嘉富盛品管人员基础知识精品文档
品管员必备知识
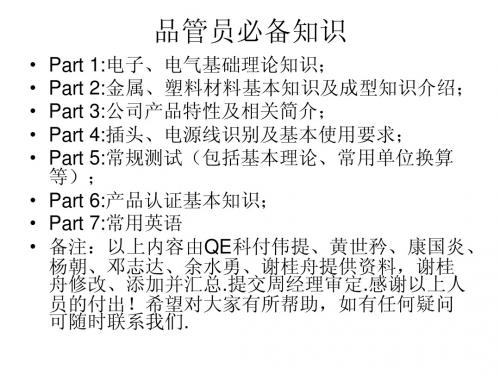
五金件常出现的缺陷:
• • 刮伤、裂痕、披锋、氧化、凹凸痕、擦伤、拉伤、变形、材质不符、脱焊、焊接错位、 焊接错件等。 目前公司五金件加工机器主要有冲床、点焊机 刮伤---手指感觉不出之线凹痕或痕迹。主要是在生产挟料、摆放过程中刮伤 裂缝---材料部份断裂,典型的例子是以生在折弯引伸加工之外侧。主要是在折弯、拉伸 工序中出现。 披锋---剪切或冲压导致残留不平整边缘,模具设计需使客人接触到的披锋减至最少。主 要是在切边工序中产生。 梗屎---通常此种痕迹产生与压印及冲压成型有关。(如多仕炉升降手柄支架成形工序 经常有发生) 氧化---材料与空气中的氧起化学变化,失去原有特性:如生锈。 凹凸痕---表面异常凸起或凹陷。主要是操作员工不及时将模具上的料渣吹干净所致。 擦伤---指材料表面因互相接触摩擦所导致的损伤。 污渍---一般为加工过程中,不明油渍或污物附着造成。 拉模---一般为加工过程中,因冲制拉伸或卸料不良导致。 变形---指不明造成的外观形状变异。主要是针对材料较薄的零件,如钢带。 焊痕---焊接所留下的痕迹。 喷溅---点焊时,从焊件贴合面或电极与焊件接触面间飞出熔化金属颗粒的现象。 脱焊---焊点分离。 错位---指焊件未正确定位。 错件---未依规定零件。 用错材料:未按规定使用材料.
•
塑料的识别
• 辨别热固性塑料和热塑性塑料 将小块样本放入试管中然后加热,如样本 变色或未经软化就已分解的话就必定是热 固性塑料.如样本溶化,那就及已可能是热塑 性塑料.例如:PP. 另一方法为将一加热焊枪放置在样本上,如 样本上出现有压印即可能是热塑性塑料,因 焊枪不会将热固性塑料软化.例如:电木 (PF).
品管员必备知识
• • • • • Part 1:电子、电气基础理论知识; Part 2:金属、塑料材料基本知识及成型知识介绍; Part 3:公司产品特性及相关简介; Part 4:插头、电源线识别及基本使用要求; Part 5:常规测试(包括基本理论、常用单位换算 等); • Part 6:产品认证基本知识; • Part 7:常用英语 • 备注:以上内容由QE科付伟提、黄世矜、康国炎、 杨朝、邓志达、余水勇、谢桂舟提供资料,谢桂 舟修改、添加并汇总.提交周经理审定.感谢以上人 员的付出!希望对大家有所帮助,如有任何疑问 可随时联系我们.
品管基础知识培训

二﹑游標卡尺的使用 1.歸零:清幹凈固定基面和測量面後看卡尺能否準確歸零,有無間隙。 2.被測值:主尺上以mm為單位之整數+表盤讀數*精確度,看讀數時,眼睛與表盤 垂直。(圓盤卡尺). 3.測量完畢將尺擦幹淨﹐附尺移至離原點0.5mm﹐鎖緊螺絲放於盒內。 4.被測物愈靠近主尺,愈準確。 三﹑保養 1.清潔卡尺。 2.輕拿輕放,不能重摔,不能反置和調歸零鈕 3.不能直接接觸腐蝕性物體。4.定期校驗。
QC七大手法﹑9大步驟
一﹑QC的七大手法﹕ 查檢表﹑層別法﹑柏拉圖﹑特性要因圖﹑散布圖﹑直方圖﹑管制圖 二﹑QC七大手法特點 1.根據事實﹐數據發言-------圖表﹑查檢表﹑散布圖 2.整理原因與結果之關系以探討潛伏性之問題---------特性要因圖 3.有變異性存在﹐須考慮帄均值與變異數--------直方圖﹑管制圖 4.數據須根據來源考濾適當分層----------層別法 5.重點管理﹐對影響較大之2~~3項原因采取措施
量測基礎
一﹑量測的意義和人員的素質﹕ 消除感官錯覺的最好方法尌是靠量測﹑計數及秤重﹐經過這些 動作我們才可以擺脫感光對大小﹑數量及重量的控制﹐這尌是量 測的意義。量測人員必須誠實嚴謹﹐實事求是﹐尊重事實﹐量測 結果不能帶有主觀意識。 二﹑量測注意事項﹕ 1.不要提供不准確及假數據 2.按圖紙要求建立基准﹐要注意圖紙的版本及設變尺寸 3.操作儀器時要嚴格按照儀器使用要求 4.儀器要定期 5.不使用不合格的儀器 6.儀器遇到意外傷害時﹐應立即報告相關人員進行點檢﹐校正 7.要注意儀器防鏽﹐防塵的要求﹐必要時戴手套操作 8.要注意儀器啟動時相關參數的調整﹐如電壓﹐氣壓等 9.量測中有意外情況發生時要及時記錄﹐便于追蹤 10.量測人員要不斷學習互相交流共同進步
品管人员学习资料

品管人员学习资料一.概念篇.1.品质的四大要素.品质:不仅仅指产品的品质,而且包括工作的品质,品质的要素可分为以下几点.2、品质的定义—符合规格什么是符合规格呢?这就是你要依据以下几点完成你的工作:(1)依照公司的政策与程序.(2)依照上司的指示.(3)依照顾客或公司其他部门之要求.(4)在自己职责或权力范围内.(5)在指定的时间内完成工作.由上可以看出,品质定义不单适合于生产或产品上,也同样适合于公司每一个部门上司与下属的关系.如果下属是供应商,上司是顾客,上司列出合理的工作要求,如工作之安排,指定的目标,工作认真,依时做好等,如下属能准确做到,则下属就是符合品质,同样下属代表客户,上司代表供应商一样可行.例如下属可提出关于工作所需的训练或教育,工资增长,升迁之机会,如上司能够办到,则对于下属而言,该上司一样是符合品质的.对品质定义的理解要牢牢抓住“符合规格”四字,品质不是用来衡量一件产品好或坏的标准,一件产品也许是较完美的,但若不符合客户的要求则不是好的品质,客户的要求对我们来说便是规格.3、品质的系统—预防错误以往品质的哲学是要翻查,矫正及严谨的控制来避免错误.而现在最有效能达到高品质的方法是预防错误.员工要被训练到“第一次就把工作做好”来预防错误之产生,这种方法除了保证高品质之外更能达到低成本效益.预防错误是要使工作程序更趋完善与合理化,而不在于解决问题本身,如果在工作中只忙于去解决问题,那么问题还会不断地产生.如果我们通过改善系统,提供有效的方法去预防,就从根本上控制了问题即防患于未然,所以高效率的公司通常会花80%的时间在找寻问题的起源和改善系统,而低效率的公司会花90%的时间去解决遇到的问题,而从未考虑用何种方法去预防问题.4、品质的标准—零次废率对品质的标准而言,零次废率只是一种理想状态,实际上任何一家公司,无论品质系统多完善,都不可能达到零次废率,但我们可通过不断完善系统而无限地接近它.5、1999品质的衡量—偏差的代价我们是用错误及有关的代价来衡量一件产品或工作是否高品质,不符合规格的代价可以是10倍,100倍,甚至1000倍于原先的成本.例如营业部发出错误的指示导致生产部生产了错误的产品而导致顾客退货,那么,生产部,品管部,业务部,顾客服务部均需浪费很大的资源寻找之所在,接着而来的是修理费用,运输费用,调派人手在本地或国外重工之费用,维修人员的机票,住宿费等费用之高可想而知,最坏的是因顾客印象不佳而不下订单.二.品质的三不原则.不进不良品不产不良品不出不良品此三不原则对处于生产链上各环节的人员提出了明确的品质要求.事实上每个人员在生产链中都扮演了双重角色即供应商与客户对前制程而言我们是客户,对后制程而言我们是供应商.首先,进料是品质的第一道关口,原材料既已不良,再谈品质是一句空话,所谓投入的是垃圾,制造的是垃圾,所以进料人员一方面必须督促厂商改善系统,以预防不良产品,再把不良品拒之门外.其次,制程人员必须树立“品质从我做起”的观念,严格按要求作业,不放任何的不规范行为,以确保不产不良品,因为前制程的不良会造成后制程的困扰,即流毒无穷.三.品质管制演进史.品质管制从初级阶段到高级阶段,不断地演变进化,其发展历程大致经历了以下阶段:第一阶段:操作者品质管制(十八世纪)这一阶段可称为品质管制的萌芽期,其特征为产品从头到尾,由同一人负责操作,检验及处理,这种方式类似于一个人既为球员又当裁判,其判断的公正性如何自不言而喻.第二阶段:领班者品质管制(十九世纪)这一阶段可称为品质管制的觉醒期,其特征为多数人在一个领班的监督之下,由领班来负责每一个作业员的品质,这种方式已把操作与检验都分开,但品质管制工作并设有专职化.第三阶段:检验员品质管制(一战期间)这一阶段可称为品质管制的发展期,其特征为指定专人负责产品检验,与前两个阶段相比,此阶段把品质管制的工作赋予专职的人员来负责,但此阶段对品质管制的工作依然停留在对产品之检验上. 第四阶段:统计品质管制(Statistical Quality Control)这一阶段可称为品质管制的转型期,自1924年美国W.A She Wart利用统计手法提出第一管制图开始,以此品质管制进入了新纪元,同时抽样检验亦诞生.与前三个阶段相比,此阶段对品质管制的工作已不再停留于对产品的检验,而是深入到产品的生产过程,统计手法的运用使品质管制开始对制程发生作用.另外,抽样检验的诞生亦提高了工作效率. 第五阶段:全面品质管制全面品质管制是把以往品管的做法前后延伸至市场调查,研究发展,品质设计,原料管理.品质保证及售后服务等部门,建立品质系统.第六阶段:全公司管理(Company—Wide Quality Control ).即结合全公司所有部门的每一员工,通力合作,构成一个能共同认识,易于实施的体系,使生产的各要素,每一阶段均能有效管理,且全员参入,即为CWCN.第七阶段:全集团品质管制(Group—Wide Quality Control ,GWQC)结合中心厂,协力厂,销售公司成一个庞大的品制裁系统即GWQC.四、如何防止不良品.不良品的来源主要与以下五个方面的困素有关即4MIEMan—人Method---方法Material---材料2Machine---机器Environment---环境因此,要想有效防止不良品,须以以上五个方面着手.(1)稳定的人员.影响企业发展的各因素中,人是最重要的因素,人员稳定程度往往反映员工对企业的认同程度,在高人员流动率的企业,一切成长的条件将随人员的流动而流失.(2)良好的教育训练.企业成长的关键在于人,而人的工作熟练程度对于效率的提升,品质的稳定有决定性的影响,一套良好的教育训练计划在公司是很重要的.(3)建立标准化.标准化即制度化,制度建立,则有法可依,公司只有建立一套完善的品质制度,各项作业各个专案才有一个统一的标准依循,事实上ISO 9000也是一套制度,ISO 9000之实施事实上也是作业标准化,制度化,文件化的过程.(4)消除环境之乱象.品质产生变异的一个原因是环境因素,要解决这一问题,则推行5S很为有效.(5)推行统计品管(SQC—Statistical Quality Control)统计品管重在利用统计分析以发现潜在不良,有目的的改善制程,进而提升品质.(6)稳定的供料厂商.(7)完善的机器保养制度.五、抽样检验.(1)来源及定义:源于二战中的美国,其定义为以群体中,随机抽出一定数量的样本,经过试验或测试后,以其结果与判断基准作比较,然后利用统计方法,判定比群体是合格或不合格的检验过程,谓抽样检验.(2)抽样检验的分类.A.规准型抽样检验.同是考虑交货者及验收者的利益和损失,而判断群体的合格与不合格.B.选别型抽样检验.对于判断为不合格的群体,采取整批全检,并将全检后的不良品退换良品.C.调整型抽样检验.依照检验的结果采用:a.正常检验.b.加严检验.c.减量检验.D.连续型抽样检验.适用于大量生产而连续生产的产品不断流动时的抽样检验.(3).抽样检验与全数检验之采用.抽样检验并非任何场合都适合,有时须作全检,主要视检验群体的性质,数量,体积大小或检验所产生的费用或检验方式而定.适用抽样检验的场合:3A.破坏性检验,如材料强度试验.B.检验群体数量多,如螺丝等.C.检验群体体积大,如原棉等.D.产品属于连续性物品,如棉纱等.适用物全数检验的场合:A.检验快,费用少,如灯泡点火试验.B.产品必须全数良品.C.产品中只要有少数不良品,就会严重影响人的生命财产安全.(4)抽样检验的优劣.优点:A.费用比全检少.B.检验数少,可较详细.C.判断不合格,全部退货,可刺激供方加强品质.缺失:A.虽判为合格,也难免有不良品.B.可能把良品群体判为不合格,亦可能把不良品的群体判为合格.(5)MIL—STD—105E II抽样步骤.(6)MIL—STD—105E II全称为:Military Standard 105E II即军事的或军方的标准.其抽样步骤如下:A.决定品质基准.B.决定品质允收水准AQL.C.决定检验水准,通常使用II级.D.群体批之构成,尽可能接近同一条件下之产品.E.求样本代字.F.决定抽检方式,使用一次抽样还是多次抽样.G.决定检验的严格性.a.一般开始使用正常检验.b.正常→加严:连续五批中有二批拒收.c.加严→正常:连续五批允收.d.正常→减量:连续十批全被允收.e.查出抽检方式:f.由表上查出样本代字的行.g.由表上查出所指定AQL的列.h.由样代字的行与AQL值的列交会点,查出合格(AC)判定个数与不合格(RE) 判定个数.六、品质成本.企业内推行品管不力或品管功能不彰,分析原因,相当程度上企业主管们对于品质成本缺乏认识,品质成本是品抽经济性的一部分,着眼于确保和保证满意的品质时所发生的费用,以及当没有获提满意的品质时所受的损失.员工教育是预防成本.品质检验是鉴定成本.4不良品是失败成本.销售收入=品抽成本+制造成本+利润品质成本可分为: 个字目,21个细目.A.品质工作费.B.品质培训费.C.品质奖励费.D.产品评审费.E.品质改进措施费.F.工资及福利奖金.(2)鉴定成本.鉴定成本是指评定产品是否满足规定的品质要求所需的费用,有4个细目.A.检测试验费.B.工资及福利奖金.C.办公费.D.检测试验折旧费.(3)内部损失成本.内部损失成本,是指产品出厂前因不满足规定的品质要求而造成损失的费用,有5个细目:A.废品损失.B.返修损失.C.返工损失.D.事故分析处理费.E.产品降级损失.(4)外部损失成本.外部损失成本是指产品出厂后因不能满足规定的品质要求而造成损失的费用,有5个细目.A.索培费用.B.退货损失.C.保修费用.D.诉讼费用.E.产品降价损失.品质成本是在60年代由美国品管专家费根堡姆博士提出并将它作为全面品质管理的三在基石之一,许多实践证明,通过改善品质成本,企业可以获得可观的经济效益,品质成本的作用如下:A.可使产品成一核算完整,准确反映产品品质现状,建立品质成本后,可纠正产品品质好坏,在产品中得不到准确反映的情况,并有效控制废品损失,同时可将控制废品所节省的费用,用于各项产品品质合理预防性开支中,增加经济效益.B.品质成本是衡量企业品质管理成效的手段.通过品质成本控制和考核,可以检验分析品质职能的成效,如:企业人,财,物在品质形成过程中的使用情况;从经济上分析产品品质形成过程是否处于受控状态;提供品质成本信息,以此优化品质管理,控制降低产品总成本.C.建立品质成本有助于分析企业效益.5品质成本与产品产量都是企业效益的组成因素,以往企业往往注意销售额多,重视产品品质成本少,建立品质成本后,企业效益核算将更符合实际了.D.为用户提供品质成本费用数据,提高信誉.对一些机电产品及涉及安全和品质后果严重,价值昂贵的产品,企业提供品质成本数据单,表明该产品品质是在严格的品质管理中完成的,不仅有利于产品之审定,也为用户对产品品质要求作出保证,提高产品信誉.七、品管功能及工厂检验制度设计.品管部要想在公司充分发挥自己的效用,首先必需清楚在公司主要丞担哪些品质责任,一般而言,品管部应具有以下之责任:(1)对全公司品质管制教育之实施.(2)品质活动之制定与推动.(3)品质规范之建立.(4)制程能力之解析.(5)异常之对策改善活动.(6)提供管制图或品质报告.(7)供料厂商之辅导,评核.(8)客户品质报怨之处理.(9)品质成本计算.(10)各种检查工作之执行.一般而言,工厂品管制度之建立可以以下方面考量:(1)进料品质管制.(2)制程中品质管制.(3)出货品质管制.(4)仪器管理.(5)信赖度测试.(6)品质稽核.(7)品质系统文件管制.二.ISO 9000系列.1.ISO及ISO 9000之理解.ISO即国际标准组织(International Organization For6Standardization),创立于1946年总部设于瑞士日内瓦,系由各国标准团体所组成的世界性联盟,由各个会员国所组成,各国均以最具代表性之标准制定组织为加盟代表.该组织成立的宗旨是“制定统一标准,促进国际合作”,每月约出版新订或修订标准800种,制定标准的单位为技术委员会(TC),其下有分科委员会(SC)及各个工作小组(WG),基本上各项标准由技术委员会所制定,在ISO理事会批准成为国际标准之前,需经至少75%会员团体投票通过,并且每五年检讨标准一次,ISO 9000—品质管理与品质保证系列标准,是由ISO/TC 176品质保证技术委员所制定,并于1987年正式公布.2.ISO 9000之来源及发展历程.ISO 9000最初来源于美国,二战结束后世界形成了以美,苏两个超级大国对抗的格局,虽然世界性的战争已基本消除,但局部战争依然存在,甚至部分地区有升级的趋势,美,苏两国军备竞赛愈演愈烈,因军工产品与人的生命,财产安全有关,因此其生产过程必须严格控制,在此情况下,美国于1959年出台了一个美军品保标准MIL—Q—9858 ( 《质量大纲要求》).后来逐渐发展成为今天的国际标准即ISO 9000.其发展的历程可用以下流程图概述:71959年《质量大纲要求》《检验系统要求》标准编号1968年1979年Part1 Part2 Part3至今3.ISO 9000的组成及适用情况.ISO 9000—94版系列标准包括如下内容:ISO 9000(1994年版)—品质管理与品质保证术语.8ISO 9000(1.2.3.4)94版—品质管理与品质保证标准选用之指导纲要.ISO 9001—品质制度,开发设计,生产,安装和售后服务的品质保证模式.ISO 9002—品质制度,生产,安装和售后服务的品质保证模式.ISO 9003—品质制度,最终检验与测试的品质保证模式.ISO 9004(1.2.3.4.5.6.7)—品质管理与品质制度要项指导纲要.以上各标准的内容现简述如下:ISO 8402—确定了用于产品或服务与品质概念相关的,基本和重点术语条目共157个,并给出了定义,这些定义是品质和品质管理领域内统一使用的术语,具有准确性,通用性,协调性,实践性和发展性.ISO 9000—指导性的总体概念标准,是品质管理和品质标准的选择,使用和贯彻指南,它阐述了重要品质术语的定义及概念上的差别与联系,对选择,使用品质管理和品质保证的两类标准作了说明,并指出本品质体系标准适用于合同与非合同两种环境.ISO 9001—9003适用于合同环境下供需双方的通用外部品质,保证它是供需双方或供方必须选择确定的三个品质保证模式,其中ISO 9001适用于负有开发,设计责任的企业,而ISO 9002适用于引进开发设计的企业,ISO9003适用于具有最终检验与测试能力的企业.4.企业应如何选择品质保证模式.ISO 9000系列标准的三个不同水平的品质保证模式,是在分析了大量的具体产品的基础上抽象典型,按照产品的重要性和复杂程度设计的,它们覆盖了企业品质保证模式的所有情况,具有较强的代表性,这就为供需双方应用外部品质保证提供了较大的选择余地.企业生产的产品的重要性和复杂性要求商,对产品品质有直接影响的要素就多,作为外部品质保证体系实施控制的要素就要多,供方实施品质保证所需的成本就大,因而企业应根据合同的要求,产品的结构和自身情况进行选择.ISO 9001包括20项体系要素,是三个模式中水平最高的一个,ISO 9002包括19项体系要素,次于ISO 9001,而ISO 9003只包括16项体系要素,是三个模式中水平最低的模式.依照合同中对供方品质系统的要求,随着国际上对供品质系统的要求,很多买主往往在合同中规定所要提供的品质系统保证模式的要求,如国际招标书,企业只有依照这些要求,方能使产品进入国际市场.95.品质管理系统与品质保证系统之区别.ISO 9000系列标准向用户提供了两类共4个品质系统标准,它们是ISO 9004品质管理体系标准和ISO 9001,ISO 9002以及ISO 9003品质保证系统标准,这两类标准分别指导企业的品质管理和品质保证,为用户提供合格,满意的产品,这两类标准既有区别又有联系,区别主要表现为:(1)对象不同品质管理系统是针对企业全面品质管理的需要而制定的,因而一个企业只有一个品质管理系统.品质保证系统是针对企业生产的产品,为能满足用户的需求建立的一个企业,由于产品的复杂程度,安全性能以及用户对产品附加要求不同,可以对需要的部分或个别类型产品建立品质保证系统,故,一个企业可以有几个品质保证系统.(2)功能不同品质管理系统是为企业的品质管理提供系统全面的管理标准,而品质保证系统的功能是向用户或第三方提供外部证明,证实其产品符合合同或规定的要求.(3)品质坏境不同当企业建立了健全的品质管理系统,能生产满足用户所需的产品时,企业所处的是非合同环境或生产标准产品,反之,一个企业建立了完善的品质管理系统仍不能满足用户对产品的要求时,企业所处的是合同环境,生产非标准产品.这两个系统不是平行并列,也不是各自独立的,而是有着密切的内存联系,任何一个企业,无论处于哪种环境,首先它一方面可以满足内部管理之需要,使体系正常运行,另一方面直接满足非合同环境的要求,如果遇到合同环境,则以已经建立的品质环境中抽出若干品质系统要素,组成特定的品质系统,满足合同及环境要求,从这个意义上说品质保证系统是以品质管理系统中派生出来的,品质管理系统是基础.6.推行ISO 9000的过程.10(1)顾问公司评估之流程.(2)ISO 9000导入与推展流程.11(3)ISO 9000管理制度建立之流程12(4)品质系统文件制作流程.13(5)认证申请作业流程7.ISO 9000之精髓.14制度须有涵盖性:所有与品质有关的人,事,物,及其他活动皆须纳入管制.制度合理化且有说服力:制度合理化即所建立的品质制度必须适合公司的实际动作,制度不能太严,不能脱离实际,否则制度不能落实下去,制度具有说服力即能够让客户相信品质制度对于确保品质是有效的.以证据证明按制度实施:品质制度是否贯彻落实,必须提供足够的证据作为品质制度切实执行的佐证资料.说,写,做一致:即实际作业与制度要求一致.注重预防且强调事后矫正能力:ISO 9000制度重在对影响品质的各要素于生产前进行有效管制从而达到防患于未然之目的. 8.品质系统文件架构.品质手册:为达成品质经营目标之要求,并落实有效地执行品质系统所使用最重要之基本原则,其目的在于提供一套执行与维护品质系统运作之有效性及适切性的最基本的指导纲要原则.程序文件:为维护品质系统运作,在公司内各组织间,各机能间,各项作业间,将其间之目的,范围,权责单位,作业内容透过流程,步骤,顺序以流程图加以阐示.指导书:为有效落实执行品质系统,将每一项动作基准加以说明,包括适用范围,使用工具,设备,仪器,治具,方法方式及人员,时间,地点等详细说明,便于第一线人员使用.15表单:为记录有关品质系统落实执行情形及维持系统运作之佐证资料所使用之空白表格.(1)品质手册之结构.A.封面页a.公司中英文名称b.手册中英文名称c.文件编号d.手册流水号e.制定,审查核准栏f.公司地址,电话,传真,公司标志g.文件发行章B.目录C.公司简介,包括创立时间,发展沿革,规模,产品名称等D.品质政策,目标,包括订定方式,宣导方式E.公司组织架构,品保组织架构F.品质管理权责h.高阶管理人员之权责i.各部门之权责G.品质手册制定,核准,修订之规定H.品质系统概述:ISO 9000之各要素在本公司的概述I.ISO 9000条文与公司程序书之对照(2)程序书与三阶文件之架构A.目的B.范围C.权责D.定义:文件中不易理解之名词E.作业内容F.流程图G.相关文件H.所用表单九、ISO 9000辅导步骤1617十、认证型态第二者认证第三者认证十二、总体◆经营者的决心与员工的共识◆全公司各部门、各阶层的共同参与、执行◆积极的心态,彻底地执行◆循序渐进,面面俱到◆横向性整合,纵向性落实◆持续性推动,形成良性循环附录:1词汇1品质——一项产品或服务整体的特征和特性,此种整体性的特征和特性,具有满足顾客规定,或潜在需求的能力。
品管部新进人员基础培训

品管部品管员培训资料一、认识品质管理1、什么是质量?质量是一个特性满足要求的程度。
2、什么是质量管理?质量管理是指导和控制组织的关于质量体系相互的活动。
通常包括质量方针,质量目标,质量策划,质量控制,质量保证,质量改进。
3、什么是检验?检验是通过观察和判断,必要是结合测量、实验所进行的符合性评价。
4、什么是验证?验证是通过提供客观证据对规定要求已得到满足的认定。
5、确认的定义?确认是通过提供客观证据对特定的预期使用及应用要求已得到满足的认定。
二、QC基础知识1、什么叫做QC?简易的讲就是质量管理。
2、质量管理发展历程2、1认识品质管理想获得品质必须认识品质管理,品质管理从无到有,从单一到系统,经历了几个阶段。
2、1、1质量检验阶段-----QC(1920----1940年)特点:专业检验工人按照技术文件的规定,采用各种检测技术,对产品进行各项检验和试验。
做出合格与不合格判断,合格才能出厂,才能保证到达客户手中的都是合格产品。
优点:不合格品通向市场之路被切断。
局限性:能够“把关”,不能“预防”。
2、1、2质量控制阶段SQM(1940-----1960年)特点:将数理统计方法运用于质量控制之中,主要是在生产过程中使用大量的统计手法(柏拉图、排列图、层别图、控制图)等。
通过统计手法获得品质波动信息,对这些信息加以汇总,分析,并及时采取措施消除波动异常因素,提高一次合格成品率,减少废品造成的损失。
优点:既能把关。
又能预防。
2、1、3全面质理管理TQM(90年代)特点:随着科学技术的发展,大型复杂的机械,电子新产品的出现,使人们对产品的安全性,可靠性,可维修性等性能提出了更高的要求,而这些光靠生产过程进行质量控制已经无法控制,要达到上述要求,必须将质量活动向市场调查,产品设计,售后服务等过程扩展,以实现在产品形成过程中进行质量控制。
全面质量管理的含义是“以客户为中心、领导重视、全员参与、全部文件化、全过程控制、预防为主、上下工序是客户、一切为用户”的管理思想和理念。
品管员基础知识.doc

品管(QC)员基础知识—员工培训教材一、何谓品管?品管就是以质量管理、控制、预防为主,组织有关人员利用品管的各项职能和控制手法达到产品质量能满足客户需求的目的。
二、品管的职责协助现场和监督现场抓好质量,为公司质量系统能够有效运用和自我完善。
从原物料到入库之各阶段进行检验和监督,以此来提升产品的质量及企业的商业形象。
三、抽样检验1、定义:从群体中,随机抽出一定数量的样本,经过试验或测定以后,以其结果与判定基准作比较,然后利用统计方法,判定此群体是合格或不合格的检验过程。
2、用语说明:A、检验群体:所提出之同一生产批(LOT)的制品谓检验群体,简称群体。
B、样本:从群体内随机抽取部分的单位体,谓之样本。
3、合格判定数:作为判定群体是否合格的基准不良数,谓合格判定数,符号以C(AC)表示。
4、缺点:制品的单位其质量特性不合乎契约(合同、订单)所规定的规格、图面、购买说明书等要求者,谓之缺点。
缺点一般可分为:A、致命缺点:有危害制品的使用者及擒携带者的生命或安全之缺点。
B、重缺点(即主缺点):不能达成制品的使用目的之缺点。
C、轻缺点(即次缺点):并不影响制品使用目的之缺点。
5、不良品A、一般制品均有多种质量特性,而这些质量特性里,所特定须检验项目,谓检验项目。
B、如果其中有一个或一个以上检验项目不合乎规格时,这个制品就被判为不良品,全部检验项目都合乎规格的制品叫良品。
四、抽样检验的形态分类1、规准型抽样检验主要是以同时考虑交货者及验收者的利益和损失,而判断群体的合格与不合格为目的。
X>C拒收x<=c允收2、选别型抽样检验对于被判为不合格的群体采取整批全检,并将全检后的不良品退换应品。
3、调整型的抽样检验依照检验的结果采用:正常检骑、加严检验、减量检验。
在长期交易中,利用紧或松的方式,以确保质量。
4、连续生产型抽样检验适用于大量而连续生产的产品不断流动时的抽样检验。
5、抽样检验与全数检验之采用A、适用于抽样检验的场合a.属于破坏性检验,如材料强度试验。
品管人员应知应会知识
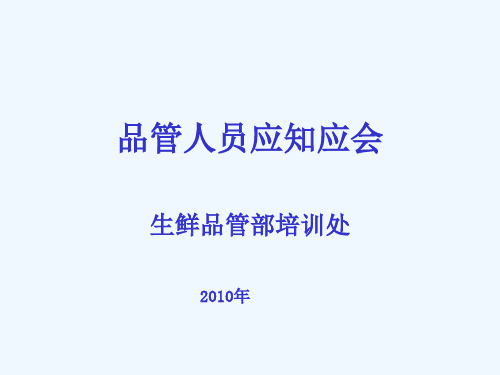
三、微生物与卫生
三、微生物与卫生
三、微生物与卫生
三、微生物与卫生
三、微生物与卫生
三、微生物与卫生
三、微生物与卫生
三、微生物与卫生
三、微生物与卫生
三、微生物与卫生
三、微生物与卫生
三、微生物与卫生
三、微生物与卫生
三、微生物与卫生
三、微生物与卫生
三、微生物与卫生
三、微生物与卫生
三、微生物与卫生
三、微生物与卫生
四、质量管理理念
➢ 一、集团公司十二项原则: 集团经营、管理原则建设的坚决方针、指导思想:“不为利益而丧失 原则,不为信任而丧失监督”。
➢ 原则一:坚决反对任何形式的腐败; ➢ 原则二:一切为经营服务原则; ➢ 原则三:创新、创意、创造; ➢ 原则四:质量一票否决制; ➢ 原则五:人才培养一票否决制; ➢ 原则六:任何岗位必须建立完善的评价体系(职责、目标、机制、评
二、卫生消毒基本知识
3.二氧化氯:(1)、 新配制的二氧化氯消毒水应为黄绿色 溶液,在使用过程中如颜色消褪,则必须更换;车间用的二 氧化氯消毒水要求每四小时更换一次;(2)、模具消毒时, 必须浸泡五分钟以上;员工手消毒时,必须浸泡一分钟以上; 拆袋产品浸泡一分钟以上;产品在消毒时必须完全浸入消毒 水中,30秒以上;(3)、生产用的器具消毒时,一定要先 用水将表面的油污洗干净后,再浸入消毒水中。
价、回报、责任与淘汰); ➢ 原则七:业绩评价末位淘汰; ➢ 原则八:领导负责制;
四、质量管理理念
➢ 原则九:首问负责制; ➢ 原则十:成本管理永无止境; ➢ 原则十一:现金交易原则; ➢ 原则十二:保密原则; ➢ 重点注解:原则四:质量一票否决制 ➢ ①质量是百年企业的根本,更是食品企业的生命线,质量真正体现了
品管员品质知识培训教材

市众盈电子品管员品质知识培训教材培训对象: 品管员培训容: 品管知识编制:审批:版本:A实施日期:2007-12-1目录第一章ISO9000基础知识3第二章品管基础知识5第一节质量的概念 5 第二节质量管理 8 第三节品管发展吏 11 第四节名称解说 11 第五节品管部组织职能 12 第六节品质控制的关键 14 第七节影响品质的因素 15 第八节PDCA 17 第九节品管工作的性质和技巧 19 第十节检验控制方法 20 第十一节质量检验的方式 23 第十二节质量统计和分析 31 第十三节不合格品管制 31 第三章进料品质控制 33 第四章制程品质控制 36第一章 ISO9000基础知识1.ISO的含义:ISO是国际标准化组织,其英文 International Organization For Standardization的缩写.2.ISO的核心容是什么?ISO的核心容是(1)文件及资料控制, (2)品质审核,(3)纠正及预防措施3.ISO核心思想是什么?ISO的核心思想是纠正及预防4.公司的品质最高决策者是谁?ISO9000工作的推行一般由谁来完成?公司的品质最高决策者是公司的最高管理者(总经理,或董事长);ISO9000工作的推行一般由管理者代表来完成,有的工厂由品管部同时代行其权力。
5.ISO9000文件结构怎样?BOM单是哪一阶文件?ISO9000文件共分四层:第一层为质量手册(质量方针),第二为程序文件,管理办法,第三层为作业规、检验标准,第四层为记录、报表;BOM表单是第三阶文件6.ISO的精神是什么?ISO的精神是说,写,做一致(写我所做,做我所写、证明给我看)7.ISO的组成部分有?●ISO的基本原理和术语●质量管理体系------要求●ISO9004实施●ISO19011管理体系审核指南●其它8 ISO9001:2000版特点?⑴强调了“过程”管理模式⑵注重了“顾客”导向⑶提出了法律要求⑷明确了资源管理围⑸强调了对最高管理层的要求⑹注重了目标管理⑺扩充了人力资源管理的围等9.2000版ISO000族文件结构是?ISO9000 ISO9001 ISO9004 ISO9011 质量管理体系基础知识并规定质量管理体系术语规定质量管理体系要求提供考虑质量管理体系的有效性和效率两方面的指南提供审核质量和环境指南ISO10006ISO10007ISO10013ISO10014ISO10015ISO10017✧质量管理原理---选择和使用✧小型企业的应用10。
品管基础知识培训质量控制-精选文档

互检
下道工序员工对上道工序员工生产的产品或作业方法进 行检验;或员工相互对各自生产的产品进行检验。在互检过 程中员工要清楚上道工序或其他员工所生产产品的质量标准 和作业标准。
制造过程的质量控制
首检 对生产的第一件产品进行检验。首检的时机包括:关键 工序的作业人员变更后的首件产品;生产设备变更或维修 后生产的首件产品;生产工艺参数调校及生产设备状态调 整确定后的首件产品;生产工艺方法改变后的首件产品; 新产品第一次生产或换型后的首件产品;生产换班后或更 换生产批次后生产的首件产品。 巡检 对生产过程和产品质量进行巡回检查。巡检要规定检查的 频次、检查的标准,对检查结果进行记录。 全检 按照规定对产品的一种或几种质量特性实行全数检验。如 阳极组件的频率调整、白球组件的泄漏检查、磁控管的出 厂检查等。
输入
实施
输出
制造过程的质量控制
1、工序是制造过程控制的主要环节。工序控制的基本概念包 括:工序、工序质量、工序分析、工序控制、工序质量改进 。工序质量控制的目的是为实现产品设计质量通过制造最终 达到预期目标及满足用户要求 工序:是指产品制造过程中的基本环节。该环节为保证产品 质量要求,必须具备必要的生产手段和技术条件。 工序质量:是指工序本身对满足产品制造质量要求的优劣程 度。工序质量可通过制造的产品质量来体现和反映,也可以 通过工序质量因素状态来表示。
出货通报
AQL
检验标准
指导书
检验
检验报告
出货品质控制(OQC)
OQC的作业方式 1、实施出货检验的时间:出货前一定时间(具体时间根据公 司实际情况而定)内完成检验工作并出具检验结果。流出如 下:
制造过程的质量控制
1. 五按 按程序、按线路、按标准、按时间、 按操作指令 2. 五干 干什么、怎么干、什么时间干、按什 么线路干、干到什么程度 3. 五检 由谁来检查、什么时间检查、检查什 么项目、检查的标准是什么、检查的 结果由谁来落实
品管学习基础知识材料

品质常识一、品质术语1.品质:就是产品质量,亦即产品符合标准的程度并且满足客户需求的各种要素属性的总和。
2.品质保证:通过采取事先措施,把不良现象消灭在萌芽状态,从而保证所生产的产品符合要求的过程;3.质量:产品,体系或过程的一组固有特性满足顾客和其他相闫方要求的能力;4.过程:使用资源,将输入转化为输出的活动系统;5.产品:使用资源,将输入转化为输出的活动系统的结果(硬件/软件/服务/流程性材料);6.标准:指的是品质规范,技术指标,限度要求等有关产品外观,功能,结构方面的特性和接收准则;7.签板:指的是对样板进行签名确认;8.限度样板:表示的特性状态为最低的接收控制限度,低于此板时拒收;9.标准样板:表示的特性为最佳的值;10.合格:满足要求;11.不合格:未满足要求;12.缺陷:未满足预期或规定用途有关的要求;13.预防措施:为消除潜在不合格或其他潜在不期望情况的原因所采取的措施。
14.纠正措施:为消除已发现的不合格或其他不期望情况的原因所采取的措施。
15.纠正:为消除已发现的不合格所采取的措施;16.偏离许可:产品实现前,在限定的产品数量或期限内,对特定用途允许其偏离原规定要求的授权;17.让步:对使用或放行不符合规定要求的产品的授权;18.放行:进入过程下一个阶段的授权;19.返修:为使不合格产品满足预期使用对其所采取的措施;20.返工:为使用不合格产品符合要求对其所采取的措施;21.降级:为使不合格产品符合不同于原有的要求而对其等级的改变;22.报废:避免不合格产品原有的预期使用而对其采取的措施;23.本体不良:是材料本身发生的不良;24.作业不良:是材料在制造过程发生的不良;25.客户:被服务的对象,一般分为外部客户和内部客户;26.认证:由可以充分信任的第三方证实某一经鉴定的产品或服务符合特定标准或规范性文件的活动。
二、英文缩写1.QC:Quality control(品质管理);2.QS:Quality system(品质系统);3.IQC:Incoming quality control(进料检验)4.IPQC:In process quality control(制程检验)5.OQC:Outgo quality control(出货检验)6.QA:Quality assurance(质量保证)7.QE:Quality engineer(品质工程师)8.SOP:Standard Operating Procedure(作业指导书)9.SIP: Standard inspection Procedure(检验规范)10.B OM: Bill of material(物料清单)11.I SO:Intemational organization for standardization(国际标准化组织)12.A QL:Acceptable quality level(允收品质水准)13.C AR:Corrective action requirment(纠正措施要求)14.C R:致命缺陷、MAJ严重缺陷、MIN轻微缺陷、AC允收、RE拒收三、基本知识1.检验七要素:(1)目标、(2)抽样、(3)比较、(4)判定、(5)结果、(6)处理、(7)记录。
嘉富盛品管人员基础知识
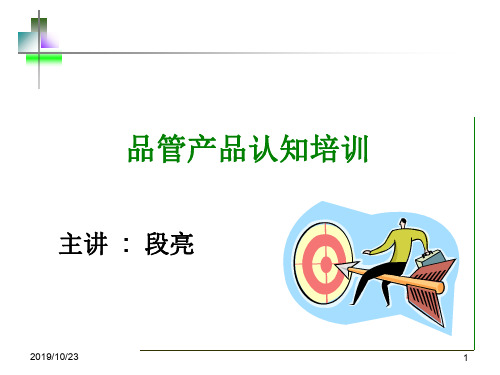
• *品质成本(Quality Cost):预防成本,鉴定成本,内部 失败成本,外部失败成本
• 停止未端大量的检验行为,而应力求改善,从根本做 起.他认为未端检验绝不可能获致有竞争力的品质.
2019/10/23
一些基本特性用于定义“好的”测量系统,它们包括:
足够的分辨率和灵敏度(1:10法则) 测量系统应该是统计控制的。(普通原因而非特殊原因) 测量系统的变异性必须比公差带和制造过程变差小;依据特性
的公差评价测量系统。 测量系统统计特性可能随被测项目的改变而变化。若真的如此,
则测量系统最大的(最坏)变差应小于过程变差和公差带两者 中的较小者。
– 对于产品和过程条件,可能是评价人、环境(时间)或方法的误差; – 通常指A.V.-评价人变差; – 系统间(条件)变差; – ASTM E456-96包括重复性、实验室、环境及评价人影响。
• GRR或量具R&R
– 量具重复性和再现性:测量系统重复性和再现性的合成评估; – 测量系统能力:依据使用的方法,或不包括时间影响。
有的过程控制管理,统计或逻辑技术均能应用。 通过评价过程结果或参数,可以获得过程正在做什
么的知识。------检验
2019/10/23
13
1 通用测量系统指南—1.3测量过程
测量系统的统计特性
理想的测量系统在每次使用时,应只产生“正确”的 测量结果。每次测量结果应该与一个标准值相符。一个能 产生理想测量结果的测量系统,应具有零方差、零偏倚和 对所测的任何产品错误分类为零概率的统计特性。
品管产品认知培训
主讲 : 段亮
2019/10/23
品管管理基础知识培训资料
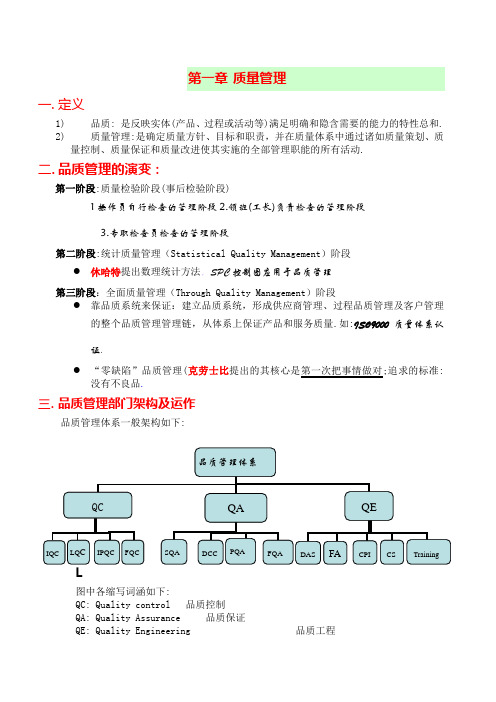
第一章质量管理一.定义1)品质: 是反映实体(产品、过程或活动等)满足明确和隐含需要的能力的特性总和.2)质量管理:是确定质量方针、目标和职责,并在质量体系中通过诸如质量策划、质量控制、质量保证和质量改进使其实施的全部管理职能的所有活动.二.品质管理的演变:第一阶段:质量检验阶段(事后检验阶段)1操作员自行检查的管理阶段2.领班(工长)负责检查的管理阶段3.专职检查员检查的管理阶段第二阶段:统计质量管理(Statistical Quality Management)阶段●休哈特提出数理统计方法,SPC控制图应用于品质管理第三阶段:全面质量管理(Through Quality Management)阶段●靠品质系统来保证:建立品质系统,形成供应商管理、过程品质管理及客户管理的整个品质管理管理链,从体系上保证产品和服务质量.如:ISO9000质量体系认证.●“零缺陷”品质管理(克劳士比提出的其核心是第一次把事情做对;追求的标准:没有不良品.三.品质管理部门架构及运作品质管理体系一般架构如下:图中各缩写词涵如下:QC: Quality control 品质控制QA: Quality Assurance 品质保证QE: Quality Engineering 品质工程IQC: Incoming Quality Control 来料品质控制LQC: Line Quality Control 生产线品质控制IPQC: In Process Quality Control 制程品质控制FQC: Final Quality Control 最终品质控制OQC: Outgoing Quality Control 出货品质控制SQA: Source(Supplier) Quality Assurance 供应商品质保证DCC: Document Control Center 文件控制中心PQA: Process Quality Assurance 制程品质保证FQA: Final Quality Assurance 最终品质保证DAS: Defects Analysis System 缺陷分析系统FA: Failure Analysis 坏品分析CPI: Continuous Process Improvement 连续工序改善CS: Customer Service 客户服务Training 培训1)供应商品质保证(SQA):是通过在供应商处设立专人进行抽样检验,并定期对供应商进行审核、评价,从源头实施品质保证的一种方法.主要职责:A.对从来料品质控制(IQC)/生产及其它渠道所获取的信息进行分析、综合,将结果反馈给供应商,并要求改善.B.根据派驻检查员提供的品质情报对供应商品质进行跟踪.C.定期对供应商进行审核、及时发现品质隐患D.不定期给供应商导入先进的品质管理手法及检验手段,推动其品质保证能力的提升E.根据本公司生产反馈的状况、派驻人员检验结果、对投诉的反应速度及态度对供应商进行排序,为供应商取舍提供依据.供应商管理的主要方法:A.驻检验员B.定期审核 ,审核项目包括:a>品质:包括管理职责;文件控制;质量计划;追溯性;检查与测试;工序控制/统计控制;计量;纠正/预防行动;搬运,存贮,包装,交付;培训;客户方面;品质成本;连续过程改善.根据以上内容作“供应商品质保证体系评价表”b>生产支持:包括物料管理;反应能力;生产性仪器设备布局;能力;变化点控制;设备、工具、治具设计、设备工具保养维修程序.c>技术能力及新产品导入.包括技术能力、工序能力d>一般事务:包括组织和管理;公司目标;生产和市场能力等C.定期对供应商排序:排序准则:a>SQA批合格率不得低于95%b>IQC批合格率不得低于95%c>部品抽入后的品质问题要求总的工序直通合格率不低于85%d>回复纠正行动报告(CAR)的态度和速度要及时响应,对问题作令人信服的分析,并有纠正预防措施e>交货期履行情况,能积极履行合约,并对廷期交货作合理说明f>审核结果分数至少在60分以上g>与本公司人员的在各项事务中配合是否良好D.帮助供应商导入新的体系和方法对供应商的评鉴,通常采用5R法:Right Quality(适质)、Right Price(适价)、Right Quantity(适量)、Right Time(适时)、Right Place(适地)2)来料品质控制(IQC):又称验收检验,是管制不让不良原物料进入物料仓库的控制点。
- 1、下载文档前请自行甄别文档内容的完整性,平台不提供额外的编辑、内容补充、找答案等附加服务。
- 2、"仅部分预览"的文档,不可在线预览部分如存在完整性等问题,可反馈申请退款(可完整预览的文档不适用该条件!)。
- 3、如文档侵犯您的权益,请联系客服反馈,我们会尽快为您处理(人工客服工作时间:9:00-18:30)。
国际实验室
国家实验室
国家认可的 校准机构
企业的校准 实验室
检测设 备制造厂
测量结果
生产现场
2019/10/15
12
1 通用测量系统指南—1.3测量过程
为了有效地控制任何过程变差,需要了解:
过程应该做什么? 什么能导致错误? 过程在做什么?
规范和工程要求规定过程应该做什么。 测量和分析活动是一个过程------一个测量过程。所
24
测量系统的有效分辨率 ( discrimination)
要求不低于过程变差或允许偏差( tolerance)的十分之一 零件之间的差异必须大于最小测量刻度
极差控制图可显示分辨率是否足够
– 看控制限内有多少个数据分级 不同数据分级(ndc)的计算为
零件的标准变差(PV)/ 总的量具变差(GRR)* 1.41. 一般要求它大于5 才可接受
– 当极差图中只有一、二或三个极差值在控制 界限内时。
– 如果极差图显示有四个或以上的极差值在控 制界限内,但超过1/4以上的极差值为零。
2019/10/15
27
2计量型测量系统研究—2.2稳定性
稳定性(Stability)
时间-2
用控制图的方法分析。
注:过程必须没有出现明 显可见的特殊原因影响。
测量不确定度和MSA:
MSA的重点是了解测量过程,确定在测量过程中的误差总量,及评 估用于生产和过程控制中的测量系统的充分性,目的是减少变差; 不确定度是测量值的一个范围,由置信区间来定义,与测量结果有 关,并希望包括测量的真值。
2019/10/15
20
1 通用测量系统指南—1.6测量问题分析
– 对于以分析过程为目的的测量系统,通常单凭经验来确定测量系统 的可接受性的规则如下:
• 误差<10%,通常认为测量系统是可接受的。 • 10%~30%,基于应用的重要性、测量装置的成本、维修成本等方面的
考虑,可能是可以接受的 。 • 超过30%,认为是不可接受的,应该做出各种努力来改进测量系统。 • 此外,过程能被测量系统区分开的分级数(ndc) ≥10为可接受, (ndc)
2019/10/15
10
1 通用测量系统指南—1.2术语/定义
溯源 示 例 国家
标准
引用标准 计量测试所
工作标准
(企业计量部门)
生产量具 (生产人员)
波长标准
干涉比测器
激光干涉仪
引用量具量块/比测
CMM
量块
夹量具
千分尺
2019/10/15
11
1 通用测量系统指南—1.2术语/定义
标准的传递
国际标准 国家标准 地方标准
2019/10/15
8
1 通用测量系统指南—1.2术语/定义
宽度变差(2) • 测量系统能力:
– 测量系统变差的短期评估(例如“GRR”包括图形)。
• 测量系统性能:
– 测量系统变差的长期评估(长期控制图法)。
• 灵敏度:
– 最小的输入产生可探测出的输出信号; – 在测量系统变化时测量系统的响应; – 由量具设计(分辨率)、固有质量(OEM)、使用中的维修及仪器
有的过程控制管理,统计或逻辑技术均能应用。 通过评价过程结果或参数,可以获得过程正在做什
么的知识。------检验
2019/10/15
13
1 通用测量系统指南—1.3测量过程
测量系统的统计特性
理想的测量系统在每次使用时,应只产生“正确”的 测量结果。每次测量结果应该与一个标准值相符。一个能 产生理想测量结果的测量系统,应具有零方差、零偏倚和 对所测的任何产品错误分类为零概率的统计特性。
2
2
2
obs actual msa
• 对产品决策的影响( Ⅱ区):
– 好的零件被拒收,也称为生产者风险或误发警报; – 坏的零件被接收,也称为消费者风险或漏发警报。
• 对改进决策的影响:
上限 Ⅰ
Ⅱ
下限
Ⅲ
Ⅰ
Ⅱ
– 改进生产过程,减小过程变差,没有零件出现在Ⅱ区;
– 改进测量系统,减小Ⅱ区的宽度,降低作出错误决定的风险。
<5为不接受,5≤ (ndc) <10为可选择性接收。
2019/10/15
22
1 通用测量系统指南—1.8分析时机
• 新生产之产品PV有不同时 • 新仪器,EV有不同时 • 新操作人员,AV有不同时(appraiser) • 易损耗之仪器必须注意其分析频率。
2019/10/15
23
2计量型测量系统研究—2.1有效分辨率
.28 .279 .2794
.28 .282 .2822
直尺 卡尺 千分尺
.28 .282 .2819
.28 .279 .2791
2019/10/15
25
2 简单测量系统实践—2.3稳定性
2019/10/15
26
2计量型测量系统研究—2.1有效分辨率
分辨率不足的表现 • 在过程变差的SPC极差图上可看出:
• 能力:
– 短期获取读数的变异性。
• 性能:
– 长期获取读数的变异性; – 以总变差为基础。
• 不确定度:
– 关于测量值的数值估计范围,相信真值包括在此范围内。
溯源性(ISO-VIM定义)
测量特性或标准值,此标准是规定的基准,通常是国家或国际 标准,通过全部规定了不确定度的不间断的比较链相联系。
和标准的操作备件确定; – 总是以一个测量单位报告。
• 一致性:
– 重复随时间的变化程度; – 一个一致的测量过程是考虑到宽度(变异性)下的统计受控。
• 均一性:
– 整个正常操作范围重复性的变化; – 重复性的一致性。
2019/10/15
9
1 通用测量系统指南—1.2术语/定义
系统变差
测量系统变差可以具有如下特征:
2019/10/15
17
1 通用测量系统指南—1.3测量过程
测量系统变异性的影响(续)
•对过程决策的影响: -把普通原因报成特殊原因;
-把特殊原因报成普通原因。
观测到的过程变差 实际的过程变差
2019/10/15
测量系统的变差
18
1 通用测量系统指南—1.4测量问题
评价一个测量系统时必须考虑的三个基本问题: 测量系统必须显示足够的灵敏性
3
一 品质的概念
• 质量的概念 • 质量:一组固有特性满足要求的程度。 • 固有特性:特性按类别分为:物的特性,感官的
特性,行为的特性,时间的特性,等 • 特性可以是固的有也可以是赋予的。其是相对的。 • 要求指“明示的、通常隐含的或必须履行的需
求或期望” • 质量具有经济性、广义性、时效性和相对性。
分辨力/分辨率(1/10) 有效分辨率
测量系统必须是稳定的
在重复性的条件下,测量系统变差只归因于普通原 因而不是特殊原因。
测量分析者必有经常考虑到这一点对实际应用和统 计的重要性。
在预期范围(被测项目)内一致可用于过程分析或过程 控制。
2019/10/15
19
1 通用测量系统指南—1.5测量不确定度
– 对于产品和过程条件,可能是评价人、环境(时间)或方法的误差; – 通常指A.V.-评价人变差; – 系统间(条件)变差; – ASTM E456-96包括重复性、实验室、环境及评价人影响。
• GRR或量具R&R
– 量具重复性和再现性:测量系统重复性和再现性的合成评估; – 测量系统能力:依据使用的方法,或不包括时间影响。
品管产品认知培训
主讲 : 段亮
2019/10/15
1
目錄
• 第一节 质量概念简介 • 第二节 产品用途及使用 • 第三节 质量管制重点及技巧
2019/10/15
2
一 品质的概念
• 品质 用经济的手段产生符合客户要求的产品.
• 在充满竞争性的经济社会中,品质改进与成本降低 方面从事持续的活动是维持企业生存的不二法门.
2019/10/15
4
产品用途及使用
• 产品使用 1,电源接插头—电源传输 如:T-11RB,T-14RA , HTJ-020-04-12 2,信号的传输 HTJ-064-04-02/03
2019/10/15
5
二,产品用途及使用
• 客户的生产方式 1, 组装
2019/10/15
6
1 通用测量系统指南—1.2术语/定义
量
值
时间-1
时间 稳定性
2019/10/15
28
2计量型测量系统研究—2.2稳定性
2019/10/15
29
2计量型测量系统研究—2.2稳定性
2019/10/15
30
2019/10/15
31
2计量型测量系统研究—2.2稳定性
造成不稳定的可能因素
• 仪器需要校准,缩短校准周期 • 仪器、设备或夹具的磨损 • 正常的老化或损坏 • 维护保养不好:空气、动力、液体、过滤器、腐蚀、尘土、清洁 • 基准的磨损或损坏,基准的误差 • 不适当的校准或使用基准设定 • 仪器质量不好—设计或符合性 • 仪器缺少稳健的设计或方法 • 不同的测量方法—作业准备、载入、夹紧、技巧 • 变形(量具或零件) • 环境变化—温度、湿度、振动、清洁 • 错误的假设,应用的常数不对 • 应用—零件数量、位置、操作者技能、疲劳、观测误差(易读性、
• 位置误差
– 位置误差通常是通过分析偏倚和线性来确定。 – 一般地,一个测量系统的偏倚或线性的误差若是与零误差差别较明
显或是超出量具校准程序确立的最大允许误差,那幺它是不可接受 的。在这种情况下,应对测量系统重新进行校准或偏差校正以尽可 能地减少该误差。