转炉炼钢自动控制基础及工艺61页
冶金转炉炼钢自动化控制的技术研究

冶金转炉炼钢自动化控制的技术研究1.引言冶金转炉炼钢是一种重要的钢铁生产工艺,其控制系统的先进性直接关系到炼钢过程的稳定性、产品质量和能源消耗。
随着自动化技术的发展,冶金转炉炼钢的自动化控制系统已经取得了长足的进步。
本文将就冶金转炉炼钢自动化控制的技术研究进行分析和探讨。
2.冶金转炉炼钢自动化控制的概述冶金转炉炼钢自动化控制系统主要包括转炉操作过程的监测与控制、炉前准备与调度控制、炉后工艺检测与指导、数据采集与分析等方面的内容。
其核心目标是实现炼钢过程的自动化、智能化和信息化,提高炼钢过程的生产效率和产品质量。
3.冶金转炉炼钢自动化控制的关键技术(1)炉内温度、压力、成分等参数的在线监测与控制利用先进的传感器和控制技术,实现炉内重要参数的实时监测与控制,提高了炉内温度、压力、成分等参数的稳定性和精度,从而提高了炼钢的生产效率和产品质量。
(2)炉料配料与计量控制通过先进的计量仪表和控制系统,可以实现炉料的准确配料和计量控制,使炉料的成分和质量得到保障,从而提高了炼钢过程的稳定性和产品质量。
(4)炉后工艺检测与指导通过先进的检测仪器和工艺指导系统,对炼钢过程中的重要参数进行实时检测和指导,提高了炼钢过程的生产效率和产品质量。
实现了对炼钢过程的数据采集和分析,为工艺优化和控制改进提供了重要依据。
4.冶金转炉炼钢自动化控制的发展趋势随着自动化技术的不断发展,冶金转炉炼钢自动化控制系统将迎来新的发展机遇和挑战。
未来,冶金转炉炼钢自动化控制系统将进一步实现智能化、网络化和智慧化,以适应生产过程的变化和需求。
(1)智能化利用人工智能和大数据技术,实现对炉内各项参数的智能监测与控制,提高了炉内参数的稳定性和精度。
(2)网络化通过建设信息化平台,实现炼钢过程实时监测与远程控制,使生产过程的信息化和网络化。
这将为炼钢企业的生产管理提供更多的便利。
(3)智慧化利用云计算和大数据技术,实现对炼钢过程的智能化管理和优化控制,提高了生产效率和产品质量。
转炉炼钢工艺过程与计算机控制
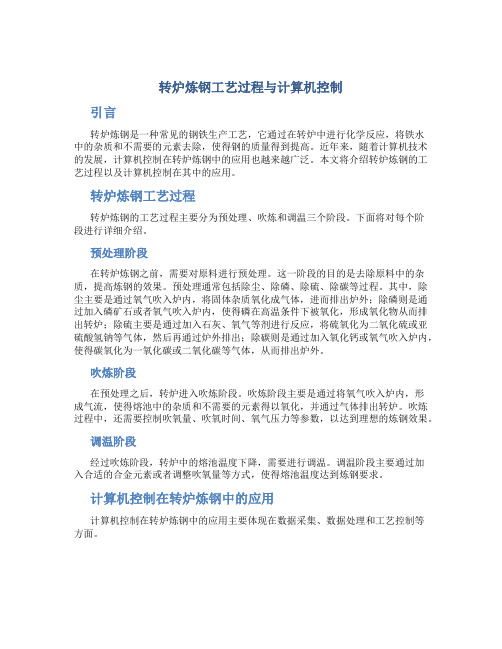
转炉炼钢工艺过程与计算机控制引言转炉炼钢是一种常见的钢铁生产工艺,它通过在转炉中进行化学反应,将铁水中的杂质和不需要的元素去除,使得钢的质量得到提高。
近年来,随着计算机技术的发展,计算机控制在转炉炼钢中的应用也越来越广泛。
本文将介绍转炉炼钢的工艺过程以及计算机控制在其中的应用。
转炉炼钢工艺过程转炉炼钢的工艺过程主要分为预处理、吹炼和调温三个阶段。
下面将对每个阶段进行详细介绍。
预处理阶段在转炉炼钢之前,需要对原料进行预处理。
这一阶段的目的是去除原料中的杂质,提高炼钢的效果。
预处理通常包括除尘、除磷、除硫、除碳等过程。
其中,除尘主要是通过氧气吹入炉内,将固体杂质氧化成气体,进而排出炉外;除磷则是通过加入磷矿石或者氧气吹入炉内,使得磷在高温条件下被氧化,形成氧化物从而排出转炉;除硫主要是通过加入石灰、氧气等剂进行反应,将硫氧化为二氧化硫或亚硫酸氢钠等气体,然后再通过炉外排出;除碳则是通过加入氧化钙或氧气吹入炉内,使得碳氧化为一氧化碳或二氧化碳等气体,从而排出炉外。
吹炼阶段在预处理之后,转炉进入吹炼阶段。
吹炼阶段主要是通过将氧气吹入炉内,形成气流,使得熔池中的杂质和不需要的元素得以氧化,并通过气体排出转炉。
吹炼过程中,还需要控制吹氧量、吹氧时间、氧气压力等参数,以达到理想的炼钢效果。
调温阶段经过吹炼阶段,转炉中的熔池温度下降,需要进行调温。
调温阶段主要通过加入合适的合金元素或者调整吹氧量等方式,使得熔池温度达到炼钢要求。
计算机控制在转炉炼钢中的应用计算机控制在转炉炼钢中的应用主要体现在数据采集、数据处理和工艺控制等方面。
数据采集转炉炼钢过程中,需要对各种参数进行实时监测和采集,以便进行后续的数据处理和分析。
计算机控制系统可以通过传感器和数据采集设备,实时采集转炉内的温度、压力、气体成分等关键参数。
数据处理采集到的数据需要进行处理和分析,以便对转炉的运行状态进行监控和评估。
计算机控制系统可以通过算法和模型对采集到的数据进行处理,得出转炉内各种物理和化学参数的变化趋势,以及各种异常情况的预警。
炼钢厂转炉系统自动化控制
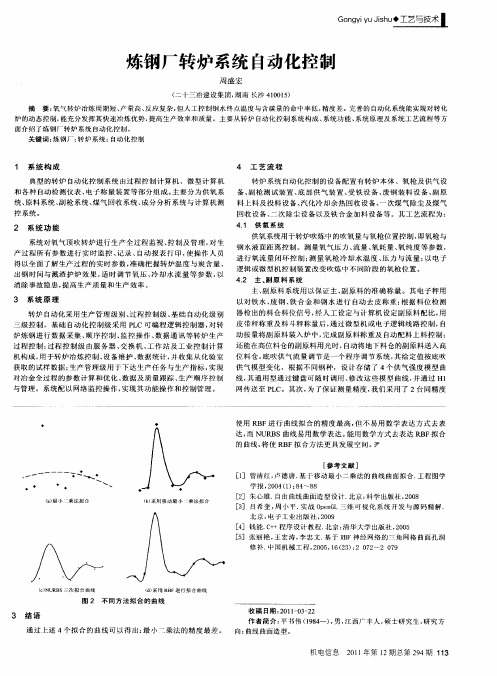
炼钢 厂转炉 系统 自动化控制
周 盛 宏
( 十 三 冶 建 设 集 团 , 南 长沙 4 0 1) 二 湖 10 5 摘 要 : 气 转 炉 冶 炼 周 期 短 、 量 高 、 应 复 杂 , 人 工 控 制 钢 水 终 点 温 度 与 含碳 量 的 命 中 率 低 , 度 差 。完 善 的 自动 化 系 统 能 实 现 对 转 化 氧 产 反 但 精
1 系统构 成
典型 的转 炉 自动化 控制 系 统 由过程 控 制 计算 机 、微 型计 算 机
4 工 艺 流 程
转 炉系 统 自动 化控 制 的设 备配 置有 转 炉本 体 、氧 枪及 供 气 设
和 各 种 自动检 测仪 表 、 电子 称 量装 置等 部 分组 成 。 要分 为供 氧 系 备 、 枪测 试 装 置 、 部供 气 装 置 、 铁 设 备 、 主 副 底 受 废钢 装 料 设 备 、 原 副 统 、 料 系统 、 原 副枪 系统 、 气 回收 系统 、 分分 析 系统 与计 算 机测 料 上料 及投 料 设备 、 化冷 却余 热 回收 设 备 、 收设 备 、 二次 除 尘设 备 以及铁 合 金加 料 设备等 。其 工 艺流 程为 :
2 系 统 功 能
系 统对 氧气 项吹 转 炉进 行生 产全 过 程监 视 、 制及 管 理 , 生 控 对 产 过程 所 有参 数 进行 实 时 监控 、 录 、 记 自动报 表 打 印 , 操 作 人员 使
得 以全 面 了解生 产过 程 的实 时参 数 , 准确 把 握转 炉温 度 与炭 含 量 、
[3 朱 心 雄 . 由 曲线 曲面 造 型 设 计 . 京 : 学 出版 社 ,0 8 2 自 北 科 2 0 1] 吕 希 奎 , 小 平 . 战 0 e G - 3 周 实 p n L三 维 可 视 化 系 统 开 发 与 源 码 精 解 .
炼钢厂转炉PLC系统自动控制

炼钢厂转炉PLC系统自动控制摘要:随着PLC技术的发展,PLC系统在工业企业中的应用越来越广泛。
钢铁企业已普遍采用PLC 来实现电气和自动化控制。
基于此,本文首先阐述炼钢厂转炉的工艺和系统功能,然后分析了转炉PLC自动控制系统的构架,并探讨了转炉PLC系统设计。
关键词:炼钢厂;转炉;PLC系统;自动控制引言:利用计算机控制系统对炼钢厂作业进行自动化调控,不仅降低了生产人员的作业难度,也大大优化了生产工艺流程,降低了企业运行的生产成本,有助于炼钢工艺的优化调整。
1、炼钢厂转炉的工艺和系统功能1.1转炉炼钢的工艺目前,在不同的程度上对容积比较大的转炉炼钢所采用的均为自动控制。
本文将对自动化控制系统作简单介绍,包括转炉本体、散装料、一次除尘(OG 法)、吹氩站、循环的水泵房、炉后铁合金、二次除尘、混铁炉的除尘、三万气柜、VD炉水的处理等。
冶炼散装料主要是通过四条胶带机由低位料仓将转炉炼钢需要加入的配料送到转炉炉顶料仓;转炉本体作为整个系统核心的部分,进行转炉吹氧炼钢,到1700℃时从炉后钢包流出钢水,然后向转炉吹氮,经过溅渣护炉,向炉前出渣;把钢水倒入钢包之后,加入合金调节钢水成分;转炉烟气通过两个除尘的系统排出:一次除尘系统是通过高压的风机从转炉烟罩抽风,二次除尘系统是通过高压的风机,抽出天车从转炉倒入钢水的烟气。
1.2转炉系统功能系统对于生产全过程的情况进行监视,控制和管理的过程,这一点相较于过去的传统生产而言,更加精确的将生产过程中的数据进行了定位,检测,能够让操作人员对于生产过程中的实时参数更加的了解,这样转炉的运用就能够更加的高效和安全。
典型的转炉自动化控制系统的主要组成部分分为过程控制计算机,微型计算机和各种自动检测仪和电子称量装置等各个部分,这些部分共同组成了转炉的自动化系统,而且辅助系统还分为了供氧系统,原料系统和煤气回收系统等,这些都由计算机测控系统来检测。
计算机测控在本次研究中,采用的是PLC系列的产品,选择CPU是系列中较为高性能的53414CPU型号,现场总线采用的是CRP系列产品,编程软件使用施奈德的产品Concept2.6。
转炉炼钢工艺流程
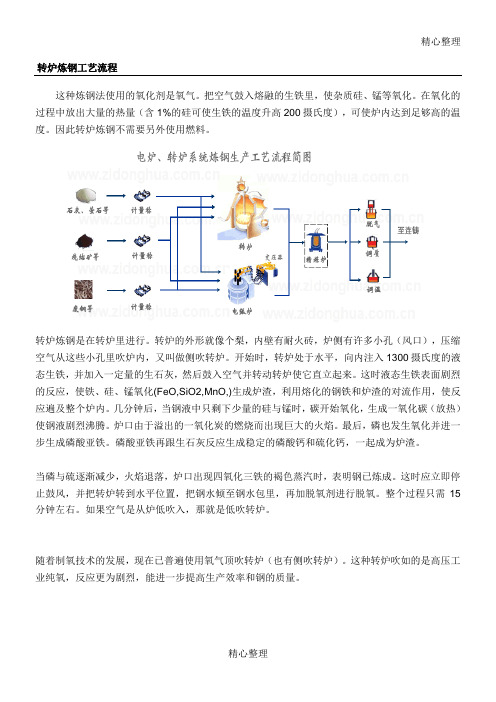
精心整理转炉炼钢工艺流程这种炼钢法使用的氧化剂是氧气。
把空气鼓入熔融的生铁里,使杂质硅、锰等氧化。
在氧化的过程中放出大量的热量(含1%的硅可使生铁的温度升高200摄氏度),可使炉内达到足够高的温度。
因此转炉炼钢不需要另外使用燃料。
摄氏度(放热)15分钟左右。
如果空气是从炉低吹入,那就是低吹转炉。
随着制氧技术的发展,现在已普遍使用氧气顶吹转炉(也有侧吹转炉)。
这种转炉吹如的是高压工业纯氧,反应更为剧烈,能进一步提高生产效率和钢的质量。
转炉一炉钢的基本冶炼过程。
顶吹转炉冶炼一炉钢的操作过程主要由以下六步组成:(1)上炉出钢、倒渣,检查炉衬和倾动设备等并进行必要的修补和修理;(2(3(4(5(6小型转炉为2.5-4.5m3/(t·min);120t以上的转炉一般为2.8-3.6m3/(t·min)。
◆开吹时氧枪枪位采用高枪位,目前是为了早化渣,多去磷,保护炉衬;◆在吹炼过程中适当降低枪位的保证炉渣不“返干”,不喷溅,快速脱碳与脱硫,熔池均匀升温为原则;◆在吹炼末期要降枪,主要目的是熔池钢水成分和温度均匀,加强熔池搅拌,稳定火焰,便于判断终点,同时使降低渣中Fe含量,减少铁损,达到溅渣的要求。
◆当吹炼到所炼钢种要求的终点碳范围时,即停吹,倒炉取样,测定钢水温度,取样快速分析[C]、[S]、[P]的含量,当温度和成分符合要求时,就出钢。
◆当钢水流出总量的四分之一时,向钢包中的脱氧合金化剂,进行脱氧,合金化,由此一炉钢冶炼完毕。
炼钢学概述航天航空、交通运输、农业、国防等许多重要的领域均需要各种类型的大量钢材,我们的日常生活更离不开钢。
总之,钢材仍将是21世纪用途最广的结构材料和最主要功能材料。
炼钢方法(1)最早出现的炼钢方法是1740年出现的坩埚法,它是将生铁和废铁装入由石墨和粘土制成的坩埚内,用火焰加热熔化炉料,之后将熔化的炉料浇成钢锭。
此法几乎无杂质元素的氧化反应。
1856年英国人亨利·贝塞麦发明了酸性空气底吹转炉炼钢法,也称为贝塞麦法,第一次解决了用铁水直接冶炼钢水的难题,从而使炼钢的质量得到提高,但此法要求铁水的硅含量大于0.8%,而且不能脱硫。
转炉炼钢自动化控制技术探讨

转炉炼钢自动化控制技术探讨转炉炼钢是目前钢铁行业主要的炼钢方法之一,其炉内化学反应过程复杂,对于操作人员的要求高,因此转炉炼钢自动化控制技术的研究和应用具有重要意义。
转炉炼钢自动化控制技术的研究旨在通过引入先进的仪器设备和智能化的控制系统,实现炼钢全过程的自动化管理和控制,提高生产效率,降低操作风险,提高产品质量。
自动化控制技术的应用可以实现对转炉温度、氧气、燃料等关键参数的精确控制和调节,提高炉内反应的稳定性和一致性,降低转炉炼钢的能耗和原材料消耗。
目前,转炉炼钢自动化控制技术主要包括以下方面的内容:首先是数据采集与处理技术。
通过传感器等设备,精确地采集炉内的温度、压力、浓度等关键参数,并将采集到的数据送入控制系统进行处理。
数据采集与处理技术的应用可以实现对炉内状态的实时监测和分析,为后续的控制决策提供准确的依据。
其次是模型建立与优化控制技术。
基于转炉炼钢的动态特性和炼钢过程的非线性特点,建立数学模型,通过优化控制算法,实现对转炉炼钢过程的精确控制。
模型建立与优化控制技术可以有效地提高炉内温度、浓度等参数的控制精度,减小温度偏差和成分变化,提高产品的一致性和质量。
再次是人机交互界面设计技术。
转炉炼钢控制系统的人机交互界面是操作人员与设备之间的重要桥梁,直接影响到操作效率和安全性。
人机交互界面设计技术通过合理的界面布局和清晰的指示说明,提供直观的操作界面和友好的操作方式,简化操作流程,降低操作风险,减少人为失误。
最后是网络通信与远程监控技术。
网络通信与远程监控技术的应用可以实现对转炉炼钢过程的远程监控和远程控制,实现操作人员的远程实时监测和控制,提高工作效率,降低操作风险。
网络通信与远程监控技术的发展,使得炼钢过程的自动化控制技术不再受制于时间和空间的限制。
转炉炼钢的自动化控制技术研究
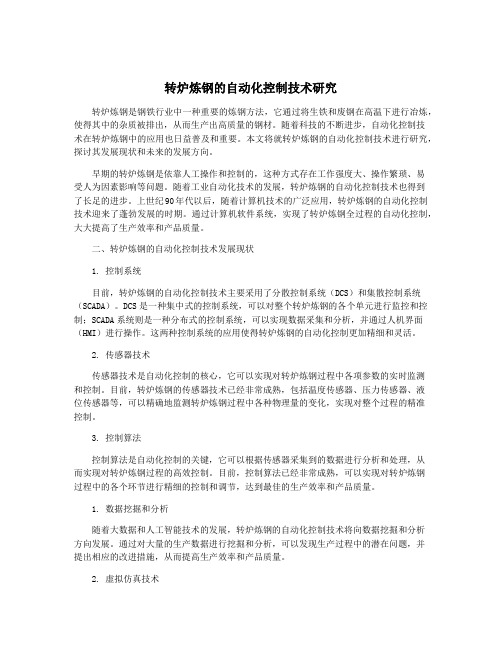
转炉炼钢的自动化控制技术研究转炉炼钢是钢铁行业中一种重要的炼钢方法,它通过将生铁和废钢在高温下进行冶炼,使得其中的杂质被排出,从而生产出高质量的钢材。
随着科技的不断进步,自动化控制技术在转炉炼钢中的应用也日益普及和重要。
本文将就转炉炼钢的自动化控制技术进行研究,探讨其发展现状和未来的发展方向。
早期的转炉炼钢是依靠人工操作和控制的,这种方式存在工作强度大、操作繁琐、易受人为因素影响等问题。
随着工业自动化技术的发展,转炉炼钢的自动化控制技术也得到了长足的进步。
上世纪90年代以后,随着计算机技术的广泛应用,转炉炼钢的自动化控制技术迎来了蓬勃发展的时期。
通过计算机软件系统,实现了转炉炼钢全过程的自动化控制,大大提高了生产效率和产品质量。
二、转炉炼钢的自动化控制技术发展现状1. 控制系统目前,转炉炼钢的自动化控制技术主要采用了分散控制系统(DCS)和集散控制系统(SCADA)。
DCS是一种集中式的控制系统,可以对整个转炉炼钢的各个单元进行监控和控制;SCADA系统则是一种分布式的控制系统,可以实现数据采集和分析,并通过人机界面(HMI)进行操作。
这两种控制系统的应用使得转炉炼钢的自动化控制更加精细和灵活。
2. 传感器技术传感器技术是自动化控制的核心,它可以实现对转炉炼钢过程中各项参数的实时监测和控制。
目前,转炉炼钢的传感器技术已经非常成熟,包括温度传感器、压力传感器、液位传感器等,可以精确地监测转炉炼钢过程中各种物理量的变化,实现对整个过程的精准控制。
3. 控制算法控制算法是自动化控制的关键,它可以根据传感器采集到的数据进行分析和处理,从而实现对转炉炼钢过程的高效控制。
目前,控制算法已经非常成熟,可以实现对转炉炼钢过程中的各个环节进行精细的控制和调节,达到最佳的生产效率和产品质量。
1. 数据挖掘和分析随着大数据和人工智能技术的发展,转炉炼钢的自动化控制技术将向数据挖掘和分析方向发展。
通过对大量的生产数据进行挖掘和分析,可以发现生产过程中的潜在问题,并提出相应的改进措施,从而提高生产效率和产品质量。
转炉炼钢的自动化控制技术研究

转炉炼钢的自动化控制技术研究1. 引言1.1 研究背景转炉炼钢是目前钢铁行业中一种广泛应用的生产工艺,其通过将废钢和生铁等原料放入转炉中,通过高温燃烧氧化还原反应,最终得到所需的合金钢。
传统的转炉炼钢过程存在着能耗高、生产效率低、操作风险大等问题,为了提高转炉炼钢的生产效率和质量,降低能耗和环境污染,自动化控制技术成为了当今转炉炼钢行业发展的关键。
自动化控制技术能够通过引入先进的控制系统和设备,实现转炉炼钢整个生产过程的智能化和网络化管理,提高生产效率和产品质量,降低劳动强度和生产成本,具有重要的现实意义和应用前景。
对转炉炼钢的自动化控制技术进行深入研究,不仅符合钢铁行业的发展需求,也与我国推进工业智能制造和绿色生产的战略目标相一致。
为此,本文探讨了转炉炼钢的自动化控制技术研究现状,分析了其研究意义和未来发展趋势,旨在为相关领域的研究者和实践者提供参考和借鉴。
1.2 研究意义转炉炼钢是钢铁生产中的重要环节,其自动化控制技术的研究意义主要体现在以下几个方面:转炉炼钢的自动化控制技术可以提高生产效率,减少人力成本和生产周期,实现工厂生产的智能化和自动化,从而提高钢铁生产的整体竞争力。
自动化控制技术可以提高生产的稳定性和可靠性,减少生产过程中的人为因素造成的误差,保证钢铁产品的质量稳定,降低质量风险。
自动化控制技术的研究还可以促进产业的技术升级和转型,提高钢铁行业的核心竞争力,推动整个行业向智能化、信息化方向发展。
转炉炼钢的自动化控制技术研究具有重要的现实意义和广阔的应用前景。
2. 正文2.1 转炉炼钢的基本原理转炉炼钢是利用转炉对生铁或废钢进行高温炼炉处理,以去除杂质、调整成分和改善钢的质量的工艺。
其基本原理是通过将生铁或废钢装入转炉后,同时加入适量石灰、焦炭等原料,在高温下氧化还原反应,使得杂质被氧化或还原,将其除去,从而得到合格的钢水。
转炉炼钢的基本原理包括物料的加料和熔化、氧化还原反应、渣钢分离和钢水出钢等阶段。
炼钢工艺控制点

炼钢主要工艺控制点一、转炉炉后工艺控制点1、脱氧合金化要求:(1)合金加入顺序必须遵循先弱后强的原则。
即硅锰——硅铁——脱氧剂;为了保证合金的有效收得率,在过氧化钢水的处理上可以先加部分硅铁或脱氧剂进行预脱氧,但为了避免钢水翻包,预脱氧剂不能加到包底。
(2)合金加入时间必须遵循在出钢到四分之一开始加入,在钢水出到四分之三时必须加完。
出钢时间必须大于三分钟。
(3)为避免钢水成分不均匀,严禁在出完钢后补加合金。
(4)有条件的钢车可以在加入合金后来回晃动,增加合金的融化速度和均匀性。
(5)合金加入点必须对准钢流加入。
2、出钢挡渣要求:(1)任何钢种必须进行双挡渣操作。
即出钢之前必须检查挡渣塞是否堵好。
(2)出钢到五分之四时必须加入挡渣锥或挡渣球。
(3)出完钢后检查出钢口情况,必须把残渣或堵塞物清理干净,然后堵上挡渣塞。
3、精炼要求:(1)出完钢后必须进行吹氩气(或氮气)操作,有条件的必须在出钢过程中进行。
(2)吹气时间必须大于五分钟,吹气效果以钢水表面微翻波动为准则,为避免钢水二次氧化不允许钢水大翻。
吹气压力0.4-.0.6Mp.(3)吹气前和吹完气后必须进行钢水测温,其温度制度根据不同的钢种和上连铸包次要求执行工艺制度。
(4)同时在吹完气后必须进行取样观察和检验,如果钢水成分和含氧量不合乎要求,必须经行喂丝操作,具体数量根据成分和含氧量而定。
(5)完毕后必须加入钢包覆盖剂,具体数量已覆盖钢包表面为原则。
二、钢包工艺控制点1、必须热包出钢,钢包烘烤温度大于800℃要求。
2、钢包出钢前必须清理干净,不允许有残渣或残钢,特别是水口和透气砖部分。
3、出钢前必须对底吹透气砖进行确认检查是否透气。
4、出钢前必须对引流砂确认检查,要求覆盖碗口且成堆积状。
三、连铸浇注平台工艺控制点1、中间包浇注前工艺检查要求(1)中间包浇注前必须烘烤,烘烤温度必须大于800℃。
(2)中间包浇注前必须检查是否清理干净,特别是水口部位。
转炉炼钢的自动化控制技术研究

转炉炼钢的自动化控制技术研究【摘要】本文对转炉炼钢的自动化控制技术进行了深入研究。
在介绍了转炉炼钢的背景和研究意义,明确了研究目的。
在正文部分首先概述了转炉炼钢技术及其在工业生产中的应用,然后分析了传统转炉炼钢存在的问题,接着介绍了自动化控制技术在该领域的研究现状,并提出了改进转炉炼钢自动化控制技术的方向。
在总结了转炉炼钢的自动化控制技术研究成果,并展望了未来的发展方向,同时指出了研究的局限性和不足之处。
通过本文的分析,可以为转炉炼钢行业提供关于自动化控制技术的参考,促进该领域的技术进步和发展。
【关键词】转炉炼钢、自动化控制技术、研究、技术概述、应用、问题、研究现状、改进方向、成果总结、发展展望、局限性、不足之处1. 引言1.1 背景介绍转炉炼钢是一种重要的冶金工艺,广泛应用于钢铁生产领域。
随着现代工业的发展,对钢铁生产效率和质量要求越来越高,自动化控制技术在转炉炼钢过程中的应用变得日益重要。
传统的转炉炼钢存在着很多问题和挑战,如操作复杂、生产效率低、产品质量难以保证等。
研究和优化转炉炼钢的自动化控制技术具有重要的现实意义和理论意义。
自动化控制技术能够提高转炉炼钢的生产效率和产品质量,减少人为因素的干扰,降低生产成本,实现智能化生产。
目前,国内外在转炉炼钢的自动化控制技术研究方面取得了一些进展,但仍然存在着许多问题和挑战,如传感器精度不高、控制算法不够灵活、系统稳定性不足等。
本文旨在对转炉炼钢的自动化控制技术进行深入研究和探讨,分析现有技术存在的问题,提出改进方向和措施,为提高转炉炼钢生产效率和产品质量提供理论支持和技术指导。
1.2 研究意义转炉炼钢是目前钢铁生产中最主要的炼钢方法之一,对于提高钢铁质量、降低生产成本、增加生产效率具有重要意义。
随着钢铁行业的发展和技术进步,自动化控制技术在转炉炼钢中的应用变得越来越重要。
对转炉炼钢的自动化控制技术进行研究具有重要的意义。
自动化控制技术的应用可以提高生产效率和节约人力资源。
转炉炼钢原理及工艺

转炉炼钢原理及工艺
转炉炼钢是通过加热合金材料,然后将其在氧气中抽出到转炉,形成一个旋转坩埚里,再使材料在转炉内不断熔化、混合、渣滓沉淀,达到钢的熔化和净化,最后冷却固化,即可获得均匀的高质量的钢的过程。
转炉炼钢的工艺路径主要包括:原料进炉、熔炼、净化、合金添加、出炉等步骤。
1、原料进炉:将碳钢和合金料装入转炉,加热至溶化温度,开始熔融。
2、熔炼:转炉内熔融的温度受多种因素的影响,如加料量、加料温度、炉气系统的平衡性、熔炼时间等。
3、净化:即清洁熔化渣滓,消除杂质,把金属液中的杂质置于渣滓中,让金属液纯度升高。
4、合金添加:将净化后的钢液入合金添加系统,加入合金钢料,使钢液按照要求的成分,营造钢种具有相应的技术性能。
5、出炉:金属液改变形态,冷却成指定的形状和尺寸,经过纯化后形成高质量钢。
转炉炼钢原理及工艺介绍
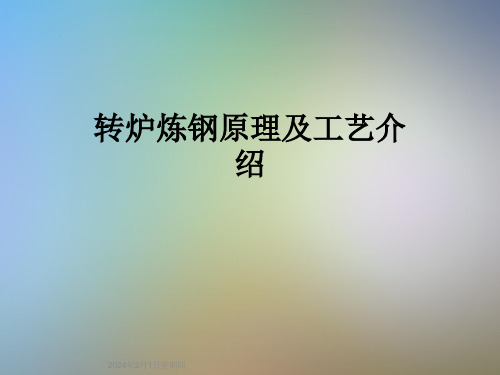
锰的氧化反应有三种情况:
(1)锰与气相中的氧直接作用
[Mn]+ 1/2{O2}=(MnO)
(2)锰与溶于金属中的氧作用
[Mn]+ [O2] =(MnO)
(3)锰的氧化与还原
3)锰与炉渣中氧化亚铁作用
[Mn]+(FeO)=(MnO)+ [Fe]
第三个反应在炉渣——金属界面上迸行,是锰氧化的主要反应。
锰的氧化还原与硅的氧化还原相比有以下基本特点:
1)在冶炼初期锰和硅一样被迅速大量氧化,但锰的氧化程度要低些
,这是由于硅与氧的结合能力大于锰与氧的结合能力;
2)MnO为弱碱性氧化物,在碱性渣中( MnO)大部分呈自由状态存
在。因此,在一定条件下可以被还原。由于锰的氧化反应是放热反应,故
温度升高有利于锰的还原。所以在生产实践中冶炼后期熔池中会出现回锰
1)在某一温度下,几种元素同时和氧相遇时,位置低的元素先氧化。如1500℃ 时,氧化顺序为Al、Si、C、V、Mn。
2)位置低的元素可将位置高的氧化物还原。炼钢过程中脱氧就是利用Al、Si等 元素将FeO还原。
3)CO的分解压曲线的斜率与其它氧化物的不同,它与Si、Mn、V等的氧化物分 解与压CO曲分线解有压一曲交线点相,交此点点对所应对的应温的度温为度15称30为℃氧,化当转t>化15温30度℃。时例,如Si,先S于iOC2被分氧解化压;曲当线 t<1530℃时,则C先于Si被氧化。1530℃即为Si、C的氧化转化温度。
• 所谓炼钢,就是通过冶炼降低生铁中的 碳和去除有害杂质,在根据对钢性能的要求 加入适量的合金元素,使其成为具有高的强 度、韧性或其他特殊性能的钢。
•二、炼钢基本原理
• 因此,炼钢的基本任务可归纳为:
转炉炼钢的自动化控制技术研究
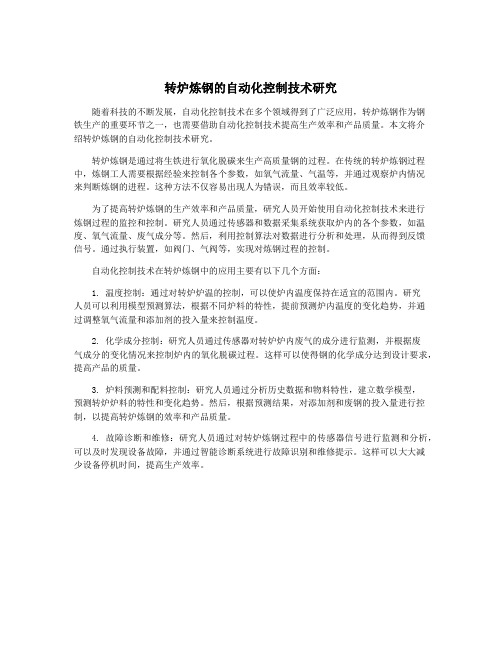
转炉炼钢的自动化控制技术研究随着科技的不断发展,自动化控制技术在多个领域得到了广泛应用,转炉炼钢作为钢铁生产的重要环节之一,也需要借助自动化控制技术提高生产效率和产品质量。
本文将介绍转炉炼钢的自动化控制技术研究。
转炉炼钢是通过将生铁进行氧化脱碳来生产高质量钢的过程。
在传统的转炉炼钢过程中,炼钢工人需要根据经验来控制各个参数,如氧气流量、气温等,并通过观察炉内情况来判断炼钢的进程。
这种方法不仅容易出现人为错误,而且效率较低。
为了提高转炉炼钢的生产效率和产品质量,研究人员开始使用自动化控制技术来进行炼钢过程的监控和控制。
研究人员通过传感器和数据采集系统获取炉内的各个参数,如温度、氧气流量、废气成分等。
然后,利用控制算法对数据进行分析和处理,从而得到反馈信号。
通过执行装置,如阀门、气阀等,实现对炼钢过程的控制。
自动化控制技术在转炉炼钢中的应用主要有以下几个方面:1. 温度控制:通过对转炉炉温的控制,可以使炉内温度保持在适宜的范围内。
研究人员可以利用模型预测算法,根据不同炉料的特性,提前预测炉内温度的变化趋势,并通过调整氧气流量和添加剂的投入量来控制温度。
2. 化学成分控制:研究人员通过传感器对转炉炉内废气的成分进行监测,并根据废气成分的变化情况来控制炉内的氧化脱碳过程。
这样可以使得钢的化学成分达到设计要求,提高产品的质量。
3. 炉料预测和配料控制:研究人员通过分析历史数据和物料特性,建立数学模型,预测转炉炉料的特性和变化趋势。
然后,根据预测结果,对添加剂和废钢的投入量进行控制,以提高转炉炼钢的效率和产品质量。
4. 故障诊断和维修:研究人员通过对转炉炼钢过程中的传感器信号进行监测和分析,可以及时发现设备故障,并通过智能诊断系统进行故障识别和维修提示。
这样可以大大减少设备停机时间,提高生产效率。
转炉炼钢自动控制系统

转炉炼钢自动控制系统一、转炉炼钢自动化概述转炉炼钢自动化的直接处理对象是铁水,它来自于炼钢企业,在经过一系列流程之后,完成对其加工,钢便在如此的情况下形成了。
这个过程中,首先要进行的环节是氧化,其目的是将铁水中存在的杂质进行去除;接下来需要添加石灰料,通过这种添加可以实现氧化性炉渣的产生,对于这个环节而言,温度是一个较为重要的参数,因此,必须按照规定将温度控制在一定的范围内,最终的环节仍然需要添加辅助性物料,以确保钢材的最终生成,需要添加的物料包括脱氧剂和合金。
从具体的方向进行描述,转炉炼钢的自动化主要包含以下几个方面:炼钢的原料,也就是由钢铁企业运送过来的铁水,当然还需要添加氧化剂;熔炉比必须控制在合理的范围内,确保炉子的深度和铁水的深度比例能够保证炼钢工作顺利进行;供养规范,它要求供养压力、强度和氧枪的喷嘴都要具备的一定标准;炉渣标准,这要求炉渣在碱度方面必须达到规定的标准,在这过程中,对于石灰料的添加环节而言,可以在计算机的辅助之下完成,添加方式最好采取分批添加的形式;温度方面,在这方面必须采取良好的控制手段,在确定钢出炉的温度之后,还要对冷却剂的添加进行了解,确保添加的剂量符合现实要求;最终控制盒钢材的合金化,这个环节对计算机的使用程度较高,其最终控制技术会使得炉和炭的温度都在同步的情况下被控制在精准的范围内,当然在上述环节完成之后,还要注意脱氧工作,在钢材出炉的过程中,要确认炉渣被挡住,如果疏忽就会严重影响钢材质量。
二、自动控制过程转炉炼钢自动化控制基本流程就是通过完善的控制软件,应用计算机通信、优化的静态模型和动态模型、顶底复吹、快速复枪测试和溅渣补炉技术,实现转炉炼钢从吹炼条件、吹炼过程控制,直至终点前动态预测和调整,吹制设定的终点目标自动提枪的全程计算机控制,实现转炉炼钢终点成分和温度达到双命中,做到快速出钢,提高钢水质量,提高劳动生产率,降低成本。
三、转炉氧枪系统控制转炉氧枪系统主要由氧枪供氧、氧枪冷却水、氧枪氮封阀、氧枪升降位置控制和主备枪换枪的横移控制等系统组成。
转炉炼钢自动控制基础及工艺

转炉仪表控制系统介绍
自动控制知识
自动化控制系统是指在表征生产过程中的温度、压力、流量、物位等状态参数作为被控对象的系统。包括:常规过程控制系统和计算机过程控制系统
仪表基本常识之误差
一、测量误差 1、按误差数值表示方法可分为:绝对误差、相对误差、 引用误差; 绝对误差=测量值-真值。 相对误差=绝对误差/仪表示值*100% 引用误差=绝对误差/量程*100% 仪表精度等级是根据引用误差来划分的 2、按误差出现规律可分为:系统误差、随机误差、误差; 系统误差又称规律误差,其大小和符号均不改变或按 一定规律变化。 随机误差又称偶然误差。 疏忽误差又叫粗差。
新转炉控制系统
8、连铸系统; 9、铸坯热送; 以下分述:
本体流程图
转炉本体之电气控制
转炉倾动系统的连锁控制。 转炉倾动润滑系统的控制。 转炉倾动位置控制。 底吹系统控制。 氧枪升降位置系统的连锁控制。 氧枪横移小车行走和锁定装置的控制。 氧枪钢丝绳张力保护控制。
转炉本体之电气控制
炉后合金加料设施的控制。 挡火门和挡渣塞的控制。 渣车系统控制。 振动给料机的控制。 电磁阀的控制。 溶剂称量斗及集中斗称量控制。 其他辅助设备控制。
GE90-30
32640 输入 / 32640 输出 模拟量 2048 输入 / 2048 输出 开关量 240K 程序代码空间 .22ms / K 程序代码 3-5 ms 每个闭环刷新间隔
Hot Standby
ETHERNET (TCP/IP)
iFix HMI
数学模型 Alpha/VMS C++编程工具包
转炉本体之检测点
●氮气总管压力、流量测量 ● 溅渣护炉氮气流量、压力测量 ● 氮气总管压力调节 转炉稀油站系统 ● 稀油箱稀油液位测量 ● 稀油箱稀油压力测量 ● 稀油箱稀油温度测量
转炉炼钢的自动化控制技术探讨

转炉炼钢的自动化控制技术探讨在国际钢材市场的冲击下,需要不断提高我国钢材的产品质量,所以我国钢铁企业要尽快创新转炉炼钢技术,加快生产速率,不但要保障钢的质量,还要尽量减少能耗,这样才能与国际钢铁行业接轨。
文章就我国转炉炼钢自动化控制技术的运用与转炉炼钢智能化系统的功能展开剖析。
标签:钢材市场;转炉炼钢;自动化控制技术0 引言因为转炉炼钢的生产环境差,过程相当繁琐,并且工作期间无法精准地实施不间断的测量,所以使用一般的进程控制办法控制起来相当难,而单凭人工经验来控制炼钢终点又无法保障高品质钢材、操作稳定和低能耗,这与现今钢铁市场低成本高品质的标准相差太远,而如果想增强产品的市场争夺力,就一定要提升炼钢科技化水平,一定要精确地智能控制炼钢生产,只有如此才能提升炼钢的生产速率与成品质量。
转炉炼钢中的主材料有铁水、废钢、铁合金等,当加热的铁水与废钢和铁合金混合在一起时就会发生热化学反应,从而在转炉里进行炼钢。
在转炉炼钢技术中融入了计算机信息技术、网络技术、工业控制技术等,通过这些技术对变量控制更精准,其被认为是炼钢中最核心的环节。
随着工作生产中涌现出大量的智能控制技术,随之带动了各大钢铁企业的转炉炼钢自动化技术,同时需要的人力与物力大幅减少,但钢质量却大幅提升。
1 转炉炼钢自动化控制的优势最多见的自动化转炉炼钢系统关键是二级计算机控制体系,就是一级基础性智能控制模块和二级过程的智能控制模块,其中一级基础性智能控制模块关键涵盖了氧枪智能控制体系、底吹控制体系、转炉智能化仪表系统、副枪智能控制体系、除尘智能控制体系等,二级过程性智能控制模块关键包含数据收集系统、补吹校正运算系统、报表打印系统等这种转炉炼钢智能化控制体系可将过程中的参数集中显示与管理,并创建强可视性的界面,显示的内容有模拟的工艺程序、趋势曲线等,在减轻繁重工作的同时,还让人直观地认识工艺与设备的运营状态。
通過实际运用汇总得出,运用转炉炼钢智能化控制技术拥有绝对的技术优势,其体现出的优点关键表现为:一是超过一半的转炉不需要后吹,直接将终点温度和碳的命中率提升至90%;二是不再需要较长的冶炼周期,炼钢速度也加快了;三是降低了30%喷溅率和3kg/t的石灰消耗率,同时使得铁率上升了0.5%左右;四是对炼钢工经验的依赖性大幅缩减,有助于标准化、规范化管理水平的提升,显著减少能耗,增加经济利润。
转炉炼钢自动化控制技术探讨

转炉炼钢自动化控制技术探讨转炉炼钢自动化控制技术是钢铁行业应用最广泛的自动化技术之一,主要包括机械化控制、电气自动化控制、计算机控制和人机接口控制等方面。
其中,机械化控制主要是用来控制转炉各种阀门的机械传动;电气自动化控制主要包括对转炉各种电器设备的自动控制和监测;计算机控制主要是对转炉生产过程进行数字化处理和自动控制;人机接口控制主要是将计算机控制与生产现场紧密结合,实现实时控制和监测。
目前,转炉炼钢自动化控制技术已经发展到了非常成熟的阶段,能够实现智能化、数字化、网络化、可视化和安全化等方面的要求,在提高操作效率、保证质量安全、降低人工成本等方面具有非常重要的作用。
转炉炼钢自动化控制技术的主要优势体现在以下几个方面:1. 提高生产效率:通过自动化控制,能够实现多项工艺参数的自动调节,从而提高生产效率和品质。
2. 保证质量安全:自动化控制可以实现全程监测和报警,从而确保生产过程中的安全性和质量。
3. 降低人工成本:自动化控制可以减少人工操作,降低了人工成本,提高了生产效率。
4. 提高生产环境:自动化控制可以降低炉厂的噪音污染、粉尘和废气排放,提高生产环境的整洁度和卫生质量。
5. 改善信息管理:自动化控制可以将生产信息数字化处理,提高信息管理和传递效率。
1. 云计算技术:利用云计算技术,可以将大量的数据资源存储在云端,实现互联网信息共享、平台无缝对接。
2. 物联网技术:通过物联网技术,可以实现设备的自主互联和数据的实时监测,提高设备的自动化程度。
3. 人工智能技术:利用人工智能技术,可以实现更加智能化的控制和生产过程的优化管理,进一步提高生产效率和品质。
4. 增强现实技术:通过增强现实技术,可以将虚拟世界和现实世界进行有机结合,提高生产过程的可视化效果和安全性。
5. 自适应控制技术:通过自适应控制技术,可以根据生产过程的实际情况,不断调整控制参数,提高生产效率和品质。
总之,转炉炼钢自动化控制技术是钢铁行业中重要的发展方向之一,在不断完善和发展的过程中,可以实现更加高效、安全、可控的生产过程。
- 1、下载文档前请自行甄别文档内容的完整性,平台不提供额外的编辑、内容补充、找答案等附加服务。
- 2、"仅部分预览"的文档,不可在线预览部分如存在完整性等问题,可反馈申请退款(可完整预览的文档不适用该条件!)。
- 3、如文档侵犯您的权益,请联系客服反馈,我们会尽快为您处理(人工客服工作时间:9:00-18:30)。
自动控制知识
自动化控制系统是指在表征生产过程中 的温度、压力、流量、物位等状态参数 作为被控对象的系统。包括:常规过程 控制系统和计算机过程控制系统
仪表基本常识之误差
一、测量误差 1、按误差数值表示方法可分为:绝对误差、相对误差、 引用误差; 绝对误差=测量值-真值。 相对误差=绝对误差/仪表示值*100% 引用误差=绝对误差/量程*100% 仪表精度等级是根据引用误差来划分的 2、按误差出现规律可分为:系统误差、随机误差、误差; 系统误差又称规律误差,其大小和符号均不改变或按 一定规律变化。 随机误差又称偶然误差。 疏忽误差又叫粗差。
压力测量
在压力测量中常有大气压力、绝对压力、表 压力、负压力之分。 P表压力=P绝对压力-P大气压力 P表压力<0时,则称为负压 压力测量仪表分类有以下几种: 1、液柱式:U形管 2、弹性式:薄膜式压力表、弹簧管压力表 3、电气式:电容式Rosement1151S、3051扩 散硅式EJA120\430、硅电阻Honeywell 3000
气柜系统
5×104m3干式煤气柜 ● 进柜煤气压力、流量检测 ● 进柜煤气温度检测 ● 柜内煤气压力检测 ● 柜内煤气温度检测 ● 气柜煤气储量检测 ● 活塞上部CO含量检测 ● 活塞倾斜度检测
活塞高度、运行速度检测 ● 氮气压力检测
转炉煤气加压站
● 加压风机进口总管煤气压力检测 ● 加压风机进口煤气压力检测 ● 加压风机进出口煤气压力就地检测 ● 加压风机进出口煤气温度就地检测 ● 加压机房CO含量检测 ● 加压机出口总管煤气压力、温度、流 量检测 ● 防回火水封水位检测、控制 ● 泄爆水封水位检测、控制
转炉本体之检测点
●底吹氩气,氮气分支总管压力调节 ●底吹氩气,氮气分支总管压力、温度、流 量测量 ●底吹氩气,氮气切换控制
流程图
吹氩站系统控制
振动给料机 称量小车 电振动给料机 吹氩枪升降电机
吹氩站系统检测
● ● ● ● ● 氩气压力测量、控制 氩气流量测量 钢包钢水温度测量 铁合金称量 废钢称量
称重设备
电子衡器的组成: 承重和传力机构 称重传感器 测量和显示 新转炉主要测量点有:氧枪称重、散 装料称重、废钢秤、铁合金小车、铁 水包、钢水行车、钢包。
工业自动化化
现代钢铁工业自动化化系统一般可分为: 基础自动化、过程自动化和管理自动化。 一级基础自动化级为设备级控制,包括 检测仪表及控制、电力等传动系统控制 和监控。 二级过程自动化是在数据采集的基础上 又增加一些控制和管理功能。 三级管理自动化又分为总厂经营管理和 分厂管理。
本体流程图
转炉本体之电气控制
转炉倾动系统的连锁控制。 转炉倾动润滑系统的控制。 转炉倾动位置控制。 底吹系统控制。 氧枪升降位置系统的连锁控制。 氧枪横移小车行走和锁定装置的控制。 氧枪钢丝绳张力保护控制。
转炉本体之电气控制
炉后合金加料设施的控制。 挡火门和挡渣塞的控制。 渣车系统控制。 振动给料机的控制。 电磁阀的控制。 溶剂称量斗及集中斗称量控制。 其他辅助设备控制。
流程图
上料系统
散装料系统PLC主要功能: 振动给料机的控制。 上料皮带机的控制。 卸料小车行走的控制。 其他辅助设施的控制。 其他辅助设备的控制。 ●高位料仓料位测量
流程图
气柜系统
主要包括煤气柜、煤气加压站系统 煤气柜油泵及气阀控制。 煤气加压机控制。 煤气进出口阀的调节。 流量、压力、温度、液位、一氧化碳 等的数据采集。 与转炉生产的联系信号。
给水系统
其回水仅是温度升高,水质未受污染, 自流到热水池,用泵送到清水冷却塔, 降温处理后再用泵加压循环使用。系 统损失水量由生产新水管网接管补给。 系统设有无阀砂滤罐用于旁滤水处理。
转炉给水系统
转炉烟气除尘浊循环给水系统 该系统包括转炉烟气除尘污水处理和 污泥处理两部分。
转炉给水系统
转炉烟气除尘浊环水处理系统 转炉烟气净化采用“双文”并联湿法 除尘给水系统,每座60t转炉除尘用水 量约为:700 m3/h。该系统主要供给 转炉烟气一文、二文喷水除尘、冷却 和弯管冲洗之用,属于直接冷却,其 回水不仅温度升高,水质还受到污染
浏览站
DCS 工程师 站
SDB GE Tool Box
EGD / SRTP
90-70 PLC PA70 DCS
ETHERNET (TCP/IP)
Hot Standby
Innovation Controller
VersaMax PLC
VME底板总线
分散I/O
轧线控制
Profibus/Genius/Devivenet
应用层协议 TCP/IP
TCP / UDP
以太网 通讯,模型
网际层(IP)
网络介质访问层
以太网
OpenProcess的远程访问技术
GE 工业系统集团
远程拨号访问 Windows NT RAS Server
远程计算机 电话线
Viewer 或 IE4.0 / Netscape
工程师站 (服务器)
VIEWERS (浏览站)
功能
设定控制。如参考模型手动输入控制吹氧 流量控制、氧枪高度控制、副原料装入控 制、底吹控制等。 转炉吹炼终点控制。根据初始装料(铁水 和废钢)条件计算好副原料加料和底吹供 气模型。参考模型手动输入控制。 主原料计算及副原料管理。
计算机控制系统简介
可分为: 下位机:PLC控制 上位机:工业监控
PLC控制系统
流程图
烟气净化
主要完成功能: 一次烟气冷却系统: 活动烟罩升降控制。 冷却水泵的控制。 排气阀、排水阀控制。 一次烟气净化系统: 电磁阀的控制。电动阀的控制。 冷却水泵的控制。 润滑站的控制。
烟气净化烟气净化
● ● ● ● ● ● ● 烟气成份(CO、O2)分析 一文进口烟气温度测量 二文进、出口烟气温度测量 一文、二文进出口差压测量 偶合器供、排油温度测量 引风机进出口烟气温度、压力测量 引风机、电机轴承温度测量
转炉本体之检测点
●氮气总管压力、流量测量 ● 溅渣护炉氮气流量、压力测量 ● 氮气总管压力调节 转炉稀油站系统 ● 稀油箱稀油液位测量 ● 稀油箱稀油压力测量 ● 稀油箱稀油温度测量
转炉本体之检测点
转炉底吹系统 ● 底吹氩气, 氮气总管压力,流量测量 ● 底吹氩气,氮气支管压力,流量测量 ● 底吹氩气,氮气总管压力调节 ● 底吹氩气,氮气支管流量调节
温度是衡量物体冷热和谐的一个物理量。 常用温标有华氏温度、摄氏温度和开氏温 度。 测量方法有:热电偶、热电阻、非接触式。 热电偶、快速热电偶、热电阻Pt100、连 续测温表等。配套仪表有:测温表 具体有:铁水处理、炉前、吹氩、精炼炉、 中间包、钢坯表面。
物位测量
测量方式有静压式、雷达、超声波、 核辐射式等。 如:单法兰变送器、双室平衡容器、 雷达、光纤柜位计、超声波水 位计等。
烟气净化
汽化冷却系统 ● 锅筒压力,水位测量、控制 ● 蓄热汽包压力及水位测量、控制 ● 给水压力测量 ● 给水流量测量及控制 ● 蒸汽压力,流量测量 ● 工业水压力,流量测量
烟气净化
二次除尘系统
● ● ● ● ● ● ● 除尘器进、出口压力测量 烟气流量测量 引风机进、出口压力测量 引风机进、出口温度测量 液力偶合器供排油温度测量 除尘器进口掺冷风控制 支管烟气阀门控制
Profibus/Genius/D-Lan
加热炉控制
交直流传动
系统特点: 1. 2. 3. 4. 开放的Windows NT或VMS操作系统 VME总线控制器 GE专有的数学模型 提供NT或VMS平台上的C++开发工具,允 许用户自建的数学模型与控制器完成 EGD/SRTP网络数据通讯
MCC
SRTP / EGD
厂区局域网
Plant-Wide Network
远控制系统
新转炉控制系统按PLC的CPU分包括: 1、转炉本体; 2、汽化系统; 3、二次除尘; 4、上料系统; 5、吹氩站; 6、五万气柜; 7、水处理系统;
新转炉控制系统
7、精炼炉系统; 8、铁水预处理; 9、连铸系统; 10、铸坯热送; 以下分述:
流量测量仪表
流量是指:单位时间内通过管道某一截面 的流体数量。可分为体积流量和质量流量 常用单位有:m3/h、l/min、t/h、Nm3/h 流量仪表检测原理有:差压式、频率式、 电磁式等。 新转炉用到的流量计有: 孔板、弯管流量计、阿牛巴流量计、威 力巴流量计、旋进式流量计、电磁流量计
温度测量仪表
32640 输入 / 32640 输出 模拟量 2048 输入 / 2048 输出 开关量 240K 程序代码空间 .22ms / K 程序代码 3-5 ms 每个闭环刷新间隔
GE Total Solution
iFix
HMI
GE 工业系统集团
数学模型 Alpha/VMS C++编程工具包 Web 服务 器
仪表的质量指标
准确度和准确度等级: 准确度是指测量结果和实际值的一致 程度。 准确度等级是仪表按准确度高低分 成的等级。它决定仪表在标准条件下 的误差限,也就是仪表基本误差的最 大允许值。 准确度习惯上又称精确度或精度, 准确度等级也称精确度等级或精度等 级
仪表分类
凡是用来直接或间接将被测参数和测 量单位作比较的设备,均称为测量仪 表。其分类有以下几种: 1、按被测参数不同,可分为:压力测 量仪表、物位测量仪表、流量测量仪 表、温度测量仪表、成分分析仪表等。 2、按显示方式:可分为指示式、指示 记录、累积式、数字式和屏幕式等。
流程图
转炉水处理系统
工作方式选择及连锁控制。 水泵电机的速度调节。 信号转换及处理。 水泵与阀门连锁及处理。
转炉净循环给水系统
该系统主要供给转炉氧枪高压水,转炉 炉口、托圈、炉帽、耳轴、炉前等中压 水,炉前炉后摇炉室、一文除尘隔热水 套和等低压水,LF炉、除尘设备冷却和 空调等用户冷却之用,属于间接冷却