[管理心语] FORD G8D详细讲解
G8D.讲义教材简体版..
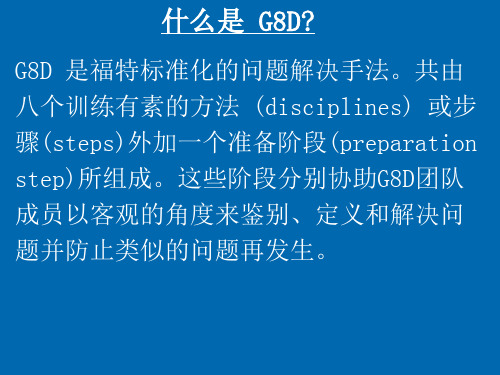
选择和验证ERA (Select and Verify an ERA)
为了要确保一个ERA能有效的保护顾客,ERA一定要在经过验证 (verify)之后才可以实施(implement)。这样才能保护客户不 会在徵状的影响被隔离之后又再遭遇了新的问题。
验证方法可包括: 测试(test)和证明(demonstration)。 用类似新行动但已证明(proven)有效的行动的结果作为新行动 的参考。 在正式发布前,审核新设计的文件(程序书,政策,规范)。
G8D团队的目标必须依靠每一位团队成员的努力才能完 成,而每一位成员要能成功的扮演好自己的角色才能让 团队运作顺畅.
每一个角色必须着重在其功能上的发挥,而非担任该角 色人员本身的特质.这样团队才能持续专注在G8D的工 作流程上,而不会胶着在人们性个不同之间造成的摩擦.
G8D团队的各个角色是互相依靠的,没有任何人能单独 完成所有的工作
紧急应变行动 (Emergency Response Action, ERA)
ERA流程: 1.选择(Select) 3.执行(Implement)
2.验证 (verify) 4.确认(Validate)
紧急应变行动ERA: 是基于手上现有的有限资料所采取的紧急应变行动。 采取ERA所付出的代价程度可大可小,这要取决于问 的本质,成本的考量,和顾客抱怨的严重度。 是马上要执行的动作,没有多少时间来对ERA做研究。
D5
cause and identify escape
point)
选择并验证永久性对策 (Choose and verify Permanent Corrective
Action, PCA)
PAST 过去 PROBLEM SOLVING
G8D步骤讲解

G8D步骤讲解CQDC(CorporateQualityDevelopmentCenter)培训2003年11月19日星期三一.STA的工作范围1.STA一般分为项目工程师,现场工程师,常驻工程师2.现场工程师对分割模式1/2供应商的主要工作:通过现场审核推进Q1;推动供应商持续改进;为改进供应商质量体系而提供技术支持;审核APQP/PPAP,确定PPAP递交等级;投产前准备及按节拍生产的审核;出现质量问题时与供应商分担等.二.FPDS(FordProductDevelopmentSytem)以J1(正式投产)为基准向前推算时间进度.在SI阶段确定供应商.对不存在设计的中国供商来说CP阶段与J1阶段是比较重要的.三.供应商质量分割(SupplierQualitySegmentation)Ford公司依据供应商的质量表现与产品的重要性将供应商分为四块模式进行管理.四.G8D(Global8DAnalyi)G8D与8D相比增加了D0与D8中的小组总结1.D0中需考虑的的问题:症状是否被定义;症状是否量化;是否需要紧急应急措施;紧急应急计划是否被验证;紧急应急措施是否补确认.D0中常使用的质量工具:趋势图;柏拉图;培因图2.D1中需考虑的问题:解决问题的领导是否确定;小组中是否有分供商与顾客;是否有技术方面的专家.3.D2中需考虑的问题:描述问题是否处在顾客的立场;问题的描述是否有开始与结束的时间;是否描述了问题发生的百分比;是否描述了问题发生的频率;是否有问题的测量报告;规范的标准是否被描述.D2常使用的质量工具:是/不是分析图;柏拉图;过程流程图;鱼刺图D2时不要假设问题发生的不成熟的理由4.D3中需考虑的问题:所有的问题产品是否被考虑;所采取临时措施的有效性;措施所用的数据是否被列出;是否满意确定的筛选方法;对措施是否进行过评估.常用的质量工具:培因图;SPC数据;FMEA5.D4:是否使用鱼刺图进行分析;是否用是/不是分析法;是否确定了一个可接受的根本原因;每一个根本原因的贡献率是否被列出;是否认识到过程与系统的根本原因;是否确定了一个逸离点;…质量工具:鱼刺图;FMEA;是/不是分析法DOE;6.D5:所需采取措施的数据是否被表明;规定的措施是否覆盖率过程原因与系统原因;措施是否充分列出了时间\\条件\\测量要求质量工具:培因图;鱼刺图;FMEA;DVP&R7D6需考虑的问题:是否列出了纠正措施的有效率;是否有培因图来验证措施的有效性;纠正措施是否列出了探测手段质量工具:培因图;是/不是分析法;FMEA;PPAP;SPC8D7需考虑的问题:PFMEA是否被审核;PFMEA是否被修订;控制计划是否被修订;工艺卡是否被修订9D8需考虑的问题:报告是否是最新经过调整;是否所有的工作都已经完成.在不同阶段可使用同一种质量工具.。
8D 质量问题解决工具详解

8D8D最早是美国福特公司使用的经典质量问题分析手法二战期间,美国政府率先采用一种类似8D的流程——“军事标准1520”,又称之为“不合格品的修正行动及部署系统”。
1987年,福特汽车公司首次用书面记录下8D法,在其一份课程手册中这一方法被命名为“团队导向的问题解决法”(Team Oriented Problem Solving)。
当时,福特的动力系统部门正被一些经年累月、反复出现的生产问题搞得焦头烂额,因此其管理层提请福特集团提供指导课程,帮助解决难题。
问题解决8步法8D(8 Disciplines)问题解决8步法8D的原名叫做8 Disciplines,意思是8个人人皆知解决问题的固定步骤。
原始是由Ford公司,全球化品质管制及改善的特殊必备方法,之后已成为QS9000/ISO TS16949、福特公司的特殊要求。
凡是做FORD的零件,必须采用8D 作为品质改善的工具,目前有些企业并非FORD 的供应商或汽车业的合作伙伴,也很喜欢用这个方便而有效的方法解决品质问题,成为一个固定而有共识的标准化问题解决步骤。
Discipline 1. 成立改善小组(Form the Team):由议题之相关人员组成,通常是跨功能性的,说明团队成员间的彼此分工方式或担任的责任与角色。
Discipline 2. 描述问题(Describe the Problem):将问题尽可能量化而清楚地表达,并能解决中长期的问题而不是只有眼前的问题。
Discipline 3. 实施及确认暂时性的对策(Contain the Problem):对于解决D2 之立即而短期行动,避免问题扩大或持续恶化,包含清库存、缩短PM时间、加派人力等。
Discipline 4. 原因分析及验证真因(Identify the Root Cause):发生D2 问题的真正原因、说明分析方法、使用工具(品质工具)的应用。
Discipline 5. 选定及确认长期改善行动效果(Formulate and Verify Corrective Actions):拟订改善计划、列出可能解决方案、选定与执行长期对策、验证改善措施,清除D4 发生的真正原因,通常以一个步骤一个步骤的方式说明长期改善对策,可以应用专案计划甘特图(Gantt Chart),并说明品质手法的应用。
G8D知识.

D1 成立团队
D2 描述问题
D3 制订执行 围堵措施
D4 寻找根因
D5 制订长期 改善措施
D6 验证长期 改善效果
D7 预防措施
D8 肯定贡献
要描述一个问题,你需要:
1. 对问题进行陈述: 是简单、简洁明了的陈述,它确定了发生问题的对象及这个
问题的缺陷,但引起这个问题的原因不确定。对问题陈述的两个步骤:
D1
D2
D3
D4
准备过程
成立团队
D8
描述问题
制订、执行围堵措施
寻找根本原因和 问题逃出点
D7
D6
D5
肯定团队与个人贡献 防止问题再发生
执行和验证 永久修正行动
制订和验证永久性 纠正措施
8D与G8D的区别:
1. G8D相对于8D而言,增加了D0(准备步骤); 2. G8D相对于8D而言,增加和强调了对问题逃出点的查找和控制; 3. G8D相对于8D而言,在软件系统和全球平台上面得到了更为全面的支持,
D6 验证长期 改善效果
D7 预防措施
D8 肯定贡献
在G8D里,把原因分成以下三类: 可能原因:任何原因,在因果图(鱼骨刺图)上描述一种结果可能发生的任何原因; 最有可能原因:以可得到的数据为基础,它可能最能解释详细的问题描述; 根本原因:一个被验证过的,可以解释问题的原因,最好能够故障再现。
通常情况下,确定根本原因有以下四个步骤: 1)回顾问题描述 2)完成变化-引起情况的比较分析 3)制定潜在的理论原因 4)确定最可能原因 验证了最有可能原因后才能得到根本原因。 建议验证的做法是被动验证和主动验证同时进行,例如,通过观测(被动验 证),找到存在问题的零件,确认前面确定的原因是否存在,如不存在,那可 能不是根本原因,如存在,通过改变确定的原因(主动验证),确认问题是否 消失,如不能消失,那么可能不是根本原因或者不止一个根本原因。
有史以来最易懂的8D,从FMEA角度看G8D报告

有史以来最易懂的8D,从FMEA角度看G8D报告D0:准备8D过程D1:组建团队D2:描述问题D3:制定临时处置措施(ICA)D4:确定并验证根本起因和遗漏点D5:选择并验证针对根本原因和遗漏点的永久性纠正措施(PCA)D6:执行并确认PCAD7:预防问题重现D8:表彰小组和个人的贡献针对每一步,我们详细介绍其使用过程:D0:准备8D过程实施本阶段的原因:G8D过程是一个可能涉及大量人力、时间和资源的过程,如果使用不适当将会浪费很多时间、人力和相关的一些资源。
D0帮助我们把焦点放在问题上,以便有效地使用资源。
本阶段实施过程:了解症状并量化症状,决定是否需要ERA,选择并验证ERA,执行并确认ERA,查看是否适用G8D标准。
紧急反应措施(ERA)是保护顾客及相关的各方不受症状的影响的任何措施,它在G8D把问题和症状区分开来确认G8D是否有必要启动时应用。
症状是可测量的事件或效果(它们必须是顾客体验到的),它表示一个或多个问题存在。
如果没有症状,你就无法得知有问题存在。
当症状能被测量或量化时,它才被考虑在内。
通常有许多工具可以用来测量并量化故障:Paynter图,柏拉图,运行(趋势)图,风险图等。
G8D的适用标准:1.症状被定义;2.确定了顾客;3.存在性能差距;4.原因未知;5.管理层致力于从根本起因的层面去解决问题,并采取预防措施防止问题再次发生;6.症状很复杂,不可能单凭一个人的能力完成。
如果六个标准都满足,并且没有其他的G8D团队为同样的或类似的问题工作,那么就应该开始G8D过程。
D1:组建团队组建团队是G8D过程中的重要部分。
团队成员的指导方针:1.团队成员的人数控制在4到10个之间;2.选择具有所需技能、知识、资源、权力等,这样的人作为团队成员来解决现有的问题;3.各类成员之间合理搭配;4.按需要调整团队成员。
G8D的过程依赖于所有团队成员的努力来达到团队的目标。
为了达到团队目标,每个成员扮演一个角色。
福特(Ford)8D培训教材

也不要写工作报告
Page 10 of 47
成员包括:
❖ 指导员(CHAMPION) 一般为主管阶层,对小组的进度有 监督, 支持及决策决定 权力.
❖ 组长(LEADER)-负责协调,活动进行的引导,汇总小组的意 见及决策并呈报,尽量不要深入某部份细节,以免迷失方向.
❖ 问5次为什么的做法:
➢对于某个问题,为何会引起?其原因①先搞明白。 ➢为何会引起原因①的发生?将原因②也搞清楚。 ➢为何会引起原因②的发生?将原因③弄明白。 ➢为何会引起原因③的发生?将原因④弄明白。 ➢为何会引起原因④的发生?将原因⑤弄明白。
Page 20 of 47
❖ 用这种方式持续地去做,根本的原因就能显現出来。 ❖ 分析出来的根本的原因必须是能导出具有効果、
且有効率的再发防止对策才行。 ❖ 要注意的是问题发生的原因不一定只有一个。
❖ 通常第一个答案不会是真正的答案 ❖ 5 Why 可以找出真正的原因 ❖ 简单的案子可能4Why,3Why或2Why即找出根本原
因,但复杂的或许要5 Why, 6 Why, 7 Why…
Page 21 of 47
做5 Why 分析时应注意事项
因会影响结果时,不能说有因果关系)。
Page 23 of 47
5 Why 范例: 为何停机
❖ 问1:为什么机器停了? 答1:因为机器超载, 保险丝烧断了
❖ 问2:为什么机器会超载? 答2: 因为轴承的润滑不足
❖ 问3:为什么轴承会润滑不足? 答3: 因为润滑系统失灵了
❖ 问4: 为什么润滑系统会失灵? 答4: 因为润滑系统的轮轴耗损了
福特公司8D的培训资料
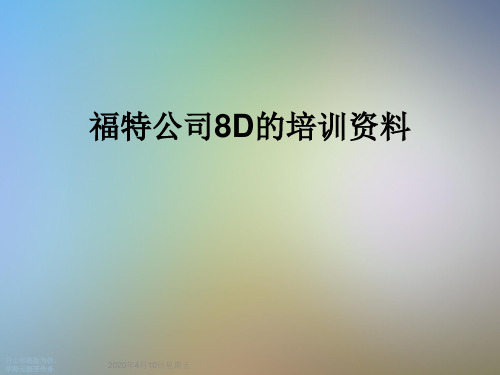
Symptoms vs. Problems
Symptoms 是显示一个或多个问题存在 的可测量的事件或结果。
Problems 是期望值的偏差,或未知原 因引起的任何有害作用。
Symptoms 是 Problems 的表现。 没有Symptoms 就不知道有 Problems
。 D0帮助我们对Symptoms 作出反应
书山有路勤为径, 学海无涯苦作舟
D0工具
当我们启动G8D时,只有Symptoms 是可以估 量或量化的。如果我们不能估量Symptoms 反应了我们没有足够的信息和充分的理由可以 启动G8D。
量化Symptoms 的数据可以从已有的数据中 得到,如保修量或保修费用,顾客满意度评估 等。也可以从其他方法来量化Symptoms。
规范等)。 因为ERA验证通常以常识为基础,很难用量化来
验证。如根据常识,对受到影响的产品停止发 运时,顾客就不会再受到影响。
书山有路勤为径,在起作用。
证实就是提供ERA运行时达到了预期目 的而又没产生新问题的有关证据。
两种验证方法: 到达顾客前的验证:测试、检查、观察
(Permanent Corrective
Actions)并客观地防止问题再发的过程。
G8D致力于寻找问题的根源、实施永久性对策 ,促进制造系统的不断改进。
一个有效的8D的实施不但可以解决问题、保护 顾客、还可以防止问题再发、有效提高产品质 量、提高顾客满意度、促使整个福特系统向世 界领先的汽车制造业迈进。
书山有路勤为径, 学海无涯苦作舟
柏拉图pareto chart
柏拉图依据费用、频率或总变差将所有的潜在 问题区域或来源作了分类。如少数问题占据了 绝大多数的费用或变差,则解决问题的精力就 要集中到这些主要原因上来。
质量管理G8D作成要领说明
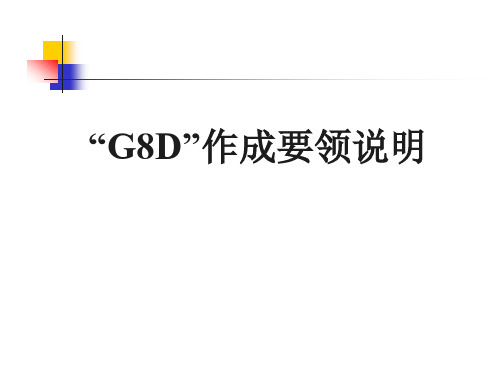
被充分地评审和修订?
2、是否对类似产品或工艺进行了措施的水平
展开?
注意:增加过程检验或作一个单独的审核,不
能算作是预防措施。Fra bibliotek有效率 实施日 %: 期:
预防措 预防措 施的有 施的实 效性 施日期
“G8D”的作成要领
D8-受表彰的小组和个人
总结小组在问题解决过程中的经验,对小组及 小组成员的贡献进行表彰。
产品或工艺名称:
公司或部门:
指发生问题的产品或涉及 指发生问题的供应商名称或及其部
的加工过程
门
“G8D”的作成要领
D0-现象:
指问题的定义和清晰/量化的描述
D0-应急反应活动:
有效率%: 实施日期:
为了不影响顾客生产,对采取的应急措施 应急措施的 应急措施
的有效性进行验证后而采取的应急活动,有效性
报告人 时间
有效率 %:
永久措 施的有 效性
实施日 期:
永久措 施的实 施日期
“G8D”的作成要领
D7-预防措施
再发防止
对相关的文件进行修订,以防止该问题及类似
问题的再发。如有必要,建议从体系或系统的
角度着手改进(包括方针、惯例、程序文件、
流程等) 。
(标准化)
采取预防措施时,通常考虑以下方面:
1、PFMEA、控制计划及相关的过程表单是否
1、是否识别出了可接受的根本原因? 2、每一个根本原因对发生本次问题的贡献率有多大? 3、找到的原因在工艺上认可了吗? 4、找到的原因在体系/体制上认可了吗?
影响比 例%
每一个根 本原因的 贡献率
“G8D”的作成要领
D5/D6-永久性的纠正措施
针对D4的根本原因(发生/流出)确定永久性的纠 正措施并进行验证。在制定永久性的纠正措施时, 应考虑以下方面:
福特8D培训资料
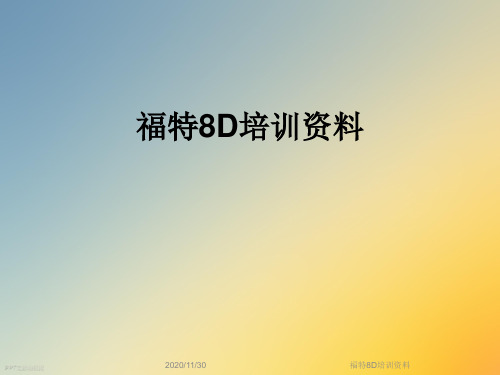
趋势图trend (run) chart
l 趋势图显示出性能随时间的变化 l Trend (Run) Chart
Source: 1 MIS Warranty (60-day sample) Vehicle Instrument Panel
PPT文档演模板
福特8D培训资料
柏拉图pareto chart
PPT文档演模板
福特8D培训资料
What is wrong with what?
l What is wrong是缺陷:产品或过程中的 有害特性。
l With what 是对象:是表现出某种缺陷的 确定的产品或过程。
l 问What is wrong with what?可以使成员 聚焦在你所需的描述问题的两个基本元 素上——缺陷和对象。
l 继续问为什么直到不能肯定的回答,如 果原因未知且需要找到根本原因,则最 后一个对象和缺陷就是问题的陈述。
l 重复问“Why is that happening to that object?” 的过程称为“repeated whys” 技巧。(为什么阶梯)
PPT文档演模板
福特8D培训资料
l D1建立团队的开展表示G8D正式启动,目的是 组织一个有所需特征和动力的人员来解决问题。
l 建立团队是G8D的一个重要要素,很少有一个 人具有所需的资源、信息和技能去解决一个复 杂的问题。但对于一个团队,可以拥有所需的 资源和发挥每一个人的技能去解决问题。
l G8D的成功依赖于团队合作,因此建立一个合 适的团队(is a team,not a group)十分重要。
PPT文档演模板
福特8D培训资料
G8D 步骤
l D0:准备开展G8D(ERA) l D1:建立8D团队 l D2:问题描述 l D3:实施临时对策(ICA) l D4:定义并验证根本原因 l D5:选择并验证永久对策 l D6:实施并证实永久对策(PCA) l D7:再发性预防措施 l D8:表彰小组和个人贡献。
ford-G8D福特公司8D培训资料
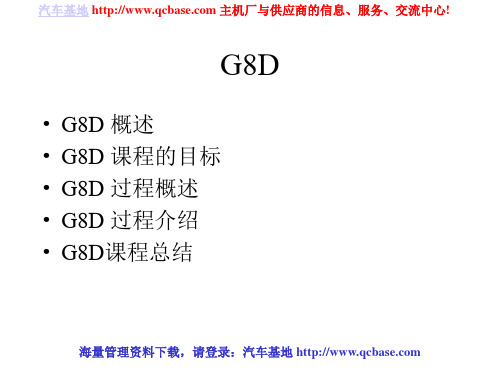
汽车基地 主机厂与供应商的信息、服务、交流中心!
G8D过程概述(续)
• D3 开发临时控制行动。
– 定义、验证和执行临时控制行动以将问题的 影响同内部和外部的顾客隔离开。临时行动 将执行到永久修正计划采用为止。证实临时 行动的有效性.。
G8D概述
• G8D是福特公司解决问题的标准方法。 • 由8个步骤和一个准备步骤组成。 • 这些步骤用来客观地确定、定义和解决 问题并防止相似问题的再次发生。
海量管理资料下载,请登录:汽车基地
汽车基地 主机厂与供应商的信息、服务、交流中心!
D0 准备G8D
• 为什么要为G8D过程作准备
– G8D的过程是很精深的。可能涉及大量的时间、人 员和资源。当然也会浪费大量的时间、人员和资源, 如果使用G8D过程是不合适的。 – G8D的使用标准帮助判别使用G8D过程是合适的。 如果不使用G8D的标准来判定是否使用G8D,那么, 您可能用精深的过程来解决每一个单一的问题。 – 福特公司的最终目标是在卓越的产品和顾客满意度 方面居于行业领先。D0允许执行(ERA)来保护顾 客。ERA也是保持顾客满意度和达到我们目标的重 要部分。
海量管理资料下载,请登录:汽车基地
汽车基地 主机厂与供应商的信息、服务、交流中心!
D0 准备G8D
• 紧急反应行动(ERA)
– 紧急反应行动是在决定是否采用G8D时用来 保护顾客和受影响的各方的任何行动。 – 顾客是经历症状的一个人、组织或驾驶员。 例如,一个驾驶员由于空调问题将车开来维 修,驾驶员就是顾客。 – 受影响的各方是指将被症状影响的人、组织 或驾驶员。例如,处理空调保修的服务人员 是受影响的各方。
• D8 表彰个人和小组的贡献
8D-讲义-8D-表格-8D-制作规范PPT课件
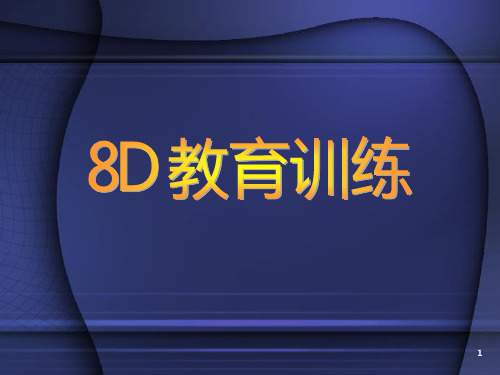
D2: Describe the Problem. 叙述问题
D3: Develop an Interim Containment Action. (ICAs) 暂时围堵行动
D4: Define and Verify the Root Cause and Escape Point. 定义并验证根本原因以及忽略点
➢ D2使公司可以通过确认”什么东西发生什么 问题”来描述内外部客户的问题,并在详细表 单中记录问题细节.
7
Overview of D3: Develop an Interim Containment Action (ICA) D3综述: 开展暂时围堵行动(ICA)
➢ D3 provides the opportunity to develop Interim Containment Actions until Permanent Corrective Actions are implemented. The ICAs isolate the effects of the problem from any internal/external customer. Also at D3, ICAs must be validated.
D7: Prevent ence. 防止再度发生
D8: Recognize Team and Individual Contributions. 肯定团队及个人的贡献
3
Terms and definitions术语和定义
ERA: Emergency Response Action . ERA: 紧急应对措施. ICA: Interim Containment Action . ICA: 暂时围堵措施 PCA: Permanent Corrective Action . PCA: 永久矫正措施 error proofing 防错 product and manufacturing process design and development to prevent manufacture of nonconforming products 防止制造不合格品的产品设计开发以及制造过程设计开发。 矫正措施(corrective action):为消除已发现的不合格或其他不期望情况的原因
福特8D培训资料教程

福特8D培训资料教程在当今复杂多变的制造业环境中,有效的问题解决方法对于企业的持续发展至关重要。
福特 8D 方法作为一种系统、全面的问题解决工具,被广泛应用于各个领域。
接下来,让我们深入了解一下福特 8D 培训资料教程。
一、什么是福特 8D福特 8D 是一种解决问题的方法,它由 8 个步骤组成,每个步骤都有其特定的目的和任务。
这 8 个步骤分别是:D1 成立小组、D2 问题描述、D3 临时措施、D4 根本原因分析、D5 长期措施、D6 措施验证、D7 预防措施、D8 小组祝贺。
二、8D 方法的特点1、系统性福特 8D 方法不是孤立地处理问题,而是将问题放在一个系统中进行全面分析。
它从问题的表象入手,逐步深入挖掘根本原因,从而制定全面、有效的解决方案。
2、团队合作解决问题需要多个部门和专业人员的共同参与。
8D 方法强调成立跨职能小组,汇集各方的知识和经验,共同攻克难题。
3、以数据为依据在问题解决过程中,8D 方法要求基于客观的数据和事实进行分析,避免主观臆断和猜测。
4、预防为主除了解决当前的问题,8D 方法更注重采取预防措施,防止类似问题的再次发生。
三、8D 方法的步骤详解1、 D1 成立小组小组成员应具备解决问题所需的专业知识和技能。
小组组长负责协调和推进问题解决的进程。
2、 D2 问题描述清晰、准确地描述问题是解决问题的关键。
问题描述应包括问题的具体表现、发生的时间、地点、影响范围等信息。
3、 D3 临时措施在找到根本原因和长期解决方案之前,需要采取临时措施来控制问题的影响,如对不合格产品进行隔离、筛选等。
4、 D4 根本原因分析运用各种工具和方法,如鱼骨图、5Why 分析法等,深入挖掘问题的根本原因。
5、 D5 长期措施根据根本原因,制定切实可行的长期解决方案。
长期措施应能够彻底解决问题,并具有可持续性。
6、 D6 措施验证对实施的长期措施进行效果验证,确保问题得到有效解决。
7、 D7 预防措施为了防止类似问题的再次发生,制定预防措施并纳入相关的管理体系中。
- 1、下载文档前请自行甄别文档内容的完整性,平台不提供额外的编辑、内容补充、找答案等附加服务。
- 2、"仅部分预览"的文档,不可在线预览部分如存在完整性等问题,可反馈申请退款(可完整预览的文档不适用该条件!)。
- 3、如文档侵犯您的权益,请联系客服反馈,我们会尽快为您处理(人工客服工作时间:9:00-18:30)。
[质量书籍] FORD G8D详细讲解(持续更新中)G8D概述G8D是福特标准化的解决问题的方法。
它由8个步骤和1个准备步骤组成,这些步骤分别协助G8D团队成员以客观的角度来确定、定义和解决问题并防止类似的问题再发生。
在开始我们的讲解之前,我想先谈谈以下两点:1.问题还是机会?在每一个问题的背面都隐藏着它的反面-机会,关键是我们能否去除它的伪装,找到机会--无名我想负责跟踪质量的每个人都可能碰到过这样的情况:出了个质量问题,你一看,咿……这个问题我们在去年或者以前不是解决过了吗?为什么现在又出来了?如果这种事情,很不幸发生在你们的身上的话,我可以想象你们会有多恼火,一次又一次花费大量的精力在相同的问题上。
因此,从系统上评估影响并从根本上解决问题在长远来说,提供了节省时间、金钱和资源的机会。
但是能否把握这种机会的前提是:我们是否知道真正的问题所在。
2.问题的认识不管露在水上的冰山一角有多大,80%仍然是在水面之下,问题也是一样。
不管从表面上看来,问题有多严重或者压力有多大,它仅仅是问题的表象。
表象可能小到只是个小缺陷,也可能大到停产、召回。
这里提到的冰山一角,其实就是二八原则,通过对20%的表象的研究,找到机会,解决80%的问题。
以上是我觉得大家对问题应该持有的态度。
G8D的背景和优点1987年,福特汽车公司开始部署8D,解决内部过程中和在其整个北美一级供应商的问题。
由于它纳入了朱兰,戴明等的思想,此后不久,获得世界范围的承认和执行。
1995年,福特汽车组建跨组织的指导小组,将该过程进行标准化并建立起全球G8D数据库系统,以避免不同区域及国家的差异。
G8D集合了团队工作、经验学习、鱼骨刺图、头脑风暴、FMEA等各种工具,因此不仅仅是现在大家对其比较单薄的认识,我会在后续给大家一一展示,目前大家所接触到得G8D,只是G8D的思路和方法,并没有机会进入到FORD的数据库系统,使用G8D软件在数据库中查询、更新和提交。
综上,归纳G8D作用如下1.G8D是一种标准化的解决问题的方法,2.G8D是QS 9000, ISO 9000等其它标准的一部分,3.G8D给福特,或者广泛点来说-质量人,提供了一种共通的语言。
DO:准备G8D1.为什么要为G8D过程作准备G8D的过程是很精深的,前面已经提到部分工具,后续还会继续介绍。
可能涉及大量的时间、人员和资源(通常来说,1个标准的G8D,需要90天的时间)。
如果使用不适当(并不是所有的问题都适合采用G8D)将会浪费更多的时间、人力和相关的资源。
D0帮助你把焦点放在真正需要采用G8D解决的问题上,以便有效的地使用资源。
2.D0需要做什么采取紧急响应措施ERA(Emergency Response Action)确定是否适合采用G8D3.紧急响应措施ERA(Emergency Response Action)定义:紧急响应措施(ERA)确认G8D是否必要时或之前所采取的措施,目的在于保护顾客及相关的各方不受故障现象影响。
那么谁是顾客?谁又是相关的各方呢?顾客是指经历故障现象的一个人、组织或驾驶员;受影响的各方是指将被故障现象影响的人、组织或驾驶员。
例如:一个驾驶员由于空调问题将车开来维修,驾驶员就是顾客;处理空调保修的服务人员是相关的各方。
思考题:一个驾驶员载着他的朋友一起,由于空调问题,将车开来到4S店来找维修人员维修,请问,在此案例中,谁是顾客,谁是受影响的各方?细化:当现场发生问题时,顾客反馈给你的可能就是一个故障现象,例如:车门打不开,空调不制冷、零件装不上。
什么原因,它们不知道,甚至并不知道是不是你的零件的问题。
你不能要求你的顾客跟你清楚你们自己零件一样了解你的零件。
因此,你需要时间去了解更多的信息或者再做相关的初步调查。
而在你调查这段时间里面,怎么样来保证说不合格的件不流出到底最终顾客手上,造成影响,你需要采取措施。
因此,ERA有以下特点:ERA是基于你手头现有的信息而制定的措施ERA可能是大到影响停止所有发运,也可能是小到什么都不用做ERA可能是须立即执行的措施——你不必花太多时间去研究应急措施ERA不一定是必需的,根据问题的严重性和顾客的影响来决定是否需要ERAERA是在成立C8D小组之前实施的,通常由监督人(对问题负责并有权解决的人)决定是否执行ERA。
有时,ERA可能在量化数据收到前执行。
在任何情况下都需要评估是否需要ERA。
有时需要不止一个ERA来完全保护我们的顾客。
例如,一个ERA用来保护顾客,另一个用来保护他们免受第一个ERA带来的副作用。
通常的ERA有哪些?1.停产(停产了,当然没有不合格件流出了,自然不会对顾客和相关的各方产生影响)2.挑选(挑出合格件,不让不合格件流出)3.停止发货、换货、紧急空运物料、100%检查等等例如一个水坝有一个小洞正在漏水,一个小孩看见后立即用自己的手指塞住水坝上的洞,从而挽救了整个村子。
ERA就是:小孩用手指塞住水坝上的洞,阻止水的流出ERA的实施和确认:实施ERA后,必须确认ERA能够起作用。
提供证据证明ERA达到了目的并且没有引起新的问题。
验证主要分成两块,到达顾客前的验证和顾客之后的确认。
到达顾客前的验证主要是用来确定我们的产品是否符合设计的要求,主要方式是:1)测试2)检测3)观察4)关于产品和过程的质量检查顾客确认为顾客反馈,主要是用来确定采取ERA的件之后,原来的故障现象是否已经消除。
通常使用Paynter图可以用来确认ERA。
例如:有个零件,顾客反馈非常难装配,由于涉及到几个相关零件,而暂时也不知道哪个零件不合格,那么为了满足生产,可能ERA就是对其中的某个零件进行扩孔,如从∮10改到∮12,那么在选择和验证该ERA的时候,可能就需要考虑扩孔后对强度、装配定位等等是否有影响,并通过相关的实验、或CAE分析、或者借鉴以前的经验进行验证,如无风险,可采取。
那么采取之后,也就是实施之后,到达顾客前,我们当然需要通过检测等方式去测量我们的∮10孔是否改到∮12,而不是∮11或者∮13,要不然不进行测量,直接送到顾客,又发现装配不上,这个时候不仅没有起到作用反而误导了大家,时间也白白浪费掉了,更谈不上支持生产了.OK,如果扩孔后没问题,那么零件给了顾客之后,顾客使用新零件装配,是否还存在难装配这样一个故障现象?如果没有的话,那就是ERA确认有效;当然,中间还会涉及到以下几点,因情况不同,但需要注意:1.ERA理论上要求在24小时内实施;2.如果真的从∮10改到∮12,那么需要顾客的确认;3)ERA的件需要考虑增加标识,以进行区分。
综上:我们可以看出,ERA主要针对的是顾客经历的故障现象的消除。
前面也讲到了,在D0阶段,我们只接到了顾客的抱怨,并不知道故障现象之后的问题是什么,更谈不上原因的分析了。
而由于顾客生产的压力等各种原因,时间紧急,又不能给顾客造成损失,因此我们采取ERA,让他们不再受这种故障现象的困扰。
给我们腾出时间,去找问题和分析原因,进行后续工作。
但要强调的一点就是:不要以为有了ERA,顾客没有抱怨了,我们就可以高枕无忧,或者舒缓后续的工作。
前面ERA的细化中提到:通常由监督人(对问题负责并有权解决的人)决定是否执行ERA。
有时,ERA可能在量化数据收到前执行,然后再看看ERA通常的方式。
为什么要有监督人或公司高层来决定是否适合采用ERA?我们可以看到ERA通常会有比较大的影响,或者涉及到额外费用、人力和资源的投入,是不经济的,所以我们要做的就是尽快进行后续工作,缩短ERA的时间。
由于8# sky66666 提到不清楚怎么样使用Paynter图来确认ERA。
我结合上面的举例,简单说明下:从附件简示图上可以看出,实施之后,故障现象消除,确认有效。
Paynter图举例.jpg (14.49 KB)G8D的适用标准:以上我们讲解了D0中的ERA,那么还有一个重点就是判断是否采用G8D这种方法来解决问题。
那么在列出具体的判定标准之前,为便于后续大家的理解,我想先跟大家明确一个概念:故障现象和问题。
什么是故障现象,什么是问题,我想大家听起来都觉得可以理解,但是在实际操作中却又非常容易混淆,因此会通过比较详细的例子来给大家建立一个比较深的印象。
下面给出故障现象和问题的定义;1.故障现象是指可测量的事件或效果(它们必须是顾客体验到的)。
它表示一个或多个问题存在。
2.问题是指同期望有偏差或任何由未知原因引起的有害的后果。
3.故障现象是问题的显示4.G8D过程区别了故障现象和问题。
适用标准的大部分是故障现象。
没有故障现象,不会知道有问题。
例如在水坝漏水的案例中:现象是水坝漏水,问题就是水坝上有小洞。
思考题:下面冰激凌的故事是来自本论坛上,在此对原作者表示感谢,在此引用只是想大家能够更好的理解故障现象和问题。
希望大家能够在看完这个小故事后,回帖告诉我,你们觉得在此案例中,什么是故障现象,什么是问题?香草冰激凌的故事这是一个发生在美国通用汽车的客户与该公司客服部间的真实故事。
有一天美国通用汽车公司的庞帝雅克(Pontiac)部门收到一封客户抱怨信,上面是这样写的∶“这是我为了同一件事第二次写信给你,我不会怪你们为什么没有回信给我,因为我也觉得这样别人会认为我疯了,但这的确是一个事实。
”“我们家有一个传统的习惯,就是我们每天在吃完晚餐后,都会以冰淇淋来当我们的饭后甜点。
由于冰淇淋的口味很多,所以我们家每天在饭后才投票决定要吃哪一种口味,等大家决定后我就会开车去买。
”“但自从最近我买了一部新的庞帝雅克后,在我去买冰淇淋的这段路程问题就发生了。
”“你知道吗?每当我买的冰淇淋是香草口味时,我从店里出来车子就发不动。
但如果我买的是其它的口味,车子发动就顺得很。
为什么这部庞帝雅克当我买了香草冰淇淋它就发不动,而我不管什么时候买其它口味的冰淇淋,它就一尾活龙?为什么?为什么?”事实上庞帝雅克的总经理对这封信还真的心存怀疑,但他还是派了一位工程师去查看究竟。
当工程师去找这位仁兄时,很惊讶的发现这封信是出之于一位事业成功、乐观、且受过高等教育的人。
工程师安排与这位仁兄的见面时间刚好是在用完晚餐的时间,两人于是一个箭步跃上车,往冰淇淋店开去。
当他们买好香草冰淇淋回到车上后,车子果然发不动了。
这位工程师之后又依约来了三个晚上。
第一晚,巧克力冰淇淋,车子没事;第二晚,草莓冰淇淋,车子也没事;第三晚,香草冰淇淋,车子发不动。
这位思考有逻辑的工程师,到目前还是死不相信这位仁兄的车子对香草过敏。
因此,他仍然不放弃继续安排相同的行程,希望能够将这个问题解决。
工程师开始记下从开始到现在所发生的种种详细资料,如时间、车子使用油的种类、车子开出及开回的时间……,根据资料显示他有了一个结论,这位仁兄买香草冰淇淋所花的时间比其它口味的要少。