催化裂化汽油加氢脱硫技术及工艺流程分析
汽油加氢处理工艺流程

汽油加氢处理工艺流程是一种利用氢气对汽油进行加氢反应的工艺,以提高汽油的质量和性能。
汽油加氢处理主要是通过加氢裂化、加氢脱硫、加氢脱氮和加氢脱芳等工艺来提高汽油的辛烷值、减少硫、氮等杂质的含量,提高汽油的清洁度和燃烧效率。
汽油加氢处理工艺流程通常包括以下几个主要步骤:1. 精制汽油原料的准备:首先需要将原油经过初步的精制处理得到催化裂化汽油或者石化汽油。
这些原料汽油包含大量的不饱和烃、硫、氮和芳烃等杂质,需要通过加氢处理来改善其性能。
2. 加氢裂化:将精制汽油原料与氢气混合,并通过加热至一定温度、压力下进行加氢处理,使得其中的不饱和烃(烯烃、芳烃)和饱和烃发生加氢反应,生成高辛烷值、低芳烃含量的汽油。
加氢裂化是汽油加氢处理的核心步骤。
3. 加氢脱硫:经过加氢裂化处理后的汽油还含有一定量的硫化物,需要进行加氢脱硫处理。
加氢脱硫过程中,硫化物与氢气在催化剂的作用下发生反应,生成硫化氢并得到脱硫汽油。
4. 加氢脱氮:加氢处理后的汽油可能还含有一定量的氮杂质,影响汽油的清洁度和燃烧效率。
因此,需要进行加氢脱氮处理,将氮杂质也去除。
5. 加氢脱芳:芳烃是汽油中的一种重要成分,但过多的芳烃含量会影响汽油的清洁度和辛烷值。
因此,需要通过加氢反应将部分芳烃转化成饱和烃或环烷烃,以提高汽油的品质。
6. 分离和提纯:经过加氢处理后的汽油通过冷却、分离等步骤,将其中产生的硫化氢、氨和其它杂质分离,最终得到高质量、清洁的汽油产品。
7. 催化剂再生:加氢处理中用到的催化剂随着时间的延长会受到积碳、中毒等影响,影响催化剂的活性和寿命。
因此,需要对催化剂进行再生处理,以恢复催化剂的活性和延长使用寿命。
总的来说,汽油加氢处理工艺流程是一种重要的汽油炼制技术,可以有效提高汽油的品质和性能,满足现代汽车对清洁高效燃料的需求。
在石油加工行业中有着广泛的应用和良好的市场前景。
催化裂化工艺流程
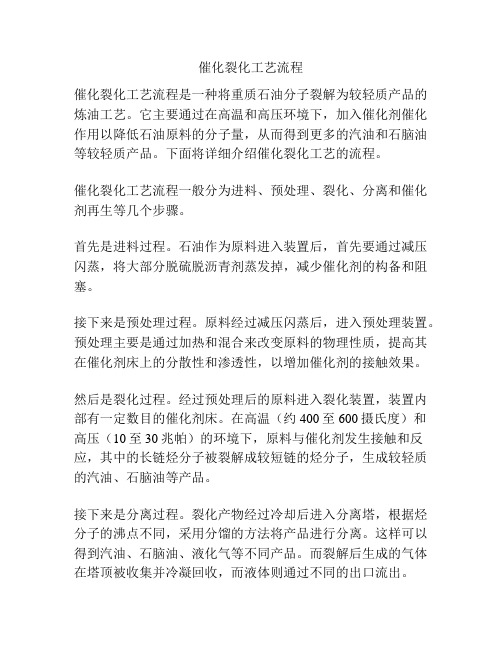
催化裂化工艺流程催化裂化工艺流程是一种将重质石油分子裂解为较轻质产品的炼油工艺。
它主要通过在高温和高压环境下,加入催化剂催化作用以降低石油原料的分子量,从而得到更多的汽油和石脑油等较轻质产品。
下面将详细介绍催化裂化工艺的流程。
催化裂化工艺流程一般分为进料、预处理、裂化、分离和催化剂再生等几个步骤。
首先是进料过程。
石油作为原料进入装置后,首先要通过减压闪蒸,将大部分脱硫脱沥青剂蒸发掉,减少催化剂的构备和阻塞。
接下来是预处理过程。
原料经过减压闪蒸后,进入预处理装置。
预处理主要是通过加热和混合来改变原料的物理性质,提高其在催化剂床上的分散性和渗透性,以增加催化剂的接触效果。
然后是裂化过程。
经过预处理后的原料进入裂化装置,装置内部有一定数目的催化剂床。
在高温(约400至600摄氏度)和高压(10至30兆帕)的环境下,原料与催化剂发生接触和反应,其中的长链烃分子被裂解成较短链的烃分子,生成较轻质的汽油、石脑油等产品。
接下来是分离过程。
裂化产物经过冷却后进入分离塔,根据烃分子的沸点不同,采用分馏的方法将产品进行分离。
这样可以得到汽油、石脑油、液化气等不同产品。
而裂解后生成的气体在塔顶被收集并冷凝回收,而液体则通过不同的出口流出。
最后是催化剂再生过程。
随着催化剂的使用,其活性会逐渐降低。
因此,需要对催化剂进行再生。
催化剂再生的方法有多种,常用的方法包括烧结再生和煅烧再生。
再生后的催化剂可以继续使用。
催化裂化工艺流程是一种高效、可靠的炼油工艺,能够将重质石油分子裂解成较轻质的产品,提高汽油和石脑油等产量。
然而,催化裂化工艺也存在一些挑战,例如对催化剂的选择和再生过程的控制等。
因此,在实际生产中,需要不断优化和改进工艺流程,以提高产量和质量,降低能耗和环境污染。
催化裂化汽油加氢脱硫(DSO)技术开发及工业试验
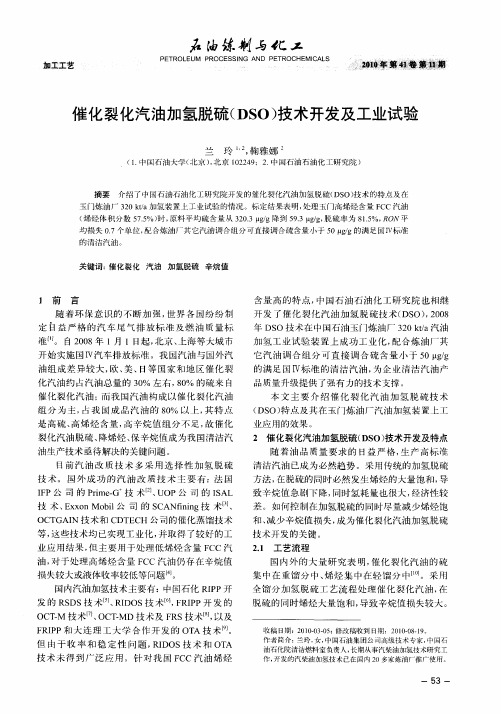
均损失 O7个单 位, . 配合炼油厂其它汽油调合组分可直接调合硫含量小于 5 gg的满足国Ⅳ标 准 0P /
的清洁汽油 。
关键词:催化裂化 汽油 加氢脱硫 辛烷值
1 前
言
含 量 高 的 特 点 , 国石 油 石 油 化 工 研 究 院 也相 继 中 开 发 了 催化 裂 化 汽 油 加 氢 脱 硫 技 术 ( O) 2 0 DS , 0 8 年 DS O技术 在 中 国石 油玉 门炼 油厂 3 0k/ 汽 油 2 t a 加 氢 工 业试 验 装 置 上 成功 工业 化 , 配合 炼 油 厂 其 它 汽 油 调 合 组 分 可 直 接 调 合 硫 含 量 小 于 5 gg 0P /
国内 汽油加 氢技 术 主要 有 :中 国石 化 RP IP开
发 的 R DS技 术[、 I S 5 R DOS技 术[, RIP开 发 的 ] 6F P ]
脱 硫 的同时 烯 烃 大量 饱 和 , 导致 辛烷 值 损 失较 大 。
收槁 日期 :2 1—30 ;修改稿收到 日期:2 1.8 1 。 0 00 —5 0 00 —9 作者 简介 :兰玲, 中国石油集团公司高级技术专家 , 女, 中国石 油石化院清洁燃料室负责人 , 长期从事汽柴油加 氢技术研究工 作, 开发的汽柴油加氢技 术已在国内 2 O多家炼油厂推广使用。 53 —
催化 裂 化 汽 油 ; 我 国 汽 油构 成 以 催化 裂 化 汽 油 而
的 满 足 国 Ⅳ标 准 的 清 洁汽 油 , 企 业 清洁 汽 油 产 为 品 质量升 级提 供 了强有 力 的技术 支撑 。 本 文 主 要 介 绍 催 化 裂 化 汽 油 加 氢 脱 硫 技 术
( O) 点 及其 在 玉 门炼 油 厂汽 油加 氢 装 置上 工 DS 特
催化裂化工艺流程
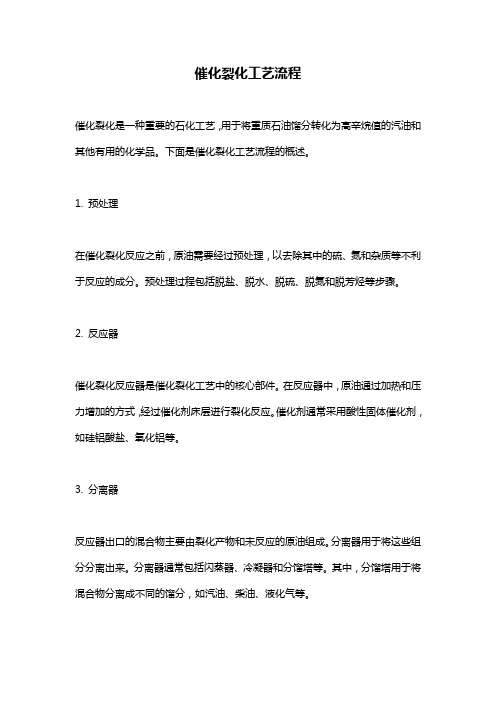
催化裂化工艺流程
催化裂化是一种重要的石化工艺,用于将重质石油馏分转化为高辛烷值的汽油和其他有用的化学品。
下面是催化裂化工艺流程的概述。
1. 预处理
在催化裂化反应之前,原油需要经过预处理,以去除其中的硫、氮和杂质等不利于反应的成分。
预处理过程包括脱盐、脱水、脱硫、脱氮和脱芳烃等步骤。
2. 反应器
催化裂化反应器是催化裂化工艺中的核心部件。
在反应器中,原油通过加热和压力增加的方式,经过催化剂床层进行裂化反应。
催化剂通常采用酸性固体催化剂,如硅铝酸盐、氧化铝等。
3. 分离器
反应器出口的混合物主要由裂化产物和未反应的原油组成。
分离器用于将这些组分分离出来。
分离器通常包括闪蒸器、冷凝器和分馏塔等。
其中,分馏塔用于将混合物分离成不同的馏分,如汽油、柴油、液化气等。
4. 产品处理
裂化产物需要进一步加工处理,以满足市场需求。
处理过程包括脱硫、脱氮、脱蜡、加氢、重整等步骤。
总的来说,催化裂化是一种复杂的工艺流程,需要各种设备和催化剂的协同作用,以实现高效、稳定和可控的反应。
催化裂化汽油加氢脱硫及芳构化工艺反应条件的研究
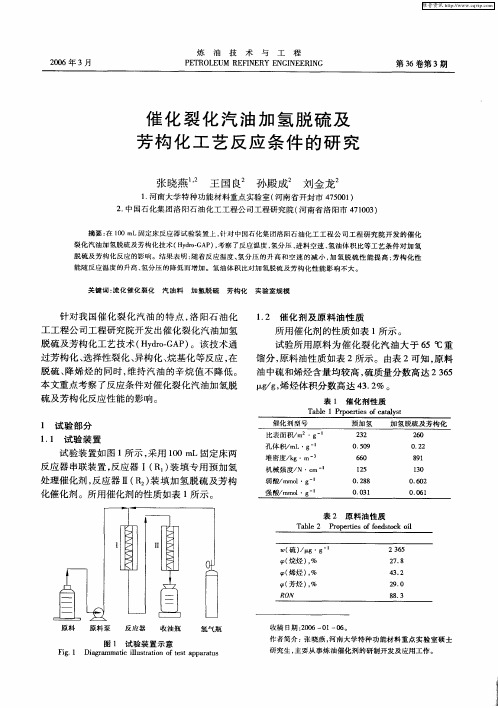
下, 应尽量提高进料空速 , 降低装置的投资和操作 费 用 , 高经 济效 益 。 提
表 4 氢 分 压 的 影 响
Ta e 4 Efe to dr g n p e s e on hy o s f rz fo bl f c hy o e r s ur drde ulu ia n f i a d a o tz to n r maia n o FCC a o ie i f g ln s
张 晓燕 王 国 良 孙殿成 刘金龙
1河南大学特 种功能材料重点实验室 ( . 河南 省开封市 4 50 ) 7 0 1
2 中国 石 化 集 团 洛 阳 石 油 化 工 工 程 公 司 工 程 研 究 院 ( 南 省 洛 阳市 4 10 ) . 河 7 0 3
摘 要: 10 m 在 0 L固定床 反应器 试验装 置上 , 针对中国石化集团洛阳石 油化 工工程公 司工程研 究院开发 的催 化 裂化 汽油加氢脱硫及芳构化技术 ( y r- A ), H doG P 考察 了反应温度 , 氢分压 、 进料空速 、 油体 积 比等工艺条件对加 氢 氢 脱硫及 芳构 化反应 的影响 。结果表 明: 随着 反应温度 、 氢分压 的升 高和空 速的减 小 , 氢脱硫 性能提 高 ; 加 芳构化 性 能随 反应温度 的升 高、 氢分压 的降低而增加 。氢油体 积比对加氢脱硫及芳构化性 能影 响不大。
化催 化 剂 。所用 催化 剂 的性质 如表 1 示 。 所
表 2 原 料 油 性 质
Ta l P o eri so e d tc i b e2 r p te fe so k ol f
石油炼化七种常用工艺流程
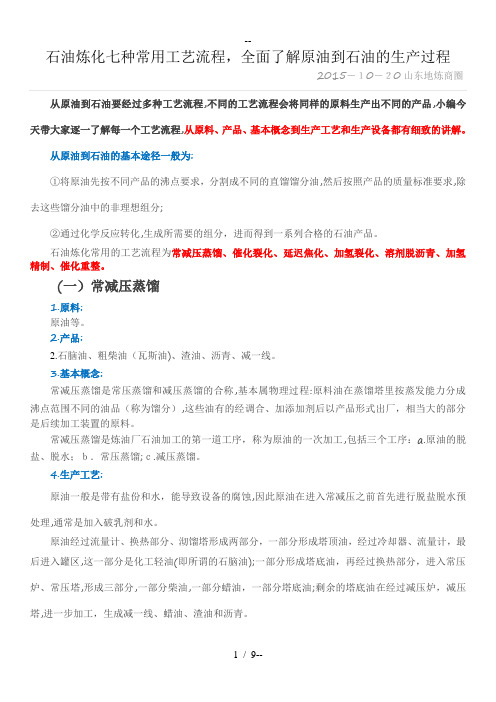
石油炼化七种常用工艺流程,全面了解原油到石油的生产过程2015-10-20山东地炼商圈从原油到石油要经过多种工艺流程,不同的工艺流程会将同样的原料生产出不同的产品,小编今天带大家逐一了解每一个工艺流程,从原料、产品、基本概念到生产工艺和生产设备都有细致的讲解。
从原油到石油的基本途径一般为:①将原油先按不同产品的沸点要求,分割成不同的直馏馏分油,然后按照产品的质量标准要求,除去这些馏分油中的非理想组分;②通过化学反应转化,生成所需要的组分,进而得到一系列合格的石油产品。
石油炼化常用的工艺流程为常减压蒸馏、催化裂化、延迟焦化、加氢裂化、溶剂脱沥青、加氢精制、催化重整。
(一)常减压蒸馏1.原料:原油等。
2.产品:2.石脑油、粗柴油(瓦斯油)、渣油、沥青、减一线。
3.基本概念:常减压蒸馏是常压蒸馏和减压蒸馏的合称,基本属物理过程:原料油在蒸馏塔里按蒸发能力分成沸点范围不同的油品(称为馏分),这些油有的经调合、加添加剂后以产品形式出厂,相当大的部分是后续加工装置的原料。
常减压蒸馏是炼油厂石油加工的第一道工序,称为原油的一次加工,包括三个工序:a.原油的脱盐、脱水;b.常压蒸馏;c.减压蒸馏。
4.生产工艺:原油一般是带有盐份和水,能导致设备的腐蚀,因此原油在进入常减压之前首先进行脱盐脱水预处理,通常是加入破乳剂和水。
原油经过流量计、换热部分、沏馏塔形成两部分,一部分形成塔顶油,经过冷却器、流量计,最后进入罐区,这一部分是化工轻油(即所谓的石脑油);一部分形成塔底油,再经过换热部分,进入常压炉、常压塔,形成三部分,一部分柴油,一部分蜡油,一部分塔底油;剩余的塔底油在经过减压炉,减压塔,进一步加工,生成减一线、蜡油、渣油和沥青。
各自的收率:石脑油(轻汽油或化工轻油)占1%左右,柴油占20%左右,蜡油占30%左右,渣油和沥青约占42%左右,减一线约占5%左右。
常减压工序是不生产汽油产品的,其中蜡油和渣油进入催化裂化环节,生产汽油、柴油、煤油等成品油;石脑油直接出售由其他小企业生产溶剂油或者进入下一步的深加工,一般是催化重整生产溶剂油或提取萃类化合物;减一线可以直接进行调剂润滑油。
长周期稳定运转的催化裂化汽油选择性加氢脱硫技术
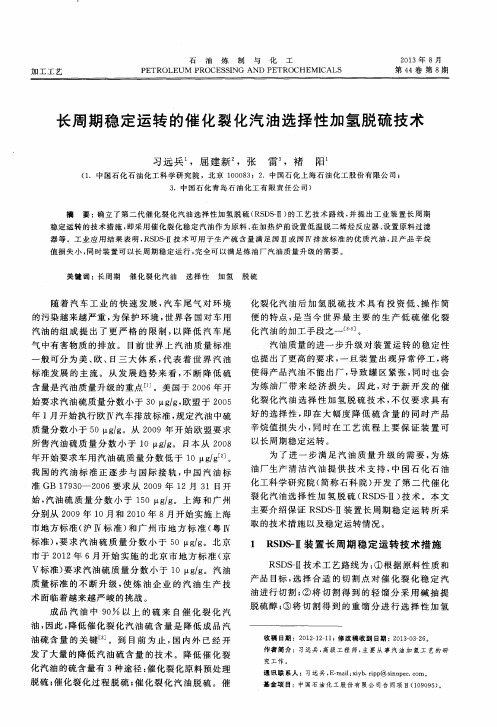
汽油 的组 成 提 出 了更 严 格 的 限制 , 以 降 低 汽 车 尾
气 中有 害物质 的排放 。 目前 世 界 上 汽 油 质 量 标 准
一
汽油 质量 的进 一 步 升级 对 装 置 运转 的稳 定 性
般 可分 为 美 、 欧、 日三 大 体 系 , 代 表 着 世 界 汽 油
( 1 .中 国 石 化 石 油 化 工 科 学 研 究 院 ,北 京 1 0 0 0 8 3 ;2 .中 国石 化 上 海 石 油化 工股 份 有 限公 司 ; 3 .中 国 石化 青 岛 石 油 化 工 有 限 责 任 公 司 )
摘
要: 确 立 了第 二 代催 化 裂 化 汽 油 选 择 性 加 氢 脱 硫 ( R S D Ⅱ) 的工艺技术 路线 , 并 提 出工 业 装 置 长 周 期
以长周期 稳定 运转 。 为 了 进 一 步 满 足 汽 油 质 量 升 级 的需 要 , 为炼
始要 求汽 油硫 质量 分数 小 于 3 O u g / a , 欧盟于 2 0 0 5 年 1月 开始 执行 欧 Ⅳ汽车排 放标 准 , 规定 汽 油 中硫 质量 分数 小 于 5 O u g / g 。从 2 0 0 9年 开始 欧 盟 要求 所 售 汽油 硫质 量 分数 小 于 1 0 g / g 。 日本 从 2 0 0 8 年开 始要 求车 用 汽油 硫 质 量分 数 低 于 1 0 u g / g E 2 ] 。 我 国的汽 油 标 准 正 逐 步 与 国 际 接 轨 , 中国 汽 油 标 准 GB 1 7 9 3 O 一2 O O 6要 求从 2 0 0 9年 1 2月 3 1日开 始, 汽 油硫 质 量 分 数 小 于 1 5 0 g / g 。上 海 和 广 州 分 别从 2 0 0 9年 l O月和 2 0 1 0年 8月 开始 实施 上海 市 地方 标 准 ( 沪 Ⅳ标 准 ) 和广州市地方标准 ( 粤 Ⅳ 标准) , 要求汽油硫质量分 数小于 5 0 g / g 。北 京
催化裂化流程
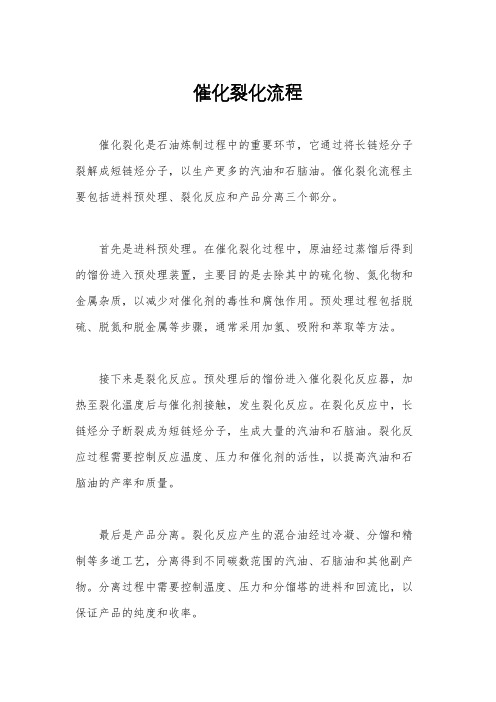
催化裂化流程
催化裂化是石油炼制过程中的重要环节,它通过将长链烃分子裂解成短链烃分子,以生产更多的汽油和石脑油。
催化裂化流程主要包括进料预处理、裂化反应和产品分离三个部分。
首先是进料预处理。
在催化裂化过程中,原油经过蒸馏后得到的馏份进入预处理装置,主要目的是去除其中的硫化物、氮化物和金属杂质,以减少对催化剂的毒性和腐蚀作用。
预处理过程包括脱硫、脱氮和脱金属等步骤,通常采用加氢、吸附和萃取等方法。
接下来是裂化反应。
预处理后的馏份进入催化裂化反应器,加热至裂化温度后与催化剂接触,发生裂化反应。
在裂化反应中,长链烃分子断裂成为短链烃分子,生成大量的汽油和石脑油。
裂化反应过程需要控制反应温度、压力和催化剂的活性,以提高汽油和石脑油的产率和质量。
最后是产品分离。
裂化反应产生的混合油经过冷凝、分馏和精制等多道工艺,分离得到不同碳数范围的汽油、石脑油和其他副产物。
分离过程中需要控制温度、压力和分馏塔的进料和回流比,以保证产品的纯度和收率。
催化裂化流程的优化对提高汽油和石脑油的产率和质量至关重要。
通过改进预处理工艺、优化裂化反应条件和提高产品分离效率,可以降低能耗、减少废物排放,提高产品质量和经济效益。
总的来说,催化裂化流程是炼油工艺中的重要环节,它通过预
处理、裂化反应和产品分离三个部分,将原油转化为更多的汽油和
石脑油。
优化催化裂化流程对提高产率和质量具有重要意义,需要
综合考虑预处理、反应和分离等环节,以实现经济、高效和环保的
生产目标。
催化汽油加氢脱硫工艺介绍.doc
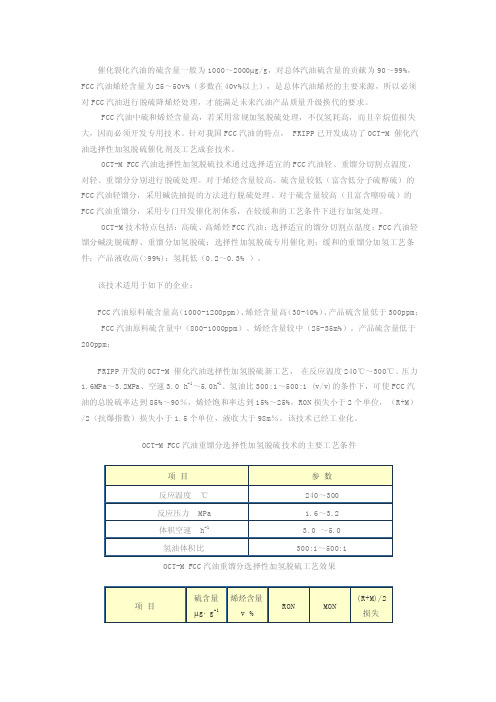
催化裂化汽油的硫含量一般为1000~2000μg/g,对总体汽油硫含量的贡献为90~99%,FCC汽油烯烃含量为25~50v%(多数在40v%以上),是总体汽油烯烃的主要来源,所以必须对FCC汽油进行脱硫降烯烃处理,才能满足未来汽油产品质量升级换代的要求。
FCC汽油中硫和烯烃含量高,若采用常规加氢脱硫处理,不仅氢耗高,而且辛烷值损失大,因而必须开发专用技术。
针对我国FCC汽油的特点, FRIPP已开发成功了OCT-M 催化汽油选择性加氢脱硫催化剂及工艺成套技术。
OCT-M FCC汽油选择性加氢脱硫技术通过选择适宜的FCC汽油轻、重馏分切割点温度,对轻、重馏分分别进行脱硫处理。
对于烯烃含量较高、硫含量较低(富含低分子硫醇硫)的FCC汽油轻馏分,采用碱洗抽提的方法进行脱硫处理。
对于硫含量较高(且富含噻吩硫)的FCC汽油重馏分,采用专门开发催化剂体系,在较缓和的工艺条件下进行加氢处理。
OCT-M技术特点包括:高硫、高烯烃FCC汽油;选择适宜的馏分切割点温度;FCC汽油轻馏分碱洗脱硫醇、重馏分加氢脱硫;选择性加氢脱硫专用催化剂;缓和的重馏分加氢工艺条件;产品液收高(>99%);氢耗低(0.2~0.3% )。
该技术适用于如下的企业:FCC汽油原料硫含量高(1000-1200ppm)、烯烃含量高(30-40%),产品硫含量低于300ppm;FCC汽油原料硫含量中(800-1000ppm)、烯烃含量较中(25-35m%),产品硫含量低于200ppm;FRIPP开发的OCT-M 催化汽油选择性加氢脱硫新工艺,在反应温度240℃~300℃、压力1.6MPa~3.2MPa、空速3.0 h-1~5.0h-1、氢油比300:1~500:1 (v/v)的条件下,可使FCC汽油的总脱硫率达到85%~90%,烯烃饱和率达到15%~25%,RON损失小于2个单位,(R+M)/2(抗爆指数)损失小于1.5个单位,液收大于98m%。
催化裂化工艺流程介绍

催化裂化工艺流程介绍
《催化裂化工艺流程介绍》
催化裂化是一种重要的石油加工工艺,用于将原油转化为高附加值的石油产品,如汽油、柴油和润滑油基础油。
催化裂化工艺通过将长链烃分子裂解为较短的链烃分子,从而提高产品的烃值和增加汽油产量。
催化裂化工艺的流程包括以下几个关键步骤:
1. 原料预处理:原油首先经过脱盐、脱硫等预处理工序,去除杂质和硫化物,净化原料。
2. 加热:经过预处理的原油被加热至裂化温度,通常在450-500摄氏度。
3. 进料分级:加热后的原油通过分级器进行分级,分离出不同碳数的馏分。
4. 裂化反应:分级后的原油进入裂化反应器,通过加入催化剂进行裂解,长链烃分子裂解成较短链烃分子。
5. 产品分离:裂化反应后,得到混合产品,通过分馏塔将产品进行分离,得到汽油、柴油等各种石油产品。
6. 催化剂再生:用过的催化剂需通过再生系统进行再生,以恢复其活性。
催化裂化工艺是炼油厂中一项复杂而重要的工艺,通过裂解原油,提高产品附加值,提高炼油厂的经济效益。
同时,催化裂化工艺也面临着环保和安全等方面的挑战,需要技术和设备的不断改进与升级。
催化裂化汽油选择性加氢脱硫工艺流程选择

催化裂化汽油选择性加氢脱硫工艺流程选择李明丰,习远兵,潘光成,聂 红(石油化工科学研究院,北京100083)摘要 研究了催化裂化汽油加氢脱硫各种可能的加工流程。
结果表明,将汽油切割成轻重馏分分别进行处理,可以大幅度减少汽油烯烃在加氢脱硫过程中的饱和;轻馏分汽油中硫醇可以通过碱抽提方式脱除,不影响汽油烯烃含量;由于汽油中的二烯烃在较缓和条件下能促进胶质的生成,需要进行选择性脱二烯烃;由于循环氢中的硫化氢对加氢脱硫反应有抑制作用、对烯烃饱和反应有促进作用,应增加循环氢脱硫化氢系统;产品中的硫醇可经固定床氧化脱除。
根据催化裂化汽油原料特性、反应动力学及工业应用需要确定选择性加氢脱硫的工艺流程。
关键词:催化裂化 汽油 选择性 加氢脱硫 流程 硫醇收稿日期:2009-09-29;修改稿收到日期:2009-12-04。
作者简介:李明丰,教授级高级工程师,博士,主要从事馏分油加氢精制和加氢裂化催化剂的开发以及加氢催化剂活性相结构研究与设计工作。
申请专利40余项,发表论文10余篇。
基金项目:国家重点基础研究发展计划(973项目,2006CB202506);国家科技支撑计划(2007BAE43B01)。
1 前 言近年来,我国经济高速发展促进了石油消费量的急剧增加,目前中国已成为仅次于美国的第二大石油消费国。
大量的石油消费带来严重的空气污染问题。
根据我国年度环境报告,机动车排放污染已逐渐成为大、中城市中心地带空气的主要污染源。
降低汽车尾气污染、改善空气质量已经成为世界范围内的共识。
试验结果表明,降低汽油中的硫含量是减少汽车排放的有效手段之一[1]。
对于多数欧洲国家,从2005年开始,产品汽油硫含量已经小于50 µg/g 。
欧盟从2009年开始所售汽油硫含量需要小于10 µg/g 。
我国汽油标准GB 17930—2006要求从2009年12月31日开始,汽油硫含量小于150 µg/g 。
第二代催化裂化汽油选择性加氢脱硫技术开发及工业应用通过技术鉴定

认 真控 制 好 环 管 聚合 系统 , 证 “ 剂 ” 保 三 的精 确注 入 , 避免 产生 无规 聚合 物 和低 聚合 物 , 即俗 称
的 “ 料 ” 这 种 料 在 液 相 丙 烯 中影 响 还 不 大 , 是 粘 , 但
一
沟槽 , 析认 为 可 能 是 此 磨损 沟槽 导 致 了漏 气 量 分 增 大 , 卸料 器 的充 填 系数 降低 。 使 经 过对 沟槽 的堆焊 修复 , 和重 新更 换 轴封 , 安
2u 4u
转 速/ ・ l ( mi r l )
漏 泄 压 力 较 高 的 空 气 时 , 于 局 部 压 力 的 平 衡 而 由 形 成 的类 似 的压缩 拱 。
图 6 高 转 速 负 荷 反 倒 下 降 经 验 曲线
堵塞 的原 因包 括 固结 、 粘结 、 电 、 静 水分 等 , 多 半是 由 于粉体 表 面性质 的改变 而增 加 了粘 附力所
装 投 用 后 RF 0 8 1的输 送 负 荷 即 达 到 1 / 7t h左 右 ,
旦 浆料 流速 降低 或 遇管 线弯 头 或遇 节流 类设 备
如孔 板 、 节 阀等 , 会 析 出 粘 乎乎 的无 规 物 , 调 就 粘 性 很 大 , 牢牢 附在 阀芯或 容器 内壁上 , 而不 但 能 继
Ⅱ技 术 工 艺 流 程 可 行 , 品 质 量 稳 定 , 油 辛 烷 值 损 失 较 产 汽
低 , 到 同类 技 术 的先 进 水 平 。 达 ( 国 石 化 工 程 建 设 公 司 技 术 部 张 维 忠 供 稿 ) 中
致 。
影 响卸 料 器工 作性 能 除上 述 诸 因素 外 , 有 还 温 度 , 料 器 体 的 结 构 强 度 , 度 , 造 精 度 及 装 卸 刚 制
重油催化裂化工艺流程
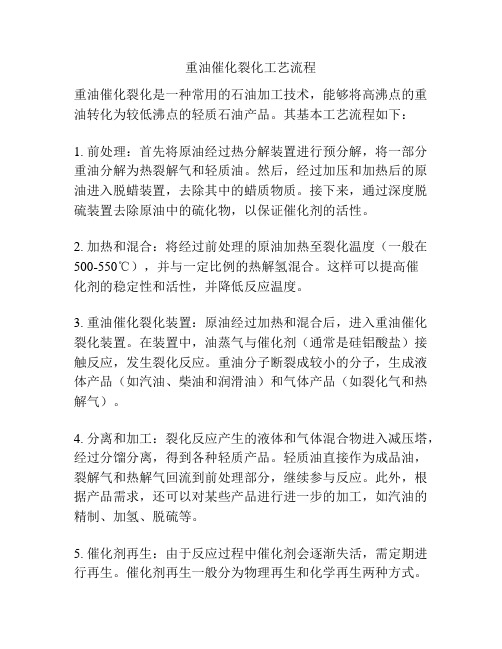
重油催化裂化工艺流程重油催化裂化是一种常用的石油加工技术,能够将高沸点的重油转化为较低沸点的轻质石油产品。
其基本工艺流程如下:1. 前处理:首先将原油经过热分解装置进行预分解,将一部分重油分解为热裂解气和轻质油。
然后,经过加压和加热后的原油进入脱蜡装置,去除其中的蜡质物质。
接下来,通过深度脱硫装置去除原油中的硫化物,以保证催化剂的活性。
2. 加热和混合:将经过前处理的原油加热至裂化温度(一般在500-550℃),并与一定比例的热解氢混合。
这样可以提高催化剂的稳定性和活性,并降低反应温度。
3. 重油催化裂化装置:原油经过加热和混合后,进入重油催化裂化装置。
在装置中,油蒸气与催化剂(通常是硅铝酸盐)接触反应,发生裂化反应。
重油分子断裂成较小的分子,生成液体产品(如汽油、柴油和润滑油)和气体产品(如裂化气和热解气)。
4. 分离和加工:裂化反应产生的液体和气体混合物进入减压塔,经过分馏分离,得到各种轻质产品。
轻质油直接作为成品油,裂解气和热解气回流到前处理部分,继续参与反应。
此外,根据产品需求,还可以对某些产品进行进一步的加工,如汽油的精制、加氢、脱硫等。
5. 催化剂再生:由于反应过程中催化剂会逐渐失活,需定期进行再生。
催化剂再生一般分为物理再生和化学再生两种方式。
物理再生通过热氧焚烧去除积碳物质,化学再生则使用一些酸碱溶液进行催化剂表面的脱碳和脱硫处理。
总结起来,重油催化裂化工艺流程包括前处理、加热和混合、重油催化裂化、分离和加工、催化剂再生等步骤。
通过这一流程,可以将高沸点的重油转化为更具经济价值的轻质石油产品,提高石油资源的利用效率。
这种工艺流程在石化工业中得到了广泛的应用,并为能源开发和环境保护做出了积极的贡献。
炼油化工企业催化裂化汽油选择性加氢工艺技术初探

28通过合理控制汽油中硫和烯烃的含量来实现对汽油的进一步清洁净化,进而有助于充分降低汽车在行驶过程中排放的尾气对自然环境的污染问题。
当前我国炼油化工企业在催化裂化汽油的生产方面越来越注重技术的优化,利用技术改进的方法逐渐降低硫含量的同时,保留汽油的高辛烷值,在未来的发展中采用先进催化裂化汽油选择性加氢工艺技术来实现对催化裂化汽油质量的进一步升级。
1 炼油化工企业催化裂化汽油选择性加氢工艺技术应用现状1.1 催化裂化汽油选择性加氢工艺技术发展成熟我国技术体系的不断完善,针对于石油化工的技术也在进行不断的革新与完善。
尤其是近几年来,催化裂化汽油选择性加氢工艺技术在发展过程当中取得了巨大的突破,技术工艺水平得到提升,目前国内外炼油企业主要采用选择性加氢脱硫技术对催化裂化汽油进行深度脱硫,该类技术操作条件缓和,经济性好,汽油收率高并且氢耗低,辛烷值损失小,是催化汽油脱硫技术的主流。
国内某公司开发的GARDES工艺技术的核心在于其分步脱除催化裂化汽油中硫醇性硫、大分子含硫化合物和小分子噻吩类含硫化合物的“阶梯”脱硫技术和将烯烃定向转化为高辛烷值异构烷烃和芳烃技术的耦合,因而可在大幅度降低催化裂化汽油硫含量和烯烃含量的同时保持其辛烷值,因而具有广泛的原料和产品方案适应性。
国外某公司开发的Prime-G +技术,主要由选择性预加氢系统SHU、预分馏系统和选择性加氢脱硫系统HDS组成。
该技术采用双功能HR催化剂,工艺条件缓和,不会发生芳烃饱和及裂化反应,具有较高的脱硫选择性,在脱硫率大于98%时,马达法辛烷值损失小于1,抗爆性指数损失小于1.5,可用于生产超低硫汽油。
1.2 典型汽油加氢工艺流程全馏分催化裂化汽油先在临氢条件下,通过预处理罐进行胶质等杂质的脱除(需备用另一个预处理罐进行串并联切换操作),再经装有选择性脱双烯/脱硫醇催化剂的预加氢反应器,使硫醇硫与二烯烃作用生成硫醚而转移到重汽油(HCN)中,然后进入分馏塔进行馏分切割;切割后的轻汽油(LCN)中硫醇性硫含量很低,且其总硫含量也较低,因而可直接用于汽油产品调和,而HCN则在临氢条件下进入选择性加氢脱硫反应器以及补充脱硫反应器处理后得到总硫和硫醇含量符合调和要求的改质HCN;最后,将LCN、HCN调和而得到满足标准的清洁汽油调和组分。
催化裂化汽油选择性深度加氢脱硫技术OCT—MD的开发

根 据 F C汽 油选 择性加 氢 脱 硫 技术 的思 路 , C
为 了提 高产 品 总脱硫 率 , 提 高 H N脱硫 率 的 同 在 C 时, 必须 大 幅度 降低 L N 的硫 含 量 。开 发高 脱 硫 C 选择 性 的新 一 代催 化 剂 是 提 高 H N脱 硫 率 的 关 C
维普资讯
2 0 年 7月 08
炼 油 技 术 与 工 程 P T O E M E IE YE G N E I G E R L U R FN R N I E R N
第 3 卷第 7期 8
催 化 裂 化 汽 油 选 择 性 深 度 加 氢 脱 硫 技 术 O T MD 的 开 发 C—
含 量是 生产 超 清 洁 汽油 的关 键 。近 年 来 , 内外 国 成 功开发 了许 多 辛 烷 值 损 失 较 小 的 F C汽 油 选 C
择性 加 氢 脱 硫 新 技 术 , O TM_ ,cn nn _ 如 C . 1 Saf ig2 J i J
和 Pi eG 。这 些技 术根 据 F C汽 油 中烯 烃 集 r — m C 中分布 在低沸 点 的轻馏 分 ( C L N)、 化 物集 中分 硫 布在 高沸 点重 馏分 ( C ) H N 中的特点 , 将 F C汽 先 C 油分 馏为 L N和 H N, 后 对 H N进 行加 氢处 C C 然 C
催化裂化汽油脱硫技术的研究进展
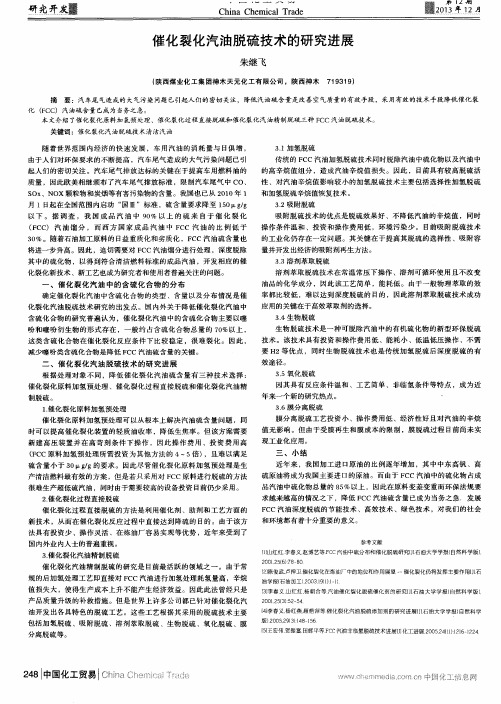
S O x 、N O X颗粒 物和炭 烟等有 害污染物 的含量 。我国 也已从 2 0 1 0 年1 月 1日 起 在全 国范 围内启 动 “ 国 Ⅲ”标准 ,硫 含 量要求 降至 1 5 0 g / g 以 下 。据 调 查 ,我 国 成 品 汽 油 中 9 0 % 以上 的 硫 来 自 于 催 化 裂 化 ( F C C ) 汽 油 馏 分 ,而 西 方 国 家 成 品 汽 油 中 F C C汽 油 的 比 例 低 于 3 0 %。随着 石油加 工原 料 的 日益重 质化和 劣质 化 ,F C C汽 油硫 含量 也
起 人们 的密 切关 注 。汽车 尾气 排放 达标 的关 键在 于提 高车 用燃 料油 的
质 量 ,因此欧 美相继 颁布 了汽 车尾气 排放 标准 ,限制 汽车尾 气 中 C O、
的高 辛烷值 组分 ,造成 汽油 辛烷值 损 失 。因此 ,目前具 有较 高脱 硫活
性 、对 汽 油辛烷 值 影响较 小 的加 氢脱硫 技术 主 要包括 选 择性 加氢脱 硫
量并开发 出经济 的吸附 剂再生 方法 。 3 , 3溶 剂萃取脱 硫 溶 剂萃取 脱硫 技术 在常 温常 压 下操作 、溶 剂可 循环 使 用且 不 改变
其 中的硫化 物 ,以得 到符 合清 洁燃 料标 准 的成 品汽 油 ,开 发相 应的 催
化 裂化新 技术 、 新 工艺也 成为研 究者和 使用者普 遍关注 的问题 。
确定 催化 裂化 汽油 中含 硫化 合物 的类 型 、含量 以及 分 布情 况是 催 化 裂化 汽油 脱硫 技 术研 究的 出发 点 。国 内外关于 降低 催化 裂化 汽油 中 含硫化 合物 的研 究 普遍 认为 ,催化 裂化 汽 油 中的含硫 化合 物主 要 以噻
石油加氢处理—加氢处理工艺流程

2RSSR (油相) + 4NaOH (水相)
一、汽油加氢处理
抽
脱去酸性杂质
提 塔
的轻汽油馏分
空 气 催 化 剂
脱硫醇汽油
过剩空气
氧
化
二硫化物
塔
分离罐
40~65 oC操作 碱液泵
碱液抽提工艺流程
一、汽油加氢处理工艺流程
3. 选择性脱二烯烃
危害:二烯烃较活泼,易反应生
课程:石油炼制运行与操控 知识点:加氢处理工艺流程(一)
一、汽油加氢处理工艺流程
轻馏分汽油
预碱洗
碱液抽提
全馏分 FCC汽油
分馏
碱液再生
循环氢脱 硫化氢
固定床氧 化脱硫醇
重馏分汽油
选择性 脱二烯
固定床选择 性加氢脱硫
高分
催化裂化汽油选择性加氢脱硫工艺原则流程图
全馏分脱硫 精制汽油
一、汽油加氢处理工艺流程
重汽油
一、汽油加氢处理工艺流程
2. 碱液抽提
目的:对轻汽油进行脱硫醇处理(硫醇具有氧化性和腐蚀性) 碱液抽提原理:硫醇具有一定的酸性,可与NaOH发生酸碱反应
RSH (油相) + NaOH (水相)
NaSR (水相) + H2O
氧化再生原理:硫醇钠在催化剂的作用下被氧化成二硫化物
4NaSR (水相) + O2 + 2H2O 催化剂
二、柴油加氢处理工艺流程
软化水
原料油 新氢
污水
蒸汽
三、渣油加氢处理工艺流程
渣油加氢处理条件更
苛刻
流程包括三部分:加
氢反应系统,加氢生 成油分离系统,循环 氢系统
齐鲁石化VRDS装置流程
- 1、下载文档前请自行甄别文档内容的完整性,平台不提供额外的编辑、内容补充、找答案等附加服务。
- 2、"仅部分预览"的文档,不可在线预览部分如存在完整性等问题,可反馈申请退款(可完整预览的文档不适用该条件!)。
- 3、如文档侵犯您的权益,请联系客服反馈,我们会尽快为您处理(人工客服工作时间:9:00-18:30)。
催化裂化汽油加氢脱硫技术及工艺流程分析
摘要:经济与社会不断发展、进步,人们生活水平不断提升,我国机动车数量也在快速攀升,与此同时,由机动车尾气排放对环境造成的污染也越来越明显,因此对催化裂化汽油加氢脱
硫技术进行研究极具现实意义。
基于此,文章对汽油燃烧排放的硫化物种类及其危害进行了
阐述,分析了催化加氢脱硫(HDS)反应原理,并对催化裂化汽油加氢脱硫技术及其工艺流程进
行可分析,以期能够为提升汽油脱硫处理质量提供有效参考。
关键词:催化裂化;汽油;加氢脱硫;应用
低硫含量是当前世界车用汽油应用发展的主要趋势之一。
对于我国的车用汽油而言,其四分
之三以上是催化裂化汽油,也称为FCC汽油。
然而,FCC汽油具备烯烃、硫含量较高,安定
性不高的缺陷,对车用汽油指标造成不良影响,此类汽车用油的污染物排放标准难以达到国
际先进标准,甚至与国内最新的机动车污染物排放指标相去甚远。
虽说汽油中硫化物含量值
不是最高,但是其产生的危害却极大。
一方面,硫化物燃烧生成物主要是SOx的形式,也是
引发酸雨的主要因素,而且SOx排放过大也会刺激NO,、CO这些有毒有害气体的生产与排放。
另一方面,硫化物还会使汽油燃烧时还会导致汽车尾气转化器催化剂失效,NO、SOx、CO等
有害气体的排放量进一步增加,降低城市空气质量。
除此之外,硫化物也会对金属设备产生
一定程度腐蚀危害,影响汽油泵等相关部件的使用寿命,提高了事故概率。
一、催化加氢脱硫(HDS)反应原理分析
HDS反应原理,主要是利用在石油中加氢使得含硫化合物氢解形成相应的烃合物与H2S,进
而脱去石油中的硫原子,其过程中C—S键的断裂与相应断裂物的饱和是最为基本的化学反应。
例如噻吩和苯并噻吩的HDS过程通常包含了加氢与裂解两途径。
通过加氢使噻吩环双键饱和
接着开环脱硫形成烷烃,再通过裂解反应使开环脱硫形成丁二烯,丁二烯在氢环境中饱和。
噻吩经过加氢脱硫处理后主要产生丁二烯、丁烯,丁烷、C2、C3产物则少得多。
硫化物主要
以非杂环与杂环两种类型存在于原油中。
非杂环类硫化物以硫醇、硫醚等结构为主,具备较
高的反应活性,加氢脱除较为容易。
而噻吩、甲基、苯基等杂环类硫化物具备与芳烃相似的
稳定结构,所以去除较为困难。
二、催化裂化汽油加氢脱硫技术工艺流程分析
催化裂化汽油加氢脱硫处理,要求其过程能够最大限度地完成脱硫工作,并将汽油辛烷值损
失控制在最低范围。
此外,催化裂化汽油加氢脱硫处理流程还应满足一下要求:①装置要能
够实现长周期运转,且单周期要和催化裂化装置检修周期相同;②装置选择应经济、适用,
有效降低加氢脱硫成本;③基于确保反应质量的前提制定工艺流程;④使工艺流程和国I、
国IV标准要求最大限度地保持一致;⑤采取有效技术方法提高工艺流程可行性与可衔接性;
⑥确保技术在产品中的应用稳定与高质量,并具备一定灵活性。
将催化裂化汽油的烯烃集中在轻馏分中,汽油中的硫则集中在重馏分中。
结合烯烃与硫在催
化裂化汽油中分布特点,有选择地展开预加氢反应,混氢原料油经过催化剂作用把二烯烃转
化成单烯烃,如此便可避免在后续加氢脱硫反应器发生结焦问题。
其中一些轻含硫物与轻疏
醇会在硫醚化反应中转化为重含硫化合物,同时还催生了烯烃异构化反应使得辛烷值得到了
一定程度的增加。
催化裂化汽油分馏,应把预加氢催化裂化汽油划分出重汽油与轻汽油。
对
于重汽油处理环节借助催化剂作用脱硫与烯烃饱和反应,同时实现了将重汽油以分馏比例调和。
三、常见的FCC汽油脱硫技术
现阶段,在汽油脱硫处理方面应用较为成熟,较为广泛的脱硫技术无疑是催化加氢脱硫工艺,许多发达国家的FCC汽油处理采用了这一技术。
HDS技术主要分为了传统型与选择性型HDS
技术。
前者应用虽然能够使汽油硫含量有效减少,然而在脱硫过程中国烯烃饱和率也会大幅提升,使得汽油辛烷值出现较大损失。
而后者应用的最大优势能够在满足汽油脱硫要求的同时烯烃饱和率不至于过高,辛烷值损失较少,因此具备较好的应用发展前景。
现阶段应用较为成熟选择性HDS技术主要下面几种工艺:
(一)SCANFining技术
这一技术应用始于美国,使用的RT-225催化剂。
核心工艺在于把全馏分催化轻汽油分为低硫高烯烃、硫和烯烃含量中等、高硫低烯烃3个组分的催化重汽油,进而针对性的选择合适脱硫技术生成调和油,达到92%~95%的汽油脱硫率,并且将抗爆指数损失控制在可2个单位以下。
(二)ISAL技术
这一技术由美国UOP公司与委内瑞拉石油研究及技术中心联合开发,运用了常规固定床工艺,与最新型的沸石催化剂,可解决现阶段炼化企业面临的大部分共性难题,不但有效减少了汽油硫与烯烃含量,而且确保辛烷值不会减小。
这一技术主要是通过调整催化剂大小、表面积、孔容孔径、酸度等对反应烃链长度进行有效控制,避免了辛烷值出现损失。
ISAL技术可应用与含硫在30μg/g清洁汽油生产,并且操作周期大于2年。
(三)Prime-G和Prime-G+技术
该技术由法国石油研究院最先开发,关键点在于对FCC汽油选择性加氢脱硫处理时采用双催化剂工艺,脱硫率较高,甚至实现汽油硫含量小于10μg/g,并且工艺应用条件相对缓和,烯烃饱和率也比较小,不会出现芳烃饱和及裂化反应现象,有着98%以上的脱硫率,耗氢较少且辛烷值损失低。
(四)OCTGAIN技术
该技术由Mobil公司开发,具备较高的FCC汽油脱硫处理效率,并且产物辛烷值的可控性较高。
在脱硫方面采用了固定床催化工艺,脱硫率大于95%,然而会发生5%~10%的汽油损失率。
(五)CDTECH技术
这一脱硫工艺应用了两个催化蒸馏塔,采用两段式反应。
第一阶段是在催化蒸馏加氢脱己烷塔中的反应,在催化剂作用下,轻汽油馏分中二烯烃与硫醇发生反应,得到高沸点产物进入重馏分,从塔顶形成的C5、C6馏分中硫醇含量控制在1μg/g以下,并对剩余的二烯烃进行选择加氢。
第二阶段应用CDHDS技术,将催化汽油中C7以上组分的硫去掉,总脱硫率达高于95%,辛烷值损失可控制在1.0以下。
(六)RIDOS技术
该技术由中石化石油化工科学研究院开发,先把FCC汽油原料在70~100℃之间按照轻、重两部分进行切割,轻汽油馏分经过碱洗处理后将硫醇、氮脱除,重汽油馏分、氢气则与加氢精制催化剂混合接触,实现脱硫、脱氮,以及与烯烃饱和反应效果,得到的产物和辛烷值恢复催化剂反应分流得到轻烃与汽油馏分,氢气可重复利用。
最后把脱硫重馏分与加氢精制轻馏分混合,进而获得调和产品。
四、结束语
综述可知,研究与分析催化裂化汽油加氢脱硫技术的应用,可以有效提升催化裂化汽油脱硫率,有效控制烯烃饱和,减少降低辛烷值损失,在提升汽油利用效率的同时改善城市生活环境,带来较大的经济与社会效益。
参考文献:
[1]赵航,曹祖斌,韩冬云,庞庆聪,宫建远.催化裂化汽油加氢脱硫降烯烃技术[J].当代化
工,2015(05):1090-1093.
[2]习远兵,张登前,褚阳,高晓东.催化裂化汽油全馏分选择性加氢脱硫技术的开发[J].石油炼制与化工,2016(47):1-4.
[3]方柳亚,王国清,石国芳,瞿东蕙,沈喜洲.汽油脱硫的技术现状及发展趋势[J].武汉工程大学报,2016(38):218-225.。