5 whys
精益生产名词解析:5why分析法
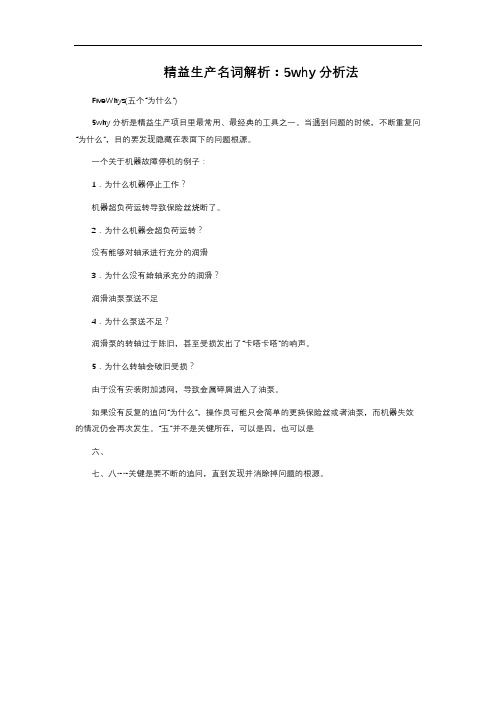
精益生产名词解析:5why分析法FiveWhys(五个“为什么”)
5why分析是精益生产项目里最常用、最经典的工具之一。
当遇到问题的时候,不断重复问“为什么”,目的要发现隐藏在表面下的问题根源。
一个关于机器故障停机的例子:
1.为什么机器停止工作?
机器超负荷运转导致保险丝烧断了。
2.为什么机器会超负荷运转?
没有能够对轴承进行充分的润滑
3.为什么没有给轴承充分的润滑?
润滑油泵泵送不足
4.为什么泵送不足?
润滑泵的转轴过于陈旧,甚至受损发出了“卡嗒卡嗒”的响声。
5.为什么转轴会破旧受损?
由于没有安装附加滤网,导致金属碎屑进入了油泵。
如果没有反复的追问“为什么”,操作员可能只会简单的更换保险丝或者油泵,而机器失效的情况仍会再次发生。
“五”并不是关键所在,可以是四,也可以是
六、
七、八……关键是要不断的追问,直到发现并消除掉问题的根源。
5 Whys Training(5Why 培训
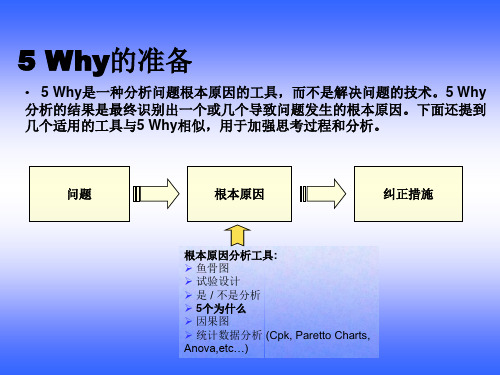
根本原因分析工具: 根本原因分析工具 鱼骨图 试验设计 是 / 不是分析 5个为什么 个为什么 因果图 统计数据分析 (Cpk, Paretto Charts, Anova,etc…)
Why的准备 5 Why的准备
• 任何 Why’s 必须同时考虑两个不同的问题。第一个是有关不良产品 任何5 必须同时考虑两个不同的问题。 的制造过程 (“为什么制造 为什么制造?”) 为什么制造 • 第二必须思考为什么监测系统未能在问题发生之前发现不良品。对不 第二必须思考为什么监测系统未能在问题发生之前发现不良品。 良品缺乏检验是监测系统问题,必须单独对待,而不是产品问题。 良品缺乏检验是监测系统问题,必须单独对待,而不是产品问题。 (“为什么没有发现 为什么没有发现?”) 为什么没有发现 • 即使被称为 个为什么,有时不需要达到5就可以找到问题的根本原因; 即使被称为5个为什么,有时不需要达到 就可以找到问题的根本原因 就可以找到问题的根本原因; 个为什么 又或者需要问超过5个为什么才能挖掘到问题根源 个为什么才能挖掘到问题根源。 又或者需要问超过 个为什么才能挖掘到问题根源。这要取决于过程 或问题本身的复杂性。 或问题本身的复杂性。 • 无论如何,依据经验来说通常需要问5个为什么,可以找到大多数问 无论如何,依据经验来说通常需要问 个为什么 个为什么, 题的根本原因。但不需要担忧是否超过或未达到这个数字。 题的根本原因。但不需要担忧是否超过或未达到这个数字。只是跟随 思考的过程来决定需要问几个为什么。 思考的过程来决定需要问几个为什么。
5 Why’s – 第3个 Why
•至此仍不能马上得到答案,应继续依循思考过程,即使一些潜在的根本 至此仍不能马上得到答案,应继续依循思考过程, 至此仍不能马上得到答案 原因已经浮出水面。 原因已经浮出水面。 •第3个为什么是在明显和不明显之间过渡的关键。前两个为什么使你聚 第 个为什么是在明显和不明显之间过渡的关键 个为什么是在明显和不明显之间过渡的关键。 焦在问题的发生,剩下的三个为什么将带你更深入的理解问题。 焦在问题的发生,剩下的三个为什么将带你更深入的理解问题。使产品 生产过程可视化(过程流程图)并锁定问题发生的最可能的根源。 生产过程可视化(过程流程图)并锁定问题发生的最可能的根源。 •你不需要同时回答所有的为什么,这是一个调查过程,有时需要你到现 你不需要同时回答所有的为什么,这是一个调查过程, 你不需要同时回答所有的为什么 场去观察可能最初就漏掉的事情。 场去观察可能最初就漏掉的事情。 •因为匆忙的看似“合理”的解释,你可能遗漏了很明显的东西。 因为匆忙的看似“合理”的解释,你可能遗漏了很明显的东西。 因为匆忙的看似
QC小组活动方法

QC小组活动方法为了提高团队协作能力和群体凝聚力,许多组织都会组织各种形式的团队活动。
在进行QC(质量控制)小组活动时,为了确保质量控制过程的顺利进行,需要选择合适的活动方法。
下面给出几种常见的QC小组活动方法。
1. 五个为什么(5 Whys)五个为什么是一种经典的QC工具,可以用于问题分析和根本原因追踪。
在QC小组活动中,可以使用五个为什么方法来鼓励小组成员进行深入分析和讨论,找到问题的根本原因。
这种方法可以帮助团队成员思考问题的深层次原因,进而提出有效的解决方案。
2. 核对表(Checklist)核对表是一种标准化工具,可以帮助QC小组完成一系列的检查工作。
在QC小组活动中,可以使用核对表来记录每个环节的检查情况和结果。
通过使用核对表,团队成员可以清晰地了解需要完成的任务和标准,提高工作的准确性和一致性。
3. PDCA环(PDCA Circle)PDCA环是质量管理中常用的一个概念,也可以应用于QC小组活动中。
PDCA环由计划(Plan)、执行(Do)、检查(Check)和行动(Action)四个环节组成。
在QC小组活动中,可以使用PDCA环来指导质量控制的整个过程。
团队成员可以先制定计划、实施计划、检查结果,然后根据检查结果进行调整和改进。
4. 魱原因分析(Fishbone Diagram)魱原因分析,也称为鱼骨图,是一种用于问题分析和根本原因追踪的工具。
在QC小组活动中,可以使用魱原因分析来帮助团队成员理清问题的各个方面和可能的原因。
通过使用魱原因分析,团队成员可以更好地理解问题的本质和影响因素,同时也能够更好地找到解决问题的方向。
5.分组讨论和分享分组讨论和分享是一种常见的QC小组活动方法。
团队成员可以根据自己的专业领域或感兴趣的话题,自由组成小组进行讨论和分享。
通过这种方式,团队成员可以互相学习、交流经验和知识,增进相互之间的了解和合作。
6.案例研讨案例研讨是一种体验式的学习方法,可以帮助团队成员更好地理解质量控制的实际应用。
什么是5Why分析法?(附案例)
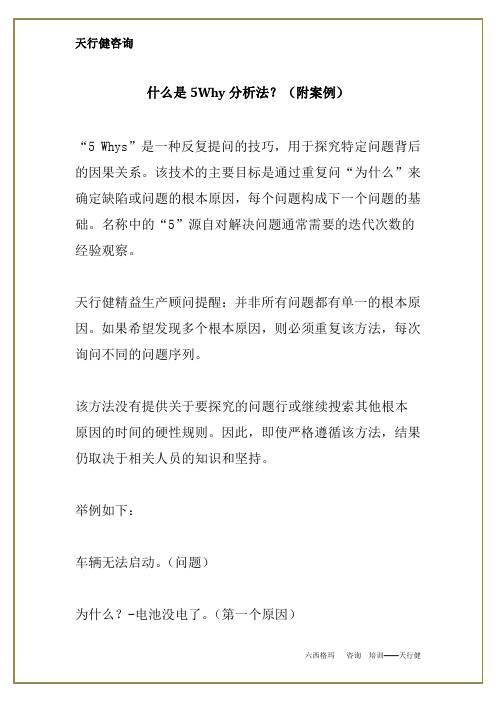
什么是5Why分析法?(附案例)
“5 Whys”是一种反复提问的技巧,用于探究特定问题背后的因果关系。
该技术的主要目标是通过重复问“为什么”来确定缺陷或问题的根本原因,每个问题构成下一个问题的基础。
名称中的“5”源自对解决问题通常需要的迭代次数的经验观察。
天行健精益生产顾问提醒:并非所有问题都有单一的根本原因。
如果希望发现多个根本原因,则必须重复该方法,每次询问不同的问题序列。
该方法没有提供关于要探究的问题行或继续搜索其他根本原因的时间的硬性规则。
因此,即使严格遵循该方法,结果仍取决于相关人员的知识和坚持。
举例如下:
车辆无法启动。
(问题)
为什么?-电池没电了。
(第一个原因)
为什么?-交流发电机不工作。
(第二个原因)
为什么?-交流发电机皮带断裂。
(第三个原因)
为什么?-交流发电机皮带已超过其使用寿命,未更换。
(第四个原因)
为什么?-车辆没有按照推荐的保养计划进行保养。
(第五个原因,根本原因)
这个例子的问题可以进一步深入到第六、第七或更高的层次,但五次反复询问原因通常足以找到根本原因。
关键是鼓励问题解决者避免假设和逻辑陷阱,而是以直接递增的方式追踪因果关系链,从效果到任何抽象层,再到与原始问题仍有一定联系的根本原因。
请注意,在本例中,第五个原因表明了一个中断的过程或一个可改变的行为,这表明达到了根本原因级别。
此外,在每个级别执行必要性和充分性的逻辑测试可以帮助避免选择虚假原因,并促进对多个根本原因的考虑。
五个为什麼(5 Whys)
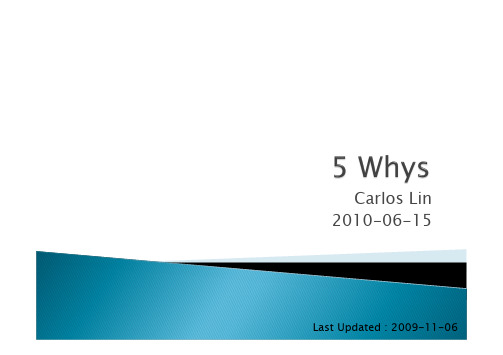
Carlos Lin 2010-06-15Last Updated : 2009-11-06❝ The 5 Whys was originally developed by Sakichi Toyoda( ) and was later used within Toyota Motor Corporation during the evolution of their manufacturing methodologies.❝ The 5 Whys is a critical component of problem solving training delivered as part of the induction into the Toyota Production System.❝ The 5 Whys has been widespread use beyond Toyota, and it now used within Kaizen, lean manufacturing, and Six Sigma.❝ The 5 Whys is a technique used in the Analyze phase of the Six Sigma DMAIC methodology.❝ It is a great Six Sigma tool that doesn’t involve data segmentation, hypothesis testing, regression or other advanced statistical tools.❝ In many cases can be completed without a data collection plan.❝ Help identify the root cause of a problem.❝ Determine the relationship between different root causes of a problem.❝ One of the simplest tools; easy to complete without statistical analysis.❝ When problems involve human factors or interactions.❝ In day-to-day business life; can be used within or without a Six Sigma project.1. Write down the specific problem.2. Ask Why the problem happens and write the answer down below the problem.3. If the answer you just provided doesn’t identify the root cause of the problem that you wrote down in step 1, ask again and write that answer down.4. Loop back to step 3 until the team is in agreement that the problem’s root cause is identified.“ ”,❝ If you don’t ask the right questions, you don’t get the right answers.❝ A question asked in the right way often points to its own answer.❝ Asking questions is the ABC of diagnosis. Only the inquiring mind solves problems.❝ T he 5 Whys is a question-asking method used to explore the cause/effect relationships underlying a particular problem.❝ U ltimately, the goal of applying the 5 Whys method is to determine a root cause of a defect or problem.。
5why分析法案例范文简单

5why分析法案例范文简单英文回答:5 Whys Analysis Case Study.Problem: A customer complains that their product is not working properly.Why 1: Why is the product not working properly?The product is not functioning because it has a faulty component.Why 2: Why does the product have a faulty component?The product has a faulty component because it was not assembled correctly.Why 3: Why was the product not assembled correctly?The product was not assembled correctly because the assembly line was not properly calibrated.Why 4: Why was the assembly line not properly calibrated?The assembly line was not properly calibrated because the maintenance team did not follow proper procedures.Why 5: Why did the maintenance team not follow proper procedures?The maintenance team did not follow proper procedures because they were not properly trained.Root Cause: The root cause of the customer's complaint is the lack of proper training for the maintenance team.Corrective Action: The corrective action is to provide proper training for the maintenance team to ensure that they follow proper assembly procedures.Preventive Action: The preventive action is to implement a quality control system to regularly check the assembly line to ensure that it is properly calibrated.中文回答:5 Why分析法案例分析。
五个为什么
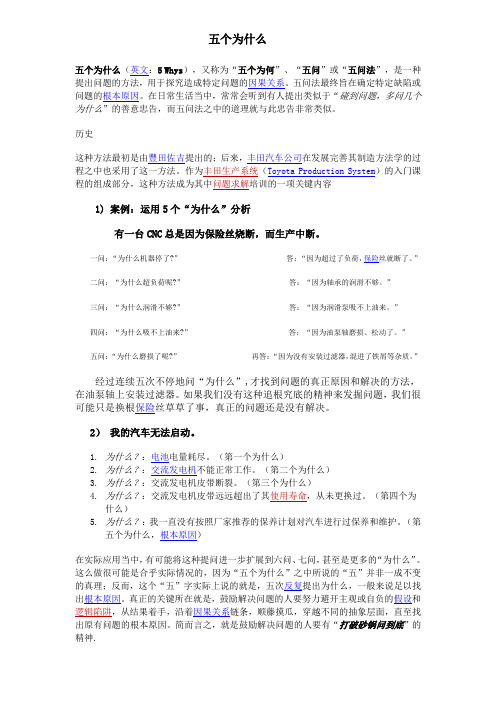
五个为什么五个为什么(英文:5 Whys),又称为“五个为何”、“五问”或“五问法”,是一种提出问题的方法,用于探究造成特定问题的因果关系。
五问法最终旨在确定特定缺陷或问题的根本原因。
在日常生活当中,常常会听到有人提出类似于“碰到问题,多问几个为什么”的善意忠告,而五问法之中的道理就与此忠告非常类似。
历史这种方法最初是由豐田佐吉提出的;后来,丰田汽车公司在发展完善其制造方法学的过程之中也采用了这一方法。
作为丰田生产系统(Toyota Production System)的入门课程的组成部分,这种方法成为其中问题求解培训的一项关键内容1)案例:运用5个“为什么”分析有一台CNC总是因为保险丝烧断,而生产中断。
一问:“为什么机器停了?”答:“因为超过了负荷,保险丝就断了。
”二问:“为什么超负荷呢?”答:“因为轴承的润滑不够。
”三问:“为什么润滑不够?”答:“因为润滑泵吸不上油来。
”四问:“为什么吸不上油来?”答:“因为油泵轴磨损、松动了。
”五问:“为什么磨损了呢?”再答:“因为没有安装过滤器,混进了铁屑等杂质。
”经过连续五次不停地问“为什么”,才找到问题的真正原因和解决的方法,在油泵轴上安装过滤器。
如果我们没有这种追根究底的精神来发掘问题,我们很可能只是换根保险丝草草了事,真正的问题还是没有解决。
2)我的汽车无法启动。
1.为什么?:电池电量耗尽。
(第一个为什么)2.为什么?:交流发电机不能正常工作。
(第二个为什么)3.为什么?:交流发电机皮带断裂。
(第三个为什么)4.为什么?:交流发电机皮带远远超出了其使用寿命,从未更换过。
(第四个为什么)5.为什么?:我一直没有按照厂家推荐的保养计划对汽车进行过保养和维护。
(第五个为什么,根本原因)在实际应用当中,有可能将这种提问进一步扩展到六问、七问,甚至是更多的“为什么”。
这么做很可能是合乎实际情况的,因为“五个为什么”之中所说的“五”并非一成不变的真理;反而,这个“五”字实际上说的就是,五次反复提出为什么,一般来说足以找出根本原因。
5个为什么(five-whys)

5个为什么(five-whys)⽂章⾮常好,我认为我们必须实施这⼀思想。
原⽂:翻译:正⽂:第⼀部分:创业公司免疫系统概要:⽆论何时当发现问题时,应连续追问五个为什么寻找到问题的根源。
然后在分析的各个层⾯进⾏修正。
发现问题时应⽤五个为什么,你将(1)发现技术问题下的⼈员问题,(2)为你的创业公司建⽴⼀套免疫系统。
⼤野耐⼀是丰⽥⽣产⽅式的发明⼈之⼀。
他的书《丰⽥⽣产⽅式》是⼀份很吸引⼈的读物,虽然它并不实⽤。
读完这本书,你甚⾄可能都没法意识到丰⽥是做汽车业务的。
但是我清楚地从这本书学习到了⼀个⼗分具体的⽅法:问五个为什么。
我认为这是⼀个关键的精益创业⽅法。
当问题出现时,我们倾向于将其视作危机并追究责任。
更好的办法是将其视作⼀次学习的机会。
但并不是泛义的整体⾃我提升。
⽽是通过五个为什么寻找到问题的根源然后进⾏修正。
发现问题时追问五个为什么。
具体是这样进⾏的。
⽐如,你发现你的⽹站崩溃了。
显然,你第⼀反应是恢复它。
但是危机⼀旦过去,应开展事后调查询问为什么:1. 为什么⽹站崩溃了?因为所有前端服务器上的 CPU 使⽤率都达到了 100%。
2. 为什么 CPU 使⽤率达到 100%?因为⼀段新代码包含⼀个⽆限循环。
3. 为什么会出现这样的代码?因为某员⼯出错了。
4. 为什么他会出现这样的错误?因为他没有为这个功能写单位测试代码。
5. 为什么他没有写单位测试代码?因为他是⼀名新员⼯,且没有在测试驱动开发⽅⾯接受正确培训。
在这五个地⽅进⾏修正。
⽬前为⽌,这与主管运营团队⾯对⽹站崩溃会作的分析相差不⼤。
接下来:你要承诺按⼀定⽐例投资⽤于对分析的各个层⾯进⾏修正。
因此,在上⾯的例⼦中,我们需要作五处的修正:1. 恢复⽹站。
2. 移除错误代码。
3. 帮助出错的某员⼯了解为什么他的代码没有起到预期作⽤。
4. 培训该员⼯学习测试驱动开发相关知识。
5. 将测试驱动开发纳⼊新⼯程师⼊门指导内容。
进⾏修正可建⽴创业公司免疫系统。
5Whys经典案例-杰斐逊纪念馆大楼
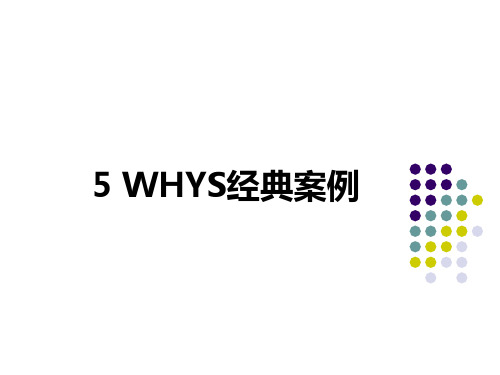
问题
5个为什么 N个为什么
根源
有些问题并不像我们看起来的那样复杂 只是我们还没有找到解决问题的简单办法
5 Whys
为什么这里的蜘蛛特别多?
因为墙上有蜘蛛最喜欢吃的飞虫。
5 Whys
为什么这里的飞虫这么多?
因为飞虫在这里繁殖特别快。
为什么飞虫在这里繁殖特别快?
因为开着的窗阳光充足:
拉上窗帘!
杰弗逊纪念馆至今完好,不信可以自己去看!
5 Whys
5 WHYS经典案例
5 Whys
美国首都华盛顿广场的杰弗逊纪念馆大楼
为纪念美国第三任总统托马斯·杰弗逊而建, 1938年在罗斯福主持下开工,至1943年落成。 纪念馆按杰弗逊喜爱的罗马万神殿式圆顶建筑风格设计,是一座高96英尺 的白色大理石建筑。
5 Whys
这座大厦历经风雨沧桑,年久失修,表面斑驳陈旧 政府非常担心,派专家调查原因。
5 Whys
为什么会出现斑驳?
因为冲洗墙壁所含的清洁剂对建筑物有强烈的腐蚀作用,而该大厦墙 壁每日被冲洗的次数大大多于其他建筑,因此腐蚀就比较严重
5 Whys 为什么每日冲洗呢?
因为大厦被大量的鸟粪弄得很脏。
为什么这么多鸟粪?
因为大厦周围聚集了很多燕子。
为什么燕子专爱聚集在这里?
因为建筑物上有燕子爱吃的蜘蛛。
5 Whys
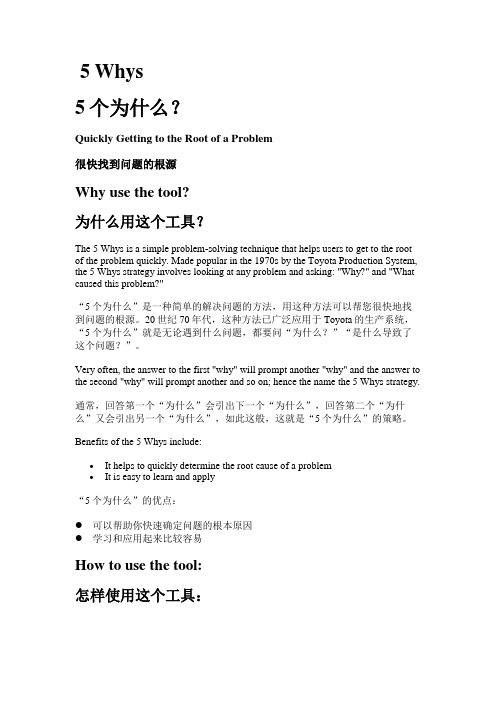
5 Whys5个为什么?Quickly Getting to the Root of a Problem很快找到问题的根源Why use the tool?为什么用这个工具?The 5 Whys is a simple problem-solving technique that helps users to get to the root of the problem quickly. Made popular in the 1970s by the Toyota Production System, the 5 Whys strategy involves looking at any problem and asking: "Why?" and "What caused this problem?"“5个为什么”是一种简单的解决问题的方法,用这种方法可以帮您很快地找到问题的根源。
20世纪70年代,这种方法已广泛应用于Toyota的生产系统,“5个为什么”就是无论遇到什么问题,都要问“为什么?”“是什么导致了这个问题?”。
Very often, the answer to the first "why" will prompt another "why" and the answer to the second "why" will prompt another and so on; hence the name the 5 Whys strategy.通常,回答第一个“为什么”会引出下一个“为什么”,回答第二个“为什么”又会引出另一个“为什么”,如此这般,这就是“5个为什么”的策略。
Benefits of the 5 Whys include:∙It helps to quickly determine the root cause of a problem∙It is easy to learn and apply“5个为什么”的优点:●可以帮助你快速确定问题的根本原因●学习和应用起来比较容易How to use the tool:怎样使用这个工具:When looking to solve a problem, start at the end result and work backward (toward the root cause), continually asking: "Why?" This will need to be repeated over and over until the root cause of the problem becomes apparent.遇到一个需要解决的问题时,从结果入手,倒推原因(向着问题的根源推),不断地问自己:“为什么?”这个过程需要不断的重复,直到问题的根源暴露出来。
5why 人员 流程
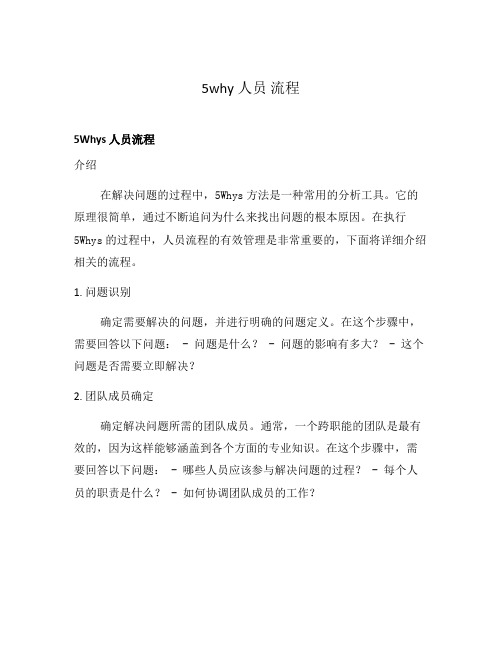
5why 人员流程5Whys 人员流程介绍在解决问题的过程中,5Whys方法是一种常用的分析工具。
它的原理很简单,通过不断追问为什么来找出问题的根本原因。
在执行5Whys的过程中,人员流程的有效管理是非常重要的,下面将详细介绍相关的流程。
1. 问题识别确定需要解决的问题,并进行明确的问题定义。
在这个步骤中,需要回答以下问题: - 问题是什么? - 问题的影响有多大? - 这个问题是否需要立即解决?2. 团队成员确定确定解决问题所需的团队成员。
通常,一个跨职能的团队是最有效的,因为这样能够涵盖到各个方面的专业知识。
在这个步骤中,需要回答以下问题: - 哪些人员应该参与解决问题的过程? - 每个人员的职责是什么? - 如何协调团队成员的工作?3. 问题分析通过使用5Whys方法,深入分析问题的根本原因。
在这个步骤中,需要回答以下问题: - 为什么会出现这个问题? - 这个问题是什么导致的? - 这个问题在流程中的哪个环节出现?4. 问题解决基于问题分析的结果,制定解决方案并实施。
在这个步骤中,需要回答以下问题: - 有哪些解决方案可以尝试? - 每个解决方案的优缺点是什么? - 如何进行解决方案的实施?5. 结果评估评估解决方案的效果,并根据实际结果进行调整。
在这个步骤中,需要回答以下问题: - 解决方案是否解决了问题? - 解决方案是否产生了预期的效果? - 是否需要进一步优化解决方案?总结在解决问题的过程中,人员流程的管理至关重要。
通过良好的流程管理,可以确保问题的准确识别和高效解决。
遵循上述的5个流程,将能够更好地应对各种问题,并取得良好的解决效果。
以上就是关于5Whys人员流程的详细说明。
希望这份文章对您有所帮助!附加流程:问题跟踪在问题解决的过程中,问题跟踪是非常重要的一环。
通过及时跟踪问题的处理进度和结果,可以确保问题的彻底解决。
下面是问题跟踪的具体流程:1. 问题记录在问题解决过程中,及时记录每一个出现的问题。
5 whys training
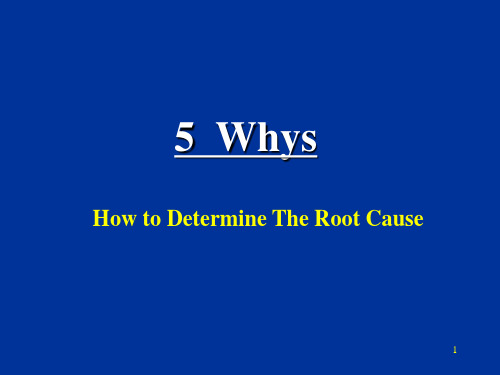
3
何时5 Whys方法最有用 方法最有用? 3. 何时5 Whys方法最有用?
· 当问题涉及人的因素或相互关系时 , · 在日常业务工作中; 5 WHYS 方法可单独使用,亦可用 于6 Sigma 项目.
4
方法? 4. 如何运用 5 Whys 方法?
1) 描述具体问题。把问题情况写下来,有助于问题的 描述具体问题。 突出及完整性。同时,有助于一个 team 集中精力在 同一个问题上。 提出为什么该问题会发生,把答案写在问题下面。 如果你提出的答案并不能识别问题的根本原因,再 问一遍为什么,并把答案写下来。 循环回到第 3步,直到team 一致同意问题的根本原 因已得到识别。 另外,有时可能只要问少于5 Whys就可找到根本原 因,也有可能要问多于5 Whys才能找到根本原因.
5
2) 3) 4)
Whys和 5 Whys fishbone diagram(鱼骨图)
• 鱼骨图可帮你找到问题的潜在或真正原 因。 • 所有原因列出后,可利用5 Whys 5 Whys方法对 每个原因往下挖,直至找到根本原因。
6
Example 1
问题陈述: 问题陈述
顾客收到了不满足他们要求的产品,所以佷不 满意。
在下班回家的途中,你的车停在半路上。
10
5 Whys 方法运用
答:因为没油了。
1) 为什么车停在半 路上? 2) 为什么会没油?
答:因为我在上班途中没有买油。
3) 为什么没买油?
答:因为我没有钱了。
4) 为什么没钱?
答:因为我在前晚玩牌时,把钱输掉了。
5) 为什么会在前晚 输钱?
答:因为我牌技不精。。
11
结 论:
问了5次为什么后,就可发现:牌技不精,导致输钱,最 终会导致车停在半路上。
5why具体指什么指哪五个

5why具体指什么指哪五个
5why具体没有特别的五个它是大概的意思
一、五why(又称,五个为什么、五问)分析法:
对一个问题点连续以5个“为什么”来自问,以追究其根本原因。
二、两种方法:
①从应有的状态入手;
②从原理原则入手分析;
三、七个要点:
①现象和为什么的描述尽量简短;
②“为什么”解析完了之后,一定要从最后的“为什么”的部分开始以追溯的形式解决,确认理论是否正确;
③从4M的角度思考,一个现象的要因是否列举完全。
相反的,也可以思考“如果这个要因不发生,前面的现象会不会发生”,并以这种方式确认;
④持续问“为什么”直到出现能引出再发措施的原因;
⑤只列出认为是异常的事项;
⑥原因追究要避免人的心理层面,应该追究硬件方面或管理机制方面的原因;
⑦不使用“很差”“不充分”“不足”等词语,要用明确而具体的词语来表现;
四、十条实施法则:
①“现象”或“为什么”的主语为1个,以“XX 发生了 XX”的方式简短描述;
②刚开始的“为什么”聚焦在能直接诱发现象产生的部分,之后以发生(或诱发)的原理为基础展开;
③“为什么”分析之后,要逆向解读分析结果,确认理论是否正确,或论点是否有跳跃的地方;
④要多问如果该原则不发生,前面的“为什么”真的不会发生么吗?另外并列关系的要因不要遗漏;
⑤要注意不自然的“为什么”;
⑥使用大家都能理解的具体的语言描述;
⑦对于作为对比基准的物品或事项也要追究“为什么”;
⑧避免对人的心理层面的原因追究;
⑨持续“为什么”分析,直到出现可以导出防止再发措施的要因为止;。
5whys分析法模板
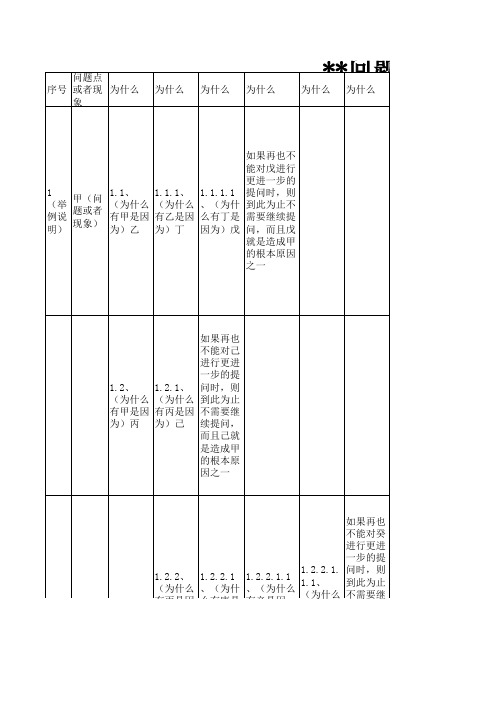
进行更进 一步的提 1.2.2.1. 问时,则 1.2.2、 1.2.2.1 1.2.2.1.1 1.1、 到此为止 (为什么 、(为什 、(为什么 (为什么 不需要继 有丙是因 么有庚是 有辛是因 有壬是因 续提问, 为)庚 因为)辛 为)壬 为)癸 而且癸就 是造成或 者产生甲 的根本原 因之一 1、相关 部门针对 **没有制 定规范、 要求,无 法执行 1、没有 对执行者 进行**规 范或者要 求的培训
1、原有的 关于**规范 或要求的教 2、没有 材没有及时 教材编写 关于**规 更新 (含更 范或要求 新)管理 的合适的 执行不到 培训教材 位
训,但没 有效果 2、没有 关于**规 范或要求 的合适的 2、编写出 培训教材 的关于**规 范或要求的 教材没有经 过评审 3、培训 **规范或 **执行 要求的老 2 不到位 师不负责 任,应付 了事 4、培训 **规范或 要求的后 不用考试 1、没有 对编写出 的**规范 1、**规 或者要求 范或要求 进行评审 3、针对 中存在错 2、评审 漏。 **有规 **规范或 范,但规 者要求时 范无法执 走过场 行 2.**规范 所编制的 或要求中 **规范或 有部分不 者要求没 具备操作 有经过执 行者的验 性 证 1、过程 中针对** 缺少对对 的规范或 **的规范 者要求存 或者要求 在着可以 关键节点 不执行的 的监控 空间,心 存侥幸。 1、没有 根据是否 4、执行 执行**的 者不愿意 2、执行 规范或者 去执行针 和不执行 要求进行 对**的规 的**的规 及时奖惩 范或者要 范或者要 求对自己 求 的切身利 益影响不 大 教材编写 (含更 新)管理 执行不到 位
针对每一 条应急措 应急措施:在解决戊的长期措施还不能采取或者不能保证有效 施制定对 果的前提下需要采取的临时措施,即过渡阶段的控制措施 应的完成 时间
Ask5Whys
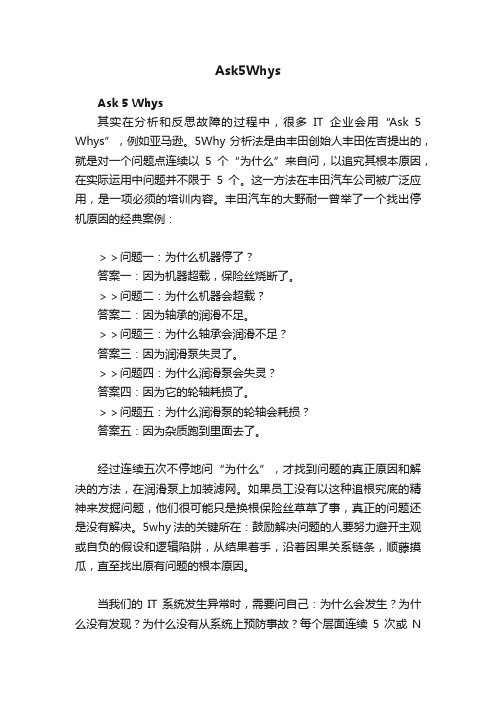
Ask5WhysAsk 5 Whys其实在分析和反思故障的过程中,很多IT企业会用“Ask 5 Whys”,例如亚马逊。
5Why分析法是由丰田创始人丰田佐吉提出的,就是对一个问题点连续以5个“为什么”来自问,以追究其根本原因,在实际运用中问题并不限于5个。
这一方法在丰田汽车公司被广泛应用,是一项必须的培训内容。
丰田汽车的大野耐一曾举了一个找出停机原因的经典案例:>>问题一:为什么机器停了?答案一:因为机器超载,保险丝烧断了。
>>问题二:为什么机器会超载?答案二:因为轴承的润滑不足。
>>问题三:为什么轴承会润滑不足?答案三:因为润滑泵失灵了。
>>问题四:为什么润滑泵会失灵?答案四:因为它的轮轴耗损了。
>>问题五:为什么润滑泵的轮轴会耗损?答案五:因为杂质跑到里面去了。
经过连续五次不停地问“为什么”,才找到问题的真正原因和解决的方法,在润滑泵上加装滤网。
如果员工没有以这种追根究底的精神来发掘问题,他们很可能只是换根保险丝草草了事,真正的问题还是没有解决。
5why法的关键所在:鼓励解决问题的人要努力避开主观或自负的假设和逻辑陷阱,从结果着手,沿着因果关系链条,顺藤摸瓜,直至找出原有问题的根本原因。
当我们的IT系统发生异常时,需要问自己:为什么会发生?为什么没有发现?为什么没有从系统上预防事故?每个层面连续5次或N次的询问,得出最终结论。
只有以上三个层面的问题都探寻出来,才能发现根本问题,并寻求解决。
例如Gitlab事件,需要问很多问题:为什么会出现数据库不同步?为什么会丢失数据?为什么轻易在生产环境上执行删除命令?为什么运维过程如此混乱?为什么备份机制都失效?为什么备份失效平时未检查?只有把这些问题一个个搞清楚,一个个进行5why分析,才能把问题和隐患一个个解决。
操作化方法举例 -回复

操作化方法举例-回复操作化方法举例。
操作化方法是一种分析和解决问题的方法,它通过将问题拆解成一系列具体的操作步骤,以便更清晰地理解问题的本质,并采取适当的措施来解决问题。
在现实生活和工作中,我们经常使用操作化方法来应对各种挑战和困境。
下面,我将以操作化方法举例为主题,为您详细介绍一些典型的操作化方法及其应用。
一、五步法(5 Whys)五步法是一种常用的操作化方法,它通过连续提问“为什么”来揭示问题的根本原因。
通过不断追问,我们可以把一个复杂的问题简化为几个核心因素,并找出解决问题的办法。
这里以一个简单的例子来说明五步法的应用。
假设某工厂生产线上出现一个设备故障,导致产量降低。
我们可以按照以下步骤使用五步法进行分析和解决:第一步,明确问题:为什么产量降低?答:设备故障。
第二步,追问原因:为什么设备故障?答:设备老化。
第三步,再次追问原因:为什么设备老化?答:缺乏定期保养。
第四步,继续追问原因:为什么缺乏定期保养?答:管理不善。
第五步,最终追问原因:为什么管理不善?答:缺乏培训和监督。
通过五步法,我们发现设备故障的根本原因是缺乏培训和监督。
因此,为了解决产量降低的问题,我们应当加强员工培训和管理监督,确保设备得到定期的保养和维护。
二、PDCA循环PDCA循环是一个经典的操作化方法,它由四个步骤组成:计划(Plan)、执行(Do)、检查(Check)和行动(Act)。
这个方法适用于复杂的问题和项目,并可以帮助我们持续改进和优化工作流程。
以下是一个使用PDCA循环解决质量问题的例子:第一步,计划(Plan):明确问题、设定目标和制定行动计划。
比如,某制造公司的产品出现质量问题,我们可以设定目标为提高产品质量,制定行动计划包括培训员工、改进工艺流程等。
第二步,执行(Do):按照计划执行行动。
执行行动计划,培训员工、改进工艺流程等。
第三步,检查(Check):评估行动的效果,收集数据和反馈信息。
通过检查产品质量指标,收集客户反馈等数据,评估行动的效果。
5-whys分析法
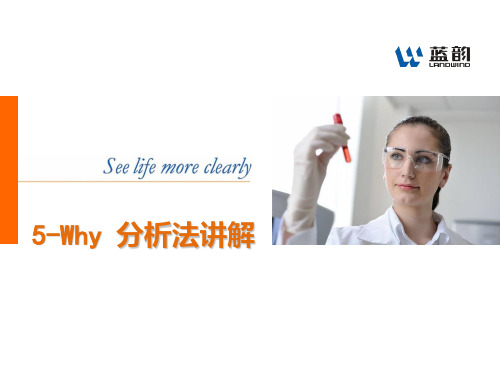
为什么 小孩在哭 今天暴雨
?
今天暴雨
所以
不能去动 ??? 物园
???
所以
小孩在哭
15
16
“5-Why” 应用注意事项 (2)
只选择异常的状况作为原因。
为什么? 为什么? 为什么? 为什么?
无尘室内灰 尘量超出标 准
设备引起 灰尘
设备连续 运转
生产量多
订单过多
真因?
这些都是正常情况,不应列在原因之内。
6
7
什么是 “5-Why”
问题
防堵措施
(Containment Action)
防呆措施
(Error-proofing)
7
8
“5-Why”的特点
工具的用途
找到问题的根源
应用上的优势
从根本上解决问题
工具的掌握
简单、易学
8
9
如何应用“5-Why”
举例:
When Where Who What How
解决问题的思路:
13
14
“5-Why” 举例-cont’d
Why#4: 为什么炉管的热电偶控制器不能够控制到炉管加热的整个区域? Answer#4: 这个热电偶比之前的一个短 Why#5: 为什么这个热电偶比之前的一个短? Answer#5: 这个热电偶是从一个新的供应商那里采购的
Why#6: 为什么要从这个新的供应商处采购? Answer#6: 降低成本
22
谢 谢
LSL
USL 12
13
“5-Why” 举例
Problem: 在某个双极晶体管(bipolar)工厂,WAT测试中发现BiCMOS 工艺中的双极晶体管增益高出规范的要求
如何使用5Whys进行根本原因分析?

如何使用5Whys进行根本原因分析?当出现诸如客户不满意,市场份额下降,质量低下等问题时,你必须了解问题的根本原因。
只有解决根本原因,才能解决问题。
根本原因分析(RCA)是一种解决问题的方法,用于识别故障或问题的根本原因,它被广泛用于各种行业。
01什么是根本原因?所有的树木都有树干,树枝和树叶。
这些是我们可以立即看到的,因此立即浮现在脑海中。
我们看不到的部分是将树锚定到地面的根系,该根系统通常比树本身占据更大的面积,即使树的树枝已经被硬修剪,它也继续增长。
这就是为什么深入研究问题核心的系统称为“根本原因分析”。
02为什么要进行根本原因分析?根本原因分析是使公司能够做出正确更改以防止故障反复发生的重要步骤。
有三种处理重复出现的问题的方法,我们可以:别理他们。
执行临时修复。
首先了解为什么它们会发生。
如果我们选择第一种选择,那么这个问题将永远无法解决,并且有可能升级。
如果我们选择第二种方法,那相当于在污渍上涂上油漆或在泄漏处贴上胶带,并希望它能保持住–你正在治疗的是症状,而不是原因。
采用第三个选项,即分析根本原因,是最耗时的,但应该允许你采取措施以确保将来不再发生此问题。
03如何使用5个为什么分析?以下是一些有效执行5 WHY分析的简单步骤:写下问题,写作可以帮助你形式化问题并完整地描述问题。
如果你与团队合作,则还可以帮助团队专注于同一问题。
问问自己为什么会发生问题,并写下答案。
再次问自己-查看你的答案-为什么会发生问题,并写下答案。
再一次,问自己-查看你的答案-为什么会发生此问题。
在团队同意确定问题的真正根本原因之前,请经常问自己这个问题。
这可能比5个WHYS花费的时间更少或更多。
使用树形图执行多个5个为什么的根本原因分析与一次分析单个5个为什么原因的单个原因不同,树形图可用于缩小并消除图中的可能原因,理想情况下,在一个单个图上考虑一个或多个可解决的根本原因。
04如何创建5个Whys树形图?“五个为什么”练习是一种质疑技术,可以超越问题的症状来识别问题的根本原因或根本原因。
追因分析报告法5why分析报告法
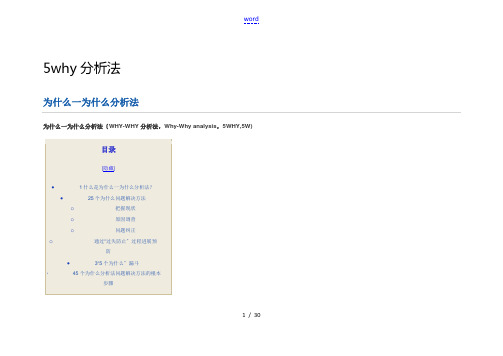
5why分析法为什么一为什么分析法为什么一为什么分析法〔WHY-WHY分析法,Why-Why analysis,5WHY,5W)1 / 30[编辑]什么是为什么一为什么分析法?为什么-为什么分析,也被称作5个为什么分析,它是一种诊断性技术,被用来识别和说明因果关系链,它的根源会引起恰当地定义问题。
不断提问为什么前一个事件会发生,直到回答“没有好的理由〞或直到一个新的故障模式被发现时才停止提问。
解释根本原因以防止问题重演。
文件中所有带有“为什么〞的语句都会定义真正的根源(通常需要至少5个“为什么〞,但5个why不是说一定就是5个,可能是1个,也可能是10都没有抓到根原)。
2 / 30[编辑]5个为什么问题解决方法在一些组织里,一个普通的解决问题方法被用来分析和解决质量问题。
3 / 30这个方法有4个主要局部:•把握现状。
•原因调查。
•问题纠正。
•通过“过失防止〞过程进展预防。
[编辑]把握现状在方法的第一局部里,你:•识别问题•澄清问题•查找原因要点(PoC)[编辑]原因调查在方法的第二局部里,你可以引导一次5个为什么的调查来识别根本原因。
•针对明确的问题。
4 / 30•针对为什么没有发现问题•针对为什么系统允许问题发生[编辑]问题纠正在方法的第三局部里,你:•采取明确的措施来纠正问题。
至少要求采取短期临时措施来保护顾客利益。
[编辑]通过“过失防止〞过程进展预防在方法的第四局部里,你:•采取明确的措施来确保问题不会再发生,典型的措施是“过失防止〞过程。
•铭记吸取到的教训。
[编辑]“5个为什么〞漏斗5 / 30[编辑]5个为什么分析法问题解决方法的根本步骤6 / 30[编辑]第一局部:把握现状步骤1: 识别问题在方法的第一步中,你开始了解一个可能大、模糊或复杂的问题。
你掌握一些信息,但一定没有掌握详细事实。
问:我知道什么?步骤2: 澄清问题方法中接下来的步骤是澄清问题。
为得到更清楚的理解,问:•实际发生了什么?•应该发生什么?步骤3: 分解问题在这一步,如果必要,将问题分解为小的、独立的元素。
深度理解5WHY

2、只问为什么会发生问题(Why happen),而不问为什么问题会流出 (Why escape)。
解读:客户(包括内部与外部客户)不仅仅关心为什么会有问题发生,而 且也非常关注为什么你自身的控制流程无法防止问题流出。
*做得更细致的人还可能会问:为什么我的质量管理体系没有防止这个问题 的发生。
3、用主观推测(推论)代替客观事实来描述问题/分析问题。
- 为什么钻孔偏移?
- 因为对位不准(推测)。
错误的分析:工程师没有第一时间去现场分析,而是基于个人的判断与推 测。事实可能是图纸错误,对位再准确也会偏移。
解读:坚持“三现原则”,现实(亲自去了解客观事实)、现场(亲自到 问题发生现场分析问题)和现物(亲自查看实物)。
4、每一个为什么永远只有一个原因与之对应,而实际上一个问题之所以发 生往往是多个原因的共同结果。
错误地描述问题: 例子:刚才还在使用的手机,现在找不到了,如何描述这个问题? 错误的描述:手机掉了 —— 推测手机之所以找不到是因为掉了,没有事实 支撑。
正确的描述:手机现在不在一直放手机的口袋里 —— 客观事实 事实可能是图纸错误,对位再准确也会偏移。
错误地分析问题:例子:生产源自场发现钻孔位置偏移。经典的丰田公司的例子:
7、针对每一层Why找到的原因,假定为正确,而不做反向的验证。
解读:在每一层的分析完成后,可行时都应该进行反向的验证,以确定找 到的原因是否正确,假设检验能很好的解决这个验证问题。
THANKS!
• 请在此输入您的副标题
深度理解5WHY
• 避免常犯的7个错误
5-Why分析法,又称“五问”法,也就是我们中国人常说的打破沙锅问到 底,首创于丰田公司的大野耐一。5-Why方法的逻辑非常简单,如下图所 示。
- 1、下载文档前请自行甄别文档内容的完整性,平台不提供额外的编辑、内容补充、找答案等附加服务。
- 2、"仅部分预览"的文档,不可在线预览部分如存在完整性等问题,可反馈申请退款(可完整预览的文档不适用该条件!)。
- 3、如文档侵犯您的权益,请联系客服反馈,我们会尽快为您处理(人工客服工作时间:9:00-18:30)。
PRACTICAL PROBLEM SOLVINGIntroductionIn the Delphi organization, a common problem solving process is used to analyze and solve quality problems.There are four major parts of the process:∙Grasp the Situation∙Cause Investigation∙Problem Correction∙Prevention through Errorproofing♦Grasp the SituationDuring the first part of the process, you:∙Identify the Problem∙Clarify the Problem∙Locate the Point of Cause (PoC)♦Cause InvestigationIn the second part of the process, you:∙Conduct a “5-Why” inves▪for the specific problem▪for why the problem was not detected▪for why the “system” allowed the problem to occur♦Problem CorrectionIn the third part of the process, you:∙Take specific action to correct the problem. At a minimum, short-term temporary measures are required to protect the customer.♦Prevention Thru ErrorproofingIn the fourth part of the process, you:∙Take specific action to make sure the problem cannot recur, typically through errorproofing∙Capture Lessons LearnedPRACTICAL PROBLEM SOLVING MODEL5 Why FunnelT I O N¯Root Cause¯Corrective Action¯Lessons LearnedBASIC STEPS OFPRACTICAL PROBLEM SOLVINGPart I – Grasp the Situation♦Step 1: Identify the ProblemIn the first step of the process, you become aware of a problem that may be large, vague, or complicated. You have some information, but do not have detailed facts.Ask:▪What do I know?♦Step 2: Clarify the ProblemThe next step in the process is to clarify the problem. To gain a more clearunderstanding, ask:▪What is actually happening?▪What should be happening?♦Step 3: Break Down the ProblemAt this point, break the problem down into smaller, individual elements, ifnecessary.▪What else do I know about the problem?▪Are there other sub-problems?♦Step 4: Locate the Point of Cause (PoC)Now, the focus is on locating the actual point of cause of the problem. You need to track back to see the point of cause first-hand. Ask:▪Where do I need to go?▪What do I need to see?▪Who might have information about the problem?♦Step 5: Grasp the Tendency of the ProblemTo grasp the tendency of the problem, ask:▪Who?▪Which?▪When?▪How often?▪How much?It is important to ask these questions before asking “Why?”Part II: Cause Investigation♦Step 6: Identify and confirm the direct cause of the abnormal occurrence.If the cause is visible, verify it. If the cause is not visible, consider potential causes and check the most likely causes. Confirm the direct cause based on fact. Ask: ▪Why is the problem occurring?▪Can I see the direct cause of the problem?▪If not, what do I suspect as potential causes?▪How can I check the most likely potential causes?▪How can I confirm the direct cause?♦Step 7: Use 5-Why investigation to build a chain of cause/effect relationships that lead to the root cause. Ask:▪Will addressing the direct cause prevent recurrence?▪If not, can I see the next level of cause?▪If not, what do I suspect as the next level of cause?▪How can I check and confirm the next level of cause?▪Will addressing this level of cause prevent recurrence?If not, continue asking “Why?” until you find the root cause.Stop at the cause that must be addressed to prevent recurrence. Ask:▪Have I found the root cause of the problem?▪Can I prevent recurrence by addressing this cause?▪Is this cause linked to the problem by a chain of cause/effect relationships that are based on fact?▪Does the chain pass the “therefore” test?▪If I ask “Why?” again, will I be into another problem?Be sure you have used 5-Why Investigation to answer these questions:▪Why did we have the problem?▪Why did the problem get to the customer?▪Why did our “system” allow it to occur?5 WHY CAUSE INVESTIGATIONRoot CauseStep 8: Take Specific Action to Address the ProblemUse temporary measures to eliminate the abnormal occurrence until the root cause can be addressed. Ask:▪Does it contain the problem until a permanent solution can be implemented?Implement corrective actions to address the root cause to prevent recurrence.Ask:▪Does it prevent the problem?Follow-up and check results. Ask:▪Is the solution working?▪How do I know?PRACTICAL PROBLEM SOLVING CHECKLISTTo be sure you have followed the problem solving model, use this checklist as you complete the problem solving process.ACTIVITY:FLEX INDUSTRIES CASE STUDYDirections:▪Use the Delphi Problem Solving Process to evaluate the Flex Industries Case Study below and on the following pages. Review the 5-Why Investigation results on Page 11.▪Use the worksheets on Pages 13 and 14 to record your work.▪Use only the information provided.▪Do not try to re-engineer the rivets or solve the technical problems in the case study. The purpose of this activity is to use the Problem Solving model to organize the given data.FLEX INDUSTRIES CASE STUDYBackgroundJake Ryan is the Quality Manager at Flex Industries. Flex is a component supplier that manufactures metal stampings and light assembly products. The company has a reputation for supplying high quality parts on a consistent basis. Seldom has there been a customer complaint. Flex has Quality representatives called Customer Support Engineers (CSE’s) at every customer assembly plant. The CSE’s report any problems to Jake for investigation and follow-up.At 7:00 a.m. this morning, Jake received a call from Janet, CSE at the Winding River Assembly Plant. Janet informed him that the customer had found five defective stabilizing brackets on second shift last night. She checked the remaining inventory and there were no defects in the remaining 326 pieces. The manufacturing sticker on the back of the brackets indicated that they were made by the second shift operator. Normally, the stabilizing bracket is fastened to the regulator motor with three rivets. The five defective brackets had only two rivets in them. The lower set of rivets on all five brackets was missing a rivet. This was the first time that the problem occurred.GOOD BADJake set-up containment procedures at the plant warehouse to sort for discrepant materials. As of this morning, two more defective brackets had been found in the remaining 2019 pieces of inventory at Flex.Cause InvestigationJake went out to the floor to talk with the team leader of the two rivet lines (East and West) and the area quality assurance auditor. He informed Sam (the team leader) of the quality problem and asked him to identify the line which runs the stabilizing bracket assembly. Sam directed Jake to the East line which runs Winding River assembly brackets only.At the East Line, he spoke with Judy (the QA Auditor for the area) and asked to see the quality log sheets. Jake and Judy reviewed the Nov. 11th log sheet and could not find anything out of the ordinary. He asked her to set-up in-house containment procedures to sort for any discrepant material in the finished goods area.Next, Jake tried to locate the second shift operator whose clock number was on the defective parts. Since that operator was gone, Jake spoke with the current machine operator (Ben). He asked Ben about any recent difficulties with the rivet machine. Ben said that he hadn’t noticed anything out of the ordinary. Ben also mentioned, however, that there had never been any quality bulletins posted in the two years that this particular part has been running.Jake decided to stay in the area to watch the machine run for a while. After about 15 minutes, he watched Ben dump rivets into the feeder bowl to prepare for the next run.Shortly after restarting rivet operations, Ben walked over to another riveter and came back with a steel rod. Ben poked around the rivet chute and then continued working. Jake approached Ben and asked him about the steel rod. Ben replied that from time to time the chute gets jammed and he has to clear it out. This happens two or three times during a shift. He didn’t mention this in his earlier conversation with Jake because the problem has existed ever since he started working with this machine. The previous operator showed him how to clear the chute. All the rivet machines are like this.Jake called the Machine Repair Department and asked that someone look at the rivet track. A slight gap in the track was found and removed, and Ben continued to work. Two hours later, Jake got a call from Ben saying that the track was still jamming. As far as Jake could see, only rivets were in the bowl. Next, Jake looked into the rivet supplier containers. There was some foreign material in the blue container, but none in the red container. The label on the blue container showed that it was from Ajax Rivet, Inc., and the label on the red c ontainer indicated that it was from Frank’s Fasteners. Obviously, the foreign material was entering the rivet feeder bowl and jamming the track.Jake called Maintenance and requested that the bowl be cleaned. He also added the cleaning operation to the preventive maintenance schedule on the equipment. He then called both Ajax Rivet, Inc. and Frank’s Fasteners. He asked about the cleaning procedures on the returnable containers. Frank’s did a full container purge and clean. Ajax just re-introduced the containers back into their system. When Jake asked why Ajax did not clean their containers, he was told that Ajax was not aware that such a policy was needed.Upon further investigation, Jake learned that Frank’s Fasteners supplies other major automotive companies. Since these companies require that all returnable containers be cleaned, Frank’s instituted the purge as part of its practice for all customers. Ajax Rivet, however, depends primarily on Flex as its major customer. No such policy has ever been required of them.and requested that a container maintenancepolicy be drafted which would apply to all theirsuppliers. He also asked that a machinemodification be developed to sense for thepresence of rivets. Hopefully, this woulderror-roof the process.5-Why Cause Investigation Reference No. _______________(Spill, PR/R…)1. Make supplier part of APQP activities.5-Why AnalysisReference No. __________ (Spill, PR/R…)Delphi 5-Why Template to be used for all 5-Why InvestigationsFLEX INDUSTRIES WORKSHEETCorrective Action¯Lessons LearnedCorrective Action¯Lessons Learned。