LCD 阵列工艺技术介绍
TFTLCD阵列工艺介绍解析ppt

光学材料
如液晶、彩色滤光片等,用于实现 图像显示。
制程中的工艺技术
光刻技术
刻蚀技术
薄膜淀积技术
离子注入技术
其他技术
利用光学曝光将设计好 的电路图案转移到半导 体或导体材料上。
通过化学或物理方法将 不需要的材料去除,形 成电路和元件结构。
在半导体或导体表面形 成一层或多层薄膜,以 实现电子元件的功能。
tftlcd阵列工艺介绍解析ppt
xx年xx月xx日
目 录
• tftlcd阵列工艺简介 • tftlcd阵列工艺制程 • tftlcd阵列工艺技术特点 • tftlcd阵列工艺应用 • tftlcd阵列工艺的未来展望
01
tftlcd阵列工艺简介
tftlcd定义
显示屏幕的构成
TFT-LCD(Thin-Film Transistor Liquid Crystal Display)是薄膜晶体管液晶显示 器的英文缩写,它是一种被动式矩阵液晶 显示器,由彩色滤光片、偏光片、TFT( 薄膜晶体管)等部件构成。
医疗器械应用
随着医疗器械的不断发展,TFT-LCD技术将越来越被广泛应用于 医疗设备和器械中,例如医用监护仪、彩超等。
AR/VR领域
随着AR/VR技术的不断发展和普及,TFT-LCD技术将在这个领域发 挥越来越重要的作用,例如头戴式显示器等设备。
THANKS
感谢观看
加省电并具有更长的续航时间。
响应速度快
03
TFT-LCD的响应时间相对较快,能够在短时间内完成图像切换
,从而提高用户的交互体验。
工艺技术的不足
成本高
由于TFT-LCD阵列工艺的生产过程复杂,需要精密的设备和原 材料,因此其成本相对较高。
LCD基础知识及制造工艺流程介绍

02
LCD制造工艺流程
玻璃基板加工
玻璃基板清洗
去除玻璃表面的杂质和 污垢,保证基板的洁净
度。
涂布光刻胶
在玻璃基板上涂布光刻 胶,用于保护下面的材
料。
曝光与显影
通过曝光和显影,将光 刻胶上的图案转移到玻
璃基板上。
去胶和蚀刻
去除多余的光刻胶,并 对玻璃基板进行蚀刻处
理,形成像素阵列。
彩色滤光片制作
后视镜
部分汽车后视镜采用LCD显示屏, 提高夜间或恶劣天气下的可视性。
LCD在其他领域的应用
医疗器械
工业控制
LCD技术在医疗设备中广泛应用,如 监护仪、超声波诊断仪等,提供高清 晰度的图像。
在工业自动化领域,LCD显示屏用于 各种控制面板和仪器仪表,方便操作 和维护。
航空航天
LCD显示屏在航空航天领域用于飞行 控制、导航系统等关键部位,确保安 全可靠。
LCD的工作原理
要点一
总结词
LCD的工作原理主要涉及到背光板、液晶层和偏振片等组 件的作用。当电流通过背光板时,会产生光线,光线经过 液晶层和偏振片调制后形成图像。不同的LCD类型和结构 在具体工作原理上略有差异。
要点二
详细描述
LCD的基本工作原理是利用液晶的物理特性进行光调制。 背光板负责提供均匀分布的光线,这些光线随后穿过液晶 层。液晶分子在电场的作用下发生排列变化,对光线进行 调制,最后通过偏振片,形成可以观察到的图像。不同的 LCD类型在具体结构和工作原理上略有差异,例如彩色 LCD需要额外的彩色滤光片来生成彩色图像。
像素密度
像素密度,也称为分辨率密度,是指每英寸屏幕中的像素数 ,它反映了屏幕的精细程度。像素密度越高,显示效果越细 腻。
LCD_阵列工艺技术介绍

CH-DE
7
三、ARRAY基板的工艺流程
工艺名称 洗净 溅射(SPUTTER) P-CVD PR/曝光 湿刻(WE) 干刻(DE) 剥离 工艺目的 清洁基板表面,防止成膜不良 成Al膜、Cr膜和ITO膜 成a-Si膜、n+a-Si膜和SiNx膜 形成与MASK图案相一致的光刻胶图案 刻蚀掉未被光刻胶掩蔽的金属膜 刻蚀掉未被光刻胶掩蔽的非金属膜 去掉残余的光刻胶
工艺腔体 压力控制
真空排气 空排气
除害装置 (scrubber) )
泵
21
剥离
1次剥离 冲淋
2次剥离 US Dip
1次 rinse 循环冲淋
2次 rinse 纯水冲淋
干燥 A/K
剥离液
Cascade
剥离液
US
循环水
纯水
DA
22
四、TN与SFT工艺对比
G工程 (Gate) I工程 (Island) D工程 (Drain) C工程 (Contact) PI工程 (Pixel)
Array工程
[GLASS]
4Mask 工程名 所需时间 lot构成 受入洗净 20 G-Sputter 36 G-PR 70 178 G-WE 28 PR剥离 24 成膜前洗净 20 1stSiNx-CVD 25 成膜前洗净 20 3层-CVD 50 成膜前洗净 20 D-Sputter 40 579 D/I-PR 70 DI-WE 40 I/PR-DE 120 D2-WE 30 CH-DE 120 PR剥离 24 成膜前洗净 20 PA-CVD 30 C-PR 70 354 C-DE 210 PR剥离 24 成膜前洗净 20 PI-Sputter 31 PI-PR 70 PI-WE 32 287 PR剥离 24 退火前洗净 20 退火 90 总计: 1398 5Mask 工程名 所需时间 lot构成 受入洗净 20 G-Sputter 36 G-PR 70 G G-WE 28 PR剥离 24 成膜前洗净 20 1stSiNx-CVD 25 成膜前洗净 20 I 3层-CVD 50 I-PR 70 I-DE 120 I-剥离 24 成膜前洗净 20 D-Sputter 40 D-PR 70 D D-WE 40 PR剥离 24 CH-DE 120 成膜前洗净 20 PA-CVD 30 C C-PR 70 C-DE 210 PR剥离 24 成膜前洗净 20 PI-Sputter 31 PI-PR 70 PI PI-WE 32 PR剥离 24 退火前洗净 20 退火 90 总计: 1462
制屏工程工艺简介

2、边框胶涂布 2.1目的:为了防止液晶泄露,在CF基板四周涂上 边框胶,使TFT和CF基板通过边框胶而粘 接在一起。 2.2原理:通过激光变位计对玻璃基板表面不平度 的探测,来进行边框胶的涂布。方法是 笔划法,加上一定的压力,使注射笔画 出所要求的图形。
3、边框胶干燥 3.1目的:通过加热板,使CF基板表面均匀受热, 使边框中的溶剂充分挥发。
通过加压和减压的压力差,让封止剂恰 当地收缩入封口内,再通过紫外光的作 用,使其本身发生化学交连作用,形成 牢固的封口。
18
液晶洗净
• 目的:液晶洗净是将液晶盒表面残留的 一些液晶及其它污物除掉,然后才能直 接贴上偏光片制成液晶显示器成品。
19
二次退火
• 原理:由于在液晶注入过程中液晶分子 的有序排列被打乱,需重新形成有序排 列。本工序即在常压下把液晶盒加热到 120℃,并保持90分钟,使液晶完全成为 液体状态,从炉中取出后,立即把液晶 盒放到急冷装置中,用5米/秒以上的强风, 在常温下急吹10分钟,通过快速降温, 使其回到液晶状态,分子重新形成一致 的 有序排列。
31
终检
• 目的:对液晶屏进行检查,将质量合格 的屏转入模块分厂。
• 原理:给液晶屏加上电信号,通过不同 的检查画面,对屏进行等级分类。
32
4、UV/O3洗净 4.1目的:对一次划片及倒棱和倒角时发生在基板上的玻 璃碎屑进行清除。 4.2原理:UV清洗是利用点亮低压水银灯时发生活性化 氧气,使其与基板上的有机物发生学反应, 变成挥发物除去。
4
取向(PI)工位
基本流程: PI前洗净→PI印刷→PI预烘→PI主烘 1、PI前洗净
1.1目的: 用化学和物理的方法去除TFT、CF表面灰尘等 污染,避免PI印刷不良。
TFT-LCD技术及生产工艺流程简介
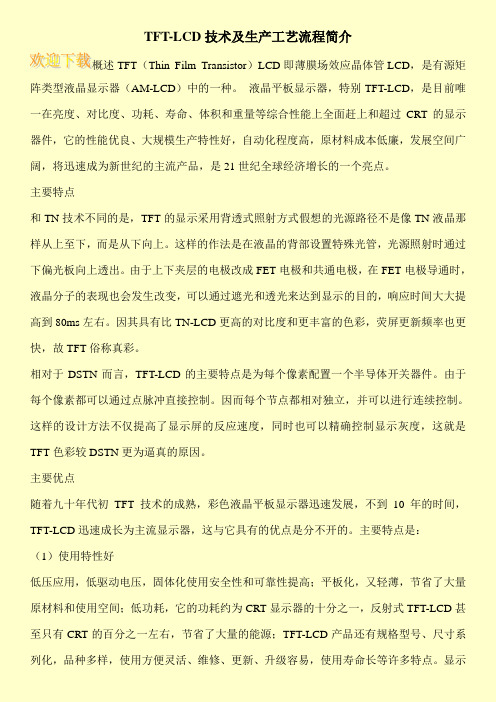
TFT-LCD技术及生产工艺流程简介概述TFT(Thin Film Transistor)LCD即薄膜场效应晶体管LCD,是有源矩阵类型液晶显示器(AM-LCD)中的一种。
液晶平板显示器,特别TFT-LCD,是目前唯一在亮度、对比度、功耗、寿命、体积和重量等综合性能上全面赶上和超过CRT的显示器件,它的性能优良、大规模生产特性好,自动化程度高,原材料成本低廉,发展空间广阔,将迅速成为新世纪的主流产品,是21世纪全球经济增长的一个亮点。
主要特点和TN技术不同的是,TFT的显示采用背透式照射方式假想的光源路径不是像TN液晶那样从上至下,而是从下向上。
这样的作法是在液晶的背部设置特殊光管,光源照射时通过下偏光板向上透出。
由于上下夹层的电极改成FET电极和共通电极,在FET电极导通时,液晶分子的表现也会发生改变,可以通过遮光和透光来达到显示的目的,响应时间大大提高到80ms左右。
因其具有比TN-LCD更高的对比度和更丰富的色彩,荧屏更新频率也更快,故TFT俗称真彩。
相对于DSTN而言,TFT-LCD的主要特点是为每个像素配置一个半导体开关器件。
由于每个像素都可以通过点脉冲直接控制。
因而每个节点都相对独立,并可以进行连续控制。
这样的设计方法不仅提高了显示屏的反应速度,同时也可以精确控制显示灰度,这就是TFT色彩较DSTN更为逼真的原因。
主要优点随着九十年代初TFT技术的成熟,彩色液晶平板显示器迅速发展,不到10年的时间,TFT-LCD迅速成长为主流显示器,这与它具有的优点是分不开的。
主要特点是:(1)使用特性好低压应用,低驱动电压,固体化使用安全性和可靠性提高;平板化,又轻薄,节省了大量原材料和使用空间;低功耗,它的功耗约为CRT显示器的十分之一,反射式TFT-LCD甚至只有CRT的百分之一左右,节省了大量的能源;TFT-LCD产品还有规格型号、尺寸系列化,品种多样,使用方便灵活、维修、更新、升级容易,使用寿命长等许多特点。
TFTLCD阵列工艺介绍 ppt课件

曝光原理
FlyEye
光源
CCD
弧状Slit Mask
横倍率
台形 Mirror
X非线形
凸面 Mirror
凹面 Mirror
Scan
16
图11 曝光原理示意图
TFTLCD阵列工艺介绍
湿刻原理
■湿刻是通过对象材料(一般为金属导电膜)与刻蚀液之间的化学反应,对对象材 料进行刻蚀的过程。
■湿刻的过程 刻蚀液在对象物质表面的移送阶段
①初期状态
② 膨润·界面浸透
③ 溶解
光刻胶
膜
图14 剥离原理示意图
19
2.3 阵列基板的制造工艺流程
4mask
G-SP G-PR G-WE G-PR剥离 1st SiN CVD 三层CVD D-SP DI-PR D1-WE I/PR DE D2-WE CH-DE DI-PR剥离
PA-CVD C-PR C-DE
C-PR剥离 PI-SP PI-PR PI-WE
PI-PR剥离
G-SP G-PR G-WE
5mask G-PR剥离
1st SiN-CVD 三层CVD I-PR I-DE I-PR剥离 D-SP D-PR D-WE CH-DE D-PR剥离
图15 4mask和5mask工艺流程图
PA-CVD C-PR C-DE
TFTLCD阵列工艺介绍
1
TFTLCD阵列工艺介绍
一、TFT-LCD的基本构造 二、 ARRAY工艺简介 三、 阵列检查介绍
2
TFTLCD阵列工艺介绍
电路部件
偏光板
图1 TTFFTT--LCLDC液D晶M显o示d屏u的le构造
3
TFTLCD阵列工艺介绍
TFT-LCD阵列工艺介绍解析

表6 膜厚check项目
工程 G绝缘膜 (G-SiNx) DIPR (3层CVD后) C-PR (PA-SiNx) 测量项目 G-SiNx膜厚 G-SiNx、a-Si、n+ a-Si三层膜 厚 PA-SiNx膜厚
31
检测原理: 光线经过透明薄膜表面进行反射时,由于光线在薄膜上下表面均产 生反射,因此反射光产生光程差Δ(图1所示)。当入射光为线偏光时, 反射光为椭偏光。根据光线反射前后偏振状态的改变,可以测量薄膜的光 学参数和膜厚,这种方法叫做Ellipsometry法(椭圆偏光解析法)。
倾斜角θ
Channel长L
Resist
1.5um 残膜厚T
Drain
Gate
26
3.4 自动外观
检查装置:自动外观测定装置(AOI) 原理: 本装置通过对基板上形成的图案进行对比检查, 检测出制造过程中发生的各种类型的缺陷.
表5 自动外观check项目
工程 G-PR DIPR IDE C-PR PIPR 测量项目 G Mask起因共通缺陷检查 DI Mask起因共通缺陷检查 DI Mask起因(沟道部分)共通缺陷检查 C Mask起因共通缺陷检查 PI Mask起因共通缺陷检查
MFC MFC MFC
gas flow
gas box
除害装置
Dry pump
图9 PCVD成膜示意图
14
2.2 阵列基板的制造原理
PR•曝光原理
膜 Photolithography 工程 基板
① Photoresist涂布 ② 曝光 ③ 显影
图10 PR工程示意图
15
Photoresist
2.2 阵列基板的制造原理
AMP
液晶材料与技术(12)——LCD工艺技术讨论—阵列2

快
慢
慢
线宽控制
高
低
低
形状控制
低
高
高
液晶材料与技术
49
在刻蚀过程中若有气泡产生,在刻蚀的前半阶 段必须要选择有除气泡功能的喷淋方式。否则 ,气泡被吸附在膜层上,具有与Mask相似的功 能,从而容易导致刻蚀残余发生;而在刻蚀的 后半阶段,由于刻蚀对象物质露出的部分较少 ,气泡比较难以被吸附在膜层上,此时根据性 能要求选择其他的刻蚀方式。
液晶材料与技术
26
(2)反射镜投影一次曝光 大直径透镜制作,控制球面像差等非常困难,而反射
镜一次曝光是由反射镜替代透镜,将掩膜图形一次投 影转写在玻璃基板上。 由光源发出的光照射掩膜板,通过掩膜板的光在一对 凹面镜和凸面镜,以及台形发射镜的联合反射作用下 ,最终将掩膜图形转写在玻璃基板上。 由于成像区域仅限于具有一定宽度限制的圆弧状的图 形,要将整个掩膜图形转写在玻璃基板上,需要掩膜 板和玻璃基板之间进行整体扫描。
液晶材料与技术(12)
——LCD工艺技术2
■ 阵列关键工艺 ——曝光与显影、刻蚀、
光刻胶剥离与退火
光刻技术主要由清洗、光刻胶涂布、坚 膜、曝光、显影、 湿刻(金属膜)或干刻(非金属膜) 、剥离等工艺组成。
液晶材料与技术
2
曝光是精密地将掩膜板上的图形转写到光刻胶上的光 化学反应。
过程涉及的主要对象有镀膜的基板、清洗设备、光刻 胶、涂胶机、掩膜板、曝光机、显影液及显影设备、 坚膜设备等多个方面。
在TFT阵列制作工艺中,根据不同的膜一般需要多次曝 光。第5代以上的TFT-LCD生产线的曝光次数已经减少 到了4次,第7代生产线的曝光工艺已经减少到了3次。
随着玻璃基板的增大,对曝光技术不断提出技术挑战 ,改进提高曝光技术是TFT技术进步的重大课题。
阵列工艺介绍
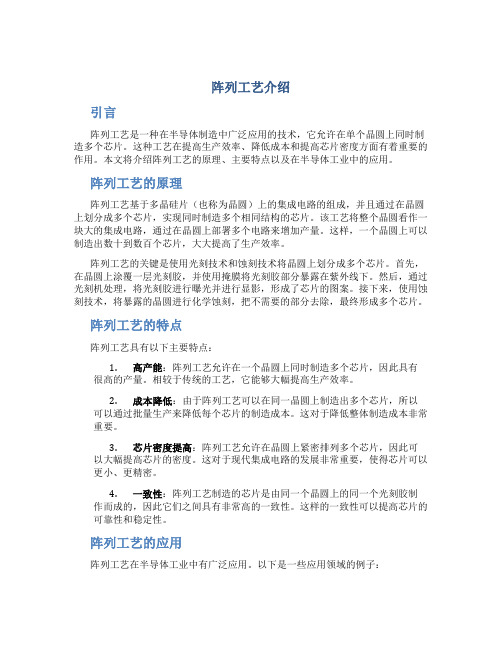
阵列工艺介绍引言阵列工艺是一种在半导体制造中广泛应用的技术,它允许在单个晶圆上同时制造多个芯片。
这种工艺在提高生产效率、降低成本和提高芯片密度方面有着重要的作用。
本文将介绍阵列工艺的原理、主要特点以及在半导体工业中的应用。
阵列工艺的原理阵列工艺基于多晶硅片(也称为晶圆)上的集成电路的组成,并且通过在晶圆上划分成多个芯片,实现同时制造多个相同结构的芯片。
该工艺将整个晶圆看作一块大的集成电路,通过在晶圆上部署多个电路来增加产量。
这样,一个晶圆上可以制造出数十到数百个芯片,大大提高了生产效率。
阵列工艺的关键是使用光刻技术和蚀刻技术将晶圆上划分成多个芯片。
首先,在晶圆上涂覆一层光刻胶,并使用掩膜将光刻胶部分暴露在紫外线下。
然后,通过光刻机处理,将光刻胶进行曝光并进行显影,形成了芯片的图案。
接下来,使用蚀刻技术,将暴露的晶圆进行化学蚀刻,把不需要的部分去除,最终形成多个芯片。
阵列工艺的特点阵列工艺具有以下主要特点:1.高产能:阵列工艺允许在一个晶圆上同时制造多个芯片,因此具有很高的产量。
相较于传统的工艺,它能够大幅提高生产效率。
2.成本降低:由于阵列工艺可以在同一晶圆上制造出多个芯片,所以可以通过批量生产来降低每个芯片的制造成本。
这对于降低整体制造成本非常重要。
3.芯片密度提高:阵列工艺允许在晶圆上紧密排列多个芯片,因此可以大幅提高芯片的密度。
这对于现代集成电路的发展非常重要,使得芯片可以更小、更精密。
4.一致性:阵列工艺制造的芯片是由同一个晶圆上的同一个光刻胶制作而成的,因此它们之间具有非常高的一致性。
这样的一致性可以提高芯片的可靠性和稳定性。
阵列工艺的应用阵列工艺在半导体工业中有广泛应用。
以下是一些应用领域的例子:1.处理器和存储器:阵列工艺可以用于制造处理器和存储器等高性能集成电路。
由于阵列工艺提供了高产量和低成本的优势,因此可以满足大规模生产的需求。
2.传感器:阵列工艺也可以用于制造各种传感器,如图像传感器、压力传感器、温度传感器等。
TFT-LCD工艺流程

第二章TFT显示器的制造工艺流程和工艺环境要求第一节阵列段流程一、主要工艺流程和工艺制程〔一〕工艺流程〔二〕工艺制程1、成膜:PVD、CVD2、光刻:涂胶、图形曝光、显影3、刻蚀:湿刻、干刻4、脱膜二、辅助工艺制程1、清洗2、打标及边缘曝光3、AOI4、Mic、Mac 观测5、成膜性能检测〔RS meter、Profile、RE/SE/FTIR〕6、O/S电测7、TEG电测8、阵列电测9、激光修补三、返工工艺流程PR返工Film返工四、阵列段完整工艺流程五、设备维护及工艺状态监控工艺流程Dummy Glass 的用途Dummy Glass 的流程第二节制盒段流程取向及PI返工流程制盒及Spacer Spray返工流程切割、电测、磨边贴偏光片及脱泡、返工第三节模块段流程激光切线、电测COG邦定、FPC邦定、电测装配、电测加电老化包装出货TFT显示器的生产可以分成四个工序段:CF、TFT、Cell、Module .其相互关系见下列图:阵列段是从投入白玻璃基板,到基板上电气电路制作完成.具体见下图:口[Glass 基普^布^^P R■ ।। [।[Mask曝光|Fi3W象।L L刻蚀I 一CF工序是从投入白玻璃基板,到黑矩阵、三基色及ITO制作完成.具体见下列图:Cell工序是从将TFT基板和CF基板作定向处理后对贴成盒,到切割成单粒后贴上片光片.具体见下列图:Module工序是从LCD屏开始到驱动电路制作完成,形成一个显示模块.具体示意图如下:O勺[LCD Module]/在以下的各节中,我们将逐一介绍TFT、Cell、Module的工艺制程c 由于天马公司现在没有规划CF工厂,所以CF的工艺流程在此不作详细介绍第一节阵列段流程一、主要工艺流程和工艺制程〔一〕工艺流程上海大马采用背沟道刻蚀型〔BCE 〕 TFT 显示象素的结构.具体结构见 下列图:Data line对背沟道刻蚀型TFT 结构的阵列面板,根据需要制作的膜层的先后顺序 和各层膜间的相互关系,其主要工艺流程可以分为5个步骤〔5次光照〕:第一步 栅极〔Gate 〕及扫描线形成C具体包括:Gate层金属溅射成膜,Gate光刻,Gate湿刻等工艺制程〔各工艺制程的具体介绍在随后的章节中给出〕.经过这些工艺,最终在玻璃基板上形成扫描线和栅电极,即Gate电极.工艺完成后得到的图形见下列图:第二步栅极绝缘层及非晶硅小岛〔Island 〕形成具体包括:PECVD三层连续成膜,小岛光刻,小岛干刻等工艺制程〔各工艺制程的具体介绍在随后的章节中给出〕.经过这些工艺,最终在玻璃基板上形成TFT用非晶硅小岛.工艺完成后得到的图形见下列图:第三步 源、漏电极〔S/D 〕、数据电极和沟道〔Channel 〕形成 具体包括:S/D 金属层溅射成膜,S/D 光刻,S/D 湿刻,沟道干刻等工 艺制程〔各工艺制程的具体介绍在随后的章节中给出〕.经过这些工艺,最终 在玻璃基板上形成TFT 的源、漏电极、沟道及数据线.至耻匕,TFT 已制作完 成.工艺完成后得到的图形见下列图:X.a-Si/n+ 4―匕 SiN第四步保护绝缘层〔Passivition 〕及过孔〔Via〕形成具体包括:PECVD成膜,光刻,过孔干刻等工艺制程〔各工艺制程的具体介绍在随后的章节中给出〕.经过这些工艺,最终在玻璃基板上形成TFT沟道保护绝缘层及导通过孔.工艺完成后得到的图形见下列图:Ci第五步透明象素电极ITO的形成具体包括:ITO透明电极层的溅射成膜,ITO光刻,ITO湿刻等工艺制程〔各工艺制程的具体介绍在随后的章节中给出〕.经过这些工艺,最终在玻璃基板上形成透明象素电极.至此,整个阵列工序制作完成.工艺完成后得到的图形见下列图:CStorage capacitorITO pixel electrodeCros-section -Ca-Si TFTCSelect lineData line至此,整个阵列工序制作完成.简单来说5次光照的阵列工序就是:5 次成膜+ 5次刻蚀.〔二〕工艺制程在上面的工艺流程中,我们提到,阵列的工艺流程是成膜、光刻、刻蚀等工艺制程的反复使用.以下就这些工艺制程作具体的介绍.1、成膜顾名思义,成膜就是通过物理或化学的手段在玻璃基板的外表形成一层均匀的覆盖层.在TFT阵列制作过程中,我们会用到磁控溅射〔Sputter ,或称物理气相沉积PVD〕和等离子体增强型化学气相沉积〔PECVD〕.A〕磁控溅射〔Sputter 〕溅射是在真空条件下,用He气作为工作气体.自由电子在直流DC电场的作用下加速获得能量,高能电子碰撞He原子,产生等离子体.He离子在DC电场的作用下,加速获得能量,轰击在靶材上,将靶材金属或化合物原子溅射出来,沉积在附近的玻璃基板上,最后形成膜.磁场的作用是限制等离子体的分布,使成膜均匀.磁控溅射的原理示意图如下:B) PECVDPECVD 是通过化学反响在玻璃基板外表形成透明介质膜.等离子体的作 用是使反响气体在低温下电离,使成膜反响在低温下得以发生.其原理示意图 如下:RF power 13.56 MHz-I'wrYi 印Used for ITO (Indium Tin Oxide transparentconductor) and for metals (Al, Mo, Ti, Cr,〜1 mTorrGlass Target/rcrjki I生产用磁控溅射设备如下列具体溅射原理的介绍和详细的设备介绍参见后面相关的章节RF power ~ 100 mW/cm2)PLASMA -1 TorrT=300 oCsubstrateFeed gas MaterialFunctio nSiH4, H2a-Si SemiconductorSiH4, N2, NH3Si3N4Gateinsulator,passivationSiH4, N20SiO2Gateinsulator,passivationSiH4, PH3, H2n+ a-Si Contactlayer at sourceand drain成各类股所使用得化学气体见下表: 典型的PECVD设备如下列图:□ □□□2、光刻:涂胶、图形曝光、显影光刻的作用是将掩模版〔Mask 〕上的图形转移到玻璃外表上,形成 PR具体通过涂胶、图形曝光、显影来实现.见以下示意图:Mask Transfer robot I..,Cassette station具体PECVD 原理的介绍和详细的设备介绍参见后面相关的章节Layer to be patterned心网4士A 〕涂胶在玻璃外表涂布一层光刻胶的过程叫涂胶.对于小的玻璃基板,一般使 用旋转涂布的方式.但对大的基板,一般使用狭缝涂布的方式.见以下示意 图:B 〕图形曝光涂胶后的玻璃基板经枯燥、前烘后可以作图形曝光.对于小面积的基 板,可以采用接近式一次完成曝光.但对大面积的基板,只能采用屡次投影曝 光的方式.下列图是Canon 曝光机的工作原理图:glassResistPatterned layerPhotoresist strippingPhotoresistcoatingExposure through maskPhotoresist developingI ■Etching of layerResist dispenserExtrusion headPhotoresistSpin coatingSlit (extrusion) coating由于大面积的均匀光源较难制作,Canon采用线状弧形光源.通过对Mask和玻璃基板的同步扫描,将Mask上的图形转移到玻璃基板上.C〕显影经图形曝光后,Mask上的图形转移到玻璃基板上,被光阻以潜影的方式记录下来.要得到真正的图形,还需要用显影液将潜影显露出来,这个过程叫显影.如果使用的光阻为正性光阻,被UV光照射到的光阻会在显影过程中被溶掉,剩下没有被照射的局部.显影设备往往会被连接成线,前面为显影,后面为漂洗、枯燥.示意图如下:3、刻蚀:湿刻、干刻刻蚀分为湿刻和干刻两种.湿刻是将玻璃基板浸泡于液态的化学药液中,通过化学反响将没有被PR覆盖的膜刻蚀掉.湿刻有设备廉价、生产本钱低的优点,但由于刻蚀是各向同性的,侧蚀较严重.干刻是利用等离子体作为刻蚀气体,等离子体与暴露在外的膜层进行反应而将其刻蚀掉.等离子体刻蚀有各向异性的特点,容易限制刻蚀后形成的截面形态;但但高能等离子体对膜的轰击会造成伤害.湿刻与干刻的原理见下图:O2 containing etching gasPhotoresistEtched layerGlass substrate干刻设备与PVD及PECVD设备一样,一般采用多腔体枚叶式布局.由于设备内是真空环境,玻璃基板进出设备需要1-2个减压腔.其余腔体为工艺处理腔.见以下示意图:II Anisotropic dry etching Photoresist Etched layerGlass substrateWet etching vs. dry etching (RIE)Etched layerlotoresis.hotoresistGlass substrate湿刻的设备一般与后面清洗、枯燥的设备连成线,见下列图:般金属膜采用湿刻,介质膜采用干刻4、脱膜刻蚀完成后,需要将作掩模的光阻去除,去除光阻的过程叫脱膜.一般脱膜设备会与其随后的清洗、枯燥设备连线.见下列图:二、辅助工艺制程阵列工序的工艺流程中,除了以上介绍的主要工艺制程外,为了监控生产线的状态,提升产品的合格率,方便对产品的治理和增加了一些辅助的制程,如:清洗、打标及边缘曝光、AOI、Mic/Mac观测、成膜性能检测、电测等.以下就这些辅助工艺制程逐一作个简单介绍.1、清洗清洗,顾名思义就是将玻璃基板清洗干净.这是整个LCD工艺流程中使用最频繁的工艺制程.在每次成膜前及湿制程后都有清洗.清洗有湿洗和干洗,有物理清洗和化学清洗.其作用和用途详见下表:具体在工艺流程中,玻璃基板流入生产线前有预清洗;每次成膜前有成膜前清洗;每次光阻涂布前有清洗;每次湿刻后及脱膜后也有清洗.一般清洗设备的结构如下:由于清洗设备的结构与湿刻及脱膜设备的结构非常相识,所以这三个制程往往统称为湿制程2、打标及边缘曝光为了方便生产线的治理,我们需要对在生产线流通的每一张玻璃基板和Panel打上ID,这是通过打标制程来完成的.通常打标制程会放在栅极光刻制程中,即栅极图形曝光后,显影前.打标一般采用激光头写入.随着玻璃基板的增大,曝光机的制作和大面积均匀光源的获得变得较难.为了有效利用曝光设备,在图形曝光时只对玻璃基板中间有图形的有效区域进行曝光.之后采用一种不需要Mask的边缘曝光设备对边缘区域曝光,然后去做显影.这一过程叫边缘曝光.3、自动光学检测〔AOI 〕为了提升产品的合格率,在每次显影后和刻蚀后,一般会作一次光学检测.一般采用线性CCD 对玻璃基板上的图形进行扫描,将扫描后的图像作计算机合成处理后,与设计图形作比对,以发现可能存在的问题.此过程即称为自动光学检测.其典型设备如下列图:4、宏微观检查〔MAC/MIC 〕微观检查主要是通过显微镜对AOI或其他检测过程中发现的问题作进步观测确认.宏观检测是利用人眼对光和图像的敏锐观察,以发现显影后或刻蚀后大面积的不均匀.微观、宏观检查往往设计在同一机器上.典型的机器见下列图:5、成膜性能检测在阵列的制程中有5次成膜.成膜质量的好坏直接关系到产品的性能和合格率的上下.所以生产中有许多对膜性能作检测的工序,尽管这些工序也许只是抽测.对导电膜,一般会用四探针测试仪〔RS Meter 〕作膜层方块电阻测试;用反射光谱仪〔SR〕作反射性能测试.对介质膜,一般会用椭偏仪〔SE〕作膜厚和透过性能测试;用付氏红外分析仪〔FTIR〕作成分分析.对所有的膜层都会用台阶仪〔Profile 〕作膜厚分析;用Mac作宏观检查;用AFM作外表形貌分析.6、开路/短路〔O/S 〕电测TFT沟道刻蚀主要是刻掉非晶硅外表的一层N型参杂的接触层.这一层具有改善接触电阻的作用.但这一层在沟道的局部必须完全刻蚀干净,否那么沟道短路或漏电流偏大.沟道是否刻蚀干净,用光学的方法不能检测,由于N型参杂层是透明的.所以在沟道刻蚀后插入开路 /短路〔O/S〕电测.开路/短路电测的原理很简单:将两个探针放在电极的两端,检测电流以判断电极是否开路;将两个探针放在相邻的两个电极上,检测电流以判断这两个电极问是否短路.下列图是原理的示意图和相关设备图:7、TEG (Test Element Group )电测在阵列制作的工艺过程中,有许多中间环节的电气性能直接影响到产品的最终性能,必须加以检测.如层间的接触电阻,电极间的电容等.为了检测这些中间环节的电气性能,会在正常显示屏电气线路以外的区域,专门设计一些检测中间性格的电气单元(Test Element Group ),并通过专门的TEG检测设备作测试.常见的TEG电气单元有:引线电阻、TFT、存储电容、接触电阻、跨越台阶的引线电阻等.TEG的位置及设计范例如下列图:8、阵列电测阵列电路制作完成后,其电气性能如何需要作阵列电测,以挑出有缺陷 的屏,不让其流到后面的工序,减少材料的损失.阵列电测大致分为电荷检测、电子束检测和光学检测三种检测方法.这 三种检测方法各有优劣.目前大马采用光学的检测方法.其原理和相关设备见 下列图:TE G□ □囱[QX □ □□EQ□ □口 口□口 口口目日SBOm m■T«L Hems;Elldon,也H 口Vih fJhtoMty tjS factorr.SgsUa 怕 cturgaei folia frRwiBtance3nMetiofl. Cor t«t*□opi 与 chedt) 配而Odans 旧中 WO¥0Vbd 侬W 】郡帆RMHCI, S4 氏 hHlIng.Cofilamnaticxi)Hi 曲 Spe«d 60 fps cameraHi 的 Resoliuil.i0inii DRCrPAOS for alignment Opticnai IV probeSAFE Modulator详细的设备介绍见后面相关章节9、激光修补对在AOI或电测中发现的问题,如短路、开路等,一般考虑采用激光修补的方法进行补救.这一方法对大屏的制作尤其有效.常见的激光修补设备见下列图:三、返工工艺流程以上介绍的是正常工艺流程.在生产过程中由于品质管控的要求,在某些指标达不到要求时,产品会进入返工流程.阵列段最常见的返工是:PR返工和Film返工.1、PR返工在曝光、显影后,膜层刻蚀前,如果被AOI或MAC/MIC 检测发现严重质量问题,如果不返工会导致产品报废或合格率很低.这时产品会进入PR返工流程,即先脱膜,然后从新作光刻.2、Film返工Gate电极和S/D电极在刻蚀后,如果被AOI或MAC/MIC 检测发现严重质量问题,如果不返工会导致产品报废或合格率很低.这时产品会进入Film 返工流程,即先脱膜后,湿刻掉所有金属膜,然后从新作成膜.四、阵列段完整工艺流程在主要工艺流程和制程的根底上,参加辅助工艺制程和返工流程,一个阵列段完整的工艺流程如下列图:图中同时给出了制作高开口率的有机膜工艺流程和半反半透膜工艺流程.其器件原理参见其他文献的介绍.以上工艺流程图的详细工艺步骤描叙,请参见本章后的详细的具体附五、设备维护及工艺状态监控工艺流程产品是靠生产线和设备作出来的,所以生产线的状态和设备状况直接关系到产品的质量.定时对设备作维护(Prevent Maintenance )和对设备、环境状态作监测是有效治理的的必然选择.通常的做法是采用白玻璃( Dummy Glass)作某个工艺制程,之后拿去检测.这样Dummy Glass就有一个流程, 1、白玻璃(Dummy Glass )的用途在生产线遇到以下几种情况时,需要流通白玻璃:A、在新的生产线安装调试阶段,用白玻璃作一系列的试验;B、设备或工艺调整后,用白玻璃确认工艺状况;C、设备作维护保养后,用白玻璃确认工艺状况D、设备和工艺状态需要作定期监测时E、工艺洁净环境需要作定期监测时2、白玻璃的流程根据使用白玻璃的目的的不同,其流通流程也完全不同.这里只简单举一个例子.例如,如果我们需要了解设备内的清洁状态,白玻璃会流过以下制程:白玻璃清洗-要检测的设备-异物检测机对于各种情况下白玻璃的详细流程,请参考本章附表.第二节制盒段流程Cell段的工艺流程可以大概分为四块:取向、成盒、切断、贴偏光片以下简单介绍一下各块工艺目的和主要工艺制程.一、取向工艺取向工艺的目的是在TFT和CF基板上制作一层透明的PI膜,经摩擦后,使液晶分子沿摩擦方向排列.其原理请自己查看相关文献.所以在这一块,有两个主要的工艺制程:PI印刷和摩擦.1、PI印刷PI ( Polyimide )是一种透明的有机高分子材料,有主链和侧链,经涂布烘烤后,会牢固地附着在CF和TFT基板外表.PI的涂布采用一种凸版印刷的技术.其工作原理见以下示意图:PI印刷除凸版印刷的主工艺制程外,还有一些辅助的工艺制程,如:印刷前清洗、印刷后预烘、自动光学检查、固化,以及PI返工制程等.这里不再逐一介绍.2、摩擦摩擦的作用是用绒布在PI上摩过,将PI的侧链梳理到一个方向.示意图如下:回事云配向膜付W基板装置?摩擦后还有辅助工艺制程:摩擦检查.二、ODF成盒工艺成盒就是将CF和TFT玻璃基板对贴、粘结起来,同时要在两个玻璃基板间的间隙中(盒中)放入液晶并限制盒的厚度.传统的成盒工艺是先完成空盒制作,然后灌注液晶.现在的ODF (One Drop Filling )工艺是先在TFT或CF玻璃基板上滴下液晶,然后在真空环境下对贴制盒,最后经紫外固化和热固化后成盒.ODF成盒工艺可以分成四块:衬垫料喷洒,边框料、银点料、液晶涂布,真空环境下对贴制盒,紫外固化和热固化.以下逐一作简单介绍:1、衬垫料喷洒盒厚限制是靠选择设定的球形衬垫料的直径来实现的.衬垫料需要在贴合前均匀地喷洒到玻璃基板地外表,这是通过一种让衬垫料带电后干喷的设备完成的.其示意图如下:基板2、边框料、银点料、液晶涂布边框料的作用有三:一是将CF与TFT基板粘结在一起;二是将盒厚固定下来;三是将液晶限制在盒内.银点料的作用是导通CF和TFT上的Common电极.对ODF工艺而言,边框料和银点料必须是采用快速固化的UV固化胶.液晶(Liquid Crystal )的作用是改变盒的光学状态.这三种材料的涂布都是采用一种叫Dispensor的涂布头来完成的.其示意图分别如下:边框涂布窒素力'久加压银点涂布液晶涂布液晶3、真空环境下对贴制盒将涂布有衬垫料、边框料、银点料、液晶的CF与TFT玻璃基板在真空环境下对贴,以完成制盒.其工作原理见下列图:人亍一ODF制盒完成后,为了预防CF与TFT玻璃基板的相对移动,在四个角滴上UV胶,并作UV固化.4、紫外固化和热固化前面已经提到,对ODF工艺而言,边框料和银点料必须是采用快速固化的UV固化胶.ODF制盒完成后,对贴好的玻璃会作UV固化处理,使边框料和银点料固化.为了预防UV光对液晶的破坏,边框以外有液晶的地方会用Mask遮挡.假设UV光从CF侧照射,CF可以起到Mask的作用.假设UV光从TFT侧照射,需要准备专用的Mask.UV型边框料有快速固化的特点,但粘接强度不如热固化型胶.且当UV从TFT侧照射时,在引线下的边框料UV光照射不到.为了解决以上问题, ODF边框料一般都是UV型与热固化型环氧树脂的混合体. UV固化后还必须经过充分的热固化.以上是ODF的主要工艺制程.此外还有一些辅助工艺制程,如:摩擦后〔衬垫料散布前〕清洗,衬垫料返工,边框料、液晶涂布前USC干洗,边框料涂布后自动光学检查,边框固化后目测、盒厚检测、及偏位检测等.、切割、磨边、电测1、切割由于玻璃基板的尺寸一定,而各产品的尺寸不同,在一张玻璃基板上会排列有多个产品盒.见下列图:在产品盒制作完成后,需要将这些排列在一起的盒分割成独立的屏.这个过程就称为切割.切割是通过金刚刀轮在玻璃外表滑过来完成的.具原理图如下:裹面力加压1>、通常切割后还有裂片的工艺.但随着刀轮技术的改良,目前已有切痕很深的技术,其切割后不需要裂片.2、磨边玻璃切割成单个屏后,每个屏的边会有许多细小的裂纹.为了预防这些裂纹在随后的流通中因碰撞而造成崩裂,需要作磨边处理.3、电测电测是生产的辅助工序,在生产的过程中屡次使用.但此处电测非常重要,由于这是第一次加电检测LCD的显示性能.其检测原理很简单,即在个显示象素上加上电,通过偏光片,观察盒的显示性能.此处一般利用阵列检测的短路条加电.电测后,将不良的屏挑出来,以免流到后面造成材料的浪费.其他辅助工艺制程包括:切割后目测,磨边后清洗等.四、贴偏光片LCD是通过偏振光来工作的,偏光片的贴附是必须的工艺制程.其工作原理图如下:C F 基板T F T 基板偏光片的贴附过程中,静电防护非常重要.其他辅助工艺制程包括:贴片前清洗,贴片后消泡,偏光片返工,贴片 后电测等.口一 7偏光板七,S Lz 一夕一第三节模块段流程模块的主要工艺制程包括:COG 、FPC 邦定,装配等.以下逐一介绍 1、COG 、FPC 邦定COG (Chip on Glass )和 FPC (Flexible Printed Circuit )是一种电 路的连接方式.由于电极多,一对一的排线连接很困难.现在通常的做法是将 玻璃上的引线作成阵列,IC/FPC 上的引线也作成对应阵列,通过一种各向异性导电膜(ACF)将IC/FPC 上的电极与玻璃上的电极一对一连接导通.玻璃上的eripheral seal PolarizersVPanel 1ILCL Films引线电极阵列示意图如下:邦定后IC/FPC 、屏、及ACF 的相对位置如下列图:Anisotropic Conductive Adhesive Driver101r plate「FT plateBacklightPCB的布局示意图如下:2、组装模块段除去以上主要工艺制程外,还有一些辅助的工艺制程,如:激光 切线,切线后电测,邦定后电测,组装后电测,切线后显微镜检查,绑定后显 微镜检查或自动光学检查,IC 邦定后剪切力剥离测试,FPC 邦定后拉力剥离测 试,组装后加电老化,包装出货等.对自动化生产线而言,COG 邦定与FPC 邦定一般连成一条线.具设备-"O-JCB5 D/T 1 i-1 5 E 3 L亡K三L»« ri«^■«■I;rAt-F |i ■ p » iitl ICONFIDENTIAL;'1I> _组装是将背光源、屏、限制电路板、及触摸屏等部件组合在一起,形成 一个完整的显示模块.组装一般是由手工来完成的,熟练的技术工人在这里非 常重要.见下列图:以上两节提到Cell和Module段的工艺制程可以归纳为以下工艺流程图:。
阵列工艺流程

阵列工艺流程阵列工艺流程是指在光刻和半导体制造的过程中,将多个芯片或器件同时制作在同一晶圆上的工艺流程。
下面将介绍一个常见的阵列工艺流程。
首先,需要准备晶圆,晶圆是一个平坦的硅片,通常直径为12英寸。
晶圆有不同的材料,根据工艺要求选择合适的晶圆材料。
然后,将晶圆通过一系列清洁的步骤进行清洁,以去除表面的杂质和污染物。
接下来,进行光刻工艺。
光刻是利用光源和掩模,将模版上的图案转移到晶圆表面的工艺。
首先,在晶圆表面涂覆光刻胶,光刻胶是一种感光的材料。
然后,将晶圆和掩模对准,通过紫外光照射晶圆表面,使得光刻胶在受光区域发生化学变化,形成图案。
接着,利用化学腐蚀或离子注入等方法,将晶圆表面非受光区域的材料去除或改变。
这一步叫做刻蚀工艺。
刻蚀的目的是将受光区域的图案转移到晶圆表面的材料上,形成芯片的结构。
然后,进行沉积工艺。
沉积是将材料以气相或液相的形式,通过化学反应沉积在晶圆表面的工艺。
常见的沉积工艺有化学气相沉积(CVD)和物理气相沉积(PVD)。
通过沉积工艺,可以在晶圆表面形成薄膜,用于制作电路的导线、绝缘层等。
接下来,进行清洗和退火工艺。
清洗是为了去除沉积过程中产生的杂质和残留物,以保证晶圆表面的洁净度。
退火是利用高温处理,使得晶圆表面的材料重新结晶,提高材料的结晶度和晶粒的尺寸。
退火能够改善材料的电学和机械性能。
最后,通过薄膜的切割和外围电路的连接,将晶圆分割成多个芯片。
这一步叫做切割和封装工艺。
切割可以使用机械切割或激光切割等方法。
封装是将芯片放入封装盒中,并连接外部引脚,以方便芯片的连接和使用。
总结起来,阵列工艺流程包括晶圆的清洁、光刻、刻蚀、沉积、清洗、退火、切割和封装等步骤。
通过这些步骤,可以将多个芯片制作在同一晶圆上,提高生产效率和芯片的集成度。
阵列工艺流程在电子产业中广泛应用,是现代半导体制造的重要工艺之一。
lcd点阵屏工作原理

lcd点阵屏工作原理
当我们提及LCD点阵屏,首先浮现在脑海中的是那些细致入微的像素点阵列,它们共同构成了我们所看到的每一个画面。
LCD点阵屏的工作原理,其实是一个微观世界的魔法展现。
LCD点阵屏的构造远比我们肉眼所见的复杂。
在它的核心,是液晶分子。
这些分子仿佛是微观世界的舞者,随着电场的变换,它们不断地扭曲、旋转,从而改变了光的路径。
正是这一神奇的现象,使得每个像素点能够独立地亮起或熄灭,进而形成我们所见的图像。
这些液晶分子仿佛是受到指挥的队伍,在外加电压的作用下,它们开始进行有规律的排列。
当电压较小,液晶分子的排列较为疏松,透光性较好,像素点呈现亮色;而当电压逐渐增大,液晶分子的排列越来越紧密,透光性逐渐减弱,像素点便逐渐变暗。
这种微妙的控制,使得每一个像素点都能够实现从亮到暗的渐变,从而呈现出细腻的图像。
不仅如此,LCD点阵屏的显示效果还与其制造工艺密切相关。
基板的平整度、液晶材料的纯度、电压的稳定性等,都直接影响着屏幕的清晰度和色彩饱和度。
正因为有了这些因素的严格把控,我们才能够欣赏到如此清晰、真实的画面。
而点阵式LCD液晶显示屏的出现,更是推动了显示技术的进步。
它利用了液晶分子的特性,通过精确控制电压的大小,实现了对像素点的独立控制。
这一技术不仅提高了显示效果,还为后续的平板显示技术奠定了基础。
总之,LCD点阵屏的工作原理是一个微观世界与显示技术的完美结合。
它不仅让我们看到了一个五彩斑斓的世界,更是推动了显示技术的发展。
在未来,我们有理由相信,随着科技的进步,LCD点阵屏将会为我们带来更加惊艳的视觉体验。
- 1、下载文档前请自行甄别文档内容的完整性,平台不提供额外的编辑、内容补充、找答案等附加服务。
- 2、"仅部分预览"的文档,不可在线预览部分如存在完整性等问题,可反馈申请退款(可完整预览的文档不适用该条件!)。
- 3、如文档侵犯您的权益,请联系客服反馈,我们会尽快为您处理(人工客服工作时间:9:00-18:30)。
TN 4Mask Process I工程和D工程 一起进行
SFT 5Mask Process C-Pattern 在周边部位 PI-Pattern 在周边部
23
四,TN与SFT工艺对比
TN:
构造简单 PR数少,成本低,LT短 开口率大
SFT:
液晶分子水平排列,视角大 常黑模式,不良点为暗点, 不易发现 电极面积大导致开口率小 Pattern密度高,易受异物 影响 为了增加亮度必须增大背光 源辉度,功耗较大
电路部件 偏光板
TFT部位侧视
DRAIN n+ a-Si GLASS a-Si GATE
G-SiNx
3
一, TFT的基本构造
接触孔 ITO像素电极 C工程 SOURCE DRAIN D工程 P-SiNx PI工程
n+ a-Si a-Si I 工程 GATE G工程
GLASS
G-SiNx
4
二,4Mask与5Mask工艺对比
1.节省时间:1462-1398=64min 2.节省设备:1套 InlinePR+曝光机
6
二,4Mask与5Mask工艺对比
5 Mask – D工程和I 工程
曝光 I-工艺 DI-工艺
4 Mask – D/I 工程
曝光
D1-WE
I-DE 曝光 D-工艺
I-DE
PR-DE
D-WE
D2-WE
CH-DE
加热盘
O-Si(CH4)3+NH3↑
气流控制, 气流控制,膜厚改善
EBR处理 处理
基板端面的光刻胶除去→减少垃圾 基板端面的光刻胶除去 减少垃圾 的光刻胶除去
预烘
光刻胶中的溶剂除去, 光刻胶中的溶剂除去,烧成 →改善膜厚均一性和密着性 改善膜厚均一性和 改善膜厚均一性
N2 洗浄液 排 气 非接触式栓 加热盘
CH-DE
7
三,ARRAY基板的工艺流程
工艺名称 洗净 溅射(SPUTTER) P-CVD PR/曝光 湿刻(WE) 干刻(DE) 剥离 工艺目的 清洁基板表面,防止成膜不良 成Al膜,Cr膜和ITO膜 成a-Si膜,n+a-Si膜和SiNx膜 形成与MASK图案相一致的光刻胶图案 刻蚀掉未被光刻胶掩蔽的金属膜 刻蚀掉未被光刻胶掩蔽的非金属膜 去掉残余的光刻胶
基板倾斜,显像液流下
基板全面喷纯水
显影液
回收 显影液
纯水
18
湿刻
WE① WE② 循环水洗 纯水洗 干燥
P
废 液
新 液
P
D A
排 水
P
纯 水
排 水
D A
19
干刻
转移腔 工艺腔ー 工艺腔ーL 装料腔 机械手 S/R-L R-L 工艺腔-R 工艺腔-R 工艺腔-C 工艺腔-C
S/R-R R-R
20
干刻
8
洗净
周转盒 共通
MS MS 高 圧 高压喷射 刷洗 薬 液 药液喷淋 UV UV 传送装置
卸料 机械手 传送装置 气刀
ロボ ット 机械手 ロー ダ 装料
9
洗净
UV 药液 刷子 高圧 MS A/K
P U V
D A
排 水
P 刷洗
P 高 压 喷射
Array工程
[GLASS]
4Mask 工程名 所需时间 lot构成 受入洗净 20 G-Sputter 36 G-PR 70 178 G-WE 28 PR剥离 24 成膜前洗净 20 1stSiNx-CVD 25 成膜前洗净 20 3层-CVD 50 成膜前洗净 20 D-Sputter 40 579 D/I-PR 70 DI-WE 40 I/PR-DE 120 D2-WE 30 CH-DE 120 PR剥离 24 成膜前洗净 20 PA-CVD 30 C-PR 70 354 C-DE 210 PR剥离 24 成膜前洗净 20 PI-Sputter 31 PI-PR 70 PI-WE 32 287 PR剥离 24 退火前洗净 20 退火 90 总计: 1398 5Mask 工程名 所需时间 lot构成 受入洗净 20 G-Sputter 36 G-PR 70 G G-WE 28 PR剥离 24 成膜前洗净 20 1stSiNx-CVD 25 成膜前洗净 20 I 3层-CVD 50 I-PR 70 I-DE 120 I-剥离 24 成膜前洗净 20 D-Sputter 40 D-PR 70 D D-WE 40 PR剥离 24 CH-DE 120 成膜前洗净 20 PA-CVD 30 C C-PR 70 C-DE 210 PR剥离 24 成膜前洗净 20 PI-Sputter 31 PI-PR 70 PI PI-WE 32 PR剥离 24 退火前洗净 20 退火 90 总计: 1462
成膜
CVD·Sputter [膜] [Glass]
G
178
Lithography
反复 (a) (b) 曝光 (c) 显像 (d) Etching (e) 剥离
C D/I
329
[Mask]
314
354
PI
287
5
二,4Mask与5Mask工艺对比
1600 1400 1200 时间 时间/min 1000 800 600 400 200 0 579 329 G 178 4Mask 178 5Mask 314 287 354 287 354 PI C D I D/I
D - Cr PI - ITO 类型 G配线 D配线 像素电极 G1 - AlNd G2 - MoNb 名称 MoNb/AlNd Cr ITO 作用 传递扫描信号 传递数据信号 存储数据信号
11
Sputter设备
整体图
(SMD-1200)
基板搬入(加热)/ 搬出(冷却)室 (L1,L2) 搬送室(Tr) 成膜室(X1,X3)
ห้องสมุดไป่ตู้工艺腔体 压力控制
真空排气 空排气
除害装置 (scrubber) )
泵
21
剥离
1次剥离 冲淋
2次剥离 US Dip
1次 rinse 循环冲淋
2次 rinse 纯水冲淋
干燥 A/K
剥离液
Cascade
剥离液
US
循环水
纯水
DA
22
四,TN与SFT工艺对比
G工程 (Gate) I工程 (Island) D工程 (Drain) C工程 (Contact) PI工程 (Pixel)
非接触方式→改善静电, 非接触方式 改善静电, 改善静电 背面污染, 背面污染,热应力等方面 16
曝光
光源 FlyEye CCD
円弧状Slit Mask 横倍率 凹面 台形 Mirror 弓なり补正 X非线形 凸面 Mirror 基板 Scan
17
Mirror
显影
显影槽 显影液回收 清洗槽 风刀干燥
加热腔 ヒート 工艺腔 プロセス
机械手 トランスファー
纳入(大气到真空 大气到真空)/ 纳入 LL/UL 大气到真空 真空到大气) 送出腔(真空到大气 真空到大气
ローダー 装载台
所用设备加热装置放在工艺室中, 注:S1所用设备加热装置放在工艺室中,且只有两个工艺室 所用设备加热装置放在工艺室中
13
PECVD
气体供给 流量控制 流量控制
MFC MFC MFC
控制台 RF power
M. Box RF电源 RF电源 (PE场合 场合) (PE场合)
Gas box
上部电极 上部电极 气体吹出
等离子体 C/M
汽缸cabinet 汽缸
压力检出 压力检出 特气对应
下部电极 下部电极
APC阀 阀
C/M 控制 APC 控制
气体供给
MFC MFC MFC
RFpower RF
气体BOX 气体
M.BO X 气体吹出电极 阴极) (阴极) 下部电极 下部电极 阳极) (阳极)
P
RF电源 RF电源
流量控制 流量控制
汽缸cabinet 汽缸
等离子体
ヒーター
压力计
工艺腔体 (电极部) 电极部
压力控制
控制
节流阀
干泵 除害装置 (scrubber) )
Sputter X1Type (1Target)
S1枚叶Sputter ULVAC SMD-1200
Glass Size 1100×1300(mm)
S3 X1Type 1sheet
S4 X3Type 1sheet Max3sheet
Sputter X3Type (1~3Target)
VacRob 2sheet
UpperSlot-Load (Heating) UnderSlot-Unload (Cooling)
Cassette Loader
AtmRob 2sheet
cassette1 20sheet
cassette2 20sheet
cassette3 20sheet
cassette4 20sheet
12
PECVD
纯 水
排 水 M S
D A
药 液
洗净 功能 洗净对象 作 用
氧化分解 有机物 (浸润性改善) UV/O3
溶 解 有机物 溶 解
机械剥离 微粒子 (大径) 接触压
机械剥离 微粒子 (中径) 水压
机械剥离 微粒子 (小径) 加速度 cavitation 10
Sputter
TFT中Sputter薄膜的种类和作用
特气对应
真空排气
14
InlinePR
加热盘 搬送机械手
冷却盘
旋转涂布单元 (洗净,涂布,预烘等)
15
InlinePR