良率改善报告参考文档
良率提升改善报告ppt
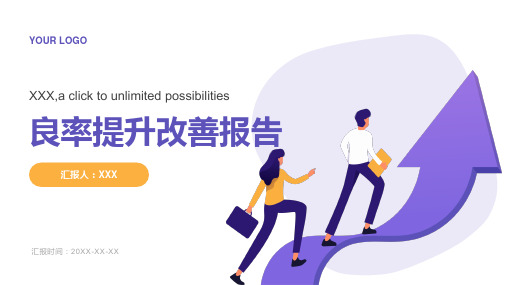
培训员工:对员工进行技 能培训,提高生产效率和 质量意识
优化流程:对生产流程进 行优化,提高生产效率和 质量稳定性
实施监控:对生产过程进 行实时监控,及时发现和 解决问题
定期评估:定期对实施效 果进行评估,及时调整计 划和策略
持续改进:根据评估结果, 持续改进生产流程和员工 技能,提高良率
关键节点与里程碑
良率提升百分比:衡量良率提升的幅度 生产效率提升:衡量生产效率的提高程度 成本降低:衡量生产成本降低的程度 质量稳定性:衡量产品质量的稳定性和一致性 客户满意度:衡量客户对产品质量的满意度 员工满意度:衡量员工对生产环境和工作条件的满意度
评估方法与流程
添加标题
确定评估目标:明 确评估的目的和预 期效果
提升良率的挑战
技术瓶颈:现有技术无法满足生 产需求
市场竞争:竞争对手的良率提升 速度更快
添加标题
添加标题
添加标题
添加标题
成本压力:提高良率需要增加投 入
人员素质:员工技能和素质需要 提升
良率提升策略
第二章节
工艺流程优化
优化生产工艺,提高生产效率 引入自动化设备,减少人工操作误差 加强质量控制,提高产品合格率 优化供应链管理,降低原材料成本
设备故障问题:设备故障导 致生产过程不稳定,影响良
率
人员操作问题:员工操作不 当或技能不足,影响产品质
量
良率提升的必要性
提高产品质量: 良率提升可以减 少不良品,提高 产品质量
降低成本:良率 提升可以减少废 品率,降低生产 成本
提高生产效率: 良率提升可以减 少返工和维修时 间,提高生产效 率
增强市场竞争力 :良率提升可以 提高产品竞争力 ,增强企业在市 场中的地位
产品良率专案改善-定版

0
0.00%
0.00%
100.00%
2021年5月XX挤压不良统计表
序号
不良类型
投入总量 (支)
不良数量 (支)
不良率 (%)
占不良比例 (%)
累积比率 (%)
总不良数 (支)
总不良率 (%)
1
模痕
39
2.40%
43.38%
43.38%
2
内壁拉伤
12
0.74%
13.35%
56.73%
3
外宽不良
10.5
期限 2021.3.20 2021.3.20
2021.3.20 2021.3.20 2021.3.20
六-1 效果确认
序 号
整改内容
整改对策
挤压表面 调整冷床的平整度、加大产品之间的间 1 不良 距;转运过程中叉车匀速行驶严禁急停
急起。
当担者 生产
计划完 成时间
5月
2月25日
进展跟踪 3月15日 4月15日
直后均在图纸技术要求范围内;挤压生
3
产时做好首件、中间尾件检验,出现异 常及时调整反馈追溯,保证生产产品满
生产 品质
5月
足技术图纸要求,不批量生产不良,不
流出不良。
弯曲不良 1、挤压校直时型材保持平行一致选择
合理校直量;2、模具优化模具型腔使
生产
4
出料口速度稳定;3、裁切成品超过公
品质
5月
差弯曲在0.2-0.3mm之间的单独摆放发
高低不良
1.长料对接部分单独存放单片全检尺寸(暂时单独放 置)定期更换锯切平台工装;2.29002产品1出5改为1 出3根5米的跟踪验证裁切后报废率 ;3.开发就现有 产品裁切高度公差带进行梳理与客户技术沟通是否有 放宽的空间。
良率提升改善报告[优质PPT]
![良率提升改善报告[优质PPT]](https://img.taocdn.com/s3/m/65686175c850ad02df80410d.png)
白色颗粒可擦拭
3区
1区
导光板与扩散之间
白色胶状可擦拭
5区
3区
反射与导光板之间
白色胶状不可擦拭
4区
层次 导光板与扩散之间 导光板与扩散之间 反射与导光板之间 导光板与扩散之间 导光板与扩散之间 导光板与扩散之间 导光板与扩散之间 导光板与扩散之间 导光板与扩散之间 导光板与扩散之间
不良状态 白色颗粒可擦拭 白色颗粒可擦拭 白色胶状可擦拭 白色胶状可擦拭 白色胶状不可擦拭 白色胶状可擦拭 白色胶状可擦拭 白色颗粒可擦拭 白色胶状不可擦拭 白色胶状不可擦拭
1
23
4 56 789
1
1
SF0006良率提升改善报告
工程部:杨兴强
2
2
目录
1 不良分析 2 分析方向 3 改善方法1 4 改善方法2 5 改善方法3 6 改善方法4 7 改善方法5 8 改善方法6 9 改善方法7 10 改善数据对比 11 结束语
3
3
p 1.不良分析
拆解20pcs不良品白点分析数据
改善后
差异点:取消导光板和铁壳在组装过程中压覆灯条的动作,避开 与导光板的1区到3区的直接接触。
11
11
p 9改善方法
减小压榨在取料过程中,压块与半成品的接触面积
改善前
改善后
差异点:减小压榨工位在取料的过程中,压块与导光板的接触面 积。
12
12
p 10改善数据
白点改善前与改善后的对比图
日期 白点数量
OK,动态测试NG.
到17s,风淋人数《2
员),可得出人员污染很大,需改进无尘服。
机
机台内部环境OK
?
?
清洁后的导光板上机后,机
提升测试良率专项改善报告
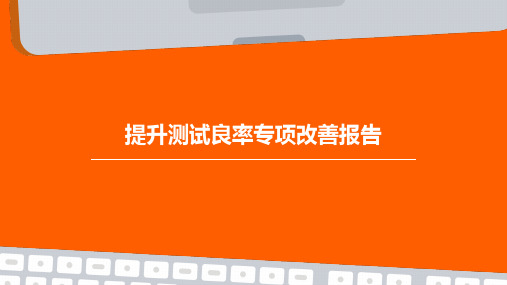
01
通过实施一系列改善措施,我们成功地将测试良率提高了20%,
显著降低了不良率和产品退货率。
生产效率得到优化
02
改进后的测试流程更加高效,缩短了生产周期,提高了整体生
产效率。
质量管理体系进一步完善
03
通过持续的质量改进,我们完善了质量管理体系,加强了过程
控制和数据分析。
对未来产品质量和生产的展望
持续优化产品质量
详细描述
通过对现有工艺流程进行全面分析,识别瓶颈和问题点,采取针对性措施进行优 化,包括简化流程、减少冗余环节、提高自动化程度等,以提高生产效率和测试 良率。
设备与工具升级
总结词
升级设备和工具是提高测试良率的有 效途径。
详细描述
根据工艺需求和测试要求,对现有设 备和工具进行评估和升级,引进先进 的测试设备和工具,提高测试精度和 可靠性,从而提升测试良率。
生产效率提高
改善过程提高了生产线自 动化水平,使得整体生产 效率提高了20%。
质量损失减少
通过减少不良品,质量损 失成本降低了30%。
客户反馈与市场表现
客户满意度提升
产品质量的提高使得客户满意度 大幅度提升,客户投诉率下降了 20%。
市场占有率扩大
由于产品质量的提升和客户满意 度的提高,产品在市场的占有率 扩大了5%。
报告范围和限制
范围
本报告主要针对测试良率低的问题,从分析原因、提出改善措施、实施改善计 划等方面展开论述。
限制
由于数据收集和调查的局限性,本报告主要基于现有数据和信息进行分析,可 能存在一定的局限性。同时,由于改善行动的实施需要一定时间,本报告的结 论和建议主要是基于当前情况和经验进行的推断。
02
良率提升方案格式模板
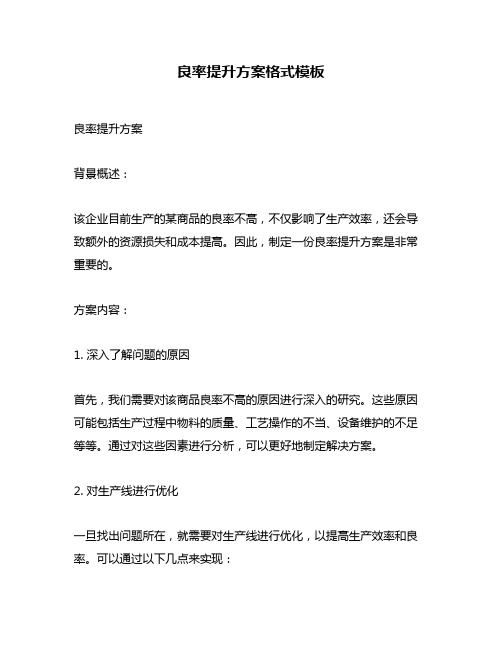
良率提升方案格式模板良率提升方案背景概述:该企业目前生产的某商品的良率不高,不仅影响了生产效率,还会导致额外的资源损失和成本提高。
因此,制定一份良率提升方案是非常重要的。
方案内容:1. 深入了解问题的原因首先,我们需要对该商品良率不高的原因进行深入的研究。
这些原因可能包括生产过程中物料的质量、工艺操作的不当、设备维护的不足等等。
通过对这些因素进行分析,可以更好地制定解决方案。
2. 对生产线进行优化一旦找出问题所在,就需要对生产线进行优化,以提高生产效率和良率。
可以通过以下几点来实现:1)对物料进行品质管理——提高采购标准,加强对供应商的管理,确保物料达到所需的品质标准。
2)对生产工艺进行优化——根据生产线的情况,针对每个工艺环节的弱点,对工艺流程进行优化。
3)安排培训课程——对操作人员进行培训,增加他们对生产线操作的质量和态度的重视程度,提高其专业技能水平。
4)设备维护——实施严格的设备维护计划,保证设备始终处于最佳状态。
3. 实施现代监控系统安装现代化的监控系统有助于提高生产效率和生产工艺的良率。
该系统可以监测每个环节的工艺流程,及时发现问题,从而防止不良品的产生。
4. 建立质量保证体系建立一个质量保证体系可以保证每一件产品符合要求,并减少不良品的出现。
该质量保证体系应包含以下几点:1)原材料和成品的检验标准2)生产过程的检验标准和程序3)产品抽样和检验的方式和程序4)管理和报告程序5. 增强培训除了操作人员的培训以外,还需要加强中层管理人员的工作培训。
他们负责督促、协调生产、管理人员以及故障的解决,因此需要加强他们的工作能力和协调能力。
此外,鼓励技术研发人员提供更好的产品设计和过程技术,以提高产品的质量。
结论:总的来说,提高某生产线的良率确实需要一系列的综合改进。
在长期的生产管理中,还需要不断积累经验,发现问题所在,进一步完善该方案以及生产流程。
这样才能更好地提高生产效率和产品质量。
FPC良率提升持续改善报告
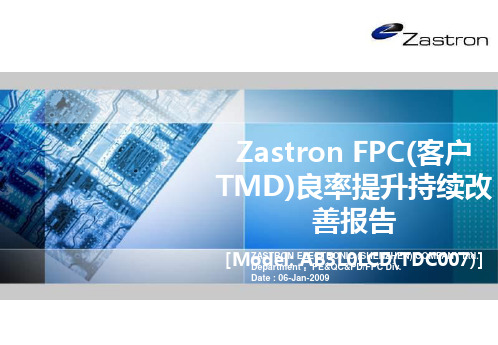
50.0%
40.0%
30.0%
20.0%
10.0%
0.0%
銅見え
不良割合 累計不良率
13.2% 13.2%
導体欠け メッキビッド 導体凹み
12.6%
9.4%
8.6%
25.9%
35.3%
43.9%
金面キズ 7.5% 51.4%
12月前五大不良推移图
不良割合
80% 70% 60% 50% 40% 30% 20% 10% 0%
不良率% 1.28%
3.06% 1.87% 0.60% 1.11% 0.51%
各不良 所占% 15.15%
36.36%
22.22% 7.07% 13.13% 6.06%
不良描述
现象:不良处表面铜被过蚀, 周边铜 面平整 大小:凹陷程度不一 位置:无面次
现象:不良处有底铜,周边铜面呈不规 则凸点状 凸点大小:1-2mil 位置:无面次
数据来源: FQC 报表
Goal (2月)
① ② ③ ④ ⑤ 统合
3.1% 2.0% 0.5% 1.0% 1.0% 10.0%
改善率 为
60%
统合步留 不良率: 7%(Q2)
8
四、良率提升改善小组改善小结(阶段性)
改善项目 1.线路不良
2.露铜不良
3.导体变色 4.CVL异物 不良 5.金面划伤 不良
100%
80%
69.14%
60% 37.33%
40%
20%
0% 9月(样品)
10月
67.06%
11月
74.47%
12月
原定(9月)计划良率2008/11达到90%; 目前实际步留(12月)为:74.47%; 09年1月将对良率提升的关键工序:黑 孔线进行改造及制订的相关对策在09年 2月份才能实施; 重新制定良率目标计划 (09年2月良率目标:90%).
良率报告格式
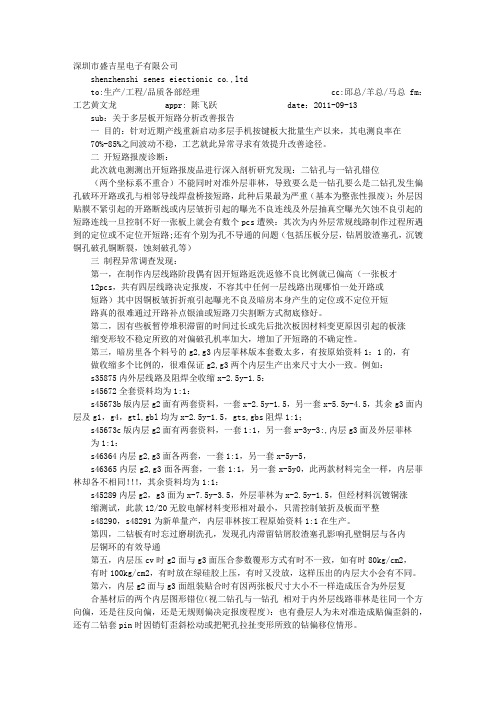
深圳市盛吉星电子有限公司shenzhenshi senes eiectionic co.,ltd to:生产/工程/品质各部经理 cc:邱总/羊总/马总 fm:工艺黄文龙 appr: 陈飞跃 date:2011-09-13 sub:关于多层板开短路分析改善报告一目的:针对近期产线重新启动多层手机按键板大批量生产以来,其电测良率在70%-85%之间波动不稳,工艺就此异常寻求有效提升改善途径。
二开短路报废诊断:此次就电测测出开短路报废品进行深入剖析研究发现:二钻孔与一钻孔错位(两个坐标系不重合)不能同时对准外层菲林,导致要么是一钻孔要么是二钻孔发生偏孔破环开路或孔与相邻导线焊盘桥接短路,此种后果最为严重(基本为整张性报废);外层因贴膜不紧引起的开路断线或内层皱折引起的曝光不良连线及外层抽真空曝光欠蚀不良引起的短路连线一旦控制不好一张板上就会有数个pcs遭殃:其次为内外层常规线路制作过程所遇到的定位或不定位开短路;还有个别为孔不导通的问题(包括压板分层,钻屑胶渣塞孔,沉镀铜孔破孔铜断裂,蚀刻破孔等)三制程异常调查发现:第一,在制作内层线路阶段偶有因开短路返洗返修不良比例就已偏高(一张板才12pcs,共有四层线路决定报废,不容其中任何一层线路出现哪怕一处开路或短路)其中因铜板皱折折痕引起曝光不良及暗房本身产生的定位或不定位开短路真的很难通过开路补点银油或短路刀尖割断方式彻底修好。
第二,因有些板暂停堆积滞留的时间过长或先后批次板因材料变更原因引起的板涨缩变形较不稳定所致的对偏破孔机率加大,增加了开短路的不确定性。
第三,暗房里各个料号的g2,g3内层菲林版本套数太多,有按原始资料1:1的,有做收缩多个比例的,很难保证g2,g3两个内层生产出来尺寸大小一致。
例如:s35875内外层线路及阻焊全收缩x-2.5y-1.5:s45672全套资料均为1:1:s45673b版内层g2面有两套资料,一套x-2.5y-1.5,另一套x-5.5y-4.5,其余g3面内层及g1,g4,gtl,gbl均为x-2.5y-1.5,gts,gbs阻焊1:1;s45673c版内层g2面有两套资料,一套1:1,另一套x-3y-3:,内层g3面及外层菲林为1:1:s46364内层g2,g3面各两套,一套1:1,另一套x-5y-5,s46365内层g2,g3面各两套,一套1:1,另一套x-5y0,此两款材料完全一样,内层菲林却各不相同!!!,其余资料均为1:1:s45289内层g2,g3面为x-7.5y-3.5,外层菲林为x-2.5y-1.5,但经材料沉镀铜涨缩测试,此款12/20无胶电解材料变形相对最小,只需控制皱折及板面平整s48290,s48291为新单量产,内层菲林按工程原始资料1:1在生产。
良率改善报告参考文档

汪达舰/ 各拉长
2
前置设备的确认 (中山、吴江区 分)
顺畅搬迁生产
考虑分批搬迁的有序性,中山预留拉线 的需求,再次进行完善区分搬迁
2012年4月12日 星期四
陈科科
机
3
面罩周转样板车 的设计与制作(2 辆)
避免减少面罩 设计新的隔层立体面罩周转车,制作样 的破损,刮花,板车试用验证.
2012年4月13日 星期五
76 99.4%
4.3 11364
52 99.5%
4.5 8198 55 99.3%
4.6 13650
84 99.4%
4.7 13050
74 99.4%
【 上周改善计划完成情况】
5M 序号
待改善项目
实施对策
责任人 协助人 完成 时间
人
1
物料员岗位轮岗,培 养一人多岗能力
1.确定人员轮岗的岗位; 2.新岗位职责的确认; 3.3月27日实施岗位调配。
1
彩标 条形码
2
批号标
1.贴标人员每20PCS一次进行贴
“彩标” 、“条形码” 、“批 1.定岗定员,禁止顶岗
号标”.
贴标;
2.贴标(装箱)人员禁止换;离 2.每20pcs一次性贴标
岗多能工顶位,禁止其他的人员 完成(中间不间断).
顶岗贴标.
3 Opple标
取面罩与玻璃等,第一工序贴 标贴放在易取放,员工
【本周改善计划】
项目
序号 (No.)
工作内容(What)
目标(Why)
工作步骤/方法(How)
完成时间(When)
责任人 (Who)
人
1
吴江多能工、物 料人员的最后确 定与换岗换位
关于产品良率改善报告
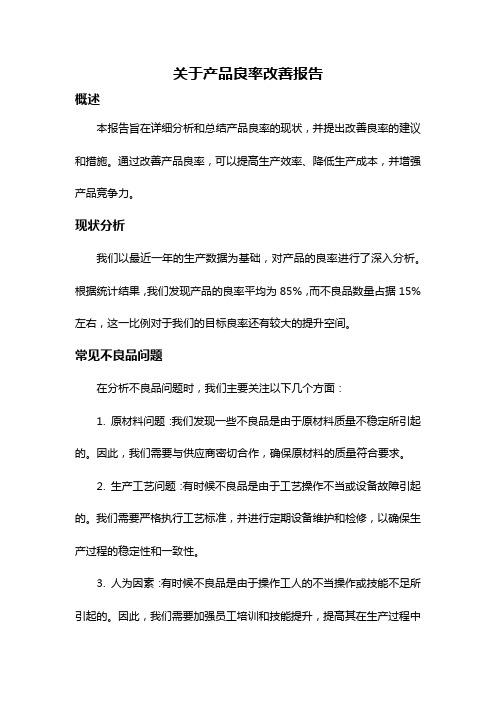
关于产品良率改善报告概述本报告旨在详细分析和总结产品良率的现状,并提出改善良率的建议和措施。
通过改善产品良率,可以提高生产效率、降低生产成本,并增强产品竞争力。
现状分析我们以最近一年的生产数据为基础,对产品的良率进行了深入分析。
根据统计结果,我们发现产品的良率平均为85%,而不良品数量占据15%左右,这一比例对于我们的目标良率还有较大的提升空间。
常见不良品问题在分析不良品问题时,我们主要关注以下几个方面:1. 原材料问题:我们发现一些不良品是由于原材料质量不稳定所引起的。
因此,我们需要与供应商密切合作,确保原材料的质量符合要求。
2. 生产工艺问题:有时候不良品是由于工艺操作不当或设备故障引起的。
我们需要严格执行工艺标准,并进行定期设备维护和检修,以确保生产过程的稳定性和一致性。
3. 人为因素:有时候不良品是由于操作工人的不当操作或技能不足所引起的。
因此,我们需要加强员工培训和技能提升,提高其在生产过程中的专业水平和工作效率。
影响因素统计为了更好地了解产品良率的影响因素,我们进行了数据统计和分析,并得出以下结论:1. 原材料质量是影响产品良率最重要的因素之一。
我们需要与供应商建立长期稳定的合作关系,并在原材料质量监控方面加强把控。
2. 生产工艺和设备状态对产品良率也有着重要影响。
我们需要定期检查设备并进行维护,同时对工艺进行优化和改进。
3. 操作工人的技能和经验对产品良率也起到至关重要的作用。
我们需要加强员工培训和技能提升,以提高其工作质量和效率。
改善措施为了提高产品的良率,我们制定了以下改善措施:1. 与供应商密切合作:我们将与供应商共同制定进一步的原材料质量标准和监控机制。
同时,我们还将定期进行质量审核,确保原材料的稳定性和可靠性。
2. 优化生产工艺和设备:我们将对生产工艺进行全面评估,并制定改进方案。
同时,我们还将定期对设备进行维护和检修,确保其正常运行和一致性。
3. 员工培训和技能提升:我们将加强员工培训计划,提高员工的技能水平和工作质量。
年度良率总结报告(3篇)
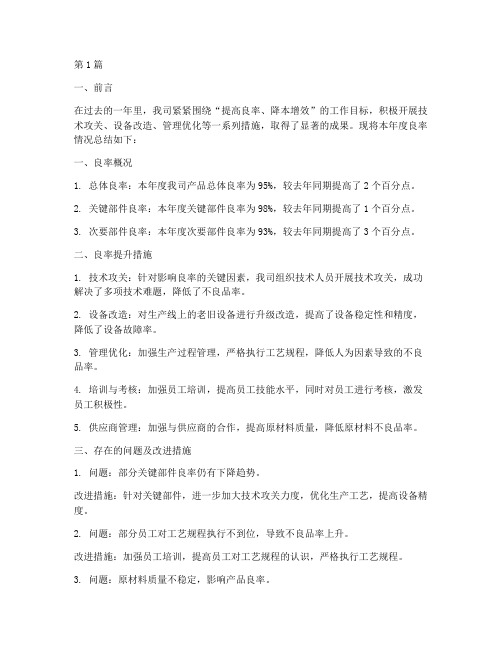
第1篇一、前言在过去的一年里,我司紧紧围绕“提高良率、降本增效”的工作目标,积极开展技术攻关、设备改造、管理优化等一系列措施,取得了显著的成果。
现将本年度良率情况总结如下:一、良率概况1. 总体良率:本年度我司产品总体良率为95%,较去年同期提高了2个百分点。
2. 关键部件良率:本年度关键部件良率为98%,较去年同期提高了1个百分点。
3. 次要部件良率:本年度次要部件良率为93%,较去年同期提高了3个百分点。
二、良率提升措施1. 技术攻关:针对影响良率的关键因素,我司组织技术人员开展技术攻关,成功解决了多项技术难题,降低了不良品率。
2. 设备改造:对生产线上的老旧设备进行升级改造,提高了设备稳定性和精度,降低了设备故障率。
3. 管理优化:加强生产过程管理,严格执行工艺规程,降低人为因素导致的不良品率。
4. 培训与考核:加强员工培训,提高员工技能水平,同时对员工进行考核,激发员工积极性。
5. 供应商管理:加强与供应商的合作,提高原材料质量,降低原材料不良品率。
三、存在的问题及改进措施1. 问题:部分关键部件良率仍有下降趋势。
改进措施:针对关键部件,进一步加大技术攻关力度,优化生产工艺,提高设备精度。
2. 问题:部分员工对工艺规程执行不到位,导致不良品率上升。
改进措施:加强员工培训,提高员工对工艺规程的认识,严格执行工艺规程。
3. 问题:原材料质量不稳定,影响产品良率。
改进措施:加强与供应商的合作,提高原材料质量,确保产品良率。
四、展望新的一年,我司将继续以提高良率为核心,不断优化生产工艺、加强设备管理、提升员工素质,努力实现以下目标:1. 产品总体良率达到97%以上。
2. 关键部件良率达到99%以上。
3. 次要部件良率达到95%以上。
4. 降低不良品率,提高客户满意度。
总之,我司将继续努力,为实现年度目标而努力拼搏,为我国制造业的发展贡献自己的力量。
第2篇一、报告概述尊敬的领导,亲爱的同事们:本报告旨在对2022年度公司良率情况进行全面总结,分析存在的问题,并提出改进措施。
良率专案报告模板
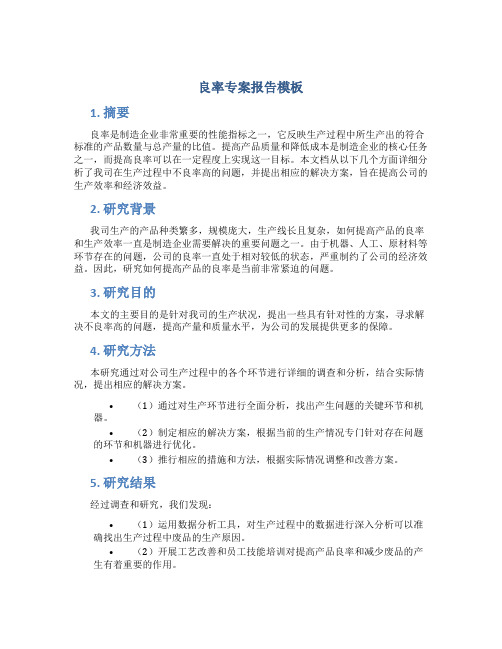
良率专案报告模板1. 摘要良率是制造企业非常重要的性能指标之一,它反映生产过程中所生产出的符合标准的产品数量与总产量的比值。
提高产品质量和降低成本是制造企业的核心任务之一,而提高良率可以在一定程度上实现这一目标。
本文档从以下几个方面详细分析了我司在生产过程中不良率高的问题,并提出相应的解决方案,旨在提高公司的生产效率和经济效益。
2. 研究背景我司生产的产品种类繁多,规模庞大,生产线长且复杂,如何提高产品的良率和生产效率一直是制造企业需要解决的重要问题之一。
由于机器、人工、原材料等环节存在的问题,公司的良率一直处于相对较低的状态,严重制约了公司的经济效益。
因此,研究如何提高产品的良率是当前非常紧迫的问题。
3. 研究目的本文的主要目的是针对我司的生产状况,提出一些具有针对性的方案,寻求解决不良率高的问题,提高产量和质量水平,为公司的发展提供更多的保障。
4. 研究方法本研究通过对公司生产过程中的各个环节进行详细的调查和分析,结合实际情况,提出相应的解决方案。
•(1)通过对生产环节进行全面分析,找出产生问题的关键环节和机器。
•(2)制定相应的解决方案,根据当前的生产情况专门针对存在问题的环节和机器进行优化。
•(3)推行相应的措施和方法,根据实际情况调整和改善方案。
5. 研究结果经过调查和研究,我们发现:•(1)运用数据分析工具,对生产过程中的数据进行深入分析可以准确找出生产过程中废品的生产原因。
•(2)开展工艺改善和员工技能培训对提高产品良率和减少废品的产生有着重要的作用。
•(3)建立起完善的品质管理体系可以使公司的管理和监督更为科学、规范。
6. 结论针对我公司的实际情况,提出了以下解决方案:•(1)对生产过程中产生问题的针对性进行分析,找出问题的关键环节和机器,进行相应的修复和维护。
•(2)在每一道工序中加强品质管理,完善品质控制体系,减少生产损失和废品。
•(3)对员工进行技能培训,提高员工自我调控和解决问题的能力。
研磨良率改善报告
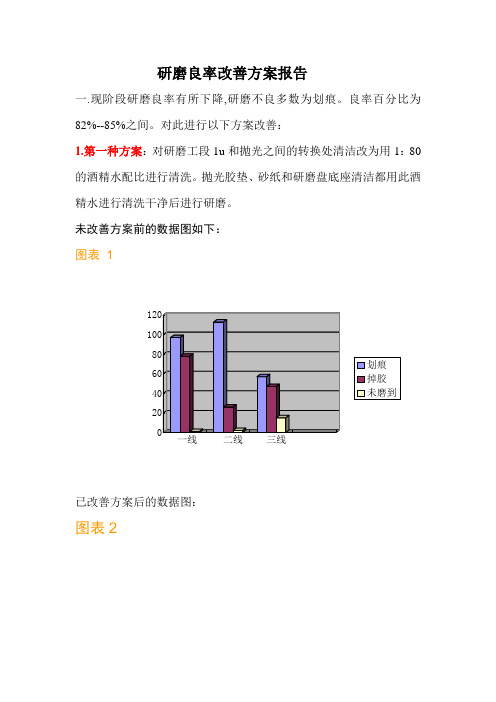
研磨良率改善方案报告
一.现阶段研磨良率有所下降,研磨不良多数为划痕。
良率百分比为82%--85%之间。
对此进行以下方案改善:
1.第一种方案:对研磨工段1u和抛光之间的转换处清洁改为用1:80的酒精水配比进行清洗。
抛光胶垫、砂纸和研磨盘底座清洁都用此酒精水进行清洗干净后进行研磨。
未改善方案前的数据图如下:
图表 1
一线 二线 三线
已改善方案后的数据图:
图表2
一线二线三线
以上改善方案结果如上述图表(表格1.2)所示:
.研磨良率分析表格如下所示:
未改善前不良分析(研磨总数为3240pcs)
改善后不良分析(研磨总数为3240pcs)
总结:
由上述表格所示,研磨良率有很大空间可以提升,采用上述方案对研磨划痕能够得到很大的改善,目前可以提升2-3个百分点。
但是总体良率较严重的在9u上,因为9u砂纸用的别人用过四角加压后拿来中心加压研磨,给研磨带来很多不良因素。
(大掉胶增多,对后面
工段造成影响,可能导致后面工段不良因素产生。
)。
测试良率改善项目报告11.20
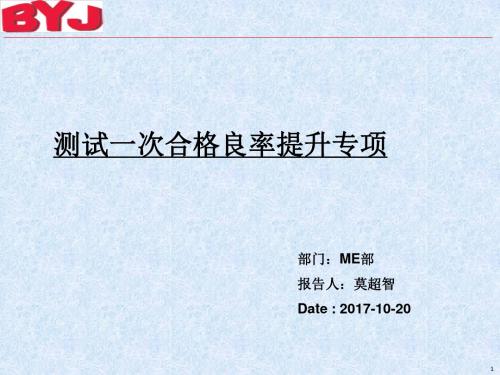
不良数量 383 395 313 790 1425 725 776 870 654 626 1303 981 620 617 629
合格数量 11410 13634 18611 25097 27581 20743 22914 22075 21864 28779 25855 26280 21684 22655 20968
不合格
问题数 合格数
短路 开短路 量
量
1
4
222
263
9
8
845
2028
13
17
409
473
10月6日 DE18215 1776
76%
399
21
10
430
1346
10月7日 DE18565 3219
73%
832
12
17
861
2358
10月8日 DE18215 4736
67%
1361
130
77
1568 3168
98%
98%
98%
97%
97%
98%
97%
97%
98%
98%
97%
本月累计一 次合格率
97%
97%
98%
97%
97%
97%
97%
97%
97%
97%
97%
97%
97%
97%
97%
98% 97% 96% 95% 94% 93%
97%
合格率
98%
98%
97%
97%
97% 97%
97%
97% 97% 97%
88%
97%
88%
电路板合格率提升持续改善改进报告范本
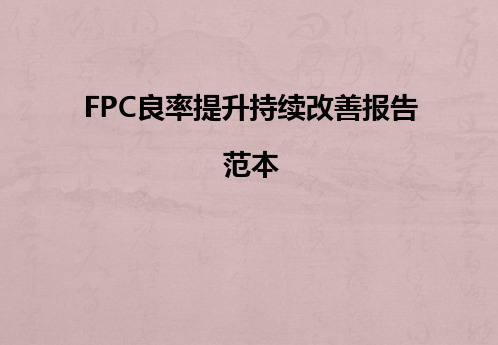
××× FPC(**)良率提升持续改善内容概要
一、××× ** FPC 生产良率状况
二、××× ** FPC 品质良率目标
三、××× ** FPC 良率提升改善小组(计划、目标)
四、良率提升改善小组改善小结(阶段性)
五、各良率提升改善小组改善结果报告:
①线路不良改善
6
三、××× ** FPC 良率提升改善小组(计划、目标)
3.2、××× ** FPC 良率提升改善小组:
Champion: Mr.陈嘉彦(OP)
Key Member: 工程部:Mr.熊华庆 生产部:Mr.蔡兆龙 品保部:Mr.张治民
改善小组
小组 1
小组 2 小组 3 小组 4 小组 5
改善内容
①线路不良 改善
②露铜不良改善
③导体变色不良改善
④CVL异物不良改善
⑤金面划伤不良改善
For Model: ××(×)型号: AB***CD(TDC007) 客户(**)型号: NEL***0221
2
一、××× ** FPC生产良率状况
1.1、2018年9月样品阶段到10-12月量产AB***CD(TDC007)生产良率状况如下:
60%
××(×)型号: AB***CD(TDC007) 客户(**)型号: NEL***0221
5
三、××× ** FPC 良率提升改善小组(计划、目标)
3.1、2018年10-12月份AB***CD(TDC007)主要五项生产不良状况:
10月份前五大不良
60%
不良割合
累計不良率
50%
40%
30%
①銅見え、②導体欠け③メッキ突起④導 体凹み⑤金面キズ
XXX良率提升改善报告

感谢团队的各成员参与分析检讨, 并跟进验证。
Thank You!
4.分析改善验证
1.印刷不良调整 2.贴片不良优化
1.SPI程式优化 2.AOI程式优化
生产组
品质组
1.员工岗位培训 2.员工执行力加强 3.数据收集
1.员工岗位培训 2.生产作业过程品质 监控
二、问题分析:
原因分析
原因分析1: 从贴片与炉后不良品外观确认,景旺PCB有变形现象,如下图所示
一次过炉后超出标准1.73MM
3
空焊
开焊/虚焊
81
漏件立碑3 Nhomakorabea抹板
漏料
6
墓碑
锡桥
2
移位
总计
141
总计
不良数量 2 14 1 15 21 4 17 76
150
总结:TOP前三项移位,漏件,虚焊不良。
一.背景介紹:
问题
不良问题描述及影响度
调查
1、CHIP料移位/墓碑:
CHIP料移位,墓碑,影响测 试不通电,不开机。
一.背景介紹:
问题
C4 百分比
HG产品6月份不良机型的 Pareto 图
400 100
300
80
60 200
40 100
20
0
0
C1 WS831-10 HG532e-10 HG658b-20 HG255e-10 HG658
其他
C4
179
72
63
24
12
10
百分比
49.7
20.0
17.5
6.7
3.3
2.8
累积 %
49.7
二、问题分析:
良率提升改善报告ppt
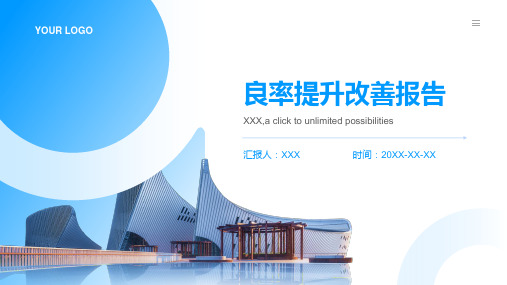
提高市场竞争力:提高产品质量, 增强市场竞争力
良率提升目标
提高产品质量
降低生产成本
提高生产效率
提升企业竞争力
PART 2
良率提升方案
方案一:工艺改进
改进工艺流程,提高生产效率 优化设备性能,减少故障率 加强员工培训,提高操作技能 引入新技术,提高产品质量方案二:设备升级设备升目的:提高生产效 率,降低不良率
方案四:质量管理体系优化
建立完善的质 量管理体系
加强员工培训, 提高质量意识
定期进行质量 检查,发现问
题及时整改
引入先进的质 量管理工具和 方法,如六西 格玛、精益生
产等
PART 3
良率提升实施计划
实施时间安排
制定计划:2023年1月1 日-2023年1月10日
实施准备:2023年1月 11 日 - 2 0 2 3 年 1 月 2 0 日
THANK YOU
汇报人:XXX
汇报时间:20XX/01/01
导
市场风险:可 能面临市场竞 争压力,需要 提前进行市场
调研和预测
实施效果评估方法
设定评估指 标:如良率、 生产效率、
成本等
收集数据: 通过生产记 录、质量检 测报告等收
集数据
分析数据: 使用统计分 析方法,如 方差分析、 回归分析等
制定评估标 准:根据评 估指标设定 评估标准, 如良率提升 多少为有效
设备升级内容:更换老旧设 备,引进先进技术
设备升级效果:提高生产效 率,降低不良率
设备升级时间:根据实际情 况制定升级计划
设备升级预算:根据设备升 级内容制定预算
设备升级注意事项:确保设 备升级不影响生产进度,确 保设备升级后的稳定性和可 靠性。
良率提升改善报告ppt

03 效果评估
对品质检测和控制强化方案进行定期评估, 确保改善方案的有效性和可持续性
建立完善的品质检测和控制体系,提高检测 设备的精度和可靠性
02 实施措施
人员培训与技能提升
培训计划
制定针对不同岗位的培训计划, 提高员工的专业技能和操作水 平。
技能评估
定期对员工进行技能评估,找 出技能短板,制定针对性的提 升计划。
关键问题点分析
设备故障
设备故障是影响良率的关键因素 之一,需要定期维护和检查。
原材料质量
原材料质量不稳定也会导致良率 下降,需要严格控制原材料的质 量。
生产工艺问题
生产工艺问题也是影响良率的关 键因素之一,需要不断优化和改 进生产工艺。
改善需求与目标设定
根据良率现状分析,明确改善的需求和重 点,确定需要优化或改进的环节。
激励机制
建立员工技能提升与绩效挂钩 的激励机制,鼓励员工自主学 习和提升。
03
改善成果评估与总结
改善前后数据对比分析
01 良率提升情况
对比改善前后的数据,可以看出产品合格率有了显著提 高。
02 不合格产品原因分析
经过改善,主要的不合格产品原因得到了有效控制,如 制程稳定性和物料不良等。
03 未来改进方向
良率提升改善报 告PPT
汇报人:XXX
目录
01. 良 率 现 状 分 析 02. 改 善 方 案 与 实 施 03. 改 善 成 果 评 估 与 总 结
01
良率现状分析
良率水平及分布情况
良率水平
当前产品良率水平为XX%,相较 于之前有一定提升,但仍需进一
步优化。
不良品分布情况
不良品主要集中在XX环节,占比 达到XX%。
良率提升改善报告
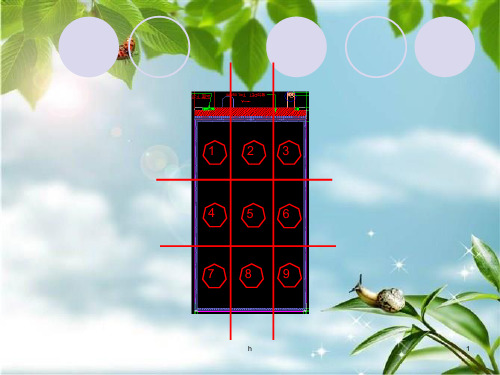
行验证)
法
导光板保护膜清洁后,上机 后还是过脏。(其它严格按 照SOP执行)
每半个小时清洁导光板工位清洁粘滚及导光板拖块 (用粘滚清洁)。
环
车间静态测试OK,机台内部 测试OK
ok
指标达成
h
5
3改善方法
膜材清洁机粘滚高度调整
改善前
改善后
差异点:在粘滚的四个角增加0.5cm厚度,避免粘滚在清洁导 光板压的太紧造成白点。
1 23 4 56 789
h
1
SF0006良率提升改善报告
工程部:杨兴强
h
2
2
目录
1 不良分析
2 分析方向
3 改善方法1
4 改善方法2
5 改善方法3
6 改善方法4
7 改善方法5
8 改善方法6
9 改善方法7
10 改善数据对比
11 结束语
h
3
1.不良分析
拆解20pcs不良品白点分析数据
区域
层次
不良状态
3区
1区
导光板与扩散之间
白色胶状可擦拭5区3区反射与导光板之间白色胶状不可擦拭
4区
层次 导光板与扩散之间 导光板与扩散之间 反射与导光板之间 导光板与扩散之间 导光板与扩散之间 导光板与扩散之间 导光板与扩散之间 导光板与扩散之间 导光板与扩散之间 导光板与扩散之间
不良状态 白色颗粒可擦拭 白色颗粒可擦拭 白色胶状可擦拭 白色胶状可擦拭 白色胶状不可擦拭 白色胶状可擦拭 白色胶状可擦拭 白色颗粒可擦拭 白色胶状不可擦拭 白色胶状不可擦拭
9月24日 221
10月6日 26
改善前 9月25日 145
改善后 10月7日 71
提升测试良率专项改善报告2014
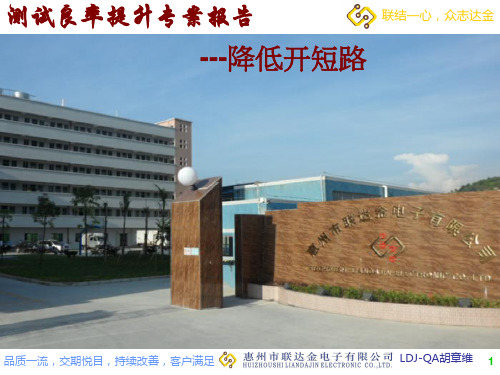
品质一流,交期悦目,持续改善,客户满足
专案小组
专案名称
改善期限 领航员/江海珍 组长/李巧生 小 组 组 员 测试:罗仲深 钻孔:李刚 组员 电镀:王营渠 Q C:王富华
联结一心,众志达金
降低开短路专案
2014/10/01—2015/03/30 主导员/胡章维、黄贵泉 技术指导/蒋丁荣 工程:武建文 线路:王坤伦 阻焊:何晓清 FQC:林桂玉
测试良率提升专案报告
联结一心,众志达金
---降低开短路
品质一流,交期悦目,持续改善,客户满足
LDJ-QA胡章维
1
专案改善报告目录
联结一心,众志达金
1. 2. 3. 4. 5.
专案小组简介 专案改善计划 现状分析 目标设定 要因分析
6. 改善对策 7. 对策实施 8. 跟踪比较 9. 效果确认 10.标准化 11.结论
2070.038% 0.028% 128
6-7月 589467 102 0.017%
不良数
8-9月 465432 128 0.028%
不良率
合计 2577897 545 0.021%
0.040% 0.035% 0.030% 0.025% 0.020% 0.015% 0.010% 0.005% 0.000%
王坤 伦
11月 10日
品质一流,交期悦目,持续改善,客户满足 一流品质,准确交期,持续改善,满足客户
LDJ-QA胡章维 15
主要改善对比图片
联结一心,众志达金
刀片使用记录
旧刀片回收
品质一流,交期悦目,持续改善,客户满足
LDJ-QA胡章维 16
主要改善对比图片
联结一心,众志达金
- 1、下载文档前请自行甄别文档内容的完整性,平台不提供额外的编辑、内容补充、找答案等附加服务。
- 2、"仅部分预览"的文档,不可在线预览部分如存在完整性等问题,可反馈申请退款(可完整预览的文档不适用该条件!)。
- 3、如文档侵犯您的权益,请联系客服反馈,我们会尽快为您处理(人工客服工作时间:9:00-18:30)。
/
汪达舰 /刘勇 黎辉刚
4月13日
【专项改善行动2--- 电子件不良】
11周:三段开关不良27pcs(占比26%) 12周:三段开关不良28pcs(占比29%) 13-14周:三段开关不良10pcs(占比8%)
日期
2月
3月
4月 4-2 4-3 4-5 4-6 4-7
6周 7周 8周 9周 10周 11周 12周 13周 14周
吸顶灯良率改善报告(第十七期)
部门:吸顶灯科
报告人:汪达舰
日期:Apr-9,2012
Contents
1
吸顶灯良率趋势图
2
上周改善计划完成情况
3
专项改善行动
4
制程稽核问题点
5
外部门协助事项
6
本周改善计划
【 良率趋势图---大灯】
日期 2011年11月 2011年12月 1月
2月
3月 14周 4-2
降21%
【专项改善行动3--- 自动封口机1】
机型
1 号机 2 号机 3 号机 4 号机 5 号机
拉别
17、18线 7、8线
11、12线 2、13线 方灯3、4线
投入时间(H)=拉别人数 实际产出时间=投入
*当日出勤时间
时间-异常时间
异常时间
机器利用率
1400
672
728
48.00%
1365
1307.8
环
5
《漏混装作业规范》 局;
制定、培训
2.制定教材,组织员工培训;并稽查是否
汪达舰/ 赵英军/ 培训在持续进 曹志新 刘林强 行中
按规范进行操作.
【 专项改善行动1---面罩不良 】
960方骏: 11周:破损12 pcs(26%) ;刮花8pcs(17%). 12周:破损9 pcs(18%);刮花4pcs(8%). 13-14周:破损3pcs
【 良率趋势图---小灯】
日期 生产数 不良数
良率
11月
12月
1月
2月
72540 404095 221475 287357
699
4729
1781
1102
99.04% 98.83% 99.20% 99.64%
3月 310243 1738 99.43%
4.1 10500
52 99.5%
4.2 12500
日期
12月 1月 2月 9周 10周 11周 12周 13周 14周 4-2 4-3 4-5 4-6 4-7
产量
36350 15520 60827 14945 20772 18514 16035 12272 12190 1590 3025 1820 3100 2655
不良数 127 49 90 16 12 30 37 18 18
周别
改善点
步骤/内容
责任人 完成情况
大灯电子件配送方 式与数量的改善
本周起大灯电子件的配送按所需电子件的型 号,各型号每1次只允许配送1箱.(避免现场 的堆叠、损坏)
上周完成
三段开关不良的改 跟进电子件车间的不良分析、改善方案,并 善实施与跟进 及时的反馈。
熊贤辉
彭武/ 汪达舰
现按标准实施 操作
三段开关不良 占比较上周下
周别
改善点
步骤/内容
责任人
完成情况
上周完成
面罩+边框前置加工& 1.对前置的面罩+边框进行前置加工; 配送(全线推广) 2.按每箱进行配送上线.
熊贤辉/ 8条线全部推广(12陈科科 13线暂未实施)
本周计划
面罩周转样板车的设 计与制作(2辆)
避免减少面罩的破损,刮花,设计新的面罩周 转车,制作样板车试用验证.
76 99.4%
4.3 11364
52 99.5%
4.5 8198 55 99.3%
4.6 13650
84 99.4%
4.7 13050
74 99.4%
【 上周改善计划完成情况】
5M 序号
待改善项目
实施对策
责任人 协助人 完成 时间
人
1
物料员岗位轮岗,培 养一人多岗能力
1.确定人员轮岗的岗位; 2.新岗位职责的确认; 3.3月27日实施岗位调配。
产量 11928 13133 19590 14945 20772 18514 16035 12272 12190 1590 3025 1820 3100 2655
不良数 46 56 67 35 55 103 96 58 75 18 13 16 18 10
日不良率 0.39% 0.43% 0.34% 0.23% 0.26% 0.56% 0.60% 0.47% 0.62% 1.13% 0.43% 0.88% 0.58% 0.38%
0
4
3
6
5
破损
不良率 0.35% 0.32% 0.15% 0.11% 0.06% 0.16% 0.23% 0.15% 0.15% 0.00% 0.13% 0.16% 0.19% 0.19%
不良数 刮花
不良率
3
13 17 13
1
5
0
1
0
1
3
0.02% 0.06% 0.09% 0.08% 0.01% 0.04% 0.00% 0.03% 0.00% 0.03% 0.11%
*待机:与产品工程沟通更改无印字收缩膜袋,(实施 中)
4-3
4-5
4-6
4-7
产量
11861
53607 23941 55830 82538 12190 1590 3025 1820 3100 2655
不良数
593
1316
208
682
857ห้องสมุดไป่ตู้
96
13
26
6
23
28
良率 95.00% 97.55% 99.13% 98.78% 98.96% 99.21% 99.18% 99.14% 99.67% 99.26% 98.95%
汪达舰/ 赵英军/ 完成两批次的
曹志新 刘林强
培训
法
4
包材配套配送检讨标 准及制定下一步改善 计划
1.部分多能工及配送人员及全部拉长列出 包材配套配送的问题点; 2.确定改善方案; 3.按照改善方案进行改善配送。
已按照新的配 曹志新 刘林强 送标准进行
配送
1.针对目前的问题点,结合产线的排位布
培训教材完成,
57.2
95.81%
682.5
630.5
52
92.38%
1417.5
1336.5
81
94.29%
1320
待机生产 外贸订单 共计11H
1020
300
77.27%
【主要原因】 一、5#待机246H(生产外贸订单)电机坏
二、3#链条断裂、
三、4#整灯输送带电机坏
四、1#机待机中试日本订单10H
【应对措施】
曹志新
赵英军/ 对物料员4人 刘林强 进行轮岗操作
跟进ME人员对四台收 1.标示维护机台及常常出现故障问题点;
已对四台设备
机 2 缩膜机的全面维护与 2. 跟进Me在本周完成设备的全面维护与保 曹志新 黎辉刚 进行了维护保
保养
养
养
3 拉线平衡的培训
1.制定培训教材; 2.本周三完成对拉长的培训; 3.拉长针对产线情况制定改善计划。