汽车车身零件通用定位要求
关键零部件和材料COP-车身

1、装配正确,铆接牢固,可靠,铆接后总成表面不允许有划伤等影响外观的缺陷;
2、总成中各运动部位开启灵活,无卡滞现象;
3、在可见区域无毛刺,外观无缺损、裂纹等缺陷,部件装配前,转动和滑动部位进行润滑;
4、3C标识清晰完整
目测
每次采购
每批随机抽5件,少于5件全检/(0,1)
质量部
零部件检查成绩书
1、光滑平整,无飞边毛刺。镀层彩锌色彩均匀一致;
2、3C标识压印字迹清晰,字迹深0.3-0.5mm
目测
每次采购
每批随机抽5件,少于5件全检/(0,1)
质量部
零部件检查成绩书
总成关键尺寸
铰链安装孔:Ø11
游标卡尺
每次采购
每批随机抽5件,少于5件全检/(0,1)
质量部
零部件检查成绩书
铰链安装孔:Ø11 ×14
游标卡尺
每次采购
每批随机抽5件,少于5件全检/(0,1)
质量部
零部件检查成绩书
54±0.25
游标卡尺
每次采购
每批随机抽5件,少于5件全检/(0,1)
质量部
零部件检查成绩书
性能
功能实现
铰链铆接牢固可靠,转动灵活,无异响。
手动测试
每次采购
每批随机抽5件,少于5件全检/(0,1)
质量部
零部件检查成绩书
其他
质量部
零部件检查成绩书
铰链安装孔:Ø13
游标卡尺
每次采购
每批随机抽5件,少于5件全检/(0,1)
质量部
零部件检查成绩书
27±0.25
游标卡尺
每次采购
每批随机抽5件,少于5件全检/(0,1)
质量部
零部件检查成绩书
车身技术要求

技术要求1. 车身制图按QC/T490-2000《汽车车身制图》执行;2. 车身外观质量按Q/HMAC024-2000《车身外观质量标准》执行;3. 图中专用符号按Q/HMAC100.210-2008《汽车用零件的工程制图符号》规定;4. 焊点螺母按Q/HMAC101[1].201-226-2005《焊接螺母的质量》规定;5. 焊接螺栓按Q/HMAC101.201-229-2005《螺栓的焊接质量》规定;6. 点焊质量按Q/HMAC101.201-228-2005《点焊焊点质量》规定;7. MAG的焊接质量按Q/HMAC101.201-230-2005《MAG焊接质量》规定;8. 减震胶质量按Q/HMAC 101[1].103-001-2006《减震胶和点焊胶检验试验标准》的规定执行。
9. 焊点个数(涂胶处数)总共64个,具体见数模;10. 未注尺寸见三维数据;11.冲压件不能有锈斑、表面镀层脱落、裂纹、非造型引起的起皱和压痕;12.主定位面面轮廓公差0.4,平面度公差0.4;13.符号○FS为配合部位,FS配合部位的公差要求:焊接面段差±0.7,焊接面切边±1.0;14.定位孔、辅助定位孔的公差要求:圆孔孔径公差+0.05+0.2,位置度公差⌀0.1;长圆孔宽度公差+0.05+0.2,长度公差+0.05+0.2,位置度公差⌀0.1;15. 冲压件毛刺在0.3mm以内,材料厚度变薄率不超过30%;16. 孔的序号、数量、规格、用途和冲孔方向见下表。
17. 数模指示侧.18. 未注公差尺寸按Q/HMAC 101.201-206-2005《冲压件未注公差尺寸的极限偏差》的规定;NOTE1. BODY DRAWING TO QC/T490-2000“BODY DRAWING FOR AUTOMOBILE”PERFORM.2. QUALITY OF BODY APPEARANCE REFER TO Q/HMAC024-2000“QUALITY OF BODY APPEARANCE ”PERFORM.3. THE SYMBO OF DRAWING REFER TO Q/HMAC100.210-2008“SYMBOL OF ENGINEERING DRAWING OF AUTOMOBILE PART” PERFORM.4.WELDING NUT REFER TO Q/HMAC101[1].201-226-2005“QUALITY OF WELDING NUT”PERFORM.5.WELDING BOLT REFER TO Q/HMAC101.201-229-2005“QUALITY OF WELDING BOLT”PERFORM.6. WELDING SPOT REFER TO Q/HMAC101.201-228-2005“QUALITY OF WELDING SPOT”PERFORM.7. QUALITY OF THE MAG WELDING REFER TO Q/HMAC101.201-230-2005“QUALITY OF MAG WELDING” PERFORM.8. QUALITY OF SHOCK ABSORPTION GLUE ACORDING TO Q/HMAC 101[1].103-001-2006“TEST AND TRIAL STANDARDS FOR ABSORPTION GLUE AND WELDING GLUE”PERFORM.9. THE TOTAL OF WELDING SPOT (GLUE)IS 64, OTHERWISE SPECIFIED REFER TO 3D DA TA.10. UNLESS OTHERWISE SPECIFIED DIMENSION, REFER TO 3D DATA.11. PART IS NO RUST、SURFACE PLATING LAYER FALL OFF、CRACK、CRINKLE AND IMPRESS OF NON-STYLE.12. FACE PROFILE OF TORELENCE LOCATION FACE IS 0.4, POSITION TORELENCE IS ⌀0.113.○FS IS SIGN OF MATCHING FACE,THE MATCHIN FACE○FS TORELENCE REQUIMENT:JOGGLE OF WELDING SURFACE: ±0.7,ELDGE OF WELDING SURFACE: ±1.0 14. LOCA TIONG HOLE AND ASSISTANT HOLE TORELENCE REQUIMENT;DIAMETER TORELENCE: +0.05+0.2, POSITION TORELENCE:⌀0.1ASSITANT HOLE DIAMETER TORELENCE: +0.05+0.2, POSITION TORELENCE:⌀0.1 15. FIN OF THE PART IS NO MORE THAN 0.3MM, MATERIAL THICKNESSATTENUATION IS NO MORE THAN 30%.16. SERIAL NUMBER、QUANTITY、SIZE、FUNCTION AND PRESS DIRECTION OF THEHOLES SEE THE FOLLOWING TABLE.17. CAD DIGITAL DA TA DEFINE SURF18. UNSPECIFIED TOLERANCE REFER TO Q/HMAC 1 0 1.201-206-2005 “LIMITED TOLERANCE FOR UNSPECIFIED TOLERANCE DIMENSIONS”。
汽配销售指定方案

汽配销售指定方案
背景
随着汽车行业的快速发展,汽车配件市场也越来越重要。
对于汽车制造商和维修厂来说,怎样获得最佳的汽配产品和解决方案是一项重要的任务。
需求
汽配销售方案需要具备以下几点要求:
•多样化的产品线:涵盖车身、电动、驾驶系统等组件。
•精准的定位:根据目标群体需求和使用场景定位售卖产品。
•质量保障:优质的原材料和严格的生产流程来保证产品的质量。
•快速的物流供应:快速物流和稳定的供应链,保证产品能够及时送达。
解决方案
本方案的解决方案如下:
产品线
我们的产品线涵盖了各种汽车零部件的制造和供应。
包括车身零部件、内饰零部件、电动零部件、驾驶系统零部件和其它常用的零部
件等组成。
我们的销售方案可以根据不同的客户需求来制定合适的产品组合。
定位
我们会针对不同客户的需求、使用场景以及使用习惯进行分析,根据分析结果为客户提供适合的产品解决方案。
同时,我们将按照客户实际的购买情况进行产品的调整和优化,从而提供更好的服务。
质量保障
我们将优先采用高质量的原材料,并建立完善的生产流程。
我们会对每个产品都进行严格的质量检测和测试。
并使用专业的设备和技术,来确保每一个零部件的质量达到公认的高标准。
快速物流供应
我们承诺在最短的时间内将订单发出,并通过可靠的物流网络来保证送货的奏效。
同时,我们的供应链系统确保产品能够快速到达客户手中。
总结
汽配销售方案针对汽车制造商和维修厂,建立适合并高效的售卖体系,从而提高销售效率和客户满意度。
提供优质的产品和服务,也将有助于不断提升客户的信任和忠诚度。
白车身焊装定位

--定位方式和定位原则
什么是定位
• 定位就是最终将零件固定在准确的位置 • 定位的目的:保证白车身最终的尺寸要求
定位的基本方式
• 数模孔+孔+面 • 夹具销+销+支撑夹紧块
c 2 定位孔 1 2
定位面
支撑块 定位销
1
定位孔的作用
c
c 2 2 1 1 1 1
定位孔1的销定位,a/b向平移约束
• 固定销:结构简单、定位精度高、装取件
操作简单; • 伸缩销:结构复杂、定位精度较高、装取 件操作复杂; • 翻转销:翻转机构复杂、定为精度差、装 取件操作复杂
固定销使用条件:两个孔轴线共面并且该面
与主平面垂直
直板 装件 配垂
板件
平行固定销
固定销机构简 单,定位精度 高,工件可直 接装配和取出, 操作简单
两孔的间距大于零件尺寸的2/3
定位销 1 定位孔 孔距较大 1 2` 2 板件 2` 2
孔距小 1 2` 2
偏 差 大
两个孔轴线共面并且该面与主平面 垂直(可以使用固定销定位)
定位孔 长孔为n×(n+3), 不宜过长,影响孔 的强度
固定销垂 直主平面
定位孔轴线
平行固定销
防旋转 的长孔
定位销按运动方式有:固定销、伸用条件:定位孔轴线与主
平面不垂直,两个定位销不平行
板件 伸缩销
伸缩销机构复 杂,定位精度 较高,工件安 装困难
伸缩销 气缸
伸缩销定位示意图
翻转销使用条件:定位销空间受限
制的情况
板件
基础件
翻转销机构复 杂,定位精度 差,工件安装 困难
翻转销定位示意图
汽车车身整车尺寸公差标准

汽车车身整车尺寸公差标准
对于汽车车身整车尺寸公差标准,根据中国国家标准的《机动车尺度、轴距、前悬和后悬标准的规定》(GB1589-2016),机动车的长宽高误差范围为正负5mm,即实际尺寸与设计尺寸之间的差距应小于等于5mm。
此外,对于整车的宽度,公差按照其所在面而定。
如果是A面,公差是±1.0毫米;如是B面,公差是±2.0毫米;如是C面,公差为±2.0毫米。
B面与C面没有差别,因为B件大多为结构件,与其他件关系密切,也就是被制约,C件相对而言更自由一些,由其他件传导的误差要小一些。
通常,如果测量点位于夹具的控制点上,其公差可以取下限,因为车身是按由外向内的装配方式装配的,误差就会被推往车内,外面的误差较之车内会小一些。
以上标准仅供参考,建议查阅相关汽车技术规范或联系相关汽车制造商获取更准确的信息。
车身零件图纸解读

文件名后缀“TM.CATpart”文件 为产品3D数模
3、图纸标题栏内容 (图纸右下角)
德文/英文
使用软件版本
材料标准-材质
厚度公差标准-厚度
零件净重
图纸表示方法 图纸比例
零件名称 零件编号
4、图纸坐标表示方法
图纸坐标长度方向以 数字表示,高度 方向以字母表示
5、RPS基准:在大众公司,RPS系统被制定成公司标准VW01055。RPS是德语单词
1
H xy
表示该基准孔定位xy坐标方向
表示RPS序号 表示基准面(face),“F”为主基准面, 准面定位z坐标方向
6、特点特性表示
表示轮廓尺寸允许双 向(正负)0.5mm 误差 表示翻边高度允许正 负0.3mm误差
接触区域允许公差
6、特点特性表示
表示轮廓尺寸只允 许向外单方向 1mm误差
车身坐标值以前轮轴心上下 方向确定为Z坐标方向, 向上为正值、向下为负 值
Z + X + -
车身坐标值以前轮轴心前后 方向确定为X坐标方向, 向后为正值、向前为负 值
Z
车身坐标值以前轮轴心连线中 心左右方向确定为Y轴坐 标方向,向左为正值、向 右为负值
+ Y + -
2、CATIA文档命名
文件名后缀“TM.CATDrawing” 文件为产品2D 产品图纸
附注:对整段轮廓允许 的褶皱(波浪)公 差正负0.2mm
零件所有冲孔方向(毛刺方向)要求由车身 内部向外部
江苏合润汽车车身模具有限公司
6、特点特性表示
表示轮廓尺寸允许双方 向0.25mm误差
表示修边线尺寸 只允许单方 向1mm误差
6、特点特性表示
部分匹配面R+1,R-1
轿车整车通用设计规范..

白车身设计规范一、冲压件设计规范1.孔1.1钣金上的冲孔设计要与钣金冲压方向一致。
1.2孔的公差表示方法1.3过线孔1.3.1过线孔翻边1.3.1.1过线孔翻边至少要3mm高。
此翻边对钣金起加强作用,防止在安装过程中产生变形,从而影响此孔的密封性。
1.3.1.2如果通过过线孔的零件是面积≤6的固体,或者钣金足够厚,使其在不借助翻边时也能够承受住过线孔安装时的压力,那么此过线孔可以不翻边。
1.3.2过线孔所在平面尺寸1.3.2.1过线孔为圆孔(半径设为Rmm)时,孔周圈的平面半径应为(R+6)mm1.3.2.2过线孔为方孔时,孔周边的平面尺寸应比孔各边尺寸大6mm。
1.4法兰孔1.4.11.5排水孔1.5.1排水孔设计在车身内部空腔的最低处,其直径一般为6.5mm。
1.5.2对于车身内部加固的防撞梁,应同样在其空腔的最低处布置排水孔。
1.5.3在车身结构件的空腔及凹陷处必须布置排水孔。
1.6空调管路过孔1.7螺栓过孔1.8管道贯通孔2.圆角2.1对于在同一个件上喷涂两种不同颜色的零件,要设计分界特征,并且最小特征圆角为1.5mm。
3.边3.1密封边3.1.1行李箱下端3.1.1.1.为了使水排出止口,如图所示需要留出3.0mm的间隙。
3.1.1.2安装用止口应该具备恒定的高度和厚度(用于弯角的凸缘除外)。
3.1.1.3车门开口周围的止口厚度变化,包括制造变差的范围通常在1.8mm至6.0mm之间。
厚度的极端值会产生较高的插入作用力和密封条稳定性等问题。
3.1.1.4止口厚度的变化在任何位置不得超过一个金属板的厚度。
如果可能,仅可以使垂直的止口产生厚度变化,绝对不要使弯角半径产生厚度变化。
止口厚度的阶段变化会使密封条托架中的水渗漏。
3.1.1.5应该避免带有焊点的止口出现燃油和其它润滑油,这些物质会降低稳定性。
3.1.1.6止口结构类型及其优缺点3.1.2行李箱上端为了防止水从密封条止口泄漏并且进入行李舱,可按下面结构进行设计:3.1.2.1支架内的胶黏料或可发泡的热熔胶需符合漏水防止设计手册。
汽车零部件包装器具规范v2.0(原版)
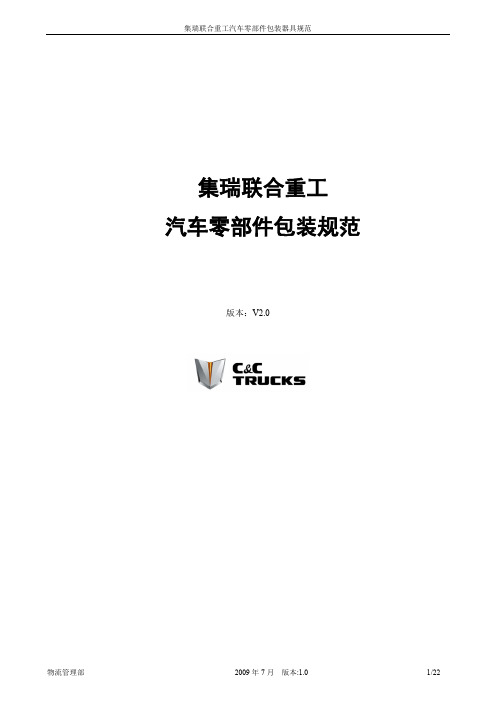
集瑞联合重工汽车零部件包装规范版本:V2.01.目的作为物流的始点,包装在物流中有重要的作用,同时对物流各环节有极大的影响。
对于复杂的汽车零部件物流,由于汽车零部件种类繁多、规格各异,生产装配工艺复杂,物流环节复杂等因素的影响,汽车零部件包装种类繁多,规格不一。
如不对其加以规范,将极大影响物流作业效率。
出于以上原因制定本包装规范,以满足精益生产、精益物流的需要。
2.适用范围所有集瑞联合重工供应商所供的生产用汽车零部件。
3.包装概述3.1包装定义国家标准《包装通用术语》中将包装定义为:1.包装为在流通过程中保护产品、方便储运、促进销售,按一定的技术方法而采用的容器、材料及辅助物等的总称。
2.指为了达到上述目的而采用容器、材料及辅助物的过程中施加一定技术方法等的操作活动。
3.2包装的定位包装是生产的终点,物流的始点。
作为物流的始点,包装完成后便具有物流的能力,在整个物流过程中包装便可以发挥对产品的保护作用。
如果包装是从生产的终点要求出发,就难以满足流通需要。
包装与物流的关系比与生产的关系要密切的多,作为物流始点的意义比作为生产终点的意义要大的多,因此包装属物流系统。
3.3包装在物流中的功能3.3.1.保护商品:保护商品不受外界影响和损伤是包装的首要功能,主要体现在以下几个方面:(1).防止商品破损变形(2).防止商品发生化学变化(如生锈、老化、发霉等)3.3.2.方便流通:(1).方便储存:在包装的规格、质量、形态上适合仓储作业,便于识别、存取、盘点、验收及分类等作业;(2).方便装卸搬运:适宜的包装便于装卸搬运,便于使用装卸搬运机械提高效率,标准的包装为集合包装提供了条件,并且能够极大提高装载能力;(3).方便运输:包装的形状、规格、质量与物品运输关系密切,尺寸与运输车辆、船、飞机等运输工具的容积相吻合,提高装载能力及运输效率。
4.包装原则原则:安全、质量、成本、人机工程、环保5. 包装分类5.1常用包装分类方式包装分类方式分类较多,按包装在流通中的作用可分为工业包装和商业包装,按包装层次不同可分为个包装、中包装、外包装,按包装使用次数可分为一次用包装、多次用包装和周转用包装,按包装适用性分类可分为专用包装和通用包装,等等。
提高汽车车身零件的三坐标测量
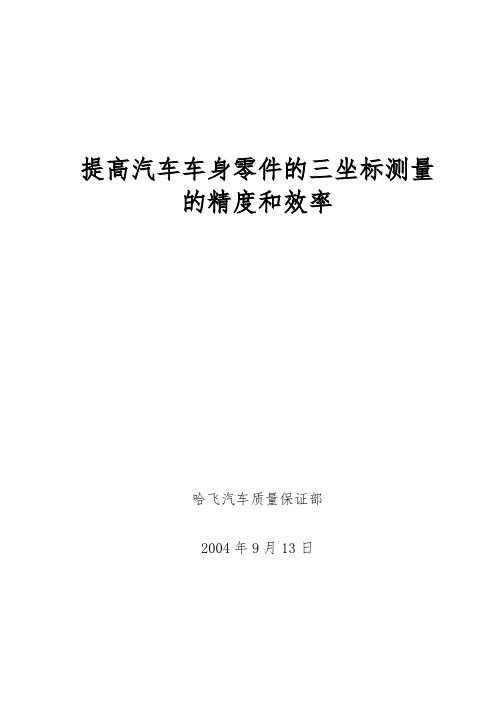
提高汽车车身零件的三坐标测量的精度和效率哈飞汽车质量保证部2004年9月13日目录一、建立正确的零件坐标系,是实现汽车车身零件精确测量的基础1、建立正确的零件坐标系的重要性2、建立坐标系的原则和基准的选择3、建立坐标系的方法和应用4、三阶平面在建立坐标系中的应用5、临时坐标系的运用6、建立零件坐标系过程的自动测量二、正确的零件夹紧方案是汽车车身零件测量精度的保证1、夹紧方案选择2、FIVE U-unique柔性夹具系统在车身零件夹紧定位上的应用三、测量方案的选取1、编制自动测量程序,实现车身零件的自动测量2、单件零件的测量3、矢量点的测量四、测量的准备阶段——探针的校准,是精确测量的保证和前提五、测量数据的处理和应用[摘要]:本文从零件坐标系的建立,测量基准的选择,测量方案的制定、测量夹紧方案的选择、以及自动测量程序的编写等方面内容,结合实际工作中积累的经验和研究对如何保证汽车车身零件的三座标测量的精度和提高测量的效率进行了论述。
[关键词]:三坐标测量机测量坐标系基准精度效率测量方案[前言]:随着汽车工业的高速发展,行业间的竞争也更加激烈,而质量是赢得竞争的基础,不论是对冲压件还是焊接总成零件的质量要求都越来越高,对测量工作也提出了更高的要求。
三坐标测量机以其快捷、精确、方便的特点在汽车制造业发挥着越来越大的作用,成为质量控制不可缺少的手段。
利用三坐标测量机强大的空间检测能力和分析计算功能可以实现对汽车车身零部件快速准确的测量,提供形状、尺寸、和位置的完善测量,并可执行包括首件检测、轮廓测量、逆向工程、焊接生产线的夹具调整、过程控制以及文件归档等在内的多种测量与检测任务,从而为降低开发研制周期,进行产品全过程控制,提高产品的质量,增加经济效益,提高产品的竞争力作出贡献。
简化测量机的使用方法、减少人机对话实现自动测量减少人为因素造成的误差、缩短测量工时提高利用率是三坐标使用中的主要课题和研究探索的方向。
江淮汽车检具通用要求

江淮汽车检具通用要求江淮汽车是国内知名的汽车制造企业之一,秉承“品质至上,用户至上”的宗旨,不断提升产品质量和用户体验。
为了确保江淮汽车的产品能够满足用户的需求,并达到国际标准,江淮汽车制定了一系列的检具通用要求。
以下是江淮汽车的检具通用要求:1.标准合格:检具必须符合国家和江淮汽车的相关标准,同时满足设计要求和制造工艺,确保产品的质量和可靠性。
2.检具稳定性:检具必须具有良好的稳定性和刚度,能够在长时间使用和高负荷工况下保持形状和精度,避免误差和变形。
3.测量准确性:检具的测量精度必须满足江淮汽车的要求,能够准确测量零部件的尺寸、形位公差和表面质量等指标。
4.可追溯性:检具必须具有可追溯性,能够追溯到原材料的批次、制造工艺和使用记录,以确保产品的质量可控。
5.检具定期校准:检具必须按照江淮汽车的规定进行定期校准,以确保其测量结果的准确性和可靠性。
6.检具保养和维护:检具在使用过程中必须进行保养和维护,保持其良好的工作状态和使用寿命,减少误差和损坏的可能。
7.检具标识和管理:检具必须进行标识和管理,包括检具的编号、用途、存放位置等信息,以方便使用、查找和管理。
8.检具记录和溯源:检具使用时必须有相应的记录,包括检具的使用时间、使用人员、使用目的等信息,并能够追溯到具体的生产批次和检具信息。
9.检具故障排查和处理:检具出现故障时,必须及时进行排查和处理,确保其正常使用和工作效率。
10.检具培训和技能提升:检具使用人员必须接受相应的培训和技能提升,提升其对检具的操作技能和质量意识。
总之,以上是江淮汽车的检具通用要求,江淮汽车通过严格的检具管理,确保产品的质量可控,提升用户满意度,为客户提供更好的产品和服务。
江淮汽车检具通用要求
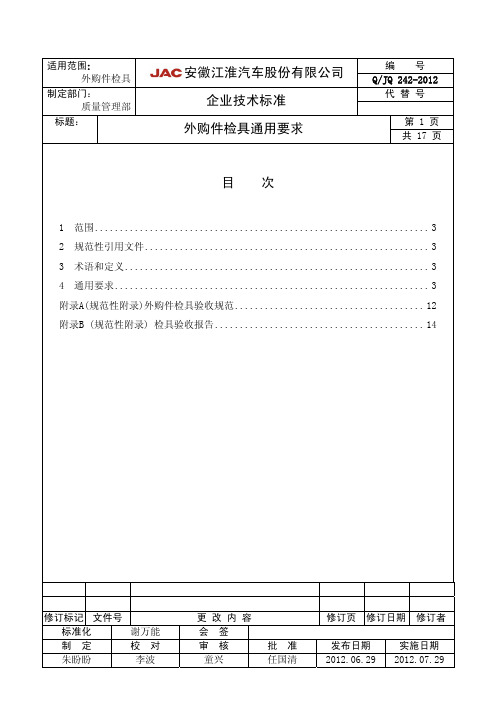
附录A(规范性附录)外购件检具验收规范...................................... 12 附录B (规范性附录) 检具验收报告.......................................... 14
修订标记 文件号 标准化 谢万能 制 定 校 对 朱盼盼 李波
更 改 内 容 会 签 审 核 童兴
修订页 修订日期 修订者 批 准 任国清 发布日期 2012.06.29 实施日期 2012.07.29
适用范围: 外购件检具 标题:
安徽江淮汽车股份有限公司 外购件检具通用要求 前 言
编 号 Q/JQ 242-2012 第 2 页 共 17 页
本标准《Q/JQ 242-2012 外购件检具通用要求》是公司质量综整车品质,严格控制外购件的质量要求,质量部门特编制此标准。 本标准由公司技术中心提出。 本标准由技术中心标准法规与信息管理部归口管理。 本标准起草单位:技术中心质量管理部。 本标准主要起草人:童兴 本标准参与起草人:谢万能 本标准为首次发布 李波 朱盼盼 王康平 蒲松柏 田伟琴 刘翠平
适用范围: 外购件检具 标题:
安徽江淮汽车股份有限公司 外购件检具通用要求
编 号 Q/JQ 242-2012 第 7 页 共 17 页
件的软硬等稳定性状况由实际情况酌情决定。必要时,有意考虑过定位,以增加零件 的稳定性。 -定位面和支撑面,原则上必须通常为可拆卸式镶块结构。 4.2.4.4 检测面 -各种类型零件的周边、翻边和零件断面的检测可以通过设置检具检测面来实现,检 测面检测包括:零件等距离 5mm 间隙检测(对于小型零件可以采用 3mm 检测)和周边 平整度检测。为此在型体 5mm 间隙上必须按 CAD 数据加工出 5mm(或 3mm)的间隙检 测面和周边平整度检测面。同时在相应检测面下部贴上提示铭牌或标记。如图 1。
大众汽车车身覆盖件检具设计技术要求

检具技术要求目录1. 目的 (3)2. 适用范围 (3)3. 责任 (3)4. 规定 (3)4.1 检具(测量支架)的概述 (3)4.2 检具设计与制造的技术要求 (4)4.3 检具和测量支架的验收和交付 (12)5. 存档 (13)6. 评审与更改 (14)7. 分发 (14)8. 附件清单 (14)附件一:关于检具定位销和检验销的说明 (15)1. 检具定位销概述 (15)2. 定位销A1的结构形式 (16)3. 定位销A2的结构形式 (19)4 . 零件检查销的结构和计算 (23)5. 轴套结构图示介绍 (26)附件二:检具(测量支架)认可流程 (28)附件三: 检具(测量支架)设计认可报告 (29)附件四:检具(测量支架)制造认可报告 (30)1. 目的通过制订《检具(测量支架)技术要求》,使检具(测量支架)在规划、设计与制造、验收与使用时,能够遵循统一的技术标准和评价指标。
2.适用范围本技术要求适用于车身检具及对零件型面尺寸或装配尺寸与车身坐标系统有关联的内外饰件的检具。
3. 责任***负责本技术要求的编制、维护、升级及分发等工作。
***零件供应商负责本技术要求在检具(测量支架)规划、设计、制造、验收和使用过程中的贯彻和执行。
4. 规定4.1 检具(测量支架)的概述4.1.1检具(测量支架)的定义检具是一种用来测量和评价零件尺寸质量的专用检验设备。
在零件生产现场, 通过检具实现对零件的在线检测,为此需要将零件准确地安装于检具上, 然后通过目测,或测量表,或卡尺对零件型面,周边进行检查,也可以借助检验销或目测对零件上不同性质的孔及零件与零件之间的联接位置进行目检,从而保证在试生产及起步生产时实现零件质量状态的快速判断。
在此情况下,通过目检或测量可以判断: 零件轮廓周边大小和形状区域以及相对位置与通过CAD/CAM直接加工的检具理论值之间的偏差。
对于零件上的某些极其重要的功能性尺寸,还能利用检具进行数值检测。
汽车白车身钣金零件定位与公差研究
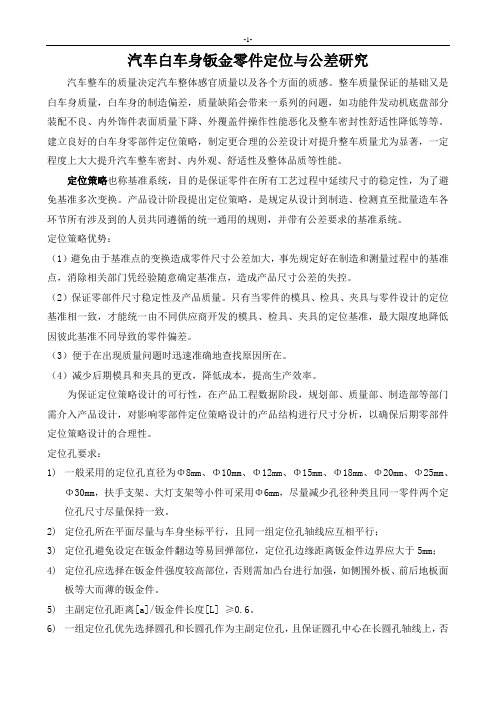
汽车白车身钣金零件定位与公差研究汽车整车的质量决定汽车整体感官质量以及各个方面的质感。
整车质量保证的基础又是白车身质量,白车身的制造偏差,质量缺陷会带来一系列的问题,如功能件发动机底盘部分装配不良、内外饰件表面质量下降、外覆盖件操作性能恶化及整车密封性舒适性降低等等。
建立良好的白车身零部件定位策略,制定更合理的公差设计对提升整车质量尤为显著,一定程度上大大提升汽车整车密封、内外观、舒适性及整体品质等性能。
定位策略也称基准系统,目的是保证零件在所有工艺过程中延续尺寸的稳定性,为了避免基准多次变换。
产品设计阶段提出定位策略,是规定从设计到制造、检测直至批量造车各环节所有涉及到的人员共同遵循的统一通用的规则,并带有公差要求的基准系统。
定位策略优势:(1)避免由于基准点的变换造成零件尺寸公差加大,事先规定好在制造和测量过程中的基准点,消除相关部门凭经验随意确定基准点,造成产品尺寸公差的失控。
(2)保证零部件尺寸稳定性及产品质量。
只有当零件的模具、检具、夹具与零件设计的定位基准相一致,才能统一由不同供应商开发的模具、检具、夹具的定位基准,最大限度地降低因彼此基准不同导致的零件偏差。
(3)便于在出现质量问题时迅速准确地查找原因所在。
(4)减少后期模具和夹具的更改,降低成本,提高生产效率。
为保证定位策略设计的可行性,在产品工程数据阶段,规划部、质量部、制造部等部门需介入产品设计,对影响零部件定位策略设计的产品结构进行尺寸分析,以确保后期零部件定位策略设计的合理性。
定位孔要求:1)一般采用的定位孔直径为Φ8mm、Φ10mm、Φ12mm、Φ15mm、Φ18mm、Φ20mm、Φ25mm、Φ30mm,扶手支架、大灯支架等小件可采用Φ6mm,尽量减少孔径种类且同一零件两个定位孔尺寸尽量保持一致。
2)定位孔所在平面尽量与车身坐标平行,且同一组定位孔轴线应互相平行;3)定位孔避免设定在钣金件翻边等易回弹部位,定位孔边缘距离钣金件边界应大于5mm;4)定位孔应选择在钣金件强度较高部位,否则需加凸台进行加强,如侧围外板、前后地板面板等大而薄的钣金件。
车身钣金件未注尺寸公差QCAF01 0300 P-42-2008
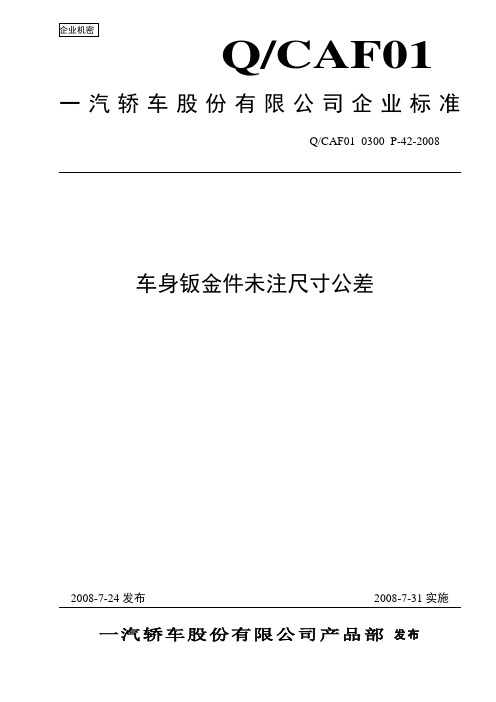
Q/CAF01车身钣金件未注尺寸公差一汽轿车股份有限公司产品部 发布Q/CAF01 0300 P-42-2008前言为保证冲压、折弯或拉伸工艺制造的汽车金属零件及其焊接总成的加工精度及其经济性,规范尺寸公差,特制定本标准。
本标准由一汽轿车股份有限公司产品部提出并归口。
本标准由一汽轿车股份有限公司产品部负责起草。
本标准主要起草人:籍龙慧I冲压件未注尺寸公差标准1范围本标准规定了通过冲压、折弯或拉伸工艺制造的汽车金属零件的通用尺寸公差。
本标准同时还包含在上述零件之间焊接成的总成以及上述零件与焊接螺母、焊接螺栓等焊接成的总成的通用公差。
2规范性引用文件下列文件中的条款通过本标准的引用而成为本标准的条款,其最新版本适用于本标准。
Q/CAF01 0300 P-43-2008 焊接螺栓的焊接质量3定义3.1 孔的直径:如图1,直径d。
3.2 孔位偏差:如图1,B与B′之间的偏移量(理论孔心与实际孔心之间的距离)。
3.3A:主定位孔的孔心B:制图上的孔心B′:实际孔心图13.4 修边线:如图2所示,线D。
3.5 翻边宽度:如图2所示,宽度E。
图23.6 焊接面的搭接深度:如图3所示,深度F。
3.7 焊接面的搭接位置:如图3所示。
搭接位置G。
3.8 焊接面:如图3和图4所示,表面H。
图3 图43.9 螺母或螺栓的位置偏差:如图5所示,I与I',J与J'之间的偏移量。
3.10螺母或螺栓的间距:如图5所示,I与J间的距离。
I -J:理论间距I′—J′:实际间距图53.11冲压件:通过冲床和模具对板材、带材、管材和型材等施加外力,使之产生塑性变形或分离,从而获得所需形状和尺寸的工件的成形加工方法,得到的工件就是冲压件。
4通用尺寸公差通用尺寸公差应按照表1执行。
4.1 如果在中间尺寸与最终尺寸之间应用通用尺寸公差有重叠,优先在最终尺寸上应用该标准。
4.2 焊接头部在支撑面上的焊接螺栓的焊接位置公差见Q/CAF01 0300 P-41-2008表1单位: 毫米注释:○1图纸上没有注明的间隙孔,应按照装配孔的位置公差标准执行。
汽车车身制图规范

汽车车身制图规范车身制图规范1 范围本标准规定了汽车车身制图的要求。
本标准适用于本公司汽车白车身产品图样。
2 规范性引用文件下列文件对于本文件的应用是必不可少的。
凡是注日期的引用文件,仅注日期的版本适用于本文件。
凡是不注日期的引用文件,其最新版本(包括所有的修改单)适用于本文件。
QC/T 490-2000 汽车车身制图3 术语和定义3.1 总成图表达产品中零部件间连接关系及反映其全部组成情况的图样,且包括装配(加工)与检验必需的数据和技术要求等内容。
表达两件或多件焊接(螺接)在一起的总成图,简称总成图。
3.2 零件图用于表达单个冲压件的图样。
3.3 A面本标准中所述A面系指:车身外部零件所形成的面,即车身外侧表面(含侧围、前后车门、后背门外表面、顶盖、发动机罩外表面、翼子板、加油口盖外表面)。
3.4 RPS定位点系统本标准中的RPS定位系统是指:零部件或总成的定位基准。
4 2D制图总要求(详细要求见第5~11)4.1 车身钣金零件按车身制图国家标准表达,应做到:a)按零件选择正确的基准(孔中心、面或线),将零件放置在车身坐标系内;b)对一般孔要求标注其孔径、孔中心坐标;c)装配孔要求标注孔径及孔径公差、孔中心坐标、孔中心距及公差要求并标注“XXX装配孔”字样;d)基准孔要求标注孔径及孔径公差、孔中心坐标、孔位置度公差;e)过孔要求标注孔径、孔中心坐标、过孔功能(如线束过孔)、位置度公差;f)零件的必要几何尺寸需标注;g)零件的技术条件(要求);h)比较复杂的曲面允许在数模测量,简单曲线应按车身制图表达;i)为使图面清晰,零件投影图中弯折部位的圆角与两侧面的切线不予表示,仅表示倒圆前的理论交线。
4.2 钣金总成图纸应做到:a)所表达的总成必须表达组成部件的基准(孔中心、面、线),然后放置在车身坐标系里;b)组成焊装部件的各零件的图号;c)焊装总成各零部件之间相对位置的控制尺寸;d)焊装总成焊点大小、位置的描述;e)总成内部件之间相对孔位及边界控制尺寸及公差表达;f)不允许有不必要的零件尺寸。
汽车车身零件通用定位要求

图6 图4 图5“□〞内为推荐优先选用孔径➢ 形状相似零件的定位孔孔距要求长度不一,防止错装;➢ 模具包边的零件定位孔建议采用翻边孔,以提高孔对销的导向作用,建议优先采用Φ16、Φ20两种尺寸; ➢ 受重力影响的零件如侧围外板、门内板,尽可能采用翻边孔定位。
5. 过孔的设计➢ 避让定位孔的过孔要求比定位孔直径至少大2mm ;➢ 避让螺母孔的过孔要求比螺母焊接定位孔至少大2mm ;➢ 具体内容参见?白车身孔数据通用标准?6. 定位面的要求➢ 设计的定位面的大小为20×20mm 、20×40mm 〔实际生产中夹具使用夹紧块截面宽度可能为12mm 、16mm 、19mm ,检具夹紧块较夹具更小〕,能够满足正常的工装需要;➢ 主定位面尽可能与主平面平行;➢ 定位面有足够的区域,以避让零件型面和止边,如下列图4,尺寸b 为满足零件定位面的区域,距离相邻的型面R 角距离大于5mm ,即b <a-10,如下列图5,定位面距离零件止边的距离大于3mm 。
7. 其它➢ 在焊接装配定位时要考虑定位销运动方向上有5mm 的定位销运动空间〔如图6〕,随销直径的增大,运动空间相应增大;➢ 减少零件的上定位,即减少翻销的使用;➢ 梁类件要在定位上防止装反、装错;工艺孔孔径大小 主定位孔Φ32、Φ□30、Φ□25、Φ□20、Φ□16、Φ□12、Φ□10、Φ□8、Φ6、Φ5 辅助定位孔〔长圆孔〕 32×38、30×36、25×31、20×26、16×20、12×16、10×14、8×12、6×10、5×9 SE 分析手册编号:SE-BP-#-001类别:定位 第 3 页 共 3 页 名称:零件通用定位要求图7图8目的:标准钣金件定位设置,满足焊接及车身精度根本需求➢ 两零件定位孔孔径、位置一样,即共用定位孔,原那么上只能使用一次,如图7,中间的共用定位孔在单件工位使用后,在分总成工位不得继续使用。
规控开发需要的车身参数

规控开发需要的车身参数
规控开发需要的车身参数包括但不限于:
1. 车身长度:汽车长度方向两个极端点间的距离,即从车前保险杆最凸出的位置量起,到车后保险杆最凸出的位置,这两点间的距离。
2. 车身宽度:汽车宽度方向两个极端点间的距离,也就是车身左、右最凸出位置之间的距离。
根据业界通用的规则,车身宽度不包含左、右后视镜伸出的宽度,即最凸出位置应在后视镜折叠后选取。
3. 车身高度:从地面算起,到汽车最高点的距离。
而所谓最高点,也就是车身顶部最高的位置,但不包括车顶天线的长度。
4. 轴距:汽车前轴中心至后轴中心的距离。
5. 轮距:同一车轿左右轮胎胎面中心线间的距离。
6. 前悬:汽车最前端至前轴中心的距离。
7. 后悬:汽车最后端至后轴中心的距离。
8. 最小离地间隙:汽车满载时,最低点至地面的距离。
9. 接近角:汽车前端突出点向前轮引的切线与地面的夹角。
10. 离去角:汽车后端突出点向后轮引的切线与地面的夹角。
此外,还有最大总质量、最大装载质量、最大轴载质量等参数。
如需更多信息,建议查阅关于规控开发需要的车身参数的资料,或咨询汽车行业专业人员。
汽车设计-汽车车身用标准件选型规范模板
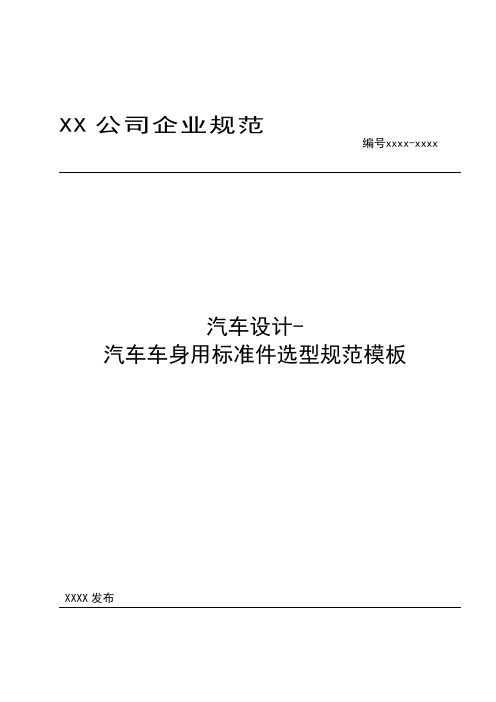
XX公司企业规范编号xxxx-xxxx汽车设计-汽车车身用标准件选型规范模板汽车车身用标准件选型规范1 范围本规范主要介绍了车身所用标准件的常见类型,阐述了各类标准件在车身上的应用及选取则,包括螺栓长度的选用、螺栓和螺母公称直径的选用、螺纹牙距的选用、特殊螺栓、螺母的选用等,为以后车身标准件选用提供一个参考。
本规范适用于众泰轿车、SUV等车型的设计。
2 规范性引用文件下列文件对于本文件的应用是必不可少的。
凡是不注日期的引用文件,仅注日期的版本适用于本文件。
凡是不注日期的引用文件,其最新版本(包括所有的修改单)适用于本文件。
GB/T3098.1 紧固件机械性能螺栓、螺钉和螺柱GB/T3098.2 紧固件机械性能螺母粗牙螺纹GB/T3098.3 紧固件机械性能紧定螺钉GB/T3098.4 紧固件机械性能螺母细牙螺纹GB/T3098.5 紧固件机械性能自攻螺钉GB/T5779.1 紧固件表面缺陷—螺栓、螺钉和螺柱GB/T5779.2 紧固件表面缺陷—螺母GB/T94.1 弹性垫圈技术条件弹簧垫圈QC/T607 六角螺母和锥形弹性垫圈组合件GB/T5783 六角头螺栓—全螺纹—A和B级GB/T5789 六角法兰面螺栓—加大系列—B级GB/T1664 六角法兰面螺栓GB/T2673 内六角花形沉头螺钉GB/T29.2 十字槽凹穴六角头螺栓GB/T5782,GB/T5783 六角头螺栓—粗牙GB/T5785,GB/T5786 六角头螺栓—较细牙GB/T6177 六角法兰面螺母GB/T6560 十字槽盘头自攻锁紧螺钉GB/T70 内六角圆柱头螺钉GB/T819 十字槽沉头螺钉GB/T845 十字盘头自攻螺钉GB/T847 十字槽半沉头自攻螺钉QC/T613 六角法兰面自排屑螺母GB/T9074.1 十字槽盘头螺钉和平垫圈组合件GB/T9074.3 十字槽盘头螺钉和弹簧垫圈组合件GB/T9074.14 六角头螺栓和平垫圈组合件GB/T9074.15 六角头螺栓和弹簧垫圈组合件GB/T9074.17 六角头螺栓、弹簧垫圈和平垫圈组合件GB/T9074.18 十字槽盘头自攻螺钉和平垫圈组合件GB/T9074.19 十字槽盘头自攻螺钉和大垫圈组合件GB/T9074.4 十字槽盘头螺钉、弹簧垫圈和平垫圈组合件GB/T9456 十字槽凹穴六角头自攻螺钉GB/T96 大垫圈GB/T95 平垫圈QC/T330 A型簧片螺母QC/T340 六角法兰面承面带齿螺栓QC/T602 十字槽大半圆头自攻螺钉GB/T6187 全金属六角法兰面锁紧螺母GB/T 16823.1 螺纹紧固件应力截面积和承载面积GB/T10125 人造气氛腐蚀试验盐雾试验QC/T625 汽车用涂镀层和化学处理层QC/T326 汽车标准件产品编号规则3 汽车车身所用标准件常见类型汽车车身所用标准件常见类型主要分为三大类:螺栓、螺钉和螺母,每一类又根据是否焊接和结构形式的不同分为若干类,常见的类型列举如下。
- 1、下载文档前请自行甄别文档内容的完整性,平台不提供额外的编辑、内容补充、找答案等附加服务。
- 2、"仅部分预览"的文档,不可在线预览部分如存在完整性等问题,可反馈申请退款(可完整预览的文档不适用该条件!)。
- 3、如文档侵犯您的权益,请联系客服反馈,我们会尽快为您处理(人工客服工作时间:9:00-18:30)。
32×38、30×36、25×31、20×26、16×20、12×16、10×14、8×12、6×10、5×9
“□”内为推荐优先选用孔径
形状相似零件的定位孔孔距要求长度不一,避免错装;
模具包边的零件定位孔建议采用翻边孔,以提高孔对销的导向作用,建议优先采用Φ16、Φ20两种尺寸;
3.定位精度
1)位置
将高精度的装配孔/点设为定位孔/点,以保证其最终定位精度;
定位孔之间的距离应该大于该件在此平面最大距离的三分之二;
零件定位孔所在面需为平面设计,不可在曲面上;
定位孔处零件刚性相对较好;
同一零件定位孔法线方向尽可能相互平行,并尽可能缩减同一零件/总成的定位孔平面间距离;
大型零件、总成主定位孔须与设计主平面平行;
尽可能避开焊点位置;
杜Байду номын сангаас定位孔径向受力;
降低装配难度。
2)数量
确保零件装配稳定,定位点须合理使用,谨慎使用过定位。
3)误差积累
误差积累方向为从上到下、从左到右、从前到后;
定位点的统一与延续性及误差积累方向的一致性;
模块化生产方式贯穿其中,须有误差消减措施;
在车身装配工序上,X、Y、Z方向上都要有可以消减误差的滑动平面。
受重力影响的零件如侧围外板、门内板,尽可能采用翻边孔定位。
5.过孔的设计
避让定位孔的过孔要求比定位孔直径至少大2mm;
避让螺母孔的过孔要求比螺母焊接定位孔至少大2mm;
具体内容参见《白车身孔数据通用标准》
6.定位面的要求
设计的定位面的大小为20×20mm、20×40mm(实际生产中夹具使用夹紧块截面宽度可能为12mm、16mm、19mm,检具夹紧块较夹具更小),能够满足正常的工装需要;
半圆形定位孔(豁孔)只针对小件(最大尺寸小于300mm)使用,如图8,但需注意豁口处定位的直线段长度大于2mm,(即定位孔大于半圆形状)。
更改记录:
时间
更改人
要点记录
N
4.定位孔的要求
孔径与所定位零件重量相匹配,如料太薄,可采用翻边孔、台阶孔,翻边孔的翻边直线部分不得少于3mm;
定位孔大小要求如下表:
SE分析手册
编号:SE-BP-#-001
类别:定位
第2页共3页
名称:零件通用定位要求
目的:规范钣金件定位设置,满足焊接及车身精度基本需求
工艺孔
孔径大小
主定位孔
Φ32、Φ 、Φ 、Φ 、Φ 、Φ 、Φ 、Φ 、Φ6、Φ5
减少零件的上定位,即减少翻销的使用;
梁类件要在定位上防止装反、装错;
SE分析手册
编号:SE-BP-#-001
类别:定位
第3页共3页
名称:零件通用定位要求
目的:规范钣金件定位设置,满足焊接及车身精度基本需求
两零件定位孔孔径、位置相同,即共用定位孔,原则上只能使用一次,如图7,中间的共用定位孔在单件工位使用后,在分总成工位不得继续使用。
定位方式的选择建议优先选择图1,对于大且刚性较差板件优先选择图2、3。
尽可能实现圆孔、椭圆孔定位,避免使用方孔、不规则孔等定位;
两孔定位方式优先于其它形式定位,除非有特殊需求及孔定位结构上不合理;
对于不上夹具的小零件可以采用凸点定位;
减少采用螺母孔定位方式;
对于装配精度要求较低的结构件,可采用翻边自定位、简化的捆绑、夹持等定位形式,以简化夹具。
主定位面尽可能与主平面平行;
定位面有足够的区域,以避让零件型面和止边,如下图4,尺寸b为满足零件定位面的区域,距离相邻的型面R角距离大于5mm,即b<a-10,如下图5,定位面距离零件止边的距离大于3mm。
7. 其它
在焊接装配定位时要考虑定位销运动方向上有5mm的定位销运动空间(如图6),随销直径的增大,运动空间相应增大;
SE分析手册
编号:SE-BP-#-001
类别:定位
第1页共3页
名称:零件通用定位要求
目的:规范钣金件定位设置,满足焊接及车身精度基本需求
内容:
1.应用范围
钣金件及具备一定刚性的装配附件
2.定位原则
N-2-1原则,随零件的大小、板件刚性的强弱,N的数量也不同;
确保焊接可以实施;
定位孔连线方向与车身坐标系方向尽可能平行,定位面尽可能与主平面平行;