城轨车辆铝合金车体结构服役寿命评估方法
铝合金车身材料疲劳寿命预测

铝合金车身材料疲劳寿命预测随着汽车工业的不断发展,对车身材料的要求也越来越高。
钢材为主要车身材料,但由于其重量较重,对燃油效率的影响较大,因此研究并采用轻质材料已成为汽车制造的趋势。
铝合金作为一种重要的轻质材料,广泛应用于汽车制造中,但其疲劳性能的变化却是一个令人担忧的问题。
因此,铝合金车身材料的疲劳寿命预测成为研究的热点之一。
一、铝合金车身材料的疲劳特性铝合金车身材料最重要的特性是其轻质、高强度和抗腐蚀性强等优点。
然而,其疲劳寿命相比于钢材较低,其原因在于以下几点:1. 铝合金的晶粒细度相对较细,微观裂纹的形成对其疲劳寿命的影响更大。
2. 铝合金的热膨胀系数比较大,易在热作用下出现疲劳裂纹。
3. 铝合金的低温韧性差,易在冷却过程中发生疲劳损伤。
因此,对于铝合金车身材料的疲劳特性进行研究是十分必要的。
二、铝合金车身材料疲劳寿命预测方法铝合金车身材料疲劳寿命预测方法的研究目的是为了在实际使用中能够更好地预测材料在疲劳载荷下的寿命,并在设计中充分考虑材料属性,在提高材料的使用寿命的同时降低生产成本。
1. 经典金属材料疲劳寿命预测方法经典的材料疲劳寿命预测方法是强度理论方法。
这种方法基于一个假设:在材料内部存在无限多的缺陷,这些缺陷在受载荷作用下会形成裂纹,裂纹继续扩展,最终导致材料疲劳破坏。
这种方法的优点是适用范围广,可以理论预测材料的疲劳寿命。
但是,这种方法假设了缺陷数量是无限的,而且实际缺陷种类很多,因此对于特定的疲劳载荷具有很大的误差。
2. 基于网格法的疲劳寿命预测方法网格法是一种数值模拟方法,可将材料的几何形状转化为网格形式,在此基础上描述其物理性质。
在基于网格法的疲劳寿命预测中,首先利用CAD系统绘制材料的几何结构,然后将其转换为网格形式。
接着,利用FEM数值模拟软件,对材料的受力情况进行计算,并对其疲劳寿命进行预测。
这种方法的优点是可以模拟不同尺寸、不同载荷的材料,具有很高的准确性。
三、疲劳寿命预测在铝合金车身材料中的应用铝合金车身材料的疲劳寿命预测方法在实际中的应用十分广泛。
城市轨道交通车辆的车体结构组成讲解
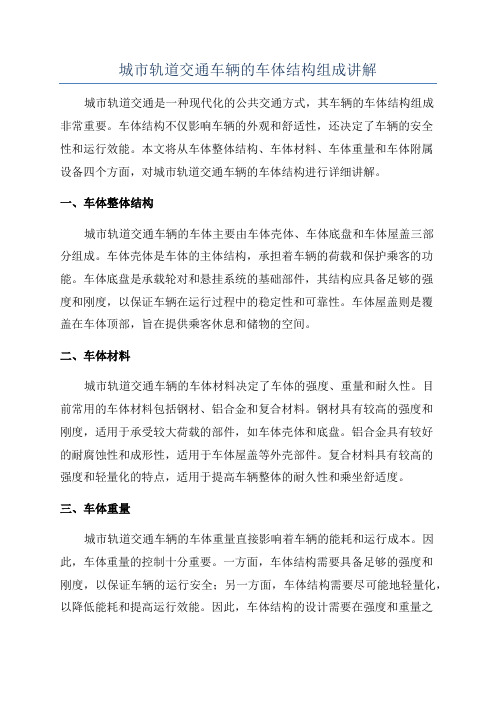
城市轨道交通车辆的车体结构组成讲解城市轨道交通是一种现代化的公共交通方式,其车辆的车体结构组成非常重要。
车体结构不仅影响车辆的外观和舒适性,还决定了车辆的安全性和运行效能。
本文将从车体整体结构、车体材料、车体重量和车体附属设备四个方面,对城市轨道交通车辆的车体结构进行详细讲解。
一、车体整体结构城市轨道交通车辆的车体主要由车体壳体、车体底盘和车体屋盖三部分组成。
车体壳体是车体的主体结构,承担着车辆的荷载和保护乘客的功能。
车体底盘是承载轮对和悬挂系统的基础部件,其结构应具备足够的强度和刚度,以保证车辆在运行过程中的稳定性和可靠性。
车体屋盖则是覆盖在车体顶部,旨在提供乘客休息和储物的空间。
二、车体材料城市轨道交通车辆的车体材料决定了车体的强度、重量和耐久性。
目前常用的车体材料包括钢材、铝合金和复合材料。
钢材具有较高的强度和刚度,适用于承受较大荷载的部件,如车体壳体和底盘。
铝合金具有较好的耐腐蚀性和成形性,适用于车体屋盖等外壳部件。
复合材料具有较高的强度和轻量化的特点,适用于提高车辆整体的耐久性和乘坐舒适度。
三、车体重量城市轨道交通车辆的车体重量直接影响着车辆的能耗和运行成本。
因此,车体重量的控制十分重要。
一方面,车体结构需要具备足够的强度和刚度,以保证车辆的运行安全;另一方面,车体结构需要尽可能地轻量化,以降低能耗和提高运行效能。
因此,车体结构的设计需要在强度和重量之间找到一个平衡点,通过优化设计和材料选择,使车辆在满足强度要求的同时,尽可能地减轻车体重量。
四、车体附属设备城市轨道交通车辆的车体还包括一些附属设备,如车门、窗户、灯光和通风系统等。
这些设备主要用于提供乘客进出车辆的通道,保证车内的采光和通风,以及提供车辆行驶时的灯光照明。
车辆的附属设备需要与车体的结构相适应,确保设备的稳固性和可靠性。
同时,附属设备的设计还需要满足乘客的舒适性和安全性要求。
城市轨道交通车辆的车体结构组成是一个综合性的工程问题,需要考虑多个因素的综合影响。
轨道车辆焊接结构疲劳寿命评估方法探究

轨道车辆焊接结构疲劳寿命评估方法探究摘要:随着我国经济与科技的不断发展,客运列车逐步的高速化与货运列车逐步的重载化已成为现代轨道车辆发展的新趋势。
随着客运列车的不断提速,轨道车辆焊接结构所承受的振动载荷频带范围不断宽泛,产生结构振动的可能性大大增加。
焊接结构长期处于随机振动环境下更易发生疲劳断裂,影响其疲劳寿命,因此,对轨道车辆焊接结构的疲劳评估显得尤为重要。
本文主要对轨道车辆焊接结构疲劳寿命评估方法进行了分析,以供参考。
关键词:轨道车辆;焊接结构;疲劳寿命;评估方法1、焊接结构在轨道车辆结构中的重要地位焊接结构在轨道车辆结构中扮演着重要的角色。
随着轨道交通的发展和技术的进步,焊接技术被广泛应用于轨道车辆的制造过程中。
(1)能够提供轨道车辆所需的强度和稳定性轨道车辆需要具备足够的强度以承受运行过程中的各种力和压力。
采用焊接结构可以将多个构件连接成一个整体,使得整车的结构更加牢固,能够有效地抵抗外界的力和震动。
此外,焊接结构还能够提高车辆的稳定性,减少车辆运行过程中的晃动和摇晃,提高乘坐舒适度。
(2)能够提高轨道车辆的安全性焊接接头具有较高的强度和密封性,能够有效地避免接头的松动和破裂,从而保证车辆在行驶过程中的安全性。
焊接结构还能够减少车辆的结构疲劳和腐蚀,延长车辆的使用寿命。
对于轨道车辆来说,安全性至关重要,焊接结构的应用可以提高车辆的整体安全性能。
(3)提高轨道车辆的运行效率焊接结构具有较高的刚性和轻量化特点,能够减少车身的重量,并提高车辆的运行速度和加速度。
同时,焊接结构能够降低车辆的阻力,使得车辆在运行过程中消耗更少的能量,提高能源利用效率。
这对于轨道交通系统来说,既能够减少能源消耗,又能够改善运输效率,具有重要的意义。
(4)提高轨道车辆的制造效率和降低成本轨道车辆采用焊接结构可以简化制造工艺,减少零部件的数量,缩短制造周期,并且能够提高产品的一致性和质量稳定性。
焊接结构还能够实现批量生产,降低生产成本,提高企业的竞争力。
轨道客车车体关键部件寿命评估方法研究及应用

s p e c t r u m i s p r e p a r e d . T h e b e n c h t e s t o n p a s s e n g e r t r a i n c a r b o d y i s c o n d u c t e d b y u t i l i z i n g t h e l o a d i n g s p e c t r u m t o s i m— u l a t e t h e a p p l i c a t i o n o f t h e k e y c a r b o d y l o a d d u r i n g v e h i c l e o p e r a t i o n i n t h e l a b o r a t o r y . S u c h a t e s t me t h o d e a l r p r o —
摘 要 :为对某 型号轨道 客车车体关键 部件进行寿命评 估 ,研究 一种利用实 际线 路载荷数据 并通过 台
架试 验方式实现 的方法 。通过 对在实际线路 上运行车辆 的关键载荷部 位进行跟踪测 试 ,得到车 体关键部位 的动态应 变及加速 度数据 ,并进行 载荷等 效转换 。利用线路 实测数 据和仿 真分析对 比,结 合德 同 F K M 理 论 .编制 试验载 荷加载谱 。利用该加载谱 在实验室模拟 车辆运行 时车体主要载 荷的施加 ,完成 客车车体 台 架试 验。该试验方法可为轨道车辆车体 的研 发提供数据 支持。 关键 词 :轨道客车 ;车体 ;台架试验 ;寿命评估
中国铁道学会车辆委员会各学组2019年度重点学术活动项目

中国铁道学会车辆委员会各学组2019年度重点学术活动项目
号
称
学
会
1
轨道交通制动技术创新论坛
2
高速重载轮轴学术研讨会
3
轨道车辆电气安全设计规则讨论会
4
轨道交通车辆软件评测技术论坛
5
故障
健康管
讨会
6
城轨车辆学 立大会暨城市轨道车辆创新技术研讨会
7
铁路货运市场发展和多样化运输装备技术研讨会
变化范围所对应的应
的应力换 到#
线路试验时,
量各个 等级
的应力-时
间#
正常运营状态时,测量从车辆开始运营直至一天
运营结束期间的应力-时间 #
4.4. 1.2 数据处理
结合实际线
对信号进行牵零、趋势项 :、
奇异
、数字化
。低通
100 Hz。采用雨流计数法对应力-时间 统计处理,获取应 #
进行
4.4.2 疲劳寿命评估
梁件
寿命的最小 车体结构的服役寿命#
参考文献:
何霖,朱士友,陈凯,等.广州地铁1号线铝合金车体结构服役寿命 研究铁道车辆,2018,56(4)14. [2] EN 1999—1一3一2007,Eurocode 9: Design of aluminium structures一 Part 1-3: Structures susceptible to fatigue[S—
பைடு நூலகம்
下或正常运
进行线路试验#用重物
时,根据表1
的
等级在车内 {重
物,在各个
等级下,应至少
次;正常运
线路试验车内不需
,试验设备的布置
不应 车辆的正常客流量,在
铝合金车身结构疲劳寿命研究

铝合金车身结构疲劳寿命研究第一章引言随着汽车工业的不断发展,对汽车的性能、安全性和环保性能的要求也越来越高。
作为汽车车身主要材料之一的铝合金,在提高汽车性能的同时,也面临着疲劳寿命有限等问题。
因此,研究铝合金车身结构的疲劳寿命,具有极其重要的理论和现实意义。
第二章铝合金车身结构的疲劳机制铝合金车身结构的疲劳现象主要表现为裂纹扩展和断裂。
其疲劳机制主要是由于铝材的微观结构存在缺陷和组织非均匀性,受到加载作用下存在的应力集中区域所引起的。
该过程中,裂纹扩展的速度逐渐上升,导致材料疲劳寿命的逐渐消耗。
第三章铝合金车身结构疲劳寿命测试方法为了研究铝合金车身结构的疲劳寿命,需要采用一系列的测试方法。
目前常用的测试方法包括疲劳试验和数值模拟试验两种。
疲劳试验是指将标准试样进行加载,通过测量其失效次数和失效时间来分析试样的疲劳寿命。
该方法的优点是数据直观,可以对获得的结果进行直接对比和分析,但其缺点是测试周期长,需要大量的时间和人力资源。
数值模拟试验则是通过有限元方法进行模拟,分别以其在真实加载条件下的强度、拉伸、挤压等进行计算,并将结果与实验结果进行比较,从而预测材料的疲劳寿命。
该方法具有数据处理速度快、成本较低等优点,但其模拟结果受模型精度及试验参数设置等因素的影响,需要进行多次改进和验证。
第四章铝合金车身结构疲劳寿命的影响因素铝合金车身结构的疲劳寿命受多种因素的影响。
其中,应力水平、加载模式、材料缺陷及施加频率等因素是疲劳寿命影响的主要因素。
此外,诸如环境温度、湿度和材料氧化等因素也会对其疲劳寿命产生影响。
第五章铝合金车身结构疲劳寿命的延长方法为了延长铝合金车身结构的疲劳寿命,需要采取一系列措施。
常用的措施包括:改进工艺、提高材料质量、加强零部件的设计和加工精度等。
此外,针对不同的疲劳破坏类型和部位,还需要采用相应的补救措施,例如对于裂纹的处理、加壳或补强等。
第六章结论综上所述,铝合金车身结构的疲劳寿命研究十分重要,主要围绕着疲劳机制、测试方法、影响因素和延长疲劳寿命等方面展开。
城轨交通车辆车体与车门—铝合金车体

五、铝合金车体在设计和制造中应注意的问题
铝合金车体有许多的优点,但在设计、制造中尚需注 意许多问题,如铝合金选材、铝合金结构焊接工艺的研究、 铝合金材料疲劳特性和寿命的试验、结构优化设计、刚度、 防腐蚀等问题。
1.铝合金材料的合理选择 2.铝合金车体的组装
一、铝合金材料的特性
质轻且柔软,
耐蚀性能好。
四、铝合金车体的结构
1.底架
底架是车体的基础结构,底架结构模块包括地板、边梁 (左和右)、枕梁(2根)、牵引梁(2根)组件。边梁、枕梁、 牵引梁采用连续焊接组合在一起,将地板、隔热隔声材料、 底架下管路和电线槽预先与底架组成一体,然后与侧墙和端 部模块连接,底架边梁在整个长度上与侧墙模块进行机械连 接,在底架的架车位置进行局部加强。
车体由底架、侧墙、车顶、端墙等预先装配好 的模块组成,车体总装配时,用螺栓将这些预装配 好的模块按顺序联结在一起。
车体的模块是用铝型材(占车体质量约90%) 焊接而成的,几乎所有的挤压型材都是由合金 ENAW 6005A 制成,它们是空心的。
四、铝合金车体的结构
由于强度要求,底架的牵引梁用铝合金ENAW 7020 (铝合金板和一块铝合金挤压型材)制成。某些低应力区 域由合金板 ENAW 5083制成。每车模块的每侧有5对客 室门结构和4个车窗结构,带司机室的拖车模块每侧还包 括一个司机室门框架和一个前端门框架,中间端宽度与贯 通道宽度几乎相同。
三、铝合金车体的形式
1.纯铝合金车体
(2)车体结构是板条骨架结构,用气体保护的熔焊作为连接方法。 (3)在车体结构中应用整体结构,板皮和纵向加固件构成高强度
大型开口型材。 (4)车体采用空心截面的大型整体型材,结构更加简单。型材平
行放置并总是在车体的全部长度上延伸,通过自动连续焊接进 行连接。该车体结构以具有多种多样截面的型材为基础,并充 分利用铝合金良好的机械性能。
城市轨道交通车辆全寿命周期成本分析
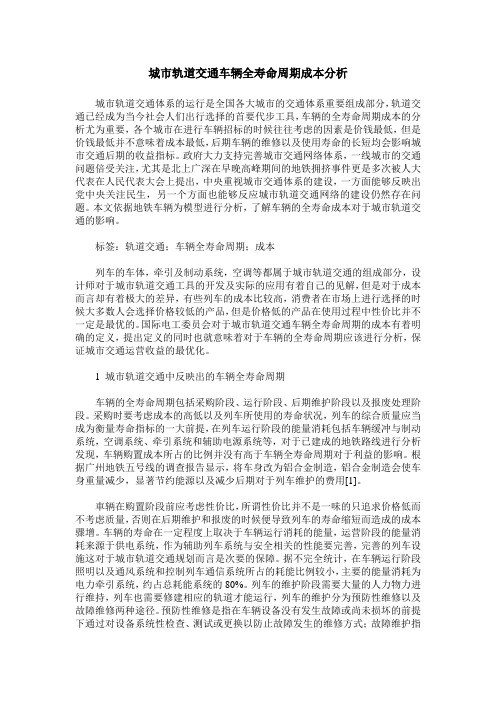
城市轨道交通车辆全寿命周期成本分析城市轨道交通体系的运行是全国各大城市的交通体系重要组成部分,轨道交通已经成为当今社会人们出行选择的首要代步工具,车辆的全寿命周期成本的分析尤为重要,各个城市在进行车辆招标的时候往往考虑的因素是价钱最低,但是价钱最低并不意味着成本最低,后期车辆的维修以及使用寿命的长短均会影响城市交通后期的收益指标。
政府大力支持完善城市交通网络体系,一线城市的交通问题倍受关注,尤其是北上广深在早晚高峰期间的地铁拥挤事件更是多次被人大代表在人民代表大会上提出,中央重视城市交通体系的建设,一方面能够反映出党中央关注民生,另一个方面也能够反应城市轨道交通网络的建设仍然存在问题。
本文依据地铁车辆为模型进行分析,了解车辆的全寿命成本对于城市轨道交通的影响。
标签:轨道交通;车辆全寿命周期;成本列车的车体,牵引及制动系统,空调等都属于城市轨道交通的组成部分,设计师对于城市轨道交通工具的开发及实际的应用有着自己的见解,但是对于成本而言却有着极大的差异,有些列车的成本比较高,消费者在市场上进行选择的时候大多数人会选择价格较低的产品,但是价格低的产品在使用过程中性价比并不一定是最优的。
国际电工委员会对于城市轨道交通车辆全寿命周期的成本有着明确的定义,提出定义的同时也就意味着对于车辆的全寿命周期应该进行分析,保证城市交通运营收益的最优化。
1 城市轨道交通中反映出的车辆全寿命周期车辆的全寿命周期包括采购阶段、运行阶段、后期维护阶段以及报废处理阶段。
采购时要考虑成本的高低以及列车所使用的寿命状况,列车的综合质量应当成为衡量寿命指标的一大前提,在列车运行阶段的能量消耗包括车辆缓冲与制动系统,空调系统、牵引系统和辅助电源系统等,对于已建成的地铁路线进行分析发现,车辆购置成本所占的比例并没有高于车辆全寿命周期对于利益的影响。
根据广州地铁五号线的调查报告显示,将车身改为铝合金制造,铝合金制造会使车身重量减少,显著节约能源以及减少后期对于列车维护的费用[1]。
地铁铝合金车体疲劳强度评估

7 8
劳强度负荷无 限寿命设计法 的要求 。
1 . 3 许 用应 力 的 确 定
( 5 )
a v 称为满负荷 比, 当 也 <1的情 况下 , 即判定焊缝 的疲
把 结构 中的最小 应力 与最大应 力之 比称之 为应力 比 R,
即:
R = —r a — i n
D r r I a 】 c
式 中: a ∥ 一 平行 于焊缝方 向的应力分量负荷 比,
( 3 )
( 4 )
式中: N 一载荷循环次数, c 一 与材料相关的常数 ,
△ 一 应力 幅 ,
a I 一垂直于焊缝方向的应力分量负荷比,
一
剪应力分量负荷比,
∥ 一平行于焊缝方向的应力分量,
[ ∥ ] 一平行 于焊缝方 向的许用应力 ,
1 疲劳 强度评定 的标准及依据
1 . 1 S —N曲线及无限寿命设 计法
( 2 )
l 6 - I
研究表明 , 材料 的疲劳 强度与 载荷 的循 环次数 有一 定 的
关系 , 用 S —N曲线表达 , 即:
Ⅳ= ( 1 )
。 上 l 茼 l
啦 } 南 I
下列公式计算E 2 J :
[ ∥】
/ /
疲劳强度的评定是车体可靠性设计的一项重要指标。
由于铝合金焊接后 , 焊缝及热影 响区 的强 度将大 大降低 , 且焊缝 中存在着各 式各样 的缺 陷及应 力集 中 , 焊缝 的疲 劳强 度将远远小于母材 的疲劳强度 , 因此 , 焊缝 的疲 劳强度将是 主 要 的评定对象 。
一
n rs —N曲线的斜率 。 图1 为铝合 金 S —N曲线E 1 J , S —N曲线表 明 , 当载荷达 到
高速列车车体结构疲劳分析与寿命评估
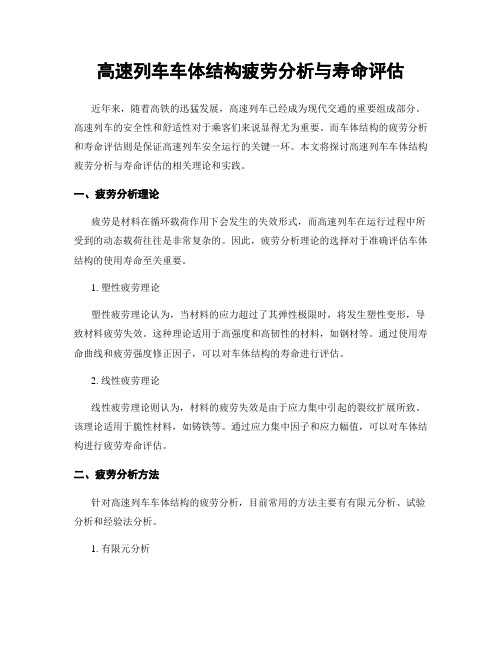
高速列车车体结构疲劳分析与寿命评估近年来,随着高铁的迅猛发展,高速列车已经成为现代交通的重要组成部分。
高速列车的安全性和舒适性对于乘客们来说显得尤为重要。
而车体结构的疲劳分析和寿命评估则是保证高速列车安全运行的关键一环。
本文将探讨高速列车车体结构疲劳分析与寿命评估的相关理论和实践。
一、疲劳分析理论疲劳是材料在循环载荷作用下会发生的失效形式,而高速列车在运行过程中所受到的动态载荷往往是非常复杂的。
因此,疲劳分析理论的选择对于准确评估车体结构的使用寿命至关重要。
1. 塑性疲劳理论塑性疲劳理论认为,当材料的应力超过了其弹性极限时,将发生塑性变形,导致材料疲劳失效。
这种理论适用于高强度和高韧性的材料,如钢材等。
通过使用寿命曲线和疲劳强度修正因子,可以对车体结构的寿命进行评估。
2. 线性疲劳理论线性疲劳理论则认为,材料的疲劳失效是由于应力集中引起的裂纹扩展所致。
该理论适用于脆性材料,如铸铁等。
通过应力集中因子和应力幅值,可以对车体结构进行疲劳寿命评估。
二、疲劳分析方法针对高速列车车体结构的疲劳分析,目前常用的方法主要有有限元分析、试验分析和经验法分析。
1. 有限元分析有限元分析是一种基于数值计算的方法,可将车体结构分割为有限个单元,通过求解单元的位移和应力状态,进而得到整个结构的应力和变形情况。
这种方法可以模拟不同工况下的载荷作用,对车体结构的疲劳寿命进行预测和评估。
2. 试验分析试验分析可以通过在车厢上设置传感器,对实际运行过程中的载荷进行采集和记录。
通过对采集到的数据进行分析,可以得到不同工况下的应力和变形情况。
这种方法适合于对现有车型的寿命评估和改进设计提供依据。
3. 经验法分析经验法分析则是基于历史数据和经验公式进行疲劳分析,适用于相似结构的寿命预测。
该方法相对简单,但准确性较低。
三、寿命评估在进行疲劳分析的基础上,寿命评估是对高速列车车体结构使用寿命的估计和预测。
寿命评估的关键是确定疲劳载荷和材料疲劳性能的参数。
城市轨道交通铝合金车体

城市轨道交通铝合金车体铝合金车体和不锈钢车体是目前使用最多的两种新型材料车体结构,铝合金车体和不锈钢车体均属于轻型整体承载结构,主体材料分别是铝合金型材、不锈钢板材等,通常采用模块化结构或焊接组装。
铝合金和不锈钢车体都有材料密度小、比强(结构的最大承载力与所耗材料重量之比)大的优点,在满足车体强度和刚度的条件下自重轻而倍受青睐。
1、铝合金材料的特性(1)质轻且柔软,能轻量化制造。
(2)强度好。
(3)耐蚀性能好。
(4)加工性能好。
(5)易于再生。
根据铝合金车体结构及制造、运用情况,选择材料时应遵循以下原则:从轻量化方面考虑,要求强度、刚度好,而重量轻;从寿命方面考虑,要求耐蚀性、表面处理性、维护保养性好;从制造工艺方面考虑,要求焊接性、挤压加工性、成型加工性高。
根据以上原则,铝合金车体主要使用5000 系列、6000系列、7000 系列的铝合金。
2、铝合金车体的特点(1)能大幅度降低车辆自重,与碳素钢车体相比,铝合金车体自重减轻30%〜35%,比强约为碳素钢车体的 2 倍。
2)有较小的密度,铝合金对冲击载荷有较高能量吸收能力3)运用大型中空挤压型材,提高车辆密封性能,提高乘坐舒适性。
(4)采用大型中空挤压型材制造的板块式结构,减少了连接件的数量和重量。
(5)减少维修费用,延长使用寿命。
3、铝合金车体的形式(1)纯铝合金车体。
纯铝合金车体可分为四种形式:①车体由铝板和实心型材制成,铝板和型材通过铝制铆钉、连续焊接、金属惰性气体点焊等进行连接。
②车体结构是板条骨架结构,用气体保护的熔焊作为连接方法。
③在车体结构中应用整体结构,板皮和纵向加固件构成高强度大型开口型材。
④车体采用空心截面的大型整体型材,结构简单。
(2)混合铝合金车体。
城轨车辆除纯铝合金车体外,还有钢底架的混合铝合金车体。
车体侧墙与底架的连接基本都采用铆接或螺栓连接的方式。
其作用有两点:一是可避免热胀冷缩带来的问题,二是取消了成本很高的车体校正工序。
铝合金材料的疲劳寿命测试方法

铝合金材料的疲劳寿命测试方法铝合金材料常用于各种工业产品和结构材料中,其疲劳寿命测试方法是评估其使用寿命和可靠性的重要手段之一。
以下将介绍几种常见的铝合金材料疲劳寿命测试方法。
一、旋转梁试验法旋转梁试验法是最常用的铝合金材料疲劳寿命测试方法之一。
该方法使用旋转梁进行试验,通过施加往复加载,观察铝合金材料在不同次数循环加载下的疲劳行为。
试验结果可以得到材料的疲劳极限、疲劳寿命和疲劳裂纹扩展速率等重要参数。
在旋转梁试验中,需要注意加载方式和加载幅值的选择。
加载方式可以选择轴向加载、弯曲加载或轴向加弯曲加载等不同方式,根据具体材料和应用情况选择最适合的加载方式。
加载幅值应根据材料的强度和载荷情况进行合理选择,以保证试验结果的准确性和可靠性。
二、往复加载试验法往复加载试验法是另一种广泛应用于铝合金材料疲劳寿命测试中的方法。
该方法使用往复加载设备,通过施加不同载荷幅值和频率进行试验,观察铝合金材料在循环加载下的疲劳响应。
试验结果可以提供材料的疲劳极限、疲劳寿命和变形行为等信息。
在往复加载试验中,需要确保加载设备的精度和稳定性,以及试验样品的准备和保护。
加载幅值和频率的选择需要根据具体应用场景和材料的实际工作条件进行合理确定,以模拟实际使用情况,确保试验结果的真实性和代表性。
三、应力比加载试验法应力比加载试验法是一种将不同振幅应力加载到铝合金材料上的方法,通过控制应力的大小和比例,评估材料在不同载荷工况下的疲劳性能。
该方法可用于疲劳极限的测定和预测材料在实际工程中的疲劳寿命。
在应力比加载试验中,需要选择合适的应力比例和加载振幅,以模拟真实工作环境中的应力状态。
同时,需要保证试验设备的精度和稳定性,以及试验样品的准备和保护,以获取准确可靠的试验结果。
总结:铝合金材料疲劳寿命测试方法可以通过旋转梁试验法、往复加载试验法和应力比加载试验法等多种方法进行。
不同的试验方法适用于不同的材料和实际工程应用场景,试验过程中需要注意加载方式、加载幅值和频率的选择,以及试验设备的准确性和试样的保护。
汽车车身结构疲劳寿命分析方法

u 车 结 疲 寿 分 方 、 身构 劳 命 析 法 L 晕 P 弓
● 温树 德
’ 汽车车 身金属 板结 构 的疲 劳失 效检 测一般 依 赖于试 车 场的跑 车试 验 。如果 发现设 计 上 存 在缺点, 在试 验 阶段 的整 车 装 配将 耗费 大量 的 试验 费用 。 且 , 果汽 车通 过 了可靠性 试验 也 而 如 很难 确定 “ 计能 力过 剩 ” 设 问题 , 国 福特 汽 车 美 公 司研 制 了 一种 计 算 机辅 助 工 程 分析 方 法 , 克
设计指导原 则如下 : 1 设 计 低应 力 影响 系数 ; .
,
2 具 有适 当的弯 曲/ 转强 度 ; . 扭 3 避 免 强度 沿车 身长 度方 向的剧 烈变 化 ; . 5 .在车 身 应 力 敏 感 区避 免 槽 、 、 点 存 孔 焊
接触位置的三维方向。在每个单位载荷下使用
步骤1 完整的车 l
l身模型
惯 性释 放 分析
应力 输
彩色
显 示
出 信息
敏 感 因 素
步 样 寿命l l 过程 面 骤0 车全 I 全 平
I 过程道路载 H 交叉或立体
I 荷数据 l l 交叉直方图
疲劳 寿 命 分析 程序
车身紧固 l I 极限车 载荷初步 一I 身紧固
“ 性 释 放 ” 法 确 定 车 身 结 构 的 时 间一 惯 方 应 力 。 该 注意 车身 结构 同时受 到 许 多载 荷 作用 。 应 试 验 表 明每 个载 荷 的 影 响 基本 在附近 位置 . 换
在;
6 避 免小 半径 尖 角和刻 槽 的存 在 。 .
句话说 , 前悬挂载荷 几乎在后悬挂 附近不引起
铝合金车体的有限元分析和结构评估方法研究

2019年(第 41卷)第 6期 doi:10.19562/j.chinasae.qcgc.2019.06.001
汽 车 工 程 Automห้องสมุดไป่ตู้tiveEngineering
2019(Vol.41)No.6
铝合金车体的有限元分析和结构评估方法研究
王万林,徐从昌,王震虎,王哲阳,李落星
(1湖南大学,汽车车身先进设计制造国家重点实验室,长沙 410082; 2湖南大学机械与运载工程学院,长沙 410082)
关键词:铝合金车体;有限元分析;广义结构刚度;结构评估方法;轻量化
AStudyonFiniteElementAnalysisandStructuralAssessment MethodforAluminumalloyVehicleBody
WangWanlin,XuCongchang,WangZhenhu,WangZheyang& LiLuoxing
基于等效结构应力的铝合金地铁车体疲劳寿命预测

基于等效结构应力的铝合金地铁车体疲劳寿命预测作者:李伟伟等来源:《计算机辅助工程》2014年第05期摘要:为评估某铝合金地铁车辆的疲劳寿命,采用美国ASME标准中的网格不敏感的主SN曲线法对该车焊缝进行疲劳寿命预测.用HyperMesh对车体进行有限元建模,并对焊缝处网格细化;用ANSYS计算焊缝处应力;运用自主开发的FEWeld软件对其进行等效结构应力的计算和疲劳寿命的预测;对疲劳寿命不符合设计要求的结构进行改进和优化,改进后结构的疲劳寿命符合设计要求.网格不敏感的主SN曲线法具有重要工程应用推广价值.关键词:地铁;焊缝建模;疲劳寿命预测;有限元;等效结构应力法; ASME标准;主SN曲线;铝合金焊接结构中图分类号: U270.2;TB115.1文献标志码: BAbstract: To evaluate the fatigue life of an aluminum subway vehicle, the weld line fatigue life of the vehicle is predicted by the meshinsensitive master SN method in ASME standard of the United States. The finite element model of the car body is built by HyperMesh and the mesh of weld lines is refined; the stress near weld lines is calculated by ANSYS; by the selfdeveloped software FEWeld, the equivalent structural stress is calculated and the fatigue life is calculated; the structures where the fatigue life cannot meet the design requirements are improved and optimized,and the fatigue life of the improved structure meets the design requirements. The meshinsensitive master SN curve method has great promotion value on engineering application.Key words: subway; weld line modeling; fatigue life prediction; finite element;equivalent stress method; ASME standard; master SN curve; aluminum welded structure引言轨道车辆车体由底架、侧墙、端墙、车顶和司机室等几部分组成,一个合格的车体不仅要满足强度和稳定性的要求,疲劳寿命也是重要指标之一.近几年来,城市轨道疲劳失效事故时有发生,不仅影响旅客安全,还造成经济损失.车体疲劳是一种车体焊接结构发生损伤的过程,在这个过程中,在循环载荷的作用下,即使应力低于材料的屈服极限,车体也会出现疲劳裂纹.一般来说,焊接接头是车体结构发生疲劳破坏的薄弱环节,因此对车体结构进行疲劳评估主要是对焊接接头进行疲劳寿命评估.随着高速列车和轻轨、地铁的发展,列车的高速化和轻量化等课题越来越受到重视.铝合金材料具有质量轻,屈服强度和抗拉强度高,耐腐蚀,以及加工性能好等优点,逐渐被广泛应用于客车车体.铝合金车体的主要特点包括:(1)大幅降低车体质量,同等条件大约是普通钢质车的30%~35%;(2)铝合金车体由大断面铝合金中空挤压型材整体焊接而成,使由底架、侧墙、端墙、车顶和司机室等组成的车体能够承受横向、纵向、垂向和扭转等载荷.本文以某铝合金轨道车辆头车为载体,对其进行有限元建模,参考EN 126631:2010标准[1],基于ANSYS和自主开发的FEWeld软件,计算车体在对称载荷作用下的疲劳寿命,并比较2种方案的分析结果.结果表明:改进结构使焊缝形状更圆滑,减少应力集中的影响,可以增加车体的疲劳寿命.1结构应力法结构应力法,又称主SN曲线法、Verity方法或网格不敏感的结构应力法. [2]该方法是美国新奥尔良大学DONG Pingsha博士基于断裂力学原理及大量焊接疲劳试验发明的计算焊缝疲劳寿命的最新的最准确的方法.该方法采用网格不敏感的结构应力计算方法及其主SN曲线模型,可以相对准确地计算出空间任意走向的焊缝的疲劳寿命. [34]1.1结构应力由于焊接接头的疲劳裂纹一般发生在焊趾处,所以研究焊趾处的应力组成极其重要.焊趾处应力由焊接引起的残余应力和远端外力引起的结构应力2部分组成.残余应力在焊缝处为自平衡力,且在结构运行过程中幅值不变,所以对结构疲劳无明显作用,而结构应力因为存在交变作用,所以是产生疲劳破坏的主要因素.[5]厚度为t的板焊趾处的结构应力分布见图1(a),将结构应力简化为弯曲应力σb和膜应力σm,见图1(b).结构应力为1.2等效结构应力由于焊接结构疲劳裂纹客观存在的特殊性,从力学机理上看,其扩展过程是与材料性能无关的纯力学行为,因此焊接结构的疲劳寿命可以应用断裂力学的理论求解. [6]用裂纹的扩展过程判定结构的疲劳强度. [5]在求解过程中定义一个概念——等效结构应力,其考虑载荷模式、板厚尺寸、焊趾缺口效应和应力集中等对疲劳寿命的影响.此外,传统的疲劳寿命评估方法以名义应力为基本参数,但对于复杂焊接结构,不管是名义应力法还是热点应力法,都存在焊接接头难以分类、SN曲线难以界定的困难.结构应力法以节点力为基本参数[7],基于节点力的计算结果对网格的敏感性比基于应力计算的低,因此节点力法的结构应力计算可实现对网格的不敏感,即对有限元网格的类型和质量要求低,在这一点上较传统计算方法具有明显优势.等效结构应力法具有更严格的理论基础.其有2项关键技术:网格不敏感的结构应力计算和等效结构应力的转化.这2项技术使其在疲劳寿命评估方面具有很大优势,例如,分析部位没有严格的有限元网格离散要求、焊趾热点部位的应力计算结果精确可靠,因此疲劳强度评定和寿命预测精度较高.4结论通过以上分析,可以得出如下结论:(1)对原结构进行改进,车体各部位在垂向载荷、纵向载荷和横向载荷这3种工况作用下,疲劳寿命均大于107,表明加宽和圆滑圆角的上盖板刚度得到协调,应力集中得到有效抑制.(2)在机车车辆焊接结构中,疲劳破坏的原因是应力集中过于严重.在结构设计过程中,千方百计降低各式各样的应力集中是提高其抗疲劳能力、增加疲劳寿命的第一要素.(3)在产品设计阶段通过有限元法对车体进行疲劳寿命评估,能够及时发现疲劳强度的薄弱部位,是提高产品设计质量的重要环节,为车体设计的进一步改进提供一定参考.参考文献:[1]EN 126631:2010Railway applicationsstructural requirements of railway vehicle bodies[S].[2]周晓坤. 大轴重货车部件强度分析与焊缝疲劳寿命预测[D]. 大连:大连交通大学, 2010.[3]王立航,方吉,马纪军. 铝合金车体疲劳寿命预测新方法及其应用[J]. 大连交通大学学报, 2010, 31(3): 911.WANG Lihang, FANG Ji, MA Jijun. Design principle and new method of fatigue life prediction for aluminumalloy carbody[J]. J Dalian Jiaotong Univ, 2010, 31(3):911.[4]何兴旺. 铝合金地铁车体性能仿真分析[D]. 大连:大连交通大学, 2010.[5]芦旭. 基于刚柔耦合的CRH3车体振动疲劳强度分析[D]. 大连:大连交通大学, 2010.[6]岳译新,刘永强,李晓峰. 基于主SN曲线法的地铁车体焊缝疲劳分析[J]. 机车电传动, 2012(5): 7981.YUE Yixin, LIU Yongqiang, LI Xiaofeng. Weld line fatigue analysis of metro carbody based on master SN curve method[J]. Electr Drive Locomotives, 2012(5): 7981.[7]王剑,兆文忠. 基于结构应力法的焊接结构优化设计[J]. 大连海事大学学报, 2011, 37(2): 124126.WANG Jian, ZHAO Wenzhong. Structural stress method based optimization design of welding structure[J]. J Dalian Maritime Univ, 2011, 37(2): 124126.[8]李晓峰,王宇,李光,等. 等效结构应力法在铁路车辆焊接结构中的应用[J]. 大连交通大学学报, 2011, 32(4): 2023.LI Xiaofeng , WANG Yu, LI Guang, et al. Application of equivalent structural stress method in weld structure of railway cars[J]. J Dalian Jiaotong Univ, 2011, 32(4): 2023.[9]刘婷婷,刘海涛,陈秉智. 不锈钢点焊地铁车车体结构稳定性分析[J]. 大连交通大学学报, 2013, 34(1): 69.LIU Tingting, LIU Haitao, CHEN Bingzhi. Structural stability analysis of weld stainless steel subway car body[J]. J Dalian Jiaotong Univ, 2013, 34(1): 69.[10]李娅娜,蓝志峰. 基于等效结构应力法的电机机座焊接结构疲劳寿命预测[J]. 大连交通大学学报, 2012, 33(3): 1013.LI Yana, LAN Zhifeng. Fatigue life prediction of motor base with equivalent structural stress method[J]. J Dalian Jiaotong Univ, 2012, 33(3): 1013.(编辑于杰)。
铝合金材料的疲劳寿命评估
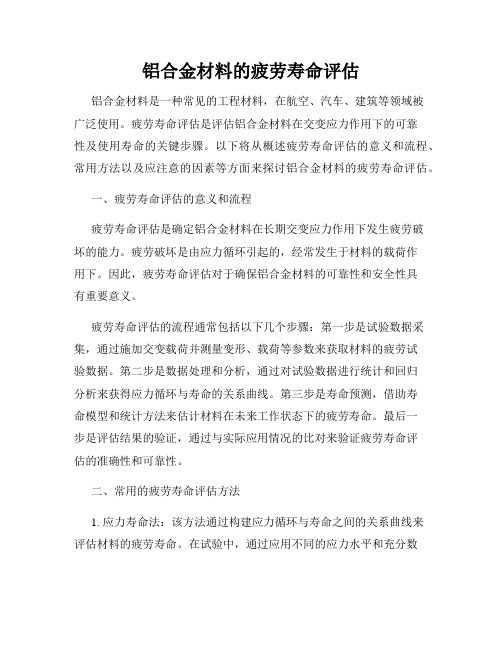
铝合金材料的疲劳寿命评估铝合金材料是一种常见的工程材料,在航空、汽车、建筑等领域被广泛使用。
疲劳寿命评估是评估铝合金材料在交变应力作用下的可靠性及使用寿命的关键步骤。
以下将从概述疲劳寿命评估的意义和流程、常用方法以及应注意的因素等方面来探讨铝合金材料的疲劳寿命评估。
一、疲劳寿命评估的意义和流程疲劳寿命评估是确定铝合金材料在长期交变应力作用下发生疲劳破坏的能力。
疲劳破坏是由应力循环引起的,经常发生于材料的载荷作用下。
因此,疲劳寿命评估对于确保铝合金材料的可靠性和安全性具有重要意义。
疲劳寿命评估的流程通常包括以下几个步骤:第一步是试验数据采集,通过施加交变载荷并测量变形、载荷等参数来获取材料的疲劳试验数据。
第二步是数据处理和分析,通过对试验数据进行统计和回归分析来获得应力循环与寿命的关系曲线。
第三步是寿命预测,借助寿命模型和统计方法来估计材料在未来工作状态下的疲劳寿命。
最后一步是评估结果的验证,通过与实际应用情况的比对来验证疲劳寿命评估的准确性和可靠性。
二、常用的疲劳寿命评估方法1. 应力寿命法:该方法通过构建应力循环与寿命之间的关系曲线来评估材料的疲劳寿命。
在试验中,通过应用不同的应力水平和充分数量的循环以获得数据,然后通过回归分析得到应力寿命曲线。
该方法适用于均匀应力循环的情况下。
2. 应变寿命法:这种方法通过应变循环与寿命之间的关系来评估材料的疲劳寿命。
在试验中,通过施加不同的应变幅值和循环次数以获得数据,然后通过回归分析得到应变寿命曲线。
该方法适用于均匀应变循环的情况下。
3. 塑性应变寿命法:该方法是针对非均匀应力或应变循环情况下的疲劳寿命进行评估。
在试验中,通过施加不同的塑性应变幅值和循环次数以获得数据,然后通过统计分析得到疲劳寿命曲线。
该方法通常用于不同应变幅值下的应力集中部位。
三、应注意的因素在进行铝合金材料的疲劳寿命评估时,需要注意以下因素:1. 材料特性:铝合金材料的化学成分和物理性质对其疲劳寿命具有重要影响。
轨道交通车辆的整体性能评估与优化

轨道交通车辆的整体性能评估与优化随着城市化进程的加快和人口数量的增加,轨道交通作为一种高效、环保的交通方式在现代城市中得到了广泛应用。
轨道交通车辆的性能评估与优化是确保运输安全和提高运行效率的关键。
本文将从轨道交通车辆的能源消耗、安全性能和乘客舒适度三个方面,探讨整体性能评估与优化的问题。
一、能源消耗的评估与优化轨道交通车辆的能源消耗是影响整体性能的重要指标之一。
能源消耗的高低既关系到运营成本,又影响城市交通的环境影响。
因此,对轨道交通车辆的能源消耗进行评估和优化对于节约能源、降低污染具有重要意义。
为了评估轨道交通车辆的能源消耗,可以采用一系列的综合指标,包括单位运输能耗、能源利用效率等。
同时,通过对车辆设计进行优化,比如减轻车体重量、提高轮轨摩擦系数等方式,可以有效降低车辆能源消耗。
此外,结合运行管理系统,实现车辆能源的动态优化也是一个很有前景的研究方向。
二、安全性能的评估与优化轨道交通车辆的安全性能是车辆运行中不可忽视的方面。
以高速列车为例,其行驶速度较高,对安全性能的要求尤为严格。
因此,评估和提升车辆的安全性能具有重要意义。
在安全性能的评估中,可以关注车辆的制动性能、防撞安全装置、车体结构强度等方面。
通过进行实验和数值仿真,可以对车辆在不同速度和复杂路况下的安全性能进行评估,并对车辆设计进行优化。
此外,结合先进的通信技术和智能控制系统,实现车辆在运行过程中的实时监测和安全预警,也是提升车辆安全性能的有效途径。
三、乘客舒适度的评估与优化乘客舒适度是衡量轨道交通车辆性能的重要指标之一。
乘客在使用轨道交通系统时,希望能够得到稳定舒适的乘坐体验。
因此,评估和提升车辆的乘客舒适度是一个不容忽视的问题。
乘客舒适度的评估可以包括车辆的振动、噪声水平、空调效果等方面。
通过采用先进的振动隔离技术、噪声控制技术和舒适性设计,可以有效提升车辆的乘客舒适度。
同时,结合车辆的运行管理系统,调整车辆运行速度和运行曲线,也可以改善车辆的乘客舒适度。
基于等效结构应力的铝合金地铁车体疲劳寿命预测

基于等效结构应力的铝合金地铁车体疲劳寿命预测李伟伟;陈秉智【摘要】为评估某铝合金地铁车辆的疲劳寿命,采用美国ASME标准中的网格不敏感的主S-N曲线法对该车焊缝进行疲劳寿命预测.用HyperMesh对车体进行有限元建模,并对焊缝处网格细化;用ANSYS计算焊缝处应力;运用自主开发的FE-Weld 软件对其进行等效结构应力的计算和疲劳寿命的预测;对疲劳寿命不符合设计要求的结构进行改进和优化,改进后结构的疲劳寿命符合设计要求.网格不敏感的主S-N 曲线法具有重要工程应用推广价值.【期刊名称】《计算机辅助工程》【年(卷),期】2014(023)005【总页数】7页(P22-28)【关键词】地铁;焊缝建模;疲劳寿命预测;有限元;等效结构应力法;ASME标准;主S-N曲线;铝合金焊接结构【作者】李伟伟;陈秉智【作者单位】大连交通大学交通运输工程学院,辽宁大连116028;大连交通大学交通运输工程学院,辽宁大连116028【正文语种】中文【中图分类】U270.2;TB115.10 引言轨道车辆车体由底架、侧墙、端墙、车顶和司机室等几部分组成,一个合格的车体不仅要满足强度和稳定性的要求,疲劳寿命也是重要指标之一.近几年来,城市轨道疲劳失效事故时有发生,不仅影响旅客安全,还造成经济损失.车体疲劳是一种车体焊接结构发生损伤的过程,在这个过程中,在循环载荷的作用下,即使应力低于材料的屈服极限,车体也会出现疲劳裂纹.一般来说,焊接接头是车体结构发生疲劳破坏的薄弱环节,因此对车体结构进行疲劳评估主要是对焊接接头进行疲劳寿命评估.随着高速列车和轻轨、地铁的发展,列车的高速化和轻量化等课题越来越受到重视.铝合金材料具有质量轻,屈服强度和抗拉强度高,耐腐蚀,以及加工性能好等优点,逐渐被广泛应用于客车车体.铝合金车体的主要特点包括:(1)大幅降低车体质量,同等条件大约是普通钢质车的30% ~35%;(2)铝合金车体由大断面铝合金中空挤压型材整体焊接而成,使由底架、侧墙、端墙、车顶和司机室等组成的车体能够承受横向、纵向、垂向和扭转等载荷.本文以某铝合金轨道车辆头车为载体,对其进行有限元建模,参考EN 12663-1:2010标准[1],基于ANSYS和自主开发的FE-Weld软件,计算车体在对称载荷作用下的疲劳寿命,并比较2种方案的分析结果.结果表明:改进结构使焊缝形状更圆滑,减少应力集中的影响,可以增加车体的疲劳寿命.1 结构应力法结构应力法,又称主S-N曲线法、Verity方法或网格不敏感的结构应力法.[2]该方法是美国新奥尔良大学DONG Pingsha博士基于断裂力学原理及大量焊接疲劳试验发明的计算焊缝疲劳寿命的最新的最准确的方法.该方法采用网格不敏感的结构应力计算方法及其主S-N曲线模型,可以相对准确地计算出空间任意走向的焊缝的疲劳寿命.[3-4]1.1 结构应力由于焊接接头的疲劳裂纹一般发生在焊趾处,所以研究焊趾处的应力组成极其重要.焊趾处应力由焊接引起的残余应力和远端外力引起的结构应力2部分组成.残余应力在焊缝处为自平衡力,且在结构运行过程中幅值不变,所以对结构疲劳无明显作用,而结构应力因为存在交变作用,所以是产生疲劳破坏的主要因素.[5]厚度为t的板焊趾处的结构应力分布见图1(a),将结构应力简化为弯曲应力σb和膜应力σm,见图1(b).结构应力为图1 焊趾处应力分布示意Fig.1 Schematic of stress near weld toe1.2 等效结构应力由于焊接结构疲劳裂纹客观存在的特殊性,从力学机理上看,其扩展过程是与材料性能无关的纯力学行为,因此焊接结构的疲劳寿命可以应用断裂力学的理论求解.[6]用裂纹的扩展过程判定结构的疲劳强度.[5]在求解过程中定义一个概念——等效结构应力,其考虑载荷模式、板厚尺寸、焊趾缺口效应和应力集中等对疲劳寿命的影响.此外,传统的疲劳寿命评估方法以名义应力为基本参数,但对于复杂焊接结构,不管是名义应力法还是热点应力法,都存在焊接接头难以分类、S-N 曲线难以界定的困难.结构应力法以节点力为基本参数[7],基于节点力的计算结果对网格的敏感性比基于应力计算的低,因此节点力法的结构应力计算可实现对网格的不敏感,即对有限元网格的类型和质量要求低,在这一点上较传统计算方法具有明显优势.等效结构应力法具有更严格的理论基础.其有2项关键技术:网格不敏感的结构应力计算和等效结构应力的转化.这2项技术使其在疲劳寿命评估方面具有很大优势,例如,分析部位没有严格的有限元网格离散要求、焊趾热点部位的应力计算结果精确可靠,因此疲劳强度评定和寿命预测精度较高.以断裂力学为理论基础,从裂纹开始形成到最终发生疲劳断裂的疲劳寿命可用式(2)实现.式中:Mkn为缺口应力放大因子,其中:r为结构中弯曲应力与结构应力的载荷比,r=Δσb/(Δσm+Δσb);MknT为纯拉(r=0)接头的 Mkn;fm和fb为无量纲函数.式(2)中的积分对af不敏感,因此可用相对裂纹长度的形式表达,其中:I(r)为载荷影响的因子,可表示为因此无量纲的I(r)函数的确定式(4)就可以用N表示为可见,结构应力是关于t和弯曲比r的函数,等效结构应力ΔSs的计算公式可表达为以等效结构应力变化范围ΔSs为参数的主S-N曲线的焊缝疲劳寿命计算公式为式(2)~(8)中:t反映板厚度的影响,可解释为实际厚度与单位厚度的比率,是一个无量纲量;Δσs为结构应力,反映应力集中的影响;I(r)反映加载模式的影响;m=3.6;Cd和h为主S-N曲线试验常数(见表1),由ASME标准提供;N为疲劳寿命的循环次数.表1 疲劳曲线参数Tab.1 Parameters of fatigue curve统计数据铁和不锈钢铝Cd h Cd h中值19 930.2 0.319 50 3 495.13 0.277 12大于95%疲劳曲线23885.8 0.319 50 4 293.19 0.277 12小于95%疲劳曲线16 629.7 0.319 50 2 845.42 0.277 12大于98%疲劳曲线28 626.5 0.319 50 5 273.48 0.277 12小于98%疲劳曲线13 875.7 0.319 50 2 316.48 0.277 12大于99%疲劳曲线34 308.1 0.319 50 6 477.60 0.277 12小于99%疲劳曲线11 577.9 0.319 50 1 885.87 0.277 12使用此方法评估疲劳寿命时,用一条主S-N曲线取代其他标准的各种不同接头的S-N曲线,从而使计算结果更加准确,更接近真实值.[8]运用主S-N曲线法进行疲劳寿命预测时,使用依据该方法开发的专用软件FE-Weld.该软件进行寿命预测的基本求解步骤如下:(1)借助HyperMesh在原有限元模型的基础上建立焊缝有限元模型并定义焊缝,在定义焊缝时记录焊缝起始节点的节点号和起始单元的单元号以及焊根处板材的厚度,导出inp格式的焊缝数据文件.(2)对定义完焊缝的有限元模型施加载荷与约束,导入到ANSYS中计算,提取计算完成后rst格式的应力结果文件.(3)将焊缝数据文件和应力结果文件导入到FE-Weld中计算.先导入数据并定义焊缝,然后计算结构应力和等效结构应力,再选取给定的载荷谱和主S-N曲线进行疲劳寿命计算.运用FE-Weld进行疲劳寿命计算对焊缝处网格质量有严格要求,特别是搭接焊缝处的网格,要求在定义焊缝时所选的单元〔图2(b)中标记的单元〕必须为四节点单元,不能出现三角形单元,尤其要注意的是在拐角处不能出现三角形单元,定义焊缝的节点与单元对应时节点数比单元数大1,见图2(b).图2 焊缝建模细节示意Fig.2 Schematic of details of weld line modeling2 车体有限元模型利用HyperMesh,依据三维几何模型建立铝合金地铁车体的有限元模型.在建立有限元模型时,根据铝合金车体的结构特点和受力特点,尽量多考虑对该车刚度和强度有贡献的结构,以最大可能地真实反映该车的实际情况.有限元模型网格以任意四节点的等参薄壳单元为主,尽量减小模型中三节点薄壳单元的数量.与梁单元和板单元相比,等参薄壳单元综合考虑构件头面上的弯曲刚度、平面刚度和曲率效应,具有较高的计算精度.[9]头车车体有限元模型单元总数975 297个,节点总数1 238 539个.头车有限元模型见图3.图3 头车有限元模型Fig.3 Finite element model of head car3 车体疲劳寿命预测3.1 疲劳载荷工况依据任务书的计算要求,该车的疲劳寿命高于107.对于实际工程中的疲劳强度设计,当应力循环次数即疲劳寿命大于107次时已经完全能够满足使用要求.对某铝合金头车车体进行疲劳寿命预测定性计算时,参考EN 12663-1:2010标准中的表15和16,即对车体垂向施加(1±0.15)g,纵向和横向分别施加±0.15g的加速度,以重力加速度的方式加在整车有限元模型中,其疲劳载荷工况见表2.表2 疲劳强度计算载荷工况Fig.2 Loading conditions for fatigue strength calculation工况工况描述 x向 y向 z向1 横向加速度±0.15g 2 垂向加速度(1±0.15)g 3 纵向加速度±0.15g边界条件:在空气弹簧座垫板处施加约束.如图3(d)所示,A,B,C和D代表4个空气弹簧坐垫的位置,约束加载方式为:A点施加垂向(y向),纵向(z向)和横向(x 向)这3个方向的平动自由度,B点施加垂向(y向)和纵向(z向)平动自由度,C点施加横向(x向)和垂向(y向)平动自由度,D点施加垂向(y向)平动自由度.3.2 重要评估焊缝位置按照任务书的要求确定车体需要评估的重要焊缝为115条,在本文中选取设计过程中比较关心的6条焊缝作为研究对象,其位置和焊缝走向见表3和图4.表3 重点评估的焊缝位置Tab.3 Weld line positions for emphatic evaluation 编号位置说明38二位端枕梁上盖板与底架下表面之间焊缝39二位端枕梁上盖板与底架下表面之间焊缝40二位端枕梁上盖板与底架下表面之间焊缝41一位端枕梁上盖板与底架下表面之间焊缝42一位端枕梁上盖板与底架下表面之间焊缝43一位端枕梁上盖板与底架下表面之间焊缝图4 重点评估的焊缝位置Fig.4 Weld line positions for emphatic evaluation 3.3 计算结果分析3.3.1 初始方案的计算结果根据铝合金地铁车体在各疲劳载荷工况下的有限元应力结果计算各工况下的结构应力,根据铝合金车体的材料和所施加的载荷选用表1中98%可靠度-2σ的主S-N 曲线(小于98%疲劳曲线的铝的Cd和h参数),计算在各工况下各焊缝达到疲劳破坏时的应力循环次数,即疲劳寿命.初始方案3个工况的疲劳寿命预测的结构应力见图5.结构应力是用来判断应力集中的[10],结构应力大或者有突变的点往往就是疲劳寿命小的点,依据这一点找到每条焊缝疲劳寿命最短的点.重点评估焊缝的疲劳寿命结果见表4.图5 初始结构应力-焊缝长度曲线Fig.5 Curves of structure stress vs weld line length of initial structure表4 重点评估焊缝的疲劳寿命预测结果Tab.4 Prediction results of weld lines for emphatic assessment焊缝编号工况1 工况2 工况3危险节点寿命/次危险节点寿命/次危险节点寿命/次38 974863 1.369 64E+9 974862 2.111 45E+8 974871 6.391 09E+11 39 975024 7.452 89E+7 974881 1.326 18E+7 974881 3.877 63E+10 40 974786 1.208 17E+9 974785 2.317 59E+8 974794 6.261 26E+11 41 974099 1.711 59E+9 974098 1.713 60E+8 974107 3.041 18E+8 42 975295 1.661 42E+8 974424 9.087 97E+6 974424 2.143 72E+6 43520071 5.457 16E+8 974404 1.719 44E+8 974413 3.171 40E+83.3.2 改进设计方案的计算结果依据车体初始设计方案的疲劳寿命预测结果对寿命未达到要求的部位,即一位端枕梁中间部位和第42条焊缝所在位置,对一位端和二位端枕梁上盖板形状进行优化(见图6),增加其宽度并圆滑圆角,以减小应力集中,形成车体改进设计方案.对头车的疲劳寿命进行重新计算,改进方案焊缝结构应力-焊缝长度曲线见图7,改进结构重点评估焊缝的疲劳寿命预测结果见表5.与原方案相比,改进方案的结构应力曲线更圆滑,说明结构应力变化更缓和,但是,焊缝结构应力仍存在突变和激增.查看模型发现,突变点的产生是由于底架地板下存在支撑筋板,支撑筋板对焊缝的结构应力存在影响,因此在焊缝设计时也可以通过改变支撑筋板的板厚对模型进行改进.改进方案的疲劳寿命均有所提高并大于107,通过初始设计方案与改进设计方案结果对比可以发现,枕梁上盖板的改进使得该处焊缝的疲劳寿命有所增加,因此改进结构并圆滑圆角,可以改善应力集中,有效提高车体的疲劳寿命.图6 改进结构重点评估的焊缝位置Fig.6 Positions of weld lines of improved structure for emphatic assessment图7 改进结构第43条焊缝结构应力-焊缝长度曲线Fig.7 Curves of structure stress vs weld line length of 43rd weld line of improved structure表5 改进结构重点评估焊缝的疲劳寿命预测结果Tab.5 Prediction results of weld lines of improved structure for emphatic assessment工况1 工况2 工况3编号焊缝位置危险节点寿命/次危险节点寿命/次危险节点寿命/次38 二位端枕梁上盖板与底架下表面之间焊缝 989985 3.600 73E+10 989997 2.91762E+8 989999 8.051 04E+11 39 二位端枕梁上盖板与底架下表面之间焊缝990778 1.45 142E+9 989922 1.975 96E+7 989922 2.324 08E+11 40 二位端枕梁上盖板与底架下表面之间焊缝 989900 1.560 61E+9 989906 3.016 03E+8 989908 7.932 24E+11 41 一位端枕梁上盖板与底架下表面之间焊缝 987408 2.042 19E+9 987415 2.276 01E+8 987396 4.063 97E+8 42 一位端枕梁上盖板与底架下表面之间焊缝 991335 2.222 58E+9 987464 1.560 59E+7 991327 1.207 50E+7 43 一位端枕梁上盖板与底架下表面之间焊缝 988045 2.15316E+10 988057 2.241 13E+8 988038 4.306 17E+84 结论通过以上分析,可以得出如下结论:(1)对原结构进行改进,车体各部位在垂向载荷、纵向载荷和横向载荷这3种工况作用下,疲劳寿命均大于107,表明加宽和圆滑圆角的上盖板刚度得到协调,应力集中得到有效抑制.(2)在机车车辆焊接结构中,疲劳破坏的原因是应力集中过于严重.在结构设计过程中,千方百计降低各式各样的应力集中是提高其抗疲劳能力、增加疲劳寿命的第一要素.(3)在产品设计阶段通过有限元法对车体进行疲劳寿命评估,能够及时发现疲劳强度的薄弱部位,是提高产品设计质量的重要环节,为车体设计的进一步改进提供一定参考.参考文献:【相关文献】[1]EN 12663-1:2010 Railway applications-structural requirements of railway vehicle bodies[S].[2]周晓坤.大轴重货车部件强度分析与焊缝疲劳寿命预测[D].大连:大连交通大学,2010.[3]王立航,方吉,马纪军.铝合金车体疲劳寿命预测新方法及其应用[J].大连交通大学学报,2010,31(3):9-11.WANG Lihang,FANG Ji,MA Jijun.Design principle and new method of fatigue life prediction for aluminum-alloy car-body[J].J Dalian Jiaotong Univ,2010,31(3):9-11.[4]何兴旺.铝合金地铁车体性能仿真分析[D].大连:大连交通大学,2010.[5]芦旭.基于刚柔耦合的CRH3车体振动疲劳强度分析[D].大连:大连交通大学,2010. [6]岳译新,刘永强,李晓峰.基于主S-N曲线法的地铁车体焊缝疲劳分析[J].机车电传动,2012(5):79-81.YUE Yixin,LIU Yongqiang,LI Xiaofeng.Weld line fatigue analysis of metro carbody based on master S-N curve method[J].Electr Drive Locomotives,2012(5):79-81.[7]王剑,兆文忠.基于结构应力法的焊接结构优化设计[J].大连海事大学学报,2011,37(2):124-126.WANG Jian,ZHAO Wenzhong.Structural stress method based optimization design of welding structure[J].J Dalian Maritime Univ,2011,37(2):124-126.[8]李晓峰,王宇,李光,等.等效结构应力法在铁路车辆焊接结构中的应用[J].大连交通大学学报,2011,32(4):20-23.LI Xiaofeng ,WANG Yu,LI Guang,et al.Application of equivalent structural stress method in weld structure of railway cars[J].J Dalian Jiaotong Univ,2011,32(4):20-23.[9]刘婷婷,刘海涛,陈秉智.不锈钢点焊地铁车车体结构稳定性分析[J].大连交通大学学报,2013,34(1):6-9.LIU Tingting,LIU Haitao,CHEN Bingzhi.Structural stability analysis of weld stainless steel subway car body[J].J Dalian Jiaotong Univ,2013,34(1):6-9. [10]李娅娜,蓝志峰.基于等效结构应力法的电机机座焊接结构疲劳寿命预测[J].大连交通大学学报,2012,33(3):10-13.LI Yana,LAN Zhifeng.Fatigue life prediction of motor base with equivalent structural stress method[J].J Dalian Jiaotong Univ,2012,33(3):10-13.。
基于BS 7910—2019标准的地铁车辆车体焊缝裂纹安全寿命评估

基于BS 7910—2019标准的地铁车辆车体焊缝裂纹安全寿命评估陈朝;张枝森【期刊名称】《城市轨道交通研究》【年(卷),期】2024(27)S01【摘要】[目的]针对上海轨道交通铝合金车体焊接裂纹问题,探索科学合理的裂纹安全评估方法,这对保障列车的安全运营具有重要意义。
[方法]通过BS 7910—2019中失效评估图和断裂力学理论,构建了一套适用于铝合金车体焊缝裂纹的安全寿命评估模型,并以上海轨道交通01A01型列车TC(带司机室拖车)牵引梁的10 mm焊缝表面裂纹为评估对象,进行铝合金车体焊缝裂纹安全寿命评估实践。
[结果及结论]该车车体焊缝裂纹尺寸处于可接受的安全范围内,安全临界裂纹尺寸为45.8 mm,剩余安全寿命为3.8年。
对该裂纹可采取每半年检查1次的维保策略,在列车退役前不必进行其他修复措施。
评估模型已考虑到车体结构及载荷的复杂性,采取的保守估计方法能在确保安全性的前提下做到定量预测。
评估模型可为生产实践提供指导,对裂纹状态管控红线的划定具有重要价值。
建议在列车大修时,对车体进行全面的状态评估,包括车体探伤、材料分析、载荷数据收集,为后续裂纹安全寿命评估积累基础信息。
【总页数】6页(P12-17)【作者】陈朝;张枝森【作者单位】上海地铁维护保障有限公司车辆分公司【正文语种】中文【中图分类】U270.3【相关文献】1.基于标准BS7910的管道螺旋焊缝缺陷评估方法研究2.基于BS7910标准的X70钢环焊缝超声相控阵检出埋藏缺陷的安全评定3.基于BS标准与ASME标准的不锈钢地铁车辆车体关键焊缝疲劳强度分析4.基于BS7910对含裂纹T型板的安全性评估研究5.基于标准BS 7910的某车型车体服役寿命评估因版权原因,仅展示原文概要,查看原文内容请购买。
- 1、下载文档前请自行甄别文档内容的完整性,平台不提供额外的编辑、内容补充、找答案等附加服务。
- 2、"仅部分预览"的文档,不可在线预览部分如存在完整性等问题,可反馈申请退款(可完整预览的文档不适用该条件!)。
- 3、如文档侵犯您的权益,请联系客服反馈,我们会尽快为您处理(人工客服工作时间:9:00-18:30)。
构,
、侧墙、
车顶等主要结构
。
整备状态下的车体质量m1 (mass of the car body
收稿日期2018-08-10 作者筒介:左亮(1983-),男,工程师。
图1车体坐标系
3服役寿命评估流程
服役寿命评估流程见图2。
-1 -
铁道车辆 第57卷第6 C 2019年6月
资料收集与分析
图2服役寿命评估流程
综述$述评
铁道车辆 第57卷第6期2019年6月
文章编号:1002-7602(2019)06-0001-03
城轨车辆铝合金车体结构服役寿命评估方法
左亮",任玉鑫2,阎锋2,汤劲松2,龚晓波2,高超2
(1.广12铁集团有限公司,广东广州510330; 2.中车青岛?方车辆研究所有限公司,山东青岛266031)
当时,N, =5
•
106
(亍^')) !
( — )!1 5
;
当! % △九时,不产生疲劳损伤#
式中:",------第/级应 围的循环次数;
N——第i级应 围相对应的 寿命(失效
循环次数);
!--- 第/级应力范围;
△死——基准疲劳强度(2X106次循环);
AffD 常
限(5X106次循环);
----
阶段有必要对铝合金车体结构的服役寿命进行评估,
以确定城轨车辆铝合金车体结构设计寿命到期后是延
长服役时间还是直接更换#但是,迄今 国内 J 无标准的铝合金车体结构服役寿命评估方法 ,因此,必
铝合金车体结构服役寿命评估
的研究,规
范城轨车辆铝合金车体结构服役寿命评估方法#
城轨车辆铝合金车体结构服役寿命评估方
统计数据,确定设计寿命周期内 上下车引起的载
变化范围等级 循环次数#
根据Palmgren-Miner 计算疲劳载荷工况中
个
生的损伤,
有
生的
损伤得到总损伤。首先根据各部位的结构
应力
,从EN 1999—1—3—2007附录J中选取对应的
△旷N曲线,图3
公式(1)计算总损伤Dq:
△旷N曲线;后
当时,N,= 2 • 106 (学)1 ;
致,记录两者的差异;
(2) 检查车体结构如牵引梁、枕梁、车钩梁、侧梁、
地板等
腐蚀部位的腐蚀 ,若存在腐蚀,记
录腐蚀 ,并测量腐蚀构件的 变化;
(3) 对车体结构如牵引梁、枕梁、车钩梁、侧梁、门
、窗角、底架设
位置、端墙等
ቤተ መጻሕፍቲ ባይዱ生的
部位进行无损探伤,检查有无结构缺陷或 :。
4.3基于有限元的疲劳分析
根据4. 1,4. 2条收集的资料和获取的信息建立车
4服役寿命评估方法
4.1资料收集与分析
(1) 收集车体主要设计技术参数、车体结构图样、
车体设 量 心信息;
(2) 收集检修记录并进行分析,识别车体结构有 无修补以及检修过程中发现的危险部位,若车体结构
进行过修补,需收集修补相关图样信息;
(3) 收集至少一周的客流量信息,分析车体的实
际承载状态,车辆一周主要
法,2016年2月,广州地铁集团有限公司立项 广
州地铁1号线地铁铝合金车体结构的服役寿命 :。
项目制定了详细的
,经过近2年的时间,各项
到了预期目标#
用该项目 的成
!
国内 车体结构服役寿命评估 !
in working order m1):完全装配好的车体与整备品及
量之和。
额定有效载荷!3 (rated payload !3 ):坐席和站
有特定功能的装置,如空调、变压器、变流器等。
腐蚀(corrosion):由化学及电化侵蚀导致的材料
表面所发生的变化。
2坐标系
编制了城轨车辆铝合金车体结构服役寿命评估方法,
以期
城轨车辆铝合金车体结构服役寿命评
估
定。
1术语和定义
车体坐标系如图1所示。X轴(对应于车体纵轴) 正 位于运行 ;Z轴(对应于车体竖直轴)正方 向指向上;y轴(对应于车体横轴)位于水平面,与x 轴和z轴组成一个右手坐标系#
限(108次循环);
!1——S-N双对数折线的
(第1段);
!——S-N双对数折线的
(第2段)
4.4 基于
的疲劳寿命分析
4.4.1 线路试验
试验线路应为城轨车辆实际运行的线路 #试验车
载荷状态等级二
载荷状态等级三
注:为控制线路试验次数,载荷状态等级以不超过3个等级为宜#
表2 一周乘客上下车引起的载荷变化范围 等级及循环次数统计表
乘客上下车引起的 变化范围等级
变化 围等级
变化范围 (以的百分
比表示)/%
一周循环次数
变化 围等级二
变化 围等级三
•2•
4.2现场检查
(1) 检查实车车体结构与图样是否一致,若不一
等级
占的
里程比例和运营里程统计表示例见表1, 一周 上 下车引起的 变化范围等级及循环次数统计表示例
见表2 ;
(4) 收集运营里程信息,计算车辆的年运营里程#
表1车辆一周主要载荷状态等级及其所占 的里程比例和运营里程统计表
主要载荷 状态等级
等级
大小
以的
所占里程
比例/%
百分比表示)/%
运营里 程/km
城轨车辆(urban rail vehicle):在城市轨道线路上
运营,用于运
的单元载运 #
车体(car body):容纳乘客、整备品等,由转向架
,主要
用,是车辆的一个
#
铝合金车体(aluminium alloy car body):车体承
或大 用铝合金制成的车体#
车体结构(body structure):车体的主要承载结
摘要:介绍了城轨车辆KL金车体结构服役寿命评估方法的编制背景及内容%
关键词:城轨车辆;KL金车体;服役寿命;评估
中图分类号:U271
文献标志码:B
目前,铝合金车体结构在国内各个城市轨道交通
系统中的应用非常广泛,在广州地铁、上海地铁、深圳
地铁等地铁公司均已运用接近或超过20年,即将面临 大量铝合金车体结构设计寿命到期的问题#因此,现
席乘客质量之和,乘客质量取60 kg/人,站席乘客按6 ./m2计算。
超常有效载荷(exceptional payload !D):坐席
量, 9人/m2计#
量 60kg/ ,
服役寿命(service life):车体结构可经济使用的
时间期限或 有者实际使用的时间期限#
车体设备(car body equipment):安装在车体上具
体有限
#
应至少包括惯性载荷工况和乘客上
下车 #
:(1)丄
,士 0. 15gJ
!1 +叫),作用107次循环;(2)(方向,士 0. 15gJ
(!1+!3),作用 10* 次循环;(3))方向,(1 士 0. 15)g
J(!1+!3),作用10*次循环。各
。乘
客上下车工况:根据4.1条获得的客流量和运营里程