机织物在各个方向上的剪切性能
增强材料 机织物试验方法 第5部分

增强材料机织物试验方法第5部分增强材料是指由两种或两种以上的材料组成的复合材料,具有优异的力学性能和耐久性。
机织物是增强材料中常用的一种,具有良好的拉伸、压缩和剪切强度。
为了评估机织物的性能和品质,需要进行一系列试验。
本文将介绍机织物试验的方法,主要包括拉伸试验、压缩试验、剪切试验和疲劳试验。
机织物的拉伸试验是评估其力学性能的一种重要方法。
该试验通常使用万能试验机进行,首先将机织物样品固定在试验机夹具上,然后以一定的速度施加拉力,测量样品的应力-应变曲线。
拉伸试验的参数包括弹性模量、屈服强度、抗拉强度和断裂强度等。
弹性模量是材料在弹性变形范围内的刚度度量,屈服强度是材料开始塑性变形的应力,抗拉强度是材料在拉断前的最大应力,断裂强度是材料在拉伸过程中发生断裂的最大应力。
机织物的压缩试验用于评估材料在受到压缩力时的性能。
该试验通常使用压缩试验机进行,将机织物样品放置在试验机夹具中,施加一定的压力进行压缩。
压缩试验的参数包括压缩弹性模量、屈服强度、抗压强度和断裂强度等。
压缩弹性模量是材料在弹性阶段的刚度度量,屈服强度是材料开始塑性变形的应力,抗压强度是材料在压断前的最大应力,断裂强度是材料在压缩过程中发生断裂的最大应力。
机织物的剪切试验用于评估材料在受到剪切力时的性能。
该试验通常使用剪切试验机进行,将机织物样品放置在试验机夹具中,施加一定的剪切力进行剪切。
剪切试验的参数包括剪切模量、屈服强度、抗剪强度和剪切失效应力等。
剪切模量是材料在剪切变形范围内的刚度度量,屈服强度是材料开始塑性变形的应力,抗剪强度是材料在剪切断裂前的最大应力,剪切失效应力是材料发生剪切失效的最大应力。
机织物的疲劳试验用于评估材料在长期受力条件下的耐久性能。
疲劳试验通常采用拉伸-压缩交替加载方式,将机织物样品固定在试验机夹具上,以一定的频率施加拉伸和压缩加载,进行多次循环,直到样品发生破坏。
疲劳试验的参数包括疲劳寿命、疲劳极限和循环应力等。
实验指导——织物的力学性能测试

5、结果计算 (1)计算 5 块试样的顶破强力算术平均值,精确至小数点后 1 位。 (2)当试验不在标准大气条件下进行时,需根据试样的实际回潮率计算其校
正顶破强力。 校正顶破强力=修正系数 K×实测顶破强力
棉毛、棉汗布针织物的顶破强力修正系数 K 值见表。 表 棉毛针织物顶破强力修正系数 K 值
(3)抓样法条样:试样宽度大于夹持宽度。适用于机织物,特别是经过重浆 整理的,不易抽边纱的和高密度的织物。
比较 3 种形态试样的试验结果,拆边法的强力不匀较小,而强力值略低于抓 样法。
2、试验参数 织物拉伸断裂的试验参数见表。
表 织物拉伸断裂的试验参数
试样 试样尺寸
夹持长度 织物断裂 拉伸速度
类型 宽(mm)×长(mm) /mm
四、结果计算 (1)计算试样的经、纬向平均断裂强力(N)。 计算精度:平均值≤10N 时,修约至 0.1N;10N<平均值<1000N 时,修约至
1N;平均值≥1000N 时,修约至 10N。 (2)计算试样的经、纬向断裂伸长率及其平均值。 预张力夹持试样时:
断裂伸长率 = ΔL ×100% L0
松式夹持试样时:
4、试验结果计算 分别计算 5 块试样的经向及纬向的撕破强力算术平均值(N),修约到 1 位小
数,必要时,记录样品每个方向的最大或最小撕破强力。
织物的顶破性能测定
顶破是指织物在垂直于织物平面的外力作用下,鼓起扩张而逐渐破坏的现 象。顶破的受力方式与单向拉伸断裂不同,它属于多向受力破坏。服装的肘部、 膝部的受力情况,袜子、鞋面布、手套等的破坏形式,降落伞、气囊袋、滤尘袋 等的受力方式都属于这种类型。对于某些延伸性较大的针织物(如纬编针织物), 顶破试验更具优越性。顶破试验机有弹子式、气压式及液压式等类型。
5-服装用织物及成衣加工性能

2.测定 (1)拧绞法 在一定张力下对浸渍后的试样拧绞, 在一定张力下对浸渍后的试样拧绞 , 释放 对比样照。 后,对比样照。 样照: 级最差。 样照 : 1-5 级 , 1 级最差 。 也可用湿态下折 痕恢复性评定。 痕恢复性评定。
10
(2)落水变形法 手执样品两角在水中轻轻摆动后提出水面, 手执样品两角在水中轻轻摆动后提出水面 , 反复数次,晾干与样照对比。 反复数次,晾干与样照对比。 (3)洗衣机法 按规定条件在洗衣机内洗涤,干燥后, 按规定条件在洗衣机内洗涤,干燥后,对 比样照。 比样照。 影响因素: 纤维的吸湿性、 影响因素 : 纤维的吸湿性 、 初始模量和织 物的湿态抗皱性。涤纶的洗可穿性最好。 物的湿态抗皱性。涤纶的洗可穿性最好。
6
测试方法: 测试方法: 试样对折在一定负荷下保持一定时间, 试样对折在一定负荷下保持一定时间,负 荷去除恢复一定时间测量折痕的回复角。 荷去除恢复一定时间测量折痕的回复角。 指标: 指标: 抗皱性好; 折痕恢复角(急,缓),大,抗皱性好;
7
形状记忆面料
8
9
又称免烫性) 三、洗可穿性(又称免烫性) 1.洗可穿性 1.洗可穿性 织物洗涤后不加熨烫或稍加熨烫就可保持 衣服可穿用)性能,称之为~ 平挺(衣服可穿用)性能,称之为~。
16
2.纱线性质 2.纱线性质 (1)捻度高不易起球(纱线结构紧); 捻度高不易起球(纱线结构紧) 纱线条干均匀,不易起球; (2)纱线条干均匀,不易起球; 股线不易起毛起球(结构紧,条干好) (3)股线不易起毛起球(结构紧,条干好); (4)花式线,膨体纱易起毛起球(结构松)。 花式线,膨体纱易起毛起球(结构松)。
服装气候
22
影响服装穿着舒适性各因素相关图
纺织材料的力学性能测试与分析

纺织材料的力学性能测试与分析在纺织领域,了解和评估纺织材料的力学性能是至关重要的。
这不仅对于确保纺织品的质量和性能至关重要,还对纺织产品的设计、生产和应用具有重要的指导意义。
纺织材料的力学性能涵盖了多个方面,包括拉伸性能、弯曲性能、压缩性能、剪切性能和摩擦性能等。
这些性能的优劣直接影响着纺织品在使用过程中的表现和寿命。
拉伸性能是纺织材料最基本和最重要的力学性能之一。
通过拉伸试验,可以获得诸如断裂强力、断裂伸长率、初始模量等关键参数。
断裂强力反映了材料抵抗拉伸破坏的能力,而断裂伸长率则表示材料在断裂前能够承受的伸长程度。
初始模量则体现了材料在小变形范围内的刚性。
在进行拉伸性能测试时,需要使用专门的拉伸试验机。
测试过程中,试样被夹持在试验机的夹具上,然后以一定的速度进行拉伸,直至试样断裂。
测试结果会受到多种因素的影响,例如试样的长度、宽度、夹持方式、拉伸速度以及环境温湿度等。
为了获得准确可靠的测试结果,必须严格按照标准测试方法进行操作,并对测试条件进行精确控制。
弯曲性能反映了纺织材料在弯曲过程中的抵抗变形能力。
常用的弯曲性能测试方法有悬臂梁弯曲法和三点弯曲法。
悬臂梁弯曲法适用于较薄和柔软的材料,而三点弯曲法则适用于较厚和硬挺的材料。
弯曲性能的测试结果通常用弯曲刚度和弯曲模量来表示,这些参数对于评估纺织品的手感、悬垂性和成型性具有重要意义。
压缩性能对于像非织造布和填充材料等具有重要的意义。
压缩性能测试可以评估材料在受到压力时的变形和恢复能力。
通过测量材料在不同压力下的厚度变化,可以计算出压缩率和压缩弹性回复率等参数。
这些参数对于设计具有良好保暖性和舒适性的纺织品非常重要。
剪切性能主要用于评估纺织材料在受到剪切力时的变形特性。
剪切性能测试方法包括平面剪切法和扭转剪切法。
剪切性能对于织物的抗皱性和尺寸稳定性有着重要的影响。
摩擦性能也是纺织材料力学性能的一个重要方面。
摩擦性能的好坏直接关系到纺织品的穿着舒适度和耐用性。
学习织物的基本结构参数及基本性能

学习织物的基本结构参数及基本性能织物的基本结构参数及基本性能一、机织物1 、经纬纱细度:指经纬纱的粗细程度。
表示经纬纱细度的指标主要有:英制支数、公制支数、特数、旦数。
2、密度 M织物密度是指织物中经向或纬向单位长度内的纱线根数,表示为:根/10cm 或者根/英寸。
3、紧度 E织物紧度指织物中纱线挤紧的程度,有经向紧度和纬向紧度之分,用单位长度内纱线直径之和所占百分率来表示。
4 、覆盖系数覆盖系数是指纱线的投影面积占织物面积的百分率,用R表示。
Et--经向紧度 Ew--纬向紧度5、织物的长度、宽度和厚度长度:即匹长,单位为米。
宽度:是指织物横向的最大尺寸,称为幅宽。
单位为厘米。
厚度:织物在一定压力下正反两面间的垂直距离,以毫米为计量单位。
影响织物厚度的主要因素:•纱线线密度;•织物组织;•纱线在织物中的屈曲程度;•生产加工时的张力。
6、单位面积重量织物的重量通常以每平方米织物所具有的克数来表示,称为平方米重。
棉织物常以每平方米的退浆干重来表示,毛织物则常采用每平方米的公定重量来表示。
也有其他表示方式:如全幅一米重、条重等。
P t--经向密度 P w--纬向密度 N tT--经纱特数 N tw--纬纱特数上式未考虑织物的中经纬纱的缩率、回潮率等。
二、针织物1、横密与纵密横密:指沿线圈横列方向在规定长度(50mm)内的线圈数。
纵密:指沿线圈纵行方向在规定长度(50mm)内的线圈数。
2、线圈长度针织物的线圈长度是指每一个线圈的纱线长度,它由线圈的圈干和延展线组成。
线圈长度愈长,针织物密度愈小、愈稀薄;尺寸稳定性、弹性、耐磨性愈差;强度愈低;脱散性愈大;抗起毛起球和抗勾丝性愈差;透气性愈好。
3、未充满系数未充满系数为线圈长度与纱线直径的比值。
此值越大,表明织物中未被纱线充满的空间愈大,织物愈是稀松。
4、平方米重用每平方米的干燥重量克数来表示。
三、织物的坚牢度织物在使用过程中,受力破坏的最基本形式是拉伸断裂、撕裂、顶裂和磨损。
棉织物(机织)介绍
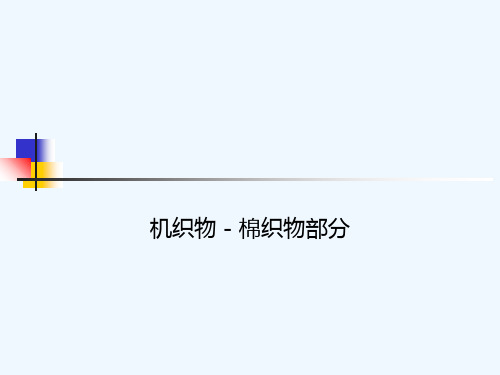
2019/2/12
16
(4)哔叽(SERGE)
哔叽质地柔软,也来源于毛织物,采用2/2加强斜纹组织,
正反面织纹相同,斜向约为45,但方向相反。 经密:纬密=6:5,经纬紧度与平布相近。 纱哔叽用28-32tex(21s-28s)单纱织制较多。线哔叽多用 14tex×2-18tex×2(42/2-32/2s)织制,半线哔叽常用单纱作纬。 元色和杂色哔叽多数用作老年服装、童装,印花哔叽常用作妇女、 儿童衣料,大花哔叽可用被面、窗帘等。
12
斜纹(TWILL)
2019/2/12
13
(1)斜纹布
2/1左斜纹,经纬纱交织次数比平纹少,经向密度比平 纹布大 。
常用经纬纱支为42-18tex(14s-32s),经纬特相等或接 近。经纬向紧度比为3:2,紧度大于平纹 斜纹布坯布主要用作橡胶鞋基布,球鞋夹里布,金钢 砂基布,染整加工后的成品,可制作服装、被套、台 布、阳伞等。 特点是厚实,表面有明显得斜向纹路,方面织纹不明 显,近似平纹,因此又称为单面斜纹。
2019/2/12
幅 宽:57″/58″
39
(3)轧纹布
利用合成纤维热塑性形成。 方法是将已经染色的或者印花的细布, 用有凹凸花纹的滚筒轧褚凹凸不平的花 纹来,然后再经过树脂整理,使轧出的 花纹定型。
2019/2/12
40
帆布(CANVAS)
帆布是经纬纱均采用多股线织制的粗厚织物。紧密厚 实,手感硬挺,坚实耐磨。
2019/2/12 3
(2)府绸(POPLIN)
平纹组织,经密高于纬密(约5:3或2:1)
一般经纬纱支相同,或纬纱略粗于经纱。 其细度范围: ⑴ 纱府绸29~10tex(20~60英支) 经纬纱多为40英支(14.5tex), 克重在110~125g/m2之间 ⑵ 线府绸14tex×2~5tex×2(42/2~120/2英支) 一般经纱为股线,纬纱为单纱 高级纯棉线府绸则用120/2~80/2英支股线制织 可做衬衫、睡衣、床上用品等。
纺织品检测之物理性能详解

纺织品检测之物理性能详解一、介绍不同面料其性能表现各不一样,带来服装应用范围和最终用途也会大相径庭。
因此,认识和掌握面料的各种性能,对正确地选用材料,合理地设计服装,满意地穿着服装会大有帮助,产生事半功倍的效果。
面料的性能包括物理机械性能、化学性能、外观性能以及卫生保健性能和缝纫加工性能等服用性能。
二、定义:织物在外力作用下引起的应力与变形间的关系所反映的性能叫做织物的物理机械性能。
它包含强度、伸长、弹性及耐磨性等方面的性能。
织物在服用过程中,受到较大的拉伸力作用时,会产生拉伸断裂。
将织物受力断裂破坏时的拉伸力称为断裂强度;在拉伸断裂时所产生的变形与原长的百分率,称为断裂伸长率。
⑴纤维的性质:纤维的性质是织物拉伸断裂性能的决定因素。
纤维的断裂强度是指单位细度的纤维能承受的最大拉伸力,单位:CN/dtex。
在天然纤维中,麻纤维的断裂强度最高,其次是蚕丝和棉,羊毛最差。
化纤中,锦纶的强度最高,并且居所有纤维之首,其次是涤纶、丙纶、维纶、腈纶、氯纶、富强纤维和粘胶纤维。
其中,粘胶纤维强度虽低,但略高于羊毛,在湿态下,其强力下降很多,几乎湿强仅为干强的40~50%。
除粘胶纤维外,羊毛、蚕丝、维纶、富强纤维的湿强也有所下降,但棉、麻纤维例外,其湿强非但没有下降反而有所提高。
涤纶、丙纶、氯纶、锦纶、腈纶等则因吸湿小,而使其干、湿态强度相差无几。
至于断裂伸长率,则属麻纤维最小,只有2%左右,其次为棉,只有3~7%,蚕丝15~25%,而羊毛属天然纤维之首,可达25~35%。
化纤中,以维纶和粘胶纤维的断裂伸长率最低,在25%左右,其它合纤均在40%以上。
⑵纱线结构:一般情况下,纱线越粗,其拉伸性能越好;捻度增加,有利于拉伸性能提高;捻向的配置一致时,织物强度有所增加;股线织物的强度高于单纱织物。
⑶织物的组织结构:在其它条件相同的情况下,在一定长度内纱线的交错次数越多,浮长越短,织物的强度和断裂伸长率越大。
因此,三原组织中以平纹的拉伸性能为最好,斜纹次之,缎纹织物最差。
第9章-织物剪切性能设计
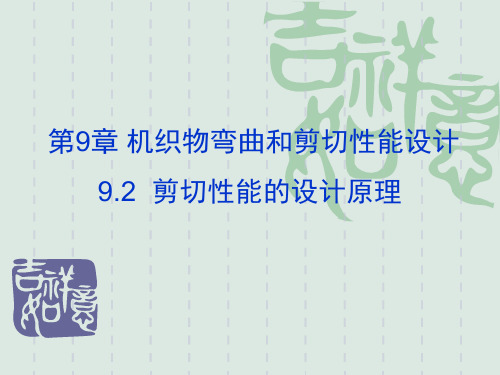
织物组织和经纬纱线屈曲率的函数。
剪切刚度G与原料、结构的关系
由方程 (1)、(2)和(5)可得方程(6):
F m 2 N u (C ) L
微分可得力学方程:
G1
G2
F1 u 1 (C ) 100 k n2 ( 1 (C ) u )
F m f L
m k n1 n2
m-单位面积织物中经纬纱线的交织点数 ; f-单个交织点处经纬纱间的摩擦力; L-受剪切力的试样长度(5cm)。
n1 n2 织物经、纬纱密度
k 组织系数,平纹k=1,2/2斜0.5
摩擦力f分析 张力N作用下纱线受力状态如图,交织 点处纱线间的摩擦力f为:
f P u
u
(2)
- 经纬纱线间的摩擦系数。
图9-7 纱线在恒定张力下的受力状态
压力P与张力N的关系取决于织物结构,可用下 面近似方法求取,织物结构简化模型如图9-8
(C )
(a)小浮长模型 (b)大浮长模型 图9-8 织物结构的简化模型
P 2 N (C )
(5)
式中 (C ) -
12
2.2 精纺毛型织物剪切刚度
1 , 2 与织物结构参数的相关系数
1
经纬纱接触面积(s) 0.77
2
0.80
经纱捻系数
纬纱捻系数 含毛率(%) 织物组织(k)
-0.51
-0.06 -0.14 -0.64
-0.55
-0.07 -0.12 -0.64
s d1 d 2 •经纬纱接触面积s∝经纬纱直径之积 •摩擦系数变化率与经纬纱接触面积的关系最密切
2.1 织物剪切刚度G的理论方程
织物三向正交结构特点

织物三向正交结构是一种特殊的纺织结构,其特点是纱线在三个方向相互垂直交织。
这种结构在织物中形成了一个完整的立体网状结构,具有以下特点:
1.高强度和刚性:由于纱线在三个方向上都相互交织,因此织物具
有很高的强度和刚性。
它能够承受较大的压力和拉伸力,不易变形。
2.优异的稳定性:由于三向正交结构中纱线在各个方向上都相互交
叉连接,织物不容易产生滑动或扭曲,因此具有很好的稳定性。
3.良好的透气性和保暖性:由于三向正交结构的网状结构,空气可
以在其中自由流动,因此织物具有良好的透气性。
同时,这种结构也使得织物具有一定的保暖性。
4.优良的疲劳性能:三向正交结构中的纱线在多个方向上都具有一
定的支撑作用,可以分散承受外力的作用,因此织物具有良好的抗疲劳性能。
5.易于设计和制作:三向正交结构可以通过计算机辅助设计软件进
行精确的设计和计算,并且可以采用现代化的纺织技术进行大规模的生产制作。
超细纤维织物的弯曲性能和剪切性能的研究
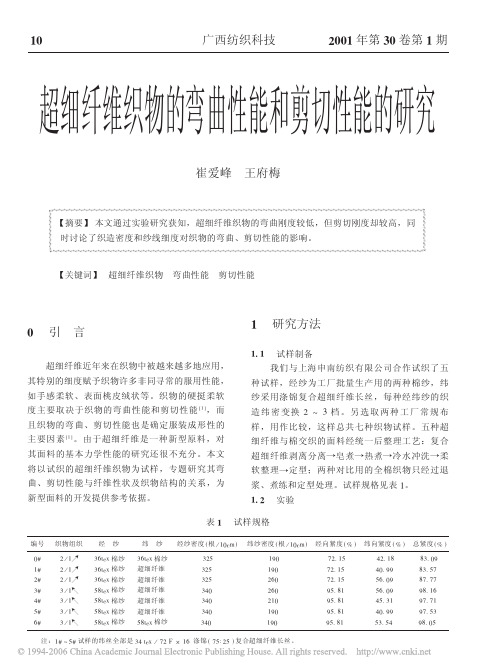
超细纤维织物的弯曲性能和剪切性能的研究崔爱峰王府梅表!试样规格编号织物组织经纱纬纱经纱密度!根"#$%&’纬纱密度!根"#$%&’经向紧度!(’纬向紧度!(’总紧度!(’$)*"#(+,-./棉纱+,-./棉纱+*0#1$2*3#04*3#55+3$1#)*"#(+,-./棉纱超细纤维+*0#1$2*3#04$3115+302*)*"#(+,-./棉纱超细纤维+*0*,$2*3#00,3$152322+)+"#)05-./棉纱超细纤维+4$*,$1035#0,3$1153#,4)+"#)05-./棉纱超细纤维+4$*#$1035#403+#1232#0)+"#)05-./棉纱超细纤维+4$#1$1035#4$3111230+,)+"#)05-./棉纱05-./棉纱+4$#1$1035#0+304153$0注:#)60)试样的纬丝全部是+4-./"2*78#,涤锦!209*0’复合超细纤维长丝。
超细纤维近年来在织物中被越来越多地应用,其特别的细度赋予织物许多非同寻常的服用性能,如手感柔软、表面桃皮绒状等。
织物的硬挺柔软度主要取决于织物的弯曲性能和剪切性能:#;,而且织物的弯曲、剪切性能也是确定服装成形性的主要因素:#;。
由于超细纤维是一种新型原料,对其面料的基本力学性能的研究还很不充分。
本文将以试织的超细纤维织物为试样,专题研究其弯曲、剪切性能与纤维性状及织物结构的关系,为新型面料的开发提供参考依据。
!研究方法!%!试样制备我们与上海申南纺织有限公司合作试织了五种试样,经纱为工厂批量生产用的两种棉纱,纬纱采用涤锦复合超细纤维长丝,每种经纬纱的织造纬密变换*6+档。
另选取两种工厂常规布样,用作比较,这样总共七种织物试样。
五种超细纤维与棉交织的面料经统一后整理工艺:复合超细纤维剥离分离$皂煮$热煮$冷水冲洗$柔软整理$定型;两种对比用的全棉织物只经过退浆、煮练和定型处理。
结构参数对三维机织复合材料拉伸和剪切性能的影响

浙江理工大学学报,第51卷,第1期,2024年1月J o u r n a l o f Z h e j i a n g S c i -T e c h U n i v e r s i t yD O I :10.3969/j.i s s n .1673-3851(n ).2024.01.008收稿日期:2022-12-09 网络出版日期:2023-07-07基金项目:国家自然科学基金面上项目(52075498);浙江理工大学科研启动基金(11152932612007)作者简介:武维莉(1990- ),女,安徽宿州人,讲师,博士,主要从事复合材料方面的研究㊂结构参数对三维机织复合材料拉伸和剪切性能的影响武维莉,潘忠祥(浙江理工大学纺织科学与工程学院(国际丝绸学院),杭州310018) 摘 要:为了研究三维机织结构参数与复合材料力学性能之间的关系,设计织造了4种不同结构的三维机织物,包括浅交直联㊁层层角联锁㊁接结纬接结和接结纬接结+衬纬纱结构,并分别将其制备成复合材料,通过材料试验机探究所得复合材料的结构参数对拉伸㊁剪切性能的影响㊂结果表明:纤维体积分数相同时,纱线的屈曲和纱线交织结构决定了复合材料的拉伸性能及尺寸稳定性㊂经向上,浅交直联结构复合材料拉伸性能和尺寸稳定性最佳,经纱屈曲大的接结纬接结+衬纬纱结构复合材料拉伸性能和尺寸稳定性最差;纬向上,接结纬接结结构复合材料拉伸性能和离散性最差㊂对比2个方向的拉伸性能发现,复合材料的纬向拉伸性能远远优于经向拉伸性能㊂织物的交织结构决定了剪切性能及尺寸稳定性,浅交直联复合材料的结构紧密,剪切模量最大,接结纬接结复合材料的结构疏松,剪切模量最小,而剪切强度几乎呈相反的规律㊂该研究明确了纤维体积分数㊁纱线屈曲程度㊁织物交织结构等结构参数对三维机织复合材料拉伸和剪切性能的影响,为三维机织复合材料的研究和应用提供了参考㊂关键词:三维;机织复合材料;拉伸性能;剪切性能;尺寸稳定性中图分类号:T S 195.644文献标志码:A文章编号:1673-3851(2024)01-0063-11引文格式:武维莉,潘忠祥.结构参数对三维机织复合材料拉伸和剪切性能的影响[J ].浙江理工大学学报(自然科学),2024,51(1):63-73.R e f e r e n c e F o r m a t :W U W e i l i ,P A N Z h o n g x i a n g .T h e e f f e c t o f s t r u c t u r a l p a r a m e t e r s o n t h e t e n s i l e a n d s h e a r p r o pe r t i e s of 3D w o v e n c o m p o s i t e s [J ].J o u r n a l o f Z h e j i a ng S c i -T e ch U ni v e r s i t y,2024,51(1):63-73.T h e e f f e c t o f s t r u c t u r a l p a r a m e t e r s o n t h e t e n s i l e a n d s h e a r p r o p e r t i e s o f 3D w o v e n c o m po s i t e s W U W e i l i ,P A N Z h o n g x i a n g(C o l l e g e o f T e x t i l e S c i e n c e a n d E n g i n e e r i n g (I n t e r n a t i o n a l I n s t i t u t e o f S i l k ),Z h e j i a n g S c i -T e c h U n i v e r s i t y ,H a n gz h o u 310018,C h i n a ) A b s t r a c t :T o i n v e s t i g a t e t h e r e l a t i o n s h i p be t w e e n t h e p a r a m e t e r s of T h r e e -d i m e n s i o n a l (3D )w o v e n s t r u c t u r e s a n d t h e m e c h a n i c a l p r o p e r t i e s o f c o m po s i t e s ,f o u r s t r u c t u r e s o f 3D w o v e n f a b r i c s w e r e p r e p a r e d ,i n c l u d i n g s h a l l o w c r o s s -l i n k e d ,l a y e r -b y -l a y e r a n g l e -i n t e r l o c k ,"s t i t c h i n g we f t "w e f t k n i t t e d a n d "s t i t c h i n g w e f t "w e f t k n i t t e d +i n s e r t e d w e f t s t r u c t u r e s .T h e y w e r e p r e p a r e d i n t o c o m p o s i t e s ,a n d b yu s i n g a m a t e r i a l t e s t i n g m a c h i n e ,t h e e f f e c t s o f s t r u c t u r a l p a r a m e t e r s o n t e n s i l e a n d s h e a r p r o pe r t i e s of t h e c o m p o s i t e s w e r e e x p l o r e d .T h e r e s u l t s s h o w t h a t w i t h t h e s a m e f i b e r v o l u m e f r a c t i o n ,t h e y a r n c r i m p an d t h e i n t e r l a c i n g s t r u c t u r e o f y a r n s d e t e r m i n e t h e t e n s i l e p r o p e r t i e s a n d d i m e n s i o n a l s t a b i l i t y of t h e c o m p o s i t e s .I n t h e w a r p d i r e c t i o n ,t h e s h a l l o w c r o s s -l i n k e d w o v e n c o m po s i t e s e x h i b i t t h e m o s t e x c e l l e n t t e n s i l e p r o p e r t i e s a n d d i m e n s i o n a l s t a b i l i t y ,w h i l e t h e "s t i t c h i n g we f t "w e f t k n i t t e d+i n s e r t e d w e f t r e i n f o r c e d c o m p o s i t e s w i t h l a r g e w a r p c r i m p at t a i n t h e w o r s t t e n s i l e p e r f o r m a n c e .I n t h e w e f t d i r e c t i o n ,t h e s t r u c t u r e "s t i t c h i n g w e f t "w e f t k n i t t e d r e i n f o r c e d c o m p o s i t e s s t i l l e x h i b i t t h e w o r s t t e n s i l e p r o p e r t y a n d d i s c r e t e n e s s .C o m p a r i s o n o f t h e t e n s i l e p r o p e r t i e s i n b o t h d i r e c t i o n s i n d i c a t e s t h a t t h e t e n s i l e p r o p e r t yo f t h e c o m p o s i t e s i n t h e w e f t d i r e c t i o n i s s u p e r i o r t o t h a t i n t h e w a r p d i r e c t i o n.T h e i n t e r l a c i n g s t r u c t u r e o f t h e f a b r i c s d e t e r m i n e s t h e s h e a r p r o p e r t i e s a n d d i m e n s i o n a l s t a b i l i t y.T h e s h a l l o w c r o s s-l i n k e d c o m p o s i t e s p e r f o r m t h e h i g h e s t s h e a r m o d u l u s w i t h a d e n s e s t r u c t u r e,w h i l e t h e"s t i t c h i n g w e f t"w e f t k n i t t e d c o m p o s i t e s w i t h a l o o s e r s t r u c t u r e r e s u l t i n a l o w e s t s h e a r m o d u l u s.H o w e v e r,t h e s h e a r s t r e n g t h s h o w s a n a l m o s t o p p o s i t e l a w.T h i s s t u d y c l a r i f i e s t h e e f f e c t s o f t h e s t r u c t u r a l p a r a m e t e r s s u c h a s f i b e r v o l u m e f r a c t i o n,y a r n c r i m p d e g r e e,a n d f a b r i c i n t e r l a c i n g s t r u c t u r e o n t h e t e n s i l e a n d s h e a r p r o p e r t i e s o f3D w o v e n c o m p o s i t e s,p r o v i d i n g r e f e r e n c e f o r t h e r e s e a r c h a n d a p p l i c a t i o n o f3D w o v e n c o m p o s i t e s.K e y w o r d s:3D;w o v e n c o m p o s i t e s;t e n s i l e p r o p e r t y;s h e a r p r o p e r t y;d i m e n s i o n a l s t a b i l i t y0引言纤维增强复合材料因具有较高的比强度㊁比模量以及较好的耐疲劳和耐腐蚀特性,广泛应用于航空航天㊁船舶㊁汽车㊁建筑等领域㊂由于层间或Z向纱的增强作用,三维机织增强复合材料的层间力学性能明显优于二维结构[1-4]㊂B e h e r a等[5]发现,三维机织复合材料具有优异的抗冲击性㊁防刺穿及动态热机械性能㊂P e e r z a d a等[6]研究发现,三维机织结构中Z向纱的存在使经纬纱承担的负荷减少,提升了复合材料的整体强度和刚度㊂B r a n d t等[7]发现,Z向纱明显提高了复合材料的层间性能,其含量的增加使经纬向的拉伸强度下降,但压缩强度不受影响㊂C o x等[8]探究了三维机织复合材料的拉伸㊁压缩和弯曲性能,结果发现与二维复合材料相比,三维复合材料的面外性能增加,面内性能有所降低㊂I v a n o v等[9]认为,三维复合材料的杨氏模量与二维复合材料接近,但在45ʎ方向上,三维复合材料的最大应力㊁应变明显高于二维复合材料㊂P o t l u r i等[10]探究了三维复合材料的抗冲击性能,发现不同结构的三维复合材料的损伤面积和宽度相似,但远小于二维复合材料㊂针对不同结构的三维复合材料力学表现,国内外学者展开了相关研究㊂S a l e h等[11]研究了3种不同结构(正交结构㊁层层角联锁和角联锁结构)的三维机织复合材料的准静态拉伸性能,发现不同结构的复合材料的拉伸刚度与强度主要取决于经纱和纬纱含量,而结构类型的影响较小㊂其他学者也发现,织物结构对复合材料力学性能有重要影响㊂B e h e r a 等[5]探究了三维机织复合材料的拉伸性能,发现不同结构的材料,其拉伸强度在经向上的大小排序为三维正交结构复合材料㊁经向联锁结构复合材料㊁角联锁结构复合材料,而在纬向上则相反㊂H u a n g 等[12]测试了4种玻璃纤维三维机织复合材料的拉伸性能,包括层与层绑定的正交结构㊁完全正交结构㊁角联锁结构㊁改进的角联锁结构,发现织物结构与复合材料的拉伸强度及尺寸稳定性有很大关系㊂X u等[13]㊁D a i等[14]和J i a o等[15]探讨了织物结构对三维复合材料拉伸性能的影响,发现结构不同导致富树脂区不同,角联锁结构复合材料在经纱方向上具有较大的拉伸模量和强度㊂S t i g等[16]验证了这一观点,并且通过实验发现三维复合材料的刚度和强度随着纱线的屈曲增加呈现非线性下降,添加填充纱可以增加复合材料的力学性能㊂上述工作探究了三维机织结构复合材料与力学性能之间的关系,但是三维机织结构种类繁多,设计人员须根据使用工况选择合适的织物结构㊂然而,目前三维机织结构与力学性能之间的关系研究不够充分,影响了对其力学性能可靠性的评估㊂本文设计织造了4种不同结构的三维机织物,包括浅交直联㊁层层角联锁㊁接结纬接结和接结纬接结+衬纬纱结构,并分别将其制备成复合材料,对三维机织复合材料的拉伸性能和剪切性能进行测试,分析了织物结构参数对复合材料的拉伸和剪切性能的影响㊂本文的研究结论为三维机织复合材料的设计和应用提供了指导㊂1实验部分1.1实验材料碳纤维纱线(T70012K,纤度954.3t e x)购于日本东丽公司;环氧树脂(R T M3266)购于中航复合材料有限责任公司;多综眼多剑杆织机,自研㊂纤维和树脂的基本参数见表1㊂表1实验材料的基本参数实验材料密度/(g㊃c m-3)抗拉模量/G P a抗拉强度/M P a断裂伸长率/%碳纤维1.8023049002.1环氧树脂1.252605.0 1.2实验方法1.2.1三维织物织造本文设计了4种不同组织结构的碳纤维三维机46浙江理工大学学报(自然科学)2024年第51卷织结构,包括浅交直联结构㊁层层角联锁结构㊁接结纬接结结构和接结纬接结+衬纬纱结构,在多综眼多剑杆织机上完成织造㊂三维织物实物照片及沿织物经向的截面结构示意图如图1所示,其中:结构示意图中绿色椭圆点代表纬纱,白色屈曲的纱线代表经纱;白色实线表示观察切面上的经纱,而虚线则表示交织着的相邻经纱㊂上机织造及织物参数见表2,织物的上机图如图2所示㊂图14种三维织物实物照片和沿经向截面结构示意图表2三维机织物的织物参数织物结构经密/(根㊃10c m-1)纬密/(根㊃10c m-1)平方米质量/(k g㊃m-2)厚度/m m浅交直联61.842.665518.51层层角联锁59.430.674638.81接结纬接结接62.857.8796810.02接结纬接结+衬纬纱60.057.4766010.62注:为了对比方便,表中经密㊁纬密指单层交织结构的纱线根数㊂而实际上三维机织结构在厚度上有多层交织结构,总的经纬密度还应该乘以交织层数㊂1.2.2复合材料的制备实验采用树脂传递模塑成型工艺(R e s i n T r a n s f e r M o l d i n g,R T M)制作复合材料,其工艺过程及原理如图3所示㊂首先在预设厚度的模具内放置三维织物,闭合模具并灌注树脂,然后在常温条件下固化,制备复合材料㊂在成型过程中,固定的模腔深度导致4种三维机织复合材料的厚度一致,复合材料的厚度均为8.30m m㊂由于织物平方米质量不同导致复合材料的纤维体积分数(F i b e r v o l u m e f r a c t i o n,V f)有所区别,4种三维复合材料的V f见表3㊂1.3测试与表征1.3.1复合材料的拉伸性能测试采用材料实验机(I n s t r o n5940,美国I n s t r o n公司)测试复合材料的经向和纬向性能,测试方法采用A S T M D3039/D3039M-08S t a n d a r d T e s t M e t h o d f o r T e n s i l e P r o p e r t i e s o f P o l y m e r M a t r i x C o m p o s i t e M a t e r i a l s㊂经向拉伸采用矩形长条试样,示意图如图4(a)所示㊂由于纬向纱线伸直度高,断裂失效容易发生在试样两端,因此纬向拉伸试样设计成狗骨形状,示意图如图4(b)所示㊂实验时首先调节拉伸夹具的标距,设为150m m,安装试验件,然后连接应变片和数采系统㊂为了使夹具夹紧试样,对夹具施加一定的预加张力(纬向拉伸为3k N,经向拉伸2k N),拉伸速度设定为2m m/m i n㊂每种结构测试5个样品㊂1.3.2复合材料的剪切性能测试剪切测试采用A S T M D5379/D5379M-12 S t a n d a r d T e s t M e t h o d f o r S h e a r P r o p e r t i e s o f C o m p o s i t e M a t e r i a l s b y t h e V-N o t c h e d B e a m M e t h o d,测试试样示意图和夹具实物照片如图5所示㊂实验时把试样放置在V型切口剪切夹具内部,将夹具安装到材料试验机的压缩盘上,调节上压盘靠近夹具的压杆上,设定测试速度为2m m/m i n㊂根据测试56第1期武维莉等:结构参数对三维机织复合材料拉伸和剪切性能的影响图2 4种三维织物的织造上机图标准,在剪切应变大于5%时,试样视为破坏,测试终止㊂每种结构测试5个样品㊂1.3.3 试样编号测试前对实验试样进行系统性地编号,定义4种复合材料的经向拉伸性能(编号 -T J )和纬向拉伸性能(编号 -T W )㊁剪切性能(编号 -S),每种结构测试5个试样,其编号分别是N o .1㊁N o .2㊁N o .3㊁N o .4㊁N o .5㊂4种织物结构(浅交直联㊁层层角联锁㊁接结纬接结接㊁接结纬接结+衬纬纱)的编号分别是01㊁02㊁03㊁04㊂例如,浅交直连复合材料的经向拉伸5个试样测试编号分别是01-T J -N o .1㊁01-T J -N o .2㊁01-T J -N o .3㊁01-T J -N o .4㊁01-T J -N o .5,测试试样的具体编号见表4㊂2 结果与讨论2.1 织物结构分析本文设计织造的4种组织结构中经纬纱的交织规律不同,其中三维织物浅交直联和层层角联锁结构相似,而接结纬接结和接结纬接结+衬纬纱结构更为相似㊂相对于接结纬接结,接结纬接结+衬纬纱在纬向上又添加了额外的衬纬纱,使得纬纱含量有所增加㊂三维机织结构在厚度方向上形成多层的经纬纱交织,相比二维机织物,三维机织结构层间性能更佳,作为复合材料增强体结构具有一定的优势㊂织物的交织程度决定了结构的紧密程度,也影响了力学性能的稳定性㊂纱线交织点越多,形成的织物结构越稳定,纱线自由度小,受到载荷时材料的力学性能越稳定㊂以浅交直联结构为例,在织造打纬时,经纱每横跨两根纬纱交织形成扣锁一次,即在1㊁3㊁5列纬纱处形成紧密的交织结构,如图6所示㊂在织造2和4列纬纱时,经纱只发生上下移动形成梭口用来添加纬纱,而不会施加较大的力锁紧纱线㊂同理,对于层层角联锁结构,织造每一根纬纱都会交图3 R T M 工艺过程及原理图66浙江理工大学学报(自然科学)2024年 第51卷表3 三维机织结构复合材料的纤维体积分数V f织物结构V f /%浅交直联41.85层层角联锁48.00接结纬接结接43.44接结纬接结+衬纬纱51.13织扣紧一次,使得织物结构变得紧密㊂定义图6中1至3列的纬纱隔距为打纬交织宽度T ㊂T 越小,纱线交织次数越多,织物结构越紧密;T 越大,经纱及纬纱受到的束缚越小,织物结构越疏松㊂4种结构的打纬交织宽度的统计数据见表5㊂图4 复合材料拉伸测试试样示意图图5 复合材料剪切测试试样示意图及测试设备表4 4种三维复合材料的测试编号织物结构经向拉伸编号纬向拉伸编号剪切编号浅交直联01-T J -N o .1㊁01-T J -N o .2㊁01-T J -N o .3㊁01-T J -N o .4㊁01-T J -N o .501-T W -N o .1㊁01-T W -N o .2㊁01-T W -N o .3㊁01-T W -N o .4㊁01-T W -N o .501-S -N o .1㊁01-S -N o .2㊁01-S -N o .3㊁01-S -N o .4㊁01-S -N o .5层层角联锁02-T J -N o .1㊁02-T J -N o .2㊁02-T J -N o .3㊁02-T J -N o .4㊁02-T J -N o .502-T W -N o .1㊁02-T W -N o .2㊁02-T W -N o .3㊁02-T W -N o .4㊁02-T W -N o .502-S -N o .1㊁02-S -N o .2㊁02-S -N o .3㊁02-S -N o .4㊁02-S -N o .5接结纬接结接03-T J -N o .1㊁03-T J -N o .2㊁03-T J -N o .3㊁03-T J -N o .4㊁03-T J -N o .503-T W -N o .1㊁03-T W -N o .2㊁03-T W -N o .3㊁03-T W -N o .4㊁03-T W -N o .503-S -N o .1㊁03-S -N o .2㊁03-S -N o .3㊁03-S -N o .4㊁03-S -N o .5接结纬接结+衬纬纱04-T J -N o .1㊁04-T J -N o .2㊁04-T J -N o .3㊁04-T J -N o .4㊁04-T J -N o .504-T W -N o .1㊁04-T W -N o .2㊁04-T W -N o .3㊁04-T W -N o .4㊁04-T W -N o .504-S -N o .1㊁04-S -N o .2㊁04-S -N o .3㊁04-S -N o .4㊁04-S -N o .52.2 结构参数对三维机织复合材料的拉伸性能的影响2.2.1 经向拉伸性能三维机织复合材料的经向拉伸应力-应变曲线如图7所示㊂由图7可知:4种复合材料的拉伸应力-应变曲线表现不同,随着应变增加,浅交直联结构复合材料和层层角联锁结构复合材料的拉伸应力-应变呈线性关系,复合材料表现出线弹性的材料属性;而接结纬接结结构复合材料和接结纬接结+衬纬纱结构复合材料的拉伸应力在应变较小时呈线性增加,但是随着应变的增大,拉伸应力增长速度减缓,即拉伸模量(应力/应变)呈下降的趋势㊂分析经向拉伸离散性,发现:浅交直联结构复合材料和层层角联锁结构复合材料的经向拉伸一致性最好,表现为5个试样的拉伸曲线离散程度小㊂相反,接结纬接结结构复合材料和接结纬接结+衬纬纱结构复合76第1期武维莉等:结构参数对三维机织复合材料拉伸和剪切性能的影响图6 三维机织打纬交织示意图表5 三维机织结构的打纬宽度织物结构打纬宽度/m m浅交直联2.34层层角联锁3.26接结纬接结接6.92接结纬接结+衬纬纱2.34材料的拉伸离散程度大,即尺寸稳定性不佳,这与织物交织结构有关㊂三维机织结构中的经纱由于交织作用,纱线往往呈屈曲的状态,且纱线的屈曲程度会影响拉伸方向上的力学性能㊂纱线的屈曲程度(C )可以采用式(1)计算:图7 4种三维机织复合材料的经向拉伸应力-应变曲线C =l l 0(1)其中:l 代表织物中纱线屈曲状态下的跨距长度,l 0代表纱线从织物中提取出来完全伸直的实际长度㊂图8显示了纱线屈曲形成的纱线交织方式㊂表6汇总了4种三维复合材料的拉伸性能参数及经纱屈曲情况㊂从表6可以发现,经纱屈曲会影响复合材料的拉伸模量,接结纬接结+衬纬纱结构的纱线屈曲最高,模量最低㊂但是拉伸强度与纱线屈曲之间不具有明显的规律,这可能需要同时考虑经向上的纱线含量㊂图8 纱线屈曲示意图已有研究发现,三维机织复合材料的力学性能与纤维体积分数关系很大,经纬向上的纱线含量直接影响复合材料的拉伸性能[17]㊂为了有效评估经纬向上不同含量的三维机织复合材料的拉伸性能,对复合材料的力学性能进行归一化处理,即将不同复合材料的拉伸性能统一转换经向或纬向上V f 为86浙江理工大学学报(自然科学)2024年 第51卷表64种三维复合材料的经向拉伸性能参数结构经纱屈曲拉伸模量/G P a拉伸模量C V/%拉伸强度/M P a拉伸强度C V/%经纱V f/%浅交直联1.08322.489.02311.076.1525.53层层角联锁1.15624.983.41238.926.5826.19接结纬接结接1.13922.8520.03194.876.5526.81接结纬接结+衬纬纱1.33017.3624.48175.0121.8429.5425%的等效拉伸性能㊂断裂强度和抗拉模量的归一化计算为:σ'=σVfˑ25(2)E'=E Vfˑ25(3)其中:σ'是纤维体积分数为25%时的强度,M P a;σ为未归一化转换前的强度,M P a:E'为纤维体积分数为25%时的模量,G P a;E为未归一化转换前的模量,G P a㊂图9为经纱V f归一化处理后的4种复合材料拉伸模量㊁强度与经纱屈曲的关系㊂由图7可知,经纱屈曲程度会影响复合材料的拉伸性能,当经纱V f 统一为25%后,经纱屈曲程度越高,三维复合材料经向拉伸性能越差㊂三维机织结构复合材料的经向拉伸模量和强度整体上呈现相似的规律,大小排序为浅交直联结构复合材料㊁层层角联锁结构复合材料㊁接结纬接结结构复合材料㊁接结纬接结+衬纬纱结构复合材料㊂当经纱含量相同时,浅交直联结构复合材料的纱线屈曲最小(C=1.083),拉伸时经纱更容易发挥轴向上的力学优势,纱线强度利用率高,导致模量和强度达到最佳状态㊂接结纬接结+衬纬纱结构复合材料的经纱屈曲最大(C=1.330),受力时经纱强度利用率低,拉伸性能最差,且离散值最大㊂浅交直联结构复合材料的拉伸离散度较小,尺寸稳定性好,这与经纱交织宽度相关㊂由表6的数据可知,浅交直联结构复合材料和层层角联锁结构复合材料的交织宽度最小,分别是2.34m m和3.26m m㊂较小的纱线交织宽度导致在织造打纬时受到的打纬力更大,纱线的交织次数更多,织物结构更紧密,导致复合材料的拉伸离散性更小㊂相反,接结纬接结接结构复合材料和接结纬接结+衬纬纱结构复合材料的交织宽度较大,分别为6.92m m和8.55m m,导致织物结构不够紧密,拉伸模量和强度离散性大[18]㊂图10为V f归一化后,4种机织结构复合材料经向上的拉伸模量衰减情况,衰减速率大小排序为接结纬接结+衬纬纱相近㊁接结纬接结㊁层层角联图9归一化处理后4种机织结构复合材料的经向拉伸模量和强度(V f=25%)锁㊁浅交直联,这与经纱的屈曲状态和经纬纱的交织情况有关㊂伸直的纱线对拉伸性能的贡献大于屈曲的纱线[19],纱线屈曲明显的结构,如接结纬接结+衬纬纱结构复合材料和接结纬接结结构复合材料,无法充分发挥纤维的力学优势,受拉时屈曲的纱线有伸直的趋势;当拉伸载荷增加,经纱试图伸直造成树脂剪切破坏[20],导致复合材料的失效,从而模量发生明显的衰减㊂浅交直联结构复合材料由于经纱屈曲小,拉伸时纱线伸直变形小,且经纬纱交织结构紧密,失效前拉伸模量一直保持稳定不变㊂图104种机织结构复合材料经向拉伸模量随拉伸应变的变化曲线(V f=25%) 2.2.2纬向拉伸性能三维机织复合材料的纬向拉伸应力-应变曲线如图11所示㊂与经向拉伸曲线有所不同,4种复合材料纬向的拉伸应力-应变曲线均呈线性特征,表现出了线弹性的属性㊂由于织造时的打纬运动,纬纱在织物中几乎处于伸直状态[19],在纬向拉伸时,复96第1期武维莉等:结构参数对三维机织复合材料拉伸和剪切性能的影响合材料主要的变形来自于纬纱的拉伸和伸长,因此拉伸曲线呈线性特征㊂相比经向拉伸行为,4种结构复合材料的5个试样的纬向拉伸离散程度较小,拉伸曲线一致性好㊂其中,浅交直联结构复合材料的纬向试样拉伸离散性最小,接结纬接结+衬纬纱结构复合材料的离散性最大㊂与经向拉伸行为相似,这主要与织物结构有关㊂图11 4种机织结构复合材料的纬向拉伸应力-应变曲线 表7汇总了复合材料纬向上的拉伸性能,可以发现纬纱的屈曲程度远远小于经纱,与经纱的屈曲规律相同,纬纱的屈曲从小到大的顺序为:浅交直联㊁层层角联锁㊁接结纬接结接㊁接结纬接结+衬纬纱㊂拉伸性能同时受到纬纱含量的影响,因此对纬纱含量进行归一化后,从而对比纬向上的拉伸性能㊂表7 4种三维复合材料的纬向拉伸性能参数织物结构纬纱屈曲拉伸模量/G P a拉伸模量C V /%拉伸强度/M P a 拉伸强度C V /%纬纱V f/%浅交直联1.00430.004.07489.772.9116.33层层角联锁1.00543.804.48629.772.2621.82接结纬接结接1.00927.147.83411.6215.8820.31接结纬接结+衬纬纱1.01247.228.59726.672.5421.58图12为V f 统一为25%后的纬向拉伸模量㊁强度㊂由图12可知:当V f 相同时,4种结构复合材料的纬向上的拉伸模量㊁强度呈现相似的规律,从大到小的顺序为:接结纬接结+衬纬纱结构复合材料㊁层层角联锁结构复合材料㊁浅交直联结构复合材料㊁接结纬接结结构复合材料㊂与经向拉伸相同,浅交直联结构复合材料和层层角联锁复合材料的纬向拉伸性能依然优于接结纬接结结构复合材料,表明这两种材料具有结构上的优势㊂浅交直联结构复合材料和层层角联锁结构复合材料的纬纱屈曲小,且纱线交织宽度小导致交织次数多,织物结构紧密,对纬纱的束缚张力大,纬向拉伸离散小㊂而接结纬接结结构复合材料和接结纬接结+衬纬纱结构复合材料的经纬纱交织点少,纱线之间束缚少㊁自由度大,织物结构疏松,导致纬向上的拉伸性能离散性大㊂2.2.3 经向和纬向拉伸性能对比图13对比了4种复合材料在经㊁纬方向上的拉伸性能㊂由图13可知,V f 归一化后,经向上的拉伸模量和强度明显低于纬向,这是由于纬纱伸直程度高于经纱,受拉时纬纱能承受较大的载荷㊂经纱由于屈曲大,不利于发挥碳纤维的力学优势,导致经向上的拉伸模量较低㊂当拉伸载荷增加时,经纱有从7浙江理工大学学报(自然科学)2024年 第51卷图12归一化处理后4种结构复合材料纬向拉伸模量和强度(V f=25%)屈曲到伸直的趋势,但是此过程会导致纱线周围的树脂受到挤压,造成剪切破坏,从而引起整个试样迅速失效,因此经向上的拉伸强度均低于纬向㊂2.3结构参数对三维机织复合材料剪切性能的影响本文对4种三维机织复合材料的剪切性能进行分析,剪切应力-应变曲线如图14所示㊂由图14可知,4种复合材料的剪切曲线相似,初始受剪时,复合材料的应力-应变曲线呈线弹性属性,剪切应力随着应变的增加呈线性增加;随着载荷的增加,应力-图134种机织结构复合材料经㊁纬向的拉伸性能对比(V f=25%)图144种机织结构复合材料剪切应力-应变曲线17第1期武维莉等:结构参数对三维机织复合材料拉伸和剪切性能的影响应变曲线进入非线性阶段,剪切应力继续增大但增长速度下降,即剪切刚度下降,直至强度达到最大后试样失效㊂复合材料施加剪切载荷时,当剪切力较小时,材料中的纱线和树脂同时受力,由于树脂模量远低于碳纤维,树脂首先发生变形㊂纱线受剪切力后由屈曲状态伸直,交织处的经纬纱逐渐锁紧,当载荷持续增大,锁结处的纱线摩擦力增大直至无法承受载荷,此时交织的纱线发生滑移㊁抽拔㊁断裂㊂树脂的断裂伸长率大,碳纤维断裂前树脂还未发生破坏,但是树脂强度远低于碳纤维,碳纤维断裂后树脂迅速破坏,最后整个复合材料试样失效[21]㊂图15显示了4种复合材料的剪切性能及离散情况㊂由图15可知,V f 相同时,浅交直联结构复合材料的剪切模量最大,接结纬接结结构复合材料的剪切模量最小,而剪切强度几乎呈相反的规律㊂浅交直联结构复合材料的结构紧密,受剪切时复合材料不易发生变形,剪切模量最大,但这导致在纱线交织处容易形成应力集中,试样失效早[22],剪切强度小㊂接结纬接结结构复合材料由于经纬纱的交织少㊁结构疏松,受剪切时结构容易发生变形,剪切模量小,但是疏松的结构不易形成应力集中,剪切失效发生晚,因此剪切强度最大㊂图15 归一化处理后4种复合材料剪切模量和强度(V f =25%)与拉伸性能相似,接结纬接结结构复合材料和接结纬接结+衬纬纱结构复合材料的剪切离散值最大,尺寸稳定性最差,而浅交直联结构复合材料和层层角联锁结构复合材料的剪切离散性最小,这与织物结构中是纱线交织情况有关㊂接结纬接结结构复合材料和接结纬接结+衬纬纱结构复合材料中纱线交织宽度大,交织点少,纱线自由度大,受剪切时材料的失效位置具有较大的不确定性,离散度大;而浅交直联结构复合材料和层层角联锁复合材料的结构交织较为紧密㊁稳定,受剪切时离散性最小㊂3 结 论为了研究三维机织结构参数与复合材料力学性能之间的关系,本文设计制备了4种不同结构的三维机织复合材料,测试分析了复合材料的拉伸性能(经向和纬向)和剪切性能,所得主要结论如下:a)纤维体积分数㊁纱线屈曲和纱线交织程度决定了三维复合材料的拉伸和剪切性能㊂V f 相同时,纱线屈曲导致拉伸性能下降,而交织结构紧密会改善拉伸性能和离散性㊂b )经向拉伸时,4种结构复合材料的拉伸响应和曲线离散性不同,但拉伸模量和强度呈现相同的规律,大小排序为浅交直联结构复合材料㊁层层角联锁结构复合材料㊁接结纬接结结构复合材料㊁接结纬接结+衬纬纱结构复合材料㊂纬向拉伸时,4种结构复合材料的拉伸应力-应变曲线呈线弹性,且离散值小,这与纬纱屈曲小有关,同时纬向上的拉伸性能远远优于经向㊂不管是经向还是纬向上,浅交直联结构复合材料和层层角联锁结构复合材料的拉伸性能和离散性较小,而接结纬接结结构复合材料的拉伸性能最差,说明此结构不具有优势㊂c )4种复合材料的剪切应力-应变曲线呈非线性的特征㊂织物中经纬纱的交织结构决定了剪切性能及离散性,其中浅交直联复合材料的结构紧密,剪切模量最大,接结纬接结复合材料的结构疏松,剪切模量最小,而剪切强度几乎呈相反的规律㊂此研究明确了结构参数对三维机织复合材料的拉伸性能和剪切性能的影响,对三维织物的结构设计和力学性能优化有一定的指导作用,为将来三维机织复合材料的工程化应用提供借鉴和参考㊂参考文献:[1]杨彩云,李嘉禄,陈利,等.树脂基三维机织复合材料结构与力学性能的关系研究[J ].航空材料学报,2006,26(5):51-55.[2]L i M R ,W a n g P,B o u s s u F ,e t a l .A r e v i e w o n t h e m e c h a n i c a l p e r f o r m a n c e o f t h r e e -d i m e n s i o n a l w a r pi n t e r l o c k w o v e n f a b r i c s a s r e i n f o r c e m e n t i n c o m po s i t e s [J ].J o u r n a l o f I n d u s t r i a l T e x t i l e s ,2022,51(7):1009-1058.[3]D a h a l e M ,N e a l e G ,L u pi c i n i R ,e t a l .E f f e c t o f w e a v e p a r a m e t e r s o n t h e m e c h a n i c a l p r o pe r t i e s of 3D w o v e ng l a s s c o m p o s i t e s [J ].C o m po s i t e S t r u c t u r e s ,2019,223:27浙江理工大学学报(自然科学)2024年 第51卷。
织物力学性能分析与优化设计

织物力学性能分析与优化设计织物在我们的生活中无处不在,是人类文明的重要组成部分。
无论是建筑、服装、汽车、航空等领域都离不开织物。
织物的性能对于产品的质量和使用寿命至关重要。
因此,对织物力学性能的分析和优化设计具有非常重要的意义。
一、织物的力学性能织物的强度、耐磨、抗拉、耐撕裂等性能直接关系到产品的使用寿命和质量,因此,对于织物的力学性能的研究是非常必要的。
在织物的应用过程中,织物的负载状态及荷载可归纳如下:1. 单向拉伸2. 单向压缩3. 三维应力状态(复合材料)4. 屈曲5. 剪切6. 双向拉伸7. 扭曲针对这些负载状态和荷载,需进行相应的织物力学性能分析。
二、织物力学性能测试为了确定织物的性能,需要对其进行一系列的力学性能测试。
根据不同的负载状态,常见的织物力学性能测试如下:1. 水平拉伸/压缩测试2. 垂直拉伸/压缩测试3. 悬挂杆测试4. 色牢度测试5. 弯曲测试6. 撕裂测试7. 穿孔测试这些测试为织物力学性能提供了基础的数据和结论,为织物的优化设计奠定了基础。
三、织物的优化设计织物的优化设计应从材料、结构和技术三个方面入手,以提高织物的力学性能。
具体包括以下几个方面:1. 材料方面:选择合适的原材料,如纤维的种类和长度、纤维的密度等。
2. 结构方面:优化织物的结构设计,如织物的厚度、纱线的织法等。
3. 技术方面:根据织物的应用场景,选择合适的加工工艺,如印染、涂层、复合等。
织物优化设计的目的是提高其力学性能,同时降低成本和提高生产效率。
四、结语织物力学性能分析与优化设计是一项复杂而又必要的工作。
它为我们提供了对织物无限延伸的可能性,同时也在我们的日常生活中随处可见。
在此,希望能够有更多的专业人士致力于织物力学性能分析与优化设计,推动产品的不断创新和技术的不断进步,为人类社会的发展做出更大的贡献。
织物的力学性能测试

织物的力学性能测试(拉伸性能、撕裂性能、顶破性能、耐磨性能)织物的力学性能是指织物在各种机械外力作用下所呈现的性能。
它是织物的基本性能。
织物抵抗因外力引起损坏的性质称为织物的耐久性或坚牢度,大多是通过测试织物的拉伸断裂、顶裂、撕裂以及耐磨性等来反映这一性能的。
织物在小负荷作用下呈现的性质近年来备受人们的关注,如织物手感、视觉风格、起毛起球、勾丝等。
这里主要介绍织物的坚牢度试验。
织物的拉伸断裂试验织物拉伸断裂试验目前主要采用单向(受力)拉伸,即测试织物试条的经(纵) 向强力、纬(横)向强力,或与经纬向呈某一角度的强力。
它适用于机械性能具有各向异性、拉伸变形能力较小的制品。
对于容易产生变形的针织物(特别是易卷边的单面针织物)、编织物以及非织造布一般采用顶破试验为宜。
一、试验原理将一定尺寸的试样,按等速伸长方式拉伸至断裂,测其承受的最大力——断裂强力及产生对应的长度增量——断裂伸长。
必要时,还可画出织物的强力——伸长曲线,算出多种拉伸指标。
二、试验参数选择1、试样形状根据织物的品种不同,试样的形状有以下3种形式,见图。
图织物拉伸断裂试验的试条形状和夹持方法(1)拆边纱法条样:用于一般机织物试样。
裁剪的试样宽度应比规定的有效试验宽度宽5mm或lOmm(按织物紧密程度而定),然后通过拆边纱法从试样宽度两侧拆去数量大致相等的纱线,直至试样宽度符合规定要求,以确保试验过程中纱线不会从毛边中脱出。
(2)剪切法条样:适用于针织物、涂层织物、非织造布和不易拆边纱的机织物试样。
(3)抓样法条样:试样宽度大于夹持宽度。
适用于机织物,特别是经过重浆整理的,不易抽边纱的和高密度的织物。
比较3种形态试样的试验结果,拆边法的强力不匀较小,而强力值略低于抓样法。
2、试验参数织物拉伸断裂的试验参数见表。
注:拆边纱法条样应先裁剪成6 mm宽或7 mm宽(疏松织物),然后两边抽去等量边纱,使试样的有效宽度为5 mm。
为便于施加张力,试样长度宜放长30~50 mm。
纺织面料耐用性检测—织物撕裂、顶裂和勾丝性能检测

拉伸速度:100㎜/min等。
01
打印试验结果。
05
02
夹装试样。
03
开启 “拉伸”试样至破裂。如果 试样不是顶破,而是滑移,需删 除本次实验,重新取样。
04
复位后,重复上述操作,至
完成规定的试验次数。
4、影响织物顶破性质的因素 织物拉伸断裂强力对顶破强力有直接影响,通常,随着织物拉伸强力的增加,顶破
顶破是织物破坏的一种形式。将一定面积的织物四周固定,从织物的一面给予垂直的作用力 使其破坏,称为顶破,也称为顶裂。顶破与服装在人体肘部、膝部的受力,手套、袜子、鞋面在 手指或脚指处的受力相似。顶破试验可提供织物多向强伸特征的信息,特别适用于针织物、三向 织物、非织造布及降落伞用布等。
由于机织物和针织物在强度和变形方面是一种各向异性的物体,在顶力作用下各向伸长, 沿经、纬(或直、横)两方向张力复合的剪应力,首先在变形最大、强度最弱的一点上使纱线断 裂,接着沿经向或纬向(直向或横向)撕裂,因而裂口一般呈直角形或直线形。
由同种纤维组成经纬纱的织物,一般表现为: ①织缩率大而经纬向织缩率接近,则织物的顶破强度较高。这是由于经、纬纱对顶裂强度同时发 挥作用的缘故,其裂口形状常为三角形。 ②若经纬向纱线的变形能力不同或织缩率相差大时,则变形能力小的或织缩率低时一个系统纱线 在顶裂过程中首先到达断裂伸长而告破裂,裂口常为一直线,这是由于经纬向纱线没有同时发挥 最大作用,而顶裂强度较低; ③若经纬向纱线相同,经纬向密度差异大时,裂口也呈一直线。
P
环形夹具
上支架
织物 钢球
顶 杆
下支架
P
v
(a) 弹子式
(b) 气压式
织物中纤维和纱线由于勾挂而被拉出于织物表面的程度称为勾丝性。织物的勾丝 主要发生在长丝织物和针织物中。它不仅使织物外观明显变差,而且影响织物耐用性 。随着长丝针织物尤其是丝袜大量进入服装领域,这一缺点显得十分突出。
纺织材料的力学性能与应用研究

纺织材料的力学性能与应用研究在我们的日常生活中,纺织材料无处不在,从衣物到家居用品,从工业用布到医疗领域的特殊材料,纺织材料的应用极其广泛。
而纺织材料的力学性能,作为决定其使用性能和应用范围的关键因素,一直是纺织科学领域研究的重要课题。
纺织材料的力学性能主要包括拉伸性能、弯曲性能、压缩性能、剪切性能、摩擦性能和疲劳性能等。
这些性能相互关联又相互影响,共同决定了纺织材料在不同应用场景中的表现。
拉伸性能是纺织材料最基本的力学性能之一。
当我们拉伸一块布料时,它所能承受的最大拉力以及在拉力作用下的伸长程度,就是拉伸性能的主要指标。
具有良好拉伸性能的纺织材料,如高强度的聚酯纤维,常用于制作运动服装和户外用品,因为这些产品需要能够承受较大的拉伸力而不破裂或变形。
弯曲性能则反映了纺织材料在弯曲过程中的抵抗能力。
想象一下我们折叠一块布料,它的柔软度和恢复原状的能力就与弯曲性能有关。
柔软的丝绸具有较好的弯曲性能,常用于制作高档的服装,给人以舒适和优雅的感觉。
压缩性能在一些特定的应用中至关重要。
例如,在床垫和坐垫的制作中,纺织材料需要具有一定的压缩回弹性,以提供舒适的支撑和使用体验。
具有良好压缩性能的海绵状纺织材料能够有效地分散压力,减少人体的疲劳感。
剪切性能对于一些特殊的纺织制品,如降落伞布和滑翔伞布,具有重要意义。
这些材料在受到气流剪切力时,必须能够保持结构的稳定性和强度,以确保使用者的安全。
摩擦性能影响着纺织材料的手感和耐用性。
我们在穿着衣物时,衣物与皮肤之间的摩擦力会影响舒适度;而在工业应用中,如输送带和传动带,良好的摩擦性能可以确保传动的准确性和稳定性。
疲劳性能则反映了纺织材料在反复受力作用下的耐久性。
比如,袜子在经常受到脚趾和脚跟的摩擦和拉伸后容易破损,这就与纺织材料的疲劳性能有关。
纺织材料的力学性能不仅取决于其组成纤维的性质,还受到纤维的排列方式、纺织工艺和后整理工艺等因素的影响。
在纤维层面,纤维的长度、细度、强度和伸长率等都会对纺织材料的力学性能产生影响。
平纹SiC纤维织物剪切性能

第42卷第3期2023年3月硅㊀酸㊀盐㊀通㊀报BULLETINOFTHECHINESECERAMICSOCIETYVol.42㊀No.3March,2023平纹SiC 纤维织物剪切性能侯耀晟树1,郭纬愉1,杜永龙1,张㊀毅2,张大旭1(1.上海交通大学船舶海洋与建筑工程学院,上海㊀200240;2.西北工业大学超高温结构复合材料重点实验室,西安㊀710072)摘要:SiC 纤维织物是耐高温陶瓷基复合材料的一种重要增韧材料㊂本文以平纹SiC 纤维织物为研究对象,开展了单轴拉伸试验和ʃ45ʎ偏轴拉伸试验,得到了其拉伸和剪切性能;进行了纱线抽出试验,得到其经纬纱线间的摩擦系数;通过X 射线CT 检测,得到其细观结构;利用最小二乘法拟合出经纬纱线的横截面和卷曲形状曲线;通过建立纱线的简支梁模型,计算出剪切变形中经纬纱线摩擦力矩,预测了平纹SiC 纤维织物的剪切应力-应变曲线㊂剪切变形过程分为纯剪和纱线挤压阶段,两个阶段的交界点为织物的锁紧角㊂研究结果对设计和制备平纹SiC 纤维织物预制体具有参考价值㊂关键词:拉伸试验;剪切性能;SiC 纤维;锁紧角;平纹织物;纱线抽出中图分类号:TB332㊀㊀文献标志码:A㊀㊀文章编号:1001-1625(2023)03-1063-11Shear Properties of Plain Weave SiC Fiber FabricsHOU Yaoshengshu 1,GUO Weiyu 1,DU Yonglong 1,ZHANG Yi 2,ZHANG Daxu 1(1.School of Naval Architecture,Ocean and Civil Engineering,Shanghai Jiao Tong University,Shanghai 200240,China;2.Science and Technology on Thermostructural Composite Materials Laborary,Northwestern Polytechnical University,Xi an 710072,China)Abstract :SiC fiber fabric is an important toughening material for high temperature resistant ceramic matrix composites.In this paper,plain weave SiC fiber fabrics were taken as the research object.The uniaxial tensile test and ʃ45ʎoff-axis tensile test were carried out to obtain tensile and shear properties.Yarn extraction test was performed to obtain the friction coefficient between the warp direction and weft direction yarns.X-ray computed tomography (CT)scan was carried out to obtain miscrostructure,and the cross-section and crimp shape of the warp direction and weft direction yarns were fitted by the least squares method.The simply beam model of the yarn was established to calculate the friction moment of the yarn under shearing process,and the shear stress-strain curve of plain weave SiC fiber fabrics can be predicted.The shearing process of plain weave SiC fiber fabrics is divided into two stages,the pure shearing stage and the yarn extrusion stage,andthe junction point of the two stages can be defined as the locking angle of plain weave SiC fiber fabrics.The results have reference value for the subsequent design and preparation of plain weave SiC fiber fabric preforms.Key words :tensile test;shear property;SiC fiber;locking angle;plain weave;yarn extraction收稿日期:2022-11-21;修订日期:2023-01-05基金项目:国家自然科学基金(12072192,U1831105,51802263)作者简介:侯耀晟树(1994 ),男,硕士研究生㊂主要从事纤维织物力学行为的研究㊂E-mail:372551306@ 通信作者:张大旭,博士,教授㊂E-mail:daxu.zhang@0㊀引㊀言近年来,复合材料织物由于其力学性能优良,结构轻巧,被广泛运用于航空航天㊁土木能源㊁交通运输等领域㊂陶瓷基复合材料(ceramic matrix composites,CMCs)因其优越的耐高温性能,成为航空航天发动机㊁空天飞行器㊁核反应堆等装备中高温部件的理想选材㊂SiC 纤维具有优异的抗高温氧化能力,一般先将其纺织成SiC 纤维织物,然后制成预制体用于CMCs 的制备,能提高CMCs 的韧性和强度㊂SiC 纤维织物的剪切性能是SiC 预制体设计和制作的基本技术参数,也影响着CMCs 的制备质量㊂织物在剪切作用下,易发生平面外的变形,且由于经纱㊁纬纱的纺织方法不同,也会对变形程度产生影响,继而引起剪切变形㊁膜面褶皱甚至剪切破坏等现象㊂关于织物剪切性能,邓金海等[1]研究了石英纤维织物在剪切的作用下1064㊀陶㊀瓷硅酸盐通报㊀㊀㊀㊀㊀㊀第42卷发生的变形情况;林国昌等[2]研究了织物剪切破坏与锁紧角的关系;尹红灵[3]㊁张必超[4]㊁黄小双[5]和胡虹玲[6]提出了几种织物材料成形过程中的本构关系;Labanieh 等[7]对织物剪切过程中纱线的变形情况进行了分类㊂要评价织物的剪切性能,需要得到织物的剪切模量和细观尺寸㊂现阶段国内外测试织物剪切模量试验方法主要有图框法[8]㊁双轴剪切试验[9-10]㊁偏轴拉伸试验㊂陈务军等[11]和高成军等[12]通过双轴剪切试验机对织物膜材的剪切性能进行了研究;杜永龙等[13]通过X 射线CT(X-ray computed tomography)扫描对SiC 复合材料进行了原位拉伸损伤演化分析㊂虽然国内外开展了大量纤维织物的剪切性能研究,但关于SiC 纤维织物的剪切性能鲜有报道,其剪切性能技术参数有待研究㊂本文利用剪切性能试验㊁高分辨率X 射线CT 无损检测㊁统计分析㊁解析模型等方法研究了SiC 纤维织物的剪切性能和变形机理㊂首先使用电子万能试验机对SiC 纤维织物进行偏轴拉伸试验;再借助X 射线-CT 扫描和图像重构技术[14]得到其单胞模尺寸,通过最小二乘法[15]拟合出纱线的形状特征[16];对SiC 纤维织物成型过程中不同的剪切变形阶段进行分析,将试验结果与建模结果相比较,揭示SiC 纤维织物的剪切变形机理,并对其剪切性能进行预测㊂1㊀实㊀验图1㊀拉伸试验总体布局Fig.1㊀Overall layout of tensile testing本文需进行的试验包括单轴拉伸试验㊁偏轴拉伸试验和纱线抽出试验,加载试验机为UTM4000系列双柱落地式电子万能试验机,拉伸试验总体布局如图1所示,使用10kN 传感器测量拉力变化,使用大变形计测量试件拉伸方向的变形㊂在单轴拉伸试件表面制作了散斑,采用数字图像相关(digital image correlation,DIC)技术识别散斑变形,得到加载过程中试件的应变云图,用以计算断裂伸长率与工程应变㊂对SiC 纤维织物在室温空气环境下进行单轴拉伸和偏轴拉伸试验,探究SiC 纤维基本力学性能㊂试件原材料采用国产Ⅲ代SiC 纤维,型号为Cansas-3303,线密度为189tex,平均直径为12.5μm㊂SiC 纤维平纹织物幅宽为800mm,每根纱线界面的纤维根数为0.5K(1K =1000根)㊂参考织物拉伸试验标准[17-18],按照单轴和偏轴角度要求裁剪出相应的试件,试件具体尺寸如图2所示㊂对于单轴拉伸试验,包含经向拉伸与纬向拉伸两组,每组6个试件,分别编号为ATJ-1~ATJ-6,ATW-1~ATW-6(A 表示单轴拉伸,T 表示试验,J 表示经向,W 表示纬向),得到经纬向断裂强力与断裂伸长率;对于偏轴拉伸试验,设置纤维束与拉伸方向呈ʃ45ʎ,4个试件,编号为BT-1~BT-4(B 表示偏轴拉伸)㊂1.1㊀单轴拉伸试验1.1.1㊀拉伸强度计算采用式(1)计算拉伸强度,结果保留三位有效数字㊂如果计算拉伸模量,则采用式(2)确定所要求的每一个数据点的拉伸应力㊂F u =p max l (1)σi =p i l(2)式中:F u 为拉伸强度,N /mm 2;p max 为破坏前的最大载荷,N;σi 为第i 个数据点的拉伸应力,N /mm 2;p i 为第i 个数据点的力,N;l 为试件原有效宽度,mm㊂1.1.2㊀断裂伸长率计算采用式(3)计算断裂伸长率㊂ε=Δllˑ100%(3)第3期侯耀晟树等:平纹SiC纤维织物剪切性能1065 式中:ε为断裂伸长率,%;Δl为试样断裂失效时的断裂伸长,mm。
精纺毛型织物剪切性能的实验研究

0. 67 0. 48 1. 14 0. 72 0. 50 1. 10
0. 66 0. 35 0. 95 0. 57 0. 30 0. 83
0. 39 0. 13 0. 45 0. 43 0. 26 0. 60
0. 33 0. 30 0. 62 0. 31 0. 98 0. 98
0. 52 0. 77 1. 23 0. 50 0. 63 1. 00
2 结果讨论
211 剪切刚度
用织物 (计 33 种) 得到织物剪切刚度与织物具
体参数之间的线性回归方程 (1) 和 (2) 。
G1 = - 0. 518 + 1. 634 ×0101 ×纬向紧度 - 01392
×平均浮长 + 1. 411 ×0101 ×经向紧度
(1)
相关系数 : R = 0. 806
经纱细
度 (tex) 25. 6 ×2 12. 5 ×2 22. 7 ×2 32. 3 ×2 21. 7 ×2 12. 8 ×2 18. 5 ×2 23. 3 ×2 19. 2 ×2 13. 9 ×2
13. 2 38. 5 ×2 27. 8 ×2
25 ×2 37 ×2 12. 8 ×2 12. 8 ×2 11. 2 ×2 17. 2 ×2 13 ×2
0பைடு நூலகம் 62 0. 39 1. 10 0. 53 0. 40 0. 83
0. 62 0. 43 0. 89 0. 56 0. 43 0. 87
0. 51 0. 40 0. 90 0. 55 0. 61 1. 09
0. 87 0. 22 1. 18 0. 84 0. 33 1. 22
0. 65 0. 48 1. 10 0. 63 0. 48 1. 10
三维机织物的分类、性能及织造

三维机织物的分类、性能及织造胡慧娜;裴鹏英;胡雨;龚小舟【摘要】文章主要从织物组织结构、织物的结构特征、织物的截面形状等3方面对三维机织物进行分类,并综述了目前有关三维机织物在组织结构、织造工艺以及织机设备改进等3方面的研究进展,旨在为三维机织物的研究发展提供参考.【期刊名称】《纺织导报》【年(卷),期】2017(000)012【总页数】6页(P25-30)【关键词】三维机织物;织物分类;组织结构;织造工艺;织机设备改进【作者】胡慧娜;裴鹏英;胡雨;龚小舟【作者单位】武汉纺织大学纺织科学与工程学院;武汉纺织大学纺织科学与工程学院;武汉纺织大学纺织科学与工程学院;武汉纺织大学纺织科学与工程学院【正文语种】中文【中图分类】TS105随着材料技术的飞速发展,人们对于复合材料性能各个方面的要求愈来愈高,现代纺织技术与树脂工业的结合催生了纺织复合材料,而三维纺织技术的发展,更为制备具有优良整体性和力学结构合理性的高性能复合材料提供了有力的保证。
以三维织物为增强体的纺织复合材料,具有比强度高、比刚度高、可设计性好、耐疲劳性能好、耐化学腐蚀性能好、生产成本低等优势,同时克服了传统二维平面织物层状复合材料存在抗冲击性能差、层间强度低的缺点,因而广泛应用于航空航天、船舶汽车、建筑仓储等诸多领域。
根据织造成形工艺的不同,三维织物又可分为三维机织物、三维针织物、三维编织物,其中三维针织物主要是经编织物为主,但受于生产设备的限制只能加工轻薄型织物;三维编织物生产效率较低,无法适应大规模生产;而三维机织物,可以利用传统织机或对传统织机加以改进进行大规模生产,且生产效率最高、制件尺寸最大,因而在所有三维纺织品中的应用有望最为广泛。
根据纱线交织规律的不同,二维机织物基础组织可分为平纹、斜纹和缎纹,由这 3 种基础组织变化组合,又可衍生出多种多样的复杂组织。
同理,三维机织物的基础组织包括正交、角联锁和多层接结等 3 种,由这 3种组织变化组合,又可衍生出各种复杂组织结构的三维机织物。
第2节机织物的撕裂撕破性能
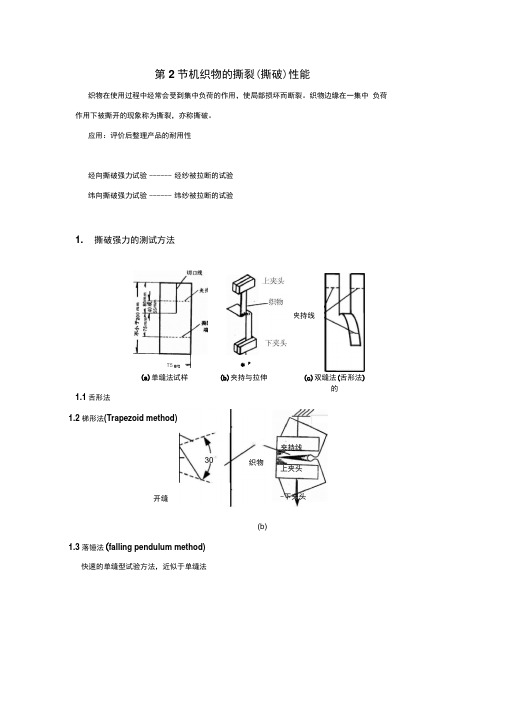
(c)双缝法(舌形法)的织物开缝第2节机织物的撕裂(撕破)性能织物在使用过程中经常会受到集中负荷的作用,使局部损坏而断裂。
织物边缘在一集中 负荷作用下被撕开的现象称为撕裂,亦称撕破。
应用:评价后整理产品的耐用性经向撕破强力试验 ------ 经纱被拉断的试验 纬向撕破强力试验 ------ 纬纱被拉断的试验1. 撕破强力的测试方法1.1舌形法1.2 梯形法(Trapezoid method)夹持线上夹头-下夹头(b)1.3 落锤法(falling pendulum method)快速的单缝型试验方法,近似于单缝法T5曲啦(a)单缝法试样* P (b)夹持与拉伸线 持 夹也称为冲击撕裂强力2. 撕裂破坏机理显然有:△l i >拉断纱线开裂将拉断将拉断-纱线A l i纱线i第i +1根断裂纱线A l i+1(b)梯形法(a)落锤法撕破仪1.4 翼形法(Wing tear method)从单缝法发展而来(1)撕裂破坏主要是靠撕裂三角形区域的局部应力场作用(2)纱线逐根断裂单缝法一一剪切作用(b)落锤撕破试样(b)夹持方法P梯形法一一拉伸作用2.1单缝法破坏机理双缝法/落锤法/翼形法机理相似被拉伸纱线屈曲消失T伸直,并滑动(在非拉伸纱线上)形成受力三角形T经纬交织点处切向阻力使纵向纱线靠拢受力三角形增大T非拉伸纱线张力迅速增大,伸长变形急剧增加受力情况:三角形底边的第1根非拉伸纱线变形、张力最大,其余纱线承受的张力随离第1根纱线距离的增大而逐渐减少断裂:当撕拉到第1根非拉伸纱线达到断裂伸长率时,发生断裂,出现第一个负荷峰值非拉伸纱线发生逐根断裂使织物撕破单缝法撕破时,断裂的纱线是非受拉伸系统的纱线即沿经向拉伸,纬纱断裂沿纬向拉伸,经纱断裂、/、一―、、> * *注意!试样长边平行于经向的撕裂称为纬向撕破”△L (cm)△L (cm)2.2梯形法撕裂机理同样存在受力三角形受力三角形形成:被拉伸纱线的伸直和变形受力情况:紧边的纱线首先受拉伸直,第1根纱线变形量最大,其余纱线承受的张力随离第1根纱线距离的增大而逐渐减少,直到受力三角形顶点处的纱线,张力为零断裂:第1根纱线达到断裂伸长率时,发生断裂,出现第一个负荷峰值纱线发生逐根断裂,受力三角形的顶点不断向前扩展,最后使织物撕破梯形法撕破时,断裂纱线是受拉伸系统的纱线即沿经向拉伸,经纱断裂沿纬向拉伸,纬纱断裂2.3织物撕裂破坏过程织物撕破过程是纱线的逐根断裂,即受力三角形中纱线的受力是不均匀的,受力三角形底边的纱线受力最大,受力三角形顶点处的纱线尚未受力织物撕破强力总是小于其拉伸断裂强力撕裂强力大小与撕破过程中的受力三角形的大小成正相关3.1水平倾角(梯形法) 内在因素=> 受力的纱线根3. 影响机织物撕裂强力的因素――纱线强度和有效承担外力的纱线根数 (1) 受力三角形大小 纱线的断裂伸长率 织物织缩 (2) 纱线根数纱线的摩擦系数(舌形法) 机织物的组织类型(舌形法) 织物密度织物后整理(2) 织物组织经纬纱的交织点数 一一纱线的相对移动程度 平纹最小,方平最大,缎纹和斜纹介于两者之间 (3)织物织缩正效应:织缩T 织物伸长T 受力三角形T 撕裂强力增加(主导因素)(1)纱线性质负效应:织缩T纱线受弯曲程度T纱线间相互挤压和摩擦T受力三角形(4)织物经纬密梯形法:密度T承力纱线根数舌形法:A.密度f T承力纱线根数fB.密度f T纱线间摩擦阻力f T受力三角形J纱线相对移动程度(如纱布)经纬密都较大,受力三角形变小日常应用出现横向断裂经密比纬密大时,梯形法——经向撕破强力大于纬向(如府绸)现象(5)织物后整理影响纱线的滑动能力抗皱整理(树脂整理):滑动能力J柔软整理:滑动能力f3.2 试验条件(1)试样尺寸A. 梯形法第1根纱线长度f,最大撕裂强度f受力纱线的根数与试样条和夹头水平线夹角有关我国规定15°B. 单缝法试样宽度小于撕裂过程中两组纱线相互滑动影响的长度,强力降低(2)撕裂速度纤维集合体具有粘弹性能纱线间的滑移与作用时间有关梯形法:速度f,撕裂强力f (拉伸)单缝法:速度J,撕裂强力J (滑移)(3)温湿度影响纱线的断裂强度和断裂伸长率、纱线的表面摩擦条件4. 织物的纰裂织物的纰裂是指织物在使用过程中受到外力作用后所产生的纱线横向滑移经纬纱交织不够牢固,在很小外力作用下被扒出裂缝的一种损坏现象如衣裤接缝、多次受摩擦的外拱处4.1织物纰裂产生的原因纤维:摩擦系数小、伸直度高、硬度和抗弯刚度大织物:经纬密度小、结构松、交织点小纱线:结构紧、表面光滑、捻度大织造:上机张力丝绸织物、长丝纤维机织物和低密度机织物纰裂测试指标:织物中纱线的滑移阻力和滑移量方法:缝合法、模拟缝合法和摩擦法4.2防止织物纰裂办法纤维:提高纤维的表面粗糙度和摩擦系数,增加纤维的卷曲,以改善纤维间的相互作用及机械锁结。
- 1、下载文档前请自行甄别文档内容的完整性,平台不提供额外的编辑、内容补充、找答案等附加服务。
- 2、"仅部分预览"的文档,不可在线预览部分如存在完整性等问题,可反馈申请退款(可完整预览的文档不适用该条件!)。
- 3、如文档侵犯您的权益,请联系客服反馈,我们会尽快为您处理(人工客服工作时间:9:00-18:30)。
机织物在各个方向上的剪切性能W.M.Lo 等著 纪 峰 译郭永平 校 剪切性能是影响机织物外观及力学行为的重要特性之一。
本文在K ilby 等人工作的基础上建立模型,预测机织物在各个方向上的剪切刚度。
基于现有文献,我们发现剪切刚度(G )、015°及5°角的剪切滞后有明显的线性关系。
因此通过比较理论结果与实验数据,并将它们在极坐标图上展现出来,证明该模型亦可用于预测大范围类型机织物的剪切滞后。
实验结果表明,剪切刚度与剪切滞后的这种线性关系不仅存在于经、纬两个主方向上,也存在于与经纬向成各种夹角的方向上。
在实验中还发现,机织物剪切刚度的最大值出现在与经纬向成±45°夹角的方向上。
在实际应用中,纺织面料要经受大量的复杂变形,因此织物的剪切性能在许多实际应用中显得非常重要。
为探索机织物剪切行为的力学本质,Dreby 等人先后设计开发了测试机织物剪切性能的方法和仪器。
后来,Cusick 等人通过建立数学模型,采用一种量化的方法来描述织物的剪切性能。
他们在文章中阐明,剪切过程中的滞后现象是由织物内部经纬纱交织点处纱线的相互扭转产生的摩擦约束决定的。
而且,现有的文献都证明了剪切是影响织物的悬垂性、柔韧性及手感的重要性能之一。
机织物的剪切性能不仅在经纬方向上,而且在其他各个方向上都影响着织物的弯曲和拉伸性能。
机织物在经纬方向的剪切行为一直受到广泛关注,因其显著影响着织物的其他力学行为。
但织物在与经纬向成各种夹角方向上的剪切性能却很少被注意,因为它们涉及复杂的力学因素。
所以,当两组纱线在交织点处的夹角发生变化时,获取该位置上有关剪切的量的信息也是很有用处的。
在研究中,我们采用KES 2F 测试系统测出的剪切刚度(G )、015°和5°角的剪切滞后量(2HG ,2HG 5)来表征一块机织物的剪切性能。
剪切刚度反映了织物抵抗剪切变形的能力,而剪切滞后量反映了织物在一个剪切变形周期中能量的损失状况。
在实验中,我们采用KES 2F 测试仪对大量的不同类型织物从各个方向上进行测试得到实验数据,基于这些数据我们建立数学模型,预测织物在各个不同方向上的剪切刚度。
已有文献资料显示,剪切刚度与剪切滞后之间有着显著的相关性。
例如,在Collier 等人的结论中都证明剪切刚度和剪切滞后的相关系数很高,分别可达到0197、0194和0192。
尽管决定机织物剪切刚度和剪切滞后的力学因素可能有所不同,根据前人结论和我们自己的实验结果,我们假设剪切刚度和剪切滞后是遵从相似的内在力学因素。
由此,基于机织物剪切刚度预测模型的有效性,我们将这一模型应用到对各类机织物剪切滞后性能的预测上。
将实验数据与理论结果进行对比,我们将这一模型应用到对各类机织物剪切滞后性能的预测上。
将实验数据与理论结果进行对比,并在极坐标图上表示出来,可以证明该模型的有效性,同时发现剪切刚度与剪切滞后的这种线性关系不仅存在于经纬两个主要方向上,也存在于其他各个方向上。
1 对机织物在各个方向上的剪切性能进行建模 K ilby 等人将传统的弹性理论与认为织物是各向异性的薄片的假设结合起来。
根据弹性理论,织物的拉伸和剪切性能可由在经纬向及其他—93—各方向的柔量进行理论推导得出。
经过理论推导,我们得出机织物在各个方向上剪切刚度的计算公式:1 Gθ=(4G45)cos2θsin2θ+1G(cos2θ-sin2θ)2(1)θ的值为偏离正方向(经向或纬向)的角度。
根据公式(1),当测出了织物在经、纬向及±45°方向上的剪切刚度值后,可计算织物在其他各个方向上的剪切刚度(G)。
因为剪切刚度反映了在织物发生微小剪切变形时,织物内部在经纬纱交织点处对相对扭转运动的抵抗性能。
我们也可以确定经向剪切刚度与纬向剪切刚度的关系。
Mahar等人通过研究找到了经向剪切刚度与纬向剪切刚度的线性关系,说明可以对织物剪切刚度的测试进行简化,只需测一个主方向上的量值。
在实验中遇到经向和纬向的剪切刚度值差异较大时,我们取两个方向上的平均值。
织物的剪切滞后可理解为在织物发生剪切变形并自然恢复到原来状态的一个循环中能量的损耗。
一些学者通过研究证实剪切刚度(G)与剪切滞后量(2HG,2HG5)存在明显的线性关系。
基于这个结论,我们将预测机织物各个方向上剪切刚度的理论模型用来预测各种类型织物的剪切滞后性能。
在研究中,我们对比了实验数据与理论结果,并将结果在极坐标图上表示出来。
2 实验我们选择了分为3种组织结构(平纹、斜纹、缎纹)共35种服装面料作为试样。
其中12种试样是实验室内部生产的100%纯棉布,其他为一些市场上常见的机织面料,成分分别有腈纶、纯棉、涤/棉、涤/丝、尼龙、人造棉及丝、羊毛等等。
表1为试样的组织结构及相应的试验数据,以下选取了4组数据。
为使实验结果准确、可靠,所有试样在测试前都置于相对湿度为65%±2%,温度为20℃±2℃的大气环境下进行24h的温湿处理,处理后还测试了试样的厚度。
表1 机织物试样的结构特性及各个方向上的剪切性能测试数据试样组织结构纱线(根数/in)各个方向上理论与实验值之差G2HG2HG5各个方向上剪切刚度与剪切滞后的相关系数2HG和G2HG5和G2HG5和2HG1平纹60×54212311931122019727019920019579 2斜纹108×60314911881110019315019914019875 7斜纹80×42110031151125019688019978019931 25缎纹254×116414251715169019653019944019405 在布面上,我们通常把与经向或纬向所成的锐夹角叫做偏角。
在实验时我们采用人们习惯的偏角定义,统一取沿顺时针偏离经纱方向的角。
在布面上规定沿经纱方向为0°,纬纱方向为90°,沿顺时针方向的角为正,而逆时针方向的角为负。
由此,在极坐标图上,+15°代表15°和195°,-15°代表165°和345°,依此类推。
对一块组织结构对称的试样来说,例如平纹织物,取经向到纬向之间90°的测量范围就足够了。
而对于非对称结构的织物如斜纹和缎纹组织,则要剪取0°~180°范围内的试样进行测试。
剪取试样要沿经向、纬向,以及偏离经向±15°、±30°、±45°、±60°和±75°的方向。
按各个方向剪取了试样后,可对它们按通常的方法在KES2F测试系统上进行测试。
测得数据用于建立θ的极坐标图,如图1所示。
从图上我们可以看到,对每一种类型的织物,不管是取了7个方向的平纹织物还是取了12个方向的斜纹和缎纹织物,它们的极坐标曲线在0°~360°的范围内都出现了4次重复。
3 结果与讨论311 理论与实验结果的比较31111 机织物在各个不同方向上的剪切刚度通过对各类试样的理论计算剪切刚度(G)与实验结果进行比较,发现理论与实际有很好的一致性,偏差不超过8184%(如表1所示)。
在所有的机织物试样中我们选取了平纹织物(F1)、斜纹织物(F7)、缎纺织物(F25)3种试样,表1中列出—4—了理论与测试结果,并在图1a 、b 、c 的极坐标图中表示出来。
在图1中,剪切刚度的极坐标曲线是沿经向或纬向的对称形状。
参数值随着偏角的改变发生变化,但在与经向、纬向约成±45°的位置都有一个峰值,说明机织物的剪切刚度值在经向和纬向之间存在一个明显的最大值。
图1 试样剪切刚度理论与实验结果的极坐标图 (a )平纹F1 (b )斜纹F7 (c )缎纹F25图2 试样F1理论值与实验值的剪切滞后曲线 (a )2HG (b )2HG 5 在理论研究中,我们通过测出±45°方向的剪切刚度值,然后由公式(1)来确定织物的剪切刚度G 在其他方向上的值。
对于不同类型的织物,它们的剪切刚度极坐标曲线也有差别,造成这种差别的主要原因可能有:织物组织结构、后整理工艺、织物内部纱线、纤维的刚度、两组纱线在交织点的接触面积,以及纤维在纱线中的集束紧密度等等。
任何上述因素的综合都可导致机织物剪切性能的差异,即使这些织物是由同种原料加工成的。
从织物的几何结构中我们知道,织物内部两组纱线的交织点存在法向压力,它引起摩擦约束。
因为加在织物上的剪切力通常远大于织物内部所有交织点处的摩擦约束之和,因此导致织物的剪切变形,并伴随有滞后效应。
发生剪切变形时,在纱线交织点处因为合成纤维之间的接触面积较小,所以合成纤维织物的滞后量要小于天然纤维织物的滞后量。
织物经后整理加工后剪切性能降低。
这是因为经后整理加工后,随着交织区内法向内应力的—14—减少,纱线内部的残余应力得以释放。
所以市场上的机织物试样的剪切性能要低于实验室内生产的机织物。
31112 机织物在各个不同方向上的剪切滞后将理论剪切刚度模型应用于预测机织物在各个方向上的剪切滞后量(2HG、2HG5),我们得到这些机织物试样的理论值与实测值的偏差值(如表1中所示)。
理论值与实验结果取得很好的一致,偏差不高于10%。
图2分别列出了剪切滞后(2HG、2HG5)的实验值与理论值的极坐标曲线。
图2的结果进一步证实了理论与实验的吻合,说明我们的模型对于预测机织物的剪切滞后性能也是相当可靠的。
因为剪切变形取决于织物内部的摩擦力和弹性力。
当结构紧密的机织物发生剪切变形时,在织物内部纱线交织点处由于一定数量的纱线产生相对滑移和挤压,从而可迅速生成内部的弹性力。
组织结构较松散的机织物如斜纹和缎纹织物,织物内部的摩擦力很小。
312 在各个方向上剪切刚度与剪切滞后的关系现有文献资料显示剪切刚度与剪切滞后有明显的关系。
实验结果同样证明在各个方向上剪切刚度与剪切滞后有明显的线性关系。
在各个方向上,对2HG和G来说,他们的相关系数R2= 019727;对2HG5和G,R2=019920;对2HG5和2HG,有R2=019579。
对于其他类型的织物试样都有R2>0190。
基于以上事实,我们假设机织物在经向、纬向及其他方向上的剪切刚度和剪切滞后遵循相似的物理力学规律。
因为剪切刚度主要是由纱线内部纤维间的摩擦力引起的,而剪切滞后也是由同样的摩擦力所决定的,而且在整个剪切循环中,这种摩擦力是持续存在的。
剪切刚度的最大值不是在经向或纬向,而是在与经/纬向成约±45°角的方向,剪切滞后的最大值也出现在这一方向上。