良率提升改善报告[优质PPT]
良率提升改善报告ppt

改善方向与重点
根据当前问题和瓶颈,确定 后续改善的重点和方向,并
制定相应的实施计划。
谢谢
汇报人:XXX
03
改善成果评估
改善成果数据展示
良率提升幅度
改善后产品良率提升了XX%,达到
了XX%。 01
质量合格率提升
改善后产品质量合格率提升了XX%,
减少了产品不良率。
03
生产效率提升
通过改善,生产线的生产效率提高了
XX%,降低了生产成本。 02
改善成果与预期目标的对比分析
改善成果评估
改善实施后,产品良率明显提升,达到预期目标。
影响良率的因素
设备老化
设备老化可能导致产品加工精度 下降,从而影响良率。
员工操作不当
员工操作不熟练或失误可质量不佳
原物料质量不符合标准可能导致 产品不良,从而影响良率。
良率问题的潜在风险
设备老化
设备老化可能导致生产过程中出现故障, 从而影响良率。
员工操作不规范
员工操作不规范可能导致生产出的产品不 符合标准,从而影响良率。
02
改善方案实施
制定改善方案
改善方案实施
针对良率低的问题,制定具体的改善方案,包括工艺改进、设备更新、员工培训等方面,确 保改善措施落地。
方案实施步 骤
01
方案准备
确认改善方案的目标和计 划,准备好所需的资源、 人员和物资。
02
方案实施
按照计划逐步实施改善方 案,确保每个步骤都得到 有效执行。
03
方案跟踪与调整
对改善方案的实施过程进 行跟踪,及时发现和解决 出现的问题,并根据实际 情况调整方案。
方案实施过程中的关键节点与责任人
如何提高良率ppt课件

二、提高良率方法
良率一定是靠人做出来的,特别是我们公司这种自动化不高
人
的设备,所以对人的要求特别高,一定要有责任心,上班时 间不能做与工作无关的事情,要全身心的投入到工作中去
每天交接班的时候要对机床进行点检,各重要部位都是正常
机
的,机床不能带病生产,这是最基本的原则 ,否则容易出品
质问题
料
对来料的质量要进行监控,发现问题及时反馈,同时加料要 进行三看:即看标识,状态和有无方向反的料
关注
每天良率低的员工我们一定要去关注他为什么做得 低了?原因是什么?怎么帮助他提高良率?教给他
方法,是人机料法环哪个环节出了问题?
关爱
对于新员工和良率一直很低的员工,我们要多帮助 他们解决困难,这是我们的职责,帮他们其实也是
在帮助自己
5
四、适当的激励和鼓励
员工什么时候 干劲最大?
赞扬鼓励的时候 意见被尊重的时候 有竞争对手的时候
激励的时候 张扬个性的时候
6
跟大家分享几句话
跌倒了要学会自己跑起来,受伤了要学会自己疗伤 生命只有干出来的精彩,没有等待出来的辉煌 有目标的人在奔跑
目录
一、良率目标管理 二、提高良率方法 三、过程管控 四、适当的激励
2
一、良率目标管理
公司级目标
生产线目标
只有每台机的目标完成了,以上所有 的目标才能完成,这就说明如果我们 要完成良率目标,必须要盯紧现场每 台机每个班次的目标,这就是目标管
理和目标分解
工序目标
班组目标
个人目标 每台机目标
法
看机的方法很重要,要按照作业标准的要求去做,勤测量尺 寸 ,勤检查外观,勤观察机床运行状态,怎么拿料,放料,
加料,转料等都要严格标准
良率提升改善报告ppt
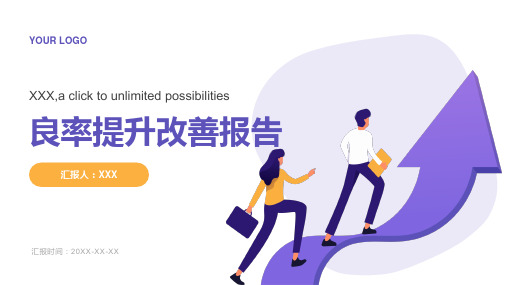
培训员工:对员工进行技 能培训,提高生产效率和 质量意识
优化流程:对生产流程进 行优化,提高生产效率和 质量稳定性
实施监控:对生产过程进 行实时监控,及时发现和 解决问题
定期评估:定期对实施效 果进行评估,及时调整计 划和策略
持续改进:根据评估结果, 持续改进生产流程和员工 技能,提高良率
关键节点与里程碑
良率提升百分比:衡量良率提升的幅度 生产效率提升:衡量生产效率的提高程度 成本降低:衡量生产成本降低的程度 质量稳定性:衡量产品质量的稳定性和一致性 客户满意度:衡量客户对产品质量的满意度 员工满意度:衡量员工对生产环境和工作条件的满意度
评估方法与流程
添加标题
确定评估目标:明 确评估的目的和预 期效果
提升良率的挑战
技术瓶颈:现有技术无法满足生 产需求
市场竞争:竞争对手的良率提升 速度更快
添加标题
添加标题
添加标题
添加标题
成本压力:提高良率需要增加投 入
人员素质:员工技能和素质需要 提升
良率提升策略
第二章节
工艺流程优化
优化生产工艺,提高生产效率 引入自动化设备,减少人工操作误差 加强质量控制,提高产品合格率 优化供应链管理,降低原材料成本
设备故障问题:设备故障导 致生产过程不稳定,影响良
率
人员操作问题:员工操作不 当或技能不足,影响产品质
量
良率提升的必要性
提高产品质量: 良率提升可以减 少不良品,提高 产品质量
降低成本:良率 提升可以减少废 品率,降低生产 成本
提高生产效率: 良率提升可以减 少返工和维修时 间,提高生产效 率
增强市场竞争力 :良率提升可以 提高产品竞争力 ,增强企业在市 场中的地位
良率提升改善报告ppt

当前良率:具体 数 值 , 如95%
良率影响因素: 生产工艺、原材 料质量、设备状 况等
良率提升目标: 提高良率,降低 生产成本,提高 产品质量
良率提升的必要性
降低生产成本:减少不良品 产生的浪费,降低生产成本
提高产品质量:降低不良品 率,提高产品合格率
提高生产效率:减少不良品 返工,提高生产效率
方案二:设备升级
升级目标:提高生产效率,降低不良率 设备选择:根据生产需求选择合适的设备 升级计划:制定详细的升级计划,包括时间、费用等 培训员工:对员工进行新设备的操作培训,确保生产顺利进行
方案三:人员培训
培训目标:提高员工技能和素质,提升良率 培训内容:生产流程、质量控制、设备操作等 培训方式:内部培训、外部培训、在线培训等 培训效果评估:定期考核、反馈、改进等
优化生产流程:减少浪费,提高效率
总结提升经验:分享成功案例,推广 至其他部门
实施效果评估
良率提升幅度:具体数值 实施周期:具体时间 成本节约:具体金额 生产效率提升:具体百分比
实施中遇到的问题及解决方案
添加标题
问题:生产过程中 出现质量问题
添加标题
解决方案:加强 质量管理,提高员 工技能水平
添加标题
问题:设备故障导 致生产效率下降
添加标题
解决方案:定期 维护设备,及时更 换故障部件
添加标题
问题:原材料供应 不足
添加标题
解决方案:加强 供应链管理,确保 原材料供应稳定
添加标题
问题:员工士气低 落
添加标题
解决方案:加强 员工培训,提高员 工满意度,增强团 队凝聚力
良率提升成果
提升后的良率数据
良率提升时间:从原来的3 个月缩短至1个月
提升测试良率专项改善报告
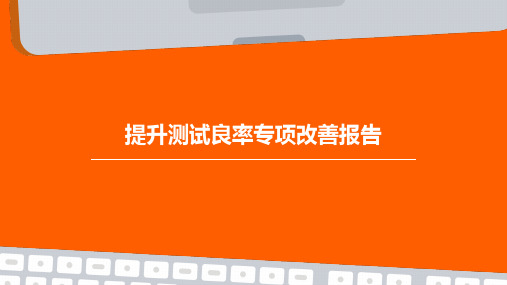
01
通过实施一系列改善措施,我们成功地将测试良率提高了20%,
显著降低了不良率和产品退货率。
生产效率得到优化
02
改进后的测试流程更加高效,缩短了生产周期,提高了整体生
产效率。
质量管理体系进一步完善
03
通过持续的质量改进,我们完善了质量管理体系,加强了过程
控制和数据分析。
对未来产品质量和生产的展望
持续优化产品质量
详细描述
通过对现有工艺流程进行全面分析,识别瓶颈和问题点,采取针对性措施进行优 化,包括简化流程、减少冗余环节、提高自动化程度等,以提高生产效率和测试 良率。
设备与工具升级
总结词
升级设备和工具是提高测试良率的有 效途径。
详细描述
根据工艺需求和测试要求,对现有设 备和工具进行评估和升级,引进先进 的测试设备和工具,提高测试精度和 可靠性,从而提升测试良率。
生产效率提高
改善过程提高了生产线自 动化水平,使得整体生产 效率提高了20%。
质量损失减少
通过减少不良品,质量损 失成本降低了30%。
客户反馈与市场表现
客户满意度提升
产品质量的提高使得客户满意度 大幅度提升,客户投诉率下降了 20%。
市场占有率扩大
由于产品质量的提升和客户满意 度的提高,产品在市场的占有率 扩大了5%。
报告范围和限制
范围
本报告主要针对测试良率低的问题,从分析原因、提出改善措施、实施改善计 划等方面展开论述。
限制
由于数据收集和调查的局限性,本报告主要基于现有数据和信息进行分析,可 能存在一定的局限性。同时,由于改善行动的实施需要一定时间,本报告的结 论和建议主要是基于当前情况和经验进行的推断。
02
良率提升改善报告PPT幻灯片
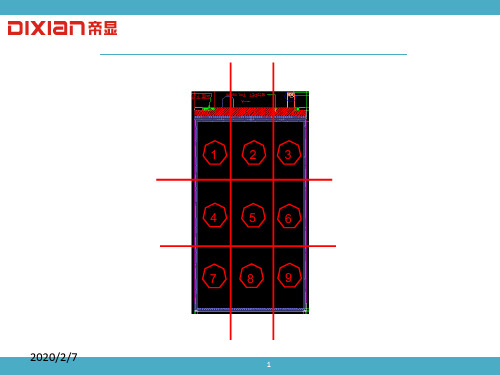
改善后
差异点:所以吸嘴避开导光板的1区到3区直接接触。
2020/2/7
9
9
7改善方法
取消灯条贴附时的缓冲距离
改善前
改善后
差异点:在灯条缓冲位置处增加0.5cm的厚度,同时压覆灯条气 缸下限距离上升0.5cm,避免在贴附灯条是导光板发生形变。
2020/2/7
10
Hale Waihona Puke 10 8改善方法取消导光板与铁壳组装过程中压附步骤
每半个小时清洁导光板工位清洁粘滚及导光板拖块 (用粘滚清洁)。
环
车间静态测试OK,机台内部 测试OK
ok
指标达成
2020/2/7
5
5
3改善方法
膜材清洁机粘滚高度调整
改善前
改善后
差异点:在粘滚的四个角增加0.5cm厚度,避免粘滚在清洁导 光板压的太紧造成白点。
2020/2/7
6
6
4改善方法
2020/2/7
1
23
4
56
789
1
1
SF0006良率提升改善报告
工程部:杨兴强
2020/2/7
2
2
2020/2/7
目录
1 不良分析 2 分析方向 3 改善方法1 4 改善方法2 5 改善方法3 6 改善方法4 7 改善方法5 8 改善方法6 9 改善方法7 10 改善数据对比 11 结束语
3
3
导光板拖块接触面改善
改善前
改善后
差异点:在拖块表面贴附一层铁氟龙,然后在上中下各自贴附 一条泡沫棉,缩小导光板与拖块的接触面积。
2020/2/7
7
7
5改善方法
导光板拖块位置改善
良率改善报告演示幻灯片
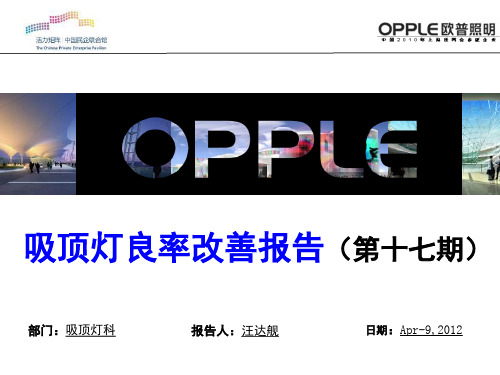
1.部分多能工及配送人员及全部拉长列出 包材配套配送的问题点; 2.确定改善方案; 3.按照改善方案进行改善配送。
已按照新的配 曹志新 刘林强 送标准进行
配送
1.针对目前的问题点,结合产线的排位布
培训教材完成,
环
5
《漏混装作业规范》 局;
制定、培训
2.制定教材,组织员工培训;并稽查是否
汪达舰/ 赵英军/ 培训在持续进 曹志新 刘林强 行中
熊贤辉/ 8条线全部推广(12陈科科 13线暂未实施)
本周计划
面罩周转样板车的设 计与制作(2辆)
避免减少面罩的破损,刮花,设计新的面罩周 转车,制作样板车试用验证.
/
汪达舰 /刘勇 黎辉刚
4月13日
【专项改善行动2--- 电子件不良】
11周:三段开关不良27pcs(占比26%) 12周:三段开关不良28pcs(占比29%)
699
4729
1781
99.04% 98.83% 99.20%
2月 287357 1102 99.64%
3月 310243 1738 99.43%
4.1 10500
52 99.5%
4.2 12500
76 99.4%
4.3 11364
52 99.5%
4.5 8198 55 99.3%
4.6 13650
不良数 刮花
不良率
3
13 17 13
1
5
0
1
0
1
3
0.02% 0.06% 0.09% 0.08% 0.01% 0.04% 0.00% 0.03% 0.00% 0.03% 0.11%
周别
改善点
步骤/内容
责任人
关于产品良率改善报告
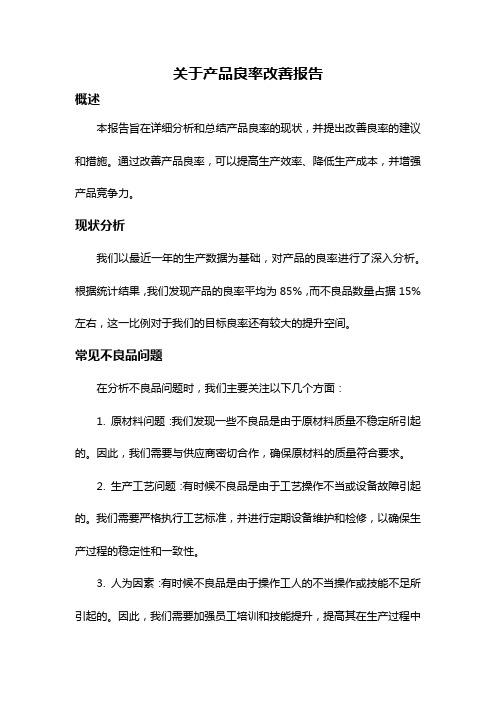
关于产品良率改善报告概述本报告旨在详细分析和总结产品良率的现状,并提出改善良率的建议和措施。
通过改善产品良率,可以提高生产效率、降低生产成本,并增强产品竞争力。
现状分析我们以最近一年的生产数据为基础,对产品的良率进行了深入分析。
根据统计结果,我们发现产品的良率平均为85%,而不良品数量占据15%左右,这一比例对于我们的目标良率还有较大的提升空间。
常见不良品问题在分析不良品问题时,我们主要关注以下几个方面:1. 原材料问题:我们发现一些不良品是由于原材料质量不稳定所引起的。
因此,我们需要与供应商密切合作,确保原材料的质量符合要求。
2. 生产工艺问题:有时候不良品是由于工艺操作不当或设备故障引起的。
我们需要严格执行工艺标准,并进行定期设备维护和检修,以确保生产过程的稳定性和一致性。
3. 人为因素:有时候不良品是由于操作工人的不当操作或技能不足所引起的。
因此,我们需要加强员工培训和技能提升,提高其在生产过程中的专业水平和工作效率。
影响因素统计为了更好地了解产品良率的影响因素,我们进行了数据统计和分析,并得出以下结论:1. 原材料质量是影响产品良率最重要的因素之一。
我们需要与供应商建立长期稳定的合作关系,并在原材料质量监控方面加强把控。
2. 生产工艺和设备状态对产品良率也有着重要影响。
我们需要定期检查设备并进行维护,同时对工艺进行优化和改进。
3. 操作工人的技能和经验对产品良率也起到至关重要的作用。
我们需要加强员工培训和技能提升,以提高其工作质量和效率。
改善措施为了提高产品的良率,我们制定了以下改善措施:1. 与供应商密切合作:我们将与供应商共同制定进一步的原材料质量标准和监控机制。
同时,我们还将定期进行质量审核,确保原材料的稳定性和可靠性。
2. 优化生产工艺和设备:我们将对生产工艺进行全面评估,并制定改进方案。
同时,我们还将定期对设备进行维护和检修,确保其正常运行和一致性。
3. 员工培训和技能提升:我们将加强员工培训计划,提高员工的技能水平和工作质量。
某企业改善报告PPT课件
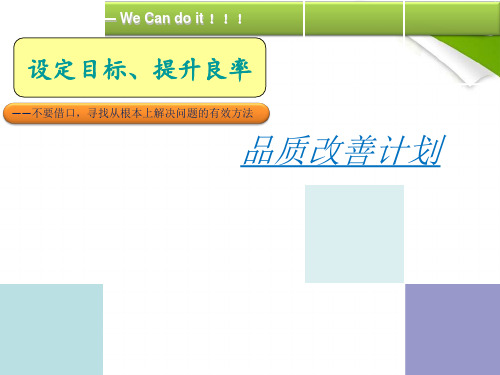
Zero De六fec、t —内—部W异e常Ca清n 单do it !!!
内部制程异常问题分类
1.12月份第1-2周制程异常单6件,未回复0件,回复率100%
Zero Defect五—、—改We善C活an动d验o it证!!!
目标
A
P
四阶段
C
D
目标
A
P
三阶段
C
D
目标
标准化
改善
A
学习
C
计划
P 标准
4
2905 2652 91.29% 253 170 12 49
5
16782 15372 91.60% 1410 1054 279
56
6
6256 5391 86.17% 865 457 329
0
合计
34921 30906 88.50% 4015 2465 865 438
Ze一ro、D1e2fe月ct份—第— 2W周e CCNaCn良do率it数!据!!
4
37711 33055 87.65% 4656 3570 638
0
5
37123 31616 85.17% 086 45776 86.23% 7310 5793 957
64
合计
231493 199206 86.05% 32237 25100 4127
752
Z一er、o D1e2f月ec份t —第—2周We精C磨an良do率it数!据!!
Z一er、o D1e2f月ec份t —第—1周We精C磨an良do率it数!据!!
检验数 合格数
良率 不良数
划伤 崩边 沙崩
1
32468 27617 85.06% 4851 3593 578 432
维修良率提升报告PPT课件

作业产出:专案项目
作业成效:Cost down金额;人力成本 金额;效率提升幅度
8
提案实施
提案改善流程
提案提出
提案评审
提案奖励
改善循环
9
专案推动实施
1.专案推动 目标拟定
3.成效激励 作业
目标
2.专案推动 实施
10
专案推动目标拟定
由各部门专案推动委员根据部门状况拟定各作业项目之成本节省金额、人 力精实指标,并制定专案推动计划,经副主委、主委核定后实施执行:
定期检讨
成果标准化
行政系统、流程管理 部、生产中心管理部 提供技术指导及协助 支持,并监督各事业 部、各中心、各系统、
各部门贯彻执行;
技术指导与支持
5
人力精实 –完善组织编制
作业内容
作业方法
作业产出
检讨组织编制
以业绩达成为导向,在充分满足组 织职能实现的基础上,定编(工作 量、饱和度)、定岗(适合度、匹 配度)、定人(能力素质),精简 组织,避免组织臃肿,人员冗繁, 人浮其事;
奖项 名额 奖金
第一名 1
20,000
第二名 1
15,000
第三名 1
10,000
对各阶段未达成专案目标的部门实施奖金惩罚,惩罚金额为部门绩效 奖金总额的5%;
15
专案推动实施作业流程
推动委员会 推动委员
归口 验收
成效标准化、 制度化、流
程化
缺失 检讨
结果 公布
持续作业
副主委
奖惩 提报
主委
成效 核定
目前维修状况
维修人力
维修良率
培训内容
3
目前维修状况
维修人力
提升测试良率专项改善报告2014
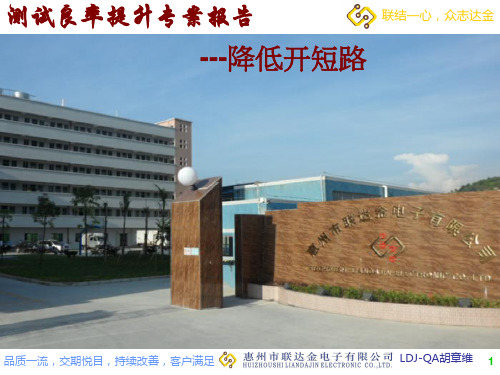
品质一流,交期悦目,持续改善,客户满足
专案小组
专案名称
改善期限 领航员/江海珍 组长/李巧生 小 组 组 员 测试:罗仲深 钻孔:李刚 组员 电镀:王营渠 Q C:王富华
联结一心,众志达金
降低开短路专案
2014/10/01—2015/03/30 主导员/胡章维、黄贵泉 技术指导/蒋丁荣 工程:武建文 线路:王坤伦 阻焊:何晓清 FQC:林桂玉
测试良率提升专案报告
联结一心,众志达金
---降低开短路
品质一流,交期悦目,持续改善,客户满足
LDJ-QA胡章维
1
专案改善报告目录
联结一心,众志达金
1. 2. 3. 4. 5.
专案小组简介 专案改善计划 现状分析 目标设定 要因分析
6. 改善对策 7. 对策实施 8. 跟踪比较 9. 效果确认 10.标准化 11.结论
2070.038% 0.028% 128
6-7月 589467 102 0.017%
不良数
8-9月 465432 128 0.028%
不良率
合计 2577897 545 0.021%
0.040% 0.035% 0.030% 0.025% 0.020% 0.015% 0.010% 0.005% 0.000%
王坤 伦
11月 10日
品质一流,交期悦目,持续改善,客户满足 一流品质,准确交期,持续改善,满足客户
LDJ-QA胡章维 15
主要改善对比图片
联结一心,众志达金
刀片使用记录
旧刀片回收
品质一流,交期悦目,持续改善,客户满足
LDJ-QA胡章维 16
主要改善对比图片
联结一心,众志达金
XXX良率提升改善报告

感谢团队的各成员参与分析检讨, 并跟进验证。
Thank You!
4.分析改善验证
1.印刷不良调整 2.贴片不良优化
1.SPI程式优化 2.AOI程式优化
生产组
品质组
1.员工岗位培训 2.员工执行力加强 3.数据收集
1.员工岗位培训 2.生产作业过程品质 监控
二、问题分析:
原因分析
原因分析1: 从贴片与炉后不良品外观确认,景旺PCB有变形现象,如下图所示
一次过炉后超出标准1.73MM
3
空焊
开焊/虚焊
81
漏件立碑3 Nhomakorabea抹板
漏料
6
墓碑
锡桥
2
移位
总计
141
总计
不良数量 2 14 1 15 21 4 17 76
150
总结:TOP前三项移位,漏件,虚焊不良。
一.背景介紹:
问题
不良问题描述及影响度
调查
1、CHIP料移位/墓碑:
CHIP料移位,墓碑,影响测 试不通电,不开机。
一.背景介紹:
问题
C4 百分比
HG产品6月份不良机型的 Pareto 图
400 100
300
80
60 200
40 100
20
0
0
C1 WS831-10 HG532e-10 HG658b-20 HG255e-10 HG658
其他
C4
179
72
63
24
12
10
百分比
49.7
20.0
17.5
6.7
3.3
2.8
累积 %
49.7
二、问题分析:
良率提升改善报告ppt课件
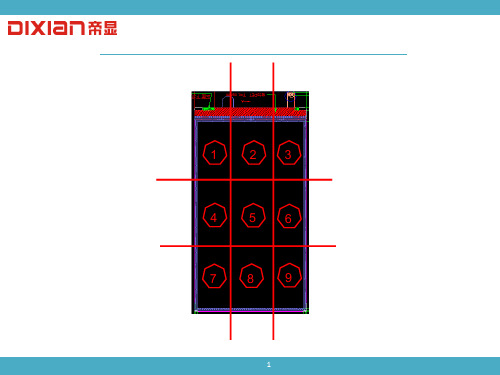
白色颗粒可擦拭
3区
1区
导光板与扩散之间
白色胶状可擦拭
5区
3区
反射与导光板之间
白色胶状不可擦拭
4区
层次 导光板与扩散之间 导光板与扩散之间 反射与导光板之间 导光板与扩散之间 导光板与扩散之间 导光板与扩散之间 导光板与扩散之间 导光板与扩散之间 导光板与扩散之间 导光板与扩散之间
不良状态 白色颗粒可擦拭 白色颗粒可擦拭 白色胶状可擦拭 白色胶状可擦拭 白色胶状不可擦拭 白色胶状可擦拭 白色胶状可擦拭 白色颗粒可擦拭 白色胶状不可擦拭 白色胶状不可擦拭
改善前
改善后
差异点:所以吸嘴避开导光板的1区到3区直接接触。
9
9
7改善方法
取消灯条贴附时的缓冲距离
改善前
改善后
差异点:在灯条缓冲位置处增加0.5cm的厚度,同时压覆灯条气 缸下限距离上升0.5cm,避免在贴附灯条是导光板发生形变。
10
10
8改善方法
取消导光板与铁壳组装过程中压附步骤
改善前
区域
层次
不良状态
区域
5区
导光板与扩散之间
白色颗粒不可擦拭
1区
1区
导光板与扩散之间
白色胶状可擦拭
2区
3区
反射与导光板之间
白色颗粒可擦拭
2区
2区
导光板与扩散之间
白色胶状可擦拭
1区
3区
导光板与扩散之间
异物造成白点可擦拭
3区
3区
导光板与扩散之间
白色胶状可擦拭
3区
1区
导光板与扩散之间
白色胶状可擦拭
2区
1区
导光板与扩散之间
日期 白点数量
良率提升改善报告ppt

03 效果评估
对品质检测和控制强化方案进行定期评估, 确保改善方案的有效性和可持续性
建立完善的品质检测和控制体系,提高检测 设备的精度和可靠性
02 实施措施
人员培训与技能提升
培训计划
制定针对不同岗位的培训计划, 提高员工的专业技能和操作水 平。
技能评估
定期对员工进行技能评估,找 出技能短板,制定针对性的提 升计划。
关键问题点分析
设备故障
设备故障是影响良率的关键因素 之一,需要定期维护和检查。
原材料质量
原材料质量不稳定也会导致良率 下降,需要严格控制原材料的质 量。
生产工艺问题
生产工艺问题也是影响良率的关 键因素之一,需要不断优化和改 进生产工艺。
改善需求与目标设定
根据良率现状分析,明确改善的需求和重 点,确定需要优化或改进的环节。
激励机制
建立员工技能提升与绩效挂钩 的激励机制,鼓励员工自主学 习和提升。
03
改善成果评估与总结
改善前后数据对比分析
01 良率提升情况
对比改善前后的数据,可以看出产品合格率有了显著提 高。
02 不合格产品原因分析
经过改善,主要的不合格产品原因得到了有效控制,如 制程稳定性和物料不良等。
03 未来改进方向
良率提升改善报 告PPT
汇报人:XXX
目录
01. 良 率 现 状 分 析 02. 改 善 方 案 与 实 施 03. 改 善 成 果 评 估 与 总 结
01
良率现状分析
良率水平及分布情况
良率水平
当前产品良率水平为XX%,相较 于之前有一定提升,但仍需进一
步优化。
不良品分布情况
不良品主要集中在XX环节,占比 达到XX%。
良率提升计划(2)PPT课件

5.1 用洒精擦拭来清洁导光板,存在不彻底现象,流程过程中存在落尘
5.2
清洁和放板工位无尘布及手指套更换时间未进行要求。易造成交叉污染。
备注
2021/7/24
11
4.整改对策
4M NO 1E
1.1 1人
2021/7/24
3
3.不良分析
XC0246A-350前三大不良跟线趋势图
白印
异物
黑白点
0.90% 0.80% 0.70% 0.60% 0.50% 0.40% 0.30% 0.20% 0.10% 0.00%
0.64% 0.53% 0.41%
4月份
0.590%.68% 0.51%
5月份
0.68% 0.72% 0.46%
1.2
2 机 2.1 3.1
3.2 3 料 3.3
3.4
4.1 4环
变异项改善
完成时间
备注
1.对产线人员进行岗前培训.培训考试合格后方可进行奇美专线上岗与 LQC与OQC进行漏检率.误判率排查.不合格者重新培训合格后上岗 2.作业员工严格按SOP作业 IPQC监督. 6月10号左右产线增加二次全检. 降低不良流出率.
1.2 部份后测员工与OQC漏检率与误判率较高。 2.1 机台使用时产生出污染
3.1 导光板来料出现白印,后检与OQC人员漏检与误判导致不良品流出。
3.2 下BEF来料出现凸点,后检与OQC人员漏检与误判导致不良品流出
3.3 现使用的洒精浓度为97℅,干燥时间过短未充分挥发,造成导光板白块。 3.4 目前使用的无尘布编制线较粗,有造成擦伤导光板的隐患。
- 1、下载文档前请自行甄别文档内容的完整性,平台不提供额外的编辑、内容补充、找答案等附加服务。
- 2、"仅部分预览"的文档,不可在线预览部分如存在完整性等问题,可反馈申请退款(可完整预览的文档不适用该条件!)。
- 3、如文档侵犯您的权益,请联系客服反馈,我们会尽快为您处理(人工客服工作时间:9:00-18:30)。
白色颗粒可擦拭
3区
1区
导光板与扩散之间
白色胶状可擦拭
5区
3区
反射与导光板之间
白色胶状不可擦拭
4区
层次 导光板与扩散之间 导光板与扩散之间 反射与导光板之间 导光板与扩散之间 导光板与扩散之间 导光板与扩散之间 导光板与扩散之间 导光板与扩散之间 导光板与扩散之间 导光板与扩散之间
不良状态 白色颗粒可擦拭 白色颗粒可擦拭 白色胶状可擦拭 白色胶状可擦拭 白色胶状不可擦拭 白色胶状可擦拭 白色胶状可擦拭 白色颗粒可擦拭 白色胶状不可擦拭 白色胶状不可擦拭
1
23
4 56 789
1
1
SF0006良率提升改善报告
工程部:杨兴强
2
2
目录
1 不良分析 2 分析方向 3 改善方法1 4 改善方法2 5 改善方法3 6 改善方法4 7 改善方法5 8 改善方法6 9 改善方法7 10 改善数据对比 11 结束语
3
3
p 1.不良分析
拆解20pcs不良品白点分析数据
改善后
差异点:取消导光板和铁壳在组装过程中压覆灯条的动作,避开 与导光板的1区到3区的直接接触。
11
11
p 9改善方法
减小压榨在取料过程中,压块与半成品的接触面积
改善前
改善后
差异点:减小压榨工位在取料的过程中,压块与导光板的接触面 积。
12
12
p 10改善数据
白点改善前与改善后的对比图
日期 白点数量
OK,动态测试NG.
到17s,风淋人数《2
员),可得出人员污染很大,需改进无尘服。
机
机台内部环境OK
?
?
清洁后的导光板上机后,机
料
设备稳 台导光板粘滚清洁过脏。手
指套和无尘布掉碎屑.(导光 板原材需点灯检查,还未进
更换导光板保护膜原材(李经理还在联系厂家改 善),手套和无尘布厂家在送样验证。
无尘布和手套掉碎屑,机台清洁改用粘滚清洁 (已实施)
总结:白点1区到3区共17pcs,不良比85%,可擦拭白点共16pcs,不良比 80%。不可擦拭白点共4pcs,不良比20%。
4
4
p 2分析方向
五个影响产品质量的因素分析
影响因素 安生测试产结果
改善对策
备注
人
无尘服测试NG 车间静态测试 进入风淋之前必须粘滚。风淋时间由之前的10s延长 改善后车间静态OK(无人员),动态NG(有人
6
6
p 4改善方法
导光板拖块接触面改善
改善前
改善后
差异点:在拖块表面贴附一层铁氟龙,然后在上中下各自贴附 一条泡沫棉,缩小导光板与拖块的接触面积。
7
7
p 5改善方法
导光板拖块位置改善
改善前
改善后
差异点:把拖块想上移动1cm,避开导光板的1区到3区的直接 接触。
8
8
p 6改善方法
调整吸嘴1到3区接触位置
日期 白点数量
9月24日 221
10月6日 26
改善前 9月25日 145
改善后 10月7日 71
9月26日 194
10月8日 52
9月27日 181
10月9日 24
9月28日 241
10月10日 65
改善前
改善后
从数据可以看出改善后的白点与改善前的白点下降了75.7%。
13
13
p 11结束语
感谢大家观看
区域
层次
不良状态
区域
5区
导光板与扩散之间
白色颗粒不可擦拭
1区
1区
导光板与扩散之间
白色胶状可擦拭
2区
3区
反射与导光板之间
白色颗粒可擦拭
2区
2区
导光板与扩散之间
白色胶状可擦拭
1区
3区
导光板与扩散之间
异物造成白点可擦拭
3区
3区
导光板与扩散之间
白色胶状可擦拭
3区
1区
导光板与扩散之间
白色胶状可擦拭
2区
1区
导光板与扩散之间
改善前
改善后
差异点:所以吸嘴避开导光板的1区到3区直接接触。
9
9
p 7改善方法
取消灯条贴附时的缓冲距离
改善前
改善后
差异点:在灯条缓冲位置处增加0.5cm的厚度,同时压覆
10
10
p 8改善方法
取消导光板与铁壳组装过程中压附步骤
改善前
14
14
畅想网络
Imagination Network
感谢观看!
文章内容来源于网络,如有侵权请联系我们删除。
15
15
行验证)
法
导光板保护膜清洁后,上机 后还是过脏。(其它严格按 照SOP执行)
每半个小时清洁导光板工位清洁粘滚及导光板拖块 (用粘滚清洁)。
环
车间静态测试OK,机台内部 测试OK
ok
指标达成
5
5
p 3改善方法
膜材清洁机粘滚高度调整
改善前
改善后
差异点:在粘滚的四个角增加0.5cm厚度,避免粘滚在清洁导 光板压的太紧造成白点。