零件试验大纲
03_零部件性能试验大纲-车身

产品名称(Part name):车门锁和铰链产品型号(Product No.):T-XXXX-00X序号No.试验项目Item标准值Standard value试验方法Test method试验地点Testplace试验周期Testcycle试验设备Test equipment样品要求Sample size备注Remark1 门锁静态纵向负荷试验门锁在半锁紧位置承受4440N的纵向负荷;或在全锁紧位置承受11110N的纵向负荷时,均不得脱开。
a.用两套门锁分别作半锁紧位置和全锁紧位置的试验。
将锁体和挡块(或锁扣)安装在静态纵向负荷试验夹具上,使其相互啮合,并分别处于半锁紧位置和全锁紧位置,然后将夹具安装到拉力试验机上,使拉力与锁体和挡块(或锁扣)的啮合面的中心在一条直线上;b.在锁体和挡块(或锁扣)上施加890N的横向负荷,使锁体和挡块(或锁扣)有向着开门方向分离的趋势;c.拉力试验机以不超过5mm/min的速度增加负荷,直至所规定的值拉力试验机静态纵向负荷试验夹具2门锁静态横向负荷试验门锁在半锁紧位置承受4440N的横向负荷;或在全锁紧位置承受8890N的横向负荷时,均不得脱开。
当门锁在纵向或横向受到294.2m/s2(30g)的加速度时,必须保持在全锁紧位置不得脱开a.用两套门锁分别作半锁紧位置和全锁紧位置的试验。
将锁体和挡块(或锁扣)安装在静态横向试验夹具上,使其相互啮合,并分别处于半锁紧和全锁紧位置。
然后将夹具安装到拉力试验机上,使拉力沿车门开启方向,并与锁体和挡块(或锁扣)的啮合面的中心在一条直线上;b.拉力试验机以不超过5mm/min的速度增负荷,直至所规定的值拉力试验机静态横向负荷试验夹具3门锁耐惯性力分析利用静力学分析法,对门锁的有关构件进行受力分析,在任意方向均能承受30g的惯性负荷作用,并能保持全锁紧位置GB15086-94《汽车门锁及门铰链的性能要求及试验方法》也等效采用SAE的推荐方法进行计算校核,在按钮式外手柄上,受到294.2m/s2(30g)的减速度作用。
04_零部件试验大纲-内外饰
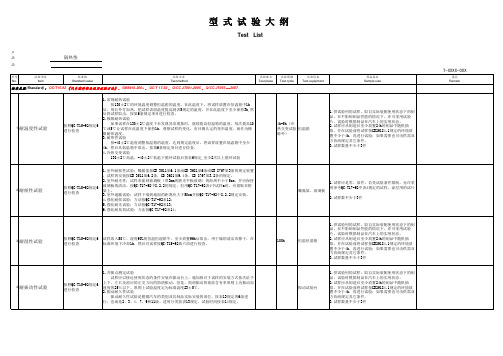
4
耐振动性试验
1.共振点测定试验 试样应以接近使用状态的条件安装在振动台上。施加相对于试样的安装方式依次给予上 下,左右及前后的正交方向的简谐振动。但是,简谐振动的谐波含有率原则上为振动加速度的 按照QC/T15-92规定6进 25%以下。原则上试验温度定为标准温度23±5℃。 行检查 2.振动耐久性试验 振动耐久性试验是根据汽车的类别及其制品实际安装的部位,按表13规定的6级进行,也 就是2、3、4、7、9和11级。适用分类按表13规定,试验时间按表14规定。
2
耐候性试验
1.室外耐候性试验:曝露架按GB 3511第6.1条或GB 3681第6条或GB I767第3条的规定装置。 试样的安装按GB 3511第6.2条,GB 3681第9.4条、GB 1767第3.2条的规定。 2.室外耐光性:试样表面到玻璃板(厚3mm的磨光平板玻璃)的距离不小于5cm,并应保持玻 按照QC/T15-92规定6进 璃板的清洁。按QC/T17-92中8.2.2的规定,但用QC/T17-92表4中试样a时,应紧贴在框架上。 行检查 3.室外遮蔽试验:试样下端到地面的距离应大于50cm并按QC/T17-92中8.2.2规定安装。 4.强化耐候试验:方法按QC/T17-92表12; 5.强化耐光试验:方法按QC/T17-92表13; 6.强化耐臭氧试验:方法按QC/T17-92表14;
8
耐擦伤性试验
1.刮伤试验 制品表面用000#钢纤维摩擦,表面压力为6.5kpa,速度为6m/min,摩擦次数由供需双方 商定。 按照QC/T15-92规定6进 2.洗涤试验 行检查 用符合规定性质的泥水涂在制品表面,使表面均匀湿润,让其自然干燥,制品表面的泥 用水粗略除去,然后用海绵、布或塑料刷洗刷三至五次,最后 使制品自然干燥。
检验大纲

检验大纲
检验项目应用到的设备及检验手段 1. 几何外观尺寸
毛坯、原材料进厂——进货检验 2. 外协质量相关文件卡尺、深度尺、千分尺
无损检测:壁厚检测卡尺、荧光磁粉探伤机、超
声波测厚仪、着色探伤剂
理化检验:⑴材质检测、⑵机械性能、⑶化学试验卡尺、冲击试验机、光谱仪
及手工操作检定
机加工零部件检验:按图纸及标准要求对各个零部件进行检验卡尺、深度尺、百分表
卡钳、千分尺、长爪内侧尺标识检验:各个零部件跟踪记录并编号刻字笔
焊接检验:阀门焊件的焊缝、结构长、缺陷等相关焊连接检验卡尺、内径千分棍
装配检验:阀门各零部件组装过程中一系列的跟踪检验卡尺、图纸
整机试验检验:按客户合同及相关标准进行压力试验液压试验台
合格证、铭牌、质量文件的制作:给合格品制作相关质量文件、合格证、铭牌等
外观检验:表面粗糙度、铭牌标识内容及位置是否正确是否正确卡尺
成品出厂、入库,不合格品相关处理及记录在案
各种量具均由计量室进行周期检定
质检部
2009-3-10
理化性能检验
机加工零部件检验
壁厚检测
标识检验
焊接检验
装配检验
整机试压检验
毛坯、原材料进厂检验
铭牌及合格证制作
外观检验。
产品试验大纲

产品试验大纲 Test Outline
GB /T 18377-2001热振动试验试验时发动机过量空气系数为
1±0.2,催化转化器空速为
(48000±480)h-1;催化转化
器入口排气温度为600℃以上;
振动加速度为(28±3)g、振动
频率为(100±5)Hz;试验时
间为5h。
试验结束后,检测密封
情况。
第三方检测中心20天零件是否
GB T 10125—1997盐雾试验中性盐雾试验72小时内无白锈宁波新华英达
理化实验室
7天材料是否
产品图纸流量测试通入105kPa的压缩空气下,分
别测试流量在125g/s、110g/s
、95g/s、80g/s下的压力,要
求各支管之间的最大压力损失差
异不超过3%。
第三方检测中心14天零件是否
GMW 14058熔深试验焊接熔深试验满足
GMW14058要求
宁波新华英达
理化实验室
3天零件是是
Q/YC 11-2004清洁度检测杂质质量(mg)≤65;
颗粒度A(mm)≤0.8
第三方检测中心7天零件是否
SGMWJ 0849-2013禁用物质检测铅、汞、六价铬、多溴联苯
(PBBs)、多溴二苯醚
(PBDEs)的质量百分数不得超
过0.1%,镉的质量百分数不得超
过0.01%
第三方检测中心10天材料是否
编制: 审核: 批准; 五菱柳机产品工程师/WLLJ PE : 日期:日期: 日期:日期:。
1 轮毂轴承性能试验大纲

车型零部件性能试验试验大纲产品名称:轮毂轴承产品图号:试验类型:性能检验试验日期:编制:审核:批准:1.试验依据:乘用车及商务车轮毂轴承技术标准2.试验目的:验证产品的性能是否满足要求。
3.试验对象:轮毂轴承。
4.要求:负荷试验机的压力不小于10KN,室温在20±1℃。
5.试验方法5.1密封泥水试验5.1.1定义:泥水试验是使轴承在泥浆水喷溅的条件下,用轴承寿命来描述轴承防泥水能力的试验。
5.1.2试验准备5.1.2.1样本容量:2套,抽样4套,其中2套为备品及分析用5.1.2.2样品套圈的端面上逐套编号5.1.2.3样品在各项测试前应擦试干净,不得有油污5.1.2.4称质量采用的天平精度应不低于6级,并定期鉴定.5.1.2.5轴承在上机试验前称其质量5.1.2.6与轴承配合的轴与壳体的公差应符合要求5.1.2.7试验轴承必须安装正确,不得有压偏现象,不准敲打密封圈5.1.3试验条件5.1.3.1试验机为通过鉴定合格的轴承试验机5.1.3.2试验条件:泥水应符合:JISZ8901 8级,重量比为5%;流量:1×103m3/min转速:N=300rpm时,向密封件喷溅试验1小时N=1000rpm时,不喷溅试验1小时目标时间:100小时5.1.4试验过程5.1.4.1凡因设备仪器故障或操作人员违反试验规程造成轴承失效时,应从记录中剔除5.1.4.2试验轴承出现异常振动、噪声及其它异常现象时,应及时停机处理5.1.4.3试验在载荷下起动和停机5.2漏脂试验5.2.1定义:漏脂试验是轴承在一定条件下运转,用轴承腔内润滑脂泄漏到轴承外部的情况来描述其防漏脂能力的试验。
5.2.2试验准备5.2.2.1样本容量:4套,抽样数量6套,其中2套为备品及分析用。
5.2.2.2样品套圈的端面上逐套编号5.2.2.3样品在各项测试前应擦试干净,不得有油污5.2.2.4称质量采用的天平精度应不低于6级,并定期鉴定.5.2.2.5轴承在上机试验前称其质量5.2.2.6与轴承配合的轴与壳体的公差应符合要求5.2.2.7试验轴承必须安装正确,不得有压偏现象,不准敲打密封圈5.2.3试验条件5.2.3.1试验机为通过鉴定合格的密封轴承试验机5.2.3.2试验条件:试验转速:900转/分环境温度: 10~30ºC试验径向载荷:1500N试验时间:48小时螺母扭紧力:200Nm~260Nm5.2.4试验过程5.2.4.1开始每30分钟记录一次轴承温度及环境温度,待温度稳定后,每一小时记录一次.5.2.4.2凡因设备仪器故障或操作人员违反试验规程造成轴承失效时,应从记录中剔除5.2.4.3试验轴承出现异常振动、噪声及其它异常现象时,应及时停机处理5.2.4.4试验在载荷下起动和停机5.3强化试验5.3.1 本试验大纲制定参考STI-03C标准改动而成的。
液压制动硬管试验大纲(江淮汽车)
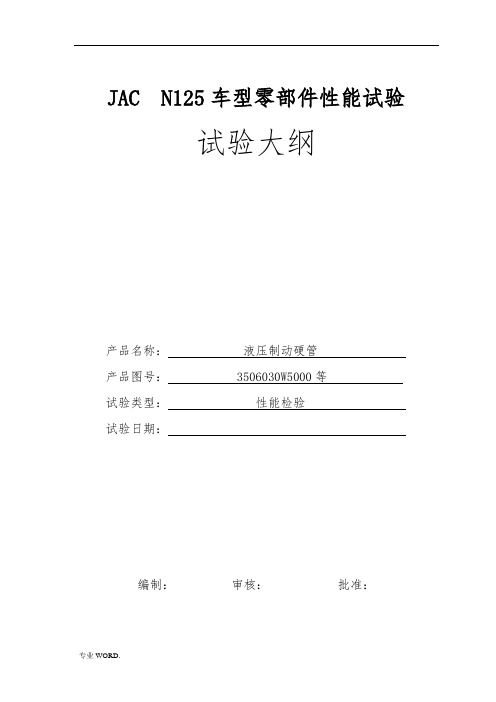
JAC N125车型零部件性能试验试验大纲产品名称:液压制动硬管产品图号: 3506030W5000等试验类型:性能检验试验日期:编制:审核:批准:专业WORD.目录1.验依据 (3)2.试验目的 (3)3.试验对象 (3)4.技术要求 (3)4.1 性能 (3)4.2 耐腐蚀性能 (3)4.3 形式、规格和质量 (4)5.试验容 (4)5.1 压扁和弯曲符合试验 (4)5.2 扩口试验 (4)5.3 弯曲试验 (4)5.4 双层扩口试验 (4)5.5 耐压试验 (5)5.6 耐温度试验 (6)5.7 密实性 (6)5.8 表面质量 (6)5.9 表面清洁度 (6)5.10盐雾试验 (6)5.11刮刻试验.............................................................. 错误!未定义书签。
附录 A. (7)附录 B (8)1.验依据SAE J463-2002 锻铜和铜合金SAE J527-2000 铜焊双层壁低碳钢管SAE J533-1999 管的扩口SAE J1290-2002 汽车液压制动系统——公制管联接件YB/T 4164-2007 双层铜焊钢管2.试验目的检验液压制动硬管是否满足相关标准的要求。
3.试验对象N125 液压制动硬管、离合硬管,外径为φ4.76mm,真空硬管,外径为φ10mm。
4.技术要求汽车用钢管应圆滑并且没有损害工艺或操作性的锈斑和缺陷。
管子焊脊高度不能超过外径公差并且不能防碍扩口成型操作或密封接头的装配。
基本制管材料应为SAE1008或SAE1010冷轧钢。
钎焊材料应为铜或铜合金,按照SAEJ463要求,铜合金UNS C51000标准。
4.1 性能4.1.1 强度抗拉强度≥300Mpa;屈服强度≥最小200Mpa;延伸率≥25%。
4.1.2管子应该能够在合适的折弯夹具上绕中心线以三倍于管子外径的半径折弯不出现过度断面收缩或压扁。
主机厂长安DV样件可靠性试验大纲AQ2A-01-R005(V01)

1. 跌落后如果所有DUT均发
工作模式:1.1
生明显的外观损坏,则对DUT
样品状态:带包装和不带包装
功能不做要求,但应报告功
21
跌落试验
样品数量:带包装、不带包装各3个 高度:1000mm
能检测结果; 2. 试验后如果至少一个DUT
单臂跌落台
跌落次数:每个轴向正反面各一次
没有发生外观损坏,则要求
跌落地面:水泥地面或钢板
1.连接上输入电压,是DUT正常运行; 2.断开DUT的一个管脚10s,检查此时DUT的功能状态,
开路状态不小于10M欧;
恢复正常的工作电压连接 后,DUT功能状态应满足C级
要求;
DUT功能状态应满足C级要 求;
直流电源,目 视
直流电源,目 视
室温下,工作模式3.2,试验时间10s,开路电阻大于等 于10M欧;
高温寿命
室温下,工作模式3.2 试验时间 60s, 试验电压;间距小于3.8mm时,100V DC;
间距大于3.8mm时,500V DC;
试验结束后,要求测得的绝 绝缘电阻测试
缘电阻应大于10MΩ
仪
按照功能测试规范进行功能测试 按照功能测试规范进行功能测试 按照功能测试规范进行功能测试
符合整车音效主观对比评价 规范
1. DUT功能状态应满足A级要 求: 2. 防尘等级:IP5X(防尘), 有少量灰尘进入,但进入的 灰尘不影响DUT正常工作,功 能正常;
委外
工作模式:正常出货包装状态
16
防水试验
防护等级为:IP52 试验时间及试验试验方法:见《汽车电子电器部件环境
功能状态应满足A级要求
委外
条件及试验标准》防水试验部分,防护等级2的要求;
S2塑料件试验大纲
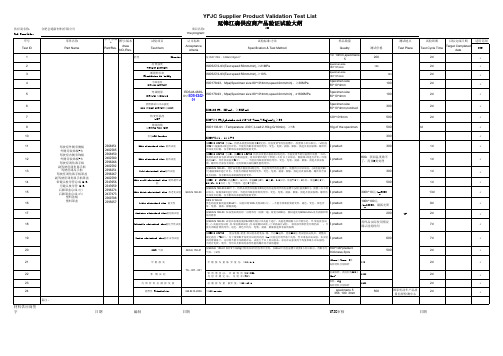
1d 1d 13d
√ √ √
Heat cycle resistance test 耐热循环试 验
Heat aging resistance test 热老化试验
SES N 190-03
16 17
Light resistance test 耐光性
5 preduct 1 preduct
9d 2d
√ √
Abrasion resistance test耐划痕试验
Specimen size 150*10*4mm1002d 2d
Specimen size 80*10*4mm Specimen size 80*10*4mm Specimen size 80*10*4mm,notched 120*10*4mm
100
5
弯曲模量 Flexural Modulus
悬臂梁缺口冲击强度 Izod Impact Strength (Notch)
Test Place
ISO527/2-93(Test speed:50mm/min),≥21MPa ISO527/2-93(Test speed:50mm/min),≥10% ISO178-93,Mpa(Specimen size 80*10*4mm,speed:2mm/min),≥30MPa EDS-M-4639ISO178-93,Mpa(Specimen size 80*10*4mm,speed:2mm/min),≥1600MPa 01/ EDS-424201
YFJC Supplier Product Validation Test List 延锋江森供应商产品验证试验大纲
供应商名称: The Supplier: 序号 Test ID 1 2 3 4 零件名称 Part Name 零件号/版本图号/版本 Part/Rev. draw NO./Rev.
产品型试实验大纲

型式试验大纲零件名称:
零件号:
试验材料:
型式试验大纲填写说明:零件名称:被测试的零件主体名称;
2.零件号:被测试零件主体编号;
3.试验项目:被测试的零件特性参数;
4.试验标准:测试所参照的试验标准;
5.试验来源:相应的零件图纸编号;
6.标准值:标准和图纸上规定的特性参数控制范围;
7.试验方法:相应标准上规定的完成试验所采用的测试方法;
8.试验地点:完成全部零件测试的现场;
9.试验周期:完成零件全部测试的时间;
10.试验设备:实施测试工作所使用的设备;
11.样品要求:为完成试验所制作的测试样品尺寸和数量要求。
检验和试验大纲

检验和试验大纲一、进货检验根据采购文件,采购物质分为A类、B类、C类,及公司现有测试条件,原则上进行验证,对某些金属材料及铁合金,要求供应商有质保单。
水玻璃需进行检验,由仓库填写化验委托单,交化验室化验,根据化验结果对照有关标准,合格物资方可入库。
对不合格物资,按照不合格控制程序进行处理。
对于改做他用的进货物质,品质部在工艺上采取必要措施,通知物资使用部门。
A、B类. 物资对产品质量影响较大,公司在无检验测试条件时(或测试费用过大)通过选择有持续稳定质量水平的合格供应商供货来控制,合格供应商的控制参照合格供应商程序文件执行。
C类. 物质的进货验证参照采购文件执行。
二、过程检验根据嘉山精密铸造工艺过程框图,并结合本公司实际情况,为保证产品质量,设置下列检验点及检验项目。
(一)、新产品试制检验根据用户提供图纸或样品,进行工艺设计,落实模具制造,完成后,试打蜡模,对蜡模进行测量,不符合要求进行模具修理。
基本符合图纸或样品及工艺要求,投入试生产过程,待样品试出来后,对铸件进行详细测量,必要时进行解剖,观察热节点有否缩孔,缩松缺陷,发现有因缩尺原因或工艺不当引起铸件不符合要求,再次进行修改模具。
对大批量产品发用户试加工,待用户认可再投入批量生产。
新产品测试由总工或技术部负责人负责。
(二)、蜡模蜡模是精铸生产过程中首道工序。
蜡模的表面质量、几何形状和尺寸精度直接影响铸件质量。
为了不使不合格产品流入下道工序,减少废品损失,保证产品质量,注蜡工必须做好产品自检工作,并在注蜡车间设置质量检验点。
修边员工对蜡模产品缺陷(缺肉、裂纹、表面缩凹、表面流线花纹、表面粗糙、有麻坑、气泡外露、鼓胀等)进行修补,对于去边过大,错位、变形等缺陷报蜡模检验员处理。
蜡模检验项目包括:1、蜡模尺寸:由于模具破损或模料温度不当收缩引起蜡模尺寸不符要求,可到技术部依据设计图进行测量。
2、蜡模表面缺陷:缺肉,裂纹,表面缩凹,表面流线花纹,表面粗糙,有麻坑,气泡外露,气泡鼓胀。
主机厂吉利DV样件可靠性试验大纲AQ2A-01-R007(V01)

备连接,样品被施加24V电压保持1分钟。 DUT的电气部分与绝缘体之间承受频率为50Hz,幅值 为550V(有效值)的正弦波电压历时1min时,其绝
缘不应被击穿; 工作模式 3.2 试验温度 +75℃ 试验时间 96h 工作模式 1.1 试验温度 +90℃ 试验时间 72h 按GB/T2423.3-1993规定的方法进行试验。 温度要求 50±2℃ 相对湿度 93%±2% 试验时间 72小时 工作模式 1.1 工作模式 3.2 试验温度 -30℃ 试验时间 12h 工作模式 1.1 试验温度 -40℃ 试验时间 24h
编号:
期: 准: 期:
日期 开始 结束
计划编制人:
项目批准:
报告工程师:
测试报告
实际结果
备注
应符合Ⅰ类判定要求。
DUT功能状态应满足Ⅲ类要求。
按GB/T 2423.22规定的方法进行试验。 工作模式 3.2 试验参数
13
耐温度变化试验
Q/JLY J711063-2008
试验后应符合Ⅰ类要求。
循环次数 6 需要严格控制湿度,以避免冷凝:
上限温度 +55℃±10℃ 下限温度 -10℃±10℃
Q/JLY J711063-2008
Q/JLY J711063-2008 Q/JLY J711063-2008
记录序号: (适用)项目:
供方:
DVP编号:
计划日期: 部门批准: 报告日期:
目标要求
材料满足 Q/JLY J711169-2009的要 求
材料满足 Q/JL J124004-2010的要求 材料满足JLYY-JT23-08的要求 材料满足 JIS G3302-2007的要求
主机厂长安铃木DV样件可靠性试验大纲 AQ2A-01-R006(V01
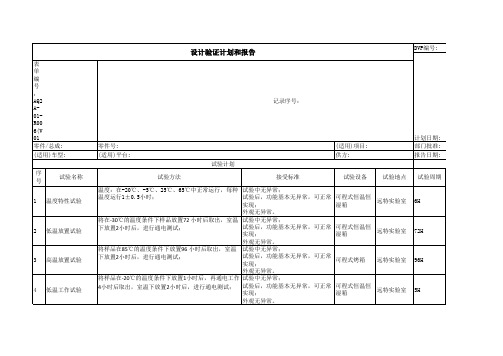
5高温工作试验将样品在65℃的温度条件下放置1小时后,再通电工作4小时后取出,室温下放置2小时后,进行通电测试;试验中无异常;试验后,功能基本无异常,可正常实现;外观无异常。
可程式烤箱远特实验室5H6温度循环试验将样品在-30℃的环境中放置1个小时,按下图规定的温度变化实施10 个周期,在此期间样品正常通电工作,10个周期完成后,在室温下放置2个小时,再进行通电实验;试验中无异常;试验后,功能基本无异常,可正常实现;外观无异常。
可程式恒温恒湿箱远特实验室81H7热冲击试验将样品放置在-30℃的恒温环境中1小时,取出并迅速将其放入85℃的恒温环境中放置1小时,按下图规定的方式循环100个周期,100周期完成后,在室温条件下放置2小时以上后,进行通电测试。
实验后,功能性能基本满足,无焊接断裂和裂缝。
可程式恒温恒湿箱&可程式烤箱远特实验室200H8恒温恒湿试验在温度45℃,湿度85%的环境下放置1小时后,接通电源持续工作96小时,最后在室温条件下放置2小时以上后进行测试。
试验中无异常;试验后,功能基本无异常,可正常实现;外观无异常。
可程式恒温恒湿箱远特实验室97H9温-湿度循环试验将样品放置在25℃的恒温、湿度65%的环境中2.5小时,样品必须正常工作,按下图规定对温湿度进行10个周期的调整,10个周期完成后,在室温条件下放置2小时以上后进行测试。
注:温度为55度时,湿度要求降低到85%;达到75度高温时,不加湿度试验中无异常;试验后,功能基本无异常,可正常实现;外观无异常。
可程式恒温恒湿箱远特实验室242.5H10结露试验将样品放入-5℃的环境中2个小时,然后取出放入35℃、湿度85%的环境中通电10分钟,循环4次。
实验中无异常;实验后产品基本功能性能保持良好;外观无异常;可程式恒温恒湿箱&可程式烤箱远特实验室9H11振动试验将样品放置到振动台进行上下、左右、前后以及快慢变换方向进行实验,周期如下表:试验中无异常;试验后,功能基本无异常,可正常实现;标识破损,可识别刻印,支架轻微弯曲等可接受振动试验机远特实验室12H12端子强度试验接插件端子,插入方向和拔出方向个施加98N(10kgf)的力1min。
检验大纲
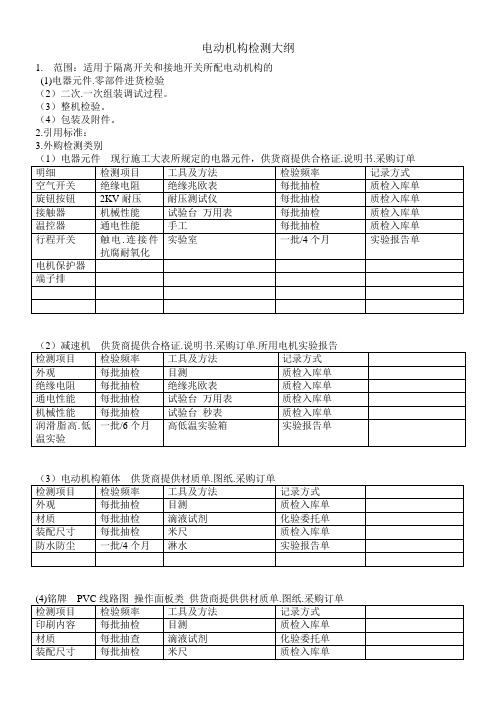
绝缘电阻
绝缘兆欧表
每批抽检
质检入库单旋钮按钮Leabharlann 2KV耐压耐压测试仪
每批抽检
质检入库单
接触器
机械性能
试验台万用表
每批抽检
质检入库单
温控器
通电性能
手工
每批抽检
质检入库单
行程开关
触电.连接件抗腐耐氧化
实验室
一批/4个月
实验报告单
电机保护器
端子排
(2)减速机供货商提供合格证.说明书.采购订单.所用电机实验报告
外观
每批抽检
目测
质检入库单
材质
每批抽检
滴液试剂
化验委托单
装配尺寸
每批抽检
米尺
质检入库单
防水防尘
一批/4个月
淋水
实验报告单
(4)铭牌PVC线路图操作面板类供货商提供供材质单.图纸.采购订单
检测项目
检验频率
工具及方法
记录方式
印刷内容
每批抽检
目测
质检入库单
材质
每批抽查
滴液试剂
化验委托单
装配尺寸
每批抽检
米尺
转角逛量
按比例/合同
测试仪器
检测报告
未定义测试仪器无
检测项目
检验频率
工具及方法
记录方式
外观
每批抽检
目测
质检入库单
绝缘电阻
每批抽检
绝缘兆欧表
质检入库单
通电性能
每批抽检
试验台万用表
质检入库单
机械性能
每批抽检
试验台秒表
质检入库单
润滑脂高.低温实验
一批/6个月
高低温实验箱
CCS船级社认可试验大纲

豫飞鹏升锻造股份CCS工厂认可试验大纲1.认可围2.认可依据CCS《材料与焊接规》(2012) 及其修改通报第一篇,第一,二,五章3.关键零件认可试验项目:6T吊钩组关键零件试验项目表10 T吊钩组关键零件试验项目表50 T吊钩组关键零件试验项目表125 T吊钩组关键零件试验项目表注:×表示适用,—表示不适用3.1化学成份分析化学成分:C,Si,Mn,S,P,Cr,Ni,Mo,Cu,及其他细化晶粒元素(标示Nb,V,Ti,Al)等。
化学成分包括钢锭熔炼样成分、钢锭成分及成品成分。
在钢锭和成品上分别化学成份样。
钢锭进厂进行复检,锻造完成后进行成品复检。
成分围应符合《材料与焊接规》(2012)及GB/T10051-2010标准的要求;成分偏差符合GB222要求。
6T吊钩组关键零件10T吊钩组关键零件50T吊钩组关键零件125T吊钩组关键零件3.2 力学性能试验项目和验收指标:试验结果应符合CCS《材料与焊接规》(2012)第1篇第5章相关要求及GB/T10051-2010标准的要求,即如下表:6T吊钩组关键零件10T吊钩组关键零件50T吊钩组关键零件125T吊钩组关键零件参考标准:GB/T228《金属材料室温拉伸试验方法》GB/T229《金属材料夏比缺口冲击试验方法》GB/T231.1《金属布氏硬度试验第一部分试验方法》3.3超声波无损检测在机加工到适当阶段和最终热处理后,应对锻钢件进行超声波检测,锻件的超声波检测的质量等级评定不低于标准JB/T5000.15-2007表1规定的Ⅱ级;锻件的磁粉检测的质量等级符合标准JB/T5000.15-2007规定。
3.4表面质量与几何尺寸检查按CCS规及标准GB908-87检查。
锻件应无有害的缩孔、裂纹、疤痕、折叠或其他非理想现象。
4力学性能试样形状和尺寸等说明4.1 试验用锻件的试样均从锻件本体上取得,按CCS材料规则确定的部位、尺寸进行取样,试样上将保留验船师留下的钢印,按CCS规要求制作试验试棒,进行拉伸、冲击试样的制备加工和性能检测,均提供验船师确认。
检验和试验大纲

检验和试验大纲一、进货检验根据采购文件,采购物质分为A类、B类、C类,及公司现有测试条件,原则上进行验证,对某些金属材料及铁合金,要求供应商有质保单。
水玻璃需进行检验,由仓库填写化验委托单,交化验室化验,根据化验结果对照有关标准,合格物资方可入库。
对不合格物资,按照不合格控制程序进行处理。
对于改做他用的进货物质,品质部在工艺上采取必要措施,通知物资使用部门。
A、B类. 物资对产品质量影响较大,公司在无检验测试条件时(或测试费用过大)通过选择有持续稳定质量水平的合格供应商供货来控制,合格供应商的控制参照合格供应商程序文件执行。
C类. 物质的进货验证参照采购文件执行。
二、过程检验根据嘉山精密铸造工艺过程框图,并结合本公司实际情况,为保证产品质量,设置下列检验点及检验项目。
(一)、新产品试制检验根据用户提供图纸或样品,进行工艺设计,落实模具制造,完成后,试打蜡模,对蜡模进行测量,不符合要求进行模具修理。
基本符合图纸或样品及工艺要求,投入试生产过程,待样品试出来后,对铸件进行详细测量,必要时进行解剖,观察热节点有否缩孔,缩松缺陷,发现有因缩尺原因或工艺不当引起铸件不符合要求,再次进行修改模具。
对大批量产品发用户试加工,待用户认可再投入批量生产。
新产品测试由总工或技术部负责人负责。
(二)、蜡模蜡模是精铸生产过程中首道工序。
蜡模的表面质量、几何形状和尺寸精度直接影响铸件质量。
为了不使不合格产品流入下道工序,减少废品损失,保证产品质量,注蜡工必须做好产品自检工作,并在注蜡车间设置质量检验点。
修边员工对蜡模产品缺陷(缺肉、裂纹、表面缩凹、表面流线花纹、表面粗糙、有麻坑、气泡外露、鼓胀等)进行修补,对于去边过大,错位、变形等缺陷报蜡模检验员处理。
蜡模检验项目包括:1、蜡模尺寸:由于模具破损或模料温度不当收缩引起蜡模尺寸不符要求,可到技术部依据设计图进行测量。
2、蜡模表面缺陷:缺肉,裂纹,表面缩凹,表面流线花纹,表面粗糙,有麻坑,气泡外露,气泡鼓胀。
产品试验大纲

1天
零件级
Y
第 1 页,共 4 页
9 编制:
பைடு நூலகம்
齿圈
表面硬度为HRC45—55(在X处检 测)
1天
审核:
零件级
Y
批准:
第 2 页,共 4 页
文件编号:
是否PPAP
试验
PPAP
(Y/N) 试验地点PPAP Test
PPAP
Location
Test (Y/N)
Y Y Y Y
Y
Y Y Y
第 3 页,共 4 页
零件级
Y
片状。
6
齿圈
S45C:SAE-J-4031045
拉力试验
σb≥570MPa
2天
零件级
Y
7
齿圈
GB/T13320-2007
金相
金相按GB/T13320-2007第一组评 级图(图1)1~3级验收
1天
零件级
Y
8
齿圈 GB/T 4340.1-2009 有效感应层层深度
A处:1.0—2.5(HV350) B处:0.3—2.5(HV350)
试验周 期
(天)Test Cycle(D
ay)
计划时间 Planning
Time
是否OTS 试验级 试验 别Test (Y/N) Grade OTS
Test(Y/N)
OTS 试验地点
OTS Location
1
飞轮总成
动平衡试验
15g.cm
1天
零件级
Y
2
飞轮总成
飞轮齿圈分离力试验
≥304N.m
1天
零件级
Y
第 4 页,共 4 页
形式试验大纲

Q/HAG JC-002-2014 《电
满足等级A。
31
磁兼容性限值及其测试方
法》一汽海马C类零部件
感应开关 交流电机负荷卸载 (瞬态传导抗扰性)
EMC验证标准试验脉冲、 试验等级Us/V及时间: 脉冲 1:-100V,5000个
脉冲
脉冲2a:+50V,5000个脉
冲
应满足的要求: 脉冲 1:等级Ⅲ, 脉冲2a:等级Ⅰ, 脉冲2b:等级Ⅲ, 脉冲3a:等级Ⅰ, 脉冲3b:等级Ⅰ, 脉冲 4:等级Ⅲ。
铁将 军
222 222 222 222 222 222 222 222 222 222 222 222
1 1
2hour 2-3 s月
2hour 2-3 s月
鉴定 后小 批 鉴前 定 后小 批 鉴前 定
1 6days 4月 后小
1
10day 2-3 s月
批 鉴前 定 后小 批 鉴前 定
1 1hour 4月 后小
试验报告(委托 铁将军)
试验报告(委托 铁将军)
试验报告(委托 铁将军)
试验报告(委托 铁将军)
试验报告(委托 铁将军)
试验报告(委托 铁将军)
试验报告(委托 铁将军)
试验报告(委托 铁将军)
试验报告(委托 铁将军)
试验报告(委托 铁将军)
试验报告(委托 铁将军)
试验报告(委托 铁将军)
2 2 2 1 1day 5月 后小 ok 防尘试验报告
老化监 控系统
三维振 动台
液相色 谱仪
力学试 验仪 按键耐
part5.4操作力8N-11N, 常,按键操作力符合 久性
音S量V 和HU电I-源Q0开04关-210510300 SPEC要求,并且实验前 测试仪
试验大纲(新)

2
航宇
09.10.16
江辉
介电强度
EQ 1358§7.3
介电强度:1000V 50Hz 1分钟
安培表、电压表、示波器
2
航宇
09.10.16
江辉
绝缘电阻
EQ 1358§7.4
绝缘电阻:在500V下最小100 Mohm
安培表、电压表、示波器
2
航宇
09.10.16
江辉
大气环境耐候性
耐外部温度性能
振动试验台
4
航宇
09.10.20
(肖勇)
耐老化性能
EQ 1358§9.1.
经过5次大气循环:+85°C湿度95%环境中保持16±1 h;-20°C环境中保持3±1 h;+85°C环境中保持6±1 h。循环试验结束后,在室温中保持24 h。试验后机械及电气功能正常
温湿度箱
4
航宇
09.10.18
(肖勇)
(肖勇)
儿童锁紧装置
EQ 1358§8.5.1
在环境温度下,施加1.0Nm的力矩(在两个方向末端位置);在-40°C至+85°C下施加0.5Nm的力矩(在两个方向末端位置);在相对于儿童锁止装置按钮轴45°方向施加F > 90 N的力。
扭矩扳手
2
航宇
09.10.12
(肖勇)
电器性能
锁体功耗
EQ 1358§7.1
高低温试验箱
4
航宇
09.10.15(肖勇)
低温试验
EQ 1358§9.6.1.
EQ 1588
门锁按装车位置,在-40°C下保持2小时,放到环境温度下直到形成水滴,再放在-20°C保持1小时,然后切断制冷使温度回升到-5°C,在-5°C下保持3小时。再取出样件放在环境温度下保持2小时,然后对样件洒水2分钟再从-20°C开始进行上述循环。试验后机械和电气功能正常。
型式试验大纲

JG系列船用液压缸型式试验大纲泸州市巨力液压有限公司2006年4月10日1.0 目的及范围:1.1 本大纲规定了JG系列液压缸型式试验内容。
1.2 通过型式试验,验证产品的制造质量和技术性能是否符合设计要求。
1.3 本大纲适宜于JG系列所有型号的液压缸。
2.0 编制依据2.1 CCS《钢质海船入级规范》(2006)2.2 GB/T15622-2005《液压缸试验方法》2.3 JB/T10205-2000《液压缸技术条件》3.0 说明3.1 此次认可采用JG450-500/250作为JG系列液压缸的型式试验样机。
型号说明: J G 450- 500/ 250- 2300× 4400代号安装距行程自编号缸径杆径3.2 JG450-500/250的原材料、密封件、焊接材料等均应持有CCS 证书或CCS认可的生产厂家。
3.3 提交JG450-500/250的全套零部件制造与完工质量合格检验报告。
3.4 JG450-500/250须按出厂试验大纲试验合格。
3.5 试验中,检测各项技术指标符合设计要求,如发现异常应立即停机检查,查出故障原因并经排除之后,方可继续测试。
3.6 油口连接螺纹尺寸应符合GB/T2878的规定。
3.7 活塞杆螺纹尺寸应符合GB/T2348的规定。
3.8 密封应符合GB/T2879、GB/T2880、GB/T6577、GB/T6578的规定。
3.9 零部件装配技术要求应符合GB/T7935-1987中的1.5~1.8的规定。
3.10 试验结束后应拆检,不得有异常现象。
4.0 试验条件4.1 用于型式试验的液压试验台应满足上述规范及标准要求。
4.2 使用油温在40℃时的运动粘度为29~74mm/s的液压油(YC-N32)。
4.3 型式试验时油温应保持在50±2℃范围内进行。
4.4 测试、试验用压力表,压力传感器测量范围为1.5倍最大工作压力(30Mpa),应在检定有效期内。
- 1、下载文档前请自行甄别文档内容的完整性,平台不提供额外的编辑、内容补充、找答案等附加服务。
- 2、"仅部分预览"的文档,不可在线预览部分如存在完整性等问题,可反馈申请退款(可完整预览的文档不适用该条件!)。
- 3、如文档侵犯您的权益,请联系客服反馈,我们会尽快为您处理(人工客服工作时间:9:00-18:30)。
DA01002B0 零部件試驗大綱
擬制/日期:劉志洪/李儒康3/6/2002 審查/日期:李儒康//6/2002
批準/日期:廖健化//7/2002
2002-03-07
發布2002-03-07 實施
富士高產品開發部發布
表1.0
表1.0
表1.0
表1.0
表1.0
表1.0
表1.0
表1.0
表1.0
表1.0
表1.0
表1.0
表1.0
表1.0
表1.0
表1.0
表1.0
表1.0
表1.0
表1.0
表1.0
表1.0
注「本試驗大綱中帶號表示為選用項目,未注明的時間誤差為土 5秒,未注明的溫度誤差為土 2C .
2•在打樣和首批進料時需完成相關項目.
3•正常進料時IQC需要根据具体情況來定抽測頻次和項目
4 •實際操作中如產品有特別的要求,則應遵照執行.
Welcome To Download !!!
欢迎您的下载,资料仅供参考!
精品资料。