汽车部件品质外观检验规范DOC.doc
汽车零部件检验标准

汽车零部件检验标准1. 引言本文档旨在制定适用于汽车零部件检验的标准。
汽车零部件检验是为了保证零部件的质量和性能,以保障整车的安全和可靠性。
本标准适用于所有汽车制造商以及其供应商。
标准制定的目的是提供一个统一的检验标准,确保汽车零部件的合格率和质量稳定性。
2. 术语和定义- 零部件:指汽车制造中的各种独立组件。
- 检验:通过对零部件进行检测、测量和评价,验证其是否满足要求。
- 合格:指零部件在检验中符合相应标准并具备所规定的性能和质量要求。
3. 检验内容3.1 外观检验- 检验零部件外观是否完整,表面是否有破损、划痕、变形等。
- 检验零部件表面的涂装是否均匀、光滑。
- 检验零部件各个接口的装配是否正常。
3.2 尺寸检验- 检验零部件的尺寸是否符合设计要求。
- 检验零部件不同部位的尺寸是否一致。
- 检验零部件的几何形状是否符合规定。
3.3 性能检验- 检验零部件在正常工作条件下的性能是否满足要求。
- 检验零部件在极端环境条件下的性能是否稳定。
- 检验零部件的耐久性、可靠性和安全性。
3.4 材料检验- 检验零部件所使用的材料是否符合相关标准。
- 检验材料的物理力学性质是否符合要求。
4. 检验方法4.1 目测检验- 使用肉眼对零部件的外观进行检查。
- 对零部件的装配进行观察和检验。
4.2 量测检验- 使用测量工具对零部件的尺寸进行测量。
- 对测量结果进行记录和分析。
4.3 功能测试- 将零部件放入相应设备中进行正常工作条件下的功能测试。
- 运行测试结果进行记录和评估。
4.4 实验检验- 使用实验设备对零部件的材料性质进行测试。
- 对测试结果进行分析和评估。
5. 检验结论- 根据检验结果,对零部件做出合格或不合格的判断。
- 对不合格的零部件进行详细记录,并提出改进建议。
6. 监督和管理- 检验过程应有专门的人员进行监督和管理。
- 定期对检验工具和设备进行检修和校准。
- 根据不同类型的零部件制定相应的检验计划。
零部件检验规范

零部件检验规范
1.目的:
1.1规范检验过程,使检验时做到有据可依;
1.2确保所有零件在入库前都是检验合格品,符合标准和采购使用要求的.
2.适用范围
本规范适用于本公司产品的所有零部件.分为全检项与抽检项
全检项:所有的非标零部件
抽检项:采购的批量标准件或批量生产的零件,按20%的比例抽样
3.职责
3.1品管部负责所有相关检验过程,发现不良品,不接受不良品,不流转不良品,并记录相
关数据并向生产部门及采购部门反馈问题,统计和分析不良原因并跟踪改善.
4.检验依据
4.1检验项目依据公司审核图纸中的尺寸及技术要求
4.2依据GB控制自由公差要求
5.检验过程
5.1图纸中重要尺寸的确定
5.2确认零件是否加工完成,达到图纸要求的几何形状
5.3检验过程中发现超差,检验员在不确定的情况下,可向组长反映情况,由技术部来判定,
按不合格品控制程序来处理
6.检验项目:
检具上大致由底板,型面,定位,铝柱,铝板标准件,车磨件销子,仓库备用标准件夹钳,基
准块,球头手柄,弹簧等
底板检验规范
型面检验规范
定位角检验规范。
(全方位)汽车零部件进货检验验收规范

(全方位)汽车零部件进货检验验收规范全方位汽车零部件进货检验验收规范1. 目的本文档旨在规范汽车零部件的进货检验验收流程,确保零部件的质量符合要求,以提高汽车整车的质量和可靠性。
2. 适用范围本规范适用于所有进货的汽车零部件,包括但不限于发动机、制动系统、转向系统、底盘系统等。
3. 检验验收流程3.1 进货前准备在进货前,采购部门应与供应商确认以下事项:- 零部件的规格、型号和数量是否与采购合同一致;- 零部件的质量标准和技术要求是否符合公司的要求。
3.2 进货检验进货检验是确保进货零部件质量的关键步骤,具体流程如下:1. 检查零部件外观是否完好,无明显损坏或瑕疵;2. 根据质量标准和技术要求,对零部件的尺寸、重量、材料等进行检测;3. 对关键部件进行功能性测试,确保其正常工作;4. 检查零部件的标识和包装是否完好;5. 针对特殊要求的零部件,进行必要的特殊检验。
3.3 验收判定根据进货检验结果,对零部件进行验收判定,判定结果如下:- 合格品:零部件符合质量标准和技术要求,可以进入下一步的使用或存放;- 不合格品:零部件未能满足质量标准和技术要求,应立即与供应商联系进行退货或替换。
4. 质量记录对每批进货的零部件,应及时记录以下内容:- 零部件的名称、规格、型号和数量;- 进货日期和供应商信息;- 进货检验结果和验收判定结果。
5. 质量问题处理如果发现进货的零部件存在质量问题,应立即采取以下措施:1. 停止使用或安装该零部件;2. 通知供应商,并要求其解决问题;3. 对已使用或安装的零部件进行追溯和处理,确保不会对整车质量和安全造成影响;4. 针对质量问题进行分析和改进,以防止类似问题再次发生。
6. 监督和改进为确保持续改进零部件的质量,应建立监督机制,并定期评估和改进进货检验验收流程。
以上是全方位汽车零部件进货检验验收规范的内容,希望能够对公司的进货质量管理提供指导和参考。
根据具体情况,可以进行适当调整和补充。
汽车产品pcba外观检验标准

汽车产品pcba外观检验标准汽车产品的PCBA外观检验标准是确保汽车电子产品的质量和外观一致性的重要措施。
下面是一些可以参考的汽车产品PCBA外观检验标准的相关内容。
1. 印刷线路板(PCB)外观检查:- 确保PCB表面平整,无明显凹陷、划痕或凸起。
- 检查PCB表面覆盖层是否均匀、光滑,无气泡、裂纹或色差。
- 检查焊盘、焊道和导线是否均匀、紧密,无焊锡溢出或未焊接或开焊现象。
2. 元件安装质量检查:- 检查元件的容器是否完好无损。
- 检查元件是否正确安装在PCB上,无偏移或错位。
- 检查元件引脚是否焊接牢固,无明显焊锡溢出或多余焊锡。
3. 焊接质量检查:- 检查焊接是否均匀、光滑,无焊锡球、焊锡桥或冷焊等质量问题。
- 检查焊锡是否具有良好的锡峰形态,并且与元件引脚完全覆盖。
- 检查焊接是否完全,无漏焊或开焊现象。
4. 焊盘质量检查:- 检查焊盘是否平整,无明显凹陷或外形变形。
- 检查焊盘表面质量是否均匀,无刮痕、氧化或其他污染。
5. 标识和标志检查:- 检查PCBA上的标识和标志是否清晰可辨,无模糊、破损或不规范的情况。
- 检查标识和标志的位置是否准确,与相关元件、线路或功能相符合。
6. 清洁度检查:- 检查PCBA表面是否清洁,无灰尘、污渍或其他杂质。
- 检查PCBA表面是否有必要的防尘罩或其他保护措施。
这些参考内容可以作为汽车产品的PCBA外观检验标准的基础。
具体的标准可以根据不同的汽车电子产品和制造要求进行定制。
在实际的制造过程中,还需要根据关键性元件和组件的特殊要求,以及PCBA的特定规范和技术文件进行相关的检验和检查。
汽车零部件外观品质检验规范
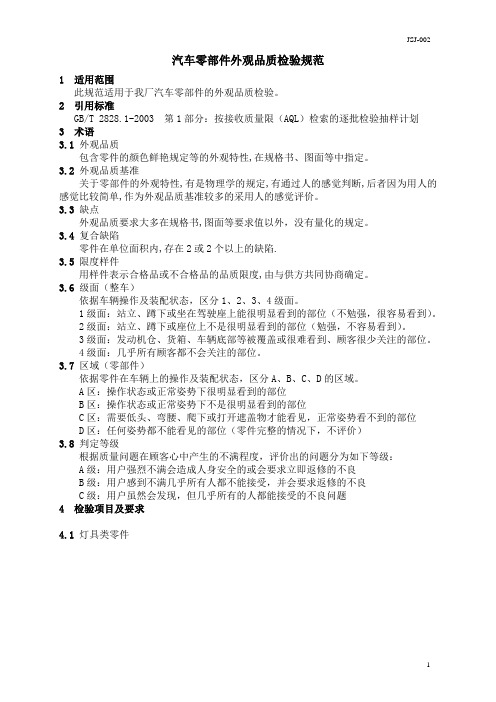
汽车零部件外观品质检验规范1 适用范围此规范适用于我厂汽车零部件的外观品质检验。
2 引用标准GB/T 2828.1-2003 第1部分:按接收质量限(AQL)检索的逐批检验抽样计划3 术语3.1 外观品质包含零件的颜色鲜艳规定等的外观特性,在规格书、图面等中指定。
3.2外观品质基准关于零部件的外观特性,有是物理学的规定,有通过人的感觉判断,后者因为用人的感觉比较简单,作为外观品质基准较多的采用人的感觉评价。
3.3缺点外观品质要求大多在规格书,图面等要求值以外,没有量化的规定。
3.4复合缺陷零件在单位面积内,存在2或2个以上的缺陷.3.5限度样件用样件表示合格品或不合格品的品质限度,由与供方共同协商确定。
3.6级面(整车)依据车辆操作及装配状态,区分1、2、3、4级面。
1级面:站立、蹲下或坐在驾驶座上能很明显看到的部位(不勉强,很容易看到)。
2级面:站立、蹲下或座位上不是很明显看到的部位(勉强,不容易看到)。
3级面:发动机仓、货箱、车辆底部等被覆盖或很难看到、顾客很少关注的部位。
4级面:几乎所有顾客都不会关注的部位。
3.7区域(零部件)依据零件在车辆上的操作及装配状态,区分A、B、C、D的区域。
A区:操作状态或正常姿势下很明显看到的部位B区:操作状态或正常姿势下不是很明显看到的部位C区:需要低头、弯腰、爬下或打开遮盖物才能看见,正常姿势看不到的部位D区:任何姿势都不能看见的部位(零件完整的情况下,不评价)3.8判定等级根据质量问题在顾客心中产生的不满程度,评价出的问题分为如下等级:A级:用户强烈不满会造成人身安全的或会要求立即返修的不良B级:用户感到不满几乎所有人都不能接受,并会要求返修的不良C级:用户虽然会发现,但几乎所有的人都能接受的不良问题4 检验项目及要求4.1灯具类零件4.2 电镀类零件4.3 全车玻璃级面:全车玻璃整车属一级面、零件属A区域部位代号:“①”:前挡玻璃中央部位“②”:前挡玻璃周围部及其它玻璃区域图:品质要求项目品质要求值A区域B区域C区域前期处理流痕W5.0㎜L10.0㎜以内W8.0㎜L15.0㎜以内台阶状变形0.5㎜以下(密封面0.2㎜以下)0.8㎜以下(密封面0.2㎜以下)缩孔0.5㎜×15.0㎜以下0.8㎜×20.0㎜以下留下出入口0.5㎜×15.0㎜以下0.5㎜×15.0㎜以下表面处理积压W3.0㎜ L30.0㎜以下可有划伤10.0㎜以下15.0mm以下切入口W1.0㎜ L10.0㎜以下可有表面麻点Ø1.0㎜以下,[边(区域)1个以内距离300㎜以上2个以内]可有结合部位偏差分开长度2.0㎜以内分开长度2.0㎜以内分开长度 2.0㎜以内接合部位面差0.3㎜以下0.8㎜以下异物形状:无突起感200㎜×200㎜㎜范围内·ø0.5㎜以下不评价·ø0.6~1.7㎜3个以下·ø2.0㎜1个以下·ø2.0㎜以上不合格缺陷间距离:20㎜以上形状:无突起感尺寸测量参照供应商提供的检查报告书进行测量验证,测量关键及安装尺寸,段面尺寸提供10倍图性能要求参照供应商提供定期性能试验报告4.5全车门饰板4.6 车内饰板杂物(涂装)φ0.5mm以下1个以内φ1.0mm以下2个以内尺寸测量参照供应商提供的检查报告书进行测量验证,测量关键及安装尺寸性能要求参照供应商提供定期性能试验报告4.7 车内顶蓬品质要求项目品质要求值适用B区C区合成橡胶毛线针织不织布凸凹直径30㎜以下凸凹高度0.5㎜以下○皱纹(L)15㎜×(W)1㎜以内500㎜×500㎜范围允许一个○○划伤(L)15㎜×(W)1㎜以内(L)25㎜×(W)1㎜以内○500㎜×500㎜范围允许一个异物混入(黑点) 直径1㎜以内500×500㎜内1个○毛边依照限度样本依照限度样本○○脏污直径5㎜以内直径8㎜以内○○500㎜×500㎜范围允许一个尺寸测量参照供应商提供的检查报告书进行测量验证,测量关键及安装尺寸性能要求参照供应商提供定期性能试验报告区域定义A 通常的乘车状态下看见的部位,通常的操作下接触频度频繁的部位B 通常的乘车状态下难以见到的部位.开闭等操作时能见部位.偶尔可能接触的部位C 零件重叠,难以看见的部位品质要求项目品质要求值A区域B区域C区域线头露出长度限20㎜以内,数量限2个,缺陷间的距离150㎜以上长度限80㎜以内,数量限4个,缺陷间的距离150㎜以上未规定表面异物、杂点直径0.3㎜以下,限3个,各缺陷间隔100㎜以上直径0.8㎜以下,限5个,各缺陷间隔100㎜以上未规定褶皱存在较大的褶皱(依照限度样本)存在大的褶皱(依照限度样本)未规定塑料包装不允许有撕裂现象尺寸测量参照供应商提供的检查报告书进行测量验证,测量关键及安装尺寸性能要求参照供应商提供定期性能试验报告座椅使用不良评价不良项目级别品质要求范围操作不良 A ·操作力非常沉重·靠背不能自动返回或返回非常慢·操作途中卡住·头枕操作力非常重或非常轻A4.9安全带4.10油管、水管、排气管4.11底盘类4.12电器类4.13 开关按钮类4.14密封圈、密封垫片类4.15油漆外观质量等级(包括塑料件、锻件和铸件等油漆外观质量)类JSJ-0025 验收标准和判定原则5.1在等级表中没有尺寸要求的缺陷项目均使用目测;5.2一般零部件采用B级精度,如果在检查过程中,如有一个或多个项目超出B级精度要求的零部件均判定为不合格;5.3 影响到零部件安全、性能的部位,其外观质量采用A级精度,其余部位按B级精度验收。
外观检验标准
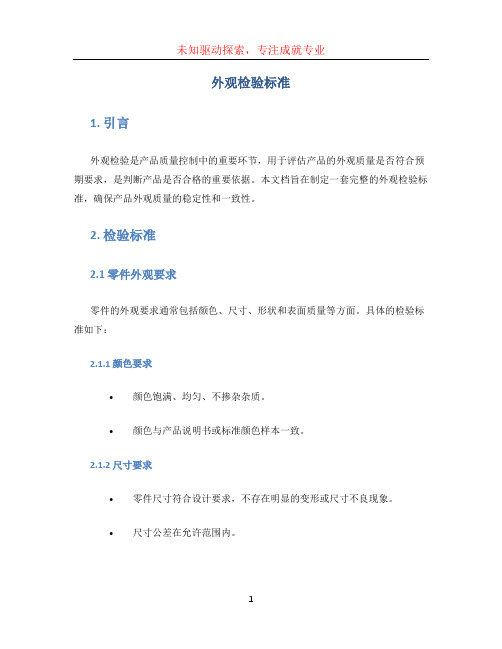
外观检验标准1. 引言外观检验是产品质量控制中的重要环节,用于评估产品的外观质量是否符合预期要求,是判断产品是否合格的重要依据。
本文档旨在制定一套完整的外观检验标准,确保产品外观质量的稳定性和一致性。
2. 检验标准2.1 零件外观要求零件的外观要求通常包括颜色、尺寸、形状和表面质量等方面。
具体的检验标准如下:2.1.1 颜色要求•颜色饱满、均匀、不掺杂杂质。
•颜色与产品说明书或标准颜色样本一致。
2.1.2 尺寸要求•零件尺寸符合设计要求,不存在明显的变形或尺寸不良现象。
•尺寸公差在允许范围内。
2.1.3 形状要求•零件形状无明显破损、变形、断裂等缺陷。
•检查零件边缘的锐利度和倒角是否符合要求。
2.1.4 表面质量要求•表面光滑、平整,无划痕和明显的凹凸。
•无明显的气泡、白点、斑点等缺陷。
2.2 成品外观要求成品外观的检验标准通常依据产品的用途和市场需求来确定。
2.2.1 外观一致性•各组件之间的外观一致性良好,形成整体感。
•产品不应有明显的色差或瑕疵。
2.2.2 标志和标识•产品的标志和标识清晰、完整可辨认。
•标志和标识的位置与规定一致。
2.2.3 表面处理和涂装•表面处理和涂装均匀、平整,无色差和脱落现象。
•涂层的厚度和粘附力符合要求。
3. 检验方法3.1 目视检查目视检查是最常用的检验方法之一,通过肉眼观察来评估产品的外观质量。
目视检查应该在光线充足的环境下进行,避免视觉误差。
3.2 触觉检查触觉检查可以用于评估产品的表面质量。
通过手感来判断产品的光滑度、凹凸等情况。
触觉检查需要注意产品不得有锋利和刺激性的边缘。
3.3 仪器检测仪器检测可以使用一些专业设备和工具,如显微镜、光谱仪、涂层测厚仪等,来进一步评估产品的外观质量。
仪器检测结果更加客观和精确。
4. 结论本文档制定了一套完整的外观检验标准,确保产品外观质量的稳定性和一致性。
在执行外观检验时,应根据具体产品的特点和市场需求,综合运用目视检查、触觉检查和仪器检测等方法,确保产品的外观质量符合要求。
汽车产品pcba外观检验标准

汽车产品pcba外观检验标准
汽车产品PCBA外观检验标准应包括以下方面:
1.外观整体:PCBA应呈现平整、光滑、干净的外观,不能有划痕、凹凸、灰尘等问题。
2.引脚排列:引脚排列应整齐、对称,不能存在错位、偏移等问题。
3.焊点质量:PCBA上的焊点应呈现导电性良好、焊接均匀、无异常缺陷(如裂纹、气孔、虚焊等)等情况。
4.标识清晰:PCBA上的标识(如组件名、编号、生产日期等)应清晰、规范,不能存在漏打、损坏等问题。
5.器件尺寸:各类器件(如电容、电阻、芯片、插件等)的尺寸应符合相关规范,不能存在配合过紧或过松等问题。
6.器件摆放:各类器件的摆放应符合相关要求(如间距、平整度、过孔等),不能存在摆放偏斜、垂直度差等问题。
7.打样样品与设计图纸的一致性:PCBA打样样品应与设计图纸完全一致,无任何偏差或变形。
8.其它特殊要求:根据具体情况(如防爆、防水、耐高温等要求),可增加相关检验项。
总体来说,汽车产品PCBA的外观检验应全面细致,确保产品质量和安全性。
汽车零部件外观检验质量标准和规范标准

汽车零部件外观检验质量标准和规范标准
简介
本文档旨在提供汽车零部件外观检验的质量标准和规范标准,
以确保汽车零部件的质量和外观符合相关要求。
检验对象
所有进入生产线的汽车零部件都应进行外观检验,包括但不限
于以下方面:
- 表面平整度
- 颜色均匀度
- 尺寸和形状的准确性
- 表面缺陷和瑕疵
质量标准
为确保零部件的质量和外观符合要求,以下质量标准应被遵守:
1. 表面平整度:零部件表面应平整,不得有凹凸不平、麻点等
缺陷。
2. 颜色均匀度:零部件的颜色应均匀,不得有明显的色差。
3. 尺寸和形状的准确性:零部件的尺寸和形状应符合设计要求,不得有偏差超过规定范围。
4. 表面缺陷和瑕疵:零部件表面不得有划痕、气泡、氧化等缺陷,不得有明显的色差。
规范标准
为确保检验的一致性和可靠性,以下规范标准应被遵守:
1. 检验员资质:负责进行外观检验的检验员应具备相关的知识
和技能,并经过培训和认证。
2. 检验环境:外观检验应在干燥、清洁、光线充足的环境中进行,以确保有效的观察和判断。
3. 检验工具:使用适当的检验工具,如测量仪器、放大镜等,
以帮助进行准确的外观检验。
4. 检验记录:对每个零部件的外观检验结果进行记录,包括通
过与不通过的判定,并进行必要的数据分析。
总结
本文档提供了汽车零部件外观检验的质量标准和规范标准,以
确保零部件的质量和外观符合要求。
通过严格遵守这些标准,可以
提高汽车零部件的可靠性和合格率,以保障汽车的质量和安全。
车辆质量验收标准

车辆质量验收标准
引言
本文档为车辆质量验收标准,旨在确保通过有效的质量检查和验收程序,将合格的车辆交付给用户。
质量验收标准
车辆质量验收标准包括以下几个方面:
1. 外观检查
- 车身漆面应平整、无明显划痕和气泡。
- 镀铬件应完好,无锈蚀和掉漆现象。
- 玻璃应完整、清晰,无破损和龟裂。
2. 内饰检查
- 座椅应平整、舒适,无磨损和脱线现象。
- 仪表盘应完好,指示清晰,各功能开关正常。
- 空调系统应正常工作,温度调节准确。
3. 功能性检查
- 发动机应运转平稳,无异常噪音。
- 刹车系统应灵敏,无异常刹车距离。
- 转向系统应灵活,无异常抖动和失灵现象。
4. 安全性检查
- 车辆应符合相应的安全标准和法规要求。
- 安全带应完好,制动系统应正常。
- 车辆应配备应急工具和安全警示标志。
验收程序
车辆质量验收程序应包括以下步骤:
1. 车辆外观和内饰检查
- 检查车身漆面、镀铬件和玻璃状况。
- 检查座椅、仪表盘和空调系统功能。
2. 功能性检查
- 启动发动机,检查运转情况和噪音。
- 进行刹车和转向系统测试。
3. 安全性检查
- 检查车辆的安全性能和配备情况。
4. 记录和报告
- 对车辆检查结果进行记录和报告。
总结
车辆质量验收标准的执行,可以确保交付给用户的车辆质量合格、功能正常,并满足安全要求。
质量验收标准和验收程序的执行应严格执行,以确保车辆质量的可靠性和安全性。
谢谢!。
外观检验标准
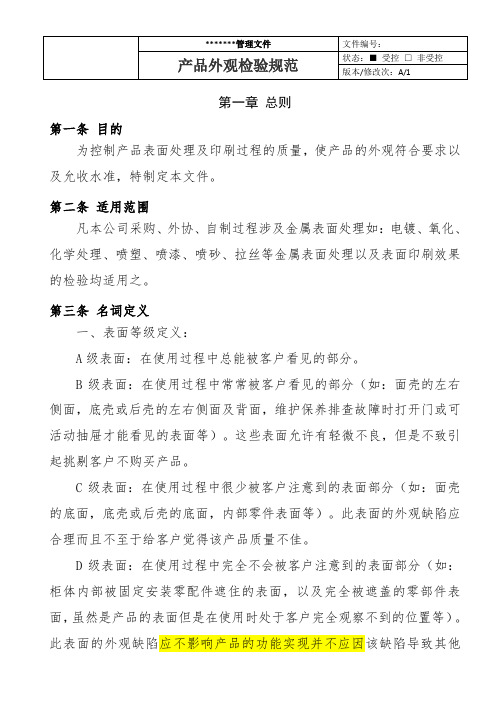
第一章总则第一条目的为控制产品表面处理及印刷过程的质量,使产品的外观符合要求以及允收水准,特制定本文件。
第二条适用范围凡本公司采购、外协、自制过程涉及金属表面处理如:电镀、氧化、化学处理、喷塑、喷漆、喷砂、拉丝等金属表面处理以及表面印刷效果的检验均适用之。
第三条名词定义一、表面等级定义:A级表面:在使用过程中总能被客户看见的部分。
B级表面:在使用过程中常常被客户看见的部分(如:面壳的左右侧面,底壳或后壳的左右侧面及背面,维护保养排查故障时打开门或可活动抽屉才能看见的表面等)。
这些表面允许有轻微不良,但是不致引起挑剔客户不购买产品。
C级表面:在使用过程中很少被客户注意到的表面部分(如:面壳的底面,底壳或后壳的底面,内部零件表面等)。
此表面的外观缺陷应合理而且不至于给客户觉得该产品质量不佳。
D级表面:在使用过程中完全不会被客户注意到的表面部分(如:柜体内部被固定安装零配件遮住的表面,以及完全被遮盖的零部件表面,虽然是产品的表面但是在使用时处于客户完全观察不到的位置等)。
此表面的外观缺陷应不影响产品的功能实现并不应因该缺陷导致其他慢性外观缺陷或功能缺陷(如:易锈蚀材料表面划伤涂层和底材导致后续生锈,电接触部分因裸露老化后导致接触不良等其他故障等)二、表面处理及其缺陷定义:金属表面:包括电镀、氧化、钝化等表现为金属质感的表面,非喷涂表面。
基材花斑:电抛光、电镀或氧化前因基体材料腐蚀、或者材料中的杂质、材料微孔等原因所造成的、与周围材质表面不同光泽或粗糙度的斑块状花纹外观。
抛光区:对基材上的腐蚀、划伤、焊接区、铆接区等部位进行机械打磨抛光后表现出的局部高光泽、光亮区域。
浅划痕:镀(膜/塑/漆)层表面划伤,但未伤及底层(即底层未暴露);对其它无镀(膜/塑/漆)层表面则为:目测不明显、手指甲触摸无凹凸感、未伤及材料本体的伤痕。
数控冲床加工中机床台面对板材的摩擦产生的轻微痕迹属于此类划痕。
深划痕:镀(膜/塑/漆)层表面划伤,且已伤至底层(即底层已暴露出来);对其它无镀(膜/塑/漆) 层表面则为:目测明显、手指甲触摸有凹凸感、伤及材料本体的伤痕。
汽车及配件的质量标准和检验方法
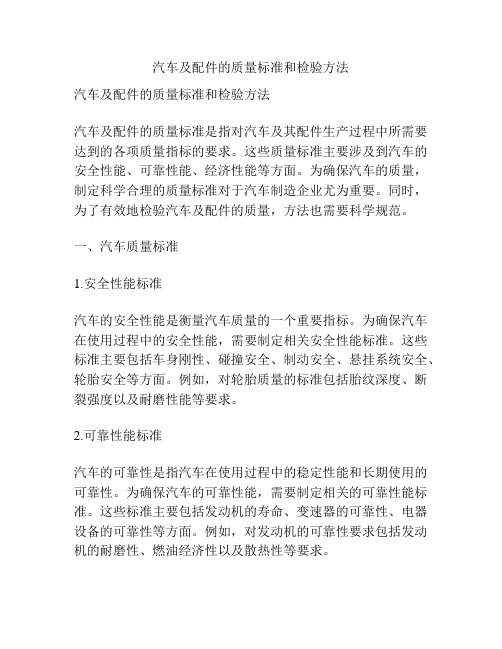
汽车及配件的质量标准和检验方法汽车及配件的质量标准和检验方法汽车及配件的质量标准是指对汽车及其配件生产过程中所需要达到的各项质量指标的要求。
这些质量标准主要涉及到汽车的安全性能、可靠性能、经济性能等方面。
为确保汽车的质量,制定科学合理的质量标准对于汽车制造企业尤为重要。
同时,为了有效地检验汽车及配件的质量,方法也需要科学规范。
一、汽车质量标准1.安全性能标准汽车的安全性能是衡量汽车质量的一个重要指标。
为确保汽车在使用过程中的安全性能,需要制定相关安全性能标准。
这些标准主要包括车身刚性、碰撞安全、制动安全、悬挂系统安全、轮胎安全等方面。
例如,对轮胎质量的标准包括胎纹深度、断裂强度以及耐磨性能等要求。
2.可靠性能标准汽车的可靠性是指汽车在使用过程中的稳定性能和长期使用的可靠性。
为确保汽车的可靠性能,需要制定相关的可靠性能标准。
这些标准主要包括发动机的寿命、变速器的可靠性、电器设备的可靠性等方面。
例如,对发动机的可靠性要求包括发动机的耐磨性、燃油经济性以及散热性等要求。
3.经济性能标准汽车的经济性是指汽车在运行过程中的能耗和运营成本。
为确保汽车的经济性能,需要制定相关的经济性能标准。
这些标准主要包括汽车的油耗、排放标准以及运行成本等方面。
例如,对汽车的油耗要求包括城市道路工况、高速公路工况等行驶工况下的油耗要求。
二、汽车配件质量标准1.材料质量标准汽车配件的材料质量直接影响汽车整体的质量。
为确保汽车配件材料的质量,需要制定相关的材料质量标准。
这些标准主要包括金属材料的硬度、抗拉强度、抗压强度等方面的要求。
同时,对非金属材料的质量标准也需要进行规定。
2.加工工艺标准汽车配件的加工工艺直接关系到配件的质量。
为确保汽车配件的加工质量,需要制定相关的加工工艺标准。
这些标准主要包括加工精度、表面光洁度、尺寸偏差等方面的要求。
三、汽车及配件质量检验方法1.外观检验外观检验是对汽车及配件外观进行检查,确认是否存在缺陷和不良品。
汽车行业汽车制造质量检测规程

汽车行业汽车制造质量检测规程随着全球汽车市场的持续发展,对汽车制造质量的要求也日益提高。
为了确保汽车在生产过程中符合相关标准,各个汽车制造商都制定了一系列的汽车制造质量检测规程。
本文将从整车检测、发动机检测、安全性能检测、环境保护检测以及质量管理等方面,对汽车行业的质量检测规程进行详细论述。
一、整车检测1. 车身外观检测车身外观检测主要包括车身漆面、贴膜、喷漆等方面的检测。
通过采用光线照射、人工目视和仪器测量等方法,对车身外观的光洁度、色差、涂层附着力等进行检测,确保汽车外观无明显缺陷。
2. 功能性检测功能性检测是对汽车各个系统的功能进行检验和验证,包括悬挂系统、制动系统、传动系统等方面。
通过测试和参数分析等方法,确保汽车各个系统的正常运行和协调配合。
二、发动机检测1. 排放检测排放检测是对发动机尾气中的有害物质进行监测和评估,包括废气排放、燃油消耗等方面。
通过使用尾气分析仪等设备,对发动机的排放性能进行检测,确保其符合环保要求。
2. 动力性能检测动力性能检测是对发动机的输出动力进行评估和检验,包括最大功率、最大扭矩等方面。
通过使用发动机试车台和动力性能测试仪等设备,对发动机的各项参数进行检测,确保其性能符合标准要求。
三、安全性能检测1. 碰撞安全性检测碰撞安全性检测是对汽车在碰撞事故中的安全性进行评估和验证,包括正面碰撞、侧面碰撞等方面。
通过使用碰撞试验台和高速摄像机等设备,对车辆在碰撞过程中的变形情况和安全性能进行检测,确保车辆在碰撞事故中能够提供有效的保护。
2. 制动安全性检测制动安全性检测是对汽车制动系统的性能进行检验和验证,包括制动力、制动距离等方面。
通过使用制动性能测试仪和刹车试验台等设备,对制动系统的响应时间、制动效果等进行检测,确保车辆在紧急情况下能够提供稳定和可靠的制动效果。
四、环境保护检测1. 噪音检测噪音检测是对汽车运行过程中产生的噪音进行评估和控制,包括车体噪音、发动机噪音等方面。
零部件外观检验标准

零部件外观检验标准TF/UIS8.2.4-04版本号:A/0零部件外观检验标准编制:审核:批准:2009-10-15 发布 2009-10-15实施北京汇影互联科技有限公司发布目录橡胶件外观检验作业指导 1-4 钣金件外观检验作业指导 5-7电器元件外观检验作业指导 8-9PCB板外观检验作业指导 10-11电线外观检验作业指导 12-13五金件外观检验作业指导 14-15橡胶件外观检验作业指导 16-19北京汇影互联科技有限公司United Imaging Systems (Beijing) Co., Ltd.文件编号 TF/UIS8.2.4-04-01零件外观检验标准版本号 A/O生效日期年月日塑料件外观检验作业指导标题页次第页共页1、目的:掌握塑料进检验方法及标准,使塑料件外观来料更好地符合我公司的技术要求。
2、适用范围:适用于本公司对外购的所有涉及产品制造过程中使用的塑料件进籵检验。
本标准书与图纸要求相冲突时,均以图纸要求为准(无法用语言描述的缺陷,供需双方封样方法解决)。
3、塑料件的外表面应光滑平整,不得有发白、起泡、针孔、胀起、开裂、剥落、露底、流挂、积聚物、鱼磷状、碰伤、擦伤、污迹、变形、光泽不均匀等现象。
4、内容:4.1术语:1) 杂色:与本身颜色不同的杂点或混入胶料中的杂点暴露在表面上。
2) 流纹:胶料融合不佳形成条形纹路3) 缩水:由于射出压力低,使产品局部整体表面下陷。
4) 合模线:产品在成型过程中,上模和下模相闭合的线,目视及手感都有感觉。
5) 缺料:产品某个部位不饱满6) 白印:由于内应力,在产品表面产生与本色不同的白色痕迹。
7) 披锋:(毛刺)由于种种原因,产品非结构部分产生多余的料8) 封堵:应该穿透的地方由于披锋造成不通。
9) 断裂:塑料局部断开后的缺陷。
10) 拉毛:因摩擦而产生的细皮,附在注塑间表面的现象。
11) 油丝:油痕,加工原因,油污(脱模式剂)在产品表面留下的痕迹,使该部位发光并带有流动样。
汽车外检时的规章制度

汽车外检时的规章制度一、车辆外观检测1.车身外观检测(1)检查车身表面是否平整,是否有明显凹凸、破损等情况;(2)检查车身颜色是否整齐,是否有脱落或变色的现象;(3)检查车窗玻璃是否完好,是否有裂痕或破损;(4)检查车灯、雨刷器、挡泥板等外部配件是否安装牢固,正常运转。
2.车辆动力系统检测(1)检查车辆发动机盖是否关闭好,发动机是否有渗油、冒烟等异常情况;(2)检查排气管是否有漏气、冒烟情况;(3)检查制动系统是否灵敏、有效,制动灯是否正常亮起。
3.车轮及悬挂系统检测(1)检查轮胎花纹是否磨损均匀,气压是否符合标准;(2)检查轮毂是否有变形、裂纹等情况;(3)检查悬挂系统是否有异响、松动等异常情况。
4.车辆环保及安全装置检测(1)检查废气排放是否符合国家标准;(2)检查安全带是否完好,是否处于可正常使用状态;(3)检查灭火器、急救箱等安全装置是否齐全、有效。
二、车辆操作检测1.启动检测(1)检查启动系统是否正常,是否需要多次启动才能打着;(2)检查发动机启动后的怠速是否稳定。
2.行驶检测(1)检查车辆是否能够正常驶入车检设备,是否会有异响或顿挫感;(2)检查车辆行驶过程中是否有异响、抖动等异常情况。
3.转向检测(1)检查车辆转向灵活性,是否出现卡滞、漏油等情况;(2)检查方向盘是否存在不正常松动、抖动等情况。
4.制动检测(1)检查制动性能是否符合标准,制动距离是否正常;(2)检查车辆行驶过程中,制动系统是否有异常噪声或顿挫感。
5.起步和停车检测(1)检查车辆停车制动性能是否正常,制动是否有效;(2)检查车辆起步是否平稳,是否有发动机熄火、死火等情况。
通过上述规章制度的汽车外检,可以有效确保车辆在道路上行驶时的安全性和可靠性。
同时,也提醒车主们保养爱车、注意驾驶安全,共同建设安全、文明的道路交通环境。
汽车制造质量检验规范范文

汽车制造质量检验规范范文一、前言车辆制造质量对于用户的安全和使用体验至关重要。
为了确保汽车制造质量符合相关标准和要求,制定本汽车制造质量检验规范,以提供指导和参考。
二、检验标准1. 外观检验外观是消费者对汽车第一眼的印象,因此外观质量的检验至关重要。
对于整车外观零部件的检验,应严格按照相关标准,确保零部件没有划痕、凹陷、色差、裂纹等缺陷。
2. 内饰检验内饰是汽车的重要组成部分,对用户的乘坐舒适度和使用体验有直接影响。
内饰零部件的检验应包括座椅、仪表板、中控台等,确保其装配质量和材料质量合格。
座椅应舒适稳固,仪表板和中控台应牢固、无裂纹,并符合设计要求。
3. 功能检验汽车作为交通工具,各项功能的正常运行是关键。
包括发动机、悬挂系统、制动系统、灯光系统等各个方面的功能检验,确保其满足相关标准和要求。
例如,发动机应正常启动、运转平稳;制动系统应灵敏可靠;灯光系统应亮度均匀、符合规定。
4. 安全检验安全是汽车制造质量的核心要素之一。
检验应包括车辆的被动安全和主动安全方面。
被动安全指在事故发生时,车辆能够提供合理的保护,如车身结构强度、气囊系统等;主动安全指车辆的各项辅助系统是否正常运行,如防抱死刹车系统、电子稳定控制系统等。
三、检验方法1. 外观检验方法外观检验应在光线充足的环境下进行,使用视觉观察和触摸的方式。
检验人员需要认真检查零部件的表面是否平整、有无瑕疵,按照要求进行验收。
2. 内饰检验方法内饰检验可以通过目视观察和手动操作来进行。
检验人员应仔细观察内饰零部件的装配情况和材料质量,并检查其是否牢固、无异味等。
3. 功能检验方法功能检验需要仪器设备的辅助进行,例如使用发动机检测仪检测发动机性能,使用刹车测试设备检测制动系统性能等。
检验人员应熟悉相关设备的操作和检验方法,确保检验结果准确可靠。
4. 安全检验方法安全检验应参照相关标准和规程,使用专业检测设备进行。
例如,使用碰撞试验设备测试车身结构强度,使用碰撞测试仪进行气囊系统的检验等。
- 1、下载文档前请自行甄别文档内容的完整性,平台不提供额外的编辑、内容补充、找答案等附加服务。
- 2、"仅部分预览"的文档,不可在线预览部分如存在完整性等问题,可反馈申请退款(可完整预览的文档不适用该条件!)。
- 3、如文档侵犯您的权益,请联系客服反馈,我们会尽快为您处理(人工客服工作时间:9:00-18:30)。
JSJ-002汽车部件品质外观检验规范1适用范围此规范适用于我厂汽车零部件的外观品质检验。
2引用标准GB/T 2828.1-2003 第 1 部分:按接收质量限( AQL)检索的逐批检验抽样计划3术语3.1外观品质包含零件的颜色鲜艳规定等的外观特性, 在规格书、图面等中指定。
3.2外观品质基准关于零部件的外观特性 , 有是物理学的规定 , 有通过人的感觉判断 , 后者因为用人的感觉比较简单 , 作为外观品质基准较多的采用人的感觉评价。
3.3缺点外观品质要求大多在规格书, 图面等要求值以外,没有量化的规定。
3.4复合缺陷零件在单位面积内 , 存在 2 或 2 个以上的缺陷 .3.5限度样件用样件表示合格品或不合格品的品质限度, 由与供方共同协商确定。
3.6级面(整车)依据车辆操作及装配状态,区分1、2、3、4 级面。
1 级面:站立、蹲下或坐在驾驶座上能很明显看到的部位(不勉强,很容易看到)。
2 级面:站立、蹲下或座位上不是很明显看到的部位(勉强,不容易看到)。
3级面:发动机仓、货箱、车辆底部等被覆盖或很难看到、顾客很少关注的部位。
4级面:几乎所有顾客都不会关注的部位。
3.7区域(零部件)依据零件在车辆上的操作及装配状态,区分A、B、C、D 的区域。
A区:操作状态或正常姿势下很明显看到的部位B区:操作状态或正常姿势下不是很明显看到的部位C区:需要低头、弯腰、爬下或打开遮盖物才能看见,正常姿势看不到的部位D区:任何姿势都不能看见的部位(零件完整的情况下,不评价)3.8判定等级根据质量问题在顾客心中产生的不满程度,评价出的问题分为如下等级:A级:用户强烈不满会造成人身安全的或会要求立即返修的不良B级:用户感到不满几乎所有人都不能接受,并会要求返修的不良C级:用户虽然会发现,但几乎所有的人都能接受的不良问题4检验项目及要求4.1灯具类零件1JSJ-002 部位品质要求项目品质要求范围30×30mm范围以内的缺陷数气泡电镀麻点反光镜配光镜线痕灯罩(一级面)伤痕电镀面其它外观要求尺寸测量组合灯总成∮1.5mm以上不合格∮1.0~ ∮ 1.5mm允许 1 个∮1.0mm以下允许 4 个∮0.5mm以下不评价50×100 范围内只允许 1 个W0.5 ㎜ L2.4 ㎜以下宽度< 1mm,长度> 13mm A级长度>5~13mm B级宽度> 1mm,长度> 7mm A 级长度>3~7mm B级相互连接的伤痕要将其总数值作为尺寸大小。
参照本标准“ 2、电镀类标准”无破损开裂、缺料、断裂、电镀层脱落、错漏装、密封胶外溢、毛刺划手等不良。
参照供应商提供的检查报告书进行测量验证,测量关键及安装尺寸性能要求参照供应商提供定期性能试验报告注:个别判定基准存在异议时,参照样件、标准车件、整车检查标准判定4.2 电镀类零件品质要求品质要求值A 区B 区C 区·φ 1.5mm以内·φ2mm以内( 100mm鼓起(300mm以上间距限 2 ——以上间距 5 个以内)个)·φ 2.5mm 以内允许 2 ·φ2.5mm以内允许 5凹陷个个(间距在 100mm以——(间距在 300mm以上)上)2JSJ-002 划痕·7mm以下 1 个以内· 15mm以下 1 个以内——变形侧面向光看不明显可接侧面向光看明显——受正面不明显可接受颜色不匀·依据限度样本·依据限度样本——厚度不匀·依据限度样本·依据限度样本——电镀脱落不允许不明显无明显脱落残留物其它外观无破损开裂、缺料、断裂等不良要求尺寸测量参照供应商提供的检查报告书进行测量验证,测量关键及安装尺寸性能要求参照供应商提供定期性能试验报告注:个别判定基准存在异议时,参照样件、标准车件、整车检查标准判定4.3全车玻璃级面:全车玻璃整车属一级面、零件属 A 区域部位代号:“①”:前挡玻璃中央部位“②”:前挡玻璃周围部及其它玻璃品质要求项目品质要求值线痕的长度长度超过 7.0 ㎜不合格·重痕“①”线痕“②”长度超过 15.0 ㎜不合格·中痕“①”长度超过 15.0 ㎜不合格“②”长度超过 30.0 ㎜不合格划伤(指甲能感·长度超过 3.0mm不合格(注:宽度大于 0.5mm 时,觉到)长度× 2 计算)擦伤(指甲感觉长度超过 25.0mm不合格一不到)气泡大小般玻·“①”,含变形的部分超过 2.0 ㎜不合格,气泡大小璃气泡0.6 ㎜以下·“②”,含变形的部分超过 3.0 ㎜不合格,气泡大小0.8 ㎜以下夹层面内的异物尺寸·“①”超过∮ 1.0 ㎜不合格异物·“②”超过∮ 2.5 ㎜不合格单层玻璃的异物·“①”含变形的部分超过∮ 1.0 ㎜不合格·“②”含变形的部分超过∮ 1.5 ㎜不合格裂纹、爆边·“①”超过 1.0 ㎜不合格·“②”超过 1.5 ㎜不合格3缺陷的分布黑点,杂点玻璃变形覆漏光盖玻璃( 遮异物光)尺寸测量性能要求JSJ-002 缺陷的个数·“①” φ 300 ㎜的圆内 3 个以内,但重痕 5.0 ~7.0 ㎜ 1个以内·“②” 150 ㎜× 150 ㎜内 5 个以内,但重痕 10.0 ~15.0 ㎜ 1 个以内φ300 ㎜圆内的缺陷:·φ0.5 ㎜以下 5·φ0.3 ㎜以下不评价个以下·φ1.0 ㎜以上不·φ1.0 ㎜以下 1 个以下合格缺陷间的距离 20 ㎜以上离玻璃 1-3 米,从玻璃正面及侧面进行评价·透过玻璃物体失真严重A级·透过玻璃物体有一些失真B级·透过玻璃物体略有失真C级(可接受)200 ㎜× 200 ㎜内缺陷个数 , 最大一个 , 但是㎜ 1个以·φ0.2 ㎜以下不评价·φ0.3下·φ 0.4 ㎜以上不合格长度 200 ㎜的范围内缺陷的个数 , 最大 5 个, 但·φ0.4 ㎜以下 5 个以下·φ0.8 ㎜以下 2个以下·φ1.2 ㎜ 1 个以下·φ1.3 ㎜以上不合格缺陷间的距离 20 ㎜以上参照供应商提供的检查报告书进行测量验证,测量关键及安装尺寸参照供应商提供定期性能试验报告注:个别判定基准存在异议时,参照样件、标准车件、整车检查标准判定4.4全车胶条区域图:4JSJ-002品质要求项目品质要求值A 区域B 区域C 区域前期处理流痕W5.0㎜ L10.0 ㎜以内W8.0 ㎜ L15.0 ㎜以内台阶状变形0.5 ㎜以下 ( 密封面 0.2 0.8 ㎜以下 ( 密封面 0.2 ㎜以下 ) ㎜以下 )缩孔0.5 ㎜× 15.0 ㎜以下0.8 ㎜× 20.0 ㎜以下留下出入口0.5 ㎜× 15.0 ㎜以下0.5 ㎜× 15.0 ㎜以下表面处理积压W3.0㎜ L30.0 ㎜以下可有划伤10.0 ㎜以下15.0mm以下切入口W1.0㎜ L10.0 ㎜以下可有?1.0 ㎜以下,[ 边( 区表面麻点域 )1 个以内可有距离 300 ㎜以上 2 个以内 ]结合部位偏差分开长度 2.0 ㎜以内分开长度 2.0 ㎜以内分开长度 2.0 ㎜以内接合部位面差0.3 ㎜以下0.8 ㎜以下形状:无突起感200 ㎜× 200 ㎜㎜范围内·?0.5 ㎜以下不评价异物·?0.6~1.7 ㎜ 3 个以下形状:无突起感·?2.0 ㎜ 1 个以下·?2.0 ㎜以上不合格缺陷间距离: 20 ㎜以上尺寸测量参照供应商提供的检查报告书进行测量验证,测量关键及安装尺寸,段面尺寸提供10 倍图性能要求参照供应商提供定期性能试验报告4.5全车门饰板5品质要求品质要求值项目A 区B 区C区表面凸φ 2.0mm以下 1 个以内φ2.0mm以下 1 个以内φ 5.0mm 以下 1 ( 但是间距 300mm以上 2( 但是间距 300mm以上 2 个以内 ) 个以内个以内 )表面凹 1φ 3.0mm以下 1 个以内φ3.0mm以下 1 个以内φ 5.0mm 以下 1(成型面)( 但是间距 300mm以上允个以内许有 2个)表面凹 2 参照限度样件(垫块)沫塑料热不允许裂线痕长度 3.0mm 以下1 个以内擦痕长度 3.0mm 以下3 个以内无白色化气泡φ 1.0mm以下 1 个以内( 但是间距 300mm以上 2个以内 )异物φ 2.0mm以下 1 个以内偏色30×50mm以下 1 个以内脱色φ 1.0mm以下 1 个以内( 但是间距 300mm以上 2 个以内 )亮斑50×50mm以下 2 个以内泡沫斑30×20mm以下 1 个以内( 但是仅限周边部分 )参照限度样件不允许长度 5.0mm 以下1个以内长度 5.0mm 以下3个以内无白色化φ2.0mm以下 1 个以内( 但是间距300mm以上2个以内 )φ4.0mm以下 1 个以内100×50mm以下 1 个以内φ2.0mm以下 1 个以内( 但是间距300mm以上2 个以内 )30×20mm以下 1 个以内参照限度样件不允许线痕擦痕φ5.0mm 以下 3个以内尺寸测量参照供应商提供的检查报告书进行测量验证,测量关键及安装尺寸性能要求参照供应商提供定期性能试验报告64.6车内饰板品质要求项目划伤(指甲能感觉到)擦伤(指甲感觉不到)表面凸表面凹气泡白化毛刺缺料缩水痕线痕杂物(涂装)尺寸测量性能要求品质要求值A 区域B 区域C区域无泛白无泛白无泛白长度 :2 ㎜以下长度 :2 ㎜以下长度 :2 ㎜以下数量 :1 个数量 :1 个数量 :2 个以内长度 :5 ㎜以下长度 :8 ㎜以下数量 :3 个以内数量 :4 个以内φ2.0mm以下 1 个以φ2.0mm 以下 1 个以内内φ5.0mm以下( 但是间距 300mm以上( 但是间距 300mm以上2 1 个以内2个以内) 个以内 )φ3.0mm 以下 1 个以φ 3.0mm以下 1 个以内φ5.0mm以下内( 但是间距 300mm以上 1 个以内允许有 2 个)大小 : φ1.0 ㎜以下大小 : φ 1.0 ㎜以下数量 :2 个以内数量 :2 个以内间距 :300 ㎜以上间距 :50 ㎜以上长度 :2 ㎜以下长度 :4 ㎜以下数量 :1 个数量 :3 个以内(安装受力部位不允(安装受力部位不允许)许)无刮手的毛刺长度 :2 ㎜以下无刮手的毛刺数量 :3 个以下不允许不允许不允许正面看不明显长度 3.0mm 以下长度 5.0mm 以下1 个以内 1 个以内φ 0.5mm以下φ1.0mm以下1 个以内2 个以内参照供应商提供的检查报告书进行测量验证,测量关键及安装尺寸参照供应商提供定期性能试验报告7JSJ-002 4.7车内顶蓬品质要求值适用品质要求项目B 区C区合成橡毛线针不织布胶织凸凹直径 30 ㎜以下○凸凹高度 0.5 ㎜以下(L)15 ㎜× (W)1 ㎜以皱纹内 500 ㎜× 500 ㎜范○○围允许一个(L)15 ㎜× (W)1 ㎜以(L)25 ㎜×划伤内(W)1 ㎜以内○500㎜× 500 ㎜范围允许一个异物混入直径 1 ㎜以内○( 黑点) 500× 500 ㎜内 1 个毛边依照限度样本依照限度样本○○直径 5 ㎜以内直径 8 ㎜以内脏污○○500㎜× 500 ㎜范围允许一个尺寸测量参照供应商提供的检查报告书进行测量验证,测量关键及安装尺寸性能要求参照供应商提供定期性能试验报告4.8车内座椅区域定义A通常的乘车状态下看见的部位 , 通常的操作下接触频度频繁的部位B通常的乘车状态下难以见到的部位 . 开闭等操作时能见部位 . 偶尔可能接触的部位C零件重叠 , 难以看见的部位8JSJ-002 A品质要求项目品质要求值A 区域B 区域C区域长度限 20 ㎜以内,数量限长度限 80 ㎜以内,数量限线头露出 2 个,缺陷间的距离 150 4 个,缺陷间的距离 150 未规定㎜以上㎜以上表面异物、杂直径 0.3 ㎜以下,限 3 个,直径 0.8 ㎜以下,限 5 个,未规定点各缺陷间隔 100 ㎜以上各缺陷间隔 100 ㎜以上褶皱存在较大的褶皱(依照限存在大的褶皱(依照限度未规定度样本)样本)塑料包装不允许有撕裂现象尺寸测量参照供应商提供的检查报告书进行测量验证,测量关键及安装尺寸性能要求参照供应商提供定期性能试验报告座椅使用不良评价不良项目级别品质要求范围·操作力非常沉重·靠背不能自动返回或返回非常A 慢·操作途中卡住·头枕操作力非常重或非常轻操作不良B ·操作力沉重·靠背返回慢·操作途中有卡住感·头枕操作力重或轻C ·操作有的地方略微沉重A 须用力摇晃身体才能锁住(在较广的范围发生)滑动锁定不良 B 轻轻摇晃身体就能锁住(在较窄的范围或一部分区域发生)C 稍稍摇晃身体就能锁住9坐下的舒适度动作时异音(包括坐下时)面差、阶差( 正面及侧面评价)松动缝合线断线4.9安全带不良项目回缩器卷缠不良回缩器拉出时异音扭曲锁闭与松开不良JSJ-002 A·到达底部(身体接触到框架)·有异物感·有到达底部的感觉(身体有接触到框架的感觉)B·有些异物感觉·左右舒适度不同·没有支撑感(不能彻底的支撑身体,向前滑动等)·略微有到达底部的感觉(略微有接触到框架的感觉)C·略微有异物的感觉A非常大的异音B大的异音C小的异音A>30mm,发生部位座椅形状有棱角 , 很明显B15~30mm,发生部位座椅形状呈圆弧形 , 不是很明显C<15mmA有的位置时常发生大的松动B有的位置时常发生小的松动C有的位置时常发生极小的松动A缝合线断开,缝合处的表皮浮起B断开长度 5~25mm,但未达到缝合处表皮浮起的程度C虽然缝合线断开,但难以发现级别品质要求范围·卷缠中有时卡住(不卷缠)·拉出非常沉重,或不能A拉出·带有儿童固定机构的安全带不能发挥作用B·卷缠慢,费时间·有 150~200mm的剩余·拉出沉重C·有不到150mm的剩余·拉出有些沉重A拉出、返回(松开)有较大的声音B拉出、返回(松开)有引人注意的声音C拉出、返回(松开)有稍微引人注意的声音A扭曲形态改不过来B虽然扭曲,但能轻易恢复原样C--·锁舌难进入(不光滑、卡住、紧)·松开按钮的操作很费力·锁舌进入扣口以外的其它地方·即使按下松开按钮,锁舌也不能脱开·安全带调节器的动作不良(不光滑、卡住、紧)·锁舌有些难进入(有些不光滑、有些卡住、有些紧)·松开按钮的操作力有些费力B·松开按扭操作后,锁舌返回不良(松开有些缓慢)·安全带调节器的动作有些不良·锁舌插入扣口困难C·锁舌插入扣口有些困难A长度> 15mm(宽度> 1mm或划伤严重,长度× 2 计算)织带划伤B长度在10~15mm(宽度>1mm或划伤严重,长度× 2计算)C长度< 10mm(宽度> 1mm或划伤严重,长度× 2 计算)织带脏污、黑点尺寸测量性能要求A 脏污>∮ 10mm 黑点>∮ 5mmB 脏污∮ 3~∮10mm 黑点∮ 2~∮5mmC 脏污<∮ 3 黑点<∮ 2mm参照供应商提供的检查报告书进行测量验证,测量关键及安装尺寸参照供应商提供定期性能试验报告4.10 油管、水管、排气管品质要求项目品质要求值质地应均匀,无明显飞边和毛刺,内外表面不胶管外观充许有缺胶和结块,不充许有分层、喷霜等缺陷表面应无划伤、破裂等明显缺陷,表面应光滑、硬管外观规整、镀层应均匀,不得有裂纹、皱磷层、凹坑、划伤、压扁、锈蚀、镀层脱落等明显缺陷·各焊接位置应保证焊缝光滑平整,无焊瘤结疤、漏焊和焊缝开裂等缺陷。