ENX300 Lesson 11
MAX300系列NanoMax 3-Axis Flexure Stage 用户手册说明书

MAX300 Series NanoMax 3-Axis Flexure StageUser GuideContentsChapter 1 Safety (3)1.1Safety Information (3)1.2General Warnings (3)Chapter 2 Introduction (4)2.1Description of the NanoMax TS 3-Axis Flexure Stage (4)2.2Component Identification (4)Chapter 3 Operation (8)3.1Manual Differential Drives and Differential Micrometer Drives (8)3.2NanoStep Motor Drives (8)3.3Piezo Actuators (9)Chapter 4 Installation (10)4.1Unpacking (10)4.2Attaching to a Work Surface (10)4.3Calibration of Motor Drives (10)4.4Fitting and Removal of Drives (11)4.5Orienting the Moving Platform (12)4.6Mounting Equipment. (13)4.7Transportation. (13)4.8Dimensions (14)Chapter 5 Specifications (17)Chapter 6 Parts and Consumables (18)6.1Parts List (18)Chapter 7 Regulatory (19)7.1Declarations Of Conformity (19)7.2Waste Electrical and Electronic Equipment (WEEE) Directive (20)Chapter 8 Thorlabs Worldwide Contacts (23)2HA0094T Rev 11 April 20113Chapter 1Safety1.1Safety InformationFor the continuing safety of the operators of this equipment, and the protection of the equipment itself, the operator should take note of the Warnings, Cautions and Notes throughout this handbook and, where visible, on the product itself.The following safety symbols may be used throughout the handbook and on the equipment itself.1.2General WarningsGiven when there is a risk of injury from electrical shock.Given when there is a risk of injury to users.Given when there is a risk of damage to the product.Clarification of an instruction or additional information.If this equipment is used in a manner not specified by the manufacturer, the protection provided by the equipment may be impaired. In particular,excessive moisture may impair operation.Spillage of fluid, such as sample solutions, should be avoided. If spillage does occur, clean up immediately using absorbant tissue. Do not allow spilled fluidto enter the internal mechanism.Chapter 2Introduction2.1Description of the NanoMax TS 3-Axis Flexure StageThe NanoMax 3 axis flexure stage has been designed to integrate seemlessly into the Thorlabs Modular Electronic System and provide nanometric positioning on three orthogonal axes. It is suited to the alignment of optical fibres, waveguides, optoelectronic packages and any other high resolution alignment or positioning application including general purpose laboratory tasks. The innovative flexure design, combined with the system of modular drives, offers exceptional performance and flexibility.Three types of drive are available, the DRV001 stepper motor drive, the DRV3 differential micrometer and the DRV004 thumbscrew. Also available are two external piezo actuators which increase the piezo travel to 40 µm or 100 µm.2.2Component Identification2.2.1NanoMax StageThe NanoMax-TS 3 axis flexure stage is available in three versions; piezo-actuated with feedback on all axes, piezo-actuated without feedback and without piezo actuation, as shown in Fig. 2.1 to Fig. 2.4.Fig. 2.1 MAX301 NanoMax piezo-actuated stage with feedback on all axes45MAX300 Series 3-Axis Flexure StagesFig. 2.2 MAX302 NanoMax piezo-actuated stage without feedbackThe piezo-actuated models deliver 20 microns of travel, each piezo channel has a coaxial SMC connector (see Fig. 2.1 and Fig. 2.2). In addition, the NanoMax 301 has a 7-pin LEMO connector for each feedback channel (see Fig. 2.1). A corresponding number of leads for connection to the Thorlabs piezoelectric controllers are also supplied.The piezo-actuated models deliver 30 microns of travel, with a coaxial SMC connector for each piezo channel.Fig. 2.3 Feedback Lemo connector pin functionsPin Description1+15 V2Oscillator +30 V4Sig Out -5Sig Out +6-15 V7TravelSMC connectorsChapter 2Fig. 2.4 MAX303 NanoMax without piezo-actuation The NanoMax 303 has no electrical connections.2.2.2Drives and ActuatorsThere are three types of drive available for the NanoMax, a motorized drive as shown in Fig. 2.5. and two manual drives as shown in Fig. 2.6. In addition, external piezoNoteThe DRV001 stepper motor drive must be used in conjunction with the BSC benchtop driver or the MST601 control module. It cannot be driven by theTST001 T-Cube driver.Fig. 2.5 DRV001 NanoStep motor drive6HA0094T Rev 11 April 2011MAX300 Series 3-Axis Flexure StagesChapter 3Operation3.1Manual Differential Drives and Differential Micrometer Drives3.1.1Adjusting Micrometer DrivesTurn the coarse adjustment clockwise until the platform of the NanoMax begins to move. By use of the fine adjustment, sub-micron resolution is now achievable.MAX300 Series 3-Axis Flexure StagesTable 3.1 Standard configurations for motor drivesParameter ValueMaximum Velocity 2.5 mm s-1Minimum Velocity1mm s-1Slope 1 mm s-2Backlash control1Backlash distance–0.01 mmMode LinearMicrosteps to units40000Offset 3 mmMinimum position0.00 mmMaximum position 4.00 mmThe NanoStep modular drives have no +ve limit switch. The drive reachesa mechanical stop at a position dependent on the axis to which it isattached. The design is such that occasional driving into the stop will notcause any damage.If the axis is driven towards the –ve limit switch, at a certain position theplatform stops moving while the drive itself continues to move until thelimit switch is reached. The drive must then be moved positively by acertain distance before the platform begins to move. This distance is justless than the offset.When creating a program to control the NanoMax, it is preferable to avoidrunning into the +ve limit.3.3Piezo ActuatorsPiezo actuators are used to give nanometric positioning of the top platform over a range of 20 microns (40 µm or 100 µm if external piezo actuators are used). They can also modulate the position of the platform at high frequency.On a piezo-actuated NanoMax, position feedback may be incorporated on the linear axes to enhance the repeatability and linearity of piezo motion.The piezo-actuated NanoMax should be used together with one of the Thorlabs piezoelectric controllers – see the handbook for the relevant piezoelectric controller.The NanoMax monitors the ambient temperature using thermistors and applies small movements to the stage to compensate for the expansion and contraction of metals within the stage. Note that this compensation is active only when the associated piezo controller is set to ‘closed loop’ (feedback on) mode – see the relevant piezo controller handbook for more details on the operation of piezo actuators.910Chapter 4Installation4.1Unpacking 4.2Attaching to a Work SurfaceThe base of the NanoMax is provided with a number of fixing holes and slots for attachment to metric or inch optical tables, as supplied by Thorlabs and other manufacturers. Bolting the unit down minimizes the risk of damage from dropping.When mounting the NanoMax close to other equipment, ensure that the travel of the moving platform is not obstructed. If the moving platform is driven against a solid object, damage to the internal flexures could occur. The range of travel on each axis is 4 mm total, that is ± 2 mm about the nominal position.4.3Calibration of Motor DrivesCalibration enables the server to correct for any mechanical errors inherent in the system. Mechanical components, such as the leadscrew and linkages, can be machined only within a certain tolerance, e.g. the leadscrew may be nominally 1mm but actually 1.0005mm, giving a 0.5 micron error. In practice, these errors accumulate from a number of sources, however they are repeatable and therefore, can be compensated.During calibration, the total positional error is measured at a large number of points and these errors are stored as a look up table (LUT). The LUT is saved as a calibration file, one file for each axis on a particular stage. These files are then linked to the appropriate axis as part of the Stage association process performed using the APT Config utility. Whenever the stage is moved, the LUT is consulted to ascertain the precise movement required to achieve the demanded position.Retain the packing in which the unit was shipped, for use in futuretransportation.Once removed from its packaging, the NanoMax is easily damaged by mishandling. The unit should only be handled by its base, not by the topplatform or any attachments to the top platform.This section is applicable only to motor drives when a calibration hasbeen requested.MAX300 Series 3-Axis Flexure Stages When the stage is calibrated at the factory, the stepper motor controller, channel number, motor, stage and axis are configured in a certain manner. For the calibration to be effective, it is important to re-assemble the stage with the motors fitted to the same axis for which they were calibrated. This information is contained in the table below.Furthermore, the correct calibration files must be associated with the correct stage axis. In this regard, it is important to confirm what stage axes are connected to particular channels on particular motor units. It is then a simple task to use the APT Config utility to associate the correct calibration file with a particular serial numbered hardware unit and channel.The use of a calibration file is optional. Without it, the repeatability and resolution of the stage are unaffected, but no compensations are made to enhance the accuracy Details on assigning a calibration file are contained in the APTConfig On Line Helpfile.Table 4.1 Calibration detailsNanoMax serial numberAxis Motor Serial number Calibration File RemarksXYZ4.4Fitting and Removal of DrivesThis section is applicable only to Part Numbers MAX301, MAX302 and MAX303.The following procedure details how to fit a drive to the NanoMax 300 stage. A micrometer drive is shown for illustration purposes but the procedure is equally applicable to motor or thumbscrew actuators.1)For manual drives, rotate the coarse adjuster counter-clockwise a few turns toretract the drive rod. For motor drives, retract the drive rod by turning the manual adjuster clockwise.Then, referring to Fig. 4.1 on the next page...2)Insert the drive into the mounting bush.3)Tighten the knurled locking ring until finger tight.To remove a drive reverse the above procedure.When removing a motor drive, rotate only the locking ring, do not rotatethe motor body.11Chapter 4Fig. 4.1 Micrometer drive inserted into mounting bush4.5Orienting the Moving PlatformThe stage is normally oriented such that the X axis is the optical axis. If it is necessary to change the orientation for left or right-handed use, the Y axis becomes the optical axis as shown in Fig. 4.2 (The Z axis is always vertical).Fig. 4.2 Platform orientation12HA0094T Rev 11 April 201113MAX300 Series 3-Axis Flexure Stages4.6Mounting Equipment.Thorlabs manufacture a variety of fibre chucks, holders and fixtures to fit the NanoMax stage. However, custom hardware can be designed using a tongue-in-groove arrangement and the cleats provided, see Fig. 4.3 for a typical fixture.Fig. 4.3 Typical fixture, view along X-axis, length as required4.7Transportation.When attaching accessories (e.g. fiber holders) to the top platform or angle brackets (e.g. AMA007 and AMA009) to the side of the unit, do not use long bolts which protrude into the internal mechanism as this couldcause damage to the internal flexures.The weight attached to the moving platform must not exceed 1 kg.Do not apply excessive forces to the moving platform.CautionThe drives should be removed before transporting the NanoMax.When packing the unit for shipping, use the original packing. If this is not available, use a strong box and surround the NanoMax with at least 100mm of shock absorbent material.all dimensions in mmChapter 44.8DimensionsFig. 4.4 Dimensions – top platform14HA0094T Rev 11 April 2011MAX300 Series 3-Axis Flexure Stages 4.8.2Fig. 4.5 External piezo actuatorsFig. 4.6 Dimensions – modular drives15Chapter 44.8.4NanoMax 3-Axis StageFig. 4.7 Dimensions – NanoMax 3-axis stage16HA0094T Rev 11 April 201117MAX300 Series 3-Axis Flexure StagesChapter 5Specifications. .ParameterValueWeight (without drives):800 g Load capacity: 1 kgTravelManual (coarse) and motor4 mmManual (fine)300µm Piezo20 micronResolutionManual (coarse)0.5mm per revolutionManual (fine)50µm per revolution Motor0.06 µm min incremental movementPiezo (without feedback)20 nm Piezo (with feedback)5 nmArcuate displacement (maximum):80 micronThe resolution of a manual drive corresponds to a 0.5 degree adjustment of the thimble; the actual resolution obtained depends on the skill of zthe user. The resolution of the motor drives is the smallest step that can be executed (i.e. 1 microstep). The resolutions of the piezo actuators arethose typically obtained using Thorlabs controllers.Power supplyPiezoactuated NanoMax Nominal maximum input voltage:75 V Absolute maximum input voltage:100 V Stepper MotorMaximum input voltage:24 VThe NanoMax should only be used in conjunction with the appropriateThorlabs Piezoelectric Controllers.Chapter 6Parts and Consumables6.1Parts ListPart Number DescriptionMAX316D and MAX316D/M NanoMax stage with differential micrometer drives MAX315D and MAX315D/M NanoMax stage with piezo actuator and differentialmicrometer drivesMAX314D and MAX314D/M NanoMax stage with feedback piezo actuator anddifferential micrometer drives.MAX343 and MAX343/M NanoMax stage with stepper motor drives.MAX342 and MAX342/M NanoMax stage with piezo actuator and stepper motordrives.MAX341 and MAX341/M NanoMax stage with feedback piezo actuator andstepper motor drives.MAX303 and MAX303/M NanoMax stage onlyMAX302 and MAX302/M NanoMax stage with piezo actuatorMAX301 and MAX301/M NanoMax stage with feedback piezo actuator. 166038SMC connector lead134667LEMO connector lead131030Mounting cleat120992Cable clampha0094T Handbook18Chapter 7Regulatory7.1Declarations Of Conformity7.1.1For Customers in EuropeThis equipment has been tested and found to comply with the EC Directives89/336/EEC ‘EMC Directive’ and 73/23/EEC ‘Low Voltage Directive’ as amended by 93/68/EEC.Compliance was demonstrated by conformance to the following specifications which have been listed in the Official Journal of the European Communities:Safety EN61010: 2001 Installation Category II, Polution Degree II.EMC EN61326: 19977.1.2For Customers In The USAThis equipment has been tested and found to comply with the limits for a Class A digital device, persuant to part 15 of the FCC rules. These limits are designed to provide reasonable protection against harmful interference when the equipment is operated in a commercial environment. This equipment generates, uses and can radiate radio frequency energy and, if not installed and used in accordance with the instruction manual, may cause harmful interference to radio communications.Operation of this equipment in a residential area is likely to cause harmful interference in which case the user will be required to correct the interference at his own expense.Changes or modifications not expressly approved by the company could void the user’s authority to operate the equipment.19Chapter 77.2Waste Electrical and Electronic Equipment (WEEE) Directive7.2.1ComplianceAs required by the Waste Electrical and Electronic Equipment (WEEE) Directive of the European Community and the corresponding national laws, we offer all end users in the EC the possibility to return "end of life" units without incurring disposal charges.This offer is valid for electrical and electronic equipment•sold after August 13th 2005•marked correspondingly with the crossed out "wheelie bin" logo (see Fig. 1)•sold to a company or institute within the EC•currently owned by a company or institute within the EC•still complete, not disassembled and not contaminatedFig. 7.1 Crossed out "wheelie bin" symbolAs the WEEE directive applies to self contained operational electrical and electronic products, this "end of life" take back service does not refer to other products, such as •pure OEM products, that means assemblies to be built into a unit by the user (e. g.OEM laser driver cards)•components•mechanics and optics•left over parts of units disassembled by the user (PCB's, housings etc.).If you wish to return a unit for waste recovery, please contact Thorlabs or your nearest dealer for further information.7.2.2Waste treatment on your own responsibilityIf you do not return an "end of life" unit to the company, you must hand it to a companyspecialized in waste recovery. Do not dispose of the unit in a litter bin or at a publicwaste disposal site.20HA0094T Rev 11 April 2011MAX300 Series 3-Axis Flexure Stages 7.2.3Ecological backgroundIt is well known that WEEE pollutes the environment by releasing toxic products during decomposition. The aim of the European RoHS directive is to reduce the content of toxic substances in electronic products in the future.The intent of the WEEE directive is to enforce the recycling of WEEE. A controlled recycling of end of life products will thereby avoid negative impacts on the environment.2122Chapter 8Thorlabs Worldwide ContactsUSA, Canada, and South America Thorlabs, Inc.435 Route 206Newton, NJ 07860USATel: 973-579-7227Fax: 973-300-3600 (West Coast) email:********************* Support:************************ EuropeThorlabs GmbHHans-Böckler-Str. 685221 DachauGermanyTel: +49-(0)8131-5956-0Fax: +49-(0)8131-5956-99www.thorlabs.deemail:*******************UK and IrelandThorlabs Ltd.1 Saint Thomas Place, Ely Cambridgeshire CB7 4EXGreat BritainTel: +44 (0)1353-654440Fax: +44 (0)1353-654444www.thorlabs.deemail:*****************.com Support:*************************** FranceThorlabs SAS109, rue des Côtes78600 Maisons-LaffitteFranceTel: +33 (0) 970 444 844Fax: +33 (0) 811 381 748www.thorlabs.deemail:*********************ScandinaviaThorlabs Sweden ABBox 141 94400 20 GöteborgSwedenTel: +46-31-733-30-00Fax: +46-31-703-40-45www.thorlabs.deemail:************************ JapanThorlabs Japan Inc.Higashi IkebukuroQ Building 1st Floor 2-23-2Toshima-ku, Tokyo 170-0013JapanTel: +81-3-5979-8889Fax: +81-3-5979-7285www.thorlabs.jpemail:*****************ChinaThorlabs ChinaOasis Middlering Centre3 Building 712 Room915 Zhen Bei RoadShanghaiChinaTel: +86 (0)21-32513486Fax: +86 (0)21-32513480email:***********************2324Thorlabs Ltd.Saint Thomas Place, Ely Cambridgeshire CB7 4EX, UKTel:+44 (0) 1353 654440Fax:+44 (0) 1353 Thorlabs Inc.435 Route 206 North Newton, NJ07860USATel:+1 973 579 7227Fax:+1 973 300 。
布希安全系统产品说明书

Connector
Screw terminal block
* Technical performance data acc. to IEC 60268-5 Mechanical
Dimensions (L x Dmax)
499 x 490 mm (20 x 19.6 in)
Weight
4.5 kg (9.9 lb)
LBC 3484/00 Electrical*
Maximum power
75 W
Rated power
50 / 25 / 12.5 W
Sound pressure level at 50 W / 1 W (1 kHz, 1 m)
127 dB / 110 dB (SPL)
Effective frequency range (-10 dB)
Color
Light gray (RAL 7035)
Cable diameter Environmental
6 mm to 12 mm (0.24 in to 0.47 in)
Operating temperature
-25 ºC to +55 ºC (-13 ºF to +131 ºF)
Storage and transport temperature
CE-label LBC3482/00
CE-label LBC3483/00
Bosch Security Systems B.V.
Installation note
2016.5 | V1.01 |
Bosch Security Systems B.V. Torenallee 49 5617 BA Eindhoven Netherlands © Bosch Security Systems B.V., 2016
Connect X300 智能设备安装说明说明书

INSTALLATION INSTRUCTIONS Connect X300DescriptionConnect X300 is a physical device that is the gateway connection between a Cloud service and a controlled/monitored system. This system in a building can include fire alarm control panels, devices, sensors, detectors, etc.X61X60X63X30X31X1 P1X2 P1X70ON/OFF X80L+MEARTH SCREWX62NOT USEDNOT USEDNOT USEDNOT POWER SUPPLYFIRE PANEL INTERNET ACCESSFigure 1Connect X300 GatewayConnections and Indicators•X1P1: Connection to Desigo Fire Safety Modular/Cerberus PRO Modular via FCM2041-U2/-U3 Operator Interface.Connection to Desigo FC2025/FC2050 and Cerberus PRO FC922/FC924 via FCM2018/2019/2035-U2/-U3 Operating Units.Connection to Desigo FV2025/2050 and Cerberus PRO FV922/924 via VCA2002-A1 Card Cage.X2P1: Connection to internet networkFeatures• Two Ethernet ports for WAN and LAN• Remote firmware and configuration data update over the IP Interface • LED indication of activities and state • Operating voltage DC 24V • Max current load: 515mA DC• Plug-in screw terminal block for supply •Mounting on wall using enclosuresDepending on firmware, the following functions are supported (examples):• Multi-site management • Remote monitoringApplicationThe device integrates Desigo Fire Safety Modular, Cerberus PRO Modular, DesigoFC2025/FC2050/FV2025/FV2050, and Cerberus PRO FC922/FC924/FV922/FV924 fire panels over IP. It transmits data to the cloud over IP networks or over mobile networks (3G/4G/LTE).FunctionsThe Connect X300 provides two integration levels to connect fire alarm control panels to the cloud: System integration (between the Connect X300 and the fire panels) and cloud integration (between the ConnectX300 and the cloud). The Connect X300 supports Ethernet and 3G/4G/LTE for cloud connectivity.Mounting and WiringThe Connect X300 can be mounted inside the ENCL-01, P/N S54465-C63-A1, or PAB-ENCL Siemens enclosures using adaptor plates. Adaptor plate CGAP, P/N S54811-B101-A1, is used with the ENCL-01 enclosure while adaptor plate CGAP2, P/N S54811-B102-A1, is used for the PAB-ENCL enclosure. Refer to Figures 2 through 6.Wiring the Connect X300 Gateway inside PAB-ENCL EnclosuresTo connect the ethernet cable, see Figure 3. Use knockouts from the right side; wires are considered Power Limited. To connect the power to the Connect X300 Gateway, see Figure 2.Option: The FP2011-U1 Power Supply can be used with the cable provided to connect the power fromthe FP2011-U1 Power Supply to the Connect X300 Gateway. Use knockout close to the location of the Power Supply to enter the box. Wires are considered Non-Power Limited.Modular/Cerberus PRO Modular Enclosure)DETAIL E SCALE 2 : 512-22 AWG BlackWires are Power LimitedFor UL applications: wiring limited to20 ft in conduit located in the same room.For ULC applications: wiring inmetallic conduit located in the same roomNOTE : All high voltage and non-power limited wiring must be kept separate from power limited wiring. A ¼” separation must be maintained with high voltage and non-power limited wiring running in separate conduit openings from power wiring. Wiring within the cabinet should be routed around the perimeter of the cabinet.Figure 2Desigo Fire Safety Modular/Cerberus PRO Modular System Power Connection to Connect X300Rear View ofFCM2041-U2/-U3Operator Interface (Located in the S55842-Z121-A100Connect X300GatewayEthernet Cable 6 ft. long (User Provided)Wires are Power LimitedFor UL applications: wiring limited to20 ft. in conduit located in the same room.For ULC applications: wiring inmetallic conduit located in the same room not exceeding 18 m.NOTE : All high voltage and non-power limited wiring must be kept separate from power limited wiring. A ¼” separation must be maintained with high voltage and non-power limited wiring running in separate conduit openings from power wiring. Wiring within the cabinet should be routed around the perimeter of the cabinet.Figure 3Desigo Fire Safety Modular/Cerberus PRO Modular System Ethernet Connection to Gateway12-22 AWG BlackWires are Power LimitedFor UL applications: wiring limited toDETAIL ESCALE 2 : 5Figure 4Desigo and Cerberus PRO Power Connection to Connect X300 GatewayGateway(Can be mountedinside the enclosuresP/Ns S54465-C63-A1,S54339-A8-A1, &Figure 5Desigo and Cerberus PRO Fire Only Panel Ethernet Connection to Connect X300 GatewayGateway(Can be mounted inside the enclosures P/Ns S54465-C63-A1, S54339-A8-A1, &LOCAL CAN MODULE+24 VDCPOWER VCC LOCAL MONETFigure 6Desigo and Cerberus PRO Fire Voice Panel Ethernet Connection to Connect X300 GatewayConfiguring for the Cerberus PRO FC922/FC924/FV922/FV924 and DesigoFC2025/FC2050/FV2025/FV2050Refer to FG2004 Commissioning Guide, Document ID A6V11382550.Configuring for the Desigo Fire Safety Modular/Cerberus PRO Modular using Zeus1. Insert a Custom Enclosure.2. Under this, insert the X300 Gateway.a. To enable supervision of this gateway, check the property for Connection Supervision.i. When checked, a Not responding trouble will be reported each time the connectionbetween the Operator Interface and Connect X300 is lost.ii. By default, this property is unchecked.b. To add the gateway to the battery calculations, check the Cloud Battery Backup option.i. By default, the value is checked.Cyber security disclaimerSiemens provides a portfolio of products, solutions, systems and services that includes security functions that support the secure operation of plants, systems, machines and networks. In the field of Building Technologies, this includes building automation and control, fire safety, security management as well as physical security systems.In order to protect plants, systems, machines and networks against cyber threats, it is necessary to implement – and continuously maintain – a holistic, state-of-the-art security conc ept. Siemens’ portfolio only forms one element of such a concept.You are responsible for preventing unauthorized access to your plants, systems, machines and networks which should only be connected to an enterprise networkor the internet if and to the extent such a connection is necessary and only when appropriate security measures (e.g. firewalls and/or network segmentation) are in place. Ad ditionally, Siemens’ gui dance on appropriate security measures should be taken into account. For additional information, please contact your Siemens sales representative or visit https:///global/en/home/company/topicareas/ future-of-manufacturing/industrial-security.html.Siemen s’ portfolio undergoes continuous developme nt to make it more secure. Siemens strongly recommends that updates are applied as soon as they are available and that the latest versions are used. Use of versions that are no longer supported, and failure to apply the latest updates may increase your exposure to cyber threats. Siemens strongly recommends to comply with security advisories on the latest security threats, patches and other related measures, published, among others, under https:///cert/en/cert-security-advisories.htm.。
现代汽车高性能车辆说明书:i30 N、i30 Fastback N、i20 N、KONA N

i30 NBorn in Namyang. Honed at Nürburgring.生於南陽長於紐布靈In 2017, the award-winning i30 N marked the premiere of the new Hyundai Nhigh-performance range. Today, we are proud to present you with the next generation: the new i30 N and new i30 Fastback N. Together with i20 N and KONA N, they join an impressive range of high-performance vehicles that are joyfully fun to drive, delivering both everyday usability and race track capable performance. N stands for Namyang, home of our global Research & Development centre. Born in Namyang and honed atthe legendary Nürburgring, one of the most demanding racetracks in the world– the N logo also symbolises a racetrack’s chicane curve. Hyundai N cars are designedto perform – and to put a grin on your face. Engineered to satisfy drivers who want to feel the burst of adrenaline that gets your heart beating faster – the pure joy of driving.享負盛名的i30 N於2017 年首次亮相,為現代汽車N系高性能設計揭開序幕。
ETSI EN 303 447 V1.1.1中文版【经典】

ETSI EN 303 447 V1.1.1 (2017-09)短程装置(SRD)频率范围为0Hz-148.5kHz的具有感应回路系统的自动割草机涵盖指令2014/53/EU第3.2节基本要求的协调标准1目录知识产权 (4)前言 (4)情态动词术语 (4)简介 (5)1范围 (6)2参考文献 (7)2.1规范性引用文件 (7)2.2参考资料 (7)3定义、符号和缩写 (8)3.1定义 (8)3.2符号 (9)3.3缩写 (9)4技术要求规范 (10)4.1环境条件 (10)4.2概述 (10)4.2.1期望的性能指标 (10)4.2.2RMI功能模式 (10)4.2.2.1概述 (10)4.2.2.2操作模式 (10)4.2.2.3安全模式 (11)4.2.3测试设备介绍 (11)4.3发射机一致性要求 (11)4.3.1工作频率范围(OFR) (11)4.3.1.1适用范围 (11)4.3.1.2说明 (11)4.3.1.3限制 (12)4.3.1.4一致性 (12)4.3.2发射机磁场(H-field)要求 (12)4.3.2.1适用范围 (12)4.3.2.2说明 (12)4.3.2.3限制 (12)4.3.2.4一致性 (13)4.3.3发射机杂散发射 (13)4.3.3.1适用范围 (13)4.3.3.2说明 (13)4.3.3.3限制 (14)4.3.3.4一致性 (14)4.3.4发射机带外(OOB)发射 (14)4.3.4.1适用性 (14)4.3.4.2描述 (14)4.3.4.3限制 (15)24.3.4.4一致性 (15)4.4接收机一致性要求 (15)4.4.1介绍 (15)4.4.2接收机无用发射 (15)4.4.3接收机阻塞(干扰) (15)4.4.3.1适用性 (15)4.4.3.2说明 (15)4.4.3.3限制 (15)4.4.3.4一致性 (16)5符合技术要求的试验 (17)5.1试验环境条件 (17)5.2试验一般条件 (17)5.2.1产品介绍 (17)5.3正常和极端的测试条件 (17)5.4人造天线 (17)5.5辐射测量的试验场地和总体布置 (17)5.6测量接收机 (17)5.7测量结果的不确定度 (18)5.8测量结果的解释 (18)6发射机和接收机的一致性测量方法 (19)6.1概述 (19)6.2发射机一致性方法 (19)6.2.1工作频率范围(OFR) (19)6.2.2磁场 (20)6.2.3发射机无用发射(杂散和带外(OOB)发射) (20)6.3接收机一致性方法 (21)6.3.1接收机杂散发射 (21)6.3.2接收机阻塞干扰 (21)附录A(资料性)本文件与2014/53/EU指令基本要求的关系 (24)附录B (规范性): 测试场地和程序 (25)B.1 设置1:试验园的磁场测量 (25)B.2设置2:使用人造天线测量载波电流 (25)B.2.1概述 (25)B.2.2差模测量 (26)B.2.3共模测量 (26)B.3使用消声室或开放区域测试场所进行辐射测量 (26)附件C(规范性):人造天线,用于30 MHz以下的传导测量 (27)附件D (资料性): 变更历史 (29)历史 (29)3知识产权必要专利本文件所必需或潜在必需的知识产权可能已向ETSI申报。
EN300 019-1-1

ETSI EN 300 019-1-1 V2.1.4 (2003-04)European Standard (Telecommunications series)Environmental Engineering (EE);Environmental conditions and environmental testsfor telecommunications equipment;Part 1-1: Classification of environmental conditions;StorageReferenceREN/EE-01027-1-1[2]Keywordsenvironment, testing, equipment practiceETSI650 Route des LuciolesF-06921 Sophia Antipolis Cedex - FRANCETel.: +33 4 92 94 42 00 Fax: +33 4 93 65 47 16Siret N° 348 623 562 00017 - NAF 742 CAssociation à but non lucratif enregistrée à laSous-Préfecture de Grasse (06) N° 7803/88Important noticeIndividual copies of the present document can be downloaded from:The present document may be made available in more than one electronic version or in print. In any case of existing or perceived difference in contents between such versions, the reference version is the Portable Document Format (PDF). In case of dispute, the reference shall be the printing on ETSI printers of the PDF version kept on a specific network drivewithin ETSI Secretariat.Users of the present document should be aware that the document may be subject to revision or change of status.Information on the current status of this and other ETSI documents is available at/tb/status/status.aspIf you find errors in the present document, send your comment to:editor@Copyright NotificationNo part may be reproduced except as authorized by written permission.The copyright and the foregoing restriction extend to reproduction in all media.© European Telecommunications Standards Institute 2003.All rights reserved.DECT TM, PLUGTESTS TM and UMTS TM are Trade Marks of ETSI registered for the benefit of its Members.TIPHON TM and the TIPHON logo are Trade Marks currently being registered by ETSI for the benefit of its Members.3GPP TM is a Trade Mark of ETSI registered for the benefit of its Members and of the 3GPP Organizational Partners.ContentsIntellectual Property Rights (4)Foreword (4)1 Scope (5)2 References (5)3 Definitions (5)classes (6)4 Environmental4.1 Class 1.1: Weatherprotected, partly temperature-controlled storage locations (6)4.2 Class 1.2: Weatherprotected, not temperature-controlled storage locations (7)4.3 Class 1.3: Non-weatherprotected storage locations; class 1.3E: non-weatherprotected storage locations-extended (8)conditions (9)5 Environmental5.1 Climaticconditions (9)conditions (9)5.2 Biological5.3 Chemically active substances (10)substances (10)5.4 Mechanicallyactiveconditions (11)5.5 Mechanical History (12)Intellectual Property RightsIPRs essential or potentially essential to the present document may have been declared to ETSI. The information pertaining to these essential IPRs, if any, is publicly available for ETSI members and non-members, and can be found in ETSI SR 000 314: "Intellectual Property Rights (IPRs); Essential, or potentially Essential, IPRs notified to ETSI in respect of ETSI standards", which is available from the ETSI Secretariat. Latest updates are available on the ETSI Web server (/IPR/home.asp).All published ETSI deliverables shall include information which directs the reader to the above source of information.ForewordThis European Standard (Telecommunications series) has been produced by ETSI Technical Committee Environmental Engineering (EE).The present document is part 1, sub-part 1 of a multi-part deliverable covering the classification of environmental conditions and environmental tests for telecommunications equipment, as identified below:Part 1: "Classification of environmental conditions";Sub-part 0: "Introduction";Sub-part 1: "Storage";Sub-part 2: "Transportation";Sub-part 3: "Stationary use at weatherprotected locations";Sub-part 4: "Stationary use at non-weatherprotected locations";Sub-part 5: "Ground vehicle installations";Sub-part 6: "Ship environments";Sub-part 7: "Portable and non-stationary use";Sub-part 8: "Stationary use at underground locations";Part 2: "Specification of environmental tests".Part 1 specifies different standardized environmental classes covering climatic and biological conditions, chemically and mechanically active substances and mechanical conditions during storage, transportation and in use.Part 1-0 forms a general overview of part 1.Part 2 specifies the recommended test severities and test methods for the different environmental classes.National transposition datesDate of latest announcement of this EN (doa): 31 July 2003Date of latest publication of new National Standardor endorsement of this EN (dop/e): 31 January 2004Date of withdrawal of any conflicting National Standard (dow): 31 January 20041 ScopeThe present document defines classes of environmental conditions and their severities to which telecommunication equipment may be exposed during storage. The severities specified are those which will have a low probability of being exceeded; generally less than 1 %.NOTE 1: Temporary storage during transport is included in part 1-2: Transportation.NOTE 2: If the equipment is stored in its package, the environmental conditions apply to the packaged equipment.2 ReferencesThe following documents contain provisions which, through reference in this text, constitute provisions of the present document.•References are either specific (identified by date of publication and/or edition number or version number) or non-specific.•For a specific reference, subsequent revisions do not apply.•For a non-specific reference, the latest version applies.Referenced documents which are not found to be publicly available in the expected location might be found at/Reference.[1] ETSI ETR 035: "Equipment Engineering (EE); Environmental engineering; Guidance andterminology".[2] IEC 60721-3-1: "Classification of environmental conditions - Part 3: Classification of groups ofenvironmental parameters and their severities - Section 1: Storage".[3] IEC 60068-2-27: "Environmental testing. Part 2: Tests. Test Ea and guidance: Shock".[4] IEC 60721-2-4: "Classification of environmental conditions. Part 2: Environmental conditionsappearing in nature: Solar radiation and temperature".3 DefinitionsFor the purposes of the present document, the following terms and definitions apply:absolute humidity: mass of water vapour in grammes which is associated with one cubic metre of dry air in anair/water vapour mixturenon-weatherprotected location: location at which equipment is not protected from direct weather influencesrelative humidity: ratio of the partial pressure of the water vapour in moist air at a given temperature, to the partial pressure of the water vapour in saturated air at the same temperaturestorage: certain site where the equipment is placed for long periods but is not intended for use during these periods weatherprotected location: location at which the equipment is protected from weather influences NOTE 1: Totally weatherprotected location: Direct weather influences are totally excluded.NOTE 2: Partly weatherprotected location: Direct weather influences are not completely excluded.4 Environmental classesThe classes shown in parentheses, e.g. (1C1), may be selected for special applications.4.1Class 1.1: Weatherprotected, partly temperature-controlledstorage locationsThis class is a combination of classes 1K3/1Z2/1B1/1C2(1C1)/1S2/1M2 in IEC 60721-3-1 [2].This class applies to weatherprotected partly temperature controlled storage. Humidity is usually not controlled. The climatogram is shown in figure 1.Heating may be used to raise low temperatures especially where there is a significant difference between the conditions of this class and the open-air climate. Building construction is designed to avoid extremely high temperatures. This class applies to storage locations: -where equipment may be exposed to solar radiation and heat radiation. It may also be exposed to movements of the surrounding air due to draughts in buildings, e.g. through open windows. It is not subjected to precipitation and water from sources other than rain;- without particular risks by biological attacks. This includes protective measures, e.g. special package design, or storing at locations of such construction that mould growth, attacks by animals etc. are not probable; - with normal levels of contaminants experienced in urban areas with industrial activities scattered over the whole area, and/or with heavy traffic;- without special precautions to minimize the presence of dust or sand, but not situated in proximity to dust or sand sources;-with vibration of low significance and insignificant shock.The conditions of this class may occur in ordinary storage rooms for frost-resistant products.-20-1001020304050102030405060708090100Relative Air Humidity [%]A i r T e m p e r a t u r e [°C ]A b s o l u t e A i r H u m i d i t y [g /m ³]291Figure 1: Climatogram for class 1.1: weatherprotected,partly temperature-controlled storage locations4.2Class 1.2: Weatherprotected, not temperature-controlled storage locationsThis class is a combination of classes 1K4/1Z2/1Z3/1Z5/1B2/1C2(1C1)/1S3/1M2 in IEC 60721-3-1 [2].This class applies to weatherprotected storage having neither temperature nor humidity control. The location may have openings directly to the open air, i.e. it may be only partly weatherprotected. The climatogram is shown in figure 2. This class applies to storage locations: -where equipment may be exposed to solar radiation and temporarily to heat radiation. They may also beexposed to movements of the surrounding air due to draughts, e.g. through doors, windows or other openings. They may be subjected to condensed water, dripping water and to icing. They may also be subjected to limited wind-driven precipitation including snow;- where mould growth, or attacks by animals, except termites, may occur;- with normal levels of contaminants experienced in urban areas with industrial activities scattered over the whole area, and/or with heavy traffic;- in areas with sources of sand or dust, including urban areas; -with vibration of low significance and insignificant shock.The conditions of this class may occur in: - unattended buildings; - some entrances of buildings; -some garages and shacks.-30-20 -10 0 10 20 30 40 50 60 0102030405060708090100 Relative Air Humidity [%]A i r T e m p e r a t u r e [°C ]A b s o l u t e A i r H u m i d i t y [g /m 3]290,5Figure 2: Climatogram for class 1.2: weatherprotected, not temperature-controlled storage locations4.3Class 1.3: Non-weatherprotected storage locations; class 1.3E: non-weatherprotected storage locations-extendedClass 1.3 is a combination of classes 1K8/1Z1/1Z4/1B2/1C2/1S3/1M3(1M4) in IEC 60721-3-1 [2]. Class 1.3E is a combination of classes 1Z1/1Z4/1B2/1C2/1S3/1M3(1M4) in IEC 60721-3-1 [2] and the severities given in clause 5.1. NOTE:If more severe mechanical conditions are expected, IEC class 1M4 may be chosen.This class applies to storage which is not protected from direct weather influences. The climatogram is shown in figure 3.This class applies to storage locations: - which are directly exposed to an open-air climate including solar radiation, movement of the surrounding air, precipitation and water jets;- where mould growth, or attacks by animals but excluding termites, may occur;- with normal levels of contaminants experienced in urban areas with industrial activities scattered over the whole area, and/or with heavy traffic;- in areas with sources of sand or dust, including urban areas;-with significant vibration and shock, e.g. transmitted from machines or passing vehicles in the vicinity, etc.-60-50-40-30-20-10010203040500102030405060708090100Relative Air Humidity [%]A i r T e m p e r a t u r e [°C ]A b s o l u t e A i r H u m i d i t y [g /m ³]30250,03Figure 3: Climatogram for class 1.3 and 1.3E: non-weatherprotected storage locations5 Environmental conditions5.1 Climatic conditionsTable 1: Climatic conditions for environmental classes 1.1 to 1.3EClassEnvironmental parameterUnit1.1 1.2 1.3 1.3Ea) Low air temperature (see note 1) °C -5 (see note 8) -25 -33 (see note 9) -45(see note 9)b) High air temperature (see note 1) °C 45 55 40 45 c) Low relative humidity (see note 1) % 5 10 15 8 d) High relative humidity (see note 1) % 95 100 100 100e) Low absolute humidity (see note 1) g/m 31 0,5 0,26 0,03 f) High absolute humidity (see note 1) g/m 3 29 29 25 30 g) Rain intensity mm/min no no 6 15 h) Rate of change of temp. (see note 2) °C/min 0,5 0,5 0,5 0,5 i) Low air pressure (see note 3) kPa 70 70 70 70 j) High air pressure (see note 4) kPa 106 106 106 106 k) Solar radiation W/m2 700 1 120 1 120 1 120 l) Heat radiation W/m 2 (see note 7) (see note 7) negligible negligible m) Movement of the surrounding air m/s 1,0 30 50 50 n) Conditions of condensation none yes yes yes yes o) Conditions of precipitation (rain, snow, hail, etc.) none no (see note 6) yes yes yesp) Low rain temperature (see note 5) °C no no 5 5 q) Conditions from water from sources other than rain none no dripping water splashing water splashingwater r) Conditions of icing and frosting none yes (see note 8)yes yes yesClimatogram figure number 1 2 3 3NOTE 1: For simultaneous occurrence of parameters a) to f) see figures 1 to 3. NOTE 2: Averaged over a period of 5 minutes.NOTE 3: 70 kPa represent a limit value for open-air storage, normally at about 3 000 m. NOTE 4: Conditions in mines are not considered.NOTE 5: This rain temperature should be considered together with high air temperature b) and solar radiation k). Thecooling effect of the rain has to be considered in connection with the surface temperature of the equipment.NOTE 6: Applies to wind-driven precipitation.NOTE 7: Conditions of heat radiation, e.g. in the vicinity of room heating systems. NOTE 8: For certain items storage conditions must be maintained above 5°C.NOTE 9: On cloudless nights an object exposed to atmospheric radiation will radiate more heat than it receives off thesurface, compared to the ambient air temperature. In practice (under extreme conditions) the surface may come down to a temperature in the order of 10°C to 20°C below ambient air temperature, when the ambient air temperature ranges from +20°C to -30°C (see IEC 60721-2-4 [4]).5.2 Biological conditionsTable 2: Biological conditions for environmental classes 1.1 to 1.3EClassEnvironmentalparameter Unit 1.1 1.2, 1.3, 1.3Ea) Flora none negligible Presence of mould, fungus, etc.b) FaunanonenegligiblePresence of rodents and other animalsharmful to equipment but excluding termites.5.3 Chemically active substancesTable 3: Chemically active substances for environmental classes 1.1 to 1.3EClass 1.1 to 1.3ESpecial (1C1) (see note 1) for classes 1.1 and 1.2Environmental parameterUnit (see note 2)Mean value (see note 3) Maximum value (see note 4) Maximum value (see note 4)a) Salts none sea (see note 5) and road salt mistb) Sulphur dioxide (SO 2) mg/m 3cm 3/m 30,3 0,11 1,0 0,37 0,1 0,037 c) Hydrogen sulphide (H 2S) mg/m 3cm 3/m 30,1 0,071 0,5 0,36 0,01 0,0071 d) Chlorine (Cl) mg/m 3cm 3/m 30,1 0,034 0,3 0,1 0,1 0,034 e) Hydrogen chloride (HCl) mg/m 3cm 3/m 30,1 0,066 0,5 0,33 0,1 0,066 f) Hydrogen fluoride (HF) mg/m 3cm 3/m 30,01 0,012 0,03 0,036 0,003 0,0036 g) Ammonia (NH 3) mg/m 3cm 3/m 31,0 1,4 3,0 4,2 0,3 0,42 h) Ozone (O 3) mg/m 3cm 3/m 30,05 0,025 0,1 0,05 0,01 0,005 i) Nitrogen oxides (see note 6) (NO X ) mg/m 3cm 3/m 30,5 0,26 1,0 0,52 0,1 0,052 NOTE 1: Because of the low probability of simultaneous occurrence of these gases at the levels of IEC class 1C2, thevalues of 1C1 are considered more appropriate to describe the long-term environmental conditions.NOTE 2: The values given in cm 3/m 3 have been calculated from the values given in mg/m 3and refer to a temperatureof 20°C and a pressure of 101,3 kPa. The table uses rounded values.NOTE 3: Mean values are the average values (long term values) to be expected.NOTE 4: Maximum values are limit or peak values, occurring over a period of time of not more than 30 minutes per day. NOTE 5: Sea salt mist may be present at sheltered locations in coastal areas. NOTE 6: Expressed as equivalent values of nitrogen dioxide.5.4 Mechanically active substancesTable 4: Mechanically active substances for environmental classes 1.1 to 1.3EClassEnvironmental parameter Unit 1.1 1.2, 1.3, 1.3Ea) Sand mg/m 3 30 300 b) Dust (Suspension) mg/m 30,2 5,0 c) Dust (Sedimentation)mg/(m 2h)1,5 20conditions5.5 MechanicalTable 5: Mechanical conditions for environmental classes 1.1 to 1.3EClass Environmental parameter Unit 1.1 and 1.2 1.3 and 1.3E Special (1M4)a) Stationary vibration,sinusoidal:displacement amplitude (see notemm 1,5 3,0 7,01)acceleration amplitudem/s2 5 10 20 (see note 1)frequency range (note 3) Hz 2 to 9 9 to 200 2 to 9 9 to 200 2 to 9 9 to 200b) Non-stationary vibration,including shock: (see note 2)shock response spectrum type I,peak acceleration (â) m/s2 100duration ms 11shock response spectrum type IIpeak acceleration (â) m/s2250 duration ms 6shock response spectrum type Lpeak acceleration (â) m/s240duration ms 22c) Static load kPa 5 5 5NOTE 1: Peak values.NOTE 2: For definition of Model Shock Response Spectra (First Order Maximax Shock Response Spectra) see IEC 60721-3-1 [2], and Maximax see IEC 60068-2-27 [3].NOTE 3: Cross-over frequency is a rounded value.HistoryDocument history Edition 1 February 1992 Publication as ETS 300 019-1-12002 PublicationV2.1.2 April2003 PublicationV2.1.4 April。
Maritime RobotX Challenge WAM-V USVx 使用与保养手册说明书

Owner’s Operation and Service ManualMaritime RobotX Challenge WAM-V® USVxRead & Completely Understand this OWNER’S OPERATION AND SERVICE MANUAL Prior to Operating.Table of ContentsSafety Precautions (3)Included With Your Vessel (4)Design Specifications and Construction (5)Major Dimensions and Payload Requirements: (5)Sub Assembly Specifications and Construction (6)Assembly Procedure: (8)Hull Inflation (8)Assembly Steps (10)Disassembly (17)Hinge System and Propulsion Interface (18)Suspension System and Payloads (23)Setting Your Spring Pressure (23)Setting Your Damping Rate (25)Pre-Launch Checklist: (26)Vessel Launching (27)Trailer Launching (27)Side Davit/Hoist Launching (27)Towing: (29)Periodic Maintenance: (30)Inflatable Hull Care, Maintenance & Repair (32)Packing For Shipment (33)Vendors: Component Specifications and Manuals (40)Cane Creek: (40)SKS: (40)Gommorizzo: (40)Safety PrecautionsThis vessel is designed for a maximum payload capacity of 300 lbs (136 kg).DO NOT EXCEED.The inflatable hulls should be inflated to a pressure of 2.0 – 2.2 psi (140 – 150 millibar). Maximum pressure rating is 3.0 psi (205 millibar), DO NOTEXCEED.After operation, deflate both hulls to 1.0 psi (70 millibar) to avoid over pressurization and internal baffle rupture due to temperature changes.CRITICAL: Inspect all push button quick release pins to ensure that the spring loaded retaining ball is functioning properly. Replace immediately if there is any sign of damage or if the internal spring mechanism is notfunctioning properly. Failure to do so may result in catastrophic damage or loss of the vessel.Hoisting: Always lift RobotX WAM-V USVx by securely attaching to all 4 payload tray lift points using hardware and slings that are appropriatelyrated for the load being lifted. See “Side Davit/Hoist Launching” section of this manual for the location of the hoist points on the payload tray. Do not walk beneath the vessel during lifting. Improper use of hoisting hardware, slings, or lift points may result in injury or death.The payload tray has attachment points for securing payloads. Please make sure payloads are always secured prior to operation.Included With Your VesselThe following spare parts and tools are included with your RobotX WAM-V USVx.2 x ¼” diameter, 1.5” long stainless steel quick release locking pin1 x ¼” diameter, 4.0” long stainless steel quick release locking pin1 x ¼” diameter, 1.75” long stainless steel quick release locking pin, with lanyard attached1 x 3/8” diameter, 3.0” long stainless steel quick release locking pin8 x retaining rings for ½” shaft size8 x ¼”-20 set screws w/ nylon patch4 x 8-32 set screws w/ nylon patch1 x wrench set: 3/8” – 1”1 x allen key set w/ vinyl pouch: 11 piece, 0.05” – 3/8”1 x double open ended wrench, 7/16” – 9/16”1 x double open ended wrence, 7/16” – ½”1 x T27 torx drive bit4 x 2500 lb load rated lifting sling, 3’ length6 x 1 ton lifting shackle, 3/8” screw pin1 x 3300 lb load rated high depth shackle1 x West Marine hand operated inflator pump1 x SKS SAM suspension pump2 x replacement fill valves for hypalon hulls1 x Cane Creek DBair shock absorber w/ adjustment tool [shipped separately]2 x Cane Creek DBair shock absorber valve cap w/o-ring [shipped separately]2 x IGUS KSTM-30 pillowblock bearing [shipped separately]1 x IGUS KSTM-GT35 pillowblock bearing [shipped separately]Design Specifications and Construction Major Dimensions and Payload Requirements: Beam: 96” (244 cm) [outside to outside]Overall Hull Length: 154” (391 cm)Ski Length: 112” (284 cm)Hull Diameter: 16.75” (42.6 cm)Payload: 300 lbs. (136 kg) maximumFull Load Displacement: 560 lbs. (255 kg) (estimated)Draft: 6.5” (16.5 cm) (estimated)Primary drawing dimensions in inchesPrimary drawing dimensions in inchesSub Assembly Specifications and Construction1.Payload TrayMaterial and Construction: Riveted tube frame and stress skin construction using 5086 and 6061-T6 series aluminum components anodized to MIL-A-8625 Type III. Rear Arch and Front Arch Assembly bearing surfaces are Delrin and reinforced nylon respectively.Weight: 54.5 lbs (24.7 kg).Primary drawing dimensions in inches2.Rear ArchMaterial and Construction: CNC bent tube construction using 6061-T6 series extruded and machined aluminum components anodized to MIL-A-8625 Type III. Inserts and reinforcements riveted in place.Weight: 33.5 lbs (15.2 kg).3.Front ArchMaterial and Construction: CNC bent tube construction using 6061-T6 series extruded and machined aluminum components anodized to MIL-A-8625 Type III. Inserts and reinforcements riveted in place.Weight: 11 lbs (5.0 kg).4.SuspensionMaterial and Construction: Structurally riveted construction consisting of water-jet cut 6061-T6 aluminum plate and extruded sections. CNC machined mounting brackets for all suspension component attachments. All components anodized to MIL-A-8625 Type III. Shock absorbers provided by Cane Creek feature integrated air spring and damper combination with all stainless steel and anodized aluminum construction. Custom valving optimized for WAM-V suspension dynamics featuring external adjustability of spring and damping rates via Schrader valve and barrel adjusters respectively.Weight: 16.5 lbs (7.5 kg). (each)5.SkiMaterial and Construction: Custom 6061-T6 series aluminum extrusion with water-jet cut and CNC machined mounting brackets and reinforcements. Ski-Can is constructed of rolled and welded 0.080” (2 mm) Aluminum 6061-T6 sheet. Can is attached to Ski extrusion via water-jet cut and bent 5086 Aluminum brackets and structural rivets. All components anodized to MIL-A-8625 Type III.Weight: 42.5 lbs (19.3). (each)6.HullMaterial and Construction: Hypalon/polyester (Orca 866 manufactured by Pellel & Flipo).Weight: 20 lbs (9 kg). (each)Assembly Procedure:Hull InflationThe RobotX WAM-V USVx is equipped with hypalon fabric hulls mounted to a rigid aluminum ski. Your RobotX WAM-V USVx was shipped with hull valves locked open. Hull valves must be unlocked before inflation. To unlock the valves, depress and rotate the green button clockwise until green button extends fully. The hulls must be inflated before assembly. Each hull contains a central baffle separating two independent inflation chambers. To inflate, remove the valve cover by rotating the cover counterclockwise.Insert the hand pump valve and rotate clockwise to lock and seal the pump to the hull valve.Inflate each chamber to 2.0 – 2.2 psi (140 – 150 millibar). Replace valve covers by inserting cover and rotating clockwise until locked. In the event of over inflation, depress the green valve release button until desired pressure is reached.To deflate fully, depress the green release button and rotate clockwise until release valve is locked in the open position. After deflation, rotate green release button counterclockwise to close valve.Assembly Steps1. Clear an 8’ x 14’ (2.4 m x 4.3 m) space on the ground (or trailer) and lay out both hulls roughly80” (2 m) apart (centerline to centerline).2.Remove both foot pins by retracting the ¼” (6.3 mm) locking pin and pulling the pin free fromthe foot clevis. Set foot pin aside.3. Set both rear arch foam wedges over the aft most handle on the top of each ski. Line eachwedge up with the inboard edge of each ski.4. Carefully insert the base of the rear arch into the each foot clevis until the pin hole is aligned.Insert foot pin through both ends of the clevis and lock by inserting the ¼” (6.3 mm) locking pin vertically into the locking side of the foot clevis.5.IMPORTANT: Lay the rear arches back until they are resting on the rear arch foam wedgesinstalled in step 3. Failure to do so will result in damage to the rear arch and/or foot assemblies.6. While holding the front arch in between the forward portion of the hulls, slide the front archclevis over the forward balljoint of the suspension assembly and insert 3/8” (9.5 mm) locking pin.7. Repeat this procedure (6) for the opposite hull, laying the front arch forward after both pins arein place.8.Lift the payload tray in between the two arches. Insert the front balljoint shaft into thepillowblock balljoint mounted in the center of the front arch. Place the balljoint shaft cap on the front of the shaft, and secure with the ¼” (6.3 mm) retaining pin attached to the payload tray by inserting the retaining pin vertically through both the shaft and shaft cap.9.Lift the aft end of the payload tray until it is roughly level with the ground. While holding thetray, rotate the rear arch into place. Secure each arch tube in the C-shaped arch mounts.10.Rotate the plastic clamp so that it makes contact with the inside walls of each arch tube. Insertthe ¼” (6.3 mm) locking pin into the pin guide hole at the aft-most arch mounts, locking the clamp in place.11.Remove and store the rear arch foam wedges.DisassemblyDisassembly of the RobotX WAM-V USVx is conducted in the reverse order from the Assembly procedure. For step by step directions, follow the procedure laid out in the “Assembly Procedure” portion of this manual in reverse.Hinge System and Propulsion InterfaceThe RobotX WAM-V USVx is equipped with a quick release hinge system at the transom of each hull. This system allows easy and secure attachment of various propulsion units, independent of propulsion unit design. Each hinge system is composed of a locking handle, accessible on the upper aft portion of the ski, which controls the extension of a pair of locking pins. These locking pins extend into a pair of hinge tongues, mounted on the hinge tongue plate (show below), which is bolted securely to the propulsion unit.Hinge Tongue Plate AssemblyHinge TonguesBolt this face topropulsion unitHinge Tongue Plate Assembly is locked in place by these pins. Pins extend outward into Hinge Tongues via clockwise rotation of control handle at the top of the hull (see pictures on page 22).Rear View of Assembled UnitRear IsometricView of Assembled UnitUnlocked position ofhandleLocked position ofhandle with retainingpin installedSuspension System and PayloadsThe RobotX WAM-V USVx is equipped with a highly adjustable suspension system. Both the spring rate and damping are adjustable through the Cane Creek DBAir shock absorbers equipped on each hull. The RobotX WAM-V USVx can accommodate payloads up to 300 lbs (136 kg). All payloads should be securely fastened to the payload tray via straps or other load rated fasteners.Setting Your Spring PressureNOTE:When removing the valve cap to your DBAir shock absorbers, ensure that the sealing o-ring stays in the cap body. Replace o-ring immediately if lost or damaged.Due to the variability of the payload and payload weight distribution, suspension air pressure must be adjusted to accommodate various payloads. Air pressure can be adjusted using the SKS SAM Schrader valve hand pump supplied with your vessel. IMPORTANT: This pump is outfitted with a zero loss Schrader valve. Please refer to the SKS SAM pump packaging for instructions on the proper use of this valve. Proper use of this valve is essential to charging your DBAir spring to the desired pressure.Zero loss SchradervalveAir pressureadjustment valvePlease refer to page 19 of the DBAir owner’s manual for instructions on how to pressurize the shock. The DBAir contains an internal negative air spring, so care must be taken to set the suspension pressure accurately. Additional service and adjustment information can be found in the DBAir manual included with your vessel or via the link included in the “Vendors: Component Specifications and Manuals” section of this manual.Port and Starboard suspension pressures must be matched such that there is no front view rotation of the front arch.Setting Your Damping RateThe Cane Creek DBAir shock absorbers allow simple external adjustability of compression and rebound settings for both high and low speed damping. The DBAir dampers on your vessel have been adjusted to the following initial setting: HSC – 2 turns +, LSC – 1 turn +, HSR – maximum +, LSR – maximum +Please refer to the Cane Creek DBAir Tuning Field Guide included with your vessel for information on how to adjust your damper settings. Adjustment tools can be found in the spare parts box included with your vessel.Compression Adjustment Side Rebound Adjustment SidePre-Launch Checklist:All locking pins are properly installed and retaining mechanism is functioning properly.Hulls are inflated to 2.0 – 2.2 psi (140 - 150 millibar).Payload is secured to payload tray.Hinge system is properly greased and in locked position with retaining pin installed correctly.Suspension system is properly charged and greased with Schrader valves and O-rings installed correctly.Suspension system pins are installed correctly with C-Clips in place.All fasteners are tightened fully with nuts in place.Vessel LaunchingTrailer Launching1.Before backing down launch ramp, ensure that all tie-down straps holding the vessel to thetrailer are removed and stowed.2.Reverse tow vehicle down the launch ramp until both hulls are sufficiently submerged to lift thevessel off the trailer deck.3.Push or pull the vessel off the trailer and secure to the dockside.Side Davit/Hoist LaunchingThe RobotX WAM-V USVx is equipped with four (4) hoist point connections on the corners of the payload tray. Additionally, a hoisting bar, lifting straps and shackles are included with your vessel.The hoisting bar is designed such that the center lifting shackle can be moved fore and aft to accommodate the change in vessel center of gravity due to various payloads and propulsion unit configurations. When lifting, be sure to secure all payloads as the boat may tilt depending on shackle location. A properly load rated lifting strap must be secured at each hoist point connection in such a way that the majority of the load through the hoist point is in the vertical direction. An example of proper lifting rigging is shown on the following page.Towing:The RobotX WAM-V USVx is equipped with tow point connections on the front inboard side of each ski (shown below).In order to tow the RobotX WAM-V USVx, a tow bridle must be connected to BOTH tow point connections. Do not attempt to lift the vessel using the tow points.Periodic Maintenance:1.Spray down the boat thoroughly after each use.2.Wash down Cane Creek DBAir shock absorbers with soapy water. Rinse clean.3.Ensure all suspension pins are properly greased. If not, apply fresh marine grease via pinmounted zirc fittings.Apply grease here4.Ensure hinge system is properly greased. If not, apply fresh marine grease via hinge shaftmounted zirc fittings.Apply grease here5.Inspect suspension system C-Clips. Replace if damaged or not seated properly.Replace ifdamaged6.Inspect all quick release retaining pins for proper spring retention mechanism function. Test bytrying to remove each pin without depressing the release button. If the pin comes free, replace immediately.7.Every three months, thoroughly clean both hulls and apply an inflatable hull protectant forhypalon boats.pin to work properly. Replace immediatelyif damaged or seized.Inflatable Hull Care, Maintenance & RepairHulls are made of hypalon fabric. In the unlikely event of damage or puncture, please contact a local inflatable hull service center or manufacturer for repair. Do not attempt to patch the hulls. Every three months, thoroughly clean both hulls and apply an inflatable hull protectant for hypalon boats. This will reduce fading and drying caused by repeated UV exposure.Packing For ShipmentPlease refer to the following instructions when packing your RobotX WAM-V USVx for shipment.y font arch and rear arch into shipping box.2.Insert arch foam supports.3.Place payload tray upside down on 4x4 wooden standoffs, ensuring that the tray is constrainedlaterally and longitudinally.4.Secure the payload tray and arches with a single ratchet strap around the payload tray.5.Wrap ratchet strap handle to prevent scratching and damage to hulls during transit.6.Attach hull protection foam to the payload tray.7.Install front cross brace.8.With hulls deflated and suspension air pressure removed, rest skis in the foam saddles withforward portion resting on the cross brace.IMPORTANT: Ensure that the hull is not pinched when ratcheting down the skis.lifting handle.Secure the rear capture crossbar with a ratchet strap.11.Secure the front capture crossbar with a ratchet strap.12.Check to make sure all components are secure and that suspension systems are deflated enoughfor lid clearance.13.Place lid on shipping box. Be sure to line up the lid properly as indicated by the black paintmarking at the corner of the box14.Secure the lid by locking all fasteners.Vendors: Component Specifications and ManualsHardcopies for all commercial off the shelf components are included with this manual. If hard copies are unavailable, digital copies may be downloaded via the links provided below (if available).Cane Creek:DB Air: /tech-center/suspension/manualsSKS:SAM Pump: See backside of included packaging for instructions on how to use, or contact an SKS representative via /index.php.Gommorizzo:Hulls: http://www.gommorizzo.it/index.asp40。
戴尔 Latitude X300 用户指南说明书

Dell™ Latitude™ X300 用户指南单击左侧的链接可以获得有关计算机特性和操作的信息。
有关计算机附带的其它说明文件的信息,请参阅“查找信息”。
注、注意和警告缩写词和缩略词有关缩写词和缩略词的完整列表,请参阅词汇表。
____________________本说明文件中的信息如有更改,恕不另行通知。
© 2003 Dell Computer Corporation 。
版权所有,翻印必究。
未经 Dell Computer Corporation 书面许可,严禁以任何形式进行复制。
本文中使用的商标:D e l l 、D E L L 徽标、Latitude 、Dell Precision 、OptiPlex 、Inspiron 、Dimension 、Dell TravelLite 和 DellNet 是 Dell Computer Corporation 的商标;I n t e l 、Pentium 和 I n t e l SpeedStep 是 Intel Corporation 的注册商标,Centrino 是 Intel Corporation 的商标;Microsoft 和 Windows 是 Microsoft Corporation 的注册商标;Bluetooth 是 Bluetooth SIG, Inc. 的商标,并授权 Dell Computer Corporation 使用;能源之星是美国环保局的注册商标。
作为能源之星的伙伴公司,Dell Computer Corporation 确定此产品符合能源之星关于节能的规定。
本说明文件中述及的其它商标和产品名称是指拥有相应商标和产品名称的公司或其制造的产品。
Dell Computer Corporation 对其它公司的商标和产品名称不拥有任何专利权。
型号:P P 04S2003 年 5 月 P/N D0979 Rev. A00警告: 遵循《系统信息指南》中的安全说明有助于防止您的计算机受到损坏并确保您的人身安全。
欧洲花洒行业标准EN

标识 喷头应该有制造商或供货商的标签,标签必须是永久和清 晰的。产品的包装上应有产品的规格标识。
材料 ➢ 化学和卫生要求
所有与人类用水相接触的材料,都不可在水温90℃以下产 生不利于健康的因素。对于任何用水也不可影响水的质量、 外观、气味或味道。
当产品工作在推荐范围(在第1节中规定)内的条件下时, 所用材料不可引起喷头发生任何性能的变化。
1
EN1112
定义 ✓喷头:一种让水流成喷射状或滴流状的以用于淋浴的装置。 ✓弯臂:将花洒头与供水系统相连的组件。 分类 ✓手握花洒:通过的软管(符合EN1113标准)与卫浴龙头 连接,可用手握持,在一定范围内移动的花洒。能够直接 挂在龙头或墙面的支撑部件上。 ✓花洒头:与固定出水管路连接,安装在头顶,无法移动, 但可以调节喷射角度的花洒。 ✓侧喷:安装在竖直墙面,让水从侧面对淋浴者进行喷淋的 花洒。
9
机械性能 ➢概要 此测试适于实验室操作,非生产过程中所进行的质量控制测试。 ➢按照图示6或图示7对手握花洒施加测试力F ➢程序 将手握花洒连接螺纹旋入测试装置,按照图示6或图示7施加测试力F,并保持 5min。 ➢要求 经过本项测试后,产品不应出现破裂或明显永久变形。
10
11
热冲击测试 ➢本项测试是模拟极限使用温度条件,评估完整产品的性能。 ➢供水管路应该能够提供水压为0.3MPa±0.02MPa的70℃±2℃的热水和 20℃±2℃的冷水,流量大约为0.1L/s。从热水到换到冷水的时间最长2秒。 ➢10.3.4程序 ➢将产品接入测试管路,进行2min冷水,然后2min热水的300个循环测试。测 试流量设定在大约0.1L/s。 ➢10.3.5要求 ➢测试过程中和测试后产品不应出现渗漏、破裂、明显永久变形和功能变差现 象。
电梯米高3003微机中文说明书
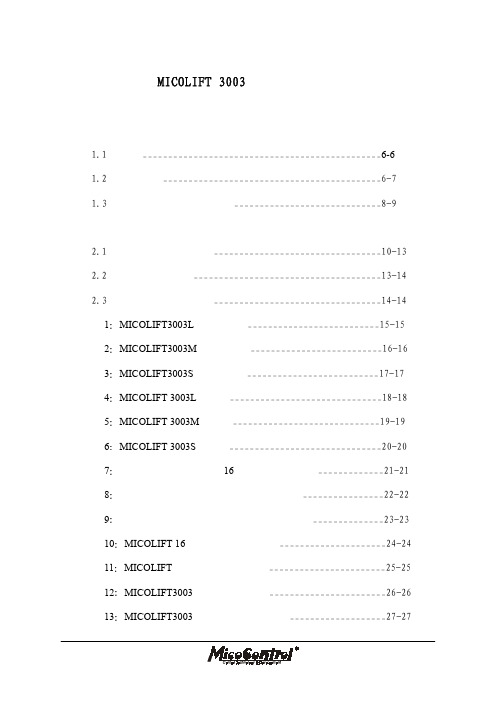
3.5 减速距离的确定_________________________________________56-56 第四章 003B 调试器使用说明______________________________________57-57
4.1 楼层显示_______________________________________________58-58 4.1_____________________________58-58 4.1.2 坚显示方式___________________________________________58-58 4.2 调试菜单_______________________________________________59-59 4.2.1 调试菜单首页_________________________________________59-59 4.2.2 调试菜单主界面_______________________________________59-60 4.2.3 调试主菜单界面_______________________________________60-62 4.3 菜单描述_______________________________________________62-63 4.3.1 配置菜单_____________________________________________63-67 4.3.2 时间设置菜单_________________________________________67-69 4.3.3 基站的设定___________________________________________69-71 4.3.4 呼梯菜单_____________________________________________71-73 4.3.5 输入输出菜单_________________________________________73-74 4.3.6 开门菜单_____________________________________________74-75 4.3.7 故障记录菜单_________________________________________76-77 4.3.8 密码菜单_____________________________________________77-78 4.3.9 脉冲监控菜单_________________________________________78-80 4.3.10 输入选择菜单_________________________________________81-81 第五章 003 系列液晶显示器说明 5.1 规格___________________________________________________82-82 5.1.1 型号说明_____________________________________________82-82
博施安全设备总概述说明书

u Excellent low-light performance (0.017 lx in color)uBuilt-in Intelligent Video Analytics to trigger relevant alerts and quickly retrieve datauIntelligent Dynamic Noise Reduction reducesbandwidth and storage requirements by up to 50%u Outstanding wide dynamic range (100 dB with IAE)uAuto back focus for fast installationThe DINION IP starlight 7000 HD camera provides clear images 24/7 – even at night or under low-light conditions.High sensitivity in color (0.017 lx) and monochrome mode (0.0057 lx) enables this camera to work with a minimum of ambient light. This exceptional light sensitivity combined with Content-Based Imaging Technology (CBIT) ensures crisp, clear, detailedimages in all lighting conditions. The camera can also provide up to 60 images per second.System overviewCompared to SD cameras, the DINION IPstarlight 7000 HD offers, at no higher cost, motorized autofocus, higher resolution, better sensitivity, higher frame rates, and improved picture quality, and is still more bandwidth-efficient. Video storage costs are significantly reduced.Hybrid operationA surge-protected analog video output allows full hybrid operation. This means that high resolution IP video streaming and an analog video output are available simultaneously. The hybrid functionality offers an easy migration path from legacy CCTV to a modern IP-based system.FunctionsExceptional low-light performanceThe latest sensor technology combined with thesophisticated noise suppression results in a sensitivity of 0.017 lx in color. The low-light performance is so good that the camera continues to provide excellent color performance even with a minimum of ambient light.The camera is a true day/night camera with a mechanical filter for truly outstanding nighttimeperformance (0.0057 lx in monochrome). The filter can be switched remotely, or automatically via a light level sensor or contact input.Content Based Imaging TechnologyContent Based Imaging Technology (CBIT) is used to radically improve image quality in all lighting conditions and to identify areas for enhancedprocessing. The camera examines the scene usingIntelligent Video Analytics and provides feedback to re-tune the image processing. This provides better detail in the areas that matter and better all-roundperformance. With IVA, the Intelligent Auto Exposure technology, for example, allows you to view moving objects in bright and dark areas of a scene.Intelligent Dynamic Noise Reduction reduces bandwidth and storage requirementsThe camera uses Intelligent Dynamic Noise Reduction which actively analyzes the contents of a scene and reduces noise artifacts accordingly.The low-noise image and the efficient H.264 compression technology provide clear images while reducing bandwidth and storage by up to 50% compared to other H.264 cameras. This results in reduced-bandwidth streams that still retain a high image quality and smooth motion. The camera provides the most usable image possible by cleverly optimizing the detail-to-bandwidth ratio.Area-based encodingArea-based encoding is another feature which reduces bandwidth. Compression parameters for up to eight user-definable regions can be set. This allows uninteresting regions to be highly compressed, leaving more bandwidth for important parts of the scene. The average typical optimized bandwidth in kbits/s for various image rates is shown in the table:Fast performanceThe 60 images-per-second mode provides for optimum performance in fast action scenes and is particularly suitable for casino and banking applications. Multiple streamsThe innovative multi-streaming feature delivers various H.264 streams together with an M‑JPEG stream. These streams facilitate bandwidth-efficient viewing and recording as well as integration with third-party video management systems.An upright mode can be selected for the second stream. In this mode an image of 400 x 720 (9:16 aspect ratio) is cropped from the full sensor image. When the scene to be monitored is suitable to this mode, the bandwidth and storage requirements are reduced.Regions of interest and E-PTZRegions of Interest (ROI) can be user defined. The remote E-PTZ (Electronic Pan, Tilt and Zoom) controls allow you to select specific areas of the parent image. These regions produce separate streams for remote viewing and recording. These streams, together with the main stream, allow the operator to separately monitor the most interesting part of a scene while still retaining situational awareness.Intelligent Tracking can follow objects within the defined regions of interest. Intelligent Tracking can autonomously detect and track moving objects or the user can click on an object which the tracker will then follow.Scene modesThe camera has a very intuitive user interface that allows fast and easy configuration. Nine configurable modes are provided with the best settings for a variety of applications. Different scene modes can be selected for day or night situations.•Indoor – general day-to-night changes in an indoorenvironment without sun highlights or street lighting effects.•Outdoor – general day-to-night changes in an outdoor environment with sun highlights and street lightingeffects.•Traffic – for monitoring traffic movement on roads or parking lots. It can also be used in industrialapplications where fast moving objects are to bemonitored. Motion artifacts are minimized.•Night-optimized – optimized for details in low lightenvironments.•Intelligent AE – optimized for scenes with fluctuating front and back light caused by sunlight or otherilluminated objects in the scene.•Vibrant – enhanced contrast, sharpness andsaturation.•Low bit rate – reduces bandwidth requirements.•Sports and gaming – high-speed capture, andimproved color rendition and sharpness.•Retail – improved color rendition and sharpness with reduced bandwidth requirements.Storage managementRecording management can be controlled by the Bosch Video Recording Manager (VRM) or the camera can use iSCSI targets directly without any recording software.Edge recordingInsert a memory card into the card slot to store up to 2 TB of local alarm recording. Pre-alarm recording in RAM reduces recording bandwidth on the network, and extends the effective life of the memory card. Video analyticsWith built-in video content analysis, the camera reinforces the Intelligence-at-the-Edge concept where edge devices become increasingly intelligent. The MOTION+ video motion analysis system that is built into all camera versions is the perfect solution for applications where standard video content analysis features are required.The IVA version of the camera uses the latest generation of the Bosch Intelligent Video Analysis (IVA) software. This IVA system is the guard-assistant system of choice when reliable indoor or outdoor video analytics is needed. The state-of-the-art system reliably detects, tracks, and analyzes moving objects while suppressing unwanted alarms from spurious sources in the image.The face detection feature detects faces in the scene and forwards a high quality JPEG image of the best shot of each face when the face disappears from the scene.Retrospective forensic search capabilities are available remotely from the web browser or theBosch Video Client.Cloud-based servicesThe camera supports time-based or alarm-based JPEG posting to four different accounts. These accounts can address FTP servers or cloud-based storage facilities (for example, Dropbox). Video clips or JPEG images can also be exported to these accounts.Alarms can be set up to trigger an e-mail or SMS notification so you are always aware of abnormal events.Access securityPassword protection with three levels and 802.1x authentication is supported. To secure Web browser access, use HTTPS with a SSL certificate stored in the camera.Complete viewing softwareThere are many ways to access the camera’s features: using a web browser, with the Bosch Video Management System, with the free-of-chargeBosch Video Client, with the video security mobile app, or via third-party software.Video security appThe Bosch video security mobile app has been developed to enable Anywhere access to HD surveillance images allowing you to view live images from any location. The app is designed to give you complete control of all your cameras, from panning and tilting to zoom and focus functions. It’s like taking your control room with you.This app, together with the separately available Bosch transcoder, will allow you to fully utilize our dynamic transcoding features so you can play back images even over low-bandwidth connections.System integrationThe camera conforms to the ONVIF Profile S, ONVIF Profile Q and ONVIF Profile G specifications. Compliance with these standards guarantees interoperability between network video products regardless of manufacturer.Third-party integrators can easily access the internal feature set of the camera for integration into large projects. Visit the Bosch Integration Partner Program (IPP) website () for more information.True day/night switchingThe camera incorporates mechanical filter technology for vivid daytime color and exceptional night-time imaging while maintaining sharp focus under all lighting conditions.Easy installationPower for the camera can be supplied via a Power-over-Ethernet compliant network cable connection. With this configuration, only a single cable connection is required to view, power, and control the camera. Using PoE makes installation easier and more cost-effective, as cameras do not require a local power source.The camera can also be supplied with power from+12 VDC/24 VAC power supplies. To increase system reliability, the camera can be simultaneously connected to both PoE and +12 VDC/24 VAC supplies. Additionally, uninterruptible power supplies (UPS) can be used, which will allow continuous operation, even during a power failure.The auto-focus lens wizard makes it easy for an installer to accurately focus the camera for both day and night operation. The wizard is activated from the web browser or from the on-board camera push button making it easy to choose the workflow that suits best. The automatic motorized back focus adjustment with 1:1 pixel mapping ensures the camera is always focused accurately.HD standardsComplies with the SMPTE 296M-2001 Standard in:–Resolution: 1280x720–Scan: Progressive–Color representation: complies with ITU-R BT.709–Aspect ratio: 16:9–Frame rate: 50 and 60 frames/sStandardsHowever, if the system in which this camera is used needs to comply with this standard, then any power supplies used must comply with this standard.Installation/configuration notes ControlsDimensionsParts includedTechnical specificationsSensitivity – (3200K, reflectivity 89%, 1/60 sec shutter time, F1.2,30IRE)Resolutions (H x V)Ordering informationDINION IP starlight 7000 HDHigh-performance IP box camera for intelligent HD surveillance in low light. Hybrid IP/analog; 720p60; PoE; IDNR ; ROI; day/night; H.264 quad-streaming; free viewing Apps; cloud services; audio/motion detection; MOTION+Order number NBN-71013-BDINION IP starlight 7000 HDHigh-performance IP box camera for intelligent HD surveillance in low light. Hybrid IP/analog; 720p60; PoE; IDNR; ROI; day/night; H.264 quad-streaming; free viewing Apps; cloud services; audio/motion detection; IVAOrder number NBN-71013-BAAccessoriesVarifocal SR Megapixel LensVarifocal SR megapixel IR corrected lens. 1/2.5" sensor; CS-mount; 4-pin SR-iris; 5 MP; 9 to 40 mm;F1.5 to F8Order number LVF-5005C-S0940Varifocal SR Megapixel LensVarifocal SR megapixel lens. 1/2" sensor; C-mount; 4-pin SR-iris; 3 MP; 3.8 to 13 mm; F1.4 to F8Order number LVF-5003N-S3813Varifocal SR Megapixel LensVarifocal SR megapixel IR corrected lens. 1/2.5" sensor; CS-mount; 4-pin SR-iris; 5 MP; 1.8 to 3 mm;F1.8 to F8Order number LVF-5005C-S1803Varifocal SR Megapixel LensVarifocal SR megapixel IR corrected lens.1/1.8” sensor; CS-mount; 4-pin SR-iris; 5MP; 4.1 to9 mm; F1.6 to F8Order number LVF-5005C-S4109Varifocal Megapixel LensVarifocal megapixel IR corrected lens. 1/1.8" sensor max; C-mount; 4-pin DC-iris; 5 MP; 12 to 50 mm; F1.6 to T360Order number LVF-5005N-S1250S1374 AdapterAdapter to convert C mount lens to CS mount camera Order number S1374UPA-2430-60 Power SupplyPower supply for camera. 120 VAC, 60 Hz; 24 VAC,30 VA OutOrder number UPA-2430-60UPA-2410-60 Power SupplyPower supply. 120 VAC, 60 Hz; 24 VAC, 10 VA Out Order number UPA-2410-60Monitor/DVR Cable SMB 0.3M0.3 m (1 ft) analog cable, SMB (female) to BNC (female) to connect camera to coaxial cableOrder number NBN-MCSMB-03MMonitor/DVR Cable SMB 3.0M3 m (9 ft) analog cable, SMB (female) to BNC (male) to connect camera to monitor or DVROrder number NBN-MCSMB-30MVIDEOJET XTC XF Video TranscoderHigh-performance video transcoder. H.264; CF card slot; ROI; max resolution 1080p; 2 channelsOrder number VJT-XTCXFMonitor/DVR Cable SMB 3.0M3 m (9 ft) analog cable, SMB (female) to BNC (male) to connect camera to monitor or DVROrder number NBN-MCSMB-30MNPD-5001-POE Midspan PoE InjectorPower-over-Ethernet midspan injector for use with PoE enabled cameras; 15.4 W, 1-portOrder number NPD-5001-POENPD-5004-POE Midspan PoE InjectorPower-over-Ethernet midspan injectors for use with PoE enabled cameras; 15.4 W, 4-portsOrder number NPD-5004-POERepresented by:North America:Europe, Middle East, Africa:Asia-Pacific:China:Latin America and Caribbean:Bosch Security Systems, Inc. 130 Perinton Parkway Fairport, New York, 14450, USA Phone: +1 800 289 0096 Fax: +1 585 223 9180***********************.com Bosch Security Systems B.V.P.O. Box 800025617 BA Eindhoven, The NetherlandsPhone: + 31 40 2577 284Fax: +31 40 2577 330******************************Robert Bosch (SEA) Pte Ltd, SecuritySystems11 Bishan Street 21Singapore 573943Phone: +65 6571 2808Fax: +65 6571 2699*****************************Bosch (Shanghai) Security Systems Ltd.203 Building, No. 333 Fuquan RoadNorth IBPChangning District, Shanghai200335 ChinaPhone +86 21 22181111Fax: +86 21 22182398Robert Bosch Ltda Security Systems DivisionVia Anhanguera, Km 98CEP 13065-900Campinas, Sao Paulo, BrazilPhone: +55 19 2103 2860Fax: +55 19 2103 2862*****************************© Bosch Security Systems 2016 | Data subject to change without notice 14148787083 | en, V15, 30. May 2016。
Eaton XV300产品安全配置指南说明书

XV303Secure Hardening GuidelinesEaton Product Cybersecurity CoEXV300Recommended Secure Hardening GuidelinesIntroductionXV300 has been designed with Cybersecurity as an important consideration. Number of Cybersecurity features are now offered in the product which if implemented as per the recommendations in this section would minimize Cybersecurity risk to XV300. This section “secure configuration” or “hardening” guidelines provide information to the users to securely deploy and maintain their product to adequately minimize the cybersecurity risks to their system.Eaton is committed to minimizing the Cybersecurity risk in its products and deploys cybersecurity best practices and latest cybersecurity technologies in its products and solutions; making them more secure, reliable and competitive for our customers. Eaton also offers Cybersecurity Best Practices whitepapers to its customers that can be referenced at /cybersecurityXV300 - SECURE CONFIGURATION GUIDELINESReferences[R1] Cybersecurity Considerations for Electrical Distribution Systems (WP152002EN):/ecm/groups/public/@pub/@eaton/@corp/documents/content/pct_1603172.pdf [R2] Cybersecurity Best Practices Checklist Reminder (WP910003EN):/content/dam/public/powersystems/resources/library/1100_EAS/WP910 003EN.pdf[R3] NIST SP 800-82 Rev 2, Guide to Industrial Control Systems (ICS) Security, May 2015.https:///Standards-and-References[R4] National Institute of Technology (NIST) Interagency “Guidelines on Firewalls and Firewall Policy, NIST Special Publication 800-41”, October 2009./nistpubs/Legacy/SP/nistspecialpublication800-41r1.pdf。
Henny Penny ODS-300.02 300.03 油浇洒机操作手册说明书

Henny PennyOil DisposalShuttleODS-300.02ODS-300.03(Translated Documents Available On CD within Manual) OPERATOR’S MANUAL REGISTER WARRANTY ONLINE AT TABLE OF CONTENTSSection Page Section 1. INTRODUCTION ............................................................................................................1-1 1-1. Introduction .............................................................................................................1-11-2. Features ...................................................................................................................1-11-3. Proper Care .............................................................................................................1-11-4. Assistance ...............................................................................................................1-11-5. Safety ......................................................................................................................1-2 Section 2. ASSEMBLY .....................................................................................................................2-1 Section 3. OPERATION ....................................................................................................................3-1 Section 4. PART INFORMATION ...................................................................................................4-1 4-1. Introduction .............................................................................................................4-14-2. Genuine Parts ..........................................................................................................4-14-3. How to Order ..........................................................................................................4-14-4. Prices .......................................................................................................................4-14-5. Delivery...................................................................................................................4-14-6. Warranty .................................................................................................................4-14-7. Recommended Spare Parts for Distributors ............................................................4-1I 208Where information is of particular importance or is safety related, thewords NOTICE, CAUTION, or WARNING are used. Their usage isdescribed below:SAFETY ALERT SYMBOL is used with DANGER, WARNING, or CAUTION which indicates a personalinjury type hazard.NOTICE is used to highlight especially important information.CAUTION used without the safety alert symbol indicates a potentially hazardous situationwhich, if not avoided, may result in property damage.CAUTION used with the safety alert symbol indicates a potentially hazardous situation which, if not avoided, may result in minor or moderate injury.WARNING indicates a potentially hazardous situation which, if not avoided, could result in death or serious injury.DANGER INDICATES AN IMMINENTLY HAZARDOUS SITUATION WHICH, IF NOT AVOIDED, WILL RESULT IN DEATH OR SERIOUS INJURY.2081-12-1 10107142-22-3714ATTACH HANDLE TOPUMP.1. Release cover latch and hinge cover back on oil disposal shuttle. Make sure crumb catcher is in place.2. Remove filter drain pan assembly from under fryer and roll oil disposal shuttle under fryer until it stops. Make sure drain aligns with opening in shuttle.TO AVOID PERSONAL INJURY, BURNS,SPILLS, AND CORROSION:▪ DO NOT OVERFILL. SHUTTLE HOLDS OIL FROM ONE FULLSIZE FRYPOT OR TWO SPLIT FRYPOTS▪ SHORTENING ONLY! DO NOT PUT WATER AND/OR CLEANER IN THE SHUTTLE▪ DO NOT TRANSPORT OIL WITHOUT COVER IN PLACE3. Press and hold (on either side) until display shows *FILTER MENU*, along with “1.AUTO FILTER?”.4. Press and release twice until display shows“3.DISPOSE”. Press √ button and display shows “DISPOSE?” along with “YES NO”.5. With oil disposal shuttle rolled into place, press & hold √ button and displays shows “DISPOSING”. Oil now drains from the vat into the shuttle.On LVE/LVG-10X fryers, if oil disposal shuttle is not properly in place, “IS DISPOS AL UNIT INPLACE?” shows in display. Adjust center bracket on the front of shuttle as needed by loosening 6 nutsholding bracket and moving bracket up or down. Onceproperly adjusted, the display shows “DISPOSING”.10103-16. Display shows VAT EMTY, along with “YES NO”.Verify that vat is empty, and press √ button.7. Display shows “CLN VAT COMPLETE”, along with“YES NO”. Once vat is clean, press √ button.8. Display shows “MANUAL FILL POT”, followed by“VAT FULL”, along with “YES NO”. Fill the vat tothe lower indicator line on the rear of the vat and thenpress √ button. Controls return to normal operation.9. Remove the oil disposal shuttle from under fryer andreplace with the filter pan assembly.10. Replace and latch the cover and roll oil disposal shuttleto disposal container.To avoid burns and personal injury, allow oil to coolto 100o F (38 o C) or below before transporting shuttle to the disposal area.11. Turn thumb screw on bracket to loosen pump assembly.12. Swivel pump assembly over disposal container andtighten thumb screw on bracket.3-2 101013. Turn pump handle rapidly (fast) in order to primethe pump and to get oil to flow through pump.To avoid damage to pump,▪only pump oil at 100o F (38o C) or below▪do not pump water or water-based liquids14. Once shuttle is empty, loosen thumb screw on bracketand swivel pump assembly back over lower unit andtighten handle.CLEANING15. Daily, remove the crumb catcher and take it to a sinkand clean with soap and water. Clean the exterior ofthe shuttle with a soft cloth and soap and water. It’s notnecessary to clean the interior of the unit, but if desired, it can be wiped down with paper towels.To avoid damage to pump, do not use water orwater-based liquids to clean the interior of the shuttle.1010 3-34-1. INTRODUCTION This section identifies and lists the replaceable parts of the HennyPenny ODS-300, Oil Disposal Shuttle.4-2. GENUINE PARTSUse only genuine Henny Penny parts in your unit. Using a part of lesser quality or substitute design may result in unit damage or personal injury.4-3. HOW TO FIND PARTS To find items you want to order from the Parts List, proceed asfollows:1. Refer to the exploded drawing in this section to identify the partneeded.2. Use the item number from the exploded drawing to locate thecorresponding part in the parts list in this section. In this list willbe the Henny Penny part number and description of the part.4-4. HOW TO ORDER PARTS Once the part you want to order has been found in the Part List,write down the following information:1. From the exploded drawing and Parts List (Sample)Item Number 7Part Number 77237Description ASSY -COVER LVE DRAIN PAN DOLLY2. From the data plate (Sample)Serial Number 001004-5. PRICES Your distributor has a price parts list and will be glad to inform youof the cost of yours parts order.4-6. DELIVERY Commonly replaced items are stocked by your independent HennyPenny distributor and will be sent out when your order is received.Other parts will be ordered by the distributor from Henny PennyCorporation. Normally, these will be sent to your distributor withinthree working days.4-7. WARRANTY All replacement parts (except lamps and fuses) are covered underwarranty for 90 days against manufacturing defects and workman-ship. If damage occurs during shipping, notify the carrier at once sothat a claim may be properly filed. Refer to the warranty in thismanual for other rights and limitations.Recommended replacement parts, stocked by your distributor, areindicated with in the parts lists. Please use care when orderingrecommended parts, because all voltages and variations aremarked. Distributors should order parts based upon commonvoltages and equipment sold in their territory.4-1 2081243Item PartNumber Number Description Qty-- 03616FILTER HOSE ACCESSORY --1 81066FILTER HOSE ASSY 12 85135HOLDER BRACKET 13 80995FILTER HOSE HOLDER 14 SC06-013U-BOLTS 25* NS02-002NUTS 4* not shown1010 4-24-3 312 Item PartNumber Number Description Qty1 84368 WELD ASSY-DRAIN PAN DOLLY HAND 12 FP02-021NIPPLE – ¾ NPT X3 IN LG-BI 13 FP01-098 ELBOW-3/4NPT X 90 FEMALE BI 14 FP02-056NIPPLE-3/4NPT X 18.25 INCH BI 15 FP01-140PLUG – ¾ PIPE BI 16 FP01-097TEE-3/4 NPT FEMALE PIPE BI 17 FP02-033 NIPPLE-3/4NPT X 4 IN LONG BI 1A 8 72490PUMP-MANUAL OIL DISCARD 19 FP01-227REDUCER 1" MALE TO 3/4" FEMALE 110 16282NIPPLE 3/4 X CLOSE 1A 11 21800 VALVE-3/4 CHECK 112 84376 PIPE-BLACK 3/4 113 84003 WELD ASSY-LVE DRAIN PAN DOLLY 114 NS02-005NUT HEX KEPS #6-32 C 215 83994 BRKT-HINGE MOUNTING 1A 16 MS01-532 LATCH-BREADING MACHINE DRUM 1B 17 84001 ASSY-COVER LVE DRAIN PAN DOLLY 1B 18 84453 WELD ASSY-CRUMB BASKET 1B 19 84519 BRACKET-DRAIN SW ENGAGEMENT 120 NS02-006 NUT – HEX – KEPS #10-24 C 4B 21 19004 CASTER 2" SWIVEL PLATE 122 NS02-006 NUT – HEX – KEPS #10-24 C 8B 23 SC06-074 SCREW-1/2X1-1/2 SHOULDER 3/8-16224 LW01-010 LOCKWASHER – SPLIT-RING 3/8 S 225 NS01-001 NUT – HEX 3/8-16 2B 26 77815 WHEEL-8 INCH LVE 2B 27 SC01-057 SCREW – ¼-20 x ½ HEX HDC 428 NS02-002 NUT KEPS 1/4-20 C 429 84481 WELD ASSY-LOCKNUT & PUMP 130 SC01-057 SCREW – ¼-20 x ½ HEX HD C 231 NS02-002 NUT KEPS 1/4-20 C 232 SC06-076 SCREW – THUMB M8 X 25MM BLK KNOB 133 NS02-006NUT – HEX – KEPS #10-24 C 334 SC01-038SCREW #10-24 X 3/8 PH THD S 335 NS02-006NUT – HEX – KEPS #10-24 C 336 88527 BRACKET-ODS DRAIN SWITCH 1B 37 SC01-113SCREW #6-32 X 9/16 PH PHD BLAK 4B 38 NS02-005NUT HEX KEPS #6-32C 4 312 4-4Henny Penny CorporationP.O.Box 60Eaton,OH 453201-937-456-84001-937-456-8402 FaxToll free in USA1-800-417-84171-800-417-8434 Fax Henny Penny Corp., Eaton, Ohio 45320, Revised 7-16-14。
欧洲汽车维修设备_桑普安_亨福曼_四杆抬升机_产品说明书

Release Date: Oct, 2011 Priority Status: None Model(s)Affected:Hofmann:John Bean:GENERAL OVERVIEW: __________________________________________________________________________ Snap-on Equipment presents the all new John Bean and Hofmann Quad-Rack™ model 4-Post lift with Open Front design and integrated full floating flush mounted rear slip plates. The new design incorporates an Industry leading 90" long rear slip plates that will accommodate long and short wheelbase vehicles with 4 wheel alignment requirements from 70" up to 158". Proven maintenance reduced rear slip plates use heavy duty encapsulated bearings to support and provide smooth movement to ease alignment adjustments. Strategically positioned openings under the front and rear plates allow for reduced water and dirt entrapment, minimizing maintenance.Certified to the industry’s leading ANSI/ALI automotive lift standard. Lifts are designed and built right here, in North America.DETAILS: _____________________________________________________________________________________•Heavy duty lifting capacity, 14,000 lbs.•Wide Open front design allows easy access to vehicle adjustment points•22” wide, “Pro-Style” runways save time when loading vehicles of narrow to wide track widths.•Ultra low profile design allows “Easy-On” approach angle for low profile vehicles, lowered height just 7”.•4-Wheel Alignment capabilities, Micro and Sub-compact vehicles, 70” to full size vehicles 158” wheelbases.2-Wheel Alignment up to of 188” and General Service wheelbases up to 205”.•Industry leading 90” long rear slip plates – no need to repositioning front turn plates to accommodate longer or shorter vehicles.•Full floating flush mounted rear slips plates – uses encapsulated bearings to fully support the load, move the vehicle effortlessly during alignments. Flush mounting offers smooth transiting during vehicle roll backprocedures.•Strategically positioned openings reduce water and dirt entrapment under the front and rear alignment plates – minimizing corrosion.•Fully raised height of 74” to the runway surface, with 27 alignment level locking positions.•Industry proven; roll formed front columns and traverse beam design, spreads critical load forces over larger supporting area – ensuring alignment accuracy.•10” diameter pulleys with fiber wound bushing – improves cable performance and life.•Under runway mounted hydraulic cylinder adds to accessibility and no vehicle door damage. Enhanced pivoting end ensures direct alignment of the primary lifting components, reducing stress while improvingperformance.•ANSI/ALI Certified - designed and built here in North America.SpecificationsTop View LayoutWheelbase LayoutSPECIAL CONSIDERATION: ______________________________________________________________________Premium 7000 lb. capacity Air over Hydraulic - Jack Beam -EELR508AOptional AccessoriesWork Step (Qty of 2, Part # 22119)Drive Thru Kit (Qty of 2, Part # 31089)Air Electric Power Station ( Part # JBC000896)SPECIAL CONSIDERATION: ______________________________________________________________________ Additional Competitive Product Enhancements1. QUAD-RACK™ CompetitorTurn Plate PocketRequires Filler Plate90” Long x 22” Wide Flush Mounted Rear Slip Plates 80” Long x 18” Wide Flush Mounted Rear Slip Plates4 QUAD-RACK™Front Traverse Beams uses box design toadd support. Added support capture thesafety ladder, ensuring relationshipbetween the safety lock and safety ladderis always maintained.5 QUAD-RACK™ CompetitorTop ViewGlide Blocks are on inside of column. Clean painted surface. Safety ladder has 27 alignment level locking positions. Top ViewRollers run on 2” x 2” square tube welding to “U” shaped column. Unpainted surface. Safety ladder has 13 alignment level lock positions.6 QUAD-RACK™ CompetitorLadder held inposition byplastic retainers.Safety ladderhas 13 lockpositions.Safety Ladders have 27level locking positionsLR-1094 Page 11 of 11 October, 2011PHOTOS: _____________________________________________________________________________________Without vehicle With Large Ford Extended Cab Pick UpWith Fait 500C Lowered With Fait 500C Raised。
2017年汉达督斯说明书

See the following headings for other important information: NOTICE Information to prevent damage to your scooter, other property or the environment. JST Page 3 Importance of Maintenance ..................................Page 35 Maintenance Schedule .... .. . .... .....
2017 honda ruckus owners manual pdf
Honda ruckus battery dimensions. 2017 honda ruckus value. How to wash a honda ruckus. 2016 honda ruckus Nhomakorabeavalue.
Contents Scooter safety P.2 AWNER manual P.16 Machine maintenance P. 34 Troubleshooting P. 74 Information P. 82 Specifications P. 104 Index P. 10720161103142821_31GGA6800_FRK_BOBOT 6201 (1610) Page 2 on safety Your safety and yours safety are very important. Operating a scooter safely comes with many responsibilities. To help you make informed safety decisions, we have included operating procedures and other information on safety labels and throughout this manual. This notice alerts you to potential hazards that could cause injury to you or others. Of course, it is neither practical nor possible to inform you of all the risks involved in using or maintaining a scooter. You have to use common sense. You will find important safety information in various forms, including: "Scooter Safety Labels" Safety messages preceded by a warning symbol and one of three signal words: DANGER, WARNING, or CAUTION. These signal words mean: 3 DANGER if instructions are not followed. instructions YOU MAY BE KILLED or SERIOUSLY INJURED 3 WARNING If you don't follow instructions, you could be killed or SERIOUSLY INJURED 3 WARNING If you don't follow instructions, you could be injured. Other important information can be found under the following headings: NOTICE Information to help prevent damage to your scooter, other property, or the environment. ...... ........... ...page 35 Maintenance Schedule...............
жеп ЖL Load Level Kit 安装说明书

1Important Notes:Prior to beginning this install, or any installation, read the instructions thoroughly to familiarize yourself with the required steps. Evaluate if you are experienced and capable to personally perform these modifications.A factory service manual should be used in conjunction with these installation instructions.This product will change the highway handling characteristics of your vehicle, exercise caution. After alter-ing the suspension it is always advisable to have an alignment done by a competent 4 wheel drive shop or by an alignment shop that is experienced with lifted 4 wheel drive vehicles.Refer to the parts list to ensure that all necessary components and hardware has been included. If any parts are missing please contact your local TeraFlex dealer for assistance.When reinstalling OEM hardware, refer to the torque specs given in the Factory Service Manual. Tools Needed:- Metric Sockets and Open End Wrenches - Factory Service Manual- Torque Wrench - General Mechanics ToolsMaintenance Note:After the first 300 miles and every 3,000 miles after that, re-torque all the suspensioncomponents and bolts.1 23654REMOVE FRONT TIRES1SUPPORT FRONT AXLEREMOVE BRAKE LINE BRACKETS FROM LOWER CONTROL ARMS 4REMOVENUT 15MM BOLT 18mmDISCONNECT ACTUATORS & VENT HOSE AT THE FRONT AXLEDO NOT REMOVE THE CONTROL ARM BOLTSLOOSENBOLT & NUT18mmLOOSENBOLT 21mmNUT 24mm REMOVE SHOCKS AT THE AXLEBOLT &LOWER AXLE & REMOVE FRONT SPRINGSTRIM TO FIT (ABOUT HALF)TRIM TO FIT (ABOUT HALF)1FULLY SEAT THE SPRINGS INTO THE LOWER SPRING ISOLATORREINSTALL FRONT SPRINGS.*DRIVERS SIDE FIRST*STOCK SPRING ISOLATORNOTE: IF ONLY FRONT OF JEEP WAS LIFTED, REINSTALL TIRES AND LOWER JEEPBACK TO THE GROUND BEFORE LIFTING THE REAR BOLT & NUT18mm 56 ft lbsREINSTALL ANY REMAINING CONNECTORSREMOVE REAR TIRESREAR INSTALLLIFT AND SUPPORT AT FRAMESUPPORT REAR AXLE16REMOVE E-BRAKE CABLE BRACKET AND DISCARD19BOLT15mmLOOSEN REAR CONTROL ARM BOLTSDO NOT REMOVE THE CONTROL ARM BOLTSLOOSENBOLT & NUT18mmREMOVE SWAY BAR LINKS AT THE AXLEBOLT 13mm2X22REMOVE THE TRACK BAR FROM THE AXLEBOLT 21mm23REMOVE THE REAR SHOCKS AT THE AXLETORQUE415 FT LBS6BOLT 17mm53NUT 14mm 2INSTALL REAR SPRINGSNOTE: MAKE SURE TO FULLY SEATINTO THE UPPER SPRINGISOLATORRAISE THE REAR AXLE AND INSTALL SHOCKSBOLT & NUT18mm56 ft lbsTORQUE TO FACTORY SPEC TORQUE FRONT AND REAR CONTROL ARM BOLTS TO FACTORY SPECS3132BOLT 21mm REAR BOLT & NUT18mm BOLT & NUT 18mmBOLT 21mmNUT 24mmREINSTALL BOLT 13mm 33。