丰田三厂色差管理范围
色差国标范围
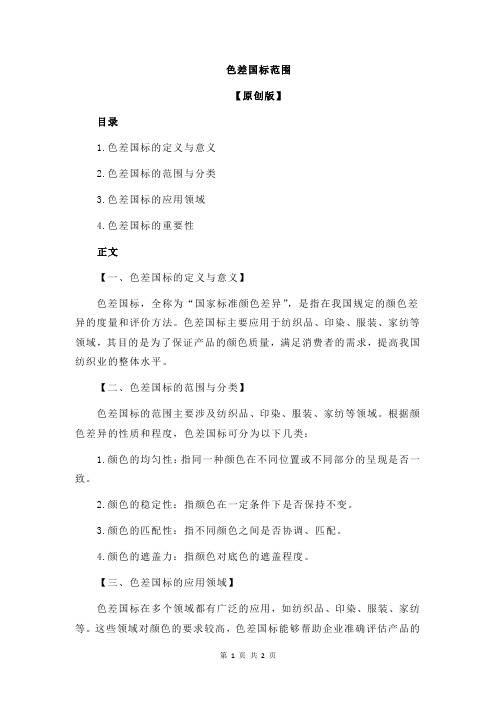
色差国标范围
【原创版】
目录
1.色差国标的定义与意义
2.色差国标的范围与分类
3.色差国标的应用领域
4.色差国标的重要性
正文
【一、色差国标的定义与意义】
色差国标,全称为“国家标准颜色差异”,是指在我国规定的颜色差异的度量和评价方法。
色差国标主要应用于纺织品、印染、服装、家纺等领域,其目的是为了保证产品的颜色质量,满足消费者的需求,提高我国纺织业的整体水平。
【二、色差国标的范围与分类】
色差国标的范围主要涉及纺织品、印染、服装、家纺等领域。
根据颜色差异的性质和程度,色差国标可分为以下几类:
1.颜色的均匀性:指同一种颜色在不同位置或不同部分的呈现是否一致。
2.颜色的稳定性:指颜色在一定条件下是否保持不变。
3.颜色的匹配性:指不同颜色之间是否协调、匹配。
4.颜色的遮盖力:指颜色对底色的遮盖程度。
【三、色差国标的应用领域】
色差国标在多个领域都有广泛的应用,如纺织品、印染、服装、家纺等。
这些领域对颜色的要求较高,色差国标能够帮助企业准确评估产品的
颜色质量,从而提高产品的市场竞争力。
【四、色差国标的重要性】
色差国标对于保证产品质量、满足消费者需求、提高我国纺织业整体水平具有重要意义。
通过执行色差国标,企业可以建立科学的颜色管理制度,有效控制颜色差异,降低生产成本,提高生产效率。
同时,色差国标也有利于规范市场秩序,保护消费者的权益。
总之,色差国标对于纺织品、印染、服装、家纺等领域的产品质量评价具有重要作用。
色差控制
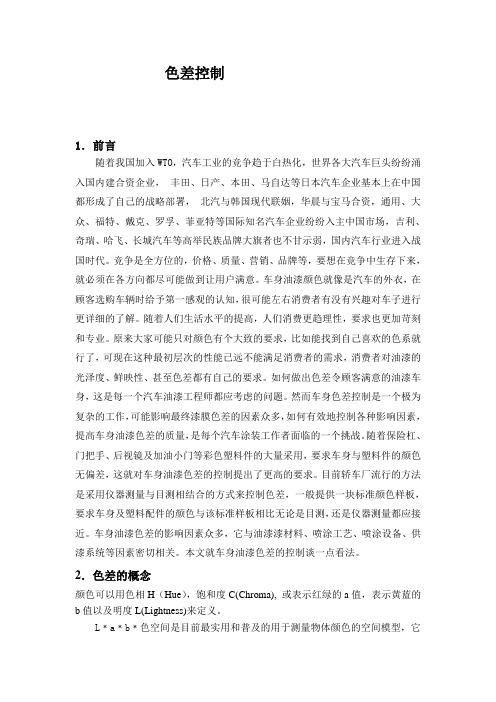
色差控制1.前言随着我国加入WTO,汽车工业的竞争趋于白热化,世界各大汽车巨头纷纷涌入国内建合资企业,丰田、日产、本田、马自达等日本汽车企业基本上在中国都形成了自己的战略部署,北汽与韩国现代联姻,华晨与宝马合资,通用、大众、福特、戴克、罗孚、菲亚特等国际知名汽车企业纷纷入主中国市场,吉利、奇瑞、哈飞、长城汽车等高举民族品牌大旗者也不甘示弱,国内汽车行业进入战国时代。
竞争是全方位的,价格、质量、营销、品牌等,要想在竞争中生存下来,就必须在各方向都尽可能做到让用户满意。
车身油漆颜色就像是汽车的外衣,在顾客选购车辆时给予第一感观的认知,很可能左右消费者有没有兴趣对车子进行更详细的了解。
随着人们生活水平的提高,人们消费更趋理性,要求也更加苛刻和专业。
原来大家可能只对颜色有个大致的要求,比如能找到自己喜欢的色系就行了,可现在这种最初层次的性能已远不能满足消费者的需求,消费者对油漆的光泽度、鲜映性、甚至色差都有自己的要求。
如何做出色差令顾客满意的油漆车身,这是每一个汽车油漆工程师都应考虑的问题。
然而车身色差控制是一个极为复杂的工作,可能影响最终漆膜色差的因素众多,如何有效地控制各种影响因素,提高车身油漆色差的质量,是每个汽车涂装工作者面临的一个挑战。
随着保险杠、门把手、后视镜及加油小门等彩色塑料件的大量采用,要求车身与塑料件的颜色无偏差,这就对车身油漆色差的控制提出了更高的要求。
目前轿车厂流行的方法是采用仪器测量与目测相结合的方式来控制色差,一般提供一块标准颜色样板,要求车身及塑料配件的颜色与该标准样板相比无论是目测,还是仪器测量都应接近。
车身油漆色差的影响因素众多,它与油漆漆材料、喷涂工艺、喷涂设备、供漆系统等因素密切相关。
本文就车身油漆色差的控制谈一点看法。
2.色差的概念颜色可以用色相H(Hue),饱和度C(Chroma), 或表示红绿的a值,表示黄蓝的b值以及明度L(Lightness)来定义。
L﹡a﹡b﹡色空间是目前最实用和普及的用于测量物体颜色的空间模型,它是CIE (国际照明委员会,法文:Corporación Interamericana de Entretenimiento ,英文名称:International Commission on Illumination )定义的色空间(如图1所示),本文中所提及的Lab 均为CIE 模型标准。
车身色差实例分析与控制预防

车身色差实例分析与控制预防一汽海马汽车有限公司技术工程部王捷【摘要】以我厂淡金色车身色差问题为实例,进行原因分析并提出合理的控制预防建议。
【关键词】色差分析解决控制预防1前言色差是指保险杠、门拉手、外后视镜等颜色塑料外饰件与车身的色相、明度、彩度有差异的问题。
因为门拉手、外后视镜这类小件与车身不在一个安装平面上,且着色面积较小,所以涂装领域通常所讨论的色差问题,主要是指车身颜色变化导致与保险杠无法匹配的情况。
图1 车身与保险杠色差示意图据统计,2015年淡金色车身产量占我厂彩色系车身总产量的49%,作为我厂主打车型的主推颜色,其质量的好坏对生产效率、成本、乃至公众口碑都有着直接或间接的影响。
然而淡金色这种色漆明度高,颜色鲜艳,对缺陷的遮盖力较差,材料、施工等过程稍有变化,都有可能引起色差问题。
图2 2015年彩色系车身产量统计图2 现状经分析,我厂淡金色色差问题主要集中在两个方面,油漆批次色差和车身颜色分布不均。
油漆批次色差。
2015年6月至11月,三厂涂装共使用7个批次淡金色油漆,每次油漆批次切换时,都会导致车身颜色状态不同程度的变化,如表1所示。
虽然通过油漆导入先期确认、协调生产、提前进车对色、调整保险杠颜色配方等临时措施避免了色差问题的批量发生,但也使得生产、质量、技术等各方面较为被动,耗费人力和资源。
表1 2015年6-11月淡金色油漆批次切换使用情况记录表车身颜色分布不均。
车身上涉及到与保险杠匹配的区域主要是前后翼子板。
由于保险杠是由供应商负责喷涂的,为了确保保险杠和车身颜色状态的稳定性,及时发现色差问题,在涂装车间存放了每种颜色车型的保险杠封样件,用于每班每种颜色车型的首检确认,如图3所示。
然而自淡金色转三厂涂装生产后,车身颜色分布不均问题日益显著,并且开始影响日常对色和保险杠封样件的评审工作。
主要表现为左侧翼子板黄相b比右侧大,后翼子板黄相b比前翼子板大,使得车身与保险杠的匹配始终无法达到理想效果。
色差检验标准环境
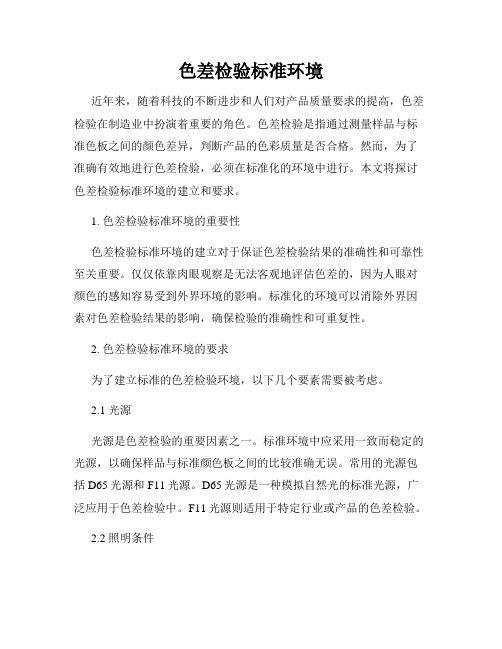
色差检验标准环境近年来,随着科技的不断进步和人们对产品质量要求的提高,色差检验在制造业中扮演着重要的角色。
色差检验是指通过测量样品与标准色板之间的颜色差异,判断产品的色彩质量是否合格。
然而,为了准确有效地进行色差检验,必须在标准化的环境中进行。
本文将探讨色差检验标准环境的建立和要求。
1. 色差检验标准环境的重要性色差检验标准环境的建立对于保证色差检验结果的准确性和可靠性至关重要。
仅仅依靠肉眼观察是无法客观地评估色差的,因为人眼对颜色的感知容易受到外界环境的影响。
标准化的环境可以消除外界因素对色差检验结果的影响,确保检验的准确性和可重复性。
2. 色差检验标准环境的要求为了建立标准的色差检验环境,以下几个要素需要被考虑。
2.1 光源光源是色差检验的重要因素之一。
标准环境中应采用一致而稳定的光源,以确保样品与标准颜色板之间的比较准确无误。
常用的光源包括D65光源和F11光源。
D65光源是一种模拟自然光的标准光源,广泛应用于色差检验中。
F11光源则适用于特定行业或产品的色差检验。
2.2 照明条件除了光源的选择外,适当的照明条件也是建立标准环境的关键。
一般来说,色差检验室应保持均匀、中性的照明条件,避免强光或弱光对检验结果的影响。
在人眼感知色彩时,周围的照明条件应趋于均匀,以消除主观色差的可能性。
2.3 背景颜色色差检验标准环境中使用的背景颜色也需要考虑。
常见的背景颜色有中性灰、白色和黑色等。
选择合适的背景颜色可以减少感知色差的干扰,提高比较的准确性。
中性灰背景一般较为常用,因为它能够更好地突出样品的颜色。
2.4 温度和湿度标准环境的温度和湿度对色差检验结果也有一定影响。
过高或过低的温度会导致检验的不准确,因此应保持适宜的温度范围。
一般来说,标准环境的温度应在20-25摄氏度之间,湿度应在40-60%之间。
3. 色差检验标准环境的建立和管理为了确保色差检验标准环境的有效性,建议采取以下措施:3.1 定期校准仪器色差检测仪器需要定期校准以保持准确度。
汽车涂装中的涂装色差与配色技术
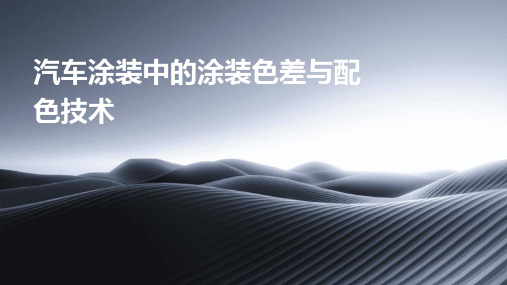
未来发展趋势预测
智能化技术应用
随着人工智能、大数据等技术的不断发展,未来汽车涂装将实现更高程度的自动化和智 能化,提高生产效率和涂装质量。
环保法规要求提高
随着全球环保意识的增强和环保法规的日益严格,汽车涂装行业将面临更高的环保要求 和挑战,需要采取更环保的涂料和涂装工艺。
为满足市场多元化需求,提升车型竞争力,某汽车厂商决定对旗下某款车型进行全新颜色设计。
设计过程
设计团队首先进行了市场调研,分析了目标消费者的喜好和流行趋势,然后结合车型特点和品牌定位,制定了多种颜 色方案。经过多次评审和修改,最终选定了符合市场需求和品牌形象的车身颜色。
设计成果
新颜色方案的应用显著提升了该车型的视觉效果和辨识度,赢得了消费者的广泛好评,同时也为品牌注 入了新的活力。
建立色差管理体系
建立完善的色差管理体系,包括色差标准制定、色差检测、色差分 析和处理等环节,以确保涂装质量的稳定性和一致性。
强化质量意识教育
加强员工的质量意识教育,使员工充分认识到色差对产品质量和客户 满意度的影响,提高员工对色差控制的重视程度。
05
配色技术应用实践
某车型车身颜色设计案例分享
设计背景
01
案例一
某汽车制造厂涂装车间出现色差问题,通过目视法和色差计法进行检测
,发现ΔE值超过了企业标准。经过调整涂料配方和工艺参数,最终使
色差控制在标准范围内。
02
案例二
某汽车零部件供应商向主机厂提供的涂装件存在明显色差,经过光谱分
析发现涂料中某种颜料含量不足。供应商对涂料进行调整后,重新提供
的涂装件颜色与主机厂要求一致。
汽车涂装生产中塑料件油漆色差的产
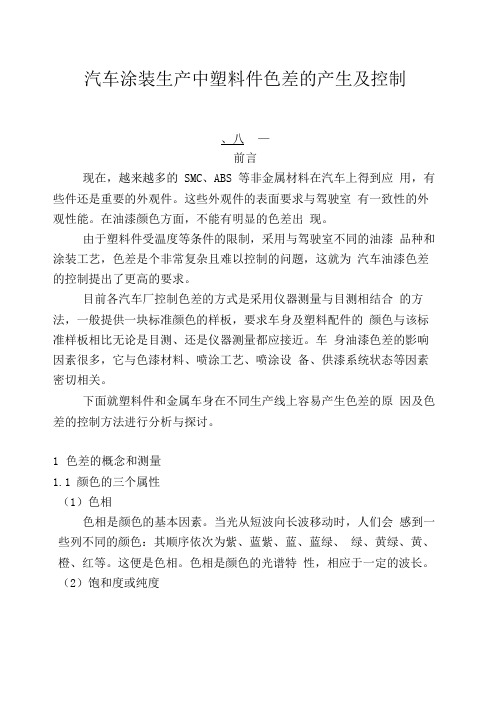
汽车涂装生产中塑料件色差的产生及控制、八—前言现在,越来越多的 SMC、ABS 等非金属材料在汽车上得到应用,有些件还是重要的外观件。
这些外观件的表面要求与驾驶室有一致性的外观性能。
在油漆颜色方面,不能有明显的色差出现。
由于塑料件受温度等条件的限制,采用与驾驶室不同的油漆品种和涂装工艺,色差是个非常复杂且难以控制的问题,这就为汽车油漆色差的控制提出了更高的要求。
目前各汽车厂控制色差的方式是采用仪器测量与目测相结合的方法,一般提供一块标准颜色的样板,要求车身及塑料配件的颜色与该标准样板相比无论是目测、还是仪器测量都应接近。
车身油漆色差的影响因素很多,它与色漆材料、喷涂工艺、喷涂设备、供漆系统状态等因素密切相关。
下面就塑料件和金属车身在不同生产线上容易产生色差的原因及色差的控制方法进行分析与探讨。
1色差的概念和测量1.1 颜色的三个属性(1)色相色相是颜色的基本因素。
当光从短波向长波移动时,人们会感到一些列不同的颜色:其顺序依次为紫、蓝紫、蓝、蓝绿、绿、黄绿、黄、橙、红等。
这便是色相。
色相是颜色的光谱特性,相应于一定的波长。
(2)饱和度或纯度饱和度代表颜色的纯度,最接近光谱色的是最纯的光,称纯色或者饱和度高。
无彩色的纯度最低,当光刺激中混入无彩色成分时,纯度降低。
(3)明度或亮度明度是物体反射光的量度,一个明亮的彩色物体以为着它反射(或透过)了大部分投射在其上的光。
如果将色谱上的彩色光投在灰度不同的银幕上,会看到颜色的光亮程度随着银幕的反射能力的变化而变化,其中白色的银幕反射能力最强,明度最高,黑色的银幕不能反射任何光,故明度为 0。
1.2 色差的判断依据常用的方法有两种:目测和仪器测量。
目测是最主要和基本的方法,将产品与标准板相邻地放置在同一水平面,在标准光源和标准背景的环境中,判断产品颜色在不同视角下是否可以接受。
色差的测量一般采用分光测色法,首先测出待测光的光谱分布或试样的光谱反射率,然后通过计算求出色度值。
丰田3s管理制度范文

丰田3s管理制度范文丰田3S管理制度范1.引言丰田汽车公司作为全球领先的汽车制造商之一,以其卓越的汽车品质和持续不断的创新而闻名。
在丰田的成功背后,有一套完善的管理制度,即丰田3S管理制度(Sales, Service, Spare parts)。
这一制度是丰田在全球范围内推行的,旨在提供卓越的售后服务和确保顾客满意度。
本文将详细介绍丰田3S管理制度的内容和实施方法。
2.丰田3S管理制度的内容2.1 销售(Sales)丰田的销售部门是公司与顾客之间的桥梁,负责销售汽车和相关产品。
丰田3S管理制度要求销售部门必须具备以下能力和特点:2.1.1 产品知识丰富:销售人员必须对丰田的汽车产品有深入的了解,并能够准确地向顾客介绍产品的特点和优势。
2.1.2 顾客服务技巧:销售人员必须具备良好的沟通能力和高水平的顾客服务技巧,能够主动倾听顾客需求并提供专业的咨询和建议。
2.1.3 销售目标达成能力:销售人员必须具备较强的销售能力,能够根据市场需求和竞争情况制定销售目标,并积极努力实现目标。
2.2 售后服务(Service)丰田的售后服务部门是为顾客提供维修和保养服务的单位。
丰田3S管理制度要求售后服务部门必须具备以下能力和特点:2.2.1 技术专业性:售后服务人员必须具备专业的汽车维修和保养知识,能够准确诊断和解决汽车故障,并进行有效的保养工作。
2.2.2 故障排除能力:售后服务人员必须具备快速排除汽车故障的能力,能够通过精确的分析和判断找出故障原因,并采取适当的措施进行修复。
2.2.3 服务态度:售后服务人员必须具备友好、耐心和细致的服务态度,能够及时回应顾客的需求和反馈,并解答顾客的疑问。
2.3 零配件(Spare parts)丰田的零配件部门负责采购和管理汽车零配件的供应。
丰田3S管理制度要求零配件部门必须具备以下能力和特点:2.3.1 供应链管理:零配件部门必须建立和维护与丰田合作伙伴的紧密关系,确保零配件供应的可靠性和及时性。
汽车油漆色差产生的原因以及控制措施分析

汽车油漆色差产生的原因以及控制措施分析油漆喷涂色差是目前我国汽车喷涂行业里十分棘手的一个现象,有着十分重要的研究价值。
但是目前,我国关于汽车油漆喷涂色差出现以及相关控制策略的研究还相对较少,针对这样的实际情况,需要制定切实可行的方式对其进行不断总结与完善。
例如可以通过制定事先标准化的作业流程、强化施工材料选择、提升员工自身喷涂技能、基于技术层面进行分析等角度对其进行完善。
1 颜色属性自然界的颜色千千万万,但所有的颜色都有着三个共同的特点,就是具备一定的色彩相貌、浓淡程度和明亮程度。
一般来说,我们把颜色的这三个特点可以共称为颜色的三个特性或属性,分别为色调、明度与彩度,不管是什么颜色都可以利用这三个特性进行评定,可以对其进行定性、定量的描述。
此外颜色的这三个特性也可以利用现代仪器进行测定,也可以利用目测的方式对其进行评定。
1.1 色调色调又可称作是色别或者是色相,是色彩最为显著的特征,也是不同色彩之间最容易区别的特征之一。
色调一般表示为带有一定波长的单色光,能够准确表示颜色类别,也可以利用其对颜色类别名称进行分类,比如红、橙、黄、绿、青、蓝、紫,其所对应的都是某一具体的色调,紫红、红、红黄都是属于红色中的不同色调,其颜色之间的差别也可称之为色调差别。
1.2 明度明度又可稱为深浅度、亮度或者是黑白度,其代表的是物体反射光线的颜色属性,也是人们视觉上所能够看到的颜色明暗程度差别,同一种色调可以有不同的明度,不同的色调也可以存在不同的明度。
比如对于太阳光谱来说,紫色的明度最低,处于中等明度的颜色为红色、绿色,所有颜色中黄色的明度最高,这也是为什么我们感觉黄色是最亮的一种颜色的原因。
1.3 彩度彩度又可称作是饱和度或是纯度,指的是具有反射光线或是透射光线接近光谱色的一种程度,比如彩度一般可以分成0-20档,如果小于0.5,就可以称作为无彩度;如果彩度接近20,则可以称作是饱和度。
一般彩度是人体的心理纯度感觉,对于可见光谱来说,单色光是最纯的颜色,也可称作为极限纯度。
色差允许值
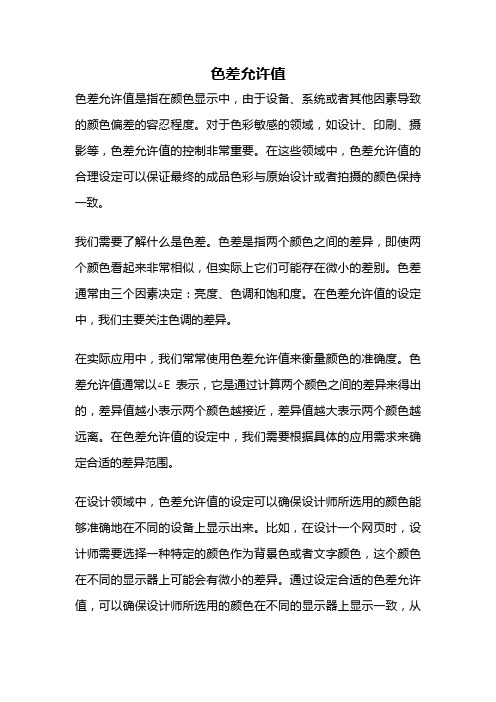
色差允许值色差允许值是指在颜色显示中,由于设备、系统或者其他因素导致的颜色偏差的容忍程度。
对于色彩敏感的领域,如设计、印刷、摄影等,色差允许值的控制非常重要。
在这些领域中,色差允许值的合理设定可以保证最终的成品色彩与原始设计或者拍摄的颜色保持一致。
我们需要了解什么是色差。
色差是指两个颜色之间的差异,即使两个颜色看起来非常相似,但实际上它们可能存在微小的差别。
色差通常由三个因素决定:亮度、色调和饱和度。
在色差允许值的设定中,我们主要关注色调的差异。
在实际应用中,我们常常使用色差允许值来衡量颜色的准确度。
色差允许值通常以△E表示,它是通过计算两个颜色之间的差异来得出的,差异值越小表示两个颜色越接近,差异值越大表示两个颜色越远离。
在色差允许值的设定中,我们需要根据具体的应用需求来确定合适的差异范围。
在设计领域中,色差允许值的设定可以确保设计师所选用的颜色能够准确地在不同的设备上显示出来。
比如,在设计一个网页时,设计师需要选择一种特定的颜色作为背景色或者文字颜色,这个颜色在不同的显示器上可能会有微小的差异。
通过设定合适的色差允许值,可以确保设计师所选用的颜色在不同的显示器上显示一致,从而保证用户的浏览体验。
在印刷领域中,色差允许值的设定可以确保印刷品的色彩与原始设计保持一致。
在印刷过程中,使用的油墨、纸张、设备等都可能会对最终的色彩产生影响。
通过设定合适的色差允许值,可以确保印刷品的色彩与原始设计尽可能接近。
在摄影领域中,色差允许值的设定可以确保照片的色彩准确传达摄影师的意图。
在拍摄过程中,光线、环境等因素都可能会对照片的色彩产生影响。
通过设定合适的色差允许值,可以确保照片的色彩与摄影师的意图尽可能一致。
色差允许值的设定在色彩敏感的领域中非常重要。
合理设定色差允许值可以确保颜色的准确传达,保证最终成品与原始设计或者拍摄的颜色保持一致。
在实际应用中,我们需要根据具体的需求和应用场景来确定合适的色差允许值。
正常色差允许范围
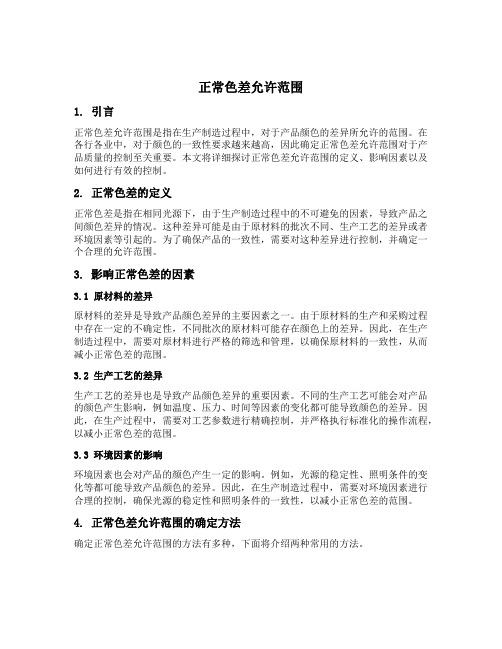
正常色差允许范围1. 引言正常色差允许范围是指在生产制造过程中,对于产品颜色的差异所允许的范围。
在各行各业中,对于颜色的一致性要求越来越高,因此确定正常色差允许范围对于产品质量的控制至关重要。
本文将详细探讨正常色差允许范围的定义、影响因素以及如何进行有效的控制。
2. 正常色差的定义正常色差是指在相同光源下,由于生产制造过程中的不可避免的因素,导致产品之间颜色差异的情况。
这种差异可能是由于原材料的批次不同、生产工艺的差异或者环境因素等引起的。
为了确保产品的一致性,需要对这种差异进行控制,并确定一个合理的允许范围。
3. 影响正常色差的因素3.1 原材料的差异原材料的差异是导致产品颜色差异的主要因素之一。
由于原材料的生产和采购过程中存在一定的不确定性,不同批次的原材料可能存在颜色上的差异。
因此,在生产制造过程中,需要对原材料进行严格的筛选和管理,以确保原材料的一致性,从而减小正常色差的范围。
3.2 生产工艺的差异生产工艺的差异也是导致产品颜色差异的重要因素。
不同的生产工艺可能会对产品的颜色产生影响,例如温度、压力、时间等因素的变化都可能导致颜色的差异。
因此,在生产过程中,需要对工艺参数进行精确控制,并严格执行标准化的操作流程,以减小正常色差的范围。
3.3 环境因素的影响环境因素也会对产品的颜色产生一定的影响。
例如,光源的稳定性、照明条件的变化等都可能导致产品颜色的差异。
因此,在生产制造过程中,需要对环境因素进行合理的控制,确保光源的稳定性和照明条件的一致性,以减小正常色差的范围。
4. 正常色差允许范围的确定方法确定正常色差允许范围的方法有多种,下面将介绍两种常用的方法。
4.1 CIE Lab色差公式CIE Lab色差公式是一种常用的确定正常色差允许范围的方法。
该方法基于人眼对颜色的感知,通过计算样品与标准样品之间的色差值来确定允许范围。
具体计算过程较为复杂,需要使用专业的色差仪和相关软件进行计算。
4.2 制定标准样品制定标准样品是另一种确定正常色差允许范围的常用方法。
制造中心颜色控制管理规定
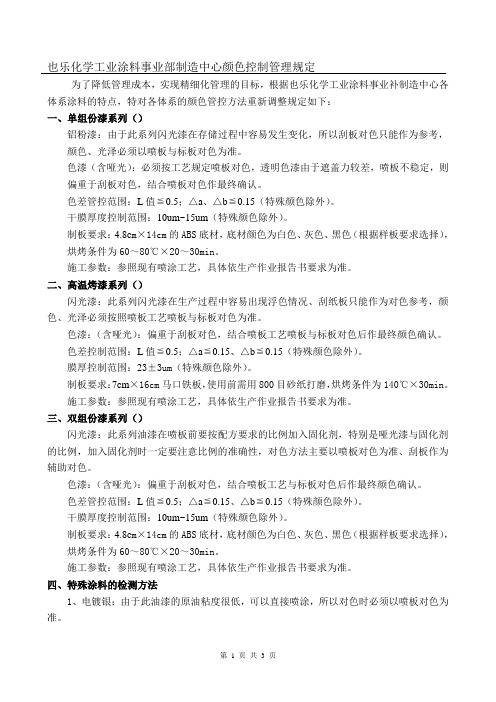
为了降低管理成本,实现精细化管理的目标,根据也乐化学工业涂料事业补制造中心各体系涂料的特点,特对各体系的颜色管控方法重新调整规定如下:一、单组份漆系列()铝粉漆:由于此系列闪光漆在存储过程中容易发生变化,所以刮板对色只能作为参考,颜色、光泽必须以喷板与标板对色为准。
色漆(含哑光):必须按工艺规定喷板对色,透明色漆由于遮盖力较差,喷板不稳定,则偏重于刮板对色,结合喷板对色作最终确认。
色差管控范围:L值≦0.5;△a、△b≦0.15(特殊颜色除外)。
干膜厚度控制范围:10um~15um(特殊颜色除外)。
制板要求:4.8c m×14cm的ABS底材,底材颜色为白色、灰色、黑色(根据样板要求选择),烘烤条件为60~80℃×20~30min。
施工参数:参照现有喷涂工艺,具体依生产作业报告书要求为准。
二、高温烤漆系列()闪光漆:此系列闪光漆在生产过程中容易出现浮色情况、刮纸板只能作为对色参考,颜色、光泽必须按照喷板工艺喷板与标板对色为准。
色漆:(含哑光):偏重于刮板对色,结合喷板工艺喷板与标板对色后作最终颜色确认。
色差控制范围:L值≦0.5;△a≦0.15、△b≦0.15(特殊颜色除外)。
膜厚控制范围:23±3um(特殊颜色除外)。
制板要求:7cm×16cm马口铁板,使用前需用800目砂纸打磨,烘烤条件为140℃×30min。
施工参数:参照现有喷涂工艺,具体依生产作业报告书要求为准。
三、双组份漆系列()闪光漆:此系列油漆在喷板前要按配方要求的比例加入固化剂,特别是哑光漆与固化剂的比例,加入固化剂时一定要注意比例的准确性,对色方法主要以喷板对色为准、刮板作为辅助对色。
色漆:(含哑光):偏重于刮板对色,结合喷板工艺与标板对色后作最终颜色确认。
色差管控范围:L值≦0.5;△a≦0.15、△b≦0.15(特殊颜色除外)。
干膜厚度控制范围:10um~15um(特殊颜色除外)。
质量管理培训之色差篇
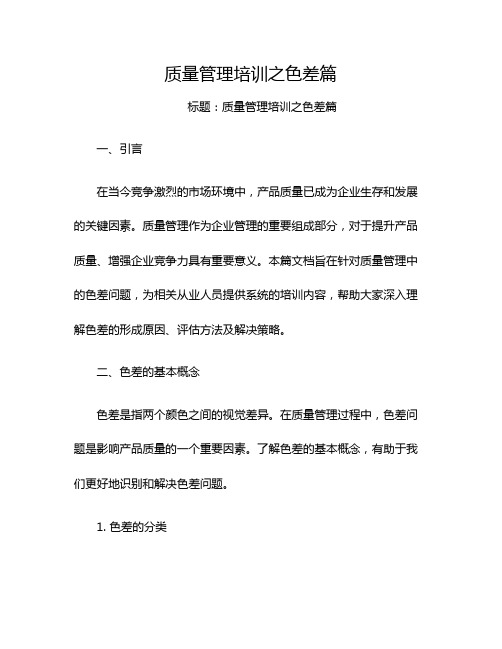
质量管理培训之色差篇标题:质量管理培训之色差篇一、引言在当今竞争激烈的市场环境中,产品质量已成为企业生存和发展的关键因素。
质量管理作为企业管理的重要组成部分,对于提升产品质量、增强企业竞争力具有重要意义。
本篇文档旨在针对质量管理中的色差问题,为相关从业人员提供系统的培训内容,帮助大家深入理解色差的形成原因、评估方法及解决策略。
二、色差的基本概念色差是指两个颜色之间的视觉差异。
在质量管理过程中,色差问题是影响产品质量的一个重要因素。
了解色差的基本概念,有助于我们更好地识别和解决色差问题。
1. 色差的分类色差可以分为两类:客观色差和主观色差。
客观色差是指颜色在物理属性上的差异,如亮度、色调和饱和度等;主观色差是指颜色在心理感知上的差异,如色彩喜好、色彩搭配等。
2. 色差的产生原因(1)原材料色差:由于原材料批次不同、产地不同等原因,导致颜色存在差异。
(2)生产工艺色差:生产过程中,如温度、湿度、压力等工艺参数波动,可能导致颜色出现偏差。
(3)设备色差:生产设备磨损、老化、校准不准确等原因,可能引起颜色差异。
(4)环境色差:生产环境中的光线、温度、湿度等因素,可能对颜色产生影响。
(5)人为因素:操作人员技术水平、视觉识别能力等差异,可能导致颜色判断不准确。
三、色差的评估方法色差的评估方法主要包括客观评估和主观评估两种。
1. 客观评估方法客观评估方法主要依靠仪器设备进行测量,具有较高的准确性和重复性。
常见的客观评估方法有:(1)色差仪测量:通过色差仪测量样品的亮度、色调和饱和度等参数,计算出色差值。
(2)分光光度计测量:通过分光光度计测量样品的光谱反射率或透射率,分析颜色差异。
2. 主观评估方法主观评估方法主要依靠人眼观察和判断,具有一定的主观性。
常见的主观评估方法有:(1)对比法:将样品与标准色板进行对比,判断颜色差异。
(2)色标法:使用色标进行颜色排序,评估颜色差异。
(3)色彩喜好测试:通过调查问卷等方式,了解消费者对颜色的喜好程度。
色差控制管理规定
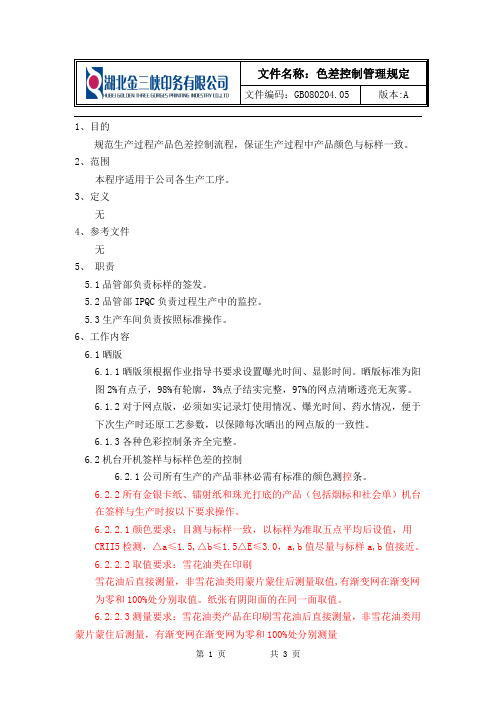
文件编码:GB080204.05版本:A1、目的规范生产过程产品色差控制流程,保证生产过程中产品颜色与标样一致。
2、范围本程序适用于公司各生产工序。
3、定义无4、参考文件无5、职责5.1品管部负责标样的签发。
5.2品管部IPQC负责过程生产中的监控。
5.3生产车间负责按照标准操作。
6、工作内容6.1晒版6.1.1晒版须根据作业指导书要求设置曝光时间、显影时间。
晒版标准为阳图2%有点子,98%有轮廓,3%点子结实完整,97%的网点清晰透亮无灰雾。
6.1.2对于网点版,必须如实记录灯使用情况、爆光时间、药水情况,便于下次生产时还原工艺参数,以保障每次晒出的网点版的一致性。
6.1.3各种色彩控制条齐全完整。
6.2机台开机签样与标样色差的控制6.2.1公司所有生产的产品菲林必需有标准的颜色测控条。
6.2.2所有金银卡纸、镭射纸和珠光打底的产品(包括烟标和社会单)机台在签样与生产时按以下要求操作。
6.2.2.1颜色要求:目测与标样一致,以标样为准取五点平均后设值,用CRII5检测,△a≤1.5,△b≤1.5△E≤3.0,a,b值尽量与标样a,b值接近。
6.2.2.2取值要求:雪花油类在印刷雪花油后直接测量,非雪花油类用蒙片蒙住后测量取值,有渐变网在渐变网为零和100%处分别取值。
纸张有阴阳面的在同一面取值。
6.2.2.3测量要求:雪花油类产品在印刷雪花油后直接测量,非雪花油类用蒙片蒙住后测量,有渐变网在渐变网为零和100%处分别测量文件编码:GB080204.05版本:A6.2.2.4蒙片要求:干净,统一,细哑光,与被检测色接触紧密。
6.2.2.5签样要求:目测与标样一致,△a≤1.5,△b≤1.5△E≤3.0,a,b值尽量与标样a,b值接近,横向密度D±0.03,D值尽量与标样一致。
6.2.2.6控制要求:目测与标样一致,△a≤1.5,△b≤1.5△E≤3.0,a,b值尽量与标样a,b值接近,横向密度D±0.03,D值尽量与标样一致,整批密度D ±0.05,白卡或铜版纸密度D±0.02.6.2.3直接在白卡纸或铜版纸上面印刷的产品(包括烟标和社会单)机台在签样和生产时,颜色以仪器检测△a≤1.0,△b≤1.0,深色△E≤1.3,浅色△E≤0.8,横向密度D±0.02,整批密度D±0.03.目测与标样一致。
丰田技术标准TSH3131G
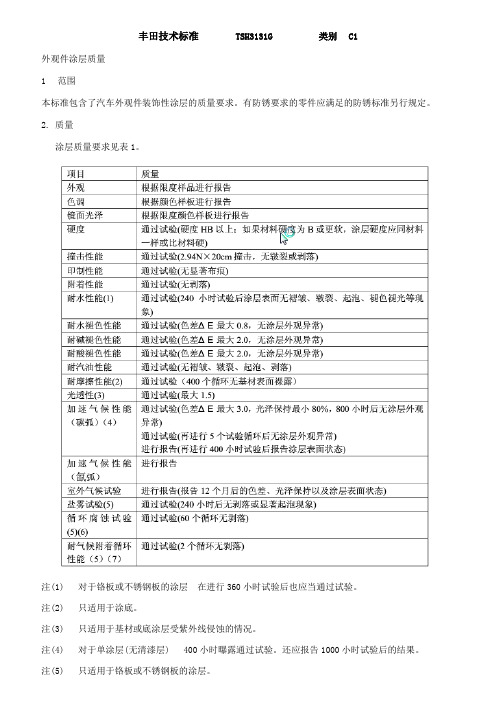
丰田技术标准 TSH3131G 类别C1外观件涂层质量1范围本标准包含了汽车外观件装饰性涂层的质量要求。
有防锈要求的零件应满足的防锈标准另行规定。
2. 质量涂层质量要求见表1。
注(1)对于铬板或不锈钢板的涂层在进行360小时试验后也应当通过试验。
注(2)只适用于涂底。
注(3)只适用于基材或底涂层受紫外线侵蚀的情况。
注(4)对于单涂层(无清漆层) 400小时曝露通过试验。
还应报告1000小时试验后的结果。
注(5)只适用于铬板或不锈钢板的涂层。
注(6)对于单涂层(无底漆)30个试验循环不能出现剥落。
注(7)只适用于双涂层(有底漆)。
3. 试验方法从正常生产的产品上截取适当尺寸制作成试验样品或者将产品使用的材料制成平板并按照产品的喷涂工艺进行喷涂。
3.1外观目视检查外观。
3.2 色调目视检查外观。
3.3镜面光泽根据TSH1519G第3节规定测量60度镜面光泽。
3.4硬度根据TSH1539G 2.1规定。
因基材导致的破损不要包括在评估之内。
3.5撞击性能根据TSH1504G 2.1.1规定。
如果基材开裂不要包括在评估之内。
3.6印制性能根据TSH1501G 2.1规定。
3.7附着性能根据TSH1503G第2节规定。
3.8耐水性能根据TSH1505G 2.1规定。
3.9耐水褪色性能根据TSH1509G 2.1.1规定。
3.10耐碱褪色性能根据TSH1509G 2.1.2规定。
3.11耐酸褪色性能根据TSH1509G 2.1.3规定。
3.12耐汽油性能根据TSH1508G 2.1.2规定。
不过采用[JIS]1号汽油作为试验液。
3.13耐摩擦性能在100mm×100mm尺寸厚度3毫米以上的样品中心位置镗一个直径约为7毫米的孔然后将其固定在TSL2100G 4.18规定的锥形摩擦试验机上,用CS#10摩擦盘施加4.9N负载进行旋转摩擦试验。
测定由于摩擦导致塑料表面裸露和涂层剥落所需要的试验循环数。
至于试验结果的判断只要塑料表面曝露即便是部分涂膜剥落就算试验试验透过涂层可以看到的塑料表面可以接受。
汽车厂外饰件面漆色差管理办法
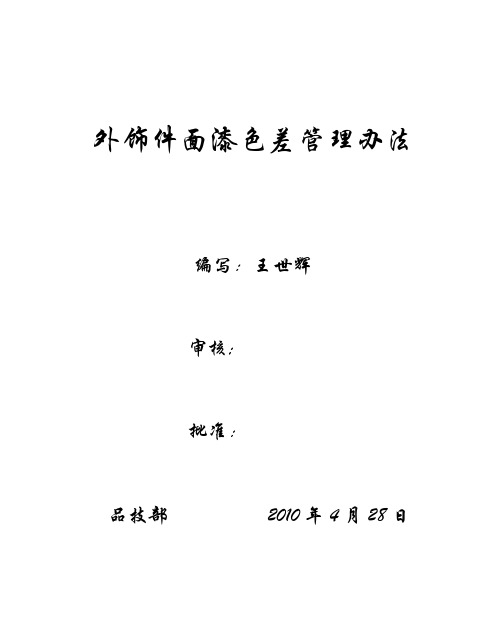
外饰件面漆色差管理办法
编写:王世辉
审核;
批准:
品技部2010年4月28日
外饰件面漆色差管理办法
针对外饰件,车身大包围、后视镜、车门外把手、扰流板、备胎罩等,同体色产品,存在面漆色差和早期老化褪色质量问题,为了统一颜色标准,满足质量要求。
特制订该外饰件面漆色差管理办法。
1外饰件面漆色差管理办法;2漆料色差管理办法;3面漆褪色老化试验4整车色差监控
一、外饰件面漆色差管理办法;
二、漆料色差控制程序
三、面漆褪色老化试验
四、整车色差监控(含车身在内的外饰件色差偏离区域)
色差监控表:(颜色偏深—●颜色偏浅—○颜色适中—▲)年月日
注:1.按日实施进货跟踪
2.标注进货批次
3.按旬编写整车色差监控报告(异常情况及时报告)
4报送品技部。
TSHG-外部涂层零件的漆膜质量(丰田技术标准)
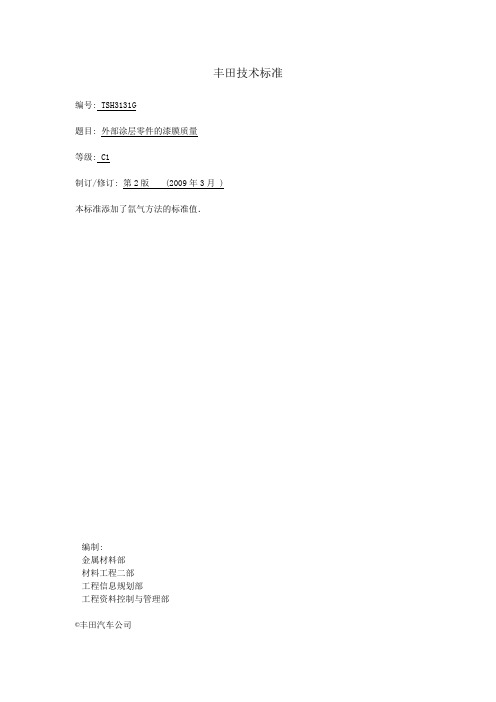
丰田技术标准编号: TSH3131G
题目: 外部涂层零件的漆膜质量
等级: C1
制订/修订: 第2版(2009年3月 )
本标准添加了氙气方法的标准值.
编制:
金属材料部
材料工程二部
工程信息规划部
工程资料控制与管理部
©丰田汽车公司
机密不可复制
2/8
3/8 机密不可复制
4/8 机密不可复制
5/8
机密 不可复制
进行
250MJ/m 2氙
板的一半打蜡
在未打蜡部分检查△E*和GR
在未打蜡部分检查△E*和GR
进行额外的400MJ/m 2氙
检查△E*和GR (打蜡部分)
板的一半打蜡
检查△E*和GR (打蜡部分)
6/8
机密 不可复制
检查△E*和GR (打蜡部分)
板的一半打蜡
板的一半打蜡
检查△E*和GR (打蜡部分)
在未打蜡部分检查△E*和GR
在未打蜡部分检查△E*和GR
进行400h SWOM
进行额外的400h SWOM
7/8 机密不可复制
8/8。
色差控制标准
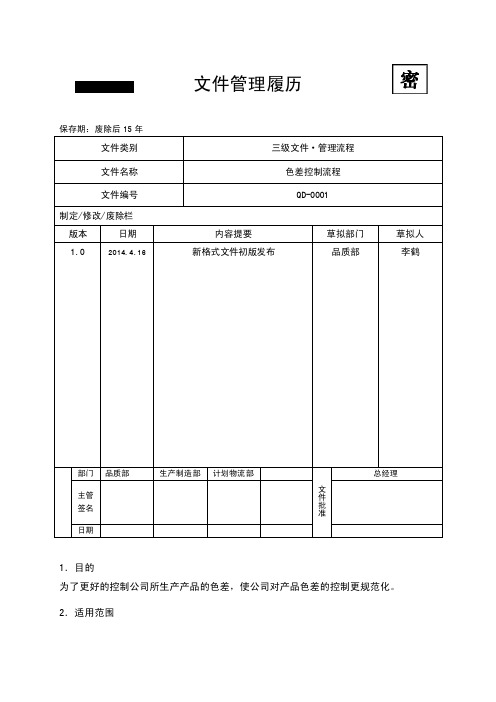
文件管理履历保存期:废除后15年1.目的为了更好的控制公司所生产产品的色差,使公司对产品色差的控制更规范化。
2.适用范围适用于公司生产的所有产品。
3.术语和省略语・无。
4.来料检验环节控制4.1对于每批到货的色母料,必须要求供应商提供色板,并要求进货检验员对来料色板使用专用色差仪进行测量,并保证色差值△E≤0.5,L值在±0.5以内,a、b值在±0.3以内,色差达到要求可以办理收货入库,否则退货。
5.生产过程控制环节5.1 IPQC检验员对生产过程中的产品进行色差控制。
6.首中末件色差确认6.1检验员对于首末件的色差确认应包括以下的确认:①首中末件与该项目标准色板的色差比较要符合色差要求,PP料:△E≤1,L值在±1以内,a、b值在±0.5以内。
PC/ABS料:△E≤1.5,L值在±1.5以内,a、b值在±0.5以内。
②首中末件与其相应的配合产品、上批次产品的色差目测合格。
以上两点均满足,方可对产品进行封首中末件,并记录色差值,通知生产部门可以批量。
7.过程产品色差控制环节7.1由过程巡检对生产过程的产品色首、中、末件进行色差确认,并记录在IPQC 检验记录表中。
8.出货检验环节8.1出货检验员根据色差需要满足以下要求:与上批次末件目测合格方可进行发货。
下面是余秋雨经典励志语录,欢迎阅读。
不需要的朋友可以编辑删除!!关于年龄1.一个横贯终生的品德基本上都是在青年时代形成的,可惜在那个至关重要的时代,青年人受到的正面的鼓动永远是为成功而搏斗,而一般所谓的成功总是带有排他性、自私性的印记。
结果,脸颊上还没有皱纹的他们,却在品德上挖下了一个个看不见的黑洞。
2.我不赞成太多地歌颂青年,而坚持认为那是一个充满陷阱的年代。
陷阱一生都会遇到,但青年时代的陷阱最多、最大、最险。
3.历史上也有一些深刻的哲人,以歌颂青年来弘扬社会的生命力。
但这里显然横亘着一种二律背反:越是坚固的对象越需要鼓动青年去对付,但他们恰恰因为年轻,无法与真正的坚持相斡旋。
色差管理作业办法Rve.0
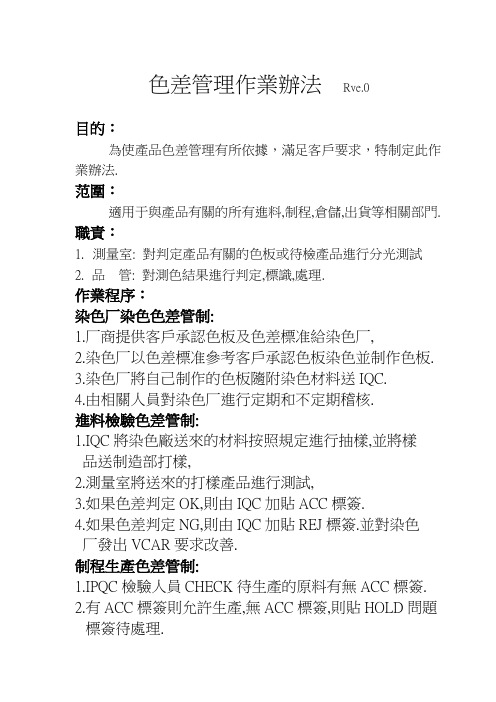
色差管理作業辦法Rve.0目的:為使產品色差管理有所依據,滿足客戶要求,特制定此作業辦法.范圍:適用于與產品有關的所有進料,制程,倉儲,出貨等相關部門.職責:1.測量室: 對判定產品有關的色板或待檢產品進行分光測試2.品管: 對測色結果進行判定,標識,處理.作業程序:染色厂染色色差管制:1.厂商提供客戶承認色板及色差標准給染色厂,2.染色厂以色差標准參考客戶承認色板染色並制作色板.3.染色厂將自己制作的色板隨附染色材料送IQC.4.由相關人員對染色厂進行定期和不定期稽核.進料檢驗色差管制:1.IQC將染色廠送來的材料按照規定進行抽樣,並將樣品送制造部打樣,2.測量室將送來的打樣產品進行測試,3.如果色差判定OK,則由IQC加貼ACC標簽.4.如果色差判定NG,則由IQC加貼REJ標簽.並對染色厂發出VCAR要求改善.制程生產色差管制:1.IPQC檢驗人員CHECK待生產的原料有無ACC標簽.2.有ACC標簽則允許生產,無ACC標簽,則貼HOLD問題標簽待處理.3.調機的首件產品作色差測試,如果符合要求才允許生產.4.生產部將不同生產批的產品分開送驗產品最終檢驗色差管制:1.生產部送成品至待驗區,2.品管人員以規定抽樣,並至少作3PCS產品的色差測試.3.品管人員保証抽驗的產品是同一生產批.倉儲產品色差管制:1.倉庫對不同生產批次的產品要分區放置.2.產品的儲存時間超過3個月,要進行檢驗;如果色差不符合要求,則以不良品處理.成品出貨色差管制:1.對于同一生產批的材料,品管對出貨產品進行抽樣檢驗,色差符合標准出貨.2.對于不同生產批的材料,品管對出貨產品進行抽樣檢驗,要求色差一致,且符合標准才可出貨.附件:<<色差管制計划>>核准:審核:制定:。
- 1、下载文档前请自行甄别文档内容的完整性,平台不提供额外的编辑、内容补充、找答案等附加服务。
- 2、"仅部分预览"的文档,不可在线预览部分如存在完整性等问题,可反馈申请退款(可完整预览的文档不适用该条件!)。
- 3、如文档侵犯您的权益,请联系客服反馈,我们会尽快为您处理(人工客服工作时间:9:00-18:30)。
L
68.1 68.23 -0.18 -5.18
a
-0.3 -0.5 0.74 -1.26
b
-1.8 -1.87 1.05 -0.95
L
43.6 43.73 2.03 -3.97
a
-0.3 -0.51 0.58 -1.42
b
-1.5 -1.54 0.88 -1.12
103.9 103.72 -0.86 -5.86
丰田三厂涂装色差管理品管基准(2013-1-16)
颜 色
L
丰田承认板(绝对值)
25 a
-0.8 -0.82 0.87 -1.13
b
1.7 1.97 0.91 -1.09
L
92.1 92.07 1.13 -1.87
45 a
-0.9 -0.84 0.87 -1.13
b
1.7 1.87 1.01 -0.99
a
43.6 43.67 1.34 -0.66
b
28 28.21 0.07 -1.93
L
17.3 17.29 0.78 -2.22
a
37.4 37.37 0.97 -1.03
b
23.8 23.86 -0.17 -2.17
29.8 30.05 2.18 -0.82
3R3
色差计中基准(绝对值) 基准上限 基准下限
L
84.6 84.17 1.17 -1.83
75 a
-0.8 -0.76 0.88 -1.12
b
1.4 1.5 1.1 -0.9
92.6 92.63 1.01 -1.99
040
色差计中基准(绝对值) 基准上限 基准下限
L
丰田承认板(绝对值)
a
-0.7 -0.65 1.06 -0.94
b
-0.5 0.37 0.52 -1.48
L
丰田承认板(绝对值)
a
-1.2 -1.24 1.04 -0.96
b
-2.8 -2.59 1.24 -0.76
L
19.9 20.55 1.95 -1.05
a
-0.5 -0.49 0.99 -1.01
b
-2.4 -2.57 0.67 -0.83
L
8 8.52 1.58 -1.42
a
0 -0.13 1.63 -0.87
1F7
色差计中基准(绝对值) 基准上限 基准下限
L
丰田承认板(绝对值)
a
-1.4 -1.34 0.95 -1.05
b
-1.8 -1.66 1.05 -0.95
L
4.3 4.39 1.48 -1.52aΒιβλιοθήκη -0.5 -0.46 1 -1
b
-1 -1.03 1.02 -0.98
L
1.6 1.63 1.78 -1.22
b
-11.8 -11.97 1.61 -0.39
L
2.1 1.93 1.88 -1.12
a
1 0.84 0.68 -1.32
b
-3.9 -3.82 0.92 -1.08
10.7 10.74 2.14 -0.86
8S6
色差计中基准(绝对值) 基准上限 基准下限
a
-0.1 -0.11 0.9 -1.1
b
-0.3 -0.3 1.06 -0.94
12.7 12.78 0.27 -2.73
209
色差计中基准(绝对值) 基准上限 基准下限
L
丰田承认板(绝对值)
a
51.9 52.05 0.96 -1.04
b
28.2 28.88 1.01 -0.99
L
22.8 22.97 1.03 -1.97
b
-1.3 -1.59 0.79 -0.71
40.2 42.08 0.92 -2.08
1G3
色差计中基准(绝对值) 基准上限 基准下限
L
丰田承认板(绝对值)
a
-0.1 -0.15 0.49 -1.51
b
-23.7 -23.7 2.84 0.84
L
4.1 4.01 1.86 -1.14
a
1.1 1.04 0.55 -1.45
L
丰田承认板(绝对值)
a
17.15 1 -1
b
22.15 1 -1
L
13.36 1.50 -1.50
a
11.06 1 -1
b
12.47 1 -1
L
6.11 1.50 -1.50
a
5.44 1 -1
b
4.37 1 -1
无 24.66 1.50 -1.50
4U3
色差计中基准(绝对值) 基准上限 基准下限