单元三:晶圆的制程与量测
晶圆制造前道量检测工艺分类、特征、价值分析
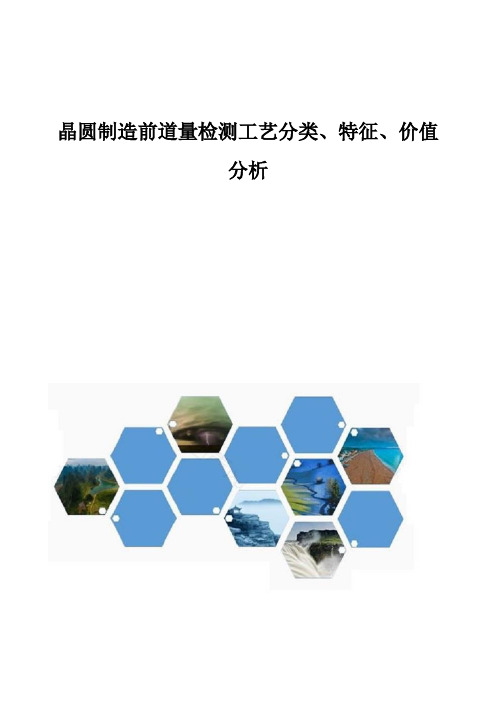
晶圆制造前道量检测工艺分类、特征、价值分析(一)前道量检测贯穿晶圆制造环节始终,是芯片生产线的“监督员”前道量检测使整条前道工艺产线的控制达到最佳化,同时也为追寻芯片生产中发现的问题提供了重要的追寻线索。
半导体芯片制造工艺步骤极多,各步骤之间可能会相互影响,因此很难根据最后出厂产品的检测结果准确分析出影响产品性能与合格率的具体原因。
而且如果不能在生产过程中及时检测到工艺缺陷,则此批次工艺中生产出来的大量不合格产品也会额外增加厂商的生产成本。
因此前道量检测贯穿芯片制造环节始终,对加工制造过程进行实时的监控,确保每一步加工后的产品均符合参数要求。
而且,产品小组可以通过分析前道量检测产生的检测数据及时发现问题根源,使之能够采取最有效的方式进行应对,从而制造出参数均匀、成品率高、可靠性强的芯片。
前道量检测根据测试目的可以细分为量测和检测。
量测主要是对芯片的薄膜厚度、关键尺寸、套准精度等制成尺寸和膜应力、掺杂浓度等材料性质进行测量,以确保其符合参数设计要求;而检测主要用于识别并定位产品表面存在的杂质颗粒沾污、机械划伤、晶圆图案缺陷等问题。
前道量检测分类及主要技术资料来源:公开资料前道量测、检测均会用到光学技术和电子束技术,但是两种技术在量测与检测下各具不同的特点。
光学量测通过分析光的反射、衍射光谱间接进行测量,其优点是速度快、分辨率高、非破坏性,但缺点是需借助其他技术进行辅助成像;电子束量测是根据电子扫描直接放大成像,其优点是可以直接成像进行测量,但缺点是速度慢、分辨率低,而且使用电子束进行成像量测操作时需要切割晶圆,(立鼎产业研究网)因此电子束量测具有破坏性。
光学检测是通过光信号对比发现晶圆上存在的缺陷,其优点是速度快,但缺点是无法呈现出缺陷的具体形貌;而电子束检测可以直接呈现缺陷的具体形貌,但是该方法在精度要求非常高的情况下会耗费大量的时间。
在实际的芯片制造过程中,光学技术与电子束技术常常被结合使用,比如检测环节一般先采用光学检测定位缺陷位置,再使用电子束检测对缺陷进行精确扫描成像,两种技术的结合使用可以提高量检测的效率,并降低对芯片的破坏性。
晶圆测试全流程详解

晶圆测试全流程详解In the semiconductor industry, wafer testing, also known as wafer probing or crystal wafer testing, is a critical step in the production process. 在半导体行业,晶圆测试,也称为晶圆探针测试或晶圆测试,是生产过程中至关重要的一步。
Wafer testing is the process of testing the integrated circuits (ICs) on a semiconductor wafer to ensure they function correctly before they are diced and packaged into individual ICs. 晶圆测试是在晶圆上测试集成电路(IC)以确保它们在被切割成单个IC 并封装之前能够正确运行的过程。
This thorough testing is essential to identify any defects or faults in the ICs before they are assembled into electronic devices. 这种彻底的测试是为了在将IC组装成电子设备之前识别出IC中的任何缺陷或故障是至关重要的。
A wafer testing process typically involves several key steps, including wafer loading, prober testing, electrical testing, and sorting. 晶圆测试过程通常包括几个关键步骤,包括晶圆装载、探针测试、电子测试和分选。
The process begins with loading the semiconductor wafers onto a prober, which is a machine designed to make physical contact with the integrated circuits on the wafer. 这个过程始于将半导体晶圆装载到一台探测机上,探测机是一种专门设计用来与晶圆上的集成电路进行物理接触的机器。
晶圆检测的流程

晶圆检测是半导体制造工艺中非常重要的环节,用于确保晶圆质量和产品可靠性。
以下是晶圆检测的一般流程:1.准备工作:首先,需要准备晶圆检测所需的设备和测试工艺。
这可能包括测试设备、探针卡、测试程序等。
此外,还需要准备相关的测试标准和规范,以作为判断晶圆是否合格的依据。
2.晶圆上机:将待测晶圆安装到测试设备上,通常是使用专用的晶圆探针卡将晶圆与测试设备连接起来。
探针卡上的针脚与晶圆上的测试点相对应,以实现对晶圆上各个区域的测试。
3.电性能测试:对晶圆进行电性能测试,以评估晶体管、寄生电容、电阻等电器特性。
这通常涉及在不同测试点进行电压和电流的测量,并记录相应的电器参数。
4.光性能测试:对晶圆进行光学性能测试,以评估其光学特性。
这可能包括测量晶圆上的光散射、透明度、反射系数等参数。
对于光电器件,还可能需要进行光功率、谱响应等测试。
5.结果分析:对测试数据进行分析和比较,以确定晶圆是否符合规格要求。
通过与标准进行对比,评估晶圆的良品率和缺陷类型。
对于有缺陷的晶圆,可能需要进一步分析其缺陷的位置、大小、形态等信息。
6.结果判定:基于测试数据和分析结果,进行晶圆的结论判定。
通常会根据设定的标准和规范,将晶圆分为合格品、不良品或需进一步验证的品质。
7.记录和报告:对测试结果进行记录和报告,包括测试数据、缺陷分布、结论判定等重要信息。
这有助于跟踪晶圆的质量和缺陷情况,并为日后的制程改进提供参考。
在整个流程中,关键是准确选择合适的测试方法、保证测试设备的稳定性和可靠性,并按照标准和规程进行操作。
只有经过细致和全面的检测,才能确保生产出质量可靠的晶圆和半导体产品。
简述晶圆测试流程

简述晶圆测试流程晶圆测试流程通常包括以下几个步骤:1. 准备工作在进行晶圆测试之前,首先需要对测试设备进行准备工作。
这包括清洁测试设备和测试工具,确保它们的精度和准确性。
同时,还需要准备好测试程序和测试规范,以确保测试的质量和准确性。
2. 外延片测试在晶圆测试的第一步是对外延片进行测试。
外延片是由单晶硅生长而成的薄片,它是晶圆的基础。
在外延片测试中,通常使用探针测试仪来测试外延片的电性能和其他关键参数,以确保外延片的质量和稳定性。
3. 晶圆测试一旦外延片测试通过,接下来就是对晶圆进行测试。
晶圆测试通常包括以下几个步骤:a. 探针测试在探针测试中,测试仪将探针接触到晶圆表面的不同位置,测量不同位置的电性能和其他关键参数。
这些参数包括电导率、电阻率、电容率等。
通过这些测试,可以了解晶圆的整体质量和性能。
b. 光学测试光学测试是对晶圆表面进行光学检测和测量的过程。
通过光学测试,可以检测晶圆表面的缺陷、杂质和其他问题,以确保晶圆的表面质量和稳定性。
c. 热测试热测试是对晶圆进行热性能测试的过程。
通过热测试,可以了解晶圆在不同温度下的性能和稳定性,以确保其可以在各种环境下正常工作。
4. 数据分析和报告一旦完成晶圆测试,就需要对测试数据进行分析,并生成测试报告。
测试报告包括测试结果、测试数据、测试参数、测试结论等。
通过数据分析和报告,可以评估晶圆的质量和稳定性,以确保其符合要求。
总之,晶圆测试是半导体制造过程中的一个非常关键的环节。
它是确保晶圆质量和性能的关键步骤,需要进行外延片测试、晶圆测试、数据分析和报告等多个步骤。
只有通过严格的测试流程,才能确保晶圆的质量和稳定性,从而保证最终芯片的性能和可靠性。
晶圆测试

晶圆测试Wafer probe 在半导体制程上,主要可分成IC 设计、晶圆制程(Wafer Fabrication ,简称Wafer Fab )、晶圆测试(Wafer Probe ),及晶圆封装(Packaging )。
晶圆测试是对芯片上的每个晶粒进行针测,在检测头装上以金线制成细如毛发之探针(probe ),与晶粒上的接点(pad )接触,测试其电气特性,不合格的晶粒会被标上记号,而后当芯片依晶粒为单位切割成独立的晶粒时,标有记号的不合格晶粒会被洮汰,不再进行下一个制程,以免徒增制造成本。
晶圆测试是对芯片上的每个晶粒进行针测,在检测头装上以金线制成细如毛发之探针(probe ),与晶粒上的接点(pad )接触,测试其电气特性,不合格的晶粒会被标上记号,而后当芯片依晶粒为单位切割成独立的晶粒时,标有记号的不合格晶粒会被洮汰,不再进行下一个制程,以免徒增制造成本。
晶圆边缘和背面缺陷检测系统Nanophotonics 公司新推出的结合边缘和背面的缺陷检测系统,该系统可供制造过程中的边缘和背面缺陷的检测,随着晶圆制造向12寸及以上发展,晶圆制造商对边缘和背面缺陷检测有了更多更新的要求, Nanophotonics 公司针对此情况,进一步创新,研发出具有更高的产能,更小的设备尺寸及更高兼容性的边缘和背面的缺陷检测系统,为晶圆制造商提供了完美的解决方案。
宏观缺陷检测模块2008-05-04 点击:39 Axi 940是全表面Explorer Inspection Cluster 设备的一部分,主要用于对晶圆前表面的宏观缺陷检测。
其智能软件可以自动完成很多操作员才能完成的任务,因而降低了配方准备的时间。
Axi 还可以在簇群其他部分仍处于运行状态时进行离线的配方准备。
拉曼扫描SWIFT 和DuoScan 是支持对大面积样品进行快速绘图的拉曼扫描技术。
SWIFT 可保证每个像素点的扫描时间只有7毫秒。
可在6分钟内获得五万个光谱图像。
晶圆生产流程及每道工序的关键工艺参数
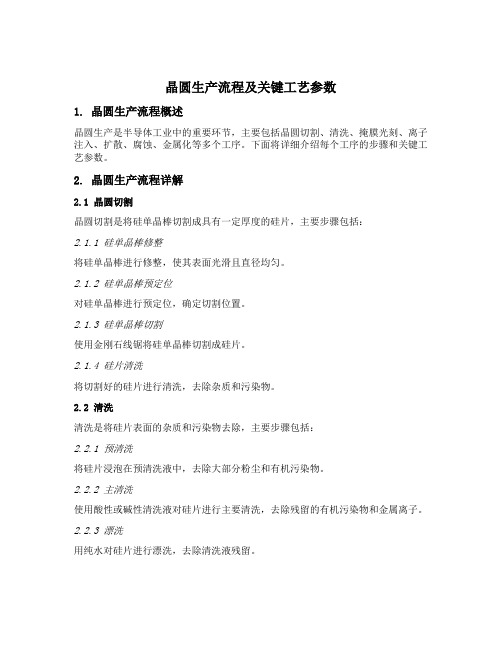
晶圆生产流程及关键工艺参数1. 晶圆生产流程概述晶圆生产是半导体工业中的重要环节,主要包括晶圆切割、清洗、掩膜光刻、离子注入、扩散、腐蚀、金属化等多个工序。
下面将详细介绍每个工序的步骤和关键工艺参数。
2. 晶圆生产流程详解2.1 晶圆切割晶圆切割是将硅单晶棒切割成具有一定厚度的硅片,主要步骤包括:2.1.1 硅单晶棒修整将硅单晶棒进行修整,使其表面光滑且直径均匀。
2.1.2 硅单晶棒预定位对硅单晶棒进行预定位,确定切割位置。
2.1.3 硅单晶棒切割使用金刚石线锯将硅单晶棒切割成硅片。
2.1.4 硅片清洗将切割好的硅片进行清洗,去除杂质和污染物。
2.2 清洗清洗是将硅片表面的杂质和污染物去除,主要步骤包括:2.2.1 预清洗将硅片浸泡在预清洗液中,去除大部分粉尘和有机污染物。
2.2.2 主清洗使用酸性或碱性清洗液对硅片进行主要清洗,去除残留的有机污染物和金属离子。
2.2.3 漂洗用纯水对硅片进行漂洗,去除清洗液残留。
2.2.4 干燥将硅片在干燥器中进行干燥,去除水分。
2.3 掩膜光刻掩膜光刻是通过光刻胶和掩膜模板将芯片图形转移到硅片上,主要步骤包括:2.3.1 光刻胶涂覆将光刻胶均匀涂覆在硅片上。
2.3.2 掩膜对位将掩膜模板对准硅片,并通过对位器进行精确定位。
2.3.3 曝光使用紫外光将掩膜模板上的芯片图形转移到硅片上。
2.3.4 显影使用显影液去除未曝光的光刻胶,形成芯片图形。
2.4 离子注入离子注入是将特定元素注入硅片表面,改变硅片的导电性能,主要步骤包括:2.4.1 离子源准备准备离子源和加速器设备,确定注入元素和能量。
2.4.2 离子束对准将离子束对准硅片表面,并通过对位器进行精确定位。
2.4.3 注入通过加速器加速离子束,使其注入硅片表面,并控制注入剂量和深度。
2.5 扩散扩散是将特定元素在硅片中进行扩散,形成PN结构,主要步骤包括:2.5.1 清洗将注入后的硅片进行清洗,去除污染物。
晶圆(Wafer) 制程工艺学习

晶圆(Wafer)制程工藝學習晶圆(Wafer)的生产由砂即(二氧化硅)开始,经由电弧炉的提炼还原成冶炼级的硅,再经由盐酸氯化,产生三氯化硅,经蒸馏纯化后,透过慢速分解过程,制成棒状或粒状的「多晶硅」。
一般晶圆制造厂,将多晶硅融解后,再利用硅晶种慢慢拉出单晶硅晶棒。
一支85公分长,重76.6公斤的8吋硅晶棒,约需2天半时间长成。
经研磨、拋光、切片后,即成半导体之原料晶圆片。
光学显影光学显影是在光阻上经过曝光和显影的程序,把光罩上的图形转换到光阻下面的薄膜层或硅晶上。
光学显影主要包含了光阻涂布、烘烤、光罩对准、曝光和显影等程序。
小尺寸之显像分辨率,更在 IC 制程的进步上,扮演着最关键的角色。
由于光学上的需要,此段制程之照明采用偏黄色的可见光。
因此俗称此区为黄光区。
干式蚀刻技术在半导体的制程中,蚀刻被用来将某种材质自晶圆表面上移除。
干式蚀刻(又称为电浆蚀刻)是目前最常用的蚀刻方式,其以气体作为主要的蚀刻媒介,并藉由电浆能量来驱动反应。
电浆对蚀刻制程有物理性与化学性两方面的影响。
首先,电浆会将蚀刻气体分子分解,产生能够快速蚀去材料的高活性分子。
此外,电浆也会把这些化学成份离子化,使其带有电荷。
晶圆系置于带负电的阴极之上,因此当带正电荷的离子被阴极吸引并加速向阴极方向前进时,会以垂直角度撞击到晶圆表面。
芯片制造商即是运用此特性来获得绝佳的垂直蚀刻,而后者也是干式蚀刻的重要角色。
基本上,随着所欲去除的材质与所使用的蚀刻化学物质之不同,蚀刻由下列两种模式单独或混会进行:1. 电浆内部所产生的活性反应离子与自由基在撞击晶圆表面后,将与某特定成份之表面材质起化学反应而使之气化。
如此即可将表面材质移出晶圆表面,并透过抽气动作将其排出。
2. 电浆离子可因加速而具有足够的动能来扯断薄膜的化学键,进而将晶圆表面材质分子一个个的打击或溅击(sputtering)出来。
化学气相沉积技术化学气相沉积是制造微电子组件时,被用来沉积出某种薄膜(film)的技术,所沉积出的薄膜可能是介电材料(绝缘体)(dielectrics)、导体、或半导体。
晶圆测试

每颗IC在后工序之前都必须进行CP(Chip Prober),以验证产品的功能是否正常,并挑出不良的产品和区分性能等级。
CP主要设备包括测试机(Tester)和探针台(Prober)。
测试机主要包括测试主机、测试板(DUT板)、测试软体、数据线、PC主机等。
操作:1. 确认DUT板、数据线连接正确;2. 打开电源,启动PC,进入测试软体;3. 打开测试程序;4. 打开测试主机电源,此时PC上会显示系统初始化。
探针卡主要部件:真空泵、探针卡、显微镜、打点器、操作软件、8''至4''真空旋钮、托盘(Tray)、旋转手轮等。
测试前操作:1. 确认真空泵和主机电源打开,打开软体初始化系统;2. 进入扫描模式,移动Tray到一个角落安装prober card。
将prober card安装在探针台上,一端对齐固定架并固定好,整理好数据线,引出接在DUT板上,并注意对应好标号;3. 调整预置高度使之降低为0(防止上片时把prober和wafer刮坏);4. 清洁工作盘,确认测试wafer size并调节真空旋钮,带好手套讲被测wafer放入tray正中央(先确认wafer缺口方向使IC pin与探针相对应),用真空使wafer吸附在tray上;5. 进片,调整预置高度(针压),边上升高度(探针卡固定,tray上升)边观察wafer离probercard的距离,调整到适当的距离时停止上升(wafer和prober距离不能太近以防wafer刮到prober),调节显微镜调到最清晰的视窗,然后把wafer的水平位置扫直;6. 填写测试数据,包括wafer size、X、Y步距、测试方法和测试map数据等等(注意X、Y的移动距离、多测的排列顺序应该与prober card的site的排列顺序一致);7. 对针痕,微动模式移动wafer,使针尖对准die pad,慢慢调整预置高度(针压),直到可以在die pad上扎出针痕(注意针痕不能太重,高度只能一点一点增加,直至出现针痕马上停止),微动调整针痕的位置,使之一定扎在die pad的中心位置。
晶圆的测试方法与流程

晶圆的测试方法与流程晶圆测试方法与流程是指对晶圆进行一系列测试来确定其物理、化学和尺寸等方面的特征,从而为半导体制造和器件设计提供基础数据。
以下是晶圆测试方法与流程的正文:1. 物理测试物理测试用于测量晶圆的尺寸、形状、密度和表面质量等特征。
常用的物理测试方法包括扫描电镜(SEM)、X射线衍射(X射线衍射(XRD))和表面测量技术(STEM)等。
扫描电镜可以测量晶圆表面的细节和形状,以及其尺寸和形状误差。
X射线衍射可以测量晶圆的原子结构和尺寸,以及晶圆的晶体结构。
表面测量技术则可以测量晶圆表面的粗糙度和形状误差。
2. 化学测试化学测试用于测量晶圆中的化学成分和化学键的位置等特征。
常用的化学测试方法包括原子力显微镜(AFM)和化学分析技术等。
AFM可以测量晶圆表面的化学成分和键的位置,以及其表面结构和尺寸。
化学分析技术则可以分析晶圆中的元素和化合物的种类和分布。
3. 尺寸测量尺寸测量用于确定晶圆的大小和形状,以及其表面和内部的特征。
常用的尺寸测量方法包括光学测量技术(光学显微镜(OM))和电子测量技术(EM))等。
光学测量技术可以测量晶圆表面的尺寸和形状,以及其内部的特征。
例如,扫描隧道显微镜(STM)可以测量晶圆表面的三维尺寸和表面形貌。
电子测量技术则可以测量晶圆内部的尺寸和形状,以及其原子结构和晶体结构。
4. 性能测试性能测试用于评估晶圆的半导体性能,例如导电性、光吸收、热传导等。
常用的性能测试方法包括热膨胀测试、电学测试和光学测试等。
热膨胀测试可以测量晶圆在温度变化时的膨胀和收缩行为,从而评估晶圆的热稳定性。
电学测试可以测量晶圆在不同电场下的电学性质,从而评估晶圆的导电性。
光学测试则可以测量晶圆在不同光照下的光吸收和反射等特性,从而评估晶圆的光吸收性能。
晶圆测试方法与流程是一个复杂的过程,需要多种测试技术的配合,才能准确评估晶圆的物理、化学和尺寸等特征,为半导体制造和器件设计提供基础数据。
晶圆制造的全制程详细流程步骤

晶圆制造的全制程详细流程步骤1.晶圆制造的第一步是原料的准备和筛选。
The first step in wafer manufacturing is the preparation and screening of raw materials.2.接着是将原料进行混合和研磨,以确保质地均匀。
Then the raw materials are mixed and ground to ensure uniform texture.3.混合研磨后的原料被压制成圆形块状。
The mixed and ground raw materials are compressed into circular blocks.4.圆形块状的原料经过高温高压处理,形成晶体结构。
The circular block of raw materials is processed at high temperature and high pressure to form a crystalline structure.5.接着是将晶体块状材料切割成薄片,形成晶圆的基础材料。
Then the crystalline block material is cut into thin slices to form the basic material for wafers.6.切割后的晶圆基础材料需要进行清洗和化学处理,以去除杂质和提高表面光洁度。
The cut wafer base material needs to be cleaned and chemically treated to remove impurities and improve surface smoothness.7.清洗处理后的晶圆基础材料需要进行光刻,将图形和结构转移到表面。
The cleaned and treated wafer base material needs to undergo photolithography to transfer patterns and structures onto the surface.8.光刻之后,晶圆基础材料被浸入化学溶液中进行腐蚀和刻蚀。
晶圆封装测试工序和半导体制造工艺流程

A.晶圆封装测试工序一、IC检测1. 缺陷检查Defect Inspection2. DR-SEM(Defect Review Scanning Electron Microscopy)用来检测出晶圆上是否有瑕疵,主要是微尘粒子、刮痕、残留物等问题。
此外,对已印有电路图案的图案晶圆成品而言,则需要进行深次微米范围之瑕疵检测。
一般来说,图案晶圆检测系统系以白光或雷射光来照射晶圆表面。
再由一或多组侦测器接收自晶圆表面绕射出来的光线,并将该影像交由高功能软件进行底层图案消除,以辨识并发现瑕疵。
3. CD-SEM(Critical Dimensioin Measurement)对蚀刻后的图案作精确的尺寸检测。
二、IC封装1. 构装(Packaging)IC构装依使用材料可分为陶瓷(ceramic)及塑胶(plastic)两种,而目前商业应用上则以塑胶构装为主。
以塑胶构装中打线接合为例,其步骤依序为晶片切割(die saw)、黏晶(die mount / die bond)、焊线(wire bond)、封胶(mold)、剪切/成形(trim / form)、印字(mark)、电镀(plating)及检验(inspection)等。
(1) 晶片切割(die saw)晶片切割之目的为将前制程加工完成之晶圆上一颗颗之晶粒(die)切割分离。
举例来说:以0.2微米制程技术生产,每片八寸晶圆上可制作近六百颗以上的64M微量。
欲进行晶片切割,首先必须进行晶圆黏片,而后再送至晶片切割机上进行切割。
切割完后之晶粒井然有序排列于胶带上,而框架的支撑避免了胶带的皱褶与晶粒之相互碰撞。
(2) 黏晶(die mount / die bond)黏晶之目的乃将一颗颗之晶粒置于导线架上并以银胶(epoxy)粘着固定。
黏晶完成后之导线架则经由传输设备送至弹匣(magazine)内,以送至下一制程进行焊线。
(3) 焊线(wire bond)IC构装制程(Packaging)则是利用塑胶或陶瓷包装晶粒与配线以成集成电路(Integrated Circuit;简称IC),此制程的目的是为了制造出所生产的电路的保护层,避免电路受到机械性刮伤或是高温破坏。
晶圆制造质量测试报告

晶圆制造质量测试报告晶圆制造质量测试报告为了确保晶圆制造的质量,我们进行了详细的测试和评估。
以下是我们的测试报告。
1. 测试目的:评估晶圆的物理和电学性能。
2. 测试方法:我们使用了一系列测试设备和工具,包括:显微镜、化学分析仪、力学测试机和电子测试仪器等。
3. 测试内容:a. 物理性能测试:(1) 晶圆外观检查:检查晶圆表面的平整度、光洁度和是否有明显的缺陷。
(2) 尺寸测量:使用显微镜和光学测量仪器测量晶圆的直径和厚度。
(3) 硬度测试:使用硬度计测量晶圆表面的硬度。
b. 化学性能测试:(1) 成分分析:使用化学分析仪检测晶圆材料的化学成分。
(2) 杂质检测:通过化学分析和显微镜检测晶圆中是否存在杂质。
c. 电学性能测试:(1) 导电性测试:使用电阻计测量晶圆的导电性能。
(2) 电容性测试:使用电容计测量晶圆的电容性能。
4. 测试结果:a. 物理性能:(1) 晶圆外观:晶圆表面平整、光洁,无明显缺陷。
(2) 尺寸:晶圆直径为30mm,厚度为2mm。
(3) 硬度:晶圆表面硬度为70HRC。
b. 化学性能:(1) 成分分析:晶圆材料主要成分为硅(Si),杂质含量小于0.1%。
(2) 杂质检测:未检测到明显的杂质。
c. 电学性能:(1) 导电性:晶圆导电性良好,电阻率为1x10^-6 Ω·cm。
(2) 电容性:晶圆电容性稳定,电容值为2μF。
5. 结论:根据以上测试结果,晶圆的质量良好,符合制造要求。
晶圆具有良好的物理、化学和电学性能,适用于后续半导体制造工艺。
我们将持续监控和改进晶圆制造过程,以确保产品质量的稳定性和可靠性。
半导体晶圆 检测精度要求标准(一)

半导体晶圆检测精度要求标准(一)半导体晶圆检测精度要求标准引言随着半导体技术的不断发展,晶圆的检测精度对于半导体行业的发展起着至关重要的作用。
合理的检测标准能够有效地提高生产效率,降低生产成本,同时确保产品的质量稳定。
本文将对半导体晶圆的检测精度要求标准进行详细探讨。
1. 检测目标在制定半导体晶圆的检测精度要求标准之前,首先需要明确检测的目标。
以下是晶圆检测的核心目标: - 检测表面缺陷,如划痕、裂纹等 - 检测层厚度的一致性,确保每个区域的材料厚度符合要求 -检测杂质、污染物的存在,以保证晶圆的纯净度 - 检测图案的位置和尺寸准确性,确保电路布局的精确性2. 检测方法针对晶圆的检测需求,常用的检测方法包括以下几种: - 光学检测:通过光学显微镜等设备对晶圆进行表面缺陷检测和层厚度测量 -X射线检测:利用X射线能够透过晶圆进行成分分析和污染物检测 -激光检测:利用激光器对晶圆进行位置和尺寸的测量 - 探针测量:采用电子探针等设备对电学性能进行测试,如电阻、电容等3. 检测精度要求根据晶圆的应用领域和制造工艺的要求,制定适当的检测精度标准是非常重要的。
以下是常见的检测精度要求: - 表面缺陷:能够检测到微米以下的小尺寸缺陷 - 层厚度一致性:精度要求在%以内 -杂质、污染物:能够检测到1ppm以下的微量杂质 - 图案位置和尺寸:精度要求在1微米以内 - 电学性能:电阻、电容等测量误差在1%以内4. 检测设备要求为了满足以上的检测精度要求,需要配备高质量的检测设备。
以下是常见的检测设备要求: - 光学检测设备:具备高分辨率、高对比度、大深度视场等特点 - X射线检测设备:探测器灵敏度高,对X射线的能量分辨率高 - 激光检测设备:激光器功率稳定,测量系统的抗干扰性强 - 探针测量设备:具备高分辨率、低噪声、高速度等特点总结半导体晶圆的检测精度标准是确保产品质量的关键因素之一。
本文从检测目标、方法、精度要求以及设备要求等方面对半导体晶圆的检测精度要求进行了详细阐述。
晶圆边界和凹槽轮廓尺寸测量_概述说明以及解释

晶圆边界和凹槽轮廓尺寸测量概述说明以及解释1. 引言1.1 概述晶圆边界和凹槽轮廓尺寸测量是半导体制造和微电子封装领域中非常重要的任务。
在这些工业过程中,精确测量晶圆边界和凹槽轮廓的尺寸具有关键意义,因为它们直接影响着产品的品质和性能。
本文将详细介绍晶圆边界和凹槽轮廓尺寸测量的要点、方法以及注意事项。
同时,我们还将分析这些测量任务所面临的挑战,并提供解决方案。
1.2 文章结构本文章共分为五个部分。
首先是引言部分,它提供了对晶圆边界和凹槽轮廓尺寸测量主题的简要介绍。
接下来,第二部分将详细介绍晶圆边界测量要点、凹槽轮廓尺寸测量要点以及相应的测量方法。
第三部分将着重讨论注意事项和挑战,包括精度要求与误差分析、测量工具选择与校准以及数据处理与分析方法。
在第四部分,我们将通过典型应用案例分析,探讨晶圆边界测量在半导体制造中的应用和凹槽轮廓尺寸测量在微电子封装中的应用,并分享一些成功的案例和经验总结。
最后,在第五部分中,我们将对全文进行总结,并展望未来晶圆边界和凹槽轮廓尺寸测量的发展方向。
1.3 目的本文的目的是为读者提供关于晶圆边界和凹槽轮廓尺寸测量的全面概述以及详细解释。
通过阅读本文,读者将了解到如何在半导体制造和微电子封装领域中进行有效、精准地测量晶圆边界和凹槽轮廓尺寸,并能够了解相关挑战及其应对策略。
同时,我们希望通过案例分析来启发读者在实践中运用这些技术,并为未来的研究和发展提供展望。
2. 晶圆边界和凹槽轮廓尺寸测量晶圆边界和凹槽轮廓尺寸测量是在半导体制造和微电子封装过程中非常重要的环节。
这些测量提供了对晶圆的形状、大小和结构等关键参数进行评估和分析的能力。
本部分将介绍晶圆边界和凹槽轮廓尺寸测量的要点,并介绍常用的测量方法。
2.1 晶圆边界测量要点在晶圆制造过程中,准确地确定晶圆的边界是十分重要的。
晶圆边界决定了材料的利用效率,并且影响到后续工艺步骤的精度和可靠性。
因此,进行晶圆边界测量时需要注意以下要点:- 测量方法选择:常用的晶圆边界测量方法包括显微镜观察、投影仪、光学扫描等。
晶圆的快速测试方法

晶圆的快速测试方法晶圆的快速测试方法摘要:晶圆测试(wafer probe)是对晶片上单个晶粒通过探针测试,筛选不良品的一种方法。
它是集成电路生产中的一个重要环节,不仅能最大限度的节约封装及成品测试(Finial Test)成本,还能及时反映出晶圆制造厂的良品率。
本文主要介绍如何通过快速测试(speed probe)来降低晶圆测试成本,缩短测试时间,提高测试效率。
关键字:晶圆测试;晶圆快速测试;测试时间1 引言随着集成电路工艺的迅猛发展,也促使集成电路测试技术不断更新,以提高半导体行业的生产效益。
其中晶圆测试对整个集成电路生产过程的良品率及成本控制起着重要的作用。
2 晶圆测试概述2.1 晶圆测试介绍晶圆测试是半导体后段区分良品与不良品的第一道工序,主要目的是对晶圆中独立的晶粒(die)进行测试,通过探针卡接触晶粒上的触点(bond pad),测试其电气功能特性,把不良片筛选出来,同时按照电性不良类型把不合格的产品分类(bin),提供给晶圆制造厂进行数据分析,改进工艺。
不合格的晶粒会被标上记号,而后当芯片依晶粒为单位切割成独立的晶粒时,标有记号的不合格晶粒会被洮汰,不再进行下一个制程,以免徒增制造成本。
2.2 晶圆测试分类通常情况下,晶圆测试是对一片晶圆上每一个独立完整的芯片进行测试,逐一执行程序中设定的所有测试项(Full Probe),即完全测试,它主要针对研发阶段及设计生产逐步走向成熟的产品。
但随着晶圆生产工艺的不断完善,测试环节的成本控制就会显得尤为重要。
更重要的一个因素是,随着电子行业的飞速发展,半导体厂需要以更快更优的方式把产品提供给客户。
这就决定了测试工程师必须进一步分析测试程序,研究什么需要被测试以及以何种方式满足这些测试。
因此晶圆的快速测试方法应运而生,它是一个既满足成本控制,又能提高测试效率的最佳解决方案。
3 晶圆的快速测试方法在晶圆快速测试(speed probe)中,首先把整片晶圆按照良品率分为两个区域。
晶圆检测流程

晶圆检测流程下载温馨提示:该文档是我店铺精心编制而成,希望大家下载以后,能够帮助大家解决实际的问题。
文档下载后可定制随意修改,请根据实际需要进行相应的调整和使用,谢谢!并且,本店铺为大家提供各种各样类型的实用资料,如教育随笔、日记赏析、句子摘抄、古诗大全、经典美文、话题作文、工作总结、词语解析、文案摘录、其他资料等等,如想了解不同资料格式和写法,敬请关注!Download tips: This document is carefully compiled by theeditor. I hope that after you download them,they can help yousolve practical problems. The document can be customized andmodified after downloading,please adjust and use it according toactual needs, thank you!In addition, our shop provides you with various types ofpractical materials,such as educational essays, diaryappreciation,sentence excerpts,ancient poems,classic articles,topic composition,work summary,word parsing,copy excerpts,other materials and so on,want to know different data formats andwriting methods,please pay attention!晶圆检测流程通常包括以下步骤:1. 外观检查:查看晶圆表面是否有划痕、污染等缺陷。
晶圆宏观检测

晶圆宏观检测
晶圆宏观检测是指在晶圆制造完成后,对晶圆进行全面的外观和尺寸检测,以确保晶圆的完整性和一致性。
以下是晶圆宏观检测的步骤:
外观检测:使用自动化机器视觉系统对晶圆表面进行快速扫描,检测表面是否存在裂纹、划痕、凹坑等缺陷。
这些缺陷可能会影响晶圆的性能和可靠性。
尺寸检测:测量晶圆的直径、厚度等关键尺寸,确保它们符合设计要求。
同时,还需要检查晶圆的翘曲度和平行度,以确保晶圆具有良好的平面度和稳定性。
边缘检测:检查晶圆的边缘是否平滑、无毛刺,以及边缘的形状是否符合设计要求。
定位检测:使用激光干涉仪等高精度测量设备对晶圆进行定位检测,确保晶圆在封装前后的位置和旋转角度准确无误。
材料检测:通过化学分析、X射线衍射等方法对晶圆材料的成分和结构进行检测,以确保晶圆的质量和可靠性。
通过以上步骤,可以全面评估晶圆的外观、尺寸、边缘、定位和材料等方面的质量,为后续的封装和测试提供可靠的保障。
晶圆(Wafer) 制程工艺学习

晶圆(Wafer)制程工藝學習晶圆(Wafer)的生产由砂即(二氧化硅)开始,经由电弧炉的提炼还原成冶炼级的硅,再经由盐酸氯化,产生三氯化硅,经蒸馏纯化后,透过慢速分解过程,制成棒状或粒状的「多晶硅」。
一般晶圆制造厂,将多晶硅融解后,再利用硅晶种慢慢拉出单晶硅晶棒。
一支85公分长,重76.6公斤的8吋硅晶棒,约需2天半时间长成。
经研磨、拋光、切片后,即成半导体之原料晶圆片。
光学显影光学显影是在光阻上经过曝光和显影的程序,把光罩上的图形转换到光阻下面的薄膜层或硅晶上。
光学显影主要包含了光阻涂布、烘烤、光罩对准、曝光和显影等程序。
小尺寸之显像分辨率,更在 IC 制程的进步上,扮演着最关键的角色。
由于光学上的需要,此段制程之照明采用偏黄色的可见光。
因此俗称此区为黄光区。
干式蚀刻技术在半导体的制程中,蚀刻被用来将某种材质自晶圆表面上移除。
干式蚀刻(又称为电浆蚀刻)是目前最常用的蚀刻方式,其以气体作为主要的蚀刻媒介,并藉由电浆能量来驱动反应。
电浆对蚀刻制程有物理性与化学性两方面的影响。
首先,电浆会将蚀刻气体分子分解,产生能够快速蚀去材料的高活性分子。
此外,电浆也会把这些化学成份离子化,使其带有电荷。
晶圆系置于带负电的阴极之上,因此当带正电荷的离子被阴极吸引并加速向阴极方向前进时,会以垂直角度撞击到晶圆表面。
芯片制造商即是运用此特性来获得绝佳的垂直蚀刻,而后者也是干式蚀刻的重要角色。
基本上,随着所欲去除的材质与所使用的蚀刻化学物质之不同,蚀刻由下列两种模式单独或混会进行:1. 电浆内部所产生的活性反应离子与自由基在撞击晶圆表面后,将与某特定成份之表面材质起化学反应而使之气化。
如此即可将表面材质移出晶圆表面,并透过抽气动作将其排出。
2. 电浆离子可因加速而具有足够的动能来扯断薄膜的化学键,进而将晶圆表面材质分子一个个的打击或溅击(sputtering)出来。
化学气相沉积技术化学气相沉积是制造微电子组件时,被用来沉积出某种薄膜(film)的技术,所沉积出的薄膜可能是介电材料(绝缘体)(dielectrics)、导体、或半导体。
半导体晶圆的生产工艺流程介绍

半导体晶圆的生产工艺流程介绍•从大的方面来讲,晶圆生产包括晶棒制造和晶片制造两大步骤,它又可细分为以下几道主要工序(其中晶棒制造只包括下面的第一道工序,其余的全部属晶片制造,所以有时又统称它们为晶柱切片后处理工序):晶棒成长--> 晶棒裁切与检测--> 外径研磨--> 切片--> 圆边--> 表层研磨--> 蚀刻--> 去疵--> 抛光--> 清洗--> 检验--> 包装1 晶棒成长工序:它又可细分为:1)融化(Melt Down)将块状的高纯度复晶硅置于石英坩锅内,加热到其熔点1420°C以上,使其完全融化。
2)颈部成长(Neck Growth)待硅融浆的温度稳定之后,将〈1.0.0〉方向的晶种慢慢插入其中,接着将晶种慢慢往上提升,使其直径缩小到一定尺寸(一般约6mm左右),维持此直径并拉长100-200mm,以消除晶种内的晶粒排列取向差异。
3)晶冠成长(Crown Growth)颈部成长完成后,慢慢降低提升速度和温度,使颈部直径逐渐加大到所需尺寸(如5、6、8、12吋等)。
4)晶体成长(Body Growth)不断调整提升速度和融炼温度,维持固定的晶棒直径,只到晶棒长度达到预定值。
5)尾部成长(Tail Growth)当晶棒长度达到预定值后再逐渐加快提升速度并提高融炼温度,使晶棒直径逐渐变小,以避免因热应力造成排差和滑移等现象产生,最终使晶棒与液面完全分离。
到此即得到一根完整的晶棒。
2 晶棒裁切与检测(Cutting & Inspection)将长成的晶棒去掉直径偏小的头、尾部分,并对尺寸进行检测,以决定下步加工的工艺参数。
3 外径研磨(Su rf ace Grinding & Shaping)由于在晶棒成长过程中,其外径尺寸和圆度均有一定偏差,其外园柱面也凹凸不平,所以必须对外径进行修整、研磨,使其尺寸、形状误差均小于允许偏差。
- 1、下载文档前请自行甄别文档内容的完整性,平台不提供额外的编辑、内容补充、找答案等附加服务。
- 2、"仅部分预览"的文档,不可在线预览部分如存在完整性等问题,可反馈申请退款(可完整预览的文档不适用该条件!)。
- 3、如文档侵犯您的权益,请联系客服反馈,我们会尽快为您处理(人工客服工作时间:9:00-18:30)。
晶圓的製造1-1 什麼是晶圓?台灣目前是世界晶圓代工的重要國家,也是半導體的製造與資訊工業產品生產的大國,晶圓(Wafer)是製造積體電路(Integrated Circuit, IC)的基本材料,通常是由矽(Silicon, Si)或砷化鎵(Gallium Arsenide, GaAs)等半導體(Semiconductor)所組成,目前積體電路產業以矽晶圓為主。
矽晶圓是利用特殊的拉晶(Crystal Pulling)裝置將熔化的純矽,緩慢旋轉逐漸拉升冷卻以獲得單晶(Crystal)結構的晶棒(Ingot),如圖1所示。
矽晶棒再經過研磨、拋光、切片,即成矽晶圓,如圖2所示。
矽晶圓的表面光滑明亮如一片圓鏡,需要經過積體電路製造技術在晶圓的表面上製作電路元件,才能成為可用的積體電路,如圖3所示。
在矽晶片上加工製作成各種電路元件結構,成為具有特定電性功能的IC 產品。
台積電、聯電等「晶圓代工」廠,就是取得電子產品設計公司客戶委託的產品製造訂單後,將電子產品的設計圖,透過光罩製作公司轉製在數層光罩上,再以矽晶圓為基材,經過積體電路晶圓生產製造流程,將每一層光罩上的設計圖案轉置在晶圓上,每片晶圓在完成製造程序後,即可在晶圓上形成數百到數千顆相同的積體電路 (IC)小晶片。
製作完成的晶圓還要再經過測試、切割、封裝等過程,才能成為一顆顆具有各種功能的積體電路產品,如圖4所示。
圖1 晶棒 圖2 晶圓片圖3 矽晶圓與壹圓 圖4 晶片的封裝 50微米為什麼矽晶片是圓的?矽晶片的形成是從矽熔爐中,旋轉並緩慢地拉升出圓棒狀的矽晶棒;另外,晶圓外圍的電路圖樣原本就是屬於製造過程中的犧牲品;如果晶圓是四方形的,在處理、運送過程中,邊角上的晶粒反而很容易毀損。
因此圓形的晶片是最有效率的面積使用方式。
晶圓的尺寸晶圓的尺寸是以它的直徑來表示,單位是英吋。
從早期的3吋、4吋、6吋、8吋,目前半導體廠主力的12吋,和下一代的18吋,它的演進是朝向大尺寸發展,如此才能在製造的過程中有較多的面積可以使用,12吋晶圓的面積約是8吋晶圓的2.25倍,也就是可以得到較多的晶粒,以降低製造的單位成本。
1-2 晶棒成長製程矽晶棒的長成,首先需要將純度相當高的矽礦放入熔爐中,並加入預先設定好的金屬物質,使產生出來的矽晶棒擁有要求的電性特質,接著需要將所有物質融化後再長成單晶的矽晶棒。
在凝固的過程當中,固體與液體的熔質成分是不同的,在長單晶的時候,所謂的熔質指的就是雜質,雖然晶圓使用的矽相當的純,但是在凝固的過程中,雜質的影響很大,所以在凝固過程中,對於熔質進入到固體的控制是絕對嚴格。
圖5 矽晶圓的製造過程 在凝固過程之中固體設定為完全擴散,也就是固體為完全均質,而液體與固體的界面處會因為固體凝固的收縮及固體與液體的溫度差而產生所謂的熱對流,這個熱對流將影響到固體中的熔質成分,為了降低雜質的影響,又能讓液體側的成分能夠均勻,所以在液體這邊會施以擾動來降低對流所產生的邊界層(boudary layer),來讓液體側在拉晶凝固的過程中能保持一樣的成分。
柴可拉斯基長晶法 (Czochralski growth)就是利用這種原理,在液態的矽坩堝讓它有擾動,然後用小塊單晶矽當種晶(seed)下降到接觸到液態矽,之後以邊旋轉邊上拉的方式,並且控制爐溫與上拉的速度,以達到控制長出來的晶圓的直徑。
因為是有上拉的動作,稱為拉單晶。
晶圓成長的直徑、長度及雜質,都與旋轉的速度與上拉的速度以及爐溫有關聯。
晶棒長成製程如下:拉晶晶棒 晶圓1.熔化(MeltDown)此過程是將置放於石英坩鍋內的塊狀複晶矽加熱製高於攝氏1420度的熔化溫度之上,此階段中最重要的參數為坩鍋的位置與熱量的供應,若使用較大的功率來熔化複晶矽,石英坩鍋的壽命會降低,反之功率太低則融化的過程費時太久,影響整體的產能。
2.頸部成長(Neck Growth)當矽熔漿的溫度穩定之後,將晶種漸漸注入熔液中,接著將晶種往上拉昇,並使直徑縮小到一定,維持此直徑並拉長10-20cm,以消除晶種內的排差。
3.晶冠成長(Crown Growth)長完頸部後,慢慢地降低拉速與溫度,使頸部的直徑逐漸增加到所需的大小。
4.晶體成長(Body Growth)利用調整拉速與溫度來維持固定的晶棒直徑,所以坩鍋必須不斷的上升來維持固定的液面高度,而且拉速必須逐漸地降低,以避免晶棒扭曲的現象產生。
5.尾部成長(Tail Growth)當晶體成長到所要的長度後,晶棒的直徑必須逐漸地縮小,直到與液面分開。
1-3 柴可拉斯基(Czochralski)長晶法柴可拉斯基長晶法是柴可拉斯基(Czochralski)在1917年提出的長晶法,圖6為柴可拉斯基砷化鎵長晶系統,其步驟如下:(1)先將砷化鎵(GaAs)多晶(polycrystalline)放入拑鍋中,並將晶種(seed)固定在拉晶棒上,如圖6所示。
(2)為了防止熔融的砷化鎵分解,需要用熔融的三氧化二硼(B2O3),覆蓋在上面。
(3)將溫度加熱至稍高於砷化鎵的熔點約1240~1260 0C,以融解砷化鎵為熔液,等到砷化鎵熔液均勻後,就可以開始進行單晶成長。
(4)在開始進行晶體成長時,在柴可拉斯基長晶系統上方的拉晶棒開始以2~20 rpm逆時針方向旋轉,而下方的拑鍋開始以順時針方向旋轉。
(5)慢慢下降砷化鎵熔液的溫度,直到有少許的晶體材料凝固。
(6)將晶種放入已經有少許的砷化鎵固體的砷化鎵熔液中,然後以大約1~10 ㎜/小時的速度從砷化鎵熔液中拉出。
(7)砷化鎵熔液的溫度持續緩慢下降,此時晶體的直徑會逐漸增加,直到成長到所需要的大小為止。
圖6柴可拉斯基砷化鎵長晶示意圖1-4 晶棒切片與處理晶棒長成,只是整個晶圓製程的一半,接下必須將晶棒做裁切與檢測,並進行外徑研磨、切片等一連串的處理,最後才能成為一片片價值非凡的晶圓。
一支八吋矽晶棒重量約一百二十公斤,經過研磨、拋光、切割後,即成為積體電路(IC)工廠的一片片八吋矽晶圓片,以下是晶棒的處理製程。
1.切片(Slicing)從坩堝中拉出的晶柱,表面並不平整,經過工業級鑽石磨具的加工,磨成平滑的圓柱,並切除頭尾兩端錐狀段,形成標準的圓柱,被切除或磨削的部份則回收重新冶煉。
接著以以高硬度鋸片或線鋸將圓柱切成片狀的晶圓(Wafer)。
長久以來晶圓切片都是採用內徑,其鋸片是一環狀薄葉片,內徑邊緣鑲有鑽石顆粒,晶棒在切片前預先黏貼一石墨板,不僅有利於切片的夾持,更可以避免在最後切斷階段時鋸片離開晶棒所造的破裂。
2.圓邊(Edge Polishing)剛切好的晶圓,其邊緣垂直於切割平面為銳利的直角,由於矽單晶硬脆的材料特性,此角極易崩裂,不但影響晶圓強度,更為製程中污染微粒的來源,且在後續的半導體製成中,未經處理的晶圓邊緣也為影響光組與磊晶層之厚度,將片狀晶圓的圓周邊緣以磨具研磨成光滑的圓弧形的作用有:(1)防止邊緣崩裂,(2)防止在後續的製程中產生熱應力集中,(3)增加未來製程中鋪設光阻層或磊晶層的平坦度。
3.研磨(LAPPING)與蝕刻(ETCHING):由於受過機械的切削,晶圚表面粗糙,凹凸不平,及沾附切屑或污漬,研磨的目的在於除去切割或輪磨所造成的鋸痕或表面破壞層,同時使晶圓表面達到可進行拋光處理的平坦度。
因此先以化學溶液(HF/HNO3)蝕刻(Etching),去除部份切削痕跡,再經去離子純水沖洗吹乾後,進行表面研磨拋光,使晶圓像鏡面樣平滑,以利後續製程。
研磨拋光是機械與化學加工同時進行,機械加工是將晶圓放置在研磨機內,將加工面壓貼在研磨墊(Polishing Pad)磨擦,並同時滴入具腐蝕性的化學溶劑當研磨液,讓磨削與腐蝕同時產生。
研磨後的晶圓需用化學溶劑清除表面殘留的金屬碎屑或有機雜質,再以去離子純水沖洗吹乾,準備進入植入電路製程。
圖7 晶片表面研磨機4. 退火(ANNEALING):將晶片在嚴格控制的條件下退火,以使晶片的阻質穩定。
5. 拋光(POLISHING):晶片小心翼翼地拋光,使晶片表面光滑與平坦,以利將來再加工。
6. 洗淨(CLEANING):以多步驟的高度無污染洗淨程序-包含各種高度潔淨的清洗液與超音動處理-除去晶片表面的所有污染物質,使晶片達到可進行晶片加工的狀態。
7. 檢驗(INSPECTION):晶片在無塵環境中進行嚴格的檢查,包含表面的潔淨度、平坦度以及各項規格以確保品質符合顧客的要求。
8. 包裝(PACKING):通過檢驗的晶片以特殊設計的容器包裝,使晶片維持無塵及潔淨的狀態,該容器並確保晶片固定於其中,以預防搬運過程中發生的振動使晶片受損。
矽晶棒所切割出的晶圓片中,品質較好的,稱為生產晶圓,更高級的稱為磊晶圓,生產晶圓及磊晶圓幾乎都集中在矽晶圓棒的中間部分。
頭尾兩端所切出的晶圓,出現瑕疵的機會較大,通常用做非生產用途,稱為測試晶圓,測試晶圓通常送至美日等國再加工成再生晶圓。
最後矽晶圓片送至晶圓廠內製造晶片電路,每塊矽晶圓片上可翻製出數以百計的相同矽晶片。
這些晶片電路再經封裝測試等程序,經過複雜的化學和電子製程後,其上佈滿著多層精細的電子線路,便成為市面上一顆顆的IC。
IC是把數以千計萬計的電子元件如電阻、電容等設計均收縮在一片不到指甲大小的矽晶片上,可以將傳統電子零件的體積小型化。
1-5 磊晶(Epitoxy)磊晶一詞源自於希臘文的epi(在上)和 taxis(有秩序的排列),其意乃有秩序的排列在其上。
磊晶是單晶基板上成長薄膜的延伸,經由在單晶基板上增添的原子而形成的一個單晶結構的連續體。
其原理可分為:(1) 液相磊晶(Liquid Phase Epitoxy,LPE)液相磊晶成長是從液相中直接利用沉積法,在晶質基板上成長磊晶層,這種方法對於砷化鎵(GaAs)的成長和其相關的III-V族化合物特別有用。
液相磊晶成長適合成長薄的磊晶層(≧0.2μm),因為它具有低的成長速率,所以較其他方法有用。
(2) 氣相磊晶(Vapor Phase Epitoxy,VPE)氣相晶矽層的成長稱為氣相磊晶。
在其過程中,是用基板晶圓(Substrate wafer)當作一晶種。
在各種磊晶成長方法中,氣相磊晶成長是目前成長矽元件最主要的方法。
而在氣相磊晶中又可分成物理氣相沉積(Physical Vapor Deposition,PVD)和化學氣相沉積(Chemical Vapor Deposition,CVD) 兩種技術。
前者主要是藉物理現象而後者則主要是以化學反應的方式,來進行薄膜的沉積。
而PVD的應用大都侷限在金屬薄膜的沉積上,相反的,凡是所有半導體元件所需要的薄膜,不論半導體、導體或介電材料(Dielectrics),都可藉由CVD 法來進行配製。
因為CVD是藉反應氣體間的化學反應來產生所需要的薄膜,因此CVD法所製作的薄膜材料,其結晶性(Crystallinity)和理想配比(Stoichiometry)等與材質相關的一些性質,都比PVD法好很多。