直径500mm二辊中厚板热轧实验机组的自动控制系统
中厚板轧机模糊PID控制系统的研究
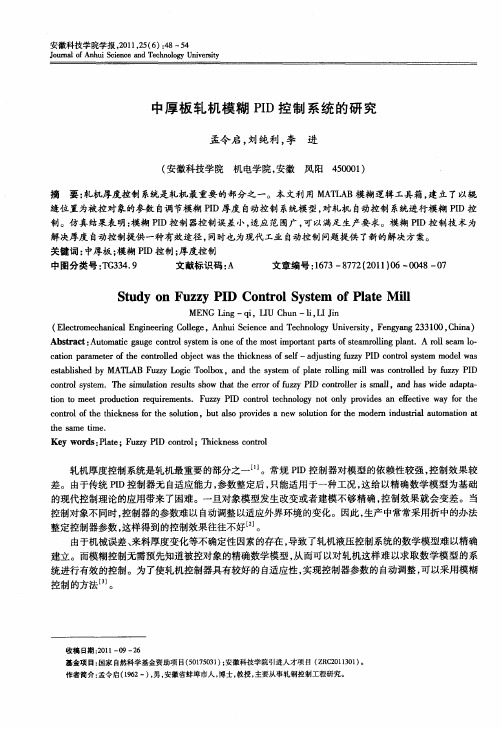
轧 机厚度 控制 系统是轧 机最 重要 的部分 之一 … 。常规 PD控 制器 对模 型 的依赖 性较 强 , 制 效果 较 I 控
差 。由于传统 PD控制器无 自适应能力 , I 参数整定后 , 只能适用于一种工况, 这给以精确数学模型为基础 的现代控制理论的应用带来 了困难。一旦对象模型发生改变或者建模不够精确 , 控制效果就会变差 。当 控制对象不同时 , 控制器的参数难 以自动调整以适应外界环境的变化。因此 , 生产中常常采用折 中的办法 整定控制器参数 , 这样得到的控制效果往往不好 。 由于机械误差、 来料厚度变化等不确定性 因素的存在 , 导致了轧机液压控制系统的数学模型难 以精确 建立。而模糊控制无需预先知道被控对象的精确数学模型 , 从而可以对轧机这样难以求取数学模型 的系 统进行有效的控制。为了使轧机控制器具有较好的 自 适应性 , 实现控制器参数的 自动调整 , 可以采rm tr fh o  ̄ H dojc w s h i n s o l— dut gfzyPD cn o ss m m d l a a o aa e een o e bet a et c es f e - jsn z I o t l yt o e w s i e ot t h k sf a i u r e et lh db A L B F zyL gcT o o , n ess m o l erln i a ot l db uz I s bi e yM T A uz o ol x a dt yt f a ol gm lw scn o e yfz P D a s i b h e pt i l rl y
中厚板生产中自动化控制系统的应用与优化

中厚板生产中自动化控制系统的应用与优化摘要:中厚板轧制自动化系统反映了线材轧制控制的自动化程度,采用中厚板轧机自动控制系统不仅可以提高生产质量和利用率,而且可以满足特殊的控制要求。
从AGC绝对厚度控制、轧区跟踪系统和自动轧制三个方面介绍了自动控制优化的实际应用关键词“绝对AGC”;中厚板;自动化系统钢铁行业是典型的制造生产过程包括各种钢铁工业,具有很高的针对性和渗透性。
生产过程不仅包括成本、质量和效率等市场竞争因素,还包括资源、能效和可承受性等因素,以及过程排放、环境兼容性和工业生态系统等可持续发展因素。
一、中厚板生产工艺概述轧制产品(各种钢材)作为钢铁行业长流终端技术,直接服务于各行各业。
轧钢工艺的品种和质量首先代表了钢铁行业的整体生产水平,经过检查和清理的坯料被送到铸坯车间原料跨进行切割所需的长度。
按类型、来源、钢种和生产计划储存。
推料机将一个轧制坯料一个接一个推入辊道,并将其送入加热炉;送料机将板材加热至1150-1250℃后将其推入热炉,板材通过辊子输送至轧机。
除鳞箱经过首先氧化铁皮从高压水中去除;然后进入轧机。
四辊可逆式轧机。
轧机配有锥形工作辊,用于轧制工件。
高压水去除轧制表面的氧化铁。
通用13-17次往复轧,至最终产品的尺寸,轧制后,钢板由钢板矫直机矫直,钢板矫直后由冷床冷却。
在生产过程中,钢板的加工主要包括厚度、宽度、钢板长度等物理尺寸。
为了提高轧制板材的机械性能,通常在轧机后部安装快速冷却装置,将轧制板材冷却到一定温度,以获得所需的板材性能。
厚板自动轧制系统的控制功能包括:将工件从原来的厚度、宽度和长度轧制到所需的厚度、宽度和工件长度。
快速冷却板具有良好的机械性能。
计划在该地区增加产量,以提高生产速度和生产率。
在生产过程中,操作者必须在生产过程中进行指导和控制,维修人员必须有一定的控制手段,以便于错误的处理。
二、案例分析1.AGC厚度绝对控制。
厚钢板轧机的自动控制系统采用AGC绝对厚度控制系统建立轧制宏微观跟踪平台,根据L2系统数据和自动轧制的主要功能,实现可逆自动轧制过程。
中厚板轧机全自动轧钢控制功能的在线实现吕斌

中厚板轧机全自动轧钢控制功能的在线实现吕斌发布时间:2022-03-14T14:34:22.842Z 来源:《中国科技信息》2021年11月下作者:吕斌[导读] 钢铁企业是我国经济发展的重要环节。
新疆八一钢铁股份有限公司吕斌摘要:轧钢是利用合适的加工方法,对钢坯或钢锭进行加工,将其压制成相应的形状,在轧钢过程中需要确保轧钢产品的质量、尺寸、形状等都能够满足生产要求,达到其精准度符合生产标准。
一般来说,在轧钢过程中,电气自动化系统有着较高的运行稳定性,对其精度控制也非常好,因此需要实现对电气自动化系统的合理应用,通过与轧钢系统融合,让轧钢过程更加精确,满足轧钢产品的生产需求,推进轧钢质量提升,保障企业具备较好的经济效益。
关键词:轧钢;自动化技术;应用前言随着科技的发展,自动化技术对基础生产领域的发展产生重要的影响,同时,对钢铁行业的工艺控制有着本质的提升。
目前,在国内钢铁行业,轧钢技术受科技智能化的影响,已采用智能电网控制、无人化和自动化生产。
通过智能电气自动化技术的推广,是提升我国钢铁工业重要的基本保障,工业制造及生产功能得到了极大的改善。
1轧钢技术及轧钢电气自动化技术简述1.1轧钢的定义轧钢技术是钢的生产和制作的一种形式,同时也是生产方式中最重要的一种。
钢铁生产中产生的一种特殊技术,目的是将钢从钢锭或钢坯的形状轧制成规定的形状。
它是通过轧制施加压力来操作的,主要是通过轧制压力挤压来实现的。
通常,轧钢生产要经过多次轧制、多轧机连续轧制,最终形成轧制目标产品。
轧钢技术是一种特殊的钢材加工,因为它主要是通过压力来进行的,所以该技术的工艺过程与其他需要压力的工艺有些相似,但不同之处在于该工艺中钢材的天然质量。
因为钢的内在质量在加压过程中相当稳定。
其次,它不同于其他技术的原因在于,轧钢技术最终可以生产出不同形状要求的钢,因此它可以通过各种形式的变化来满足不同的工艺需求,适应不同的使用场景,轧钢技术的有效应用可以在很大程度上提升钢材的性能。
辊轧机电气控制系统介绍(参考Word)

20辊轧机电气控制系统介绍发布时间:2007-11-15 来源:打印该页一系统概述某冷轧不锈钢板厂采用西门子S7 300系列的315-2DP控制器作为主控制单元,安置于主操作台上作为主站,采用2套西门子ET200 远程站作为从站,安置于前后两个操作箱内接受现场操作工控制指令。
ET200远程站与CPU315-2DP主站之间采用PROFIBUS现场总线连接进行通讯。
轧机采用前卷取、后卷取、主轧三台直流电机完成整个不锈钢板的张力轧制。
直流电机采用西门子6RA70直流调速器进行控制,控制器与CPU315-2DP之间采用PROFIBUS现场总线通讯。
同时还为此轧机配置了一台平整机,电器配置完全相同,只在功能,电机功率等参数上与主轧机略有不同。
二系统要求1.采用西门子6RA70直流调速器作为电机控制单元,调速器可以独立采集安装于电机上的编码器读取的数据,安装于轧机上的张力传感器读取的数据,作为基本参数高速运算得到当前系统所实际需要的张力,控制直流电机让其达到需要的张力。
2. PLC控制器控制液压,压下,润滑,等外部设备,同时将操作工设定的数据实时的通过PROFIUBS现场总线传输给6RA70直流调速装置。
3.采用油马达,利用液压装置实现对轧机机心的压力控制,采用上,下各10个轧辊相互之间的挤压力实现对不锈钢板的轧制。
4.甲方要求轧制线速度,主轧120M/分,平整 90M/分。
5.该设备为国内首家自发研制的20辊轧机。
三系统配置与功能实现根据现场实际情况和功能扩展要求,主轧机我们采用两台450KW的直流电机作为前后卷取电机,采用一台1250KW的电机作为主轧电机,平整机我们采用两台250KW的直流电机作为前后卷取电机,采用一台400KW的电机作为平整电机。
采用西门子S7 300系列的315-2DP的CPU 作为主控制器,采用ET200分布式I/O作为前后操作箱的控制装置。
西门子S7-300、6RA70控制器、分布式I/O ET200,特点如下:1.采用CPU315-2DP作为主控制器,利用CPU315内存大、速度快、支持PROFIBUS现场总线的特点,充分满足轧钢行业要求响应速度快,控制灵敏,要求复杂,现场施工简单的要求;2.采用远程I/O方案,最大限度减少接线;轧钢行业要求控制器对操作工的操作指令有及其灵敏的相应速度,这就造成了现场操作箱按钮密布的现象,随之带来的就是现场布接线非常复杂,采用远程分布式I/O方式可以最大限度的减少接线。
热轧实验轧机过程控制系统的研究的开题报告

热轧实验轧机过程控制系统的研究的开题报告一、项目背景热轧是金属材料加工的一种重要方法,广泛应用于钢铁、有色金属、合金等领域。
在热轧生产中,轧机过程是关键环节之一,其产品质量的好坏直接影响着整个生产线的效益。
传统热轧生产中,轧机调整和监控主要依靠工人经验和直觉,容易造成质量波动和产能偏低等问题。
因此,研发一种高效、自动化的轧机过程控制系统具有非常重要的意义。
二、研究目的和意义本项目旨在研究一种基于控制理论和智能算法的热轧实验轧机过程控制系统,并应用于实验轧机中。
具体目的包括:1. 基于轧机过程分析,建立轧机过程数学模型,研究轧制过程中关键参数的变化规律与相互关系;2. 设计一种轧机过程自动控制策略,实现轧机主要参数的闭环控制,在保证产品质量的前提下提高生产效率;3. 将研究成果运用于实验轧机中,评价该控制系统的性能和应用效果。
本研究的意义在于:1. 提高轧机生产率和产品质量,降低生产成本和能源消耗,提高经济效益;2. 推进热轧实验技术的发展和创新,促进钢铁、有色金属等行业技术进步;3. 拓展控制理论和智能算法在工业生产中的应用范围,增强研究者在相关领域的技术水平和竞争力。
三、研究内容和方法1. 系统分析和建模根据实验轧机的结构和工作原理,对轧机工艺流程进行分析,建立轧机过程数学模型,分析轧机过程中关键参数的变化规律和相互关系。
2. 控制策略设计和优化基于轧机过程分析和模型建立,设计轧机过程自动控制策略,并运用控制理论和智能算法进行系统优化。
3. 实验验证和评价将研究成果应用于实验热轧轧机中,进行实验验证和性能评价,比较控制前后的生产效率和产品质量等指标。
四、研究工作计划本项目总计工作周期为18个月,计划分为四个阶段进行:1. 材料准备和文献综述(1个月):对研究领域的相关文献进行搜集和阅读,了解国内外研究现状和前沿技术。
2. 系统分析和建模(4个月):对实验轧机进行全面分析和建模,提取轧机过程中关键参数,建立数学模型。
热轧板带厚度自动控制原理和方法

热轧板带厚度自动控制原理和方法摘要:厚度自动控制系统是热连轧精轧机组自动控制中的一个极为重要的组成部分,是实现热轧高精度轧制的重要手段。
本文阐述了厚度控制技术的意义,分析了板带钢厚度波动的原因,概述了带钢厚度控制原理,总结出精轧机组中厚度自动控制策略。
关键词:热连轧;液压AGC;厚度自动控制0 引言板带材在工业和日常生活中的应用是十分重要的,对于板带钢来说,在所有尺寸精度指标中,厚度精度指标是最基本、最重要的指标,它关系着钢铁企业的经济效益。
随着科学技术的快速发展,用户对板带钢厚度精度的要求越来越高,厚度自动控制是实现厚度精度、提高带钢质量的重要方法之一,可获得板带钢纵向厚度的均匀性,它主要取决于精轧机组。
1 板带钢厚度波动的原因根据弹性方程:,式中:h——轧出厚度,mm;——辊缝,mm;——轧制力,N;——轧机的总刚度,N/mm,可见轧机轧出的带钢厚度取决于轧机辊缝开口大小和轧机弹跳量,因此凡是会改变轧机空载辊缝和轧制力大小的因素都会影响到轧出的带钢厚度。
1.1影响轧机空载辊缝的主要因素轧机空载辊缝的变化主要受轧机机械设备和液压装置方面干扰因素的影响,包括轧辊在轧制过程中的热膨胀、磨损、轧辊制造工艺带来的偏心以及轧辊油膜轴承厚度的变化。
轧辊自身的椭圆度和偏心会造成带钢厚度的周期性波动,轧辊磨损和热膨胀分别使得轧机实际空载辊缝增大和减小。
这些都是在压下螺钉位置不变的情况下使实际辊缝发生变化,造成板带钢厚度波动。
1.2影响轧制力的主要因素轧制力变化主要受轧件方面及轧制工艺方面原因影响。
轧件方面原因主要是由于上游机架未能消除的厚度偏差导致的来料厚度波动、加热温度不均匀和轧制过程中温降不一致导致的轧件温度的波动。
轧制工艺条件因素主要为轧制前后张力的变化、轧制速度的变化、摩擦因素的波动。
连轧机组穿带过程的头部张力建立过程和上游机架抛钢后尾部失张对带钢头部厚度有明显影响,轧制过程中张力变化也会影响带钢其他部位厚度,在热轧过程中,为了防止堆钢和减少带钢窜辊,通常采用恒定小张力轧制。
热轧卷取机自动控制系统的设计与实现
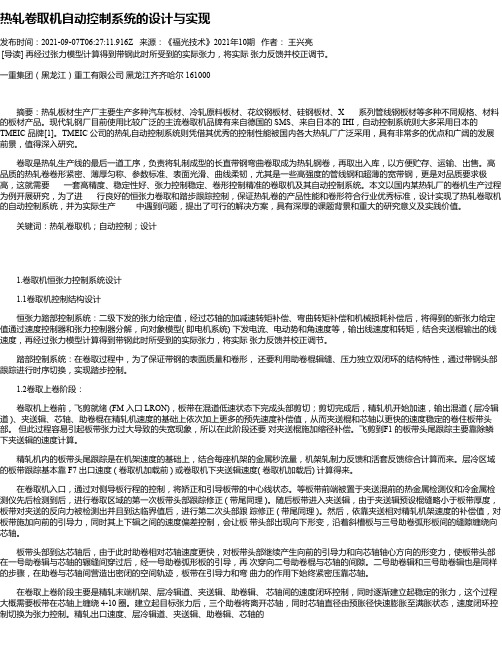
热轧卷取机自动控制系统的设计与实现发布时间:2021-09-07T06:27:11.916Z 来源:《福光技术》2021年10期作者:王兴亮[导读] 再经过张力模型计算得到带钢此时所受到的实际张力,将实际张力反馈并校正调节。
一重集团(黑龙江)重工有限公司黑龙江齐齐哈尔 161000摘要:热轧板材生产厂主要生产多种汽车板材、冷轧原料板材、花纹钢板材、硅钢板材、X 系列管线钢板材等多种不同规格、材料的板材产品。
现代轧钢厂目前使用比较广泛的主流卷取机品牌有来自德国的 SMS、来自日本的 IHI,自动控制系统则大多采用日本的TMEIC 品牌[1]。
TMEIC 公司的热轧自动控制系统则凭借其优秀的控制性能被国内各大热轧厂广泛采用,具有非常多的优点和广阔的发展前景,值得深入研究。
卷取是热轧生产线的最后一道工序,负责将轧制成型的长直带钢弯曲卷取成为热轧钢卷,再取出入库,以方便贮存、运输、出售。
高品质的热轧卷卷形紧密、薄厚匀称、参数标准、表面光滑、曲线柔韧,尤其是一些高强度的管线钢和超薄的宽带钢,更是对品质要求极高,这就需要一套高精度、稳定性好、张力控制稳定、卷形控制精准的卷取机及其自动控制系统。
本文以国内某热轧厂的卷机生产过程为例开展研究,为了进行良好的恒张力卷取和踏步跟踪控制,保证热轧卷的产品性能和卷形符合行业优秀标准,设计实现了热轧卷取机的自动控制系统,并为实际生产中遇到问题,提出了可行的解决方案,具有深厚的课题背景和重大的研究意义及实践价值。
关键词:热轧卷取机;自动控制;设计1.卷取机恒张力控制系统设计1.1卷取机控制结构设计恒张力踏部控制系统:二级下发的张力给定值,经过芯轴的加减速转矩补偿、弯曲转矩补偿和机械损耗补偿后,将得到的新张力给定值通过速度控制器和张力控制器分解,向对象模型( 即电机系统) 下发电流、电动势和角速度等,输出线速度和转矩,结合夹送棍输出的线速度,再经过张力模型计算得到带钢此时所受到的实际张力,将实际张力反馈并校正调节。
热轧基础自动化控制系统概述 [兼容模式]
![热轧基础自动化控制系统概述 [兼容模式]](https://img.taocdn.com/s3/m/1ab1c958852458fb770b567e.png)
+
总弯辊力基准
+
+
+
板形修正量
手动修正量
正弯检测
−
PID
+
正弯负弯 基准生成
+
PID
−
负弯检测
伺服阀 非线性化
正弯辊 伺服阀给定
伺服阀 非线性化
负弯辊 伺服阀给定
RAL
液压窜辊控制系统
薄带钢轧制时,为了减小轧辊的磨 损和降低边缘降,并扩大带钢的凸 度控制范围,在轧机上装备液压窜 辊装置,在保持良好平直度的同时 得到要求的板形。
RAL
热轧自动化系统硬件及网络配置
RAL
热连轧生产线自动化系统构成
¾ 配置有基础自动化与过程自动化系统,完成轧线厚度控制系统、宽度 控制系统、主令系统及辅助逻辑控制
¾ 采用高性能PLC和PC服务器,具有很高的系统处理及执行速度,并配 置有IBA数据采集及分析系统
¾ 过程自动化和基础自动化以及基础自动化之间使用工业以太网通讯, 基础自动化与传动及远程站之间使用Profibus-DP网通讯
RAL
活套高度控制
活套高度的控制实际上是活套量的控制
采用模糊控制
A
+PID调节器
Fi
R1
Fi+1
的复合控制策
略,当活套的
B
α
L1
β
C
设定值与给定
R
值偏差较大时,
θ
L3
θ0
采用模糊控制 器;当设定和 反馈偏差小于
L
一定值时,采
用PID调节器。
ΔL = (L1+ Rcosθ)2 +(Rsinθ − L3 + R1)2 + (L − L1− Rcosθ)2 +(Rsinθ − L3 + R1)2 − L
自动板形控制系统在热轧生产线的应用
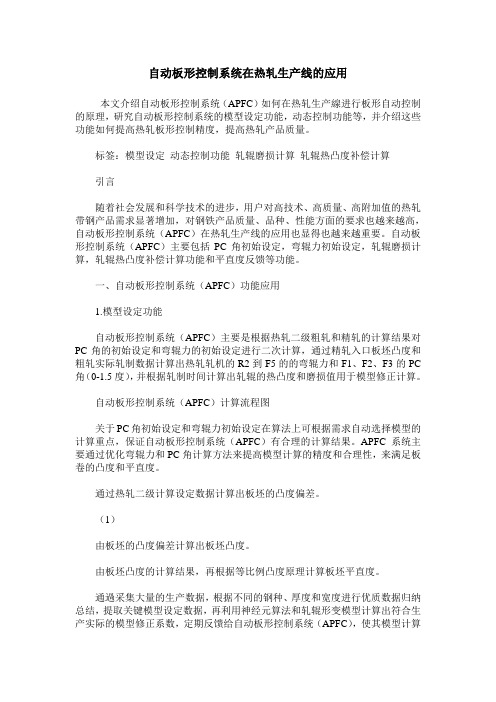
自动板形控制系统在热轧生产线的应用本文介绍自动板形控制系统(APFC)如何在热轧生产線进行板形自动控制的原理,研究自动板形控制系统的模型设定功能,动态控制功能等,并介绍这些功能如何提高热轧板形控制精度,提高热轧产品质量。
标签:模型设定动态控制功能轧辊磨损计算轧辊热凸度补偿计算引言随着社会发展和科学技术的进步,用户对高技术、高质量、高附加值的热轧带钢产品需求显著增加,对钢铁产品质量、品种、性能方面的要求也越来越高,自动板形控制系统(APFC)在热轧生产线的应用也显得也越来越重要。
自动板形控制系统(APFC)主要包括PC角初始设定,弯辊力初始设定,轧辊磨损计算,轧辊热凸度补偿计算功能和平直度反馈等功能。
一、自动板形控制系统(APFC)功能应用1.模型设定功能自动板形控制系统(APFC)主要是根据热轧二级粗轧和精轧的计算结果对PC角的初始设定和弯辊力的初始设定进行二次计算,通过精轧入口板坯凸度和粗轧实际轧制数据计算出热轧轧机的R2到F5的的弯辊力和F1、F2、F3的PC 角(0-1.5度),并根据轧制时间计算出轧辊的热凸度和磨损值用于模型修正计算。
自动板形控制系统(APFC)计算流程图关于PC角初始设定和弯辊力初始设定在算法上可根据需求自动选择模型的计算重点,保证自动板形控制系统(APFC)有合理的计算结果。
APFC系统主要通过优化弯辊力和PC角计算方法来提高模型计算的精度和合理性,来满足板卷的凸度和平直度。
通过热轧二级计算设定数据计算出板坯的凸度偏差。
(1)由板坯的凸度偏差计算出板坯凸度。
由板坯凸度的计算结果,再根据等比例凸度原理计算板坯平直度。
通過采集大量的生产数据,根据不同的钢种、厚度和宽度进行优质数据归纳总结,提取关键模型设定数据,再利用神经元算法和轧辊形变模型计算出符合生产实际的模型修正系数,定期反馈给自动板形控制系统(APFC),使其模型计算结果与生产状况保持一致。
自动板形控制系统(APFC)还可以根据用户需求进行模型计算权重分配,当需要对某一项技术指标(对平直度需求或对凸度需求)进行侧重时,模型会自动提高该项的权重,从而调高该模型计算成功率来达到用户预期需求。
热轧厚度控制系统

福欣特殊鋼專案組組內教育訓練
8
(4)张力式厚度自动控制系统
控制原理:由测厚仪直接测得带钢轧出厚度偏差,改变
张力系统的张力设定值,以改变轧制压力,或直接改变轧制
速度来控制带钢轧出厚度。
特点
张力法只用于调节小厚度偏差的情 况,作为精调。
2012/7/23
福欣特殊鋼專案組組內教育訓練
9
福欣特殊钢有限公司
热轧厚度控制系统
一、厚度自动控制的基本原理 二、厚度自动控制系统的组成
ห้องสมุดไป่ตู้
三、厚度自动控制系统的基本型式
报告人:楊朝琪 福欣技术处
2012/7/23
福欣特殊鋼專案組組內教育訓練
1
一、 厚度自动控制的基本原理
通过测厚仪或传感器(如辊缝仪和压头等)对带钢实 际轧出厚度连续地进行测量,并根据实测值与给定值相 比较后的偏差信号,借助于控制回路和装置或计算机的 功能程序,改变压下位置、张力或轧制速度,把板带厚 度控制在允许偏差范围之内。 干
福欣特殊鋼專案組組內教育訓練
6
前馈式厚度自动控制
控制原理:测厚仪安装在轧机入口侧,测量出其入 口厚度H,并与给定厚度值H0相比较,当有厚度偏差ΔH时,
便预先估计出可能产生的轧出厚度偏差Δh,确定为消除
此Δh值所需的辊缝调节量ΔS ,当执行机构完成调节时, 检测点正好到达辊缝处,厚差消失。 特点 超前的控制手段 用来控制入口厚度波动引起的轧出厚度波动
2012/7/23
福欣特殊鋼專案組組內教育訓練
7
(3)厚度计式厚度自动控制系统
控制原理:实际的辊缝值由辊缝仪检测,经自整角
机将信号送给编码器,由编码器将模拟量变为数字量,
棒材轧机的自动控制系统

轧钢厂一车间棒材轧机的自动控制系统轧钢厂一车间棒材生产线是由包头钢铁设计研究院设计。
该套年产量60万t的棒材轧机于2003年5月建成投产以后,设备运行基本稳定可靠,单位小时产量已经达到了原设计水平。
1主要工艺设备和系统配置1.1工艺设备概况该套轧机为连续式,由7台∮550mm(3台)/∮450mm (4台)可逆初轧机、1台切头切尾和事故碎断用的切头飞剪、、4台∮380mm中轧机、1台气钢推动的事故卡断剪、6台∮320㎜平立式精轧机(12H、14H、16H三架水平轧机和13V、15V、17V三架立式轧机组成)、6个活套装置、精轧后辊道、1台成品倍尺飞剪、冷床输入辊道(四段)、裙板拔钢装置、步进式冷床及横移装置、冷床输出辊道、冷剪和成品收集等设备组成,该轧机出口速度最高可达15m/s,可生产∮16~50㎜规格的圆钢和螺纹钢。
1.2系统配置根据工艺和生产的要求,在轧制线上配备了2套工控微机(在主操作台)和5套plc装置(在主电PLC室)。
Plc1 主要用于轧机辅助设备控制(如液压站、辊道、风机等);Plc 2主要完成轧制线17台直流电机的速度级联调速控制,6个活套的控制,切头飞剪和冷床的控制;Plc3用于成品倍尺飞剪区域设备的控制(整套引进意大利DANELI公司)、plc4用于精整区所有设备的控制、plc5用于冷剪设备的控制(整套引进意大利DANELI公司)。
2套工控微机各含有1个操作键盘、1台监控器CRT和1台主机。
2套工控微机都设在主操作台站内,其中,1套工控微机用于轧制表的输入和轧制速度等显示。
另1套工控微机用于监控并显示现场设备所处的状态,可记录当前和历史数据,它的CRT显示内容与前1套工控微机的内容基本相同,但是,在主操作室内,各输入参数既可供显示,也能做修改。
2主操作站功能和CRT显示主操作站内的工控微机有一个人机对话监控系统,主要用于输入各种轧制和控制用参数。
轧机监控系统的画面构成和相互调用关系.本监控系统从轧钢的工艺特点和操作要求出发,包括了轧机系统的所有主要工艺流程、检测参数、设备状态的显示,也集中了轧钢系统的监视和控制得到完全的统一。
中厚板轧机计算机控制系统的开发

中厚板轧机计算机控制系统的开发中厚板是钢铁工业产品的重要组成部分。
随着我国中厚板材生产线的新建和改造,中厚板材市场竞争日益激烈,因此提高产品质量和成材率,降低生产成本成为各个厂家追求的目标。
为此,除了努力提高管理水平外,对中厚板材生产控制自动化水平的要求也越来越高。
在国内中厚板轧机新建和改造项目中,大量的采用了国内外先进的技术和设备,实现了坯料跟踪、轧件尺寸形状的高精度控制、控制轧制和控制冷却等生产过程的计算机系统的开发。
系统结构设计中厚板分布式计算机控制系统常采用三级设计,一级为设备控制系统,即基础自动化,二级为过程控制,三级为生产管理。
基础自动化保证生产设备按照设定指令正常运行,并将生产线检测仪表信号和设备本体的采集信号实时的发送给过程计算机,为模型的计算、修正和学习提供数据基础;过程控制计算机基于工业以太网与PLC进行数据通讯,根据生产现场采集的数据实现物料跟踪、任务调度、规程优化计算及过程数据存储等任务;生产管理级主要完成生产计划的编制、工序的协调和产品质量管理等功能。
针对中厚板轧制的特点,为满足轧件跟踪、自动运钢和过程控制的要求,在轧线布置有相应的检测仪表。
为了满足控制轧制的要求,在机前、机后均设有两个待温辊道,可以实现钢坯的两待一轧,在每个待温区的入口、出口设有热金属检测器,以实现钢坯待温过程的自动摆动。
同时在待温区、轧机前后安装有相应的测温仪,为过程模型的计算和自学习提供温度基准数据。
基础自动化1主要功能轧机基础自动化的主要任务包括轧区辊道控制、主传动控制、电动压下位置自动控制(APC)、液压压下厚度自动控制(AGC)、清零、刚度测试、偏心补偿、数据通讯等。
控制系统利用PROFIBUS DP网络连接远程I/O、轧线检测仪表、变频器等设备,同时集中了全线的检测仪表信号和各设备之间的连锁信号。
轧机控制系统中安装的顶帽传感器、液压缸位移传感器、轧制力传感器、油压传感器、板宽测量仪、板厚测量仪等检测仪表为实现高速度和高精度的钢板厚度控制和液压位置自动控制提供了必要条件。
热粗轧机厚度自动控制系统应用

热粗轧机厚度自动控制系统应用铝材厚度控制精度是热轧铝板产品质量的关键指标之一,研究厚度自动控制系统技术及其应用具有重要意义。
基于此,文章综合分析了厚度误差产生的因素,同时阐述了厚度自动控制的具体应用以及故障诊断。
标签:热粗轧机;厚度自动控制系统;弹跳;辊缝引言厚度控制系统是轧制自动化系统中不可缺少的一部分,它关系到板带的厚控精度与性能及其成品率。
热粗轧轧制的产品质量,不单单影响在粗轧机工序,影响到整个热轧线的生产效率,更能影响到热精轧的轧制产品质量问题。
因此厚度控制成为生产中的重中之重,通过自动厚度控制达到消除厚差以及产品质量问题。
1 厚度误差产生原因分析一般而言,厚度误差的产生原因包括三个方面,即轧件材料因素、轧机控制系统干扰因素和机械设备因素。
(1)轧件来料干扰因素。
其中,轧件来料的宽度、硬度、厚度、平直度和断面等因素都会影响到产品的厚度。
(2)轧机控制系统的干扰因素。
控制系统中影响铝板厚度精度的主要因素包括轧机的速度、轧制力、弯辊、张力、厚度传感器。
(3)机械及液压装置的干扰因素。
轧机机械装置本身的缺点及某个参数的变化会影响出口带钢的厚度,表现为轧辊弹跳、轧机刚度、轧辊直径及宽度的变化、轧辊热胀冷缩、轧辊轴承油膜厚度等。
2 厚控控制系统组成(1)检测装置包含位置测量和压力测量,其中压下测量采用增量式编码器,用于检测压下电机的速度,进而计算出压下量。
压上测量采用磁尺位移传感器,测量压上缸行走位置,用于位置环控制。
压力传感器,用于测量压上油缸压力,用于压力环控制。
磁尺位移传感器具有高精度、高可靠性、高频响性,响应频率快,维护方便等优点。
压力传感器采用进口元件,保证高可靠性和稳定性。
高可靠性的检测装置,保证板带的轧制精度。
(2)执行机构包含压上液压油缸,压下电机和螺杆,弯辊缸,伺服阀,伺服阀放大版,西门子S7-400PLC控制器。
通过调节压上缸伺服阀的进油和出油来控制油缸的升缩,进而达到精确控制辊缝的目的。
热轧带钢厚度自动控制系统的研究

热轧带钢厚度自动控制系统的研究提要:厚度精度是热轧带钢产品质量的关键指标,本文综合运用了厚度自动控制的典型模型以及补偿措施,取得了良好效果。
文章对于冶金带钢轧制宽度控制系统的设计应用有很大的参考价值。
关键词:厚度控制;监控AGC;补偿措施1.概述厚度自动控制系统(AGC),是英国钢铁协会于20世纪40年代末50年代初发明的,该方法称之谓BIRAAGC。
之后日本、德国、美国等发明了测厚计型AGC,称之谓GMAGC。
BISRAAGC控制模型中只有轧机参数M,没有轧件参数Q,从理论上讲是不完备的。
采用传统轧制力预报模型计算,最大偏差多在20%以上,所以传统的常规的数学模型不能提供足够精确的近似值。
即使采用自适应技术,利用实测数据重新计算模型参数,但由于模型本身结构的限制,也难于适应实际生产过程。
目前,板厚自动控制技术(AGC)已日益成熟,纵向厚差的控制精度基本得到了解决。
现代控制理论及智能控制理论与技术也被广泛地应用于轧制过程中的厚度控制。
己经取得了巨大成果和经济效益。
2厚差产生原因分析(1)轧机机械及液压装置的干扰因素。
轧机机械装置本身的缺点及某个参数的变化将会使轧机的刚度及空载下的辊缝产生人们所不希望的一些变化,从而影响出口带钢的厚度,表现为轧辊直径及宽度的变化、轧辊磨损、轧辊偏心、轧辊热胀冷缩、轧辊轴承油膜厚度、压下螺丝及附件、液压缸及附件、轧机牌坊、轧机震动等。
(2)轧机控制系统的干扰因素。
轧制速度、带钢张力、弯辊、辊缝、轧制力、厚度监控器等系统的控制品质也是造成带钢厚度变化的主要因素。
(3)轧件的干扰因素。
来料厚度、来料宽度、来料硬度、来料断面、来料平直度的变化直接影响着成品厚度。
3热轧带钢AGC控制方式的综合研究与运用3.1 GMAGCGM(厚度计)方式AGC即为轧制力反馈AGC,简称GMAGC。
对于带钢热连轧机精轧机组,除入口和出口处设置有测厚仪外,其他各机架的出口处无法装设测厚仪,因此采用间接测厚AGC系统。
粗轧机厚度自动控制系统的应用
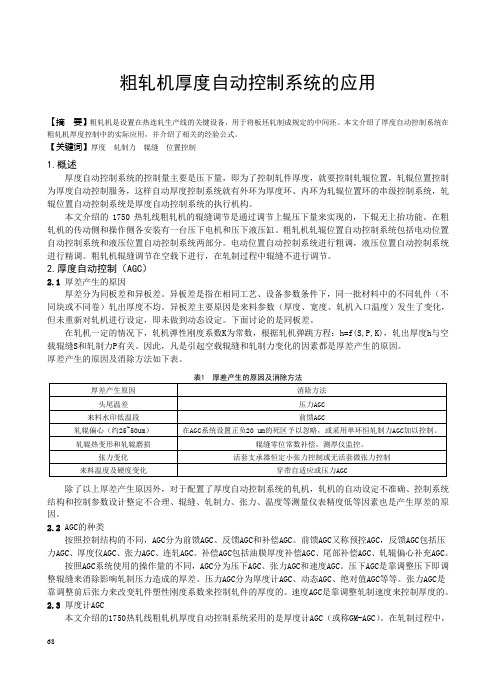
粗轧机厚度自动控制系统的应用【摘要】粗轧机是设置在热连轧生产线的关键设备,用于将板坯轧制成规定的中间坯。
本文介绍了厚度自动控制系统在粗轧机厚度控制中的实际应用,并介绍了相关的经验公式。
【关键词】厚度轧制力辊缝位置控制1.概述厚度自动控制系统的控制量主要是压下量,即为了控制轧件厚度,就要控制轧辊位置,轧辊位置控制为厚度自动控制服务,这样自动厚度控制系统就有外环为厚度环、内环为轧辊位置环的串级控制系统,轧辊位置自动控制系统是厚度自动控制系统的执行机构。
本文介绍的1750热轧线粗轧机的辊缝调节是通过调节上辊压下量来实现的,下辊无上抬功能。
在粗轧机的传动侧和操作侧各安装有一台压下电机和压下液压缸。
粗轧机轧辊位置自动控制系统包括电动位置自动控制系统和液压位置自动控制系统两部分。
电动位置自动控制系统进行粗调,液压位置自动控制系统进行精调。
粗轧机辊缝调节在空载下进行,在轧制过程中辊缝不进行调节。
2.厚度自动控制(AGC)2.1厚差产生的原因厚差分为同板差和异板差。
异板差是指在相同工艺、设备参数条件下,同一批材料中的不同轧件(不同块或不同卷)轧出厚度不均。
异板差主要原因是来料参数(厚度、宽度、轧机入口温度)发生了变化,但未重新对轧机进行设定,即未做到动态设定。
下面讨论的是同板差。
在轧机一定的情况下,轧机弹性刚度系数K为常数,根据轧机弹跳方程:h=f(S,P,K),轧出厚度h与空载辊缝S和轧制力P有关。
因此,凡是引起空载辊缝和轧制力变化的因素都是厚差产生的原因。
厚差产生的原因及消除方法如下表。
表1 厚差产生的原因及消除方法除了以上厚差产生原因外,对于配置了厚度自动控制系统的轧机,轧机的自动设定不准确、控制系统结构和控制参数设计整定不合理、辊缝、轧制力、张力、温度等测量仪表精度低等因素也是产生厚差的原因。
2.2 AGC的种类按照控制结构的不同,AGC分为前馈AGC、反馈AGC和补偿AGC。
前馈AGC又称预控AGC,反馈AGC包括压力AGC、厚度仪AGC、张力AGC、连轧AGC。
自动控制原理实验报告2

自动控制原理课程实验2010-2011学年第一学期02020801班张驰2008300566✧ 课本实验内容6-26 热轧厂的主要工序是将炽热的钢坯轧成具有预定厚度和尺度的钢板,所得到的最终产品之一是宽为3300mm 、厚为180mm 的标准板材。
他有两台主要的辊轧台:1号台与2号台。
辊轧台上装有直径为508mm 的大型辊轧台,由4470km 大功率电机驱动,并通过大型液压缸来调节轧制宽度和力度。
热轧机的典型工作流程是:钢坯首先在熔炉中加热,加热后的钢坯通过1号台,被辊轧机轧制成具有预期宽度的钢坯,然后通过2号台,由辊轧机轧制成具有与其厚度的钢板,最后再由热整平设备加以整平成型。
热轧机系统控制的关键技术是通过调整热轧机的间隙来控制钢板的厚度。
热轧机控制系统框图如下:扰动)(s N )(s R(1)已知)54(/)(20++=s s s s s G ,而)(s G c 为具有两个相同实零点的PID 控制器。
要求:选择PID 控制器的零点和增益,使闭环系统有两对对等的特征根;(2)考察(1)中得到的闭环系统,给出不考虑前置滤波器)(s G P 与配置适当)(s G P 时,系统的单位阶跃响应;(3)当)(s R =0,)(s N =1/s 时,计算系统对单位阶跃扰动的响应。
✧ 求解过程解:(1)已知)54(/)(20++=s s s s s G)(s G P )(s G C )(0s G选择 s z s K s G c /)()(2+=当取K=4,Z=1.25时,有s s s s s G c 4/25.610/)25.1(4)(2++=+= 系统开环传递函数)54(/)25.1(4)()(2220+++=s s s s s G s G c 闭环传递函数:)25.61094/()5625.15.2(4))()(1/()()()(234200++++++=+=s s s s s s s G s G s G s G s c c φ (2) 当不考虑前置滤波器时,单位阶跃输入作用下的系统输出)25.61094(/)5625.15.2(4)()()(2342++++++==s s s s s s s s R s s C φ系统单位阶跃响应如图1中(1)中实线所示。
铝热轧机板坯的厚度反馈式液压自动控制
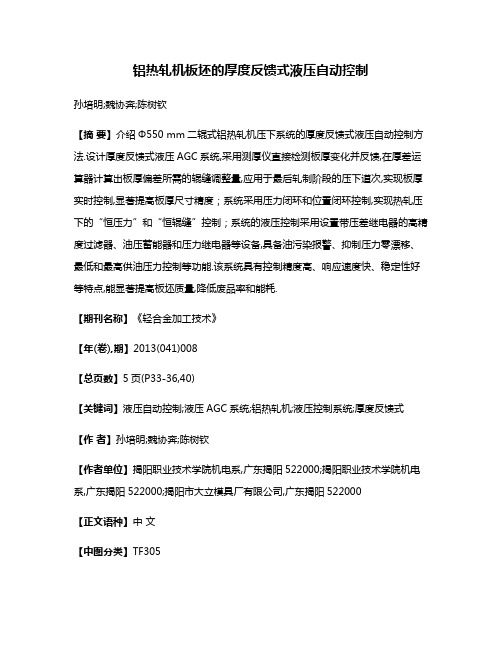
铝热轧机板坯的厚度反馈式液压自动控制孙培明;魏协奔;陈树钦【摘要】介绍Φ550 mm二辊式铝热轧机压下系统的厚度反馈式液压自动控制方法.设计厚度反馈式液压AGC系统,采用测厚仪直接检测板厚变化并反馈,在厚差运算器计算出板厚偏差所需的辊缝调整量,应用于最后轧制阶段的压下道次,实现板厚实时控制,显著提高板厚尺寸精度;系统采用压力闭环和位置闭环控制,实现热轧压下的“恒压力”和“恒辊缝”控制;系统的液压控制采用设置带压差继电器的高精度过滤器、油压蓄能器和压力继电器等设备,具备油污染报警、抑制压力零漂移、最低和最高供油压力控制等功能.该系统具有控制精度高、响应速度快、稳定性好等特点,能显著提高板坯质量,降低废品率和能耗.【期刊名称】《轻合金加工技术》【年(卷),期】2013(041)008【总页数】5页(P33-36,40)【关键词】液压自动控制;液压AGC系统;铝热轧机;液压控制系统;厚度反馈式【作者】孙培明;魏协奔;陈树钦【作者单位】揭阳职业技术学院机电系,广东揭阳522000;揭阳职业技术学院机电系,广东揭阳522000;揭阳市大立模具厂有限公司,广东揭阳522000【正文语种】中文【中图分类】TF305铝锭经过多次轧制加工成板坯,金属变形量大,温度高,易出现板厚不均匀、尺寸精度差、金属性能波动大等问题[1]。
现代铝制品业对热轧板坯要求越来越高,不仅要求板坯厚度薄,板形好,而且要求尺寸精度高。
因此,提高终轧板坯质量是一个重要技术问题,采用板厚液压自动控制是一种较为有效的板厚控制方法。
传统的铝热轧机板厚液压自动控制采用厚度计式液压AGC系统,通过检测压力变化并选取调节系数计算实际板厚,进行厚差补偿,属于间接测厚法,没有考虑轧制速度、热轧机机械精度和轧辊热膨胀等对板厚的影响,计算板厚与实际板厚存在误差。
本文介绍Φ550 mm二辊式铝热轧机压下系统的厚度反馈式液压自动控制方法,设计厚度反馈式液压AGC系统,采用测厚仪直接检测板厚变化并反馈,与各道次预设厚度比较,根据厚度偏差计算出辊缝调整量,实现板厚的实时控制。
一种自动厚度控制系统在热粗轧机上的应用

一种自动厚度控制系统在热粗轧机上的应用发布时间:2021-10-12T07:31:15.262Z 来源:《工程管理前沿》2021年第15期作者:曹宇轩[导读] 热粗轧机由于设备安装精度问题,造成使用功能受限,不能完成超薄冷作板的轧制工艺曹宇轩东北轻合金有限责任公司黑龙江省哈尔滨市 150000摘要:热粗轧机由于设备安装精度问题,造成使用功能受限,不能完成超薄冷作板的轧制工艺,无法满足国内外该类产品的生产要求,严重制约了国内外冷作板片的市场竞争力。
由此决定进行热轧机增大开口度和厚度自动控制方面的开发,以拓宽轧机的生产范围和提高轧制精度,对公司产品产量和质量是双重的保证。
关键词热粗轧机开口度厚度自动控制自动厚度控制系统的核心原理是如何在原有设备的基础上增大轧机开口度,优化液压压上伺服系统控制的精度,增加电动压下位置控制的精度,下面针对各系统作出详细介绍:一、液压压上伺服系统液压伺服系统的设计准则:液压缸(HGC)位于在轧机牌坊下方,支撑辊轴承箱底部。
构思设计实用、可靠的伺服缸,确保热轧机最大开口度达到600mm以上;该伺服缸要有足够的刚度和强度;具有良好的动态特性;1、主要技术参数缸径:1200mm行程:235mm系统额定压力:200-290bar最大轧制力:5600t2、设计方案及结构特征为适应上述加大开口度的需要,同时将增加值的绝大部分从伺服缸内找到出路,通过论证、计算机模拟以及三维有限元的分析,加上其他部分的调整,从而确保最小开口度达到6mm的目标。
通过多次模轧与实际板料轧制的实验,该伺服缸的强度和刚度均满足轧制能力参数要求。
这一方案的特点与优势在于:不改变原支承辊轴承座、也不调整轧制线标高,更不用改变轧机牌坊和基础;与改变轧机牌坊与基础相比,风险小、投资省、施工周期短、维护简便,可大大降低维修成本等。
3、主要技术指标高压部分●5台恒压变量供给泵,4台工作,1台备用,最高压力为350bar;额定工作压力:290bar;额定流量:250dm3/min(单台泵)。
550mm热轧实验机组控制系统研究与应用的开题报告
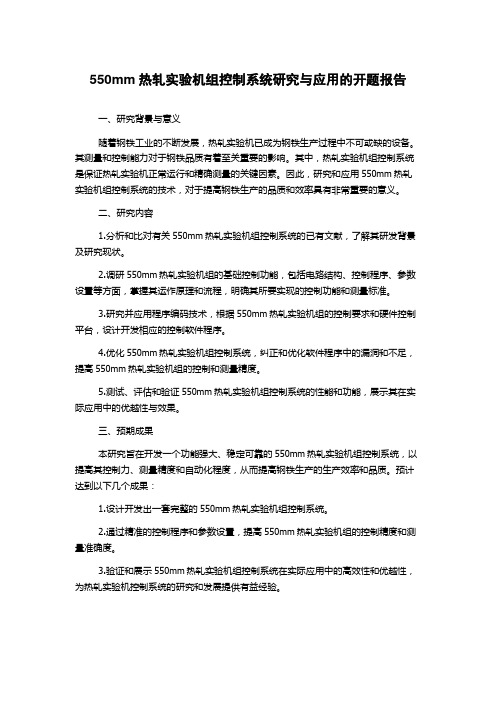
550mm热轧实验机组控制系统研究与应用的开题报告
一、研究背景与意义
随着钢铁工业的不断发展,热轧实验机已成为钢铁生产过程中不可或缺的设备。
其测量和控制能力对于钢铁品质有着至关重要的影响。
其中,热轧实验机组控制系统是保证热轧实验机正常运行和精确测量的关键因素。
因此,研究和应用550mm热轧实验机组控制系统的技术,对于提高钢铁生产的品质和效率具有非常重要的意义。
二、研究内容
1.分析和比对有关550mm热轧实验机组控制系统的已有文献,了解其研发背景及研究现状。
2.调研550mm热轧实验机组的基础控制功能,包括电路结构、控制程序、参数设置等方面,掌握其运作原理和流程,明确其所要实现的控制功能和测量标准。
3.研究并应用程序编码技术,根据550mm热轧实验机组的控制要求和硬件控制平台,设计开发相应的控制软件程序。
4.优化550mm热轧实验机组控制系统,纠正和优化软件程序中的漏洞和不足,提高550mm热轧实验机组的控制和测量精度。
5.测试、评估和验证550mm热轧实验机组控制系统的性能和功能,展示其在实际应用中的优越性与效果。
三、预期成果
本研究旨在开发一个功能强大、稳定可靠的550mm热轧实验机组控制系统,以提高其控制力、测量精度和自动化程度,从而提高钢铁生产的生产效率和品质。
预计达到以下几个成果:
1.设计开发出一套完整的550mm热轧实验机组控制系统。
2.通过精准的控制程序和参数设置,提高550mm热轧实验机组的控制精度和测量准确度。
3.验证和展示550mm热轧实验机组控制系统在实际应用中的高效性和优越性,为热轧实验机控制系统的研究和发展提供有益经验。