第三采油厂加热炉学习讲义
加热炉学习

一、管式加热炉的结构及工作原理1.1 管式加热炉在炼油和石油化工中的重要性管式加热炉是一种火力加热设备,它利用燃料在炉膛内燃烧时产生的高温火焰与烟气作为热源,加热在炉管中高速流动的介质,使其达到工艺规定的温度,以供给介质在进行分馏、裂解或反应等加工过程中所需的热量,保证生产正常进行。
与其他加热方式相比,管式加热炉的主要优点是加热温度高(可达1273K),传热能力高和便于操作管理。
近60多年所来,管式炉的发展很快,已成为近代石化工业中必不可少的工艺设备之一,在生产和建设中具有十分重要的地位。
例如:一个年处理量为2.5Mt原油的常减压蒸馏装置,虽所用的加热炉的座数不多,但其提供的总热量却达70MW,如果炉子加热能力不够,就会限制整个装置处理能力的提高,甚至无法完成预定的任务。
管式加热炉消耗的燃料量相当可观,一般加工深度较浅的炼厂,约占其原油能力的3%~6%,中等深度的占4%~8%,较深的为8%~15%,其费用约占操作费用的60%~70%,因此,炉子热效率的高低与节约燃料降低成本有密切的关系。
此外,管式炉炉管结焦、炉管烧穿、炉衬烧塌等事故也常常是迫使装置停工检修的重要原因。
在生产中,希望生产装置能达到高处理量、高质量和低消耗以及长周期、安全运转,大量实践表明,管式炉的操作往往是关键之一。
管式炉的基建投资费用,一般约占炼油装置总投资的10%~20%,总设备费用的30%左右,在重整制氢和裂解等石油化工装置中,则占建设费用的25%左右,因此,加热炉设计选型的好坏,还直接影响装置经济的合理性。
1.2 管式加热炉的分类和主要工艺指标1.2.1管式加热炉的分类管式炉的类型很多,如按用途分有纯加热和加热-反应炉,前者如:常压炉、减压炉,原料在炉内只起到加热(包括汽化的作用);后者如:裂解炉、焦化炉,原料在炉内不仅被加热,同时还应保证有一定的停留时间进行裂解或焦化反应。
按炉内进行传热的主要方式分类,管式炉有:纯对流式、辐射-对流式和辐射式。
加热炉学习资料.doc
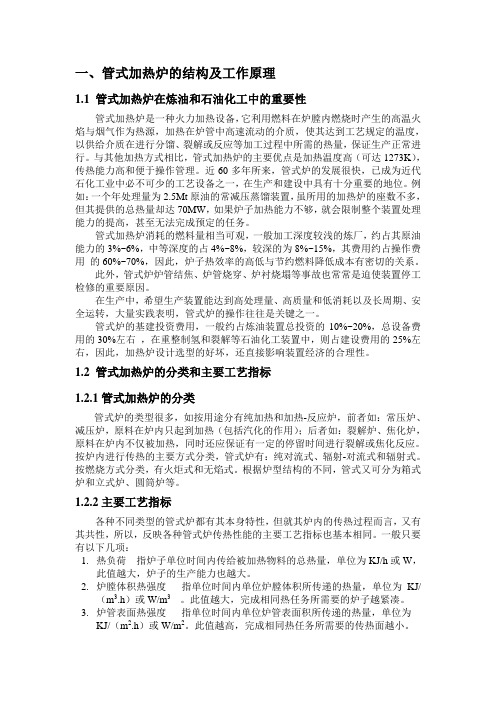
一、管式加热炉的结构及工作原理1.1 管式加热炉在炼油和石油化工中的重要性管式加热炉是一种火力加热设备,它利用燃料在炉膛内燃烧时产生的高温火焰与烟气作为热源,加热在炉管中高速流动的介质,使其达到工艺规定的温度,以供给介质在进行分馏、裂解或反应等加工过程中所需的热量,保证生产正常进行。
与其他加热方式相比,管式加热炉的主要优点是加热温度高(可达1273K),传热能力高和便于操作管理。
近60多年所来,管式炉的发展很快,已成为近代石化工业中必不可少的工艺设备之一,在生产和建设中具有十分重要的地位。
例如:一个年处理量为2.5Mt原油的常减压蒸馏装置,虽所用的加热炉的座数不多,但其提供的总热量却达70MW,如果炉子加热能力不够,就会限制整个装置处理能力的提高,甚至无法完成预定的任务。
管式加热炉消耗的燃料量相当可观,一般加工深度较浅的炼厂,约占其原油能力的3%~6%,中等深度的占4%~8%,较深的为8%~15%,其费用约占操作费用的60%~70%,因此,炉子热效率的高低与节约燃料降低成本有密切的关系。
此外,管式炉炉管结焦、炉管烧穿、炉衬烧塌等事故也常常是迫使装置停工检修的重要原因。
在生产中,希望生产装置能达到高处理量、高质量和低消耗以及长周期、安全运转,大量实践表明,管式炉的操作往往是关键之一。
管式炉的基建投资费用,一般约占炼油装置总投资的10%~20%,总设备费用的30%左右,在重整制氢和裂解等石油化工装置中,则占建设费用的25%左右,因此,加热炉设计选型的好坏,还直接影响装置经济的合理性。
1.2 管式加热炉的分类和主要工艺指标1.2.1管式加热炉的分类管式炉的类型很多,如按用途分有纯加热和加热-反应炉,前者如:常压炉、减压炉,原料在炉内只起到加热(包括汽化的作用);后者如:裂解炉、焦化炉,原料在炉内不仅被加热,同时还应保证有一定的停留时间进行裂解或焦化反应。
按炉内进行传热的主要方式分类,管式炉有:纯对流式、辐射-对流式和辐射式。
采油PPT课件:真空加热炉的结构与原理

加热炉结构图
(三)加热炉的工作原理
燃烧器将燃气充分在燃烧火筒中燃烧,高温气体 经火筒和烟管,与锅壳内中间介质——水充分换 热,水受热沸腾产生蒸汽,与密封在一个容器中 的加热盘管接触,把热量传递给盘管,由于盘管 外表面温度较低,从而使蒸汽冷凝成水,水落下 后又被加热成蒸汽,如此循环往复实现了相变换 热过程。由于蒸汽的冷凝,使炉体内形成真空状 态,产生负压。
2、操作间着火
操作间着火时,应在远距离的地点将燃料输 送管道阀门关闭,切断电源,并用灭火器进 行灭火。
3、加热炉汇管穿孔跑油着火
关闭事故炉天然气阀门; 改通流程开旁通阀; 关闭事故炉进油、出油阀门; 用蒸汽或干粉灭火机灭火; 通风扫线。 查清穿孔位置及故障原因进行处理。
4、燃烧器的故障
理检查。 1:第一安全时间完成时无火焰信号;检查游离探针系统, 2:第二安全时间完成时无火焰信号;调整更换。
程控盒 LFL透明窗口
(2)燃烧器不好点火
原因: 各参数值设定不当。 天然气内有空气或流量不够,因此没有足够的燃气维
持稳定的火焰。 由于空气和燃气的比例不正确。
排除方法: 按给定参数重新设定各参数。 排天然气,将管道内空气排除干净。 可以通过燃烧头部调节燃气进气口之间的空气通道。
(一)真空加热炉的主要参数
额定功率
1600kw
额定流量
137.88m3/h
主盘管额定压力
2.5Mpa
炉体额定压力
-0.01Mpa
出口温度
55℃
外型尺寸 8035×4447×4522
热效率
90%
(二)真空加热炉的结构
由燃烧火筒、回烟室、烟管、前烟箱、烟囱、 吸热主副工质盘管、真空阀(或安全阀)、 防爆装置、检测仪表组成。
加热炉培训讲义共32页文档

16、自己选择的路、跪着也要把它走在的事 。现在 有成就 ,以后 才能更 辉煌。
18、敢于向黑暗宣战的人,心里必须 充满光 明。 19、学习的关键--重复。
20、懦弱的人只会裹足不前,莽撞的 人只能 引为烧 身,只 有真正 勇敢的 人才能 所向披 靡。
拉
60、生活的道路一旦选定,就要勇敢地 走到底 ,决不 回头。 ——左
56、书不仅是生活,而且是现在、过 去和未 来文化 生活的 源泉。 ——库 法耶夫 57、生命不可能有两次,但许多人连一 次也不 善于度 过。— —吕凯 特 58、问渠哪得清如许,为有源头活水来 。—— 朱熹 59、我的努力求学没有得到别的好处, 只不过 是愈来 愈发觉 自己的 无知。 ——笛 卡儿
加热炉培训资料资料
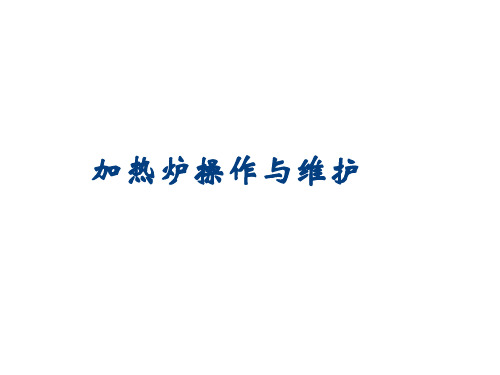
第二部分 管式加热炉简介
4、 结 构 形 式
管式加热炉由辐射室、对流室、烟囱、烟囱 挡板操纵机构、对流室梯子平台、转油线、 燃烧器、吹灰器等组成(具体见管式加热炉 结构示意图 )。主要部件有炉管、弯头、 管架与管板、火嘴以及各种配件,如烟道挡 板、看火门、防爆门、人孔门等。管式加热 炉的特点是:结构紧凑、可减少炉膛容积、 占地面积小、耗用钢材少;烟气流向合理, 烟囱不很高,沿炉截面热分布均匀。其各部 分组成说明如下:
钉头管 与
翅片管
第二部分 管式加热炉简介
第二部分 管式加热炉简介
5、 系 统 组 成
6、设计参数一览表
编号
项目
1
额定热负荷
2
被加热介质
3
介质额定流量
4
介质最小流量
5
介质入炉温度
6
介质出炉温度
7
炉管设计压力
8
压降
9
燃料
10
燃料油耗量
11
燃料气耗量
12
排烟温度
13
热效率
第二部分 管式加热炉简介
兰州首站 5000kW
第二部分 管式加热炉简介
管式加热炉工作原理示意图
第二部分 管式加热炉简介
2、性能特点
结构合理紧凑,传热效率高,露天安装,全天候运行。使 用操作简单,运行费用低。
优化热工工艺方案,采用多项节能技术,热效率设定适当, 当热负荷小于4MW,热效率η≥85%,当热负荷大于4MW, 热效率η≥90%。
传热结构布置与热工参数确定合理,传热均匀,确保管内 介质物性不受损伤,炉管使用寿命长。
第二部分 管式加热炉简介
9、氮气灭火系统
•氮气灭火系统由氮气储罐及减压阀、灭火电磁阀、过滤 器等装置组成。氮气储存于储罐中,经出口管线上的减 压阀、电磁阀、过滤器等部件,分为几路通往加热炉炉 膛内,加热炉在运行过程中,如发现异常情况(如排烟 温度过高报警),炉控系统将对制氮系统电磁阀发出信 号,通过加热炉的电磁阀将打开,进行灭火操作。 •氮气灭火系统管线上各个接头全部采用法兰连接形式, 能有效地避免氮气的大量泄露,延长氮气的使用时间。
采油PPT课件:真空加热炉的结构与原理

三、真 空 加 热 炉
主要规格有ZS-Y原油加热炉,ZS-SY含 油污水加热炉,ZS-SH采暖加热炉,ZSSL热水加热炉。
型号:ZS1600—Y/2.5—Q
(一)真空加热炉的主要参数 (二)真空加热炉的结构 (三)真空加热炉的工作原理 (四)燃烧器 (五)真空加热炉的运行操作 (六)真空加热炉的维护保养 (七)真空加热炉的故障处理
2、操作间着火
操作间着火时,应在远距离的地点将燃料输 送管道阀门关闭,切断电源,并用灭火器进 行灭火。
3、加热炉汇管穿孔跑油着火
关闭事故炉天然气阀门; 改通流程开旁通阀; 关闭事故炉进油、出油阀门; 用蒸汽或干粉灭火机灭火; 通风扫线。 查清穿孔位置及故障原因进行处理。
4、燃烧器的故障
停止燃烧器运行。将介质进口阀门打开,重新设置 XMT-100柜面板上锅筒温度上限、下限、回差值。
待温度降至工艺要求值后,重新使燃烧器启动、投 入自动运行。
3、加热炉的停止操作
在任何情况下,只要把燃烧器运行开关扳至 停运状态,即可停机。
加热炉在冬季长时间停运,必须将筒体内的 水彻底排出,以防冻结。
2、加热炉的排气、启动操作
将介质进口管道阀门关闭;
将XMT-100柜上的锅筒温度设定值提高:
上限值110℃、上限回差3 ℃,下限值95 ℃,下限 回差5 ℃。
启动燃烧器,调整燃料/空气比值达到一个良好的燃 烧状态,使锅筒内水温急剧上升。
当温度升至95 ℃以上时,自动推动真空阀排气,连 续排气5—8分钟,以排尽筒内空气。
(1)利用程控盒透明窗口闭锁指示符号来判断:
▲:因为打开讯号没有由限制开关A供给端子8;查找线路。(电机不 转,大风)
▇:由火焰监测回路故障引起;检查游离探针系统绝缘、游离电流 ▼:由于低火焰位置的位置寻好没有由辅助开关“M”提供给端子8;
加热炉讲义讲解
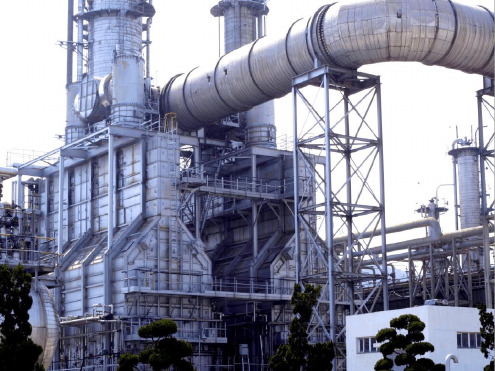
燃烧器在炉子里的排列布置(歧化车间火嘴朝上)
火嘴朝上
火嘴朝下
火嘴在炉墙侧面
多级火嘴并列
减小管式加热炉燃烧器噪音的方法
a.场地容许的情况下将加热炉放在比较偏远的 地方
b.采用隔墙将装有燃烧器的炉底围起来 c.使用低噪音燃烧器
歧化加热炉燃烧器噪音控制在85Bd以下
加热炉有害燃烧产物的控制
燃烧产物烟气中有 SO2、NOx 不完全燃烧 时还会有一氧化碳和烟尘,这些产物对环境 和人造成危害,这些污染物和燃料本身和燃 烧状况有关,当燃料中的 S含量高时烟气中 SO2含量会高,燃料中的 N和空气中的 O在燃 烧时都可能生成 NOx ,它容易和阳光产生光 化学烟雾加速生成极毒的 NO2;解决措施主要 是降低燃料中的S、N含量和控制炉膛O2含量
空气预热器的有关设计数据
名称 (37-H-101)
流量㎏ /h 入口温度℃ 出口温度℃ 允许压降 mm水柱 热负荷 MW
流量㎏ /h 入口温度℃ 出口温度℃ 允许压降 mm水柱 热负荷 MW
有无旁路
空气侧 烟气侧
热管式空气预热器
45648 15.5 175 150 2.06
48168 305 171 150 2.06
有
4.燃烧器(火盆里的各部件名称 )
歧化加热炉附件列表
名称 灭火蒸汽 灭火蒸汽
看火窗 看火孔 防爆门 烟气取样口 炉管热电偶 炉体热电偶 烟气控制挡板 烟气密封挡板 燃烧器 炉膛压力表
位置 辐射段 对流段 辐射段
炉底 辐射段 遮蔽段
炉管 对流段 对流段
烟囱 辐射段 对流段、辐射段
个数 20 12 24 12 8 3 16 32 2 1 12 18
2.燃料油的来源
加热炉工培训讲义

加热炉工培训讲义第一章 传热原理1.1 传热及传热的方式1.1.1 传热:不同温度的两个物体放在一起,不久便发现高温物体的温度降低了,低温物体的温度升高了。
这说明有一部分热量从高温物体传到了低温物体。
这种现象称为传热。
1.1.2 传热的方式:分对流传热、传导传热、辐射传热三种方式。
1.2 对流传热1.2.1 定义:依靠流体(液体或气体)本身流动而实现的热传递叫做对流传热。
1.2.2 自然对流传热:由于流体受热后体积膨胀、比重减小而上升,或流体冷却后体积收缩、比重增加而下降所产生的对流传热叫自然对流传热。
1.2.3 强制对流传热:依靠外力强制流动来实现的热量传递叫强制对流传热。
1.3 传导传热1.3.1 定义:物体通过接触,并没有发生物质的相互转移而传递热量的方式叫传导传热。
1.3.2 导热系数:单位厚度上存在1℃温差时所导热的热流值来衡量不同物质导热性能的差异,称为导热系数。
千卡/米*时*摄氏度1.3.3 传导热流的计算公式:()21t t s q -=λ式中:q ——温降方向上的热流,千卡/平方米*时λ——导热系数,千卡/米*时*摄氏度s ——物体厚度,米21t t -——物体厚度上的温差,摄氏度。
1.4 辐射传热1.4.1 定义:物体间依靠电磁波互相辐射传导热量的方式叫辐射传热。
辐射传热无需中间介质,热量传递不仅由高向低也由低向高的方式互相传递热量。
1.4.2 气体辐射传热:加热炉燃烧气体中CO2、H2O 、SO2气体能够吸收和辐射能量。
这种气体的辐射传热对钢料的加热很重要,特别是采用煤气无烟燃烧的加热炉,火焰的绝大部分是靠燃烧产物中CO2和水蒸气辐射传热传给钢料的。
1.5 热量在炉内的传递加热炉的烧嘴燃烧时,火焰中的热量靠对流和辐射方式传给炉壁和钢坯。
对流传热主要取决于贴近炉壁或钢坯表面的炉气流速。
为避免局部过热,火焰一般不宜冲着炉壁或钢坯,钢坯只与火焰的边缘接触,因此对流传热强度不大。
火焰对钢坯的辐射传热有两个途径,一个是钢坯直接接受火焰的辐射热;另一个是以炉壁为介质传递热量。
加热炉知识讲义
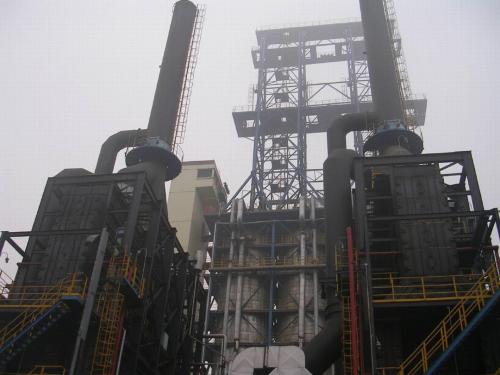
202016/11/21
14
1、炉管水平, 传热均匀; 2、占地面积大; 3、管内流动阻力 小;方便清焦。
202016/11/21
15
1、炉管长度方向受 热不均匀;
2、可节省大量高铬 镍钢的材料。
特点 火焰垂直向上, 与烟气流动方向一 致
202016/11/21
16
使火墙成为良好的 热辐射体,增加炉 膛内辐射面积
作用: 火焰和高温烟气通过辐射将热量
传给辐射管,炉壁对热量的反射 也间接地传热给辐射管
202016/11/21 28
由于瓦斯阀门关不严或多次点火未 防爆门 点着,使炉膛内存有可燃气体,在 点火时易发生爆炸。这时,炉膛压 力将防爆门推开泄掉一部分压力。 阻火器 为防止火焰倒窜入瓦斯罐或其他容 器内产生爆炸,在炉内瓦斯线上都 设有瓦斯阻火器。阻火器应设在瓦 斯入炉前的管线上。内有多层金属 网状物,传热快,一旦火焰通过时 ,热量很快散失降低温度,从而灭 火。
202016/11/21
33
用什么吹灰——吹 灰 器
作用 利用喷射蒸汽或空气清扫炉管表面的积灰
部位
主要用于对流室采用翅
片管或钉头管的部位 吹灰器种类:有蒸汽吹灰器、声 波吹灰器、激波吹灰器等。
202016/11/21
34
(五)余热回收系统
排烟温度是提高热效率的一种重要方法。 降低 利用空气预热器或余热锅炉可降低排烟温度。 但在余热回收系统易引起 低温露点 腐蚀。
44
雾化蒸汽 利用蒸汽的冲击和搅拌作用,使燃 料油喷成雾状,从而与空气得到充 分的混合,使燃料油燃烧完全 蒸汽量 大,带走热量多,降低 炉子热效率;火焰发白,易灭火。
作 用 影 响
蒸汽量 小,雾化不好,燃料油 燃烧不完全;火焰尖端发轻, 呈暗红色。 雾化蒸汽比燃料油压力 高 。
加热炉知识培训(最终版)
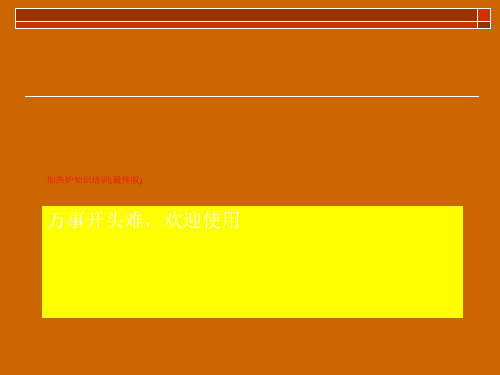
一、管式加热炉概述
②大型箱式炉 与箱式炉不同的是炉膛 宽敞,炉膛中间有隔墙, 把辐射室分成两间,从 而大大增加了传热反射 面。它在炉膛的三个侧 面都安了炉管,比箱式 炉炉壁利用率高。 对流室和烟囱放在炉顶, 烟气流动的阻力减少, 不过由于又有新的炉型 比它更好,最近也不使 用了。
31
大型箱式炉
一、管式加热炉概述
16
一、管式加热炉概述
WYQ-DQ350型油气联合燃烧器
WYQ-DQ350D型油气联合(带低瓦)燃烧器
17
一、管式加热炉概述
➢ 4.5通风系统
通风系统的任务是将燃烧用空气导入燃烧器,并将废烟气引 出炉子,它分为自然通风方式和强制通风方式两种。
强制通风 分类:
自然通风
利用外部气体输送机械鼓风
一般炉膛内微正压 利用烟囱产生抽力实现引入空气 和排除烟气
烟囱挡板及调节系统
27
一、管式加热炉概述
看火门:观看炉膛内所有火嘴的整个火焰;观看辐射 管、 底排遮蔽管的受热状况,管壁被氧化的情况, 炉管的弯曲程度等。
防爆门:负压自重式防爆门,平时靠自重关闭,当炉 内压力增高时,防爆门即被打开。
人孔门:进行安装及检修等工作。
28
一、管式加热炉概述
5、管式炉的类型
33
顶烧式箱式炉
一、管式加热炉概述
⑤斜顶炉 它由箱式炉演变 而来,是箱式炉 砍去炉膛内烟气 流动的死角区而 成。 虽然它对辐射室 的传热均匀性有 所改善,但并没 有克服箱式炉的 其它缺点。近年 来也不再建造了。
34
斜顶炉
一、管式加热炉概述
5.2.2立式炉 ①横管立式炉 传热机理同箱式炉差不多,只是造型上 采用了立式炉的特点。炉管布置在两侧 壁,中央十一列底烧的燃烧器,烟气由 辐射室、对流室经烟囱一直上行。燃烧 器能量较小,数目较多,间距较小,从 而在炉子中央形成一道火焰“膜”提高 了辐射传热效果。 现在立式炉多采用这一形式。
加热炉学习资料-
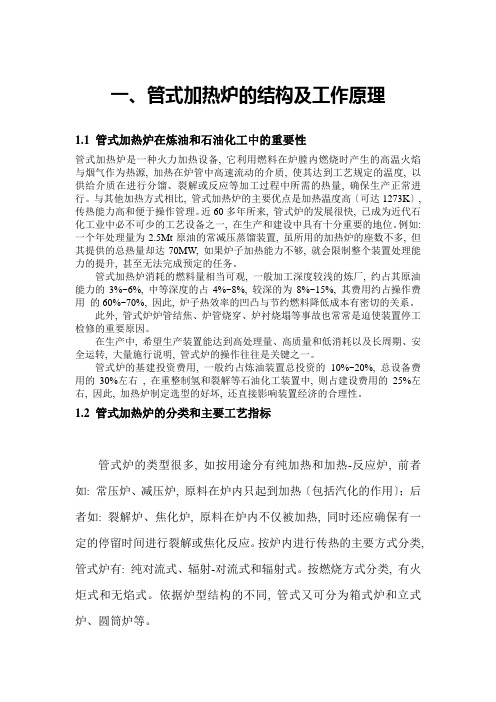
一、管式加热炉的结构及工作原理1.1 管式加热炉在炼油和石油化工中的重要性管式加热炉是一种火力加热设备, 它利用燃料在炉膛内燃烧时产生的高温火焰与烟气作为热源, 加热在炉管中高速流动的介质, 使其达到工艺规定的温度, 以供给介质在进行分馏、裂解或反应等加工过程中所需的热量, 确保生产正常进行。
与其他加热方式相比, 管式加热炉的主要优点是加热温度高〔可达1273K〕, 传热能力高和便于操作管理。
近60多年所来, 管式炉的发展很快, 已成为近代石化工业中必不可少的工艺设备之一, 在生产和建设中具有十分重要的地位。
例如: 一个年处理量为2.5Mt原油的常减压蒸馏装置, 虽所用的加热炉的座数不多, 但其提供的总热量却达70MW, 如果炉子加热能力不够, 就会限制整个装置处理能力的提升, 甚至无法完成预定的任务。
管式加热炉消耗的燃料量相当可观, 一般加工深度较浅的炼厂, 约占其原油能力的3%~6%, 中等深度的占4%~8%, 较深的为8%~15%, 其费用约占操作费用的60%~70%, 因此, 炉子热效率的凹凸与节约燃料降低成本有密切的关系。
此外, 管式炉炉管结焦、炉管烧穿、炉衬烧塌等事故也常常是迫使装置停工检修的重要原因。
在生产中, 希望生产装置能达到高处理量、高质量和低消耗以及长周期、安全运转, 大量施行说明, 管式炉的操作往往是关键之一。
管式炉的基建投资费用, 一般约占炼油装置总投资的10%~20%, 总设备费用的30%左右, 在重整制氢和裂解等石油化工装置中, 则占建设费用的25%左右, 因此, 加热炉制定选型的好坏, 还直接影响装置经济的合理性。
1.2 管式加热炉的分类和主要工艺指标管式炉的类型很多, 如按用途分有纯加热和加热-反应炉, 前者如: 常压炉、减压炉, 原料在炉内只起到加热〔包括汽化的作用〕;后者如: 裂解炉、焦化炉, 原料在炉内不仅被加热, 同时还应确保有一定的停留时间进行裂解或焦化反应。
油田用加热炉设计培训资料(33页)
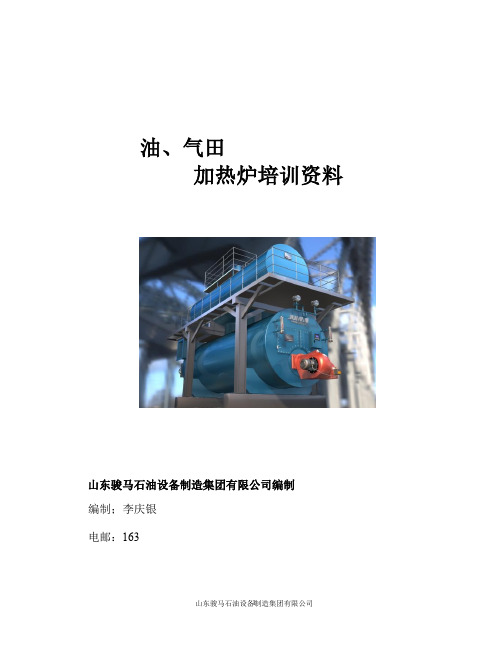
油、气田加热炉培训资料山东骏马石油设备制造集团有限公司编制编制;李庆银电邮:163目录第一章概述 ............................................................................................. 错误!未指定书签。
第一节油田加热炉 ............................................................................... 错误!未指定书签。
一、油田和长输管线加热炉的用途 ......................................................... 错误!未指定书签。
二、油田加热炉的技术装备现状 ............................................................. 错误!未指定书签。
第二节油田加热炉的炉型及基本结构 ............................................. 错误!未指定书签。
一、油田加热炉的炉型 ............................................................................. 错误!未指定书签。
一、热传递的基本概念 ............................................................................. 错误!未指定书签。
二、压力和温度 ......................................................................................... 错误!未指定书签。
三、热力学的有关概念 ............................................................................. 错误!未指定书签。
加热炉培训讲义

• (4)焊接后的焊缝质量标准
• a.外观尺寸应符合设计文件或相关规范的要求,焊缝 与母材应圆滑过渡。 • b.焊缝和热影响区表面不应有裂纹、气孔、弧坑和肉 眼可见的夹渣等缺陷。 • c.焊缝表面的咬边深度不得大于0.5mm,焊缝两侧咬 边总长度不得超过该焊缝总长度的10%。否则,应进行 修磨或补焊,使之平滑过渡。经修磨部位的炉管壁厚不 应小于设计要求的厚度。
(5)炉管的安装标准
a.炉管安装前应详细检查管板、管架和定位管的安装位置是否符合 设计要求。 b.炉管预制件在运输和吊装过程中,应有预防变形的加固措施。 c.立管吊装时应平稳,不得撞击炉墙和衬里。水平管穿管时,不得 撞击管板、管架和折流砖。 d.立管上端采用炉外支撑时,每根炉管的两个支耳应水平地支撑在 吊管梁上。若立管采用炉内吊管时,炉管上部弯管应与吊钩紧密 接触,并使吊钩确实承重,炉管中部的拉钩不应与炉管紧密接 触,以免影响炉管自由膨胀。炉管下部弯管的导向管应垂直插入 炉底的定位孔内,不得强制插入。炉管在长度方向上应能自由膨 胀。 e.立管采用炉内下部支撑时,炉管上部的导向吊挂应按设计文件要 求正确安装,炉管应能向上自由膨胀。 f.圆筒炉辐射管组焊安装后,其节圆直径误差不大于设计值的 0.2%,并不超过12mm。
• d.对接焊缝应进行100%无损探伤。检测方法宜采用射 线检测。若采用超声检测时,需用射线检测复验,复验 比例为焊缝总数的20%。射线检测合格等级为Ⅱ级,超 声检测合格等级为Ⅰ级。不能用射线或超声检测的角焊 缝,可采用磁粉或渗透检测方法检查缺陷。 • e.不合格的焊缝必须进行返修,同一部位的焊接返修次 数不宜超过两次。经过两次焊接返修仍不合格的焊缝, 如需再进行返修,应编制返修工艺措施,经技术总负责 人批准后方可实施,并将返修次数、部位和无损检测等 结果记入焊缝返修记录中。返修后仍按原规定方法进行 检测。要求焊后热处理的,应在热处理前进行返修。如 在热处理后还需返修,返修后应重新进行热处理并做硬 度测试。
第三采油厂加热炉学习讲解

第一部分基础知识一、加热炉的定义及用途通常所说的加热炉有油田和长输管线加热炉、石油炼制和石油化工加热炉,这里仅介绍油田和长输管线加热炉。
油田和长输管线加热炉指油气田和长输管道用火焰加热原油、天然气、水及其混合物等介质的专用设备。
在油、气田的集油站、集气站、联合站等站库内,加热炉对原油、井产物、生产用水和天然气等介质进行加热,以满足油气集输处理工艺的要求。
在原油和天然气长输管道中,经加热炉对原油和天然气进行加热,以满足长距离输送的要求。
油田和长输管线加热炉对介质进行加热所要求的温度都不高,一般不超过100℃,介质无化学变化,这与石油炼制和石油化工加热炉不同。
二、国内外加热炉的现状目前国外发达国家在加热炉的设计方面主要向高效率、低耗能、重环保及精密化、智能化方向发展。
技术优势主要在于燃烧器、炉体结构、绝热材料、自动控制与监测系统等方面。
进入21世纪以来,国内加热炉技术有了很大发展,与国外差距逐步缩小,特别是在新型高效加热炉方面设计方面已经基本跟上国际发展潮流。
但是,跟上潮流不等于达到国际先进水平,工业基础、国民素质等各种因素决定了,国内加热炉设计、制造、使用等方面与发达国家还有一定差距。
主要表现在:1.设计上,对新技术的使用还处于摸索阶段,产品成熟度不够,给使用中带来了一些问题。
2.制造上,由于制造工艺和材料技术的限制,带来加热炉的使用寿命较短、单位耗钢量大、热损失大等缺陷。
3.燃烧器技术上还有差距,目前新型燃烧器主要靠进口,进口燃烧器不能适应国内现状等。
4.加热炉监控技术还不够完善。
在线监控技术很少、难以实现无人值守运行、加热炉难以达到最佳经济运行状态。
三、采油三厂加热炉现状本表统计截止2011年底。
四、加热炉主要技术经济指标1.热负荷:单位时间内向炉管内被加热介质传递热量的能力称为热负荷,一般用MW表示。
它表示加热炉生产能力的大小。
2.炉膛体积发热强度:燃料燃烧的总发热量除以炉膛体积,称之为炉膛体积发热强度,简称为体积热强度,它表示单位体积的炉膛在单位时间内燃料燃烧所发出的热量,一般用KW/m3为单位。
- 1、下载文档前请自行甄别文档内容的完整性,平台不提供额外的编辑、内容补充、找答案等附加服务。
- 2、"仅部分预览"的文档,不可在线预览部分如存在完整性等问题,可反馈申请退款(可完整预览的文档不适用该条件!)。
- 3、如文档侵犯您的权益,请联系客服反馈,我们会尽快为您处理(人工客服工作时间:9:00-18:30)。
四、加热炉主要技术经济指标
1.热负荷:单位时间内向炉管内被加热介质传递热量的能力称为热负荷,一般用MW表示。它表示加热炉生产能力的大小。
2.炉膛体积发热强度:燃料燃烧的总发热量除以炉膛体积,称之为炉膛体积发热强度,简称为体积热强度,它表示单位体积的炉膛在单位时间内燃料燃烧所发出的热量,一般用KW/m3为单位。
图一常用加热炉分类归属图
二、油田加热炉的型号及表示
炉膛大小对燃料燃烧的稳定性有较大影响,如果炉膛体积过小,则燃烧的空间不够,火焰容易舔烧炉管,炉膛温度也高,不利于长周期安全运行。因此,炉膛体积热强度不允许过大,一般控制在燃油时小于125KW/m3,燃气时小于165KW/m3。
3.辐射表面热强度:辐射炉管(火筒)每单位表面积在单位时间内所传递的热量称之为炉管的辐射表面热强度,单位常为W/m2。它表示辐射传热强度的大小,与被加热介质的特性、流速、炉管(火筒)材质、炉管(火筒)尺寸、炉管的排列方式等因素有关。
4.对流表面热强度:含义同辐射热强度一样,单位也为W/m2,但它是对对流部分而言。对流表面热强度是根据管内和管外的各种数据计算出来的,与对流传热系数的关系较大。管外:烟气流速越大,外膜传热系数越高;对流平均烟气温度越高,外膜传热系数也越高;对流管外径越小,外膜传热系数也越高。管内:介质的流速越大,内膜传热系数越高;介质的粘度越小,内膜传热系数也越高。当管内为液体,控制总传热系数的主要因素还是管外条件,管内条件影响不大。
油田和长输管线加热炉指油气田和长输管道用火焰加热原油、天然气、水及其混合物等介质的专用设备。在油、气田的集油站、集气站、联合站等站库内,加热炉对原油、井产物、生产用水和天然气等介质进行加热,以满足油气集输处理工艺的要求。在原油和天然气长输管道中,经加热炉对原油和天然气进行加热,以满足长距离输送的要求。
油田和长输管线加热炉对介质进行加热所要求的温度都不高,一般不超过100℃,介质无化学变化,这与石油炼制和石油化工加热炉不同。
二、国内外加热炉的现状
目前国外发达国家在加热炉的设计方面主要向高效率、低耗能、重环保及精密化、智能化方向发展。技术优势主要在于燃烧器、炉体结构、绝热材料、自动控制与监测系统等方面。
4.热效率:它表示向炉子提供的能量被有效利用的程度,可用公式表示为η=被加热介质吸收的有效能量/供给炉子的能量。它是衡量燃料消耗、评价加热炉设计和操作水平的重要指标。
5.炉膛温度:指烟气离开辐射室进入对流室时的温度,它表征炉膛内烟气温度的高低,是加热炉操作中的重要指标。
炉膛温度高,说明辐射室传热强度大。但炉膛温度过高,则意味着火焰太猛烈,容易烧坏炉管、管板等。此外,进入对流室的烟气温度也会越高,对流炉管也容易烧坏。从保证加热炉长周期安全运转考虑,一般加热炉将这个温度控制在850℃以下。
6.排烟温度:烟气经过辐射和对流换热后,排入烟囱时的温度。排烟温度的高低决定着排烟热损失的大小,是影响热效率的重要指标。
7.炉体表面温度:即炉体表面与外界空气接触部分的即时温度,它是反映炉体保温情况和炉体热损失大小的重要指标。
8.过剩空气系数:实际供入炉膛的空气量与理论完全燃烧所需空气量的比值。过剩空气系数小于1,说明存在较大的不完全燃烧;大于1较多,说明供入的空气过多,排烟损失就越大。过剩空气系数在1.1左右为宜。
GB 3087-2008 《低中压锅炉用无缝钢管》
GB 9948-2006 《石油裂化用无缝钢管》
GB50250-2001 《钢结构工程施工质量验收规范》
GB13271-2001 《锅炉大气污染物排放标准》
GB/T19839-2005 《工业燃油燃气燃烧器通用技术条件》
第二部分 加热炉的分类、结构及其特点
3.按燃料种类分为:燃气加热炉、燃油加热炉、燃油燃气加热炉。
4.按照加热炉中被加热介质的加热方式可分为:直接加热炉(含管式直接加热炉、火筒直接加热炉)和间接加热炉(热媒间接加热炉、水套加热炉、真空加热炉、相变加热炉等)。
第2、3分类方式通常在加热炉统计中直接列出介质种类和燃料种类加以区分,加热炉的型式通常一第1、4分类表示。具体见图一:
第三采油厂加热炉学习讲义
———————————————————————————————————————————— 日期:
第一部分 基础知识
一、加热炉的定义及用途
通常所说的加热炉有油田和长输管线加热炉、石油炼制和石油化工加热炉,这里仅介绍油田和长输管线加热炉。
2.制造上,由于制造工艺和材料技术的限制,带来加热炉的使用寿命较短、单位耗钢量大、热损失大等缺陷。
3.燃烧器技术上还有差距,目前新型燃烧器主要靠进口,进口燃烧器不能适应国内现状等。
4.加热炉监控技术还不够完善。在线监控技术很少、难以实现无人值守运行、加热炉难以达到最佳经济运行状态。
三、采油三厂加热炉现状
进入21世纪以来,国内加热炉技术有了很大发展,与国外差距逐步缩小,特别是在新型高效加热炉方面设计方面已经基本跟上国际发展潮流。但是,跟上潮流不等于达到国际先进水平,工业基础、国民素质等各种因素决定了,国内加热炉设计、制造、使用等方面与发达国家还有一定差距。主要表现在:
1.设计上,对新技术的使用还处于摸索阶段,产品成熟度不够,给使用中带来了一些问题。
五、油田加热炉涉及的标准
SY/T0540-2006 《石油工业用加热炉型式与基本参数》
SY 6381-1998 《加热炉热工测定》
SY/0031-2004 《石油工业用加热炉安全规程》
SY/T0538-2004 《管式加热炉规范》
GB/T21435-2008 《相变加热炉》
SY/T5262-2009《火筒式加热炉规范》
一、加热炉的分类
油田和长输管线用的加热炉型式主要按基本结构、被加热介质种类和燃料种类进行分类:
1.按基本结构分类:管式加热炉(立式圆筒、卧式圆筒、卧式异形)、火筒式加热炉(火筒式直接加热炉、火筒式间接加热炉)两大类。
2.按被加热介质的种类分为:原油加热炉、井产物加热炉、生产用水加热炉、天然气加热炉。