FMEA Introduction-B
FMEA手册
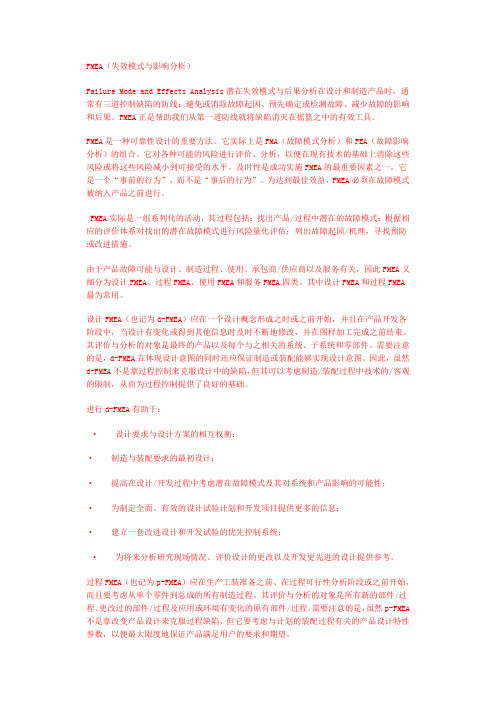
FMEA(失效模式与影响分析)Failure Mode and Effects Analysis潜在失效模式与后果分析在设计和制造产品时,通常有三道控制缺陷的防线:避免或消除故障起因、预先确定或检测故障、减少故障的影响和后果。
FMEA正是帮助我们从第一道防线就将缺陷消灭在摇篮之中的有效工具。
FMEA是一种可靠性设计的重要方法。
它实际上是FMA(故障模式分析)和FEA(故障影响分析)的组合。
它对各种可能的风险进行评价、分析,以便在现有技术的基础上消除这些风险或将这些风险减小到可接受的水平。
及时性是成功实施FMEA的最重要因素之一,它是一个“事前的行为”,而不是“事后的行为”。
为达到最佳效益,FMEA必须在故障模式被纳入产品之前进行。
FMEA实际是一组系列化的活动,其过程包括:找出产品/过程中潜在的故障模式;根据相应的评价体系对找出的潜在故障模式进行风险量化评估;列出故障起因/机理,寻找预防或改进措施。
由于产品故障可能与设计、制造过程、使用、承包商/供应商以及服务有关,因此FMEA又细分为设计FMEA、过程FMEA、使用FMEA和服务FMEA四类。
其中设计FMEA和过程FMEA 最为常用。
设计FMEA(也记为d-FMEA)应在一个设计概念形成之时或之前开始,并且在产品开发各阶段中,当设计有变化或得到其他信息时及时不断地修改,并在图样加工完成之前结束。
其评价与分析的对象是最终的产品以及每个与之相关的系统、子系统和零部件。
需要注意的是,d-FMEA在体现设计意图的同时还应保证制造或装配能够实现设计意图。
因此,虽然d-FMEA不是靠过程控制来克服设计中的缺陷,但其可以考虑制造/装配过程中技术的/客观的限制,从而为过程控制提供了良好的基础。
进行d-FMEA有助于:·设计要求与设计方案的相互权衡;·制造与装配要求的最初设计;·提高在设计/开发过程中考虑潜在故障模式及其对系统和产品影响的可能性;·为制定全面、有效的设计试验计划和开发项目提供更多的信息;·建立一套改进设计和开发试验的优先控制系统;·为将来分析研究现场情况、评价设计的更改以及开发更先进的设计提供参考。
FMEA简述

缺陷产品;不需要分拣;需要向供应商提供反馈
触感令人略微感觉不舒服。
1
非常低 没有可觉察到的影响
没有可觉察到的影响或没有影响
没有可觉察到的影响。
注:绿色为公司重点采用的相关评判标准,灰色为不常用标准。
十、第五版FMEA内容——失效原因
· 由小组结合特定的知识和经验来确定 · 失效原因能够直接确定或者通过理解失效的原理来确定
八、第四版FMEA
过程步骤/功能
要求
潜在失效模式
潜在失效影 响
SEV 严重度
分类
潜在失效原因
OCC发生 度
现行过程控制 预防
Plasma清洗
芯片背面 无污染
D/B 焊胶层 芯片背面污染 脱落,电参
失效
8
Plasma能量&时间参 数不恰当 Plasma工艺气压值偏 小或偏大
气体流量偏小
1.限制参数编辑权限,仅工程部负责人有
· 描述失效模式对客户的影响:
- 内部客户(下一个操作/后续操作/操作目标) - 外部客户(下一级/OEM/经销商)政府法律法规
- 产品或产品最终用户/操作者 - 立法机构
要求 四个螺钉
失效模式
影响
最终顾客:座垫松动,有噪音。
少于四个螺钉 制造和装配:由于受影响的部分,因而停止发
运,并进行额外挑选和返工。
1.要求作业员每班检查气罐接口是否漏气 2.气体流量超出范围时,设备自动报警
DET RP 探测度 N
4 64
4 64 2 32
推荐措施 NONE NONE NONE
Action Results/实施结果
职责和目标完 成日期
采取的措施 和有效日期
SE V 严重 度
FMEA培训教材
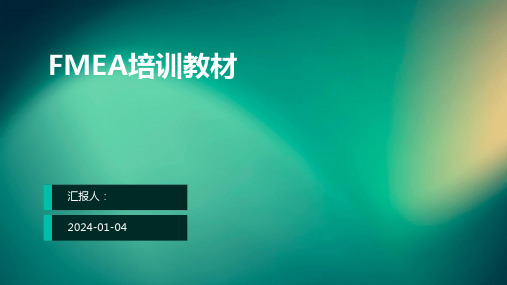
总结词
汽车刹车系统FMEA分析是一个典型的故障模式与影响 分析案例,通过对刹车系统的各个组成部分进行故障 模式分析,评估其对整个系统性能的影响。
详细描述
汽车刹车系统FMEA分析首先识别刹车系统中的各个组 成部分,然后对每个组成部分进行故障模式分析,包括 可能的故障类型、故障发生概率和故障影响程度。接着 ,根据分析结果,评估每个故障模式对刹车系统整体性 能的影响,并确定优先改进顺序。最后,制定相应的改 进措施和预防措施,降低故障发生概率和影响程度。
高级功能
介绍FMEA软件的高级功能,如 影响分析、优先级排序、报告 生成等。
常见问题与解决方案
列举使用FMEA软件过程中可能 遇到的问题,并提供相应的解 决方案。
FMEA软件应用实例
01
汽车刹车系统FMEA分析
通过实际案例,演示如何使用FMEA软件对汽车刹车系统进行故障模式
、影响和优先级分析,并提出相应的改进措施。
FMEA软件应用领域
FMEA软件广泛应用于汽车、航空、电子、医疗等制造业 领域,用于提高产品质量、降低产品风险和优化产品设计 。
FMEA软件操作教程
软件安装与启动
介绍如何下载和安装FMEA软件 ,以及如何启动软件并进入操 作界面。
基础操作
介绍FMEA软件的基本操作,如 创建项目、添加部件、设置故 障模式等。
感谢您的观看
FMEA的应用范围
总结词
FMEA可以应用于各种行业和领域,如汽车 、航空、医疗、电子等,用于评估产品设计 或流程的可靠性和安全性。
详细描述
FMEA是一种通用的质量工具,可以应用于 各种行业和领域。在汽车行业中,FMEA可 以用于评估汽车零部件的可靠性,提高车辆 的安全性能;在航空领域,FMEA可以用于 评估飞机设计和制造过程中的潜在故障模式 ,确保飞行的安全;在医疗领域,FMEA可 以用于评估医疗设备的可靠性和安全性,提 高患者的治疗效果;在电子行业,FMEA可 以用于评估产品的设计和制造流程,提高产 品的质量和可靠性。
FMEA我的讲义

FMEA的实施 FMA:Failure Mode Analysis
FMA(失效模式分析) FMEA(潜在失效模式及后果分析)
失效已经产生
失效还未产生,可能发生,但不是一 定要发生
核心:纠正
核心:预防
诊断已知的失效
评估风险和潜在失效模式的影响
开始于产品设计和工艺开发活动之前
指引开发和生产
指引贯穿整个产品周期
• 4、1985年由国际电工委员会(IEC)出版的FMECA 国际标准(IEC812),即参考MIL-STD-1629A加以部分 修改而成。
13
FMEA 之適用範圍
• 1、ISO9004 8.5節FMEA作為設計審核的要項,另 FTA(失效樹分析)風險分析亦是。
• 2、CE標志,以FMEA作為安全分析方法。
E: Effect 後果
Effect談三種: 1.對本身的立即影響
2.對同一水平的影響, 也可能對下一工序的影響 3.對產品使用者的影響
6
FMEA定義
後果的通常表現形式:
人身安全 不舒服的氣味 不穩定 作業中斷 無法繫緊 無法安裝 損壞裝備
手感不良
作業過多
無法操作
操作不良
車控不良
顧客不滿意
滲漏
外觀不良
12
FMEA 之沿革
• 1、FMEA的前身為FMECA,是在1950由格魯曼飛機 提出,用在飛機主控系統的失效分析
• 2、波音與馬丁公司在1957年正式編訂FMECA的作业 程序,列在其工程手冊中
• 3、60年代初期,美太空总署将FMECA成功的应用于 太空计划。美军同时也开始应用FMECA技术,并于 1974年出版MIL-STD-1629 FMECA作业程序。
FMEA培训教材-PPT精选全文

客户要求 方便调整
舒适 移动顺畅
ቤተ መጻሕፍቲ ባይዱ
产品规格 调节高度 坐垫厚度 旋转角度 椅轮松紧
9
1
3
9
3
1
9
9
重要性 60% 30% 10%
分值
640
330
180
90
FMEA 得原理
客户要求 方便调整
舒适 移动顺畅
分值
产品规格 调节高度 坐垫厚度 旋转角度 椅轮松紧
9
1
3
9
3
1
9
9
640
330
180
90
参数
上升50CM
FMEA 得原理
一、FMEA基本知识
练习:
公司产品:车门 客户要求:
•方便开关 •噪音小 •安全
FMEA 得原理
FMEA 得原理
FMEA 得原理
客户质量要求 Input
客户质量目标
FMEA Output
CTQ 清单 CP 控制计划
FMEA
FMEA 得原理
Output
CTQ 清单
CTQ产出原则:
压 合 状 态
方法
特
样本Sample
殊 特 性 分
产品特 性/过程 参数规 格/公差
评价/ 测量技
术
容 量
频率
类
《
首检
MODULE 检验标
准》
5-20倍 显微镜
6P CS
:6PCS/ 抽检 : 每10PCS
抽1PCS
反应计
控制方法/ 统计技术
责任人
划
《CD-HFM0419701 LCM 镜检 不良明细
措施?
FMEA简介

3. FMEA解释
●失效定义
失效是指系统的组件或某一结构发生任何形状、
尺寸或材料性质的变化,造成这些系统处于无法充
分地执行其特定的功能的状态。
产品在工作范围内,出现零件 破损、断裂、卡死、损坏的现 象
在规定条件下不能完成既定功 能
失效
在规定条件下,产品参数值不能维 持在规定的上下限之间
3. FMEA解释
主要运用在两个方面,设计(DFMEA)和过程( PFMEA)。
在产品设计阶段和过程设计阶段,对构成产品的 子系统、零件,及构成过程的各个工序逐一进行分 析,找出所有潜在失效模式,并分析其可能的结果 ,从而预先采取必要的措施,以提高产品的质量和 可靠性的一种系统化的活动,并将全部过程形成文 件。
3. FMEA解释
4. FMEA填写说明
潜在失效后果说明 ●是指失效模式对顾客产生的影响。
注意: 1.要根据顾客可能发现或经历的情况来描述失效的后果; 2.如果某一失效模式对应多个失效后果,应逐一列出,加以分析。 2.顾客可能是内部客户,也可能是外部最终客户,包括最终使用着、主机厂组装客户或下一道工序操作人员; 3 如果顾客是最终使用者,典型失效后果有:异音、异味、外观不良、触感差、不起作用、不稳定、不符合法规等。
4. FMEA填写说明
●PFMEA编辑逻辑思路:
功能、特征 或要求是什 么?
影响是什么 ?
影响有多严 重?
起因是什么 ?
发生概率有 多大?
可能有何错误?
--功能丧失 --功能降低 --功能过强 --功能间隙性中断 --非预期功能
能否被探测 到?
探测它的方 法有多好?
可以怎样改 进?
--设计变更 --过程变更 --特别的控制 --标准的更改
FMEA培训B

※责任工程师有几种方法来确保建议的措施得到实施,包括但不限于以下几种: a)对设计、过程及图样进行评审,以确保建议措施得到实施: b)确认设计更改已纳入到设计/装配/制造文件中; c)对设计/过程FMEA、FMEA的特殊应用以及控制计划进行评审。 FMEA动态文件:
初始 FMEA
修正 FMEA1
修正 FMEA2
制造和装配过程潜在失效模式及后果分析 (过程FMEA)
过程FMEA开发 ※过程FMEA是由负责制造/装配的工程师/小组主要采用的一种分析技术,用以最大 限度地保证各种潜在失效模式及其相关的起因/机理已得到充分的考虑和论述。 FMEA以最严密的方式总结了开发一个过程时小组的思想(其中包括根据以往经验可 能出错的一些项目的分析)。这种系统化的方法体现了一个工程师在任何制造策划 过程中正常经历的思维过程,并使之规范化。 ※过程FMEA: ●确定过程功能和要求; ●确定与产品和过程相关的潜在的失效模式; ●评价潜在失效对顾客产生的后果; ●确定潜在制造或装配过程起因并确定要采取控制来降低失效产生频度或失效条件 探测度的过程变量; ●确定过程变量以此聚焦于过程控制; ●编制一个潜在失效模式的分级表,以便建立一个考虑预防/纠正措施的优选体系 ●记录制造或装配过程的结果。
“我先..............所以没有” 看了天气预报 所以没有 淋成落汤鸡 评估金融大楼高度 所以没有 影响飞机安全 设计电脑防火墙 所以没有 被黑客入侵 作好桥梁设计 所以没有 造成重庆彩虹大桥倒塌
※我先 ※我先 ※我先 ※我先
注意 ※及时性是成功实施FMEA的最重要因素之一 ※它是“事前的预防”而不是“事后的追悔” ※事先花时间进行FMEA分析,能够容易且低成本地对产品设计或制程进行修改 从而减轻事后修改的危机 ※FMEA能够减少或消除因修改而带来的更大损失的机会,它是一个相互作用的 过程,永无止境的改善活动
2024版FMEA培训教材(共14)

FMEA核心思想
预防性
FMEA强调在产品设计或过程设 计阶段进行预防性的分析,识别
并消除潜在的失效模式。
结构化
FMEA采用结构化的分析方法, 通过系统的、有条理的分析过程 来识别潜在的失效模式及其影响。
优先级
FMEA根据失效模式的严重度、 发生频度和探测度来评估其风险 优先级,以便优先处理高风险失 效模式。
01
02
03
04
FMEA报告
编写FMEA报告,包括分析过 程、结果汇总、风险控制措施
和建议等。
风险矩阵图
绘制风险矩阵图,直观展示各 种失效模式的风险等级和分布
情况。
改进措施计划
针对高风险失效模式,制定详 细的改进措施计划,明确责任
人、时间节点和预期效果。
经验教训总结
总结FMEA实施过程中的经验 教训,为后续产品设计和制造
跟踪改进措施实施情况
对制定的改进措施进行跟踪,确保措 施得以有效实施并取得预期效果。
产品设计阶段FMEA案例分析
案例一
案例二
某型号手机电池过热问题。通过对手 机电池设计进行FMEA分析,发现电池 过热可能导致手机性能下降甚至引发 安全问题。经过评估,该故障模式的 严重性较高。针对这一问题,改进措 施包括优化电池散热设计、提高电池 热稳定性等。
可靠性等方面的人员。
收集资料和信息
03
收集与产品、过程、历史数据等相关的资料和信息,以便进行
全面分析。
FMEA实施过程
识别潜在失效模式
通过分析设计、制造过程、使用条件 等方面,识别产品可能出现的潜在失 效模式。
确定风险等级
综合考虑失效模式的严重度、发生频 度和探测度,确定每种失效模式的风 险等级。
第五版-FMEA-新版FMEA【第五版】

1963年
美国太空总署 (NASA)“阿 波罗”探月项目
1993年
美国三大汽车公 司和美国汽车工 业行动集团 (AIAG)等组 织编制和出版了 《FMEA参考手 册》
1234
5.FMEA工作方法
建立多方参与团队DFMEA:
678
核心团队
DFMEA协调员 设计工程师 系统工程师 零部件工程师 测试工程师
C
3 潜在失效
准备 减少开发过程中的后期变更
保持无缺陷产品的发布
4 影响和起因 2024/8/12
在内外部顾客和供应商之间进行有针对性的沟通
在公以司最内低部建的立成知识本库及,即时将提获供得的优经良验教的训产形成品文
D
件
使组件、系统和车辆符合注册获批所需的法规
2024/8/12
持续 改进
预防
防错
团队 合作
2024/8/12
实施注意事项:
FMEA的有效实施及其结果执行汽车行
业产品设计者、制造商和或组装企业的
职品实施在责FM使之EA时一用,就寿。道遵循命在以下期进规范间行: 的分运析行时明确 条, 件必A ,须B特考虑别真实产是
安明确全: 技风术术险语明确和可预见的(但非故意)不当
使真实用: 失,效影这响真点实 很重要。
FMEA 是一种 “事前” 行为202,4/8/12 而不是
FMEA是一 种“事前”
FMEA是一 种“事前”
FMEA是 一种“事 前”行为, 而不是
12345
6.FMEA时间节点
78
FMEA是一种“事前”行为, 而不是“事后”行为; 基于VDA-MLA【新零件成熟度保障】, 识别FMEA关键节点;
• 管理层负责选择和分配资源, 并确保 在计划的项目时间实施有效的风险管 理负有最终责任
FMEA技术手册

FMEA在产品策划中的运用
DMEA
跨功能小组在开展设计FMEA时,应参考以下文件和资料:
保修信息。 顾客抱怨、退货资料。 纠正和预防措施。 类似产品的设计FMEA APQP第一阶段输出,即第二阶段输入和 任何其它相应输入。
DFMEA输出
设计FMEA的输出
潜在设计失效模式。 潜在关键设计要求。 设计问题:曾经受到制造和装配作业挑
中的重要條款,並要求合約對象實施FMEA。
4.1972年美國福特汽車公司所屬北美汽車業務部 訂定之“可靠性方案”中設置一個專案小組負 責研議FMEA,其後列於該公司Q-101品質管理 規範中。
5.1974年美軍出版MIL-STD-1629 FMECA作業程 序,並於1980年修訂為MIL-STD-1629 A,延 用至今。
【化學類失效模式】 退化、剝落、腐蝕、變色、固化、污染、化學 性過熱、沸騰等。
DFMEA 影响度解析
1)影響解析乃針對各個失效模式,考慮系統之製造階 段 或使用階段(啟動、停止、部份負荷、滿載運轉等)狀況 下得機能、狀態或進行評估。
(2)利用可靠性方塊圖來檢討失效的影響範圍
(3)對相關系統或大眾、環境的影響進行解析
/
) (8)FMEA 20 (21)
7
7
/
-
6
7 294
T-118
T-109 T-301
4
7 196
T-118
T-109 T-301
a.
(
//
/
b.
7
2
# 2 28
1265
7
2
8 280
c.
7
4
4 112
(6)FMEA
1234
FMEA培训教材ppt完整版

FMEA培训教材ppt完整版•FMEA概述与基本原理•失效模式识别与评估方法•故障原因分析技巧与工具应用•风险等级划分标准与应对措施制定目录•FMEA在产品设计阶段应用实践•FMEA在生产过程监控和持续改进中作用•总结回顾与展望未来发展趋势01FMEA概述与基本原理FMEA定义及发展历程FMEA定义故障模式与影响分析(FailureModes and Effects Analysis)发展历程起源于军事领域,后广泛应用于航空、汽车、电子等各个行业FMEA核心思想与目标核心思想预防性分析,识别潜在故障模式及其对系统的影响,提前采取措施降低风险目标提高产品可靠性、减少维修成本、增强客户满意度032. 功能分析识别系统或部件的功能及潜在故障模式01适用范围产品设计、生产过程、服务流程等各个环节021. 定义范围明确分析对象及目标评估故障模式对系统性能、安全、经济等方面的影响3. 故障影响分析综合考虑故障发生概率、严重度及可检测性,对故障模式进行风险等级排序4. 风险等级评估针对高风险故障模式,制定预防措施和应急计划5. 制定措施定期回顾FMEA 结果,更新措施并持续改进6. 跟踪与持续改进02失效模式识别与评估方法产品无法实现设计功能或性能不达标,如电子设备无法开机、机械部件卡滞等。
功能性失效安全性失效可靠性失效产品存在安全隐患,可能导致人身伤害或财产损失,如汽车刹车失灵、电器短路引发火灾等。
产品在规定条件下和规定时间内无法完成规定功能,如电池寿命短、设备频繁故障等。
030201常见失效模式类型介绍失效模式识别技巧与工具技巧了解产品工作原理及结构特点分析历史故障数据及维修记录•运用头脑风暴等方法集思广益工具故障树分析(FTA)事件树分析(ETA)因果图(Cause-Effect Diagram)01020304•方法选择:根据失效模式的性质和影响程度选择合适的评估方法,如风险矩阵、风险指数等。
实施流程1. 明确评估目标和范围2. 收集相关数据和信息3.选择合适的评估方法并建立评估模型4.对失效模式进行定量或定性评估5.根据评估结果制定相应的改进措施并跟踪验证03故障原因分析技巧与工具应用故障树分析法概述故障树的建立故障树的定性分析故障树的定量分析故障树分析法(FTA )原理及应用01020304介绍FTA 的基本概念、原理、作用及适用范围。
FMEA模板及介绍

Prepared by Justin Tao 32
2. 特性分类
按状态分: 产品特性和过程特性
按重要程度分: 1)关键特性: 与安全、法规有关的关键特性(特殊特性) 与功能、装配有关的关键特性(重要特性) 2)普通特性:除关键特性之外的所有特性
4. DFMEA潜在失效后果
潜在失效后果(设计) :
就是失效模式对功能的影响,就如顾客感受的一样。 要根据顾客可能发现或经历的情况来描述失效的后
果。 要清楚地说明该失效模式是否会影响到安全性,或
与法规不符。 不同级别的系统、子系统或零件之间存在着系统层
次上的关系。
Prepared by Justin Tao 19
工程的影响
采取可行的对策
Prepared by Justin Tao 11
5. FMEA分类
依据阶段不同可分为: DFMEA PFMEA
依据作用不同可分为: 系统FMEA 子系统FMEA 零件FMEA
Prepared by Justin Tao 12
二、FMEA关键术语理解
13
1. FMEA失效
SFMEA
来自SFMEA
生的原因
PFMEA 问题产生的原因来自 和DFMEA相同 详细的过程失效
DFMEA
的后果
模式产生的原因
Prepared by Justin Tao 39
3. FMEA的时间顺序
DFMEA PFMEA
概念 初始设计 设计完成 样件制造 设计/过程 生产开始 确认
DFMEA 开始早于过程,完成时间在早期的图样完成但任何工 具的制造开始之前 PFMEA 开始于基本的操作方法讨论完成时,完成时间早于生产 计划制定和生产批准之前
FMEA标准手册(完整资料).doc

FMEA
Potential Failure Mode and Effect Analysis
潜在失效模式与后果分析
概 要
概 述
本手册介绍了潜在失效模式及后果分析(FMEA)的概念,给出了运用FMEA技术的通用指南。FMEA可以描述为一组系统化的活动,其目的是:
1)发现、评价产品/过程中潜在的失效及其后果;
时间性是成功实施FMEA的最重要因素之一,它是一个“事前行为”,而不是“事后练习”。为达到最佳效益,FMEA必须在设计或过程失效模式被无意地纳人设计产品之前进行。事先花时间很好地进行综合的FMEA分析,能够容易、低成本地对产品或过程进行修改,从而减轻事后修改的危机。FMEA能够减少或消除因修改而带采更大损失的机会。适当地加以应用,FMEA是一个相互作用的过程,永无止境。
设计FMEA
简 介
设计FMEA主要是由“负责设计的工程师/小组”采用的一种分析技术,用来保证在可能的范围内已充分地考虑到并指明各种潜在的失效模式及其相关的起因/机理。应评估最终的产品以及每个与之相关的系统、子系统和零部件。FMEA以其最严密的形式总结了设计一个零部件、子系统或系统时,一个工程师和设计组的设计思想(包括根据以往的经验和教训对可能出现问题的项目的分析)。这种系统化的方法体现了一个工程师在任何设计过程中正常经历过程,并使之规范化、文件化。
·为推荐和跟踪降低风险的措施提供一个公开的讨论形式;
·为将来分析研究现场情况、评价设计的更改及开发更先进的设计提供参考。
顾客的定义
设计FMEA中“顾客”的定义,不仅仅是指“最终使用者”,还包括负责车型更高一级装配过程设计的工程师/小组,以及在生产过程中负责制造和售后服务的工程师。
FMEA的全面实施要求对所有新的部件、更改的部件以及应用或环境有变化的沿用零件进行设计FMEA。FMEA始于负责设计工作的工程师,但对有专有权的设计来说,可能始于其供方。
FMEA培训教材(PPT14)
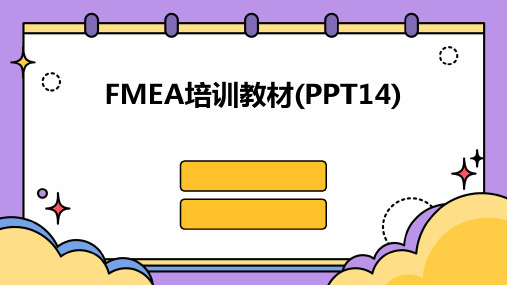
某电子厂在生产手机主板时,通过FMEA分析发现某道工序 存在潜在的静电影响,及时改进了生产工艺和防静电措施, 提高了产品质量和生产效率。
生产过程FMEA优化建议
完善数据收集机制
建立生产过程的数据收集和分析机制,为 FMEA分析提供全面、准确的数据支持。
A 加强团队培训
提高FMEA团队成员的专业技能和分 析能力,确保FMEA分析的准确性和
用的质量工具。
标准化
为了规范FMEA的实施过程,国 际标准化组织(ISO)和美国汽 车工程师学会(SAE)等机构制 定了相关的FMEA标准和指南。
FMEA核心思想
预防性
结构化
FMEA强调在产品设计或过程设计阶段进行 预防性的分析,识别并消除潜在的失效模 式。
FMEA采用结构化的分析方法,通过系统的 、有条理的分析过程,确保所有潜在的失 效模式都被充分考虑。
设定分析目标
明确FMEA分析的目的和预期结 果,例如降低故障率、提高可靠 性等。
组建FMEA团队
确定团队成员
包括具有专业背景和实际经验的跨职 能团队成员,如设计、制造、质量、 维修等。
明确团队职责
分配各成员在FMEA分析中的具体职 责和任务。
收集相关资料
01
02
03
收集历史数据
收集与分析对象相关的历 史故障数据、维修记录等 。
案例二
某医院医疗设备保养FMEA分析。医院对重 要医疗设备进行定期保养,但保养过程中经 常出现漏检、误检等问题。通过FMEA分析 ,发现保养流程不规范、人员技能不足是导 致问题的主要原因。医院采取了优化保养流 程、加强人员培训等措施,提高了医疗设备
保养的质量和效率。
THANKS
感谢观看
第五版FMEA培训教材新版

汽车制造业FMEA应用案例分享
案例分析一
案例分析二
案例分析三
某汽车制造公司针对发动机系统 的FMEA分析,通过识别潜在故 障模式、影响及危害度,制定相 应的预防措施和探测措施,成功 降低了故障率,提高了产品质量。
另一家汽车制造企业在车身设计 阶段运用FMEA方法,对车身结 构、材料、制造工艺等方面进行 全面分析,提前发现并解决了潜 在的设计问题,减少了后期更改 成本和风险。
航空航天领域
FMEA方法可用于飞机、发动机 等关键部件的设计和制造过程中, 通过识别潜在故障模式和影响, 制定相应的预防措施和探测措施, 确保航空器的安全性和可靠性。
医疗器械领域
FMEA方法可用于医疗器械的设 计、生产和使用过程中,通过对 潜在故障进行分析和预防,确保 医疗器械的安全性和有效性,保 障患者的生命健康。
03
加强与供应商和客户的沟通和协作,共同提升产品质量和可 靠性。
持续改进方向和目标设定
持续改进方向和目标设定
01
目标设定
02 降低产品故障率和维修成本,提高客户满 意度。
03
提升生产过程稳定性和效率,减少生产中 断和浪费。
04
构建完善的持续改进机制和体系,推动企 业持续改进和创新发展。
05
案例分析:典型行业应 用实例剖析
发展历程
FMEA起源于20世纪60年代的军事领 域,后来逐渐在汽车、航空航天、医 疗等行业得到广泛应用。随着工业技 术的不断进步,FMEA也在不断发展 和完善。
FMEA核心思想与目的
核心思想
FMEA的核心思想在于“预防”,即在产品或过程设计阶段,通过识别潜在的故障模式、评估其影响程度,并采 取相应的预防措施,以降低产品或过程在后续阶段出现故障的风险。
FMEA分析法讲解

评估故障模式对生产过程的影响
故障频率评估
分析历史故障数据,确定各种故障模式发生 的频率。
故障严重程度评估
评估故障模式对生产质量、成本、交货期等 方面的影响程度。
故障可检测性评估
评估在现有技术条件下,故障模式被及时检 测出的可能性。
制定预防措施以降低故障率
设备维护与保养
建立完善的设备维护与保养制度,确保设备 处于良好状态。
FMEA应用领域
制造业
服务业
FMEA在制造业中广泛应用于产品设计、过 程设计、设备维护等方面,以确保产品质 量和生产过程的稳定性。
FMEA也可应用于服务业,如金融、医疗、 教育等,用于识别服务过程中的潜在失效 模式,提高服务质量。
软件开发
风险管理
在软件开发领域,FMEA可用于识别软件系 统中的潜在故障模式,提高软件的可靠性 和稳定性。
05 FMEA在生产过程中的应用
CHAPTER
识别生产过程中的潜在故障模式
分析历史故障数据
收集并整理过去生产过程中出现的故障记录,通过统 计分析识别出常见的故障模式。
工艺流程审查
对生产流程进行详细审查,找出可能导致故障的环节 和因素。
设备与工具检查
检查生产过程中使用的设备和工具,识别其可能存在 的故障模式。
03
根据风险等级,对故障模式进行排序,优先处理高 风险故障模式。
优化产品设计以降低风险
01
针对识别出的故障模式和评估 结果,提出相应的优化措施, 如改进设计、采用更可靠的元 器件、增加冗余设计等。
02
对优化措施进行实施,并对实 施效果进行验证和评估,确保 措施的有效性。
03
通过对产品设计的持续改进和 优化,不断降低故障模式的风 险等级,提高产品的可靠性和 安全性。
FMEA培训教材(英文版)(ppt 79页)
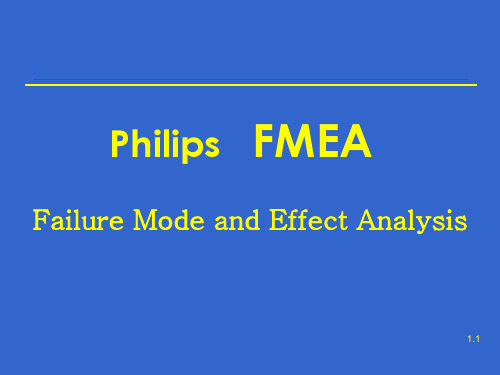
1.5
FMEA – Purpose
Failures
FMEA
CR
Time
(Productionstart)
1.6
FMEA – Purpose
actionable level Represents all wants, both spoken
and unspoken.
1.20
Describe Function
Verb
Indicates action, occurrence, being
Generate Control Display
Startingdate/ revisiondate?
1.12
Managing FMEA’s
FMEA’s are living documents and are updated ...
Modification to a product or process is planned
Component is to be used in new environment
team.
1.17
Blockdiagram
Service
Assembly
Part
Screw Component/
Weld
Part
X
Assembly
Y
User
Other systems
Adhesive
Part
Z
1.18
Example blockdiagram (Settop Wildfire)
- 1、下载文档前请自行甄别文档内容的完整性,平台不提供额外的编辑、内容补充、找答案等附加服务。
- 2、"仅部分预览"的文档,不可在线预览部分如存在完整性等问题,可反馈申请退款(可完整预览的文档不适用该条件!)。
- 3、如文档侵犯您的权益,请联系客服反馈,我们会尽快为您处理(人工客服工作时间:9:00-18:30)。
* 檢測失效的能力?
* 風險优先指數? * 改善方案?
Detection
Risk Priority Number (RPN) Recommended action
風險优先指數(RPN)
RPN 評估
理解或行動
對產品有較小的危害
1 < RPN< 50
51 < RPN <100
對產品有中等的危害,需進一步改 善
帶有報警性提
示的影響 很高
當一個潛在的失效模式影響安全生產或不适應所規定的控制要求----很高 的危害性,失效的出現可能帶有報敬性的提示 對產品生產線是主要的破坏因素,產品可能全部報廢,由于產品失去 了基本的功能需不能使用,客戶很不滿意
9
8
高
對產品生產線有較高的破坏性影響,產品需要Sorting,部分有可能報 廢,產品可以使用,但是由于性能降低而客戶不滿意
4
微小
對產品生產線有較微小的破坏性影響,部分產品有可能需要在生產線 返工,產品的不足被一般客戶所注意
3
很細微
對產品生產線有較微小的破坏性影響,部分產品有可能需要在生產線 返工,產品的不足被很敏銳的客戶所注意
2
無
1
附表3 :評估其發生的可能性
失效的可能性 很高:失效是不可避免 可能的失效率 >> = 1 in 2 1 in 3 高:通常与工序聯系在一起,類似于 經常出現失效的前工序 中:通常与工序聯系在一起,類似 1 in 8 1 in 20 1 in 80 CPk < 0.33 > = 0.33 > = 0.51 > = 0.67 > = 0.83 等級 10 9 8 7 6
對危險性高的工序作“* ”標記,表示將對此工序進行 Process FMEA.
2>. 确定所ห้องสมุดไป่ตู้分析的失效模式 (potential failure mode), 附表1。
3>. 分析失效模式對客戶的所造成的影響 (potential failure effect), 附表1。
4>. 評估影響的嚴重程度 (severity), 附表1、2。 5>. 分析失效的可能原因 (failure cause),人、机、料、法、環等原 因。見因果圖。 6>. 評估其發生的可能性 (occurrence), 附表1、3。
4、FMEA 的作用(2)
2、FMEA 可幫助我們量化确認: * 哪一种失效會發生? Failure mode * 發生后會造成什么影響? Effect * 其影響的嚴重性有多大? Severity * 是哪一种原因導致失效? Cause * 失效發生概率? * 當前工序控制方法? Occurrence Current Process Control Plan
5、FMEA 的應用范圍(2)-品質改善程序
DFMEA
PFMEA
控制方案 投入 改善系統 研究 / 測量 工序 出貨 產品
改善行動 消除變异 惡性 合并 良性
尋找預期 的變异
否 与控制界限 進行比較
研究變异 的性質 研究變异 的原因
是否變異
是
6、FMEA 的程序步驟
組成研
繪出流程圖
确定各個工序的功能
3、FMEA 的特點
分析失效模式;确定失效原因;評估失效效應;
將“失效的嚴重性、失效發生的可能性、失效檢測
的可能性”這三方面進行量化;
确認改善效果。
4、FMEA 的作用(1)
1、 FMEA 是 一种統計工具: * 控制工具; 設計控制 / 生產控制 / 過程控制; * 風險性分析工具; * 管理工具: 識別和評估潛在的失效模式及其影響; 确定能夠消除或減少潛在的失效發生的改善措施。
嚴重性(S):對應于某潛 在失效效應的嚴重程度
對工序或客戶無影響 客戶可能忽略的失效 對性能有微小影響
對性能有較小影響 對性能有影響 工序/產品性能會降 低但安全 工序/產品性能會降低 很嚴重以致不可修 复或無法使用 非常嚴重 (帶有 警報提示的影響) 安全性或可靠性故障 (不帶有警報提示的影響)
較低水平的控制 低水平的控制 難于控制 很難控制 几乎無法控制
效應 (Effect): 指失效模式對客戶(包括下工序)所造成 的影響;
2、什么是 FMEA (2)
FMEA 是一种用來确認風險的分析方法,它包含:
确認潛在的失效模式并評价其產生的效應;
确認失效模式對客戶所產生的影響;
确認潛在的產品/過程失效原因;
确認現有控制產品/過程失效的方法; 确定排除或降低失效改善方案; 設計之前預先進行風險分析,确保設計水平。
7
中等
對產品生產線有較高的破坏性影響,部分有可能報廢但不需要Sorting, 但是有諸多本該方便舒适的操作不能使用,使客戶覺得不方便
6
低
對產品生產線有破坏性影響,產品有可能全部需要返工,在降低性能 的情況下產品可以使用,但客戶還是感到不滿意
5
很低
對產品生產線有較低的破坏性影響,產品可能需要Sorting, 部分產品需 要返工,產品的不足被許多客戶所注意
工序的設計,我們可以預先進行DFMEA,盡可能周全地考慮產 品規格,工序操作水 平、 工序能力等諸多因素,使工序符合規 定的要求。
2>、生產過程的FMEA (PFMEA---Process FMEA):
在制程規劃和制程設計中,預測制程中可能出現的異常及這些異常所帶來
的對產品品質,設備,工裝,人員之影響和效應. 在異常產生的諸因素中,哪 一個系統原因影響最大?是否主要原因。。。。。其它,如 Cpk 低、生 產過程异常等等都可以通 過采用 PFMEA 直觀地找出主要原因,進行改 善達到應有的效應。並針對之進行分析評估采取預防和改善措施.
7
8 9 10
8. 實施FMEA應注意的問題
導入時機:FMEA團隊必須包括產品設計及其相關工程人員
FMEA分析 重在工程分析
FMEA先期規劃應做好 FMEA建義改善措施必須認真執行,並追蹤改善效果 FMEA導入時機 貫穿產品設計,制程設計 FMEA是個循環過程
FMEA結果利用
î ª ¨ í ¤ é ´ Á:
Responsibility& ï µ § ½® Ī G Potential Potential Effect Severity Potential Cause Occurrence Current Process Detection Failure Mode Recommended Completiont S O D R of Failure¢ ¥® Ä Ä Y « « × of Failure ¥ ¢ ® Ä µ o ¥ Í À W« × Control² { ¦ æ ± ¨ î Ë À ´ ú ¥ i ¯ à R.P.N ç ¦b ¥ ¼ ¢ ® ļ Ò Action« ØÄ ³ ± ¹ ¬ I ³ d ¤ H &§ ¹ ¦ ¨ ¤ é Action Result E C E P (1-10) (1-10) º ¼ ª ç ¦b ¼ v T Å º ç ª ¼ ¦b ì ¦] è k ¤ ª Ê © (1-10) ¦æ ° ʲ µ ª G ¦¡ Á ´ V C C N
* 确定當前的工序控制方法并評估其檢測失效的可能性(附表4)。
* 确定 RPN 值并根据 RPN 值采取相應的改善措施。
附表2: 評估影響的嚴重程度
影響 不帶有報警性 提示的影響 危害的程度 當一個潛在的失效模式影響安全生產或不适應所規定的控制要求----很高 的危害性,失效的出現可能不帶有任何報警性的提示 等級 10
* 收集數据 * 排定原因 * 選定主因 * 确認改善
修定文件, 重新排列
FMEA Development Process Work Sheet
Page:
of
潛在的原因
Design or Process Function
法 潛在影響 机 失效模式
A B C
料 人
環境
7、FMEA
1 2 3 4 5 6
3>、設備維護的FMEA (EFMEA---Equipment FMEA):
如新設備的投入運行,我們亦可以預先進行 EFMEA,分析、考慮由于設 備可能造成的產品品質問題及可靠性問題等原因,預防采取措施消除不 良因素;現有設備、特定的一种設備在運行中出現的設備故障等均可采 用FMEA進行改善,以确保設備的正常運轉。
對產品有嚴重危害,需深入調查分析
101 < RPN <1,000
5、FMEA 的應用范圍(1)
1>、設計階段的FMEA (DFMEA---Design FMEA):
預測產品設計中某些設計目標值可能產生的失效及分析這些失效 會對個產品外觀,結構,功能, 及必能穩定性,可靠性及對制程造成的
影響,並針對之從產品設計和制程設計等方面提出改善 措施如新
以分析Cosmos HFA 在組裝過程中對Slider profile影響為例
1>、确定工序 Flow chart / Risk Assessment 工序流程 / 危險性評估
Process step (工序步驟) Risk Assessment 危險性評估
* Pot mounting block & gimbals with epoxy
究小組
RPN = S x O x D
制作 Pareto 圖 選擇失效模式 進行改善
是
确定失效模式 標識其效應 標識其原因 標識當前 控制方法 估計嚴重性(S) 估計發生概率(O) 估計可測性(D)
RPN= 風險指數
完成?
明确如何改善: 嚴重性? 發生概率? 測試性?