value 0.10 % by weight in the ready-to-use powder coating.-- SD1.1.2Additional requirements specifically for UV coatings – all substrates Note: these requirements are in addition to the requirements in Table 1.1Table 1.1.2 UV coatings including UV printing inks – general requirements all substratesSubstance Requirements Test method MinimumdocumentationrequirementStenomeric acrylates It is not allowed to use any stenomeric acrylate,including acrylic acid (CAS no: 79-10-7), that isclassified as:Tox. 1-4, STOT SE 1&2, STOT RE 1&2 or Asp.Tox. 1 according to Regulation (EC) No1272/2008 (the CLP regulation) according toeither of the following:•harmonised classification according to AnnexVI in the CLP regulation•the classifications made within the PARADconsortium (see PARAD consortium report onUV/EB acrylates)Contamination limit value: 1.0 % by weight inthe ready-to-use mixture for the sum of suchstenomeric acrylates.Extraction andGC-MSSDToxic coating ingredients Coating ingredients classified as Acute Tox. 1-3,STOT SE 1 or STOT RE 1 according to Regulation(EC) No 1272/2008 are not allowed.Note: Residual substances (technical impurities)classified as toxic are allowed to be found in thecoating ingredients as long as the coatingingredient itself is not classified as toxic.--SDToxic, harmful and corrosive preparations The ready-to-use UV-coating preparation shallnot be classified as Acute Tox. 1-4, STOT SE 1 &2, STOT RE 1 & 2, Asp Tox 1, Skin Corr 1A & 1B,CMR cat. 1A, 1B & 2 or Resp. Sens. cat. 1according to Regulation (EC) No 1272/2008.--SD1.2Additional requirements for surface coatings and coverings for solidwood, wood-based materials, and wood-like natural materialsTable 1.2 Surface coatings and coverings for solid wood, wood-based materials, and wood-like natural materialsSurface coating/ covering Substance Requirements Test method MinimumDocumentationrequirementAll types of surface coatings Formaldehyde Surface coating products shall notcontain formaldehyde, i.e.:•No formaldehyde shall be addedto the surface coating product.•No formaldehyde shall be createdduring storage and curing of thesurface coating.•The formaldehyde contaminationlevel shall be maximum0.5 mg/m2h measured accordingto EN 717-2 (Gas analysismethod) with the finished surfacecoating applied to a glass plate orother inert substrate.The samplingshall reflect arealistic worstcase in com-parison to whenthe productcould reach acustomer (i.e.normal handlingin factory,storage time,packaging andtransport to thenearest desti-nation).SDSurface coverings Formaldehyde Exception from general CMR ban:formaldehyde is allowed to be usedin the following case:•In the production of low-pressurelaminates (LPL), continuous-pressure laminates (CPL), andhigh-pressure laminates (HPL),which are impregnated withmelamine/formaldehyde or urea/formaldehyde resins.•In coatings applied on thecovering as part of itsmanufacture, before the coveringis applied to the substrate.Note: in any case of use offormaldehyde-containing resins,requirements regardingformaldehyde emission stated inother parts of the productdocumentation shall be fulfilled.-- Fordocumentationrequirements,see IOS-MAT-0003.Table 1.2 Surface coatings and coverings for solid wood, wood-based materials, and wood-like natural materialsSurface coating/ covering Substance Requirements Test method MinimumDocumentationrequirementLiquid coatings and thinners OrganicsolventsSurface coatings and thinners shallhave a maximum VOC content of130 g VOC/litre of the ready-to-useproduct.In special cases and after approvalby IKEA, surface coatings andthinners containing organic solventsexceeding 130 g VOC/litre may beused if the process is performedunder conditions with efficient VOCencapsulation and VOC exhaustreduction. The total VOC emissionshall be maximum 15 % of allsolvents used in connection with theapplication of solvent-bornecoatings, including for cleaning ofcoating equipment, as per the massbalance calculation.Note: This requirement does notapply to printing of names or codesfor articles, components or materialswhen that printing has no relevancefor the design of the article.ISO 11890-2ASTM D 2369, incases wherereactive diluentsare presentSDFor special caseswith VOC exhaustreduction, asolventmanagementplan (massbalance)according to EUDirective2010/75/EUAnnex VII part 7shall be carriedout every 12months andconnected inConnect to thearticle (throughappropriatematerial/process/componentcombination).Liquid un-saturated polyester coatings Styrene andvinyl toluenemonomersThe sum of styrene and vinyl toluenemonomers shall be less than 1.0 %by weight in the ready-to-usemixture.-- SDPeroxides Aromatic peroxide hardeners are notallowed to be used.-- SD1.2.1Additional requirements specifically for UV coatingsTable 1.2.1 UV coatings for solid wood, wood-based materials, and wood-like natural materials Substance Requirements Test method MinimumdocumentationrequirementResidual free monomers (stenomeric acrylates) Residual stenomeric acrylic monomers in thefinished cured coating film and the substrateshall be less than 800 mg/m2 extractable.Note: This requirement refers to the finalproduct after curing.In order to fulfil this requirement, key UV-process parameters such as UV-radiation level,UV-lamp distance, applied amount of coating,flow speed etc. shall be fully controlled anddocumented.IOS-TM-0002,section 17SD and TRResidual photo-initiators Roller coated surfaces•Residual concentration of photo-initiators inthe finished cured coating film and thesubstrate shall be less than 2000 mg/m2extractable.Other UV-coated surfaces•No limit (but still test requirement).IOS-TM-0002,section 17SD and TROdour Smell problems caused for example byincorrect curing, or by residues of photo-initiators, their breakdown products and theirimpurities, are not allowed.If any shipment of goods emits an unpleasantor unexpected smell, or deviates from earliershipments or from reference sample in termsof emissions/odour, in a way that is deemedby IKEA to involve a risk of discomfort orhealth effects for customers, this is to beconsidered a valid cause for claim of saidshipment. In case of dispute, evaluation ofodour to bemade by IKEAwith anevaluation groupof at least six persons--1.3Additional requirements for surface coatings and treatments formetal substratesTable 1.3 Surface coatings and treatments for metal substratesSurface coating/ covering Substance Requirements Test method MinimumdocumentationrequirementHot dip galvanizing Cadmium Zinc grades with cadmium content lowerthan 40 mg/kg shall be used.ICP SDChrome plating Hexavalentchrome(Cr-VI)Not allowed to use Cr-VI (chromates,bichromates, or chromic acid) in chromeplating.-- SDChromating, passivation and anodizing Hexavalentchrome(Cr-VI)Not allowed to use Cr-VI (chromates,bichromates, or chromic acid).If Cr-VI is found according to spot testand/or boiling under extractionprocedure (qualitative tests, seeIEC 62321), this indicates that Cr-VI hasbeen used, which is not allowed.IEC 62321 SDAnodizing – correction pens AromatichydrocarbonsolventsException: The 1 % limit for totalaromatic hydrocarbons in the liquidfraction (see Table 1.1) does not applyto correction pens used to touch upanodized surfaces, if used on less than0.2 % of the total anodized surface(yearly average).Note: this exception does not apply tobenzene.--Surface coatings Formaldehyde Exception from general CMR ban:formaldehyde-containing amino resinsare allowed to be used.Note: the formaldehyde-containingresin should be fully cured after thecoating process. Emission limit forformaldehyde from complete productaccording to IOS-MAT-0010 applies.-- SD。
Ovation I O Reference Manual

This publication adds the Eight Channel RTD module to the Ovation I/O Reference Manual. It should be placed between Sections 19 and 20.Date: 04/03IPU No.243Ovation ® Interim Publication UpdatePUBLICATION TITLEOvation I/O Reference ManualPublication No. R3-1150Revision 3, March 2003Section 19A. Eight Channel RTDModule19A-1. DescriptionThe Eight (8) channel RTD module is used to convert inputs from Resistance Temperature Detectors (RTDs) to digital data. The digitized data is transmitted to the Controller.19A-2. Module Groups19A-2.1. Electronics ModulesThere is one Electronics module group for the 8 channel RTD Module:n5X00119G01 converts inputs for all ranges and is compatible only with Personality module 5X00121G01 (not applicable for CE Mark certified systems).19A-2.2. Personality ModulesThere is one Personality module groups for the 8 channel RTD Module:n5X00121G01 converts inputs for all ranges and is compatible only with Electronics module 5x00119G01 (not applicable for CE Mark certified systems).19A-2.3. Module Block Diagram and Field Connection WiringDiagramThe Ovation 8 Channel RTD module consists of two modules an electronics module contains a logic printed circuit board (LIA) and a printed circuit board (FTD). The electronics module is used in conjunction with a personalty module, which contains a single printed circuit board (PTD). The block diagram for the 8 channel RTD moduleis shown in Figure 19A-1.Table 19A-1. 8 Channel RTD Module Subsystem ChannelsElectronic Module Personality Module85X00119G015X00121G01Figure 19A-1. 8 Channel RTD Module Block Diagram and Field Connection Wiring Diagram19A-3. SpecificationsElectronics Module (5X00119)Personality Module (5X00121)Table 19A-2. 8 Channel RTD Module SpecificationsDescription ValueNumber of channels8Sampling rate50 HZ mode: 16.67/sec. normally. In 3 wire mode, leadresistance measurement occurs once every 6.45 sec.during which the rate drops to 3/sec.60 HZ mode: 20/sec. normally. In 3 wire mode, leadresistance measurement occurs once every 6.45 sec.during which the rate drops to 2/sec.Self Calibration Mode: Occurs on demand only. The ratedrops to 1/sec. once during each self calibration cycle.RTD ranges Refer to Table 19A-3.Resolution12 bitsGuaranteed accuracy (@25°C)0.10% ±[0.045 (Rcold/Rspan)]% ± [((Rcold + Rspan)/4096 OHM)]% ± [0.5 OHM/Rspan]% ±10 m V ± 1/2LSBwhere:Rcold and Rspan are in Ohms.Temperature coefficient 10ppm/°CDielectric isolation:Channel to channel Channel to logic 200V AC/DC 1000 V AC/DCInput impedance100 M OHM50 K OHM in power downModule power 3.6 W typical; 4.2 W maximumOperating temperature range0 to 60°C (32°F to 140°F)Storage temperature range-40°C to 85°C (-40°F to 185°F)Humidity (non-condensing)0 to 95%Self Calibration On Demand by Ovation ControllerCommon Mode Rejection120 dB @ DC and nominal power line frequency+/- 1/2%Normal Mode Rejection100 dB @ DC and nominal power line frequency+/- 1/2%Table 19A-3. 8 Channel RTD RangesScale #(HEX)Wires Type Tempo FTempo CRcold(ohm)Rhot(ohm)Excitationcurrent(ma)Accuracy± ±countsAccuracy± ±% ofSPAN1310OhmPL0 to1200–18 t o6496106.3 1.090.222310OhmCU 0 to302–18 t o1508.516.5 1.0 130.32D350OhmCU 32 to2840 to1405080 1.0110.2711350OhmCU 32 to2300 to1105378 1.0120.30193100Ohm PL –4 to334–16 t o16892163.671.0110.27223100Ohm PL 32 to5200 to269100200 1.0100.25233100Ohm PL 32 to10400 to561100301 1.0100.25253120Ohm NI –12 t o464–11 t o240109360 1.0100.25263120Ohm NI 32 to1500 to70120170 1.0130.32283120Ohm NI 32 to2780 to122120225 1.0110.27804100Ohm PL 32 to5440 to290100 208 1.0100.25814100Ohm PL 356 t o446180 t o230168 186 1.0300.74824200Ohm PL 32 to6980 to370200 473 1.0120.30834200Ohm PL 514 t o648268 t o342402452 1.0290.71844100Ohm PL 32 to1240 to51100120 1.0190.47854100Ohm PL 32 to2170 to103100 140 1.0130.3286 4100Ohm PL 32 to4120 to211100 180 1.0110.27874100Ohm PL 32 to7140 to379100 240 1.0100.25884120Ohm PL 511 t o662266 t o350200230 1.0240.5919A-4. 8 Channel RTD Terminal Block Wiring Information19A-4.1. Systems Using Personality Module 5X00121G01 Each Personality module has a simplified wiring diagram label on its side, which appears above the terminal block. This diagram indicates how the wiring from the field is to beconnected to the terminal block in the base unit. The following table lists and defines the abbreviations used in this diagram.Table 19A-4. Abbreviations Used in the DiagramAbbreviation Definition+IN, -IN Positive and negative sense input connectionEarth ground terminal. Used for landing shields when the shield is to begrounded at the module.PS+, PS-Auxiliary power supply terminals.RTN Return for current source connection.SH Shield connector. used for landing shields when the shield is to begrounded at the RTD.SRC Current source connection.Note:PS+ and PS- are not used by this module.19A-5. 8 Channel RTD Module Address Locations19A-5.1. Configuration and Status RegisterWord address 13 (D in Hex) is used for both module configuration and module status. The Module Status Register has both status and diagnostic information. The bit information contained within these words is shown in Table 19A-5.Definitions for the Configuration/Module Status Register bits:Bit 0:This bit configures the module (write) or indicates the configuration state of the module (read). A “1” indicates that the module is configured. Note that until the module is configured, reading from addresses #0 through #11 (B in Hex) will produce an attention status.Bit 1:This bit (write “1”) forces the module into the error state, resulting in the error LED being lit. The read of bit “1” indicates that there is an internal module error,or the controller has forced the module into the error state. The state of this bit is always reflected by the module’s Internal Error LED. Whenever this bit is set,an attention status is returned to the controller when address #0 through #11(B in Hex) are read.Table 19A-5. 8 Channel RTD Configuration/Status Register (Address 13 0xD in Hex)Bit Data Description -Configuration Register (Write)Data Description -Status Register (Read)0Configure Module Module Configured(1 = configured; 0 = unconfigured)1Force errorInternal or forced error(1 = forced error; 0 = no forced error)250/60 Hz select (0 = 60Hz, 1 = 50Hz)50/60 Hz System (1 = 50Hz) d(read back)3SELF_CAL (Initiates Self Calibration)Warming bit (set during power up or configuration)40050060Module Not Calibrated 708CH.1 _ 3/4 Wire.CH.1 _ 3/4 Wire - Configuration (read back)9CH.2 _ 3/4 Wire.CH.2 _ 3/4 Wire - Configuration (read back)10CH.3 _ 3/4 Wire.CH.3 _ 3/4 Wire - Configuration (read back)11CH.4 _ 3/4 Wire.CH.4 _ 3/4 Wire - Configuration (read back)12CH.5 _ 3/4 Wire.CH.5 _ 3/4 Wire - Configuration (read back)13CH.6 _ 3/4 Wire.CH.6 _ 3/4 Wire - Configuration (read back)14CH.7 _ 3/4 Wire.CH.7 _ 3/4 Wire - Configuration (read back)15CH.8 _ 3/4 Wire.CH.8 _ 3/4 Wire - Configuration (read back)Bit 2:The status of this bit (read) indicates the conversion rate of the module, write to this bit configures the conversion rate of A/D converters as shown below.see Table 19A-6.Bit3:Write: This bit is used to initiate self-calibration. Read: This bit indicates that the module is in the “Warming” state. this state exists after power up and ter-minates after 8.16 seconds. the module will be in the error condition during the warm up period.Bit4 & 5:These bits are not used and read as “0” under normal operation.Bit 6:This bit (read) is the result of a checksum test of the EEPROM. A failure of this test can indicate a bad EEPROM, but it typically indicates that the module has not been calibrated. A “0” indicates that there is no error condition. If an error is present, the internal error LED is lit and attention status will be returned for all address offsets 0-11 (0x0 - 0xB). The “1” state of this bit indicates an unre-coverable error condition in the field.Bit 7:This bits is not used and read as “0” under normal operation.Bit 8 - 15:These bits are used to configure channels 1 - 8 respectively for 3 or 4 wire op-eration. A “0” indicates 3 wire and a “1” indicates 4 wire operation, see Table 19A-7 and Table 19A-8).Word address 12 (0xC) is used to configure the appropriate scales for Channels 1 - 4 (refer to Table 19A-7 and Table 19A-8).Table 19A-6. Conversion Rate Conversion Rate (1/sec.)Bit 260 (for 60Hz systems)050 (for 50Hz systems)1Table 19A-7. Data Format for the Channel Scale Configuration Register(0xC)Bit Data Description Configuration (Write)Data Description Status (Read)0 Configure Channel #1scale - Bit 0Channel #1 scale configuration (read back) - Bit 01Configure Channel #1scale - Bit 1Channel #1 scale configuration (read back) - Bit 12Configure Channel #1scale - Bit 2Channel #1 scale configuration (read back) - Bit 23Configure Channel #1scale - Bit 3Channel #1 scale configuration (read back) - Bit 34Configure Channel #2 scale - Bit 0Channel #2 scale configuration (read back) - Bit 05Configure Channel #2 scale - Bit 1Channel #2 scale configuration (read back) - Bit 16Configure Channel #2 scale - Bit 2Channel #2 scale configuration (read back) - Bit 27Configure Channel #2 scale - Bit 3Channel #2 scale configuration (read back) - Bit 38Configure Channel #3 scale - Bit 0Channel #3 scale configuration (read back) - Bit 09Configure Channel #3 scale - Bit 1Channel #3 scale configuration (read back) - Bit 1Caution:Configuring any or all channel scales while the system is running will cause all channels to return attention status for up to two seconds following the reconfiguration.Caution:Configuring any or all channel scales while the system is running will cause all channels to return attention status for up to two seconds following the reconfiguration.10Configure Channel #3 scale - Bit 2Channel #3 scale configuration (read back) - Bit 211Configure Channel #3 scale - Bit 3Channel #3 scale configuration (read back) - Bit 312Configure Channel #4 scale - Bit 0Channel #4 scale configuration (read back) - Bit 013Configure Channel #4 scale - Bit 1Channel #4 scale configuration (read back) - Bit 114Configure Channel #4 scale - Bit 2Channel #4 scale configuration (read back) - Bit 215Configure Channel #4 scale - Bit 3Channel #4 scale configuration (read back) - Bit 3Table 19A-8. Data Format for the Channel Scale Configuration Register(0xE)Bit Data Description Configuration (Write)Data Description Status (Read)0 Configure Channel #5 scale - Bit 0Channel #5 scale configuration (read back) - Bit 01Configure Channel #5 scale - Bit 1Channel #5 scale configuration (read back) - Bit 12Configure Channel #5 scale - Bit 2Channel #5 scale configuration (read back) - Bit 23Configure Channel #5 scale - Bit 3Channel #5 scale configuration (read back) - Bit 34Configure Channel #6 scale - Bit 0Channel #6 scale configuration (read back) - Bit 05Configure Channel #6 scale - Bit 1Channel #6 scale configuration (read back) - Bit 16Configure Channel #6 scale - Bit 2Channel #6 scale configuration (read back) - Bit 27Configure Channel #6 scale - Bit 3Channel #6 scale configuration (read back) - Bit 38Configure Channel #7 scale - Bit 0Channel #7 scale configuration (read back) - Bit 09Configure Channel #7 scale - Bit 1Channel #7 scale configuration (read back) - Bit 110Configure Channel #7 scale - Bit 2Channel #7 scale configuration (read back) - Bit 211Configure Channel #7 scale - Bit 3Channel #7 scale configuration (read back) - Bit 312Configure Channel #8 scale - Bit 0Channel #8 scale configuration (read back) - Bit 013Configure Channel #8 scale - Bit 1Channel #8 scale configuration (read back) - Bit 114Configure Channel #8 scale - Bit 2Channel #8 scale configuration (read back) - Bit 215Configure Channel #8 scale - Bit 3Channel #8 scale configuration (read back) - Bit 3Table 19A-7. Data Format for the Channel Scale Configuration Register(0xC)19A-6. Diagnostic LEDsTable 19A-9. 8 Channel RTD Diagnostic LEDsLED DescriptionP (Green)Power OK LED. Lit when the +5V power is OK.C (Green)Communications OK LED. Lit when the Controller is communicatingwith the module.I (Red)Internal Fault LED. Lit whenever there is any type of error with themodule except to a loss of power. Possible causes are:n - Module initialization is in progress.n - I/O Bus time-out has occurred.n - Register, static RAM, or FLASH checksum error.n - Module resetn - Module is uncalibrated.n - Forced error has been received from the Controllern - Communication between the Field and Logic boards failedCH1 - CH 8 (Red)Channel error. Lit whenever there is an error associated with a channel or channels. Possible causes are:n - Positive overrangen - Negative overrangen Communication with the channel has failed。
NI 2501和NI 2503 PXI交换卡与TB-2605冷 junction 温度传感器配对的说

INSTALLATION GUIDETB-2605 Isothermal Terminal Block̭͈Ρ΅νιϋΠ͉ͅȂ βȜΐ͜ ̞̳ͦ̀͘͘ȃThis installation guide describes how to install and connect signals to theTB-2605 isothermal terminal block for use with the NI2501 and NI2503PXI switch cards.ContentsIntroduction (1)What You Need to Get Started (2)Signal Names (2)Signal Connection (4)Installing Your Terminal Block (6)Installing the Analog Bus Plug (7)Cold-Junction Temperature Sensor (9)Specifications (11)IntroductionThe TB-2605 is an isothermal terminal block that consists of a printedcircuit board with screw terminals. The terminal block connects directlyto the front panel I/O connector of the NI 2501 or NI 2503.The terminal block can easily accommodate thermocouples, resistancetemperature detectors (RTDs), thermistors, and voltage signals.The TB-2605 features an isothermal construction to minimize thetemperature gradients across the screw terminals and a high-accuracythermistor cold-junction temperature sensor for measuring withthermocouples. Enclosures keep out air currents to maintain an isothermalenvironment for the screw terminals and the cold-junction sensor.Use the screw terminals on the TB-2605 to make connections to allchannels except the cold-junction sensor. The front side of the terminalblock has two additional connectors for connecting to the analog bus. Youcan use the low-voltage AB plug to connect the analog bus of adjacentswitch cards.What You Need to Get StartedYou need the following to set up and use your terminal block:❑One of the following PXI switch cards:–NI 2501–NI 2503❑NI 2501/2503 User Manual❑TB-2605 isothermal terminal block❑0.10 in. slotted screwdriver❑No. 1 Phillips screwdriver❑Wire cutters❑Wire insulation stripper❑Analog bus connectors (to connect to multiple cards)Signal NamesThe NI 2501/2503 has several modes of operation. The following figuresshow the names of the signal connections for the different modes ofoperation.TB-2605 Isothermal Terminal Figure 1. Two-Wire ModeFigure 2. One-Wire Mode© National Instruments Corporation3TB-2605 Isothermal Terminal BlockFigure 3. Four-Wire ModeSignal ConnectionSee your NI 2501/2503 User Manual for examples of how to connect yoursignals. Refer to Figure4 as you perform the following steps to connectyour signals to your terminal block (the numbers in parentheses refer toitems in Figure4).1.Remove the terminal block cover (1) by unscrewing the two coverscrews (2) using the 0.10 in. slotted screwdriver.2.Loosen or remove the strain relief bar (3) by loosening the two strainrelief screws (10).e wire cutters and wire insulation strippers to strip the wire ends asnecessary to connect them to screw terminals.4.Loosen the screws in the screw terminals with the 0.10 in. slottedscrewdriver.5.Insert the stripped wires into the screw terminals. Tighten the screwswith the 0.10 in. slotted screwdriver.6.Connect safety ground or shield wires to the chassis ground connectiontab (7) using the provided solder lug (6).7.Tighten or replace the strain relief screws (10).8.Replace the terminal block cover (1) and tighten the cover screws (2). TB-2605 Isothermal Terminal Figure 4. TB-2605 Parts Locator Diagram© National Instruments Corporation5TB-2605 Isothermal Terminal BlockTB-2605 Isothermal Terminal Block Installing Your Terminal BlockNoteTo minimize the temperature gradient inside the terminal block and thus maintain its isothermal nature for accurate cold-junction compensation, place the terminal block and chassis away from extreme temperature differentials.Refer to Figure 5 as you perform the following steps to connect the terminal block to the NI 2501 or NI 2503 connector (the numbers in parentheses refer to items in Figure 5).NoteThe TB-2605 terminal block must be installed on the NI 2501/2503 switch card after the card is installed in the chassis.1.Install the switch card (3) into the chassis and tighten the two module screws (2).2.Guide the terminal block onto the switch card connector (4).3.Tighten the two terminal block mounting screws (1).CautionThe connectors of both the switch card and the terminal block are polarized. Youcan attach them in only one way. Do not force the terminal block when inserting it into orremoving it from the NI 2501 or NI 2503 connector.Figure 5. Connecting the TB-2605 to the Switch Card Installing the Analog Bus PlugRefer to Figure6 as you perform the following steps to install the analogbus plug. The cover should be attached to the terminal block before youconnect the analog bus plug because the plug screws into the cover(the numbers in parentheses refer to items in Figure6).1.With two terminal blocks connected to boards in adjacent slots,connect the analog bus plug (3) into the analog bus connector (1)of each terminal block.2.Tighten the screw (2) on the analog bus plug using the 0.10 in. slottedscrewdriver.© National Instruments Corporation7TB-2605 Isothermal Terminal BlockFigure 6. Installing the Analog Bus PlugAnalog Bus ConnectorThe front side of the terminal block has two connectors for connecting tothe analog bus. The low-voltage analog bus plug can be used to connect theanalog buses of adjacent switch cards, as shown in Figure6. The signalconnections for the analog bus are shown in Figure7.TB-2605 Isothermal Terminal © National Instruments Corporation 9TB-2605 Isothermal Terminal BlockFigure 7. Analog Bus ConnectorCold-Junction Temperature SensorThe TB-2605 temperature sensor voltage output varies from 198.54 mV to 19.58 mV over the temperature range 0 to 55 °C, respectively, and has an accuracy of ±0.5 °C over the 15 to 35 °C temperature range and ±0.9 °C over the 0 to 15° and 35° to 55 °C temperature ranges.1You can use the following formulas to convert the cold-junction sensor voltage to cold-junction temperature:T(°C) = T K – 273.15where T K is the temperature in kelvina = 1.295361 x 10-3b = 2.343159 x 10-4c = 1.018703 x 10-7R T = resistance of the thermistorV TEMPOUT = output voltage of the temperature sensor1 Includes the combined effects of the temperature sensor accuracy and temperature difference between the temperature sensorand any screw terminal. The temperature sensor accuracy includes tolerances in all component values, the effects caused bytemperature and loading, and self-heating.T K 1a b R T ln ()c R T ln ()3++[]---------------------------------------------------------------=R T 189K V TEMPOUT 2.5V TEMPOUT –----------------------------------⎝⎠⎛⎞=T °F ()[T(°C )]95-----------------------32+=TB-2605 Isothermal Terminal Block where T(°F) and T(°C) are the temperature readings in degrees Fahrenheit and degrees Celsius, respectively.The thermistor resistance varies from 16,305 Ω to 1,492Ω over a 0 to 55°C temperature range.NoteV TEMPOUT varies from 198.54 mV (at 0 °C) to 19.58 mV (at 55 °C). For bestresolution, use the maximum gain for this signal range on the analog input channel of your measurement device.The 200 mV range is designed to eliminate the necessity of changing a measurement device’s signal range to measure the cold-junction sensor while scanning e an average of a large number of samples to obtain the most accurate reading. Noisy environments require more samples for greater accuracy.Figure 8 shows the circuit diagram of the TB-2605 cold-junction temperature sensor.Figure 8.Temperature Sensor Circuit DiagramSpecificationsCold-junction sensorAccuracy1........................................0.5° from 15 to 35 °C0.9° from 0° to 15° Cand 35 to 55 °CRepeatability...................................0.2° from 15 to 35 °COutput.............................................198.54 mV to 19.58 mVfrom 0 to 55 °CDimensions.............................................8.4 by 10.7 by 2.0 cm(3.3 by 4.2 by 0.80 in.)Max voltage(signal + common mode).......................Each input should remain within30 V rms or 60 VDC of ground andall other channels to eliminate thepossibility of hazardous shock.1 Includes the combined effects of the temperature sensor accuracy and the temperature difference between the temperature sensor and any screw terminal. The temperature sensor accuracy includes tolerances in all component values, the effects caused by temperature and loading, and self-heating.© National Instruments Corporation11TB-2605 Isothermal Terminal BlockNational Instruments, NI, , and LabVIEW are trademarks of National Instruments Corporation. Refer to the Terms of Use section on/legal for more information about National Instruments trademarks. Other product and company names mentioned herein are trademarks or trade names of their respective companies. For patents covering National Instruments products, refer to the appropriate location: Help»Patents in your software, the patents.txt file on your CD, or /patents.© 1999–2007 National Instruments Corporation. All rights reserved.372258B Nov07。
GB射线照相检测术语

GB/T 12604.2—2005/ISO 5576:1997《无损检测术语射线照相检测》1 范围本标准界定了工业射线照相检测的术语。
2 术语和定义2.1 吸收 absorption2.2 活度 activity2.3 老化灰雾 ageing fog2.4 阳极 anode2.5 阳极电流 anode current2.6 伪像(假显示) artefact ( false indication )2.7 衰减 attenuation2.8 衰减系数 attenuation coefficientμ2.9 平均梯度 average gradient2.10 背散射 back scatter背散射线 back scattered radiation2.11 射束角 beam angle2.12 电子回旋加速器 betatron2.13 遮挡介质 blocking medium2.14 累积因子 build-up factor2.15 暗盒 cassette暗袋2.16 阴极 cathode2.17 已校验的阶梯密度片 calibrated density step wedge2.18 (胶片的)特性曲线 characteristic curve ( of a film )2.19 清澈时间 clearing time2.20 准直 collimation2.21 准直器 collimator2.22 康普顿散射 Compton scatter2.23 计算机层析成像 computerized tomography ( CT )2.24 恒电势电路 constant potential circuit2.25 连续谱 continuous spectrum2.26 对比度 contrast2.27 反衬介质 contrast medium2.28 对比灵敏度(厚度灵敏度) contrast sensitivity ( thickness sensitivity ) 2.29 衰减曲线 decay curve2.30 密度计 densitometer2.31 (胶片或相纸的)显影 development ( of a film or paper )2.32 衍射斑纹 diffraction mottle2.33 剂量计 dosemeter ( dosimeter )2.34 剂量率计 dose rate meter2.35 双焦点管 dual focus tube2.36 双线像质计 duplex wire image quality indicator双丝像质计双线图像质量指示器2.37 边缘遮挡材料 edge-blocking material2.38 均值过滤器(射线束致平器) equalizing filter ( beam flattener ) 2.39 等效X射线电压 equivalent X-ray voltage2.40 曝光 exposure2.41 曝光计算器 exposure calculator2.42 曝光曲线 exposure chart2.43 曝光宽容度 exposure latitude2.44 曝光时间 exposure time2.45 片基 film base2.46 胶片梯度 film gradientG2.47 观片灯(观察屏) film illuminator ( viewing screen )2.48 胶片处理 film processing2.49 胶片系统速度 film system speed2.50 滤光板 filter2.51 定影 fixing2.52 探伤灵敏度 flaw sensitivity2.53 荧光增感屏 fluorescent intensifying screen2.54 金属荧光增感屏 fluorometallic intensifying screen2.55 荧光透视 fluoroscopy2.56 焦点 focal spot2.57 焦点尺寸 focal spot size2.58 焦距 focus-to-film-distanceffd2.59 灰雾度 fog density2.60 伽玛射线照相 gamma radiography2.61 伽玛射线 gamma raysγ射线2.62 伽玛射线源 gamma-ray source2.63 伽玛射线源容器 gamma-ray source container 2.64 几何不清晰度 geometric unsharpness2.65 颗粒性 graininess2.66 颗粒度 granularity2.67 半衰期 half life2.68 半价层 half value thicknessHVT2.69 光源 illuminator观片灯2.70 图像对比度 image contrast2.71 图像清晰度 image definition2.72 图像增强 image enhancement2.73 图像增强器 image intensifier2.74 像质 image quality图像质量2.75 像质计 image quality indicator图像质量指示器IQI2.76 像质值 image quality value图像质量值IQI灵敏度 IQI sensitivity2.77 入射射线束轴线 incident beam axis2.78 工业放射学 industrial radiology2.79 固有过滤 inherent filtration2.80 固有不清晰度 inherent unsharpness2.81 增感因子 intensifying factor2.82 增感屏 intensifying screen2.83 潜影 latent image2.84 直线电子加速器 linear electron accelerator ( LINAC ) 2.85 屏蔽 masking2.86 金属屏 metal screen2.87 微焦点射线照相 microfocus radiography2.88 调制传递函数 modulation transfer functionMTF2.89 运动不清晰度 movement unsharpness2.90 工件对比度 object contrast2.91 工件至胶片距离 object-to-film distance2.92 周向曝光 panoramic exposure2.93 透度计 penetrameter2.94 压痕 pressure mark2.95 初始射线 primary radiation2.96 投影放大率 projective magnification2.97 投影放大技术 projective magnification technique2.98 (射线束)质量 quality ( of a beam of radiation )2.99 照射对比度 radiation contrast2.100 辐射源 radiation source2.101 射线照相底片/照片 radiograph2.102 射线照相胶片 radiographic film2.103 射线照相 radiography2.104 放射性同位素 radioisotope2.105 射线透视 radioscopy2.106 棒阳极管 rod anode tube2.107 散射线 scattered radiation2.108 增感型胶片 screen type film2.109 源固定器 source holder2.110 源尺寸 source size2.111 源至胶片距离(sfd) source-to-film distance ( sfd ) 2.112 空间分辨力 spatial resolution2.113 比活度 specific activity2.114 阶梯楔块 step wedge2.115 立体射线照相 stereo radiography2.116 靶 target2.117 管子光阑 tube diaphragm2.118 管头 tube head2.119 管罩 tube shield2.120 管子遮光器 tube shutter2.121 管子窗口 tube window2.122 管电压 tube voltage2.123 未密封源 unsealed source2.124 不清晰度 unsharpness2.125 有效密度范围 useful density range 2.126 真空暗盒 vacuum cassette2.127 观察屏蔽 viewing mask2.128 可视对比度 visual contrast2.129 X射线 X-rays2.130 X射线胶片 X-ray film2.131 X射线管 X-ray tube。
浴室暖气设备的技术参数手册说明书

JIS SymbolX12ASP 334561/8 standard 1/4 standard 3/8 standard 1/2 standardBody sizeUniversalPilot check valvePort sizeWith seal Symbol01020304F02F03F04N01N02N03N04Cylinder sideR 1/8R 1/4R 3/8R 1/2R 1/4R 3/8R 1/2NPT 1/8NPT 1/4NPT 3/8NPT 1/2Applicable tubing O.D.Metric sizeInch size06081012ø6ø8ø10ø1207091113ø1/4"ø5/16"ø3/8"ø1/2"ASP330FASP430FASP530FASP630F2005103211004005106421002003000607,08,0915005102015105001011,12,131000551014108050010002126410,1108,0930F 0106SWith One-touch fittingPilot port M5 x 0.8Rc 1/8Rc 1/8Rc 1/4G 1/8G 1/8G 1/410-32 UNF NPT 1/8NPT 1/8NPT 1/4Made to OrderLubricant: VaselineX12Ex.) ASP330F-01-06S-X12548Series ASPHow to OrderNeedle Valve/Flow CharacteristicsNumber of needle rotations Inlet pressure : 0.5 MPaInlet pressure : 0.5 MPaInlet pressure : 0.5 MPaInlet pressure : 0.5 MPaF l o w r a t e (l /m i n (A N R ))E f f e c t i v e a r e a (m m 2)Number of needle rotationsF l o w r a t e (l /m i n (A N R ))E f f e c t i v e a r e a (m m 2)F l o w r a t e (l /m i n (A N R ))E f f e c t i v e a r e a (m m 2)Number of needle rotationsF l o w r a t e (l /m i n (A N R ))E f f e c t i v e a r e a (m m 2)Number of needle rotationsd T1D1R 1/8R 1/4R 3/8R 1/26868810101211.615.212.815.215.218.518.520.9Applicable tubing O.D. ødL2L3ML 1H1(Hexagon width across flats)L 5A 1 ∗A 2 ∗øD 3øD 1øD2Metric SizeL 5T2M5 x 0.81/81/81/4H112171924H28121217D214.218.523 28.6D341.746.964.8L4 (1)Max.Min.Model ASP330F-01-06S ASP330F-01-08S ASP430F-02-06S ASP430F-02-08S ASP530F-03-08S ASP530F-03-10S ASP630F-04-10S ASP630F-04-12SL114 15.818 19.720.323.125.9L238.444.743.446.451.354.164.266L322.928.225.228.228.232.632.634.439.638.936.741.957.334.633.911.815 19.826.5L538.648.255.169.4A1 (2)35.242.450 61.8A2 (2)10.510.914.418.3M 13.718.716.818.718.720.820.821.8Mass (g)32356568107110212215T2T1H2(Hexagon width across flats)d T1D1NPT 1/8NPT 1/4NPT 3/8NPT 1/21/4"5/16"1/4"5/16"5/16"3/8"3/8"1/2"13.215.213.215.215.218.518.521.7Inch SizeT210-32 UNF NPT 1/8NPT 1/8NPT 1/4H11/2"11/16"1915/16"H281/2"1/2"11/16"D214.218.523 28.6D341.746.964.8L4 (1)Max.Min.Model ASP330F-N01-07S ASP330F-N01-09S ASP430F-N02-07S ASP430F-N02-09S ASP530F-N03-09S ASP530F-N03-11S ASP630F-N04-11S ASP630F-N04-13SL120.323.125.926.5L242.244.743.946.451.354.164.266.3L325.628.225.628.228.232.632.634.738.936.741.957.333.911.815 19.826.5L538.648.255.169.4A1 (2)35.142.650.361.8A2 (2)10.510.914.418.3M 17 18.717 18.718.720.820.821.8Mass (g)1071162202303568L4Applicable tubing O.D. ødL2L3ML 1H1(Hexagon width across flats)A 1 ∗A 2 ∗øD 3øD 1øD 2T2T1H2(Hexagon width across flats)L4Note 1)Reference dimensionsNote 2)Reference dimensions of R thread after installation.Note 1)Reference dimensionsNote 2)Reference dimensions of NPT thread after installation.15.818549Series ASPSpeed Controller with Pilot Check Valvewith One-touch FittingDimensionsAS ASP ASN AQ ASVAK VCHCASSKE TMHASR ASQComponent PartsNo.12345678910111213Body A Elbow body Handle Pilot body Body B Needle Needle guide Guide Lock nut Piston Valve Cover U seal Material PBT PBT PBTBrassBrassBrassBrassBrassBrassBrassStainless steel, NBRBrassHNBRNote Electroless nickel plated Electroless nickel plated Electroless nickel plated Electroless nickel plated Electroless nickel plated Electroless nickel plated Electroless nickel plated Black zinc chromated Description No.141516171819202122232425Material NBR NBRStainless steel Stainless steel—NBR —NBR NBR NBR NBRStainless steelNoteDescription DY seal DY seal Spring Spring Cassette Seal Spacer O-ring O-ring O-ring O-ring RingComponent Parts550Series ASPConstructionSeries ASPSpecific Product PrecautionsBe sure to read before handling. Refer to front matters 58 and 59 for Safety Instructionsand pages 412 to 414 for Flow Control Equipment Precautions.Design/SelectionWarning1.This product cannot be used for accurate andprecise intermediate stops of the actuator.Due to the compressibility of air as a fluid, the actuator willcontinue to move until it reaches a position of pressurebalance, even though the pilot check valve closes with anintermediate stop signal.2.This product cannot be used to hold a stop positionfor an extended period of time.Pilot check valves and actuators are not guaranteed for zeroair leakage. Therefore, it is sometimes not possible to hold astop position for an extended period of time. In the event thatholding for an extended time is necessary, a mechanicalmeans for holding should be devised.3. Consider the release of residual pressure.Actuators may move suddenly due to residual pressure, whichcan be dangerous during maintenance procedures.4. When used in a balance control circuit, there areinstances in which the check valve cannot release,even though the pilot pressure is 50% of theoperating pressure. In these cases, the pilot pressure should be the same as the operating pressure.5. For reference, SMC has conducted endurance testsin which ON, OFF operation of the check valve was performed at the maximum operating pressure, with a confirmed endurance of 10 million operations.Since the tests were performed under limited conditions, use caution in evaluating the results.InstallationWarning1.When mounting, please firmly align the tool withthe hexagon width across flats of the pilot body. If the hexagon width across flats is damaged as a result of failure to properly align the tool, the pilot body will be deformed, and poor pilot operation may result.Air sourceWarning1.If moisture enters the inside of the connectingpiping, the cover may corrode, and it may lead to a pilot operation malfunction.ASASPASNAQASVAKVCHCASSKETMHASRASQ551NF124-BLockOpen Close Door locking Pressing and liftingPicking and placingLifterPressRetraction lockDrop prevention for lifterExtension lockDrop prevention for press fitting jigFlow controlw/residual pressure reliefRelated ProductsResidual pressure relief ValveManual residual pressure release valve for quickrelease of cylinder pressureMeter-out flow control for cylinder speed regulationOne-touch fitting for simple connection of supply air Universal type for piping convenienceIntegral pilot operated check valve to hold position until pilot signal is provided G threadCan rotate 360° to desired piping positionNot for constant rotational useAPPLICATIONSAS-FEKESpecificationsASP-X352 Speed Control Valvewith Manual Override Pilot Operated Check ValveUni-fit for compatibility with NPT, BSPT, BSPP and G thread forms (alternate thread forms can be offered as non-standard options)Air217.5 psi (1.5MPa)14.5 to 145psi (0.1 to 1 MPa)More than 50% of operating pressure10 turnsNylon, Soft nylon, PolyurethaneFluidProof pressureOperating pressure rangePilot check valve operating pressure Number of needle rotations Applicable tubing material© 2012 SMC Corporation of America, All Rights Reserved.All reasonable efforts to ensure the accuracy of the information detailed in this catalog were made at the time of publishing. However, SMC can in no way warrant the information herein contained as specifications are subject to change without notice.DimensionsHow to OrderUni-fit thread form0Modelsyour SMC representative for availability .SMC Corporation of America10100 SMC Boulevard, Noblesville, Indiana 46060, U.S.A.Phone: 317-762-7621 Fax: 317-899-3102SMC Pneumatics (Canada) Ltd.2715 Bristol Circle, Oakville, Ontario L6H 6X5 CanadaPhone: 800-762-7621 Fax: 905-812-8686www.smcpneumatics.ca。
ZXSC310单 多元LED驱动器说明书
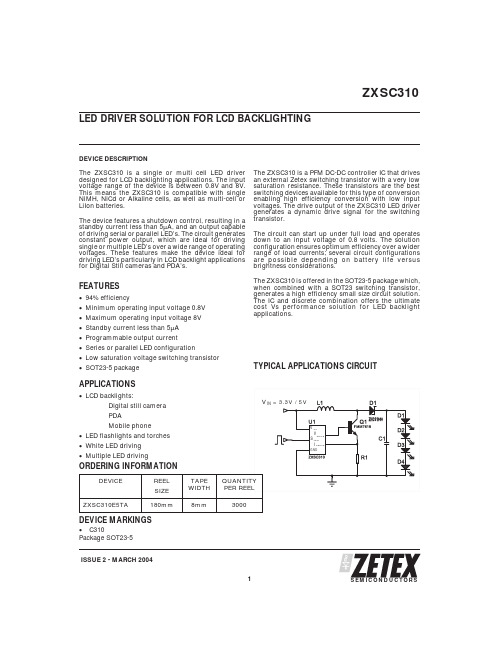
DEVICE DESCRIPTIONThe ZXSC310is a single or multi cell LED driver designed for LCD backlighting applications.The input voltage range of the device is between 0.8V and 8V.This means the ZXSC310is compatible with single NiMH,NiCd or Alkaline cells,as well as multi-cell or LiIon batteries.The device features a shutdown control,resulting in a standby current less than 5µA,and an output capable of driving serial or parallel LED’s.The circuit generates constant power output,which are ideal for driving single or multiple LED’s over a wide range of operating voltages.These features make the device ideal for driving LED’s particularly in LCD backlight applications for Digital Still cameras and PDA’s.FEATURES·94% efficiency·Minimum operating input voltage 0.8V ·Maximum operating input voltage 8V ·Standby current less than 5µA ·Programmable output current ·Series or parallel LED configuration ·Low saturation voltage switching transistor ·SOT23-5 packageThe ZXSC310is a PFM DC-DC controller IC that drives an external Zetex switching transistor with a very low saturation resistance.These transistors are the best switching devices available for this type of conversion enabling high efficiency conversion with low input voltages.The drive output of the ZXSC310LED driver generates a dynamic drive signal for the switching transistor.The circuit can start up under full load and operates down to an input voltage of 0.8volts.The solution configuration ensures optimum efficiency over a wider range of load currents;several circuit configurations are possible depending on battery life versus brightness considerations.The ZXSC310is offered in the SOT23-5package which,when combined with a SOT23switching transistor,generates a high efficiency small size circuit solution.The IC and discrete combination offers the ultimate cost Vs performance solution for LED backlight applications.ZXSC310ISSUE 2 - MARCH 20041S E M I C O N D U C T O R SLED DRIVER SOLUTION FOR LCD BACKLIGHTINGTYPICAL APPLICATIONS CIRCUITDEVICE MARKINGS·C310Package SOT23-5ABSOLUTE MAXIMUM RATINGS:Supply Voltage-0.3 to 10V Maximum Voltage other pins -0.3 to V CC +0.3V Power Dissipation 450mW Operating Temperature -40 to 85°C Storage Temperature-55 to 150°CS E M I C O N D U C T O R SZXSC310ISSUE 2 - MARCH 20042ELECTRICAL CHARACTERISTICS:Test conditions unless otherwise stated:V =1.5V,T =25COPERATING CONDITIONS1 Application dependent, see reference designs2 These parameters guaranteed by Design and characteristics3 Total supply current =I Q +I VDRIVE , see typical characteristics4 Operating frequency is application circuit dependent. See applications section.FMMT618For the circuits described in the applications section Zetex FMMT618is the recommended pass transistor.ZHCS1000For the maximum brightness circuit described in the applications section Zetex ZHCS1000is the recommended Schottky diode.The following indicates outline data for the device,more detailed information can be found in the Zetex surface mount products data book or on Zetex Web page:The following indicates outline data for the ZHCS,more detailed information can be found on Zetex Web page:ZXSC310ISSUE 2 - MARCH 2004S E M I C O N D U C T O R S3ELECTRICAL CHARACTERISTICS:Test conditions unless otherwise stated:T AMB =25C5Measured under pulse conditions. Pulse width=300µs. Duty cycle Յ2%ELECTRICAL CHARACTERISTICS:Test conditions unless otherwise stated:T =25CPart NumberV R I F I FSM V F at I R at Capacitance at V R =25V,f =1MHzPackage Max.VMax.mA Max.A Max.mV I F mA Max.A V R V Typ.pF SOT23BAT54302000.6500302502510SOT23-6ZHCS200040200020500200010003060SOT23ZHCS10004010001250010001003025SOT23ZHCS75040750125407501003025SOT23ZHCS50040500 6.75550500403020SOT23ZHCS400404006.75500400403020SOT323S E M I C O N D U C T O R SZXSC310ISSUE 2 - MARCH 20044TYPICAL CHARACTERISTICSDEVICE DESCRIPTIONThe ZXSC310is PFM,controller IC which,when combined with a high performance external transistor, enables the production of a high efficiency boost converter for LED driving applications.A block diagram is shown for the ZXSC310 below.The on chip comparator forces the driver circuit and therefore the external switching transistor off if the voltage at I SENSE exceeds19mV.An internal reference circuit and divider set this threshold.The voltage at I SENSE is taken from a current sense resistor connected in series with the emitter of the switching transistor.A monostable following the output of the comparator forces the turn-off time of the output stage to be typically1.7us.This ensures that there is sufficient time to discharge the inductor coil before the next on period.With every on pulse the switching transistor is kept on until the voltage across the current-sense resistor exceeds the threshold of the I SENSE input.The on-pulse length,and therefore the switching frequency,is determined by the programmed peak current,the input voltage and the input to output voltage differential.See applications section for details.The driver circuit supplies the external switching transistor with a fixed drive current.To maximise efficiency the external transistor switched quickly, typically being forced off within 30ns.ZXSC310ISSUE 2 - MARCH 20045S E M I C O N D U C T O R SREFERENCE DESIGNSThree typical LED driving applications are shown.Firstly a typical LCD backlight circuit,then maximum brightness LED driving solution and lastly an optimised battery life LED driving solution.This application shows the ZXSC310in a typical LCD backlight application for Digital Still Cameras and PDA’s.The input voltage for these backlight circuits are usually fixed from the main system power,typically 3.3V or 5V.The LED’s are connected serially so that the light is distributed uniformly in each LED.The current provided to the LED’s can either be pulsed or DC.The DC current is programmable via a sense resistor,R SENSE ,and is set to an optimum LED current of 20mA for the reference designs.DC current is achieved by adding a Schottky rectifying diode and an output capacitor, as shown in the reference design below.S E M I C O N D U C T O R SZXSC310ISSUE 2 - MARCH 20046LCD backlightcircuitRef Value Part Number Manufacture CommentsU1N/A ZXSC310E5Zetex Plc Single cell converter,SOT23-5Q1N/A FMMT618Zetex Plc Low V CE(sat )NPN,SOT23D1N/A ZHCS1000Zetex Plc1A Schottky diode,SOT23C1 2.2F Generic Various 0805Size R16150m ⍀Generic Various 1206Size R17250m ⍀GenericVarious1206SizeL1868µHSurface mount inductorMaterials list6Used for 3.3V input,I LED set to 20mA Ϯ10%.7Used for 5V input,I LED to 20mA Ϯ10%.8See Application section.(Notes)ZXSC310ISSUE 2 - MARCH 20047S E M I C O N D U C T O R SThis circuit provides a continuous current output to the LED by rectifying and buffering the DC-DC output.This ensures maximum LED brightness.Ref Value Part Number Manufacturer CommentsU1N/A ZXSC310E5Zetex Plc Single cell converter,SOT23-5Q1N/A FMMT617Zetex Plc LowVCE(sat)NPN,SOT23D11A ZHCS1000Zetex Plc 1A Shottky diode,SOT23R1100m ⍀Generic Various 0805SizeC1 2.2F GenericVariousLow ESR ceramic capacitor L1100µH8Surface mount inductorMaterials list8See Application section.Maximum brightness solution(Notes)To ensure optimum efficiency,and therefore maximum battery life,the LED is supplied with a pulsed current.Maximum efficiency is ensured with the removal of rectifier losses experienced in the maximum brightness solution .S E M I C O N D U C T O R SZXSC310ISSUE 2 - MARCH 20048Ref Value Part Number Manufacturer CommentsU1N/A ZXSC310E5Zetex Plc Single cell converter,SOT23-5Q1N/A FMMT617Zetex Plc Low V CE(SAT)NPN,SOT23R1330m ⍀GenericVarious0805SizeL1100H 8Surface mount inductorMaterials list8See Application section.Maximum battery life solution(Notes)APPLICATIONS INFORMATIONThe following section is a design guide for optimum converter performance.Switching transistor selectionThe choice of switching transistor has a major impact on the converter efficiency.For optimum performance,a bipolar transistor with low V CE(SAT)and high gain is required.The Zetex FMMT618is an ideal choice of transistor,having a low saturation voltage.A data sheet for the FMMT618is available on Zetex web site or through your local Zetex sales office.Outline information is included in the characteristics section of this data sheet.Schottky diode selectionFor the maximum battery life solution a Schottky rectifier diode is not required.As with the switching transistor the Schottky rectifier diode has a major impact on the converter efficiency.A Schottky diode with a low forward voltage and fast recovery time should be used for this application.The diode should be selected so that the maximum forward current is greater or equal to the maximum peak current in the inductor,and the maximum reverse voltage is greater or equal to the output voltage.The Zetex ZHCS1000meets these needs.Datasheets for the ZHCS Series are available on Zetex web site or through your local Zetex sales office.Outline information is included in the characteristics section of this data sheet.For the maximum brightness solution a pulsed current is supplied to the LED and thus a Schottky rectifier diode is required.Inductor selectionThe inductor value must be chosen to satisfy performance,cost and size requirements of the overall solution.For the LCD backlight reference design we recommend an inductor value of 68uH with a core saturation current rating greater than the converter peak current value and low series resistance.Inductor selection has a significant impact on the converter performance.For applications where efficiency is critical,an inductor with a series resistance of 500m ⍀or less should be used.A list of recommended inductors is shown in the table below:ZXSC310ISSUE 2 - MARCH 2004S E M I C O N D U C T O R S9Part No.Manufacture L I PK R DC DO1608C-683Coilcraft 68H 0.4A 0.86⍀CR54-680Sumida 68H 0.61A 0.46⍀P1174.683Pulse 68H 0.4A 0.37⍀SFOP5845-R61680Samwha 68H 0.61A 0.46⍀SIS43-680Delta68H0.41.125⍀Peak current definitionThe peak current rating is a design parameter whose value is dependent upon the overall application.For the high brightness reference designs,a peak current of was chosen to ensure that the converter could provide the required output power to the LED.In general,the I PK value must be chosen to ensure that the switching transistor,Q1,is in full saturation with maximum output power conditions,assuming worse-case input voltage and transistor gain under all operating temperature extremes.Once I PK is decided the value of R SENSE can be determined by:A selection guide of sense resistor and inductor values for given input voltages,output currents and number of LED connected in series is provided in the table below.S E M I C O N D U C T O R SZXSC310ISSUE 2 - MARCH 200410R V I SENSE ISENSE PK=Output Power CalculationBy making the above assumptions for inductance and peak current the output power can be determined by:Note:V OUT =output voltage +Schottky rectifier voltage drop.WhereT OFF ≅1.7us (internally set by ZXSC310)and andWhereOperating frequency can be derived by:Capacitor selectionFor pulsed operation,as in the maximum battery life solution,no capacitors are required at the output to the LED.For rectified operation,as in the maximum brightness solution,a small value ceramic capacitor is required, typically 2.2uF.Generally an input capacitor is not required,but a small ceramic capacitor may be added to aid EMC,typically 470nF to 1uF.(notes)ZXSC310ISSUE 2 - MARCH 200411S E M I C O N D U C T O R S()I I V V T LMIN PK OUT IN OFF=−−×()F T T ON OFF =+1I I I AV PK MIN=+2()T T V V V ON OFF OUT IN IN=−P V V I T T T OUT OUT IN AV OFFON OFF=−××+()Shutdown ControlThe ZXSC310offers a shutdown mode that produces a standby current of less than 5uA when in operation.When the voltage at the S TDN pin is 0.7V or higher the ZXSC310is enabled,hence the driver is in normal operation.When the voltage at the S TDN pin is 0.1V or lower the ZXSC310is disabled,hence the driver is in shutdown mode.If the S TDN pin is open circuit the ZXSC310 is also enabled.Layout of LCD backlighting solutionDemonstration boardA demonstration board for the LCD backlighting solution,is available upon request.These can be obtained through your local Zetex office or through Zetex web pages.For all reference designs Gerber files and bill of materials can be supplied.S E M I C O N D U C T O R SZXSC310ISSUE 2 - MARCH 200412Top SilkDrill FileTop Copper Bottom CopperZXSC310ISSUE 2 - MARCH 200413S E M I C O N D U C T O R SSTDN VCC Gnd ISENSEVDRIVE 12345Top ViewPINOUT DIAGRAMPin No.Name Description1V CC Supply voltage,generally Alkaline,NiMH or NiCd single cell2G nd Ground 3S TDN Shutdown4I SENSE Inductor current sense input.Internal threshold voltage set to 19mV.Connect external sense resistor 5V DRIVEDrive output for external switching transistor.Connect to base ofexternal switching transistor.PIN DESCRIPTIONS(NOTES)S E M I C O N D U C T O R SZXSC310ISSUE 2 - MARCH 200414ZXSC310 (NOTES)ISSUE 2 - MARCH 200415S E M I C O N D U C T O R SS E M I C O N D U C T O R SZXSC310ISSUE 2 - MARCH 200416SCZXSC310DS1EuropeZetex GmbHStreitfeldstraße 19D-81673 München GermanyTelefon: (49) 89 45 49 49 0Fax: (49) 89 45 49 49 49**********************AmericasZetex Inc700 Veterans Memorial Hwy Hauppauge, NY 11788USATelephone: (1) 631 360 2222Fax: (1) 631 360 8222*******************Asia PacificZetex (Asia) Ltd3701-04Metroplaza Tower 1Hing Fong Road, Kwai Fong Hong KongTelephone: (852) 26100 611Fax: (852) 24250 494********************Corporate Headquaters Zetex plcFields New Road,Chadderton Oldham, OL9 8NP United KingdomTelephone (44) 161 622 4444Fax: (44) 161 622 4446************These offices are supported by agents and distributors in major countries world-wide.This publication is issued to provide outline information only which (unless agreed by the Company in writing)may not be used,applied or reproduced for any purpose or form part of any order or contract or be regarded as a representation relating to the products or services concerned.The Company reserves the right to alter without notice the specification, design, price or conditions of supply of any product or service.For the latest product information,log on to ©Zetex plc 2004DIMMillimeters InchesMINMAX MIN MAX A 0.90 1.450.0350.057A10.000.150.000.006A20.90 1.30.0350.051b 0.350.500.0140.020C 0.090.200.00350.008D 2.80 3.000.1100.118E 2.60 3.000.1020.118E1 1.501.750.0590.069e 0.95 REF 0.037 REF e1 1.90 REF 0.075 REF L 0.100.600.0040.024a°1010SOT23-5PACKAGE DIMENSIONSSOT23-5PACKAGE OUTLINE。
MBN_10447_2010-05_EN_Quality Management Standard-Elektrics-Elektronics for Mercedes-Benz Cars_nng
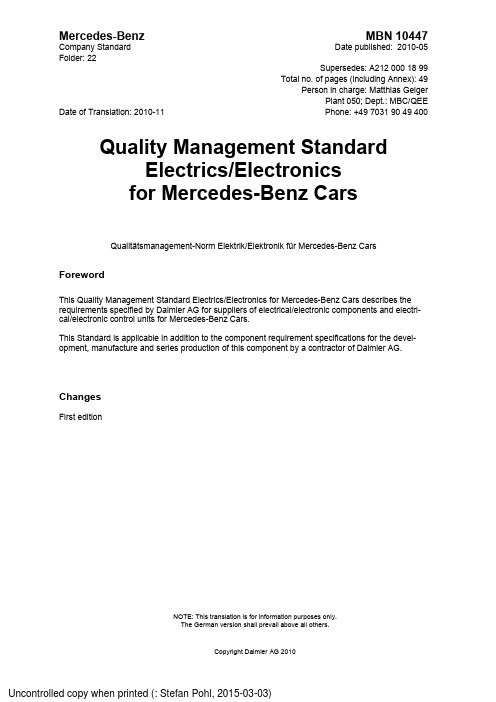
10447 Mercedes-Benz MBN Company Standard Date published: 2010-05Folder: 22Supersedes: A212 000 18 99Total no. of pages (including Annex): 49Person in charge: Matthias GeigerPlant 050; Dept.: MBC/QEEDate of Translation: 2010-11 Phone: +49 7031 90 49 400Quality Management StandardElectrics/Electronicsfor Mercedes-Benz CarsQualitätsmanagement-Norm Elektrik/Elektronik für Mercedes-Benz CarsForewordThis Quality Management Standard Electrics/Electronics for Mercedes-Benz Cars describes therequirements specified by Daimler AG for suppliers of electrical/electronic components and electri-cal/electronic control units for Mercedes-Benz Cars.This Standard is applicable in addition to the component requirement specifications for the devel-opment, manufacture and series production of this component by a contractor of Daimler AG.ChangesFirst editionNOTE: This translation is for information purposes only.The German version shall prevail above all others.Copyright Daimler AG 2010Contents1Scope (5)2Normative references (6)3Terms and definitions (7)3.1List of abbreviations (7)3.2Nomenclature (8)4General requirements (9)4.1Contacts at Daimler AG (9)4.2Contacts at the supplier and its sub-suppliers (10)4.3Key processes (10)5Preventive maturity level management (11)5.1Start of preventive maturity level management (11)5.2Scope (11)5.3Tracking of sub-supplier maturity level (12)5.4Changes following start of production (12)5.4.1Process and sub-process relocation (12)5.4.2Replacement or exchange of machines or equipment (12)5.4.3Change of a sub-supplier (13)6Detection of anomalies (14)7Process capability and product reliability (15)7.1Proof of machine and process capability for SMT processes (15)7.1.1Machine and process capability of paste printer (15)7.1.2Machine capability placement machines (15)7.1.3Verification of solder profile (16)7.2Proof of reliability of the assembly and connection technology (16)7.3Proof of reliability of the devices used (16)7.4Board bending test (17)7.5Requalification (18)7.5.1Complete repeat of the environmental and life tests (18)7.5.2Q-Review Environment E/E (18)8Manufacturing processes for electronic components (20)8.1Storage (20)8.1.1Moisture sensitive devices (20)8.2Printed circuit board magazines (21)8.3Transportation of devices and components (21)8.4Soldering paste printing (21)8.4.1Initial part approval during series production (21)8.4.2Soldering paste (21)8.4.3Paste printer (22)8.4.4Cleaning of the stencil (22)8.4.5Cleaning of circuit boards following soldering paste printing (22)8.4.6Mechanical stress in double-sided PCB assembly (23)8.5PCB assembly (23)8.5.1Initial part approval (23)8.5.2Reel change (23)8.5.3Mechanical stress (23)8.5.4Process control (23)8.5.5Maintenance (23)8.6Assembly and connection technology (24)8.6.1Reflow soldering (24)8.6.1.1Machine malfunctions (25)8.6.1.2Temperature profile (25)8.6.2Press-fit technology (25)8.6.3Selective soldering with mini-wave (26)8.6.3.1Flux (26)8.6.3.2Temperature pretreatment and temperature gradient (26)8.6.3.3Temperature monitoring (27)8.6.3.4Machine malfunctions (27)8.6.3.5Solder residue (27)8.6.3.6Solder bath (27)8.6.3.7Solder filling level (27)9Rework (28)10Test technology in series production (29)10.1Inspection of soldered joints (29)10.1.1Inspection of paste printing (29)10.1.2Inspections after reflow soldering (29)10.1.3Inspections after selective soldering (30)10.1.4Manual visual inspections (30)10.2In-circuit test (30)10.3Contacting of components (31)10.4End-of-line test (31)10.5Test parameters (32)10.6Mechanical interfaces (32)10.7Product audit (32)10.7.1Temperature cycle test (33)10.7.2Additional component-specific tests (33)10.7.3Changes (34)10.8Early defect detection (34)10.8.1Realization of early defect detection (34)10.8.2Active run-in (34)10.9Test coverage analysis (35)10.10Evaluation and reporting of internal test results (36)10.11Haptic measurements (36)10.12Testing of function, switch and controls illumination (37)10.13Noise testing (37)10.14Process documentation and process records (38)10.14.1Soldering paste printing (38)10.14.2Placement machines (38)10.14.3Reflow soldering (38)10.14.4Selective soldering with mini-wave (38)10.14.5Rework (39)10.14.6Test parameters (39)11Mechanical manufacturing processes (40)11.1Circuit board separation (40)11.1.1Milling (40)11.1.2Punching (V-cutting) (40)11.1.3Sawing (40)11.1.4Laser cutting (41)11.2Assembly and screw-fastening processes (41)11.3Zero Insertion Force (ZIF) connectors (41)11.3.1Manual joining of zero insertion force connectors (42)11.3.2Semi or fully automatic joining of zero insertion force connectors (42)11.3.3Testing of the connection of zero insertion force connectors (42)11.3.4Opening of the plug connection of zero insertion force connectors (42)12Traceabilty of devices and components (43)12.1Incoming goods (43)12.2PCB assembly (43)12.3Tests (44)12.4End-of-line test (44)12.5Outgoing goods (44)12.6Rework (44)13ESD (45)13.1ESD protection measures in electronics production (45)13.2Personnel grounding (45)13.3Rework (45)14Flashing of components (46)14.1Handling (46)14.2Contacting and flashing (46)14.3Testing and traceability of flashed components (46)14.4Capacity of the flashing process (47)15Failure analysis (48)15.1Analysis reports (48)15.2Priority failures (48)15.3NTF failures (complaints) (48)15.4Failure analysis on site (48)16On-site support (49)16.1Professional requirements for staff (49)16.2Time-related requirements (49)16.3Other requirements (49)1 ScopeThis Quality Management Standard Electrics/Electronics applies irrespective of the model to all electri-cal/electronic components in general.2 Normative referencesMB Special Terms Mercedes Benz Special Termsof Electronic AssembliesANSI/IPC-A-610D AcceptabilityIPC/JEDEC J-STD-033B.1 Handling, Packing, Shipping and Use of Moisture/ReflowSensitive Surface Mount DevicesDIN EN ISO 9453 Soft Solder Alloys – Chemical Compositions and FormsA2110039899 Design Rules for E/E ComponentsDIN EN 61340-5-1 Protection of Electronic Devices from Electrostatic Phenom-ena — General RequirementsIEC/TR 61340-5-2 Protection of Electronic Devices from Electrostatic Phenom-ena – User GuideDIN EN 61340-4-5 Standard Test Methods for Specific Applications – Methodsfor Characterising the Electrostatic Protection of Footwearand Flooring in Combination with a PersonDIN EN 61340-4-3 Standard Test Methods for Specific Applications – Footwear AEC-Q100 Stress Qualification for Integrated CircuitsAEC-Q101 Stress Test Qualification for Discrete SemiconductorsAEC-Q200 Stress Test Qualification for Passive ComponentsAEC-Q004 Zero Defects Guideline (Draft version)ANSI/IPC J-STD-001D Requirements for Soldered Electrical and Electronic Assem-bliesMBN 10448 Field Failure Analysis3 Terms and definitions3.1 List of abbreviationsTwo-dimensional2DThree-dimensional3DAEC Automotive Electronic Council (body for quality standards in the automotive indus-try)InspectionOpticalAutomatedAOI(Ausführungsvorschrift)regulationAVImplementationBGA Ball Grid Array componentsBR Vehicle model series (Baureihe)cmk Short-term process capabilitycapabilityprocessLong-termcpksupplyspecification (Liefervorschrift)Daimler-BenzDBLDS Identification and documentation of safety relevancedocumentation of certification relevanceandIdentificationDZE/E component Electrical/electronic componentProgrammable Read-Only MemoryEEPROM ElectricallyErasableX-rayspectroscopyEnergy-dispersiveEDXEOL End Of Line testOverStressEOSElectricalDischargeElectroStaticESDFMEA Failure Mode and Effects AnalysisLevelingAirHotHALHIL Hardware In the LoopHardWareHWStandardizationISOforOrganisationInternationalCircuitsIC IntegratedIn-Circuit-TestICTspecifications (Komponentenlastenheft)requirementComponentKLHMBN Mercedes-Benz standard (Mercedes-Benz Norm)SystemDevelopmentMercedes-BenzMDSInterfaceMan-MachineMMIMSD Moisture Sensitive DeviceLevelSensitiveMSLMoistureSystemProductionMercedes-BenzMPSMTTF Mean Time To FailureNTF No Trouble Foundprocess and product approvalPPAProductioncapabilityprocessPreliminaryppkPRG Product maturity level (Produkt-Reifegrad)GateQGQualityQualityManagementQMStatusQ-Status QualityMemoryAccessRandomRAMMemoryOnlyReadROMTemperatureRoomRTUnitControlCUMountedTechnologySurfaceSMTSOP Start of ProductionSoftWareSWTechnologyHoleThroughTHT3.2 NomenclatureBelow, electrical/electronic components and electrical/electronic control units are termed "components" for the reader’s convenience.Below, the contractor of Daimler AG is termed "supplier".Below, the sub-components of components such as circuit boards, electronic devices (e.g. controllers, transceivers, micromechanical semiconductors) and mechanical units (e.g. housings) are termed "de-vices" for the reader’s convenience.Below, requirements for documentation and the recording of data are specified. In this context, "docu-ment" refers to instructions and specifications (e.g. work instructions, process descriptions, etc). The term "record" refers to evidential data (e.g. completed checklists, audit evidence, etc).4 GeneralrequirementsFor safety requirements, homologation and quality, the existing statutory requirements and laws shall be complied with. In addition, the relevant requirements of Daimler AG apply.All materials, procedures, processes, components, and systems shall conform to the current regulatory (governmental) requirements regarding regulated substances and recyclability.This Quality Management Standard Electrics/Electronics makes reference to applicable laws, standards and regulations etc. The supplier shall be responsible for compliance with all laws, standards and regula-tions and for the development and production of the component in line with the state of the art. In this con-text, due consideration shall be given to the fact that the vehicles of Daimler AG containing this compo-nent are sold worldwide.This Quality Management Standard Electrics/Electronics makes reference to other applicable documents of the component requirement specifications (KLH) (specifications, test methods, implementation regula-tions, instructions of Daimler AG). Where this Quality Management Standard Electrics/Electronics contains deviating or contradictory information compared with other standards, specifications or implementation regulations, the more severe specification shall apply. In case of doubt, clarifying agreements following discussions with Daimler AG Quality Management shall be set down in writing.The supplier shall supply conforming products to Daimler AG, and the supplier shall maintain the zero-defect target.If the supplier is aware of measures or alternatives serving to increase quality or reliability, the supplier shall notify these to Daimler AG Quality Management.All information and documents associated with the development, manufacture and production of the com-ponent shall be treated confidentially.4.1 Contacts at Daimler AGThe responsible component developer and other contacts at Daimler AG are listed in the component re-quirement specifications (KLH).Mercedes-Benz Cars Quality Management is divided into two units:- Preventive Quality Management (Prevention) and- Quality Management Production in the worldwide Daimler assembly, body, paintwork and stamp-ing plants (e.g. Sindelfingen, Bremen, Tuscaloosa, South Africa etc.).During the development phase (requirement specification phase up to the launch of the component in production), a staff member from Prevention is the responsible quality contact for the supplier. Together with the responsible staff member from Prevention, the supplier shall hold coordination discussions re-garding quality management requirements. The supplier shall seek approval from the responsible staff member from Prevention for any deviations from these quality management requirements.During the production phase (launch of component in production up to discontinuation of production), a Quality Management staff member from each assembly, body, paintwork and stamping plant is the re-sponsible quality contact for the supplier. The supplier shall seek approval for all changes to the compo-nent or production process during the production phase from the responsible Quality Management staff member from the assembly, body, paintwork and stamping plants. In the event of deviations from the re-lease status of the component, the supplier shall present appropriate measures and samples and have any changes approved.Any deviation from the requirements of this Quality Management Standard Electrics/Electronics are sub-ject to the written approval of Daimler AG Quality Management.4.2 Contacts at the supplier and its sub-suppliersThe supplier shall submit an organizational diagram to Daimler AG Quality Management showing all per-sons responsible for the project and their functions.The supplier shall reveal the complete supply chain of devices for the project to Daimler AG Quality Man-agement. In this process, the supplier shall document the scope of supply and supplier name of each de-vice.4.3 Key processesTo facilitate the successful implementation of the project, the supplier shall provide evidence of docu-mented process structures for the following key processes during the concept presentation:1. Requirements analysis process2. Test strategy process3. Configuration and change management process4. Problem analysis process5. Project management5 Preventive maturity level managementThe objective of preventive maturity level management is to recognize quality-related problems and defi-cits concerning the product and/or production process as early as during the development phase of the component and to be able to initiate countermeasures. Timely completion of the project and defect-free implementation of all specified functions are the top priorities for Daimler AG.The supplier shall document and maintain a preventive maturity level management system. As part of this system, the supplier shall determine and record characteristic data (metrics, process capability indices, inspections, etc.).In this context, all company units of the supplier involved with the product creation process shall be sub-ject to the maturity level management system.Assessment of the maturity level shall be based on the specified quality targets and quality criteria throughout the product and process development process.The supplier shall document compliance with and fulfillment of all requirements from the component re-quirement specifications (KLH) and this Standard.To track all activities during development, the supplier shall maintain a list of open issues, and grant Daim-ler AG Quality Management access to this list on request.The supplier shall submit regular reports to Daimler AG Quality Management regarding maturity level pro-gress. The supplier shall document maturity level reports in writing. The supplier shall record the maturity level reports for the Quality Gates (according to MDS) and submission of A, B, C, D and PPF samples in writing.5.1 Start of preventive maturity level managementThe supplier shall initiate preventive maturity level management at the time of project start - immediately following the commencement of hardware and software development and the start of the production proc-ess.5.2 ScopeThe supplier shall coordinate and document the scope of preventive maturity level management with Daimler AG Quality Management.The preventive maturity level tracking during the product creation process includes the monitoring of the degree of fulfillment of all requirements. In this context, the supplier shall document and record the (func-tional and non-functional) requirements for the component and the production process during the devel-opment phase of the component.The supplier shall carry out an assessment on the basis of the degree of implementation of the require-ments at the relevant project date. The maturity level is divided into four stages:- Requirement not implemented by the deadline- Requirement is in the process of being implemented- Requirement has been implemented by the deadline- Requirement has been implemented and tested successfully by the deadline5.3 Tracking of sub-supplier maturity levelThe supplier shall document and implement a preventive maturity level management system at all sub-supplier companies involved in the project (Tier 2, Tier 3, …).The supplier shall inform Daimler AG Quality Management of the status of the preventive maturity level management if there is a risk of the sub-suppliers involved in the project failing to reach the project objec-tive.On request, the supplier shall grant Daimler AG Quality Management access to records concerning the maturity level management of the sub-suppliers involved in the project.5.4 Changes following start of productionAny changes to the component or an existing manufacturing process shall be subject to the approval of Daimler AG Quality Management and be approved using a PPA process.The supplier shall qualify any change, e.g. in the event of changes to devices (material or manufacturing process of the device) or in the manufacturing process of the component. The supplier shall provide evi-dence of and document qualification in accordance with the component requirement specifications.Deviations from a complete qualification by the supplier shall be subject to the approval of Daimler AG Quality Management.Qualification shall be carried out using components manufactured on the production equipment at the se-rial production location.The documentation of changes shall be coordinated with Daimler AG Quality Management.The supplier shall adhere to a previously defined time frame for pre-advice to Daimler AG Quality Man-agement.In the cases indicated below, the supplier shall inform the following Daimler AG units: Quality Manage-ment, Development, Purchasing and Logistics.5.4.1 Process and sub-process relocationIn the case of any type of process and sub-process relocation, the supplier shall inform Daimler AG Qual-ity Management no later than 9 months before the intended implementation of the change. The supplier shall submit a relocation scenario and seek the approval of Daimler AG Quality Management for such scenario.This time frame also applies to the outsourcing of processes or sub-processes to sub-suppliers.5.4.2 Replacement or exchange of machines or equipmentIn the case of the replacement or exchange of machines or equipment or other systems, the supplier shall inform Daimler AG Quality Management no later than 3 months before the intended implementation of the change.5.4.3 Change of a sub-supplierIn the case of a change of a sub-supplier or manufacturer of a device of the component, the supplier shall submit a change scenario to Daimler AG Quality Management and seek the approval of Daimler AG Qual-ity Management for such scenario. The supplier should inform Daimler AG Quality Management no later than 6 months before the intended implementation of the change.6 Detection of anomaliesThe statistical detection of anomalies is intended for the detection of unusual features in the functionality or measurement parameters. These may be anomalies which lie within the specification limits provided, but are unusual compared to other components. The anomalies may point towards pre-damage to the component.In order to ensure the process capability and product reliability, the supplier shall document and use a method for the detection of anomalies, and provide evidence by means of records.To verify the process capability and product reliability, the supplier shall use this method, starting with the manufacture of initial samples, and create records. Evidence shall be provided no later than at the time of submission of the initial sample documentation.7 Process capability and product reliabilityIn accordance with VDA 2, the supplier shall provide evidence of the process capabilities for its production processes.For the deadline and the required values for the process capabilities, refer to MBST.At the time of submission of the initial samples, the supplier shall document the final evidence of the proc-ess capabilities and product reliabilities required.The initial samples shall be manufactured on production equipment and selected randomly.The supplier shall have any deviations from these specifications approved by Daimler AG Quality Man-agement.7.1 Proof of machine and process capability for SMT processesWithin the framework of the zero-defects strategy in relation to the customer, the supplier shall make every effort to prevent and detect nonconformances. From the point of view of customer satisfaction and with a view to ensuring the quality of the components, it is essential that nonconformances are detected as early as possible and eliminated. The focus shall therefore be on the process capability of the supplier's manufacturing process. This includes the determination of the ongoing process capability, the control of the production process and continuous process improvement.The supplier shall supply regular evidence of the process capabilities of production as a whole and each production process and maintain the appropriate records.7.1.1 Machine and process capability of paste printerThe supplier shall check the machine capability once every year and maintain the pertinent records.Evidence of the machine capability of the paste printer can be provided by means of a reference stencil. The relevant parameters for this purpose are the positioning accuracy in the x and y direction of the solder deposit.The supplier shall check the process capability of the paste printer with the product-specific original stencil and maintain appropriate records. During this process, the supplier shall document reference points and determine their positioning accuracies in x and y position as well as the volume. To do so, the supplier may use the paste AOI provided that the AOI measuring data can be analyzed.7.1.2 Machine capability placement machinesThe supplier shall check the machine capability every other year and maintain the pertinent records.The supplier shall check the machine capability using a glass board and glass devices or ceramic pads and maintain appropriate records. To prove capability, the supplier shall document the critical SMD shapes and test these.7.1.3 Verification of solder profileThe supplier shall verify that the solder profile determined allows each solder joint to reach the required soldering temperature and the required temperature profile. The supplier shall maintain appropriate re-cords.The supplier shall verify that "thermally critical" devices on the circuit board are not overheated. The sup-plier shall maintain appropriate records.The supplier shall observe the specifications of the board, device and soldering paste manufacturers, and provide evidence of compliance. The temperature profile shall therefore be recorded with the printed com-ponent circuit board.7.2 Proof of reliability of the assembly and connection technologyThe supplier shall document the development progress at the time of each delivery of sample parts.At the time of submission of the initial samples, the supplier shall perform a full qualification on the basis of the requirements of the KLH and provide the appropriate evidence.The supplier shall coordinate the number and scope of the tests with Development and Daimler AG Qual-ity Management and document the results.In order to allow the impact of changes on the component to be assessed, the supplier shall document a comparison of measuring results before and after the intended change.Qualification shall be carried out using components manufactured on the series production equipment. 7.3 Proof of reliability of the devices usedOn delivery, the supplier shall provide evidence of device qualification.For ICs, the supplier shall provide evidence of the device qualification in accordance with AEC-Q100, for discrete components in accordance with AEC-Q101, and for passive components in accordance with AEC-Q200.To achieve the zero-defects strategy, the supplier shall document the methods as per AEC-Q004 and provide evidence of the records to Daimler AG Quality Management.The supplier shall have any deviations from these specifications approved by Daimler AG Quality Man-agement.7.4 Board bending testThe supplier shall ensure that soldered circuit boards or devices cannot be damaged as a result of me-chanical stresses. Excessive mechanical stresses result in the danger of the board or devices becoming pre-damaged due to microcracks. The supplier shall support the PCB boards using an appropriate fixture.By means of a board bending test, the mechanical stress to which a soldered circuit board is exposed during the production process can be determined.The supplier shall perform a bending test for the following production steps on the component-specific board and maintain the relevant records:- Paste printer (only for double-sided boards)- SMD placement machines- ICTseparatorboard- Circuit- Press-fit process for contacts- Press-fit and assembly fixtures and jigs for installing boards in a housing- Transport systems, including gripping devices.The supplier shall repeat the board bending test at regular time intervals and record the relevant results.The supplier shall use the bending test for fault finding in the event of failures of devices (e.g. damage, microcracks on ceramic capacitors). The supplier shall record the results and submit them to Daimler AG Quality Management on request.The supplier shall use an appropriate measurement procedure for carrying out the board bending test.The maximum critical bending of boards depends on the individual circuit board or the devices used. The supplier shall take care to ensure that the sensors are positioned on the board at the point of maximum bending.The supplier shall take care to ensure that circuit board is assembled and soldered in line with the relevant process step to be examined.During the processing of ceramic capacitors, the supplier shall ensure that the specifications ofAV A2110039899 "Design Rules for E/E Components“ are complied with for all manufactured compo-nents.7.5 RequalificationThe supplier shall check at least once every year whether its deliveries conform to the specifications of Daimler AG.As a minimum requirement, the test scope shall include evidence that the specifications with regard to dimensional, material, reliability, environmental, process and statutory rules have been complied with.The supplier shall coordinate and document the test scopes with Daimler AG Quality Management. This coordination shall be based on the environmental and lifetime tests specified in the component require-ment specifications (KLH) as well as other specifications such as DBL, MBN, AV, etc.The supplier can choose between the following methods to prove compliance with the specifications of the environmental and life tests required in KLH:- complete annual repeat of the of the environmental and life tests specified in KLH- annual execution of a so-called "Q-Review Environment E/E“.7.5.1 Complete repeat of the environmental and life testsThe supplier shall record the results of the repeat and submit them to Daimler AG Quality Management on request.The supplier shall notify Daimler AG Quality Management of any deviations from the specification without delay.The supplier shall supply regular evidence of the process capabilities of production as a whole and each production process and maintain the appropriate records.If the tests show that the required cp or cpk values are not achieved and that the equipment requires read-justment, the supplier shall shorten the test interval.7.5.2 Q-Review Environment E/ETo perform a "Q-Review Environment E/E“, the supplier is required to comply with the following conditions: The environmental and life tests specified in the KLH have been performed once successfully, and the relevant results recorded.Another condition for the execution of a "Q-Review Environment E/E“ is that the following requirements have been fulfilled during the previous 12 months:- The supplier has used a statistical method for the early detection of faults in production. This method has ensured that 100% of the manufactured parts have been covered, the results recorded and evaluated regularly. All measures defined as part of the early fault detection system during the previous 12 months must have been effectively implemented.- The required qualification tests shall have been passed successfully with regard to any changes to the component or the production process.- All failures during the tests in production have been determined, and the relevant results recorded and regularly evaluated. All measures defined during the previous 12 months shall have been effectively im-plemented.- All measures defined during internal and external audits during the previous 12 months shall have been effectively implemented.- All 0-km failures and field failures during the previous 12 months shall have been analyzed and evalu-ated. Any resulting measures shall have been implemented effectively.。
光学元件技术要求和检验国际新标准

第三,表面特征,涉及:
Part 5 表面面形偏差
Part 6 Part 7 Part 8
中心偏差 表面缺陷公差 表面微观轮廓
第四,其他要求,涉及:
Part 9 表面处理与镀膜
Part10 透镜元件数据旳列表表达
Part11 非公差数据
Part12 非球面
Part13 激光辐射损伤阈值
3.2 一般规范 基本要求:波长:546.07nm 单位:mm 温度:22°±2° 视图:阴影线;无阴影线
提议
• 普及方面:举行短训班,知识讲座等 • 提升方面:
加强新概念旳认识和了解以及 研究报 导有深度旳论文,如PSD旳应用及检验原 则;抛光微缺陷旳定量测试与分级等
• 新国标旳修订方面: • 直接全方面采用? • 修改制定国标?
6 结语
• ISO10110内容及其丰富 • 仅就个人感到主要旳几种内容作粗浅旳
Ra=0.012m ▽14
• ISO10110-7
I. 5/N×A;CN’ ×A; LN”×A”; EA’” II. 5/TV或RV,EA’”
• 用Suface texture
表4.4 措施I用旳疵病原则板旳详细数值
SCRATCH SAMPLE
10 20 40 60 80
DIG SAMPLE
4. 值得关注旳若干问题
1. 分级相反旳要求 材料缺陷-非均匀性及条纹旳分级与国
内原则分级含义恰恰相反。
ISO 数字小
国标 数字小
值大(差) 值小(高) Hoya都如此见附录4.1
Schotl、
附录4.1 国标光学均匀性及条纹度
附录 4.2 几家企业材料非均匀性原则旳比较
附录 4.3
用Δn=eλ/t 求解材料厚 度、均匀性 及波前畸变 旳关系。
优化织布缺陷检测的图像处理和模糊逻辑方法说明书

Optimizing Woven Fabric Defect Detection Using Image Processing and Fuzzy Logic Method at PT.Buana Intan GemilangRatna SafitriSchool of Industrial and System EngineeringTelkom University Bandung, Indonesia *************************Tatang MulyanaSchool of Industrial and System EngineeringTelkom University Bandung, Indonesia*********************************.idAbstract —The development of textile industry which 3rd position in the largest export values in Indonesia prove that the quality of textile must be one of factors that should be considered for all of textile companies. Buana Intan Gemilang is one of the companies that produce woven fabric. This company s produce curtain woven fabric. Quality is the most important factor to reach high level customer satisfaction. To get the best quality of product needs to consider their quality control. According to inspection process in Buana Intan Gemilang, manual inspection for woven fabric defect detection need 19.87 second for average inspection time. Therefore, unbalance of production volume with inspection process cause the bottle neck in inspection process. In this research, proposed designing automated fabric inspection using image processing and Fuzzy Logic Model. This processed uses GLCM as feature extraction with three parameters are cluster shade, cluster prominence, and number of object. The proposed fabric inspection using Fuzzy Logic implemented with MATLAB provides better result in identifying fabric defect and optimizing process time. This research using 120 training data, 80 offline test data, and 80 real time test data. Identification automation defect of woven fabric test data can produce accuracy 97, 5% and averaging process time 1.15 second. This result is better than manually inspection process that took 19.87 second for scanning defect of woven fabric.Keywords optimizing; defect; detection; image-processing; fuzzy logic method; woven-fabricsI. I NTRODUCTIONThe statistical value of the top ten industrial groups with the largest export value in Indonesia., shows that the textile industry is in position with export value of 12.26 billion US $. One of the companies engaged in the textile industry is PT. Buana Intan Gemilang located in Banjaran, West Java. This company produces textile in the form of woven curtains. To produce a product that meets the standards and quality of consumer process quality is required to control the resulting product. This is done by conducting an inspection process on products that have been completed in production in order to meet the standards. At this time, the inspection process on the company is still done manually using the human eye with the help of lighting in the form of lights. Based onobservations to the company the manual inspection process takes longer time to process time of 19.7 seconds because of human limitations. Based on the human error factor there will also be defects that are also missed or not visible if the inspection is done without tools. Based on the company's data the company's production volume is not proportional to the inspection volume so as to cause unspoiled fabrication of fabrics on inspection workstations and result in unmet demand on time. The development of image processing technology will help to overcome the problems in the inspection process in order to reduce the time of the inspection process with more accurate results. This study designs a system that focuses on the optimization of the inspection process to detect the types of defects found on the fabric. Thus, appropriate identification techniques are needed to detect defects. The method used in this research is fuzzy logic method that able to handle ambiguity, and variable uncertainty used [1]. This study supports automation systems to identify defects in fabrics using the fuzzy logic method by replacing the function of human vision into digital image processing. The Supervisory Control and Data Acquisition (SCADA) monitoring system is built based on Graphical User Interface (GUI) by using IGSS software. Development of the SCADA application leverages the Wonderware Information Server with Active Factory and Generic Data Grid in order to obtain reporting system a system that can be accessed online. The researcher has been presented these SCADA such as [2-5]. The modelization for the control system is made using Simulink graphical model. In the process, diagram block is used by [6-7]. Mathematical model for a process control plant is important because it provides key information as to the nature and characteristic of the system which is vital for the investigation and prediction of the system operation. Through mathematical equation model, we can study about the dynamics of the process, stability of the system, design controller etc. The mathematical equation model is used to determine a performance of the system [8-16].International Conference on Industrial Enterprise and System Engineering (IcoIESE 2018)Atlantis Highlights in Engineering (AHE), volume 2II. B ASIC T HEORY AND M ETHODOLOGYQuality is a characteristic that a product is expected to have, and is an important factor for customers to choose a product or service [17, 19]. The quality of a product is inversely proportional to the number of defects. The higher the quality of a fabric the less the defects are in the fabric and vice versa. Type of defect in fabric based on Indonesia National Standard (SNI) 08-0277-1989 consisting of 17 types of defects as contained in TABLE I, type of defects based on manual inspection in the company can be seen in TABLE II, and the equation of both can be seen in TABLE III.TABLE I. T YPES OF D EFECTTS ON F ABRICS BASED ON SNI 08-0277-1989No. Defect TypeDefect Definition1 Nep Nep2 Sub Thread wrapped, Broken yarn, Dirt, Knot thread3 Uneven yarn Big thread, Thread.4 Yarn broken Lacking defective defect , Empty feed defect5 Yarn tense / saggy Wrinkle shrub fabrics, arch.6 Fold lines Cloth folded7Warp linesDifferent thread structures, Comb line, Double warp, Tight warrant, Rare warp, Different types of fiber, Big thread, thread.8 The feed line Double feed, stop mark, Feed tight, Empty feed defect, big thread, thread. 9 Wrong pattern Defect pattern, Wrong shape stamp, Wrong webbing, The stamp pattern misses, Wrong color weaving style10 Bare Different thread structures, Different types of fiber, Empty feed defect 11 Striped Colorlessness, different Color 12 TornHole, torn 13 The thread is not woven Yarn jumping14 Stains Rust stains, Color stains 15 Defect width -16 Feed bias Feed bias including curved feed 17Flaw defects-TABLE II.T HE F ABRIC D EFECT T YPE B ASED ON M ANUAL I NSPECTIONIN PT. B UANA I NTAN G EMILANGNo. Type of Defect1Hairy Empty Feed 2Brodol Empty Feed3Lacking Defective 4 Tense Lacking Defective 5Comb DisabilityNo. Type of Defect6 Card Damage7 Plotting8 Lusi Double 9Long MustacheTABLE III. SIMILARITY OF FABRIC DEFECT TYPE BASED ON SNIAND MANUAL INSPECTION IN PT. BUANA INTAN GEMILANGNo.Defect SimilaritySNIObservation Result1 Nep Hairy Empty Feed2 SlubBrodol Empty Feed 3 Yarn Disconnected Lacking defective 4 Yarn Tense Tense Lacking defective 5 Lusi Line Comb Disability 6 Wrong Pattern Card Damage 7Unfinished YarnPlottingFuzzy model is a process of input in the form of a value converted by fuzzification into fuzzy value at U value which is then processed by inference with fuzzy rule which then reasserted with defuzzification which will determine is output in the form of firm value (crisp) [1]. The use of fuzzy model in this research, can be seen in Fig. 1.Defuzzification is a mapping of the fuzzy set on to a firm value (crisp) [17]. It can be interpreted that Defuzzification is a transformation process that states the change of form of the fuzzy set resulting from fuzzy inference to its assertion value (crisp) based on a defined membership function. The value of defuzzification is the output of the fuzzy logic process. In GUI design extraction features, there are three push buttons used, including browse picture, process, exit, and reset. There are also two axes that serve to display images that exes greyscale and axes identification. In addition, there are four edittex, edittext box after browse picture to display the location of the image taken, edittext box beside the number of objects that function display the value of the number of objects, edittext cluster shade box that displays the value of the cluster shade, and the edittext cluster prominence Which serves to display the value of cluster prominence. In addition, there are three statictext that is writing number of object, cluster prominence, and cluster shade contained in GUI extraction feature. GUI design features extraction can be seen in Fig. 2. Extraction feature results in the value of cluster shade, cluster prominence, and number of objects. Examples of extraction feature results can be seen in Fig. 3.Fig. 2.GUI design of feature extraction.Fig. 3.GUI design result of feature extraction.In designing GUI extraction feature there are four push buttons used, including browse picture, manual, auto, and identification. There are also two axes that serve to display images of exes preview and axes identification. In addition, there are three edittext, edittext box after browse picture to display the location of the picture taken if the mode used there is manual mode, edittext box beside identification that serves to show the identification result, and edittext box beside time functioning display real time image identification time, In addition there is one statictext that is writing time found on the GUI identification. The design view of GUI identification can be seen in Fig. 4.Fig. 4.GUI design result of defect identification.III.R ESULT AND D ISCUSSIONThe steps undertaken in this research is done with the steps as follows that is, take pictures or imagery via MATLAB using the distance of 16 cm camera, light intensity 1600 lux, and 1.3 megapixel. The next step is to change the image of the capture that is still in the form of RGB (Red, Green, Blue) to grayscale. After the image is converted into greyscale form then the image is converted into binary form. Once the image is in a binary image, the next step is to extract the image usingthe GLCM extraction feature to find out the value of cluster shade, cluster prominence, and number of objects. The results of the extraction feature can be seen in TABLE IV.TABLE IV. R ESULT OF THE F EATURE E XTRACTIONType of defect Oil defectLackingDefectiveDefectEmptyfeedDefectNormalCluster Shade -9,04638 -1,00373 -0,01449 0,04977 ClusterProminence-3,29245 0,18070 0,31701 -0,03391Number ofObject2 3 7 0 Identification Defect Defect Defect NormalInput on fuzzy Mamdani is the values of cluster shade, cluster prominance, and number of objects. With membership functions A1 through A9, B1 to B9, and C1 to C9. Furthermore, the value will be the limit for each parameter used. For fuzzy Mamdani output this is normal and defective. The total of the rules used is 729. Identification is done on the 120-data train so that obtained the results of identification as in TABLE V. Based on the table can determine a accuracy rate used equation in (1) is 95%.Accuracy rate = (Amount of data is correct)/(Total test data) x 100% (1)TABLE V. I DENTIFICATION R ESULT OF THE T RAINING D ATANo. Image DataTypeInput TrainingdataOutput ModelTrue False1 Oil Defect 30 30 02 LackingDefectivedefect30 30 03 Empty Feeddefect30 30 04 Normal 30 24 6In the offline system the process of detecting defects is done without being integrated with software and hardware other than camera and excel database. The fabrics to be classified are derived from camera captures that have been stored in the database. Matlab software is used to process images taken from the database for identification. TABLE VI shows results of offline identification. Based on the formula, the accuracy of the test data using the fuzzy model with the triangular representation of the fuzzy membership function, fuzzy mamdani inference, and centroid deffuzification, and 729 fuzzy rules is 93.75%.TABLE VI. O FFLINE I DENTIFICATION R ESULTImage Data Input Training Output ModelNo. Type data True False1 Oil Defect 20 20 02LackingDefectivedefect20 20 03Empty Feeddefect20 20 04 Normal 20 15 5In the automatic fabric defect identification system, the process of detecting defects is already integrated with software and other hardware, i.e. PLC, HMI, inverter, motor, webcam, and excel database. Cloth to be classified comes from the results of camera capture in real time. MATLAB software is used to process images taken from the capture process in real time for identification. After the previous fuzzy rules and deffuzification value ranges obtained from the training data, the next step is to test the value against 80 test data. The test results on 80 test data in real time system can be seen in TABLE VII. Based on the formula, the accuracy of test data using fuzzy model with integrated human machine interface system, PLC, database is 97.5%. Trials were conducted to analyze the accuracy and analyze the average processing time. The result of processing time from 80 test data in real time system can be seen in TABLE V.TABLE VII. O NLINE I DENTIFICATION R ESULTNo.Image DataTypeInput TrainingdataOutput ModelTrue False1 Oil Defect 20 20 02LackingDefectivedefect20 19 13Empty Feeddefect20 20 04 Normal 20 19 1From the data table process time 80 test data, obtained the average time for the identification of test data with integrated system of 1.150148 seconds. TABLE VIII shows data processing time identification of automatic fabric defects.TABLE VIII. I DENTIFICATION R ESULT OF D ATA P ROCESSING T IMETestingData ProcessTimeTestingDataProcessTime1 4.32 41 1.244042 3.04 42 0.733393 2.98 43 0.723564 2.88 44 0.707535 2.86 45 0.66115 … … … …Testing Data ProcessTimeTestingDataProcessTime20 2.99 60 0.8144321 1.76464 61 0.6926622 1.73764 62 0.7017123 1.47355 63 0.6778624 1.61301 64 0.6752625 1.74046 65 0.68613… … … …40 1.74136 80 0.69093In the existing process, there is an average time to do a recap of data manually by filling form defects. In this study, the form of defects replaced with a database of excel. Automatic data recap time can be seen in TABLE IX. From the data table recap time 80 test data, obtained the average time for the process of recording test data with an integrated system of 3.54 seconds. Based on the research that has been done, the comparison of processing time from the existing system that is still manual with the system of ideas that have been automated can be seen in TABLE X. Based on TABLE X, process time required to perform scanning process defects in the existing process by manual in the company is equal to 19.87 seconds, while using the automatic defect detection tool that has been integrated to be reduced by the process time of 1.16 seconds. For a manual defect recap in the company takes 13.5 seconds, while using an automated tool is reduced to 3.54 seconds. For the total overall activity, the existing process takes an average time of 33.37 seconds and for the proposed system takes 4.67 seconds. Thus, the decline in processing time for the all system amounted to 28.69 seconds.TABLE IX. R ECAP T IME O NLINE I DENTIFICATION R ESULTTesting Data ProcessTimeTestingDataProcessTime1 4.3241 3.912 3.04 42 3.773 2.98 43 3.834 2.88 44 3.925 2.86 45 3.75 … … … …20 2.99 60 3.9121 2.93 61 3.9222 2.99 62 3.8123 3.26 63 3.93TestingDataProcessTimeTestingDataProcessTime24 3.03 64 3.7425 3.09 65 3.87… … … …40 3.69 80 3.79TABLE X. C OMPARISON OF E XISTING AND P ROPOSED S YSTEMSNo. Activity Existing(Seconds)Proposed(Seconds)1 Defect Scanning 19.87 1.162 Defect Recap 13.50 3.54Process Time 33.374.68IV.C ONCLUSIONImage processing is required to improve accuracy and to reduce inspection time. The use of fuzzy logic method in image processing with GLCM extraction feature and cluster shade parameter, cluster prominence, and number of object is a step proposed in this research. Thus, fuzzy logic applied by using MATLAB software can give better result in detecting defects in fabric. The process time required to perform the scanning process of defects in the existing process by manual in the company is 19.87 seconds, while using the automatic defect detection tool that has been integrated to be reduced with a process time of 1.16 seconds. For a manual defect recap in the company takes 13.5 seconds, while using the automated tool is reduced to 3.54 seconds for the total activity, the existing process takes an average time of 34.08 seconds and for the proposed system takes 4.67 seconds. Thus, the decrease of process time for the all system is 28.69 seconds. Accuracy rate obtained in the training data of 95%, on the offline test data of 93.75% and on the real-time test data of 97.5%R EFERENCES[1]Mulato, F. Y., 2014. Klasifikasi Kematangan Buah Jambu Biji Merah(Psidium Guajava) dengan Menggunakan Model Fuzzy. In: SKRIPSI.Yogyakarta: Universitas Negeri Yogyakarta.[2]H. Rachmat, T. Mulyana, S.H. Hasan, M.R. Ibrahim, Design Selectionof In-UVAT Using MATLAB Fuzzy Logic Toolbox, Proceedings of SCDM 2016.[3]R.A. Anugraha, T. Mulyana, Monitoring and Controlling of EMS-SCADA via SMS Gateway, Proceedings of the 3rd International Conference on Information and Communication Technology 2015 (ICoICT 2015), pp. 615-619.[4]H. Rachmat, R.A. Anugraha, T. Mulyana, EMS-SCADA Design ofAC Usage on a Building, Proceeding 8th International Seminar on Industrial Engineering and Management 2015 (ISIEM 2015), PS45-49.[5]H. Rachmat, T. Mulyana, Website Design of EMS-SCADA for ACUsage on a Building, Proceedings of the 3rd International Conference on Information and Communication Technology 2015 (ICoICT 2015), pp. 17-22.[6] F.D.M. Fauzi, T. Mulyana, Z.I. Rizman, M.T. Miskon, W.A.K.W. Chek,M.H. Jusoh, Supervisory fertigation system using interactive graphical supervisory control and data acquisition system, International Journal on Advanced Science, Engineering and Information Technology, 2016, Vol. 6, Issue No. 4, pp. 489-494.[7]T. Mulyana, M.N.M. Than, D. Hanafi, A. Ali, Digital control designfor the boiler drum BDT921, Proceeding of Conf. on Industrial and Appl. Math., Indonesia 2010, pp. 257-260.[8]T. Mulyana, M.N.M. Than, D. Hanafi, I. Muhaimin, Simulation ofvarious PI controllers setting for boiler drums T11 QAD Model BDT 921, IndoMS International Conference on Mathematics and its Applications 2009 (IICMA 2009), UGM, Yogyakarta - Indonesia, Oct 12-13, 2009 034/Mulyana/IICMA/2009.[9]T. Mulyana, M.N.M. Than, N.A. Mustapha, Identification of heatexchanger QAD Model BDT 921 based on hammerstein-wiener model, Proceedings of the International Seminar on the Application of Science & Mathematics 2011 (ISASM 2011).[10]T. Mulyana, M.N.M. Than, D. Hanafi, A discrete time model of fourheat exchanger types HE158C, Proceedings of the 7th International Conference on Heat Transfer, Fluid Mechanics and Thermodynamics (HEFAT2010), 19-21 July 2010, Antalya, Turkey.[11]T. Mulyana, M.N.M. Than, D. Hanafi, A Discrete Time Model ofBoiler Drum and Heat Exchanger QAD Model BDT 921, Proceedings of the International Conference on Instrumentation, Control & Automation (ICA2009), October 20-22, 2009, Bandung, Indonesia, pp.154-159. [12]T. Mulyana, F.N. Suhaimi, D. Hanafi, M.N.M. Than, ARX Model ofFour Types Heat Exchanger Identification, Proceedings of the MUiCET 2011.[13]T. Mulyana, NNARX model structure for the purposes of controllerdesign and optimization of heat exchanger process control training system operation, AIP Conference Proceedings 1831, 020040 (2017).[14]T. Mulyana, M.N.M. than, Identification of Co Current Plate HeatExchanger Model HE158C, Proceedings of 2010 IEEE Student Conference on Research and Development (SCOReD 2010), 13 - 14 Dec 2010, Putrajaya, Malaysia.[15]T. Mulyana, A nonparametric system identification based on transientanalysis with plant process of heat exchanger as study case, International Journal of Innovation in Mechanical Engineering & Advanced Materials (IJIMEAM) Vol.1 (No.1). 2015. pp. 19-26 Published online: December 1, 2015, ISSN: 2477-541X.[16]T. Mulyana, J. Alhilman, E. Kurniawan, Data Analysis using SystemIdentification Toolbox of Heat Exchanger Process Control Training System, Proceedings of the 2016 Fourth International Conference on Information and Communication Technologies (ICoICT 2016), pp. 466-471.[17] D. C. Montgomery, Design and Analysis of Experiments, New York:John Wesley and Sons, 2013.[18]Wang, Li-Xing, A course in Fuzzy System And Control. Pretice Hall,1997.[19]M.P. Groover, Otomasi Sistem Produksi dan Computer-IntegratedMnufacturing.New Jersey:Pearson, 2001.。
- 1、下载文档前请自行甄别文档内容的完整性,平台不提供额外的编辑、内容补充、找答案等附加服务。
- 2、"仅部分预览"的文档,不可在线预览部分如存在完整性等问题,可反馈申请退款(可完整预览的文档不适用该条件!)。
- 3、如文档侵犯您的权益,请联系客服反馈,我们会尽快为您处理(人工客服工作时间:9:00-18:30)。
s c i e n c eSelected copper(I) complexes as potential anticancer agentMichał PŁOTEK, Karol DUDEK, Agnieszka KYZIOŁ – Jagiellonian University in Krakow, PolandPlease cite as: CHEMIK 2013, 67, 12, 1181–1190IntroductionCancer is the second most frequent cause of death in the world [1]. The discovery of antitumor activity of cisplatin began a search for other metal complexes with cytotoxic properties against cancer cells. One of the transition metal, whose complexes are extensively tested for antitumor application is copper. Copper is a trace element essential for human life. It is a building element of several important enzymes (e.g. superoxide dismutase, cytochrome oxidase, tyrosinase) and it regulates the intracellular redox potential, while its complexes possess antibacterial, antifungal, antiviral, anti-inflammatory and anticancer properties. As potential anticancer drugs, there are currently extensively studied mainly complexes of copper(II). There are only few complexes of copper(I) in the literature, whereas they also show a very strong cytotoxic activity against tumor cells in vitro [2].Anticancer activity of copperOver 95% of copper (both Cu(II) and Cu(I)) that is present in serum is bound to ceruloplasmin (ferroxidase). However, it is not responsible for transporting copper inside the cell. Before they enter the cell, copper(II) ions are reduced to copper(I) by metalo-reducatases located on the cell’s surface. Cu + ions are transported into the cell mainly by a specific copper transporter (hCtr). The independent system of entering the cell, enables biologically active copper compounds to penetrate the cell surface without binding to other agents as opposite to coordination compounds of other metals [2÷4].Anticancer activity of copper(I) compounds may be a result of different mechanisms. They are described in the following paragraphs of this review.Anticancer activity of copper complex compounds is related to their ability to produce reactive oxygen species (ROS). Copper(I) ions can reduce hydrogen peroxide to hydroxyl radical. Copper(II) ions may in turn be reduced to Cu(I) by superoxide anion(O 2•-), or glutathione. Therefore, it can be concluded that the production of reactive oxygen species such as OH • are driven by the copper, regardless of the form in which it is initially introduced into the body – Cu +, or Cu 2+ [2, 5].Cu 2+ + O 2•– → Cu + + O 2Cu + + H 2O 2 → Cu 2+ + OH • + OH –Superoxide anion (O 2•-) is the product of reduction of the molecular oxygen that occurs in many biological processes. It is converted into hydrogen peroxide through dismutation. Both of these forms of ROS lead to the formation of another type of reactive oxygen species – the hydroxyl radical (OH •). It occurs in a reaction catalysed by copper (or iron) ions. This radical is believed to be the main factor causing DNA damage in cells under oxidative stress [6].Copper compounds are also thought to have nuclease activity. The ability of copper to cut a DNA helix has been proved in studies conducted with the use of Cu(I) complexes with two molecules of 1,10-phenanthroline (phen). [Cu(phen)2]+ was initially non-covalently bound to DNA. In this form, it was oxidized to a copper(II) compound in the presence of hydrogen peroxide. The final result of those processes was cutting DNA or RNA strands into fragments. The postulated factor directly responsible for cutting the DNA was an adduct in which [Cu(phen)2]2+ was coordinated with the hydroxyl radical OH • and linked by non-covalent interactions with DNA [7, 8].Copper compounds coordinated to phenanthroline skeleton ligands (see Fig. 1), such as [Cu(dmp)2]+, are thought to have the ability of intercalation. Furthermore, it was indicated that the [Cu(dmp)2]+ (dmp=2,9-dimethyl-1,10-phenanthroline) can be an inhibitor of the process of DNA transcription [9]. The [Cu(bcp)2]+ (bcp=2,9-dimethyl-4,7-diphenyl-1,10-phenanthroline) is in turn believed to possess the ability of forming bridges between double-stranded fragment of DNA and another fragment of such a type [10].Selected cuprous complexesSelected complexes of copper(I), which were extensively investigated for anticancer activity, are presented in the subsequent paragraphs. Diversity of ligands used to synthesize those complexes causes that each one could possess other mechanism of action.Mononuclear compoundsIn 1987 Berners-Price and co-workers [11] presented copper(I) complexes with molecular formula [Cu(P-P)2]Cl, where central Cu + ion was coordinated with two molecules of bidentate phosphine. The structures of these complexes are presented in Figure 1.Fig. 1. The structures of copper(I) complexes with bidentate phosphineCytotoxicity of compounds 1B and 1C are several times higher than the one presented by uncoordinated ligands tested in the same cell line. Compound 1D possesses anticancer activity (only in vitro ), however it is lower than in 1B and 1C . Moreover, 1C also possesses in vivo anticancer activity. Additionally, the equilibrium between mononuclear [Cu(dppe)2]Cl and binuclear form (CuCl)2(dppe)3 is observed in 1A solution. For this reason cytotoxicity cannot be unambiguously assigned to mononuclear [Cu(dppe)2]Cl [11].In order to increase solubility of copper(I) complexes in water, Marzano et al. introduced the hydroxyl groups to analysed phosphines. It is worth to mention that introduction of OH does not destabilize cuprous complexes. Structure of copper(I) complex ion of compound [Cu(thp)4][PF 6] (2), synthesized by the same research group, is shown in Figure 2. In this compound central ion Cu + iscoordinated with four molecules of tris(hydroxymethyl)phosphine.s c i e n c eFig. 2. Complex ion of the compound [Cu(thp)4][PF 6][Cu(thp)4][PF 6] exhibits even 40-fold higher cytotoxicity than cisplatin (e.g. for colorectal adenocarcinoma cell line CaCo-2: IC 50 =1.08 ± 0.12 µM for 2, IC 50 = 35.42 ± 1.40 µM for cisplatin; 48-hours test) [12]. Moreover, in survey performed on cancer cells of a colon 2 reacts selectively with cancer cells, but at the same time it is not harmful for healthy cells. The selectivity is higher than the one observed at cisplatin or oxaliplatin – the drug applied in colorectal cancer treatment (e.g. for non-tumour human fibroblasts cell line MRC-5: IC 50 = 32.67 ± 1.34 µM for 2, IC 50 = 19.66 ± 1.31 µM for cisplatin and IC 50 =23.93 ± 1.35 µM for oxaliplatin; 72-hours test) [13]. What is more, this compound is effective in case of those types of cancer which are resistant to platin complexes (e.g. for colon carcinoma cell line LoVo IC 50=2.05 ± 0.43 µM for oxaliplatin, 1.37 ± 0.35 µM for compound 2, whereas for resistant to oxaliplatin cell line LoVo-OxPt IC 50=10.89 ± 1.34 µM for oxaliplatin and IC 50=1.46 ± 0.27 µM for 2; 48-hours assay) [13]. The described complex of copper leads to cell death via nonapoptotic way (so-called type III cell death). Cell death is not caused by DNA fragmentation. What is more, activation of caspases does not take place. On the contrary, 2 may even inhibit caspases 3 and 7. Characteristic of this type of cell death are: massive cytoplasmic vacuolization, endoplasmic reticulum stress and inhibition of proteasome 26S functions. Furthermore, an increased production of reactive oxygen species (ROS) was observed, which caused an oxidative stress and led cells to death. It was unexpected that the complex [Cu(bhpe)2][PF 6] synthesized by the same research group (Fig. 3), where monodentate phosphines were replaced by bidentate phosphines, would show only an inconsiderable anticancer activity. It was much lower not only than 2, but also than cisplatin (e.g. for colorectal adenocarcinoma cell line CaCo-2: IC 50 = 52.50 ± 0.81 µM for 3, IC 50 = 1.08 ± 0.12 µM for 2, IC 50 = 35.42 ± 1.40 µM for cisplatin; 48-hours test) [12].The reason for an insignificant cytotoxicity of compound 3 could be its high stability and inertness in process of ligands exchange. It could be confirmed by results obtained from a mass spectrometry. For complex 3 no fragmentation was observed, as opposed to 2, in whose spectrum not only [Cu(thp)4]+ ion peak was observed, but also peaks ascribed to [Cu(thp)3]+ and [Cu(thp)2]+. It can be concluded that ability to exchange ligands has crucial influence for cytotoxicity of the described complexes [12,13].Fig. 3. Complex ion of compound [Cu(bhpe)2][PF 6]Anticancer activity is exhibited by copper(I) complexes possessing pyridine-type ligands (pyridine, bipyridine, phenanthroline ect.), or such where copper(I) ion is coordinated to phosphine ligands. Presumably, introduction of both types of ligands mentioned to one molecule would make it possible to create a compound with an increased activity against cancer cells. Marzano research group, mentioned before, synthesized complexes depicted in Figure 4, which contained triazolylborate ligands.Fig. 4. Complexes of Cu + with triazolylborate ligandsThese compounds present activity higher than the one observed at cisplatin for all cell lines tested (Tab. 1), especially for lung adeno-carcinoma cells (A549 cell line), where the IC 50 value was approxi-mately 17-fold lower for compound 4B (IC 50 = 2.35 ± 0.9 µM) and 26-fold lower for complex 4A (IC 50=1.52 ± 0.7 µM), than for tested in the same condition cisplatin (IC 50=39.27 ± 1.9 µM; 48-hours test) [14]. The mechanism of the action has been unknown so far. Howe-ver, it is posited that it could be similar to that exhibited by copper(I) complex showed in Figure 5.Fig. 5. Complex of Cu(I) leading to cell death in a nonapoptotic wayCompound 5 exhibits activity from 2 to 19 times higher than cisplatin for investigated cell lines (e.g. for breast cancer cell line MCF-7 IC 50=1.55 ± 0.19 µM for 5 and IC 50 = 30.18 ± 1.5 µM for cisplatin; 48-hours test) [15]. In vitro tests suggest that the complex mentioned leads to cell death in a nonapoptotic pathway, as it was observed at[Cu(thp)4][PF 6] (2). Lack of caspase 3 activity, an increase in a cell size and a cytoplasmic vacuolization confirm this hypothesis [15].Other interesting compound revealing much higher cytotoxicity than cisplatin is a coordination compound of copper(I) displayed in Figure 6 (e.g. for colon carcinoma cell line HCT-15 IC 50=1.05 ± 0.31 µM for 6 and IC 50 = 16.65 ± 2.63 µM for cisplatin) [16].Fig. 6. Electrically neutral copper(I) complexs c i e n c eDue to the fact that the applied tridentate ligand simultaneously neutralizes positive charge of Cu + ion, the received compound 6 is electrically neutral. A mechanism of cellular internalization has not been explained so far. It is assumed that penetration of a cell membrane is not supported by human copper transporters (hCtr), which can transfer positively charged molecules. As the authors postulate, a dentate ligand could be the factor, which supports complexes’ transfer. It acts as ionophore, as it was the case with copper(II) complexes [16, 17].Coordination number 4 is not the only one possible coordination number for copper(I) complexes. In Figure 7 a two-coordinated compound of Cu + is depicted. In vitro cytotoxic activity of the presented compound was approximately 2,5-fold higher than the one measured for cisplatin. What is remarkable, this effect was also observed for cell lines resistant to cisplatin (e.g. for sensitive to cisplatin human ovarian cancer cell line 2008 IC 50 = 1.84 ± 0.32 µM for 7 and 3.12 ± 1.03 µM for cisplatin; in case of resistant to cisplatin human ovarian cancer cell line C13* IC 50 is 2.08 ± 0.72 for 7 and 22.18 ± 2.01 for cisplatin; 72-hours assay) [18]. Presumably, mechanism of activity of compound 8 is connected with its confirmed ability to disturb respiration by altering mitochondrial membrane potential and producing reactive oxygen species [18].Fig. 7. T wo-coordinated complex of Cu(I)Starosta et al. [19÷24] synthesized copper(I) complexes, whose general structure is displayed in Figure 8.Fig. 8. General structure of copper(I) complexes containing phosphine, phenanthroline-type ligand and iodide ionThe obtained complexes show high cytotoxicity not only to human ovarian carcinoma cell lines sensitive to cisplatin, but also to those resistant to this drug (for resistant to cisplatin human ovarian carcinoma cell line SKOV 3 IC 50 is approximately 2–3 µM depending on examined copper(I) compounds, whereas for cisplatin IC 50 = 180.5 ± 9.3 µM; for sensitive to cisplatin human ovarian carcinoma cell line MDAH 2774 IC 50 is approximately 2–7 µM for analysed copper(I) complex and 77.2±7.6 µM for cisplatin; 24-hours test) [19]. As the authors proved, activity exhibited by investigated cuprous compound is many times higher than the one presented by uncoordinated diimine or phosphine ligands (IC 50:100–500 µM in case of both cell lines: SKOV 3 and MDAH 2774) [19÷24].Polinuclear compoundsIn 2010 Balakrishna and co-workers [25] exhibited group of polinuclear copper(I) complexes, which possessed in their coordination sphere both pyridine-type and phospine-type ligands. In Figures 9 and 10 examples of synthesized compounds are depicted.Fig. 9. Binuclear copper(I) complexes synthesized by Balakrishna et alFig. 10.Octanuclear Cu + compound synthesized by Balakrishna et alAntiproliferative activity for cervical cancer cells was proved for all three copper complexes presented in Figures 10 and 11. Moreover, it was observed that inhibition of proliferation was more effective for the complexes discussed, than for cisplatin, especially for 9B (antiproliferative ability was assessed as a percent of inhibition of cervical cancer HeLa cell line proliferation: 50 ± 4 % for 9A , 62 ± 9 % for 10, 100 % for 9B and 49 ± 7 % for cisplatin; in 10 µM concentration) [25]. Biological tests carried out with the use of this complex show that 9B inhibits proliferation not only of cervical cancer cells, but also of human breast cancer cells and Chinese hamster ovary cells. Moreover, it is several times more efficient than cisplatin. Furthermore 9B has an ability to damage the DNA integration, block cell cycle in G1 phase and induce apoptosis [25].Another interesting binuclear cuprous compound revealing anticancer activity, is depicted in Figure 12 complex with formula [Cu 2(dppe)3(CH 3CN)4](ClO 4).s c i e n c eFig. 11. [Cu 2(dppe)3(CH 3CN)4](ClO 4)2The anticancer activity of compound 11 was confirmed by tests carried out on several cell lines (Table 1) [26]. 11 managed to damage DNA helix, inhibit processes of its synthesis, stop cell cycle in G1 and G2 phases and induce apoptosis. If 11 and adriamycin (drug in cancer therapy) are used simultaneously in treatment, synergism of action is observed. 11 increases therapeutic effect of adriamycin and vice versa. It is believed that 11 binds to DNA by displacement of acetonitrile molecules. Simulations with a use of molecular modelling methods imply that the most profitable donor of a pair of electrons is the atom N7 of guanine. Since in one molecule of 11 two Cu + ions are present, the discussed copper(I) complex acts as chelate agent. It creates two bonds with DNA, as a result of replacement of two acetonitrile molecules for two guanine molecules of deoxyribonucleic acid. Mutual strengthening of anticancer activity between 11 and adriamycin suggests that both agents bind to other helix regions. Moreover each one causes changes in DNA in a way that facilitates binding of the second one [27].SummaryMechanisms of anticancer activity discussed in this article are presented on Scheme 1. Copper(I) coordination compounds described in this review are in turn collected in Table 1. It summarises their biological activity and types of cell line, in which complexes were tested in vitro .Copper(I) compounds may become an alternative for cisplatin, which possesses a few drawbacks but is still most popular. Copper, as an essential element for human life is supposed to be less toxic than other metals, like platinum or ruthenium, analysed for medical application. Both copper ions, Cu + and Cu 2+ can induce oxidation stress via catalysis and production of reactive oxygen species. Superiority of copper(I) compounds over copper(II) compounds results from nuclease activity of Cu + complexes and selectivity exhibited by human copper transporters (hCtr) in introduction of Cu + ions to cells. Copper as an antibacterial agent is used in hospitals, health centres and public buildings for various sanitary applications (for instance handles, holders, handrails ect.) [28]. As it was presented in this article, copper(I) coordination compounds have remarkable application potential. Intensive research may enable to finally apply them as anticancer drugs.Scheme 1. Selected examples of anticancer activity and modeof action of Cu(I) complexesT able 1Biological activity of described cuprous complexesLiteratureAmerican Cancer Society, Global Cancer – Facts & Figures 2007, p. 11. Marzano C., Pellei M., Tisato F ., Santini C.: Copper Complexes as Antican -2. cer Agents. Anti-Cancer Agents Med. Chem. 2009, 9, 185–211Puig S., Lee J., Lau M., Thiele D.J.: Biochemical and Genetic Analyses of3. Yeast and Human High Affinity Copper T ransporters Suggest a Conserved Mechanism for Copper Uptake. J. Biol. Chem. 2002, 277, 26021–26030s c i e n c ePuig S., T 4. hiele D.J.: Molecular mechanisms of copper uptake and distri -bution. Curr. Opin. Chem. Biol. 2002, 6, 171–180Tisato F ., Marzano C., Porchia M., Pellei M., Santini C.: Copper in Di -5. sease and T reatments, and Copper-Based Anticancer Stretegies. Med. Res. Rev. 2010, 30, 4, 708–749Ścibior-Bentkowska D., Czeczot H.: Komórki nowotworowe a stres6. oksydacyjny. Postępy Hig. Med. Dosw. 2009, 63, 58–72Thederahn T .B., Kuwabara M.D., Larsen T .A., Sigman D.S.: Nuclease7. Activity of 1,10-Phenantroline-Copper: Kinetic Mechanism. J. Am. Chem. Soc. 1989, 111, 4941–4946Sigman D.S., Mazumder A., Perrin D.M.: Chemical Nucleases. Chem.8. Rev. 1993, 93, 2295–2316McMillin D.R., McNett K.M.: Photoprocesses of Copper Complexes9. That Bind to DNA. Chem. Rev. 1998, 98, 1201–1219Liu F ., Meadows K.A., McMillin D.R.: DNA-binding studies oc Cu(bcp)10. 2+and Cu(dmp)2+: DNA Elongation without Intercalation of Cu(bcp)2+. J. Am. Chem. Soc. 1993, 115, 6699–6704Berners-Price S.J., Johnson R.K., Mirabelli C.K., Faucette L.F ., McCabe11. F .L., Sadler P .J.: Copper(I) Complexes with Bidentate T ertiary Phosphine Ligands: Solution Chemistry and Antitumor Activity. Inorg. Chem. 1987, 26, 3383–3387Marzano C., Gandin V ., Pellei M., Colavito D., Papini G., Gioia Lobbia12. G., del Giudice E., Porchia M., Tisato F ., Santini C.: In Vitro Antitumor Activity of the Water Soluble Copper(I) Complexes Bearing the T ris(hy -droxymethyl)phosphine. J. Med. Chem. 2008, 51, 798–808Gandin V ., Pellei M., Tisato F ., Porchia M., Santini C., Marzano C.: A no -13. vel complex induces paraptosis in colon cancer cells via the activation of ER stress signaling. J. Cell. Mol. Med 2012, 16, 142–151Marzano C., Pellei M., Alidori S., Brossa A., Gioia Lobbia G., Tisato14. F ., Santini C.: New copper(I) phosphane complexes of dihydrobis(3-nitro-1,2,4-triazolyl)borate ligand showing cytotoxic activity. J. Inorg. Biochem. 2006, 100, 299–304Marzano C., Pellei M., Colavito D., Alidori S., Gioia Lobbia G., Gandin15. V ., Tisato F ., Santini C.: Synthesis, Characterization, and in Vitro Anti -tumor Properties of T ris(hydroxymethyl)phosphine Copper(I) Comple -xes Containing the New Bis(1,2,4-triazol-1-yl)acetate Ligand. J. Med. Chem. 2006, 49, 7317–7324Porchia M., Dolmella A., Gandin V ., Marzano C., Pellei M., Peruzzo16. V ., Refosco F ., Santini C., Tisato F .: Neutral and charged phosphine/scorpionate copper(I) complexes: Effects of ligand assembly on their antiproliferative activity. Eur. J. Med. Chem. 2013, 59, 218–226Tardito S., Bassanetti I., Bignardi C., Elviri L., T egoni M., Mucchino C., Bus -17. solati O., Franchi-Gazzola R., Marchio L.: Copper Binding Agents Acting as Copper Ionophores Lead to Caspase Inhibition and Paraptotic Cell Death in Human Cancer Cells. J. Am. Chem. Soc. 2011, 133, 6235–6242Zanella A., Gandin V ., Porchia M., Refosco F ., Tisato F ., Sorrentino F .,18. Scutari G., Rigobello M.P ., Marzano C.: Cytotoxicity in human cancer cells and mitochondrial dysfunction indeuced by a series of new cop-per(I) complexes containing tris(2-cyanoethyl)phosphine. Invest. New Drugs 2011, 29, 1213–1223Starosta R., Stokowa K., Florek M., Król J., Chwiłkowska A., Kulbac -19. ka J., Saczko J., Skała J., Jeżowska-Bojczuk M.: Biological activity and structure dependent properties of cuprous iodide complexes with phe-nanthrolines and water soluble tris (aminamethyl) phosphanes. J. Inorg. Biochem. 2011, 105, 1102–1108Starosta R., Puchalska M., Cybińska J., Barys M., Mudring A.V .: Structures,20. electronic properties and solid state luminescence of Cu(I) iodide comple-xes with 2,9-dimethyl-1,10-phenanthroline and aliphatic aminomethylpho-sphines or triphenylphosphines. Dalton T rans. 2011, 40, 2459–2468Starosta R., Brzuszkiewicz A., Bykowska A., Komarnicka U.K., Bażanów21. B., Florek M., Gadzała Ł., Jackulak N., Król J., Marycz K.: A novel cop -per(I) complex, [CuI(2,2’-biquinoline)-P(CH 2N(CH 2CH 2)2O)3] – Syn-thesis, characterisation and comparative studies on biological activity. Polyhedron 201, 50, 481–489Starosta R., Komarnicka U. K., Puchalska M., Barys M.: Solid state lumi -22. nescence of copper(I) (pseudo)halide complexes with neocuproine and aminomethylphosphanes derived from morpholine and thiomorpholi-ne. New J. Chem., 2012, 36, 1673–1683Starosta R., Florek M., Król J., Puchalska M., Kochel A.: Cooper(I) iodi -23. de complexes containing new aliphatic aminophosphine ligands and dii-mines–luminescent properties and antibacterial activity. New J. Chem., 2010, 34, 1441–1449Starosta R., Bykowska A., Płotek M., Kyzioł A. Copper(I) (pseudo)hali -24. de complexes with neocuproine and aminomethylphosphanes derived from morpholine and thiomorpholine – the interactions with DNA and the serum albumins and cytotoxic activity in vitro. Chem. Biol. & Drug Des., w drukuBalakrishna M.S, Suresh D., Rai A., Mague J.T ., Panda D.: Dinuclear25. Copper(I) Complexes Containing Cyclodiphosphazane Derivatives and Pyridyl Ligands: Synthesis, Structural Studies, and Antiproliferative Ac -tivity toward Human Cervical and Breast Cancer Cells. Inorg Chem. 2010, 49, 8790–8801Adwankar M.K., Wycliff C., Samuelson A.G.: In vitro cytotoxic effect of26. new diphenylphosphinoethane-copper(I) complexes on human ovarian carcinoma cell lines. Indian J. Exp. Biol. 1997, 810–814Sanghamitra N.J, Phatak P ., Das S., Samuelson A.G., Somasundaram K.:27. Mechanism of Cytotoxicity of Copper(I) Complexes of 1,2-Bis(diphe-nylphosphino)ethane. J. Med. Chem. 2005, 48, 977–985Michał PŁOTEK – M.Sc., graduated from the Faculty of Chemistry of the Jagiellonian University (2012). Currently, he is a Ph.D. student of Coordination and Bioinorganic Physicochemistry Group of Jagiellonian University. He works on synthesis and characteristics of coordination compounds with a potential biological application. Moreover he works at Inter-Academy Institute of Conservation and Restoration of Works of Art (Warsaw-Cracow).e-mail: michalplotek@Karol DUDEK - M.Sc., graduated from the Faculty of Chemistry of the Jagiellonian University (2012). Currently, he is a Ph.D. student in the Department of Chemical Education JU. He deals with implementation of IBSE in Polish educational system and he examines the role of learning through inquiry in the development of chemical skills. He also teaches in Private Academic Secondary School No 8 of Kraków and in Private Primary School Academos.Agnieszka KYZIOŁ - Ph.D., graduated from the Faculty of Chem -istry of the Jagiellonian University (2002). In 2007 she received her PhD degree in Chemistry . Sh e is currently an assistant professor in the Coordination and Bioinorganic Physicochemistry Group at the Faculty of Chemistry UJ . Her main interests and research work are focused on metal complexes and biomaterials with potential biological activity for medical applications (anticancer therapies , antimicrobial agents). She is co-author of over 20 scientific publications and numerous conference presentations .。