重要工程品质检查表(丰田)中文版
日本施工质量检查表
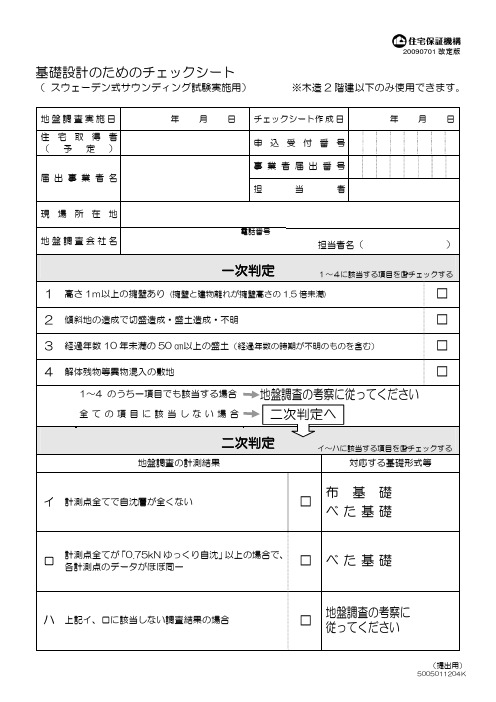
□
地盤調査の考察に 従ってください
(提出用)50050Fra bibliotek1204K□ □ □ □
地盤調査の考察に従ってください 二次判定へ
レ イ~ハに該当する項目を□チェックする
二次判定
地盤調査の計測結果
対応する基礎形式等
イ
計測点全てで自沈層が全くない
□
布 基 礎 べた基礎
ロ
計測点全てが 「0.75kN ゆっくり自沈」 以上の場合で、 各計測点のデータがほぼ同一
□ べた基礎
ハ
上記イ、ロに該当しない調査結果の場合
20090701 改定版
基礎設計のためのチェックシート
( スウェーデン式サウンディング試験実施用)
地盤調査実施日 住 宅 取 得 者 ( 予 定 ) 届 出 事 業 者 名
担 当 者 年 月 日
※木造 2 階建以下のみ使用できます。
チェックシート作 成 日 年 月 日
申 込 受 付 番 号 事 業 者 届 出 番 号
現 場 所 在 地
電話番号
地盤調査会社名
担当者名(
)
一次判定
1 2 3 4
レ 1~4に該当する項目を□チェックする
高さ 1m以上の擁壁あり (擁壁と建物離れが擁壁高さの 1.5 倍未満) 傾斜地の造成で切盛造成・盛土造成・不明 経過年数 10 年未満の 50 ㎝以上の盛土(経過年数の時期が不明のものを含む) 解体残物等異物混入の敷地 1~4 のうち一項目でも該当する場合 全ての項目に該当しない場合
丰田5S检查100条

整顿
丰田5S检查100条
判定重点 1.工作台上的消耗品,工具,治具,计测器等无用或暂无用物品须取走 2.生产线上不应放置多余物品及无掉落的零件 3.地面不能直接放置成品,零件以及掉有零部件 4.不良品应放置在不良品区内 5.作业区应标明并区分开 6.工区内物品放置应有整体感 7.不同类型,用途的物品应分开管理 8.私人物品不应在工区出现 9.电源线应管理好,不应杂乱无章或抛落地上 10.标志胶带颜色要明确(绿色为固定,黄色为移动,红色为不良) 11.卡板,塑胶箱应按平行,垂直放置 12.没有使用的治具,工具,刃物应放置在工具架上 13.治具架上长期不使用的模具,治工具,刃物和经常使用的物品应区分开 14.测量工具的放置处应无其他物品放置 15.装配器械的设备上不能放置多余物品 16.作业工具放置的方法是否易放置 17.作业岗位不能放置不必要的工具 18.治具架上不能放置治具以外的杂物 19.零件架,工作台,清洁柜,垃圾桶应在指定标志场所按水平直角放置 20.消耗品,工具,治具,计测器应在指定标志场所按水平直角放置 21.台车,棚车,推车,铲车应在指定标志场所水平直角放置 22.零件,零件箱应在指定标志场所水平直角整齐放置 23.成品,成品箱应在指定标志场所整齐放置 24.零件应与编码相对应,编码不能被遮住 25.空箱不能乱放,须整齐美观且要及时回收 26.底板类物品应在指定标志场所水平直角放置 27.落线机,样本,检查设备应在指定标志场所水平直角放置 28.文件的存放应按不同内容分开存放并详细注明 29.标志用胶带应无破损,无起皱呈水平直角状态 30.标志牌,指示书,一口标准,工程标志应在指定标志场所水平直角放置 31.宣传白板,公布栏内容应适时更换,应标明责任部门及担当者姓名 32.休息区的椅子,休息完后应重新整顿 33.清洁用具用完后应放入清洁柜或指定场所 34.通道上不能放置物品 35.不允许放置物品的地方(通道除外)要有标识 36.各种柜,架的放置处要有明确标识 37.半成品的放置处应明确标识 38.成品,零部件不能在地面直接放置 39.不良品放置区应有明确规定 40.不良品放置场地应用红色等颜色予以区分 41.不良品放置场地应设置在明显的地方 42.修理品应放置在生产线外 43.零件放置场所的标识表示应完备 44.塑胶箱,捆包材料上应标明品名 446.应下功夫大概在放置位置放手就能放置作业工具 47.作业工具放置处应由余量 48.治具,工具架上应有编码管理及有品目表示 49.在架子前应能清楚辨明上面的编码 50.治具,工具架应导入用不同颜色标识区分 51.治具是否按使用频率放置,使用频率越高的放置越近
焊接工序点检表-丰田内部使用

有 有 x
公司名 点检日 年 月 <发行部门> 日 工厂 科 工厂名 丰田认定监查员 批准者 确认者 点检者 工序名 车种 设备 机器人・自动机・半自动 机器编号 产品编号 ▽S 有・无 品 名 换模 有・无 <评价方法:从100分为满分扣分的方式> 评价点 点 计算式:100点-(a)-(b) ○:良好 △:要改善(一般项目提问) ○良 好 项目 ▲:要改善(★:重要项目提问) ―:不符合0分 △要改善 项目 × -2.5点= 点・・・(a) ―:如不符合的项目合计时打2.5分/项目 ▲要改善 项目 × -2.5点 = 点・・・(b) ・ 是否合格判定基准:右表的B级别 ―不符合 项目 (重要项目全部齐全+得分90分以上)。 综合判定:
有 有 有 有 x x x x 有 有 x 有 有 [第5次改订] 07.5.15
16 操作盘标识自动入・焊接切时(或者焊接中途按下焊接切的按钮)设备不会自动喷射 x 17 焊丝用完的时候不发生焊接缺陷 18 焊接机异常停止时,按下夹具的「ON」键马上停止
x
目前使用的是 手工CO2气保
33 与品质相关的保全都进行品质确认结果的记录 34 为了防止试做品流到下道工序,对试做部件进行识别
35 更新因损伤・磨耗等的焊枪・工装夹具时,实施铁丝瞄准轨迹和切断检验 36 「异常处理要领书」张贴在生产线上并进行遵守 37 明确返修作业指定者,返修品由第三者进行确认 (关闭生产线作业的情况) ★38 明确了焊接时中途抽出品的处理方法 39 标明了异常处理者及不良品处理责任人的名字
★21 20个指示项目符合技术要求,并且与现状一致 22 不能出现焊枪和工装以及部品之间的干涉 8 手动焊接 (半自动) 23 有防止忘记焊接的体制 24 标准作业书上明确标明了「焊接数」・「焊接位置」・「焊接顺序」
BP FV 50项 检查表
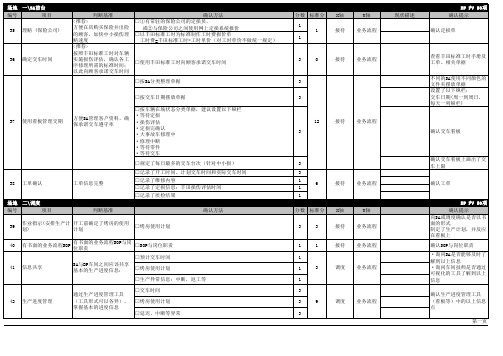
11 烤漆房的清洁状态 12 安全作业 13 员工休息场所
用指尖接触不会沾染灰尘
基本的安全护具
穿戴了施涂原子灰的安全 护具 穿戴了打磨原子灰的安全 护具 穿戴了施涂中涂底漆的安 全护具
穿戴了施涂面漆的安全护 具
为员工提供有以下休息场 所,营造出干净整洁有助 于提高工作效率的环境
□烤房四壁、地面、空气软管无灰尘附着 □工作服 □帽子 □棉手套 □安全鞋
1
1 喷漆综合 KPI
47 收益统计 48 尘点统计 49 品质统计 50 效率统计
1 技术资格与水平
统计了收益 KPI
确认工具数量
确认技师通过目视、手触 、直尺, 用白板笔标记出钢板的损 伤范围
第二页
23 去除旧漆膜
场地 四\喷漆车间
编号
项目
3 工具车的整理状态
4 干燥设备能正常使用 5 遮蔽材料
彻底清除损伤范围的旧漆 膜,尽量减少扩大钢板的 二次损伤范围
判断基准 没有不能使用的工具和辅 料 工具、辅料的摆放整齐有 序 无异常故障
□焊接面罩
□更衣室
□休息室
□沐浴室
□洗手间
□使用环氧底漆粉刷地面,颜色柔和
□地面要防滑,易于清洁
□划分出工位、工位号和过道区域
□划分出工具设备的摆放区域
□工位标有序号且标识了工位用途
□地八卦:4.5m*8.0m
15 工位尺寸
达到以下参考标准
□大量校正:5.5m*8.0m
16 照明
达到以下参考标准
17 气体保护焊机的保养 保养良好工作正常
3
3 钢板修正 品质
现状描述
·询问SA是否根据交车看 板每天在固定时间确认维 修进度 ·询问SA,当发生异常 时,车间是否主动提供过 异常信息
TPS丰田生产方式中文版(完整版)

1)自主保全 ・・・ 由制造部门实施
・第一阶段
・第二阶段
①・清扫
①・小改善
②・日常点检
②・定期换油
③・定期点检
③・定期更换
④・小维护、调整 ④・小修理(更换部件)
⑤・小停顿的恢复作业
・把握设备的功能、性能。 ・明白正常和异常。 ・掌握保全的知识和技能。
2)专业保全 ・・・由保全专业部门实施
・预防保全 ・・・ 有计划的实施 ・事后保全 ・・・ 缩短修理时间(KY训练、备齐备件)
1
TPS: Toyota Production System
丰田生产方式
・制造方法:彻底地实行JIT和自働化 ・通过TOTAL・TPS 推进成本降低
使现场充满活力
TOYOTA ENGINEERING CORPORATION 丰田ENGINEERING株式会社
2007. 10
HORIKIRI OZAWA SUZUKI
生产改善活动 生产活动
・工序改善 ・物流改善
自主研究会、生产会议
原来的TPS
业务范围 的扩展
16
・〔3〕:TOTAL-TPS的具体开展
・
1:现场的活性化 2:现场的可视化 3:作业改善
・每天的改善活动 ・营造有工作意义
的现场
4:物流改善
5:品质改善
7:改善的推进方法
8:制造工序的评价
6:新产品投产业务
成本
制造经费 加工费、物流费
②
材料、零部件费
4
〔2〕:从TPS到TOTAL-TPS的发展
TPS的发展
2007th
Profit 利润、利益
TPS的基本(2个支柱)
①・JIT(Just in Time) ②・自働化(Jidouka)
丰田全球安全大检查点检确认表-07.6

所有的都没有 伤痕 全部没有 全部没有 确实分离 不错 最大的倾斜角 度 确实实施 (有左右确认) 确实管理 确实管理 可以随时训练 、教育 有设备对措措 施 有升降设备 确实遵守 没有 有设备对措措 施 有设备对措措 施 不错 没有危险处し
(有设备对策)
不错 几乎看不到 几乎看不到 实施物体对策 好 有作业规定 不错
没有 有安全锁制度 没有 全有 有1~2处 全有 有1~2处 反馈结果 全部实行 一部分实行
调查日 评价水平 4 有动作
全员传达 一部分传达 明确责任 有机能 有机能 全部实行 全部实行 全部实行 全部实行 全部实行 一部分实行 一部分实行 一部分实行 一部分实行 一部分实行 有记录 有 有 有 有 有制度 有制度 有制度 有制度 有制度 有设备备品 有制度
有一些制度 几乎有设置 普通 设置几乎有 有规定 不好
非常不好 没有规定
在重量物下的工作
有规定并实行
评价水平 区分 项目 # 确认要点 5 理想状态 9 设备、棚等的摔到防止
有设备对措措 施 有设备对措措 施 有规定正确实 施
没有对象
4 有动作
3
2 有组织
1
0 无管理
无管理状态 (不知道) 无管理状态 (不知道) 有危险行为 显眼状态 无管理状态 (不知道) 没有规定,非 常不好
判定基准)
可以随时训练 、教育 非常好 好
取得者管理 普通
全员取得 有制度
一部分未取得 危险驾驶
15 车辆的碰伤 16 地面的轮胎痕迹 17 固定物的伤゙(墙壁、柱子、设备、门等) 18 车辆和人(常规作业场)的混在 车辆 (200) 设备・工 程 (600) 19 堆积货物的状态(叉车・牵引车・卡车等) 20 叉车的叉子(后倾)操作(一般的货物) 21 交叉点的突然停止 22 车辆钥匙的管理 23 人和车辆的分离制度(禁止入内的措施等) 24 产业车辆的驾驶资格(叉车、牵引车、其 他) 25 防止高空作业区域的摔落措施(栏等) 坠落 26 高空作业的信息发送(升降设备) 27 高空作业 触电 高热物 28 电器设备的破损(分电柜的门等) 29 防止向超高电压设备的接近(围圈・表示 等) 30 高热物使用作业场(熔汤工程等) 31 作业环境(烟・水蒸气・噪音・暑热・冷感) 其他 32 缺氧危险作业场(升降口・地下室等)
丰田汽车班组业务管理(最详细)ppt课件
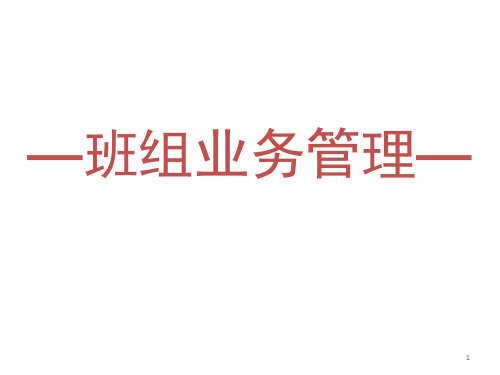
管理频率
帐票
每日
各类设备点检表 各类工装夹具点检表 停链记录表
业务日报表
周间
9
1.1.4 M领域业务
工作项目
管理频率
帐票
班前后会
考勤管理
考勤表
人员身心情况判定
操作者岗位安排 人员培训计划的实施
每日
工程管理表 工程训练表
员工工作●情困况记难录点: 小组长工1作、的探指亲导(假骨干及业年务休指等导)有薪假期的消化; 日常面谈2、劳动强度对应岗位调整; 绩效考核3、工会、团及党相关工作的支援……
确认 项目
生产目标
②
- 出勤确认 - 员工身体状况确认 - 精神状态确认 - 问候语、结束语 ③
确认 出勤
- 生产安排(车型投入批次、 预定时间、零件计划,个别 岗位调整等)
39
■ 练习
<主题>
请学员模拟开班前会,说明班前会的要点。 (1人扮演班长,5人扮演员工)
15分钟
40
『早会具体实例』
序号 1 排列队伍 2 人员出勤确认(精神状态等)
■ 清扫
实质:里里外外打扫干净。
重点:真正目的是发现问题!!
(关键词:清扫≠大扫除;点检)
难点:清理卫生死角!!
20
■ 清扫
车间地面到处 都是油渍、存 在安全隐患。
清扫前
清扫后
通道整齐、美 观给员工提供 安全、舒适的 工作环境。
■ 清洁
实质:保持上面3S的成果。
手法:制度化、标准化!! 难点:持之以恒!!
通道整齐、美观给员工提供安 全、舒适的工作环境。
1.2.3 5S的效能
讨论:开展5S有什么好处?
5S能为我们做到:
完整版丰田品质管理QC7大工具

*在最初的教育资料(P66,67)检查的作用説明
(4)察觉异常和源流对策 (5)实施对策后的跟踪和确认 (6)对自工程条件的预先控制
19
检查本身是不必要的
品质用检查来保证就是好的 ×
生产 工程 →→→→
原因无法反馈
工数
→ 检查
合格品
→
出库
↓ 不合格品
废弃
成本
不合格品在检查中被检出的体制
? 作业者对于制品
把「与平常不同 」这样的感觉作为
异常进行报告
21
关键词 15
「如实说明是职场的氛围」
22
P70
「如实说明是职场的氛围」 将事实及其关联情报如实报告 管理者的批评?生气 「如果如实报告的话就是损失」
隐瞒事实、欺骗这种阴沉的职场气氛的创造 不能捕捉不良,发现异常、不能实施根本的解决不良的对策
不成立时如何复原
28
P74
(3变)化点的可 视化
有管理板的话是否有管理没判断? 往往做不到可视化?
可视化是一种工具如果不与相关行动相连是毫无意义的。
这种工具不用于记录,而用于引起成员注意 用于判断下一步行动如何进行,确认对应状况(OK/NG ), 复原维持管理状态
29
用语要点 17
什么是可视化
30
是否质问 「为什么不按教育内容,标准来作业?」
不遵守标准,实际上“按标准难以操作”的情况比较多…
「有没有什么难以操作的地方?」
这种“根本性的 询问”很重要
17
Ⅳ.日常品质管理
18
P66
5.维持管理
在日常生产中「维持?管理」的关键点
(1)彻底遵守规则 (2)正确的工程管理=尽早检查出异常&对策
丰田原版教材QC七道具

(2)画帕雷托图
(千元) 180 160
140
120
基于 表1 的数据画出的帕雷托图如下
期间 8 / 1 ~ 3 损失金额合计: 162 千元 作成日 9 / 2 作成者 加藤
100 80 60
100 (%) 80 60 40
40 20
20
0
0
盒饭 肉 蔬菜 蛋糕 包子 水果 报纸 饮料 其他
图2 积 压 商 品 种 类 帕 雷 托 图
///// / ///// /
8 46
数据与分类
程序4 分析数据查明原因
了解的事情 1.每天的变化不大,山田比铃木出的不良多。 2.山田在那条线作业出的划痕都比磕碰要多。
QC七道具(点检表)
点检表是“取各种数据,避免漏确认,仅进行确认即可得到结果的图 或表。” 点检表的画法: 程序 1.确定点检表的目的和取哪种数据。
形状复杂
切
粉
洗净水がかかない が 取
切削位置变更
泵能力不足 泵能力不足
れ
出水量变更
恶化
恶化
な い
位置偏 接近
水量少 水压低
标准品
压力低
管径小
联络少 设定值变更
作成者: 水野 柴田 中野
洗净ノズっ
洗净水
作成日:****年**月**日
图 1 [切粉が取れない]的特性要因图 (オイルフィルタ-プラケット切削后の洗净工程)
数据和分类
(3)要有无论什么都数据化的想法
*即便确定了想要的数据也会遇到难以数值化、 没有测定仪器、没有时间等问题。
*但是,不屈服,“无论什么都数据化”的努
力和意识才是重要的。
(4)数据要清晰
*为了不要出现“这个数据是哪里来的,干什么用的 都不明白‘的情况,要明确数据的要素。(测定 的目的,特性值的种类,测定日,测定器,测定 人,测定方法等要写清楚。)
工程品质管理表HW-2

隔纸板4件 370×240×3mm 包装工
打包机
捆绑有力 设备部
目测
与纸箱配 合
与纸箱配 合
操作
工作中 工作中 工作中 工作中
工程名 故 重
工 设备名 障 要
序 供应商 类 项 编 名 型目号
管理项目
工 程 品 质 管 理 表 (2)
品质特性
规格值
担当
检查方 法
检查 频度
数据 形式
重 数据提 要 出频度 项
4 浇口,渣包断口. 5 分型面披锋及顶
针印毛刺. ※ 6 碰伤痕,冷隔纹. ※ 7 顶针印
8 孔径 9 孔径 ※ 10 定模面平面平面度.
不允许 不允许 不允许 打磨平整 挫净,刮平
擦去 0+0.10-0.25mm 4-φ10.5mm
4-φ5mm ≤0.4mm
查包工 查包工 查包工 查包工 查包工 查包工 查包工 查包工 查包工 查包工 查包工
项 目 管理项目 管理值
担当
检查方 检查 数据 法 频度 形式
砂带机
工作稳定 设备部 操作 工作中
砂带
#
120
打磨工 目测 工作中
7 除毛刺
1 分型面披锋及顶 针印毛刺.
※ 2 碰伤痕,冷隔纹.
挫净,刮平 手锉工 目测
全数
擦去
手挫工 目测
全数
8 终检
※ 1 散热片崩角,欠铸. ※ 2 表面冷隔,碰伤. ※ 3 定模面顶针位顶凸.
压铸机 模具 压铸工艺 参数
500T GY10 按工艺卡
压铸工 按机型 压铸工 按型号 压铸领班 目测 工艺员
每次 每次 4次/班 记录表
4-φ10.5mm 压铸巡检 卡尺 4次/班 记录表
丰田检查表送付用390391422工程调査のチェックシート(电着涂装、Znめっき)
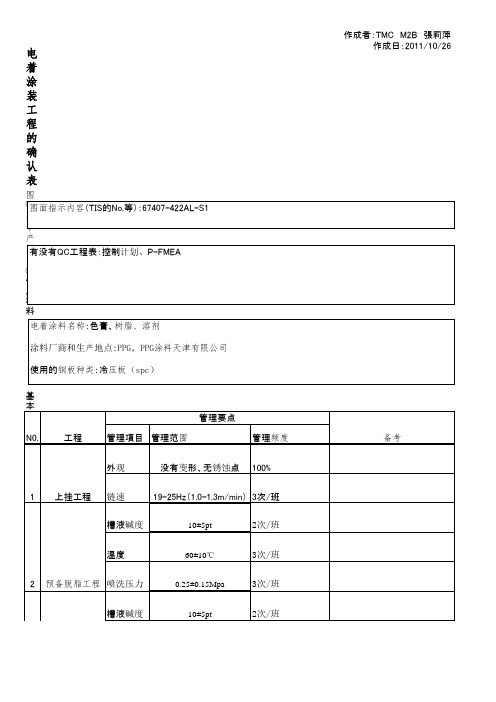
60± 10℃
0.25± 0.15Mpa
10± 5pt
60± 10℃
3
脱脂工程
喷洗压力
0.25± 0.15Mpa
3次/班
喷洗压力
0.25± 0.15Mpa
每班3次记录
4
水洗工程
温度
常温
作成者:TMC M2B 張莉萍 作成日:2011/10/26 表调剂V6513 量:3‰-5‰ pH8.5±1 每班2次化验 含 喷洗压力 5 表面调整工程 温度
0.15± 0.05Mpa 常温
3次/班 3次/班 1次/月
12
涂装干燥炉
3次/班
漆膜厚度、外观、焊接件 检验指导书是否掉落 100% 出货前最终检 外观 14 查
外观无划痕、气泡、麻点 、针孔
1次/批次
15 其他管理项目
作成者:TMC M2B 張莉萍 作成日:2011/10/26
作成者:TMC M2B 張莉萍 作成日:2011/10/26
管理频度 1次/1个工作日 1次/1个工作日 1次/1个工作日 1次/1个工作日 1次/班 3次/班 3次/班 3次/班 3次/班 1次/班 3次/班
备考
9
电着工程
10
水洗液回收再洗工程
温度 喷洗压力
3次/班
11
水洗
温度
干燥温度 干燥時間 温度分布 烘干时间 UF装置 13
喷洗压力 温度
180±20℃ 30±5min 炉温曲线图 25-35min
室温 电导率≤100μ m.cm-2 1次/班
电导率≤10μm.cm-2
每班3次记录
作成者:TMC M2B 張莉萍 作成日:2011/10/26 管理要点 N0. 工程 管理項目 管理范围
丰田审核检查表
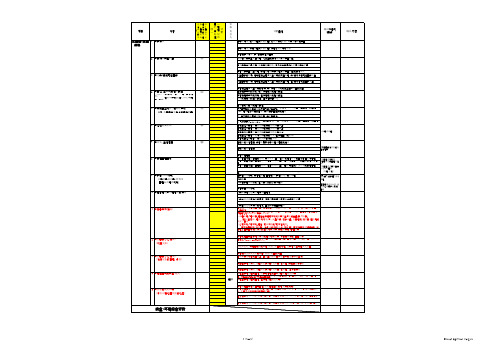
没有设计担当的组织 根据中长期开发计划,在考虑了培训教育必要周期的基础上,确保了设计人员的配置数 量 *根据中长期项目定点计划(目标)实施了设计所需工数的计划
虽然确保了现状所需的设计人员,但是中长期计划不明确
・设计人员招聘计划
*把握并确保了现有项目的必要工数
没有确保足够的设计人员
根据中期开发计划,确保了CAD等基础配备
9 ■教育・训练体制 *特别是设计者・检查员 管理人员培养机制
10 ■是否有违反环境相关的法规
没有防止再次发生对策的方法。或、没有讨论如何防止再次发生的打算 有防范于未然的体制、同时没有明显的危险部位 没有防范于未然的体制、但没有明显的危险部位 认识到有明显的危险部位、但没有改善计划
四处有可见明显的危险部位 有把握国家/汽车行业规定的禁用物质、削减使用物质、以及安全卫生上容许的基准 值,并了解本公司的现状水平、并满足基准。 另外、有设定本公司的目标、并开展改善提升的活动 有把握国家/汽车行业规定的禁用物质、削减使用物质、以及安全卫生上容许的基准 值,并了解本公司的现状水平、并满足基准。
・BMC报告书 ・BMC计划书 ・BMC结果的活用事例 (设计・评价标准 的修订等)
・问题集 ・设计检查表
・设计标准程序 ・SE实施要领 ・SE提案书
没有实施SE活动 有使用CATIA进行零件开发的实绩 *3个项目以上
有CATIA,但使用实绩不多 *只有1-2项目
・过去实绩的确认 (项目&品名)
10 ■网络系统
11 ■实验评价流程
○
12 ■实验评价能力
○
(材料、构成品、完成品的一般评价
/耐久评价)
13 ■实验评价的资源
○
14 ■CAE能力
第四版SQAM
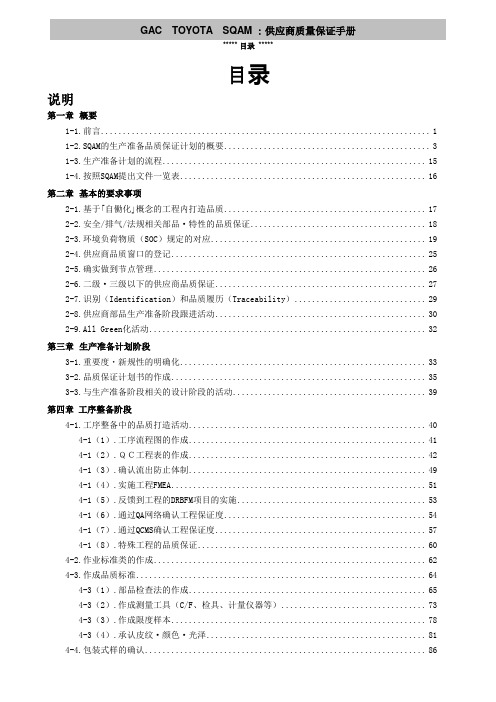
***** 目录*****目录说明第一章概要1-1.前言 (1)1-2.SQAM的生产准备品质保证计划的概要 (3)1-3.生产准备计划的流程 (15)1-4.按照SQAM提出文件一览表 (16)第二章基本的要求事项2-1.基于「自働化」概念的工程内打造品质 (17)2-2.安全/排气/法规相关部品.特性的品质保证 (18)2-3.环境负荷物质(SOC)规定的对应 (19)2-4.供应商品质窗口的登记 (25)2-5.确实做到节点管理 (26)2-6.二级.三级以下的供应商品质保证 (27)2-7.识别(Identification)和品质履历(Traceability) (29)2-8.供应商部品生产准备阶段跟进活动 (30)2-9.All Green化活动 (32)第三章生产准备计划阶段3-1.重要度・新规性的明确化 (33)3-2.品质保证计划书的作成 (35)3-3.与生产准备阶段相关的设计阶段的活动 (39)第四章工序整备阶段4-1.工序整备中的品质打造活动 (40)4-1(1).工序流程图的作成 (41)4-1(2).QC工程表的作成 (42)4-1(3).确认流出防止体制 (49)4-1(4).实施工程FMEA (51)4-1(5).反馈到工程的DRBFM项目的实施 (53)4-1(6).通过QA网络确认工程保证度 (54)4-1(7).通过QCMS确认工程保证度 (57)4-1(8).特殊工程的品质保证 (60)4-2.作业标准类的作成 (62)4-3.作成品质标准 (64)4-3(1).部品检查法的作成 (65)4-3(2).作成测量工具(C/F、检具、计量仪器等) (73)4-3(3).作成限度样本 (78)4-3(4).承认皮纹.颜色.光泽 (81)*****目录 ****第五章号试阶段5-1.实施生产调试 (88)5-2. 实施初品评价(含信赖性评价) (90)5-3.部品的纳入 (94)5-4.号试中的不良对策 (98)5-5.面向号口的最终确认 (99)第六章号口生产阶段6-1.号口初期的品质管理 (101)6-2.号口生产中的品质管理 (103)6-3.设计变更的实施和确认 (106)6-4.工程变更的申请和确认 (107)6-5.纳入不良的处理要领 (111)6-6.纳入不良的计算方法 (114)6-7.市场品质问题的保证活动 (116)6-8.广汽丰田实施的工程点检 (118)第七章品质保证关联事项/工具7-1.工程能力的思考方法 (119)7-2.防错装置的理解 (123)7-3.活用管理图维持工程管理 (125)7-4.问题解析(5 Why Analysis) (127)第八章用语集 (129)第九章业务用表格 (136)附页 (162)***** 说明*****第四版说明供应商质量保证手册(SQAM)在06年开始出版,供应商质量保证手册是一本指导广汽丰田与各零部件供应商在生准、号口、市场中品质的创立及保证的工具书。
TPS三票两表-丰田陆地巡洋舰--面漆检查指导书(左)

100制定 作业名
前面挡泥板检查
面漆检查
检查翼子板下部时左膝要抵住身体
端部用手指检查
年、月、日 修 订 者
①②③④⑤
作 业 手 順
检查翼子板上半部分检查翼子板下半部分检查翼子板外表面膝部抵住身体
作 业 指 导 书
安 全 项 目
時 间
作 业 要 领
指部弯曲要和车身表面的曲率一致
检查部位和眼睛保持水平左膝抵住身体检查
181920
1213141516176789101112345使用工具检查表・文件夹・胶带
修 订 内 容
修 订 理 由
批 准
※发现漆膜表面有不良现象时,要用胶带贴在不良部位附近
手要紧贴车身的曲面
异常处理规则:
停下生产线,报告有关领导等待
修 订 栏
合 計
该作业所必需的保护用具 帽子、静电服、安全鞋、防静电手套 该作业所必需的指名业务许可证型号所属
节拍
工 程
略 图
批准审查起草
车 型担当部署
合计时间秒
生产线凡例要素
取置
歩行①
②
③。
丰田工程管理看板、变化点管理看板资料

变化点管一、管理二、管理三、看板生产记录变化点记变化点运变化点引异常返工流程作业者发现生产线设备异常、单台工件NG 、批量不良时应立即停止生产呼叫线外或班长设备异常时具有处置资格的人员处置保留NG工件通知组长工件批量NG时班长立即停止生产保留工件、及生产线原状态通知组长等待指令具有资格或指名人员对NG工件确认修理组长确认返修状态工件修理后填写《返工记录表》通知品技、系长等待指令组长确认NG工件的位置、数量组织确认NG工件并逐台悬挂不良品标识看板单台工件NG时线外班长联系品保人员确认待确认品或报废品悬挂待确认标识或《废品记录表》通知组长返修品工程内4M 管理项目工程4M 变化点管理板看板具体内容2m各种车间使用表格放置盒准备组一工程包括本工程:(1)工程能力表(2)标准作业票(3)山积表(4)要素要领书1m工具存放区域检验区域模具存放区域出货区域焊接区域成品库叉车停放区运搬通道检查区域冲压设备区域车间工艺布局图冲压设备区域劳保用品穿戴工作帽我们的安全宣言是:“进入车间穿戴好劳保用品”!防护镜工作服耳塞安全鞋必要工序戴手套,其它工序禁止戴手套A3纸面大小○初物○初品目视化管理期间记 录重点确认确认事项谁频 度记 录作业者交替年休、事假、病假、辞职、新人培训、多技能培训、线外替岗·活用作业指导书、要领书进行作业指导·递交工程变更联络书·指导者认定表·新人培训计划表·作业标示板·无经验者:2W以上·有经验者:1W以上·变化点记录表·对无经验者进行安全品质确认作业指导者·全数·无经验着培训计划·工程变更联络书·按工程变更联络书进行品质确认·按工程变更联络书进行品质确认职位交替班长(EX)、组长(GL)交替时·职责内的品质保证项目整理·熟悉组内的品质保证体制·职位交替计划表·记录目视化·无经验者:2W以上·有经验者:1W以上·变化点记录表·对无经验者进行品质确认上位者·全数·无经验者培训计划标准作业(作业标准)变更,工程变更作业要领书变更、作业组合票变更、作业顺序变更、工程变更·作业标准类整备·作业标准票的修正·品标的修正·递交工程变更联络书·作业标示板·4台以上·变化点记录表·按照品标进行品质确认EX GL ·按初期管理标准执行·工程变更联络书·按工程变更联络书进行品质确认·按工程变更联络书进行品质确认手修理全线加工、组装手修理时·制作手修理要领书并培训·制作手修理记录表·手修理指名作业·手修理的基本规定·指名者认定表·记录目视化·手修理品流动中·手修理记录表(N/G NO 记录表)·手修理部位·手修理时的误品、欠品的品质确认EX GL ·手修理品全数·手修理记录表·对重点部位、手修理部位进行品质确认设备故障时设备故障时 其他工位的对策·制作设备故障处理要领书·事前训练·记录目视化·作业标示板·设备故障品流动中·变化点记录表·与设备相关部位 ·按照品标进行品质确认EX GL ·设备故障品全数·变化点记录表·对基本的内容进行品质确认·对相关的内容进行品质确认作业中断时手修理、加工组装作业中断时·制作作业中断处理和记录表·手修理基本规定·悬挂安全锁·安全锁的遵守状况EX GL·中断时的完成品设备条件变更设备注液条件、加热条件、运转条件变更、设备程序变更、设备电力变更、悬挂方法变更等·作业标准类整备·作业标准票的修正·品标的修正·递交工程变更联络书·作业标示板·2W以上·变化点记录表·按照精检项目一览表进行品质确认(初品)EX GL ·按初期管理标准执行·工程变更联络书·变化点记录表·按工程变更联络书进行品质确认·按工程变更联络书进行品质确认设备异常处置各个操作引起的设备异常、内部清理、设备异常复位等·制作异常处置要领书及培训·制作异常处置基本规定·制作异常处置记录表·异常处置指名作业·指名者认定表·异常处置训练记录·记录目视化·异常处置品流动中·异常处置记录表·与设备相关部位·按照品标进行品质确认EX GL ·异常处置品全数·异常处置记录表·变化点记录表设备修理机械故障、精度不良时的修理·修理后初物 ·保全记录·初物的状态·按照品标进行品质确认EX GL ·初物·异常处置记录表·变化点记录表·测定相关项目工具交换气扳手、QL扳手、FL扳手、验具、治具等的交换·制作作业要领书及培训·记录目视化·初物·变化点记录表·初物的状态·按照品标进行品质确认一般·初物·变化点记录表·测定相关项目设备改造设备故障的再发防止、设备本身的改造、工作环境的改造、暂停使用时的处置·递交工程变更联络书·递交设备改造方案·作业标示板·2W以上·变化点记录表·初品的状态·按照精检项目一览表进行品质确认EX GL ·按初期管理标准执行·工程变更联络书·变化点记录表·按工程变更联络书进行品质确认·按工程变更联络书进行品质确认工具变更新工具、治具的采用·校准·更换时等·作业标准类整备·工具配置图的变更·递交工程变更联络书·记录目视化·2W以上·变化点记录表·初品的状态·按照精检项目一览表进行品质确认EX GL·按初期管理标准执行·工程变更联络书·变化点记录表·按工程变更联络书进行品质确认·按工程变更联络书进行品质确认新设设备新设设备、移动设备、长期停止使用的设备复原时等·作业标准类整备·作业标准票的修正·品标的修正·递交工程变更联络书(长期停止使用)·作业标示板·2W以上·变化点记录表·初品的状态·按照精检项目一览表进行品质确认EX GL ·按初期管理标准执行·工程变更联络书·变化点记录表·检查相关项目·测定相关项目辅助材料的交换·补给清洗剂、FIPG胶、乐泰胶、助插剂等的交换·补给·制作作业要领书及培训·初物的状态·按照品标进行品质确认一般·初物储备品·先行品的流动非常用手持品、储备部品等的流动·使用·事先确认储备品、先行品状态·记录目视化·初物·变化点记录表·是否误品、有无划伤、油污EX GL ·初物·变化点记录表外购品的设计变更·工程变更毛坯、购入品的设计变更、材料变更、工程变更·设变切替计划书的确认·新品的检查及对照·记录目视化·新品初品流动中·设变切替计划书·E/G NO 记录表·毛坯、购入品状态·确认组装性,加工性一般EX GL ·按初期管理标准执行·变化点记录表 ·E/G NO 记录表·按初期管理标准执行·按初期管理标准执行辅助材料的变更清洗剂、FIPG胶、乐泰胶、助插剂等的变更·作业标准类整备·作业标准票的修正·品标的修正·递交工程变更联络书·作业标示板·2W以上·变化点记录表·初物的状态·按照精检项目一览表进行品质确认EX GL·按初期管理标准执行·工程变更联络书·变化点记录表·按工程变更联络书进行品质确认·按工程变更联络书进行品质确认设计变更内制品的设计变更、材料变更、特采品等·作业标准类整备·作业标准票的修正·品标的修正·设变切替计划书的确认·作业标示板·2W以上 ·特采品全数·变化点记录表·E/G NO 记录表·设变后的初品·特采品全数·按照品标进行品质确认EX GL ·按初期管理标准执行·变化点记录表 ·E/G NO 记录表·按初期管理标准执行·按初期管理标准执行人方法设备工具治具物事 前 准 备管 理 方 法相关部门对策内 容记 录变化点管理的目视化变化点管理的方法·品质结果的记录课 内品质课要因(4M)序号变化点项目变化点对象变化点管理要领变化点管理要领标识放置设备、模具、夹具产品材料作业方法环境(高低温、灯光)分类管理标识形式人新人替岗作业新替机料法环新替机料法环新替机料法环新替机料法环新替机料法环新替机料法环变化点运营标识人员管理组织机构图缺勤人员情况A4纸面大小作业者照片将全部作业者照片粘贴在此位置,每天开班前由组长将人员情况进行确认考勤表每天开班前组长将缺勤人员照片粘贴在此位置异常处置流程异常记录A4纸面大小生产计划及变化点记录设备开动率17:50-18:5006:50-07:5016:50-17:5005:50-06:5015:40-16:4004:40-05:4014:50-15:4003:50-04:4013:40-14:4002:40-03:4012:40-13:4001:40-02:4011:00-12:0000:00-01:0010:10-11:0023:10-00:0009:00-10:0022:00-23:0008:15-09:0021:15-22:00时间生产线停止原因(变化点记录)日期月 日班次:计划产量:实际生产:节拍:所有内容需要划线粘贴进行每日填写,填写后可以擦拭,每天要有记录表各种变化。
4M1E检查表

清 洁:SEIKETSU 保持光亮和卫生
习 惯:SHITSUKE 养成纪律的习惯
根据日本劳动安全协会在 1950 年推行的口号是:安全始于整理、整顿,而终于整理、整顿。可见日本早期只推
行 5S 中的整理、整顿,目的在于确保安全的作业空间,后因生产管理需求和水准的提高,另增清扫、清洁、习惯,
而成为现在的 5S,着眼点不限于安全,扩大到环境卫生、效率、品质、成本等方面。
5 个“为什么”是由日本丰田公司总结提出的,是用来找出问题原因的一种方法。它是指,对一个问题至少要连续提
出 5 个“为什么”,以求得到问题的根源。这种方法看起来十分简单,还有点机械,但很实用,很有效。
举例
问题:车门关不严:
答:对中不好;为什么(1)?
门铰链位置不正确;为什么(2)?
固定铰链的位置不正确;为什么(3)?
a. 人(Men)
b. 设备(Machine) c. 材料(Material)
d. 方法(Method)
e.
环境
(Eenvironment)
他遵守标准吗?
它满足生产需要吗? 材料正确吗?
工作标准适用吗? 场地及物品摆放清洁
他的工作效率可接受 它 的 能 力 满 足 要 求 等级正确吗?
工作标准先进吗? 整齐吗?
吗?
吗?
牌号正确吗?
工作方法安全吗? 作业区、贮存区、物
他有问题意识吗? 它的润滑适当吗? 混有杂质吗?
工作程序合理吗? 流、安全通道符合定
他的责任性强吗? 它 被 适 当 地 检 查 过 库存量适宜吗?
设定参数适宜吗? 置要求吗?
他的资格够吗?
吗?
材料有浪费吗?
与上下道过程接吗? 温度、湿度适宜吗?
丰田重要度新规性列表

序号
图纸种类
144200-33POWER XXX
S
123制作所
1级供应商
部品基本情报
供应商责任人窗口
NO
品番
品名
承认图(S)丰田图(T)供应商代
码供应商名
部门
TEL
Project Code:000*
生准方式Y/N
人窗口
E-MAIL
部品生产地点
Pass Through
:Y/N
供应商
生产工厂
保安ΔS 地址
JJ JC CC
重要度▪新规性部品列表
供应商 记入栏
工法
焊锡工程Y/N
新规性Y/N
E.电子单元说明相应项目
特殊工程 记入相应工程部品状况号口品质问题新规性Y/N
C.树脂熔着
D.橡胶加硫接着新规性Y/N
部品重点
橡胶加硫接着Y/N
采购
品管
采购
特殊工程
实施判断丰田记入栏担当品管
部品重要度重点管理部品技术中心
生管
备注
技术中心
采购
品管
技术中心
采购
品管。