微电铸中电铸液的发展现状和趋势
2023年电铸模具行业市场分析现状

2023年电铸模具行业市场分析现状电铸模具是一种用于制造金属零部件的工具,其市场规模巨大且不断增长。
目前,电铸模具行业已经成为一个重要的制造业支柱,特别是在汽车、航空、电子等行业中的广泛应用。
一、市场规模及前景据统计,全球电铸模具行业市场规模已超过300亿美元,预计到2025年将达到500亿美元,年复合增长率达到7%以上。
这主要受以下因素的影响:1.1 汽车行业的快速发展。
随着全球汽车业的持续增长和新能源汽车的兴起,对电铸模具的需求不断增加。
电铸模具在汽车制造过程中起到至关重要的作用,可以有效地提高生产效率和质量。
1.2 航空航天行业的发展。
随着航空航天技术的进步和航空产业的快速增长,对电铸模具的需求也在不断增加。
电铸模具在航空航天工业中的应用领域广泛,包括航空发动机、气动部件、螺栓等。
1.3 电子行业的高速发展。
随着电子产品的不断更新迭代和智能化的发展,对电铸模具的需求也在不断增加。
电铸模具在电子行业中的应用主要包括电子元件、电路板等。
1.4 其他行业的需求增长。
除了汽车、航空航天和电子行业,电铸模具在其他行业中的应用也在不断扩大,例如家电、建筑、机械等。
二、市场竞争及现状虽然电铸模具行业市场规模巨大,但市场竞争也非常激烈。
目前,全球市场上主要的电铸模具生产企业主要集中在德国、日本、美国、中国等地。
2.1 德国。
作为世界著名的制造业强国,德国在电铸模具领域具有较强的技术实力和市场竞争力。
德国企业以高品质、高精度和高性能的产品闻名于世。
2.2 日本。
日本在电铸模具领域的市场份额也非常大。
日本企业一直以来都以技术领先、产品质量优良而著称。
特别是在汽车和电子行业中具有重要地位。
2.3 美国。
美国是全球最大的汽车市场之一,其电铸模具行业也非常发达。
美国企业以高度自动化和先进制造技术为优势,产品在市场上具有一定竞争力。
2.4 中国。
中国在电铸模具行业的发展迅速,已成为全球最大的电铸模具生产和出口国之一。
低压铸造国内外发展趋势和现状
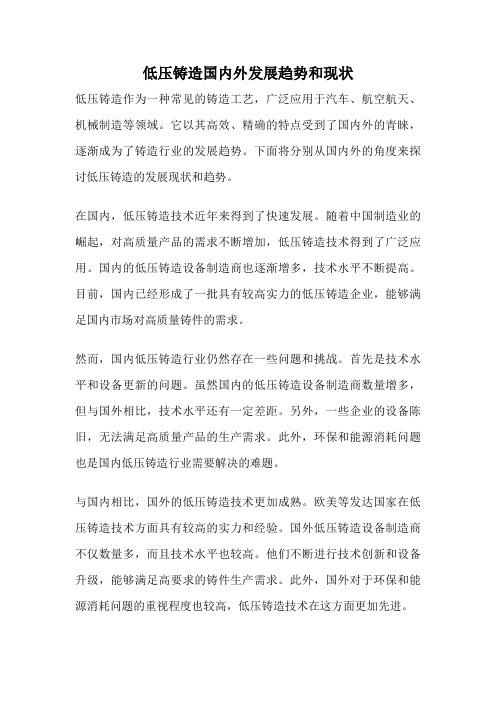
低压铸造国内外发展趋势和现状低压铸造作为一种常见的铸造工艺,广泛应用于汽车、航空航天、机械制造等领域。
它以其高效、精确的特点受到了国内外的青睐,逐渐成为了铸造行业的发展趋势。
下面将分别从国内外的角度来探讨低压铸造的发展现状和趋势。
在国内,低压铸造技术近年来得到了快速发展。
随着中国制造业的崛起,对高质量产品的需求不断增加,低压铸造技术得到了广泛应用。
国内的低压铸造设备制造商也逐渐增多,技术水平不断提高。
目前,国内已经形成了一批具有较高实力的低压铸造企业,能够满足国内市场对高质量铸件的需求。
然而,国内低压铸造行业仍然存在一些问题和挑战。
首先是技术水平和设备更新的问题。
虽然国内的低压铸造设备制造商数量增多,但与国外相比,技术水平还有一定差距。
另外,一些企业的设备陈旧,无法满足高质量产品的生产需求。
此外,环保和能源消耗问题也是国内低压铸造行业需要解决的难题。
与国内相比,国外的低压铸造技术更加成熟。
欧美等发达国家在低压铸造技术方面具有较高的实力和经验。
国外低压铸造设备制造商不仅数量多,而且技术水平也较高。
他们不断进行技术创新和设备升级,能够满足高要求的铸件生产需求。
此外,国外对于环保和能源消耗问题的重视程度也较高,低压铸造技术在这方面更加先进。
未来,低压铸造技术将继续发展壮大。
随着工业化进程的加快,对高质量产品的需求将持续增加。
低压铸造作为一种高效、精确的铸造工艺,将在这一需求下得到进一步推广和应用。
同时,随着技术的进步和设备的更新,低压铸造的技术水平将不断提高,能够生产更高质量的铸件。
此外,环保和能源消耗问题也将成为低压铸造技术发展的重要方向,更加注重绿色生产和可持续发展。
低压铸造技术在国内外都呈现出快速发展的趋势。
国内低压铸造行业虽然存在一些问题和挑战,但随着技术的不断进步和设备的更新,将能够满足国内市场对高质量产品的需求。
国外低压铸造技术更加成熟,具有较高的技术水平和经验,未来将继续引领低压铸造技术的发展。
微电铸工艺现状和发展趋势
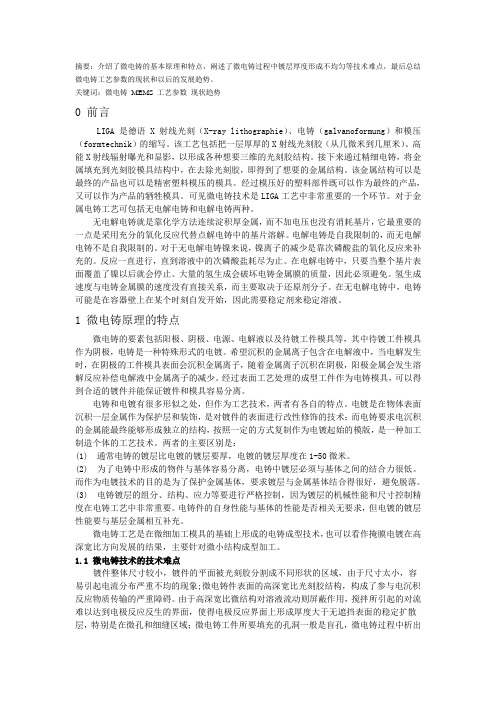
摘要:介绍了微电铸的基本原理和特点,阐述了微电铸过程中镀层厚度形成不均匀等技术难点,最后总结微电铸工艺参数的现状和以后的发展趋势。
关键词:微电铸MEMS 工艺参数现状趋势0 前言LIGA是德语X射线光刻(X-ray lithographie)、电铸(galvanoformung)和模压(formtechnik)的缩写。
该工艺包括把一层厚厚的X射线光刻胶(从几微米到几厘米)、高能X射线辐射曝光和显影,以形成各种想要三维的光刻胶结构。
接下来通过精细电铸,将金属填充到光刻胶模具结构中,在去除光刻胶,即得到了想要的金属结构。
该金属结构可以是最终的产品也可以是精密塑料模压的模具。
经过模压好的塑料部件既可以作为最终的产品,又可以作为产品的牺牲模具。
可见微电铸技术是LIGA工艺中非常重要的一个环节。
对于金属电铸工艺可包括无电解电铸和电解电铸两种。
无电解电铸就是靠化学方法连续淀积厚金属,而不加电压也没有消耗基片,它最重要的一点是采用充分的氧化反应代替点解电铸中的基片溶解。
电解电铸是自我限制的,而无电解电铸不是自我限制的。
对于无电解电铸镍来说,镍离子的减少是靠次磷酸盐的氧化反应来补充的。
反应一直进行,直到溶液中的次磷酸盐耗尽为止。
在电解电铸中,只要当整个基片表面覆盖了镍以后就会停止。
大量的氢生成会破坏电铸金属膜的质量,因此必须避免。
氢生成速度与电铸金属膜的速度没有直接关系,而主要取决于还原剂分子。
在无电解电铸中,电铸可能是在容器壁上在某个时刻自发开始,因此需要稳定剂来稳定溶液。
1 微电铸原理的特点微电铸的要素包括阳极、阴极、电源、电解液以及待镀工件模具等,其中待镀工件模具作为阴极,电铸是一种特殊形式的电镀。
希望沉积的金属离子包含在电解液中,当电解发生时,在阴极的工件模具表面会沉积金属离子,随着金属离子沉积在阴极,阳极金属会发生溶解反应补偿电解液中金属离子的减少。
经过表面工艺处理的成型工件作为电铸模具,可以得到合适的镀件并能保证镀件和模具容易分离。
微电铸工艺

微电铸的工艺参数等探究0 前言微电铸工艺(microelect roforming technology) 是在传统电铸工艺的基础上建立起来的新概念,具有微小结构成型、复杂结构成型、高精度和批量生产等突出优点,它既可以看作是在微细加工模具基础上的传统电铸技术的延伸,也可以认为是掩膜电镀在高深宽比方向发展的结果,微电铸工艺是LIGA/准LIGA 技术的核心内容,其中LIGA是德文Lithographie、Galvanoformung和Abformung三个词的缩写,是X射线深层光刻、微电铸和微复制工艺的完美结合,在MEMS技术领域有广泛应用[1]。
从本质上分析,LIGA/准LIGA工艺微电铸可以分为性质不同的两个阶段:第一阶段是在掩模微结构的深层填充金属;第二阶段是在整个光刻胶和金属结构表面沉积厚度为6-10mm的厚金属膜,以便加工成压铸膜的基座。
1 微电铸工艺的研究进展与趋势对微电铸工艺的技术难点,研究人员在理论分析的基础上,从微电铸过程的数值模拟和工作参数试验优化等方面开展工作,探索微电铸的内在规律,取得了一系列进展,形成一些有重要参考价值的工作规范和指导意见,有力的促进了微电铸技术在MEMS领域的广泛应用[2]。
首先,基于高深宽比掩膜微结构是微电铸工艺关键影响因素的认识,建立了能够体现高深宽比微区传质特征的电极界面模型。
在微流体运动中引入高深宽比结构因素,建立了能够体现高深宽比微结构对界面稳定层增厚产生影响的电极界面物理模型。
其次,通过数值解析,系统分析一般镀液体系典型结构中电流密度再分布的规律。
如果待镀微区的开口尺寸较大,也就是掩膜微结构深宽比较小,则微电铸电流在沉积区域的再分布并不充分,靠近掩膜边缘的电流密度将显著高于中心部位,形成边缘高而中间低的马鞍型厚度分布这是掩膜电镀体系中常见的厚度分布样式。
如果待镀微区开口较小,也就是高深宽比微结构掩膜存在的情形,则在进入掩膜开口区域之后,电流密度将在传质阻力的作用下实现充分再分布,形成中间部分电流密度较大,整体镀层厚度比较均匀的理想结果。
电液控制技术的现状和发展趋势
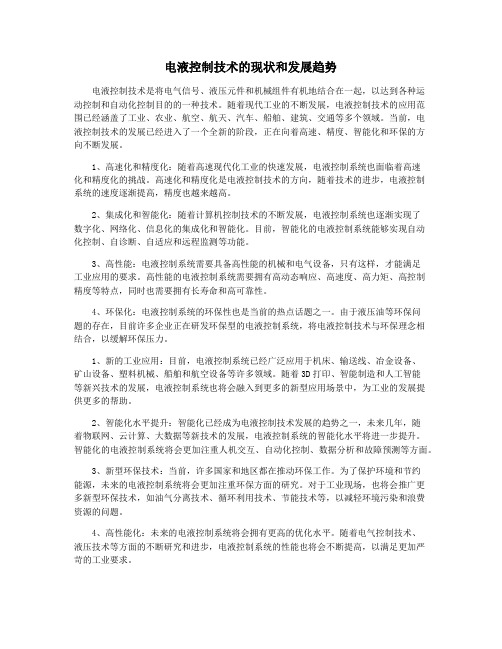
电液控制技术的现状和发展趋势电液控制技术是将电气信号、液压元件和机械组件有机地结合在一起,以达到各种运动控制和自动化控制目的的一种技术。
随着现代工业的不断发展,电液控制技术的应用范围已经涵盖了工业、农业、航空、航天、汽车、船舶、建筑、交通等多个领域。
当前,电液控制技术的发展已经进入了一个全新的阶段,正在向着高速、精度、智能化和环保的方向不断发展。
1、高速化和精度化:随着高速现代化工业的快速发展,电液控制系统也面临着高速化和精度化的挑战。
高速化和精度化是电液控制技术的方向,随着技术的进步,电液控制系统的速度逐渐提高,精度也越来越高。
2、集成化和智能化:随着计算机控制技术的不断发展,电液控制系统也逐渐实现了数字化、网络化、信息化的集成化和智能化。
目前,智能化的电液控制系统能够实现自动化控制、自诊断、自适应和远程监测等功能。
3、高性能:电液控制系统需要具备高性能的机械和电气设备,只有这样,才能满足工业应用的要求。
高性能的电液控制系统需要拥有高动态响应、高速度、高力矩、高控制精度等特点,同时也需要拥有长寿命和高可靠性。
4、环保化:电液控制系统的环保性也是当前的热点话题之一。
由于液压油等环保问题的存在,目前许多企业正在研发环保型的电液控制系统,将电液控制技术与环保理念相结合,以缓解环保压力。
1、新的工业应用:目前,电液控制系统已经广泛应用于机床、输送线、冶金设备、矿山设备、塑料机械、船舶和航空设备等许多领域。
随着3D打印、智能制造和人工智能等新兴技术的发展,电液控制系统也将会融入到更多的新型应用场景中,为工业的发展提供更多的帮助。
2、智能化水平提升:智能化已经成为电液控制技术发展的趋势之一,未来几年,随着物联网、云计算、大数据等新技术的发展,电液控制系统的智能化水平将进一步提升。
智能化的电液控制系统将会更加注重人机交互、自动化控制、数据分析和故障预测等方面。
3、新型环保技术:当前,许多国家和地区都在推动环保工作。
电铸技术的发展和应用综述

电铸技术的发展和应用综述章勇【摘要】电铸技术是一种精密特种加工技术,凭借其工艺的特殊性,在很多行业有着广泛的应用.对电铸技术的发展历史及电铸技术在特殊结构件、微细结构件和大型结构件三个方面的应用进行综述,并阐述了电铸技术的研究现状.【期刊名称】《沙洲职业工学院学报》【年(卷),期】2017(020)002【总页数】4页(P1-4)【关键词】电铸;微细;精密;结构件【作者】章勇【作者单位】沙洲职业工学院,江苏张家港215600【正文语种】中文【中图分类】TG249电铸是一种电化学加工方法,它是利用金属离子在阴极表面电沉积的原理进行零件的成型。
目前,电铸技术主要用于航空航天、精密模具、特殊结构件等行业。
与传统的金属成型工艺和其它精密加工技术相比,电铸技术具有复制能力强、重复精度高、适用范围广和电铸零件的材料性能可控性强等独特的优点[1-2]。
电铸工艺的发展首先体现在电铸层的材料成分上,其发展历程可分为单金属电铸、合金电铸和复合材料电铸三个阶段,但这三个阶段并无明显的界限,且在现阶段仍在共同发展。
对于单金属电铸工艺而言,电铸中应用最广泛的金属有铜和镍。
其中,电铸铜主要用于对导热要求高的工艺结构件,且由于其具有良好的塑性和导电性,常用于铜箔、印刷电路板、波导管、电火花电极等,有时也用于电铸镍的打底层。
与电铸铜相比,电铸镍具有较高的强度、硬度和耐腐蚀性,常用于工程结构件,电铸镍的厚度可达数十毫米,可用于某些特殊的产品中,如用于核反应堆的无缝电铸镍管、液体火箭发动机推力室身部等[3]。
随着电铸应用领域的不断拓展,有限的单金属电铸材料已难以满足科技发展的需要。
因此研究者们从19世纪末就开始进行合金电铸的研究,但一直到20世纪60年代中期,才由W.Stephenson等人成功开发出了镍锰合金电铸技术,从而掀起了合金电铸的新高潮。
目前,研究最多的合金电铸主要是以铁族金属为主体,在其中掺杂其它金属,如Ni-Co合金、Ni-Mn合金和Ni-Fe合金等[4-7]。
铸造技术的发展现状与前景探究

铸造技术的发展现状与前景探究铸造技术是一种广泛应用的金属加工工艺,其发展对于工业生产具有重要意义。
随着现代制造业的不断发展和需求的不断增加,铸造技术也得到了迅速的发展并取得了较大的成就。
本文将对铸造技术的发展现状进行探究,并展望其未来的发展前景。
一、铸造技术的发展现状1. 传统铸造技术传统铸造技术主要包括砂型铸造、金属型铸造、压力铸造等。
这些技术在工业生产中应用广泛,具有成本低、工艺简单等优点。
但是传统铸造技术也存在一些问题,如生产效率低、能源消耗大、材料利用率低等,不能完全满足现代工业对高质量、高效率、节能环保的需求。
随着科技的不断进步,先进铸造技术不断涌现,如精密铸造技术、数字化铸造技术、快速凝固铸造技术等。
这些新技术在提高铸造件的精度、降低能耗、改善材料利用率等方面具有明显优势。
先进铸造技术也在发展中遇到了一些挑战,例如技术成熟度不高、设备投资大等问题,需要不断进行技术改进和创新。
随着人工智能、大数据、云计算等技术的不断发展,智能化铸造技术也逐渐走进人们的视野。
智能化铸造技术通过智能装备、智能控制系统等手段,实现铸造过程的自动化、智能化,极大地提高了生产效率和产品质量,降低了生产成本。
智能化铸造技术的发展将有效推动铸造行业向数字化、智能化方向转变。
数字化铸造技术是近年来的热门发展方向,它通过数字化建模、仿真分析等手段,对铸造过程进行全面监控和优化。
数字化铸造技术的发展将引领铸造行业向数字化制造方向转变,实现生产智能化、灵活化、高效化。
2. 绿色铸造技术的推广随着环保意识的增强,绿色铸造技术也受到了越来越多的关注。
各种新型的绿色铸造材料和清洁生产技术不断涌现,有力地推动了铸造行业向绿色化转型。
绿色铸造技术的发展将有效解决传统铸造技术存在的环境污染和资源浪费等问题。
3. 智能化铸造技术的应用铸造技术发展现状良好,同时面临的挑战和机遇也在不断增加。
只有不断进行技术创新和提高,才能更好地满足现代制造业对高质量、高效率、节能环保的需求,铸造技术必将迎来更加美好的未来。
微电铸工艺

微电铸的工艺参数等探究0 前言微电铸工艺(microelect roforming technology) 是在传统电铸工艺的基础上建立起来的新概念,具有微小结构成型、复杂结构成型、高精度和批量生产等突出优点,它既可以看作是在微细加工模具基础上的传统电铸技术的延伸,也可以认为是掩膜电镀在高深宽比方向发展的结果,微电铸工艺是LIGA/准LIGA 技术的核心内容,其中LIGA是德文Lithographie、Galvanoformung和Abformung三个词的缩写,是X射线深层光刻、微电铸和微复制工艺的完美结合,在MEMS技术领域有广泛应用[1]。
从本质上分析,LIGA/准LIGA工艺微电铸可以分为性质不同的两个阶段:第一阶段是在掩模微结构的深层填充金属;第二阶段是在整个光刻胶和金属结构表面沉积厚度为6-10mm的厚金属膜,以便加工成压铸膜的基座。
1 微电铸工艺的研究进展与趋势对微电铸工艺的技术难点,研究人员在理论分析的基础上,从微电铸过程的数值模拟和工作参数试验优化等方面开展工作,探索微电铸的内在规律,取得了一系列进展,形成一些有重要参考价值的工作规范和指导意见,有力的促进了微电铸技术在MEMS领域的广泛应用[2]。
首先,基于高深宽比掩膜微结构是微电铸工艺关键影响因素的认识,建立了能够体现高深宽比微区传质特征的电极界面模型。
在微流体运动中引入高深宽比结构因素,建立了能够体现高深宽比微结构对界面稳定层增厚产生影响的电极界面物理模型。
其次,通过数值解析,系统分析一般镀液体系典型结构中电流密度再分布的规律。
如果待镀微区的开口尺寸较大,也就是掩膜微结构深宽比较小,则微电铸电流在沉积区域的再分布并不充分,靠近掩膜边缘的电流密度将显著高于中心部位,形成边缘高而中间低的马鞍型厚度分布这是掩膜电镀体系中常见的厚度分布样式。
如果待镀微区开口较小,也就是高深宽比微结构掩膜存在的情形,则在进入掩膜开口区域之后,电流密度将在传质阻力的作用下实现充分再分布,形成中间部分电流密度较大,整体镀层厚度比较均匀的理想结果。
电铸技术的应用与发展趋势
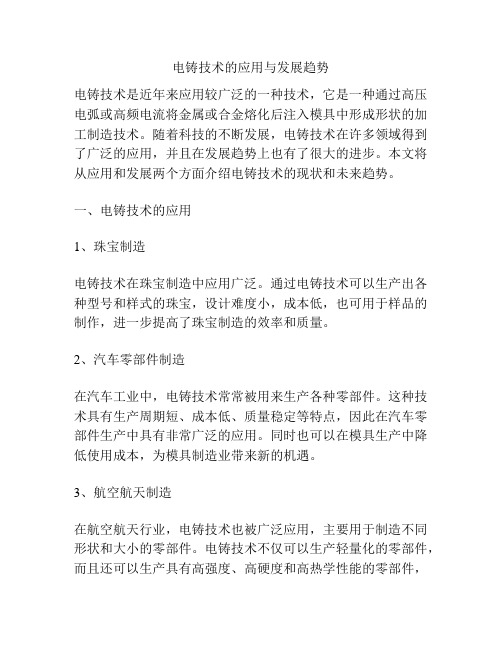
电铸技术的应用与发展趋势电铸技术是近年来应用较广泛的一种技术,它是一种通过高压电弧或高频电流将金属或合金熔化后注入模具中形成形状的加工制造技术。
随着科技的不断发展,电铸技术在许多领域得到了广泛的应用,并且在发展趋势上也有了很大的进步。
本文将从应用和发展两个方面介绍电铸技术的现状和未来趋势。
一、电铸技术的应用1、珠宝制造电铸技术在珠宝制造中应用广泛。
通过电铸技术可以生产出各种型号和样式的珠宝,设计难度小,成本低,也可用于样品的制作,进一步提高了珠宝制造的效率和质量。
2、汽车零部件制造在汽车工业中,电铸技术常常被用来生产各种零部件。
这种技术具有生产周期短、成本低、质量稳定等特点,因此在汽车零部件生产中具有非常广泛的应用。
同时也可以在模具生产中降低使用成本,为模具制造业带来新的机遇。
3、航空航天制造在航空航天行业,电铸技术也被广泛应用,主要用于制造不同形状和大小的零部件。
电铸技术不仅可以生产轻量化的零部件,而且还可以生产具有高强度、高硬度和高热学性能的零部件,大大提高了航空航天产品的性能和使用寿命。
二、电铸技术的发展趋势1、自动化与智能化发展随着社会自动化和智能化的趋势,电铸技术也将朝着自动化和智能化的方向发展。
通过与其他先进技术的结合,未来的电铸技术将实现自动化生产,提高生产效率,降低生产成本。
2、高性能金属材料的研发与应用随着科技的发展,新型材料的研究和应用已成为电铸技术发展的重要方向。
未来电铸技术将广泛应用于生产各种高性能金属材料,如合金、钛合金、耐热合金等,为工业、航空航天和军事等领域的发展提供了新的机遇。
3、环保技术的渗透未来电铸技术的发展不仅要考虑产量和生产效率的提高,更要关注其对环境的保护。
随着环保意识的增强,电铸技术将采用更环保的生产过程,提高产品的环境可持续性,这也是电铸技术未来发展的必然趋势。
综上所述,电铸技术在各个领域的应用已经越来越广泛,未来发展的趋势也呈现出自动化、智能化、高性能金属材料研发和应用以及环保技术渗透等特点,这些趋势将进一步推动电铸技术的发展和创新。
电铸技术的应用与发展趋势
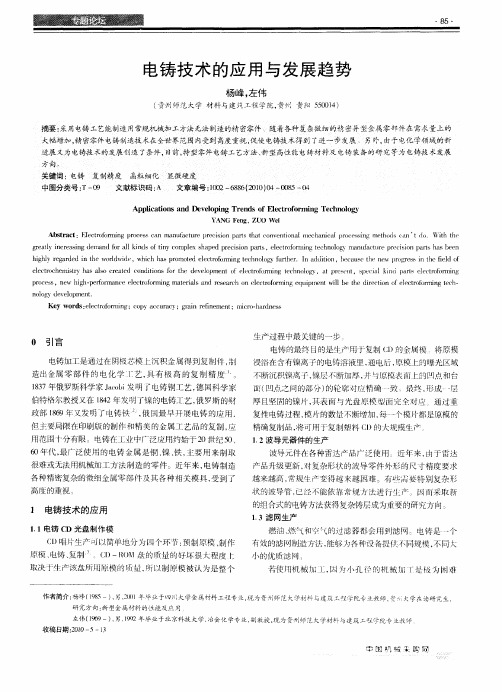
YANG e g,ZUO W e F n i
Ab t a t lc rtr n rc s a n fc ue prcso a t h tc n e to a c a i a r c si g meh dsc n’ o W ih t e sr c :E e tobmi g p o e sc n ma u a t r e iin p rst a o v nin lme h nc lp o esn t o a td . t h
Ke r y wo ds:lcrt mig;c p c ua !;g an r f me t ee toor n o ya c rc, r i e ne n ;mir — adn s i coh r es
.
0 引言
电铸加工是通过在 阴极芯模上沉 积金属得到 复制件 , 制 造出金属零 部 件 的 电化 学 艺 , 有 极 高 的 复制 精 度 。 具 13 年俄罗斯科学 家 Jcb 发明 r电铸铜工 艺, 87 ao i 德国科学家 伯特格尔教授 又在 14 82年发 日了镍 的电铸工艺 , 月 俄罗斯的财
,
prc s o e s.ne h g p ro na c lcr fr n trasa d r sa c I ee toomi ge u p ntw l b h rcin 0 lcrtr n e h w ih— efn F e ee toomi g maei l n e e rh O l lcr fr n q i me il e t edie to fee tob mig tc — l n l ̄ de eo me t oo vlp n.
中国铸造业的发展现状及方向综述
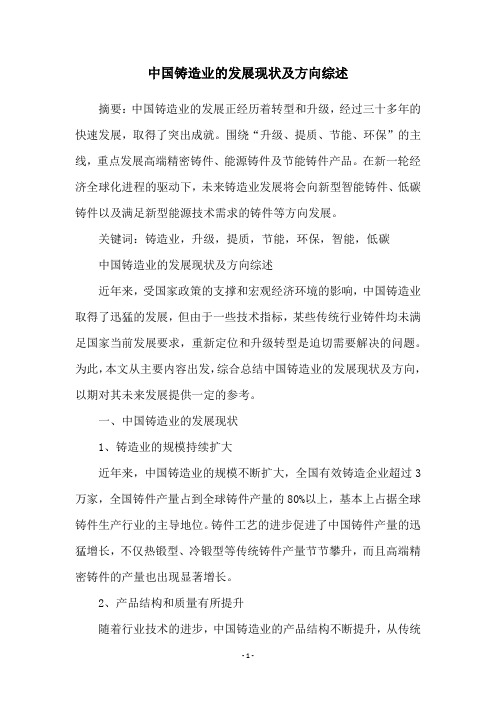
中国铸造业的发展现状及方向综述摘要:中国铸造业的发展正经历着转型和升级,经过三十多年的快速发展,取得了突出成就。
围绕“升级、提质、节能、环保”的主线,重点发展高端精密铸件、能源铸件及节能铸件产品。
在新一轮经济全球化进程的驱动下,未来铸造业发展将会向新型智能铸件、低碳铸件以及满足新型能源技术需求的铸件等方向发展。
关键词:铸造业,升级,提质,节能,环保,智能,低碳中国铸造业的发展现状及方向综述近年来,受国家政策的支撑和宏观经济环境的影响,中国铸造业取得了迅猛的发展,但由于一些技术指标,某些传统行业铸件均未满足国家当前发展要求,重新定位和升级转型是迫切需要解决的问题。
为此,本文从主要内容出发,综合总结中国铸造业的发展现状及方向,以期对其未来发展提供一定的参考。
一、中国铸造业的发展现状1、铸造业的规模持续扩大近年来,中国铸造业的规模不断扩大,全国有效铸造企业超过3万家,全国铸件产量占到全球铸件产量的80%以上,基本上占据全球铸件生产行业的主导地位。
铸件工艺的进步促进了中国铸件产量的迅猛增长,不仅热锻型、冷锻型等传统铸件产量节节攀升,而且高端精密铸件的产量也出现显著增长。
2、产品结构和质量有所提升随着行业技术的进步,中国铸造业的产品结构不断提升,从传统热锻型、冷锻型铸件向精密铸件的技术转变,从而拓宽了产品结构。
随着产品结构的拓宽,铸造产品的品质也有所改善,产品的表面粗糙度、砂浆量控制、质量检测等有所提升,使得产品铸件质量明显提高,从而满足了市场上不断提高的要求。
二、中国铸造业的未来发展方向在新一轮经济全球化进程的驱动下,中国铸造业的未来发展将会向一下几个方向发展:1、发展新型智能铸件智能铸件是当下和未来铸造业的发展趋势。
近年来,大量的智能铸件在国内外市场上得到大量应用,铸件的智能化程度不断提升,并对相关行业产生了重要影响。
发展智能铸件,可以有效地提高铸件的品质、增强铸件的抗腐蚀性与抗腐蚀性,从而提升铸件的性能和可靠性。
微电铸的工艺技术研究的开题报告

微电铸的工艺技术研究的开题报告一、选题背景和意义微电铸是一种基于微电子加工技术的微型铸造技术,可以制造出高精度、复杂形状、微小尺寸的金属零件。
其制造流程包括模具制备、金属熔化、注入模具、冷却固化和取出零件等环节,需要涉及多种工艺参数的控制以确保零件质量和生产效率。
在当前的现代化制造工业中,微电铸技术已得到广泛应用,尤其是在微机电系统、生物医学、航天航空等领域,并取得了显著的成果。
随着高新技术的不断发展,微电铸技术在未来的应用前景也十分广阔。
因此,对微电铸的工艺技术进行深入研究,对推动技术发展和产业升级都具有重要意义。
二、研究内容和研究方法本研究将针对微电铸的工艺技术进行系统研究,主要包括以下内容:(1)微电铸工艺参数的优化研究。
通过对微电铸工艺参数进行分析,结合数值模拟方法,探讨影响微电铸工艺质量的关键工艺参数及其优化控制策略。
(2)微电铸模具材料的研究。
针对微电铸模具材料的选择问题,进行材料性能测试,探究不同材料对微电铸工艺效果的影响,并提出优化措施。
(3)基于微电铸工艺的金属微零件制备。
研究微电铸工艺在制备金属微零件方面的应用,包括制备工艺流程和工艺控制方法等。
本研究将采用实验和数值模拟相结合的方法,通过实验对微电铸工艺参数和模具材料进行测试,分析实验结果并进行数值模拟分析,探讨微电铸工艺参数的优化策略。
同时,通过实际制备金属微零件,评价微电铸工艺在实际应用中的性能和效果。
三、预期成果和创新性本研究将达成以下预期成果:(1)通过对微电铸工艺参数的优化,实现微电铸工艺的质量控制和效率提高。
(2)针对微电铸模具材料问题,提出可行的优化选择方案。
(3)实现微电铸技术在制备金属微零件方面的应用,并获得具备市场竞争力的成果。
本研究的创新性在于,通过对微电铸工艺参数和模具材料的优化控制,提高微电铸工艺的质量和效率;同时,针对微电铸技术在金属微零件制备方面的应用进行实践,实现技术价值的体现。
这些成果将为微电铸技术的发展和产业升级提供新的思路和方法。
铸造现状与发展

铸造现状与发展随着现代工业的不断发展,铸造技术也在不断完善和进步,成为了制造业中不可或缺的一项技术。
铸造技术是一种将熔融金属或其他材料浇灌到模具中,经过冷却、凝固而形成所需要的物品的制造工艺。
目前铸造技术已经广泛应用于汽车、机械、航空、造船、电子、建筑等领域。
在行业中占有不可替代的地位。
目前,全球铸造业已形成了一定规模、有较完整的产业链和供应链、市场份额呈逐年扩大的趋势。
在 2021 年,世界铸造业的产值达到了 2500 亿美元的规模,预计到 2026年将达到 3000 亿美元。
中国是目前全球铸造行业的龙头,冶金铸造业现已成为中国的支柱产业。
铸造技术从传统的手工铸造到现代的机械化铸造、数字化铸造,其发展已经颇具里程碑意义。
技术进步明显提高了生产效率、产品质量和企业的竞争力。
自 20 世纪 70 年代以来,先进的 CAD/CAM/CAE 技术和计算机控制技术的广泛应用,加速了铸造技术的发展,优化了模具设计、模型制造、模铸工艺和铸造过程中关键参数的控制,提高了产品质量和良品率,降低了成本,并缩短了生产周期。
随着中国经济发展和产业结构调整,铸造行业也将迎来新的发展机遇。
国家政策的大力支持和企业的技术创新将会推动行业的健康发展。
未来,新能源汽车、航空航天、高速列车等领域将会对铸造行业带来更大的需求,同时,高效、环保、低碳的铸造技术也将成为未来世界铸造业的发展方向。
作为支撑制造业的重要一环,铸造行业面临着巨大的机遇和挑战。
在未来的发展中,铸造企业应在技术创新、质量控制、环保节能、产业链合作等方面加强合作,优化产品结构,提升品牌知名度,促进行业的成长和繁荣。
微电铸工艺—工艺参数

理工大学研究生试卷系别:机械工程学院课程名称微制造与微机械电子系统学号:姓名:考试时间:2013年1 月15 日微电铸工艺—工艺参数(理工大学机械工程学院116024)摘要:随着MEMS和LIGA两种技术的发展,微电铸工艺以其独特的优势,受到越来越多的关注。
本文介绍了微电铸的基本原理和特点及其一些研究现状和发展趋势。
文中着重强调了微电铸工艺的工艺参数,如电源波形,PH值,阴极电流密度,空气搅拌,电解液温度等。
以及研究人员为了得到更好的铸层效果,对其工艺参数进行优化所取得的成就,体现在气孔问题的解决,残余应力的消除,镀层不均的改善等。
关键词:微细加工微电铸工艺参数Micro-lectroforming Technology—Process Parameters (Dalian University of Technology,Department of Mechanical Engineering, DaLian 116024)Abstract:With the development of the technology of MEMS and LIGA, Micro-electroforming technology with its unique advantagesis inducing more and more attention.This Paper mainly introduced the fundamental and characteristics of micro-electroforming, and its some research and development trends. The article emphasized the process parameters of the micro -electroforming technology, including Power waveform,PH value,cathode current density, stirring,temperature of electrolyte and so on.As well as in order to get a better cast layer,researchers optimize the process parameters to obtain achievements,including the solution of the problem to hole,the elimination of residual internal stress,the improvement of poor evenness and so on.Key words: Micro-fabrication Micro—electroforming Process parameters0 前言微电铸工艺(Micro Electroforming Technology)是随着MEMS技术的快速发展,在继承传统电铸工艺特点的基础上,形成是一种非硅基微细结构加工的重要精密电铸技术,广泛用于MEMS技术领域[1]。
铸造技术的发展现状与前景探究

铸造技术的发展现状与前景探究铸造技术是一项古老而重要的制造工艺,广泛应用于各个工业领域。
随着科技的进步和需求的增加,铸造技术也在不断发展,不断涌现出新的成果和应用。
本文将探究铸造技术的现状和前景,并对其未来的发展进行展望。
1.1 传统铸造技术传统铸造技术是指基于传统模具和工艺的铸造过程。
它使用沙土、石膏等材料作为模具,在模具中注入熔融金属或合金,经过冷却后取出成品。
传统铸造技术简单、成本低,广泛应用于冶金、机械、汽车等行业。
随着科技的进步,先进铸造技术不断涌现。
其中包括精密铸造技术、快速凝固铸造技术、数字化铸造技术等。
精密铸造技术利用先进的模具制造技术和精确的铸造工艺,生产出高精度、高质量的铸件。
快速凝固铸造技术通过控制金属凝固速度,优化铸件的内部结构,提高铸件的性能。
数字化铸造技术利用计算机辅助设计和制造技术,实现铸件的快速设计和生产。
智能化铸造技术是指运用传感器、自动化控制和人工智能等技术,实现铸造过程的自动化和智能化。
智能化铸造技术可以提高生产效率和产品质量,减少人工操作和能源消耗。
目前,智能化铸造技术已经在一些大型铸造企业得到应用,并取得了良好的效果。
2.1 优化设计和模拟仿真随着计算机技术的发展,优化设计和模拟仿真技术在铸造领域的应用越来越广泛。
优化设计和模拟仿真可以通过数学模型和仿真软件,对铸件的几何形状、工艺参数等进行优化和模拟。
这将大大提高铸造过程的效率和产品的质量,降低成本和能源消耗。
2.2 精密铸造和材料创新精密铸造技术可以生产出高精度、高质量的铸件,广泛应用于航空、航天等高端领域。
随着科技的进步,新型材料不断涌现,对铸造技术提出了更高的要求。
材料创新和精密铸造技术的结合,将推动铸造技术的进一步发展。
2.3 绿色铸造和资源循环利用绿色铸造是指在铸造过程中减少环境污染和资源浪费的铸造技术。
绿色铸造技术可以通过节能、减排等手段,降低能源消耗和环境污染。
铸造过程中产生的废料和废渣可以通过资源循环利用进行再生利用。
电液控制技术现状及发展趋势
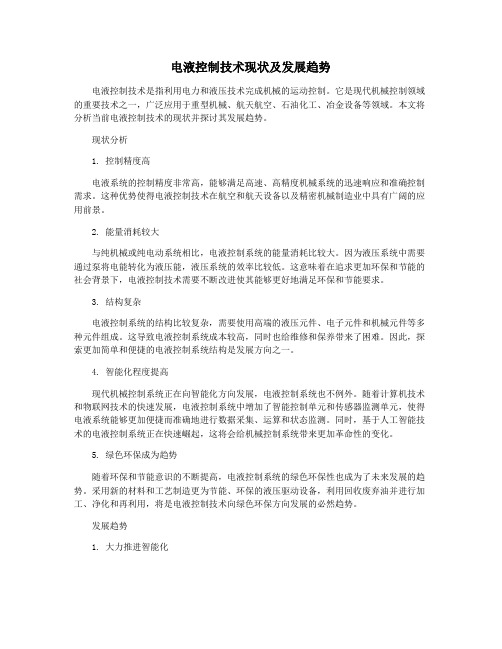
电液控制技术现状及发展趋势电液控制技术是指利用电力和液压技术完成机械的运动控制。
它是现代机械控制领域的重要技术之一,广泛应用于重型机械、航天航空、石油化工、冶金设备等领域。
本文将分析当前电液控制技术的现状并探讨其发展趋势。
现状分析1. 控制精度高电液系统的控制精度非常高,能够满足高速、高精度机械系统的迅速响应和准确控制需求。
这种优势使得电液控制技术在航空和航天设备以及精密机械制造业中具有广阔的应用前景。
2. 能量消耗较大与纯机械或纯电动系统相比,电液控制系统的能量消耗比较大。
因为液压系统中需要通过泵将电能转化为液压能,液压系统的效率比较低。
这意味着在追求更加环保和节能的社会背景下,电液控制技术需要不断改进使其能够更好地满足环保和节能要求。
3. 结构复杂电液控制系统的结构比较复杂,需要使用高端的液压元件、电子元件和机械元件等多种元件组成。
这导致电液控制系统成本较高,同时也给维修和保养带来了困难。
因此,探索更加简单和便捷的电液控制系统结构是发展方向之一。
4. 智能化程度提高现代机械控制系统正在向智能化方向发展,电液控制系统也不例外。
随着计算机技术和物联网技术的快速发展,电液控制系统中增加了智能控制单元和传感器监测单元,使得电液系统能够更加便捷而准确地进行数据采集、运算和状态监测。
同时,基于人工智能技术的电液控制系统正在快速崛起,这将会给机械控制系统带来更加革命性的变化。
5. 绿色环保成为趋势随着环保和节能意识的不断提高,电液控制系统的绿色环保性也成为了未来发展的趋势。
采用新的材料和工艺制造更为节能、环保的液压驱动设备,利用回收废弃油并进行加工、净化和再利用,将是电液控制技术向绿色环保方向发展的必然趋势。
发展趋势1. 大力推进智能化电液控制系统的智能化程度将会逐步提高。
未来,电液控制系统将会向着自主学习、自我优化、智能预测的方向发展。
相信不远的将来,电液控制技术将会与物联网技术、云计算等技术深度结合,形成更加强大的系统。
铸造技术的发展现状与前景探究

铸造技术的发展现状与前景探究铸造技术是一种利用熔融金属或合金借助模具来制造金属零件的方法,是制造工业中最重要、最基础的工艺之一。
随着现代制造技术的不断发展,铸造技术也在不断创新与改进,取得了一系列重大突破与进展,拓宽了应用领域,具有广阔的发展前景。
铸造技术的发展现状主要体现在以下几个方面:1. 材料的创新:过去,铸造只能用于一些低熔点材料的制造,如铁、铜等。
而现在,随着高温合金和精细合金的研发,铸造技术可以应用于更具挑战性的材料,如钛合金、高温合金等。
2. 工艺的改进:传统的铸造工艺存在一些问题,如缺陷率高、尺寸难控制等。
针对这些问题,工程师们通过改良模具设计、优化熔炼与浇注工艺等手段,大幅度提高了产质量与生产效率。
3. 数字化技术的应用:随着计算机技术的飞速发展,数字化铸造技术(Digital Casting)逐渐成为现代铸造技术的重要组成部分。
通过数字化仿真、虚拟实验等手段,可以在减少试验成本的预测产品形态与性能,提高生产效率。
1. 3D打印技术与铸造的结合:3D打印技术的出现为铸造技术带来了巨大的变革。
通过3D打印技术,可以直接生产出复杂形状的铸造模具,并且可以根据需要调整材料的组成,提高产品性能。
3D打印技术与传统铸造技术的结合,将进一步提高产品的准确性和复杂性。
2. 精密铸造技术的发展:精密铸造技术是近年来铸造技术的研究热点之一。
通过优化模具设计、改善熔炼工艺等手段,可以制造出更精密、更高质量的铸件。
精密铸造技术的发展,将推动铸造工艺向更高端领域发展。
3. 轻质化材料的应用:在航空航天、汽车等领域,轻质化材料的需求越来越大。
铸造技术在制造轻质材料零件方面具有独特的优势。
随着轻质材料的不断研发,铸造技术将在这些领域发挥重要作用。
4. 绿色、环保铸造技术的发展:传统铸造工艺中,燃煤熔炼与浇注过程会产生大量的废气、废渣和废水,对环境造成污染。
绿色、环保铸造技术的研发势在必行。
随着环保意识的提高,绿色铸造技术将成为未来铸造行业的发展方向。
电铸技术的发展历程

电铸技术的发展历程电铸技术是一种利用电磁力将液态金属注入模具进行成型的金属加工方法,它具有高效、精确、可重复性好等优点。
在电铸技术的发展历程中,经历了以下几个重要的阶段:第一阶段是19世纪末到20世纪初,电铸技术的雏形开始出现。
当时,人们开始尝试利用电磁力将熔融金属注入模具中,以实现金属的快速成型。
这一阶段的电铸技术主要还停留在实验室研究阶段,尚未形成实际应用。
第二阶段出现在20世纪20年代至30年代,这个阶段主要是有关电铸技术的基础研究和理论探索。
研究人员开始深入研究电流密度、磁场分布等关键参数对电铸过程的影响,并且开始尝试探索电铸工艺参数的优化方法。
这一阶段的研究奠定了电铸技术后续发展的基础。
第三阶段发生在20世纪40年代至50年代,这个阶段电铸技术开始逐渐应用于实际生产中。
在第二次世界大战期间,电铸技术在武器、航空航天等领域得到了广泛应用,为相关行业的发展做出了重要贡献。
电铸工艺在这个阶段得到了进一步改进和提高,实现了更加精确的成型。
第四阶段出现在20世纪60年代至70年代,这个阶段电铸技术开始进入工业化生产阶段。
随着电子技术的快速发展,电铸设备得到了改善和升级,大大提高了生产效率和质量。
此外,电铸材料的研究和开发也逐渐得到加强,为电铸技术的广泛应用提供了更多可能性。
第五阶段出现在20世纪80年代至今,这个阶段电铸技术进一步发展成熟并得到了广泛应用。
电铸技术在汽车制造、电子设备、医疗器械、航空航天等领域发挥了重要作用。
同时,电铸技术在工艺参数控制、模具制造、材料选择等方面也有了更深入的研究,为实现更高质量、更高效率的电铸成型提供了支持和保障。
总的来说,电铸技术经历了从雏形到发展成熟的历程,不断得到改进和提高。
随着科技的不断进步和应用的不断拓展,电铸技术在各个领域具有广阔的应用前景。
电铸工艺与电铸产品开发-202416
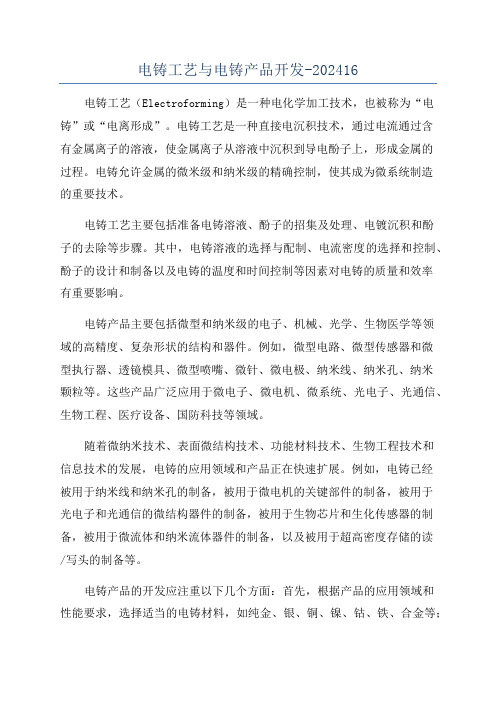
电铸工艺与电铸产品开发-202416电铸工艺(Electroforming)是一种电化学加工技术,也被称为“电铸”或“电离形成”。
电铸工艺是一种直接电沉积技术,通过电流通过含有金属离子的溶液,使金属离子从溶液中沉积到导电酚子上,形成金属的过程。
电铸允许金属的微米级和纳米级的精确控制,使其成为微系统制造的重要技术。
电铸工艺主要包括准备电铸溶液、酚子的招集及处理、电镀沉积和酚子的去除等步骤。
其中,电铸溶液的选择与配制、电流密度的选择和控制、酚子的设计和制备以及电铸的温度和时间控制等因素对电铸的质量和效率有重要影响。
电铸产品主要包括微型和纳米级的电子、机械、光学、生物医学等领域的高精度、复杂形状的结构和器件。
例如,微型电路、微型传感器和微型执行器、透镜模具、微型喷嘴、微针、微电极、纳米线、纳米孔、纳米颗粒等。
这些产品广泛应用于微电子、微电机、微系统、光电子、光通信、生物工程、医疗设备、国防科技等领域。
随着微纳米技术、表面微结构技术、功能材料技术、生物工程技术和信息技术的发展,电铸的应用领域和产品正在快速扩展。
例如,电铸已经被用于纳米线和纳米孔的制备,被用于微电机的关键部件的制备,被用于光电子和光通信的微结构器件的制备,被用于生物芯片和生化传感器的制备,被用于微流体和纳米流体器件的制备,以及被用于超高密度存储的读/写头的制备等。
电铸产品的开发应注重以下几个方面:首先,根据产品的应用领域和性能要求,选择适当的电铸材料,如纯金、银、铜、镍、钴、铁、合金等;其次,根据产品的尺寸和形状复杂度,设计适当的酚子,如光刻酚子、电化学刻蚀酚子、雕刻酚子、立体打印酚子等,以及相关的酚子招集和处理技术;第三,根据产品的精度要求,选择适当的电流密度和电镀时间,以及相关的电阻和电动势控制技术;最后,根据产品的质量和效率要求,优化电铸的温度、时间、溶液和酚子处理等工艺参数。
当前,电铸产品的开发面临着一些挑战,如增强电铸工艺的精度和效率,扩大电铸材料的种类和范围,优化电铸的工艺参数和设备,提高电铸产品的质量和稳定性,以及降低电铸的成本和环境影响等。
- 1、下载文档前请自行甄别文档内容的完整性,平台不提供额外的编辑、内容补充、找答案等附加服务。
- 2、"仅部分预览"的文档,不可在线预览部分如存在完整性等问题,可反馈申请退款(可完整预览的文档不适用该条件!)。
- 3、如文档侵犯您的权益,请联系客服反馈,我们会尽快为您处理(人工客服工作时间:9:00-18:30)。
微电铸中电铸液的发展现状和趋势摘要:本文首先阐述了微电铸技术的发展历史和现状,然后介绍了它的原理。
重点说明了电铸液的成分,最后介绍了微电铸未来的发展趋势。
关键词:微电铸;电铸液1.引言微电铸工艺(microelectroforming technology)是在传统电铸工艺的基础上建立起来的新概念,具有微小结构成型、复杂结构成型、高精度和批量生产等突出优点。
微电铸工艺是LIGA\UV-LIGA 技术的核心内容,在MEMS技术和微、纳米制造领域中有着良好的应用前景。
作为一种先进的制造技术,微电铸工艺主要用于制作各种精密、异型、复杂、微细等难以用传统加工方法制得的或加工成本很高的结构,适用于航空、航天、核工业、仪器仪表、微型机械等高新技术领域,并受到日益广泛的关注2.微电铸技术的发展历史1838年,苏联的耶可夫教授在石膏芯模上涂敷石蜡,通过石墨使其表面具有导电性,制成了电铸铜产品。
日本昭和初年,京都市工业研究所和大板造币司等单位就已积极开展了在石膏母型上铸铜、在绝缘体上电镀等方面的研究。
但是,早期由于电铸芯模的制作不仅制造技艺要求高、操作工艺繁琐,而且母型易破损,难以制出精致的复制品,所以电铸的应用范围十分有限。
20世纪中后期,随着电铸芯模材料的发展和制造技术的提高,电铸作为一项特种加工工艺方法,开始广泛应用于国民生产生活的各个方面,在欧美己用于制造火箭喷气发动机冷却室、太阳能储能飞轮,在日本用于汽车内饰件的制造,电子工业中印刷焊膏和胶粘剂模板。
国内的许多科研单位也对电铸工艺进行了大量的研究.较多应用于表面彤貌复杂的零件和各种模具的制造上。
微细电铸工艺随着MEMS工艺的发展而产生,在继承传统电铸工艺特点的同时,结合了集成电路加工工艺,受到了广泛的关注。
微细电铸技术与传统电铸技术有着相同的原理和相似的工艺过程,由于该项技术广泛用于制作微器件或者微结构,更多的涉及微米级尺度的问题,与传统大器件电铸有着显著的差别,对环境干扰有着更强的响应。
上世纪八十年代,德国卡尔斯鲁尔核研究中心发明了LIGA技术。
LIGA是德文Lithograpie,Oalvanoformung和Abformung三个词的缩写,是由X光深度光刻、微细电铸和微塑铸三个工艺组成的制造三维微器件的先进制造技术。
如图2.1所示,微细电铸技术是LIGA技术的重要核心内容,是LIGA研究人员的重要研究内容[1]。
ABB Corporate Research的Mathis等人,为了避免高温电铸液对PMMA微结构带来不必要的精度影响,对室温下的电铸进行了研究,对提高电铸精度具有重大意义[2]。
瑞士微纳米实验室的HeydennanL J等人将微细电铸技术与平板热压技术结合,实现了纳米级的结构制造[3]。
图2.1LIAG工艺流程示意图3.微电铸的基本原理电铸本质上是电镀的一种特殊形式 ,构成它的基本要素包括阳极、电解液、待镀工件模具(阴极)和电源。
然而作为工艺技术 ,电铸和电镀之间存在不少差异。
电镀是在物体表面沉积一层金属镀层 ,作为装饰或保护层 ,它一般不需要形成独立支撑结构 ,是对镀件的表面进行改性修饰的技术;而电铸则要求电沉积的金属最终能够形成独立的结构 ,按照一定的方式复制作为电镀起始物的模版 ,是一种加工制造新个体的工艺技术。
从工艺角度分析,电铸的镀层通常较厚。
一般电镀镀层厚度约在1~50μm之间,而电铸镀层厚度一般大于几十微米 ,甚至经常达到几毫米以上。
电铸形成的物件都能从基体上自然分离, 而电镀的镀层因是保护金属基体或作为装饰之用,所以镀层与阴极必须结合得很好, 以免剥落。
电铸件的自身性能与基体是无关的, 而电镀镀层的性能则与基体金属是互为补充的[4]。
如图3.1(a)所示,导电的原模为阴极用于电铸的金属材料为阳极。
电铸液中的金属离子种类与阳极金属相同。
在直流电的作用下。
阴附两极便发生电化学反应 ,即电铸液中的金属离子在阴极还原成金属,并沉积于原模表面;而阳极金属则不断地生成金属子溶解子电铸液中,使其金属离子的浓度保待不变#阴极原模上的电铸层逐渐增厚 ,直至达到加工要求为止。
铸件取出后,经脱模可获得与原模型面凹凸相反的产品。
图3.1(a)微电铸的原理示意图图3.1(b)微电铸实验单元4.微电铸的特点与传统金属成形工艺比较,电铸有其自身的独特优势。
通过电铸可以得到传统加工难以甚至不能制作的器件。
其优点主要如下[5]:(1) 尺寸精度高。
芯模加工成所需的尺寸精度后,电铸可以精确的加以复制,可以得到尺寸几乎完全相同的复制品,因此适于生产精度要求很高的工件。
(2) 芯模表面的精确复制。
电铸工艺能实现极高精度的表面细节复制,复制水平可以达到O.Olgm,具有高度的“逼真性",这是其他生产工艺难以媲美的;(3) 可以生产复杂形状器件。
可以将难以加工的内型面加工转化为外型面加工,例如特殊型面的波导管、气切割嘴、薄壁回转件的加工;(4) 可以调节沉积层的物理性质。
可以通过改变电铸条件,铸液成分等方法来调节金属电铸层的硬度、韧性和拉伸强度等机械力学性能;(5) 加工尺寸范围大。
电铸加工的尺寸范围一般只受电铸设备的限制。
一般的,产品尺寸可以从微观的毫微米级到宏观的大器件。
(6) 便于批量生产。
在一个电铸工序中,可以同时加工模具上的多种孔洞,减少了模具制作的循环周期。
芯模和电铸液均可以重复使用,因此器件加工时具有较好的重复性。
微细电铸(Micro—electroforming)是相对于常规的电铸技术而建立的新概念,它是针对微小结构(主要是微米/纳米尺度)加工技术。
与传统电铸工艺相比,微细电铸工艺的特点主要体现在以下几个方面[6]:(1) 铸件整体尺寸较小。
电沉积起始面处于同一平面,但是被电铸的不导电芯模分割成不同形状的微小区域,导致电铸过程中电流的分布存在不均匀现象;(2) 微电铸件表面分布的高深宽比光刻胶结构,构成了参与电沉积反应物质传输的严重障碍。
由于高深宽比微结构对溶液流动的屏蔽作用,搅拌所引起的对流难以到达电极反应发生的界面,致使电极反应界面上形成了厚度明显大于无遮挡表面的稳定扩散层,特别是在微孔和细缝区域,稳定扩散层的厚度与光刻胶厚度相当,远远大于无掩膜遮挡电极界面自然建立的微米级稳定层。
稳定扩散层内只能借助扩散和电迁移机制完成传质任务,并且主要是扩散过程,为此,必定要建立足够大的反应参与物质的浓度梯度和电场梯度,才能胜任有效输运反应成分的工作,而这将导致一系列不利影响:首先是反应界面的镀液组成显著偏离镀液本体,其偏离程度不但随电流密度和温度变化而异,而且不同的反应成分偏离程度也各不相同,因此,通过调整镀液校正上述偏离是非常困难的;其次,由于掩膜微结构形式多样性所造成的电极表面微区环境差异,将会导致不同电沉积区域稳定扩散层厚度的显著差异,从而使沉积速度、结晶习性和内应力出现差异,影响整体结构的一致性,然而掩膜微结构的差异往往是整体设计上所要求,因此这种差异也是无法完全弥补的。
(3) 微电铸工件所要填充的孔洞都是盲孔,镀液的浸润和完全填充需要谨慎对待,微电铸过程中析出的氢气需要设法予以排除。
开口很小的微细盲孔很难为普通电解液所填充,表面张力是主要原因,添加表面活性剂以降低电镀液的表面张力是解决问题的常用方法,但是有时仍然必须辅以机械震动或超声搅拌等辅助措施才能够使存于盲孔内的气体离开,这些都要在工艺设计中加以考虑[7]。
综合以上分析,微电铸不但兼有掩膜电镀和传统电铸两个方面的特征,而且还有其自身需要解决的独特技术问题,因此需要开展深入系统的工艺技术研究。
5.微电铸的电铸液5.1电铸液对电铸的影响按照电解液各种组分在电铸过程中所起的作用,可将电解液看成是由主盐、导电盐、缓冲剂、阳极活化物、络合剂、添加剂等组成。
对于电铸工艺来常需几十小时甚至更长时间,成分复杂,容易使电解液成分发生明显变化,从而增加溶液的维护难度。
所以,采用简单易维护的电解液配方是明智之举。
K. C. Chan 等在1997年对提高铸层均匀性方面进行了很多研究[8]。
在电解液方面,开展了添加剂和溶液成分的研究,在铜电铸实践中采用了高酸低铜配方,这一配方可较为显著地提高电解液分散能力。
在镍电铸中,现多采用分散能力强、应力低的氨基磺酸类溶液。
由于电铸镍的高精尖产品的需要,对电沉积镍层的性质,如镀层的内应力以及电解液的分散能力及深镀能力都提出了更高的要求。
目前电铸镍采用的电解液主要有瓦特型及氨基磺酸盐型两种。
瓦特型电解液的成本较低、易维护、操作简便,但镀层内应力较大;而氨基磺酸盐型电解液所得镀层内应力小,但电解液成本较高,对杂质敏感性强。
电解液的运动方式也影响电铸效果。
1982年,Kunieda 等首先开展了选择性喷射电沉积的实验研究,结果表明喷射电沉积能以高于常规电沉积的电流密度进行局部电沉积,但此实验中采用扫描的方式进行电沉积时,仅能获得点状的沉积薄层。
1997年, Kunieda 等的实验表明,在喷射电沉积的过程中,有规则地插入整平过程可提高沉积层的均匀性和稳定性[9]。
实验中生成了2 mm高的金属样件,但耗时高达20 h ,远谈不上快速制造。
Karakus 等则在实验中获得了0. 1μm 的结晶晶体[10]。
熊毅等实验研究结果表明,喷射电沉积的沉积速度可高达32μm/ min ,为常规电沉积速度的90 倍左右,沉积层的平均硬度可达552 HV ,高于常规200 HV 左右,沉积层晶体呈柱状生长,并在实验中获得了20~30 nm的镍结晶沉积层[11]。
5.2微电铸液的要求由于微电铸层厚,又有物理、机械性能要求,因而对微电铸溶液有一些的要求:1)沉积速度快:为了缩短微电铸时间,需要采用尽可能高的电流密度,来提高沉积速度,故要求溶液要能适应高速微电铸工艺的要求。
2)成分简单而且容易控制:由于铸层一般要求物理和机械性能,因而成分要力求简单,便于控制维护,以使所得的铸层保持稳定。
3)对溶液的纯度要求较高:由于微电铸层厚,各种无机、有机、机械杂质对铸层的影响tE较严重,故必须采用纯度高的微电铸液,并定期过滤和处理。
4)能得到均匀的铸层:高度均匀性是铸层的一项重要指标,故要尽可能选用均镀能力好的微电铸液。
5.3电铸液的主要成分[12](1)主盐目前可供电铸的金属与合金较有限。
最常用的金属有铜、镍、铁,合金有镍.钻及镍.铁合金。
在电铸技术中,电沉积镍获得了广泛的应用。
它具有良好的机械性能和高耐腐蚀性,同时在零度以下的温度条件下,其机械性能尚有所提高。
电沉积镍的性能具有宽幅的范围,例如沉积零件的硬度可达Hv200~750,强度可达340~1370MPa,相对伸长率为1.5~3%。
曾使用硫酸盐,而近几年来,愈来愈多地采用氨基磺酸盐作为电铸的主盐。