高速精密冲床冲压的间隙
冲压模具间隙
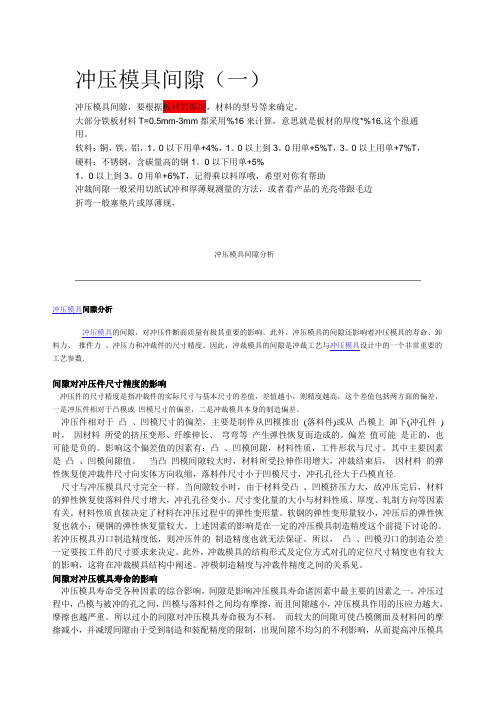
冲压模具间隙(一)冲压模具间隙,要根据板材的厚度,材料的型号等来确定。
大部分铁板材料T=0.5mm-3mm都采用%16来计算,意思就是板材的厚度*%16,这个很通用。
软料:铜,铁,铝,1。
0以下用单+4%,1。
0以上到3。
0用单+5%T,3。
0以上用单+7%T,硬料:不锈钢,含碳量高的钢1。
0以下用单+5%1。
0以上到3。
0用单+6%T,记得乘以料厚哦,希望对你有帮助冲裁间隙一般采用切纸试冲和厚薄规测量的方法,或者看产品的光亮带跟毛边折弯一般塞垫片或厚薄规,冲压模具间隙分析冲压模具间隙分析冲压模具的间隙,对冲压件断面质量有极其重要的影响。
此外,冲压模具的间隙还影响着冲压模具的寿命、卸料力、推件力、冲压力和冲裁件的尺寸精度。
因此,冲裁模具的间隙是冲裁工艺与冲压模具设计中的一个非常重要的工艺参数.间隙对冲压件尺寸精度的影响冲压件的尺寸精度是指冲裁件的实际尺寸与基本尺寸的差值,差值越小,则精度越高,这个差值包括两方面的偏差,一是冲压件相对于凸模或凹模尺寸的偏差,二是冲裁模具本身的制造偏差。
冲压件相对于凸、凹模尺寸的偏差,主要是制件从凹模推出(落料件)或从凸模上卸下(冲孔件)时,因材料所受的挤压变形、纤维伸长、穹弯等产生弹性恢复而造成的。
偏差值可能是正的,也可能是负的。
影响这个偏差值的因素有:凸、凹模间隙,材料性质,工件形状与尺寸。
其中主要因素是凸、凹模间隙值。
当凸凹模间隙较大时,材料所受拉伸作用增大,冲裁结束后,因材料的弹性恢复使冲裁件尺寸向实体方向收缩,落料件尺寸小于凹模尺寸,冲孔孔径大于凸模直径.尺寸与冲压模具尺寸完全一样。
当间隙较小时,由于材料受凸、凹模挤压力大,故冲压完后,材料的弹性恢复使落料件尺寸增大,冲孔孔径变小。
尺寸变化量的大小与材料性质、厚度、轧制方向等因素有关。
材料性质直接决定了材料在冲压过程中的弹性变形量。
软钢的弹性变形量较小,冲压后的弹性恢复也就小;硬钢的弹性恢复量较大。
上述因素的影响是在一定的冲压模具制造精度这个前提下讨论的。
如何确定冲裁模间隙值

如何确定冲裁模间隙值?2011-01-17 15:25间隙对冲裁件质量、冲裁力、模具寿命等都有很大的影响。
但很难找到一个固定的间隙值能同时满足冲裁件质量最佳、冲模寿命最长,冲裁力、最小等各方面的要求。
因此,在冲压实际生产中,主要根据冲裁件断面质量、尺寸精度和模具寿命这三个因素综合考虑,给间隙规定一个范围值。
模具制造网只要间隙在这个范围内,就能得到质量合格的冲裁件和较长的模具寿命。
这个间隙范围就称为合理间隙,这个范围的最小值称为最小合理间隙(Zmin),最大值称为最大合理间隙(Zmax)。
模具制造网考虑到在生产过程中的磨损使间隙变大,故设计与制造新模具时应采用最小合理间隙Zmin。
确定合理间隙值有理论法和经验确定法两种。
一般冲压加工的材料的厚度在2mm以内的冲裁模的间隙值可以取10%以下,如果要求毛刺小的话,可以取到5%左右(双边间隙)。
1 冲裁模间隙与模具寿命在传统设计中总是尽量选用较小间隙,因为模具在使用过程中,间隙会逐渐变大。
在满足产品技术要求的情况下,适当取大间隙可提高模具寿命。
如冲裁1.5mm厚的低碳钢板¢22mm,凸凹模间隙取料厚的8%时,冲8100件就因毛刺过大而刃磨;间隙取料厚20%时,冲51300件才刃磨,模具寿命可提高6倍。
不同材料的模具凸凹模间隙也不尽相同。
1.理论确定法主要是根据凸、凹模刃口产生的裂纹相互重合的原则进行计算。
图2.3.2所示为冲裁过程中开始产生裂纹的瞬时状态,模具制造网根据图中几何关系可求得合理间隙Z为图2.3.1 冲裁模间隙图 2.3.2 冲裁产生裂纹的瞬时状况上式可看出,合理间隙Z与材料厚度t、凸模相对挤入材料深度、裂纹角有关,而及又与材料塑性有关,见表2.3.1。
因此,模具制造网影响间隙值的主要因素是材料性质和厚度。
材料厚度越大,塑性越低的硬脆材料,则所需间隙Z 值就越大;材料厚度越薄,塑性越好的材料,则所需间隙Z值就越小。
模具制造网由于理论计算法在生产中使用不方便,故目前广泛采用的是经验数据。
扬力冲床高速精密冲床操作指南

扬力高速精密冲床HPC系列主要参数:HPC系列高速超精密压力机机身体和机架采用高强度铸铁铸造而成,具有极佳的吸震性能,在高速冲压和高速进给的情况下,机身沉稳,震动小,确保机床的长期精度;主传动采用变频调速,运动速度平稳;压力机的主轴采用进口滚动轴承,保证了压力机的传动精度,减少了压力机的总间隙和热影响;采用滑块双面导柱(双导柱,一个中心柱)结构,使动力摩擦减至最低,热变形降至最小,而精度达到了最高,保护并延长模具寿命;滑块的装模高度调节采用手动调节,数字显示模高,操作方便,模高显示精度达0.1mm;采用油压锁模装置,锁紧可靠,保证零件冲压精度;滑块采用日本THK滚珠式线性导轨,滑块两后导柱采用日本THK线性衬套,压力机精度可以达日本JIS一级精度标准,机床刚度接近于闭式压力机刚度,机床采用机械式卡模解脱装置;整机采用稀油强制循环润滑系统,整机润滑充分;电气控制采用进口品牌可编程控制器+触摸屏+电子凸轮控制器,配置4组预裁计数器、2组可配置的误送接口、2组模具故障接口及1组末料检测接口;采用美国MAC单联阀,反应速度迅速、准确,保证离合器的可靠控制。
曹海俸目前主要有:扬力冲床,扬力深喉冲床,扬力气动冲床,扬力冲床双点大台面气动冲床,扬力冲床闭式单点冲床,扬力冲床闭式双点大台面冲床,扬力冲床高速精密冲床,扬力高速冲床闭式双点高速精密冲床,扬力剪板机,扬力数控剪板机,扬力折弯机,扬力数控折弯机,扬力液压机,扬力数控冲床,扬力激光切割机等。
精密冲床广泛应用于多种批量生产之金属钣金加工冲剪、成形、引伸。
如交通车辆、钟表、家电、文具、手工具、五金、电脑等产品加工。
同时,可加装自动送料机,从事自动移送整条生产线加工。
精密冲床的特点1、高刚性高刚性、高精密的构架,采用钢板焊接,并经热处理、消除床身内应力。
2、重心平衡1.传动中心与机器整体的中心趋于一致,确保冲压的精确、稳定。
3、操作稳定、安全离合器/刹车器装置高度灵敏,再加国际顶尖的双联电磁阀和过负荷保护装置,确保冲床滑块运转及停止的精确性与安全性。
冲压模间隙的标准是什么【大全】

冲压模具冲裁间隙,根据对模具的研究和改进的经验,尺寸精度、断面垂直度要求高的制件应选用较小间隙值,断面垂直度与尺寸精度要求不高的冲压件,应以降低冲裁力、提高冲压模具寿命为主,可采用较大间隙值。
其值可按下列经验公式来计算:软材料:材料厚度t<1 mm,冲裁间隙c=(3% ~ 4%)tt = 1 ~ 3mm,c = (5% ~8%)tt = 3 ~ 5mm ,c =(8% ~10%)t硬材料:t <1mm,c = ( 4% ~5% )tt = 1 ~ 3mm,c = ( 6% ~8% )tt = 3 ~ 8mm,c = ( 8% ~ 13%)t因此影响间隙值的主要因素是材料性质和材料厚度。
材料比较硬或比较厚,间隙值越大。
在毛坯的送进方向上,具有两个或更多的工位,在压力机的一次行程中,在不同的工位上逐次完成两道或两道以上冲压工序的模具。
综合了单工序模和级进模的特点,利用机械手传递系统,实现产品的模内快速传递,可以大大提高产品的生产效率,减低产品的生产成本,节俭材料成本,并且质量稳定可靠。
扩展资料:结构零件,这类零件不直接参与完成工艺过程,也不和坯料有直接接触,只对模具完成工艺过程起保证作用,或对模具功能起完善作用,包括有导向零件、紧固零件、标准件及其它零件等。
应该指出,不是所有的冲模都必须具备上述六种零件,尤其是单工序模,但是工作零件和必要的固定零件等是不可缺少的。
高速铣削的主轴转速一般为15000r/min~40000r/min,最高可达100000r/min。
在切削钢时,其切削速度约为400m/min,比传统的铣削加工高5~10倍;在加工模具型腔时与传统的加工方法(传统铣削、电火花成形加工等)相比其效率提高4~5倍。
磨削及抛光加工由于精度高、表面质量好、表面粗糙度值低等特点,在精密模具加工中广泛应用。
精密模具制造广泛使用数控成形磨床、数控光学曲线磨床、数控连续轨迹坐标磨床及自动抛光机等先进设备和技术。
数控冲床模具维护指南(KETEC版)

数控冲床模具维护指南(KETEC版)一、数控冲床模具冲压过程退料板与板料接触→冲头接触板料,板料开始变形→材料在应力点开始断裂→废料从板材中断裂出来→冲头冲压到底→冲头回缩,废料自由下落,冲压工序完成(图1)二、从废料情况看出的信息(压塌角、光亮带、断裂带、毛刺)(图2)1、废料本质上就是成形孔的反像。
即位置相反的相同部位。
通过检查废料,你可以判断下模间隙是否正确。
如果间隙过大,废料会出现粗糙、起伏的断裂面和一窄光亮带区域。
间隙越大,断裂面与光亮带区域所成角度就越大。
如果间隙过小,废料会呈现出一小角度断裂面和一宽光亮带区域。
2、过大间隙形成带有较大卷边和边缘撕裂的孔,令剖面稍微有一薄边缘突出。
太小的间隙形成带稍微卷边和大角度撕裂,导致剖面或多或少地垂直于材料表面。
3、一个理想的废料应有合理的压塌角和均匀的光亮带。
这样可保持冲压力最小并形成一带极少毛刺的整洁圆孔。
从这点看,通过增大间隙来延长模具寿命是以牺牲成品孔质量换取的。
三、为什么要使用正确的下模间隙?1、最佳间隙:剪切裂缝接合,均衡冲压力、工件质量和模具寿命。
2、间隙太小:次等的剪切裂缝,冲压力提升,缩短模具使用寿命。
四、模具间隙的选择模具的间隙与所冲压的材料的类型及厚度有关。
不合理的间隙可以造成以下问题:1、间隙过大,所冲压工件的毛刺就比较大,冲压质量差。
如果间隙偏小,虽然冲孔的质量较好,但模具的磨损比较严重,大大降低模具的使用寿命,而且容易造成冲头的折断。
2、间隙过大或过小都容易在冲头材料上产生的粘连,从而造成冲压时带料。
过小的间隙容易在冲头底面与板料之间形成真空而发生废料反弹。
3、合理的间隙可以延长模具寿命,卸料效果好,减少毛刺和翻边,板材保持洁净,孔径一致不会刮花板材,减少刃磨次数,保持板材平直,冲孔定位准确。
对用户来讲,提高模具的使用寿命可以大大降低冲压成本。
影响模具使用寿命的因素如下:1、材料的类型及厚度。
2、是否选择合理的下模间隙。
五金冲压模具各种间隙标准

TT-QW-TI-02
版本
01
類別
各種間隙標准
制定日期
2005年12月1日
操作規範
頁次
PAGE 2 OF 3
1、間隙:
單工程模。
1.1刀口間隙:
a.以客戶要求訂定。
b.沖材≦0.6者,沖材厚之5%。
c.2.0≧沖材>0.6者,沖材厚之7%。
d.4.0≧沖材>2.0者,沖材厚之10%。
e.6.0≧沖材>4.0者,沖材厚之15%。
2.3粗割後修一:精度要求稍高之模具,模板變形量足以影響模板配合度等。
2.4粗割後修二:精度要求較高之模具。
核准
審核
編制
d.特殊用途之沖壓品,間隙另定。
2、修刀:
2.1無特別要求之模具均以割一刀為准,但Pin孔、導柱孔、∮4以下則修一刀,下模修刀口3.0。
2.2即割即修:
a.模板無大孔,可導致加工變形。
沖材厚≦0.3,模板長度≦600mm。
沖材厚≦0.4,Βιβλιοθήκη 板長度>600者。b.內角眾多之異形孔。
c.φ4.0以下之小孔。
f.特殊用途之沖壓品,刀口間隙另行議定。
1.2滑配間隙:
a.模板長度≦600者,單+0.015,沖材厚度≦0.3時另議。
b.模板長度>600者,單+0.02,沖材厚度≦0.4時另議。
1.3緊配間隙:單+0.005。
1.4Pin孔:單+0.005修一刀。
1.5導柱孔:
a.模板長度≦600者,單+0.01修一刀。
b.模板長度>600者,單+0.015修一刀。
1.6沖材厚度≦0.3者,一律以客戶協調方式制作。
冲床精度标准

冲床精度标准冲床精度标准是指冲床在工作过程中所能达到的精度要求。
冲床是一种常见的金属加工设备,广泛应用于汽车、电子、家电等行业。
在冲床的工作过程中,精度是非常重要的,它直接关系到产品的质量和性能。
因此,制定冲床精度标准对于保证产品质量和提高生产效率具有重要意义。
冲床精度标准主要包括以下几个方面:1. 冲床的位置精度:冲床的位置精度是指冲床在进行冲压加工时,冲头与工件之间的位置误差。
通常情况下,冲床的位置精度要求在0.01mm以内。
位置精度的要求越高,说明冲床的加工精度越高。
2. 冲床的尺寸精度:冲床的尺寸精度是指冲床在进行冲压加工时,所加工出来的产品尺寸与设计要求之间的偏差。
通常情况下,冲床的尺寸精度要求在0.02mm以内。
尺寸精度的要求越高,说明冲床的加工精度越高。
3. 冲床的重复精度:冲床的重复精度是指冲床在进行连续冲压加工时,每次加工出来的产品尺寸之间的偏差。
通常情况下,冲床的重复精度要求在0.02mm以内。
重复精度的要求越高,说明冲床的加工稳定性越好。
4. 冲床的平行度:冲床的平行度是指冲床在进行冲压加工时,冲头与工作台之间的平行度误差。
通常情况下,冲床的平行度要求在0.02mm以内。
平行度的要求越高,说明冲床的加工稳定性越好。
5. 冲床的垂直度:冲床的垂直度是指冲床在进行冲压加工时,冲头与工作台之间的垂直度误差。
通常情况下,冲床的垂直度要求在0.02mm以内。
垂直度的要求越高,说明冲床的加工稳定性越好。
6. 冲床的表面粗糙度:冲床的表面粗糙度是指冲压加工后产品表面的光洁程度。
通常情况下,冲床的表面粗糙度要求在Ra0.8以内。
表面粗糙度的要求越低,说明冲床加工出来的产品表面越光滑。
以上就是冲床精度标准的主要内容。
通过制定合理严格的冲床精度标准,可以有效地保证产品质量和提高生产效率。
同时,企业在使用冲床时还应注意对设备进行定期维护和保养,及时发现和解决设备故障,确保设备能够始终保持良好的工作状态。
冲压模具公差及间隙标准

公差及间隙标准
一模具零件公差及间隙标准
1 模板厚度公差要求:
1.1 配合性模板(厚度对入子零件的上下装配关系有较
大影响的模板)厚度尺寸公差取值±0.03;
1.2 非配合性模板厚度公差取值±0.08.
2零件外形和模板孔的公差及间隙要求:
详见附表一: <<模具零件公差及间隙一览表>>
二冲裁刃口要求及冲裁间隙标准
1 冲裁刃口要求
1.1 一般冲裁刃口留修(直段)3MM,斜度1︒,如下图.
1.2 一般3MM以下的小孔(含3MM),冲裁刃口留修
2MM,斜度1︒.对于其它标准有明确规定的,按照其
它标准要求执行.
1.3 产品材料厚度T<0.3或T>1.5时,请示上级.
2 冲裁间隙标准详见附表二: <<冲裁间隙一览表>>
附表一: <<模具零件公差及间隙一览表>>
附表二: <<冲裁间隙一览表>>
注: 1.上表所列间隙值均是指单边冲裁间隙Z.
2.冲裁间隙Z的取值与冲裁的料片材质、厚度及生产条件
(模具形式等)有关.
3.未作注明者均不区分模具形式是工程模/连续模.
4.对于3MM以下小孔,当冲裁的料片材质为GI或不锈钢
/CRS/铝时,单边冲裁间隙Z=10%T.
5.冲裁的料片材质上表未列出时(如铜),冲裁间隙请示上级.。
冲压模具公差及间隙标准

公差及间隙标准一模具零件公差及间隙标准
1 模板厚度公差要求:
1.1 配合性模板(厚度对入子零件的上下装配关系
有较大影响的模板)厚度尺寸公差取值±0.03;
1.2 非配合性模板厚度公差取值±0.08.
2零件外形和模板孔的公差及间隙要求:
详见附表一: <<模具零件公差及间隙一览表>>
二冲裁刃口要求及冲裁间隙标准
1 冲裁刃口要求
1.1 一般冲裁刃口留修(直段)3MM,斜度1?,如下图.
1.2 一般3MM以下的小孔(含3MM),冲裁刃口留修
2MM,斜度1?.对于其它标准有明确规定的,按照
其它标准要求执行.
1.3 产品材料厚度T<0.3或T>1.5时,请示上级.
2 冲裁间隙标准详见附表二: <<冲裁间隙一览表>>
附表一: <<模具零件公差及间隙一览表>>
附表二: <<冲裁间隙一览表>>
注: 1.上表所列间隙值均是指单边冲裁间隙Z.
2.冲裁间隙Z的取值与冲裁的料片材质、厚度及生产
条件(模具形式等)有关.
3.未作注明者均不区分模具形式是工程模/连续模.
4.对于3MM以下小孔,当冲裁的料片材质为GI或不锈
钢/CRS/铝时,单边冲裁间隙Z=10%T.
5.冲裁的料片材质上表未列出时(如铜),冲裁间隙请示
上级.。
冲床下模间隙

冲床下模间隙冲床下模间隙是指在冲压过程中,上模和下模之间的距离。
间隙的大小对冲压件的成形质量、模具的寿命以及设备的性能有着重要的影响。
正确的设置和调整冲床下模间隙可以确保冲压过程中的运动平稳,同时可以减少模具的磨损,提高产品的质量,降低成本。
首先,冲床下模间隙的设置应方便模具安装和调整。
一般来说,间隙的大小应能够容纳模具进出床台,并且能够方便地进行调整。
这样可以在模具的更换和调整中节省时间和精力。
其次,冲床下模间隙的大小应根据冲压件的要求进行调整。
间隙过大会导致冲压时上下模具的相对运动不稳定,容易产生冲床异响和震动,还可能影响产品的尺寸精度和表面质量。
间隙过小则会增加模具的磨损程度,缩短使用寿命。
因此,在调整冲床下模间隙时,需要根据冲压件的尺寸、材料和工艺要求进行合理的设置。
此外,冲床下模间隙的调整还需考虑冲床的性能特点。
间隙的大小应能够适应冲床的运动特性,并且不会影响冲压速度和产能。
例如,对于高速冲压机,间隙的调整要求更为严格,需要保证冲压时上下模具的相对运动平稳,并且能够承受高频率的工作状态。
最后,冲床下模间隙的调整还需考虑材料的变形特性。
不同材料在冲压过程中的变形特点不同,需要根据材料的特性来调整间隙的大小。
例如,对于高硬度材料,间隙应适当增大,以防止产生过多的应力和热量,从而减少模具的磨损。
综上所述,冲床下模间隙的调整是冲压过程中非常重要的一个环节,直接影响冲压件的质量和模具的寿命。
合理的间隙设置和调整能够保障冲压过程的稳定性,提高产品的质量,并且延长模具的使用寿命。
因此,在进行冲床下模间隙的调整时,需要综合考虑冲压件的要求、冲床的性能特点以及材料的变形特性。
这样才能保证冲压过程的顺利进行,并获得理想的冲压件。
精密五金冲压件外发加工,如何控制冲压模具间隙?

精密五金冲压件外发加工,如何控制冲压模具间隙?
冲压模具间隙指的是凹模和凸模的间距,在精密五金冲压件外发加工中,保证准确的模隙非常重要,关系到整条生产线的冲压件质量,有部分入行不久的模工不知道怎么控制模隙,诚瑞丰就为大家提供以下几种常用方法:
1.透光测距:
在凹模和固定板间放一个垫块,用夹钳固定,用平口钳夹住模柄,使用手电筒照射,观察下模漏料孔的透光情况来确定间隙的合格程度。
如光线在某一方向上偏多,表明间隙过大,可敲击对边的侧面,凸模的位置移动并得到微调,反复进行,直到合适为止。
注意:这种方法简单易操作,但仅适用于小型冲压模具的装配。
2.直接测量:
合并凹凸模,用尺子测量两者之间的大小,根据实际数值来调整凹凸模之间的位置,使其各部分配合一致。
注意:该方法操作简单方便,适合间隙较大的模具,例如0.02mm以上。
3.垫片方法:
根据间隙的大小,在凹凸模之间垫如厚度均匀的金属片,使其间隔标准。
注意:过程较为复杂,但效果好。
4.涂层方法:
凸模在工作中易磨损,导致长度不足,可在其表面涂上一层材料,再将凸模与凹模合并,得到合适的冲压间隙。
注意:该方式简单易操作,适合于不能用垫片法调整的模具。
精密五金冲压件外发加工选诚瑞丰,致力于生产高品质冲压件,拥有严格的日资管理体系,交付周期短,欢迎联系合作。
冲床滑块间隙调整方法

冲床滑块间隙调整方法
冲床滑块间隙调整方法包括以下几个步骤:
1. 确定调整滑块间隙的目的:首先需要明确为什么需要调整滑块间隙,是为了解决产品加工过程中的问题还是为了更好地适应工件的尺寸要求。
2. 准备工具:调整滑块间隙需要使用专门的工具,如调节螺钉或螺栓、扳手或套筒、测量工具等。
3. 安全操作:在进行调整滑块间隙之前,首先确保冲床处于停止状态,切断电源并锁住启动按钮,以防止意外启动和伤害。
4. 调整滑块间隙:根据滑块间隙的调整方向确定调节螺钉的位置。
通常情况下,顺时针旋转螺钉可以减小滑块间隙,逆时针旋转则可以增大滑块间隙。
5. 测量间隙尺寸:使用测量工具,如千分尺或游标卡尺,测量滑块间隙的尺寸。
根据产品要求或加工工艺标准进行调整。
6. 反复测试和调整:反复测试滑块间隙的尺寸,如果滑块间隙过大或过小,需要继续调整螺钉,直到达到满意的间隙尺寸。
7. 确认调整结果:在调整完滑块间隙之后,进行最后一次测试,确保滑块间隙
的尺寸符合要求。
需要注意的是,在进行调整滑块间隙时,要注意安全操作,避免直接用手触碰滑块和调节螺钉,以免造成伤害。
在进行调整之前,最好先查阅相关的操作说明或咨询专业人士的建议。
冲床模具间隙怎么计算

冲床模具间隙怎么计算 LELE was finally revised on the morning of December 16, 2020冲床模具间隙怎么计算1.冲压模具间隙,要根据板材的厚度,材料的型号等来确定。
大部分铁板材料T=都采用16%来计算,意思就是板材的厚度16%,这个很通用。
2.冲裁间隙一般采用切纸试冲和厚薄规测量的方法,或者看产品的光亮带跟毛边,折弯一般塞垫片或厚薄规。
3.看材料厚度。
材料越软,间隙越小。
向左转|向右转拓展资料:冲压模具,是在冷冲压加工中,将材料(金属或非金属)加工成零件(或半成品)的一种特殊工艺装备,称为冷冲压模具(俗称冷冲模)。
冲压,是在室温下,利用安装在压力机上的模具对材料施加压力,使其产生分离或塑性变形,从而获得所需零件的一种压力加工方法。
冲床冲模是装在压力机上用于生产冲件的工艺装备,由相互配合的上、下两部分组成。
凸模是冲模中起直接形成冲件作用的凸形工作零件,即以外形为工作表面的零件。
凹模是冲模中起直接形成冲件作用的凹形工作零件,即以内形为工作表面的零件。
防护板是防止手指或异物进入冲模危险区域的板状零件。
压料板(圈)是冲模中用于压住冲压材料或工序件以控制材料流动的零件,在拉深模中,压料板多数称为压料圈。
压料筋是拉延模或拉深模中用以控制材料流动的筋状突起,压料筋可以是凹模或压料圈的局部结构,也可以是镶入凹模或压料圈中的单独零件。
压料槛是断面呈矩形的压料筋特称。
参阅“压料筋”。
承料板是用于接长凹模上平面,承托冲压材料的板状零件。
连续模是具有两个或更多工位的冲模,材料随压力机行程逐次送进一工位,从而使冲件逐步成形。
一般建议模具总间隙为材料板厚的20%~25%。
模具的间隙是否合理,是很重要的,如果模具间隙不合适,容易造成废料反弹。
标准模具的选用:(1)模具的刃口直径应尽量大于加工板厚的2倍,直径一般应大于3mm,否则易折断,寿命极短;但也不是绝对的,3mm直径以下推荐使用进口高速钢作为模具材料。
高速冲床闭合高度的调整

高速冲床合模之后,使用寸动连转操作,使滑块降至下死点位置,检查冲压高度是否适当,并作适当调整。
1、高速冲床滑块模高调整注意事项:
(1)滑块模高调整装置不可作为预压上下模之用。
(2)滑块模高调整装置不可使用于模高调整以外的用途。
(3)使用滑块模高调整装置进行作业或加压上下模具后,会造成刹车马达发热及损坏滑块调整机构。
2、手动调整法:用六角板手调整高速冲床模高指示器旁的调整螺栓,摇板手向左或向右使
滑块上升或下降,注视模高指示器,调至适当高度,取下板手调整前请先查明模高的上下限,切莫超过规定的范围。
3、电动调整法:将冲床滑块调整选择钮置于“ON”位置,然后依照上项所确定冲压高度
若为太高时,则押下“滑块下降”按钮,注视“模高指示器”而调整至适当高度时,放开按钮即可。
高速冲床高度若为太低时,则押下“滑块上升”按钮而调整之。
但需要注意顶料装置是否遭到不正常撞击选择钮置于“OFF”再使用寸动操作,使滑块行至上死点位置。
滑块调整电气回路通电时,连转操作回路为断电状态,连转操作回路通电时,滑块升降调整操作无效。
4、特别注意:
5、(1)调整冲床滑块高度前,请将下料顶杆调至最高,以避免撞击。
6、(2)为减轻调整时的负荷,请预先将储气筒气压调低(或浅压)。
冲床的综合间隙
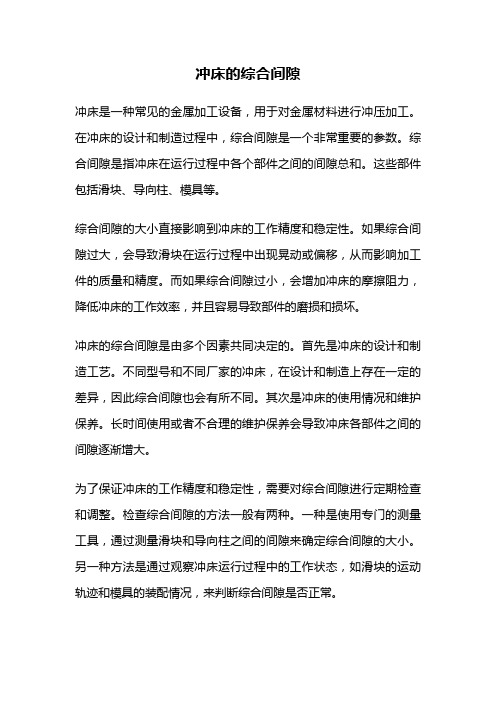
冲床的综合间隙冲床是一种常见的金属加工设备,用于对金属材料进行冲压加工。
在冲床的设计和制造过程中,综合间隙是一个非常重要的参数。
综合间隙是指冲床在运行过程中各个部件之间的间隙总和。
这些部件包括滑块、导向柱、模具等。
综合间隙的大小直接影响到冲床的工作精度和稳定性。
如果综合间隙过大,会导致滑块在运行过程中出现晃动或偏移,从而影响加工件的质量和精度。
而如果综合间隙过小,会增加冲床的摩擦阻力,降低冲床的工作效率,并且容易导致部件的磨损和损坏。
冲床的综合间隙是由多个因素共同决定的。
首先是冲床的设计和制造工艺。
不同型号和不同厂家的冲床,在设计和制造上存在一定的差异,因此综合间隙也会有所不同。
其次是冲床的使用情况和维护保养。
长时间使用或者不合理的维护保养会导致冲床各部件之间的间隙逐渐增大。
为了保证冲床的工作精度和稳定性,需要对综合间隙进行定期检查和调整。
检查综合间隙的方法一般有两种。
一种是使用专门的测量工具,通过测量滑块和导向柱之间的间隙来确定综合间隙的大小。
另一种方法是通过观察冲床运行过程中的工作状态,如滑块的运动轨迹和模具的装配情况,来判断综合间隙是否正常。
调整综合间隙的方法也有多种。
一种常用的方法是通过调整导向柱的位置来改变综合间隙的大小。
另一种方法是更换磨损严重的部件,如导向柱和滑块,以恢复综合间隙的正常状态。
除了定期检查和调整综合间隙,还应注意冲床的日常维护保养。
保持冲床的清洁和润滑,定期更换润滑油和磨损严重的部件,可以延长冲床的使用寿命,并保证其正常工作。
综合间隙是冲床运行过程中一个重要的参数,直接影响到冲床的工作精度和稳定性。
了解综合间隙的概念和调整方法,对于使用冲床进行加工的工作人员来说是非常重要的。
只有正确掌握和调整综合间隙,才能保证冲床的正常工作,提高加工效率和产品质量。
- 1、下载文档前请自行甄别文档内容的完整性,平台不提供额外的编辑、内容补充、找答案等附加服务。
- 2、"仅部分预览"的文档,不可在线预览部分如存在完整性等问题,可反馈申请退款(可完整预览的文档不适用该条件!)。
- 3、如文档侵犯您的权益,请联系客服反馈,我们会尽快为您处理(人工客服工作时间:9:00-18:30)。
高速精密冲床冲压的间隙
高速精密冲床冲裁间隙是指凸、凹模刃口间的续欧。
冲裁间隙是冲压工艺和模具设计中的重要参数,它直接影响冲裁件的质量、模具寿命和力能的消耗。
设计高速精密冲床的冲模时,应根据实际情况和需要合理地选用冲裁间隙。
1、高速精密冲床冲裁间隙分类:根据冲裁件尺寸精度、剪切面质量、模具寿命和功能消耗等主要因素,将金属材料冲裁间隙分成三种类型即大、中、小三层。
2、冲裁间隙的选用:冲裁间隙的大小与被冲材料的性质及厚度有关,料越硬、厚度越大,则间隙值就越大。
高速精密冲床在选用金属材料冲压时,应针对冲压件技术要求、使用特点和特定的生产条件等因素,采用的间隙类别,选取该类间隙数值。
另外,推荐工厂实际生产中使用的两个冲裁间隙表,其中电机、电器行业采用的(较小的)间隙值,适用于电子、仪器、仪表、精密机械等对冲压件尺寸精度要求较高。
3、在单边剪切时,刃口间隙的选取在切断、切口等分离类工序中,凸模、凹模的刃口通常是单边(非封闭轮廓)剪切材料。
在单边剪切的过程中,原材料、凸模和凹模都会产生一个侧向力(水平分力),这个侧向力会导致原材料窜动、刃口间隙增大、剪切面质堡下降等不良影响。
因此在设计冲模时,除了在结构上要采取有效措施来防止侧向力带来的不良影响(例如凸模、凹模反侧压结构或装置),在选取刃口间隙时,对于单边剪切刃口的间隙,通常取正常间隙的30%—50%。
高速精密冲床精冲包括强力压边精冲、对向凹模精冲和平面压边精冲。
目前应用较普遍的强力三好压边精冲,是在高速冲床上借助于特殊结构的模具进行的。
强力压边精冲在冲裁前,齿圈压料板先将坯料压紧在凹模上;接着凸模开始下降,与反压板一起将坯料压紧。
此时坯料处于压紧状态,剪切区的金属在v形齿圈、反压板和凸模的共同作用下,处于三向压应力状态,从而提高了塑性。
凸模继续下降,即开始冲裁。
由于凸模与凹模之间的间隙很小,加上剪切区的金属处于三向压应力状态,使冲裁过程呈纯剪切的形式,从而获得良好的剪切断面和尺寸精度。