电除尘器使用说明书_英文
FE型电袋除尘器使用说明书
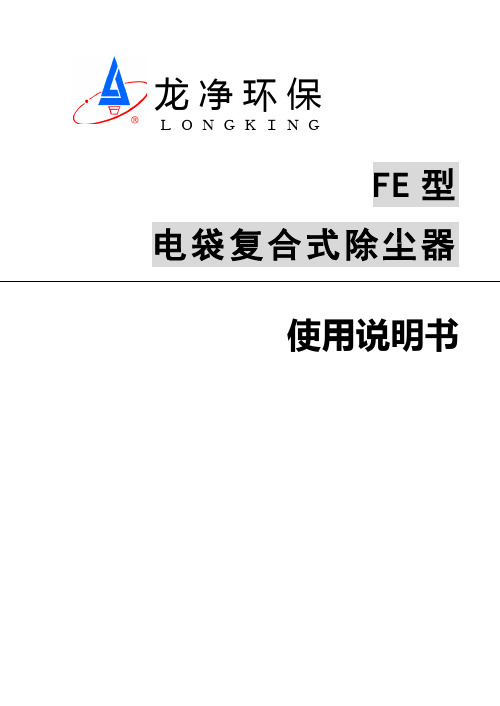
LONGKING
FE 型 电袋复合式除尘器
使用说明书
福建龙净环保股份有限公司
FUJIAN LONGKING CO.,LTD.
福建龙净环保股份有限公司
FUJIAN LONGKING CO.,LTD.
2
福建龙净环保股份有限公司
FUJIAN LONGKING CO.,LTD.
目录 第一章 概述 ................................................................................................................ 1
层剥落不完全导致阻力超过正常使用范围的一种故障现象。糊袋一般 出现在低温运行时,在滤袋表面发生水油汽的结露使粉层的粘性增大。
3
福建龙净环保股份有限公司
FUJIAN LONGKING CO.,LTD.
五. 电袋复合式除尘器型号及意义
表 1 应用分类及代号
应用分类 锅炉、燃煤电厂
水泥行业 冶金行业 化工行业 电除尘器改造
与常规布袋除尘器比较,电袋的清灰周期时间是常规布袋除尘器的 3-5 倍,压缩空气消耗量不到常规的 1/3。 4. 延长滤袋使用寿命
烟尘中的粗颗粒粉尘经过前级电场沉降和收集后,剩余细微粉尘随烟
1
福建龙净环保股份有限公司
FUJIAN LONGKING CO.,LTD.
气缓慢进入后级布袋除尘区,避免了烟气中粗颗粒磨损滤袋;运行阻力低 降低滤袋的负荷压力;清灰周期长减少滤袋清灰次数,这些都是延长滤袋 使用寿命的有利因素。只要运行维护得当,在相同运行条件下电袋复合式 除尘器的滤袋的使用寿命是常规布袋除尘器的数倍以上。 5. 运行维护费用低
DMC型喷吹脉冲袋式除尘器说明书全英文]
![DMC型喷吹脉冲袋式除尘器说明书全英文]](https://img.taocdn.com/s3/m/d24d1a82cc22bcd126ff0cb1.png)
DMC type jet pulsed bag filter manual1. Performance characteristicsDMC type jet pulsed bag filter, absorbing the advanced technicals on thebasis of the original DMC type jet pulsed bag filter, is a new generation bagfilter which is according to our current actual situation of small air filter.It adopts high pressure and high flow pulse valve and venturi which spewedout dust for every filter-bag. It has the advantage of high efficiency. Especiallywhen it clear dust on line, it can work continuously, which overcomesshortcoming of stopping out dust. It is widely used in metallurgy, mine,chemical, building, the mineral processing, grain, pharmacy and otherindustries.It filter material with polyester acupuncture felt, the emission concentrationis lower than 50mg/Nm³. With high quality filter material , it can collect 0.3~2μ dust, which is more efficient than any other dust catcher.2 Main structure 尘气65432113121110987图1 脉冲喷吹袋除尘器基本结构2.1 Airframe structure1.Ash valves2.Ash bucket3.Tank body4.Access door5.Draught fan support6.Exhaust fan7.Blowpipe8.Pulse valvepressed air bag10.Dust collecting filter bag11.Control device12.Inlet air door13.Outrigger2.2 Blowing system脉冲阀喷吹管B控制阀压缩空气主管控制2.3、Construction proformaD MC —N (A、B)A:ash hopper and discharge ashB:flangeFilter bag number of articlePulse injection typeSingle filter1.principle of operation3.1 principle of dust recoveryThe dust will fly to the bag house with airflow and spread around to the surface of the bag house equaly When the air with dust come from the air pipe or flange into the dust catcher. The dust will be stay outside of the bag house .and the air which has passed the bag house will get through the filter gate into the upside of air purification box .Then it will be atmospheric deposition through the exit exhaust fan. Some of the accumulation dust which attached to the outside of the bag house will drop into the ash hopper and some will stay still . And will make the installations resistance rise up .To make sure the installations resistance not exceeding 1500 PA . A thorough dust clean should be taken after few period .3.2principle of air blastThe drawing for the principle of air blast is as follow. The principle is the A head joint of the pulse valves will compress by-pass tube and the B head jointwill blowing the Venturi meter. the pulse valves backpressure house connect with the air exhaust valves. And the air exhaust valves is controlled by PLC. The exhaust port will be sealed by the exhaust valves and active iron core ,when the PLC no signal. And the pulse valves was closed. Also the pulse valves will open through the PLC with signal when the exhaust valves make the back pressure house connect with the atmosphere.Then the pressed air will send out to the Venturi meter through the holes and pass through the pulse valves from the main tube. Leading the bag house mentally positive pressure. Carry out the principle of pulse ash removal3.3principle of ash removalIn the air cleaning house, every filtrate bag have a spray tube ,which was connect with the pulse valves and the main tube of the air compression . There a many holes in the spray tube.Every hole correspondence the center of the filtrate bag. And the ash removal time and period can be settled in PLC according to the nature dust during working time. The plc will control automatic in the ash removal time to control kinds of pulse valves open by order.At this time the high pressure air will blow out speedy from the spray nozzle. And will attached 5 -7time of the air around from the Venturi meter to mix it into the filtrate bag. And will pass through from inside to outside like a air bladder which moved from upside to downside .then make the filtrate bag expand and trans shape lead to shock vibration times and times then make theash which outside the filtrate bag drop into the ash core.4.Installation4.1 Delivery situationFor the convenience and safe transport of the DMCdust collector, air bag pulse valve and exhaust fan in the injection system will be shipped according to the list.Tank body, ash bucket, ground jack, blast pipe, ash valves will be shipped in subpackage, and filter-bag will be shipped in packaging.4.2 Installation steps4.2.1 It needs to verify and understand the layout, equipment details figure, components of the equipment.4.2.2 It needs to check and examine the civil obligate holes, obligate steel plate, space dimension to see whether it is matched with design specification. The installation can go on if there is no errors. The installation goes on after deal with the difference.4.2.3 The installation of the ash bucketThe ash bucket can make a 180° turn. The four racks of the ash bucket should fall over the embedded steel plate, and the center of feed opening of the ash bucket is in line with the center of the obligate feed opening. No coincidence degree between the pitch and the embedded steel plate should not excess 1/4 inch. Non-levelness at the top of the ash bucket should<1/10004.2.4. Filter vessel installationThe filter vessel is at the top of the ash bucket, associated with bolts can press with the asbestos among rope close closure. You should pay more attention to the direction when you install the machine. The surface of the draught fan should be at the obligate outlet.4.2.5. The installation of the holder and the draught fan.The holder is weld at the cage to support the draught fan. Motor base, motor frame and fan tents are associated, which is connected through adapting pipe and static air chamber in the cage. At the installation, the adapting pipe should be connected to air inlet of the draught fan, and then adjust the position of the adapting pipe and the motor stand and weld them better. Mark out the position according to the draft, weld the adapted pipe, and then cut the static air chamber. Please note that spindle of the draught fan should keep horizontal.4.2.6 Pulse valve, air bag installationA gas bag on the stent, stents, fixed and fan shell welding, according to fixed position stents pulse valve is uncertain, as measured the height of the pulse valve and gas distribution between above the bag with high pressure rubber hose connection, and the height of installation error should be adjusted in rubber shall, within the scope of contentious bag keep level. Air bag on both ends of the assembly, one by pressure gauge, and the other one by air filter. 4.2.7 The installation of the air intake (don't contain ash hopper dust catcher without it)The air intake is welded by the ash hopper, its direction according to the technical requirement to determine the direction, installation height and Lou in the outside ash hopper according to determine the length of the selection chart 4.2.8 High pressure air filter installationThis part installment is under guidance of personnel, one end connect gas bag , the other side join the compressor pipe .4.2.9 Ash valves installationThe upper mouth of ash valve hooks and ash hopper with flange connection, and the lower mouth connect with the non-standard parts4.2.10 The installation of the venturi, spring skeleton and the filter bagAfter the complishment of confirming the above work,adding the venturi tube of filters DingMen into flower board (spray wind has installed first dismantled), the spring skeleton set into the filter bag inside, then from the filter with the hook with threaded through the skeleton bottom and the skeleton, and then willspring fixed frame to set the venturi tube 3, 4 circle will venturi tube top, make the filter bag stuck in the hole, adjust the flower board to appropriate levels, then Then fixing the pothook which is under the spring sketch on the open pore at the bottom of the dust-collecting catcher.五.Debugging5.1Injection system debugBefore the adjusting,all the inlet door,access door should be closed&locked. Inject system debugging is mainly to check if there are gas leaks of the Injection pneumatic system or the pulse valve works well , control apparatus to control valves control is correct or not. Switch on the power, adjust air pressure to meet the design requirements. Check pulse valve and air bags, and nozzle connection place, such as a leaks when control apparatus can be turned on and watch the pulse valve injection case, if the action and correct, and then the test run.5.2The test run5.2.1 In the above work is done, then adjust for empty load commissioning and loading test(1)Turn all the power on, compressed air source, clear grey controller(2)Start the Lord, observe empty fan load resistance (or U pipe pressure gauge)measurement of the import and export of air leakage rate, calculated leakage rate should be less than 5%. And observe fan motor temperature rise, no more than the temperature limit allowed, that is working properly.(3)If the air leakage is bigger, should be timely find air leakage points andprocessing.(4)Observing whether pulse system is functioning properly.If the above work all normal, then enter into loading test5.2.2Load test(1)Start all the process equipment, access to survive the containing gas.Observe operation resistance and dust rise vent discharge conditions, inthe new filter bag put into use, vent will have trace dust to escape, thisis normal phenomenon, over a period of time will be eliminated(2)When the dust catcher resistance rise to (1200 ~ 1500 Pa), start out dustcontroller clear grey, and observe the pressure down(3)When the whole process system stability, and then after normal cyclicaldetermination. The method is: first start out dust controller clear grey,and start time, when out dust is over, observe operation, when pressurerise to pressure (1200 ~ 1500 Pa), stop the clock. This period of timefor soot cleaning cycle. This method should be repeat three times, takethe average as soot cleaning cycle, adjust the soot cleaning controller(4)Watch out dust controller automatic control, everything is normal work,can put into normal operation.6.maintain and mendDirt catcher can maintain long-term efficient operation, routine maintenance is very important.6.1, When equipment is operational, management should be designated persons, and do the operation records.6.2, management personnel should be familiar with the principle of dirt catcher, the properties and the application conditions, and mastery of the adjustment and maintenance method.6.3, seal ring and other should be keep strict, such as the discovery of aging and damage should change in time.6.4,Hull, components such as take off paint to repairing in time, to prevent corrosion.6.5, moving parts such as fan motor should be press formulary note oil, If found not normal phenomenon promptly eliminate.6.6, Air bags and air filters should be drained contamination once per shift.6.7, solenoid valve for any failures, should be promptly eliminate, such as internal have impurity, water, should be cleared, such as diaphragm damage should be changed in time.6.8, the repair and replacement of filter bag.If dirt catcher be found have gray dust phenomenon may be damaged, the filter bag when in dividual small area, can use the old filter bag or the same material make-up. If most of the filter bag breakage, shall all be replaced. Assurance the normal operation of the dust.DMC性能表DMC CHARACTERISTICS型号Model性能characteristicsDMC-32 DMC-48 DMC-64 DMC-80 DMC-96 DMC-112总过滤面积Total Filter Area(m2) 24 36 48 60 72 84 过滤风速Filter Air Speed(m/min) 1.04~1.67 1.15~1.62 1.21~1.74 1.25~1.67 1.27~1.62 1.28~1.68 处理风量Treatment Air Flow(m3/h) 1500~2400 2500~3500 3500~5000 4500~6000 5500~7000 6500~8500 滤袋条数Number of Filter Pocket(条) 32 48 64 80 96 112 滤袋规格φ120×2000 φ120×2000 φ120×2000 φ120×2000 φ120×2000 φ120×2000 耗气量Air Consumption(m3/h) 0.032 0.048 0.064 0.08 0.096 0.11入口浓度Inlet Concentration(g/m3) 200出口浓度Oulet Concentration(mg/m3) 50喷吹压力Blastiong Pressure(MPa) 0.5~0.7承受压力Bearing Negative Pressure(Pa) 5000设备阻力Equipment Resistance(Pa) ≤1200脉冲阀Pulse V alve规格1"数量Quantity(个) 4 6 8 10 12 14电机型号功率Motor Model & Power Y90S-2 Y90L-2 Y100L-2 Y132S1-2 Y132S1-2 Y132S2-2 (kw) 1.5 2.2 3.0 5.5 5.5 7.5注:表中所列重量不包括风机重量。
静电除尘器说明书

印尼拉布湾项目:PLTU 2 BANTEN-LABUAN(2X300MW)合同号:ASM-2007-X-007阿斯米文件编号:ASM/JSH 2007-007版本:2008-02正压浓相气力飞灰输送系统技术资料天津市阿斯米机械设备制造安装工程(中国)第一部设备使用维护保养指导第二部设备及管路组件(包括备品备件和检修专用工具)第三部设备管道安装调试指导第四部设备、管路及附件的包装发运第一部设备使用维护保养指导第一章一般安全事项这套气力输送系统是按照安全操作工艺要求和国家有关安全法规设计。
尽管如此,在系统运行中也有可能发生人员伤亡和设备损坏的事故发生。
因此,操作人员必须在按照操作规程操作系统,整个系统必须处在正常状态下运行。
特别注意,对于不安全隐患,要及时处理。
这里所提供的气力输送系统是按照与客户共同确定的输送物料的特性来设计的。
所以对于因输送其它物料或用于其它目的而造成所有系统故障和事故,阿斯米公司将不负责。
这完全是客户自己的责任。
使用该系统设备的注意事项:用户必须确保以下事项:—该系统设备的操作、维护和管理人员在工作前必须要认真学习“操作指导书”,特别关注有关安全的章节。
—操作人员要经常阅读“操作指导书”。
—除此之外,设备的操作、维护和管理人员还必须熟知遵守当地有关事故预防和环境保护的法律法规,注意劳动保护。
—所有有关人员要时刻有安全意识,及早发现不安全隐患。
—该系统设备必须始终在正常状态下运行。
—该系统设备的周围环境必须井井有条和清洁。
—非安全设备要拆除或关闭。
—因维护保养设备而不得已拆除的安全保护设备,必须在这些工作一完成后马上复位。
—出于安全原因,任何对该系统设备的变更都必须在阿斯米公司的允许下才能进行。
—任何对该系统设备的控制程序的变更都必须在阿斯米公司的允许下才能进行。
—所选用的备品备件要符合阿斯米公司的技术要求。
只有这样才能保证所使用的备品备件是质量过关,安全可靠的。
人员素质要求在该系统设备工作的人员必须是诚实可靠的人。
WT系列电除尘器说明书(英文)

WT SERIES ELECTROSTATIC PRECIPITATOR OPERATING INSTRUCTIONFujian Weidong Industry CO.,Ltd.Fujian Weidong Industry CO.,Ltd.Fujian Weidong Industry Co., Ltd.ProfileFujian Weidong Industry Co., Ltd. is a national high-tech enterprise integrated research development,design,manufacture,installation and commissioning of air pollution equipment and waste water treatment equipments.The company has registered capital of 146 million yuan, covers an area of 70000m2it has built 5 standard workshops(totaling40000m2 ) ,1 scientific research building(more than 10000m2)and a modern office building(8000m2). There are three business units under the Weidong Industry:Environmental Engineering Division,Desulfurization Division,and Equipment FactoryThe Environmental Engineering Division specializes in manufacture of environmental protection equipment and on-line monitoring equipment for wastewater treatment.There are many technical and engineering specialists in environmental pollution prevention and membrane separation.we have done extensive research and develop works with institutions and universities,also integrate a large number of application processes and technologies.The Desulfurization Division has a world-dasstechnology: the fifth generation of circulating fluidized bed dry flue gas desulfurization (CFB-FGD) it is able fo achieve the desulfurization rate up to over 90% even ca/s=1.2 or higher. At the same time, it greatly enhances the stability of the desulfurization unit, it is a kind of dry flue gas desulfurization technology with the largest single tower treatment capacity and the overrall desulfurization benefit is the most in present business applications. The Environmental Protection Equipment Factory specializes equipment manufacturing.The wordshops has an area of 12,000m2, including production line of collecting plate and discharge electrode system for ESP, steel structure production line , high voltage power production line, bag and bag cage production line, water treatment equipment and electrical production line and electrical control equipment production line.The Weidong Industry owns the business philosophyas "people-oriented, technological innovation, honesty first, customer first",we stick to the path of scientific management, continuous innovation and strong development. we will strive for cooperation with friends with first-class technology, first-class products and first-class ,to make brilliant future together.CHAPTER IGENERAL DESCRIPTIONThe WT series electrostatic precipitator(ESP) is a general horizontal type ESP manufactured by our company absorbing advantages of the same kind of products ( of famous companies such as GE Company, USA ) at home and abroad.It is characterized by electromechanical integration, dynamic impedenance control of field and wide spacing structure and is an efficient reliable high-tech environment protection equipment specially suitable for dedusting in coal-burning power plants, cement industries, metallurgy industries, etc.position of WT series ESPa.Main equipments1)Main body of ESP2)HV power supply for ESP3)LV collective control system for ESP4)Electromagnetic rapper control systemb.Auxiliary equipments (Intelligent computer control system)The intelligent control system is a high-tech product with the up-to-date technologies of computer application, communication, measurement, etc. It is suitable for on-line monitor and management of ESP to achieve remote control for the HV silicon rectifying equipment, LV rapper, dust-discharging and dust-conveying systems, electrical heater, etc. in an ESP. In addition, the closed-loop control can be achieved by a feedback signal from an opacity meter installed in outlet gas flue.The system can be applied to every field of ESP expansion, particularly the power industry in which it is an important equipment for improving automatic control level of ESP and achieving an efficient-holding and energy-saving operation.2.Operating principle of WT series ESPWhen applied a negative DC HV between the collecting plate and the discharge wire, a nonuniform HV field is generated in the space between them. If the applied voltage is sufficient, the corona discharge takes place near the discharge wire and thus generating tremendous amount of electrons and positive and negative ions. In this case, when the dust-laden flue gas passes through the field, the dust will adsorb ions or electrons to be charged, the dust-charged migrates towards the unlike electrode (collecting plate) under the action of field force. When reached the collecting plate, the dust-charged will deposit on it under the action of field force and dust adhesion and in turn release its charge to the collecting plate. At the same time, the dust with positive charge will deposit on the discharge wire to make the dust particles separated out. After the dust deposited on the collecting plate and discharge wire reaches a certain thickness, by means of rapping, the dust will be dropped into the hopper and then carried off by a dust-conveying system. The process above is carried on continuously to achieve the final goal of purifying flue gas.3.Model and working conditionsa.Product modelWT □----□/ □Number of fieldsEffective cross-sectional area (m2)Number of chambers (If single, omitted)Product code nameb.Working conditions1)Flue gas amount to be treated: ≤4.5×106m3/h2)Dust concentration of inlet flue gas: ≤200g/ Nm33)Temperature of flue gas: Common type ≤200℃4)Allowable bearing pressure: -6 kPa ~ 2 kPa5)The ESP used in the rotary kiln and coal mill of building material industry must beequipped with a CO monitor alarm device and a explosion-proof device. The ESPin coal mill must be also equipped with a CO2 fire extinguisher.6)The ESP should be supplied with a special ground grid. The connection of the ESPcasing to ground grid must be secure and reliable and its ground resistance shallbe not more than 2Ω.4.Main features of WT series ESPa.Electromechanical integrationBecause the mechanical main body and its electrical control equipments manufactured by our company are designed on our own technical strength, they can be matched rationally and whole performance can be coordinated, which will avoid irrational matching between them (e.g. big main body to small power supply or otherwise) and make the equipment operation still more reliable.b.Operation under high impedance stateBy using the computer detecting technique, timely detect the dynamic impedance of field to make power supply reasonable and the field operated in a high impedance state, which will increase field strength and Coulomb force received by the dust-charged in the field, and thus increasing the dust migration velocity and the dust collection efficiency. As a result, this will make manufacturing cost of the product lowered and cost performance increased.c.Wide spacing technologyThe product is designed with the spacing between like electrodes being 400 mm or more.Because the like electrodes spacing is increased, this will bring about the following results. The unlike electrodes spacing will be also increased correspondingly, the field breakdown voltage increased, the corona area extended, the corona becomes sufficient, the fatting of the discharge wire retarded, the current density on the collecting plate uniformized, the dust migration velocity increased, the collecting performance for the high resistivity dust improved and, the dust reentrainment decreased. These above are in favour of the dust collection and improvement of dust collection efficiency. In addition, such a wide spacing design will bring about the advantages of easy to install, easy to maintenance, less drag, less power consumption and relative stable operation.d.Top rapping1) No rapping moving parts exist in fields to make the internal space utilization ratio increased. Particularly the rapping mechanism is placed on the top of ESP and isolated from flue gas, this will make maintenance easy (can be performed in operation) and operating reliability increased.2) Both the collecting plate and discharge wire are not subjected to a strong transverse shearing force to make the wire not be broken and the plate not be falled off, and thus they will have high reliability and long service life.3) The fields occupy a smaller space along the length direction to make arrangementeasy.4) The distribution of the rapping acceleration on collecting plate and discharge wire conforms with the requirements of rapping force for dust-cleaning the plate and wire, and thus using a less rapping force will achieve a better dust-cleaning effect.CHAPTER IIMAIN BODY STRUCTURE OF WT SERIES ESPThe major structure of WT series ESP main body includes collecting electrode ( CE ) system, discharge electrode ( DE ) system, CE and DE system rapping devices, inlet and outlet nozzles, gas distribution devices, HV lead-in device, casing, hopper, etc. as shown in the drawing below.1. Hopper2. Supporting structure3. Casing4. Inlet nozzle5. Gas distribution plates6. Collecting electrode7. Electromagnetic rapper8. Discharge electrode9. Stair and walkway 10. Outlet channel plate 11. Outlet nozzleMain body Structure drawing of WT series ESPCHAPTER IIIINSTALLATION OF WT SERIES ESPBecause of its large volume and heavy weight, the ESP, limited by transport conditions, will not be delivered as a whole and can be only delivered in components and parts after which are transported to the job site they are assembled into a whole by a specialized installation unit. The site assembly and installation have a large amount of works and a long project time limit. The installation quality is of vital importance for achieving desired design result and ensuring safety reliable efficient operation. In the process of installation, the installation unit must follow strictly the drawing requirements and relevant technical specifications to install, inspect, adjust and test. Only after inspected and qualified by supplier technician can the completed ESP be put into operation.CHAPTER VIOPERATION OF WT SERIES ESP1.Preparation before operationWhen the ESP being started to operate after installed, adjusted and tested or being restarted to operate after major overhaul, the following starting operating conditions should be provided.a. Technical requirements1) After relevant test items have been completed and the fractional acceptance passed, the relevant informations are kept in an equipment file. For the ESP just put into operation, these informations should include 《The installation checking record of ESP main body》,《The whole installation acceptance report of ESP》,《The performance test report of ESP》written after operated for a time specified in the contract, etc. For the ESP after major overhaul, the informations should include the measuring record of the spacing between DE and CE before and after alignment, insulation records of the field and power supply device, field no-load step-up test, V-I characteristic adjustment and test during field on-load trial operation, voltage-withstand test of transformer oil and voltage-withstand test of HV cable.2) The acceptance of auxiliary equipments and facilities should be performed well. The auxiliary equipments include the rapping time control device, dust-discharging device, dust level indicator, thermal insulation and heating devices, opacity meter, communication and illuminating equipments, etc. If equipped with CO measuring device, its reliability should be also tested.b. Environment and safety requirementsBefore the ESP being put into operation, the following requirements should be accomplished. The job site should be cleaned out to make every road unblocked; every platform,walkway and handrail should be intact; illumination should be sufficient; every rotating mechanism outside should be equipped with guard cover or baffle; safety mark should be clear; electrical safety interlock should be in good condition; control room should be equipped with lowering temperature, dustproof and fireproof measures.c. Technical training of personnelFor the personnel who hold a post in ESP operation, they should have the following conditions.1)Their working experience shall be more than three months.2)They should be graduated from a skilled-worker school or have the same educationallevel and should be qualified through technical training.3)They should have a certain practical technology ability familiar with this post.d. Preparation of technical data and appliances1)Preparation of toolsMaintenance workers should be provided with a set of conventional maintenance appliances and electric engineering tools2)Preparation of spare parts and consuming materials.3)Preparation of technical data and account books should include a complete set of machine maintenance and electrical drawings, common equipment drawings, informations and instructions, etc. In addition, include the account books, reporting forms and record sheets required for operation, such as the equipment operating regulations, record books on duty, operating daily sheet, touring inspection card, start / stop operation card, working sheet registering books, etc.2.Inspection before operationThe ESP should be inspected before the following conditions.·The ESP is going to be formally put into operation after installed and adjusted.·The ESP is going to be put into operation after major overhaul.·The ESP is going to be restarted to operate after stopped to operate for a long time.a. Inspect whether the inside of both the ESP casing and insulator compartment have any impurities and every access door is closed tightly and locked up.b. Inspect whether every transmission mechanism is in good condition, rotated flexibly and every lubricating point has sufficient lubricating oil.c. Inspect whether the ground devices of every location are intact.d. The power supply device is inspected as follows.1)Set the air switch JD to “OFF” position.2)Inspect whether every disconnector is good and fixed firmly.3)Inspect whether connectors of every PCB are inserted tightly andcomponents on them are come off.4)Inspect the insulation resistance values of T/R HV end to ground end andT/R LV end to ground end with a 2,500V megger, among which the former shallbe more than 1,000MΩ.5)Inspect whether the HV T/R has oil leakage.e. Inspect whether the control switch panel, alarm system, display system and signal system all of which be put into operation are normal and the functions of every protection device are in good condition.f. Inspect and ensure that all of working personnel have left from the inside of ESP main body.g. Inspect whether the concentrations of combustibles and explosives in flue gas and the gas temperature are in accordance with design requirements.3.Trial operation before formally put into operationa.Trial operation of rapping device1)Start the rapping device to make it continuously operated for one hour. Inspectwhether the rapping device is operated normally, its hammer head is hit on thecenter position of the raping rod and bolts are tightened.2)Perform the rapping test for one cycle according to the rapping cycle. Inspectwhether the raping program is operated according to design requirements.b.Trial operation of heating system of thermal insulation box.1)Switch on the electric heater in the thermal insulation box.2)Make the temperature signal lead-in terminals of the heater short circuit.3)Simulate the heating temperature relay value. In this case, if the heater isdisconnected, it shows that the automatic constant temperature control is operatednormally.c.Trial operation of hopper heating systemStart the electrical heating device of hopper and then inspect whether the indication on the local temperature control cabinet of the hopper is normal.4.Startinga. Blow hot air in the ESP field and make the thermal insulation box heated from the 4th hour before the field being put into operation, which will prevent insulating parts from creeping due to dewing.b. Before furnace firing, make the hopper heated to prevent the cold hopper from dewing or the fallen dust from moistening to cause dust clogging.c. Put every dust-discharging and rapping devices into operation and open corresponding dust conveying system immediately after furnace fired.d. The electrical operator is called on to close the fuses on the primary side of HV isolating switch for ESP.e. After received a notice from the chief on duty, start to supply power for fields to make the third, second and first field put into operation in order.f. The power supply for ESP is operated according to the following procedure.1) Set the switch of axial flow cooling fan in the control cabinet to the “ON” position.2) Set the power switch to “ON”position, the “power fault”lamp on the control cabinet will be lit and the LED display on the controller will indicate “888888”.3) Press the start button, the “power fault” lamp on the control cabinet will be gone out and the “running” lamp lit.4) Set the operation selection switch to “Auto”position, press the “reset”key and then the “running” key. At this moment, the output will be increased. Adjust the “current limit”knob until a flashover occurs or the rated output current is achieved. Next, adjust the “ramp rate” knob to select an optimum flashover frequency (30~70/sec) to make the fields operated in an optimum state.5.OperationThe followings should be monitored and recorded by the person on duty being chargedwith specific responsibilities.a. Strictly monitor the primary voltage, primary current, rectified voltage and rectified current of the power supply device and record them every two hours.b. Monitor the temperature rising of the HV T/R. The oil temperature shall be no more than 80℃, no abnormal sound and no abnormal discharge in the HV output network.c. Every thermal insulation box and hopper heater are operated normally.d. Every control device on the control cabinet is operated normally.e. Understand the operating condition of dust-discharging system every hour.f. Regularly inspect the spark rate which shall be within a specified range. If the spark rate is found to be out of the range, it should be adjusted in time to make the ESP in an optimum operating state.g. If the ESP and/or its auxiliary equipments are at fault or malfunction, the operator should go to the fault point immediately after received alarming notice to analyze fault reasons and get in touch with relevant departments to remedy.h. The works done by every shift is as follows.1) Overall inspection of the equipments for ESP.2) Cleaning work within the administration area of the post.3) Carefully record any abnormal operating condition and equipment defect happened in the shift.4) Relief of a shift.6.StoppingUnder normal conditions, the ESP should be stopped to operate when the boiler load being less than 35% or the boiler being burned by fully using oil.a. After received the notice of stopping the ESP, press the “reset” key to make the output current and voltage decreased to zero.b. Press the “stop” button.c. Set the power switch to “OFF” position.d. Set the axial-flow cooling exhaust fan switch on the control cabinet to “OFF” positione. After the forced draft fan and induced draft fan of boiler are stopped to operate, keep every rapping device continuously operated for 2 or 3 hours and then stop them.f. After rapping devices are stopped to operate, the dust in hoppers should be fully discharged in time.g. Only after the ESP has been stopped for 8 hours can the access doors be opened to make the ESP cooled. If required for inspection, the access doors may be opened after the ESP has been stopped for 4 hours.h. After the boiler is outfired for any fault, the ESP should be stopped immediately.CHAPTER VMAINTENANCE OF WT SERIES ESPA strict maintenance system and a practicable maintenance regulation are necessary to ensure the ESP being in long-term reliable efficient operation. The followings will present the maintenance system and its relevant regulations of the WT series ESP.1. Maintenancea. Periodical maintenancePeriodical maintenance items Period Oil easily worn position of every mechanical transmission. One week Lubricate rotating position of cooling fan for HV control cabinet and SCRdevice.Three months Tighten fixed nut of rapper. One month Oil mechanical transmission position of HV isolating switch and safetymechanical lock and inspect and adjust their operation mechanisms.Six months Measure operating condition of automatic voltage regulator with an oscilloscopeand record. Require power supply for automatic voltage regulator conforms tomanufacturer’s requirement and feedback waveform is symmetric and plentiful.Three monthsInspect whether operating procedure of rapping time control device is normaland setting time is accurate.Three monthsInspect whether temperature measuring device is normal. If abnormal, adjust orreplace temperature measuring components.One yearInspect whether surface of opacity meter lens is contaminated by foreign matterand clean it.Six monthsClean air filter of opacity meter. Six months Replace filtering tube. One year For T/R and damping resistor.1)Inspect and clean oil conservator and oil-discharging pipeline ( at highposition arrangement ).2)Inspect operating ground wire. Require connecting resistance of wire toground body being les than 0.1Ω3)Inspect and treat damping resistor connecting point.4)Wipe porcelain parts.5)Inspect and treat leading-in joint.6)Inspect and replace drying agent in T/R respirator.7)Inspect oil level of T/R and replenish with oil.Six monthsCheck and replenish common consumables-fuse, indicating lamp, lubricating oil,etc.One monthPeriodically inspect and replace fire-fighting equipments in control room, cable story, T/R, power transformer and distribution room. Specified by fire-fighting equipmentb. ESP shutdown maintenance1)Only after the rapping devices have been stopped to operate and the dust in hoppers discharged fully can the dust-discharging system be stopped. For the ESP which is stopped for a long time, the dust accumulated in ESP body and dust-discharging system should be fully removed. At severe cold season, the hydraulic dust –flushing system may be maintained properly a certain amount of dust-flushing water to avoid frost crack of piping. When temporarily or urgently stopped and the remaining dust can not be emptied in a short while, the hopper heating devices should be operated as continuously as possible.2)Close the inlet and outlet flue dampers and regularly ventilate the field for maintenance to avoid the rust of metal parts. If possible, the field can be maintained by means of hot air.3)When the ESP has been stopped temporarily for a short time, the main equipments are in the standby or operation state and the ESP will not be maintained, the electrical heating, hopper heating and hot air heating systems should be continuously operated on their original operation modes. When the rapping and dust-discharging systems are being operated continuously, the output of the dust-discharging system may be correspondingly lowered because of tremendous decrease of dust to keep a certain dust seal.4)All the dust-discharging devices should be continuously operated for an hour every week to avoid the rust of rotating parts.c. Special ESP maintenances1)After the ESP has been operated for 2,500 hours, the following main items can be determined according to relevant technical standards for ESP.·ESP pressure drop·ESP dust collection efficiency·Ratio of air leakage of ESP·ESP dust property2)For the ESP which is new put into operation, the following points should have special attention when first shutdown maintenance so as to take measures to avoid the expansion of equipment fault caused by the defects left during installation and endangering ESP normal operation in the future.·Carefully overall inspect insulators and porcelain shafts installed in the thermal insulation box at the top of ESP on which the crackle will appear soon after operated due to non-operational reasons of installation, equipment quality, etc.·Inspect joints of the CE plate assembly, DE wire assembly, fram structure, etc. If finding to be loosed, welding off and dropped, the processes, such as reinforcing, spot weld, reinforcing weld, etc. should be performed according to relevant technical requirements.·Pay attention to the expansion condition of the lower CE plates and observe whether they are deformed due to obstruction.·Observe the state of limiting device on CE plate assembly and the state of hopper baffle to see whether the baffle is welded off, the guide plate dropped, etc.·Inspect the tightness of access doors and whether the hypolon on rapper underbed is aged. If having any defect, they should be replaced and treated in time.d. Other ESP maintenances1)Regularly paint the stair, platform, rapper shell and other easily rusting exposedsurfaces to avoid rusting.2)Inspect whether the oil ring, oil nozzle, oil gage, oil leveler, etc. are perfect. Ifimperfect, they should be treated in time.3)If the oil quality is worsened and the oil level is too high or too low in thereduction machine, they should be treated in time to avoid false oil level.4)For the CO gas analytical meter, the following items should be regularly (e.g.every season) performed.·Mechanical and electrical zero correction.·Full range test.·Adjustment and test of upper/lower range action.·Inspect and clean the sampling probe and inspect whether the probe is damaged.·Replace the filtering silicon gel in time to make flow rate maintained within the range required for the meter.2. Minor overhaul of WT series ESPa. Treat the defects which can not eliminated in operation. These defects mainly include internal field faults and some faults in common systems which can be treated only after the ESP has been stopped.b. For the CE plate, mainly inspect the perfectness of CE plate (assembly).c. For DE system, mainly clean away the dust on the HV insulating parts, inspect the frame appearance and its fastening state, and treat the breakage, looseness and drop-out of DE wire.d. For DE rapping device, mainly adjust the center position of the electromagnetic rapper and tighten the nut on it, inspect and treat the ageing of asbestos packing and oil leakage, and treat the air leakage of rapper.e. For the dust-discharging device, mainly inspect and treat the fixed state of hopper baffle, eliminate leakage points, poke the dust clogging and treat the dust-discharging valve in which its rotation has been blocked and its vane split.f. For the inlet and outlet nozzles, casing, etc., mainly inspect their appearance perfectness and eliminate obvious air and dust leakage points.g. For the dust flushing and heating systems, mainly eliminate the water and steam leakage points, treat the failed valve, nozzle and pipeline and remove the sundries in dust channel.h. For the T/R and HV circuit, mainly inspect and treat the appearances of T/R, damping resister, HV isolating switch and HV cable.i. For the HV control equipment, mainly inspect and treat the appearances of HV control cabinet, reactor and automatic voltage regulator.j. For the LV electrical equipment, mainly inspect and treat the appearances of every power and control equipments and electrical equipments.k. For the opacity meter, it should be maintained according to its operating instruction.CHAPTER VIFAULTS AND THEIR REMEDIESVarious faults and common operating conditions of the ESP are usually presented in operation or power-on test states. Because the ESP is an electromechanical integration equipment in which the machine and electricity are affected each other, the same phenomenon may be caused by mechanical faults or by electrical faults. Therefore, when analyzing any fault in the ESP both the mechanical and electrical reasons should be considered comprehensively, and the process operation of boiler system, dust medium and operation conditions of relevant equipment should be also combined together to consider. The fault reasons introduced below is only a small number of examples encountered in practice.1. General faults and their remedies。
JDW高压静电除尘器说明书

1.5 When the production is normal and stable, high-voltage power supply can be used. At first, it is better to rotate a litter of the potentiometer button, that is to say, the DC voltage shouldn’t be too high, after the corona appears, increasing voltage step by step until lower than spark discharging. After it is stable for some time, if there is no local creepage flashover or penetration, then increase voltage till it is in optimum range of spark frequency, usually 30-50 times/min. Apply automatic control after it is running.
1.6 随着升压开始,逐步升压、电晕电流持续增加,要记录下来电晕临界始发电 压和伏安特性曲线。
1.6 As the voltage starts and rises gradually, the corona current also goes up, and then workers should make records about the curves of critical starting voltage of corona and of volt-ampere character.
电除尘器中英文技术交底

浙江信雅达环保工程有限公司电除尘器安装技术交底资料Sunyard ESP Erection Technical Clarifications编制:王永泉校对:冯文杰审核:周泽军浙江信雅达环保工程有限公司工程服务处目录电除尘器安装技术交底 (2)ESP Erection Technical Clarifications (2)基础划线技术交底记录 (5)Clarifications on Foundation Setting out (5)钢支架技术交底记录 (7)Technical Clarification Record on steel support structure Erection (7)支承轴承技术交底记录 (9)Clarification Record on Supporting Bearing Erection (9)底梁安装技术交底记录 (11)Clarification Record on Bottom Beam Erection (11)灰斗安装技术交底记录 (13)Technical Clarification Record on Ash Hopper Erection (13)灰斗安装技术交底记录 (14)尘中走道安装技术交底记录 (15)Technical Clarification Record on Internal Walkway Erection (15)灰斗挡风安装技术交底记录 (16)Technical Clarification Record on Ash Baffle Erection (16)构架组合安装技术交底记录 (17)Technical Clarification Record on Structure Assembly Erection (17)内顶安装技术交底记录 (18)Technical Clarification Record on Inner Roof Erection (18)内顶盖安装技术交底记录 (19)平台梯子安装技术交底记录 (20)Technical Clarification Record on platform and Ladder Erection (20)电极组合安装技术交底记录 (21)Technical Clarification Record on Electrode Assembly Erection (21)电极组合安装技术交底记录 (22)振打及传动装置安装技术交底记录 (23)Technical Clarification Record on Erection of Rapping and Driving Equipment (23)外顶盖安装技术交底记录 (25)Technical Clarification Record on Outer Roof Erection (25)进出口封头、分布板安装技术交底记录 (26)Technical Clarification Record on Erection of Inlet and Outlet Hood and Distribution (26)本体保温技术交底记录 (28)Technical Clarification Record on ESP Proper Insulation (28)雨棚安装技术交底记录 (29)Technical Clarification Record on Top Penthouse erection (29)ESP Erection Technical ClarificationsESP Erection Technical ClarificationsESP Erection Technical Clarifications基础划线技术交底记录Clarifications on Foundation Setting out电除尘器安装技术交底ESP Erection Technical ClarificationsTechnical Clarification Record on steel support structure ErectionTechnical Clarification Record on steel support structure Erection支承轴承技术交底记录Clarification Record on Supporting Bearing ErectionClarification Record on Supporting Bearing ErectionClarification Record on Bottom Beam ErectionClarification Record on Bottom Beam Erectio nTechnical Clarification Record on Ash Hopper ErectionTechnical Clarification Record on Ash Hopper Erection尘中走道安装技术交底记录Technical Clarification Record on Internal Walkway Erection灰斗挡风安装技术交底记录Technical Clarification Record on Ash Baffle Erection构架组合安装技术交底记录Technical Clarification Record on Structure Assembly Erection内顶安装技术交底记录Technical Clarification Record on Inner Roof Erection内顶盖安装技术交底记录Technical Clarification Record on Inner Roof Erection平台梯子安装技术交底记录Technical Clarification Record on platform and Ladder ErectionTechnical Clarification Record on Electrode Assembly ErectionTechnical Clarification Record on Electrode Assembly ErectionTechnical Clarification Record on Erection of Rapping and Driving EquipmentTechnical Clarification Record on Erection of Rapping and Driving Equipment外顶盖安装技术交底记录Technical Clarification Record on Outer Roof Erection进出口封头、分布板安装技术交底记录Technical Clarification Record on Erection of Inlet and OutletHood and Distribution进出口封头、分布板安装技术交底记录Technical Clarification Record on Erection of Inlet and OutletHood and DistributionTechnical Clarification Record on ESP Proper InsulationTechnical Clarification Record on Top Penthouse erection。
电除尘操作器说明书EPCON

说明书 EPCON
目
录
第一章 控制器概述.......................................................................................................................................4 1.1 控制器简介.................................................................................................................................4 1.2 系统组成图.................................................................................................................................5 1.3 前面板示意图.............................................................................................................................6 第二章 调试软件操作说明...........................................................................................................................7 2.1 调试软件简介...................................................................
电除尘说明书(通用版)

高压柜面板操作及EPIC-Ⅱ面板说明一、EPIC-Ⅱ型控制面板说明:FUSE:24V 1A电源保险丝。
ALARM:报警时指示,点亮=跳闸(报警)闪烁=警告报警TRON:变压器主接触器运行(点亮)SPARK:火花时闪烁AC-LINE:指示目前的一次线电压,EPIC锁定行扫描频率,并开始采集数据。
ALNE:通常在处理机正常运行时闪烁REMOTE:指示接受FLAKTBUS(网关)数据总线控制,视高压控制柜“手动/遥控/停止”开关位置。
TOKEN.ROTATLON:与FLAKTBUS数据总线通讯时闪烁无通讯=无闪烁NETWORK:ON=EPIC与外部FLAKTBUS联网,与RTU下位连接;OFF=(测试和维修位置)仅与RTU连接RTU:RTU接口,连接RTU,用于第一次启动和故障显示。
二、高压柜面板说明:高压柜面板上部有仪表四只,第一只为变压器初线圈电压,第二只为变压器初线圈电流,第三只为变压器次级直流电压,第四只为变压器次级直流输出电流,前2只为有效值,后2只为平均值。
手动/遥控/停止:停止:T/R退出运行,高压停运。
遥控:接受RTU操作,接受上位机控制(结合NETWORK[网络开关])手动:T/R投入运行:运行在“手动模式”>10S手动模式<10S到遥控则运行在先前模式旋钮及指示:旋钮及指示灯在柜上具已表明对应控制元件。
阳极振打手动:在T/R OFF时,阳打在手动状态下运行自动/停止/手动:停止:在T/R OFF时,阳打停止运行自动:(T/R ON时,阳打根据时序自动振打)EPIC-Ⅱ内部设置为“自动”阴极振打自动/停止/手动同“阳打自动/停止/手动”瓷套加热手动:为手动加热状态停止/手动:停止:瓷套加热停止自动:EPIC-Ⅱ内部设置为“自动\开\关”槽板振打手动:自动,都为手动振打状态自动/停止/手动停止:振打停止自动:(T/R ON时,阳打根据时序自动振打)EPIC-Ⅱ内部设置为“自动”三、操作说明启动(现场):按如下步骤:1、投入“总电源开关”(合闸)瓷套加热旋钮旋在“自动”位置(加热所需时间)2、阳、阴打必须在“自动”位置,同时“NETWORK”(网络)必须在“关”OFF位,“自动/遥控/停止”在“遥控”位。
电除尘器使用说明书

目录1、范围2、规范性引用文件3、概述4、工作原理5、设备简介6、设备的安装和检查调整7、设备的安全规程8、设备的试运转9、设备的操作规程10、设备的维修保养及故障处理电除尘器使用说明书1 范围本说明书规定了电除尘器的使用条件、考核标准、设备调整、试运转、操作、维修保养和故障分析与处理的方法以及安全注意事项。
本说明书适用于火电、冶金、造纸、建材和化工等行业用的干式、板式、卧式F型电除尘器。
GP型、ZH型等电除尘器也可参照采用。
不适用于湿式、立式电除尘器。
2 规范性引用文件下列文件中的条款通过本说明书的引用而成为本说明书的条款。
凡是注日期的引用文件,其随后所有的修改单(不包括勘误的内容)或修订版均不适用于本说明书,然而,鼓励根据本说明书达成协议的各方研究是否可使用这些文件的最新版本。
凡是不注日期的引用文件,其最新版本适用于本说明书。
GB/T13931 电除尘器性能测试方法JB6407 电除尘器调试、运行、维修安全技术规范JB/T5910 电除尘器电除尘器安装说明书3 概述电除尘器是一种高效节能的烟气净化设备,具有收尘效率高、处理烟气量大、使用寿命长、维修费用低等优点,在当前国内外对环保要求越来越高的情况下,电除尘得到了越来越广泛的应用。
在使用电除尘器时必须按电除尘器使用说明书的规定操作。
本说明书未涉事项,应按电除尘器产品有关图纸和技术文件的规定处理。
3.1 型号说明我公司生产的电除尘器其主要型号及其意义说明如下:例:2 FAA3 ⨯45 M – 2 ⨯68 – 145电场有效高度(dm)小室有效宽度(dm)单台并列小室数同极间距400mm(H为300mm)电场有效长度(dm)电场数菲达型钢结构一套设备并列台数注:上述型号简写为:2 F 197 – 3电场数为3个电场有效流通面积为197m2菲达型钢结构一套设备并列台数为2台3.2 常规电除尘器使用条件其使用范围是:烟气处理量:≤6⨯106m3/h烟气温度:≤400℃(>250℃为高温型)比电阻为:1⨯105Ω.cm ~1⨯1014Ω.cm同极间距:250mm~600mm承受许用压力:-4.0x104Pa ~0Pa(其中-1.0 x104Pa~0Pa为常规型;-4.0 x104Pa ~-1.0Pa x104Pa为高压型)同极间距:250mm ~600mm入口烟气含尘浓度:≤100g/Nm3(在标准状态下)电除尘器可以处理含有腐蚀性物质的烟气(防腐蚀型电除尘器)。
BE型电除尘器使用说明书

BE 型电除尘器的运行一、运行前准备工作电除尘器投运前必须具备的条件一台电除尘器经过安装、调试进入试运行,或者设备进行了大修后重新投运,应具备以下投运条件。
1、技术要求。
第一、要求完成有关试验项目并经分步验收合格,再将有关资料存入设备档案。
对新投运设备有以下几项试验项目:电除尘器体密封性试验,电除尘器的阴、阳极间距安装偏差测定,电场中气流分布均匀性测试,阴、阳极振打加速度测定,接地电阻测定,电场空载升压试验,并在试运行时进行额定工况下的带负荷V—I特性测试,有关技术要求详见有关标准。
其中密封性试验在电除尘器敷设保温层前进行,以反映壳体漏风的真实情况,而间距的测定宜在封顶前进行,以便发现问题时能够采取补救措施。
为了保证以上试验切实顺利进行,对以上试验项目的具体实施应在技术协议中有所体现,从我国电除尘器使用现状来看,电场中的气流分布均匀性测试与振打加速度测定也常由制造厂通过实验室验证后将有关保证数据提供用户单位,供电装置也需要进行一些检查试验,其中一些为制造厂出厂试验,负荷为制造厂内的模拟电场,这些试验有:耐压试验、空载试验、负载试验、过载保护的检验、与短路保护试验,一般由制造厂提供有关技术证明文件。
另一些是由安装单位或安装单位委托制造厂技术服务部门在设备的现场安装调试中进行,常见有:变压器的高、低压绕组的绝缘电阻测试,高压电缆(包括电缆头)的耐压试验,变压器油耐压试验,变压器抽芯检查,供电装置各种保护的现场校验等,具体内容参照有关标准、制造厂安装调试大纲与本书有关章节,安装单位应提供有关调试报告。
如果是大修后的设备,一般应进行以下检查试验并向厂技术主管部门提供相应技术报告。
属机务方面为:阴、阳极间距调整前后的测量记录,电场与供电装置的绝缘测量,电场的空载升压试验,并在试运行时进行额定工况下的V—I特性测试;属电气方面为:变压器油耐压试验,高压电缆耐压试验,供电装置的触发装置性能测试与各种保护的整定试验,电气高、低压测量回路与仪表的校验。
LG 吸尘器 V-CF761HTV 英文使用说明书

How to keep the cleaner after using
Cord winding button
The cord winds up when you press the button. Insert the spiral of the inhaler into the groove in the back or at the bottom of the body
Disassembling
The exhaust filter should be cleaned at least once half a year. Allow exhaust filter to dry in a shaded location for a dry. Cover button of the exhaust filter
If inhaling is not well done?
Stage 1 Check if the control button of the inhaling power has been put to “MAX”.
Stage 2 Clean the protection filter of the motor.
Check before reporting the trouble
If you have a problem Packing List
17 18~19 20
21 22
23
24
25
26
27 28~29 30
267
V-CF761HTV 220V~ 50Hz
1400W 1600W
400W 4.5Kg Dust Capacity: 1.2L 256mm x 397mm x 267mm
布策指南:电动洁净器说明书

The Bosch guideto vacuum cleaners.Powerful cleaning performance matchedwith superb energy efficiency.Quality and Reliability Cordless Handstick Vacuums Handheld Vacuums Features Unique to Canister Vacuums Bagged Vacuums Bagless Vacuums Accessories462425323740ContentsTested for superior quality and reliability.The Hose Test:Withstands at least 40,000bends under 2 kg of weight.The Switch Test:Operates at least45,000 times.The Roller Test:Rolls over door thresholds at least 6,000 times.4Quality and ReliabilityThe Housing Test:Withstand being dropped 35times from carrying height.The Cord Retraction Test:Rolls up at least6,000 times.The Nozzle Test:Vacuums 500 kmwithout a fault.5Quality and Reliability6Cordless Handstick Vacuums Cordless Vacuum Cleaners.Our cordless range comes with high performance with an extra long life*. No cords. No limits.* F or selected Handstick models only.Cordless Handstick Vacuums710Cordless Handstick Vacuums: Unlimited Powerful Beyond Imagination with Unlimited. Experience infinite vacuum runtimeand intensive cleaning performanceon all floors.“I enjoy quality tools that free me from limitations, and the infinite runtime on the Unlimited provides exactly that.”Andy Yang Visual ArtistPopular works include:• “Artskins” for Night to Light Festival 2018• “The Many Glimpses of Drama” 2017• The Jaguar Art Experience 201711Cordless Handstick Vacuums: UnlimitedUnlimited PossibilitiesThere's a perfect accessory for every cleaning task.AllFloorHighpower brush.Suitable for all kinds of floors, from carpet to parquet.XXL Upholstery brush.Perfect for cleaning sofas and cushioned seats.Main core for light cleaning.Great for light cleaning withoutadded accessories.12Cordless Handstick Vacuums: UnlimitedThanks to multiple accessories, you can clean up dirt spots in all kinds of spaces.2in1 Upholstery& Furniture brush. Ideal for cleaning upholstery furniture and curtains.Long flexible nozzle.Brilliant at reachingcorners and tighspots, even in cars.Extension tube.Great for extendingthe range of yourreach.13 Cordless Handstick Vacuums: UnlimitedPerformance.Convenience.Powerful performance.The Unlimited contains the latest motor tecnology: The DigitalSpin motor. Rotates faster thanFormula 1 motor.Intensive cleaning results.The motorised AllFloor HighPower brush achieves through cleaningon all floor types.Optimum cleaning performance. Special bristles on the TwinBrush optimizes cleaning performance on both carpetsand hard floors.Especially handy.Thanks to the docking station with integrated accessories, youhave everything quick to hand. Especially hygienicThe hygienic filter in the cartridge ensures that exhaust air is evencleaning than the room air. Especially easy to clean.The RotationClean system delivers 99.9% filtration and makes it easy to clean in no time. Lifetime filter materialsincluded.Especially fast.The dust box is easy to remove and empty without coming intoany contact with dust.14Cordless Handstick Vacuums: UnlimitedBBS1224BBS1114Number of Batteries 2x 1x Type of Batteries Lithium Ion Lithium Ion Battery runtime on Turbo Mode 14 (2X7) min 7 min Battery runtime on normal Mode Infinite*up to 60 min Charging time ~45 min4-5 hrsHigh Power brush Yes Yes 2in1 brush YesYesCrevice Long flexible crevice toolLong flexible crevice toolUsable without accessories Yes Yes Quick Charger YesNoEmission 99.9% filtration Filter cleaning No filter washing needed Dust box emptying Suitable for small bins Nozzle cleaningNo tools neededProductoverview* R untime is infinite with two Bosch Power batteries running on normal power mode, thanks to the included Bosch quick charger where one battery can be charged while the other is in use. Standard runtime with motorised motor: up to 45mins Standard runtime without motorised motor: up to 60 minsW ithout motorized nozzle.15Cordless Handstick Vacuums: Unlimited16Cordless Handstick Vacuums: Flexxo Cleaning made easy and within reach with Flexxo cordless.We’ve set out to make vacuuming your home quicker, and more convenient.Integrated AccessoriesA versatile rangeof accessories areincorporated into theFlexxo vacuum for easyaccess and flexibility.Performance.Convenience.RobustAir SystemDust separation is now more efficient with the help of cyclonic air guidance and optimised sealings, ensuring cleaning performance is not compromised even when thedust box fills up.Extendable Crevice ToolWith a reach of up to 55cm, thecrevice tool can be attached toyour device for easy cleaning ofceilings or cupboard tops.Furniture/UpholsteryBrush Combination ToolThe furniture brush with extralong and soft bristles cleans yourdelicate surfaces effectively.The upholstery brush featuresrobust threadlifters that gets ridof hair clumps and dust from yourtextile surfaces.17 Cordless Handstick Vacuums: Flexxo18Cordless Handstick Vacuums: Athlet Powerful, cordless and the longest runtime with Athlet. The first cordless vacuum cleaner fromBosch with the cleaning performanceof a 2400-watt vacuum cleaner*.Because life should bethis easyResults comparable to aconventional vacuum cleanerat 2400 watts*The combination of a motorwith a highest capacity lithium-ion battery (32.4V) allowsthe Bosch Athlet vacuum tofunction up to 75 minutes.**Up to 75 minutes ofautonomous operationThe SensorControl systemsends an LED alert whenthe filter requires cleaning,ensuring optimal dust pick-upevery time you vacuum.SmartSensorControlOur Li-Ion batteries are safe touse and last longer due to anelectronic 3-step protectionsystem that prevents:Safe to Use Lithium-IonTechnologyOverheatingOverchargingDeep discharge** Operation time varies depending on the model and speed setting selected.ExceptionalPerformance19Cordless Handstick Vacuums: Athlet20Cordless Handstick Vacuums: Readyy'y Readyy'y 2-in-1and cordless.A cordless handstick vacuum cleaner with a detachable handheld design for easy manoeuvring and swift cleaning.Thorough cleaningThe crevice nozzle attachment makes it easier to vacuum innarrow spaces.Performance.Convenience.Better cleaning performance with shorter cleaning time. Its high airflow and motorised brush makes cleaning every corner of your home simple and faster.** A s compared to Readyy’y NiMH and based on dust pick-up from hard floors with crevice and motorised brush activation on low setting.Flexible nozzle jointUnrestricted cordless vacuuming around and under furniturethanks to the flexible nozzle joint.Faster ChargingIt requires only 5 hours to charge with Lithium battery, allowingmore frequent cleans.Easy cleaning brushThe motorised nozzle is quick and easy to clean thanks to thepractical EasyClean system.21Cordless Handstick Vacuums: Readyy'yProduct overviewBCH7ATH32K Athlet RunTime PlusBCH65RT25KAthlet RunTime PlusBCH6ATH25AthletHandstick Type Handstick Handstick Handstick Power (Voltage)32.4v25.2v25.2vPerformance Setting 333SensorBaglessMax RunTime (min)75min75min60min Type of Battery Li-ion Li-ion Li-ion Charging Time 6 hours 6 hours 6 hoursDust Container CapacityXL size(up to 0.9L)XL size(up to 0.9L)XL size(up to 0.9L)Washable Filter Motorized Brush Easy removable & clean brush Solid freestanding withoutdocking stationAccessoriesAccessory kit(Extra wide upholsterynozzle & Extra longcrevice tool)Accessory kit(Extra wide upholsterynozzle & Extra longcrevice tool)-22Cordless Handstick VacuumsBCH3K255Flexxo BBH3ZOO25Flexxo (Tornado Red)BBHL22140Readyy’y (Royal Blue)Handstick +Handheld Handstick +Handheld Handstick +Handheld Handstick +Handheld25.2v 25.2v 21.6v 18v 2222----55min 55min 45min 40min Li-ion Li-ion Li-ion Li-ion 5 hours 5 hours 4.5 hours 4.5 hours L size (up to 0.4L)L size (up to 0.4L)L size (up to 0.4L)L size (up to 0.4L)2-in-1 furniture / upholstery nozzle & extendable crevice toolProAnimal Brush Roll, upholstery nozzle & flexible extendable crevice nozzleCrevice tool Crevice tool23Cordless Handstick Vacuums24Handheld VacuumsBHN1840LCordless HandheldExcellent Cleaning Performance• High Airflow System efficiently separates dust and features a triple filter for thorough, lasting cleaning performance• Lithium-Ion Technology: Durable batteries for constantly high performance and short charging time• Runtime up to 40 min.Easy to use• Versatile cleaning: cordless, handy and lightweight – p erfect for quick in-between cleaning and cleaning car interiorsBHN2140LCordless HandheldExcellent Cleaning Performance• High Airflow System efficiently separates dust and features a triple filter for thorough, lasting cleaning performance• Lithium-Ion Technology: Durable batteries for constantly high performance and short charging time• Runtime up to 45 min.Easy to use• Versatile cleaning: cordless, handy and lightweight – p erfect for quick in-between cleaning and cleaning car interiorsOur canister vacuums feature the latest innovations for incredible cleaning performance and whisper quiet operation.Bagged andBagless Vacuums.25Features Unique to Canister Vacuums26Features Unique to Canister VacuumsDesigned with QuattroPower for maximum performance.A irSealSpecial sealingsprevent anyleakages of air.HiSpin Motor*Improved airflow withlow energy consumption.• 15% less energy consumption• Longer life span• Q uieter + Better performanceIntroducing QuattroPower system – designed to deliver class-leading dust pick-up. Every component has been optimized for maximum airflow and incredible cleaning performance.* M ade in Germany HiSpin Motor is only applicable to Boschbagged & bagless canister vacuum cleaners.High PerformanceFloors ToolsLead to Class Adust pick-up.PowerProtect DustbagAids in effective dust filtrationand thorough cleaning.27Features Unique to Canister Vacuums28Features Unique to Canister VacuumsThe quietest vacuumcleaner in the market.SilenceSound™ system delivers powerful dust pickup atthe lowest sound level, using a comprehensive packageof sound reducing measures.Aeroplane120dBRoad traffic83dB74TalkingExhaust system with optimised airwaysThe extra-large exhaust system with its special exhaust filter expels the air slowly and quietly.Silence motorThe new motor with its specially shaped impellers reduces noise.Noise-optimised connections All connections in theIn'genius are so well sealed that almost no air escapes and thus makes a noise.New, high-performance nozzle Larger, better-sealed airways with extra-wide and deep suction channel ensure outstanding cleaningperformance while keeping noise to a minimum.4dB59dBBosch In’ Genius ProsilenceBGL8SI59GB29Features Unique to Canister VacuumsThe technology provides an intelligent solution for lowmaintenance effort and still at optimal performance throughout its life time by having a internal sensor that continously measures airflow rates.When the filters become dirty and block airflow, the system will automatically power down and activate its own self cleaning process.SensorControl (Bagless and Athlet)The SensorControl System sends an LED alert when the filter needs cleaning.31 Bagged VacuumsPowerProtect Dustbag:(BBZAFGALL)For longlasting cleaning performance.Benefits:• 99.9% fine dust particles are filtered• U p to 60%* more suction powereven when dustbag fills up• Prevent blockage of airflow* S uction power with partly filled dustbag (400g) in comparison to Bosch Type G dustbags without PowerProtect technology, tested in an appliance of BSGL5... range. Suitable for all new Bosch bagged vacuum cleaners.BGL8SI59GBIn'genius ProSilenceQuietest vacuum cleaner with excellent cleaning performance • QuattroPower System• 650W Made in Germany Hi-Spin motor• Class A dust pick up on hard floor with crevice• Parquet brush, upholstery nozzle, crevice nozzle and furniture brush • SilenceSound System - 59dB(A)Suitable for Allergy sufferers • Washable Ulpa 15 filtration• AirSafe design reduces air leakage • New improved PowerProtect dust bag• XXL size dustbag volume up to 5LHigh manoeuvrability• 15m longest operation radius• 4 x 360ºwheels for maximum stability32Bagged VacuumsSuperSilent compact vacuum cleaner with thorough andquiet cleaning• QuattroPower System• 700W Made in Germany Hi-Spin motor• Class A dust pick up on hard floor with crevice• Hard floor nozzle, upholstery nozzle, crevice nozzle, universal nozzle and furniture brush• SilenceSound System - 69dB(A)Suitable for allergy sufferer • Washable HEPA13 filtration• AirSafe design reduces air leakage • New improved PowerProtect dust bag • XL size dustbag volume up to 4L High manoeuvrability• 4 x 360ºwheels for maximum stabilityBGL4S69AGBProSilence33Bagged VacuumsSuperb cleaning performance with low energy consumption • QuattroPower System• 650W Made in Germany Hi-Spin motor• Class A dust pick up on hard floor with crevice• Parquet brush, upholstery nozzle, crevice nozzle and furniture brushCost savings & cleaner air • Washable HEPA13 filtration• AirSafe design reduces air leakage • New improved PowerProtect dust bag • XL size dustbag volume up to 4L High manoeuvrability• 4 x 360ºwheels for maximum stabilityBGL3A330GBProEnergy34Bagged VacuumsBGN2A112GBCompactExcellent cleaning performance• 600W Made in Germany Hi-Spin motor • HEPA13 filter• Dustbag capacity – up to 3.5L• Crevice tool and upholstery nozzle• Class A dust pickup on hardfloor with crevice • Dust Re-emission Class AEasy to use• Compact size and light weight35Bagged Vacuums36Bagged Vacuums ProductEnergy efficient compact vacuum with thorough and quiet cleaning • QuattroPower System• SensorBagless Technology• 700W Made in Germany HiSpin motor• Extra long crevice tool, XXL upholstery nozzle, furniture brush• SilenceSound System - 75dB(A)Suitable for allergy sufferer• Washable HEPA13 filtration• AirSafe design reduces air leakage• XL size dust container volume, up to 1.9LEasy to use• Compact size and light weightBGS4UGOGBRunn'n ProSilence37Bagless VacuumsExcellent cleaning performance and low energy consumption • 700W Made in Germany HiSpin motor• Parquet brush, upholstery nozzle, crevice nozzle Suitable for allergy sufferer • Washable HEPA13 filtration• L size dustbag volume up to 3.5L (BBZ41FGALL)Easy to use• Compact size and lightweight• Versatile bagged or bagless cleaningBGN22128GB(Bagged & Bagless)38Bagless VacuumsBGS4UGOGB Runn’n ProSilence BGN22128GB (Bagged & Bagless)Max. Power Rating 700W 700W Filtration System Washable HEPA13Washable HEPA13Dust Container Volume XL Size (Up to 1.9L)L Size (Up to 3.5L)Operating Radius (M)98Noise dB(A)75 dB(A)82 dB(A)Crevice Tool Upholstery Nozzle Furniture Brush -Turbo Brush --Parquet Brush Energy Efficiency Class A B Total Energy Consumption (kWh)2834Cleaning Performance Class Hard FloorA C Cleaning Performance Class CarpetC D Dust Re-emission ClassAAProduct overview39Bagless VacuumsAccessories –Optional nozzles.BBZ124HDParquet DuoSoft Hard Floor NozzleBBZ42TBMattress ToolCarpetBBZ124HDParquet DuoSoft Hard Floor NozzleBBZ123HDHard Floor NozzleParquetBBZ42TBMattress NozzleMattressBBZ124HDParquet DuoSoftHard Floor NozzleTiles40AccessoriesCustomer service supportyou can depend on.Trust Bosch customer service tohelp you throughout the lifetime ofyour appliance.Experts repairs from our qualified engineers with only original spare partsCreate a MyBosch account to register your appliance warrantyAdded peace of mind with ourextended warranty plansOur Customer Call Center is available from Monday to Friday 9am to 6pm and Saturday 9am to 1pm at(65) 6751 5000. Closed on Sunday and Public Holidays.Bosch online store offers you the convenience to get your cleaning & care products, that will enhance the performance of your applianceAll Bosch home appliances are produced with maximum care, in high quality materials. We promise it in our 2-year manufacturer’s warranty on all appliances.41After Sales Care42For service repair and spare parts replacement,please contact:Customer Care Line:(65) 6751 5000Customer Service Center:38C Jalan Pemimpin #01-01 Singapore 577180Operating Hours:Monday to Friday, 8.30am to 5.30pm (Excluding Public Holidays) .sgWhilst every care has been taken in the preparation of this publication, Bosch does not warrant the accuracy or completeness of the information in this publication and Bosch reserves the right to alter specifications without notice. To the extent permitted by law, Bosch excludes all liability, including negligence, for any loss incurred in reliance on the contents of this publication. ©Copyright 2019 by BSH Home Appliances Pte Ltd. Company registration number: 199608497E. Printed in Singapore.To find out more about Bosch Home Appliances:Visit us @Bosch Experience Center 11 Bishan Street 21,Bosch Building #04-01Singapore 573943Mainline: 63561080Like us on Facebook :www.facebook/BoschHomeSGFollow us on Instagram :boschhomesg 43。
电除尘DKZ-2系列使用说明书

国电南自DKZ-2系列电除尘器电源及控制装置使用说明书国电南京自动化股份有限公司GUODIAN NANJING AUTOMATION CO.,LTD安全声明本装置要求专业技术人员进行安装!感谢您购买了国电南京电力自动化股份有限公司的DKZ-2系列电除尘器电源及控制装置,为了您能安全、正确、可靠、高效地使用本装置,请务必仔细阅读以下重要信息:本说明书适用于DKZ-2系列电除尘器电源及控制装置,确保环境条件满足设备运行要求。
为确保人身和设备安全,请注意以下事项:版本声明产品说明书版本修改记录表10987654321 V1.0 第 1 版 第 1 次印刷 V1.0 2007.08 序号说明书版本号修改摘要软件版本号修改日期*本说明书可能会被修改,请注意最新版本资料*2007年 8 月 第 1 版 第 1 次印刷*国电南自技术部监制目录1 概述 (1)1.1装置简介 (1)1.2装置结构 (1)2安装和接线 (2)2.1安装说明 (2)2.1.1安装准备工作 (2)2.1.2安装调试步骤 (2)2.2产品使用条件 (3)2.3产品安装注意事项 (3)2.4接线说明 (3)2.5接地注意事项 (3)3 装置说明 (4)3.1电源控制柜结构组成 (4)3.1.1屏柜壳体 (4)3.1.2可控硅部分 (4)3.1.3低压部分 (4)3.1.4 柜体布置图 (4)3.2面板说明 (6)3.2.1 DKZ-2型装置的面板说明 (6)3.2.2 DKZ-2A型和DKZ-2D型装置的面板说明 (13)3.2.3 DKZ-2B型和DKZ-2E型装置的面板说明 (22)3.3背板说明 (23)3.3.1背板布置 (23)3.3.2端子功能说明 (24)4操作说明 (28)4.1DKZ-2型装置操作说明 (28)4.1.1按键功能介绍 (28)4.1.2开关机操作说明 (29)4.1.3高压操作 (29)4.1.4低压操作 (31)4.1.5低压部件告警处理操作说明 (33)4.2DKZ-2A DKZ-2D型装置操作说明 (33)4.2.1按键功能介绍 (33)4.2.2开关机操作说明 (34)4.2.3高压操作 (34)4.2.4低压操作 (35)4.2.5电磁振打操作 (37)4.2.6故障处理操作 (38)4.3DKZ-2B DKZ-2E型装置操作说明 (38)4.3.1菜单说明 (38)4.3.2主画面 (39)4.3.3密码设定 (41)4.3.4控制方式设定 (43)4.3.5参数整定 (43)4.3.6详细运行状态 (45)4.3.7实时曲线 (46)5 DKZ-2B30低压控制器 (48)5.1面板布置 (48)5.1.1断路器 (50)5.1.2 指示灯 (50)5.1.3 工作方式选择开关 (52)5.1.4复位按钮 (52)5.2信号端子定义 (52)5.3主要规格 (53)5.4故障判断条件及处理 (55)5.4.1空载/开路 (55)5.4.2欠流 (55)5.4.3 过载/过流 (55)5.4.4 短路/堵转 (55)5.4.5 断相 (55)5.4.6 装置异常 (55)附录 (56)附表一自检故障信息一览表 (56)附表二高压故障信息一览表 (56)附表三低压故障信息一览表 (57)附表四电磁故障信息一览表 (58)附表五高压参数设定信息一览表 (59)附表六低压参数设定信息一览表 (61)附表七电磁振打部件参数设定信息一览表 (63)1 概述1.1装置简介DKZ-2系列电除尘器电源及控制装置(以下简称电源控制柜),是在剖析国内外同类产品的基础之上开发的新一代电除尘器电源及控制装置,为电除尘器提供高压供电控制和对电除尘器的全部低压设备进行控制和检测保护,使电除尘器始终工作在高效、安全的最佳状态下。
Philips Performer 99.9% 除尘电力筒清洗机说明书

Philips Performer Active Bagged vacuum cleaner99.9% dust pick-up 900 W4LTurbo brushFC8578/09Most powerful bagged vacuum cleaner by Philips Locks >99.9%* of dust with 50% longer bag usage**The Philips Performer vacuum cleaner delivers top cleaning performance with low energy consumption. Keep the air in your home clean and healthy too thanks to our Allergy Filter, which traps 99.9%+ of harmful particles.Superior performance•Revolutionary AirflowMax technology for strong suction power•99.9% dust pick-up* to deliver deep cleaning results•Allergy Filter captures 99.9% of particles — ECARF certified•TriActive+ nozzle to deliver high performance on all floors•Turbo brush, perfect for (pet) hair and fluff cleaning•900 W motor for high suction powerEffortless cleaning•ActiveLock couplings easily adjust to every task•Easy long-lasting bags fit into large 4 litre dust chamber•Soft brush integrated into handle, always ready to useHighlightsAirflowMax technologyUniquely designed dust chamber maximises capacity and airflow with a non-clogging dust bag, which enables strong suction power right up until the dust bag is full.High-efficiency 900 W motorHigh-efficiency 900 W motor delivers high suction power for deep cleaning results.99.9% dust pick-up*TriActive+ nozzle and high suction power ensure that you can vacuum 99.9% of fine dust*.Certified Allergy Filter Certified allergy filter captures 99.9% of dust particles - including pollen, pet hair and dust mites - ideal for allergy sufferers.Integrated brushDusting brush tool is built into the handle so it's always ready to use on furniture, flat surfaces and upholstery.Long-lasting 4 L S-bagsLarge 4 litre dust chamber and long-lasting universal bags allow optimum suction power until full, plus sealed, mess-free disposal.TriActive+ nozzleTriActive+ nozzle utilises 3 cleaning actions in one go. It features a larger opening at the front to suck up larger debris while the specially designed soleplate removes dust from deep within carpets. Air channels on both sides of the nozzle pick up any dust and dirt alongside walls or furniture.ActiveLock couplingsActiveLock couplings allow attachments to easily fit to the telescopic tube with a simple snap.Turbo brushThe rotating Turbo brush is designed for optimal cleaning of pet hair and fluff, opening up carpet fibres for a deeper clean.Issue date 2023-04-13 Version: 2.2.1© 2023 Koninklijke Philips N.V.All Rights reserved.Specifications are subject to change without notice. Trademarks are the property of Koninklijke Philips N.V. or their respective owners.SpecificationsPerformance•Input power (IEC): 650 W•Airflow (max): 32.17 l/s•Sound power level: 77 dB•Vacuum (max): 17.5 kPa•Input power (max): 900 WDesign•Colour: Deep BlackUsability•Tube coupling: ActiveLock•Action radius: 9 m•Carrying handle: Front•Tube type: Metal 2-piece telescopic tube •Power control: Rotary knob•Cord length:6 m•Wheel type: Rubber Nozzles and accessories•Accessories included: Crevice tool, Integratedbrush•Standard nozzle: TriActive+ nozzle•Additional nozzle: Hard floor nozzle, Turbo brushWeight and dimensions•Dimensions of product (LxWxH): 447 x 304 x234 mm•Weight of product: 5.2 kgSustainability•Packaging: > 90% recycled materials•User manual: 100% recycled paperFiltration•Dust bag type: s-bag Classic Long Performance•Dust capacity: 4 L•Exhaust filter: Allergy filter•Motor filter: Micro filter*99.9% dust pick-up on hard floors with crevices (IEC62885-2).Filtration performance is tested in accordance with DIN EN 60312/11/2008.**Calculated with a dust bag replacement at 80% of suction powerloss, compared to the Classic paper bag FC8019/01; measuredinternally on a Philips FC895x/09 range.。
EPMAX电除尘器电源控制器说明书
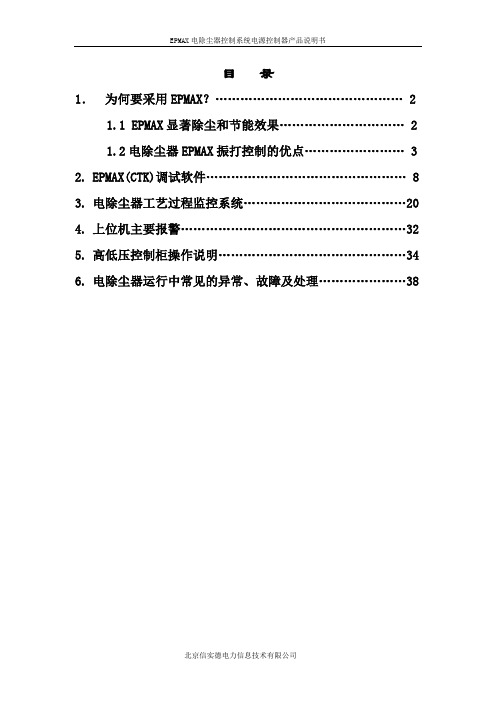
目录1.为何要采用EPMAX? (2)1.1 EPMAX显著除尘和节能效果 (2)1.2电除尘器EPMAX振打控制的优点 (3)2.EPMAX(CTK)调试软件 (8)3.电除尘器工艺过程监控系统 (20)4.上位机主要报警 (32)5.高低压控制柜操作说明 (34)6.电除尘器运行中常见的异常、故障及处理 (38)1.为何要采用EPMAX?EPMAX 与传统的电除尘器电源控制器相比,具有较高的除尘效率,显著的节能效果和低频度的振打方式;一般可达到节能30%以上,灰尘绝对排放降低10%以上和振打频度减少30%以上的运行结果。
以下以一个案例作为说明。
1.1EPMAX显著除尘和节能效果案例1:某电厂5号炉A侧电除尘器经改造后电控部分使用的是我公司集成的EPMAX 控制器。
该控制器内含电除尘器电源运行的优化软件ROQ,该软件采用间隔充电方式,根据电除尘器的运行情况(灰尘的浓度、特性,烟气的流速、温度、湿度等)实时的调整充电比和充电电流,减少反电晕的产生(在比电阻较高的情况下,效果尤其明显),从而达到最佳的除尘效率。
该电厂5号炉,灰尘的比电阻较低,因ROQ选用的充电比较低,第一电场基本选为1/5,第二电场基本选为1/9,第三电场基本选为1/7,第四电场基本选为1/5。
即便如此,A号除尘器的节能效果也是显著的。
采用EPMAX的 A侧除尘器电耗与采用传统的电控系统B侧除尘器相比,除尘效果明显。
表1:11月28日在锅炉运行工况相同的情况下的灰塵排放水平纪录A侧除尘器与侧除尘器(采用传统的电控系统)电耗列表如下,从该表中可以看出采用EPMAX的 A侧除尘器电耗与采用传统的电控系统B侧除尘器相比,降低约40%。
1.2 电除尘器EPMAX振打控制的优点EPMAX控制器有一个很独特的优点,即将高压部分可控硅的控制和低压部分振打的控制整合在同一个控制器内,实现电压控制振打(VCR)功能。
电压控制振打功能是指在振打运行的同时,把该电场内的二次电压和电流降下来(一般是把电流降到0),减小甚至关闭电场力的作用,使振打时,吸附在极板和极线上的特别细的高比电阻的粉尘容易被振落。
Vacmaster 16 Gallon 潮湿 干洗电动吸尘机说明书

Distributed ByCleva North America, Inc.601 Regent Park CourtReplacement Filters &Accessories available at:FOR YOUR SAFETY Read and understand this manual before use.Keep this manual for future reference.16 Gallon Model No. VJH1612PF 0201Operator’s Manual Wet/Dry VacuumWarranty…………………………………………………………………………………………...……... Safety Instructions & Warnings…………………………………………………………………….... Double Insulation Instructions………………………………………………………………………...... Extension Cords………………………………………………………………………………………... Unpacking & Checking Carton Contents………….……………………..…………….…………. General Assembly Instructions…………………………………………………………….………….... Dry Vacuum Operation……..………………………………………………………………………... Liquid Vacuum Operation…………………………………………………………………………..... Blower Operation……………………………………………………………………………………….. Maintenance……………………………………………………………………………….……………... Installing & Cleaning Cartridge Filter……….……………...………………..….…………….............. Installing & Cleaning Foam Wet Filter………………...………………….…..….………………..... Troubleshooting………………………………………………………………………………………….. Exploded View............................................................................................................................... Parts List…………………………………………………………………………..................................2 3 4 4 5 6 7 8 9 9 10 11 12 13 14SECTION PAGE Thank you for purchasing this Vacmaster® wet/dry vacuum cleaner. Feel confidentthat with Vacmaster® you are obtaining a high quality product engineered for optimalperformance. This vacuum is capable of picking up liquids and dry materials.FOR YOUR SAFETY: CAREFULLY READ AND UNDERSTAND ALL INSTRUCTIONS.We take pride in producing a high quality, durable product. This Vacmaster® product carries a limited five (5) year warranty against defects in workmanship and materials from date of purchase under normal household use. If product is to be used for commercial, industrial, or rental use, a 90 day limited warranty will apply. Please keep your receipt as proof of purchase. This warranty gives you specific legal rights, and you may have other rights, which vary from state to state. For product service call Customer Service at 1-866-384-8432.Not Covered by Warranty:• Any part that has become inoperative due to misuse, negligence, direct/indirect abuse, accidents, improper maintenance, repairs, or alterations;• Consumables such as filters and accessories;• Normal wear and tear of parts and attachments, such as hose, nozzles, or casters;• Normal deterioration of the exterior finish due to use or exposure;• Any product where serial number/data label is tampered with or removed;• Any product purchased from an unauthorized retailer.IMPORTANT SAFETY INSTRUCTIONS SAVE THIS MANUAL WARNING:FOR FUTURE REFERENCE.TO REDUCE THE RISK OF FIRE, ELECTRIC SHOCK, OR INJURY:READ AND UNDERSTAND ALL INSTRUCTIONS BEFORE USING THIS VACUUM. Read and understand this operator's manual and all labels on the Wet/Dry Vacuum cleaner before operating. Safety is a combination of common sense, staying alert, and knowing how your vacuum works. Use this Wet/Dry Vac only as described in this manual. To reduce the risk of personal injury or damage to your Wet/Dry Vac, use only Vacmaster ® recommended accessories.When using an electrical appliance, basic precautions should always be followed including the following:• Do not run vac unattended.• Do not vacuum, or use this Wet/Dry Vac near flammable liquids, gases, or explosive vapors like gasoline or other fuels, lighter fluids, cleaners, oil-based paints, natural gas, hydrogen, or explosive dusts like coal dust, magnesium dust, grain dust, or gun powder. Sparks inside the motor can ignite flammable vapors or dust.• Do not vacuum anything that is burning or smoking, such as cigarettes, matches, or hot ashes.• Keep cord away from heated surfaces.• Do not expose to rain. Store indoors.• Do not unplug by pulling on cord. To unplug, grasp the plug, not the cord.• Do not use with damaged cord, plug, or other parts.• If appliance is not working as it should, has been dropped, damaged, left outdoors, or dropped into water, return it to a service center.• Do not pull or carry by cord, use cord as handle, close a door on cord, or pull cord around sharp edges or corners.• Do not run Wet/Dry Vac over cord.• Do not handle plug or the Wet/Dry Vac with wet hands.• To reduce the risk of health hazards from vapors or dusts, do not vacuum toxic materials.• Do not use or store near hazardous materials.• Do not use this Wet/Dry Vac with a torn filter or without the filter installed except when vacuuming liquids as described in the operation section of this manual.• Do not allow to be used as a toy. Close attention is necessary when used by or near children.• To reduce the risk of injury from accidental starting, unplug power cord before changing or cleaning filter.• Do not leave Wet/Dry Vac unattended when plugged in. Unplug from outlet when not in use and before servicing. • Turn off Wet/Dry Vac before unplugging.• Do not put any object into ventilation openings. Do not vacuum with any ventilation openings blocked; keep free of dust, lint, hair, or anything that may reduce air flow.• Keep hair, loose clothing, fingers, and all parts of body away from openings and moving parts.• To reduce the risk of falls, use extra care when cleaning on stairs.• Unplug before connecting hose.• Use only as described in this manual. Use only manufacturer’s recommended attachments.• This appliance is provided with double insulation. Use only identical replacement parts. See “DOUBLE INSULATION INSTRUCTIONS”.When using as blower:• Direct air discharge only at work area. • Do not use Wet/Dry Vac as a sprayer.• Do not direct air at bystanders.• Keep children away when blowing.• Use safety goggles.Household TypeEXTENSION CORDSThis Wet/Dry Vac is double-insulated, eliminating the need for a separate grounding system. Use only identical replacements parts. Read the instructions for Servicing Double-Insulated Wet/Dry Vacs before servicing. Use this Wet/Dry Vac as described in this manual. Observe the following warnings that appear on the motor housing of your Wet/Dry Vac.When using an extension cord with your Wet/Dry Vac refer to the following table to determine the required A.W.G. wire size. Before using the cleaner make sure the power cord and extension cord are in good working condition. Make repairs or replacements before using the vacuum cleaner. Only use extension cords that are rated for outdoor use.• To reduce the risk of electric shock, unplug before cleaning or servicing.• DO NOT use without filters in place.CAUTION: TO REDUCE THE RISK OF INJURY FROM MOVING PARTS, UNPLUG BEFORE SERVICING.CAUTION:Do not vacuum drywall dust, fireplace soot, or ash with a standard Wet/Dry filter. This is a very fine dust which will not be captured by the filter and may cause damage to the motor. When vacuuming fine dust, use a fine dust filter (included). To purchase additional fine dust filters, call 1-866-384-8432 or get them at your local or online Vacmaster® retailer.DOUBLE INSULATED - GROUNDING NOT REQUIRED - WHEN SERVICING USE ONLY IDENTICAL REPLACEMENT PARTS.TO REDUCE THE RISK OF ELECTRIC SHOCK, DO NOT EXPOSE TO RAIN.STORE INDOORS.WARNING:Length of Extension Cord A.W.G. Wire Size Not recommended25 Feet 7.5 Meters50 Feet 15.25 Meters 100 Feet 30.5 Meters 150 Feet 45.7 Meters 110V-120V Amps 0-67-1011-1213-161818161416161612161414141212F GIKJ MRemove all contents from the box. Removethe power head and take out any contentsinside the collection tank. Check each itemagainst the carton contents list.Carton Contents List:Key Description ..…………....……….….... Qty.1121111111121ABCDEFGHIJKLMVac Assembly......................................Hose...................................................Extension Wands................................Utility Nozzle.......................................Crevice Tool........................................Floor Nozzle.......................................Foam Wet Filter..................................Cartridge Filter....................................Noise Diffuser.....................................4 Screws (Bag)...................................Caster Foot Assembly.........................Hose Storage Rack............................Operator’s Manual..............................Blower PortHandleCollection TankLatchDrainCaster FootPower HeadOn/Off SwitchHose Storage Rack Vacuum PortCasterWARNING: TO REDUCE THE RISK OF ELECTRIC SHOCK, DO NOT EXPOSE TO RAIN. MAKE SURE PLUG IS DISCONNECTED BEFORE ASSEMBLING THE WET/DRY VAC. UNPACKING YOUR WET/DRY VACUUM & GENERAL ASSEMBLY1. Verify that the power cord is disconnected from the outlet. (Fig. 1)2. Undo the latches. (Fig. 2)3. Lift the power head off the collection tank. (Fig. 3)4. Remove the contents from inside the collection tank; make sure you have all contents as listed on carton content list on page5. (Fig. 4)5. Turn the collection tank upside down and insert the four caster feet into the slots on thecollection tank and tighten with supplied screws. Verify that the casters are mounted correctly. Do not over-tighten screws. (Fig. 5)6. Position the hose storage rack as illustrated. Fully insert one end of the hose storage rack into the slot illustrated by the arrow, then pull the other end of the hose storage rack to align with the corresponding arrow and insert into the slot until it is secured in place. (Fig. 6a - 6d)7. Your vacuum comes ready for dry vacuum cleaning. For installation instructions, see page 10.8. For wet vacuum cleaning, install the supplied foam wet filter. See page 11 for filter installation.9. Place the power head back on the collection tank, and secure into place using the 2 sidelatches. (Fig. 7 & 8)10. Insert the locking end of the hose into the port on the collection tank and turn to lock into place. (Fig. 9)11. Choose the desired accessory and insert onto the end of the hose. (Fig. 10)NOISE DIFFUSERFor quiet operation, install the noise diffuser into the blower port by inserting the locking end of the diffuser into the blower port and turning clockwise to lock into place.POLARIZED PLUGTo reduce the risk of electrical shock, this appliance has a polarized plug (one blade wider than the other). This plug will fit in a polarized outlet only one way. If the plug does not fit fully in the outlet, reverse the plug. If it still does not fit, contact a qualified electrician to install the proper outlet.Do not change the plug in any way. Double insulation eliminates the need for the three wire grounded power cord and grounded power supply system.WARNING: BE SURE TO READ, UNDERSTAND, AND APPLY, INFORMATION ENTITLED ‘SAFETY INSTRUCTIONS & WARNINGS’. DO NOT VACUUM IN AREAS WITH FLAMMABLE GASES, VAPORS, OR EXPLOSIVE DUSTS IN THE AIR. FLAMMABLE GASES OR VAPORS INCLUDE BUT ARE NOT LIMITED TO: LIGHTER FLUID, SOLVENT TYPE CLEANERS, OIL-BASED PAINTS, GASOLINE, ALCOHOL, OR AEROSOL SPRAYS. EXPLOSIVE DUSTS INCLUDE BUT ARE NOT LIMITED TO: COAL, MAGNESIUM, GRAIN, OR GUN POWDER. TO REDUCE THE RISK OF HEALTH HAZARDS FROM VAPORS OR DUST, DO NOT VACUUM TOXIC MATERIALS.WARNING: DO NOT PLUG POWER CORD INTO POWER OUTLET. MAKE SURE PLUGIS DISCONNECTED BEFORE CHANGING THE FILTERS.1. Verify that the power cord is disconnected from the outlet. (Fig. 1)2. In order to prepare your vacuum for dry vacuuming, verify that the cartridge filter is securely mounted. Make sure the filter is pushed in until it stops against the power head. Your Wet/Dry Vac comes with the cartridge filter pre-installed. For installation instructions, see page 10.3. Optional: For improved dust filtering, fit collection bag flange onto the inlet port, taking care not to damage the bag. Dust bag sold separately.4. Place the power head back on the collection tank, aligning the top section with the latches, and snap into place . (Fig. 2)OPERATING INSTRUCTIONS: DRY VACUUMING5. Insert the locking end of the hose into the vacuum port and lock into place. (Fig. 3)6. Choose the desired accessory and insert onto the end of the hose. (Fig. 4)7. Plug the power cord into the outlet. (Fig. 5)8. Turn the motor on by flipping the power switch to the ‘I’ (ON) position and begin vacuuming. (Fig. 6)9. Once you have completed vacuuming, flip the power switch to the ‘O’ (OFF) position and unplug the power cord from the outlet.O = OFF I = ONDO NOT USE THE CARTRIDGE FILTER FOR LIQUID VACUUMING.DO NOT USE DUST BAG FOR LIQUID VACUUMING.CAUTION: DO NOT VACUUM DRYWALL DUST , FIREPLACE SOOT , OR ASH WITH A STANDARD WET/DRY FILTER. THIS IS A VERY FINE DUST WHICH WILL NOT BE CAPTURED BY THE FILTER AND MAY CAUSE DAMAGE TO THE MOTOR. WHEN VACUUMING FINE DUST , USEA FINE DUST FILTER (INCLUDED). TO PURCHASE ADDITIONAL FINE DUST FILTERS, CALL 1-866-384-8432 OR GET THEM AT YOUR LOCAL OR ONLINE VACMASTER® RETAILER.DRY VACUUMINGWARNING: BE SURE TO READ, UNDERSTAND, AND APPLY, INFORMATION ENTITLED ‘SAFETY INSTRUCTIONS & WARNINGS’. DO NOT VACUUM IN AREAS WITH FLAMMABLE GASES, VAPORS, OR EXPLOSIVE DUSTS IN THE AIR. FLAMMABLE GASES OR VAPORS INCLUDE BUT ARE NOT LIMITED TO: LIGHTER FLUID, SOLVENT TYPE CLEANERS, OIL-BASED PAINTS, GASOLINE, ALCOHOL, OR AEROSOL SPRAYS. EXPLOSIVE DUSTS INCLUDE BUT ARE NOT LIMITED TO: COAL, MAGNESIUM, GRAIN, OR GUN POWDER. TO REDUCE THE RISK OF HEALTH HAZARDS FROM VAPORS OR DUST, DO NOT VACUUM TOXIC MATERIALS.WARNING: DO NOT PLUG POWER CORD INTO POWER OUTLET. MAKE SURE PLUG IS DISCONNECTED BEFORE CHANGING THE FILTERS.LIQUID VACUUMING1. Verify that the power cord is disconnected from the outlet (Fig. 1). Make sure that the collection tank is clean and free from dust and dirt.2. Remove cartridge filter, then carefully install the foam wet filter over the filter cage and place the power head back on the collection tank. For filter installation instructions, see page 11.DO NOT USE THE CARTRIDGE FILTER FOR LIQUID VACUUMING.OPERATING INSTRUCTIONS: WET VACUUMING3. Fit the desired nozzle to the vacuum hose. (Fig. 2)4. Verify that the power switch is in the ‘O’ OFF position before plugging the power cord into the outlet. (Fig. 3)5. Turn the motor on by pressing the switch to the ‘I’ ON position. (Fig. 4)6. Once you have completed vacuuming, flip the power switch to the 'O' (OFF) position and unplug the power cord from the outlet.7. After use, empty the collection tank by unscrewing the drain cap. Drain liquids into a suitable receptacle or drain. (Fig. 5) Remember to refit the drain cap to the collection tank.IMPORTANT! When vacuuming large quantities of liquids, do not immerse the nozzle completely in the liquid; leave a gap at the tip of the nozzle opening to allow air inflow. The machine is fitted with a float valve that stops the suction action when the collection tank reaches its maximum capacity. You will notice an increase in motor speed. When this happens, turn off the machine,disconnect from power supply, and drain the liquid into a suitable receptacle or drain. To continue vacuuming, refit the collection tank with the drain cap. After wet vacuuming, turn the machine off and remove plug from power supply. Empty the collection tank, clean and dry the inside andoutside before storage. REMEMBER! The foam wet filter must be removed after wet vacuumingand a cartridge filter must be installed before dry vacuuming again.WARNING: ALWAYS WEAR SAFETY GOGGLES COMPLYING WITH ANSI Z87.1 (OR IN CANADA, CSAZ94.3) BEFORE USING BLOWER.WARNING: KEEP BYSTANDERS CLEAR FROM BLOWING DEBRIS.WARNING: WEAR A DUST MASK IF BLOWING CREATES DUST THAT MIGHT BEINHALED.This Wet/Dry Vac has blowing capabilities. To use the blower feature follow the instructions listed.1. Verify that the power cord is disconnected from the outlet. (Fig. 1)2. Make sure the collection tank is empty before using as a blower.3. Remove hose from the vacuum port. Remove noise diffuser from blower port.4. Insert the larger end of the hose into the blower port on the back side of the power head. (Fig. 2)5. Fit the desired attachment to the hose. (Fig. 3)6. Verify that the power switch is in the ‘O’ OFF position before plugging the power cord into the outlet. (Fig. 4 & 5)7. Before turning ON the vac, firmly hold the loose end of the hose. Turn the motor on by pressing the switch to the ‘I’ ON position. (Fig. 6)8. Once you have completed blowing, flip the power switch to the 'O' (OFF) position and unplug the power cord from the outlet. (Fig. 7)1. Verify that the power cord is disconnected from the outlet. (Fig. 1)2. Disconnect the hose from the vacuum. (Fig. 2)3. Undo the latches and remove the power head from the collection tank. (Fig. 3) Place power head on a soft, clean surface upside down.4. Clear all dirt or debris from the collection tank and hose . (Fig. 4)Emptying the Collection Tank5. Clean or replace the filters.6. Check the hose, attachments, and power cord to verify that they have not been damaged.7. Place power head on collection tank and secure latches.IMPORTANT! Clean or change the cartridge filter regularly for best performance. ALWAYS USE CARTRIDGE FILTER FOR DRY VACUUMING. If the machine is used with out the cartridge filter, the motor will burn out and the warranty will be voided. Always keep spare filters on hand. NOTICE! The filters included are made of high quality materials designed to stop small dust particles. The cartridge filter should be used for dry pick-up only. A dry cartridge filter is necessary to pick up dust. If the cartridge filter is wet, it will clog quickly and be very difficult to clean. Handle the filter carefully when removing it for cleaning and replacing it. Check the filters for tears or small holes, a small hole can let dust pass through and out of filter. Do not use a filter with holes or tears; replace it immediately.Installing Cartridge Filter 1. Verify that the power cord is disconnected from the outlet. (Fig. 1)2. Remove power head and place in upside down position.3. Install the cartridge filter over the filter cage with the flat end of the filter towards the power head. Carefully push filter in until it stops against the power head. (Fig. 2 & 3)4. Place filter retainer on top of cartridge filter over the raised lip and tighten down by turning retainer clockwise; do not over-tighten. (Fig. 4 & 5)Removing and Cleaning Cartridge Filter 1. Unlock and remove the filter retainer by turning retainer handle counter clockwise.2. Carefully hold and pull the cartridge filter up for removal. (Fig. 6)3. Clean the cartridge filter by gently tapping or brushing dirt off. Cleaning should not be done indoors in living areas. For optimal performance a new filter is recommended.Before storing your vac, the collection tank should be emptied and cleaned. The cord should be wrapped and hung on the hook of the handle. The hose and accessories should be stored as illustrated above (Fig. 1-3) so they can be readily available when needed. Store vac indoors.WARNING: ALWAYS DISCONNECT THE PLUG FROM THE POWER OUTLET BEFORE REMOVING THE POWER HEAD FROM COLLECTION TANK.4. Install cleaned or new filter as instructed above in steps 2 and 3 of Installing Cartridge Filter.5. Wet filters should be removed and allowed to air dry for 24 hours before installing onto the filter cage.IMPORTANT! Clean or change the cartridge filter regularly for best performance.ALWAYS USE CARTRIDGE FILTER FOR DRY VACUUMING. If the machine is used without the cartridge filter, the motor will burn out and the warranty will be voided. Always keep spare filters on hand.WARNING: ALWAYS DISCONNECT THE PLUG FROM THE POWER OUTLET BEFORE REMOVING THE POWER HEAD FROM THE COLLECTION TANK.Installing Foam Wet Filter1. Verify that the power cord is disconnected from the outlet. (Fig.1)2. Remove power head and place in upside down position. Follow instructions to remove cartridge filter.3. Carefully slide foam wet filter down over the filter cage making sure the cage is completely covered. (Fig. 2 & 3)4. Place the power head onto the collection tank.Cleaning Foam Wet Filter1. With the removed power head in an upside down position, carefully remove foam wet filter. (Fig. 4)2. Use a mild soap and water solution to wash foam wet filter and rinse with clean water. (Fig. 5)3. Allow filter to air dry before installing and using again.WARNING: TO REDUCE THE RISK OF ELECTRIC SHOCK, UNPLUG BEFORE TROUBLESHOOTING.SymptomPossible Causes Corrective ActionVacuum will not operate1) No power supply.1) Check power supply – cord, breakers, fuses.2) Faulty power cord.2) Unplug and check the power cord. If damaged, have it repaired by a professional.3) Collection tank full.3) Empty collection tank.Dust comes out from motor cover.1) The cartridge filter is missing or damaged.1) Attach or replace cartridge filter.Reduced efficiency and motor/speed vibration.1) There is a blockage in the nozzle, hose, or the collection tank inlet. The cartridge filter is clogged by fine dust.1) Check nozzle, hose and c o l l e c t i o n t a n k i n l e t s f o rblockage. Take off the filter and clean it or install a newcartridge filter.Part Drawing Number Description Quantity 1551006102Hose Holder 22Power Head Assembly 1 3551006103Float1 4551005104Filter Cage15Collection Tank1 6551007105Vacuum Port Assembly1 7551002110Drain Cap Assembly1 8551007106Caster Foot Assembly49V2EW Extension Wands2 10551004104Filter Retainer 1 11VCFF Cartridge Filter1 12551060104EVA Hose1 13V2FBS Floor Nozzle1 14V2CT Crevice Tool 1 15V2UN Utility Nozzle1 16551002117Noise Diffuser1 17VFF51Foam Wet Filter 1。
- 1、下载文档前请自行甄别文档内容的完整性,平台不提供额外的编辑、内容补充、找答案等附加服务。
- 2、"仅部分预览"的文档,不可在线预览部分如存在完整性等问题,可反馈申请退款(可完整预览的文档不适用该条件!)。
- 3、如文档侵犯您的权益,请联系客服反馈,我们会尽快为您处理(人工客服工作时间:9:00-18:30)。
ESP Operation InstructionsContents1. Equipment Name and model (1)3. Use and design condition (1)4. Size and technical parameters (2)5. Operational principle (2)6. Structure Characters (3)6.1 Shell (3)6.2 Ash hooper (4)6.3 Sustain axletree (4)6.4 Cathode system (4)6.5 Cathode suspend (5)6.6 Cathode quiver (5)6.7 Anode system (6)6.8 Anode quiver (6)6.9 Steel bracket (7)6.10 High pressure silicon commutate equipment and control (7)7. Special items specification (7)8. Using and maintain of the equipment (7)8.1 Safe rules (8)8.2 Debugging of the electrofilter (10)8.3 Operation rules (12)8.4 Electrofilter maintain (14)8.5 All the services the manufacture’s supply (16)9. ABB-electrofilter (17)1. Equipment Name and model1.1 Name: electrofilter1.2 Model: in the technical protocol2. Equipment Shape (in the Equipment outside drawing) and weight2.1 Electrofilter Shape Size(long*width*height): in the general drawing2.2 Equipment weight: in the general drawing3. Use and design condition3.1 Use for the fume cleaning of the coal burning boilerAccording to the user’s requirements, one or more electrofilters supply for one boiler. The electrofilters install between the air preheater and the induced draft fan. They are connected by the air flue.This equipment designed by the FLAKT Company’s electrofilter technique. Its capability is well and the service life is long.3.2 Design condition: fume volume, fume pressure, fume temperature, coal composition, fume composition, dust percent, and dust composition, all the parameters are consulted to the technical protocol.3.3 Capability parameters3.3.1 Efficiency of dust collection: seen in the capability ensure term of the technical protocol3.3.2 Fume resistance: seen in the capability ensure term of the technical protocol3.3.3 Leak rate: seen in the capability ensure term of the technical protocol3.3.4 Noise: seen in the capability ensure term of the technical protocol3.3.5 If the equipment run in the non-design condition, the capability parameters can be adjusted consult to the following correction curve and correction fomula.3.3.5.1 Inlet dust percent correction factor; Cdust3.3.5.2 Fume volume correction factor Cgas3.3.5.3 Inlet fume temperature correction factor Ct3.3.5.4 Sulfur percent in the coal correction factor Cs3.3.5.5 Flow together cut percent correction factor Carea3.3.5.6 Adjust formulaTotal correction factor: CT=Cdust×Cgas×Ct×Cs×CareaDesign K: KM=KD×CTKD={ In [ l00 / (100一EFFD) ] }EFFD—capability ensure efficiencyEFFD=ionconcentratdustinlet ionconcentratdustoutletionconcentratdustinlet×100% Correction K: KM=KD×CTCorrection dust collection efficiency: EFFM=1-e-KM4. Size and technical parameters(The size of ABB model electrofilter can be seen in the technical protocol )5. Operational principleOperational principle drawing of the electrofilter6. Structure Characters (in fig.1)6.1 Shell (in fig.2)Shell is the important part of the electrofilter. Its design connects to the total fee, installation and basement work of the equipment.The structure of the shell is sealed welding. It includes the shell side board,gable wall board and the roof prefabricate board. The side board is the horizontal or self-sustain structure. The main load transfers from the roof board to the upright column and then transfers along the upright column to the basement.The side board design uses minimum pivots.The capital upright column in the big electrofilter can transfer the load to the basement directly.Inside upright column installs in the check channels between every electric field.This structure can detract the load without high-loading materials. And the structure can ensure fastness and the electrode vertical. The machine can run in high efficiency. And most of the manufacture work can be finished in the factory. This can ensure high quality.6.2 Ash hooper (in fig.3)The dust marshals to the ash hooper. At the bottom (about 30 to 50 percent of the altitude of the ash hooper) of the ash hooper, there is effect heater to avoid ash coagulation. The block board on the bottom is used to avoid the electric field leak and ash expands.The maximal angle of the ash hooper is 35 degree.6.3 Sustain axletree (in fig.4)The sustain axletrees are installed between the shell upright column and the steel bracket to avoid the anomalistic load caused by the head expand. The sustain axletree is made by low friction material. There is ball connection on its bottom. And it can glide along the horizontal orientation and circumrotate without high load.6.4 Cathode system (in fig.5)The cathode system is the heart of the electrofilter. The cathode line is used to make the corona. It is on the symmetrical site of the electric field to avoid short circuit. The others, the cathode system must be easy to maintain and can’t be affected by the temperature. This can ensure the electrofilter running normally.The cathode line appends between the frames. The up down and middle frame coupling firm together with the suspend beam. All the frames suspend on 4 insulating bushings. The insulating bushings install on the roof heat insulating box. This can ensure the gas insulates with the outside.The design of the frame ensures the maintain workers can walk on it without any distortion. The middle frame shortens the length of the cathode line. The cathode line swings little and easy to bring effect quiver after quivering.The main characters of designing of the cathode system is as followings.The cathode line is the total tube awn line. There is protected equipment on theconnection of the cathode frame and awn line. The install model of the frame and awn line connection board is the double fasten of the inserting and bolt. This can ensure the cathode line without line drop. The running efficiency of the cathode line is 100 percent. This can avoid the electric field opening which caused by the bolt cut. The electrofilter can run stably for a long time.The corona line chose according to different dust.6.5 Cathode suspend: (in fig.7)The sustain insulator on the shell roof is installed in the sealed heat insulation box. There is a pole cover on the heat insulation box. It is easy for the heat insulation box maintain.The transformer is installed on the roof of the electrofilter. It connects with the cathode system via the leas. There are steel structure roof and onetrack suspend on the roof. It is easy to maintain. If the transformer is out work, we can use the onetrack suspend to suspend the transformer to the ground to maintain.6.6 Cathode quiver: (in fig.8)During the course of the dust catch, a small part of the dust will attach on the cathode frame and the cathode line. If the dust can be clear in time, the gathered dust will cause corona close down. And the efficiency of the dust catch will low. So the gathered dust on the cathode system must be cleared by effectively quiver. The quivering is finished by the hammer. The hammer is installed on the horizontal axis. It bumps the frame in turn. The hammer quivers on the pole of the connection of the middle frame.The hammer has high strength and can work in the fume without failure.Every bus-bas has one se quivering equipment. This can be seen in fig.9. The quivering driver installs on the electrofilter roof. It is the roof transfer. Some others are connected on the quivering axis directly. This can be seen in fig.10. It transfers via the shell side board. It is the side transfer.The driver equipment is installed on the up part of the insulator heat insulation of the roof transfer. The insulator is installed in the heat insulation box. There is check door on the insulation box to maintain and clean the insulator. The roof transfer changes to theside quiver use the pin wheel. This can be seen in fig.11. This pin wheel structure will not cause the dust block. It can work in any fume and do not need adjust and maintain.The running of the quiver equipment uses programming motor and PC control. The programming motor and PC machine can workout the best quivering frequency. We will commend one set quivering frequency table as the following. During the running course, you can adjust it according to actual condition.Quivering frequency tableDust character: normal Inlet fume concentration: 2~50g/Nm3Electricfield quantity Quivering periodCathode quiver Anode quiverA B C D E A B C D E2Quiver time (min) 2 4 1 3Circulate time (min) 10 10 10 303Quiver time (min) 2 4 6 1 3 5Circulate time (min) 10 10 30 10 30 60 4Quiver time (min) 2 4 6 6 1 3 5 5Circulate time (min) 10 10 30 30 10 30 60 90 5Quiver time (min) 2 4 6 6 6 1 3 5 5 5Circulate time (min) 10 10 30 30 30 10 30 60 90 90 6.7 Anode systemAnode system is the other important part of the electrofilter. FLAKT Company usesthe GS3-750C/480C model polar plates. The width of the polar plates is 750mm/480mm.The shape of the polar plates can be seen in fig.12. Compared with normal polar plates,this type polar plate improves the rigidity and eliminates the sharp angle spark. It isdesigned without welded line. And there is a strengthen hole on roof of the polar plates forthe top structure suspends.The bottom of the polar plates connects with the bounce pole use self-locked bolt without any welded line. And the quivering chopping block also connects with the high strength bolts. Polar plates bounce pole orients exactly from the side.6.8 Anode quiverEvery line polar plates have one hammer. It is similar to the cathode quiver. The quiver strength distributes to every polar plates via bounce pole. And the strength will not centralize to one point. We choose a minimum acceleration according to the structure antifatigue life and the quivering availability. This can ensure the acceleration uniform.To keep the proper acceleration is aim to make the dust sheet to slid to the ash tooper. This can avoid the dust fly upwards.The frequency of the quiver is also need to be controlled as low as possible. This can improve the efficiency of dust remove.6.9 Steel bracketThe steel bracket is composed of upright column, waler and diagonal bracing.The upright column has three models. One is use channel steel to form the frame. And the other is use H steel. And the third is use big caliber steel tube. We choose the third model.6.10 High pressure silicon commutate equipment and controlThe details of the high pressure silicon commutate equipment and its control can be seen in the electric products specification.7. Special items specification7.1 This specification introduces the basic circumstances of the equipment. Everybody who will use this equipment needs to read. Also everybody needs to read the content of the 8th section, especially for the self safe regulations.7.2 This equipment is the large outdoor construction. We take full consider on the self safe. All the walkways, stairs and railings are firm. And the check-doors are marked with high pressure sign.7.3 Material level-sensing equipment uses the capacitance level-sensing device. Its capability is well and easy to maintain. If you catch by some questions during debugging and daily using course, the factory will supply the on- site service and guidance.8. Using and maintain of the equipmentThe electrofilter is the large outdoors all-around equipment. Right using and effective management is important to its normal running and prolong its life. So everybody who will use this equipment needs to take a special training for using the electrofilter. And also the buyer needs to organize a special manage organization to take charge of the electrofilter’s using and maintain.This section includes the safe rules, debugging, operation rules, maintain and what service the producer can supply of the electrofilter.8.1 Safe rulesAll the workers who work on the electrofilter must stand to the safe rules, include the temporary workers, example for the check workers and the maintain body and so on. There must be a special safe administrator.8.1.1 Self-safe of the workers8.1.1.1 When work in the shell and on the roof of the electrofilter, the workers must wear the safe-cap and tie the safe-belt.8.1.1.2 When work in the electrofilter, the workers must wear the mask or the respirator. The type of the respirators chose by the type of the dust in the fume. Sometimes the workers must be supplied with the pressed air to breath.8.1.1.3 The percentage of the oxygen in the fume must be more than 20. This can be determined by the machine.8.1.1.4 If the oxygen in the fume is less than 20 percent, we must use the pressed-air equipment to supply fresh air.8.1.1.5 The workers must wear the work clothes with the cap and gloves, mask and rubber shoes. The edge of the work clothes, gloves, mask and shoes must be sealed. And the work clothes must be cleaned after work.8.1.2 Check safe rulesThe works who check the electrofilter must be minimum two. Before check the electrofilter, the check workers must learn the types of the fume and dust and what harm it will cause, and what safe protect ways we can take. This can be seen is some files. The worker who mainly takes for the check work must be familiar with the structure and partsof the electrofilter. If there is any dager, he must know what to do. We also must take consider on the dust get together, wire and blast and so on. After finishing the check work, the manager must check the amount of the workers to avoid leaving somebody in the electrofilter to cause danger.Stand to the following rules when you enter into the electrofiter,8.1.2.1 1.1 section of the self-safe rules.8.1.2.2 1.4 section, safe rules for check the high pressure silicon commutate equipment 8.1.2.3 Shut down all the quivering equipment and transfer machine motor, and use the lock to insure.8.1.2.4 Shut down the safe-switch of the high pressure silicon commutating equipment and use the lock to insure. The high pressure separate switch must be adjusted to the earth connect site.8.1.2.5 The check worker must use the earth connect stick or other effect tools to make the cathode system connect the earth. The site of the cathode is in the roof heat insulation box and the anode quivering platform check-door.8.1.2.6 Shut down the switch of the draft fan and use the lock to insure. If the draft fan is used by more than one electrofilters, don’t shut down the switch and shut down the walkway air door.8.1.2.7 Shut down the air door and electric equipment and lock to insure.8.1.2.8 Open all the check doors, and wait until the temperature is low enough. If need to low the temperature quicker, we can open the air door and the draft fan.8.1.2.9 If the draft fan is running when the workers work in the electrofilter, we must take consider of the body bear ability and the danger during operation. First lock thecheck-door on the locked site to avoid the check-door shut self.8.1.2.10 The check worker must prevent scalding.8.1.2.11 After enter the electric field, first check if there is any dust accumulates. If there is any, first clear and find the reason for the dust accumulates before re-running the electrofilter.8.1.2.12 If need to check the dust, first check the model of the level-sensing device.Operate according to the product using specification. Shut down the valves.8.1.2.13 Check the amount of the check tools after checking to avoid leaving in the electric field.8.1.3 Safe check of the equipment8.1.3.1 Checking the earth connection ability of the earth connect equipment and other protect equipment.8.1.3.2Checking the lock of the control box and switch box, other body can’t open the lock.8.1.3.3 The voltage of alternating current used on the hand light and other electric tools of the elec trofilter inside roof can’t higher than 50.8.1.4 Safe rules for high pressure silicon commutate equipment checking8.1.4.1 Shut off the power supply of high pressure silicon commutate equipment, put the switch on off site and lock to insure.8.1.4.2 Check the switch on the high pressure control board turn off.8.1.4.3Put a board marks with ―working on‖ on the high pressure control box conspicuous site.8.1.4.4 Check the ground lead.8.1.4.5 Connect the high pressure parts of the high pressure silicon commutate equipment with ground lead material.8.2 Debugging of the electrofilterAfter the installment of the electrofilter, it is must be debugged. All the debugging data must be noted for compare.8.2.1 Adjust the distance between the cathode and anodeIn order to get high dust remove efficiency, the distance between the cathode and anode must be controlled seriously. After the installment of the equipment, we must adjust the distance seriously. The cathode line must be put in the middle of the channel. And the windage is less than index value.Adjust the distance between the cathode and anode by measue the distance between the cathode frame plane and the up pole board edge plane.8.2.2 Air current distribute testThis test is used to test the gas distribution.8.2.2.1 Test site: can choose one site to test. If want to test for the whole equipment, choose the site after the first electric field8.2.2.2 Test area: divide the test cross section into a series of rectangle little area, the area is about one square. The test site is the center of every little area.8.2.2.3 RMS is the test assess standardV n V Vi r n i i ⨯--=∑=)1()(σIn the equation: Vi —— Actual wind rate(m/s)V ——Average wind rate=∑=ni Vi n 11 n ——Total test points8.2.2.4 If the test value is bigger than the index value, adjust the guide plate site. Then test until equal to the index value.8.2.3 No-load voltage current characteristic testAfter equipment installation is completed, voltage rising test is carried out to each electric field (power supply area) which is supplied with air. It can be used as a way to inspect the installation quality of ESP anode and cathode system.The way of the boost pressure test is as following:8.2.3.1 Clean the electric field to make sure there is no rubbish in the channels.8.2.3.2 Clean all the insulators, such as the insulate bushing, china axis, high pressure wall bushing and electric heater.8.2.3.3 Check the high pressure silicon commutate equipment according to the product specification before running8.2.3.4 Shut the check door and confirm there is nobody in the electric field8.2.3.5 After the electric heater working 24hs, supply the electricity by every electric field,boost the pressure slowly. Write down the electricity value every boost 2kv until to the rated value. Give out the voltage current characteristic curve. This can be the no-load voltage current characteristic standard for every installation quality and every large mend. This test can do three times. Give out a curve according to the average value.8.2.4 Wind leak testFirst shut down the inlet and outlet door of the gas channel. Then make the smoke screen in the equipment. And then shut down all the check doors. Look the fume leak circumstance. Write down and repair.The other way, open the draft fan shut the check door, using the lighter to check every weld line. If the light is excursion to the weld is leak. This way can also check the check door.8.2.5 Adjust the quivering timeBefore the equipment leave the factory, the quivering time has been adjusted. The adjust value can be seen in the 6.6 section quivering frequency table.Programming motor and the PC control quivering can adjust the quivering time in any time.8.3 Operation rulesElectrofilter operation rules have following four steps: check before running –start—running-stopOperate the electrofilter must according to the running rules. Don’t forget the safe rules.8.3.1 Check before running8.3.1.1 Check the electric field, channel and ash hooper if there is any tools or other rubbish, such ash wiriness, weld, bolt and so on.8.3.1.2 Make sure the electric machine running orientation is right. Open the quivering electric machine, ash drain equipment. Rotate machine is slid and the electric machine insurance is working. Check the height of oil level is equal to standard and the quivering point is on the middle and the site of the hammer is normal.8.3.1.3 Check the surface of every insulate bushing, china axis and high pressure wallbushing is clear and without any crack.8.3.1.4 Check the temperature relay of the electric heater. And adjust the up and down limit.8.3.1.5 Check the transformer. Leak the oil or not.8.3.1.6 Check the transformer connects to the ground. The connect ground resistance is less than 4Ω.8.3.1.7 There is no body in the electrofilter.8.3.1.8 Remove the special ground connect stick or other ground connect tools on the cathode system.8.3.1.9 Check all the man pole doors. Such as the sealed slim, shut down and the bolt and lock and so on.8.3.1.10 Shut down the heat insulate box door and locked it.8.3.1.11Check the alarming equipment on the electric control board. Press the ―try‖ button to test alarming.8.3.1.12 Check the power net pressure.8.3.1.13 Check the inlet and outlet wind doors.8.3.1.14 Check the level machine. Adjust the zero site.8.3.1.15 Check the tube system of steam heat system. Such as the leaking, flange and valves.8.3.2 Start8.3.2.1 After the check before starting, all the safe rules is down and the workers are confirmed.8.3.2.2 Electric heater has work 24hs before starting to make sure the ash hooper and all insulators are dry. If use the steam heater, need to work 24hs before.8.3.2.3 Check the current of the electric heater.8.3.2.4 Start the ash transfer system8.3.2.5 Start the quivering structure8.3.2.6 Open the doors of the inlet and outlet tubes8.3.2.7 Start the draft fan8.3.2.8 After the whole system running, the out strength of the boiler is 30%MCR. During the Plenty burning circumstance, the electrofilter can start. The cathode and anode are all running.8.3.3 RunningCheck the equipment running circumstance, and check as the following steps:8.3.3.1 Check the working current of the heater system and write down.8.3.3.2 Check the index light of the control board and alarming system. If there is any abnormity, please write down.8.3.3.3 Check the current rectifier and write down.8.3.3.4 Check the ash transfer system.8.3.3.5 Check the quivering axis and hammer. (If there is any un-normal, this can hear out the check door.)8.3.3.6 If the high pressure silicon commute equipment is out door, check the transformer oil disk liquid height. Drain the raining water in the oil box.8.3.4 StopIf need to stop the equipment, do according the following steps:8.3.4.1 Shut off the draft fan, and cut off the fume in the channel.8.3.4.2 Shut down all the commutate machine of every electric field.8.3.4.3 Shut down all the wind doors of every inlet and outlet channels.8.3.4.4 Let the quivering system and ash transfer system work about 2 hours. Drain all the ash out the electric field.8.3.4.5 Shut off the quivering equipment and ash transfer system.8.3.4.6 Shut down the power.If the stop is temporary, let the quivering equipment and ash transfer system work. 8.4 Electrofilter maintainThe daily maintain for the electrofilter is very important.8.4.1 Daily maintain8.4.1.1 One body maintains the electrofilter specially. He must be seasoned of the electrofilter. And the operator must be training carefully and be fluent to the electrofilterstructure and function.8.4.1.2 The operator check the equipment running circumstance and write down.(include the pressure ,electric current and second pressure and electric current)8.4.1.3 During the running course, the operator must check the quivering structure working circumstance and other electric danger. If there is any danger, give note to the check apartment. This can be seen in the danger exclude way.8.4.2 Maintain when the equipment is stopWhen the machine stops because of some trouble, we must check the electrofilter all-around. The machine must be middle checked every one year. Make out the check plan according to the check time. Include exchange the electric pole and some easy spoiled parts. The machine must big large mend every four years. Check the electric field and adjust and exchange some parts spoiled or affect the ability. And the lubricating oil must be changed in time.Once the machine stops, we can do some normal check, the contents are as follows: 8.4.2.1 Clean the ash in the electric field.8.4.2.2 Check if there is any cauterization on the electric field side plate, check door, roof plates , pole plate ,outside plate and other heater transfer parts. Analyses the reason and finish it.8.4.2.3 Check the transfer machine’s temperature, the inside oil plate of the reduction box, quivering axis axletree blocks or not, hammer can rotate or not. Exchange or add the oil according to the electric machine product requirements.8.4.2.4 Check ash on the distribute plate, and clean it.8.4.2.5 Check the cathode line. Use 1 point 5 meter stick hit the helix line in the channel orientation. If the cathode line is lax, it can be checked. If the helix line step distance is different, it is corrosive. Exchange the cathode line according to the check circumstance. If the own line hit without drop, this can confirm the own line is good.8.4.2.6 Check the anode plate.8.4.2.7 Brush the bushing every time when the machine is stop. Check if there is any small crack by the hand light. Discharge the bushing when brush it. This can be seen insustain axis insulate tube change way of the ―danger eliminate way‖ .8.4.2.8 Check the connect ground site. Check the resistance, corrosion and other mechanic block.8.4.2.9 Check the connect switch, electric cut machine. Clean the control board and exchange the damaged parts.8.4.2.10Check the check door’s seal ability. Exchange the sealed material according to the actual circumstance.8.4.2.11 Check the high pressure silicon commutates equipment. If there is any fault, check it according to the electric company’s specification.8.4.2.12 Check the heat parts. If it is damaged, exchange it.8.4.2.13 Check the quivering axis. If the site the hammer hit change 5 centimeters, change it.8.4.2.14 Check all the protect equipment and all the locked parts.8.5All the services the manufacture’s supplyWe can supply all the services as followingsIf you catch with some troubles when you check the faults or need to diagnose the equipments before big or middle mend, we can send one of our engineers to help settle the problems. He will give out the way to settle all the problems and supply some improve measures. And he will chat with the equipment operators, give them some technique items and tell them how to operate the machine effectively.The engineer will give out a hard copy report about his on site check of the equipment. This will give to our company’s research apartment to improve design and commend this specification.9. ABB-electrofilterFig.1Fig.2 ShellFig.3 Ash hooper heater and airflow damping plate designFig.4 Sustain axletreeFig.5 Electric discharge system steel frame design。