数控加工中的对刀方法与技巧
加工中心如何对刀步骤详解,会这六步妈妈再也不担心不会对刀了

加⼯中⼼如何对⼑步骤详解,会这六步妈妈再也不担⼼不会对⼑了⾸次使⽤数控加⼯中⼼对⼑存在疑问,随后⼩编就将如何对⼑告诉⼤家吧。
1,回零(返回机床原点)对⼑之前,⼀定要进⾏回零(返回机床原点)的操作,刹车于清除掉上次操作的坐标数据。
注意:X,Y,Z三轴都需要回零。
2,主轴正转⽤“ MDI”模式,通过输⼊指令代码使主轴正转,并保持中等旋转速度。
然后换成“⼿轮”模式,通过转换调节进⾏进⾏机床移动的操作。
3,X向对⼑⽤⼑具在⼯件的右边轻轻的碰下,将机床的相对坐标清零;将⼑具沿Z向提起,再将⼑具移动到⼯件的左边,沿Z向下到之前的同⼀⾼度,移动⼑具与⼯件轻轻接触,将⼑具提起,记下机床相对坐标的X值,将⼑具移动到相对坐标X的⼀半上,记下机床的绝对坐标的X值,并按(INPUT)输⼊的坐标系中即可(发那科系统输⼊“ X0。
”并按“测量”也可以)。
想学ug编程请加Q群699197696群⽂件下载ug学习100G学习资料。
4,Y向对⼑⽤⼑具在⼯件的前⾯轻轻地碰下,将机床的相对坐标清零;将⼑具沿Z向提起,再将⼑具移动到⼯件的后⾯,沿Z向下到之前的⾼度,移动⼑具与⼯件轻轻接触,将⼑具提起,记下机床相对坐标的Y值,将⼑具移动到相对坐标Y的⼀半上,记下机床的绝对坐标的Y值,并按(INPUT)输⼊的坐标系中即可(发那科系统输⼊“ Y0。
”按“测量”也可以)。
5,Z向对⼑将⼑具移动到⼯件上要对Z向零点的表⾯,慢慢移动⼑具⾄与⼯件上表⾯轻轻接触,记下此时的机床的坐标系中的Z向值,并按(INPUT)输⼊的坐标系中即可(发那科系统输⼊“ Z0。
”按“测量”也可以)。
6,主轴停转先将主轴停⽌转动,并把主轴移动到合适的位置,调取加⼯程序,准备正式加⼯。
机床对刀仪怎么对刀【干货技巧】数控机床对刀仪步骤

机床对刀仪怎么对刀_数控机床对刀仪步骤
内容来源网络,由“深圳机械展(11万㎡,1100多家展商,超10万观众)”收集整理!
更多cnc加工中心、车铣磨钻床、线切割、数控刀具工具、工业机器人、非标自动化、数字化无人工厂、精密测量、数控系统、3D打印、激光切割、钣金冲压折弯、精密零件加工等展示,就在深圳机械展.
数控车削加工中,应首先确定零件的加工原点,以建立准确的加工坐标系,同时考虑刀具的不同尺寸对加工的影响。
这些都需要通过对刀来解决。
(1) 一般对刀
一般对刀是指在机床上使用相对位置检测手动对刀。
下面以Z向对刀为例说明对刀方法,见图1。
图1 相对位置检测对刀
刀具安装后,先移动刀具手动切削工件右端面,再沿X向退刀,将右端面与加工原点距离N输入数控系统,即完成这把刀具Z向对刀过程。
手动对刀是基本对刀方法,但它还是没跳出传统车床的“试切--测量--调整”的对刀模式,占用较多的在机床上时间。
此方法较为落后。
(2)机外对刀仪对刀
机外对刀的本质是测量出刀具假想刀尖点到刀具台基准之间X及Z方向的距离。
利用机外对刀仪可将刀具预先在机床外校对好,以便装上机床后将对刀长度输入相应刀具补偿号即可以使用,如图2所示。
(3)自动对刀
自动对刀是通过刀尖检测系统实现的,刀尖以设定的速度向接触式传感器接近,当刀尖与传感器接触并发出信号,数控系统立即记下该瞬间的坐标值,并自动修正刀具补偿值。
自动对刀过程如图3所示.
内容来源网络,由深圳机械展收集整理!更多相关内容,就在深圳机械展!。
数控车床的对刀操作步骤
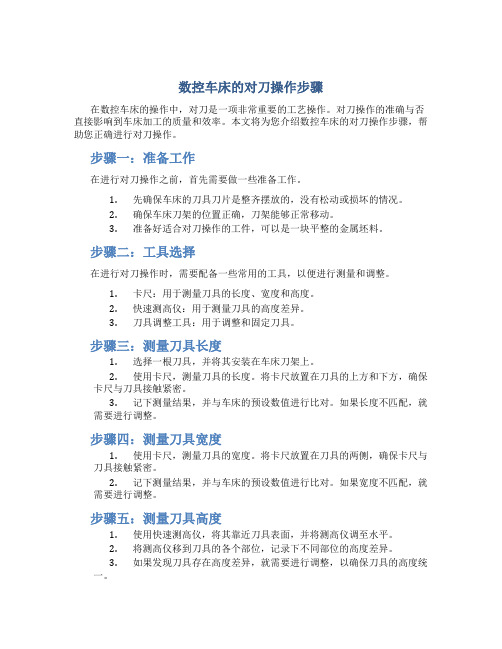
数控车床的对刀操作步骤在数控车床的操作中,对刀是一项非常重要的工艺操作。
对刀操作的准确与否直接影响到车床加工的质量和效率。
本文将为您介绍数控车床的对刀操作步骤,帮助您正确进行对刀操作。
步骤一:准备工作在进行对刀操作之前,首先需要做一些准备工作。
1.先确保车床的刀具刀片是整齐摆放的,没有松动或损坏的情况。
2.确保车床刀架的位置正确,刀架能够正常移动。
3.准备好适合对刀操作的工件,可以是一块平整的金属坯料。
步骤二:工具选择在进行对刀操作时,需要配备一些常用的工具,以便进行测量和调整。
1.卡尺:用于测量刀具的长度、宽度和高度。
2.快速测高仪:用于测量刀具的高度差异。
3.刀具调整工具:用于调整和固定刀具。
步骤三:测量刀具长度1.选择一根刀具,并将其安装在车床刀架上。
2.使用卡尺,测量刀具的长度。
将卡尺放置在刀具的上方和下方,确保卡尺与刀具接触紧密。
3.记下测量结果,并与车床的预设数值进行比对。
如果长度不匹配,就需要进行调整。
步骤四:测量刀具宽度1.使用卡尺,测量刀具的宽度。
将卡尺放置在刀具的两侧,确保卡尺与刀具接触紧密。
2.记下测量结果,并与车床的预设数值进行比对。
如果宽度不匹配,就需要进行调整。
步骤五:测量刀具高度1.使用快速测高仪,将其靠近刀具表面,并将测高仪调至水平。
2.将测高仪移到刀具的各个部位,记录下不同部位的高度差异。
3.如果发现刀具存在高度差异,就需要进行调整,以确保刀具的高度统一。
步骤六:刀具调整根据之前测量的结果,对刀具进行调整。
1.如果刀具的长度不匹配,可以通过添加刀夹片或者更换刀具来进行调整。
2.如果刀具的宽度不匹配,可以通过调整刀具的位置或者更换合适宽度的刀具来进行调整。
3.如果刀具的高度差异较大,可以通过调整刀架高度或者刀具位置来进行调整。
步骤七:验证对刀结果在完成刀具的调整后,需要进行对刀结果的验证,以确保调整准确。
1.将工件安装在车床上,并选择适当的加工程序。
2.运行加工程序,观察加工过程中切削刀具的表现。
数控车床对刀步骤
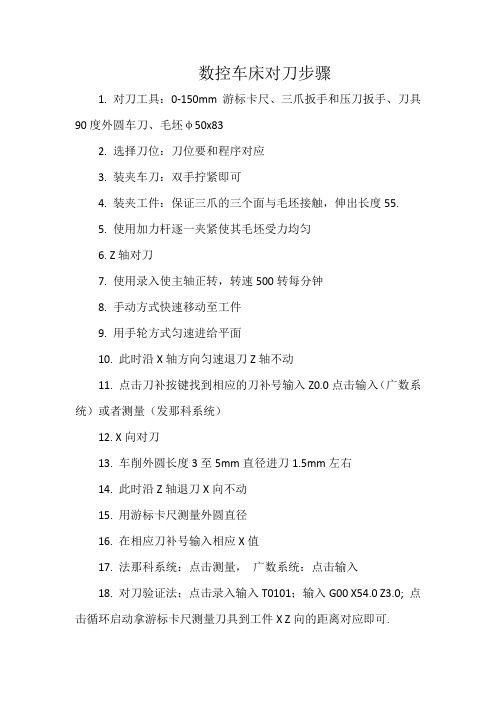
数控车床对刀步骤
1. 对刀工具:0-150mm游标卡尺、三爪扳手和压刀扳手、刀具90度外圆车刀、毛坯φ50x83
2. 选择刀位:刀位要和程序对应
3. 装夹车刀:双手拧紧即可
4. 装夹工件:保证三爪的三个面与毛坯接触,伸出长度5
5.
5. 使用加力杆逐一夹紧使其毛坯受力均匀
6. Z轴对刀
7. 使用录入使主轴正转,转速500转每分钟
8. 手动方式快速移动至工件
9. 用手轮方式匀速进给平面
10. 此时沿X轴方向匀速退刀Z轴不动
11. 点击刀补按键找到相应的刀补号输入Z0.0点击输入(广数系统)或者测量(发那科系统)
12. X向对刀
13. 车削外圆长度3至5mm直径进刀1.5mm左右
14. 此时沿Z轴退刀X向不动
15. 用游标卡尺测量外圆直径
16. 在相应刀补号输入相应X值
17. 法那科系统:点击测量,广数系统:点击输入
18. 对刀验证法:点击录入输入T0101;输入G00 X54.0 Z3.0; 点击循环启动拿游标卡尺测量刀具到工件X Z向的距离对应即可.。
数控车床对刀操作步骤及主意事项

数控车床对刀操作步骤及主要注意事项引言数控车床是一种常用的自动化机床,它能够通过计算机程序控制切削刀具进行各种精密加工。
对刀操作是数控车床上的一项重要工作,不仅关系到加工质量,还关系到操作人员的安全。
本文将介绍数控车床对刀的操作步骤及一些需要注意的事项。
操作步骤1. 准备工作在进行对刀操作之前,需要进行一些准备工作:- 检查车床设备是否正常运行,确保各项安全保护设施功能正常; - 准备好合适的刀具,并检查刀具的磨损程度;- 确定加工工件的材料和尺寸,并将工件正确装夹在车床上。
2. 测量工件和刀具对刀操作的关键是准确测量工件和刀具的尺寸。
- 使用合适的测量工具(如卡尺、游标卡尺等)测量工件的尺寸,包括直径、长度等。
记录下测量结果; - 使用刀具测量仪(或编程装置)测量刀具的长度、直径等尺寸,并记录下测量结果。
3. 汇编刀具根据测量结果,正确选择刀具,并进行刀具的汇编。
- 根据加工要求选择合适的刀具,并将其正确安装在车床的刀架上; - 使用专用工具对刀具进行调整,确保刀具的位置、夹持力等参数符合要求。
4. 进行对刀操作对刀操作是一项技术性较高的工作,需要仔细操作。
- 打开数控车床的操作界面,选择对刀操作功能; - 根据测量结果输入刀具和工件的尺寸等参数,然后启动对刀操作; - 数控车床会根据输入的参数自动调整刀具的位置和补偿值,确保加工的准确性。
5. 对刀结果检验和调整完成对刀操作后,需要对对刀结果进行检验,确保加工的准确性和质量。
- 使用测量工具对加工后的工件进行检验,与加工要求进行对比,判断偏差是否在允许范围内; - 如果测量结果有偏差,需要根据实际情况进行调整,如重新测量,重新选择刀具等。
注意事项在进行数控车床对刀操作时,需要注意以下事项,以确保操作安全和加工质量:1. 熟悉数控车床的操作规程和安全操作要求,遵守相关的安全操作规定; 2. 选择合适的刀具,并保证其质量和磨损情况符合要求; 3. 对工件进行正确的装夹,保证工件与车床床身之间的配合间隙适当; 4. 准确测量工件和刀具的尺寸,确保测量结果准确无误; 5. 在对刀操作过程中,避免手部接近刀具,以免发生意外伤害;6. 在进行刀具调整时,切勿用力过度,以免损坏刀具和车床设备;7. 对刀完成后,及时清理工作区域和设备,保持车床的清洁和良好的工作环境。
数控车床对刀
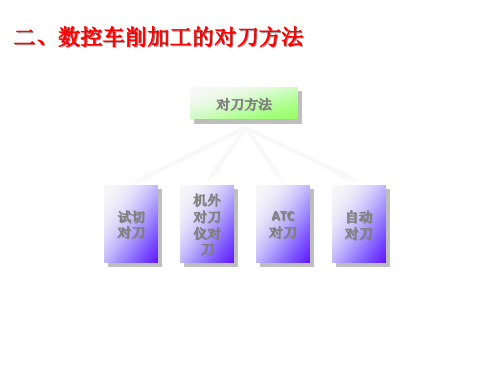
第二步:试切工件端面,把端面在工件坐标系中Z的坐标值,保持Z轴方向不动, 刀具退出。进入形状补偿参数设定界面,将光标移到相应的位置,输入Z0,按 [测量]软键对应的刀具偏移量自动输入 ;
第三步:按照第一、二步对刀方法,对其余2把刀具进行对刀及设置
928TC数控系统 对刀步骤:
第一步:在手动方式下移动刀具在工件上切出一个小台阶。测量所切出的 台阶的直径,按 I 键,屏幕显示 刀偏 X ,输入测量出的直径值,按 Enter 键
3.ATC对刀 它是在机床上利用对刀显微镜自动地计算出车刀长度的简称,
对刀镜与支架不用时取下,需要对刀时才装到主轴箱上。对刀时, 用手动方式将刀尖移到对刀镜的视野内,再用手动脉冲发生器微量 移动使假象刀尖点与对刀镜内的中心点重合(如图所示),再将光 标移到相应刀具补偿号,按“自动计算(对刀)”按键,这把刀具 在两个方向的长度就被自动计算出来,并自动存入它的刀具补偿号 中。
(2) 对刀原理
1
2
X
Z刀补
ZZxx xx
3
φD
X刀补
Xxx
试切一段外圆
Z
FANUC数控系统 对刀步骤:
第一步:用所选刀具试切工件外圆,测量试切后的工件直径,比如记为α,
保持X轴方向不动,刀具退出。点击MDI键盘上
的键,进入形状补偿参
数设定界面,将光标移到与刀位号相对应的位置,输入Xα,按菜单软键[测 量],对应的刀具偏移量自动输入 ;
谢谢观看/欢迎下载
BY FAITH I MEAN A VISION OF GOOD ONE CHERISHES AND THE ENTHUSIASM THAT PUSHES ONE TO SEEK ITS FULFILLMENT REGARDLESS OF OBSTACLES. BY FAITH I BY FAITH
数控车床对刀操作
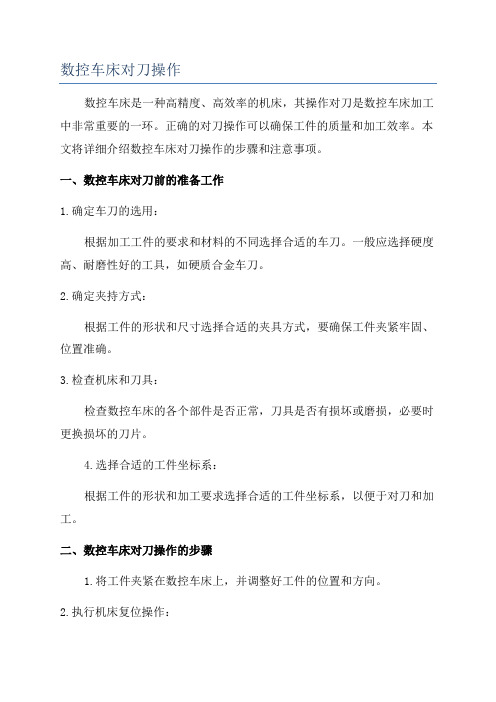
数控车床对刀操作数控车床是一种高精度、高效率的机床,其操作对刀是数控车床加工中非常重要的一环。
正确的对刀操作可以确保工件的质量和加工效率。
本文将详细介绍数控车床对刀操作的步骤和注意事项。
一、数控车床对刀前的准备工作1.确定车刀的选用:根据加工工件的要求和材料的不同选择合适的车刀。
一般应选择硬度高、耐磨性好的工具,如硬质合金车刀。
2.确定夹持方式:根据工件的形状和尺寸选择合适的夹具方式,要确保工件夹紧牢固、位置准确。
3.检查机床和刀具:检查数控车床的各个部件是否正常,刀具是否有损坏或磨损,必要时更换损坏的刀片。
4.选择合适的工件坐标系:根据工件的形状和加工要求选择合适的工件坐标系,以便于对刀和加工。
二、数控车床对刀操作的步骤1.将工件夹紧在数控车床上,并调整好工件的位置和方向。
2.执行机床复位操作:在数控系统中选择“复位”功能,使数控车床回到初始状态。
3.选择对刀方式:有多种对刀方式可供选择,如纵向对刀、横向对刀、刀尖对刀等。
根据具体情况选择合适的对刀方式。
4.第一次对刀:首先,用手摇车床将车刀靠近工件,使其与工件轻微接触,然后通过数控系统的操作将车刀靠近工件,直至工件上出现微弧光斑。
此时,数控系统会自动记录车刀位置。
5.第二次对刀:将车刀离开工件,重新摆放好刀具,再次将车刀靠近工件。
通过数控系统的操作,使车刀与工件轻微接触,并记录下车刀的位置。
6.对刀参数计算:利用数控系统的功能,计算出车刀位置需要调整的数值,并将其输入系统。
7.进行调整:根据计算结果,通过数控系统调整车刀位置,使其达到预期的位置。
8.再次对刀:将车刀重新靠近工件并进行微调,直至车刀与工件轻微接触。
通过数控系统的操作,记录车刀的准确位置。
9.完成对刀:对刀操作完成后,检查车刀位置是否准确,并进行必要的微调。
三、数控车床对刀操作的注意事项1.安全第一:操作人员在进行对刀操作时,必须严格遵守安全操作规程,切勿将手部或身体靠近旋转的刀具。
6数控车床的对刀操作

说明Z坐标已经对好!
6、检验
1、粗略检验 手轮方式下移动刀具至工件右端面,按位置键看看 工件X、Z坐标是否接近0。 2、精确检验 录入方式下输入程序段检验。
光标移动至X值——通过面板的MDI键盘编辑区输入X24——出现下 图所示情况
按测量对应的F2键——按POS按键——出现下图
说明X轴已经对好。
2、对Z轴:
启动主轴——移动刀具车工件端面——保证Z坐标值不动—— 移动X轴远离工件——光标移动至Z值——输入Z0——按F2测量
按POS按键——出现下图
4、对刀的方法
三种方法: 1、光学对刀法
2、定位对刀法 3、试切对刀法(掌握)
5、试切对刀法
1、对X轴 启动主轴——车削工件外圆——保证X坐标值不变——移动Z轴 ——刀具远离工件——停止主轴——测量刚车削的工件直径
假设测量结果为Ф24mm——按OFS/SET按键——出现下图画面
再按F2按键——出现下图画面
数控车床的对刀操作P27
相互学习、相互提高、共同进步
1、对刀概念
什么是对刀? 在加工程序执行前,调整每把刀的刀 位点,使其尽量重合于某一理想基准点 ,这一过程就叫对刀。
2、刀位点Байду номын сангаас
刀位点就是在加工程序编制中,用以 表示刀具特征的点,也是对刀和加工的 基准点。
3、对刀的作用
对刀是数控加工中的主要操作和重要 技能,在一定条件下,对刀的精度可以 决定零件的加工精度,同时,对刀效率 还直接影响数控加工效率。
数控车床对刀方法

数控车床对刀方法一、对刀对刀的目的是确定程序原点在机床坐标系中的位置,对刀点能够设在零件上、夹具上或机床上,对刀时应使对刀点与刀位点重合。
数控车床常用的对刀方法有三种:试切对刀、机械对刀仪对刀〔接触式〕、光学对刀仪对刀〔非接触式〕,如图3-9 所示。
1、试切对刀1 〕外径刀的对刀方法如图3-10 所示。
Z 向对刀如(a) 所示。
先用外径刀将工件端面( 基准面) 车削出来;车削端面后,刀具能够沿X 方向移动远离工件,但不可Z 方向移动。
Z 轴对刀输入:〝Z0 测量〞。
X 向对刀如(b) 所示。
车削任一外径后,使刀具Z 向移动远离工件,待主轴停止转动后,测量刚刚车削出来的外径尺寸。
例如,测量值为Φ50.78mm, 那么X 轴对刀输入:〝X50.78 测量〞。
2 〕内孔刀的对刀方法类似外径刀的对刀方法。
Z 向对刀内孔车刀轻微接触到己加工好的基准面〔端面〕后,就不可再作Z 向移动。
Z 轴对刀输入:〝Z0 测量〞。
X 向对刀任意车削一内孔直径后,Z 向移动刀具远离工件,停止主轴转动,然后测量已车削好的内径尺寸。
例如,测量值为Φ45.56mm, 那么X 轴对刀输入:〝X45.56 测量〞。
3 〕钻头、中心钻的对刀方法如图3-11 所示。
Z 向对刀如〔a 〕所示。
钻头( 或中心钻) 轻微接触到基准面后,就不可再作Z 向移动。
Z 轴对刀输入:〝Z0 测量〞。
X 向对刀如〔b 〕所示。
主轴不必转动,以手动方式将钻头沿X 轴移动到钻孔中心,即看屏幕显示的机械坐标到〝X0.0 ”为止。
X 轴对刀输入:〝X0 测量〞。
2、机械对刀仪对刀将刀具的刀尖与对刀仪的百分表测头接触,得到两个方向的刀偏量。
有的机床具有刀具探测功能,即通过机床上的对刀仪测头测量刀偏量。
3、光学对刀仪对刀将刀具刀尖对准刀镜的十字线中心,以十字线中心为基准,得到各把刀的刀偏量。
二、刀具补偿值的输入和修改依照刀具的实际参数和位置,将刀尖圆弧半径补偿值和刀具几何磨损补偿值输入到与程序对应的储备位置。
数控铣床对刀操作
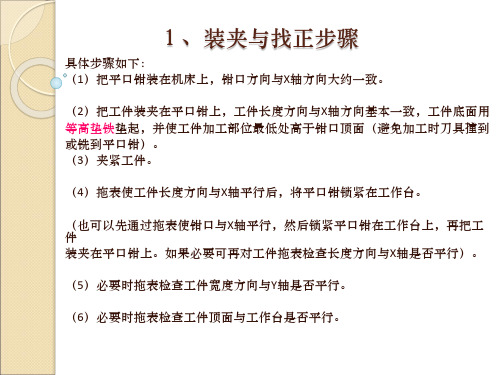
2) 基准面在底面(如图)
底面正确寻边 读出机床坐标 Z0,则工件坐标原点的机 床坐标值Z为: Z=Z0-h+H; H为工件坐标 原点离基准面(底面)的 距离。 对刀完成后,把X、Y、Z值 输入到G54中去(或G55、 G56、G57G58 、G59,依 程序所引用的代码对应)。
1、装夹与找正步骤
具体步骤如下: (1)把平口钳装在机床上,钳口方向与X轴方向大约一致。
(2)把工件装夹在平口钳上,工件长度方向与X轴方向基本一致,工件底面用 等高垫铁垫起,并使工件加工部位最低处高于钳口顶面(避免加工时刀具撞到 或铣到平口钳)。 (3)夹紧工件。
(4)拖表使工件长度方向与X轴平行后,将平口钳锁紧在工作台。 (也可以先通过拖表使钳口与X轴平行,然后锁紧平口钳在工作台上,再把工 件 装夹在平口钳上。如果必要可再对工件拖表检查长度方向与X轴是否平行)。 (5)必要时拖表检查工件宽度方向与Y轴是否平行。 (6)必要时拖表检查工件顶面与工作台是否平行。
2、对刀(确定工件坐标系原点位置) X方向(寻边器对刀):
1.第一种方法:基准边碰数对刀
图中长方体工件左下角为基准角,左 边为X方向的基准边,下边为Y方向的 基准边。通过正确寻边,寻边器与基准 边刚好接触(误差不超过机床的最小 手动进给单位,一般为0.01,精密机床可 达0.001)。 在左边寻边,在机床控制台显示屏上 读出机床坐标值X0(即寻边器中心的机床 坐 标)。 左边基准边的机床坐标为:X1=X0+R; (R为寻边器半径) 工件坐标原点的机床坐标值为: X=X1+a/2=X0+R+a/2; (a/2为工件坐标原点离基准边的距离)。
数控机床对刀步骤方法
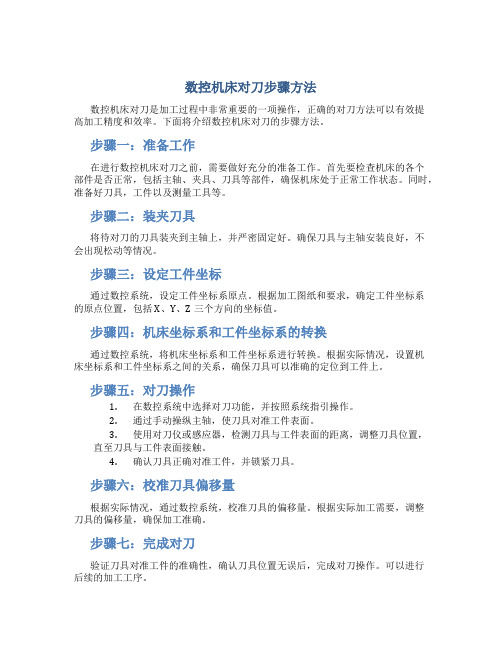
数控机床对刀步骤方法数控机床对刀是加工过程中非常重要的一项操作,正确的对刀方法可以有效提高加工精度和效率。
下面将介绍数控机床对刀的步骤方法。
步骤一:准备工作在进行数控机床对刀之前,需要做好充分的准备工作。
首先要检查机床的各个部件是否正常,包括主轴、夹具、刀具等部件,确保机床处于正常工作状态。
同时,准备好刀具,工件以及测量工具等。
步骤二:装夹刀具将待对刀的刀具装夹到主轴上,并严密固定好。
确保刀具与主轴安装良好,不会出现松动等情况。
步骤三:设定工件坐标通过数控系统,设定工件坐标系原点。
根据加工图纸和要求,确定工件坐标系的原点位置,包括X、Y、Z三个方向的坐标值。
步骤四:机床坐标系和工件坐标系的转换通过数控系统,将机床坐标系和工件坐标系进行转换。
根据实际情况,设置机床坐标系和工件坐标系之间的关系,确保刀具可以准确的定位到工件上。
步骤五:对刀操作1.在数控系统中选择对刀功能,并按照系统指引操作。
2.通过手动操纵主轴,使刀具对准工件表面。
3.使用对刀仪或感应器,检测刀具与工件表面的距离,调整刀具位置,直至刀具与工件表面接触。
4.确认刀具正确对准工件,并锁紧刀具。
步骤六:校准刀具偏移量根据实际情况,通过数控系统,校准刀具的偏移量。
根据实际加工需要,调整刀具的偏移量,确保加工准确。
步骤七:完成对刀验证刀具对准工件的准确性,确认刀具位置无误后,完成对刀操作。
可以进行后续的加工工序。
数控机床对刀是数控加工过程中的一项关键工序,正确的对刀方法可以有效提高加工精度和效率。
希望通过以上步骤方法的介绍,能够帮助操作人员更好地进行数控机床对刀操作。
数控机床对刀的方法
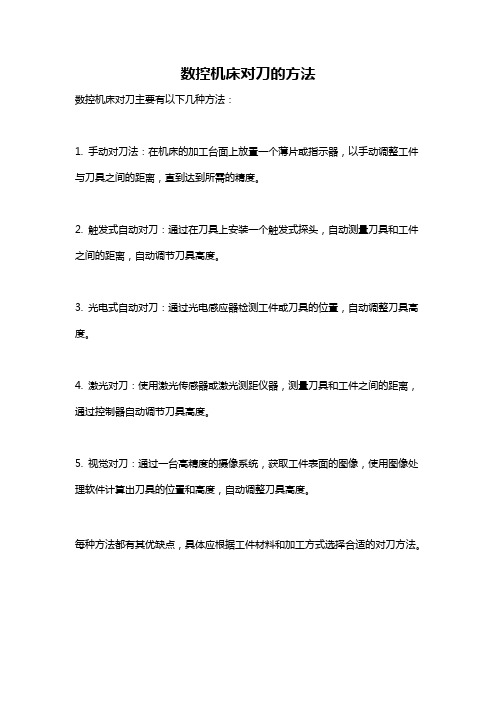
数控机床对刀的方法
数控机床对刀主要有以下几种方法:
1. 手动对刀法:在机床的加工台面上放置一个薄片或指示器,以手动调整工件与刀具之间的距离,直到达到所需的精度。
2. 触发式自动对刀:通过在刀具上安装一个触发式探头,自动测量刀具和工件之间的距离,自动调节刀具高度。
3. 光电式自动对刀:通过光电感应器检测工件或刀具的位置,自动调整刀具高度。
4. 激光对刀:使用激光传感器或激光测距仪器,测量刀具和工件之间的距离,通过控制器自动调节刀具高度。
5. 视觉对刀:通过一台高精度的摄像系统,获取工件表面的图像,使用图像处理软件计算出刀具的位置和高度,自动调整刀具高度。
每种方法都有其优缺点,具体应根据工件材料和加工方式选择合适的对刀方法。
数控铣床常用对刀方法【专业研究】
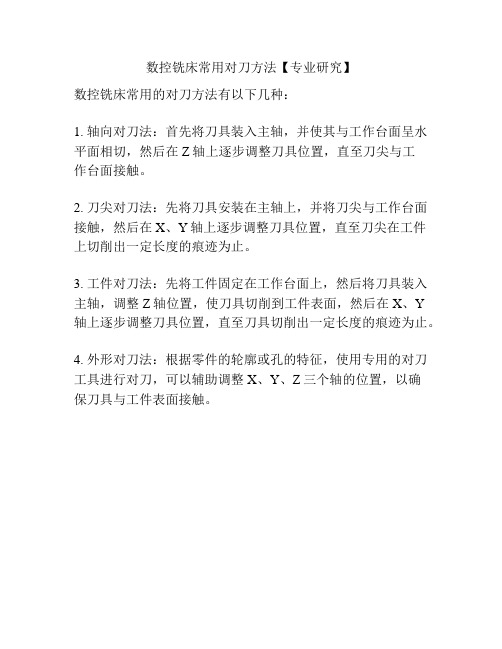
数控铣床常用对刀方法【专业研究】
数控铣床常用的对刀方法有以下几种:
1. 轴向对刀法:首先将刀具装入主轴,并使其与工作台面呈水平面相切,然后在Z轴上逐步调整刀具位置,直至刀尖与工
作台面接触。
2. 刀尖对刀法:先将刀具安装在主轴上,并将刀尖与工作台面接触,然后在X、Y轴上逐步调整刀具位置,直至刀尖在工件上切削出一定长度的痕迹为止。
3. 工件对刀法:先将工件固定在工作台面上,然后将刀具装入主轴,调整Z轴位置,使刀具切削到工件表面,然后在X、Y
轴上逐步调整刀具位置,直至刀具切削出一定长度的痕迹为止。
4. 外形对刀法:根据零件的轮廓或孔的特征,使用专用的对刀工具进行对刀,可以辅助调整X、Y、Z三个轴的位置,以确
保刀具与工件表面接触。
数控车床的对刀方法

数控车床的对刀方法一、对刀的基本概念对刀是数控加工中较为复杂的工艺准备工作之一,对刀的好与差将直接影响到加工程序的编制及零件的尺寸精度。
通过对刀或刀具预调,还可同时测定其各号刀的刀位偏差,有利于设定刀具补偿量。
1 刀位点刀位点是指在加工程序编制中,用以表示刀具特征的点,也是对刀和加工的基准点。
对于车刀,各类车刀的刀位点见下图:2 对刀对刀是数控加工中的主要操作。
结合机床操作说明掌握有关对刀方法和技巧,具有十分重要的竟义。
在加工程序执行前,调整每把刀的刀位点,使其尽量重合于某一理想基准点,这一过程称为对刀。
理想基准点可以设定在刀具上,如基准刀的刀尖上;也可以设定在刀具外,如光学对刀镜内的十字刻线交点上。
二、对刀的基本方法目前绝大多数的数控车床采用手动对刀,其基本方法有以下几种:1 定位对刀法定位对刀法的实质是按接触式设定基准重合原理而进行的一种粗定位对刀方法,其定位基准由预设的对刀基准点来体现。
对刀时,只要将各号刀的刀位点调整至与对刀基准点重合即可。
该方法简便易行,因而得到较广泛的应用,但其对刀精度受到操者技术熟练程度的影响,一般情况下其精度都不高,还须在加工或试切中修正。
2 光学对刀法这是一种按非接触式设定基准重合原理而进行的对刀方法,其定位基准通常由光学显微镜(或投影放大镜)上的十字基准刻线交点来体现。
这种对刀方法比定位对刀法的对刀精度高,并且不会损坏刀尖,是一种推广采用的方法。
3 试切对刀法在以上各种手动对刀方法中,均因可能受到手动和目测等多种误差的影响以至其对刀精度十分有限,往往需要通过试切对刀,以得到更加准确和可靠的结果。
a、直接用刀具试切对刀(FANUC series oi mate TB系统)1) 用外圆车刀先试切一外圆,测量外圆直径后,按→ → 输入“外圆直径值”,按键,刀具“X”补偿值即自动输入到几何形状里。
2) 用外圆车刀再试切外圆端面,按→ → 输入“Z 0”,按键,刀具“Z”补偿值即自动输入到几何形状里。
数控车床的对刀方法

数控车床的对刀方法一、对刀的基本概念对刀是数控加工中较为复杂的工艺准备工作之一,对刀的好与差将直接影响到加工程序的编制及零件的尺寸精度。
通过对刀或刀具预调,还可同时测定其各号刀的刀位偏差,有利于设定刀具补偿量。
1、刀位点刀位点是指在加工程序编制中,用以表示刀具特征的点,也是对刀和加工的基准点。
2、对刀对刀是数控加工中的主要操作。
结合机床操作说明掌握有关对刀方法和技巧,具有十分重要的竟义。
在加工程序执行前,调整每把刀的刀位点,使其尽量重合于某一理想基准点,这一过程称为对刀。
理想基准点可以设定在刀具上,如基准刀的刀尖上;也可以设定在刀具外,如光学对刀镜内的十字刻线交点上。
二、对刀的基本方法目前绝大多数的数控车床采用手动对刀,其基本方法有以下几种:1、定位对刀法定位对刀法的实质是按接触式设定基准重合原理而进行的一种粗定位对刀方法,其定位基准由预设的对刀基准点来体现。
对刀时,只要将各号刀的刀位点调整至与对刀基准点重合即可。
该方法简便易行,因而得到较广泛的应用,但其对刀精度受到操者技术熟练程度的影响,一般情况下其精度都不高,还须在加工或试切中修正。
2、光学对刀法这是一种按非接触式设定基准重合原理而进行的对刀方法,其定位基准通常由光学显微镜(或投影放大镜)上的十字基准刻线交点来体现。
这种对刀方法比定位对刀法的对刀精度高,并且不会损坏刀尖,是一种推广采用的方法。
3、试切对刀法在以上各种手动对刀方法中,均因可能受到手动和目测等多种误差的影响以至其对刀精度十分有限,往往需要通过试切对刀,以得到更加准确和可靠的结果。
a、直接用刀具试切对刀(广数980TD系统)1) 用外圆车刀先试切一外圆,测量外圆直径后,按→→输入“外圆直径值”,按键,刀具“X”补偿值即自动输入到几何形状里。
如实测毛坯的直径为30.68mm,在刀补页面输入X30.68即可。
2) 用外圆车刀再试切外圆端面,按→→输入“Z 0”,按键,刀具“Z”补偿值即自动输入到几何形状里。
数控车床对刀方法

数控车床对刀方法机床能对加工对象的适应性强,适应模具等产品单件生产的特点,为模具的制造提供了合适的加工方法。
下面店铺给大家整理了数控车床对刀方法大全,欢迎大家前来阅读参考。
一,直接用刀具试切对刀1. 用外园车刀先试车一外园,记住当前X 坐标,测量外园直径后,用 X 坐标减外园直径,所的值输入 offset 界面的几何形状 X 值里。
2. 用外园车刀先试车一外园端面,记住当前 Z 坐标,输入 offset 界面的几何形状 Z 值里。
二,用 G50 设置工件零点1. 用外园车刀先试车一外园,测量外园直径后,把刀沿Z 轴正方向退点,切端面到中心( X 轴坐标减去直径值)。
2. 选择 MDI 方式,输入 G50 X0 Z0 ,启动 START 键,把当前点设为零点。
3. 选择 MDI 方式,输入 G0 X150 Z150 ,使刀具离开工件进刀加工。
4. 这时程序开头:G50 X150 Z150 …… . 。
5. 注意:用G50 X150 Z150 ,你起点和终点必须一致即X150 Z150 ,这样才能保证重复加工不乱刀。
6. 如用第二参考点 G30 ,即能保证重复加工不乱刀,这时程序开头 G30 U0 W0 G50 X150 Z1507. 在FANUC 系统里,第二参考点的位置在参数里设置,在Yhcnc 软件里,按鼠标右键出现对话框,按鼠标左键确认即可。
三,用工件移设置工件零点1. 在 FANUC0-TD 系统的 Offset 里,有一工件移界面,可输入零点偏移值。
2. 用外园车刀先试切工件端面,这时 Z 坐标的位置如: Z200 ,直接输入到偏移值里。
3. 选择“ Ref ”回参考点方式,按 X 、 Z 轴回参考点,这时工件零点坐标系即建立。
4. 注意:这个零点一直保持,只有从新设置偏移值 Z0 ,才清除。
四,用 G54-G59 设置工件零点1. 用外园车刀先试车一外园,测量外园直径后,把刀沿Z 轴正方向退点,切端面到中心。
数控加工中的对刀方法

长沙航空职业技术学院
" 数控加工的对刀原理
编制完毕的数控加工程序完全是一个基于工件 坐标系的数控程序, 丝毫体现不出与机床参考点坐 标系有任何联系。所以, 在把工件装夹到机床上时, 必须确定工件在机床上的正确位置。这个确定位置 的过程就是通过对刀来实现的, 对刀就是要将刀位 点准确地定位到起刀点的位置上。刀位点是确定刀 具位置的基准点 (车刀刀位点为刀尖, 钻头刀位点为 钻尖, 平头立铣刀刀位点为端面中心, 球头刀刀位点 为球心) 。对刀也就是要通过定义刀位点与工件零 点的相对位置来保证工件在机床坐标系中的正确位
试件 测点数 ’ 圆度误差值 % 78 4 0* "/""%0
5
收稿日期: %""- 年 2 月
若! ( ", 则! "#$ 为锐角三角形; 若 #, $) ! ", ( ", 则 ! "#$ 为直角三角形或钝角三 ! #, $) " ", 角形, 此时, 若 ! ( ", 则 ! "#$ 为直角三 #, $) # ", 角形, 若! ( ", 则! "#$ 为钝角三角形。 #, $) #", 设! ( ") 为$ " 的角度判别函数, 同理可得:
数控加工七种对刀方式详解!做加工五年还没遇到几种

数控加工七种对刀方式详解!做加工五年还没遇到几种对刀是数控加工中的主要操作和重要技能。
在一定条件下,对刀的精度可以决定零件的加工精度,同时,对刀效率还直接影响数控加工效率。
仅仅知道对刀方法是不够的,还要知道数控系统的各种对刀设置方式,以及这些方式在加工程序中的调用方法,同时要知道各种对刀方式的优缺点、使用条件等。
一、对刀原理对刀的目的是为了建立工件坐标系,直观的说法是,对刀是确立工件在机床工作台中的位置,实际上就是求对刀点在机床坐标系中的坐标。
对于数控车床来说,在加工前首先要选择对刀点,对刀点是指用数控机床加工工件时,刀具相对于工件运动的起点。
对刀点既可以设在工件上(如工件上的设计基准或定位基准),也可以设在夹具或机床上,若设在夹具或机床上的某一点,则该点必须与工件的定位基准保持一定精度的尺寸关系。
对刀时,应使指刀位点与对刀点重合,所谓刀位点是指刀具的定位基准点,对于车刀来说,其刀位点是刀尖。
对刀的目的是确定对刀点(或工件原点)在机床坐标系中的绝对坐标值,测量刀具的刀位偏差值。
对刀点找正的准确度直接影响加工精度。
在实际加工工件时,使用一把刀具一般不能满足工件的加工要求,通常要使用多把刀具进行加工。
在使用多把车刀加工时,在换刀位置不变的情况下,换刀后刀尖点的几何位置将出现差异,这就要求不同的刀具在不同的起始位置开始加工时,都能保证程序正常运行。
为了解决这个问题,机床数控系统配备了刀具几何位置补偿的功能,利用刀具几何位置补偿功能,只要事先把每把刀相对于某一预先选定的基准刀的位置偏差测量出来,输入到数控系统的刀具参数补正栏指定组号里,在加工程序中利用T指令,即可在刀具轨迹中自动补偿刀具位置偏差。
刀具位置偏差的测量同样也需通过对刀操作来实现。
二、对刀方法在数控加工中,对刀的基本方法有试切法、对刀仪对刀和自动对刀等。
本文以数控铣床为例,介绍几种常用的对刀方法。
1、试切对刀法这种方法简单方便,但会在工件表面留下切削痕迹,且对刀精度较低。
- 1、下载文档前请自行甄别文档内容的完整性,平台不提供额外的编辑、内容补充、找答案等附加服务。
- 2、"仅部分预览"的文档,不可在线预览部分如存在完整性等问题,可反馈申请退款(可完整预览的文档不适用该条件!)。
- 3、如文档侵犯您的权益,请联系客服反馈,我们会尽快为您处理(人工客服工作时间:9:00-18:30)。
收稿日期:2004-11-18
作者简介:张 军(1960—),男,工程师
基金项目:教育部世界银行发展计划资助项目:A00301500040.数控加工中的对刀方法与技巧
张 军,程光明
(吉林大学机械科学与工程学院,长春 130025)
摘 要:
介绍了普通数控机床的几种对刀方式以及对刀精度的比较。
关键词:
对刀方式;起刀点;刀偏;基准刀;数控机床中图分类号:TG506 文献标识码:B 文章编号:1002-4956(2005)07-0059-03
在数控加工中,对刀是一项很重要的工作,对刀的准确程度直接影响工件的加工精度,所以,对刀这项工作是数控机床操作人员很重要的一门基本功。
下面介绍我们在数控机床加工对刀过程中常用的一些方法。
1 刀具偏置补偿(刀具偏置数据的测量和输入方法)
加工前,刀具首先回参考点。
如果刀具(例如普通数控车床刀架上可装四把车刀)安装后没有进行刀具偏置补偿,或已进行了刀具偏置补偿但刀具安装位置有变动的话,必须要进行刀偏设置。
加工一个或一批工件情况下,必须要确定对刀点。
对刀方式在应用时要针对不同的情况采用不同的对刀方式。
下面以数控车床HCNC-1型为例,说明刀偏数据的测量和输入方法。
刀偏数据的测量和输入方法,我们常用的有三种:
方法一
(1)系统在手动方式下,首先确定一把基准刀并用基准刀对准工件的一基准点,如A点,见图1。
图1
(2)按F7,“X轴清零”,则屏幕上显示的X轴坐标
清零。
按F9,“Z轴清零”,则屏幕上显示的X轴清零。
(3)采用点动方式使基准刀退出。
(4)选择刀号,在控制面板上按“刀架开/停”,使
刀架换刀。
以“点动”及步进方式,使该刀刀尖对准该
基准点A,这时屏幕显示的X、Z值就是该刀与基准刀
之间的偏置值■X、■Y。
将该偏置值输入到相应刀具
编号下面的参数输入处,回车即可。
方法二
59
中国科技论文统计源期刊 实 验 技 术 与 管 理 Vol.22 No.7 2005
60实 验 技 术 与 管 理
(1)选定基准刀,车端面一刀,沿X轴退出,记下屏幕上显示的Z轴坐标值,记为Z1。
(2)车外圆一刀,沿Z轴退出,记下屏幕上显示的X轴坐标值,记为X1。
(3)将基准刀回到点X1,Z1。
方法是先使用“工作方式”中的点动方式走大距离,然后使用“工作方式”中的步进和“进给倍率”来移动、调整到点X1、Z1。
(4)按F7,“X轴清零”,则屏幕上显示的X轴坐标清零;按F9,“Z轴清零”,则屏幕上显示的X轴坐标清零。
(5)采用点动方式使基准刀退出。
(6)选择刀号,在控制面板上按“刀架开/停”,使刀架换刀。
以“点动方式”及“步进方式”使该刀刀尖对准原X1、Z1所在点,这时屏幕显示的X、Z值就是该刀与基准刀之间的偏置值■X、■Y。
将该偏置值输入到相应刀具编号下面的参数输入处,回车即可。
方法三
(1)系统在点动方式下,用基准刀切削工件外径。
(2)点动方式使刀具沿Z轴离开工件,使主轴停转,测量被车表面外径大小,记录D1。
屏幕上显示的X轴坐标显示值记为X1。
(3)用基准刀切削工件端面,点动方式使刀具沿X轴离开工件,使主轴停转,测量被车端面与某一基准面之间的距离,记录L1。
屏幕上显示的Z轴坐标显示值记为Z1。
(注:X1、D1、Z1可视为基准值。
)
(4)退刀,选择所需的刀号,在控制面板上按“刀架开/停”,使刀架换刀。
重复步骤(1)、(2)、(3),得到X2、D2、L2、X3、D3、L3、X4、D4、L4(若刀架装四把刀的话)。
选择刀号,在控制面板上按“刀架开/停”,使刀架换刀。
以“点动方式”,使该刀刀尖对准该基准点A,这时屏幕显示的X、Z值就是该刀与基准刀之间的偏置值。
(5)计算刀偏。
若系统设置为直径编程,且1#刀为基准刀,则2#刀的刀偏量计算为
■X2=X2-X1-(D2-D1) ■Z2=Z2-Z1-(L2-L1)
若系统设置为半径编程,则
■X=X2-X1-(D2-D1)/2 ■Z=Z2-Z1-(L2-L1)/2
3#、4#刀的刀偏量计算方法与此相同。
将计算得到的偏置值输入到相应刀具编号下面的参数输入处,回车即可。
上面列举了三种方法。
第一种方法的基准刀在对准基准点时,采用的是直接观察的方式。
一般说在对准基准点前,也是外径、端面各车一刀,但并不精确回基准点A。
基准刀对基准点A和后续对基准点A都存在误差。
第二种方法的基准刀在对准基准点A时,很明显,采用的是准确定位的方式,即基准刀对A点是准确的,但后续刀对准基准点A点时,由于采用的是直接观察的方式,还是存在对刀误差。
第三种方法的基准刀在对准基准点A时,采用的是与第二种方法相同即准确定位的方式。
后续刀对基准点A点时,采用的是精确方法。
但误差还是有的,主要是测量误差,即测量D1、D2、L2、D3、L3、D4、L4时所引起的误差。
无疑,第一种方法花的时间最少,第三种方法花的时间最长,最麻烦,但两者的对刀精度的差异是明显的,第三种方式的精度是最高的。
2 对(起)刀点的确定方法
对刀点为刀具相对于工件运动的起点,用来确定机床坐标系(一般为编程坐标系)之间的关系。
在华中HCNC-I型铣削系统中,对刀点一般通过G92X**Y**Z**设置,X(Y、Z)后的数据为对刀点在工件坐标系中的坐标值,如G92X70Y70Z0等。
对刀方式(确定起刀的方法)也有以下三种。
(1)以端面圆心点为基准点来确定对刀点,在工件端面上车一刀,即平端面。
将基准刀的刀尖对准端面中心点,然后在MDI方式下,运行一句G90G01X′**Y′**Z′**(把G91改为G90也可),刀位点即位于对刀点上,按“循环起动”开始加工。
(2)以端面四分点为基准点确定对刀点“选定基准刀,车端面一刀,退出;再车外圆一刀,退出;然后以点动和步进方式使基准刀回到四分点A,在MDI方式下,运行一句G91G01X′**Y′**Z′**”,刀位点即位于对刀点上,按“循环起动”开始加工。
(3)以端面四分点为基准点来确定对刀点,精确对刀,选定基准刀,车端面一刀,沿X轴退出。
屏幕上显示的Z轴坐标值记为Z1。
再车外圆一刀,沿Z轴退出,屏幕上显示的X轴坐标值记为X1,然后以点动和步进方式使基准刀回到点X1、Z1,在MDI方式下,运行一句G91G01X′**Y′**Z′**,刀位点即位于对刀点上,按“循环起动”开始加工。
参考文献:
[1]武汉华中数控系统有限公司.华中I型车削数控系统CNC-1T使用手册[S].1997.
[2]卢子平.数控机床加工与编程[M].成都:电子科技大学出版社,1999.
[3]成大光.机械设计手册[M].北京:化学工业出版社,1997.
(上接第47页)
6 结论
根据我系传感器课程实验大纲要求,通过我们的努力,独立完成了CSY—910型传感器实验仪扩展装置及新增实验项目的开发工作,满足了传感器实验教学的需要,并节省了大量的经费。
经2001和2002级学生实验课程证明,新增实验项目效果良好。
参考文献:
[1]凌振宝,田 光,王 君,等.传感器原理及检测技术实验指导书与习题集[M].长春:吉林大学出版
社,2003.
[2]王 君,凌振宝.传感器原理及检测技术[M].长春:吉林大学出版社,2003.
[3]凌振宝,王 君,田 光.CSY—910型传感器实验仪增设实验项目电路设计[J].实验室研究与探
索,2003,(4):84-86.
[4]黄继昌,等.传感器工作原理及应用实例[M].北京:人民邮电出版社,1998.
[5]徐 欣,乐 飞,陆申龙,等.用激光光电传感器测液体的粘滞系数—经典的测量液体粘滞系数的
改进[J].实验技术与管理,2002,19(5):43-46.61
张 军,等:数控加工中的对刀方法与技巧。